直接蒸汽加热板式精馏塔设计
化工原理课程设计,甲醇和水的分离精馏塔的设计
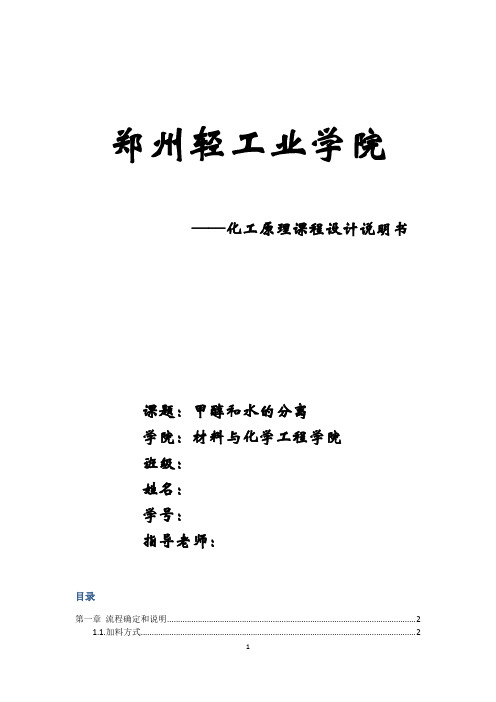
郑州轻工业学院——化工原理课程设计说明书课题:甲醇和水的分离学院:材料与化学工程学院班级:姓名:学号:指导老师:目录第一章流程确定和说明 (2)1.1.加料方式 (2)1.2.进料状况 (2)1.3.塔型的选择 (2)1.4.塔顶的冷凝方式 (2)1.5.回流方式 (3)1.6.加热方式 (3)第二章板式精馏塔的工艺计算 (3)2.1物料衡算 (3)2.3 塔板数的确定及实际塔板数的求取 (5)2.3.1理论板数的计算 (5)2.3.2求塔的气液相负荷 (5)2.3.3温度组成图与液体平均粘度的计算 (6)2.3.4 实际板数 (7)2.3.5试差法求塔顶、塔底、进料板温度 (7)第三章精馏塔的工艺条件及物性参数的计算 (9)3.1 平均分子量的确定 (9)3.2平均密度的确定 (10)3.3. 液体平均比表面积张力的计算 (11)第四章精馏塔的工艺尺寸计算 (12)4.1气液相体积流率 (12)4.1.1 精馏段气液相体积流率: (12)4.1.2提馏段的气液相体积流率: (13)第五章塔板主要工艺尺寸的计算 (14)5.1 溢流装置的计算 (14)5.1.1 堰长 (14)5.1.2溢流堰高度: (15)5.1.3弓形降液管宽度 (15)5.1.4 降液管底隙高度 (16)5.1.5 塔板位置及浮阀数目与排列 (16)第六章板式塔得结构与附属设备 (24)6.1附件的计算 (24)6.1.1接管 (24)6.1.2 冷凝器 (27)6.1.3再沸器 (28)第七章参考书录 (28)第八章设计心得体会 (29)第一章流程确定和说明1.1.加料方式加料方式有两种:高位槽加料和泵直接加料。
采用高位槽加料,通过控制液位高度,可以得到稳定的流速和流量,通过重力加料,可以节省一笔动力费用,但由于多了高位槽,建设费用相应增加;采用泵加料,受泵的影响,流量不太稳定,流速不太稳定,流速不太稳定,从而影响了传质效率,但结构简单,安装方便。
板式精馏塔设计

板式精馏塔设计一.生产工艺流程设计化工装置设计中,生产工艺流程设计的目的是,确定生产方式之后,以流程图的形式表示出由原料到产品的整个生产过程中物料被加工的顺序,及各段物料的流向。
并表示出生产中采用的化工操作单元及设备。
1.化工工艺流程草图便于进行物料衡算和热量衡算。
定性地标出物料由原料转化为产品的变化、流向及所采用的化工过程及设备。
2.带控制点的流程图此图表示出全部工艺设备、物料管线、阀件、设备的辅助管线以及工艺和自控仪表、图例、符号等。
二.精馏塔的工艺设计1.流程的选择精馏装置是由精馏塔、再沸器、冷凝器等设备组成。
精馏塔消耗的热量很多,绝大部分用于反复蒸发回流液,其余被塔顶冷凝器中的冷却水及残液冷却剂带走。
塔的热效率低节能是确定流程时应考虑的一个重要问题。
从经济方面考虑,尽量利用整个系统的热能,降低费用;另一方面要考虑操作的稳定性,保证质量。
例如:塔顶蒸汽冷凝放出大量热,但能位低,不能作塔釜热源;釜残液温度虽高,若直接预热料液,传热系数小(液—液换热)且采用温控措施。
总之在确定流程时需要考虑经济和操作控制等因素。
2.塔压的选择确定操作压力时,应根据精馏物料的工艺特性,兼技术上的可行性和经济上的合理性进行考虑。
一般除热敏性物料外,凡常压精馏能达到要求的都应采用常压,对热敏性或混合液沸点过高宜采用减压,对常压下气态物料应采用加压精馏。
3.进料状态料液的热状态与所需的塔板数目、加料板的位置及塔径的大小有密切的关系。
五种进料状况中以泡点进料最常见。
这种进料的优点是塔的操作易控制,不受季节气温变化的影响,而且精馏段、提馏段可采用相同的塔径,在设计和制造上较为方便,但需增设预热器。
4.加热方式蒸馏釜的加热方式大都采用间接蒸汽加热,设置再沸器。
5.回流比的选择回流比R 不仅影响理论塔板数,还影响加热蒸汽量和冷却水的消耗量,影响塔径、再沸器和冷凝器的尺寸及塔板的结构尺寸等。
选择适宜的回流比,主要从经济观点出发,力求使设备费和操作费之和最低。
化工原理板式塔设计
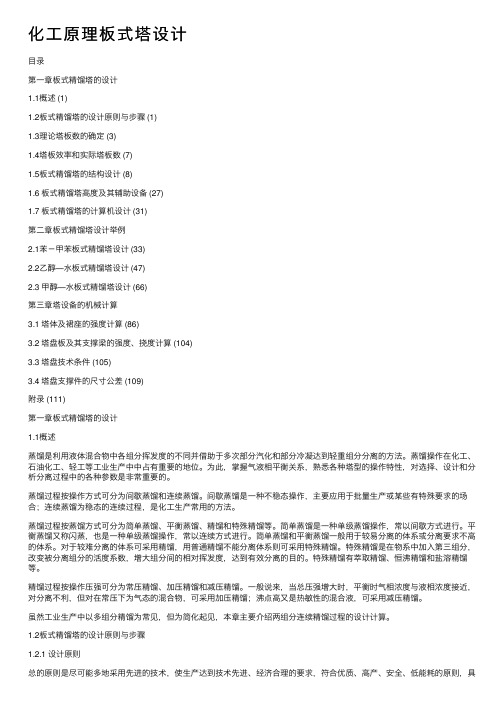
化⼯原理板式塔设计⽬录第⼀章板式精馏塔的设计1.1概述 (1)1.2板式精馏塔的设计原则与步骤 (1)1.3理论塔板数的确定 (3)1.4塔板效率和实际塔板数 (7)1.5板式精馏塔的结构设计 (8)1.6 板式精馏塔⾼度及其辅助设备 (27)1.7 板式精馏塔的计算机设计 (31)第⼆章板式精馏塔设计举例2.1苯-甲苯板式精馏塔设计 (33)2.2⼄醇—⽔板式精馏塔设计 (47)2.3 甲醇—⽔板式精馏塔设计 (66)第三章塔设备的机械计算3.1 塔体及裙座的强度计算 (86)3.2 塔盘板及其⽀撑梁的强度、挠度计算 (104)3.3 塔盘技术条件 (105)3.4 塔盘⽀撑件的尺⼨公差 (109)附录 (111)第⼀章板式精馏塔的设计1.1概述蒸馏是利⽤液体混合物中各组分挥发度的不同并借助于多次部分汽化和部分冷凝达到轻重组分分离的⽅法。
蒸馏操作在化⼯、⽯油化⼯、轻⼯等⼯业⽣产中中占有重要的地位。
为此,掌握⽓液相平衡关系,熟悉各种塔型的操作特性,对选择、设计和分析分离过程中的各种参数是⾮常重要的。
蒸馏过程按操作⽅式可分为间歇蒸馏和连续蒸馏。
间歇蒸馏是⼀种不稳态操作,主要应⽤于批量⽣产或某些有特殊要求的场合;连续蒸馏为稳态的连续过程,是化⼯⽣产常⽤的⽅法。
蒸馏过程按蒸馏⽅式可分为简单蒸馏、平衡蒸馏、精馏和特殊精馏等。
简单蒸馏是⼀种单级蒸馏操作,常以间歇⽅式进⾏。
平衡蒸馏⼜称闪蒸,也是⼀种单级蒸馏操作,常以连续⽅式进⾏。
简单蒸馏和平衡蒸馏⼀般⽤于较易分离的体系或分离要求不⾼的体系。
对于较难分离的体系可采⽤精馏,⽤普通精馏不能分离体系则可采⽤特殊精馏。
特殊精馏是在物系中加⼊第三组分,改变被分离组分的活度系数,增⼤组分间的相对挥发度,达到有效分离的⽬的。
