PLG0J122MDO1中文资料
EP1-3G2S中文资料

DESCRIPTIONThe NEC TOKIN EP2 / EP1 series are PC-board mount type automotive relays suitable for various motorcontrols and other applications that require a high level of quality and performance.EP2 series is a twin-relay and divided into two types for different usage.One is an H-bridge type designed for forward and reverse control of the motors, and the other, a separatetype containing two separated relays in one package.EP1 series is a 1 Form c relay equivalent to EP2 series in performance.FEATURESFor motor reversible control and solenoid controlApprox. 50% less relay space than conventional relayHigh performance and productivity by unique structureFlux tight housingAPPLICATIONSPower windowAntenna lifterAuto-seat positioningElectrical door lockPassive seat belt controlKeyless/Remote entry systemSliding roof controlThe information in this document is subject to change without notice.Date Published August 2002 MPrinted in Japan© NEC TOKIN Corporation 2002EP2 / EP1 SERIES2SCHEMATIC (BOTTOM VIEW)EP2 SERIESEP1 SERIESDIMENSIONS mm (inch)EP2 SERIESEP2/EP1 SERIES3EP1 SERIESPCB PAD LAYOUT mm (inch) (BOTTOM VIEW)EP2 SERIESEP1 SERIESEP2 / EP1 SERIES4SPECIFICATIONSat 25°C (77°F )Items EP2 EP1Contact Form1 Form c ×2 (H bridge type and separatetype)1 Form c Contact Material Silver oxide complex alloy(special type available) Contact Resistance 50 m Ω max. (measured at 7 A) initial Contact Switching Voltage 16 Vdc max. Contact Switching Current 25 A max. (at 16 Vdc) Contact Carrying Current 20 A max. (1 hour max.),25 A max. (2 minutes max.) at 12 Vdc25 A max. (1 hour max.),30 A max. (2 minutes max.) at 12 VdcOperate Time Approx. 5 ms (at 12 Vdc) initialRelease TimeApprox. 2 ms (at 12 Vdc) initial. without diode Normal Operate Power 0.48 W / 0.64 W (at 12 Vdc) Insulation Resistance 100 M Ω min. (at 500 Vdc) initial Breakdown Voltage 500 Vdc min. (for 1 minute) initialShock Resistance 98 m / s 2[10 G] min. (misoperating), 980 m / s 2[100 G] min. (destructive failure)Vibration Resistance10 to 300 Hz, 43 m/s 2[ 4.4 G] min. (misoperating)10 to 500 Hz, 43 m/s 2, [ 4.4 G] 200 hours (destructive failure) Ambient Temperature –40 °C to +85 °C (–40 °F to +185 °F)Coil Temperature50 °C / W (122 °F/W)(contact carrying current 0 A)Mechanical1 × 106operationsLife ExpectancyElectrical100 x 103operations (at 14 Vdc. Motor Load 20 A / 3 A) WeightApprox. 15 gn (0.53oz) Approx. 8 gr (0.28 oz)COIL RATINGEP2 SERIESat 25°C (77°F ) Part Number H Bridge Type Separate Type Nominal Voltage (Vdc) Coil Resistance (Ω±10%)Nominal Current (mA) Must Operate Voltage (Vdc max.)Must Release Voltage (Vdc min.)Nominal Operate Power (W) EP2-3L1 EP2-3L2 EP2-3L3 EP2-4L3 EP2-4L4 EP2-4L5EP2-3L1T EP2-3L2T EP2-3L3T EP2-4L3T EP2-4L4T EP2-4L5T12 12 12 12 12 12225 225 225 300 300 30053.5 53.5 53.5 40.0 40.0 40.06.57.0 7.5 7.58.0 8.50.9 0.9 0.9 0.9 0.9 0.90.64 0.64 0.64 0.48 0.48 0.48EP1 SERIESPart NumberRegularTypeHigh Carrying Current Type Nominal Voltage (Vdc) Coil Resistance (Ω±10%)Nominal Current (mA) Must Operate Voltage (Vdc max.)Must Release Voltage (Vdc min.)Nominal Operate Power (W) EP1-3L1EP1-3L2EP1-3L3EP1-4L3EP1-4L4EP1-4L5EP1-B3G1 EP1-B3G2 EP1-B3G3 EP1-B4G3 EP1-B4G4 EP1-B4G5 12 12 12 12 12 12225 225 225 300 300 30053.3 53.3 53.3 40.0 40.0 40.06.57.0 7.5 7.58.0 8.50.9 0.9 0.9 0.9 0.9 0.90.64 0.64 0.64 0.48 0.48 0.48EP2/EP1 SERIES5NUMBERING SYSTEMTYPICAL APPLICATION (H Bridge Type)MOTOR Tr1Tr2 STOP off off FORWARD on off REVERSE off onIt is necessary to take more than 100 ms intervals for on / off timing between driving Tr1 and Tr2. If the interval is less than 100 ms, an excessive current happen to flow to the relay contacts.EP2 / EP1 SERIES6TECHNICAL DATACoil Temperature Rise (EP2-3L1)Operate Time (EP2-3L1) Release time (EP2-3L1)EP2/EP1 SERIES7EP2 / EP1 SERIESPrinted on recycled paper。
DG412中文资料
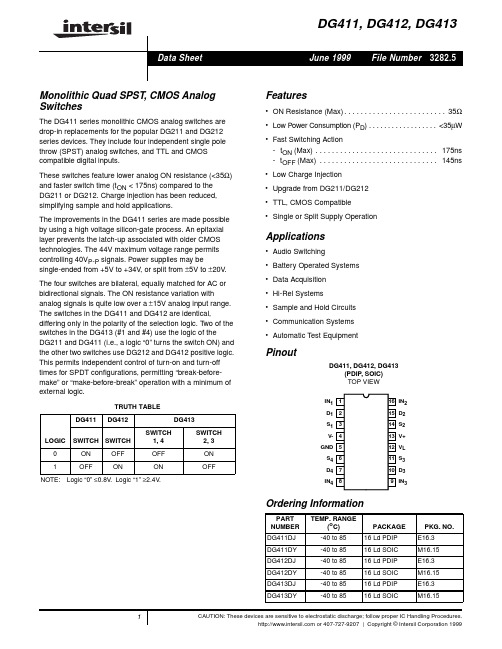
Pinout
DG411, DG412, DG413 (PDIP, SOIC) TOP VIEW
IN1 1 D1 2 S1 3 V- 4 GND 5 S4 6 D4 7 IN4 8
16 IN2 15 D2 14 S2 13 V+ 12 VL 11 S3 10 D3 9 IN3
Ordering Information
100
Maximum Junction Temperature (Plastic Packages) . . . . . . . .150oC
Maximum Storage Temperature Range . . . . . . . . . . -65oC to 150oC
Maximum Lead Temperature (Soldering 10s) . . . . . . . . . . . . 300oC
DG411
DG412
DG413
S1
S1
S1
IN1
IN1
IN1
D1
D1
D1
S2
S2
S2
IN2
IN2
IN2
D2
D2
D2
S3
S3
S3
IN3
IN3
IN3
D3
D3
D3
S4
S4
S4
IN4
IN4
IN4
D4
D4
D4
Schematic Diagram (1 Channel)
V+
VL
INX
GND V-
Pin Descriptions
Whichever Occurs First Continuous Current (Any Terminal) . . . . . . . . . . . . . . . . . . . . . 30mA Peak Current, S or D (Pulsed 1ms, 10% Duty Cycle Max) . . 100mA
J122资料

JW1221Controller for Adaptive 100/120HzCurrent Ripple Removing Circuit Parameters Subject to ChangeParameters Subject to Change Without NoticeFEATUREFEATURES SController for adaptive 100/120Hz current ripple removerBuilt-in zener diode for input voltageclampingVG output voltage high to 10VProgrammable amplitude of LED current rippleProgrammable maximum cathode voltage of LEDProgrammable maximum LED currentShort protectionOver temperature protectionSOT23-6L PackageAPPLICATIONSAPPLICATIONSLED lightingDESCRIPTIONJW1221 is a controller for driving external NMOSFET to remove the 100/120Hz LED current ripple on AC/DC power by a capacitor between VC and GND.The adaptive technology of JW1221 ensures minimum power dissipation on NMOSFET while removing LED current ripple.JW1221 clamps the input voltage on VIN pin by 30V. Only one resistor is needed when the output voltage of AC/DC power is higher than 31V.JW1221 allows user to setup maximum LED current by the sensing resistor between the source of NMOSFET and ground, which keeps NMOSFET damaged when LED short connected or hot-plug.By sensing the drain voltage of NMOSFET via a resistor between the drain and VLMT pin, JW1221 allows user to setup the maximum cathode voltage of LED string, which could help limit the power dissipation on chip.It is considered that LED is shorted when the cathode voltage of LED is higher than short connecting threshold and remains over 60us JW1221 shuts down NMOSFET when LED is shorted and recovers after 13ms.JW1221 provides over thermal protection. When the temperature of JW1221 exceed 135℃, OTP is trigged. JW1221 shuts down NMOSFET until the temperature decrease to 110℃.C o m p a n y’s L o g o i s P r o t e c t e d,“J W”a n d“J O U L W A T T”a r e R e g i s t e r e dT r a d e m a r k s o f J o u l W a t t t e c h n o l o g y I n c.TYPICAL APPLICATION TYPICAL APPLICATIONORDER INFORMATION ORDER INFORMATIONJW1221SOT23-6LJW1221Tape and reel packaging :3000 pieces/tapePIN CONFIGURATION PIN CONFIGURATIONTop ViewSOT23-6LABSOLUTE MAXIMUM RATINGVIN clamp voltage ............................. 31V VG ........................................ 20V VS, VC, VLMT ........................ -0.3V to 6V Junction Temperature2) 3)..................... 150ºCLead Temperature ......................... 260 ºC Storage Temperature ............ -65 ºC to +150 ºCRECOMMENDED OPERATIN RECOMMENDED OPERATING CONDITIONS G CONDITIONS G CONDITIONSMaximum Junction Temperature (T J )...........150ºCTHERMAL THERMAL RESISTANCE θJA JAθJ cSOT23-6L ...................... 50 ...10℃/WNote :1) Exceeding these ratings may damage the device.2) The JW1221 guarantees robust performance from -40°C to 150°C junction temperature. The junction temperature range specification is assured by design, characterization and correlation with statistical process controls.3) The JW1221 includes thermal protection that isintended to protect the device in overload conditions. Thermal protection is active when junction temperature exceeds the maximum operating junction temperature. Continuous operation over the specified absolute maximum operating junction temperature may damage the device.4) Measured on JESD51-7, 2-layer PCB.ELECTRICAL CHARATERISTICSELECTRICAL CHARATERISTICSVIN = 12V, TA = 25ºC, unless otherwise stated.VIN clamp voltage V IN_CLP29 31 33 V VIN operation current I IN5V<VIN<33V 0.24 0.3 0.58 mA VIN startup voltage threshold V THULVO15 16 17 V VIN startup voltage hysteresis V HYSUVLO 5 V Maximum VG output voltage V VG9.5 10 10.5 VVC startup current I VCST VC short to GND whenstartup0.7 0.8 0.9 mAVLMT reference voltage V VLMTR 1.95 2 2.05 VNMOSFET drain voltage limit V D_CLP Drain voltage of NMOSFETwhen voltage limit istrigged. R LIMIT=100K.3.4 44.6 VSHORT protection threshold V TH_SHORT Drain voltage of NMOSFETwhen SHORT is trigged.R LIMIT=100K.5 6 7.5 VSHORT protection delay time TSPD 60 us SHORT protection hold time TSPH 13 ms VS voltage limit V VS0.18 0.2 0.22 VPIN DESCRIPTION1 VIN Power Supply2 GND Ground3 VC LED Current Ripple Programming4 VG NMOSFET GATE driving voltage output5 VS LED current sensing input6 VLMT LED Voltage Limit and SHORT protection ProgrammingTYPICAL PERFORMANCE CHARACTERISTICS TYPICAL PERFORMANCE CHARACTERISTICSV IN = 90~264V AC , V OUT =75V, I OUT =240mA, COUT= 100µF/100V*2, TA = +25°C, unless otherwise notedPre-driver OutputSteady StateV O 20V/divILED 0.1A/div4ms/div+JW1221 OutputSteady StateEfficiency comparison(with andwithout JW1221)Open Circuit protection TestShort Circuit Protection TestContinuous poweron/off testLED Hot plug87888990919293949590110130150170190210230250E f f i c i e n c y %Vin(V)Efficiency Vs Vinwithoutwith JW1221FUNCTIONAL DESCRIPTION FUNCTIONAL DESCRIPTIONJW1221 is a controller for driving external NMOSFET to remove the 100/120Hz LED current ripple on AC/DC power.Theory of OperationThe LED string and JW1221 are both supplied by an AC/DC current source. The drain of external NMOSFET is connected to the cathode of LED string. A sensing resistor R SENSE is connected between the source of NMOSFET and GND. The gate is connected to the VG of JW1221.JW1221 drives NMOSFET to transfer the LED current ripple to voltage ripple on NMOSFET, and ensures the constant voltage across LED string and the current flow through LED string. The scalable adaptive function of JW1221 can regulate the cathode voltage of LED string to minimum to improve the efficiency of the system.Current Ripple RemovingThe capacitor C C between VC and GND is a integration capacitor. JW1221 transform the voltage on C C to a reference voltage. The current regulator regulates the voltage on R SENSE equal to the reference voltage.The relationship between the voltage on C C and R S is shown as following:V RS = I LED * R SENSE = V VC / 10C C should be large enough in order to remove the current ripple of the LED string. However, too large capacitor may slow down the dynamic response.Adaptive RegulationJW1221 control the voltage on C C by monitoring the operation state of external NMOSFET. The efficiency of system is relatively low when NMOSFET is working in the saturation region. JW1221 detects it and charges C C to raise the V VC and I LED, then the output voltage of power supply is reduced, and the voltage droponNMOSFET decreases.Conversely, when NMOSFET is working in thelinear region, LED current regulation loop is open. JW1221 detects it and discharges C C to reduce the V VC and I LED, then the output voltage of power supply is raised, and the LED current regulation loop is close.Drain Voltage of NMOSFET LimitThe voltage ripple on the drain of NMOSFET maybe very large when the current ripple is removed, which would bring large power dissipation on chip. The resistor between the drain of NOMSFET and VLMT pin can setup the limit value of drain voltage of NMOSFET.The limit threshold is calculated as below:V limit= 2V + R LMT * 20uALED Current LimitThe voltage of VS pin is limited to 0.2V internally. So the current limitation is 0.2V/R S.Current limit can protect the chip when LED is short connected or HOT-PLUG.The function of current limit is higher priority than drain voltage limit. It means that the voltage on drain of NMOSFET is not limited when LED current exceed current limit threshold.LED Short ProtectionJW1221 detect SHORT by R LMT. When the drain voltage of NMOSFET exceeds the SHORT PROTECTION THRESHOLD and the state holds for more than 60us, JW1221 considers the LED string is SHORT connected, and shut down the external MOSFET. The SHORT state is reset after 13ms.The SHORT PROTECTION THRESHOLD is calculated as:V THSCP = 2V + R LMT * 40uAOver Thermal ProtectionJW1221 monitors operation temperature. When the temperature is higher than 135℃, the NMOSFET is shut down until the temperature decrease to 115℃.PCB Design Guideline1. The bypass capacitor of VIN shouldbe placed as close as possible to the VIN pinand GND pin of IC.2. JW1221 should be placed far away from thepower devices such as MOSFET and SBD.3. The area of LED current loop should be assmall as possible.APPLICATION NOTE APPLICATION NOTEJW1221 design guide:1. Because of the 30V zener integrated andthe 4.6V V IN start threshold, the value of R VIN may satisfy the following conditions:ܴூே<ܸி−4.6ܸ0.5݉ܣV F : the voltage of LED2. The maximum voltage of VS pin is 2V inorder to limit the maximum output current especially in the short circuit condition. The value of R S can be calculated as below:ܴௌ<0.2ܸܫாI LED : the output current of the pre-driver 3. When the voltage of LED- reaches V SCPwhich is set by the R LMT , JW1221 pulls down the VIN then turns off the MOSFET. In order to ensure nothing will be damaged in the short circuit condition, the value of R LMT must satisfy the following conditions:ܸை−ܸி<ܸௌ<ܸிܸௌ<ܸூேௌ்ோ்=ܴூே∗0.5݉ܣ+4.6ܸܸௌ=2ܸ+40ݑܣ∗ܴெ்V OVP : the output voltage when thepre-driver is open.V SCP : the threshold of JW1221 shortcircuit protection.V INSTART : the output voltage of the pre-driverwhen the VIN of JW1221 is 4.6V. 4. The value of the capacitor between VC andGND can determine the final amplitude of the current ripple. It should be large enough in order to remove the current ripple of the LED string. However, too large capacitor may slow down the dynamic response. In normal condition, 1uF or 2.2uF is relatively reasonable.5. To ensure JW1221 work properly, the R DSONof MOSFET must be less than 3R S . The MOSFET will endure a large power shorting the output on the moment, so theappropriate package and R DSON of the MOSFET is necessary.6. When short the LED, there is an overshooton the drain of the MOSFET. Thebreakdown voltage of the MOSFET must be higher than V OVP . A diode connected to LED+&LED- can reduce the overshoot when short.R EFERENCE DESIGN EFERENCE DESIGN Reference:V IN: 90~260VACV OUT: 75VI OUT: 240mAPF: >0.9Current ripple: <5%PACKAGE OUTLINE PACKAGE OUTLINE。
塑料原材料牌号及用途明细表

塑料原材料牌号及用途明细表塑料原料牌号及应用通用塑料低密度聚乙烯 LDPE 型号产地熔指g/10min特性及用途LDPE-普通膜类LD100AC LD100 燕山石化 1.7-2.3用于农膜、收缩膜、透明膜、层压膜、共挤出多层膜及医用包装、各种包装袋、LLDPE的掺混料、注塑料;可用硅烷、过氧化物进行交联,用于动力电缆绝缘LD155 燕山石化 1.7-2 一般用途包装膜LD662 燕山石化1.9 适用于农膜、收缩膜、透明膜、层压膜、共挤出多层膜及医用包装、各种包装袋和LLDPE的掺混料LD600 燕山石化 2 适用于农膜、收缩膜、透明膜、层压膜、共挤出多层膜及医用包装、各种包装袋和LLDPE的掺混料LD617 燕山石化 2 适用于农膜、收缩膜、透明膜、层压膜、共挤出多层膜及医用包装、各种包装袋和LLDPE的掺混料LD160LD160AS燕山石化3-5 适用于衬里、透明膜、层压膜、超薄膜、铸膜、各种包装袋及注塑LD160BW 燕山石化 2 掺混,用于通用膜产品2102TN26 齐鲁石化2.1-2.9 通用膜料,适用于制作轻包装膜、农地膜等2436H 大庆石化 2 高透明薄膜、复合薄膜2426H 中海/扬巴大庆/兰化2 含爽滑剂、开口剂,可用作层压膜、深冷包装膜及购物袋等日用包装农用薄膜(棚膜)2426K 中海/扬巴大庆/兰化4 含爽滑剂、开口剂,可用作日用包装3026H扬巴大庆/兰化1.7-2.2 用于收缩薄膜、层压膜FD0274 卡塔尔 2.4 具有优秀的光泽度,用于生产低中强度的挤出膜,含有爽滑剂和开口剂。
LDPE-透明膜类LD104 燕山石化1.7-2.3 用于收缩膜、透明膜、层压膜、共挤出多层膜及购物袋、包装袋、医用包装并可用硅烷交联作动力电缆绝缘LD105 燕山石化 2 在LD104基础上改进。
