2半轴齿轮精锻新型模具
汽车半轴的热挤压成形工艺

塑性加工技术
ZZZ
文章编号: "RU&T$"&" ( &$$# ) $,T$$#,T$&
!"#$%&’ ()*+&,- %.’/,)")-0
汽车半轴的热挤压成形工艺
李和平 ", 金曼曼
&
( 江西 吉安 #’#$$$ ; 江西 吉安 #’#$$$ ) "( 井冈山职业技术学院, &( 江西曲轴连杆有限公司,
摘要: 介绍了汽车半轴的热挤压成形新工艺及模具设计要点。 关键词: 机械制造; 热挤压; 成形工艺; 汽车半轴 中图分类号: DV#UR(& 文献标识码: W
E
前言 图 " 为东风 @P"’$ 汽车半轴锻件图, 锻件法兰
得了显著的经济效益。
!
工艺分析及工艺流程
!!!!!!!!!!!!!!!!!!!!!!!!!!!!!!!!!!!!!!!!!!!!!
料准确送入轧制位置, 使上下模同时咬入, 以免因上 下模不同步咬入而造成轧件卡死。 为了使送料准确, 在模具前加入一送料模块,该模块按照坯料形状尺 寸设计并可调整, 同时还要求工人进行规范化操作。 通过实际生产验证, 不仅保证了送料位置准确 ! 而且 轧制工艺运作顺利。 防滑措施以打 明显不同, 应采用双 ! 角工艺参数; 麻点代替刻防滑槽( 并加楔入整形段) 。 ( # )加热温度对细小轧件内外质量的影响非常 明显, 因此, 应严格控制加热温度范围。 ( ’ )采用平板式楔横轧机可以解决细小轧件设 置导向板困难的问题。 参考文献
汽车齿轮精密锻造技术

汽车齿轮的精密锻造技术江苏森威精锻有限公司徐祥龙李明明摘要本文介绍了精密锻造成形在汽车齿轮制造中的应用,总结了各种齿形精密锻造的关键技术,特别提到分流锻造在齿形成形方面的应用。
前言齿轮精密锻造成形是一种优质、高效、低消耗的先进制造技术,被广泛地用于汽车齿形零件的大批量生产中。
随着精密锻造工艺和精密模具制造技术的进步,汽车齿轮和齿形类零件的生产已越来越多地采用精密锻造成形。
当前国外一台普通轿车采用的精锻件总质量已达到(40—45)Kg,其中齿形类零件总质量达10Kg以上。
精锻成形的齿轮单件质量可达1Kg以上、齿形精度达到(DIN) 7级。
随着汽车的轻量化要求和人们环保意识的增强,汽车齿轮制造业将更多地应用精锻成形技术。
一.伞齿轮的精锻成形1. 伞齿轮(锥齿轮)的热精锻成形(1)早期的伞齿轮精密锻造伞齿轮的精密锻造最早见于50年代德国的拜尔工厂,并在蒂森等公司得到广泛的应用(1)。
我国上海汽车齿轮厂等在70年代采用热精锻技术,成功进行了伞齿轮的精密锻造生产。
在当时社会主义大协作的环境下,伞齿轮的精锻技术很快在齿轮行业得到推广应用。
该技术的应用和发展得益于2项当时先进的技术:模具的放电加工技术和毛坯感应加热技术。
先淬火后加工的放电加工避免了模具淬火变形带来的齿廓误差;快速加热的中频感应加热解决了齿轮毛坯在加热过程中的氧化和脱碳问题,以上2项技术的应用使锻造成形的伞齿轮齿面达到无切削加工要求(图1、图2)。
图1.精锻成形的行星和半轴齿轮图2.精锻成形的汽车行星齿轮(2)锻造设备伞齿轮的锻造设备在国外一般使用热模锻压力机。
但在60-70年代的中国,热模锻压力机是非常昂贵的设备。
因此,国内企业普遍使用的锻造设备是双盘摩擦压力机(图3)。
该设备结构简单,价格便宜,很快成为齿轮精锻的主力设备。
但摩擦压力机技术陈旧、难以控制打击精度、而且能源利用率较低。
随着高能螺旋压力机和电动螺旋压力机的出现(图4),落后的摩擦压力机有被取代的趋势。
2018年天津市中小企业专精特新产品拟认定奖励公示名单

天津滨海通达动力科技有限公司 新能源风力发电机组及配套组件 天津工大海宇照明部品有限公司 J6P前标志灯路线板 天津海程橡塑制品有限公司 天津柯文实业股份有限公司 天津力生制药股份有限公司 低散发性车身NVH膨胀胶块和加强 衬板 汽车线束精密部品 吲达帕胺片
天津纽威特橡胶制品股份有限公 预制型体育运动卷材 司 天津神菱燃气设备有限公司 家用燃气采暖/热水两用炉
天津灯塔涂料工业发展有限公司 抗腐蚀飞机蒙皮涂层防护涂料 天津顶硕药业股份有限公司 “顶硕牌”薁磺酸钠(SGS)
滨海新区 滨海新区 滨海新区 滨海新区
40 30 50 30 30 40 50 40 30 30 40 30 50
天津飞悦航空工业股份有限公司 航空装配系统 天津光电华典科技有限公司 天津海晶塑料制品有限公司 天津海门建材有限公司 天津海鸥手表技术有限公司 高效智能化污水处理系统OEWS-1 新型七层共挤阻隔膜
45 46 47 48 49 50 51 52 53 54 55 56 57 58 59 60 61 62 63 64 65 66 67 68
天津莱尔德电子材料有限公司
自粘性高导热材料
滨海新区 滨海新区 滨海新区 滨海新区 滨海新区
40 40 40 50 40 50 40 40 40 50 40 30 40 30 30 40 40 30 30 40 30 40
天津市增益达精锻齿轮科技有限 增益达精锻行星半轴齿轮 公司 金大地新能源(天津)集团股份 污水源热泵系统 有限公司 天津乐凯薄膜有限公司 天津双安劳保橡胶有限公司 乐凯牌系列反射膜(RG2型) 带电作业用手形手套(拇指向下)
天津中环真美音响科技有限公司 绿色环保节能汽车扬声器 嘉思特华剑医疗器材(天津)有 生物型人工髋关节假体 限公司 (Harmony)系统 天津海顺印业包装有限公司 高端艺术复制品
差速器半轴齿轮热锻工艺流程

差速器半轴齿轮热锻工艺流程英文回答:Differential gear half axle gear hot forging process.To begin with, let me explain the hot forging process for the half axle gear in a differential gear. Hot forging is a manufacturing process that involves shaping metal by applying heat and pressure. It is commonly used to produce high-strength components with improved mechanical properties.The first step in the hot forging process is the selection of the appropriate material. For the half axle gear, a suitable alloy steel with good heat resistance and high strength is chosen. This ensures that the final product can withstand the demanding conditions of the differential gear system.Once the material is selected, it is heated to aspecific temperature in a furnace. The temperature is carefully controlled to achieve the desired