特殊精馏有萃取精馏、恒沸精馏和盐溶精馏等。
精馏过程按操作压强可分为常压精馏、加压精馏和减压精馏。
⼀般说来,当总压强增⼤时,平衡时⽓相浓度与液相浓度接近,对分离不利,但对在常压下为⽓态的混合物,可采⽤加压精馏;沸点⾼⼜是热敏性的混合液,可采⽤减压精馏。
丙酮-水板式精馏塔设计说明书

目录摘要 (I)Abstract (II)引言 (1)第1章设计条件与任务 (2)1.1设计条件 (2)1.2设计任务 (2)第2章设计方案的确定 (3)第3章精馏塔的工艺设计 (4)3.1全塔物料衡算 (4)3.1.1原料液、塔顶及塔底产品的摩尔分数 (4)3.1.2原料液、塔顶及塔底产品的平均摩尔质量 (4)3.1.3物料衡算进料处理量 (4)3.1.4物料衡算 (4)3.2实际回流比 (5)3.2.1最小回流比及实际回流比确定 (5)3.2.2操作线方程 (6)3.2.3汽、液相热负荷计算 (6)3.3理论塔板数确定 (6)3.4实际塔板数确定 (7)3.5精馏塔的工艺条件及有关物性数据计算 (8)3.5.1操作压力计算 (8)3.5.2操作温度计算 (9)3.5.3平均摩尔质量计算 (9)3.5.4平均密度计算 (10)3.5.5液体平均表面张力计算 (10)3.6精馏塔的塔体工艺尺寸计算 (12)3.6.1塔径计算 (12)3.6.2精馏塔有效高度计算 (13)第4章塔板工艺尺寸的计算 (14)4.1精馏段塔板工艺尺寸的计算 (14)4.1.1溢流装置计算 (14)4.1.2塔板设计 (15)4.2提馏段塔板工艺尺寸设计 (15)4.2.1溢流装置计算 (15)4.2.2塔板设计 (16)4.3塔板的流体力学性能的验算 (16)4.3.1精馏段 (16)4.3.2提馏段 (17)4.4板塔的负荷性能图 (18)4.4.1精馏塔 (18)4.4.2提馏段 (19)第5章板式塔的结构 (21)5.1塔体结构 (21)5.1.1塔顶空间 (21)5.1.2塔底空间 (21)5.1.3人孔 (21)5.1.4塔高 (21)5.2塔板结构 (21)第6章附属设备 (21)6.1冷凝器 (21)6.2原料预热器 (22)第7章接管尺寸的确定 (23)7.1蒸汽接管 (23)7.1.1塔顶蒸汽出料管 (23)7.1.2塔釜进气管 (23)7.2液流管 (23)7.2.1进料管 (23)7.2.2回流管 (23)7.2.3塔釜出料管 (23)第8章附属高度确定 (24)8.1筒体 (24)8.2封头 (24)8.3塔顶空间 (24)8.4塔底空间 (24)8.5人孔 (24)8.6支座 (24)8.7塔总体高度 (24)第9章设计结果汇总 (25)设计小结与体会 (27)参考文献 (28)引言在炼油、石油加工、精细化工、食品、医药等部门,塔设备属于使用量大,应用面广的重要单元设备。
精馏塔塔设计及相关计算

---------------------------------------------------------------最新资料推荐------------------------------------------------------精馏塔塔设计及相关计算2011板式精馏塔设计任务书板式精馏塔的设计选型及相关计算设计计算满足生产要求的板式精馏塔,包括参数选定、塔主题设计、配套设计及相关设计图Administrator 09 级化工 2 班xx2011/12/11/ 27目录板式精馏塔设计任务....................................... 3一.设计题目. (3)二.操作条件 (3)三.塔板类型 (3)四.相关物性参数 ................................................ 3 五.设计内容 .................................................... 3设计方案 ...................................错误!未定义书签。
一.设计方案的思考 .............................................. 6 二.工艺流程 . (6)板式精馏塔的工艺计算书 ................................... 7一.设计方案的确定及工艺流程的说明............................... 二.全塔的物料衡算 ............................................... 三.塔板数的确定 ................................................. 四.塔的精馏段操作工艺条件及相关物性数据的计算................... 五.精馏段的汽液负荷计---------------------------------------------------------------最新资料推荐------------------------------------------------------ 算 ......................................... 六.塔和塔板主要工艺结构尺寸的计算 ............................... 七.塔板负荷性能图 ...............................................筛板塔设计计算结果 .....................错误!未定义书签。
化工原理课程设计,甲醇和水的分离精馏塔的设计说明

