压铸车间生产过程质量控制办法
压铸车间的管理制度范文(3篇)

压铸车间的管理制度范文一、安全管理制度1. 压铸车间所有员工必须参加安全培训,并严格遵守相关安全操作规程。
2. 凡是进入压铸车间的人员必须佩戴个人防护装备,包括防护眼镜、耳塞、手套等。
3. 在生产过程中,不得随意调整设备,如需要调整必须关停机器并由专人负责操作。
4. 禁止未经授权擅自离开工作岗位,严禁私自拿取或使用他人工具和设备。
5. 每日生产结束后,必须对设备进行巡检,确保无异常情况,并及时上报主管领导。
二、质量管理制度1. 按照产品生产和质量控制要求,严格执行生产工艺,确保产品质量。
2. 每个工序的操作人员必须严格按照工艺要求,进行标准化操作。
3. 产品生产过程中,必须进行质量抽检,并及时记录抽检结果,确保产品质量符合标准。
三、生产管理制度1. 按照生产计划进行生产调度,确保生产进度和交货期的准时完成。
2. 每日生产结束后,必须进行设备清理和保养,并及时记录设备清理和保养情况。
3. 严禁生产中的浪费和返工,如有发现必须及时上报并进行整改。
四、岗位责任制度1. 各岗位人员必须熟悉并执行本岗位的工作职责,严格按照作业指导书进行操作。
2. 对于工作中出现的问题和提出的改进建议,必须及时进行反馈和记录。
3. 严格遵守作息时间,不得擅自旷工或迟到早退,如有特殊情况必须提前请假。
五、环境保护制度1. 严禁随意丢弃废料和化学药品,必须按照规定的方式进行分类和处理。
2. 节约用电,合理使用电力设备,减少能源浪费。
3. 在设备维修和更换时,必须进行合理排放和处理。
以上是对压铸车间管理制度的基本范本,具体的制度和规定可以根据企业的实际情况进行调整和完善。
同时,还需要相关部门和岗位人员共同遵守和执行,以确保车间的正常运营和安全高效的生产。
压铸车间的管理制度范文(2)以下是一个压铸车间的管理制度范文:压铸车间管理制度第一章总则第一条为规范压铸车间的管理,提高生产效率和产品质量,保障生产安全,特制定本管理制度。
第二章压铸车间的职责和任务第二条压铸车间的主要职责是进行压铸生产,包括铝合金压铸和锌合金压铸等工艺。
铸造生产过程质量控制点

铸造生产过程质量控制点铸造生产过程质量控制点铸造生产过程质量控制点是指在铸造生产过程中,通过采取一系列控制措施,以确保铸件质量达到设计要求的关键环节和要点。
铸造生产过程质量控制点的正确选择和实施,对于提高铸造生产过程质量、减少废品率具有重要意义。
以下是铸造生产过程中一些常见的质量控制点。
1.原材料控制原材料是影响铸件质量的关键因素之一。
在铸造生产过程中,需要对原材料进行严格的控制,包括熔炼炉料及加入剂的选择、原材料配比的控制等。
只有选择合适的原材料并正确使用,才能保证铸造产品质量的稳定性和一致性。
2.熔炼控制熔炼过程是铸造生产中最关键的环节之一。
在熔炼过程中,需要控制炉温、炉料的投入速度、炉内压力等参数,以确保金属液的质量稳定。
对于特殊材料的熔炼过程,还需要控制熔炼环境的气氛、熔炼时间等因素。
3.浇注控制浇注过程是将熔融金属注入到型腔中的过程。
在浇注过程中,需要控制浇注速度、浇注温度、浇注方式等因素,以保证浇注质量和铸件的致密性。
还需要控制浇注过程中金属液的气体排出情况,避免气孔的产生。
4.型腔控制型腔是铸造中形成铸件形状和尺寸的关键部位,对铸件质量有着重要影响。
型腔控制包括型腔设计、制造和维护等环节。
必须确保型腔的准确尺寸和光洁度,避免型腔表面的破损和变形,以确保铸件的形状精度和表面质量。
5.冷却控制冷却过程是铸件从熔融状态到固态过程中的一个关键环节。
在冷却过程中,需要控制冷却速度、冷却介质、冷却时间等因素,以保证铸件组织的均匀性和致密性。
还需要控制冷却过程中的温度梯度,避免铸件产生应力和变形。
6.热处理控制对于某些特殊材料或要求较高的铸件,还需要进行热处理过程。