metallurgical properties and to facilitate the deformation of the metal during forging. After reaching the desired temperature, the heated material is transferred to the forging press.In the forging press, the heated material is placed between two dies. The upper die is attached to a ram, which applies a compressive force on the material. The lower die is fixed in position. As the ram moves downwards, it exerts pressure on the material, causing it to deform and take the shape of the die cavities.The hot forging process involves several stages of deformation. The initial stage is known as upsetting, where the material is compressed and its height is reduced. This creates a more compact and denser structure. The next stage is known as drawing out, where the material is elongated and its cross-sectional area is reduced. This helps to refine the grain structure and improve the mechanical properties of the gear.During the hot forging process, the material undergoes plastic deformation, which rearranges the internal structure of the metal. This results in a finer grain structure and improved mechanical properties such as increased strength and toughness. Additionally, the hot forging process eliminates any porosity or voids in the material, ensuring a defect-free final product.After the forging process is completed, the half axle gear is cooled down gradually to room temperature. This is done in a controlled manner to prevent the formation of residual stresses and to improve the dimensional stability of the gear. The cooled gear is then subjected to further machining operations, such as turning and milling, to achieve the final desired shape and dimensions.In conclusion, the hot forging process for the half axle gear in a differential gear involves heating the material to a specific temperature, deforming it under pressure in a forging press, and then cooling it down gradually. This process improves the mechanical properties of the gear and ensures a defect-free final product.中文回答:差速器半轴齿轮热锻工艺流程。
半轴齿轮精锻模具寿命探讨
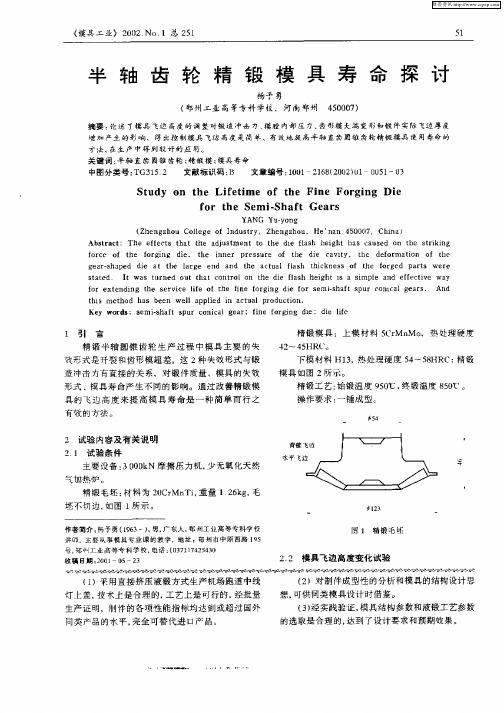
背雅
精锻 毛坯 : 材料 为 2 C Mn , 量 12 k , 0 r Ti重 6 g 毛 坯不 切边 , 图 1所示 。 如
作者简 介 : 杨予 勇 (9 3 , 广东 人, 州工 业高 等专科 学校 16 一) 男. 郑
讲师 . 要从 事模 具专 业课 的教学 .地址 : 州市 中原西 路 1 5 主 邦 9 号. 州工业 高等 专科 学 校 . 郑 电话 :0 7 ) 4 5 3 (3 172 4 0 收 稿 日期 ;0 1 0 2 2 0 5 3
f r e o t f r i g d e t e i e pr s ur o t e d e c v t t e d f r a in f t e o c f he o g n i , h nn r e s e f h i a iy h e o m to o h g a —ha e de t h l r e e d n t e a t a fa h t i k e s o t f r e p r s we e e rs p d i a t e a g n a d h c u l ls h c n s f he o g d a t r sae ttd I wa t n d o t a c nto o t e i fa h he g t s s mp e n e f c i e t s ur e ut h t o r l n h de ls i h i a i l a d fe tv wa y
有效 的方法 。
下模 材料 H1 , 处理 硬度 5 ~5HRC; 3热 4 8 精锻 模 具 如 图 2所 示 。 精锻 工艺 : 锻温度 9 0 终 锻温 度 8 0 始 5 ℃, 5 ℃。
操作 要 求 : 一锤 成 型 。
某差速器齿轮的参数化设计及有限元分析_王良模
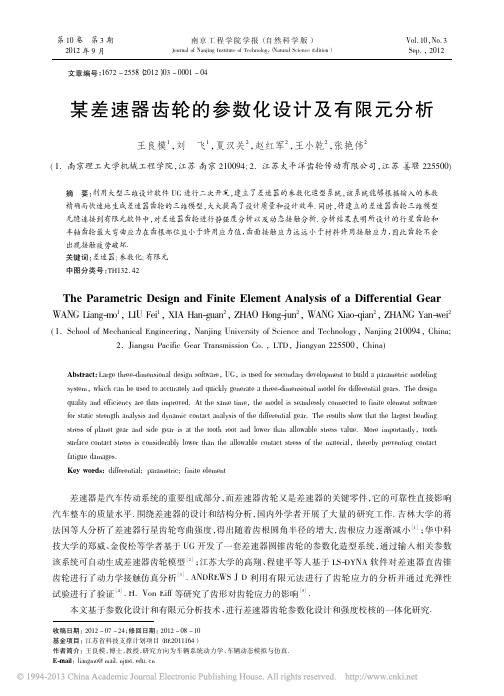