轻工业学院——化工原理课程设计说明书课题:甲醇和水的分离学院:材料与化学工程学院班级::学号:指导老师:目录第一章流程确定和说明 (1)1.1.加料方式 (1)1.2.进料状况 (2)11.3.塔型的选择 (2)1.4.塔顶的冷凝方式 (2)1.5.回流方式 (2)1.6.加热方式 (3)第二章板式精馏塔的工艺计算 (3)2.1物料衡算 (3)2.3 塔板数的确定及实际塔板数的求取 (5)2.3.1理论板数的计算 (5)2.3.2求塔的气液相负荷 (5)2.3.3温度组成图与液体平均粘度的计算 (6)2.3.4 实际板数 (7)2.3.5试差法求塔顶、塔底、进料板温度 (7)第三章精馏塔的工艺条件及物性参数的计算 (9)3.1 平均分子量的确定 (9)3.2平均密度的确定 (10)3.3. 液体平均比表面积力的计算 (11)第四章精馏塔的工艺尺寸计算 (12)4.1气液相体积流率 (12)4.1.1 精馏段气液相体积流率: (12)4.1.2提馏段的气液相体积流率: (13)第五章塔板主要工艺尺寸的计算 (14)5.1 溢流装置的计算 (14)5.1.1 堰长 (14)5.1.2溢流堰高度: (15)5.1.3弓形降液管宽度 (15)5.1.4 降液管底隙高度 (16)5.1.5 塔板位置及浮阀数目与排列 (16)第六章板式塔得结构与附属设备 (23)6.1附件的计算 (23)6.1.1接管 (23)6.1.2 冷凝器 (27)6.1.3再沸器 (28)第七章参考书录 (28)第八章设计心得体会 (29)第一章流程确定和说明1.1.加料方式加料方式有两种:高位槽加料和泵直接加料。
采用高位槽加料,通过控制液位高度,可以得到稳定的流速和流量,通过重力加料,可以节省一笔动力费用,但由于多了高位槽,建设费用相应增加;采用泵加料,受泵的影响,流量不太稳定,流速不太稳定,流速不太稳定,从而影响了传质效率,但结构简单,安装方便。
精馏塔(板式)设计

PA α= ∗ PB
(三)塔板数的确定 1、作出x-y相图 、作出 相图 2、最小回流比及操作回流比 、 3、理论板数及加料位置 、 ①求精馏塔的汽、液相负荷 求精馏塔的汽、
∗
R = 1.5 Rmin
L′ = L + qF = RD + qF
V ′ = V + (q − 1) F = ( R + 1) D + (q − 1) F
化工原理课程设计
(6)冷凝器的选择 ) 塔顶产品(全凝器)和塔釜产品(冷却器) 塔顶产品(全凝器)和塔釜产品(冷却器) (7)加料方式的选择 ) 高位槽或泵 (8)工艺流程 ) 3、正戊烷和正己烷的性质、用途等 、正戊烷和正己烷的性质、
化工原理课程设计
二.工艺计算
主要内容是( 主要内容是(1)物料衡算 (2)确定回流比 (3)确定理论板数和实 际板数 (4)塔的气液负荷计算 (5)热量衡算 塔设备的生产能力一般以千克/小时或吨/年表示, 塔设备的生产能力一般以千克/小时或吨/年表示,但在理论板 计算时均须转换成kmol/h,在塔板设计时 在塔板设计时, 计算时均须转换成kmol/h,在塔板设计时,气液流量又须用体积 流量m /s表示 因此要注意不同的场合应使用不同的流量单位。 表示。 流量 m3/s 表示 。 因此要注意不同的场合应使用不同的流量单位 。 (一)全塔物料衡算 1、原料液及塔顶、塔底产品的摩尔分数 、原料液及塔顶、
化工原理课程设计
②求精馏段、提馏段的操作线方程 求精馏段、
R xD y= x+ R +1 R +1
③作图求出理论板数 ④逐板计算求理论板数
WxW L + qF y′ = x′ − L + qF − W L + qF − W
丙酮-水溶液直接蒸汽加热筛板精馏塔设计

第一部分设计概述一、设计题目:筛板式连续精馏塔及其主要附属设备设计二、工艺条件:生产能力:30000吨/年(料液)年工作日:300天原料组成:25%丙酮,75%水(质量分率,下同)产品组成:馏出液 99%丙酮,釜液2%丙酮操作压力:塔顶压强为常压进料温度:泡点进料状况:泡点加热方式:直接蒸汽加热回流比:自选三、设计内容1、确定精馏装置流程,绘出流程示意图。
2、工艺参数的确定基础数据的查取及估算,工艺过程的物料衡算及热量衡算,理论塔板数,塔板效率,实际塔板数等。
3、主要设备的工艺尺寸计算板间距,塔径,塔高,溢流装置,塔盘布置等。
4、流体力学计算流体力学验算,操作负荷性能图及操作弹性。
5 、主要附属设备设计计算及选型塔顶全凝器设计计算:热负荷,载热体用量,选型及流体力学计算。
料液泵设计计算:流程计算及选型。
四、工艺流程图丙酮—水溶液经预热至泡点后,用泵送入精馏塔。
塔顶上升蒸气采用全冷凝后,部分回流,其余作为塔顶产品经冷却器冷却后送至贮槽。
塔釜采用间接蒸汽再沸器供热,塔底产品经冷却后送入贮槽。
精馏装置有精馏塔、原料预热器、冷凝器、釜液冷却器和产品冷却器等设备。
热量自塔釜输入,物料在塔内经多次部分气化与部分冷凝进行精馏分离,由冷凝器和冷却器中的冷却介质将余热带走。
丙酮—水混合液原料经预热器加热到泡点温度后送入精馏塔进料板,在进料板上与自塔上部下降的的回流液体汇合后,逐板溢流,最后流入塔底。
在每层板上,回流液体与上升蒸汽互相接触,进行热和质的传递过程。
流程示意图如下图图1:精馏装置流程示意图第二部分塔的工艺计算一、查阅文献,整理有关物性数据(1)水和丙酮的性质表1.水和丙酮的粘度温度50 60 70 80 90 100水粘度mpa0.592 0.469 0.40 0.33 0.318 0.248丙酮粘度mpa0.26 0.231 0.209 0.199 0.179 0.160表2.水和丙酮表面张力温度50 60 70 80 90 100水表面张力67.7 66.0 64.3 62.7 60.1 58.4丙酮表面张力19.5 18.8 17.7 16.3 15.2 14.3表3.水和丙酮密度温度50 60 70 80 90 100相对密度0.760 0.750 0.735 0.721 0.710 0.699水998.1 983.2 977.8 971.8 965.3 958.4 丙酮758.56 737.4 718.68 700.67 685.36 669.92 表4.水和丙酮的物理性质分子量沸点临界温度K 临界压强kpa 水18.02 100 647.45 22050丙酮58.08 56.2 508.1 4701.50表5. 