用于收缩膜、透明膜、层压膜、共挤出多层膜及购物袋、包装袋、医用包装并可用硅烷交联作动力电缆绝缘QLT-04 齐鲁石化 2.4-3.6 高透明包装膜Q281 上海石化 2.8 用于吹塑、高透明轻膜5320 韩国韩华 2 用于薄膜、轻包装膜F222 日本宇部 2 用于一般包装薄膜、复合膜、冷冻膜200GG 马来西亚 2 用于一般包装用膜F210-6 新加坡TPC2 用于一般包装薄膜.530G 韩国三星 2.8 用于一般用途包装膜、收缩膜、农膜FD0474 卡塔尔 4 高透明度包装膜展示膜,洗涤膜,透明度优异,优异的加工性及延展性FB3000 韩国LG 3 用于一般包装用薄膜LDPE-收缩膜/重包装膜类LD163 燕山石化0.3 用于收缩膜LD165 燕山石化0.23-0.43 用于大棚膜、收缩膜及衬里、用硅烷交联动力电缆绝缘、通讯电缆外套、吹塑、管材LD150 燕山石化0.6-0.9 用于农膜、收缩膜、重包装膜、层压膜、共挤出多层膜及购物袋、冷冻袋、包装袋和用硅烷交联的动力电缆绝缘2100TN00 齐鲁石化0.25-0.3 用于重包装膜、收缩膜、大棚膜及电缆料2420D 中海/扬巴大庆/兰化0.3 用于小型吹塑、农膜、重包装1810D 扬巴/茂名大庆/兰化0.2-0.5 用于管道涂覆、电缆料、内衬、农膜、重载膜和重载收缩膜等1810E 大庆石化0.5 重包装、收缩、吹塑2423D 大庆石化0.3 重包装、农用薄膜2420F 中海/扬巴大庆/兰化0.7 用于小型吹塑、日用包装2426F 中海/扬巴大庆/兰化0.7 含爽滑剂、开口剂,可用作日用包装3020D 扬巴0.15-0.35 用于收缩膜、层压膜FB0300 韩国LG0.3 用于重包装膜FB3003 卡塔尔0.3 用于生产重包装膜,不含任何添加剂LDPE-注塑及薄膜类18D18D0大庆石化 1.5 适用于各种薄膜及小型制品1I2A 燕山石化 2 注塑级,可用作管材,板材,吹塑2420H 中海/扬巴大庆/兰化2 注塑级,用作日用包装2420K 中海/扬巴大庆/兰化4 注塑级,用作日用包装3025K 大庆石化 2 薄膜、复合薄膜1810H 扬-巴 1.3-1.8 注塑级,用作医药包装及表面保护膜1816H 扬-巴 1.3-1.8 注塑级,用作内衬2420H 中海/扬巴大庆/兰化1.7-2.2 注塑级,用作收缩薄膜、层压膜及购物袋3020H 中海/扬巴大庆/兰化1.7-2.2 注塑级,用作收缩薄膜、层压膜、表面保护膜及管道涂覆、医药包装3020K 中海/扬巴大庆/兰化3.4-4.6 注塑级,用作收缩薄膜、层压膜、表面保护膜及医药包装3026K 中海/扬巴大庆/兰化3.4-4.6 注塑级,用作收缩薄膜、层压膜及医药包装2420K 中海/扬巴大庆/兰化3.4-4.6 注塑级,用作收缩薄膜EB-853/72 巴西OPP 2.7 注塑级,一般包装用薄膜LDPE-高熔指注塑类LD615 燕山石化12-18 用于注塑、母料基料1810S 中海/扬巴大庆/兰化17-22 用于注塑2410T 中海/扬巴大庆/兰化33-39 用于注塑2410T 中海壳牌大庆石化36 用于注塑1I50A 燕山石化50 用于人造花、盆景LD400 燕山石化20-30 冰箱食品搁架、公路、铁路护栏粉末涂料原料、母粒用载体树脂MG70 卡塔尔70 具有优异的流动性和加工性,用于注塑生产及色母料制做LDPE-发泡类1F7B 燕山石化7 用于生产各种薄膜、农地膜、水果网套、母料基料LD605 燕山石化 4.5-7.5 用于发泡、注塑及薄膜LD607/608 燕山石化5-7 用于发泡、注塑及薄膜15803 俄罗斯2-2.5 用于壁厚为3mm以上的大型制品,如10升以上的容器和一般用途的薄膜及发泡产品10803 俄罗斯2-2.5 用于棚膜、小型注塑产品、发泡产品LDPE-电缆料类2102-TN00 齐鲁石化 2.1-2.9 适用于制作轻包装膜、发泡片材、电线电缆.LD100BW/LD200BW燕山石化 2.2 用于电缆料18E 大庆石化 1.8 用于电缆或发泡DJ210 上海石化 2.1 挤出级,用作交联电缆料DJ200A 上海石化 2 注塑级,用作交联电缆料2210H 大庆石化 2 中压电缆绝缘料2220H 扬-巴 1.8-2.2 注塑级,用作电缆料LDPE-涂层类1C10A 燕山石化10 用于涂层、编织袋及牛皮纸的涂覆等1C7A 燕山石化7 用于涂层、纺织袋的涂覆等1C7A-1 燕山石化7.2 可用于食品、药品以及液体无菌包装等领域。
BLM15HG102SN1D中文资料
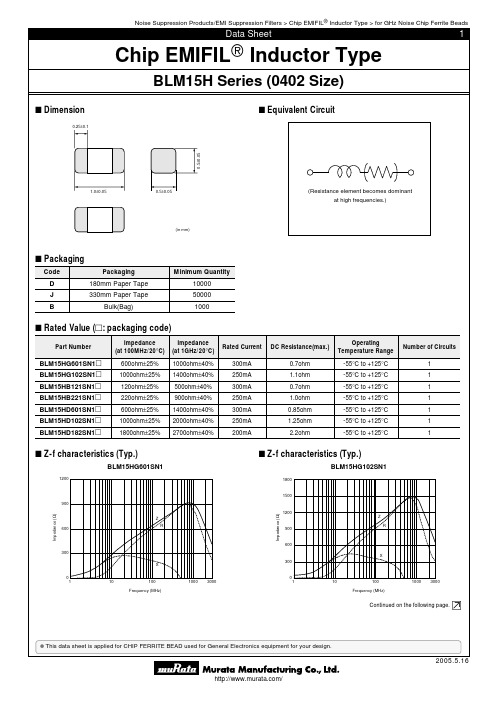
BLM15H Series (0402 Size)
I Dimension
0.25±0.1
I Equivalent Circuit
0.5±0.05
1.0±0.05
0.5±0.05
(Resistance element becomes dominant at high frequencies.)
(in mm)
800
400
0 1
Z R
X
10
100
Frequency (MHz)
1000 3000
I Z-f characteristics (Typ.)
BLM15HD182SN1
4000
I Z-f characteristics (Typ.)
BLM15HD102SN1
2500
2000
Impedance (Ω)
1500 1000
500
Z R
X
0
1
10
100
Frequency (MHz)
1000 3000
Impedance (Ω)
3000 2000 1000
Z R
X
0
1
10
100
1000 3000
Frequency (MHz)
I !Caution/Notice
!Caution (Rating) Do not use products beyond the rated current and rated voltage as this may create excessive heat and deteriorate the insulation resistance.
300mA 250mA 300mA 250mA 300mA 250mA 200mA
GT50J122中文资料
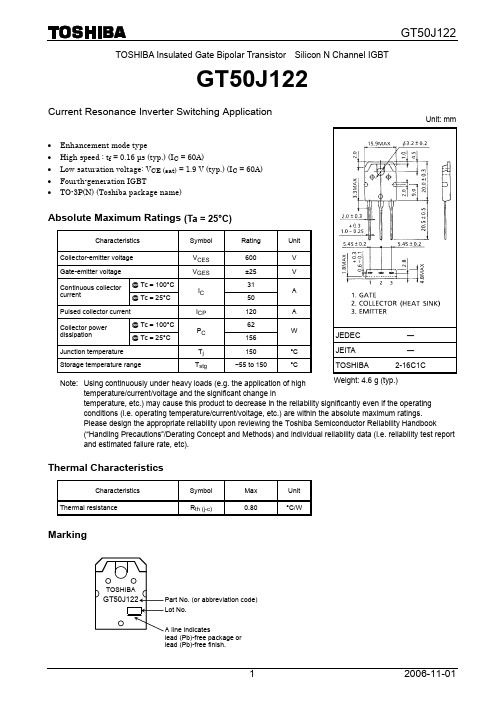
TOSHIBA Insulated Gate Bipolar Transistor Silicon N Channel IGBTGT50J122Current Resonance Inverter Switching Application• Enhancement mode type• High speed : t f = 0.16 μs (typ.) (I C = 60A)• Low saturation voltage: V CE (sat) = 1.9 V (typ.) (I C = 60A) • Fourth-generation IGBT• TO-3P(N) (Toshiba package name)Absolute Maximum Ratings (Ta = 25°C)Characteristics Symbol Rating UnitCollector-emitter voltage V CES600 VGate-emitter voltage V GES±25 V @ Tc = 100°C 31 Continuous collectorcurrent@ Tc = 25°CI C50APulsed collector current I CP 120 A @ Tc = 100°C 62 Collector power dissipation@ Tc = 25°CP C 156WJunction temperature T j 150 °C Storage temperature rangeT stg−55 to 150°CNote: Using continuously under heavy loads (e.g. the application of hightemperature/current/voltage and the significant change intemperature, etc.) may cause this product to decrease in the reliability significantly even if the operating conditions (i.e. operating temperature/current/voltage, etc.) are within the absolute maximum ratings. Please design the appropriate reliability upon reviewing the Toshiba Semiconductor Reliability Handbook(“Handling Precautions”/Derating Concept and Methods) and individual reliability data (i.e. reliability test report and estimated failure rate, etc).Thermal CharacteristicsCharacteristics Symbol Max UnitThermal resistanceR th (j-c) 0.80 °C/WMarkingUnit: mmJEDEC ― JEITA ―TOSHIBA 2-16C1CWeight: 4.6 g (typ.)lead (Pb)-free package orElectrical Characteristics (Ta = 25°C)Characteristics Symbol Test Condition Min Typ. Max UnitGate leakage current I GES V GE = ±25 V, V CE = 0 ― ― ±500nACollector cut-off current I CES V CE = 600 V, V GE = 0 ― ― 1.0 mA Gate-emitter cut-off voltage V GE (OFF) I C = 60 mA, V CE = 5 V 3.0― 6.0 VCollector-emitter saturation voltage V CE (sat) I C = 60 A, V GE = 15 V― 1.9 2.5 V Input capacitanceC ies V CE = 10 V, V GE = 0, f = 1 MHz ― 4800 ― pFRise timet r ― 0.17 ― Turn-on time t on ― 0.23―Fall time t f ―0.16 0.26Switching timeTurn-off timet offResistive Load V CC = 300 V, I C = 60 A V GG = ±15 V, R G = 30 Ω(Note 1)― 0.41 ―μs Note 1: Switching time measurement circuit and input/output waveformsC o l l e c t o r -e m i t t e r s a t u r a t i o n v o l t a g e V C E (s a t ) (V )C o ll e c t o r c u r r e n tI C (A )Collector-emitter voltage V CE (V) I C – V CEC o l l e c t or c u r r e n t I C (A )Collector-emitter voltage V CE (V)I C – V CEC o ll e c t o r c u r r e nt I C (A )Collector-emitter voltage V CE (V) I C – V CEC ol l ec t o r c u r r e n tI C (A)Gate-emitter voltageVGE (V)IC – V GECase temperature Tc (°C)V CE (sat) – TcC o l l e c t o r -e m i t t e r v o l t a g e V C E (V)S w i t ch i n g t i m e (μs )Switching Time – I CCollector currentIC (A)S w i t c h in g t i m e (μs )Collector-emitter voltage V CE (V)C – VCEC a p a c i t a n c e C (p F )G a t e -e m i t t e rv o l t a g eV G E(V )Gate charge Q G (nC)V CE, V GE – Q GSafe Operating AreaGate resistance R G (Ω)Switching Time – R GCo l l e c t o r c u r r e n t I C (A )Collector-emitter voltage V CE (V)Reverse Bias SOA0.0110 100 1000C o l l e c t o r c u r r e n t I C (A )Collector-emitter voltage V CE(V)Case temperature Tc (°C)I C max – TcM a x i m u m D C c o l l ec t o r c ur r e nt I C m a x (A )r th (t) – t wPulse width t w (s)T r a n s i e n t t h e r m a l i m p e d a n c e r t h (t ) (°C /W )RESTRICTIONS ON PRODUCT USE20070701-EN •The information contained herein is subject to change without notice.•TOSHIBA is continually working to improve the quality and reliability of its products. Nevertheless, semiconductor devices in general can malfunction or fail due to their inherent electrical sensitivity and vulnerability to physical stress. It is the responsibility of the buyer, when utilizing TOSHIBA products, to comply with the standards of safety in making a safe design for the entire system, and to avoid situations in which a malfunction or failure of such TOSHIBA products could cause loss of human life, bodily injury or damage to property.In developing your designs, please ensure that TOSHIBA products are used within specified operating ranges as set forth in the most recent TOSHIBA products specifications. Also, please keep in mind the precautions and conditions set forth in the “Handling Guide for Semiconductor Devices,” or “TOSHIBA Semiconductor Reliability Handbook” etc.• The TOSHIBA products listed in this document are intended for usage in general electronics applications (computer, personal equipment, office equipment, measuring equipment, industrial robotics, domestic appliances, etc.).These TOSHIBA products are neither intended nor warranted for usage in equipment that requires extraordinarily high quality and/or reliability or a malfunction or failure of which may cause loss of human life or bodily injury (“Unintended Usage”). Unintended Usage include atomic energy control instruments, airplane or spaceship instruments, transportation instruments, traffic signal instruments, combustion control instruments, medical instruments, all types of safety devices, etc.. Unintended Usage of TOSHIBA products listed in his document shall be made at the customer’s own risk.•The products described in this document shall not be used or embedded to any downstream products of which manufacture, use and/or sale are prohibited under any applicable laws and regulations.• The information contained herein is presented only as a guide for the applications of our products. No responsibility is assumed by TOSHIBA for any infringements of patents or other rights of the third parties which may result from its use. No license is granted by implication or otherwise under any patents or other rights of TOSHIBA or the third parties.• Please contact your sales representative for product-by-product details in this document regarding RoHS compatibility. Please use these products in this document in compliance with all applicable laws and regulations that regulate the inclusion or use of controlled substances. Toshiba assumes no liability for damage or losses occurring as a result of noncompliance with applicable laws and regulations.。
CEI122-2R1MC中文资料
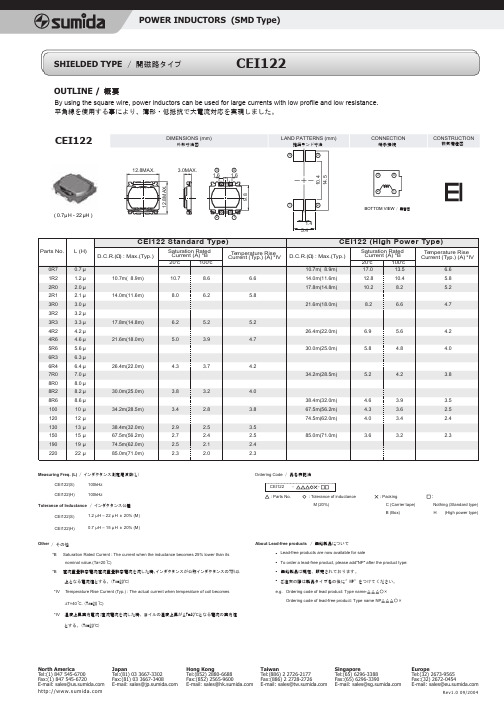
OUTLINE /CEI1221.2µH – 22µH ± 20% (M)0.7µH – 15µH ± 20% (M)/ その他Other *IV Temperature Rise Current (Typ.) : The actual current when temperature of coil becomes∆T=40°C. (Ta=20*IV温度上昇実力電流:直流電流を流した時、コイルの温度上昇がΔT=40℃となる電流の実力値°C)°C)nominal value.(Ta=20 とする。
(Ta=20℃)*B 直流重畳許容電流:直流重畳許容電流を流した時、インダクタンスが公称インダクタンスの75%以*B Saturation Rated Current : The current when the inductance becomes 25% lower than its上となる電流値とする。
(Ta=20℃)( 0.7µH - 22µH )概要By using the square wire, power inductors can be used for large currents with low profile and low resistance.平角線を使用する事により、薄形・低抵抗で大電流対応を実現しました。
/ インダクタンス公差/ インダクタンス測定周波数(L)100kHz 100kHzMeasuring Freq. (L)Tolerance of Inductance CEI122(S)CEI122(H)CEI122(S)/ 無鉛製品についてAbout Lead-free products .Lead-free products are now available for sale.To order a lead-free product, please add"NP" after the product type:無鉛製品は現在、販売されております。
S-T111B19MC-OGETFG,S-T111B20MC-OGFTFG,S-T111B21MC-OGGTFG,S-T111B22MC-OGHTFG, 规格书,Datasheet 资料

S-T111 SeriesHIGH RIPPLE-REJECTION LOW DROPOUT CMOS VOLTAGE REGULATOR© Seiko Instruments Inc., 2003-2010Rev.3.0_00 The S-T111 Series is a positive voltage regulator with a low dropout voltage, high output voltage accuracy, and low current consumption developed based on CMOS technology.A built-in low on-resistance transistor provides a low dropout voltage and large output current, and a built-in overcurrent protector prevents the load current from exceeding the current capacitance of the output transistor. An ON/OFF circuit ensures a long battery life. Compared with the voltage regulators using the conventional CMOS process, a larger variety of capacitors are available, including small ceramic capacitors. A small SOT-23-5 package realizes high-density mounting.Features• Output voltage: 1.5 V to 5.5 V, selectable in 0.1 V steps.• High-accuracy output voltage: ±1.0%• Low dropout voltage: 190 mV typ. (3.0 V output product, I OUT = 100 mA)• Low current consumption: During operation: 50 μA typ., 90 μA max.During shutdown: 0.1 μA typ., 1.0 μA max.• High peak current capability: 150 mA output is possible (at V IN ≥ V OUT(S) + 1.0 V)*1• Built-in ON/OFF circuit: Ensures long battery life.• Low ESR capacitor can be used: A ceramic capacitor of 0.1 μF or more can be used for the outputcapacitor.• High ripple rejection: 80 dB typ. (at 1.0 kHz)• Built-in overcurrent protector: Overcurrent of output transistor can be restricted.• Lead-free, Sn 100%, halogen-free*2*1. Attention should be paid to the power dissipation of the package when the output current is large.*2. Refer to “ Product Name Structure” for details.Applications• Power supply for battery-powered devices• Power supply for personal communication devices• Power supply for home electric/electronic appliances• Power supply for cellular phonesPackage• SOT-23-5S-T111 SeriesRev.3.0_00Seiko Instruments Inc.2 Block DiagramVIN VSSVOUTON/OFF *1. Parasitic diodeFigure 1Rev.3.0_00 S-T111 SeriesProduct Name Structure• The product types and output voltage for the S-T111 Series can be selected at the user’s request.Refer to the “1. Product Name ” for the construction of the product name, “2. Package ” regarding the package drawings and “3. Product Name List ” for the full product names.1. Product namewhen the output voltage is 1.5 V, *1SOT-23-5*2*3A: ON/OFF pin negative logic B: ON/OFF pin positive logic*1. Refer to the tape specifications at the end of this book. *2. Refer to the product name list.*3. Refer to 3. Shutdown (ON/OFF pin) in the “ Operation ”.2. PackageDrawing CodePackage NamePackage Tape ReelSOT-23-5 MP005-A-P-SD MP005-A-C-SD MP005-A-R-SDS-T111 SeriesRev.3.0_00Seiko Instruments Inc.4 3. Product name listTable 1Output Voltage Product Name1.5V±1.0%S-T111B15MC-OGATFx 1.6V±1.0%S-T111B16MC-OGBTFx 1.7V±1.0%S-T111B17MC-OGCTFx 1.8V±1.0%S-T111B18MC-OGDTFx 1.9V±1.0%S-T111B19MC-OGETFx 2.0V±1.0%S-T111B20MC-OGFTFx 2.1V±1.0%S-T111B21MC-OGGTFx 2.2V±1.0%S-T111B22MC-OGHTFx 2.3V±1.0%S-T111B23MC-OGITFx 2.4V±1.0%S-T111B24MC-OGJTFx 2.5V±1.0%S-T111B25MC-OGKTFx 2.6V±1.0%S-T111B26MC-OGLTFx 2.7V±1.0%S-T111B27MC-OGMTFx 2.8V±1.0%S-T111B28MC-OGNTFx 2.9V±1.0%S-T111B29MC-OGOTFx 3.0V±1.0%S-T111B30MC-OGPTFx 3.1V±1.0%S-T111B31MC-OGQTFx 3.2V±1.0%S-T111B32MC-OGRTFx 3.3V±1.0%S-T111B33MC-OGSTFx 3.4V±1.0%S-T111B34MC-OGTTFx 3.5V±1.0%S-T111B35MC-OGUTFx 3.6V±1.0%S-T111B36MC-OGVTFx 3.7V±1.0%S-T111B37MC-OGWTFx 3.8V±1.0%S-T111B38MC-OGXTFx 3.9V±1.0%S-T111B39MC-OGYTFx 4.0V±1.0%S-T111B40MC-OGZTFx 4.1V±1.0%S-T111B41MC-OHATFx 4.2V±1.0%S-T111B42MC-OHBTFx 4.3V±1.0%S-T111B43MC-OHCTFx 4.4V±1.0%S-T111B44MC-OHDTFx 4.5V±1.0%S-T111B45MC-OHETFx 4.6V±1.0%S-T111B46MC-OHFTFx 4.7V±1.0%S-T111B47MC-OHGTFx 4.8V±1.0%S-T111B48MC-OHHTFx 4.9V±1.0%S-T111B49MC-OHITFx 5.0V±1.0%S-T111B50MC-OHJTFx 5.1V±1.0%S-T111B51MC-OHKTFx 5.2V±1.0%S-T111B52MC-OHLTFx 5.3V±1.0%S-T111B53MC-OHMTFx 5.4V±1.0%S-T111B54MC-OHNTFx 5.5V±1.0%S-T111B55MC-OHOTFx Remark 1. Please contact our sales office for products with type A. 2. x: G or U 3. Please select products of environmental code = U for Sn 100%, halogen-free products.Rev.3.0_00 S-T111 SeriesPin ConfigurationTable 2Pin No. Symbol Description1 ON/OFF Shutdown pin2 VSS GNDpin3 NC *1No connection 4 VOUT Output voltage pin 5 VIN Input voltage pin*1. The NC pin is electrically open. The NC pin can be connected to VIN or VSS.5 4 1 3 2SOT-23-5Top viewFigure 2Absolute Maximum RatingsTable 3(Ta = 25°C unless otherwise specified)ItemSymbol Absolute Maximum Rating UnitV IN V SS − 0.3 to V SS + 7V Input voltage V ON/OFF V SS − 0.3 to V IN + 0.3V Output voltage V OUT V SS − 0.3 to V IN + 0.3V 300 (When not mounted on board) mWPower dissipationP D600*1mW Operating ambient temperature T opr −40 to +85 °C Storage temperature T stg −40 to +125 °C*1. When mounted on board[Mounted board](1) Board size : 114.3 mm × 76.2 mm × t1.6 mm (2) Board name : JEDEC STANDARD51-7Caution The absolute maximum ratings are rated values exceeding which the product could sufferphysical damage. These values must therefore not be exceeded under any conditions.P o w e r D i s s i p a t i o n (P D ) [m W ]Figure 3 Power Dissipation of Package (When Mounted on Board)S-T111 SeriesRev.3.0_00Seiko Instruments Inc. 6Electrical CharacteristicsTable 4*1. V OUT(S): Specified output voltageV OUT(E): Actual output voltage at the fixed load The output voltage when fixing I OUT (= 30 mA) and inputting V OUT(S) + 1.0 V*2. The output current at which the output voltage becomes 95% of V OUT(E) after gradually increasing the output current. *3. V drop = V IN1 − (V OUT3 × 0.98) V OUT3 is the output voltage when V IN = V OUT(S) + 1.0 V and I OUT = 50 mA or I OUT = 100 mA.V IN1 is the input voltage at which the output voltage becomes 98% of V OUT3 after gradually decreasing the input voltage.