SAE J1128v003
SAE_J1128_2000_(中文版)_低压初级电缆

3
S.P.L CABLE
SAE J1128-2000
5 一般要求 对于每种型号的电缆 成品应满足图表 2 规定的所有试验的要求
图表 2 一般要求 条款 5
条款
项目
要求 TWP GPE HDT
STS HTS
TWE GTE HTE
TXL GXL SXL
5 一般要求
5.1 导体
5.2 绝缘
5.3 外径
*
1 适用范围 本 SAE 标准适用于额定直流电压 60V(交流 25V)或以下地面车辆电气系统用低压初级电缆 文中的试
验旨在检验电缆在有限流体和物理应力的作用下正常使用时的质量
2 参考文献 2.1 适用出版物 -下列出版物因被本标准引用而成为本标准的一部分 除非另有规定 SAE 出版物应使用 最新版本 2.1.1 SAE 出版物
SAE1128_中文版最新
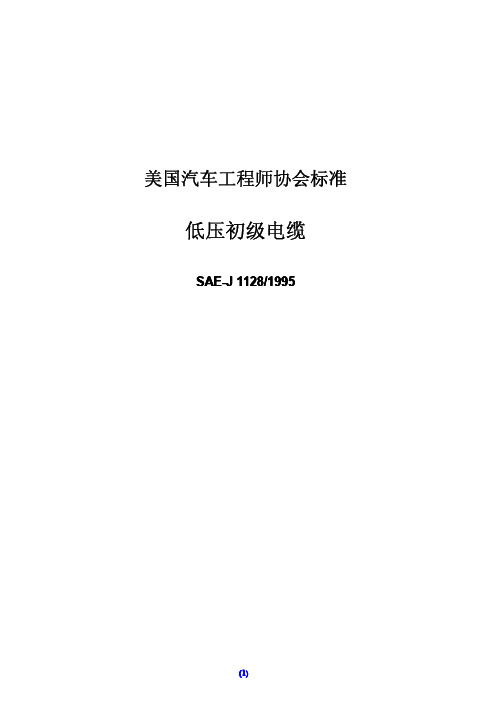
(3)
GPT 型-通用热塑性绝缘电缆 HDT 型-重型热塑性绝缘电缆
STS 型-标准负荷热固性弹性体(合成橡胶)绝缘电缆
HTS 型-重型热固性弹性体(合成橡胶)绝缘电缆 TXL 型-薄壁交联聚希烃绝缘电缆
GXL 型-通用交联聚希烃绝缘电缆
SXL 型-特种用途交联聚希烃绝缘电缆 TWE 型-薄壁热塑性弹性体绝缘电缆
表 5 机械性能
SAE 电缆 型号
TWP GPT HDT STS HTS
TXL GXL SXL TWE GTE HTE
参见 5.3 条 最小抗张强度
Mpa
psi
11
1600
7
1000
10
1500
11
1600
最小伸长率 试验温度
%
°C+/-2°C
125
110
150
110
150
155
200
150
1. 上述加速老化试验温度适用于本标准目前额定的材料。对于其他材料可能需 要不同的试验条件。
试验项目
导体截面 单线镀层 表面状态
表 2 要求的试验
参见第 4 和 5 节
SAE 电缆型号
TWP GPT HDT
STS HTS
TWE GTE HTE
TXL GXL SXL
×
×
×
×
×
×
最大外径 最小厚度 机械性能
×
×
×
×
×
×
介电试验 低温弯曲 燃烧试验
×
×
×
×
×
×
流体相容性 耐臭氧 耐切通
×
汽车线束的标准和技术条件_概述及解释说明

汽车线束的标准和技术条件概述及解释说明1. 引言1.1 概述汽车线束是指由多根导线以及管道等组成的电气设备的集合体,用于传递和控制汽车各个部件之间的信号和电力。
它在现代汽车中起着至关重要的作用,直接影响了整个车辆系统的性能和安全性。
1.2 文章结构本文将从汽车线束标准和技术条件两个方面进行论述。
首先,我们将介绍汽车线束标准的定义、重要性以及常见标准及其作用。
然后,我们将深入探讨汽车线束技术条件,包括线束材料要求与选择、线束设计与布局要点以及线束制造工艺技术要求。
接下来,我们会详细介绍汽车线束的测试与认证,包括测试方法与工具、认证流程与标准以及常见测试问题与解决方案。
最后,在结论部分对已讨论内容进行总结,并展望未来发展并提出建议和改进措施。
1.3 目的本文旨在通过对汽车线束标准和技术条件的概述和解释说明,使读者了解汽车线束在整个汽车系统中所扮演的重要角色,并且为相关行业从业人员提供有关汽车线束标准和技术的参考和指导,以促进汽车线束的发展和应用。
通过深入了解汽车线束的标准和技术条件,我们可以更好地理解其在汽车工程中的作用,并为未来的设计、生产和测试提供参考依据。
2. 汽车线束标准2.1 什么是汽车线束汽车线束是由电线、连接器、保护套等组成的综合性电气传输系统,用于将电力和信号从发动机、车身控制单元等传输到各个汽车部件和设备上。
它在汽车中起着传导电力和信号的关键作用。
2.2 汽车线束标准的重要性汽车线束标准是为了确保不同厂家生产的汽车线束在技术参数、质量要求和安全性方面达到统一的标准。
这些标准对于整个汽车产业链的健康发展和消费者的安全使用都至关重要。
首先,统一的汽车线束标准可以促进不同厂商之间的互操作性。
由于不同厂商生产的汽车具有不同的架构和系统,如果没有统一标准,各种接口可能无法兼容,导致配件选型困难以及维修、升级等工作变得复杂费时。
其次,通过制定统一的汽车线束标准,可以规范及提高生产过程中的质量管理。
低压初级电缆SAE-J-11281995
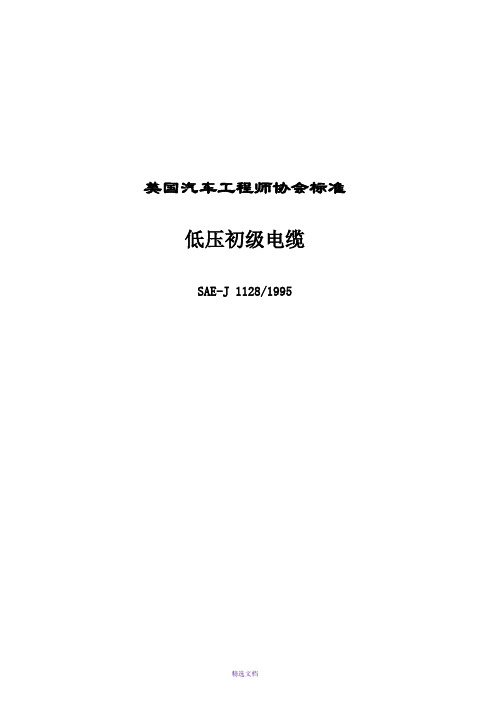
美国汽车工程师协会标准低压初级电缆SAE-J 1128/19951. 范围本SAE标准适用于额定电压50V mms或以下地面车辆电气系统用低压初级电缆。
本文的实验旨在检验正常使用条件下(很少受流体和物理应力作用)的电缆的合格性。
2. 参考文献2.1适用文件下列出版物因被本标准引用而构成本标准的一部分,其中SAE标准应使用最新版本。
2.1.1 SAE出版物EA 1128 颜色偏差参考色谱2.1.2 ASTM 出版物ASTM B1硬拉铜线规范ASTM B3 软或退火铜线规范ASTM B33 镀锡软或退火铜线规范ASTM B49 电工用二次拉伸铜杆规范ASTM B174 束绞铜导体规范ASTM B189 镀铝或铅合金软或退火铜线规范ASTM B193 导体材料电阻率标准实验方法ASTM B263 标准导体截面测试方法ASTM D412 硫化橡胶和热缩性橡胶和热缩性弹性体标准试验方法-张力法ASTM D471 橡胶性能标准试验方法-液体作用ASTM D573 橡胶性能标准试验方法-烘箱老化ASTM E145 重力对流和强迫通风烘箱规范2.1.3 军用出版物Mil-T-5438 实验机:电缆耐磨试验(老式)2.2相关标准下列标准仅供参考,它们不是本标准不可缺少的一部分。
2.2.1SAE出版物SAE J 156 可熔断线路SAE J 1127 低压电池电缆SAE J 1292 汽车、货车、牵引车、拖车和机动车辆的布线SAE J 1654 高压初级电缆SAE J 1673 高压汽车布线2.2.2 ISO出版物ISO6722 道路车辆-无屏蔽低压电缆3. 电缆型号(见表1)TWP型-薄壁热塑性绝缘电缆GPT型-通用热塑性绝缘电缆HDT型-重型热塑性绝缘电缆STS型-标准负荷热固性弹性体(合成橡胶)绝缘电缆HTS型-重型热固性弹性体(合成橡胶)绝缘电缆TXL型-薄壁交联聚希烃绝缘电缆GXL型-通用交联聚希烃绝缘电缆SXL型-特种用途交联聚希烃绝缘电缆TWE型-薄壁热塑性弹性体绝缘电缆GTE型-通用热塑性弹性体绝缘电缆HTE型-重型热塑性弹性体绝缘电缆表1SAE初级电缆型号定义参见第3节4. 通用范围对于每种电缆型号,成品电缆应满足表2规定的所有实验的要求。
SAEJ20V003

SAE Technical Standards Board Rules provide that: “This report is published by SAE to advance the state of technical and engineering sciences. The use of this report is entirely voluntary, and its applicability and suitability for any particular use, including any patent infringement arising therefrom, is the sole responsibility of the user.”SAE reviews each technical report at least every five years at which time it may be reaffirmed, revised, or cancelled. SAE invites your written comments and suggestions.TO PLACE A DOCUMENT ORDER; (724) 776-4970 FAX: (724) 776-0790SAE WEB ADDRESS Copyright 2000 Society of Automotive Engineers, Inc.and servicing2.1.4A UTOMO TIVE I NDUSTRY P UB LICATION—Available from AIAG, 26200 Lasher Road, Suite 200, Southfield, MI48034-7100.QS 9000—Quality System Requirements2.2Related Publications—The following publications are provided for information purposes only and are not arequired part of this document.2.2.1SAE P UBLICATIO NS—Available from SAE, 400 Commonwealth Drive, Warrendale, PA 15096-0001.SAE J20-1—Coolant Hose (Supplement to SAE J20 for Government Use Replacing Part of MS51230)SAE J20-2—Coolant Hose—Normal Service Type Convoluted, Wire Support Hose(Supplement to SAE J20 for Government Use Replacing Part of MS51008)3.Definitions of Hose Types3.1SAE 20R1—Heavy-duty type for service in heavy-duty application. This type is available in two wallthicknesses as indicated in 6.3.3.2SAE 20R2—Flexible heavy-duty wire embedded type for the same service as SAE 20R1.3.3SAE 20R3—Heater hose for normal service.3.4SAE 20R4—Radiator hose for normal service.3.5SAE 20R5—Convoluted wire supported type for normal service.3.6Hose Special Designators for SAE 20RXY—X Refers to the hose type. Y designators may be used forhoses with special features. Multiple Y designators may be used if needed.3.6.1HT—This High Temperature designation is for any hose type, SAE 20R1 to SAE 20R5, which is required tooperate in an environment above 125 °C. (See Section 11.)3.6.2EC—This Electrochemical designation is for any hose type SAE 20R1 to SAE 20R5 which is required tohave electrochemical resistance as defined by SAE J1684. (See Section 12.)3.6.3LT—This Low Temperature designation is for any hose type SAE 20R1 to SAE 20R5 which is required tooperate in an environment down to –55 °C. (See Section 13.)3.7Hose Classes—Compounds based on different synthetic rubber grades are specified and designated (see 5.2for test methods):Class A—high-temperature resistantClass B—high oil resistantClass C—medium oil resistantClass D-1—low oil resistant, improved serviceClass D-2—low oil resistant, standard serviceClass D-3—low oil resistant, high-temperature resistant, premium serviceClass E—low oil resistant, fiber elastomer compositePhysical characteristics for each hose class are shown in Table 1.3.8Marking—The outer cover will be printed with the designation SAE 20RXY (the X being the hose type and Y any special designator(s) such as “LT”), class, size of the inside diameter in millimeters, hose manufacturer’s code marking, and any other identification as agreed upon between user and manufacturer/supplier. It is recommended that this marking shall appear on the outer cover of the hose at intervals not greater than 380mm.3.8.1S MALL ID O R S HORT H OSE —If there is insufficient space on the hose for the required marking due to size or configuration, the marking shall be agreed upon by the customer and the manufacturer/supplier.4.Dimensional Requirements—Geometric Dimensioning and Tolerancing requirements are outlined in SAE J2370. The following requirements are minimal standards:4.1Tube and Cover Thickness—Minimum thickness shall be 1.6 mm for the tube and 0.8 mm for the cover.NOTE—This requirement does not apply for hoses without distinctive tube and cover construction.TABLE 