丙酮—水系统t—x—y数据沸点t/℃丙酮摩尔数x y10000 920.01 0.279 84.20.0250.47 75.60.050.63 66.90.10.754 62.40.20.813 61.10.30.832 60.30.40.842 59.80.50.851 59.20.60.86358.80.70.87558.20.80.89757.40.90.93556.90.950.96256.7 0.975 0.97956.5 1 1由以上数据可作出t-y(x)图如下由以上数据作出相平衡y-x线图(2)进料液及塔顶、塔底产品的摩尔分数酮的摩尔质量 A M =58.08 Kg/kmol 水的摩尔质量 B M =18.02 Kg/kmol平均摩尔质量0937.002.18/75.008.58/25.008.58/25.0=+=F x 968.002.18/01.008.58/99.008.58/99.0=+=D x 00629.002.18/98.008.58/02.008.58/02.0=+=W xM F =0.0937⨯58.08+(1-0.0937)⨯18.02=21.774 kg/kmol M D = 0.968⨯58.08+ (1-0.968) ⨯18.02=56.798 kg/kmol M W =0.00629⨯58.08+(1-0.00629)⨯18.02=18.272 kg/kmol30000000/(30024)191.3621.774F ⨯== kg/kmol最小回流比由题设可得泡点进料q=1则F x = e x ,又附图可得e x =0.0937, e y =0.749。
精馏塔直接蒸汽加热流程

精馏塔直接蒸汽加热流程
精馏塔是化工工程中常用的设备,用于将混合物分离成不同成分。
精馏塔直接
蒸汽加热流程是一种常见的操作方式,通过直接将蒸汽传热到混合物中,实现混合物的分馏。
下面将介绍精馏塔直接蒸汽加热的流程及工作原理。
工作原理
精馏塔直接蒸汽加热是利用蒸汽的高温和潜热来提供热量,将其传递给混合物,使混合物中的组分达到相应的沸点,从而实现分馏的目的。
在精馏塔中,较低沸点的组分会先汽化,通过蒸汽向上升腾,较高沸点的组分则沿着填料向下流动,从而实现组分的分离。
流程步骤
1.进料加热:混合物首先通过加热器进行预热,然后进入精馏塔的顶
部。
蒸汽从底部引入,通过加热器预热的混合物会在塔内逐渐升温。
2.蒸汽加热:蒸汽在塔内与混合物接触,释放热量给混合物,使混合
物中的组分逐渐汽化。
蒸汽在与混合物接触时会冷却凝结,形成液体,同时传递热量给混合物。
3.分馏:在整个过程中,较低沸点的组分会先汽化并向上升腾,最终
通过顶部出口排出,而较高沸点的组分则沿着填料向下流动,最终通过底部出口排出。
4.调节操作:根据需要,可以通过控制进料速度、蒸汽量、温度等参
数来调节分馏过程,以实现所需的分离效果。
优势和应用
精馏塔直接蒸汽加热具有操作简单、能耗低、效率高的优点。
它常用于石油化工、化工制药、食品加工等领域,用于纯化、分离各类混合物。
在实际应用中,需要根据待分离混合物的性质和要求来选择合适的操作参数和
设备设计,以达到最佳的分离效果。
通过精馏塔直接蒸汽加热流程,可以高效地将不同成分分离出来,实现原料的
充分利用和产品质量的提升。
直接蒸汽加热板式精馏塔设计

双组分溶液直接蒸汽加热板式精馏塔设计设计任务:规定F 、xF 、xD 、xW ,设计出能完成分离任务的板式精馏塔 1. 回流比● 最小回流比设夹紧点在精馏段,其坐标为(xe,ye)则min D ee ex y R y x -=-(1)设夹紧点在提馏段,其坐标为(xe,ye)min min 0(1)(1)e e Wy R D qF LV R D q F x x -+==+--- (2) 所需基础数据:气液相平衡数据 丙酮-水xi = [0 0.01 0.02 0.05 0.10 0.15 0.20 0.30 0.40 0.50 0.60 0.70 0.80 0.90 0.95 1.0]; % 液相丙酮平衡浓度yi = [0 0.253 0.425 0.624 0.755 0.793 0.815 0.830 0.839 0.849 0.859 0.874 0.898 0.935 0.963 1.0]; % 汽相丙酮平衡浓度ti=[ 100 92.7 86.5 75.8 66.5 63.4 62.1 61.0 60.4 60.0 59.7 59.0 58.2 57.5 57.0 56.13 ];%平衡温度 甲醇-水xi = [0 0.02 0.04 0.06 0.08 0.10 0.15 0.20 0.30 0.40 0.50 0.60 0.70 0.80 0.90 0.95 1.0]; % 液相甲醇平衡浓度yi = [0 0.134 0.234 0.304 0.365 0.418 0.517 0.579 0.665 0.729 0.779 0.825 0.870 0.915 0.958 0.979 1.00]; % 汽相甲醇平衡浓度ti=[ 100 96.4 93.5 91.2 89.3 87.7 84.4 81.7 78.0 75.3 73.1 71.2 69.3 67.6 66.0 65.0 64.5 ];%平衡温度来源:王志魁.化工原理(第三版),北京:化学工业出版社,2004 ● 确定操作回流比min(1.1~2.0)R R =用Matlab 或Excel 工具求出N 与R 间的关系以确定适宜的回流比。
《化工原理课程设计》板式精馏塔设计报告
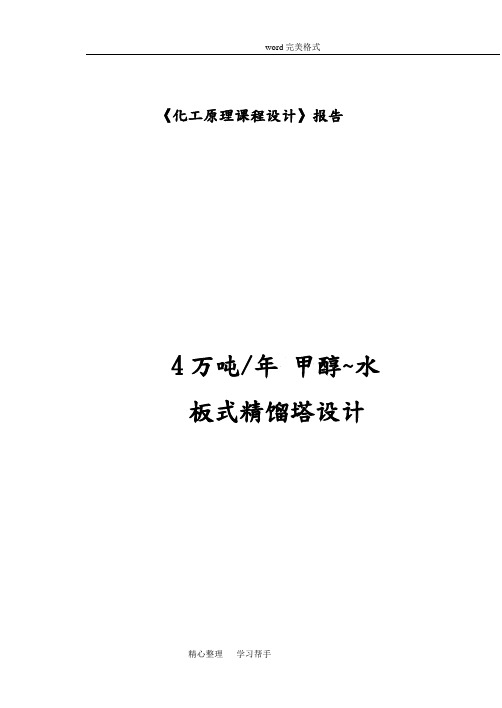
《化工原理课程设计》报告4万吨/年甲醇~水板式精馏塔设计目录一、概述 (4)1.1 设计依据·································错误!未定义书签。
1.2 技术来源·································错误!未定义书签。