热处理过程包括加热、保温和冷却等环节。
在热处理过程中,需要控制温度、保温时间、冷却速度等参数,以确保铸件组织的改善和性能的提升。
7.表面处理控制铸件的表面处理是为了提高铸件的表面质量和耐腐蚀性。
表面处理包括喷砂、抛光、电镀等工艺。
在表面处理过程中,需要控制处理剂的使用和浸溶时间,以保证铸件表面的光洁度和处理效果。
铸造质量控制

铸造质量控制一、引言铸造是一种重要的创造工艺,用于生产各种金属零件和构件。
在铸造过程中,质量控制是确保最终产品符合规格和要求的关键因素。
本文将详细介绍铸造质量控制的标准格式文本,包括质量控制的目的、方法和流程等。
二、质量控制目的铸造质量控制的目的是确保生产的铸件符合设计要求,并具有良好的机械性能和表面质量。
通过质量控制,可以减少缺陷率和废品率,提高生产效率和产品质量,降低成本和风险。
三、质量控制方法1. 工艺控制铸造工艺控制是铸造质量控制的基础。
包括合理的铸造工艺参数设置、选用合适的铸造材料、控制熔炼和浇注温度、控制浇注速度和压力等。
通过优化工艺参数,可以减少缺陷的产生,提高铸件的质量。
2. 材料控制铸造材料的选择和控制对铸件质量至关重要。
包括选用合适的铸造合金、控制原材料的化学成份和物理性能、控制熔炼过程中的杂质含量等。
通过严格的材料控制,可以提高铸件的强度、硬度和耐腐蚀性能。
3. 设备控制铸造设备的选择和控制对铸件质量也有重要影响。
包括选用合适的铸造设备、控制设备的精度和稳定性、定期维护和保养设备等。
通过优化设备控制,可以提高铸件的尺寸精度和表面质量。
4. 检测控制铸造质量控制中的检测控制是确保铸件质量的重要环节。
包括非破坏性检测和破坏性检测两种方式。
非破坏性检测包括超声波检测、射线检测和磁粉检测等,用于检测铸件的内部缺陷;破坏性检测包括拉伸试验、冲击试验和硬度试验等,用于检测铸件的机械性能。
通过合理的检测控制,可以及时发现和排除铸件的缺陷,确保产品的质量。
四、质量控制流程1. 铸造前准备在铸造前,需要进行充分的准备工作。
包括准备合适的模具和芯子、准备合适的铸造材料、准备合适的铸造设备等。
同时,需要对模具和设备进行检查和维护,确保其正常工作。
2. 铸造过程控制在铸造过程中,需要严格控制各项工艺参数。
包括控制熔炼和浇注温度、控制浇注速度和压力、控制铸造时间等。
同时,需要对铸件进行实时监测和记录,确保铸件的质量。
压铸车间质量安全管理制度

第一章总则第一条为确保压铸生产过程中的质量安全,预防安全事故发生,保障员工生命财产安全,提高生产效率,特制定本制度。
第二条本制度适用于公司所有压铸车间及其相关工作人员。
第三条压铸车间质量安全管理工作遵循“安全第一、预防为主、综合治理”的原则。
第二章组织与管理第四条压铸车间设立质量安全管理部门,负责全车间的质量安全管理工作。
第五条车间主任为质量安全第一责任人,对车间的质量安全工作全面负责。
第六条车间质量安全管理部门的主要职责:1. 制定和实施质量安全管理制度及操作规程;2. 组织开展质量安全教育培训;3. 监督检查生产过程中的质量安全情况;4. 调查处理质量安全事故;5. 定期向上级部门汇报质量安全工作。
第三章安全生产管理第七条严格遵守国家有关安全生产的法律、法规和标准。
第八条压铸车间生产设备、工具必须符合国家规定的技术标准,定期进行检修和维护。
第九条严禁违规操作,禁止操作人员将身体任何部分伸进机器的移动部位。
第十条机台电器箱内外严禁堆放任何东西,确保电器设备安全运行。
第十一条给汤机自动作动中,严禁操作人员或其他无关人员身体的任何部位靠到射出料管部位。
第十二条上班期间严禁睡觉、聊天、喧哗,严禁在车间内抽烟。
第十三条上班时必须穿工作服、戴识别证及工作帽,不准穿拖鞋、短裤。
第十四条上模前,必须把机台模壁面清理干净。
