IC卡中薄芯片碎裂失效机理的研究
芯片封装中的失效机理与故障分析研究
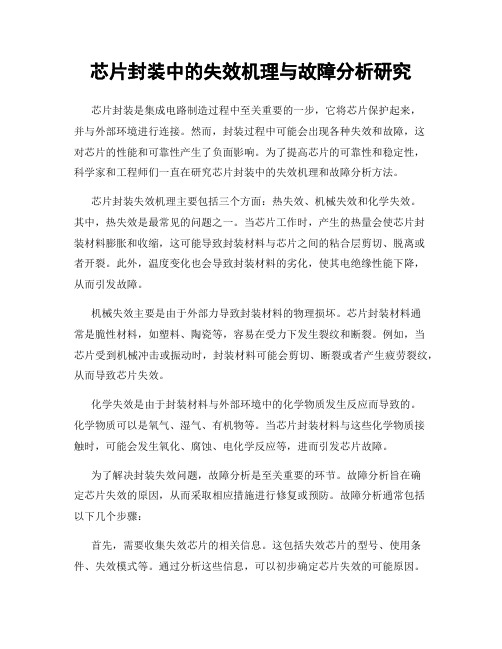
芯片封装中的失效机理与故障分析研究芯片封装是集成电路制造过程中至关重要的一步,它将芯片保护起来,并与外部环境进行连接。
然而,封装过程中可能会出现各种失效和故障,这对芯片的性能和可靠性产生了负面影响。
为了提高芯片的可靠性和稳定性,科学家和工程师们一直在研究芯片封装中的失效机理和故障分析方法。
芯片封装失效机理主要包括三个方面:热失效、机械失效和化学失效。
其中,热失效是最常见的问题之一。
当芯片工作时,产生的热量会使芯片封装材料膨胀和收缩,这可能导致封装材料与芯片之间的粘合层剪切、脱离或者开裂。
此外,温度变化也会导致封装材料的劣化,使其电绝缘性能下降,从而引发故障。
机械失效主要是由于外部力导致封装材料的物理损坏。
芯片封装材料通常是脆性材料,如塑料、陶瓷等,容易在受力下发生裂纹和断裂。
例如,当芯片受到机械冲击或振动时,封装材料可能会剪切、断裂或者产生疲劳裂纹,从而导致芯片失效。
化学失效是由于封装材料与外部环境中的化学物质发生反应而导致的。
化学物质可以是氧气、湿气、有机物等。
当芯片封装材料与这些化学物质接触时,可能会发生氧化、腐蚀、电化学反应等,进而引发芯片故障。
为了解决封装失效问题,故障分析是至关重要的环节。
故障分析旨在确定芯片失效的原因,从而采取相应措施进行修复或预防。
故障分析通常包括以下几个步骤:首先,需要收集失效芯片的相关信息。
这包括失效芯片的型号、使用条件、失效模式等。
通过分析这些信息,可以初步确定芯片失效的可能原因。
其次,进行物理分析。
物理分析是指通过观察芯片失效的外观、形态和结构,来确定失效的机理。
例如,通过显微镜观察失效芯片的微观形貌,可以确定是否存在裂纹、剥离等现象。
此外,还可以使用X射线、电子束等技术进行进一步的材料分析,以确定材料的性质和存在的异常问题。
接下来,进行电学分析。
电学分析是指通过测量失效芯片的电性能参数,来判断芯片的电路结构是否正常。
例如,使用万用表、示波器等设备对芯片进行电流、电压、功率等参数的测量,以了解失效芯片的电路状态。
各类元器件失效机理分析总结

各类元器件失效机理分析总结电子元器件在使用过程中,常常会出现失效和故障,从而影响设备的正常工作。
为了保证设备或系统能可靠的工作,对于电子元器件的可靠性要求就非常高。
可靠性指标已经成为元器件的重要质量指标之一。
了解了元器件的失效模式和失效机理,对于诊断设备故障和保持设备的可靠性是十分重要的,下文简单介绍各种元器件的失效机理。
1、电阻器常见的非绕线电阻器按照电阻体所用的材料不同可以分为四种类型即合金型、薄膜型、厚膜型和合成型。
对于固定电阻器,其主要失效模式有开路、电参数漂移等;而对于电位器,其主要失效模式有开路、电参数漂移、噪声增大等。
使用环境也将导致电阻器老化,对于电子pcba的寿命具有很大影响。
1)氧化:电阻器电阻体的氧化将使电阻值增大,是造成电阻器老化的最主要因素。
除了贵金属及合金制成的电阻体外,其他材料都会受到空气中氧的破坏。
氧化作用是长期作用的,当其他因素的影响逐渐减弱后,氧化作用将成为主要因素,高温高湿环境会加速电阻器的氧化。
对于精密电阻器和高阻值电阻器,防止氧化的根本措施是密封保护。
小编建议密封材料应采用无机材料,如金属、陶瓷、玻璃等。
有机保护层不能完全防止透湿和透气,对氧化和吸附作用只能起到延缓作用。
2)黏结剂的老化:对于有机合成型电阻器,有机黏结剂的老化是影响电阻器稳定性的主要因素,有机黏结剂主要是合成树脂,PCBA加工企业在电阻器的制造过程中,合成树脂经热处理转变为高聚合度的热固性聚合物。
引起聚合物老化的主要因素是氧化。
氧化生成的游离基引起聚合物分子键的铰链,从而使聚合物进一步固化、变脆,进而丧失弹性和发生机械破坏。
黏结剂的固化使电阻器体积收缩,导电颗粒之间的接触压力增大,接触电阻变小,使电阻值减小,但黏结剂的机械破坏也会使电阻值增大。
通常黏结剂的固化发生在前,机械破坏发生在后,所以有机合成型电阻器的电阻值呈现出以下规律:在开始阶段有些下降,然后转为增大,且有不断增大的趋势。
由于聚合物的老化与温度、光照密切相关,所以在高温环境和强烈光线照射下,合成电阻器会加速老化。
电脑芯片分析中的失效分析与故障诊断

电脑芯片分析中的失效分析与故障诊断电脑芯片是计算机系统的核心组件,承担着数据处理、指令执行等重要任务。
然而,在使用过程中,电脑芯片可能会出现各种失效和故障,给计算机性能和稳定性带来影响。
因此,进行失效分析与故障诊断对于电脑芯片的研发和维修具有重要意义。
本文将重点探讨电脑芯片失效分析与故障诊断的相关技术和方法。
一、失效分析的基本概念与方法电脑芯片失效分析是通过对失效芯片进行分析,找出故障原因和局部失效区域,以便进行故障修复和改进设计。
失效分析的基本方法包括失效样品分析、故障模式分析和失效分析原因的判定等。
失效样品分析是指对失效芯片的外观、尺寸、外围电路等进行详细观察和分析,并通过断面观察和扫描电子显微镜等手段对失效芯片的内部结构进行分析。
故障模式分析则是基于失效样品分析的基础上,通过对故障现象的总结归纳,找出失效行为的规律和模式。
最后,判定失效原因是通过对失效样品和故障现象的综合分析,通过专业知识和经验判断出失效原因,为后续的故障诊断提供指导。
二、故障诊断的技术与方法故障诊断是在失效分析的基础上,通过实验和测试手段找出故障原因的过程。
它的主要目标是确定故障根源和故障模式,以便进行相应的修复和改进。