1.3 设计任务及要求 (5)二:计算过程 (7)1. 塔型选择 (7)2. 操作条件的确定 (8)2.1 操作压力 (8)2.2 进料状态 (8)2.3 加热方式 (8)2.4 热能利用 (8)3. 有关的工艺计算 (9)3.1 最小回流比及操作回流比的确定·········错误!未定义书签。
3.2 塔顶产品产量、釜残液量及加热蒸汽量的计算错误!未定义书签。
3.3 全凝器冷凝介质的消耗量 (17)3.4 热能利用·····························错误!未定义书签。
精馏塔设计说明书(最全)
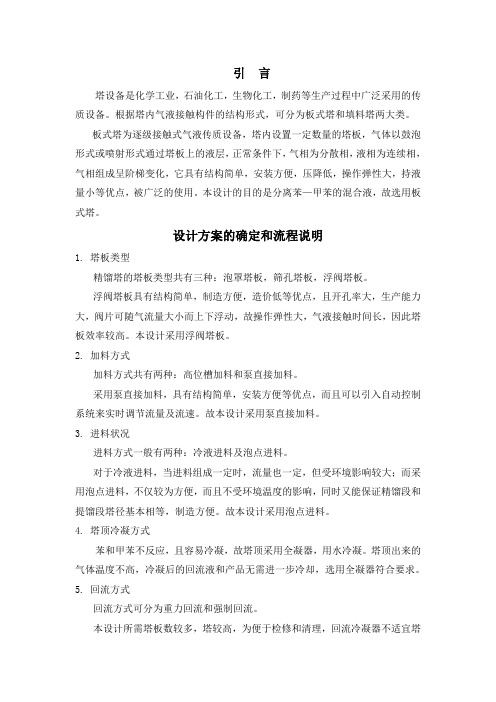
引言塔设备是化学工业,石油化工,生物化工,制药等生产过程中广泛采用的传质设备。
根据塔内气液接触构件的结构形式,可分为板式塔和填料塔两大类。
板式塔为逐级接触式气液传质设备,塔内设置一定数量的塔板,气体以鼓泡形式或喷射形式通过塔板上的液层,正常条件下,气相为分散相,液相为连续相,气相组成呈阶梯变化,它具有结构简单,安装方便,压降低,操作弹性大,持液量小等优点,被广泛的使用。
本设计的目的是分离苯—甲苯的混合液,故选用板式塔。
设计方案的确定和流程说明1.塔板类型精馏塔的塔板类型共有三种:泡罩塔板,筛孔塔板,浮阀塔板。
浮阀塔板具有结构简单,制造方便,造价低等优点,且开孔率大,生产能力大,阀片可随气流量大小而上下浮动,故操作弹性大,气液接触时间长,因此塔板效率较高。
本设计采用浮阀塔板。
2. 加料方式加料方式共有两种:高位槽加料和泵直接加料。
采用泵直接加料,具有结构简单,安装方便等优点,而且可以引入自动控制系统来实时调节流量及流速。
故本设计采用泵直接加料。
3. 进料状况进料方式一般有两种:冷液进料及泡点进料。
对于冷液进料,当进料组成一定时,流量也一定,但受环境影响较大;而采用泡点进料,不仅较为方便,而且不受环境温度的影响,同时又能保证精馏段和提馏段塔径基本相等,制造方便。
故本设计采用泡点进料。
4. 塔顶冷凝方式苯和甲苯不反应,且容易冷凝,故塔顶采用全凝器,用水冷凝。
塔顶出来的气体温度不高,冷凝后的回流液和产品无需进一步冷却,选用全凝器符合要求。
5. 回流方式回流方式可分为重力回流和强制回流。
本设计所需塔板数较多,塔较高,为便于检修和清理,回流冷凝器不适宜塔顶安装,故采用强制回流。
6. 加热方式加热方式分为直接蒸气和间接蒸气加热。
直接蒸气加热在一定回流比条件下,塔底蒸气对回流液有稀释作用,从而会使理论塔板数增加,设备费用上升。
故本设计采用间接蒸气加热方式。
7. 操作压力苯和甲苯在常压下相对挥发度相差比较大,因此在常压下也能比较容易分离,故本设计采用常压精馏。
化工原理课程设计—板式精馏塔的设计
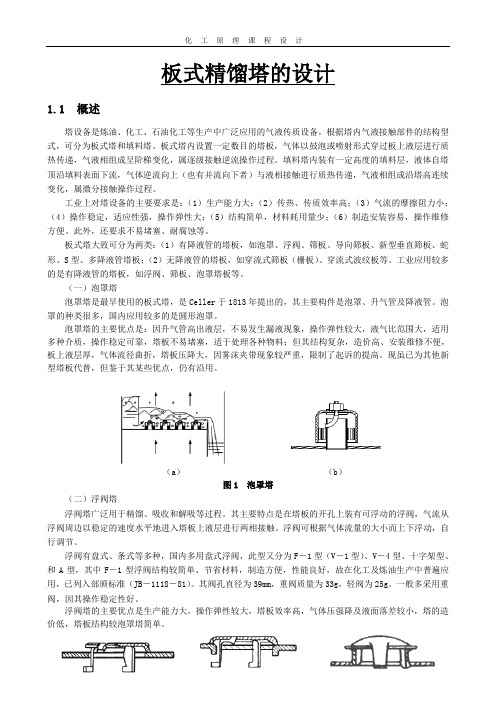
板式精馏塔的设计1.1 概述塔设备是炼油、化工、石油化工等生产中广泛应用的气液传质设备。
根据塔内气液接触部件的结构型式,可分为板式塔和填料塔。
板式塔内设置一定数目的塔板,气体以鼓泡或喷射形式穿过板上液层进行质热传递,气液相组成呈阶梯变化,属逐级接触逆流操作过程。
填料塔内装有一定高度的填料层,液体自塔顶沿填料表面下流,气体逆流向上(也有并流向下者)与液相接触进行质热传递,气液相组成沿塔高连续变化,属微分接触操作过程。
工业上对塔设备的主要要求是:(1)生产能力大;(2)传热、传质效率高;(3)气流的摩擦阻力小;(4)操作稳定,适应性强,操作弹性大;(5)结构简单,材料耗用量少;(6)制造安装容易,操作维修方便。
此外,还要求不易堵塞、耐腐蚀等。
板式塔大致可分为两类:(1)有降液管的塔板,如泡罩、浮阀、筛板、导向筛板、新型垂直筛板、蛇形、S型、多降液管塔板;(2)无降液管的塔板,如穿流式筛板(栅板)、穿流式波纹板等。
工业应用较多的是有降液管的塔板,如浮阀、筛板、泡罩塔板等。
(一)泡罩塔泡罩塔是最早使用的板式塔,是Celler于1813年提出的,其主要构件是泡罩、升气管及降液管。
泡罩的种类很多,国内应用较多的是圆形泡罩。
泡罩塔的主要优点是:因升气管高出液层,不易发生漏液现象,操作弹性较大,液气比范围大,适用多种介质,操作稳定可靠,塔板不易堵塞,适于处理各种物料;但其结构复杂,造价高、安装维修不便,板上液层厚,气体流径曲折,塔板压降大,因雾沫夹带现象较严重,限制了起诉的提高。
现虽已为其他新型塔板代替,但鉴于其某些优点,仍有沿用。
(a b)图1 泡罩塔(二)浮阀塔浮阀塔广泛用于精馏、吸收和解吸等过程。
其主要特点是在塔板的开孔上装有可浮动的浮阀,气流从浮阀周边以稳定的速度水平地进入塔板上液层进行两相接触。
浮阀可根据气体流量的大小而上下浮动,自行调节。
浮阀有盘式、条式等多种,国内多用盘式浮阀,此型又分为F-1型(V-1型)、V-4型、十字架型、和A型,其中F-1型浮阀结构较简单、节省材料,制造方便,性能良好,故在化工及炼油生产中普遍应用,已列入部颁标准(JB-1118-81)。
乙醇-水课程设计--乙醇——水筛板式精馏塔的设计
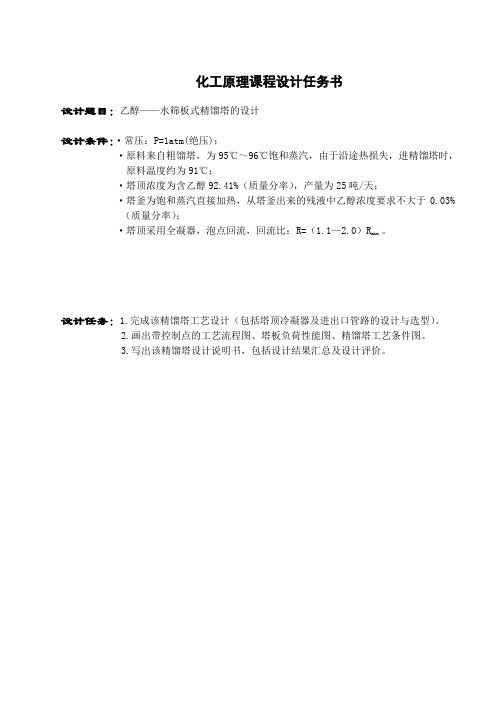
化工原理课程设计任务书设计题目:乙醇——水筛板式精馏塔的设计设计条件:·常压:P=1atm(绝压);·原料来自粗馏塔,为95℃~96℃饱和蒸汽,由于沿途热损失,进精馏塔时,原料温度约为91℃;·塔顶浓度为含乙醇92.41%(质量分率),产量为25吨/天;·塔釜为饱和蒸汽直接加热,从塔釜出来的残液中乙醇浓度要求不大于0.03%(质量分率);。
·塔顶采用全凝器,泡点回流,回流比:R=(1.1—2.0)Rmin设计任务:1.完成该精馏塔工艺设计(包括塔顶冷凝器及进出口管路的设计与选型)。
2.画出带控制点的工艺流程图、塔板负荷性能图、精馏塔工艺条件图。
3.写出该精馏塔设计说明书,包括设计结果汇总及设计评价。