第10卷第3期2012年9月南京工程学院学报(自然科学版)Journal of Nanjing Institute of Technology (Natural Science Edition )Vol.10,No.3Sep.,2012文章编号:1672-2558(2012)03-0001-04某差速器齿轮的参数化设计及有限元分析王良模1,刘飞1,夏汉关2,赵红军2,王小乾2,张艳伟2(1.南京理工大学机械工程学院,江苏南京210094;2.江苏太平洋齿轮传动有限公司,江苏姜堰225500)摘要:利用大型三维设计软件UG 进行二次开发,建立了差速器的参数化造型系统,该系统能够根据输入的参数精确而快速地生成差速器齿轮的三维模型,大大提高了设计质量和设计效率.同时,将建立的差速器齿轮三维模型无缝连接到有限元软件中,对差速器齿轮进行静强度分析以及动态接触分析.分析结果表明所设计的行星齿轮和半轴齿轮最大弯曲应力在齿根部位且小于许用应力值,齿面接触应力远远小于材料许用接触应力,因此齿轮不会出现接触疲劳破坏.关键词:差速器;参数化;有限元中图分类号:TH132.42The Parametric Design and Finite Element Analysis of a Differential Gear WANG Liang-mo 1,LIU Fei 1,XIA Han-guan 2,ZHAO Hong-jun 2,WANG Xiao-qian 2,ZHANG Yan-wei 2(1.School of Mechanical Engineering,Nanjing University of Science and Technology,Nanjing 210094,China;2.Jiangsu Pacific Gear Transmission Co.,LTD,Jiangyan 225500,China)Abstract:Large three-dimensional design software,UG,is used for secondary development to build a parametric modeling system,which can be used to accurately and quickly generate a three-dimensional model for differential gears.The design quality and efficiency are thus improved.At the same time,the model is seamlessly connected to finite element software for static strength analysis and dynamic contact analysis of the differential gear.The results show that the largest bending stress of planet gear and side gear is at the tooth root and lower than allowable stress value.More importantly,tooth surface contact stress is considerably lower than the allowable contact stress of the material,thereby preventing contact fatigue damages.Key words:differential;parametric;finite element收稿日期:2012-07-24;修回日期:2012-08-10基金项目:江苏省科技支撑计划项目(BE2011164)作者简介:王良模,博士,教授,研究方向为车辆系统动力学、车辆动态模拟与仿真.E-mail :liangmo@mail.njust.edu.cn差速器是汽车传动系统的重要组成部分,而差速器齿轮又是差速器的关键零件,它的可靠性直接影响汽车整车的质量水平.围绕差速器的设计和结构分析,国内外学者开展了大量的研究工作.吉林大学的蒋法国等人分析了差速器行星齿轮弯曲强度,得出随着齿根圆角半径的增大,齿根应力逐渐减小[1];华中科技大学的郑威、金俊松等学者基于UG 开发了一套差速器圆锥齿轮的参数化造型系统,通过输入相关参数该系统可自动生成差速器齿轮模型[2];江苏大学的高翔、程建平等人基于LS-DYNA 软件对差速器直齿锥齿轮进行了动力学接触仿真分析[3].ANDREWS J D 利用有限元法进行了齿轮应力的分析并通过光弹性试验进行了验证[4].H.Von Eiff 等研究了齿形对齿轮应力的影响[5].本文基于参数化设计和有限元分析技术,进行差速器齿轮参数化设计和强度校核的一体化研究.南京工程学院学报(自然科学版)2012年9月1差速器齿轮的参数化设计目前常用的齿轮参数化建模方法有两种[5]:一种是利用API 函数直接创建对象,利用这些对象来完成齿轮实体的建模、编辑和修改;另一种是手工创建参数化的齿轮模板,提取其中的关键参数变量,通过修改关键参数变量实现齿轮模型的更新.前一种方法涉及的知识面较宽,对编程人员要求较高;后一种方法比较简单,对于非编程人员应用难度较小.因此本文采用后一种方法,即用手工在UG 中参数化创建齿轮实体模型,并将变量用表达式来表示,得到齿轮模板.然后通过修改齿轮模板中的变量,所得到的齿轮模型实现参数驱动下的自动更新.UG /OPEN 提供的MenuScript 和UIStyler 两个模块用于制作应用程序的用户界面[6].其中MenuScript 图1“行星齿轮参数化设计”对话框用于创建和编辑UG 的下拉菜单和工具栏.使用记事本创建应用程序的菜单文件,该菜单文件包括“行星齿轮”按钮和“半轴齿轮”按钮.按钮用于齿轮的参数化设计.进入UG /OPEN UIStyler 模式,创建如图1所示的“行星齿轮参数化设计”对话框.使用VC ++6.0,创建应用程序的工程,工程名称为planet.利用向导ugopen.awx 创建应用程序,应用程序使用ufsta 函数作为入口函数,当UG 进程结束时,自动卸载.将UG /OPEN UIStyler 模块生成的对话框文件planet_template.c 和plan-et.h 分别重新命名为planet_dialog.c 和planet_dialog.h ,复制到工程文件所在的文件夹,并加入工程中.所有齿轮参数的程序编译完以后,再加上入口函数,检验部件函数,对话框回调函数和取消函数等,就完成了主体函数的编译.在“行星齿轮参数化设计”对话框中更改参数数值,单击“应用”按钮,行星齿轮模型就自动完成更新.利用开发的齿轮参数化造型系统,输入齿轮的模数、齿数、压力角等基本参数,自动生成某轿车差速器行星齿轮模型.2差速器齿轮的有限元分析对于汽车差速器锥齿轮副来说,在大多数情况下,汽车左右轮是等速或接近等速的,锥齿轮的相对转速很小,行星齿轮经常只是起个等臂推力杆的作用,弯曲强度应为主要考虑因素.因此差速器行星齿轮主要进行弯曲强度的计算[7].由于直齿锥齿轮疲劳破坏中出现几率最高的是齿面接触疲劳强度问题,如何提高车用齿轮的传动性能与使用寿命,近年来一直深受社会各界的广泛关注.本文运用ANSYS /LS-DYNA 软件,对差速器的直齿锥齿轮副的三对轮齿进行动力学接触仿真分析,得到了良好的接触形态.2.1差速器齿轮有限元模型的建立基于CAD /CAE 一体化技术,有限元软件选用ANSYS 11.0,该软件和UG 软件可无缝连接,在UG 的主菜单中添加了ANSYS 11.0菜单项[8].