1—COOLANT SYSTEM HOSE ELASTOMERIC MATERIAL, PHYSICAL PROPERTIESSAE Designation Typical Elastomer Class A Silicone Class B NBR Class C CR Class D–1EPDM Class D–2EPDM Class D–3EPDM Class E EPDM/Fiber Typical Temperature Range, °C –55 to 175–40 to 100–40 to 100–40 to 125–40 to 125–40 to 150–40 to 125Original PropertiesDurometer, points Shore A 55 to 7555 to 7555 to 7555 to 7555 to 7555 to 7565 to 85 Tensile, min, MPa 5.58.57.07.0 5.07.0 5.0 Elongation, min, %200250200300150300100Oven Aging Conditions and Change Limits, Hours/°C 70/17570/10070/10070/12570/125168/15070/125 Durometer, points Shore A +10+15+20+15+15+15+15 Tensile, max %–15–15–20–20–20–35–20 Elongation, max, %–40–50–50–50–50–65–50Oil Immersion Change Limits ASTM No. 3 Oil or IRM 903 (IRM 903 is being phased in to replace ASTM No. 3) Hours/°C 70/10070/10070/100———— Volume, max, %0 to +45–5 to +25+80———— Tensile, max, %–40–20–50————Coolant Immersion (Tube only)Change Limits Hours/at Boiling Point 707070707016870 Volume, %0 to +400 to +200 to +20–5 to +20–5 to +20–5 to +20–5 to +20 Durometer, points Shore A –10 to +10–10 to +10–10 to +10–10 to +10–10 to +10–10 to +10–10 to +10Tensile, max, %–30–20–20–20–20–20–20 Elongation, max, %–25–40–40–50–25–25–25Compression Set °C 125100100125125125125 70 h, max, %40507575857585Cold Flexibility (°C)(1)1.LT designator extends the low temperature flexibility to –55 °C.–55–40–40–40–40–40–404.2Length Tolerancea.Straight Hose—Unless otherwise specified by the customer or manufacturer, Commercial Tolerances will be used. See Table 2.b.Curved Hose—The tolerances on arm lengths, measured from end to intersection of nearest centerline, shall be as shown in Table 3.4.3General Layout Tolerances, Curved Hose—Dimensions locating bend intersections and centerline radii are to establish the theoretical design centerline of the hose. Actual outside contour of hose must be held within a total range of 9.6 mm of all planes with respect to theoretical outside contour of hose. For hose check, hose ends should first be placed in theoretical design position before checking (hose may have to be flexed to correct for any distortion caused by handling or during shipment). SAE arm length tolerances shall apply.Tolerances apply to all arm and body lengths in addition to contour tolerances. Dimensions covering more than one arm or body length are reference only and have no tolerances. The wall thickness within bends of a curved hose may differ from the wall thickness of the straight by no more than 33%.When an alignment mark is required for assembly operations, the basic identifier in Figure 1 is recommended:FIGURE 1—ALIGNMENT MARKLocation of the alignment mark and/or additional information shall be determined by the customer and the manufacturer.4.4Enlarged Ends—When the ID of one end of the hose is enlarged, normally the ID of the enlarged end should not exceed the ID of the rest of the hose by more than 33%. Enlarged ends should be considered arm lengths for tolerance purposes. The wall thickness normally changes with enlarged ends.TABLE 2—LENGTH TOLERANCELength mm Precision TolerancemmCommercial Tolerancemm0–300±3.2+9.7–3.2>300±1%+3%–1%TABLE 3—TOLERANCE ON ARM LENGTHArm Lengthmm Precision TolerancemmCommercial Tolerancemm0–300.0±4.0±6.4300.1–610.0±4.8±7.2610.1–910.0±6.4±9.7910.1–1220.0±9.7±11.21220.1–1830.0±12.7±15.9over 1830±1%±2%4.5End Squareness—All points on the hose end surface must lie within a tolerance zone consisting of twoparallel planes perpendicular to the hose axis. The tolerance zone is determined by Table 4.TABLE 4—END SQUARENESSHose ID Precision Tolerance Commercial Tolerance25.4 mm and larger10% of ID15% of IDsmaller than 25.4 mm 2.54 mm 3.75 mm4.6Finish and Roundness on Connections—Users of coolant hose should take every precaution to obtainconnections as smooth and round as practical. (Reference SAE J1231)4.7Clamps—Refer to SAE J1508 for available clamp types.5.Physical Test Requirements and Procedures5.1Finished Product5.1.1A DHES IO N—When applicable, use test procedure ASTM D 413. The minimum requirement is 1400 N/mbetween all elastomer or elastomer-coated plies.5.1.2C OLD F LEX IB ILITY—The following procedure shall be used:For hose 25.4 mm ID and smaller, specimen shall consist of a complete hose of length sufficient to perform bend test described as follows: the hose shall be placed in a cold box for 5 h at the temperature specified in Table 1. The hose shall then be flexed in the cold chamber through 180 degrees from the centerline to a diameter of ten times the maximum outside diameter of the hose within 4 s. The hose shall not fracture and shall not show any cracks or breaks in the tube or cover.For hose larger than 25.4 mm ID, specimens are to be 25.4 mm long sections of the complete hose. The specimen and test fixture shall be placed in a cold box for 5 h at the temperature specified in Table 1. The specimen is then compressed to 50% of its original inside diameter between parallel plates within 4 s. The specimen shall not crack or break. The testing fixture shall be in the cold box during the entire test.NOTE—For LT hose, refer to Section 13 for specific cold flexibility requirements.5.1.3O ZONE T EST AND R EQ UIREMENTS—The following test and requirements apply:When applicable, use test procedure ASTM D 1149.For hose 25.4 mm ID and smaller, a specimen of hose of sufficient length shall be bent around a mandrel with an outside diameter equal to eight times the specified OD of the sample. The two ends shall be tied at their crossing with enameled copper or aluminum wire. After mounting, the specimen shall be allowed to rest in an ozone-free atmosphere for 24 h at standard laboratory test temperature. The mounted specimen shall be placed in a test chamber containing ozone at a partial pressure of 50 mPa ± 5 mPa at a temperature of 40°C ± 1 °C.After 100 h of exposure, the specimen shall be removed and allowed to cool to standard laboratory test temperature and then be inspected visually under 7X magnification. The sample must not show any cracks except for the area immediately adjacent to the wire, which shall be ignored.For hose larger than 25.4 mm ID, prepare a specimen by cutting a strip of the whole hose 12.7 mm x 100mm and tie specimen (cover out) around a 12.7 mm diameter mandrel. Condition in the same manner as specified previously for the whole hose and apply the same conditions and requirements. This test applies to the cover only and cracks in the exposed tube or cut edges of the cover shall be ignored.5.1.4K INK T EST —This test applies to SAE 20R3 hose only. (Not recommended for formed hoses.)5.1.4.1Test Procedure—Condition specimen length of hose