*4. The change in temperature [mV/°C] is calculated using the following equation.1000]C /ppm [V Ta V ]V [V ]C /mV [Ta V OUT OUT )S (OUT OUT ÷°•ΔΔ×=°ΔΔ*3*2*1*1. The change in temperature of the output voltage *2. Specified output voltage*3. Output voltage temperature coefficient*5. The output current can be at least this value.Due to restrictions on the package power dissipation, this value may not be satisfied. Attention should be paid to the power dissipation of the package when the output current is large. This specification is guaranteed by design.Rev.3.0_00 S-T111 SeriesTest Circuits1.Figure 42.Figure 53.Figure 64.LFigure 75.LFigure 8S-T111 SeriesRev.3.0_00Seiko Instruments Inc.8 Standard Circuit*1. C IN is a capacitor for stabilizing the input. *2. A ceramic capacitor of 0.1 μF or more can be used for C L .Figure 9Caution The above connection diagram and constant will not guarantee successful operation.Perform thorough evaluation using the actual application to set the constant.Application ConditionsInput capacitor (C IN ): 0.1 μF or more Output capacitor (C L ): 0.1 μF or more ESR of output capacitor: 10 Ω or lessCaution A general series regulator may oscillate, depending on the external components selected.Check that no oscillation occurs with the application using the above capacitor.Selection of Input and Output Capacitors (C IN , C L )The S-T111 Series requires an output capacitor between the VOUT and VSS pins for phase compensation. Operation is stabilized by a ceramic capacitor with an output capacitance of 0.1 μF or more in the entire temperature range. However, when using an OS capacitor, tantalum capacitor, or aluminum electrolytic capacitor, a ceramic capacitor with a capacitance of 0.1 μF or more and an ESR of 10 Ω or less is required. The value of the output overshoot or undershoot transient response varies depending on the value of the output capacitor. The required capacitance of the input capacitor differs depending on the application.The recommended value for an application is 1.0 μF or more for C IN and 0.47 μF or more for C L ; however, when selecting the output capacitor, perform sufficient evaluation, including evaluation of temperature characteristics, on the actual device.Rev.3.0_00 S-T111 SeriesExplanation of Terms1. Low dropout voltage regulatorThe low dropout voltage regulator is a voltage regulator whose dropout voltage is low due to its built-inlow on-resistance transistor. 2. Low ESRA capacitor whose ESR (Equivalent Series Resistance) is low. The S-T111 Series enables use of a low ESR capacitor, such as a ceramic capacitor, for the output-side capacitor C L . A capacitor whose ESR is 10 Ω or less can be used. 3. Output voltage (V OUT )The accuracy of the output voltage is ensured at ±1.0% under the specified conditions of fixed input voltage *1, fixed output current, and fixed temperature. *1. Differs depending on the product.Caution If the above conditions change, the output voltage value may vary and exceed theaccuracy range of the output voltage. Please see the “Electrical Characteristics” and attached characteristics data for details. 4. Line Regulation ⎟⎟⎠⎞⎜⎜⎝⎛•OUTIN OUT1V ΔV ΔV Indicates the dependency of the output voltage on the input voltage. That is, the values show how much the output voltage changes due to a change in the input voltage with the output current remaining unchanged.5. Load regulation (ΔV OUT2)Indicates the dependency of the output voltage on the output current. That is, the values show how much the output voltage changes due to a change in the output current with the input voltage remaining unchanged.6. Dropout voltage (V drop )Indicates the difference between the input voltage V IN1, which is the input voltage (V IN ) at the point where the output voltage has fallen to 98% of the output voltage value V OUT3 after V IN was gradually decreased from V IN = V OUT(S) + 1.0 V, and the output voltage at that point (V OUT3 × 0.98). V drop = V IN1 − (V OUT3 × 0.98)S-T111 SeriesRev.3.0_00Seiko Instruments Inc.10 7. Temperature Coefficient of Output Voltage ⎟⎟⎠⎞⎜⎜⎝⎛•OUTOUTV ΔTa ΔV The shadowed area in Figure 10 is the range where V OUT varies in the operating temperature range when the temperature coefficient of the output voltage is ±100 ppm/°C.V OUT(E)*1Ex. S-T111B28 Typ.−40 25 °CV OUT *1. V OUT(E) is the value of the output voltage measured at 25°C.85 Ta [°C]°CFigure 10A change in the temperature of the output voltage [mV/°C] is calculated using the following equation. [][][]1000C ppm/V Ta V V V C mV/TaVOUTOUTOUT(S)OUT÷°•ΔΔ×=°ΔΔ3*2**1*1. Change in temperature of output voltage *2. Specified output voltage*3. Output voltage temperature coefficientRev.3.0_00S-T111 SeriesOperation1. Basic operationFigure 11 shows the block diagram of the S-T111 Series.The error amplifier compares the reference voltage (V ref) with V fb, which is the output voltage resistance-divided by feedback resistors R s and R f.It supplies the output transistor with the gate voltage necessary to ensure a certain output voltage free of any fluctuations of input voltage and temperature.*1.Parasitic diodeFigure 112. Output transistorThe S-T111 Series uses a low on-resistance P-channel MOS FET as the output transistor.Be sure that V OUT does not exceed V IN + 0.3 V to prevent the voltage regulator from being damaged due to inverse current flowing from the VOUT pin through a parasitic diode to the VIN pin.S-T111 SeriesRev.3.0_00Seiko Instruments Inc.12 3. Shutdown pin (ON/OFF pin) This pin starts and stops the regulator.When the ON/OFF pin is set to the shutdown level, the operation of all internal circuits stops, and the built-in P-channel MOS FET output transistor between the VIN pin and VOUT pin is turned off to substantiallyreduce the current consumption. The VOUT pin becomes the V SS level due to the internally divided resistance of several M Ω between the VOUT pin and VSS pin.The structure of the ON/OFF pin is as shown in Figure 12. Since the ON/OFF pin is neither pulled down nor pulled up internally, do not use it in the floating state. In addition, note that the current consumption increases if a voltage of 0.3 V to V IN – 0.3 V is applied to the ON/OFF pin. When the ON/OFF pin is not used, connect it to the VSS pin if the logic type is “A” and to the VIN pin if it is “B”.Table 5Logic TypeON/OFF Pin Internal Circuits VOUT Pin VoltageCurrent ConsumptionA “L”: Power on Operating Set value I SS1 A “H”: Power off Stopped V SS level ISS2 B “L”: Power off Stopped V SS level I SS2 B “H”: Power onOperatingSet valueI SS1VINFigure 12Rev.3.0_00S-T111 SeriesPrecautions•Wiring patterns for the VIN, VOUT and GND pins should be designed so that the impedance is low.When mounting an output capacitor between the VOUT and VSS pins (C L) and a capacitor for stabilizing the input between VIN and VSS pins (C IN), the distance from the capacitors to these pins should be as short as possible.•Note that the output voltage may increase when a series regulator is used at low load current (1.0 mA or less).•Generally a series regulator may cause oscillation, depending on the selection of external parts. The following conditions are recommended for this IC. However, be sure to perform sufficient evaluation under the actual usage conditions for selection, including evaluation of temperature characteristics.Input capacitor (C IN): 1.0μF or moreOutput capacitor (C L): 0.47μF or moreEquivalent series resistance (ESR): 10 Ω or less•The voltage regulator may oscillate when the impedance of the power supply is high and the input capacitor is small or an input capacitor is not connected.•The application conditions for the input voltage, output voltage, and load current should not exceed the package power dissipation.•Do not apply an electrostatic discharge to this IC that exceeds the performance ratings of the built-in electrostatic protection circuit.•In determining the output current, attention should be paid to the output current value specified in Table4 in the “ Electrical Characteristics” and footnote *5 of the table.•SII claims no responsibility for any disputes arising out of or in connection with any infringement by products including this IC of patents owned by a third party.S-T111 SeriesRev.3.0_00Seiko Instruments Inc.14 Typical Characteristics(1) Output Voltage vs. Output current (when load current increases) S-T111B15 (Ta = 25°C)S-T111B30 (Ta = 25°C)V O U T [V ]1002003004005006001.81.61.41.21.00.80.60.40.20V O U T [V ]2003004005001006003.53.02.52.01.51.00.50I OUT [mA]I OUT [mA]S-T111B50 (Ta = 25°C)V O U T [V ]2003004001005006543210600I OUT [mA]Remark In determining the output current, attention should be paid to the following. 1) The minimum output current value and footnote *5 in the “ Electrical Characteristics ” 2) The package power dissipation(2) Output voltage vs. Input voltageS-T111B15 (Ta = 25°C)S-T111B30 (Ta = 25°C)V O U T [V ]1.61.51.41.31.21.11.0 3.53.02.52.01.51.0V O U T [V ]3.13.02.92.82.72.62.5 5.04.54.03.53.02.5V IN [V]V IN [V]S-T111B50 (Ta = 25°C)V O U T [V ]5.55.04.54.03.53.02.57.06.05.04.03.02.0V IN [V]Rev.3.0_00 S-T111 Series(3) Dropout voltage vs. Output currentS-T111B15 S-T111B30V d r o p [V ]0501001502000.450.400.350.300.250.200.150.100.050V d r o p [V ]0501001502000.450.400.350.300.250.200.150.100.050I OUT [mA]I OUT [mA]S-T111B50V d r o p [V ]050100150200I OUT [mA](4) Dropout voltage vs. Set output voltageV d r o p [V ]0.400.350.300.250.200.150.100.0507123456V OTA [V]S-T111 SeriesRev.3.0_00Seiko Instruments Inc.16(5) Output voltage vs. Ambient temperatureS-T111B15 S-T111B30V O U T [V ]1.601.551.501.451.4025–2575100–5050V O U T [V ]0 25 –50–2550751003.203.153.103.053.002.952.902.852.80Ta [°C]Ta [°C]S-T111B50V O U T [V ]100755025–25–505.35.25.15.04.94.84.7Ta [°C](6) Current consumption vs. Input voltageS-T111B15 S-T111B30I S S 1 [μA ]8642I S S 1 [μA]6 4 2 0 1201008060402008V IN [V]V IN [V]S-T111B50I S S 1 [μA ]2 4 6 8V IN [V]Rev.3.0_00 S-T111 Series(7) Ripple rejectionS-T111B15 (Ta = 25°C) S-T111B30 (Ta = 25°C) V IN = 2.5 V, C OUT = 0.47 μFV IN = 4.0 V, C OUT = 0.47 μFR i p p l e R e j e c t i o n [d B ]1001k10k100k 101M100806040200R i p p l e R e j e c t i o n [d B ]1001k10k 100k 101M100806040200Frequency [Hz]Frequency [Hz]S-T111B50 (Ta = 25°C) V IN = 6.0 V, C OUT = 0.47 μFR i p p l e R e j e c t i o n [d B ]1001k10k100k101M100806040200Frequency [Hz]S-T111 SeriesRev.3.0_00Seiko Instruments Inc.18Reference Data(1) Input transient response characteristicsS-T111B15 (Ta = 25°C)S-T111B30 (Ta = 25°C)I OUT = 30 mA, tr = tf = 5.0 μs, C OUT = 0.47 μF, C IN = 0 μF I OUT = 30 mA, tr = tf = 5.0 μs, C OUT = 0.47 μF, C IN = 0 μFV O U T [V ]1.46 4.03.53.02.52.01.51.00.50-40-20020406080100120140160V I N [V ]V O U T [V]-40-200204060801001201401606 543 2 1 0V I N [V ]t [μs]t [μs]S-T111B50 (Ta = 25°C)I OUT = 30 mA, tr = tf = 5.0 μs, C OUT = 0.47 μF, C IN = 0 μFV O U T [V ]4.968 7 6 5 4 3 2 1 0-40-20020406080100120140160V I N [V ]t [μs](2) Load transient response characteristicsS-T111B15 (Ta = 25°C)S-T111B30 (Ta = 25°C)V IN = 2.5 V, C OUT = 0.47 μF, C IN = 1.0 μF, I OUT = 50↔100 mAV IN = 4.0 V, C OUT = 0.47 μF, C IN = 1.0 μF, I OUT = 50↔100 mAV O U T [V ]020406080100120140-40-201601.40150100500 –50–100–150I O U T [m A ]V O UT [V ]20406080100120140-40-20160150100500 –50–100–150I O U T [m A ]t [μs]t [μs]S-T111B50 (Ta = 25°C)V IN = 6.0 V, C OUT = 0.47 μF, C IN = 1.0 μF, I OUT = 50↔100 mAV O U T [V]020406080100120140-40-201604.90150100500 –50–100–150I O U T [m A ]t [μs]Rev.3.0_00 S-T111 Series(3) Shutdown pin transient response characteristicsS-T111B15 (Ta = 25°C)S-T111B30 (Ta = 25°C)V IN = 2.5 V, C OUT = 0.47 μF, C IN = 1.0 μF, I OUT = 100 mAV IN = 4.0 V, C OUT = 0.47 μF, C IN = 1.0 μF, I OUT = 100 mAV O U T [V ]00.20.40.60.81.0 1.2 1.4-0.4-0.21.63 21 0 –1 –2–3543210–1V O N /O F F [V ]V O U T [V ]0.20.40.60.81.0 1.2 1.4-0.4-0.21.66 420 –2 –4–61086420–2V O N /O F F [V ]t [ms]t [ms]•The information described herein is subject to change without notice.•Seiko Instruments Inc. is not responsible for any problems caused by circuits or diagrams described herein whose related industrial properties, patents, or other rights belong to third parties. The application circuit examples explain typical applications of the products, and do not guarantee the success of any specific mass-production design.•When the products described herein are regulated products subject to the Wassenaar Arrangement or other agreements, they may not be exported without authorization from the appropriate governmental authority. •Use of the information described herein for other purposes and/or reproduction or copying without the express permission of Seiko Instruments Inc. is strictly prohibited.•T he products described herein cannot be used as part of any device or equipment affecting the human body, such as exercise equipment, medical equipment, security systems, gas equipment, or any apparatus installed in airplanes and other vehicles, without prior written permission of Seiko Instruments Inc.•T he products described herein are not designed to be radiation-proof.•A lthough Seiko Instruments Inc. exerts the greatest possible effort to ensure high quality and reliability, the failure or malfunction of semiconductor products may occur. The user of these products should therefore give thorough consideration to safety design, including redundancy, fire-prevention measures, and。
PTO1 manual
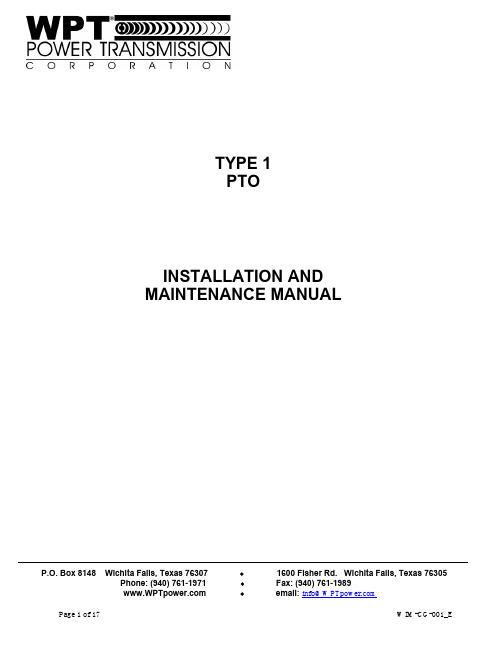
TYPE 1PTOINSTALLATION ANDMAINTENANCE MANUALP.O. Box 8148 Wichita Falls, Texas 76307 • 1600 Fisher Rd. Wichita Falls, Texas 76305 Phone: (940) 761-1971 • Fax: (940) 761-1989 • email: info@___________________________________________________________________________________________________ 1.0 INTRODUCTION1.1 The WPT Power Transmission PTO1.2 Product identification numbers1.3 Calculating required torque capacity2.0 SPECIFICATIONSdimensions2.1 Flywheel2.2 Bell housing dimensions2.3 Allowable side pullRPM2.4 Maximum3.0 MOUNTING THE SHEAVE3.1 Removing the sheave housing3.2 Removing the outboard bearing3.3 Installing the sheave3.4 Replacing the outboard bearing3.5 Replacing the sheave housing4.0 INSTALLATION4.1 Flywheel and flywheel housing alignment checks4.2 Lubrication prior to installation4.3 Mounting the PTO on the engine4.4 Installing or replacing belts5.0 OPERATION5.1 Clutch engagement procedure6.0 LUBRICATIONspecification6.1 Grease6.2 Grease specification for cold conditionsintervals6.3 Lubrication6.4 Bearing operating temperature7.0 MAINTENANCE7.1 Inspecting and adjusting the clutch7.2 Adjusting the clutch on the engine7.3 Adjusting the clutch removed from the engine8.0 DISASSEMBLY8.1 Removing the PTO from the engine8.2 Removing the sheave housing and belts8.3 Removing the outboard bearing8.4 Removing the bell housing8.5 Removing the clutch from the PTO8.6 Removing the inboard bearing9.0 ASSEMBLY9.1 Preparing the shaft9.2 Assembling the clutch9.3 Assembling the PTO9.4 Installing the sheave housing10.0 WARRANTY1.0 INTRODUCTION1.1 The WPT Power Transmission PTO is the most rugged PTO available on the market today. Follow theprocedures detailed in this Installation Maintenance Manual for years of service.1.2 When ordering parts, use the part number from the Bill of Materials supplied with this unit. Also, pleaseinclude the assembly number and the serial number from the unit itself. These will be found on a metal tag riveted to the bell housing. Your WPT Distributor can provide a copy of the Bill of Materials if the one provided should become lost.1.3 When performing installation and maintenance functions, refer to the drawing at the back of this manual.The references on the drawing in this manual DO NOT correspond to the references on the assembly drawing and Bill of Materials. Do not use the item numbers from the drawing in this manual for ordering parts.2.0 SPECIFICATIONS2.1 See Chart 3 for flywheel dimensions.2.2 See Chart 3 for flywheel housing dimensions.2.3 See Chart 4 and 5 for the allowable side pull of your PTO.2.4 The maximum RPM is listed in Chart 4 and 5 for your PTO size.3.0 MOUNTING THE SHEAVE3.1 Removing the sheave housing3.1.1 If a sheave has not been mounted, mark the shaft in the center of the distance between the bearingend caps(33)3.1.2 Remove the 6 socket head bolts (47) and 12 socket head bolts (40) holding the sheave housing tothe bearing housing and bell housing.3.1.3 Attach approved lifting eyes in the 3/4-10 NC holes in the ribs on the side of the housing if the PTOis in a horizontal position.3.1.4 Attach a pattern of lifting eyes in the ½-13 holes in the sheave housing if the PTO is in a verticalposition.3.1.5 If the housing does not separate easily, insert (2) 1/2-13 jack bolts in the end of the bell housingand tighten these evenly to move the bell housing off the bearing housing boss. The sheavehousing weighs approximately 500 lbs. for the 14” and 18” clutch and approximately 600 lbs. for the21”.3.2 Removing the outboard bearing3.2.1 Remove the 6 socket head cap screws(52) joining the bearing end caps(32) & (33) to the bearingcarrier(41).3.2.2 Slide the bearing carrier off the bearing.3.2.3 Bend the locking tab of the lockwasher(48) out of the locknut(51). Remove