化工原理课程设计任务书 ............................................ 摘要.. (4)前言 (5)绪论 (8)§1.1设计背景 (8)§1.2设计方案 (8)§1.3设计思路 (8)§1.4选塔依据[3] (9)第二章精馏塔的工艺设计 (10)§2.1全塔工艺设计计算 (10)2.1.1产品浓度的计算和进料组成确定 (10)2.1.2 Q线方程的确定: (10)2.1.3平均相对挥发度的计算 (10)2.1.4最小回流比和适宜回流比的选取 (11)2.1.5物料衡算 (11)2.1.6精馏段和提馏段操作线 (12)2.1.7逐板法确定理论板数 (12)2.1.8全塔效率 (12)2.1.9实际塔板数及实际加料位置 (13)第三章板式塔主要工艺尺寸的设计计算 (14)§3.1塔的工艺条件及物性数据计算 (14)3.1.1操作压强P (14)3.1.2操作温度T (14)3.1.3塔内各段气、液两相组分的平均分子量 (14)3.1.4精馏段和提馏段各组分的密度[8] (15)3.1.5液体表面张力的计算 (16)3.1.6液体粘度ΜM (16)3.1.7气液负荷计算 (17)精馏段气液负荷计算 (17)提馏段气液负荷计算 (17)§3.2塔和塔板的主要工艺尺寸的计算 (18)3.2.1塔径D (18)3.2.2液流形式、降液管及溢流装置等尺寸的确定 (20)3.2.3塔板布置 (20)3.2.4筛孔数N 及开孔率Φ (21)3.2.5塔有效高度Z (22)3.2.6塔高的计算[5] (22)§3.3筛板塔的流体力学校核[2] (22)3.3.1板压降的校核 (22)3.3.2液沫夹带量E V的校核 (24)3.3.3溢流液泛条件的校核 (24)3.3.4液体在降液管内停留时间的校核 (25)3.3.5漏液点的校核 (25)§3.4塔板负荷性能图[2] (26)3.4.1液相负荷下限线 (26)3.4.2液相负荷上限线 (26)3.4.3漏液线(气相负荷下限线) (26)3.4.4过量液沫夹带线(气相负荷上限线) (27)3.4.5溢流液泛线 (28)3.4.6塔气液负荷性能图 (28)3.4.7热量衡算: (29)进入系统的热量 (29)离开系统的热量 (30)热量衡算式: (30)第四章塔的附属设备的计算 (31)§4.1塔顶冷凝器设计计算 (31)4.1.1确定设计方案 (31)4.1.2确定物性数据 (31)4.1.3热负荷Q的计算 (31)4.1.4传热面积的计算 (31)4.1.5换热器工艺结构尺寸 (32)4.1.6核算总传热系数K0 (33)1.管程表面传热系数计算: (33)2.计算壳程对流传热系数 (34)3.确定污垢热阻RS (34)4.核算总传热系数K0 (34)5.传热面积裕度: (35)4.1.7壁温核算 (35)4.1.8换热器内流体的流动阻力(压降) (36)§4.2接管设计 (36)4.2.1进料管 (36)4.2.2回流管 (36)4.2.3釜液出口管 (37)4.2.4塔顶蒸汽管 (37)4.2.5加热蒸汽管 (37)4.2.6管线设计结果表 (37)§4.3泵的选型 (38)第五章设计结果汇总 (39)结束语 (41)参考文献 (42)主要符号说明 (43)附录 (45)摘 要化工生产常需进行液体混合物的分离以达到提纯或回收有用组分的目的,精馏是利用液体混合物中各组分挥发度的不同并借助于多次部分汽化和部分冷凝达到轻重组分分离的方法。
精馏塔设计指导书
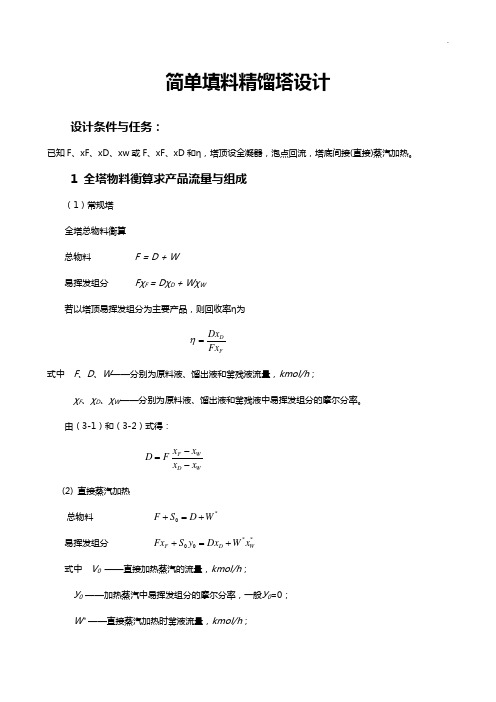
简单填料精馏塔设计设计条件与任务:已知F 、xF 、xD 、xw 或F 、xF 、xD 和η,塔顶设全凝器,泡点回流,塔底间接(直接)蒸汽加热。
1 全塔物料衡算求产品流量与组成(1)常规塔全塔总物料衡算总物料F = D + W 易挥发组分 F χF = D χD + W χW若以塔顶易挥发组分为主要产品,则回收率η为DFDx Fx η=式中 F 、D 、W ——分别为原料液、馏出液和釜残液流量,kmol/h ;χF 、χD 、χW ——分别为原料液、馏出液和釜残液中易挥发组分的摩尔分率。
由(3-1)和(3-2)式得:WD WF x x x x FD --=(2) 直接蒸汽加热 总物料*0F S D W +=+易挥发组分**00F D W Fx S y Dx W x +=+式中 V 0 ——直接加热蒸汽的流量,kmol/h ;У0 ——加热蒸汽中易挥发组分的摩尔分率,一般У0=0; W * ——直接蒸汽加热时釜液流量,kmol/h ;χ*W ——直接蒸汽加热时釜液中易挥发组分的摩尔分率。
2 计算最小回流比设夹紧点在精馏段,其坐标为(xe,ye)则 min D ee ex y R y x -=-设夹紧点在提馏段,其坐标为(xe,ye)min min (1)(1)e W e Wy x R D qF LV R D q F x x -+==+--- 基础数据:气液相平衡数据3 确定操作回流比 min (1.1~2.0)R R =4 计算精馏段、提馏段理论板数① 理想溶液 图解法或求出相对挥发度用逐板计算法求取。
② 非理想溶液 相平衡数据为离散数据,用图解法或数值积分法求取 精馏段 11 RDfN x R x n ndxN dN x x +==-⎰⎰因 111D n n x Ry x R R +=+++所以 ()/Dfx R x n n D n dxN y x x y R =---⎰(4)提馏段 11 SfWN x S x n ndxN dN x x +==-⎰⎰因 11W n n x R y x R R +'+=-''蒸汽回流比(1)(1)(1)(1)V R D q F D F R R q W W W W+--'===+-- 所以 ()/(1)fwx S x n n n w dxN y x y x R ='---+⎰(5)式(4)、(5)中塔板由下往上计数。
7.5.6其它类型精馏塔及理论塔板数的计算

第二段:两股进料之间,其下降液量和上升气量与第一段进料热状态有关
L=RD=1×7.35=7.35kmol/h; V=(R+1)D=2×7.35=14.7kmol/h
饱和液体进料,q1=1。则第二段进料口以上的上升气量和下降液量为