常用的故障诊断技术包括异常信号分析、功能测试和有限元分析等。
异常信号分析是通过对芯片运行状态和信号波形的监测与分析,找出其中的异常信号,以确定故障原因。
功能测试是通过对芯片进行一系列功能验证和测试,比较输出与预期结果的差异,从而找到故障的具体位置。
有限元分析则是一种计算机辅助技术,通过模拟芯片的物理特性和工作环境,分析其受力、热量分布等情况,找出导致故障的可能性和潜在问题。
三、失效分析与故障诊断技术的应用失效分析与故障诊断技术在电脑芯片领域有着广泛的应用。
首先,它们对于芯片设计和制造具有重要指导意义。
通过对失效样品进行分析和诊断,可以发现设计上的缺陷和制造过程中的问题,为芯片的改进提供依据。
其次,失效分析和故障诊断也广泛应用于芯片维修和故障排除。
芯片碎裂机理
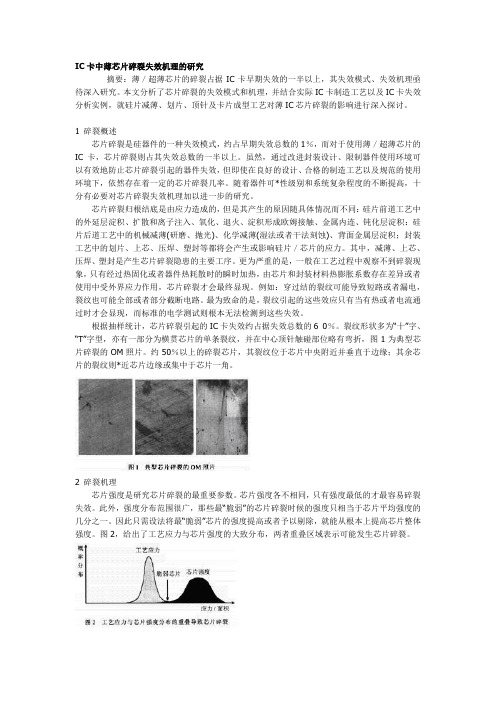
IC卡中薄芯片碎裂失效机理的研究摘要:薄/超薄芯片的碎裂占据IC卡早期失效的一半以上,其失效模式、失效机理亟待深入研究。
本文分析了芯片碎裂的失效模式和机理,并结合实际IC卡制造工艺以及IC卡失效分析实例,就硅片减薄、划片、顶针及卡片成型工艺对薄IC芯片碎裂的影响进行深入探讨。
1 碎裂概述芯片碎裂是硅器件的一种失效模式,约占早期失效总数的1%,而对于使用薄/超薄芯片的IC卡,芯片碎裂则占其失效总数的一半以上。
虽然,通过改进封装设计、限制器件使用环境可以有效地防止芯片碎裂引起的器件失效,但即使在良好的设计、合格的制造工艺以及规范的使用环境下,依然存在着一定的芯片碎裂几率。
随着器件可*性级别和系统复杂程度的不断提高,十分有必要对芯片碎裂失效机理加以进一步的研究。
芯片碎裂归根结底是由应力造成的,但是其产生的原因随具体情况而不同:硅片前道工艺中的外延层淀积、扩散和离子注入、氧化、退火、淀积形成欧姆接触、金属内连、钝化层淀积:硅片后道工艺中的机械减薄(研磨、抛光)、化学减薄(湿法或者干法刻蚀)、背面金属层淀积;封装工艺中的划片、上芯、压焊、塑封等都将会产生或影响硅片/芯片的应力。
其中,减薄、上芯、压焊、塑封是产生芯片碎裂隐患的主要工序。
更为严重的是,一般在工艺过程中观察不到碎裂现象,只有经过热固化或者器件热耗散时的瞬时加热,由芯片和封装材料热膨胀系数存在差异或者使用中受外界应力作用,芯片碎裂才会最终显现。
例如:穿过结的裂纹可能导致短路或者漏电,裂纹也可能全部或者部分截断电路。
最为致命的是,裂纹引起的这些效应只有当有热或者电流通过时才会显现,而标准的电学测试则根本无法检测到这些失效。
根据抽样统计,芯片碎裂引起的IC卡失效约占据失效总数的6 0%。
裂纹形状多为“十”字、“T”字型,亦有一部分为横贯芯片的单条裂纹,并在中心顶针触碰部位略有弯折,图1为典型芯片碎裂的OM照片。
约50%以上的碎裂芯片,其裂纹位于芯片中央附近并垂直于边缘;其余芯片的裂纹则*近芯片边缘或集中于芯片一角。
电脑芯片分析中的故障模式与失效分析方法

电脑芯片分析中的故障模式与失效分析方法电脑芯片作为计算机硬件中的核心部件,承担着数据运算和控制的重要任务。
然而,由于使用寿命、工作环境等原因,电脑芯片在长时间运行中可能会出现各种故障。
为了提高电脑芯片的可靠性和性能,对于故障模式的分析和失效分析是非常重要的。
本文将深入探讨电脑芯片分析中的故障模式与失效分析方法。
一、故障模式的分类电脑芯片存在多种故障模式,主要包括以下几种:1. 电气故障:电路连接错误、电压过高或过低、电流波动等电气问题可能导致芯片失效。
2. 结构故障:芯片制造工艺中的缺陷或外部物理损伤(如机械撞击)可能导致芯片结构破裂或元器件间隔短路等问题。
3. 热故障:电脑芯片长时间高负荷工作可能导致散热不良,温度过高使得芯片性能下降甚至失效。
4. 功能故障:芯片设计或生产过程中的缺陷可能导致功能性能下降或无法正常工作。
5. 兼容性故障:芯片与其他硬件或软件的兼容性问题可能导致芯片无法正常通信或正常协同工作。
二、失效分析方法失效分析是对电脑芯片故障模式进行深入研究和分析的过程。
以下是常用的失效分析方法:1. 键控点分析法键控点分析法是一种常用的失效分析方法,它通过确定芯片在整个系统中的关键功能点,分析关键功能点的工作状态和可能存在的潜在问题,来确定芯片的失效原因。
这种方法可以帮助工程师快速定位并解决故障。
2. 故障树分析法故障树分析法是一种通过构建故障树来分析芯片失效的方法。
故障树是一种以“与”、“或”逻辑关系为基础的树状结构,通过对芯片各种可能的失效事件进行组合和分析,以确定最终失效的原因。
这种方法可以帮助工程师深入理解芯片失效的根本原因。
3. 试验分析法试验分析法是一种通过实验手段对芯片进行失效分析的方法。
通过对芯片在不同工作条件下的试验,观察和记录芯片在实验过程中的异常现象,从而推断芯片失效的原因。
这种方法可以提供实验数据支持,更加准确地确定芯片失效的原因。
4. 统计分析法统计分析法是一种通过对大量失效数据进行统计和分析,以发现芯片故障模式的方法。
PLCC封装的CODEC芯片失效分析
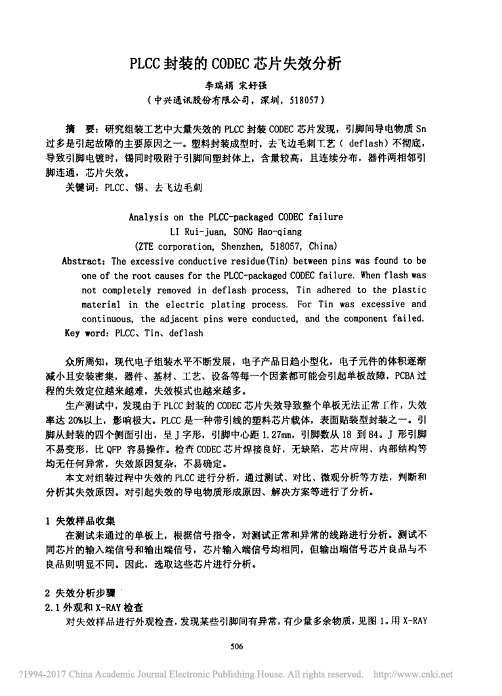
,
然 后进 行 引脚 间异 物 分 析
, ,
芯 片 引脚 间 进行 扫 描 电镜 ( S M E ) 分析
如图
4
,
某 些 引脚 塑 料 封 装成形 处 不 平 整
,
有
形
参 差不 齐 的异 物
应 为塑封 料从 二 块 模 具 的合 缝 处 渗 出 来
流 到 模 块 外 的 框架 材 料 上
,
成 的毛 刺
.