the locknut and washer.3.2.4 Remove the outboard seal spacer(43).3.2.5 Take precautions to keep the bearing clean. If the bearing does not slide easily off the shaft, installa bearing puller with splitter plates behind the bearing and remove it from the shaft. Do not pull onthe bearing end cap(33). The shaft has a ¾-10 thread at the bottom of the rotary coupling pocket.3.2.6 Remove the seal spacer(43).3.3 Installing the sheave3.3.1 If the key(57) is not in the shaft, install it now. Be sure it seats in the bottom of the slot.3.3.2 Measure the distance from the top of the key to the opposite side of the shaft.3.3.3 Compare this measurement to the mating dimension in the sheave or bushing and adjust the keyheight if necessary.3.3.4 Slide the sheave onto the shaft and lock in the approximate center determined in 3.1.1 above.3.4 Replacing the outboard bearingIf the outboard bearing(45) is not assembled as a unit with the bearing carrier(41), seal housings(32 & 33), and seals(36), go to section 9.3.243.4.1 Slide the seal spacer(43) onto the shaft until it seats against the shoulder.3.4.2 Install the outboard bearing(45) with its carrier(41), seal housings(32 & 33), and seals(36) onto theshaft. Use a light coating of grease on the seal ring and be careful to not damage the seal.3.4.3 Slide the remaining seal spacer(43) onto the shaft. Use a light coating of grease on the seal ringand be careful to not damage the seal.3.4.4 Install the bearing lockwasher(48) and locknut(51) tightening the nut ¼ turn past makeup or handtight. Lock the nut with one of the tabs of the lockwasher.3.4.5 If the rotary coupling(50) was removed, install it in its counterbore and lock in place with ring(49)and 4 socket head bolts(26).3.5 Replacing the sheave housing3.5.1 Refer to 9.4.14.0 INSTALLATION4.1 Flywheel and flywheel housing alignment checksIt is strongly recommended that these dial indicator checks be made prior to installation of the PTO,especially on new engines or when a previous PTO failure might indicate an alignment problem.4.1.1 Flywheel to housing face runout check. (see Figure 3)Mount the indicator base on the face of the flywheel and position the dial indicator tip perpendicularto the flywheel housing mounting face. Rotate the flywheel 360 degrees while holding pressureagainst the crankshaft thrust bearing.SAE #1 Housing: 0.012 inches (0.305 mm)SAE #1/2 Housing: 0.014 inches (0.356 mm)SAE #0 Housing: 0.016 inches (0.406 mm)SAE #00 Housing: 0.019 inches (0.483 mm)4.1.2 Check flywheel housing bore runout. (see Figure 4)Mount the indicator base on the face of the flywheel and position the dial indicator tip so itsmovement is perpendicular to the pilot bore of the flywheel housing.Rotate the flywheel through 360 degrees. The total indicator reading should not exceed:SAE #1 Housing: 0.012 inches (0.305 mm)SAE #1/2 Housing: 0.014 inches (0.356 mm)SAE #0 Housing: 0.016 inches (0.406 mm)SAE #00 Housing: 0.019 inches (0.438 mm)4.1.3 Check flywheel face runout. (see Figure 5)Mount the indicator base on the flywheel housing and position the dial indicator tip so that itsmovement is perpendicular to the face of the flywheel. Position the indicator tip near the drive ringmounting bolt circle diameter. Rotate the flywheel 360 degrees while holding pressure against thecrankshaft thrust bearing.The total indicator reading should not exceed 0.011 inches (0.279 mm)4.1.4 Check flywheel pilot bore runout. (see Figure 6)Mount the indicator base on the flywheel housing and position the dial indicator tip so its movementis perpendicular to the face of the flywheel. Rotate the flywheel through 360 degrees.The total indicator reading should not exceed 0.005 inches (0.127 mm)FIGURE 3 FIGURE 4FIGURE 5 FIGURE 64.2 Lubrication pior to installation4.2.1 The WPT PTO is lubricated at the factory with Lubriplate® 1200-2 lithium based grease.Lubrication should be “topped off” prior to being placed in service. See Section 6 for lubricationinstructions4.3 Mounting the PTO on the engineAlternate methods are described to align the friction discs.4.3.2 (Requires air supply) Use the drive ring (2) provided with the PTO or remove the drive ring from theengine flywheel to use as an alignment gauge. Place the drive ring over the friction discs. Centerthe drive ring relative to the O.D. of the clutch body. Engage the clutch with 100 psi compressed air.Be sure there is adequate hose length to reach the back of the engine.4.3.2 Remove the drive ring.4.3.3 (No Air Required) Use a long handled screwdriver or other tool to align the friction disc teeth withthe teeth of the drive ring. Use caution when installing the PTO to avoid damaging the teeth of thefriction discs4.3.4 Install the drive ring on the engine flywheel making sure that the ring is seated in the locating bore.Use SAE Grade 5 bolts (or equivalent) with lockwashers and torque to the specifications in Chart 1or to the engine manufacturers torque recommendation. Use the engine manufacturer’s torquerecommendation if different from that in Chart 1.4.3.5 Slowly draw the PTO toward the engine. This can be done by installing 3 or 4 equally spacedlengths of all-thread with nuts into the flywheel housing and tightening these while supporting theweight of the PTO with a hoist or cribbing.4.3.6 When the PTO is fully in place, remove the studs if used and replace with SAE Grade 5 bolts (orequivalent) with lockwashers and torque to the value in Chart 1. Use the engine manufacturer'storque recommendation if different from that in Chart 1.4.4 Installing or replacing beltsTo install/replace belts, the customer’s support bracket and sheave housing must be removed.4.4.1 Remove outboard support bracket4.4.2 Remove the 6 socket head bolts (47) and 12 socket head bolts (40) holding the sheave housing tothe bearing housing and bell housing.4.4.3 Attach approved lifting eyes in the ¾-10 NC holes in the ribs of the sheave housing.4.4.4 If the housing does not separate easily, insert (2) 1/2-13 jack bolts in the end of the bell housingand tighten these evenly to move the bell housing off the bearing housing boss. The sheavehousing weighs approximately 500 lbs. for the 14” and 18” clutch and approximately 600 lbs. for the 21”.4.4.5 Install/replacebelts.4.4.6 Reposition the sheave housing on the bell housing (30) and outboard bearing carrier (41).4.4.7 Align bolt holes and start socket head bolts (47). Supporting the sheave housing with cribbing orthreaded rods screwed into the bell housing will aid assembly.4.4.8 Evenly tighten socket head bolts (47) to the values from Chart 1.4.4.9 Remove threaded rods, if used, and install socket head bolts (40). Tighten to the values fromChart 1.4.4.10 Replace outboard support bracket and adjust belt tension.Check and adjust belt tension after the first several hours of operation.5.0 OPERATION5.1 Clutch engagement procedure5.1.1 Insure that hose or pipe sizes are adequate to supply the air to the clutch. Hoses or pipe size of 1/2inch should be a minimum for short runs. Use 3/4 inch size if runs are longer than 15 feet.5.1.2 Where high inertia loads must be started, engaging the clutch at idle speed may stall the engine.High inertia loads may be brought up to speed by engaging the clutch for short periods (1 second)at intervals long enough to prevent excessive heat build up in the friction discs. With extremely highloads, the engine may have to be operated at higher speeds while engaging the clutch.5.1.3 Once the load is turning with the clutch fully engaged, the engine RPM may be increased.Special air circuitry may be used to regulate clutch engagement. Consult WPT Power Transmissionfor recommended equipment.NOTE:UNDER NO CIRCUMSTANCES should the clutch be slipped for more than several secondswithout either fully engaging the clutch or completely disengaging the clutch to allow it to cool.Any excessive vibration in the PTO should be cause for investigation. All rotating parts of theWPT PTO are balanced at the factory.6.0 LUBRICATIONRe-lube before placing in service6.1 Grease specificationThe WPT PTO is lubricated at the factory with Lubriplate®1200-2, lithium base grease with an EP (extreme pressure) additive. This will serve under normal ambient conditions up to 2100 RPM at a maximum bearing temperature of 2OO deg. F. (93.3 deg. C.)6.2 Grease specification for cold conditionsFor ambient temperatures below -25 deg. F. (-32 deg. C.), Lubriplate® MAG-1 may be substituted.Grease Caution:Do not mix sodium or calcium based greases with lithium based grease.6.3 Lubrication intervals.There are only two places on the WPT PTO that require lubrication. Each is connected to the bearing cavity with the excess grease being forced out of a relief valve on the bottom of the unit. The small amount ofgrease expelled is an indication that enough grease is being provided.6.3.1 Every 75 hours of operation, add enough grease to expel a small amount from the relief valves.6.3.2 Every 300 hours of operation, flush the bearing with approximately7.5 oz. (1/2 tube).These lubrication intervals are suggested. The operator is responsible for establishing lubrication intervals according to the duty cycle and operating conditions in which the equipment is used.6.3.3 CLUTCH: No lubrication is required.6.3.4 ROTO-COUPLING (50): Normally no lubrication is required. If equipped with grease fittings or oilcups, any good bearing oil or grease can be used, but care should be taken not to over lubricate.6.4 Bearing operating temperature.Operating temperature range is normally between 170 deg. F. and 200 deg. F. (76.7 to 93.3deg. C.). Higher ambient temperatures will cause the bearings to run hotter. More frequent lubrication intervals and/orlubricant designed for higher operating temperatures will be required if the unit is to be used in thisenvironment. Consult the factory for lubricant recommendations where ambient temperatures areconsistently above 100 deg. F.(38 deg. C.)Note:Do not rely on checking bearing temperature with the hand. Acceptable bearing temperatures are normally hotter than the hand can stand for more than a second. A contact type thermometer should be used to take accurate temperature measurements.7.0 MAINTENANCEThe WPT PTO uses an air operated clutch which does not need frequent adjustment. It doeshowever, require periodic inspection to determine if friction discs and/or drive plates have worn, increasing clutch clearance. The clutch should be adjusted if the movement of the pressure plate is more than the value for that clutch found in Chart 2.7.1 Inspecting and adjusting the clutch7.1.1 Remove power (stop the engine) and tag any remote start devices.7.1.2 Remove hand hole covers.7.1.3 With a flashlight and short scale, measure the movement of the pressure plate as theclutch is engaged and disengaged. Compare this measurement to that shown in Chart 2.7.1.4 To adjust the clutch without removing the PTO from the engine, proceed to step 7.2. Toremove the PTO and rebuild the clutch, proceed to step 8.1It is good to periodically remove dirt and accumulated dust from the clutch. Wear a mask and eyeprotection while doing this. WPT friction material is asbestos free.7.2 Adjusting the clutch on the engine7.2.1 Remove the air hoses(23) connecting the shaft to the airtube.7.2.2 Remove the hose adapters(22)7.2.3 Remove the 4 socket head cap screws(19) in the airtube holding plate(17).7.2.4 Slide the airtube holding plate(17) and airtube(16) back to expose the shims(18).7.2.5 With snips or saw, cut the necessary number of shims and remove them.7.2.6 Replace the airtube and airtube holding plate. Torque the 4 socket head cap screws to thevalue from Chart 1.7.2.7 Replace fittings and hoses.7.2.8 Check clutch clearance per 7.1.3 above.7.2.9 Replace hand hole covers and remove tags from remote starting devices.7.3 Adjusting the clutch with PTO removed from engine7.3.1 See section (9.2.8)Whenever the PTO is removed from the engine, it is recommended that the hub and drive ringteeth be checked for wear. To do this, lay a straight edge along the side of the teeth. Any grooveworn .015” (.38mm) should indicate replacement of that part.Examine the friction surfaces of the center plates(12) and floating plate(13) for heat checking andsurface flatness. Flatness should be within .005” (.13mm) and the two sides of the centerplatesshould be parallel within the same amount.Most damage to WPT clutches is a result of misalignment or low operating pressure. Misalignmentwill cause premature wear of teeth (friction disc, center plates, hub and drive ring), and if extreme,may cause breakage of these parts. Low air pressure may cause the clutch to slip. Low airpressure or low air volume may cause the clutch to engage slowly. Slippage generates heat, whichif excessive, will shorten the life of friction discs, insulator plate and airtube. A clutch that issuspected of slipping should be removed from service for examination or repair.8.0 DISASSEMBLY(Refer to PTO Illustration at the back of this manual)8.1 Removing the PTO from the engine.8.1.1 Use a hoist or other suitable lifting equipment to support the weight of the power take-off.Attach lifting devices at several places or use cribbing to support the PTO in a horizontalposition during removal.Caution:The PTO weighs in excess of l000 lbs. (454 Kg.) Use approved lifting eyes and procedures to prevent accident or injury.8.1.2 Remove air hoses and other connections to the PTO8.1.3 Remove the mounting bolts between PTO and flywheel housing, removing those locatednear the top last. The PTO should separate from the flywheel housing. If the PTO doesn'tseparate, gently pry the flanges apart until the housing is removed from the engine flywheelhousing pilot diameter.8.1.4 Use care when removing the PTO from the engine to avoid damage to grease fittings,friction disc teeth, and other components.8.2 Removing the Sheave Housing and Belts.8.2.1 Place the PTO on the floor, clutch down, supported by wood blocks under the bell housing.Use adequate support to keep the PTO from tipping.8.2.2 Refer to 3.1 of this manual.8.2.3 Slide the belts off the pulley(s).8.2.4 The sheave housing, if replaced at this time, will help balance the PTO.8.3 Remove the outboard bearing8.3.1 Bend the tab out of the slot on the bearing lock nut(51) and remove the nut andwasher(48).8.3.2 Remove 6 flat head socket cap screws(52) and slide the bearing end cap(32) off of theshaft.8.3.3 Slide the seal spacer(43) off of the shaft.8.3.4 Slide the bearing carrier(41) off the bearing and off of the shaft.8.3.5 Slide the bearing off the shaft. If a puller is necessary, use splitter plates behind thebearing. Do not pull on the bearing end cap(33). The shaft is tapped ¾-10 at the bottom ofthe rotary coupling pocket.8.3.6 Remove the seal spacer(43).8.4 Removing the bell housing8.4.1 Remove 6 socket head cap screws(38) and lift the bell housing off the inboard bearingcarrier(39). If the bell housing does not lift off easily, insert jack bolts in the threaded holesprovided and tighten these evenly to separate the two.8.5 Removing the clutch from the PTO8.5.1 Position the shaft with the clutch at the top.8.5.2 Bend the tab out of the slot on the bearing lock nut(7) and remove the nut and washer.8.5.3 Remove the hoses(23) and hose adapters(22).8.5.4 Remove the set screw(21) in the clutch spacer(20) if equipped.8.5.5 Remove the 4 hex head cap screws(10) holding the backplate(3) and remove thebackplate.8.5.6 Remove the friction discs(4), pressure plates(12), springs(11), floating plate(13), insulatorplate(15) and airtube(16).8.5.7 Use a puller in the threaded holes in the hub(5) to pull the hub. The shaft has a 1-14 UNStapped hole in the end.8.5.8 Remove the clutch spacer(20).8.6 Removing the inboard bearing8.6.1 Remove the grease hoses(55) from the bearing carrier(39).8.6.2 Remove 6 flat head socket cap screws(37) and slide the bearing end cap(32) off of theshaft.8.6.3 Slide the bearing carrier(39) off of the shaft.8.6.4 Slide the seal spacer(35) off