at standard laboratory test temperature for at least 2h. Measure the minimum OD at the approximate center of the specimen length. When a sufficient length of hose is available, it is permissible and suggested that a length in excess of the specimen length be used in an effort to minimize the handling variable and overbending. Insert one end of the hose into one hole of the specified test fixture, carefully bend the hose (in direction of natural curvature) and insert the other hose end into the second test fixture hole. Do not overbend or bend hose with sharp motion to prevent excessive kinking or collapse. Within 30 s, measure the minimum diameter at the point of greatest collapse.5.1.4.2Test Fixture—Shall consist of 25.4 mm thick flat plate drilled with holes not to exceed the hose OD by more than 1.6 mm and separated by the specified center distances.5.1.4.3Test Requirements—See Table 5.5.1.5V ACUUM C O LLA PSE T EST —When practical, the entire hose shall be tested as specified in Tables 6A and 6B.The minimum outside diameter shall decrease by no more than 20% during application of vacuum for 15 s and not to exceed 30 s.5.1.6B URST —This test shall be performed on a straight length of hose in accordance with ASTM D 380 to meet the requirement in Tables 6A and 6B.For curved 20R3 and 20R4 hose, the same reference applies, except that the test shall be performed on the individual curved hose with one end free and unrestrained and the rate of application of pressure shall be not less than 2.0 MPa nor more than 7.0 MPa/min. The aged burst requirement (11.2.2) will apply to all HT hoses.5.1.7P RESSURE V IBRATIO N AND T E MP ERATURE OR P RE SSURE AND T EMPE RATURE T EST —This test shall be used when agreed upon between customer and manufacturer/supplier, using SAE J1610 as the referenced test method. If required, test limits can be modified if agreed upon by the customer and manufacturer/supplier.TABLE 5—KINK TEST REQUIREMENTS FOR SAE 20R3 HOSENominal Hose ID mmSpecimen LengthmmCenter DistancemmCollapse of Hose Allowed, %15 and larger 24 x ID 10 x ID 25smaller than 1524 x ID8 x ID25TABLE 6A—BURST AND VACUUM VALUES(20R1 AND 20R2)NominalSizemm20R1Heavy-DutyStandard WallMinBurstMPa20R1Heavy-DutyStandard WallMinVacuumkPa20R1Heavy-DutyHeavy WallMinBurstMPa20R1Heavy-DutyHeavy WallMinVacuum,kPa20R2WireInsertedMinBurstMPa20R2WireInsertedMinVacuumkPa10 3.2933.813 2.9333.816 2.5927.019 2.2427.022 2.2423.625 2.0623.6 2.0684.429 2.0620.332 1.9016.9 3.4533.8 1.9084.435 1.9013.538 1.7210.1 3.1033.8 1.7284.441 1.72 6.844 1.55 3.4 2.7616.9 1.5584.451 1.38 2.4110.1 1.3884.457 1.21 2.41 3.4 1.2184.460 1.2164 1.03 2.06 1.0384.4700.86 1.720.8684.4 760.60 1.720.6984.4 83890.52 1.380.5284.4 1020.34 1.030.3484.4 NOTE—For hose sizes between sizes listed, use the values for the next larger size.5.2Physical Properties are to be Obtained from Specimens Removed from Hose—See ASTMD380 for pro-cedure.NOTE—For 20R5 hoses, test specimens are to be taken from the cuffs.5.2.1D UROMETER H ARDNESS —Hardness shall be measured with a Shore A Durometer according to ASTM D 2240.5.2.2T ENSILE S TRENGTH AND E LONGATION —Test according to ASTM D 412.5.2.3O VE N A GING —Shall conform to ASTM D 573.TABLE 6B—BURST AND VACUUM VALUES(20R3, 20R4, AND 20R5)Nominal Size mm 20R3Heater Min Burst MPa 20R3Heater Min Vacuum kPa 20R4Radiator Min Burst MPa20R4Radiator Min Vacuum kPa20R5Wire SupportedMin Burst MPa20R5Wire SupportedMin Vacuum kPa5 1.7233.86 1.7233.87 1.7233.8 8 1.7233.89 1.7233.8 10 1.7233.8 1.24 13 1.7233.8 1.17 16 1.7227.0 1.10 19 1.3823.6 1.03 22 25 1.2120.30.970.97 29 32 1.2116.90.900.90 35 380.830.83 41 440.760.76 510.690.69 570.620.62 60 640.550.55700.48 760.41 830.34 890.27102NOTE—For hose sizes between sizes listed, use the values for the next larger size.5.2.4C OOLANT I MMERS ION—Volume change, tensile, elongation, and durometer changes shall be observed afterimmersion in the following mixture maintained at the boiling point under a water-cooled reflux condenser.Maintain the fluid level during the test by adding distilled water as needed.a.1/2 by volume, distilled waterb.1/2 by volume, ethylene glycol-based coolant agreed to between supplier and customerMeasurements of tensile, elongation, durometer, and volume change shall be made in accordance with appropriate ASTM methods.5.2.5O IL I MME RSIO N—Shall conform to ASTM D 471.5.2.6C OMPRESSION S E T—Test to be performed per ASTM D 395, Method B. For cover specimens, ply to 8.9 mm± 1 mm, not to exceed 7 plies where applicable. For tube specimens, ply to 12.7 mm ± 1 mm, not to exceed7 plies. When unable to meet the required thickness, use standard ASTM slabs cured at similar cureconditions as the hose.NOTE—SAE J1638 may be considered as an alternate test method with criteria to be agreed upon between customer and manufacturer.6.SAE 20R1 Heavy-Duty Type6.1Scope—This type of hose is primarily for heavy-duty service of which the diesel-locomotive application is atypical example. The hose is intended to withstand the effects of higher pressure systems. When desired, hose with one class of material in the tube and another in the cover may be obtained. In such cases, the physical properties specified for respective parts shall apply.6.2Reinforcement—The reinforcement may consist of multiple plies of woven or cord fabric, or ply or plies ofbraided, knit, or spiraled yarn and shall be such that the hose meets the minimum burst and vacuum requirements as given in Table 6A.6.3Dimensions—The ID Tolerance is ±0.8 mm for sizes smaller than 51 mm and ±1.6 mm for sizes 51 mm andlarger. The Wall Thickness Range for Standard Wall Thickness hose is 4.3 to 5.6 mm. The Wall Thickness Range for Heavy Wall Thickness Hose is 5.8 to 7.1 mm. These dimensions shall be measured at a section not including a lap.7.SAE 20R2 Heavy-Duty Wire Embedded Type7.1Scope—This is similar to SAE 20R1 hose except that it utilizes wire helix or helices built into the wall of thehose. The hose is intended to withstand high vacuum and/or some forced curvature.7.2Reinforcement—The reinforcement is typically multiple plies of woven or cord fabric or ply or plies of braidedor knot yarn and wire helix or helices such that the hose will meet the minimum vacuum and burst requirements as given in Table 6A.7.3Dimensions—The ID Tolerance is ±0.8 mm for sizes smaller than 51 mm and ±1.6 mm for sizes 51 mm andlarger. The Wall Thickness Range at hose ends exclusive of wire gauge is 4.3 to 6.4 mm.8.SAE 20R3 Heater Hose8.1Scope—This type of hose is used in connecting heater systems and other components in the coolantcirculating systems of ground vehicles.8.2Reinforcement—The reinforcement typically consists