L’=L+q1F1=7.35+10=17.35kmol/h; V’=V-(1-q1)F1=V=14.7kmol/h GLL
对第二股进料口以上作物料衡算
F1xF1 V' y s1 L'xs DxD
其它类型精馏塔理论板数的确定 直接蒸汽加热 当水是重组分时,可将加热蒸汽直接通入塔釜加热。 直接蒸汽加热不影响精馏操作线 由于塔底多了一股蒸汽流,其提 馏段的操作线与间接蒸汽加热过 程不同。其推导如下: 总物料衡算 轻组分衡算
L' S V' W
加热蒸气 S V F, xF L D, xD
V’ L’
F, xF D, xD
Q
W, xW
无回流的回收塔 GLL
其操作线方程与一般精馏塔的提馏段操作线方程相同。
ym 1 L' W ' xm ' xW V V
D V , V' D 1 q F ,
ym 1
冷液进料时
L' qF
提馏段操作线方程为
WxW qF xm D 1 q F D 1 q F
1.0 1
1
D1 xD1
q 2
yD2 y
q 2
1
y
3
F, xF
2 3
D2 xD2 (yD2)
- 1、下载文档前请自行甄别文档内容的完整性,平台不提供额外的编辑、内容补充、找答案等附加服务。
- 2、"仅部分预览"的文档,不可在线预览部分如存在完整性等问题,可反馈申请退款(可完整预览的文档不适用该条件!)。
- 3、如文档侵犯您的权益,请联系客服反馈,我们会尽快为您处理(人工客服工作时间:9:00-18:30)。
双组分溶液直接蒸汽加热板式精馏塔设计设计任务:规定F 、xF 、xD 、xW ,设计出能完成分离任务的板式精馏塔 1. 回流比● 最小回流比设夹紧点在精馏段,其坐标为(xe,ye)则min D ee ex y R y x -=-(1)设夹紧点在提馏段,其坐标为(xe,ye)min min 0(1)(1)e e Wy R D qF LV R D q F x x -+==+--- (2) 所需基础数据:气液相平衡数据 丙酮-水xi = [0 0.01 0.02 0.05 0.10 0.15 0.20 0.30 0.40 0.50 0.60 0.70 0.80 0.90 0.95 1.0]; % 液相丙酮平衡浓度yi = [0 0.253 0.425 0.624 0.755 0.793 0.815 0.830 0.839 0.849 0.859 0.874 0.898 0.935 0.963 1.0]; % 汽相丙酮平衡浓度ti=[ 100 92.7 86.5 75.8 66.5 63.4 62.1 61.0 60.4 60.0 59.7 59.0 58.2 57.5 57.0 56.13 ];%平衡温度 甲醇-水xi = [0 0.02 0.04 0.06 0.08 0.10 0.15 0.20 0.30 0.40 0.50 0.60 0.70 0.80 0.90 0.95 1.0]; % 液相甲醇平衡浓度yi = [0 0.134 0.234 0.304 0.365 0.418 0.517 0.579 0.665 0.729 0.779 0.825 0.870 0.915 0.958 0.979 1.00]; % 汽相甲醇平衡浓度ti=[ 100 96.4 93.5 91.2 89.3 87.7 84.4 81.7 78.0 75.3 73.1 71.2 69.3 67.6 66.0 65.0 64.5 ];%平衡温度 来源:王志魁.化工原理(第三版),北京:化学工业出版社,2004 ● 确定操作回流比min(1.1~2.0)R R =用Matlab 或Excel 工具求出N 与R 间的关系以确定适宜的回流比。
(课堂讲解)2 全塔物料衡算与操作方程(1)全塔物料衡算F S D W +=+ (3)F D W Fx Dx Wx =+ (4) 其中 (1)(1)S V R D q F ==+-- (5)W L RD qF ==+(6) 联立式(3)、式(4)得: F WD Wx qx D Fx Rx -=+(7)(2) 操作方程 精馏段 111D n n x Ry x R R +=+++ 提馏段 1n n W W Wy x x S S+=- 3 计算精馏段、提馏段理论板数① 理想溶液 图解法或求出相对挥发度用逐板计算法求取。
② 非理想溶液 相平衡数据为离散数据,用图解法或数值积分法求取4. 全塔组成分布、温度分布及精馏段、提馏段平均温度与组成精馏段平均温度 1()/2F t t t =+ 提馏段平均温度 ()/2F N t t t =+其中 1t ——塔顶第一板温度,由y=xd 查t-y 数据获得,因塔顶为蒸汽冷凝;F t ——加料板温度,由加料板组成xm 查t-x 数据获得; B t ——塔釜温度,由xw 查t-x 数据获得。
5物性参数的计算① 塔顶条件下的物性参数(气相密度、液相密度、表面张力及粘度) ② 进料板组成与温度条件的物性参数 ③ 塔釜条件下的物性参数 ④ 精馏段平均物性参数 ⑤ 提馏段平均物性参数附:① 气相密度用理想气体状态方程计算 pMRTρ= ② 液相密度1ABLABw w ρρρ=+A w 、B w 为组分A 与B 的质量分数,A ρ、B ρ分别为组分A 与B 的液相密度,水的密度用插值法求,甲醇或丙酮的密度查有机液体相对密度共线图(陈敏恒,化工原理(上册):北京:化学工业出版社,2006)③ 二元含水混合物的表面张力(含水溶液)(B E Poling, J M Prausnitz, J P O ’Conell 著,赵红梅,王凤坤,陈圣坤等译,气液物性估算手册,北京:化学工业出版社,2006,497-498)1/41/41/4m SW W SO O σϕσϕσ=+/()W W W W W O O x V x V x V ϕ=+ /()O O O W WO Ox V x V x V ϕ=+ lg(/)qWO B ϕϕ=2/32/30.441(/)()O O W W V Q q T V qσσ=-lg(/)qSW SO B Q ϕϕ+=1SW SO ϕϕ+=醇类,脂肪酸类 q=碳原子数,如乙酸q=2,甲醇q=1;酮类 q=碳原子数-1,例丙酮q=2σW 、σO 分别为纯水与纯有机物的表面张力,mN/m 。