在UG 中生成齿轮三维模型后,直接点击ANSYS 11.0菜单项,进入ANSYS 11.0界面,然后选择单元类型、单元尺寸、材料属性等建立差速器行星齿轮、半轴齿轮的有限元模型.2第10卷第3期王良模,等:某差速器齿轮的参数化设计及有限元分析2.2差速器齿轮弯曲强度分析载荷沿齿面接触线的分布是决定齿轮应力的基础,因此精确确定载荷沿齿面接触线的分布状态,对于齿轮强度分析具有十分重要的意义.所分析的齿轮是对称零件,因此建立行星齿轮和半轴齿轮单齿的有限元模型来进行分析.其中行星齿轮单齿有限元模型共有2982个节点,2211个实体单元,行星齿轮单齿有限元模型如图2所示.齿轮加载方法有两种:1)在齿轮轮毂加载等效力矩,此时位移的约束需施加在齿顶部位;2)将齿轮所承受的转矩转化为单齿啮合最高点所承受的线性分布力.本文所研究的差速器行星齿轮的加载方式选择后者.约束行星齿轮内圈的所有自由度,将圆周力F 1=3.52ˑ104N ,径向力F 2=1.36ˑ104N ,轴向力F 3=9.1ˑ103N 近似作线性载荷处理,按照比例施加在单齿啮合的最高点处,通过计算所得有限元结果如图3所示.图2行星齿轮单齿有限元模型图3行星齿轮单齿弯曲应力云图由图3可知,行星齿轮单齿最大弯曲应力为1697MPa ,出现在齿根处.符合行星锥齿轮的破坏多出现在齿根的实际情况.2.3差速器齿轮接触应力的有限元分析图4三对齿啮合的齿轮有限元模型利用8节点solid164实体单元和4节点shell163壳单元建立三对齿啮合的齿轮有限元模型,共有16188个节点、948个壳单元和11610个实体单元.其中齿轮实体采用solid164单元划分网格,齿轮的内圈采用shell163壳单元,并将齿轮内圈定义为刚体.有限元模型如图4所示.在ANSYS /LS-DYNA 模块中,定义4个part ,其中主动齿轮和从动齿轮为弹性体,将它们的内圈定义为刚体,以方便载荷和约束的施加.在主动齿和从动齿之间建立自动面接触,面接触的各定义选项均采用默认设置.通过对模型施加合适的边界条件,可模拟齿轮副的运动和传递的扭矩,分别对齿轮在低速和高速两种情况下进行仿真分析.对主动轮施加转速,所选用的主动齿轮转速分别取1.5rad /s 和9rad /s ,从动齿轮的负载分别为1188N ·m 和199N ·m ,计算时间分别设置为0.04s 和0.08s ,在两种速度工况下进行仿真分析,结果如图5、图6所示.计算结果显示两种转速下瞬时最大接触应力分别为161MPa 和914MPa ,齿轮的材料为20CrMnTi ,其接触疲劳极限应力为2250MPa ,所以此时的接触应力远远小于接触疲劳极限应力.另外通过比较可以得3南京工程学院学报(自然科学版)2012年9月出,主动轮的转速越大,齿轮的接触应力越大.图5齿轮啮合瞬时应力云图(1.5rad /s)图6齿轮啮合瞬时应力云图(9rad /s )3结语本文对UG 软件进行二次开发,创建了差速器齿轮的参数化建模系统,实现了汽车差速器齿轮的快速建模,得到的三维齿轮模型是进行精锻模具设计、动态接触有限元分析、机构仿真和数控编程的必要准备.齿轮参数化造型系统的开发大大缩短了差速器齿轮的设计周期,提高了设计质量和设计效率.另外通过对齿轮的静弯曲强度分析,结果表明所设计的行星齿轮和半轴齿轮所受到的最大弯曲应力都出现在齿根部位,与实际情况相符,并且小于许用值,设计满足要求.对齿轮的动态啮合分析,得到了齿轮副在啮合过程中齿面接触应力、应变的变化情况,结果表明齿面接触应力远远小于材料接触极限应力,因此齿轮不会出现接触疲劳破坏.参考文献:[1]蒋法国.差速器行星齿轮的有限元法强度分析[D ].长春:吉林大学,2006.[2]郑威,金俊松,李大才.基于UG 的汽车差速器圆锥齿轮参数化造型系统的开发[D ].武汉:华中科技大学,2007.[3]高翔,程建平.基于ANSYS /LS-DYNA 的直齿锥齿轮动力学接触仿真分析[D ].镇江:江苏大学,2008.[4]ANDREWS J D.A finite element analysis of bending stresses induced in external and internal involutes spur gears [J ].Journal of Strain Analy-sis ,1991,26(3):153-163.[5]VON EIFF H V.Influence of gear tooth geometry on tooth stress of external and internal gears [J ].Trans ASME ,J of Mech Des ,1990,112:575-583.[6]候永涛,丁向阳.UG /Open 二次开发与实例精解[M ].北京:化学工业出版社,2007.[7]刘惟信.圆锥齿轮与双曲面齿轮传动[M ].北京:人民交通出版社,1980.[8]张朝晖.ANSYS11.0结构分析工程应用实例解析[M ].北京:机械工程出版社,2008.4。
直齿圆锥齿轮精密锻造工艺及模具设计
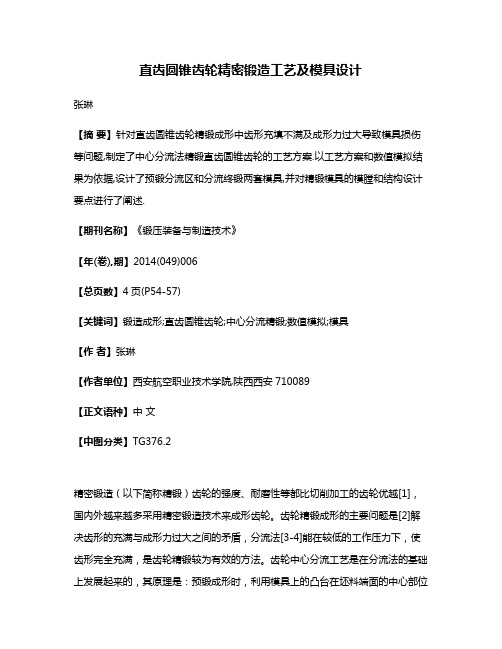
直齿圆锥齿轮精密锻造工艺及模具设计张琳【摘要】针对直齿圆锥齿轮精锻成形中齿形充填不满及成形力过大导致模具损伤等问题,制定了中心分流法精锻直齿圆锥齿轮的工艺方案.以工艺方案和数值模拟结果为依据,设计了预锻分流区和分流终锻两套模具,并对精锻模具的模膛和结构设计要点进行了阐述.【期刊名称】《锻压装备与制造技术》【年(卷),期】2014(049)006【总页数】4页(P54-57)【关键词】锻造成形;直齿圆锥齿轮;中心分流精锻;数值模拟;模具【作者】张琳【作者单位】西安航空职业技术学院,陕西西安710089【正文语种】中文【中图分类】TG376.2精密锻造(以下简称精锻)齿轮的强度、耐磨性等都比切削加工的齿轮优越[1],国内外越来越多采用精密锻造技术来成形齿轮。
齿轮精锻成形的主要问题是[2]解决齿形的充满与成形力过大之间的矛盾,分流法[3-4]能在较低的工作压力下,使齿形完全充满,是齿轮精锻较为有效的方法。
齿轮中心分流工艺是在分流法的基础上发展起来的,其原理是:预锻成形时,利用模具上的凸台在坯料端面的中心部位锻出凹坑,终锻时利用凹坑实现材料的分流。
本文将中心分流法应用到直齿圆锥齿轮(图1)的精锻成形,根据齿轮的尺寸形状特点和成形难点[5]制定合理的工艺方案,以工艺方案和数值模拟结果为依据,设计了预锻分流区-分流终锻的两套模具。
图1 直齿圆锥齿轮零件图1 直齿圆锥齿轮精锻成形工艺方案的制定1.1 中心分流精锻成形工艺路线本文所研究的直齿圆锥齿轮的参数如表1 所示,加工材料为18CrMnTi,该材料是塑性良好的渗碳钢,具有良好的综合力学性能,但变形抗力比较大。
生产实践发现,精锻锥齿轮时常会出现齿形充不满现象和成形力过大导致模具损伤等问题。
为此,该齿轮采用中心分流法锻造,通过预锻和终锻两个工步完成,其精锻工艺路线为:精密下料→车削或磨削外圆、除去表面缺陷层→少无氧化加热→预锻→精(终)锻→冷切边→热处理→后续切削加工。
汽车半轴加工工艺分析与设计