第十五条各责任区内卫生过差,发现有油污、纸屑、杂物等,当班责任区班长和机台操作人员警告30元罚款处罚。
第十六条各机台开机中不开机台冷却水者,当班班长警告30元处罚,员工小过50元处罚。
第十七条上班后,在机台模具正常情况下,在规定上班时间10分钟之内开机操作。
最迟不能超过15分钟。
下班前清扫时间不能超过半小时。
第十八条吃饭或下班因模具故障或其他原因停机时,必须先关掉马达和排风扇,或其他操作电源。
第四章质量管理第十九条严格执行国家有关产品质量的法律法规和标准。
第二十条压铸产品必须符合国家标准和客户要求。
压铸车间质量管理方案

压铸车间质量管理方案压铸车间是生产压铸件的重要场所,质量管理在压铸车间中尤为重要。
良好的质量管理方案能够确保产品质量稳定,提高生产效率,降低生产成本,增强企业竞争力。
本文将从流程控制、设备维护、员工培训和质量监控四个方面,探讨如何建立一套有效的压铸车间质量管理方案。
一、流程控制压铸车间的生产流程是影响产品质量的关键因素之一。
为确保产品质量稳定,应建立科学、规范的生产工艺流程,并制定详细的作业指导书。
作业指导书应包括每个工序的具体操作步骤、操作要点、质量要求和质量检验方法等内容,以确保每个工序的操作符合质量要求。
同时,应加强对生产工艺流程和作业指导书的培训,提高员工对流程的理解和执行能力。
二、设备维护设备是保证产品质量的基础。
为确保设备正常运行,应建立完善的设备维护制度。
制定设备维护计划,按照计划进行定期保养、维修和更换备件,确保设备的可靠性和稳定性。
同时,建立设备维护记录,记录设备维护情况和故障处理过程,以便分析设备故障原因,采取相应措施预防故障的发生。
三、员工培训员工是质量管理的重要一环。
为提高员工的职业素质和技术水平,应加强员工培训。
培训内容包括质量意识培养、工艺知识培训、操作技能培训和质量管理知识培训等。
培训形式可以采取内部培训、外部培训和岗位轮换等方式,使员工全面掌握所需的知识和技能,提高工作效率和质量水平。
四、质量监控质量监控是质量管理的核心环节。
建立有效的质量监控体系,可以及时发现和纠正质量问题,确保产品质量符合要求。
质量监控包括原材料检验、过程控制和成品检验等环节。
原材料检验应严格按照标准进行,确保原材料质量稳定可靠;过程控制要加强对关键工序和关键参数的监控,及时调整工艺参数,防止质量问题的发生;成品检验要建立完善的检验方法和标准,对产品进行全面检测,确保产品质量符合要求。
以上是建立一套有效的压铸车间质量管理方案的主要内容。
通过科学的流程控制、设备维护、员工培训和质量监控,能够有效提高产品质量,确保压铸车间的生产效率和竞争力。
铸造质量控制

铸造质量控制在现代工业生产中,铸造是一种常见的创造工艺,涉及到各种金属和合金的加工,其质量控制对产品的性能和可靠性至关重要。
本文将从不同角度探讨铸造质量控制的重要性和方法。
一、原材料质量控制1.1 选择合适的原材料:铸造过程中所使用的原材料对最终产品的质量有着决定性影响。
因此,必须选择符合标准要求的原材料,包括金属、砂型、石膏等。
1.2 原材料检测:在使用原材料之前,需要进行严格的检测,确保其符合生产要求。
例如,金属原料需要进行化学成份、机械性能等多方面的检测。
1.3 原材料存储管理:正确的原材料存储管理可以有效避免原材料受潮、氧化等问题,影响产品质量。
因此,需要建立严格的存储管理制度。
二、工艺参数控制2.1 控制铸造温度:铸造温度的控制对产品的组织结构和性能有着重要影响。
需要根据不同金属材料的特性,合理控制铸造温度。
2.2 控制浇注速度:浇注速度直接影响产品的凝固过程和内部缺陷情况。
需要根据产品的形状和尺寸,合理控制浇注速度。
2.3 控制冷却时间:冷却时间的长短会影响产品的晶粒大小和组织致密度。
因此,需要合理控制冷却时间,确保产品质量。
三、模具设计和创造控制3.1 合理设计模具结构:模具设计的合理性直接影响产品的尺寸精度和表面质量。