the shaft.8.6.5 Slide the bearing off the shaft. If a puller is necessary, use splitter plates behind thebearing. Do not pull on the bearing end cap(33).8.6.6 Slide the seal spacer(35) off the shaft.9.0 ASSEMBLY9.1 Preparing the shaft9.1.1 Clean the shaft. Remove all dirt or corrosion.9.1.2 Check the shaft to see that it is free of burrs.9.1.3 Inspect threads to see that there is no damage.9.1.4 Keyways should not be worn. Keys should be a snug fit in the slot.9.2 Assembling the clutchIt is easier to assemble and test the clutch outside the PTO. These instructions detail assembly inthat manner.9.2.1 Place the hub on a workbench with the back plate end up. Attach the backplate with hexhead cap screws (10).9.2.2 Invert the hub and backplate so the backplate is on the workbench.9.2.3 Attach the insulator plate(15) to the floating plate(13) with roll pins(14) if it is not alreadydone.9.2.4 Place the centerplates, friction discs and floating plate with insulator plate attached on thehub as shown in the diagram. Be sure the release springs(11) are properly seated in theircounterbores.9.2.5 Place the shims (18) on the hub.9.2.6 Insert the airtube(16) in the airtube holding plate(17) and set this assembly on the hub. Becareful not to damage the airtube or brass spuds.9.2.7 Attach the airtube holding plate using 4 socket head cap screws(19).9.2.8 Plug all but 1 spud and install fittings to connect this spud to a supply of compressed air(60 PSI minimum).9.2.9 Using compressed air, engage and disengage the clutch while measuring movement of theinsulator plate(15). Compare this value with that in Chart 2 and adjust the number ofshims(18) accordingly.9.2.10 Invert the clutch so the airtube holding plate is on the workbench.9.2.11 Remove the backplate, friction discs, center and floating plates and airtube.9.2.12 The hub with attached shims and airtube holding plate will be installed on the shaft as anassembly.9.3 Assembling the PTO9.3.1 Install the seals in the bearing end caps(36,32 & 33) and set these aside.9.3.2 Fix the shaft vertically with the clutch end up.9.3.3 Slide an inboard end cap(33) with seal over the shaft with the seal facing up.9.3.4 Slide a seal spacer(35) on the shaft until it stops against the raised diameter.9.3.5 Heat the inboard bearing(34) using an appropriate heat source and slide it on the shaft untilit seats against the seal spacer. Allow the bearing to cool.9.3.6 Slide the inboard bearing carrier(39) over the bearing.9.3.7 Slide the other inboard seal spacer(35) onto the shaft and seat it against the bearing.9.3.8 Slide the outboard bearing end cap(32) over the shaft and using thread locking compound,bolt both end caps to the bearing housing with 6 flat head socket cap screws(37). Torquethese per Chart 1.9.3.9 Slide the clutch spacer/s(21) over the shaft until it seats against the seal spacer. Rotate thisto expose the ports in the shaft and install the hose adapters(22).9.3.10 Install the hub key(9) in its slot and measure the distance from top of key to opposite sideof shaft. Compare this measurement to the corresponding measurement in the hub and fileor grind the key if necessary.9.3.11 Heat the hub with attached airtube holding plate using an appropriate heat source andinstall on the shaft. Use anti-seize compound and have equipment available to push thehub on the shaft if necessary.9.3.12 Allow the hub to cool and install the clutch components as shown in the diagram being surethe release springs(11) are properly seated in their counterbores.9.3.13 Use thread locking compound on the 4 hex head cap screws(19) holding the backplate(17)and torque these per Chart 1.9.3.14 Install air hoses(23) between shaft and airtube.9.3.15 Air test these connections before continuing.9.3.16 Install set screw(21) in clutch spacer if required.9.3.17 Install grease hoses(55) in the bearing housing(39).9.3.19 Lock the bearing nut with one of the tabs of the lockwasher.9.3.20 Invert the PTO so the sheave end is up. Be sure the shaft and clutch are adequatelysupported.9.3.21 Slide the bell housing over the shaft and install 6 socket head cap screws(38). Use threadlocking compound and torque to values from Chart 1.9.3.22 Connect grease hoses(55) to adapters(28).9.3.23 Fit sheave key into keyslot and mount sheave if necessary. See 3.39.3.24 Slide the other inboard bearing end cap(33) over the shaft with seal facing up.9.3.25 Slide the seal spacer(43) onto the shaft until it seats against the shoulder.9.3.26 Install the outboard bearing(45) in the outboard bearing housing(41) and slide this onto theshaft.9.3.27 Slide the remaining seal spacer(43) onto the shaft.9.3.28 Slide the outboard bearing end cap into place and bolt both end caps to the bearinghousing using flat head socket cap screws(52) and thread locking compound. Torque to thevalue listed in Chart 1 for socket head bolts.9.3.29 Install the bearing lockwasher(48) and bearing nut(51).9.3.30 Lock the bearing nut with one of the tabs of the lockwasher.9.3.31 Install the rotary coupling(50) in its counterbore and lock in place with ring(49) and 4 sockethead bolts(26)9.3.32 Install hand hole covers(25).9.4 Installing the sheave housing9.4.1 Using a hoist and approved lifting eyes, set the sheave housing over the outboard bearinghousing. Align the mating holes and install several bolts to aid assembly. Check the desiredorientation of the opening of the sheave housing with the bell housing.9.4.2 Tighten the bolts(47) drawing the sheave housing onto the bearing carrier boss whilealigning the sheave housing to bell housing bolt holes. Be sure the sheave housingcounterbore is tight against the bell housing boss. This establishes alignment of thecomponents. Install socket head cap screws(40) with thread locking compound and torqueto the value shown in Chart 1.10.0 WARRANTYWPT guarantees all products will leave the factory in good condition. The products are warranted against defects in workmanship and material for a period of 365 days(one year) after shipment. Adjustment under this warranty will be made only after completion of inspection of the part or product in our factory. Liability under the warranty shall extend only to the replacement or correction of any defective part or product as determined by WPT. All materials must be returned freight prepaid. This warranty shall not apply to any product that has been repaired or altered without the specific knowledge and consent of an authorized representative of the manufacturer; or operated or installed in a manner contrary to the manufacturer's instruction; or subjected to misuse or improper maintenance; or has been damaged by accident or negligence. This warranty is made in lieu of all other warranties, expressed or implied, including but not limited to warranties of merchantability or fitness for a particular purpose, and there are no other warranties that extend beyond this expressed warranty. WPT reserves the right to discontinue models or to change specification at any time without notice. No discontinuance or change will create any liability on the part of WPT in respect to its products in the hands of customers or products on order not incorporating such changes even though delivered after any such change. Rotating equipment is potentially dangerous and should be properly。
预设定机油枪使用说明书(中文)

路博预设定机油枪使用说明书中文试用版警告: 在操作之前请仔细读和理解用法说明。
没有按照安全规章和其他基本安全预防措施操作可能导致严重人为事故。
使用说明预设定机油枪被设计用于机油的输送,当设定的油量到达时,喷嘴会自动关闭,停止机油输送。
技术参数流量范围 1 – 35 LPM (0.3-9.2 GPM)操作压力范围0.5 – 70 Bar (7-1000 PSI)操作温度Max. 60°C (140°F)精度±0.5%粘性8-5000 mPas5-Digital LCD Display (3/8"H xQuart, Pint, Gallon, Liter3/16"W) 数显单位接头1/2" BSP电源电压 1 Alkaline cell 9V操作数字表设备使用9V可更换的碱性电池,对于电池的更换请查看说明书D部分。
1、按键按数字直接设置AUTO按AUTO进入或退出自动模式RESET在手动或自动模式清除之前的设置OK/STOP按OK键确认动作或停止动作2、安装A. 安装前的准备工作1)系统压力的释放a) 关闭泵电源或截止阀b) 慢慢地打开枪的出油口处的油路截止阀,放出系统中的油到废油容器中,进行排油c)打开系统中所有的油路截止阀,启动油泵开始向系统供油d)让油泵处于打开状态,确保系统回路压力平衡2) 关闭截止阀3) 绕管装置根据场地,为了节约空间,用户需要配置下面设备,系统中的每个装置应进行有效的接地:a) 泵:依据生产厂家推荐的方法执行b)空气和流体软管:进行有效接地c)空气压缩机:依据生产厂家推荐的方法执行d) 油桶:使用当地允许型号的油桶警告不要在管连接处用特富龙胶带,可能导致接地效果失效B. 仪表连接软管在开始操作之前关闭油泵喷嘴与仪表连接3. 仪表的操作根据需要的功能选择不同的操作选项按AUTO键,液晶屏上会显示AUTO标示按OK/STOP键,为确定或停止按RESET键从菜单或已经进行的操作中退出,可以立即进行其他操作A. 显示模式仪表开始工作前按RESET键进行清零仪表显示即时当前计注值显示存储总值按RESET键可以上排计注值清零仪表将显示如下警告存储总值默认不可被改动,如果要更改,请联系服务中心权威扣下扳机进行加油放开扳机停止加油B. 操作模式B-1.手动模式按RESET进入手动模式仪表显示手动模式扣下扳机进行加油,当到所需的油量时,释放扳机,停止加油按RESET键清零B-2. 自动模式按AUTO仪表显示1-2-3-4-last :5组预存设定值可被频繁使用。
MCP131中文资料
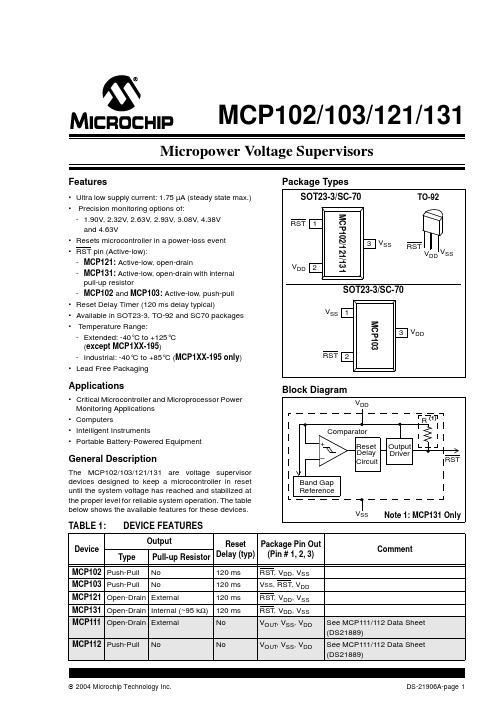
2004 Microchip Technology Inc.
DS-21906A-page 1
元器件交易网
MCP102/103/121/131
1.0 ELECTRICAL CHARACTERISTICS
Parameters
Sym
Min
Typ
Max
Units
Conditions
Operating Voltage Range
Specified VDD Value to RST low
Operating Current
MCP102, MCP103,
VDD
1.0
VDD
1.0
IDD
—
—
5.5
V
—
V IRST = 10 uA, VRST < 0.2V
- 1.90V, 2.32V, 2.63V, 2.93V, 3.08V, 4.38V and 4.63V
• Resets microcontroller in a power-loss event • RST pin (Active-low):
- MCP121: Active-low, open-drain - MCP131: Active-low, open-drain with internal
DS-21906A-page 2
2004 Microchip Technology Inc.
元器件交易网
MCP102/103/121/131
DC CHARACTERISTICS (CONTINUED)
Electrical Specifications: Unless otherwise indicated, all limits are specified for: VDD = 1V to 5.5V, RPU = 100 kΩ (MCP121 only), TA = -40°C to +125°C.
P Leo 绝缘系统1
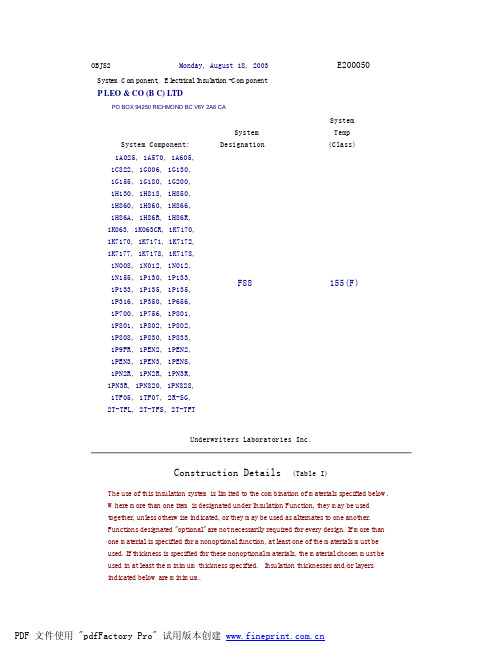
OBJS2Monday, August 18, 2003E200050 System Component, Electrical Insulation -ComponentP LEO & CO (B C) LTDPO BOX 94250 RICHMOND BC V6Y 2A6 CASystem Component:SystemDesignationSystemTemp(Class)1A025, 1A570, 1A605,1C822, 1G006, 1G130,1G155, 1G180, 1G200,1H130, 1H818, 1H850,1H860, 1H860, 1H866,1H86A, 1H86R, 1H86R,1K063, 1K063CR, 1K7170,1K7170, 1K7171, 1K7172,1K7177, 1K7178, 1K7178,1N008, 1N012, 1N012,1N155, 1P130, 1P133,1P133, 1P135, 1P135,1P316, 1P350, 1P656,1P700, 1P756, 1P801,1P801, 1P802, 1P802,1P808, 1P830, 1P833,1P9FR, 1PEN2, 1PEN2,1PEN3, 1PEN3, 1PENS,1PN2R, 1PN2R, 1PN3R,1PN3R, 1PN820, 1PN828,1TF05, 1TF07, 2R-SG,2T-TFL, 2T-TFS, 2T-TFTF88 155(F)Underwriters Laboratories Inc.Construction Details (Table I)The use of this insulation system is limited to the combination of materials specified below. Where more than one item is designated under Insulation Function, they may be used together, unless otherwise indicated, or they may be used as alternates to one another. Functions designated "optional" are not necessarily required for every design. If more than one material is specified for a nonoptional function, at least one of the materials must be used. If thickness is specified for these nonoptional materials, the material chosen must be used in at least the minimum thickness specified. Insulation thicknesses and/or layers indicated below are minimum.Winding Wire - Recognized Component - Magnet wire (OBMW2), single build or greater or- Recognized Component - Single and Multi-Layer Insulated Winding Wire (OBJT2) or- Recognized Component - Appliance Wiring Material (AVLV2)(unless otherwise noted, winding wire types listed below may be used in combination within a single product) MW 79 or 155C PolyurethaneMW 80 or 155C Polyurethane (Polyamide)MW 82 or 180C PolyurethaneMW 83 or 180C Polyurethane (Polyamide)FurukawaTEX-F 4.72 mils (0.12 mm) triple insulatedRubadue Wire Co. Inc.FEP wire 4.06 mils (0.1 mm) double or triple layer insulatedTCA3 3.62 mils (0.09 mm) double or triple layer insulatedTefzel wire 3.62 mils (0.09 mm) double or triple layer insulated Totoku ElectricTIW-3 3.86 mils (0.1 mm) triple insulatedTIW-E 3.86 mils (0.1 mm) triple insulatedGround & Interwinding InsulationDesignation (No.)mils(mm)CommentsDuPontKaladex2000 1 (0.03)Kapton 100CR 1 (0.03)Kapton 100HA 1 (0.03)Kapton 100HN 1 (0.03)Kapton 100PST 1 (0.03)Nomex 410 5(layers)P. Leo1H130 3(layers)1H860 3(layers)1H866 1(layers)1H86R 1(layers)1K7170 1(layers) Recognized Component - Insulating Tape (OANZ2)1K7177 1(layers) Recognized Component - Insulating Tape (OANZ2)1K7178 1(layers)1N012 2(layers)1P133 3(layers)1P135 3(layers)1P801 5(layers) Recognized Component - Insulating Tape (OANZ2)1P802 5(layers) Recognized Component - Insulating Tape (OANZ2)1PEN2 1(layers) Recognized Component - Insulating Tape (OANZ2)1PEN3 1(layers) Recognized Component - Insulating Tape (OANZ2)1PN2R 1(layers) Recognized Component - Insulating Tape (OANZ2)1PN3R 1(layers) Recognized Component - Insulating Tape (OANZ2)Sumitomo 3M LtdSuper 10-T 2(layers) Recognized Component - Insulating Tape (OANZ2)Super 10-W 2(layers) Recognized Component - Insulating Tape (OANZ2)Sumitomo BakeliteSumikon AM-3200 11.8(0.3)DAP Molding ComopundSumikon PM-9630 11.8(0.3)Phenolic Molding CompoundSumikon PM-9720 11.8(0.3)Phenolic Molding CompoundSumikon PM-9750 11.8(0.3)Phenolic Molding CompoundSumikon PM-9820 11.8(0.3)Phenolic Molding CompoundSumikon PM-9830 11.8(0.3)Phenolic Molding CompoundSumikon PM-9850 11.8(0.3)Phenolic Molding CompoundTeijin Dupont Films Japan Ltd.Teonex Q51 1 (0.03)Any Recognized Component Plastic (QMFZ2), polyethylene terphthalate film (PET), 5 mils (0.13 mm) - various manufacturers.Cores, Tubes, Bobbins (optional) (for mechanical support only) Designation (No.)CommentsCosmo LinkPTFE-LPTFE-TFurukawa ElectricPI-TubeGreat Holding Industrial Co., Ltd.TFLTFSTFTHitachi Cable LtdVerafit V2Kurabe IndustrialSE-1SE-2NikkanE-651U-1E-651U-2S-693-600S-693F-1Nissei ElectricRSU-1RSU-2P. Leo & Co. (B C) Ltd.2R-SG2T-TFL2T-TFS2T-TFTSumitomo Electical Fine Polymer Sumitube F2(z)Zeus Industrial Products Inc.TFE-LW-150TFE-SW-600TFE-TW-300Tapes (optional)Designation (No.)CommentsP Leo & Co (B C) Ltd1A0251A5701A6051C8221G006 aramid fiber (Nomex) paper1G130 glass cloth1G155 glass cloth1G180 glass cloth1G200 woven glass cloth, silicone adhesive 1H818 reinforced PET, rubber adhesive1H850 polyester film1H860 acrylic adhesive, polyester film1H86A1H86R1K063 silicone adhesive, polyimide film 1K063CR1K7170 Kapton film1K7171 silicone adhesive, polyimide film 1K7172 silicone adhesive, polyimide film1K71781N008 aramid fiber (Nomex), rubber adhesive 1N012 PET film, acrylic adhesive1N155 aramid fiber (Nomex), rubber adhesive 1P130 acrylic adhesive, polyester film1P133 PET film, acrylic adhesive1P135 PET film, acrylic adhesive1P3161P350 PET film, acrylic adhesive1P6561P700 polyester film1P7561P801 acrylic adhesive, polyester film1P802 acrylic adhesive, polyester film1P808 polyester film1P830 acrylic adhesive, polyester film1P833 PET film, acrylic adhesive1P9FR1PEN21PEN31PENS1PN2R1PN3R1PN820 woven polyester cloth1PN828 woven polyester cloth1TF051TF07Sumitomo 3M LimitedCU-35 (optional)Super 10-TSuper 10-W2245 (optional)Teraoka Seisakusho Co., Ltd.831S (optional)Tie Cords (optional)Designation (No.)CommentsTeijinBHT-44TPotting Compounds (optional)Designation (No.)CommentsGE Toshiba SiliconeTSE3331TSE3331KVarnishes (optional) Recognized Component - Varnishes (OBOR2) Designation (No.)CommentsHitachi Chemical Co. LtdWA-238AWF-285WP-2952F-2GWP-2952-F5John C. Dolph CoAC-43BC-346AKyocera Chemical Corp. (Toshiba Chemical)TVB-2024TVB-2180T++ ++ optional suffixMeiden Chemical#754XL Cannot be used with TEX-F#880P. D. George CoE468-2* Cannot be used with TEX-FE-468-2-7* May be followed by a one or two alphanumericsuffix indicating percent of insert fill and/orcolor.E-468-2FC* May be followed by a two three alphanumericsuffix indicating percent of insert fill and/orcolor.434 Air DryRipley Resin 468-2(+) May be followed by a two three alphanumericsuffix indicating percent of insert fill and/orcolor.711-F-2106P. D. George Co/SterlingY-21077X-010Viking ProductsV1380V1630Miscellaneous Minor Insulations (optional) Designation (No.)CommentsChang ChunPBT-4130 Coil coverE. I. Dupont de Nemours & Co.FR530 Coil cover Rynite, coil coverZytel 103HSLKolonKP212V0 Coil coverMitsubishi3010N Coil cover coil cover5010N6 coil coverTeijinCH7030 Coil cover coil coverCN7000 Coil cover coil coverCRN7000 Coil cover coil coverCRN7030 Coil cover coil coverToray Industries。
FF150R12KE3G中文资料

50
% v [w
40 30 20 10 0 0 5
@G
0,1
! Mv$E w Mv w 5 5 " !!4B 5 5 Y!! "
" 5 4 5 ! 5 5 B , YY
10 15 20 25 30 35 40 45 50
C vNw : ' 6?a( # T a&n:V # T a&n:V 6?a( 3
6g v:w
()* + ,-. ()* + ! ,-.