目录中文摘要1.前言1.1国外汽车半轴的加工工艺1.2国内后桥半轴先进的机械加工工艺技术2.材料的选择3.汽车半轴加工工艺流程及主要加工工序3.1剪料3.2摔杆3.3摆帽3.4喷丸3.5杆部校直3.6钻小端中心孔A3/7.53.7粗车大外圆3.8粗车小端3.9车大孔3.10钻中心孔B4/12.53.11粗车大端、精车大端3.12精车小端3.13冷滚轧花键3.13.1冷滚轧花键的优点3.13.2冷滚轧花键的加工方法3.13.3冷滚轧花键的工艺要求3.13.4典型的冷滚轧机技术参数3.13.5冷滚轧花键加工实例3.14半轴的热处理3.14.1热处理的具体工序3.15磁力探伤检验4.夹具设计4.1原夹具存在的问题4.2可微调新型夹具摘要汽车自19世纪末诞生至今100余年期间,汽车工业从无到有,以惊人的速度发展,写下了人类近代文明的重要篇章。
汽车是数量最多、最普及、活动范围最广泛、运输量最大的现代化交通工具。
没有哪种机械产品像汽车这样对社会产生如此广泛而深远的影响。
半轴是汽车传动系统的一个重要组成部分,半轴是用来将差速器半轴齿轮输出的动力传给驱动轮或轮边减速器,对于采用非独立式悬架的驱动桥,根据其半轴内端与外端的受力状况,一般又分为全浮式半轴、四分之三浮式半轴与半浮式半轴三种。
半轴内端以花键连接着半轴齿轮,半轴齿轮在工作时只将扭矩传给半轴,几个行星齿轮对半轴齿轮施加的径向力是互相平衡的,因而并不传给半轴内端。
主减速器从动齿轮所受径向力则由差速器壳的两轴承直接传给主减速器壳。
因而,半轴内端只受扭矩而不受弯曲力矩。
半轴是汽车的轴类零件中承受扭矩最大的零件,为了满足半轴的强度要求.多年来,世界备国除了用各种各样的计算方法外,还在材料选择、毛坯成型、机械加工和热处理等方面进行着不懈的努力。
本文主要是对半轴在锻造车间、机加车间、热处理车间的各步工艺进行分析和改进以及半轴的热处理和半轴齿轮的夹具改进。
半轴齿轮广泛用于汽车、拖拉机等一切行走机械的差速器中,应用面广。
锻造新工艺

10.1等温锻造(Isothermal forging)10.2粉末锻造(Powder forging)10.3精密模锻(Precision forging)10.4半固态模锻(Semi-solid forging)10.5超塑性锻造(Superplastic forging)10.6连铸连锻(Continuous casting and forging)10.7液态模锻(Liquid die forging)10.8辊锻(Roller forging)10.9 环轧(Ring rolling)10.10摆动辗压(Swing rolling)10.11横轧与斜轧(Cross rolling and skew rolling)10.12 径向锻造(Radial forging)第10 章锻造新工艺我们知道,金属加工的最终目的是提供零件,这些件来自于铸造(液态金属凝固)、粉末冶金(金属粉末压实)、(固体金属的)成形和(切除金属的)切削。
锻造实际是固体金属成形的一种金属加工方法。
锻造与其它方法结合便涌现出一系列新的方法,即锻造新工艺。
因此,锻造新工艺是在相关理论和工艺的基础上发展而来的。
有的工艺目前处于应用研究阶段,有的处于探索阶段。
本章介绍一些新工艺的概念、原理及工艺参数等。
10.1等温锻造(Isothermal forging)顾名思义,等温锻造为恒定温度下的锻造,而常规锻造为一定温度区间(始锻温度-终锻温度)内的锻造。
前者具有明显的优点,由于等温锻造,必然组织均匀,制品性能均匀。
10.2粉末锻造(Powder forging)与铸造相比,粉末锻造之前的铸造过程被粉末处理过程所替代,因此粉末锻造的工艺发生了变化。
粉末热锻的工艺流程为:粉末原料→预成形坯→烧结→加热→锻造。
由于粉末锻造是在普通粉末冶金和精密模锻工艺基础上发展而来的,因此它具有如下特点:1)粉末预成形坯通过加热锻造的途径,提高了制品的密度,因此使制品的性能接近甚至超过同类熔铸制品的水平;2)保持了粉末冶金工艺制造坯料的特点,因为粉末预成形坯含有80%左右的孔隙,其锻造应力比普通熔铸材料要低很多;3)材料的利用率达80%以上;4)制品的精度高、组织结构均匀、无成分偏析;5)能够锻造难于锻造的金属或合金和各种复杂形状的制品,例如难变形的高温铸造合金。
半轴齿轮温(热)精锻新型模具设计

尖 角 。 拟 分 析 及 生 产 实 践 证 明 , 具 不 易 于 齿 轮 型 模 模
腔 的 充 满 , 形 结 束 时 齿 顶 不 饱 满 , 品 率 高 。 且 成 成 废
: 玉峰 (9 2 , , 士在 读 , 事 金属 塑性 成 形 数 值 模 夏 17 一) 男 博 从
拟 模 具 C ) C A1 AM/ A / C E万 向研 究
1 引 言
孔 花 键 一 热 处 理 一 喷 丸 。
目前 ,
轮 精 锻 技 术 口益 受 到 _ r呲 界 各 的 高
上 述工 艺 能耗 大 , 料利 用 率低 , 工 效率 低 , 材 加
度 莺 视 , 国 、 固 、 本 等 发 达 国 家 在 这 方 面 的 研 德 美 口
l可 看 出 , 顶 处 ( 小 圆 圈 出 部 分 ) 最 终 充 填 区 。 齿 用 是 方 案 1模具 结 构 按 经验 设 计 , 用 平 底 凸 模 , : 采 上 凹 模 为齿 模 , 凹模 为 背 锥 模 , 模 中 齿 顶 处 不 设 下 齿
:0 7 0 0 2 0 —1 — 9
摘 要 : 用 有 限 元 模 拟 软 件 对 半 轴 齿 轮 的 温 精 锻 成 形 过 程 进 行 了数 值 模 拟 分 析 , 比分 析 了 两 种 凸 模 运 对 及 凹 模 结 构 形 状 对 齿 形 成 形 的 影 响 。 设 计 了 伞 齿 轮 完 全 闭 塞 式 锻 造 的 模 架 , 心 部 位 刚 性 锁 模 机 构 具 有 良 核
2 工 艺 分 析
0. 3。
轴 齿 轮 传 统 精 锻 ] 艺 :坯 料 加 热 一 粗 锻 一 切 去 氧 化 皮 一 加 热 一 精 锻 一 切 飞 边 一 表 面 清 压 整 形 一 切 削 内 孔 、半 轴 和 大 端 面 一 拉 削 内
汽车用齿轮类零件的精密锻造技术
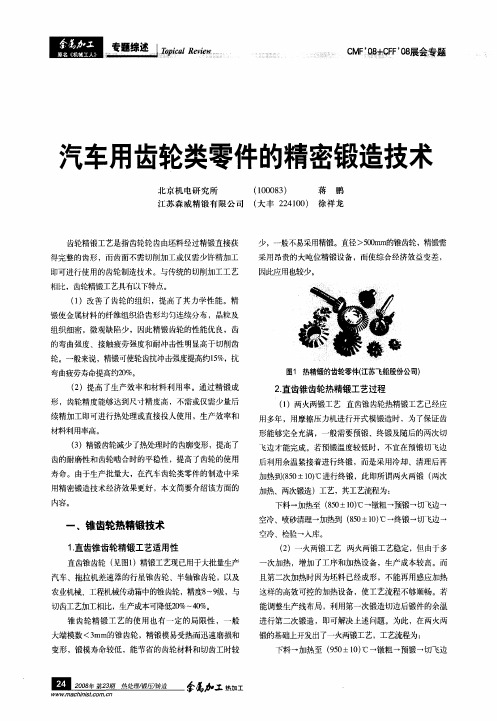
一
\
闭塞锻造的基本动作包括合模并锁紧模腔 、单个或
多个冲头进 出模具型腔 、开模及 卸料 杆顶件 出模等5 类
动作 。实质是 冲头挤 压封 闭型腔的坯件使之变形为预 先
设定 的形状 。其特 点是一次锻 造成 尺寸形状 精度高的工 件 ,实现近净形锻造 。它要求预制坯体 积误 差小 、接 触 工件的模具型 面能承受较 高的单位压 力 , 锻造工艺 力较 大 。所以对设备能力 、设备与工装模具 的刚度及工况状
。
—■●●oaew ■堡■ i v ■■ —TcRi 曼■ x l e ■■ ● ■ 苎 p ■上
CF8 F0 会 题 M Qc’展 专 士 F8
汽车用齿轮类零件的精密锻造技术
北京机 电研究所 (0 0 3 10 8 ) 蒋 鹏
江苏森威精锻有限公司 ( 大丰 2 4 0 ) 徐祥龙 2 10
下料一加热至 (5 ±1) 90 0 ℃一镦粗 一预锻 一切飞边
目 堡 塑 垫 _ 丝 竺
' 们 m aCh nl . Om . l StC 鲫
参 加 磊 工热工
C ’ C’ 会 题 M0 F0 专 F8 F8 + 展
一
, I竺 苎 堡
二 锥齿轮的冷精锻技术
1 . 锥齿轮的闭塞冷锻成形技术
o
一
态下的强度等提出了更高的要求。 闭塞锻造直 齿锥 齿轮 的锻造工步仅有制坯和成形两 步 ,工艺流程短,成形精度高。
2冷摆辗工艺 .
除 闭塞成形外 ,冷摆辗技术也可应用于汽车伞齿轮