均 无任 何 异 常
失 效 原 因 复杂 不 易 确 定 组 本文 对 装 过 程 中 失效 的 P L CC 进 行分 析
。
通 过测试
、
对比
、
微 观 分析 等方法
。
判断 和
分 析其 失 效 原 因
l
对 引起 失 效 的 导 电物 质形 成原 因
解决 方案等 进行 了分析
失效 样 品 收 集 在测 试 未通 过 的 单板 上 根据 信 号 指 令 对 测试 正 常和 异常 的 线 路进 行分 析 测 试 不 同芯 片 的 输 入 端 信 号和 输 出端 信号 芯 片输入 端信 号均 相 同 但 输 出端 信 号芯 片 良品 与不
n r a
il
u r e r e
Wh e
to
t
f la
h
e o mP
e r
l
e t e
ly
the
t
r e mo v e
i
defl
a s
h
Pr o
dhe
n
d
he
Pl
a s t
i
e
t
i
a
l
i
s
电脑芯片制造中的崩溃分析与改进

电脑芯片制造中的崩溃分析与改进随着科技的不断发展,电脑芯片已经成为现代社会中不可或缺的物品之一。
它们作为电子设备的核心,起着至关重要的作用。
然而,在电脑芯片的制造过程中常常会出现崩溃的情况,这给产业链带来了一系列的问题。
本文将探讨电脑芯片制造中的崩溃现象,并提出改进措施,以提高芯片制造的质量和稳定性。
崩溃分析电脑芯片制造中的崩溃问题是指芯片在生产过程中无法正常运行或提前损坏的情况。
常见的崩溃原因包括制造工艺不当、材料质量差、温度过高、电压不稳定等。
下面将分别对这些原因进行分析。
首先,制造工艺不当是导致芯片崩溃的常见原因之一。
芯片的制造需要经历多个工序,其中每个工序都需要严格遵循预定的工艺流程。
如果在某个工序中出现错误,就会导致整个芯片的质量下降,甚至造成崩溃。
因此,制造商需要不断提升工艺水平,减少制造工艺中的缺陷和误差。
其次,材料质量差也可能是芯片崩溃的原因之一。
电脑芯片所使用的材料需要具有良好的导电性、热传导性和物理稳定性。
然而,一些低质量的材料可能不符合这些要求,从而影响芯片的性能和稳定性。
制造商应该选择高品质的材料,并严格把关材料供应链的质量。
此外,温度过高和电压不稳定也是导致芯片崩溃的常见原因。
芯片在工作时会产生大量的热量,如果散热不良,温度就会不断升高。
高温环境会加速芯片的老化,并可能导致崩溃。
另外,电压的不稳定也会对芯片的性能和稳定性造成影响。
因此,在芯片设计和制造过程中应该考虑到散热和电源供应的问题,以保证芯片的正常运行和工作稳定。
改进措施针对电脑芯片制造中的崩溃问题,制造商可以采取一系列的改进措施,以提高芯片的质量和稳定性。
首先,制造商应该加强对制造工艺的控制。
通过改善生产工艺和加强工艺流程的监控,制造商可以降低制造工艺中的缺陷和误差。
同时,引入先进的生产设备和技术,提高芯片的制造精度和一致性。
其次,制造商应该选择高品质的材料。
与供应商建立长期合作关系,确保材料的稳定供应。
此外,制造商还可以积极参与材料的研发和改进,以满足芯片制造的需求。
智能卡失效机理研究及分析实例
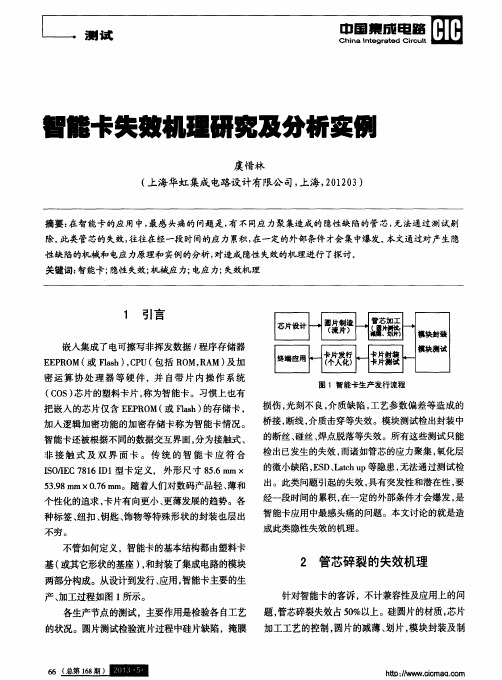
2 管芯碎裂的失效机理
针对智能卡的客诉 , 不计兼容性及应用上的问
管芯碎裂失效占 5 o  ̄1 2 : 上。硅圆片的材质 , 芯片 各生产节点 的测试 ,主要作用是检验各 自工艺 题 , 圆片的减薄、 划片 , 模块封装及制 的状况。圆片测试检验流片过程中硅片缺陷 ,掩膜 加工工艺的控制 ,
模块测试
密 运算 协 处 理器 等 硬 件 , 并 自带 片 内操作 系统
( C O S ) 芯片的塑料卡片, 称为智能卡 。习惯上也有
图 1 智 能 卡生 产 发 行 流 程
把嵌入的芯片仅含 E E P R O M( 或F l s a h ) 的存储卡 , 加入逻辑加密功能的加密存储卡称为智能卡情况。 智能卡还被根据不同的数据交互界面 , 分为接触式 、
的话 , 在细磨工艺后再采用湿法腐蚀工艺 , 去除硅片 背面残 留的晶格损伤层 。 这样能有效释放局部应力 , 大大增强圆片强度 ,改善硅片及管芯因残余应力碎 减薄后的硅片粘贴在一个带有不锈钢或塑料框 架的胶膜 ( 蓝膜或 u v膜 ) 上, 送进划片机划片。划 片质量除与前面提到的基 片、流片及减薄工艺影响 外 ,更 与划片的进刀速度及刀片的劳损程度有关 。
智能卡失效机氇研究及分析实侧
虞 惜林 ( 上 海华虹 集成 电路设计有 限公 司, 上海 , 2 0 1 2 0 3 )
摘要 : 在智能卡的应 用中, 最感头痛 的问题是 , 有不同应力聚集造成的隐性缺 陷的管芯, 无法通过测试剔
除。 此类管芯的失效, 往往在经一段 时间的应 力累积, 在一定的外部条件才会集中爆发 。 本文通过对产生 隐
性缺 陷的机 械 和 电应 力原 理和 实例 的分析 , 对 造成 隐性 失效 的机 理进行 了探 讨 。
芯片碎裂机理
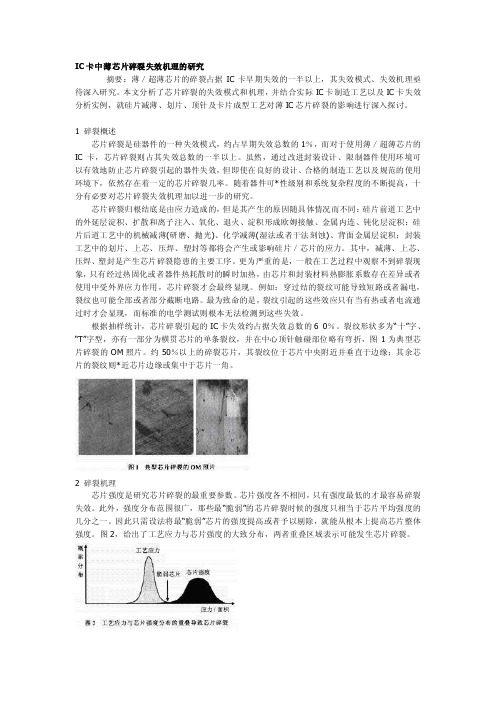
IC卡中薄芯片碎裂失效机理的研究摘要:薄/超薄芯片的碎裂占据IC卡早期失效的一半以上,其失效模式、失效机理亟待深入研究。
本文分析了芯片碎裂的失效模式和机理,并结合实际IC卡制造工艺以及IC卡失效分析实例,就硅片减薄、划片、顶针及卡片成型工艺对薄IC芯片碎裂的影响进行深入探讨。
1 碎裂概述芯片碎裂是硅器件的一种失效模式,约占早期失效总数的1%,而对于使用薄/超薄芯片的IC卡,芯片碎裂则占其失效总数的一半以上。
虽然,通过改进封装设计、限制器件使用环境可以有效地防止芯片碎裂引起的器件失效,但即使在良好的设计、合格的制造工艺以及规范的使用环境下,依然存在着一定的芯片碎裂几率。
随着器件可*性级别和系统复杂程度的不断提高,十分有必要对芯片碎裂失效机理加以进一步的研究。
芯片碎裂归根结底是由应力造成的,但是其产生的原因随具体情况而不同:硅片前道工艺中的外延层淀积、扩散和离子注入、氧化、退火、淀积形成欧姆接触、金属内连、钝化层淀积:硅片后道工艺中的机械减薄(研磨、抛光)、化学减薄(湿法或者干法刻蚀)、背面金属层淀积;封装工艺中的划片、上芯、压焊、塑封等都将会产生或影响硅片/芯片的应力。
其中,减薄、上芯、压焊、塑封是产生芯片碎裂隐患的主要工序。
更为严重的是,一般在工艺过程中观察不到碎裂现象,只有经过热固化或者器件热耗散时的瞬时加热,由芯片和封装材料热膨胀系数存在差异或者使用中受外界应力作用,芯片碎裂才会最终显现。
例如:穿过结的裂纹可能导致短路或者漏电,裂纹也可能全部或者部分截断电路。
最为致命的是,裂纹引起的这些效应只有当有热或者电流通过时才会显现,而标准的电学测试则根本无法检测到这些失效。
根据抽样统计,芯片碎裂引起的IC卡失效约占据失效总数的6 0%。
裂纹形状多为“十”字、“T”字型,亦有一部分为横贯芯片的单条裂纹,并在中心顶针触碰部位略有弯折,图1为典型芯片碎裂的OM照片。
约50%以上的碎裂芯片,其裂纹位于芯片中央附近并垂直于边缘;其余芯片的裂纹则*近芯片边缘或集中于芯片一角。
教你如何分析芯片损坏的原因
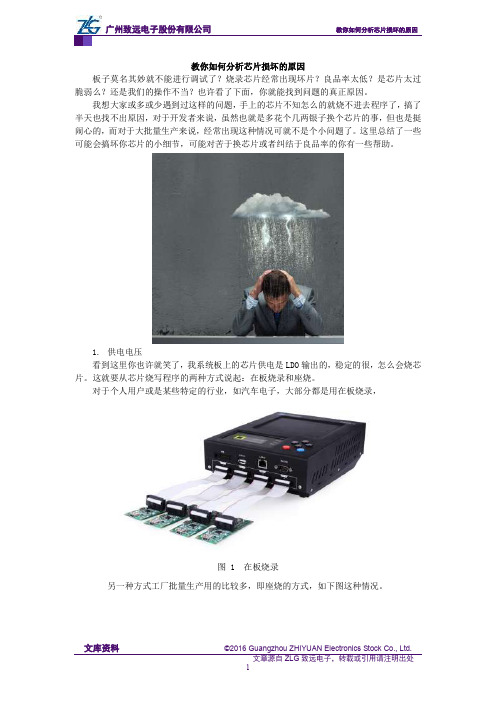