60 v:w
150 120 90 60 30
400
600
/01 v/w
800
1000 1200 1400
0
0,0 0,2 0,4 0,6 0,8 1,0 1,2 1,4 1,6 1,8 2,0 2,2 2,4
/g v/w
! "#
5
元器件交易网
元器件交易网
Technische Information / technical information
IGBT-Module IGBT-modules 62mm C-Serien Modul mit Trench/Feldstop IGBT3 und Emcon High Efficiency Diode 62mm C-series module with the trench/fieldstop IGBT3 and Emcon High Efficiency diode
0,01 0,001
\ @ 6g + T/gV
0,01
3
0,1
v w #T T
1
V V
10
& 60 + T/01V /C1 + W!, /5
PC929中文资料

g TÜV ( VDE 0884 ) approved type is also available as an option.
s Features 1. Built-in IGBT shortcircuit protector circuit 2. Built-in direct drive circuit for IGBT drive
V
VCC = V01 = 24V, RG = 47Ω
6.5 6.0 5.5
CG = 3 000pF, FS = OPEN
1
2
3
V
(9)
*9
O2 "High→Low" delay time at protection from overcurrent
tPCOHL
Ta = 25˚C
-
4
10
µs
O2 fall time at protection from overcurrent
Amp.
1 2 3 4 5 67
1 Cathode 2 Cathode 3 Anode 4 NC 5 NC 6 NC 7 NC
8 FS
9C
10 GND
11 O2 12 O1 13 VCC 14 GND
Terminals 4 to 7 : Shortcircuit in element
* "OPIC" (Optical IC) is a trademark of the SHARP Corporation. An OPIC consists of a light-detecting element and signal processing circuit integrated onto a single chip.
HLMA-PG00-N0011中文资料
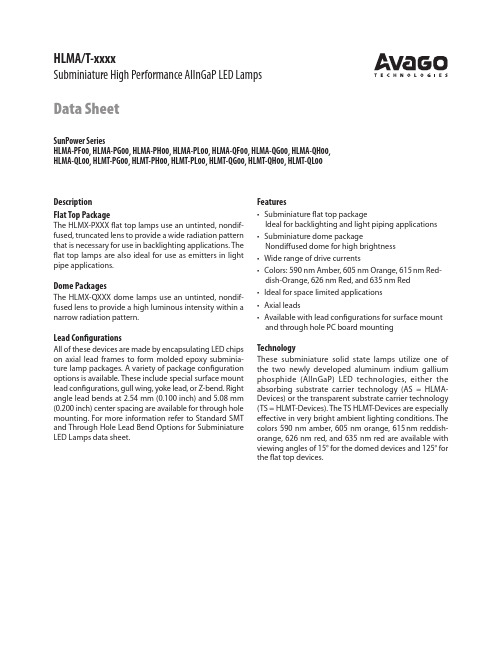
Features• Subminiature flat top packageIdeal for backlighting and light piping applications • Subminiature dome packageNondiffused dome for high brightness • Wide range of drive currents• Colors: 590 nm Amber, 605 nm Orange, 615 nm Red-dish-Orange, 626 nm Red, and 635 nm Red • Ideal for space limited applications • Axial leads• Available with lead configurations for surface mount and through hole PC board mountingDescription Flat Top PackageThe HLMX-PXXX flat top lamps use an untinted, nondif-fused, truncated lens to provide a wide radiation pattern that is necessary for use in backlighting applications. The flat top lamps are also ideal for use as emitters in light pipe applications.Dome PackagesThe HLMX-QXXX dome lamps use an untinted, nondif-fused lens to provide a high luminous intensity within a narrow radiation pattern.Lead ConfigurationsAll of these devices are made by encapsulating LED chips on axial lead frames to form molded epoxy subminia-ture lamp packages. A variety of package configuration options is available. These include special surface mount lead configurations, gull wing, yoke lead, or Z-bend. Right angle lead bends at 2.54 mm (0.100 inch) and 5.08 mm (0.200 inch) center spacing are available for through hole mounting. For more information refer to Standard SMT and Through Hole Lead Bend Options for Subminiature LED Lamps data sheet.SunPower SeriesHLMA-PF00, HLMA-PG00, HLMA-PH00, HLMA-PL00, HLMA-QF00, HLMA-QG00, HLMA-QH00, HLMA-QL00, HLMT-PG00, HLMT-PH00, HLMT-PL00, HLMT-QG00, HLMT-QH00, HLMT-QL00TechnologyThese subminiature solid state lamps utilize one of the two newly developed aluminum indium gallium phosphide (AlInGaP) LED technologies, either the absorbing substrate carrier technology (AS = HLMA-Devices) or the transparent substrate carrier technology (TS = HLMT-Devices). The TS HLMT-Devices are especially effective in very bright ambient lighting conditions. The colors 590 nm amber, 605 nm orange, 615 nm reddish-orange, 626 nm red, and 635 nm red are available with viewing angles of 15° for the domed devices and 125° for the flat top devices.HLMA/T-xxxxSubminiature High Performance AlInGaP LED LampsData SheetDevice Selection Guidel d Typ. I V Package Viewing Package Part Number (nm) (mcd) Description Angle 2q1/2 Outline HLMA-QL00 590 500 Domed, 15° B HLMT-QL00 590 1000 Nondiffused,HLMA-QJ00 605 500 UntintedHLMA-QH00 615 500HLMT-QH00 615 800HLMA-QG00 626 500HLMT-QG00 626 1000HLMA-QF00 635 500HLMA-PL00 590 75 Flat Top, 125° A HLMT-PL00 590 150 Nondiffused,HLMA-PJ00 605 75 UntintedHLMA-PH00 615 75HLMT-PH00 615 120HLMA-PG00 626 75HLMT-PG00 626 150HLMA-PF00 635 75Part Numbering SystemHLMx - x x 00 - x x x xxPackaging Option00: Straight Leads, Bulk Packaging, Quantity of 500 parts11: Gull Wing Bend, Tape & Reel – 7" Reel12: Gull Wing Bend, Bulk14: Gull Wing Bend, Tape & Reel – 13" Reel21: Yoke Bend, Tape and Reel – 7" Reel22: Yoke Bend, Bulk24: Yoke Bend, Tape and Reel – 13" Reel31: Z-Bend, Tape and Reel – 7" Reel32: Z-Bend, Bulk34: Z-Bend, Tape and Reel – 13" ReelColor Bin Selection0: Full Color Bin DistributionB: Color Bins 2 & 3K: Color Bins 2, 3 & 4R: Color Bins 2 & 4W: Color Bins 2, 4, 6 & 7X: Color Bins 4, 6 & 7Maximum Iv Bin OptionsPlease refer to the Iv Bin TableMinimum Iv Bin OptionsPlease refer to the Iv Bin TableColor OptionsL: Amber 590 nmJ: Orange 605 nmH: Reddish Orange 615 nmG: Red 626 nmF: Red 635 nmPackage OptionsQ: DomeP: Flat TopDice OptionsA: AS AlInGaPT: TS AlInGaPPackage Dimensions(A) Flat Top Lamps (B) Domed Lamps, Diffused and NondiffusedSTRIPE2.082.34(0.082)(0.092)NOTES:1. ALL DIMENSIONS ARE IN MILLIMETRES (INCHES).2. PROTRUDING SUPPORT TAB IS CONNECTED TO CATHODE LEAD.STRIPEProper right angle mounting to a PC board to prevent protruding cathode tab from shorting to anode connection.Absolute Maximum Ratings at T A = 25°CParameterHLMA-xxxxHLMT-xxxxUnitPeak Forward Current [2]100 100 mA Average Forward Current (I PEAK = 100 mA)[1,2] 30 37 mA DC Forward Current [3,5,6] 50 50 mA Power Dissipation105 120 mW Reverse Voltage (I R = 100 µA)5 V Transient Forward Current (10 µs Pulse)[5] 500 mA Operating Temperature Range –40 to +100 °C Storage Temperature Range –55 to +100°C LED Junction Temperature110°CLead Soldering Temperature [1.6 mm (0.063 in.) from body] 260°C for 5 seconds SMT Reflow Soldering Temperature260°C for 20 secondsNotes:1. Maximum I AVG at f = 1 kHz.2. Refer to Figure 5 to establish pulsed operating conditions.3. Derate linearly as shown in Figure4.4. The transient peak current is the maximum non-recurring peak current these devices can withstand without damaging the LED die and wire bonds. Operation at currents above Absolute Maximum Peak Forward Current is not recommended.5. Drive currents between 10 mA and 30 mA are recommended for best long term performance.6. Operation at currents below 5 mA is not recommended, please contact your Avago sales representative.HLMP-PH00 Anode/CathodeNO. ANODE DOWN.YES. CATHODE DOWN.Color, Viewing LuminousTotal Flux Peak Dominant Angle Efficacy Luminous Intensity f V (mlm) Wavelength Wavelength 2 q1/2h v[5]I V (mcd) @ 20 mA[1]@ 20 mA[2]l peak (nm) l d[3] (nm) Degrees[4](lm/w) Part Number Min. Typ. Max. Typ. Typ. Typ. Typ. Typ. HLMA-QL00-S00xx 160 500 – 250 592 590 15 480 HLMA-QL00-TU0xx 250 – 800 250 592 590 15 480 HLMA-QL00-TUKxx 250 – 800 250 592 590 15 480 HLMA-QL00-TVBxx 250 – 1250 250 592 590 15 480 HLMA-QL00-TVKxx 250 – 1250 250 592 590 15 480 HLMA-QL00-UV0xx 400 – 1250 250 592 590 15 480 HLMA-QL00-UVRxx 400 – 1250 250 592 590 15 480 HLMA-QL00-UWBxx 400 – 2000 250 592 590 15 480 HLMT-QL00-T00xx 250 1000 – 800 592 590 15 480 HLMA-QJ00-S00xx 160 500 – 250 609 605 15 370 HLMA-QH00-S00xx 160 500 – 250 621 615 15 263 HLMA-QH00-T00xx 250 500 – 250 621 615 15 263 HLMA-QH00-UW0xx 400 – 2000 250 621 615 15 263 HLMT-QH00-T00xx 250 500 – 800 621 615 15 263 HLMT-QH00-WX0xx 1000 – 3200 800 621 615 15 263 HLMA-QG00-S00xx 160 500 – 250 635 626 15 150 HLMA-QG00-TV0xx 250 – 1250 250 635 626 15 150 HLMT-QG00-T00xx 250 1000 – 800 635 626 15 150 HLMA-QF00-S00xx 160 500 – 250 650 635 15 110 HLMA-PL00-N00xx 25 75 – 250 592 590 125 480 HLMA-PL00-PRRxx 40 – 200 250 592 590 125 480 HLMA-PL00-PRXxx 40 – 200 250 592 590 125 480 HLMA-PL00-QRXxx 63 – 200 250 592 590 125 480 HLMT-PL00-P0Wxx 40 150 – 800 592 590 125 480 HLMA-PJ00-N00xx 25 75 – 250 609 605 125 370 HLMA-PH00-N00xx 25 75 – 250 621 615 125 263 HLMT-PH00-P00xx 40 120 – 800 621 615 125 263 HLMA-PG00-N00xx 25 75 – 250 635 626 125 150 HLMT-PG00-P00xx 40 150 – 800 635 626 125 150 HLMA-PF00-N00xx 25 75 – 250 640 635 125 110 Notes:1. The luminous intensity, I v, is measured at the mechanical axis of the lamp package. The actual peak of the spatial radiation pattern may not be aligned with this axis.2. f v is the total luminous flux output as measured with an integrating sphere.3. The dominant wavelength, l d, is derived from the CIE Chromaticity Diagram and represents the color of the device.4. q1/2 is the off-axis angle where the liminous intensity is 1/2 the peak intensity.5. Radiant intensity, I e, in watts/steradian, may be calculated from the equation I e = I v/h v, where I v is the luminous intensity in candelas and h v is the luminous efficacy in lumens/watt.CapacitanceSpeed of Response Forward Voltage Reverse Breakdown C (pF) Thermal t s (ns)V F (Volts) Voltage V R (Volts) V F = 0, Resistance Time Constant Part @ I F = 20 mA @ I R = 100 µA f = 1 MHz R q J-PIN (°C/W) e -t/t s NumberTyp. Max.Min. Typ.Typ.Typ.Typ.HLMA-Qx00 1.9 2.4 5 25 40 170 13HLMT-Qx00 2.4 2.6 5 20 70 170 13HLMA-Px00 1.9 2.4 5 25 40 170 13HLMT-Px00 2.42.65207017013Figure 1. Relative intensity vs. wavelength.WAVELENGTH – nmR E L A T I V E I N T E N S I T Y5506006507001.00.50AMBERHLMA-PXXX fig 1ORANGEREDDISH ORANGE RED 626 nm RED 635 nmFigure 2a. Forward current vs. forward voltage. HLMA-xxxx.Figure 2b. Forward current vs. forward voltage. HLMT-xxxx.Figure 3b. Relative luminous intensity vs. DC forward current. HLMT-xxxx.Figure 3a. Relative luminous intensity vs. DC forward current. HLMA-xxxx.Figure 4. Maximum forward current vs. ambient temperature.Figure 5a. Maximum average current vs. peak forward current for HLMA-xxxx.Figure 5b. Maximum average current vs. peak forward current for HLMT-xxxx.I F – F O R W A R D C U R R E N T – m A1.00V F – FORWARD VOLTAGE – V2.510060 1.52.03.0204080R E L A T I V E L U M I N O U S I N T E N S I T Y (N O R M A L I Z E D A T 20 m A )00I F - DC FORWARD CURRENT - mA 20402.51.51.010302.0500.5R E L A T I V E L U M I N O U S I N T E N S I T Y (N O R M A L I Z E D A T 20 m A )00I F - DC FORWARD CURRENT - mA20404.02.01.01030603.050I F – F O R W A R D C U R R E N T – m AT A – AMBIENT TEMPERATURE – o CI A V G – A V E R A GE C U R R E N T – m AI PEAK – PEAK FORWARD CURRENT – mA I A V G = A V E R A G E C U R R E N T– m AI PEAK – PEAK FORWARD CURRENT – mAI F - F O R W A R D C U R R E N T - m AV F - FORWARD VOLTAGE - V051015202530350123Figure 6. Relative luminous intensity vs. angular displacement for 15° device.Figure 7. Relative luminous intensity vs. angular displacement for 125° device.Color Bin LimitsPackageBinMin.Max.Yellow 0 Full Distribution 3 584.0 587.5 2 586.5 590.0 4 589.0 592.5 6 591.5 595.0 7 594.0597.5Orange 0 Full Distribution 2 599.0 602.5 3 601.5 604.0 4 603.8 608.2 5606.8611.2Intensity Bin LimitsBinMin.Max.N 25 50P 40 80Q 63 125R 100 200S 160 320T 250 500U 400 800V 630 1250W 1000 2000X 1600 3200Y 25005000N O R M A L I Z E D I N T E N S I T Y1.00ANGULAR DISPLACEMENT – DEGREES0.80.60.50.70.2-500.10.30.4-40-30-20-1010203040500.9N O R M A L I Z E D I N T E N S I T Y1.10ANGULAR DISPLACEMENT – DEGREES0.80.60.50.70.2100900.10.30.4807060504020100301020304050607080901000.91.0Mechanical Option MatrixMechanicalOption Code Definition00 Straight Leads, Bulk Packaging, Quantity of 500 Parts11 Gull Wing Leads, 12 mm Tape on 7 in. Dia. Reel, 1500 Parts per Reel12 Gull Wing Leads, Bulk Packaging, Quantity of 500 Parts14 Gull Wing Leads, 12 mm Tape on 13 in. Dia. Reel, 6000 Parts per Reel21 Yoke Leads, 12 mm Tape on 7 in. Dia. Reel, 1500 Parts per Reel22 Yoke Leads, Bulk Packaging, Quantity of 500 Parts24 Yoke Leads, 12 mm Tape on 13 in. Dia. Reel, 6000 Parts per Reel31 Z-Bend Leads, 12 mm Tape on 7 in. Dia. Reel, 1500 Parts per Reel32 Z-Bend Leads, Bulk Packaging, Quantity of 500 Parts34 Z-Bend Leads, 12 mm Tape on 13 in. Dia. Reel, 6000 Parts per Reel Note:All categories are established for classification of products. Products may not be available in all catego-ries. Please contact your local Avago representative for further clarification/information.For product information and a complete list of distributors, please go to our website: Avago, Avago Technologies, and the A logo are trademarks of Avago Technologies Limited in the United States and other countries. Data subject to change. Copyright © 2006 Avago Technologies Limited. All rights reserved. Obsoletes 5989-4442ENAV02-0309EN - April 10, 2007。
9601中文资料

TL F 66109601 DM9601 Retriggerable One ShotJune19899601 DM9601Retriggerable One ShotGeneral DescriptionThese retriggerable one shots provide the designer withfour inputs two active high and two active low This permitsa choice of either leading-edge or trailing-edge triggeringindependent of input transition times When input conditonsfor triggering are met a new cycle starts and the externalcapacitor is rapidly discharged and then allowed to chargeagain The retriggerable feature allows for output pulsewidths to be expanded In fact a continuous true output canbe maintained by having an input cycle time which is shorterthan the output cycle time Retriggering may be inhibited bytying the Q output to an active low inputFeaturesY High speed operation input repetition rate l10MHzY Flexibility of operation optional retriggering lock-outcapabilityY Output pulse width range 50ns to%Y Leading or trailing edge triggeringY Complementary outputs inputsY Input clamping diodesY DTL TTL compatible logic levelsY Alternate Military Aerospace device(9601)is availableContact a National Semiconductor Sales Office Distrib-utor for specificationsConnection DiagramDual-In-Line PackageTL F 6610–1Order Number9601DMQB 9601FMQB DM9601J DM9601W or DM9601NSee NS Package Number J14A N14A or W14BFunction TableInputs OutputsA1A2B1B2Q QH e High Logic LevelH H X X L HL e Low Logic LevelX X L X L HX e Either Low orX X X L L H High Logic LevelL X H H L H u e Low to High LevelTransitionL X u Hv e High to Low LevelL X H uTransitionX L H H L He Positive PulseX L u H e Negative PulseX L H uH v H Hv v H Hv H H HC1995National Semiconductor Corporation RRD-B30M105 Printed in U S AAbsolute Maximum Ratings(Note)If Military Aerospace specified devices are required please contact the National Semiconductor Sales Office Distributors for availability and specifications Supply Voltage7V Input Voltage5 5V Operating Free Air Temperature RangeMilitary b55 C to a125 C Commercial0 to a70 C Storage Temperature Range b65 C to a150 C Note The‘‘Absolute Maximum Ratings’’are those values beyond which the safety of the device cannot be guaran-teed The device should not be operated at these limits The parametric values defined in the‘‘Electrical Characteristics’’table are not guaranteed at the absolute maximum ratings The‘‘Recommended Operating Conditions’’table will define the conditions for actual device operationRecommended Operating ConditionsSymbol ParameterMilitary CommercialUnits Min Nom Max Min Nom MaxV CC Supply Voltage4 555 54 7555 25V V IH High Level Input T A e b55 C2Voltage TA e0 C1 9T A e25 C1 71 8VT A e75 C1 6T A e125 C1 5V IL Low Level Input T A e b55 C0 85Voltage TA e0 C0 85T A e25 C0 90 85VT A e75 C0 85T A e125 C0 85I OH High Level Output Current b0 72b0 96mA I OL Low Level Output Current1012 8mA T A Free Air Operating Temperature b55125075 C Electrical Characteristics over recommended operating free air temperature range(unless otherwise noted)Symbol Parameter Conditions(Note3)MinTypMax Units (Note1)V I Input Clamp Voltage V CC e Min I I e b12mA b1 5V V OH High Level Output V CC e Min I OH e Max2 4VVoltage V IL e Max V IH e Min (Note4)V OL Low Level Output V CC e Min I OL e Max MIL0 4Voltage V IL e Max V IH e MinCOM0 45V(Note4)I IH High Level Input V CC e Max V I e4 5V60m A CurrentI IL Low Level Input V CC e Max MIL V IN e0 40V b1 6mA Current COM VIN e0 45V b1 6I OS Short Circuit V CC e Max MIL b10b40mA Output Current(Notes2and4)COM b10b40I CC Supply Current V CC e Max25mA Note1 All typicals are at V CC e5V T A e25 CNote2 Not more than one output should be shorted at a timeNote3 Unless otherwise noted R X e10k between PIN13and V CC on all testsNote4 Ground PIN11for V OL test on PIN6 V OH and I OS tests on PIN8 Open PIN11for V OL test on PIN8 V OH and I OS tests on PIN62Switching Characteristics at V CC e5V and T A e25 C(See Section1for Test Waveforms and Output Load)Symbol Parameter From(Input)Conditions Min Max Units To(Output)t PLH Propagation Delay Time Negative Trigger C L e15pFLow to High Level Output Input to C X e040nsTrue Output R X e5k Xt PHL Propagation Delay Time Negative TriggerHigh to Low Level Output Input to40nsComplement Outputt PW(MIN)Minimum True Output65ns Pulse Widtht PW Pulse Width R X e10k X3 083 76m sC X e1000pFC STRAY Maximum Allowable Pin13to GND50pF Wiring CapacitanceR X External Timing Resistor DM9625k XR X External Timing Resistor DM8650k X Operating Rules1 An external resistor R X and an external capacitor C X arerequired for operation The value of R X can vary between the limits shown in switching characteristics The value ofC X is optional and may be adjusted to achieve the