的精密成形 , 并用于钢质同步器齿环的齿形成形。
瑞士T ( rt o o i r s 摆动辗压机是 型 Ob aC lFr n P s il d m g e )
汽车半轴生产工艺调研

汽车半轴生产工艺调研材料:需要有较好的抗弯抗剪强度和韧性,如合金调质钢中的40Cr。
抗剪强度:指外力与材料轴线垂直,对材料呈剪切作用时的强度极限。
一般工序:1.选料剪切,确定加工余量2.空气锤进行胎模锻造(搜索到新工艺是用压力机挤压工件代替空气锤锻造),摆辗机摆帽(有篇论文是新工艺方法,下面提到)3.喷丸处理4.毛坯杆部矫直工序解读:1. 摆辗工艺:●原理作用:利用一个绕中心迅速滚动的圆锥形上模对毛坯端面局部加压。
使毛坯逐步成形的一种加工方法。
能够实现对横截面是圆形的管类零件和带底的管状容器的外径径向摆动辗压并使零件壁厚产生变化的机器。
零件是致密件时径向摆动辗压可改变其外径尺寸。
●不足之处:由于还是采用二火工艺锻造,锻造中氧化皮脱落严重,一是造成环境污染,另一方面影响表面质量,掌握不好还会造成材料过烧。
⏹新工艺:一火挤辗成形。
一火锻造工艺的特点是将二次加热合为一次,预锻—成形二步合为一步,设备也由二台合为一台。
工序对比:目前,下料(圆料),整体加热,锤上拔长,局部加热,摆辗机摆辗成形或者下料(圆料),局部加热,油压机压蒜头,局部加热,摆辗机摆辗成形。
一火锻造,下料(圆料),局部加热,热挤辗机挤辗,成形。
参考:汽车半轴一火锻造工艺及设备_付建华.caj2.喷丸处理:喷丸是用来清除厚度不小于2mm的或不要求保持准确型砂及旧漆膜。
是表面涂(镀)覆前的一种清理方法。
效果:喷丸强化工艺对材料的抗拉强度σb没有明显的影响;延伸3.矫直:毛坯矫直和热处理后矫直,毛坯校直解释同晶哥晚上所画,用两个固定校直滚子装置支承半轴,由一个传动连接装置与半轴法兰端上的两个突出部位相吻合,并带动半轴旋转,尾座顶尖顶住半轴的杆部,校直机上的压头下落,半轴在滚子和压头的作用下校直。
热处理后矫直原理方法相同,但跳动不大于0.08,0.2和0.4。
一般工艺需要设备:1.锯床:2.空气锤:电动机通过减速机构和曲柄,连杆带动压缩气缸的压缩活塞上下运动,产生压缩空气。
MP-1600热模锻压力机精锻齿轮自动化锻造生产线技术方案

MP-1600热模锻压力机精锻齿轮自动化锻造生产线技术方案一、生产线整体工艺方案:根据精锻齿轮生产特点,推荐MP1600热模锻压力机生产线,主要包含MP-1600热模锻压力机、自动送料装置(步进梁)、YKT-630热模锻压力机、传送带等。
用于精锻齿轮锻件的多工位自动化锻造生产,采用四工位温热精锻加冷精整的方式,热锻频率为每分钟8-10次,工艺技术方案如下:1、精密下料后的棒料成箱用叉车放入中频感应加热炉的料箱翻斗内,传送至步进式自动上料机,自动地把坯料输送到出料输送链上,进入夹辊轮进料系统,棒料以连续均匀的预定速度通过加热感应线圈加热至设定温度;通过温度分选机构,不合格棒料排除,合格棒料通过快速出料机构送入红件输送带。
2、红件输送带将棒料送入自动输送装置始端的翻转料槽,使棒料直立,便于输送装置的夹爪夹持。
3、自动输送装置(机械手)安装在MP热模锻压力机两侧,负责锻件的自动传送工作。
4、MP热模锻压力机具有四个锻造工位:镦粗、预锻、终锻、切边。
5、模具和模架安装在热模锻压力机上,通过自动喷雾装置进行润滑和冷却。
6、锻造完成后,锻件通过输送带传送至指定料框。
7、半轴齿轮:目前锻造工艺,Ø55X90,1.67kg ,压力机上工步为:镦粗—预锻—终锻—切边。
8、行星齿轮:目前锻造工艺,Ø35X64,0.48kg ,压力机上工步为:镦粗—预锻—终锻—切边。
9、锻件冷却后进行喷砂清理去除氧化皮,表面上油后在YKT-630热模锻压力机上进行冷精整达到需要锻件精度。
(下料、喷砂清理、上油设备和装置不含在以上方案中)以上工艺为理论计算,实际生产过程会稍有变化,根据生产情况可以进行完善和调整。
生产线外形布置图如下:二、MP-1600热模锻压力机和YKT-630冷挤压机:(一)压力机主要技术参数MP-1600YKT-630(二)MP热模锻压力机主要特点1、机架:采用整体式铸造机身。
机架两侧开有侧窗口,方便横向送料。
17Cr2Ni2Mo齿轮轴锻造工艺研究

标准要求 内控
实测值
C
Hale Waihona Puke SiMnpsCr
Ni
Mo
名 I~~立; I。飞 0.14-0.19 0.17-0.35 0.40-0.60 .;;.0.030 .;;.0.030 1.50-1.80 1.40-1.70 0;25-0.35
0.1 ~·191 o. 1~~·351 0. 4~.~~·60~~~~!5
(1)该齿轮轴材质为17 Cr2Ni2Mo, 执行JB/T
一 6395 2010《大型齿轮、齿圈锻件技术条件》。在
原材料的选用上,优选真空精炼钢锭,内控各元索
化学成分含量,严格控制钢锭内有害元素S、P及
H的含量,减少钢锭原材料本身的夹杂与偏析,并
P~o. s: 要求保证
01s%, 至0. 010% , [ H]~2. ><
标得到提升。傲粗后增加保温时间,有利于金属 元素扩散均匀和改善俯析程度,同时也为锻造时 焊合大截面锻件心部的空隙缺陷创造了有利条 件。因此在墩粗后、用宽咕拔长前严格控制保温 温度,并将保温时间增加50%。较高的始锻温 度、蚽料良好的均匀加热状态为宽祜走扁方拔长、 进行中心压实、焊合还料中心疏松创造了必要条 件。
1 原材料的选择
3 罕迂 耳江 霆忽;
矗 l~:; ::il忌 ,岔i ~I
雪
图l 17Cr2Ni2Mo齿轮轴锻件图
Figure 1 Sketch of 17Ci2Ni2Mogear shaft forging
该批齿轮轴有效截面尺寸较大,最大外圆尺 寸达到0910 mm, 在我公司32 MN水压机上锻造 生产,设备能力略显不足,满足JB/T 5000. 15一
关键词:齿轮轴;锻造工艺;热处理工艺 中图分类号:TG316 文献标志码:B
22CrMo材料半轴齿轮心部硬度的控制研究

22CrMo材料半轴齿轮心部硬度的控制研究王彩;潘晓东;谢立湘【摘要】分析了影响半轴齿轮心部硬度的主要因素,通过选取合适的材料成分及J15端淬值,并根据具体的端淬值优化渗碳淬火工艺,还分析了金相组织对心部硬度散差的影响.再经过长期的热处理生产实践跟踪,发现能很好地控制半轴齿轮的心部硬度.对于提高低碳合金齿轮弯曲疲劳强度有着重要的指导意义.【期刊名称】《金属加工:热加工》【年(卷),期】2017(000)003【总页数】3页(P7-9)【关键词】半轴齿轮;心部硬度;渗碳淬火【作者】王彩;潘晓东;谢立湘【作者单位】株洲齿轮有限责任公司;株洲齿轮有限责任公司;株洲齿轮有限责任公司【正文语种】中文我公司开发制造的一种高承载能力半轴齿轮,锥齿大端模数10.3,净重3.3kg,采用精密锻造+渗碳淬火工艺。
为了满足该齿轮的弯曲疲劳强度设计要求,心部硬度需在38~45HRC,弯曲疲劳强度达到最大值。
故通过选取不同的钢材、以及同一材料不同的端淬值,在一定的热处理工艺条件下反复试验,摸索规律,稳定地控制齿根心部硬度(齿宽中部横截面上,轮齿中心线与齿根圆相交处):35~40HRC;节圆心部硬度(齿宽中部横截面上,轮齿中心线与节圆相交处):38~45HRC;心部铁素体量≤5%。