教你如何分析芯片损坏的原因板子莫名其妙就不能进行调试了?烧录芯片经常出现坏片?良品率太低?是芯片太过脆弱么?还是我们的操作不当?也许看了下面,你就能找到问题的真正原因。
我想大家或多或少遇到过这样的问题,手上的芯片不知怎么的就烧不进去程序了,搞了半天也找不出原因,对于开发者来说,虽然也就是多花个几两银子换个芯片的事,但也是挺闹心的,而对于大批量生产来说,经常出现这种情况可就不是个小问题了。
这里总结了一些可能会搞坏你芯片的小细节,可能对苦于换芯片或者纠结于良品率的你有一些帮助。
1.供电电压看到这里你也许就笑了,我系统板上的芯片供电是LDO输出的,稳定的很,怎么会烧芯片。
这就要从芯片烧写程序的两种方式说起:在板烧录和座烧。
对于个人用户或是某些特定的行业,如汽车电子,大部分都是用在板烧录,图 1 在板烧录另一种方式工厂批量生产用的比较多,即座烧的方式,如下图这种情况。
图 2 座烧对于很多开发板或者我们自己设计的系统板,调试接口的VCC一般都是直接从芯片供电引脚拉出,如果编程器供电不稳,则很容易造成芯片的过压损坏。
下图为一款MCU的供电电压范围:若编程器供电电压不准或电压不稳,超过了这个范围,则芯片将很容易损坏。
座烧就更不用说了,芯片直接由编程器供电,如果编程器供电不稳,那烧录芯片的良品率将会成为你的噩梦。
2.芯片加密一般的开发者很容易忽略芯片为我们提供的这个重要功能,但是当你的产品要大卖的时候,这个功能就显得尤为重要了,加密功能能有效防止你的产片代码被抄袭。
芯片加密等级一般有3级,我觉得这款Cypress的芯片手册给出了比较明确的说明。
OPEN:芯片没有保护,意味着你烧录到芯片中的软件可以被山寨者直接读出。
PROTECTED:芯片有了读出保护,意味着没有人可以读出来芯片中的数据,但是芯片可以擦除,擦除之后可以再次使用。
KILL:你的芯片被“杀死了”,和上一个级别的保护一样,没有人可以读取芯片数据,但是这一次,整片擦除也不起作用了,你的芯片无法重新烧录,但是不是真的“死了”,它还可以运行烧录进去的程序。
芯片失效分析

怎样进行芯片失效分析?•一般来说,集成电路在研制、生产和使用过程中失效不可避免,随着人们对产品质量和可靠性要求的不断提高,失效分析工作也显得越来越重要,通过芯片失效分析,可以帮助集成电路设计人员找到设计上的缺陷、工艺参数的不匹配或设计与操作中的不当等问题。
失效分析的意义主要表现具体来说,失效分析的意义主要表现在以下几个方面:1.失效分析是确定芯片失效机理的必要手段。
2.失效分析为有效的故障诊断提供了必要的信息。
3.失效分析为设计工程师不断改进或者修复芯片的设计,使之与设计规范更加吻合提供必要的反馈信息。
4.失效分析可以评估不同测试向量的有效性,为生产测试提供必要的补充,为验证测试流程优化提供必要的信息基础。
失效分析主要步骤和内容•芯片开封:去除IC封胶,同时保持芯片功能的完整无损,保持 die,bond pads,bond wires乃至lead-frame不受损伤,为下一步芯片失效分析实验做准备。
•SEM 扫描电镜/EDX成分分析:包括材料结构分析/缺陷观察、元素组成常规微区分析、精确测量元器件尺寸等等。
•探针测试:以微探针快捷方便地获取IC内部电信号。
镭射切割:以微激光束切断线路或芯片上层特定区域。
•EMMI侦测:EMMI微光显微镜是一种效率极高的失效分错析工具,提供高灵敏度非破坏性的故障定位方式,可侦测和定位非常微弱的发光(可见光及近红外光),由此捕捉各种元件缺陷或异常所产生的漏电流可见光。
•OBIRCH应用(镭射光束诱发阻抗值变化测试):OBIRCH常用于芯片内部高阻抗及低阻抗分析,线路漏电路径分析。
利用OBIRCH方法,可以有效地对电路中缺陷定位,如线条中的空洞、通孔下的空洞。
通孔底部高阻区等,也能有效的检测短路或漏电,是发光显微技术的有力补充。
•LG液晶热点侦测:利用液晶感测到IC漏电处分子排列重组,在显微镜下呈现出不同于其它区域的斑状影像,找寻在实际分析中困扰设计人员的漏电区域(超过10mA之故障点)。
芯片组装的失效机理及分析

芯片组装的失效机理及分析贺玲;刘洪涛【摘要】Several typical chip assembly modes are introduced,and several failure modes of bonding and welding caused by many different reasons are discussed in detail with examples. According to the characteristics of different failure modes, this paper puts forward a variety of different detection methods for the chip falling off, desoldering and fracture which maybe happens in different parts and in different forms during the process of bonding or welding. In order to avoid assembly failure to the greatest extent, the principle and failure mechanism of bonding and welding were analyzed.In addition to the routine pro-duction inspection in accordance with the national standards,the methods of improving the quality of chip assembly are discussed in depth.%介绍了几种有代表性的芯片组装模式,并结合实例详细探讨了由多种不同原因导致的几种焊接与粘接的失效模式.针对不同失效模式的特点,对芯片在粘接或焊接过程中可能会在不同部位、以不同形式出现的脱落、脱焊与断裂等,提出多种不同的检测手段.以最大程度避免出现组装失效为目的,剖析具体的粘接焊接原理与失效机制.在符合国家标准的常规生产检测之外,对改进芯片组装质量的方法进行了深入的延伸讨论.【期刊名称】《微处理机》【年(卷),期】2018(039)002【总页数】3页(P5-7)【关键词】芯片粘接;焊接;芯片组装;粘接强度;失效;失效模式;可靠性【作者】贺玲;刘洪涛【作者单位】中国电子科技集团公司第四十七研究所,沈阳110032;中国电子科技集团公司第四十七研究所,沈阳110032【正文语种】中文【中图分类】TN471 引言芯片组装技术是微组装核心技术之一,其组装质量直接影响整个器件和组件的性能[1],随着混合集成电路向着高性能、高密度以及小型化、低成本的方向发展,对芯片的组装技术和可靠性提出了更高的要求。
芯片怎样被搞坏的
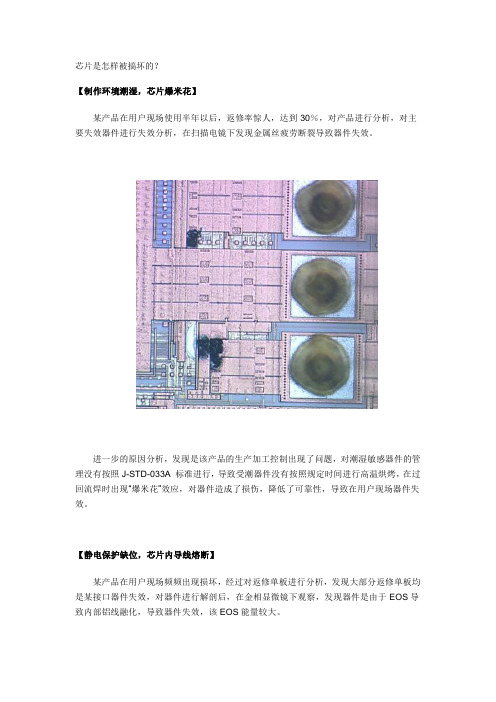
芯片是怎样被搞坏的?