需要根据产品要求,设计出合适的模具结构。
3.2 选择优质模具材料:模具材料的质量对模具的使用寿命和稳定性有着重要影响。
需要选择高强度、高耐磨的模具材料。
3.3 严格控制模具加工精度:模具加工精度直接决定了产品的尺寸精度和表面质量。
因此,需要严格控制模具的加工精度,确保产品质量。
四、工艺流程控制4.1 制定详细的工艺流程:在铸造过程中,需要制定详细的工艺流程,包括浇注、冷却、清理等各个环节,确保每一个环节都符合标准要求。
4.2 实施严格的工艺控制:在生产过程中,需要严格按照工艺流程执行,确保每一个步骤都得到正确执行,避免产生质量问题。
4.3 定期进行工艺检测:定期对工艺流程进行检测和评估,及时发现问题并进行调整,以确保产品质量稳定。
铸造生产过程的质量控制

铸造生产过程的质量控制铸造生产过程的质量控制1·引言本文档旨在提供一个铸造生产过程的质量控制参考框架,以确保铸造产品质量达到预期标准。
本文档分为以下几个部分:质量策划、工艺流程控制、工艺参数控制、检验与测试、不合格品处理和纠正措施。
2·质量策划在铸造生产过程中,质量策划是确保产品质量的重要步骤。
以下是质量策划的细化内容:2·1 确定产品质量标准和规范2·2 制定产品及生产过程检验计划2·3 根据产品特性确定质量保证措施2·4 制定质量培训计划2·5 确定质量审核和监督措施3·工艺流程控制良好的工艺流程控制是确保铸造生产过程质量稳定的关键。
以下是工艺流程控制的细化内容:3·1 设计工艺流程图3·2 确定工艺参数范围3·3 制定操作规程和作业指导书3·4 确定关键控制点及控制方法3·5 制定工艺异常处理程序4·工艺参数控制控制工艺参数是确保产品质量一致性的关键。
以下是工艺参数控制的细化内容:4·1 确定关键工艺参数4·2 设定合理的工艺参数范围4·3 使用计量设备进行工艺参数检测与记录4·4 制定工艺参数调整措施5·检验与测试检验与测试是铸造生产过程中质量控制的重要环节,以保证产品符合标准和规范要求。
以下是检验与测试的细化内容:5·1 制定检验项目及方法5·2 确定样本容量和频率5·3 质量控制检验和产品检验5·4 缺陷评定和分类5·5 检验记录和报告6·不合格品处理对于不合格品,需要采取合适的处理措施,以确保产品质量和客户满意度。
以下是不合格品处理的细化内容:6·1 不合格品鉴定和分类6·2 制定不合格品处理程序6·3 进行原因分析和改进措施制定6·4 进行不合格品追溯和召回措施7·纠正措施在发现质量问题时,需要及时采取纠正措施以防止再次发生。
铸造生产过程质量控制点
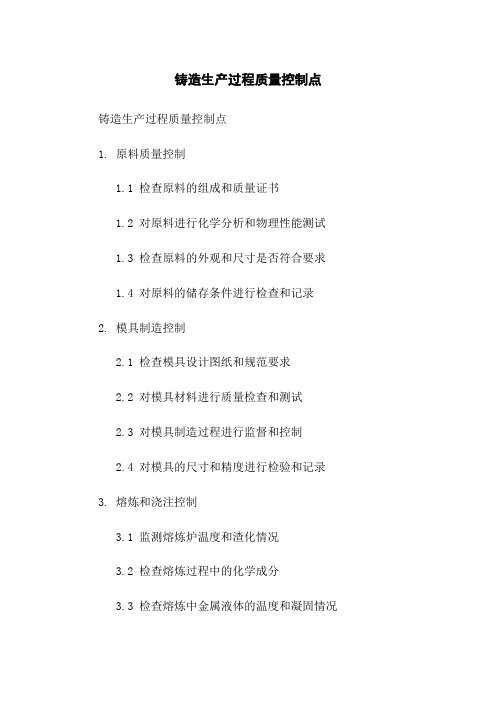
铸造生产过程质量控制点铸造生产过程质量控制点1. 原料质量控制1.1 检查原料的组成和质量证书1.2 对原料进行化学分析和物理性能测试 1.3 检查原料的外观和尺寸是否符合要求1.4 对原料的储存条件进行检查和记录2. 模具制造控制2.1 检查模具设计图纸和规范要求2.2 对模具材料进行质量检查和测试2.3 对模具制造过程进行监督和控制2.4 对模具的尺寸和精度进行检验和记录3. 熔炼和浇注控制3.1 监测熔炼炉温度和渣化情况3.2 检查熔炼过程中的化学成分3.3 检查熔炼中金属液体的温度和凝固情况3.4 对铸件的浇注过程进行监控和记录4. 铸造件外观和尺寸控制4.1 对铸件外观进行目测和检验4.2 使用光谱仪和显微镜对铸件进行化学成分和微观结构的分析4.3 使用激光扫描仪等设备对铸件的尺寸进行测量和记录4.4 对铸件进行外观和尺寸的合格判定5. 热处理控制5.1 对铸件进行退火、正火、淬火等热处理工艺的控制5.2 监测热处理过程中的温度和时间5.3 对热处理后的铸件进行硬度测试和金相分析5.4 对热处理后的铸件进行尺寸和外观的检验和记录6. 特殊工艺控制6.1 对特殊工艺参数进行监控和调整6.2 对特殊工艺工序进行质量检查和控制6.3 对特殊工艺产品的性能进行测试和验证附件:1. 铸造原料的质量证书样本2. 模具设计图纸和规范要求范本3. 铸造工艺流程图4. 铸造件外观和尺寸检验记录表5. 热处理工艺参数记录表6. 特殊工艺工序质量检查表法律名词及注释:1. 质量证书:指由生产厂商或供应商提供的证明原料质量合格的文件。