(1)化学成分材料的化学成分确定了材料端淬值的范围,而对于某一特定结构的齿轮,端淬值对心部硬度起决定性因素。
首先选取SAE8620H材料,经过数轮的材料端淬值试验选取和热处理工艺试验,该产品的节圆心部硬度均在34HRC以下。
为提升齿轮的心部硬度,经过成分、使用性能类比分析(表1为SAE8620H与22CrMo材料主要化学成分对比),选用淬透性更好的22CrMo材料。
采用22CrMo材料比8620材料有两个明显的优势:①材料原始wC提高了0.02%,可以提高心部的淬硬性。
②其中wCr增加约0.50%,可显著提高材料的淬透性,为后续热处理工艺参数的调整留有较宽的范围。
模具设计与制造—— 热锻工艺概述
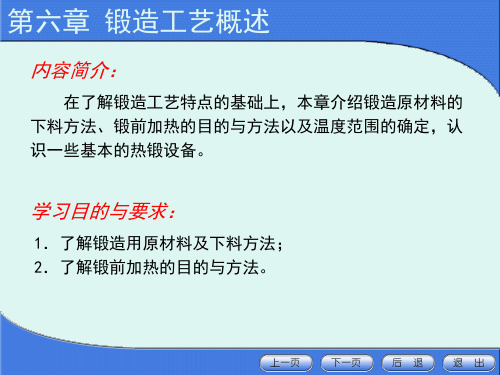
内容简介:
在了解锻造工艺特点的基础上,本章介绍锻造原材料的 下料方法、锻前加热的目的与方法以及温度范围的确定,认 识一些基本的热锻设备。
学习目的与要求:
1.了解锻造用原材料及下料方法; 2.了解锻前加热的目的与方法。
第六章 锻造工艺概述
第一节 锻造工艺特点
一、锻造生产的重要性
锻造是塑性加工的重要分支,它是利用材料的塑性,对材 料施加外力使之发生塑性变形,从而得到所需形状、尺寸、 组织和性能的锻件。
第六章 锻造工艺概述
第二节 锻造用材料及下料方法-锯切法
锯床下料极为普遍,虽效率低,锯口损耗大,但下料长 度准确,锯割断面平整,是一种主要的下料方法。有圆盘锯、 带锯、弓形锯等。
圆盘锯是由电动机带动带齿的锯盘旋转并移动,将棒料 切断。
弓形锯是由电动机带动带齿的锯条作往复移动,将棒料 切断。
第六章 锻造工艺概述
加热时间:毛坯从开始加热至始锻温度时所需的时间。不包括毛 坯在始锻温度下的保温时间。
第六章 锻造工艺概述
第六节 少无氧化加热
通常称金属烧损量在0.5%以下的锻造加热为少氧化加热。 称金属烧损量在0.1%以下的锻造加热为无氧化加热。 少无氧化加热除了可减少金属氧化、脱碳外,还可显著提高
锻件表面质量和尺寸精度,减少模具磨损等;是实现精密锻造必 不可少的配套技术。
快速加热 利用介质保护加热
少无氧化火焰加热
第六章 锻造工艺概述
第六节 少无氧化加热-炉气
第六章 锻造工艺概述
第六节 少无氧化加热-快速加热
包括:火焰炉中的辐射快速加热和对流快速加热,感应电加热和 接触电加热等。
理论依据:采用技术上可能的加热速度加热金属时,坯料内部产 生的温度应力、留存的残余应力和组织应力叠加的结果,不足以 引起坯料产生裂纹。
锻造新工艺复习资料
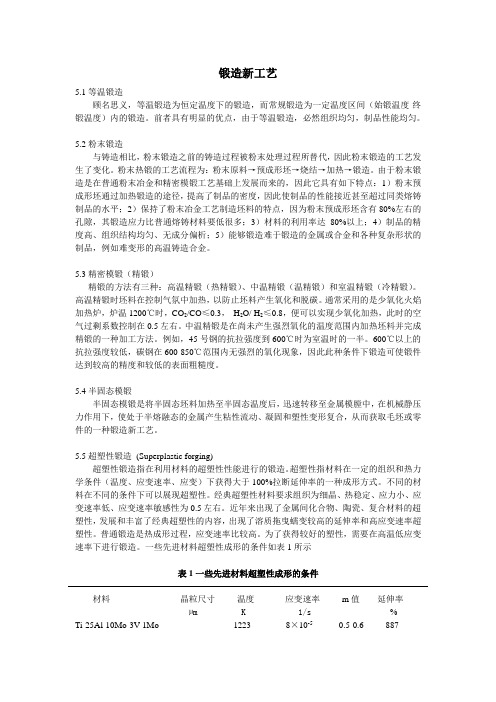
锻造新工艺5.1等温锻造顾名思义,等温锻造为恒定温度下的锻造,而常规锻造为一定温度区间(始锻温度-终锻温度)内的锻造。
前者具有明显的优点,由于等温锻造,必然组织均匀,制品性能均匀。
5.2粉末锻造与铸造相比,粉末锻造之前的铸造过程被粉末处理过程所替代,因此粉末锻造的工艺发生了变化。
粉末热锻的工艺流程为:粉末原料→预成形坯→烧结→加热→锻造。
由于粉末锻造是在普通粉末冶金和精密模锻工艺基础上发展而来的,因此它具有如下特点:1)粉末预成形坯通过加热锻造的途径,提高了制品的密度,因此使制品的性能接近甚至超过同类熔铸制品的水平;2)保持了粉末冶金工艺制造坯料的特点,因为粉末预成形坯含有80%左右的孔隙,其锻造应力比普通熔铸材料要低很多;3)材料的利用率达80%以上;4)制品的精度高、组织结构均匀、无成分偏析;5)能够锻造难于锻造的金属或合金和各种复杂形状的制品,例如难变形的高温铸造合金。
5.3精密模锻(精锻)精锻的方法有三种:高温精锻(热精锻)、中温精锻(温精锻)和室温精锻(冷精锻)。
高温精锻时坯料在控制气氛中加热,以防止坯料产生氧化和脱碳。
通常采用的是少氧化火焰加热炉,炉温1200℃时,CO2/CO≤0.3,H2O/ H2≤0.8,便可以实现少氧化加热,此时的空气过剩系数控制在0.5左右。
中温精锻是在尚未产生强烈氧化的温度范围内加热坯料并完成精锻的一种加工方法。
例如,45号钢的抗拉强度到600℃时为室温时的一半。
600℃以上的抗拉强度较低,碳钢在600-850℃范围内无强烈的氧化现象,因此此种条件下锻造可使锻件达到较高的精度和较低的表面粗糙度。
5.4半固态模锻半固态模锻是将半固态坯料加热至半固态温度后,迅速转移至金属模膛中,在机械静压力作用下,使处于半熔融态的金属产生粘性流动、凝固和塑性变形复合,从而获取毛坯或零件的一种锻造新工艺。
5.5超塑性锻造(Superplastic forging)超塑性锻造指在利用材料的超塑性性能进行的锻造。
- 1、下载文档前请自行甄别文档内容的完整性,平台不提供额外的编辑、内容补充、找答案等附加服务。
- 2、"仅部分预览"的文档,不可在线预览部分如存在完整性等问题,可反馈申请退款(可完整预览的文档不适用该条件!)。
- 3、如文档侵犯您的权益,请联系客服反馈,我们会尽快为您处理(人工客服工作时间:9:00-18:30)。
半轴齿轮精锻新型模具青岛建筑工程学院(山东青岛266033)田福祥尹德良孙宗强青岛精锻齿轮厂付志刚[摘要]指出了精锻汽车差速器半轴齿轮原模具结构存在的问题,提出了新型模具结构。
生产实践表明,新模具可显著提高使用寿命和生产效率,降低材料消耗。
关键词齿轮制造精密模锻模具[Abstract]The p roblems existin g in the p revious structure of the fine fo r g in g die for differ ential half axle g ear s o f automo biles were p ointed out,and a new_t yp e die str ucture was p ut forward. Practical production shows that the new die could greatly extend its service life,increase the p roduction efficienc y and lower the material consum p tion.Ke y words g ear manufactur in g,p recision die for g in g,mould(4)由于模具的侧向分型面较长,斜导柱带动的滑块分型尺寸较大,采用了两个同样尺寸、同样角度的斜导柱带动斜滑块进行分型,很好地保证斜滑块运动的稳定性和协调性。
该模具经生产验证,结构紧凑合理,易于加工制造,能够很好地保证塑件的形状尺寸和表面质量等要求,而且塑件的成型质量比较稳定,模具寿命长,取得了很好的经济效益。
对于埋设件较多、精度要求较高、分型方向较多的注射模结构设计有较好的借鉴价值。
参考文献1塑料模设计手册编写组.塑料模设计手册.机械工业出版社,1994.2虞传宝.冷冲压及塑料成型工艺与模具设计资料.机械工业出版社,1992.3成都科技大学.塑料成型工艺.轻工业出版社,1991.1锻件工艺分析半轴齿轮是汽车差速器的重要零件,需求量很大。
半轴齿轮原精锻工艺为:坯料加热粗锻切飞边去氧化皮加热精压切飞边表面清理冷压整形切削内孔、半轴和大端面拉削内孔花键热处理喷丸。
其中,精压工序俗称精锻工序,本文为避免该工序与整个精锻工艺的!精锻∀一词相混淆而称为精压。