re-quired output pulse width2 Output pulse width t PW may be calculated as follows t PW e K R X C X 1a0 7R X((for C X l103pF)K 0 34R X in k X C X in pF and t PW in ns(For C X k103pF see curve )3 R X and C X must be kept as close as possible to thecircuit in order to minimize stray capacitance and noise pickup If remote trimming is required R X may be split up such that at least R X(MIN)must be as close as possible to the circuit and the remote portion of the trimming re-sistor R k R X(MAX)b R X4 Set-up time(t1)for input trigger pulse must be l40ns(See Figure1)Release time(t2)for input trigger pulse must be l40ns (See Figure2)TL F 6610–2FIGURE1TL F 6610–3FIGURE25 Retrigger pulse width(see Figure3)is calculated as fol-lowst W e t PW a t PLH e K R X C X 1a0 7R X(a t PLHTL F 6610–4FIGURE3Typical‘‘K’’Coefficient Variation vs Timing Capacitance The multiplicative factor‘‘K’’varies as a function of the tim-ing capacitor C X The graph below details this characteris-ticTL F 6610–5 For further detailed device characteristics and output performance please refer to the NSC one-shot application note AN-3663Typical Performance CharacteristicsCapacitance For C X k 103pFTiming Resistance AndOutput Pulse Width vs TemperaturePulse Width vs Ambient Normalized OutputVoltagePulse Width vs Supply Normalized Output Operating Duty CyclePulse Width vsNormalized Output Resistance Pulse Width vs Timing Ambient TemperatureOutput Pulse Width vs TL F 6610–6Schematic DiagramTL F 6610–74Physical Dimensions inches(millimeters)14-Lead Ceramic Dual-In-Line Package(J)Order Number9601DMQB or DM9601JNS Package Number J14A14-Lead Molded Dual-In-Line Package(N)Order Number DM9601NNS Package Number N14A59601 D M 9601R e t r i g g e r a b l e O n e S h o tPhysical Dimensions inches (millimeters)(Continued)14-Lead Ceramic Flat Package (W)Order Number 9601FMQB or DM9601WNS Package Number W14BLIFE SUPPORT POLICYNATIONAL’S PRODUCTS ARE NOT AUTHORIZED FOR USE AS CRITICAL COMPONENTS IN LIFE SUPPORT DEVICES OR SYSTEMS WITHOUT THE EXPRESS WRITTEN APPROVAL OF THE PRESIDENT OF NATIONAL SEMICONDUCTOR CORPORATION As used herein 1 Life support devices or systems are devices or 2 A critical component is any component of a life systems which (a)are intended for surgical implant support device or system whose failure to perform can into the body or (b)support or sustain life and whose be reasonably expected to cause the failure of the life failure to perform when properly used in accordance support device or system or to affect its safety or with instructions for use provided in the labeling can effectivenessbe reasonably expected to result in a significant injury to the userNational Semiconductor National Semiconductor National Semiconductor National Semiconductor CorporationEuropeHong Kong LtdJapan Ltd1111West Bardin RoadFax (a 49)0-180-530858613th Floor Straight Block Tel 81-043-299-2309。
ZL30122GGG资料
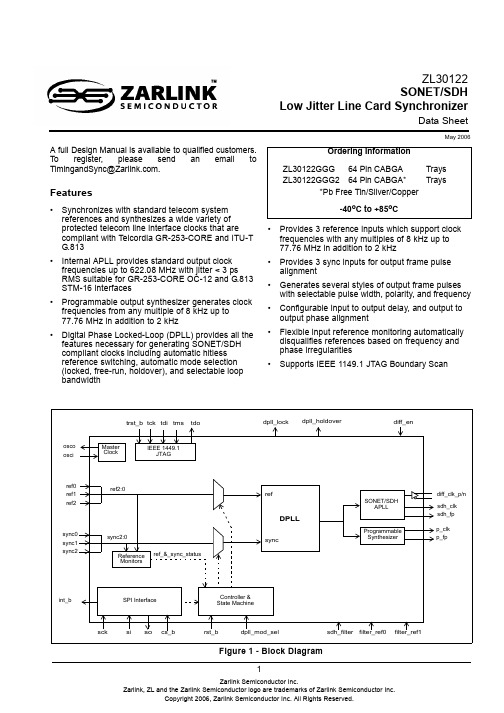
1A full Design Manual is available to qualified customers.To register, please send an email to TimingandSync@.Features•Synchronizes with standard telecom system references and synthesizes a wide variety of protected telecom line interface clocks that are compliant with Telcordia GR-253-CORE and ITU-T G.813•Internal APLL provides standard output clock frequencies up to 622.08MHz with jitter < 3 ps RMS suitable for GR-253-CORE OC-12 and G.813 STM-16 interfaces•Programmable output synthesizer generates clock frequencies from any multiple of 8kHz up to 77.76MHz in addition to 2kHz•Digital Phase Locked-Loop (DPLL) provides all the features necessary for generating SONET/SDH compliant clocks including automatic hitless reference switching, automatic mode selection (locked, free-run, holdover), and selectable loop bandwidth•Provides 3 reference inputs which support clock frequencies with any multiples of 8kHz up to 77.76MHz in addition to 2kHz•Provides 3 sync inputs for output frame pulse alignment•Generates several styles of output frame pulses with selectable pulse width, polarity, and frequency •Configurable input to output delay, and output to output phase alignment•Flexible input reference monitoring automatically disqualifies references based on frequency and phase irregularities•Supports IEEE 1149.1 JTAG Boundary ScanMay 2006Figure 1 - Block DiagramZL30122 SONET/SDHLow Jitter Line Card SynchronizerData SheetOrdering InformationZL30122GGG 64 Pin CABGA Trays ZL30122GGG264 Pin CABGA*Trays*Pb Free Tin/Silver/Copper-40o C to +85o CZL30122Data SheetApplications•AMCs for AdvancedTCA TM and MicroTCA Systems•Multi-Service Edge Switches or Routers•DSLAM Line Cards•WAN Line Cards•RNC/Mobile Switching Center Line Cards•ADM Line CardsZL30122Data SheetTable of Contents1.0 Functional Description . . . . . . . . . . . . . . . . . . . . . . . . . . . . . . . . . . . . . . . . . . . . . . . . . . . . . . . . . . . . . . . . . .91.1 DPLL Features . . . . . . . . . . . . . . . . . . . . . . . . . . . . . . . . . . . . . . . . . . . . . . . . . . . . . . . . . . . . . . . . . . . . . .91.2 DPLL Mode Of Operation . . . . . . . . . . . . . . . . . . . . . . . . . . . . . . . . . . . . . . . . . . . . . . . . . . . . . . . . . . . . .101.3 Ref and Sync Inputs . . . . . . . . . . . . . . . . . . . . . . . . . . . . . . . . . . . . . . . . . . . . . . . . . . . . . . . . . . . . . . . . .111.4 Ref and Sync Monitoring. . . . . . . . . . . . . . . . . . . . . . . . . . . . . . . . . . . . . . . . . . . . . . . . . . . . . . . . . . . . . .121.5 Output Clocks and Frame Pulses . . . . . . . . . . . . . . . . . . . . . . . . . . . . . . . . . . . . . . . . . . . . . . . . . . . . . . .141.6 Configurable Input-to-Output and Output-to-Output Delays . . . . . . . . . . . . . . . . . . . . . . . . . . . . . . . . . . .152.0 Software Configuration. . . . . . . . . . . . . . . . . . . . . . . . . . . . . . . . . . . . . . . . . . . . . . . . . . . . . . . . . . . . . . . . .163.0 References . . . . . . . . . . . . . . . . . . . . . . . . . . . . . . . . . . . . . . . . . . . . . . . . . . . . . . . . . . . . . . . . . . . . . . . . . . .21ZL30122Data SheetList of FiguresFigure 1 - Block Diagram. . . . . . . . . . . . . . . . . . . . . . . . . . . . . . . . . . . . . . . . . . . . . . . . . . . . . . . . . . . . . . . . . . . . . 1 Figure 2 - Automatic Mode State Machine. . . . . . . . . . . . . . . . . . . . . . . . . . . . . . . . . . . . . . . . . . . . . . . . . . . . . . . 10 Figure 3 - Reference and Sync Inputs. . . . . . . . . . . . . . . . . . . . . . . . . . . . . . . . . . . . . . . . . . . . . . . . . . . . . . . . . . 11 Figure 4 - Output Frame Pulse Alignment. . . . . . . . . . . . . . . . . . . . . . . . . . . . . . . . . . . . . . . . . . . . . . . . . . . . . . . 11 Figure 5 - Behaviour of the Guard Soak Timer during CFM or SCM Failures. . . . . . . . . . . . . . . . . . . . . . . . . . . . 13 Figure 6 - Output Configuration. . . . . . . . . . . . . . . . . . . . . . . . . . . . . . . . . . . . . . . . . . . . . . . . . . . . . . . . . . . . . . . 14 Figure 7 - Phase Delay Adjustments . . . . . . . . . . . . . . . . . . . . . . . . . . . . . . . . . . . . . . . . . . . . . . . . . . . . . . . . . . . 15ZL30122Data SheetList of TablesTable 1 - DPLL Features . . . . . . . . . . . . . . . . . . . . . . . . . . . . . . . . . . . . . . . . . . . . . . . . . . . . . . . . . . . . . . . . . . . . . 9 Table 2 - Set of Pre-Defined Auto-Detect Clock Frequencies . . . . . . . . . . . . . . . . . . . . . . . . . . . . . . . . . . . . . . . . 12 Table 3 - Set of Pre-Defined Auto-Detect Sync Frequencies. . . . . . . . . . . . . . . . . . . . . . . . . . . . . . . . . . . . . . . . . 12 Table 4 - Output Clock and Frame Pulse Frequencies . . . . . . . . . . . . . . . . . . . . . . . . . . . . . . . . . . . . . . . . . . . . . 14 Table 5 - Register Map. . . . . . . . . . . . . . . . . . . . . . . . . . . . . . . . . . . . . . . . . . . . . . . . . . . . . . . . . . . . . . . . . . . . . . 16ZL30122Data Sheet Pin DescriptionPin # Name I/OType DescriptionInput ReferenceB1 A3 B4ref0ref1ref2I d Input References (LVCMOS, Schmitt Trigger). These are input referencesavailable for synchronizing output clocks. All three input references can beautomatically or manually selected using software registers. These pins areinternally pulled down to Vss.A1 A2 A4sync0sync1sync2I d Frame Pulse Synchronization References (LVCMOS, Schmitt Trigger).These are the frame pulse synchronization inputs associated with inputreferences 0, 1 and 2. These inputs accept frame pulses in a clock format (50%duty cycle) or a basic frame pulse format with minimum pulse width of 5ns.These pins are internally pulled down to V ss.Output Clocks and Frame PulsesD8sdh_clk O SONET/SDH Output Clock (LVCMOS). This output can be configured toprovide any one of the SONET/SDH clock outputs up to 77.76MHz. The defaultfrequency for this output is 77.76MHz.D7sdh_fp O SONET/SDH Output Frame Pulse (LVCMOS). This output can be configured toprovide virtually any style of output frame pulse synchronized with an associatedSONET/SDH family output clock. The default frequency for this frame pulseoutput is 8kHz.G8p_clk O Programmable Output Clock (LVCMOS). This output can be configured toprovide any frequency with a multiple of 8kHz up to 77.76MHz in addition to2kHz. The default frequency for this output is 2.048MHz.G7p_fp O Programmable Output Frame Pulse (LVCMOS). This output can be configuredto provide virtually any style of output frame pulse associated with p_clk. Thedefault frequency for this frame pulse output is 8kHz.A7 B8diff_clk_pdiff_clk_nO Differential Output Clock (LVPECL). This output can be configured to provide any one of the available SDH clock frequencies. The default frequency for thisclock output is 622.08MHz.ControlG5rst_b I Reset (LVCMOS, Schmitt Trigger). A logic low at this input resets the device. Toensure proper operation, the device must be reset after power-up. Reset shouldbe asserted for a minimum of 300ns.B2dpll_mod_sel I u DPLL Mode Select (LVCMOS, Schmitt Trigger). During reset, the level on thispin determines the default mode of operation of the DPLL (Normal or Freerun).After reset, the mode of operation can be controlled directly with these pins, or byaccessing the dpll_modesel register through the serial interface. This pin isinternally pulled up to Vdd.B3diff_en I u Differential Output Enable (LVCMOS, Schmitt Trigger). When set high, thedifferential LVPECL driver is enabled. When set low, the differential driver istristated reducing power consumption. This function is also controllable throughsoftware registers. This pin is internally pulled up to Vdd.ZL30122Data SheetStatus E1dpll_lockOLock Indicator (LVCMOS). This is the lock indicator pin for the DPLL. This output goes high when the DPLL’s output is frequency and phase locked to the input reference.H1dpll_holdover OHoldover Indicator (LVCMOS). This pin goes high when the DPLL enters the holdover mode.Serial Interface C1sck I Clock for Serial Interface (LVCMOS). Serial interface clock.D2si I Serial Interface Input (LVCMOS). Serial interface data input pin.D1so O Serial Interface Output (LVCMOS). Serial interface data output pin.C2cs_b I u Chip Select for Serial Interface (LVCMOS). Serial interface chip select. This pin is internally pulled up to Vdd.E2int_bOInterrupt Pin (LVCMOS). Indicates a change of device status prompting the processor to read the enabled interrupt service registers (ISR). This pin is an open drain, active low and requires an external pulled up to VDD.APLL Loop Filter A5sdh_filter A External Analog PLL Loop Filter terminal.B5filter_ref0A Analog PLL External Loop Filter Reference.C5filter_ref1AAnalog PLL External Loop Filter Reference.JTAG and Test G4tdoOTest Serial Data Out (Output). JTAG serial data is output on this pin on the falling edge of tck. This pin is held in high impedance state when JTAG scan is not enabled.G2tdiI uTest Serial Data In (Input). JTAG serial test instructions and data are shifted in on this pin. This pin is internally pulled up to Vdd. If this pin is not used then it should be left unconnected.G3trst_bI uTest Reset (LVCMOS). Asynchronously initializes the JTAG TAP controller by putting it in the Test-Logic-Reset state. This pin should be pulsed low on power-up to ensure that the device is in the normal functional state. This pin is internally pulled up to Vdd. If this pin is not used then it should be connected to GND.H3tck I Test Clock (LVCMOS): Provides the clock to the JTAG test logic. If this pin is not used then it should be pulled down to GND.F2tmsI uTest Mode Select (LVCMOS). JTAG signal that controls the state transitions of the TAP controller. This pin is internally pulled up to V DD . If this pin is not used then it should be left unconnected.Master Clock H4osciIOscillator Master Clock Input (LVCMOS). This input accepts a 20MHzreference from a clock oscillator (XO, XTAL). The stability and accuracy of the clock at this input determines the free-run accuracy and the long term holdover stability of the output clocks.Pin # NameI/O TypeDescriptionZL30122Data SheetI - InputI d -Input, Internally pulled down I u -Input, Internally pulled up O -Output A -Analog P -Power G -GroundH5oscoOOscillator Master Clock Output (LVCMOS). This pin must be left unconnected when the osci pin is connected to a clock oscillator.Miscellaneous F5IC Internal Connection. Leave unconnected. H6IC Internal Connection. Connect to ground.H7NCNo Connection. Leave unconnected.H2 IC Internal Connection. Connect to ground.Power and Ground C3C8E8F6F8G6H8V DDP P P P P P P Positive Supply Voltage. +3.3V DC nominal.E6F3V CORE P P Positive Supply Voltage. +1.8V DC nominal.B7C4AV DD P P Positive Analog Supply Voltage. +3.3V DC nominal.B6C7F1AV COREP P P Positive Analog Supply Voltage. +1.8V DC nominal.D3D4D5D6E3E4E5E7F4F7V SSG G G G G G G G G G Ground. 0 Volts.A6A8C6G1AV SSG G G GAnalog Ground. 0 Volts.Pin # Name I/O Type DescriptionZL30122Data Sheet1.0 Functional DescriptionThe ZL30122 SONET/SDH Line Card Synchronizer is a highly integrated device that provides timing and synchronization for network interface cards. The DPLL is capable of locking to one of three input references and provides a wide variety of synchronized output clocks and frame pulses.1.1 DPLL FeaturesThe Digital Phase-Locked Loop synchronizes to one of the qualified references and provides automatic or manual hitless reference switching and a holdover function when no qualified references are available. It provides a highly configurable set of features which are configurable through the serial interface. A summary of these features are shown in Table 1.FeatureDPLLModes of Operation Free-run, Normal (locked), HoldoverLoop Bandwidth User selectable: 14Hz, 28Hz, or wideband 1 (890Hz / 56Hz / 14Hz)1. In the wideband mode, the loop bandwidth depends on the frequency of the reference input. For reference frequencies equal to or greater than 64kHz, the loop bandwidth = 890 Hz. For reference frequencies equal to or greater than 8kHz and less than 64 kHz, the loop bandwidth = 56 Hz. For reference frequencies equal to 2kHz, the loop bandwidth is equal to 14Hz.Phase Slope Limiting User selectable: 885ns/s, 7.5µs/s, 61µs/s, or unlimited Pull-in Range Fixed: 130ppm Reference Inputs Ref0, Ref1, Ref2Sync InputsSync0, Sync1, Sync2Input Reference Frequencies 2kHz, N * 8kHz up to 77.76 MHzSupported Sync Input Frequencies 166.67Hz, 400Hz, 1kHz, 2kHz, 8kHz, 64kHz.Input Reference Selection/Switching Automatic (based on programmable priority and revertiveness), or manual selectionHitless Reference Switching Can be enabled or disabled Output Clocks diff_p/n, sdh_clk, p_clkOutput Frame Pulses sdh_fp, p_fp synchronized to active sync reference.Supported Output Clock FrequenciesAs listed in Table 4Supported Output Frame Pulse Frequencies As listed in Table 4External Pins Status IndicatorsLock, HoldoverTable 1 - DPLL FeaturesZL30122Data Sheet1.2 DPLL Mode Of OperationThe DPLL supports three modes of operation - free-run, normal, and holdover. The mode of operation can be manually set or controlled by an automatic state machine as shown in Figure 2.Figure 2 - Automatic Mode State MachineFree-runThe free-run mode occurs immediately after a reset cycle or when the DPLL has never been synchronized to areference input. In this mode, the frequency accuracy of the output clocks is equal to the frequency accuracy of the external master oscillator. Lock AcquisitionThe input references are continuously monitored for frequency accuracy and phase regularity. If at least one of the input references is qualified by the reference monitors, then the DPLL will begin lock acquisition on that input. Given a stable reference input, the ZL30122 will enter in the Normal (locked) mode.Normal (locked)The usual mode of operation for the DPLL is the normal mode where the DPLL phase locks to a selected qualified reference input and generates output clocks and frame pulses with a frequency accuracy equal to the frequency accuracy of the reference input. While in the normal mode, the DPLL’s clock and frame pulse outputs comply with the MTIE and TDEV wander generation specifications as described in Telcordia and ITU-T telecommunication standards.HoldoverWhen the DPLL operating in the normal mode loses its reference input, and no other qualified references are available, it will enter the holdover mode and continue to generate output clocks based on historical frequency data collected while the DPLL was synchronized. The transition between normal and holdover modes is controlled by the DPLL so that its initial frequency offset is better than 100ppb. The frequency drift after this transition period is dependant on the frequency drift of the external master oscillator.ResetAnother reference is qualified and availablefor selectionPhase lock on the selected reference is achievedLock AcquisitionNormal (Locked)No references are qualified and available for selectionFree-RunHoldoverSelected referencefailsAll references are monitored for frequency accuracy and phase regularity, and at least one reference is qualified.Normal (Locked)ZL30122Data Sheet1.3 Ref and Sync InputsThere are three reference clock inputs (ref0 to ref2) available to the DPLL. Reference selection can be controlled using a built-in state machine or set in a manual mode.The selected reference input is used to synchronize the output clocks.Figure 3 - Reference and Sync InputsIn addition to the reference inputs, the DPLL has three optional frame pulse synchronization inputs (sync0 to sync2) used to align the output frame pulses. The sync n input is selected with its corresponding ref n input, where n = 0, 1, or 2. Note that the sync input cannot be used to synchronize the DPLL, it only determines the alignment of the frame pulse outputs. An example of output frame pulse alignment is shown in Figure 4.Figure 4 - Output Frame Pulse Alignmentref2:0sync2:0DPLLref ndiff_clk/sdh_clk/p_clksdh/p_fpWithout a frame pulse signal at the sync input, the output frame pulses will align to any arbitrary cycle of its associated output clock.sync n - no frame pulse signal presentWhen a frame pulse signal is present at the sync input, the DPLL will align the output frame pulses to the output clock edge that is aligned to the input frame pulse.ref n sync nn = 0, 1, 2n = 0, 1, 2diff_clk/sdh_clk/p_clksdh_fp/p_fpZL30122Data Sheet Each of the ref inputs accept a single-ended LVCMOS clock with a frequency ranging from 2kHz to 77.76MHz. Built-in frequency detection circuitry automatically determines the frequency of the reference if its frequency is within the set of pre-defined frequencies as shown in Table 2. Custom frequencies definable in multiples of 8kHz are also available.2 kHz8 kHz64 kHz1.544 MHz2.048 MHz6.48 MHz8.192 MHz16.384 MHz19.44 MHz38.88 MHz77.76 MHzTable 2 - Set of Pre-Defined Auto-Detect Clock FrequenciesEach of the sync inputs accept a single-ended LVCMOS frame pulse. Since alignment is determined from the rising edge of the frame pulse, there is no duty cycle restriction on this input, but there is a minimum pulse width requirement of 5ns. Frequency detection for the sync inputs is automatic for the supported frame pulse frequencies shown in Table 3.166.67 Hz(48x 125 µs frames)400 Hz1 kHz2 kHz8 kHz64 kHzTable 3 - Set of Pre-Defined Auto-Detect Sync Frequencies1.4 Ref and Sync MonitoringAll input references (ref0 to ref2) are monitored for frequency accuracy and phase regularity. New references are qualified before they can be selected as a synchronization source, and qualified references are continuously monitored to ensure that they are suitable for synchronization. The process of qualifying a reference depends on four levels of monitoring.Single Cycle Monitor (SCM)The SCM block measures the period of each reference clock cycle to detect phase irregularities or a missing clock edge. In general, if the measured period deviates by more than 50% from the nominal period, then an SCM failure (scm_fail) is declared.ZL30122Data SheetCoarse Frequency Monitor (CFM)The CFM block monitors the reference frequency over a measurement period of 30 µs so that it can quickly detect large changes in frequency. A CFM failure (cfm_fail) is triggered when the frequency has changed by more than 3%or approximately 30000ppm.Precise Frequency Monitor (PFM)The PFM block measures the frequency accuracy of the reference over a 10 second interval. To ensure an accurate frequency measurement, the PFM measurement interval is re-initiated if phase or frequency irregularities are detected by the SCM or CFM. The PFM provides a level of hysteresis between the acceptance range and the rejection range to prevent a failure indication from toggling between valid and invalid for references that are on the edge of the acceptance range.When determining the frequency accuracy of the reference input, the PFM uses the external oscillator’s output frequency (f ocsi ) as its point of reference. Guard Soak Timer (GST)The GST block mimics the operation of an analog integrator by accumulating failure events from the CFM and the SCM blocks and applying a selectable rate of decay when no failures are detected.As shown in Figure 5, a GST failure (gst_fail) is triggered when the accumulated failures have reached the upper threshold during the disqualification observation window. When there are no CFM or SCM failures, the accumulator decrements until it reaches its lower threshold during the qualification window.Figure 5 - Behaviour of the Guard Soak Timer during CFM or SCM FailuresSync Ratio MonitorAll sync inputs (sync0 to sync2) are continuously monitored to ensure that there is a correct number of reference clock cycles within the frame pulse period.refCFM or SCM failuresupper thresholdlower thresholdt d - disqualification timet q - qualification time = n * t dt dt qgst_failZL30122Data Sheet1.5 Output Clocks and Frame PulsesThe ZL30122 offers a wide variety of outputs including one low-jitter differential LVPECL clock (diff_clk_p/n ), one SONET/SDH LVCMOS (sdh_clk ) output clock and one programmable LVCMOS (p_clk ) output clock. In addition to the clock outputs, one LVCMOS SONET/SDH frame pulse output (sdh_fp ) and one LVCMOS programmable frame pulse (p_fp ) is also available.Figure 6 - Output ConfigurationThe supported frequencies for the output clocks and frame pulses are shown in Table 4.diff_clk_p/n (LVPECL)sdh_clk (LVCMOS)p_clk (LVCMOS)sdh_fp, p_fp (LVCMOS)6.48 MHz 6.48 MHz 2 kHz166.67 Hz (48x 125 µs frames)19.44 MHz 9.72 MHz N * 8 kHz (up to 77.76MHz)400 Hz 38.88 MHz 12.96 MHz 1 kHz 51.84 MHz 19.44 MHz 2 kHz 77.76 MHz 25.92 MHz 4 kHz 155.52 MHz 38.88 MHz 8 kHz 311.04 MHz 51.84 MHz 32 kHz 622.08 MHz77.76 MHz64 kHzTable 4 - Output Clock and Frame Pulse FrequenciesDPLLp_clk p_fpProgrammable Synthesizersdh_clk sdh_fpSONET/SDHAPLLdiff_clk_p/nZL30122Data Sheet1.6 Configurable Input-to-Output and Output-to-Output DelaysThe ZL30122 allows programmable static delay compensation for controlling input-to-output and output-to-output delays of its clocks and frame pulses.Both the SONET/SDH APLL and the Programmable Synthesizer can be configured to lead or lag the selected input reference clock using the DPLL Fine Delay . The delay is programmed in steps of 119.2ps with a range of -128 to +127 steps giving a total delay adjustment in the range of -15.26ns to +15.14ns. Negative values delay the output clock, positive values advance the output clock.In addition to the delay introduced by the DPLL Fine Delay, the SONET/SDH APLL and programmable synthesizer have the ability to add their own fine delay adjustments using the P Fine Delay and SDH Fine Delay . These delays are also programmable in steps of 119.2ps with a range of -128 to +127 steps.In addition to these delays, the single-ended output clocks of the SONET/SDH and Programmable synthesizers can be independently offset by 90, 180 and 270 degrees using the Coarse Delay , and the SONET/SDH differential outputs can be independently delayed by -1.6ns, 0ns, +1.6 ns or +3.2ns using the Diff Delay . The output frame pulses (sdh_clk, p_fp) can be independently offset with respect to each other using the FP Delay .Figure 7 - Phase Delay AdjustmentsDPLLP Fine Delayp_clk p_fpProgrammable SynthesizerCoarse Delay FP DelayDiff Delaydiff_clk_p/n SONET/SDHAPLLsdh_clk sdh_fpSDH Fine DelayCoarse Delay FP DelayDPLL Fine DelayFeedback SynthesizerZL30122Data Sheet 2.0 Software ConfigurationThe ZL30122 is mainly controlled by accessing software registers through the serial peripheral interface (SPI). The device can be configured to operate in a highly automated manner which minimizes its interaction with the system’s processor, or it can operate in a manual mode where the system processor controls most of the operation of the device.The following table provides a summary of the registers available for status updates and configuration of the device..Addr (Hex)RegisterNameResetValue(Hex)Description TypeMiscellaneous Registers00id_reg A6Chip and version identification and reset readyindication registerR01use_hw_ctrl00Allows some functions of the device to becontrolled by hardware pinsR/WInterrupts02ref_fail_isr FF Reference failure interrupt service register R 03dpll_isr70DPLL interrupt service register StickR 04Reserved Leave as default05ref_mon_fail_0FF Ref0 and ref1 failure indications StickR 06ref_mon_fail_1FF Ref2 failure indication.StickR 07Reserved Leave as default08Reserved Leave as default09ref_fail_isr_mask00Reference failure interrupt service registermaskR/W 0A dpll_isr_mask00DPLL interrupt service register mask R/W 0B Reserved Leave as default0C ref_mon_fail_mask_0FF Control register to mask each failure indicatorfor ref0 and ref1R/W0D ref_mon_fail_mask_1FF Control register to mask failure indicator forref2R/W 0E Reserved Leave as default0F Reserved Leave as defaultReference Monitor Setup10detected_ref_0FF Ref0 and ref1 auto-detected frequency valuestatus registerR11detected_ref_1FF Ref2 auto-detected frequency value statusregisterR 12Reserved Leave as default R 13Reserved Leave as default RTable 5 - Register MapZL30122Data Sheet14detected_sync_0EE Sync0 and sync1 auto-detected frequency value and sync failure status registerR 15detected_sync_10E Sync2 auto-detected frequency value and sync valid status registerR 16oor_ctrl_033Control register for the ref0 and ref1 out of range limitR/W 17oor_ctrl_133Control register for the ref2 out of range limit R/W18Reserved Leave as default 19Reserved Leave as default1A gst_mask FF Control register to mask the inputs to the guard soak timer for ref0 - ref2R/W1B Reserved Leave as default1Cgst_qualif_time1A Control register for the guard_soak_timer qualification time and disqualification time for the references R/WDPLL Control1D dpll_ctrl_0See Register Description Control register for the DPLL filter control; phase slope limit, bandwidth and hitless switchingR/W1E dpll_ctrl_1See Register Description Holdover update time, filter_out_en, freq_offset_en, revert enableR/W1F dpll_modesel See Register DescriptionControl register for the DPLL mode of operationR/W20dpll_refsel 00DPLL reference selection or reference selection statusR/W 21dpll_ref_fail_mask3CControl register to mask each failure indicator (SCM, CFM, PFM and GST) used for automatic reference switching and automatic holdover R/W22dpll_wait_to_restore 00Control register to indicate the time to restore a previous failed referenceR/W 23dpll_ref_rev_ctrl 00Control register for the ref0 to ref2 enable revertive signalsR/W 24dpll_ref_pri_ctrl_010Control register for the ref0 and ref1 priority valuesR/W 25dpll_ref_pri_ctrl_132Control register for the ref2 priority values R/W26Reserved Leave as default 27ReservedLeave as defaultAddr (Hex)Register NameReset Value (Hex)DescriptionType Table 5 - Register Map (continued)ZL30122Data Sheet28dpll_lock_holdover_status04DPLL lock and holdover status register R29Reserved03Leave as default R/W2A -35Reserved Leave as defaultProgrammable Synthesizer Configuration Registers36p_enable8F Control register to enable the p_clk and p_fpoutputs of the programmable synthesizerR/W 37p_run0F Control register to generate p_clk, p_fp R/W 38p_freq_000Control register for the [7:0] bits of the N ofN*8k clkR/W39p_freq_101Control register for the [13:8] bits of the N ofN*8k clkR/W3A p_clk_offset9000Control register for the p_clk phase positioncoarse tuningR/W3B Reserved Leave as default3C Reserved Leave as default3D p_offset_fine00Control register for the output/output phasealignment fine tuning for the programmablesynthesizerR/W3E p_fp_freq05Control register to select the p_fp frame pulsefrequencyR/W3F p_fp_type83Control register to select p_fp type R/W 40p_fp_fine_offset_000Bits [7:0] of the programmable frame pulsephase offset in multiples of 1/262.14MHzR/W41p_fp_fine_offset_100Bits [15:8] of the programmable frame pulsephase offset in multiples of 1/262.14MHzR/W42p_fp_coarse_offset00Programmable frame pulse phase offset inmultiples of 8kHz cyclesR/W43 -4FReserved Leave as defaultSDH Configuration Registers50sdh_enable8F Control register to enable sdh_clk and sdh_fp R/W 51sdh_run0F Control register to generate sdh_clk andsdh_fpR/W52sdh_clk_div42Control register for the sdh_clk frequencyselectionR/W53sdh_clk_offset9000Control register for the sdh_clk phase positioncoarse tuning R/WAddr (Hex)RegisterNameResetValue(Hex)Description Type Table 5 - Register Map (continued)。
- 1、下载文档前请自行甄别文档内容的完整性,平台不提供额外的编辑、内容补充、找答案等附加服务。
- 2、"仅部分预览"的文档,不可在线预览部分如存在完整性等问题,可反馈申请退款(可完整预览的文档不适用该条件!)。
- 3、如文档侵犯您的权益,请联系客服反馈,我们会尽快为您处理(人工客服工作时间:9:00-18:30)。
LG
Specifications
Higher Capacitance, Low ESR, High ripple current.Load life of 2000 hours at 105°C.Radial lead type :
Lead free flow soldering condition correspondence Adapted to the RoHS directive (2002/95/EC ).
series
Item
Performance Characteristics
Category Temperature Range Rated Voltage Range Rated Capacitance Range Capacitance Tolerance tan δESR ( 1)
Leakage Current ( 2)
Characteristics of Temperature Impedance Ratio
Endurance
Damp Heat
Resistance to Soldering Heat
Marking
–55 to +105°C 2.5 to 16V 330 to 3900µF ± 20% at 120Hz, 20°C
Not more than value of Standard ratings at 120Hz, 20°C Not more than value of Standard ratings at 100kHz, 20°C
Not more than value of Standard ratings. After 2 minute's application of rated voltage. 20°C
Z+105°C / Z+20°C 1.25 (100kHz )Z -55°C / Z +20°C 1.25
After 2000 hours' application of rated voltage
at 105°C, capacitors meet the specified value for life characteristics listed at right.
After 1000 hours' application of rated voltage
at 60°C 90%RH, capacitors meet the specified value for life characteristics listed at right.
To comply with recommended conditions for reflow soldering. Pre-heating shall be done at 150 to 200°C and for 60 to 180 sec.Peak temp. is 265°C, within 10 sec.
Measurement for solder temperature profile shall be made at a point on the terminal
nearest where the terminals protrude through the soldering side of PC board.Navy blue print on the case top.
CONDUCTIVE POLYMER
ALUMINUM SOLID ELECTROLYTIC CAPACITORS
Capacitance change tan δESR ( 1)
Leakage current ( 2)
Within ± 20% of initial value ( 3)150% or less of the initial specified value 150% or less of the initial specified value Initial specified value or less
Capacitance change tan δESR ( 1)
Leakage current ( 2)
Within ± 20% of initial value ( 3)150% or less of the initial specified value 150% or less of the initial specified value Initial specified value or less
Capacitance change tan δESR ( 1)
Leakage current ( 2)
Within ± 10% of initial value ( 3)130% or less of the initial specified value 130% or less of the initial specified value Initial specified value or less
( 1) ESR measurements should be made at a point on the terminal nearest the end seal of the capacitor.
( 2) Conditioning : If there is doubt about the measured result, measurement should be made again after the rated voltage is applied for 120 minutes at the temperature of 105°C.
( 3) Initial value : The value before test of examination of resistance to soldering.
Radial Lead Type, Higher Capacitance
LF
LG
Higher Capacitance
series
LG
CONDUCTIVE POLYMER
ALUMINUM SOLID ELECTROLYTIC CAPACITORS
Dimensions
Type numbering system (Example : 4V 1200µF)
Standard ratings
φD L P φd
8.0φ8 × 9L φ8 × 12L 8.53.50.6
8.011.53.50.6
Size φ10 × 13L 10.012.55.00.6
(mm)
Design, Specifications are subject to change without notice.
Configuration
Printed in Japan T .2007.B.3C
φD × L
Code 8 × 9CO 8 × 12DO 10 × 13
DO
V Code
2.5e
4g
Voltage
6.3j
10A
16C。