2. 模具设计图纸:指铸造过程中用于指导模具制造的图纸和规范要求。
3. 化学成分:指铸件材料中各元素的含量。
4. 光谱仪:用于分析金属材料化学成分和物理性能的仪器。
5. 显微镜:用于观察和分析铸件的微观结构和缺陷的仪器。
6. 激光扫描仪:用于测量和记录铸件尺寸的仪器。
7. 退火:指通过加热和冷却的方式改变金属材料的组织结构和性能的工艺。
铸造生产过程质量控制点

铸造生产过程质量控制点铸造生产过程质量控制点1. 概述铸造是一种常用的金属加工方法,广泛应用于制造各种零部件和工件。
在铸造生产过程中,质量控制是非常重要的,直接影响产品的质量和性能。
本文将介绍铸造生产过程中的质量控制点,以确保产品符合设计要求和质量标准。
2. 材料选择与检验铸造中最关键的环节之一是材料的选择和检验。
合适的材料选择可以保证产品具有所需的机械性能和化学成分。
在进行铸造前,应对材料进行严格的检验,包括外观检查、成分测试、力学性能测试等。
只有合格的材料才能进入下一步的生产工艺。
3. 模具制造与维护模具的质量直接关系到铸件的成型质量。
模具应具备足够的强度和硬度,能够承受铸造过程中的温度和压力。
铸造生产过程中,应定期检查和维护模具,确保其几何尺寸的准确性,防止模具磨损或变形,导致铸件尺寸偏差或表面缺陷。
4. 液态金属处理在铸造过程中,金属通常以液态形式存在,因此对液态金属的处理十分重要。
首先,需要控制金属的准确浇注温度,以确保其流动性和润湿性。
其次,应对液态金属进行除杂处理,以去除杂质和气泡。
最后,在金属浇注前,需要进行温度和成分的检测,以保证金属液在合适的条件下进行铸造。
5. 铸造工艺控制铸造工艺是决定铸件质量的关键因素之一。
在铸造过程中,需要控制浇注速度、温度、浇注压力等参数,以确保铸件形状的准确性和表面的质量。
此外,还需要对铸件冷却速度进行控制,以防止产生缩孔、夹杂等缺陷。
6. 后续处理与热处理铸件在铸造完成后,通常还需要经过一系列的后续处理和热处理过程。
后续处理包括去除毛刺、修整表面、修复缺陷等操作,以提高铸件的外观质量。
热处理则可以改善铸件的机械性能和材料结构,通过控制热处理参数,如温度、时间等,可以获得所需的性能指标。
7. 检测与检验为了确保铸件质量符合要求,需要对铸件进行严格的检测和检验。
常用的检测方法包括尺寸检测、外观检查、材料成分分析、力学性能测试等。
这些检测可以通过非破坏性检测方法,如超声波检测、X射线检测等,或者通过破坏性检测方法,如拉伸试验、冲击试验等进行。
压铸车间的管理制度范本(三篇)

压铸车间的管理制度范本压铸车间管理制度第一章总则第一条为规范和科学管理压铸车间的工作,保障员工的安全,提高生产效率和产品质量,制定本制度。
第二条本制度适用于压铸车间的所有员工和管理人员。
第三条压铸车间的管理应遵循“安全第一,质量至上,效益为本”的原则。
第四条压铸车间的每个员工都有责任遵守本制度,并按照制度规定的要求履行岗位职责。
第五条压铸车间领导应确保本制度的有效执行,并负责定期检查和评估制度的执行情况。
第二章压铸车间安全管理第六条压铸车间的安全管理应遵循以下原则:1. 加强安全意识教育,提高员工的安全意识和自我保护能力;2. 定期进行安全培训,并加强员工对危险源的识别和防范;3. 建立安全设施,保证压铸生产过程的安全;4. 建立应急预案,提高应急处理能力。