【制作环境潮湿,芯片爆米花】
某产品在用户现场使用半年以后,返修率惊人,达到30%,对产品进行分析,对主要失效器件进行失效分析,在扫描电镜下发现金属丝疲劳断裂导致器件失效。
进一步的原因分析,发现是该产品的生产加工控制出现了问题,对潮湿敏感器件的管理没有按照J-STD-033A 标准进行,导致受潮器件没有按照规定时间进行高温烘烤,在过回流焊时出现“爆米花”效应,对器件造成了损伤,降低了可靠性,导致在用户现场器件失效。
【静电保护缺位,芯片内导线熔断】
某产品在用户现场频频出现损坏,经过对返修单板进行分析,发现大部分返修单板均是某接口器件失效,对器件进行解剖后,在金相显微镜下观察,发现器件是由于EOS导致内部铝线融化,导致器件失效,该EOS能量较大。
进一步分析和该铝条相连的管脚电路应用,发现电路应用设计不当,没有采用保护电路,在用户现场带电插拔产生的电浪涌导致该器件失效。
通过模拟试验再现了失效现象。
作者简介:单承建,深圳易瑞来科技公司总经理,深圳市电子学会可靠性专业委员会主任,电子工程专辑网站“设计高手”专栏嘉宾,公司主要业务为可靠性设计和相关技术咨询。
芯片失效分析
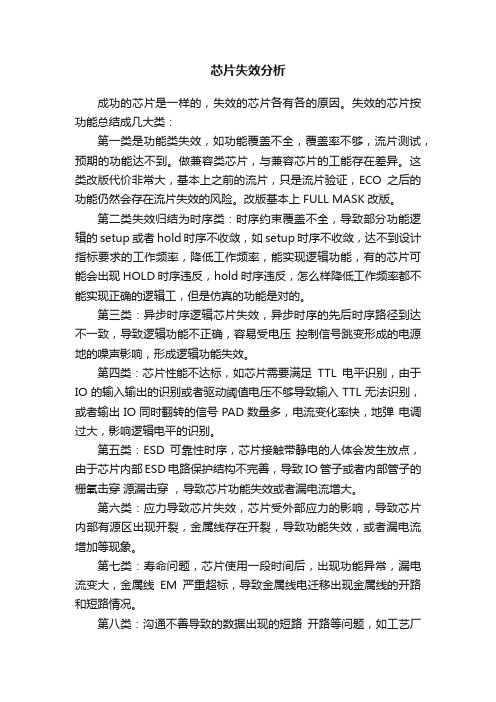
芯片失效分析成功的芯片是一样的,失效的芯片各有各的原因。
失效的芯片按功能总结成几大类:第一类是功能类失效,如功能覆盖不全,覆盖率不够,流片测试,预期的功能达不到。
做兼容类芯片,与兼容芯片的工能存在差异。
这类改版代价非常大,基本上之前的流片,只是流片验证,ECO之后的功能仍然会存在流片失效的风险。
改版基本上FULL MASK改版。
第二类失效归结为时序类:时序约束覆盖不全,导致部分功能逻辑的setup 或者hold时序不收敛,如setup时序不收敛,达不到设计指标要求的工作频率,降低工作频率,能实现逻辑功能,有的芯片可能会出现HOLD时序违反,hold时序违反,怎么样降低工作频率都不能实现正确的逻辑工,但是仿真的功能是对的。
第三类:异步时序逻辑芯片失效,异步时序的先后时序路径到达不一致,导致逻辑功能不正确,容易受电压控制信号跳变形成的电源地的噪声影响,形成逻辑功能失效。
第四类:芯片性能不达标,如芯片需要满足TTL电平识别,由于IO的输入输出的识别或者驱动阈值电压不够导致输入TTL无法识别,或者输出IO同时翻转的信号PAD数量多,电流变化率快,地弹电调过大,影响逻辑电平的识别。
第五类:ESD可靠性时序,芯片接触带静电的人体会发生放点,由于芯片内部ESD电路保护结构不完善,导致IO管子或者内部管子的栅氧击穿源漏击穿,导致芯片功能失效或者漏电流增大。
第六类:应力导致芯片失效,芯片受外部应力的影响,导致芯片内部有源区出现开裂,金属线存在开裂,导致功能失效,或者漏电流增加等现象。
第七类:寿命问题,芯片使用一段时间后,出现功能异常,漏电流变大,金属线EM严重超标,导致金属线电迁移出现金属线的开路和短路情况。
第八类:沟通不善导致的数据出现的短路开路等问题,如工艺厂没加SESRLING,导致TEST KEY与IO PAD 短路。
前后端沟通不善,出现用错版本等现象。
第九类:封装绑定导致,芯片虚假焊接,信号开路,绑定线过密出现,出现绑定线短路,导致芯片功能异常。
(二)半导体集成电路的失效机理及其预防措施

半导体集成电路的失效机理及其预防措施半导体集成电路的失效机理及其预防措施((小结小结))Xie Meng-xian. (电子科大,成都市)因为集成电路是由许多元器件组成的,所以其中元器件的失效必然会导致集成电路的失效,然而引起半导体集成电路(IC )失效的机理尚不仅如此,实际上还要复杂得多,有关系到设计方面的,也有关系到工艺方面的。
与集成电路设计密切相关的、能够做到部分或者完全避免的一些失效机理,主要有如下11种。
(1)静电放电静电放电((ESD ):IC 端头上积累的静电电荷可以产生很高的电压,从而会引起p-n 结击穿(造成短路或者大的漏电流)、或者使栅氧化层马上击穿或经过一段时间以后穿通。
为了防止静电放电所引起的失效,首先,在多数管脚上需要设置抗ESD 的保护器件;但连接到衬底的管脚、或者连接到大面积扩散区上的管脚(例如与npn 晶体管集电极相连的管脚),则不需要加保护器件。
其次,对于采用薄发射极氧化物工艺的BJT ,与管脚相连的内引线不能在薄的发射极氧化层上走线(穿越),否则可能引起薄发射极氧化层的击穿;不过对于采用较厚发射极氧化物的标准双极工艺而言,就不必考虑这种限制。
此外,在使用IC 时也要特别注意防止静电的产生和积累,如采用静电屏蔽,腕带、电烙铁和工作台要接地,室内要保持一定的湿度等。
(2)电迁移电迁移::IC 在大电流、高温下、长时间工作之后,就有可能产生电迁移失效,即出现金属电极连线发生断裂(开路)或者短路的现象。
防止电迁移的根本措施就是限制通过连线的最大电流(这与金属成分、厚度和温度有关)。
对于不穿越氧化层的导线,单位宽度上的电流一般要小于2mA/µm ;而对于穿越氧化层的导线,一般要小于1mA/µm 。
金属层的厚度和宽度越大,则抗电迁移的能力就越强。
另外,改进电迁移的主要措施有如:在电极金属Al 中掺入原子质量较大的Cu (0.5%~4%),这可使大电流承受能力提高5~10倍;采用耐热性好的势垒金属等。
IC失效分析报告
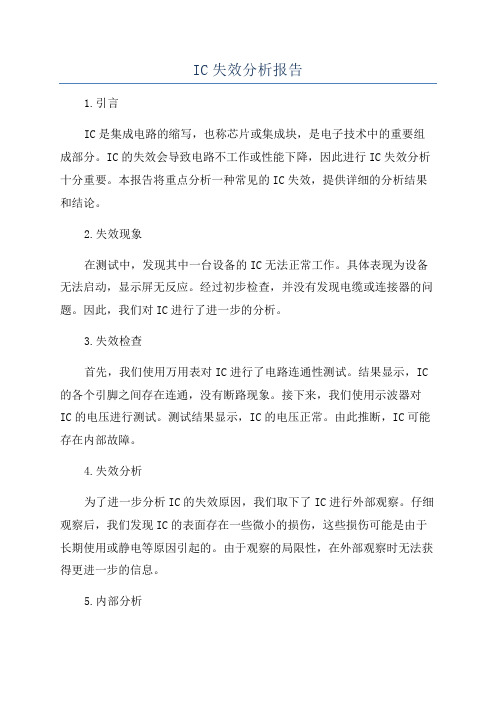
IC失效分析报告1.引言IC是集成电路的缩写,也称芯片或集成块,是电子技术中的重要组成部分。
IC的失效会导致电路不工作或性能下降,因此进行IC失效分析十分重要。
本报告将重点分析一种常见的IC失效,提供详细的分析结果和结论。
2.失效现象在测试中,发现其中一台设备的IC无法正常工作。