of one or more plies of woven, braided, knit, or spiraled yarn, or class E material, and shall be such that the hose will meet the minimum burst and vacuum requirements in Table 6B.8.3Dimensions and Tolerances—Target dimensions and tolerances are shown in Table 7. Measurement method must be agreed upon by manufacturer and customer. Since expanded ends may cause wall thickness to change, ODs and tolerances for the expanded ends must also be agreed upon by the manufacturer and customer. Tolerances and dimensions other than those listed as follows must be agreed upon by manufacturer and customer. The values in Table 7 are standard wall dimensions and commercial tolerances.If thin-wall dimensions or precision tolerances are required, refer to SAE J2387.9.SAE 20R4 Radiator Hose Normal Service Type9.1Scope—This is a hose for coolant circulating systems of automotive type engines, commonly known as radiator hose. When resistance to vacuum collapse is a requirement, an inserted wire helix may be specified if desired.9.2Reinforcement—The reinforcement typically consists of one or more plies of woven, braided, knit, or spiraled yarn, or Class E material, and shall be such that the hose will meet the minimum burst and vacuum requirements in Table 6B.9.3Dimensions—Target dimensions and tolerances are shown in 9.3.1. Measurement method must be agreed upon by manufacturer and customer. Since expanded ends may cause wall thickness to change, ODs and tolerances for the expanded ends must also be agreed upon by the manufacturer and customer. Tolerances and dimensions other than those listed as follows must be agreed upon by the manufacturer and customer.Since the wall thickness may change due to bends near the end of hoses, the wall thickness reported will be the average of 4 readings taken 90 degrees apart. The values in 9.3.1 are standard wall dimensions and commercial tolerances. If thin-wall dimensions or precision tolerances are required, refer to SAE J2387.9.3.1D IME NSIO NS AND T OLERANCES —The ID tolerance is ±0.8 mm for hose sizes smaller than 70 mm and ±1.6mm for hose sizes 70 mm and larger. The wall thickness and tolerance is 4.95 mm ± 0.65 mm (4.3 to 5.6mm) for hose sizes smaller than 50.8 mm and 5.35 mm ± 1.05 mm (4.3 to 6.4 mm) for hose sizes 50.8mm and larger.TABLE 7—STANDARD DIMENSIONS AND COMMERCIAL TOLERANCES FOR SAE 20R3ID mm IDTolerance,mmTarget OD (1)mm1. The target OD should be measured over a plug gauge equal to the specified maximum ID.OD Tolerance mm Reference Wall mmMaximum Wall ThicknessVariation mm5.0 to <9.0±0.8Maximum ID Plus 7 mm ±0.8 3.5 1.09.0 to <25.4±0.8Maximum ID Plus 8 mm±0.8 4.0 1.025.4±0.834.0±1.2 4.3 1.0>25.4±0.8Maximum ID Plus 9.9 mm±1.64.951.010.SAE 20R5 Normal Service Type Convoluted, Wire Supported Hose10.1Scope—This is a wire reinforced hose for coolant circulating systems of automotive type engines, commonlyknown as universal type hose. This hose consists of a convoluted section with plain ends. The hose shall contain a wire helix or helices in the convoluted section.10.2Reinforcement—The reinforcement is typically a ply or plies of woven or cord fabric, braided, knot, or spiraledyarn. The hose must meet the minimum burst requirements listed in Table 6B.10.3Dimensions—The ID Tolerance is +0.8 to –1.6 mm. The Wall Thickness Range is 3.6 to 4.8 mm.11.High-Temperature Service Hose HT11.1Scope—Any hose type SAE 20R1 to SAE 20R5 which is required to be operated in an environment above125°C. The letters HT will be used to designate this new requirement, for example, SAE 20R1 HT Class A standard wall.11.2Requirements11.2.1T UBE AND C OVER—The tube and cover compounds must be Class A or Class D-3.11.2.2A GED B URST—The reinforcement yarn or fabric must be such that the hose passes the minimum burstrequirements given on the appropriate table after aging 168 h at 150 °C in a hot air oven.12.Electrochemical Resistant Hose EC12.1Scope—Any hose type SAE 20R1 to SAE 20R5 which is required to have electrochemical resistance. Theletters EC will be used to designate this requirement, for example SAE 20R1 EC.12.2Requirement—Hoses shall be tested in accordance with SAE J1684. Test method 1 shall be utilized todetermine the electrochemical resistance of the hose assembly.13.Low-Temperature Service Hose LT13.1Scope—Any hose type SAE 20R1 to SAE 20R5 and any hose class which is required to be operated in anenvironment down to –55 °C. The letters LT will be used to designate this requirement, for example, SAE 20R1LT Class A standard wall.13.2Requirements—Test frequency is a minimum of annually, per QS 9000.13.2.1R ESISTA NCE TO V IBRATION—This applies to SAE 20R2 wire embedded hoses only. The requirements of5.1.7 shall apply, using SAE J1610, Test Procedure #1, as the recommended practice.13.2.2P ROOF P RESSURE—This test shall be performed on a straight length of hose in accordance with ASTM D 380with the pressure being equal to 50% of the Burst Pressure requirement in Tables 6A and 6B. For curved 20R3 and 20R4 hose, the same reference applies, except that the test shall be performed on the individual curved hose with one end free and unrestrained and the rate of application of pressure shall be not less than2.0 MPa/min nor more than 7.0 MPa/min.13.2.3C OLD F LEX IB ILITY—The test temperature shall be –55 °C. Test per 5.1.2.13.3Qualification Tests13.3.1R EQUIREMENTS FOR Q UALIFICATION—Qualification is required for all hoses to the Low-Temperature ServiceHose requirement. Qualification will consist of initial qualification testing and inspection. Each manufacturer will be responsible for meeting the requirements for qualification.13.3.2Q UALIFICATION T ESTS—For qualification tests, one 8 m length of bulk hose or 10 hoses or assemblies of eachsize to be qualified shall be tested. In order to qualify under this document, hose and hose assemblies must meet the requirements of SAE J20, type and class as specified, and the following tests: visual inspection, cold flexibility at –55 °C, proof pressure as specified in 13.3.3 and resistance to vibration (for wire embedded hoses only.)13.3.3Q UALIFICATION R ETESTS AND R EJECTION—Any hose or assembly that fails in one or more tests shall beresampled and retested. Twice the number of specimens shall be selected from the lot in question for any retests, and failure of any of the retested samples shall be cause for rejection.13.4Qualification Frequency—Testing on the LT-type family of hose shall be performed to show that the hosemeets the requirements of the Low-Temperature hose at least every two years or if the formulation is changed, or for major design or process changes. Data that supports the manufacturer meeting