第七条压铸车间的安全生产责任制:1. 压铸车间主管负责制定安全工作计划,并组织实施;2. 每个员工都有责任发现安全隐患并及时上报;3. 安全隐患必须及时整改,确保生产过程的安全;4. 安全事故发生后,应及时组织应急处理,并进行事故调查和处理。
第八条压铸车间的安全设施和防护措施:1. 确保设备符合安全标准,定期进行维护保养;2. 设置安全警示标识,明确危险区域和禁止行动;3. 配备个人防护用品,保护员工的人身安全。
第九条压铸车间的应急预案:1. 压铸车间应建立健全的应急预案;2. 定期组织应急演练,提高员工的应急处理能力;3. 建立应急联络机制,及时通报和处理突发事件。
第三章压铸车间质量管理第十条压铸车间的质量管理应遵循以下原则:1. 确保每个环节都符合质量标准,保证产品的合格率;2. 加强员工对质量的意识培养,提高员工的质量意识和责任感;3. 建立完善的质量管理体系,确保质量的持续改进。
第十一条压铸车间的质量控制:1. 对原材料进行严格的检验和评估,确保原材料的质量稳定;2. 控制加工过程中的工艺参数,确保产品的一致性和稳定性;3. 对产品进行全检,保证产品的质量符合要求。
压铸车间生产管理制度范本
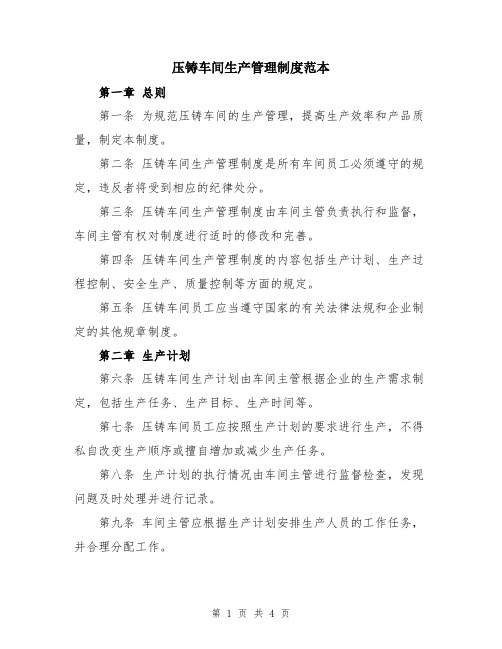
压铸车间生产管理制度范本第一章总则第一条为规范压铸车间的生产管理,提高生产效率和产品质量,制定本制度。
第二条压铸车间生产管理制度是所有车间员工必须遵守的规定,违反者将受到相应的纪律处分。
第三条压铸车间生产管理制度由车间主管负责执行和监督,车间主管有权对制度进行适时的修改和完善。
第四条压铸车间生产管理制度的内容包括生产计划、生产过程控制、安全生产、质量控制等方面的规定。
第五条压铸车间员工应当遵守国家的有关法律法规和企业制定的其他规章制度。
第二章生产计划第六条压铸车间生产计划由车间主管根据企业的生产需求制定,包括生产任务、生产目标、生产时间等。
第七条压铸车间员工应按照生产计划的要求进行生产,不得私自改变生产顺序或擅自增加或减少生产任务。
第八条生产计划的执行情况由车间主管进行监督检查,发现问题及时处理并进行记录。
第九条车间主管应根据生产计划安排生产人员的工作任务,并合理分配工作。
第十条压铸车间员工在生产任务完成后,应记录每一道工序的工作时间,为生产效率分析提供数据支持。
第三章生产过程控制第十一条压铸车间员工应按照工艺流程进行生产,不得随意改变工艺参数或试验新工艺。
第十二条压铸车间员工应对机器设备进行日常巡检,如发现异常应及时上报并停机维修。
第十三条压铸车间员工应合理使用工具和材料,杜绝浪费行为,保证生产的高效率和低成本。
第十四条压铸车间员工应使用防护设施,保障工作安全,严禁违章操作和不当使用机械设备。
第十五条压铸车间员工应按照操作要求进行上岗培训,并且定期进行岗位练习,以提高工作技能。
第四章安全生产第十六条压铸车间员工应严格遵守安全操作规程,不得存在酗酒、吸烟和违反安全规定的行为。
第十七条压铸车间员工应注意危险源,及时清理工作区域,保持工作环境整洁。
第十八条压铸车间员工应经常参加安全生产培训,提高安全意识和应急处理能力。
第十九条压铸车间员工应遵守用电规定,合理使用电源设备,并定期检查电器设备的安全运行情况。
铸造生产过程的质量控制

铸造生产过程的质量控制铸造生产过程的质量控制1. 原材料的质量控制铸造过程中使用的原材料主要包括金属合金和砂型材料。
为了保证产品的质量,必须对原材料进行质量控制。
具体控制措施包括:选择高质量的原材料供应商,并建立稳定的供应链。
对原材料进行严格的检验和筛选,确保其符合产品的要求。
对原材料进行化学成分分析和物理性能测试,以确保其质量符合标准。
2. 模具制造过程的质量控制模具是铸造过程中的重要工具,其质量直接影响到产品的精度和表面质量。
为了保证模具的质量,必须对模具制造过程进行质量控制。