上述工艺的粗锻模和精压模结构形式相同,只是模腔尺寸及齿槽精度有差异。
模具结构如图1所示,齿模在下模,半轴凹模在上模,上、下模用锁扣(或称止口)导向。
这种模具有诸多缺点:锻件车削余量大,钢材利用率,模具寿命和生产效率低。
其原因有以下几方面。
(1)粗锻时难以准确迅速地放置坯料,导致料收稿日期:1999年5月26日图1原半轴齿轮锻模1.半轴凹模2.压圈3.齿模4.顶料芯轴5.上顶杆6.下顶杆块加大。
坯料定位对于模锻,特别是精密模锻至关重要。
原模具的齿模在下模,坯料放在顶料芯轴上,因顶料芯轴上平面内的模具齿顶圆直径大于坯料直径,如图2所示,坯料靠人工目测定位,难以准确迅速地放置坯料。
尽管操作者力图放正,许多坯料仍是在偏置状态下锻造的(偏置量为 ),影响生产效率和锻件质量(锻件上下错位),为保证放偏的坯料也能成形为合格的锻件,只好加大料块。
图2坯料在原锻模上偏置(2)模具无上顶料装置,半轴模拔模斜度过大,锻件半轴金属辅料过多。
国内绝大多数齿轮精锻设备是摩擦压力机。
因摩擦压力机、原粗锻模和精锻模均无上顶料装置,因此半轴凹模留有较大的拔模斜度(7#~10#),致使锻件半轴处金属辅料过多,车削余量过大,增加了钢材消耗和车削成本,导致钢材利用率低和车削生产效率低,齿轮半轴较长时问题尤为突出。
(3)齿模温度升高,导致齿模回火或热疲劳早期失效。
原粗锻模的齿模与坯料(或锻件)之间传热包括3个阶段:∃锻打前放在顶料芯轴上热坯料对齿模的烘烤传热;%锻件成形过程中的接触传热,称为成形传热;&粗锻变形结束时,上模随滑块上行,锻件留在下模(齿模),人工操作顶料系统将锻件顶出齿模,在这段时间内热锻件与齿模的接触传热称为延时传热。
由于热锻件与齿模总传热时间较长,使齿模温度上升较高。
当齿模温度超过其回火温度时引起齿模回火,硬度降低,导致齿模塑性变形早期失效。
同时因齿模表面温度过高,而内层金属尚处于较低的温度,表层热膨胀而产生压应力(热应力)。
锻件出模后,由于向齿模表面喷洒冷却润滑剂,使齿模表面急冷而收缩,齿模表面如此骤冷骤热,产生循环热应力,使齿模表面产生裂纹,导致齿模热疲劳早期失效。
(4)粗锻模采用锁扣导向,锁扣易于损伤和早期磨损,导致上、下模错移和齿模塑性变形。
这种模具结构采用锁扣导向,受压力机滑块行程和操作空间限制,模具锁扣导向长度较短,而粗锻时,由于坯料变形量大,滑块粗锻行程(从上模接触坯料至坯料变形结束过程中的滑块行程)长,即锁扣导向长度小于滑块粗锻行程,在锁扣导入之前金属变形已经开始。
由于锁扣导入之前,金属的不均匀变形产生很大的横向力作用于上、下模,锁扣不是自由导入,而是在受很大横向力约束下导入的,使锁扣导入面被损伤并很快磨损失效。
如果继续使用该模具,则产生上、下模错移,不仅造成锻件上下错位,易出废品,而且造成锻件飞边厚度一侧厚,另一侧薄(甚至小于允许的最小飞边厚度),当某处飞边很薄时,作用在模具齿大端面上的单位压力极大,加之模具因温升过高引起回火而硬度降低等因素,致使模齿发生塑性变形。
为了解决上述问题,研制了节材、高效、高寿命的半轴齿轮新型锻模。
经工艺实验和试生产,达到了预期目的,效果很好。
2新型粗锻模新型粗锻模如图3所示,半轴模在下模,齿模在上模,采用导柱和导套导向。
该模具有以下特点:(1)坯料定位准确迅速。
由于半轴模在下模,且凹模为圆筒形,所以只要坯料直径适当(热坯料在凹模内,单边间隙0.5~0.8mm),坯料在凹模中自然准确定位,即坯料依靠其直径与凹模配合自然定位,而不是依靠人工目测。
由于该模具可使坯料定位准确,不会偏置,所以无需以增大飞边为代价来保证锻件丰满。
这样可减小坯料重量,节约钢材。
(2)锻件半轴拔模斜度小。
由于半轴凹模在下模,摩擦压力机有下顶料装置,所以半轴凹模的拔模斜度可以为零或很小(不超过1#),显著减小了锻件半轴的金属敷料,不仅提高了钢材利用率,并且减少了切削余量,提高了生产效率,降低了生产成本。
(3)齿模在上模,齿模与热锻件接触时间短,模具温升小,模具寿命高。
由于齿模在上模,热坯料(或锻件)与齿模之间只有成形传热,而无烘烤传热和延时传热。
齿模锻打锻件成形后立即随滑块上行,由于齿模对锻件的摩擦力小于半轴模对锻件的摩擦力,锻件在锻打完成后的瞬间即脱离上行的齿模。
因此齿模与锻件接触时间极短,大大减小了齿模温升,从而避免了齿模回火和热疲劳早期失效。
(4)上、下模导向准确,无错移。
由于采用导柱导套导向,导向行程足够长,上模与坯料接触之前,无横向力干涉,导柱与导套已自由导入,避免了导入面之间的损伤和早期磨损失效,确保上、下模导向准确,不发生错移。
图3新型粗锻模3新型精压模新型精压模结构如图4所示,根据粗锻件以齿定位的要求,齿模在下模。
由于精压温度(800∋以下)比粗锻温度(1050~1150∋)低得多,所以只要合理冷却,不会出现原粗锻模那样的齿模温升过高问题。
上模装有由弹性元件、托板、顶料杆和推件器组成的顶料装置。
该模具有以下特点:(1)锁扣自由导向。
锁扣止口面由导入锥面(图中未画出)和导向柱面两部分组成。
因为齿轮精压变形量小,滑块精压行程(锻件精压变形过程中的滑块行程,一般为4~6mm )远小于锁扣导向长度(导向面母线长度,一般为12~18mm ),上模与锻件接触前,上下模锁扣已自由导入圆柱面,所以锁扣导向完全满足精压要求,而不会产生锁扣损伤和早期磨损。
(2)上模(半轴模)装有上顶料装置,半轴凹模无拔模斜度。
精压前,热态的粗锻件半轴直径小于半轴凹模圆筒直径,两者之间的单边间隙约为1mm 。
精压时,仅齿轮大端承受锻造力,锻件半轴不承受锻造力(只承受弹性元件的顶料力),即半轴不变形。
精压后,齿轮锻件大端靠近半轴处压出一个2~3m m 高(约为滑块精压行程的1/2)的柱面台阶,半轴凹模圆筒内壁仅与小台阶柱面接触,与锻件半轴其余部分不接触。
来自弹性元件的顶料力仅须克服这一小段的摩擦,即可使锻件脱开上模,因此所需的上顶料力和顶料行程都很小,一般的弹性元件很容易满足其要求。
如果半轴凹模口有2~3m m 长的适当锥度,则所需的上顶料力更小,甚至不用上顶料装置锻件即可脱模,但在锻件半轴根部会多出一点金属余量。
这种模具结构既保证了锻件齿形的精压,又不改变粗锻件半轴的很小拔模斜度(小于1#),从根本上解决了原工艺存在的齿轮锻件半轴处拔模角过大、金属敷料过多的问题。
图4新型精压模4结束语新型半轴齿轮精锻模克服了原模具存在的问题,先进实用,经济效益显著。
新模具与原模具相比,材料利用率提高8%,粗锻模的齿模寿命提高3倍以上,还大大减少了设备占用和人工费用。
1.齿模套圈2.凸模3.齿模4.上模板5.导套6.导柱7.半轴模套圈8.半轴凹模9.顶杆10.下砧11.下模板1.上模板2.推件器3.弹性元件4.半轴凹模 5.半轴模套圈 6.齿模套圈7.齿模8.顶杆9.下砧10.下模板塑料产品快速制作和小批量生产用瑞士汽巴公司(Ciba)材料生产类似PE 、PP 、ABS 等塑料产品,一般4个工作日交货,开模费为钢模的1/10,塑料制品收费按合格产品重量总和计,0.8元/克。
另外,瑞士汽巴公司(Ciba)模具树脂适合制造发泡、吸塑、翻砂铸造、金属压延等模具,可替代金属模具。
欢迎咨询!北京豪仪测控工程有限公司电话:(010)6496514964992101传真:64992101联系人:韩礼华施义(013701033673、013701075480)地址:北京亚运村汇园公寓丁座707室邮编:100101。