the requirements shall be maintained and be made available to any present or prospective customer. Data may be obtained from performance of other program testing requirements, such as QS 9000 or ISO 9001, as long as it is the same design as the Low-Temperature hose described herein.14.Notes14.1Marginal Indicia—The change bar (l) located in the left margin is for the convenience of the user in locatingareas where technical revisions have been made to the previous issue of the report. An (R) symbol to the left of the document title indicates a complete revision of the report.PREPARED BY THE SAE COOLANT HOSE COMMITTEERationale—The format and verbiage have been modified to better incorporate the revisions that have been made over the past several years, such as, the LT special designator, the references to the SAE J20-1 and J20-2 publications, and the PVT paragraph.Relationship of SAE Standard to ISO Standard—Not applicable.Application—This SAE Standard covers reinforced and flexible hoses intended for use in water and ethylene glycol-based engine-coolant system applications.Reference SectionSAE J20-1—Coolant Hose (Supplement to SAE J20 for Government Use Replacing Part of MS51230) SAE J20-2—Coolant Hose—Normal Service Type Convoluted, Wire Support Hose(Supplement to SAE J20 for Government Use Replacing Part of MS51008)SAE J1231—Formed Tube Ends for Hose Connections and Hose FittingsSAE J1508—Hose Clamp SpecificationSAEJ1610—Test Method for Evaluating the Sealing Capability of Hose Connections with a PVT Test FacilitySAE J1616—Recommended Practice for Compressed Natural Gas Vehicle FuelSAE J1638—Compression Set of Hoses or Solid DiscsSAEJ1684—Test Method for Evaluating the Electrochemical Resistance of Coolant System Hoses and MaterialsSAE J2370—Geometric Dimensions and Tolerancing for Curved HoseSAE J2387—Dimensions and Tolerances for Coolant System HosesASTM D 380—Methods of Testing Rubber HoseASTM D 395—Test Methods for Rubber Property Compression SetASTM D 412—Test Method for Rubber Properties in TensionASTM D 413—Test Methods for Rubber Property Adhesion to Flexible SubstrateASTM D 471—Test Method for Rubber Property Effect of LiquidsASTM D 573—Test Method for Rubber Deterioration in an Air OvenASTMD1149—Test Method for Rubber Deterioration Surface Ozone Cracking in a Chamber (FlatSpecimens)ASTM D 2240—Test Method for Rubber Property Durometer HardnessDeveloped by the SAE Coolant Hose Committee。
SAE J1128 2000 (中文版) 低压初级电缆

1128中文电线TXL

SAE 1128 低压原电线出版:1975-1修订:2000-051 范围—本标准应用于在表面车辆电力系统中的标称系统电压为60 V DC(25 V AC)或更低的低压原电线。
测试通过对电线有限制的耐流体和机械损伤来评价电线的质量。
2 参考文献2.1 适用的刊物—以下刊物构成了本标准的一部分,除非有特殊要求,应使用SAE出版的最新版本。
2.1.1 SAE刊物—可以从SAE,400Commonwealth,Warrendale, Pa 15096—0001购买。
SAE EA-1128—电线色标卡SAE J311—客车用自动档液。
材料和测试方法的SAE 字典2.1.2ASTM文献——来源于ASTM文献的有效文献。
100Barr Harbor Drive, WestConshohocken, PA 19428—2959ASTM B 1—硬拉铜线规范ASTM B 33—镀锡软/退火铜线ASTM B 174—电气导体用绞合铜导体规范ASTM B 263—绞合导体截面积的确定方法ASTM B 298—镀银软/退火铜线规范ASTM B 354—无绝缘金属导体相关术语的定义ASTM B 355—镀镍软/退火铜线规范ASTM D 412—硫化橡胶、热塑性橡胶以及热塑性弹性体的张力测试方法规范ASTM D 471—橡胶性能——流体影响标准测试方法ASTM D 573—橡胶在空气老化箱中性能恶化的测试方法ASTM E 145—重力对流和强制通风老化箱标准ASTM F 1251—在内科和外科设备的高聚物生物相干标准术语2.1.3 IEC文件—可从ANSI,11 West 42nd Street, New York , NY 10036-8002购买。
IEC 811-2-1—电缆绝缘和护套材料的通用测试方法第一部分弹性体化合物的特殊方法第一节耐臭氧测试热延伸测试矿油浸渍测试IEC,电学,电子和电信,多媒体字典。
2.2 相关刊物—以下刊物目的仅是提供信息和不要求成为本标准的一部分。
SAE J标准目录中文
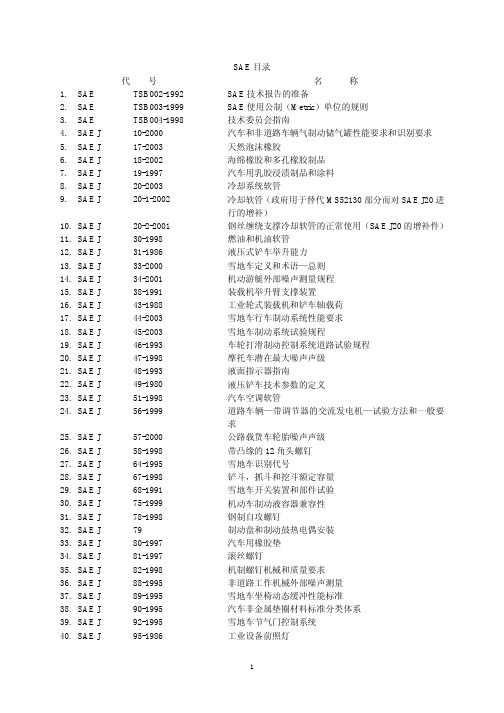
代号 180-2002 182-1997 183-2002 184-1998 185-2003 187 188-2003 189-1998 190-1998 191-2003 192-2003 193-1996 195-1988 198-2003 200-2001 201-1997 207-1985
名
称
机械制动灯开关
合成树脂塑料密封胶—不干型
前照灯开关
废气排放测量用仪器和测量技术
商用车制动器额定功率要求
点火开关
视野术语
柴油机燃油喷嘴总成—8,9,10 和 11 型
乘用车和轻型载货车稳态方向控制试验规程
车轮/轮辋—载货车—性能要求和试验规程
摩托车后视镜
车辆识别号码体系
乘用车识别号码体系
悬架弹簧额定承载能力
技术委员会指南
汽车和非道路车辆气制动储气罐性能要求和识别要求
天然泡沫橡胶
海绵橡胶和多孔橡胶制品
汽车用乳胶浸渍制品和涂料
冷却系统软管
冷却软管(政府用于替代 MS52130 部分而对 SAE J20 进
行的增补)
钢丝缠绕支撑冷却软管的正常使用(SAE J20 的增补件)
燃油和机油软管
液压式铲车举升能力
雪地车定义和术警报灯
通用工业机械人员防护
公路上使用的工业设备灯光和标志
A 类车辆风窗玻璃阴影区域
汽车鼓式制动器液力分泵
摩托车操纵件和显示器
摩托车制动系统试验代码
摩托车和动力驱动自行车行车制动系统性能要求
电动风窗玻璃刮水器开关
冷拔机械弹簧钢丝和弹簧
座椅安全带织带磨损性能要求
安全标志
纤维板褶皱弯曲试验
淬硬和回火螺纹紧固件的脱碳
GPT型汽车电线
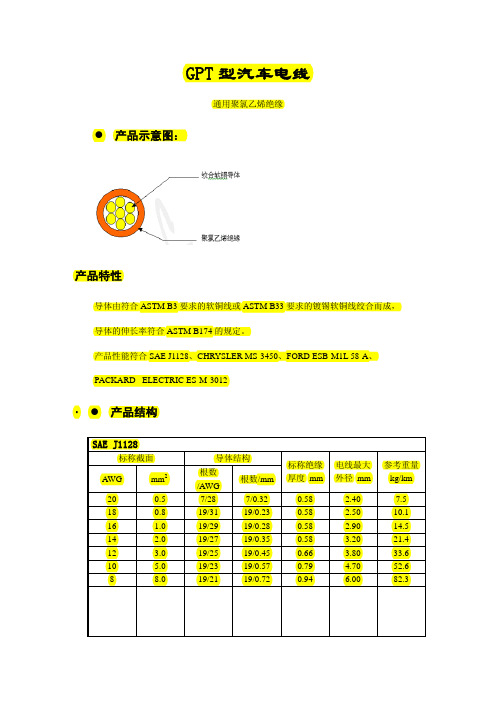
2.0
19/27
19/0.35
12
3.0
19/25
19/0.45
10
5.0
19/23
19/0.57
PACKARD ELECTRIC ES-M-3012
标称截面
导体结构
AWG
mm2
根数
根数/mm
/AWG
20
0.5
7/28
7/0.32
18
0.8
19/31
19/0.23
16
1.0
19/29
19/0.28
14
电线最大 外径 mm
2.05 2.28 2.50 2.92 3.52 4.36 5.32
参考重量 kg/km
6.9 8.7 12.0 11.4 16.0 23.6 36.5 57.2 90.0 168.6
参考重量 kg/km
4.5 8.9 12.0 12.0 16.5 23.7 36.5 57.5
参考重量 kg/km
19/0.72
6
13.0
37/21
37/0.72
FORD ESB-M1L 58-A
标称截面
导体结构
AWG
mm2
根数
根数/mm
/AWG
22
0.35
7/30
7/0.26
20
0.5
7/28
7/0.32
18
0.8
16/30
16/0.26
18
0.8
19/31
19/0.23
16
1.0
19/29
19/0.28
14
根数
根数/mm
/AWG
22
SAE1128 中文版

美国汽车工程师协会标准低压初级电缆SAE-J 1128/19951. 范围本SAE标准适用于额定电压50V mms或以下地面车辆电气系统用低压初级电缆。
本文的实验旨在检验正常使用条件下(很少受流体和物理应力作用)的电缆的合格性。
2. 参考文献2.1适用文件下列出版物因被本标准引用而构成本标准的一部分,其中SAE标准应使用最新版本。
2.1.1 SAE出版物EA 1128 颜色偏差参考色谱2.1.2 ASTM 出版物ASTM B1硬拉铜线规范ASTM B3 软或退火铜线规范ASTM B33 镀锡软或退火铜线规范ASTM B49 电工用二次拉伸铜杆规范ASTM B174 束绞铜导体规范ASTM B189 镀铝或铅合金软或退火铜线规范ASTM B193 导体材料电阻率标准实验方法ASTM B263 标准导体截面测试方法ASTM D412 硫化橡胶和热缩性橡胶和热缩性弹性体标准试验方法-张力法ASTM D471 橡胶性能标准试验方法-液体作用ASTM D573 橡胶性能标准试验方法-烘箱老化ASTM E145 重力对流和强迫通风烘箱规范2.1.3 军用出版物Mil-T-5438 实验机:电缆耐磨试验(老式)2.2相关标准下列标准仅供参考,它们不是本标准不可缺少的一部分。
2.2.1SAE出版物SAE J 156 可熔断线路SAE J 1127 低压电池电缆SAE J 1292 汽车、货车、牵引车、拖车和机动车辆的布线SAE J 1654 高压初级电缆SAE J 1673 高压汽车布线2.2.2 ISO出版物ISO6722 道路车辆-无屏蔽低压电缆3. 电缆型号(见表1)TWP型-薄壁热塑性绝缘电缆GPT型-通用热塑性绝缘电缆HDT型-重型热塑性绝缘电缆STS型-标准负荷热固性弹性体(合成橡胶)绝缘电缆HTS型-重型热固性弹性体(合成橡胶)绝缘电缆TXL型-薄壁交联聚希烃绝缘电缆GXL型-通用交联聚希烃绝缘电缆SXL型-特种用途交联聚希烃绝缘电缆TWE型-薄壁热塑性弹性体绝缘电缆GTE型-通用热塑性弹性体绝缘电缆HTE型-重型热塑性弹性体绝缘电缆表1SAE初级电缆型号定义参见第3节4. 通用范围对于每种电缆型号,成品电缆应满足表2规定的所有实验的要求。
电动车线束检验标准

金华莱德电动技术有限公司电动车线束检验标准线束是电动车电路的网络主体,没有线束也就不存在电动车电路。
在目前,不管是什么类型的电动车,线束编成的形式基本上是一样的,都是由电线、联插件和包裹胶带组成。
电动车电线都是铜质多蕊软线,几条乃至几十条软铜线包裹在塑料绝缘管(聚氯乙烯)内,柔软而不容易折断。
1:范围:本标准规定了本公司外购电动车线束的性能指标、技术要求、检验项目,作为本公司对外购电动车线束的检验标准。
2:引用标准:SAE J1127 车辆用低压电瓶线标准SAE J1128 车辆用低压主回路电缆标准UL 1581 电线电缆和软线基础标准3:检验方法及要求线束内的电线常用规格有标称截面积0.5、0.75、1.0、1.5、2.0、2.5、4.0、6.0等平方毫米的电线,它们各自都有允许负载电流值,配用于不同功率用电设备的导线。
以整车线束为例,0.5规格线适用于仪表灯、指示灯、门灯、顶灯等;0.75规格线适用于牌照灯,前后小灯、制动灯等;1.0规格线适用于转向灯、雾灯等;1.5规格线适用于前大灯、喇叭等;主电源线例如发电机电枢线、搭铁线等要求2.5至4平方毫米电线。
这只是指一般汽车而言,关键要看负载的最大电流值,例如蓄电池的搭铁线、正极电源线则是专门的汽车电线单独使用,它们的线径都比较大,起码有十几平方毫米以上,这些"巨无霸"电线就不会编入主线束内。
线束上各端头都会打上标志数字和字母,以标明导线的连接对象,操作者看到标志能正确连接到对应的电线和电气装置上,这在修理或更换线束时特别有用。
同时,电线的颜色分为单色线和双色线,颜色的用途也有规定,一般是车厂自订的标准。
我国行业标准只是规定主色,例如规定单黑色专用于搭铁线,红单色用于电源线,不可混淆。
线束用机织线或塑料粘带包裹,出于安全、加工和维修方便,机织线包裹已经淘汰,现在是用粘性塑料胶带包裹。
线束与线束之间、线束与电气件之间的连接,采用联插件或线耳。
SAE J1128 J1127美国汽车协会标准