具体表现为设备无法启动,显示屏无反应。
经过初步检查,并没有发现电缆或连接器的问题。
因此,我们对IC进行了进一步的分析。
3.失效检查首先,我们使用万用表对IC进行了电路连通性测试。
结果显示,IC 的各个引脚之间存在连通,没有断路现象。
接下来,我们使用示波器对IC的电压进行测试。
测试结果显示,IC的电压正常。
由此推断,IC可能存在内部故障。
4.失效分析为了进一步分析IC的失效原因,我们取下了IC进行外部观察。
仔细观察后,我们发现IC的表面存在一些微小的损伤,这些损伤可能是由于长期使用或静电等原因引起的。
由于观察的局限性,在外部观察时无法获得更进一步的信息。
5.内部分析为了获得更详细的信息,我们决定对IC进行内部分析。
首先,我们使用显微镜对IC进行放大观察。
观察结果显示,IC的引脚存在一些微小的氧化现象。
进一步,在IC的内部芯片上,我们发现了一些烧毁的痕迹。
通过对比正常IC的结构,我们得出结论,IC可能是由于过电流或过热引起的内部烧毁。
6.结论综合以上分析结果,我们得出如下结论:IC的故障源于内部烧毁。
内部烧毁可能是由于过电流或过热引起的。
根据设备使用情况和失效现象,我们推测过电流是导致IC内部烧毁的主要原因。
由于设备的特殊性,我们建议在使用设备时加强电流的监测,并适时采取保护措施,以防止过电流对IC造成损伤。
7.对策针对IC的内部烧毁问题,我们提出以下对策建议:首先,加强设备使用人员的培训,让其了解设备的工作原理和使用事项。
其次,我们建议在设备中安装过电流保护器,以防止过电流对IC的影响。
最后,定期进行设备的维护和检查,及时清理设备内部的灰尘和杂质。
影响智能卡贯穿性裂纹失效的多种因素分析
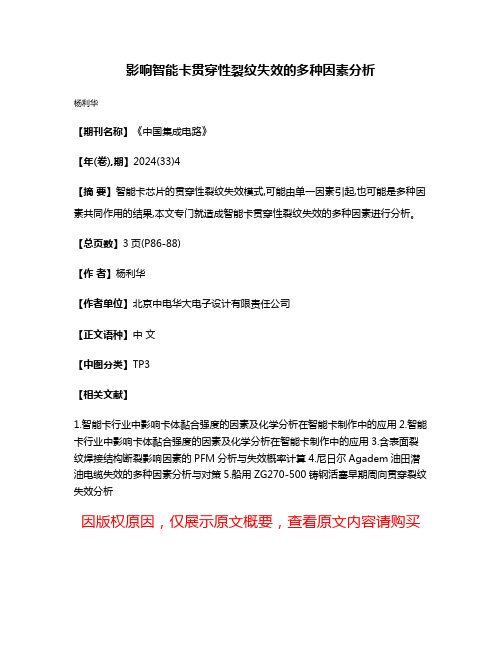
影响智能卡贯穿性裂纹失效的多种因素分析
杨利华
【期刊名称】《中国集成电路》
【年(卷),期】2024(33)4
【摘要】智能卡芯片的贯穿性裂纹失效模式,可能由单一因素引起,也可能是多种因素共同作用的结果,本文专门就造成智能卡贯穿性裂纹失效的多种因素进行分析。
【总页数】3页(P86-88)
【作者】杨利华
【作者单位】北京中电华大电子设计有限责任公司
【正文语种】中文
【中图分类】TP3
【相关文献】
1.智能卡行业中影响卡体黏合强度的因素及化学分析在智能卡制作中的应用
2.智能卡行业中影响卡体黏合强度的因素及化学分析在智能卡制作中的应用
3.含表面裂纹焊接结构断裂影响因素的PFM分析与失效概率计算
4.尼日尔Agadem油田潜油电缆失效的多种因素分析与对策
5.船用ZG270-500铸钢活塞早期周向贯穿裂纹失效分析
因版权原因,仅展示原文概要,查看原文内容请购买。
芯片卡损坏

芯片卡损坏芯片卡损坏是指存储在卡片上的芯片出现问题或损坏,导致卡片无法正常使用或无法读取其中的数据。
芯片卡损坏可能会引起诸如无法正常打开门禁、无法使用公交卡进行支付等问题。
下面将从芯片卡损坏的原因和解决方法两个方面来进行论述。
芯片卡损坏的原因主要有以下几点:1.物理损坏:芯片卡在使用过程中可能会受到物理撞击、摔落或压力等外力的作用,导致芯片的接触点松动、脱落或损坏,进而导致卡片无法正常读取。
2.电磁干扰:电磁干扰会对芯片卡的正常工作造成干扰,包括附近电磁场较强或电磁波较强的环境、使用电磁干扰源频繁接触等,都有可能引起芯片卡的损坏。
3.高温或低温环境:芯片卡对温度敏感,如果长时间处于较高或较低的温度环境中,芯片内部的电路可能会受到损坏,导致卡片无法正常工作。
4.电压过高或过低:芯片卡对电压的要求比较严格,如果电压过高或过低,会对芯片内部的电路造成不可逆的损坏,导致芯片无法正常工作。
当芯片卡损坏时,我们可以尝试以下几种解决方法:1.更换卡片:如果芯片卡存在物理损坏,比如接触点脱落或变形等问题,无法正常读取数据,那么更换一张新卡是最直接的解决办法。
2.修复芯片:对于受到物理损坏的芯片,我们可以尝试找到专业的维修人员进行修复。
他们可以通过焊接或更换芯片的方式来修复或替换坏损的芯片,使卡片恢复正常使用。
3.避免电磁干扰:为了避免由于电磁干扰而导致芯片卡损坏,我们可以尽量避免在电磁辐射较强的环境下使用芯片卡,尽量远离电磁波强烈的电器设备。
4.注意温度控制:为了避免芯片卡在高温或低温环境下损坏,我们可以尽量避免将芯片卡长时间暴露在极端温度条件下。
需要特别注意的是,在夏季高温季节或冬季寒冷季节,要注意不要将芯片卡暴露在阳光下或者靠近暖气等高温源的位置。
5.稳定电压供应:为了确保芯片卡正常工作,我们要注意供电稳定,尽量避免电压过高或过低的情况。
可以使用稳定性较好的直流电源或者稳压电源来为芯片卡提供电源。
综上所述,芯片卡损坏是由于物理损坏、电磁干扰、温度过高或过低、电压过高或过低等多种原因导致的。
芯片烧录不良的原因分析
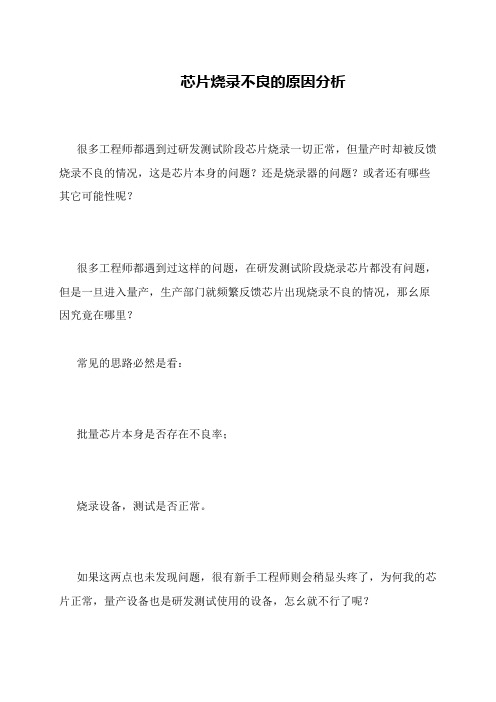
芯片烧录不良的原因分析 很多工程师都遇到过研发测试阶段芯片烧录一切正常,但量产时却被反馈烧录不良的情况,这是芯片本身的问题?还是烧录器的问题?或者还有哪些其它可能性呢? 很多工程师都遇到过这样的问题,在研发测试阶段烧录芯片都没有问题,但是一旦进入量产,生产部门就频繁反馈芯片出现烧录不良的情况,那幺原因究竟在哪里? 常见的思路必然是看: 批量芯片本身是否存在不良率; 烧录设备,测试是否正常。
如果这两点也未发现问题,很有新手工程师则会稍显头疼了,为何我的芯片正常,量产设备也是研发测试使用的设备,怎幺就不行了呢? 因为有几个隐含问题往往会被忽略: 1、你的量产烧录设备虽然和研发测试阶段设备一致,但是是否都采用了原厂仿真器?或者其他不适合量产的专烧设备? 这里要注意区分的是就烧录一颗芯片来说,专用的量产型烧录器/编程器,可实现一键操作,适合批量生产适合基础较弱的工厂人员,可以保证批量的良品率。