具体控制措施包括:制定模具制造工艺和工作指导书,确保每个环节都符合标准要求。
对模具材料进行质量检查和测试,以确保其质量达到要求。
对模具零部件进行尺寸检验和装配检验,确保模具的准确性和稳定性。
3. 铸造工艺参数的质量控制铸造工艺参数是影响产品质量的重要因素,必须进行严格的质量控制。
具体控制措施包括:确定合理的铸造温度和压力,以确保产品的致密性和机械性能。
控制铸造过程中的冷却速率和凝固时间,以确保产品的表面质量和内部组织结构。
对铸造过程中的熔炼和浇注过程进行监控和调整,以确保产品的成分和收缩率符合要求。
4. 产品质量的检验和测试铸造产品的质量必须进行全面的检验和测试,以确保其质量达到要求。
具体控制措施包括:对产品外观进行目测和尺寸测量,以检查产品的表面质量和尺寸精度。
对产品进行物理性能测试,包括硬度、拉伸强度等指标。
对产品进行化学成分分析,以确保其成分符合标准要求。
对产品进行无损检测,如X射线检测、超声波检测等,以检查产品的内部质量。
5. 不良品的处理和纠正措施在质量控制过程中,可能会出现一些不合格的产品或过程。
为了保证产品质量,必须及时进行处理和纠正措施。
具体控制措施包括:对不良品进行分类和评估,确定其影响范围和原因。
采取相应的纠正措施,如返工、修复、补救等。
对纠正措施进行跟踪和评估,以确保问题得到彻底解决。
以上就是铸造生产过程中常用的质量控制方法和措施。
压铸质量控制与检验标准

1.压铸生产的质量控制1.压铸生产的质量控制1.1环境铸造生产中涉及的主要工作场地、空间和厂房凡影响铸件质量的主要因素均属环境控制范围。
不同工艺方法或不同铸件材料之间凡不能交叉生产的工作场地应分开或隔离。
如压力铸造和熔模铸造、砂型铸造、有色金属和黑色金属、铝合金和镁合金、真空和非真空熔化浇铸之间的工作场地等。
铸造厂房和工作场地的温度,一般不低于10℃。
新设计的铸造厂房应符合TJ16的TJ36规定。
工作间或厂房内的光照度应不低于75LX。
工作间或厂房内的噪声应符合GBJ87规定.熔化和浇铸场地,地面不允许有积水。
厂房应保持良好的通风,有污染的操作区,应按有关规定进行处理。
压铸生产中释放的有害物质见表9—1其有害物质的毒理特性及极聚允许浓度见表9—2。
1.2设备、仪表和工装铸造过程中直接影响铸件质量的主要设备、仪表和工装应进行质量控制。
应控设备、仪表和工装的目录由技术部门会同使用部门提出,并规定检定项目和周期.其使用、维护、保养和管理的质量控制,工厂应规定通用量具、衡器具的使用管理控制,工厂应有计量管理规范。
设备、仪表和工装应有检定合格证,合格证应注明检定日期、有效期和责任者。
不合格者应停用或作待修等标记.生产现场不准使用未经检定合格或超过检定有效周期的器具、设备、仪表和工装。
精密、关键和贵重的仪表、设备和模具,应建立使用登记和履历本。
铸造机械设备每年应进行一次技术指标检查,技术指标应不低于工艺要求。
熔炼浇注设备每年应进行一次技术指标检查,如设备的熔化功率和熔化速度。
铸造用加热炉的类别应符合有关标准规定。
铸件热处理加热炉,按铸件材料相应的热处理技术标准规定控制。
用于重要的测温与控温的仪表最好配有温度显示自动记录装置。
安全自动报警装置。
复验报告应存档备查,材料发往生产车间时,应附有质量证明及复验报告。
使用单位对主要材应分类存放,妥善保管,防止混批混料、锈蚀和污染。
浇冒口和废铸件等回炉料应及时处理,分类存放,放置标志,严防混料。
压铸车间管理制度
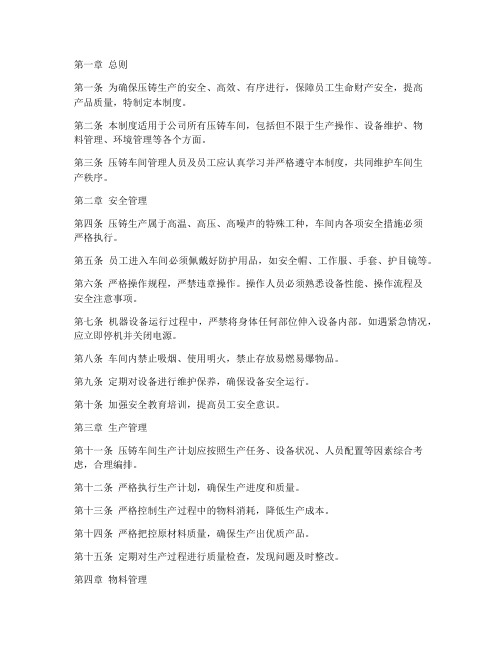
第一章总则第一条为确保压铸生产的安全、高效、有序进行,保障员工生命财产安全,提高产品质量,特制定本制度。
第二条本制度适用于公司所有压铸车间,包括但不限于生产操作、设备维护、物料管理、环境管理等各个方面。