编号 型 号 3101 GPT 3102 TWP 3103 HDT 3104 UTP 3105 GXL 3106 TXL 3107 SXL 3108 UXL 3109 TWE 3110 GTE 3111 HTE 3112 SGT 3113 STT 3114 SGX 名 称 特 性 通用PVC绝缘电线 薄壁PVC绝缘电线 加厚型PVC绝缘电线 超薄PVC绝缘电线 通用交联聚烯烃绝缘电线 薄壁交联聚烯烃绝缘电线 特种用途交联聚烯烃绝缘电线 超薄交联聚烯烃绝缘电线 薄壁热塑性弹性体绝缘电线 通用热塑性弹性体绝缘电线 重型热塑性弹性体绝缘电线 通用PVC绝缘蓄电池线 薄壁PVC绝缘蓄电池线 通用交联聚烯烃绝缘蓄电池线 通用型 外径和重量均小于GPT 绝缘厚度大于GPT,具有优良的机械性能 绝缘厚度比TWP更薄 优良的耐热和机械性能 外径和重量均小于GXL 性能优于GXL 绝缘厚度比TXl更薄 外径和重量均小于GTE 优良的耐热性和机械性能 绝缘厚度大于GTE,具有优良的机械性能 普通型 外径和重量均小于SGT 优良的耐热性和机械性能 工作温度°C 工作温度 C 80 80 80 85 125 125 125 125 100 100 100 80 80 125
常见电缆型号字母数字含义
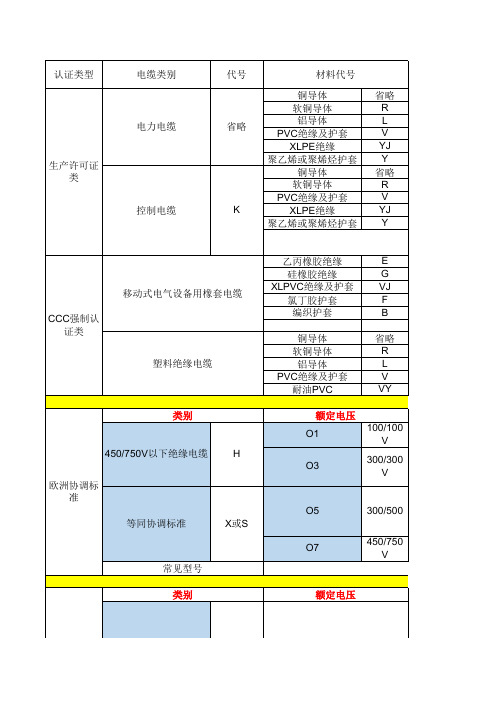
常见型号 AV AVSS AVS AVX AEX AESSX AESSX CAVS CAVUS
常见型号
V ZB-RVV ZC-RVV WDZ-BY WDZWDZB-YJY WDZAN-YJY WDZC-YJY
NH-YJV ZR-YJV
S
硅橡胶
J
T S H05V-K H07V-R H05VV-F H05RN-F H05VVH6-F H05SJ-K H05BQ-F H05VVC4V5-K
绝缘材料
Y
PVC
2X
交联聚乙烯
2Y
聚乙烯
护套材料 Y 2X 2Y
H
低烟无卤
H
NYY NYCY NYCWY NAYY NAYCY N2XH N2XY N2XCY
KVV KVV22 KVVR KVVRP KVV3 KVVP2 KVVP2-22
YG YQ YZ YZW Y
BV RV BVR BLV BVV BVVB RV RVVPS TVV TVVB
绝缘材料
V
70℃PVC
V2
90℃PVC
V3
耐寒PVC
B
乙丙橡胶
E
PE聚乙烯
X
交联聚乙烯
R
橡胶
护套材料 V V2 V3 V5 R N Q
绝缘材料
护套材料
Y
PVC
Y
2Y
聚乙烯
2Y
5Y
PTFE
5Y
6Y
FEP
6Y
7Y
ETFE
7Y
H
低烟无卤
9Y
H
LiYY LiHH LiHCH LiYCY LiYCY(TP) LiYCY(TP) LiYD11Y Li2YCY(TP) Li2
汽车导线类型及应用
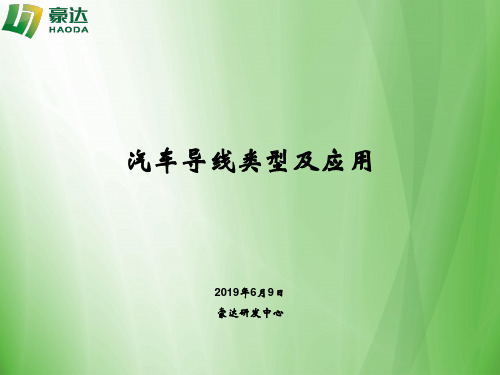
QVR、QFR、QVR-105、QVVR、QB
FLY、FLRY、FLYW、FLRYW、 FLR9Y、FLR2X、FLR13Y、FLR91X 等
PSA 9609503299
标致/雪铁龙集标准
标准单芯导线
T1—T8
FIAT 91107
JASO D 611
JASO D 608
JIS C 3406
KSC 3311 ES 91110 SAE J 1128 SAE J 1560 SAE J 1127
线径
标准
ISO SAE JIS
60
62/AWG/2/0
70
75
81/AWG3/0 85 95
100
103/AWG4/0
120
JASO
AVX AEX
AVS CAVS AVSS CAVUS
DIN AB
JB/T KS
汽车导线类型及应用
产品对比
产品名称:单芯无屏蔽薄壁PVC绝缘低压电线(FLRY) 产品标准:德国工业标准DIN72551 产品结构:
汽车导线类型及应用
各标准线径一览
线径
标准
ISO SAE JIS
0.13/AWG26 0.2
0.22/AWG24 0.3
0.35/AWG22
0.4
0.5/AWG20
0.6
0.75
0.8/AWG18
0.85
JASO
AVX AEX
AVS CAVS AVSS CAVUS
DIN AB
JB/T KS
导体结构 根数/直径-C
型
/ 19/0.16 26/0.16 38/0.16 54/0.16 76/0.16 105/0.16
saej1459v003_多楔带和带轮
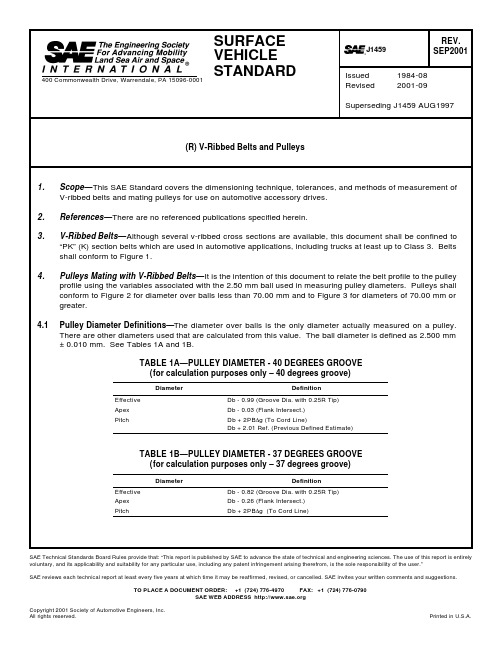
SAE Technical Standards Board Rules provide that: “This report is published by SAE to advance the state of technical and engineering sciences. The use of this report is entirely voluntary, and its applicability and suitability for any particular use, including any patent infringement arising therefrom, is the sole responsibility of the user.”SAE reviews each technical report at least every five years at which time it may be reaffirmed, revised, or cancelled. SAE invites your written comments and suggestions.TO PLACE A DOCUMENT ORDER: +1 (724) 776-4970 FAX: +1 (724) 776-0790SAE WEB ADDRESS Copyright 2001 Society of Automotive Engineers, Inc.FIGURE 1—BELT DIMENSIONING TEMPLATEFIGURE 2—PULLEY DIMENSIONING TEMPLATE (6) GROOVE SHOWN (TYPICAL)FIGURE 3—PULLEY DIMENSIONING TEMPLATE (6) GROOVE SHOWN (TYPICAL)5.Measurement Method—Since the templates in Figures 1 to 3 have profile of a line callouts, it is necessary tocapture the entire profile digitally and compare it to the drawing dimensions. This requires a digital profilometer and eliminates the optical comparator as acceptable for metrology. Because of the inherent speed of these devices, the frequency of audit may have to be reduced, depending on the process used in production. If verification of ongoing quality requires more frequent measurement, the audit with the profilometer is still required, while the supplier can use traditional methods to measure additional belts to satisfy an internal process control characteristic, if they feel the need.6.Belt Dimension Determination—The shape of the belt profile changes with bending, either as profiled backbent, if it is not molded, or between manufacture and measurement. The intent of the document is to achievea precise mating of the belt as bent around a grooved pulley. The 37 degree pulley standard deals with thedistortion of the belt around small diameter pulleys. For larger pulleys, the 40 degree belt rib angle is to be defined on a 127 mm pulley as measured in an arch with a dental compound casting, or equivalent. The detail drawing is to show the rib dimensions as measured in production with the digital profilometer (usually flat).These dimensions may be different from those measured in the arch. Once the relationship between the arch and the production measurements due to the rubber distortion is established, the arch dimensions shall not be measured on an ongoing basis, but rather the detail drawing dimensions representing the flat profilometer method.7.Metrological Issues—In order to facilitate the execution of the programs for digital profilometers to measureboth belts and pulleys, it is permissible to calculate the points defined on the flanks of the belt ribs or pulley grooves. This can be done from the line defined by points along the rib/groove flank line between the tangent points of the tip and root radii. Gage R&R improves with increasing distance between the points selected.Precise methodology can be mutually agreed upon between supplier and OEM.8.V-Ribbed Belt Size—Belt size is designated by a standard series of alphanumeric characters. Beltsmeasured on a metric length system are designated by the number of ribs followed by the belt cross-sectional size (“PK” or “PL”) and the effective length in millimeters. For example, 6PK1370 signifies a 6-rib “PK” section belt, with an effective length of 1370 mm.9.Measurement of V-Ribbed Belts—The length of a V-ribbed belt is determined by use of a measuring fixturecomprised of two pulleys of equal diameter, a method of applying force, and a means of measuring the center distance between the two pulleys. One of the two pulleys is fixed in position while the other is movable along a graduated scale. Both pulleys are allowed to rotate. The fixture is shown schematically in Figure 4. Grooves of master inspection pulleys shall be machined to dimension tolerances shown in Table 2, treated to resist wear, and checked periodically for wear and damage.FIGURE 4—DIAGRAM OF A FIXTURE FOR MEASURING V-RIBBED BELTS9.1Length—To measure the length, the belt is placed on the measuring fixture at the total measuring force shownin Table 2, and rotated around the pulleys at least two revolutions to seat the belt properly in the pulley grooves and to divide the total force equally between the two strands of the belt. The midpoint of the center distance travel of the movable pulley defines the center distance and will be measured through a minimum of one revolution of the belt after the two seating revolutions. The belt effective length is equal to two times the center distance plus the pulley effective circumference. Standard belt center distance tolerances are shown in Table3. For center distance tolerances less than standard, the belt manufacturer should be consulted.10.Other Dimensional Notes—Standard lengths up to and including 2000 mm are to be in 10 mm increments.Standard lengths over 2000 mm up to and including 4000 mm are to be in 25 mm increments.NOTE 