纯有机物的表面张力查有机液体的表面张力共线图。
x W 、x O 分别为水与有机物的液相摩尔分数V W 、V O 分别为水与有机物的液相摩尔体积,cm 3/mol T ——温度,K例估算甲醇-水混合物在303K 时的表面张力,甲醇的摩尔分数为0.122,实验数据46.1 mN/m. 解:303K 时σW =71.18 mN/m 、σO =21.75mN/m,Vw=18 cm 3/mol, V o=41cm 3/mol ,q=1。
(31000cm /mol WW WM V ρ=31000cm /mol oo oM V ρ=Mo,Mw —有机组分与水的分子量,kg/kmol; ρo,ρw —有机组分与水的密度,kg/m 3)//()0.87818/(0.12241) 3.16W o W W O O x V x V ϕϕ==⨯⨯=lg(/)lg3.160.50W O B ϕϕ===2/32/32/32/321.75410.441(/)()0.441(1/303)(71.1818)1O O W WV Q q T Vqσσ⨯=-=-⨯0.34Q =-lg(/)qSW SO B Q ϕϕ+= 0.500.34l g (/S W S O ϕϕ-=/ 1.45SW SO ϕϕ= (1)1SW SO ϕϕ+= (2)联立式(1) (2)得:0.59 41SW SO ϕϕ==1/40.250.250.5971.180.4121.75m σ=⨯+⨯46mN/m m σ=④ 水的物性数据查化工原理上册教材附录,采用内差法 ⑤ 甲醇、乙醇、丙酮的物性数据查上册教材附录 密度见p272有机液体的相对密度共线图 表面张力见p274有机液体表面张力共线图 液体粘度见p276液体粘度共线图 液体比热容见p278液体比热容共线图 气体粘度见见p284气体粘度共线图 气体比热容见p286气体比热容共线图 液体汽化热见p280液体汽化热共线图6塔效率的计算塔效率:0.2450.49()T L E αμ-=——O'Connel 公式(适用于非碳氢物系如甲醇-水物系,丙酮-水物系)丙酮-水 ① 精馏段0.2450.49()T L E αμ-=式中:α——精馏段平均温度下的相对挥发度;μL ——精馏段平均温度下的液相粘度, mPa.s 以乙醇-水体系为例:精馏段平均温度 82.79℃,0.2294A x =,0.5422A y =,查有机液体粘度共线图82.79℃下醇的粘度为0.433mPa.s ,查教材附录水的粘度为0.3439mPa.s 。
/0.5422/0.22943.98/0.4578/0.7706A AB B y x y x α===0.4330.22940.3439(10.2294)0.3643L i i x μμ==⨯+⨯-=∑mPa.s② 提馏段0.2450.49()T L E αμ-=式中:α——提馏段平均温度下的相对挥发度;μL ——提馏段平均温度下的液相粘度, mPa.s7 计算实际塔板数全塔效率:0.2450.49()T L E αμ-=——O'Connel 公式(适用于非碳氢物系)式中:α——塔顶与塔底平均温度下的相对挥发度; μL ——塔顶与塔底平均温度下的液相粘度, mPa.s ① 精馏段0.2450.49()T L E αμ-=式中:α——精馏段平均温度下的相对挥发度;μL ——精馏段平均温度下的液相粘度, mPa.s p (N )RTN E =精 注意:要圆整塔板数 ② 提馏段0.2450.49()T L E αμ-=式中:α——提馏段平均温度下的相对挥发度;μL ——提馏段平均温度下的液相粘度, mPa.s p 1(N )S TN E -=提 注意:要圆整塔板数 全塔所需塔板数:()()p p p N N N =+精提 全塔效率: (1)/T T p E N N =-提醒:全塔效率的工业测定值通常在0.3~0.7之间8 冷凝器的热负荷冷凝器的热负荷()C DV DL Q V I I =-待求量:进料温度t F 、塔顶上升蒸汽温度t DV (与x D 对应的露点温度)、回流温度t DL (与x D 对应的泡点温度)。
物性数据:① 各组分在平均温度下的液相热容、气相热容或汽化热。
② 各组分的热容方程常数如 23p c A BT CT DT =+++ ③ 由沃森公式计算汽化热 210.38211()1r V V r T H H T -∆=∆-9 估算塔径(1) 板间距的初选板间距N T 的选定很重要。
选取时应考虑塔高、塔径、物系性质、分离效率、操作弹性及塔的安装检修等因素。
对完成一定生产任务,若采用较大的板间距,能允许较高的空塔气速,对塔板效率、操作弹性及安装检修有利;但板间距增大后,会增加塔身总高度,金属消耗量,塔基、支座等的负荷,从而导致全塔造价增加。
反之,采用较小的板间距,只能允许较小的空塔气速,塔径就要增大,但塔高可降低;但是板间距过小,容易产生液泛现象,降低板效率。
所以在选取板间距时,要根据各种不同情况予以考虑。
如对易发泡的物系,板间距应取大一些,以保证塔的分离效果。
板间距与塔径之间的关系,应根据实际情况,结合经济权衡,反复调整,已做出最佳选择。
设计时通常根据塔径的大小,由表4-1列出的塔板间距的经验数值选取。
表1 塔板间距与塔径的关系化工生产中常用板间距为:200,250,300,350,400,450,500,600,700,800mm 。
在决定板间距时还应考虑安装、检修的需要。
例如在塔体人孔处,应留有足够的工作空间,其值不应小于600mm 。
(2) 估算塔径D =max (0.6~0.8) u u = 0.5m a x ()L G Gu C ρρρ-= 0.220=()20LC C σ 0.520L =f(,-h ) ( )G L T G LW C H W ρψψρ=式中:C ——操作物系的负荷因子; σL ——操作物系的液体表面张力,mN/m ;H T ——板间距;h L ——板上液层高度。