而原厂仿真器面向的是研发,操作过程无法做到如此简单,可能需要每次都操作电脑上位机按钮,或者需要连接再烧录,这些过程都增加了操作失误的人为可能性。
再者,仿真器烧录结果反馈也不明显,可能是打印字符串,或者是蜂鸣器,灯信号等,这些对于专业知识不强的工厂实际生产人员来讲都存在因不了解原理而失误的可能性,最后仿真器不是量产设备,不保证良品率的。
(仿真器外观参考图) (编程器外观参考图) 2、如果选择的烧录器/编程器是量产型没有问题,那幺是在线烧录?还是座烧?如果需要编程器适配器/芯片夹具,那幺夹具是否存在保养问题?夹具寿命目前怎样? 这点也经常被忽略,如果设备已经是量产型编程器,之前烧录也正常,那就要看看你的烧录夹具,也就是通常所说的烧录座,或者编程器适配器究竟用了多久,烧录夹具是有使用次数也就是通常说的寿命的,但是国内目前大多厂家都未提供专业烧录座/夹具的使用操作手册或者保养文档提供给客户,网上也很难下载到对应的,对于次数具体说明更是朦胧,这也导致很多烧录不良问题无法判断。
- 1、下载文档前请自行甄别文档内容的完整性,平台不提供额外的编辑、内容补充、找答案等附加服务。
- 2、"仅部分预览"的文档,不可在线预览部分如存在完整性等问题,可反馈申请退款(可完整预览的文档不适用该条件!)。
- 3、如文档侵犯您的权益,请联系客服反馈,我们会尽快为您处理(人工客服工作时间:9:00-18:30)。
IC卡中薄芯片碎裂失效机理的研究关键词: IC卡芯片碎裂失效机理摘要:薄/超薄芯片的碎裂占据IC卡早期失效的一半以上,其失效模式、失效机理亟待深入研究。
本文分析了芯片碎裂的失效模式和机理,并结合实际IC卡制造工艺以及IC卡失效分析实例,就硅片减薄、划片、顶针及卡片成型工艺对薄IC芯片碎裂的影响进行深入探讨。
1 碎裂概述芯片碎裂是硅器件的一种失效模式,约占早期失效总数的1%,而对于使用薄/超薄芯片的IC卡,芯片碎裂则占其失效总数的一半以上。
虽然,通过改进封装设计、限制器件使用环境可以有效地防止芯片碎裂引起的器件失效,但即使在良好的设计、合格的制造工艺以及规范的使用环境下,依然存在着一定的芯片碎裂几率。
随着器件可靠性级别和系统复杂程度的不断提高,十分有必要对芯片碎裂失效机理加以进一步的研究。
芯片碎裂归根结底是由应力造成的,但是其产生的原因随具体情况而不同:硅片前道工艺中的外延层淀积、扩散和离子注入、氧化、退火、淀积形成欧姆接触、金属内连、钝化层淀积:硅片后道工艺中的机械减薄(研磨、抛光)、化学减薄(湿法或者干法刻蚀)、背面金属层淀积;封装工艺中的划片、上芯、压焊、塑封等都将会产生或影响硅片/芯片的应力。
其中,减薄、上芯、压焊、塑封是产生芯片碎裂隐患的主要工序。
更为严重的是,一般在工艺过程中观察不到碎裂现象,只有经过热固化或者器件热耗散时的瞬时加热,由芯片和封装材料热膨胀系数存在差异或者使用中受外界应力作用,芯片碎裂才会最终显现。
例如:穿过结的裂纹可能导致短路或者漏电,裂纹也可能全部或者部分截断电路。
最为致命的是,裂纹引起的这些效应只有当有热或者电流通过时才会显现,而标准的电学测试则根本无法检测到这些失效。
根据抽样统计,芯片碎裂引起的IC卡失效约占据失效总数的6 0%。
裂纹形状多为“十”字、“T”字型,亦有一部分为横贯芯片的单条裂纹,并在中心顶针触碰部位略有弯折,约50%以上的碎裂芯片,其裂纹位于芯片中央附近并垂直于边缘;其余芯片的裂纹则靠近芯片边缘或集中于芯片一角。
2 碎裂机理芯片强度是研究芯片碎裂的最重要参数。
芯片强度各不相同,只有强度最低的才最容易碎裂失效。
此外,强度分布范围很广,那些最“脆弱”的芯片碎裂时候的强度只相当于芯片平均强度的几分之一。
因此只需设法将最“脆弱”芯片的强度提高或者予以剔除,就能从根本上提高芯片整体强度。
硅和其它半导体材料属于高脆性材料,在材料完整无缺陷时,外加应力在样品上的分布是均匀的。
它们在碎裂时是由于原子间的键发生断裂,因而它们的机械强度就决定于键的强度。
在材料表面出现划痕后,外加应力时,出现应力集中现象。
特别对于垂直于表面划痕的张应力,应力集中于裂纹的尖端。
裂纹的扩展取决于裂纹尖端的应力分布。
当其应力超过材料的应力强度因子时,裂纹就会失去稳定而发生扩展。
因而对于脆性材料来说,表面划痕对材料的强度有很大的影响。
尤其是对于半导体器件中的薄IC芯片,它的厚度很小,表面划痕的影响将更为严重。
对于长度为a的单边裂纹,裂纹扩展的判据是:其中,E是材料的杨氏模量;γ是表面能;a是裂纹长度。
考虑二维情形,对于半椭圆型的裂纹,若其深为a,长为2b,碎裂面垂直于芯片表面,则满足以下关系式下面,根据芯片碎裂物理机理并结合实际IC卡制造工艺以及IC 卡失效分析实例,对IC卡薄芯片的碎裂问题加以探讨。
需要说明的是,在样品失效分析中,观察IC卡中芯片的方法是:先采用酸腐蚀的方法将IC卡表面的导电金属层和芯片粘结剂除去,然后在显微镜下从背面观察芯片完整性。
实验中腐蚀过程分多步进行,以防止反应过分剧烈,酸液钻蚀芯片周围及底部环氧,引起芯片碎裂;每步反应后均用热水冲洗,以避免剧烈温差导致裂片发生。
同时将功能正常的IC卡进行芯片暴露分析,采用了相同的分析程序,结果其背面均未发现裂缝,说明了我们所采取的芯片暴露方法是可行和可信的。
3 碎裂失效机理普通的IC卡是用导电的或绝缘的黏合材料将减薄后芯片贴到胶带或者引线框上,进行金丝压焊,接着用包封材料形成模块。
然後再用氰基丙烯酸酯黏合剂或热熔技术把模块装在塑料卡上面的凹槽中,成为IC卡成品。
硅片减薄、划片、模块工艺和成型工艺将对IC卡薄芯片碎裂产生重要的影响。