1—The sides of the groove are to be 3.2 µm A.A. maximum.NOTE 2—Radial and axial run-out is not to exceed 0.25 mm full indicator movement (FIM). Run-out in the twodirections is measured separately with a ball mounted under spring pressure to follow the groove asthe pulley is rotated.NOTE 3—The diameters over the ball gauges are not to vary from groove to groove more than 0.25 mm forany one belt groove set in a pulley.NOTE 4—Centerline of groove is to be 90.0 degrees ± 0.5 degrees with pulley axis.11.Notes11.1Marginal Indicia—The change bar (I) located in the left margin is for the convenience of the user in locatingareas where technical revisions have been made to the previous issue of the report. An (R) symbol to the left of the document titles indicates a complete revision of the report.PREPARED BY THE SAE BELT DRIVE SYSTEMS COMMITTEETABLE 2—MEASURING CONDITIONS—MILLIMETERSCrossSectionSizeEffective Diameter (reference)Effective Circumference (reference)d B Ball or Rod Diameter ±0.010Diameter Over Ball or Rods ±0.10Total Measuring Force Per Rib (N)PK 95.49300 2.500 96.48100TABLE 3—STANDARD BELT CENTER DISTANCETOLERANCES (1)—MILLIMETERS1.These tolerances are for reference only, and depend on manu-facturing process as well as cost. Supplier and OEM agree-ment must be reached on each application.Belt LengthTolerance on Center Distance 0 – 1200± –4.0Over 1200 – 2000± –5.0Over 2000 – 2500± –6.0Over 2500 – 3000± –7.0Rationale—This document has been revised to update pulley dimensioning to GD&T and to create a compatible belt template.Relationship of SAE Standard to ISO Standard—Not applicable.Application—This SAE Standard covers dimensioning technique, tolerances, and methods of measurement of V-ribbed belts and mating pulleys for use on automotive accessory drives.Reference Section—There are no referenced publications specified herein.Developed by the SAE Belt Drive Systems Committee。
汽车线束设计及搭铁分析
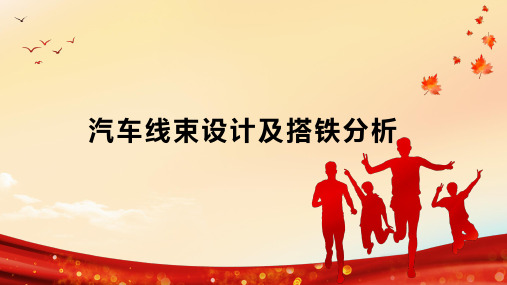
1.2汽车线束设计的作用
1.2汽车线束设计的作用
汽车线束设计的主要作用是确保汽车电路系统的正常运转和可靠性。通过合 理的线束布局和连接方式,线束能够有效地传输所需的电力和信号,同时防止电 磁干扰和过电流等潜在问题。此外,汽车线束设计还应当考虑到汽车的维护和维 修方便性,以便于故障排查和更换部件。
1、汽车线束的作用和意义
1、汽车线束的作用和意义
汽车线束是汽车电路的基础,主要作用是传输电能和信号。在汽车行驶过程 中,各种电器设备需要不断进行信息交流和电能传输,而这些都离不开汽车线束 的帮助。汽车线束的设计与布局直接影响到汽车的性能和安全性,因此,优化汽 车线束设计对于提高汽车整体性能具有重要意义。
2、汽车线束设计的原则和方法
2.3布局线束 根据汽车内部的布局情况,设计出合理的线束走向和固定方式,以节省空间 和提高可靠性。
2、汽车线束设计的原则和方法
2.4选择连接器与附件根据需要选择适当的连接器和附件,如熔断器、端子和 继电器等,以确保电路系统的安全性和可靠性。
2、汽车线束设计的原则和方法
3、汽车线束设计的相关标准和 规范
3、汽车线束设计的相关标准和规范
汽车线束设计需要遵循一系列相关标准和规范,以确保其质量和安全性。以 下是一些主要的汽车线束设计标准和规范:
3、汽车线束设计的相关标准和规范
(1)ISO标准:ISO 6722《道路车辆电气及电子设备用连接器分配器和接线 盒通用条件》等。
3、汽车线束设计的相关标准和规范
(2)SAE标准:SAE J1128《电动汽车高压电缆和组件的测试方法》等。 (3)国标标准:GB/T 《道路车辆电力电缆一般要求》等。
二、可靠性研究
二、可靠性研究
汽车线束的可靠性是指其在规定的条件下和时间内完成规定功能的能力。汽 车线束的可靠性直接影响到汽车的安全性和性能。下面将从可靠性概念和意义、 影响可靠性的因素以及提高可靠性的方法和措施三个方面进行介绍。
低压线束导线在汽车中的选择和应用研究

生产制造MANUFACTURING(4)绝缘性能:低压线束导线的绝缘材料至关重要,以防止电流泄漏和短路。
绝缘材料应具有良好的绝缘性能,能够有效地隔离导线和其他电子元件,防止电流流失或发生故障。
(5)安全性和符合标准:低压线束导线应符合汽车行业的安全标准,以确保车辆电路的可靠性和乘车人员的安全。
导线应具有耐火性能,能够防止火灾蔓延和扩散。
(6)成本和可持续性:在选择低压线束导线时,成本也是一个重要的考虑因素。
不同的导线材料和制造工艺会导致不同的成本水平,应在合理范围内选择成本效益最高的导线。
不同国家,低压汽车导线参照标准[7]也是不同的,主要可分为4个系列(表2)。
不同国家的汽车用线种类,如表3~表5所示。
选择适当的低压线束导线需要综合考虑导电性能、耐热性、耐油性、柔韧性、绝缘性能、安全性和成本等因素。
根据具体的应用需求和要求,选择合适的导线材料和制造工艺,以确保汽车电路的稳定性和可靠性。
2.3 低压线束导线的类型在汽车电路中,选择适当的低压线束导线材料至关重要,不同的材料具有不同的特性和适用范围。
以下将详细讨论常见的低压线束导线材料,包括铜导线、铝导线、铜包铝导线、铜包钢导线和铜合金导线。
(1)铜导线是最常用的一种低压线束导线材料,具有优良的导电性能和良好的耐腐蚀性能。
其导电性能高,能够提供稳定的电流传输。
此外,铜导线还具有良好的柔韧性和耐拉性,容易弯曲和安装。
然而,铜导线相对比较贵,且重量较重,不如一些其他材料节省空间。
(2)铝导线是一种相对较轻的材料,可有效减轻车辆的总重量。
它具有较好的导电性能,并且价格相对较低。
然而,相比铜导线,铝导线的导电性能略差,电阻较大,会产生能量损失。
此外,铝导线更加脆硬,不如铜导线柔韧。
(3)铜包铝导线是一种将铝芯线包覆在铜层中的导线。
它结合了铜和铝的优点,具有较低的重量和较好的导电性。
由于铜包铝导线较轻,可以更好地减轻整个车辆的负荷,同时保持良好的导电性能。
然而,铜包铝导线在一些高温环境下可能会存在导电和稳定性方面的问题。
- 1、下载文档前请自行甄别文档内容的完整性,平台不提供额外的编辑、内容补充、找答案等附加服务。
- 2、"仅部分预览"的文档,不可在线预览部分如存在完整性等问题,可反馈申请退款(可完整预览的文档不适用该条件!)。
- 3、如文档侵犯您的权益,请联系客服反馈,我们会尽快为您处理(人工客服工作时间:9:00-18:30)。
VEHICLESAE Technical Standards Board Rules provide that: “This report is published by SAE to advance the state of technical and engineering sciences. The use of this report is entirely voluntary, and its applicability and suitability for any particular use, including any patent infringement arising therefrom, is the sole responsibility of the user.”SAE reviews each technical report at least every five years at which time it may be reaffirmed, revised, or cancelled. SAE invites your written comments and suggestions. Copyright © 2005 SAE InternationalAll rights reserved. No part of this publication may be reproduced, stored in a retrieval system or transmitted, in any form or by any means, electronic, mechanical, photocopying, recording, or otherwise, without the prior written permission of SAE.3.3Cable FamilyA group with multiple conductor sizes having the same conductor strand coating, insulation formulation, and wall thickness type.3.4Coated WireWire comprised of a given metal covered with a relatively thin application of a different metal. (ASTMB 354)3.5ConductorA wire or combination of wires not insulated from one another, suitable for carrying an electrical current. (ASTMB 354)3.6Conductor SizeSee “SAE Conductor Size”.3.7CoreOne of the components in an assembly. A component may be an uninsulated conductor, an insulated conductor, a twisted pair, a shielded assembly, a coaxial cable, or any finshed cable.3.8Fluid CompatibilityThe ability of a cable to resist the effects of various fluids found in surface vehicles.3.9Hot PlateAn electrically heated device used to test thermoset cables.3.10Low Voltage (Low Tension)Usually considered to be ≤ 60 V DC (25 V AC).3.11Minimum Wall (Thickness)The lowest allowable insulation thickness at any point.3.12NominalA suitable approximate value used to designate or identify a component.3.13PlasticsAny of numerous polymeric materials that are usually thermoplastic or thermosetting, of high molecular weight and that can be molded, cast, extruded, drawn, laminated, or otherwise fabricated into objects, powders, beads, films, filaments, fibers, or other shapes. (ASTM F 1251)3.14Primary CableThe single or multi-stranded, single conductor, insulated cable used to carry electric current, by attachment to the low voltage side of an ignition coil in surface vehicles.3.15Resistance to OzoneThe ability of a material to withstand the deteriorating effect of ozone (surface cracking). (Dictionary of Materials and Testing)3.16SAE Conductor SizeA system that indicates the cross sectional area of the conductor. The Metric SAE Conductor Size is the approximate area of the conductor.3.17SeparatorA thin layer used as a barrier to prevent mutually detrimental effects between different components of a cable such as between the conductor and insulation or between the insulation and the sheath. (IE C, Electricity, Electronics and Telecommunications, Multilingual Dictionary)3.18Strip ForceThe peak axial force required to overcome the adhesion between the conductor and the insulation.3.19StrandSee wire.3.20TCR, Temperature Class RatingA class designation based on the retention of “Mechanical Properties” (tensile & elongation) after 168 h of heat aging at 30 °C above the temperature class rating.3.21ThermoplasticA plastic capable of being softened by heating and hardened by cooling through a temperature range characteristic of the plastic and, in the softened state, capable of being repeatedly shaped by flow into articles by molding, extrusion or forming. (IE C, E lectricity, E lectronics and Telecommunications, Multilingual Dictionary).6.11CrosslinkingThe usage of this test will be established by agreement between customer and supplier. 