3.1 硅片减薄硅片减薄,现一般采用的磨削法是利用固定在特定模具上的尺寸适宜的金刚砂轮对硅片背面进行磨削,金刚砂轮基材通常是陶瓷、环氧树脂或塑性材料。
标准的硅片减薄工序包括:粗磨、细磨、腐蚀,这三道工序相互配合,调节参数以得到最终所要求的厚度、最小的厚度变化以及最优的表面品质。
硅片减薄前的原始厚度大约为725μm(直径200mm硅片),通过磨削工艺减薄至150μm甚至更薄,先进行的粗磨工艺磨削量占总减薄量的90%以上,为525-565μm。
粗磨过程中会引起硅片的晶格损筋,其损伤深度可以达20-30μm。
随后进行的细磨工艺磨削量只占总减薄量的10%,为10-50μm。
细磨将消除粗磨时造成的晶格损伤,但同时也会对硅片表面产生轻微损伤,其深度约为15-20μm。
磨片引起的背面损伤极大地影响了硅片的强度,尤其在硅片不同介质层的作用下,薄硅片很容易弯曲变形,产生了碎裂隐患。
在细磨工艺后采用湿法腐蚀工艺则可以去除硅片背面的残留的晶格损伤层,大大增强了芯片强度,避免硅片因残余应力而碎裂。
硅片的损伤是与磨片损伤痕迹相关的,去除/部分去除损伤痕迹,芯片强度将大大增强,损伤层腐蚀掉越多,芯片强度越大。
通常腐蚀2 5μm深度左右的硅片可得到最大的破断强度值。
在对芯片正面和背面进行的破坏性测试中,腐蚀25μm的芯片,其破坏所需外力远远大于腐蚀深度为3μm或者10μm的芯片。
试验表明,要接近该最大破断力,腐蚀深度至少为10~15μm。
根据Griffith微裂纹扩展理论,考虑一维裂纹扩展,假设腐蚀后芯片背面残留划痕长为a,则由式(1)得平面应力状态常载荷条件下碎裂的临界强度:由此得到σ与芯片背面残留划痕长度的对应关系。
二维情况下,假设划痕长为2b,深为a,则由式(2)简化得平面应力状态常载荷条件下碎裂的临界强度由此得到口与芯片背面残留划痕长度、深度的对应关系。
当划痕长度大于1μm时,芯片碎裂临界强度急剧降低,并趋于稳定值。
上述分析表明,背面磨削技术及其工艺对芯片碎裂失效有着直接的影响,近年来,国内外不断开展硅片背面磨削新技术和新工艺的研究,通过开发新型的超精密磨床、研究超细粒度金刚石砂轮及其应用技术以及实现背面减薄工艺集成来提高硅片减薄的效率、减小表面和亚表面损伤碎裂。
3.2 划片工艺减薄后的硅片粘在一个带有金属环或塑料框架的薄膜(常称为蓝膜)上,送进划片机进行划片。
芯片划片槽的断面往往比较粗糙,有少量微裂纹和凹槽存在;同时有些地方划片时并未划到底,取片时,顶针顶力作用致使芯片“被迫”分离,致使断口呈不规则状。
实验显示,划片引起的芯片边缘的损伤同样会严重影响芯片的碎裂强度。
因而,作为划片工艺的改进,相继开发了DBG和DBT方法。
先划片后减薄(DBG,Dicing Before Grinding)法,即在背面磨削之前将硅片的正面切割出一定深度的切口,然后再进行背面磨削:减薄划片法(DBT,Dicing By Thinning),即在减薄之前先用机械的或化学的方式切割出切口,用磨削方法减薄到一定厚度以后,采用ADP腐蚀技术去除掉剩余加工量,实现裸芯片的自动分离。
这两种方法都很好地避免/减少了减薄引起的硅片翘曲以及划片引起的芯片边缘损伤,特别对于D BT技术,各相同性的Si刻蚀剂不仅能去除硅片背面研磨损伤,而且能除去芯片边缘由于划片引起的微裂缝和凹槽,大大增强了芯片的抗碎裂能力。
3.3 模块工艺模块工艺包括装片机顶针从薄膜上顶起芯片,真空吸头吸起芯片将其粘结到芯片卡的引线框上,具体操作所示。
装片过程中,顶针的伸长长度、拾取高度、吸嘴的大小必须随芯片厚度、芯片大小不同而需要进行调整,以防止顶针刺破蓝膜而损伤芯片。
但是,在装片机工艺参数调整不当情况下,如:顶力不均或过大,顶针接触位置有较大偏移,作用时间过长等,很容易导致顶针刺穿蓝膜而直接作用于芯片,并在芯片背部产生一定量的滑移过程,在其中部留下较大面积的规律性的划伤痕迹。
芯片裂纹位于顶针产生的划痕附近,表明顶针划痕严重影响了芯片强度,直接导致芯片碎裂。
顶针尖端的半径较小,在1N顶力的情况下,容易产生数十至数百MPa的瞬间压强,对比式(3),(4)的计算结果可知,顶针过程是芯片碎裂的一个主要诱因。
对于顶针划痕,通过对其形状、大小进行统计,发现划痕多为直线并带有弯钩形状,多出现于硅片裂纹处或者在其附近,且裂纹在划痕处均有不同程度的弯折。
擦痕尺寸较大,一般长数十μm,宽大于10μm,。
芯片碎裂临界强度约为70MPa,可知此类擦伤将导致芯片强度大大降低,极易造成芯片直接/间接碎裂。
3.4 成型工艺IC卡成型工艺中,需要在基片上用铣削的方法加工凹槽,在凹槽内粘贴模块。
IC卡工艺标准对模块在卡片上位置精度有较高的要求,需达到+-5μm。
考虑到工艺制作工艺因素,模块厚度、卡基凹槽几何形状等往往存在一定差异,致使两者匹配不佳,引发较大应力的产生,加上使用过程中的不同材料的热胀冷缩或者外力扭曲,容易引起芯片碎裂。
因此,迫切需要提升环氧树脂包封固化后打磨的精度,降低模块厚度极差,同时提高凹槽铣削精度,以获得两者的最佳匹配。
除了上面所述的4个因素以外,其他的诸如:芯片粘合过程中芯片与导电胶之间产生的气泡,引线键合时劈刀的瞬时作用等等,都是芯片碎裂的潜在/直接诱因,经过包封、后固化的过程,整个芯片是封闭的,温度经过室温→175℃(包封)→室温(包封后)→175℃(后固化)→室温的不断变化,应力无处释放,加上使用过程中的冷热冲击或者机械扭曲,也有可能导致最终芯片裂纹的产生。
4 结论薄芯片碎裂已经成为IC卡失效的主要模式之一,硅片减薄、划片、装片时的顶针过程以及IC卡成型工艺是芯片碎裂的主要诱因。
通过改进研磨材料和研磨工艺,采用更先进的划片技术,改善装片机的工艺参数,优化IC卡的成型工艺,将有利于降低薄芯片的碎裂几率,从而进一步提高IC卡的可靠性。