25 mm of insulation shall be removed from each end of a 600 mm sample of finished cable. The test sample shall be bent a minimum of 135 deg around a 6 mm mandrel. The cable and mandrel shall be placed againsta hot plate at least 150 mm by 150 mm which has been preheated to 250 °C ± 25 °C. A force of 5 N to7 N shall be applied for 5 s to 6 s without rubbing or scraping the cable on the plate. After exposure, the cable conductor shall not be visible through the insulation. If the visual inspection is not conclusive, the sample is to be returned to room temperature and then subjected to a dielectric test similar to that specified in 6.4. However, the immersion time and application of the voltage shall be 1 min. The requirements for the “Crosslinking” test, if any, will be established by agreement between the supplier and the customer.6.12Strip ForceThe usage of this test will be established by agreement between customer and supplier. Prepare a 75 mm test sample of finished cable. 25 mm of insulation shall be cleanly cut and carefully stripped from one end of the conductor. Care must be taken not to disturb the 50 mm ± 2 mm section when removing the residual insulation. No burrs are permitted on the ends of the metallic conductor. Insert the stripped end through a plate with an appropriate diameter hole. The conductor shall be pulled through the plate at a rate of 500 mm/min. The maximum force shall be recorded. A minimum of four readings shall be obtained. The mean of all readings shall determine the strip force of the cable under test. The requirements for the “Strip Force” test, if any, will be established by agreement between the supplier and the customer.Alternative - A 25 mm ± 2 mm sample of undisturbed insulation may be used.6.13Resistance to Hot WaterThis test is for initial qualification only. The usage of this test will be established by agreement between customer and supplier. Compliance for a cable family may be demonstrated by using “Representative Conductor Sizes for Testing”, see 4.5. 25 mm of insulation shall be removed from each end of two 2.5 m ± 0.1 m test samples of finished cable. Other test sample lengths may be used; however, in case of a dispute, the referee method shall use the 2.5 m test sample length. Closely wind a minimum of three complete turns of the first test sample around the mandrel specified in Figure 5 and secure the coil as shown in Figure 14. After removing the mandrel, immerse the first test sample in a saltwater bath with 10 g/l of NaCl in distilled water at 85 °C ± 5 °C. To avoid interaction between compounds, test samples with different insulating compounds shall not be tested in the same bath. Also, a virgin saltwater bath shall be used for each test. Connect one end of the first test sample to the positive terminal of a 48 V DC power source. Connect the negative terminal to the copper electrode in the bath. After 7 days, disconnect the 48 V DC power source, measure the insulation resistance, and calculate the “Insulation Volume Resistivity” (see 6.14). This completes one cycle. Repeat this procedure for a total of five cycles, 35 days. After conditioning, remove the test sample from the bath, allow it to cool to room temperature, and make a visual inspection of the insulation. Ignore any damage caused by the tie, which secures the coils. If no exposed conductor is visible, perform the “Dielectric” test (see 6.4) except the voltage will be applied after immersion in the salt solution for a minimum of 10 min.Perform the entire procedure for the second test sample with the polarity of the 48 V DC power source reversed.Where:ρ0 is the “Insulation Volume Resistivity”, expressed in Ω•mmL is the immersed length of the test sample, expressed in mmR is the measured insulation resistance, expressed in ΩD is the outside cable diameter, in accordance with 5.3, expressed in mmd is the conductor diameter, expressed in mmlog is log to the base 10The “Insulation Volume Resistivity” shall not be less than 109 Ω•mm.6.15 Temperature and Humidity CyclingThis test is for initial qualification only. The usage of this test will be established by agreement between customer and supplier. Compliance for a cable family may be demonstrated by using “Representative Conductor Sizes for Testing”, see 4.5. 25 mm of insulation shall be removed from each end of two 600 mm samples of finished cable. Wind the test sample around the mandrel according to 5.5 and secure the ends. Condition the sample according to the temperature and relative humidity shown in Figure 15. The “Temperature Class Rating” is shown in Figure 6. Extended transition times may be used as long as the dwell times at temperature are maintained. The cycle begins with the sample at -40 °C ± 2 °C and uncontrolled relative humidity. Completion of the schedule shown in Figure 15 will constitute one cycle. Repeat the cycle for a total of 40 cycles. While still on the mandrel, remove the test sample from the chamber, allow it to stabilize at room temperature for 30 min, and unwind it from the mandrel. Make a visual inspection of the insulation. Ignore any damage caused by the ties, which secure the ends. If no exposed conductor is visible, perform the “Dielectric” test (see 6.4) except the voltage will be applied after immersion in the salt solution for a minimum of 10 min.8.Notes8.1Marginal IndiciaThe change bar (l) located in the left margin is for the convenience of the user in locating areas where technical revisions have been made to the previous issue of the report. An (R) symbol to the left of the document title indicates a complete revision of the report.PREPARED BY THE SAE CABLE TASK FORCE OF THESAE ELECTRICAL DISTRIBUTION SYSTEMS STANDARDS COMMITTEER. E. Carroll, Inc.Citgo PetroleumKester SolderGlowe Industrial Sales, Inc. Single Roll。