第三条压铸车间管理人员及员工应认真学习并严格遵守本制度,共同维护车间生产秩序。
第二章安全管理第四条压铸生产属于高温、高压、高噪声的特殊工种,车间内各项安全措施必须严格执行。
第五条员工进入车间必须佩戴好防护用品,如安全帽、工作服、手套、护目镜等。
第六条严格操作规程,严禁违章操作。
操作人员必须熟悉设备性能、操作流程及安全注意事项。
第七条机器设备运行过程中,严禁将身体任何部位伸入设备内部。
如遇紧急情况,应立即停机并关闭电源。
第八条车间内禁止吸烟、使用明火,禁止存放易燃易爆物品。
第九条定期对设备进行维护保养,确保设备安全运行。
第十条加强安全教育培训,提高员工安全意识。
第三章生产管理第十一条压铸车间生产计划应按照生产任务、设备状况、人员配置等因素综合考虑,合理编排。
第十二条严格执行生产计划,确保生产进度和质量。
第十三条严格控制生产过程中的物料消耗,降低生产成本。
第十四条严格把控原材料质量,确保生产出优质产品。
第十五条定期对生产过程进行质量检查,发现问题及时整改。
第四章物料管理第十六条压铸车间物料实行分类存放,明确标识,便于管理。
第十七条物料出入库应严格按照规定程序办理,做好登记记录。
第十八条严禁将不合格物料投入使用,确保生产产品质量。
第五章环境管理第十九条车间内保持整洁,定期进行卫生打扫。
第二十条加强噪音、粉尘等污染治理,确保车间环境达标。
第二十一条加强设备冷却系统管理,确保设备正常运行。
第六章奖惩制度第二十二条对严格遵守本制度、表现突出的员工给予奖励。
第二十三条对违反本制度、造成不良后果的员工给予处罚。
第七章附则第二十四条本制度由公司行政部门负责解释。
第二十五条本制度自发布之日起实施。
本制度旨在规范压铸车间生产管理,提高生产效率,保障员工权益,促进公司持续健康发展。
压铸车间的管理制度

压铸车间的管理制度一、安全管理1. 压铸车间的生产设备必须符合国家安全标准,并定期检测和维护。
2. 操作人员必须经过专业的培训和考核,并持有效证书方可上岗。
3. 工作场所必须保持清洁整齐,避免堆放杂物和易燃物品。
4. 在操作和维护设备时,必须佩戴防护用品,包括安全帽、防护眼镜和耳塞等。
5. 严禁未经许可擅自改装设备,一旦发现将追究责任并立即停工。
二、质量管理1. 压铸车间必须制定质量管理手册,并按照手册的规定执行。
2. 生产过程中必须进行工序检验和成品检验,确保产品达到质量要求。
3. 检验结果必须及时记录和报告,并采取相应的纠正措施。
4. 定期进行内部质量审核,对发现的问题进行整改和改进。
5. 严禁将不合格产品流入市场,一经发现将追究责任。
三、生产计划管理1. 压铸车间必须制定详细的生产计划,包括生产任务、生产周期和产量等。
2. 生产计划必须与销售部门的需求进行协调,确保及时完成订单。
3. 生产计划必须合理安排设备和人力资源的利用,最大程度提高生产效率。
4. 生产计划必须及时调整,以应对市场需求的变化和生产异常情况。
四、物料管理1. 压铸车间必须建立完善的物料管理制度,包括采购、入库和出库等环节。
2. 采购物料必须与供应商签订合同,并对物料进行严格的验收和检验。
3. 入库物料必须按照规定的存放位置进行分类和标识,并定期进行盘点和清点。
4. 出库物料必须按照生产计划的要求进行发放,并及时更新库存记录。
5. 物料损耗必须严格控制,以降低生产成本和提高产品质量。
五、人力资源管理1. 压铸车间必须建立健全的人力资源管理制度,包括招聘、培训和考核等。
2. 招聘人员必须进行严格的面试和背景调查,确保人员质量和岗位匹配。
3. 新员工必须进行入职培训,并签订员工手册,明确岗位责任和规范行为。
4. 员工的工作表现必须进行定期评估和绩效考核,并进行奖惩措施。
5. 压铸车间必须建立员工激励机制,包括薪酬福利和职业发展等方面的激励措施。
压铸车间生产管理制度(5篇)
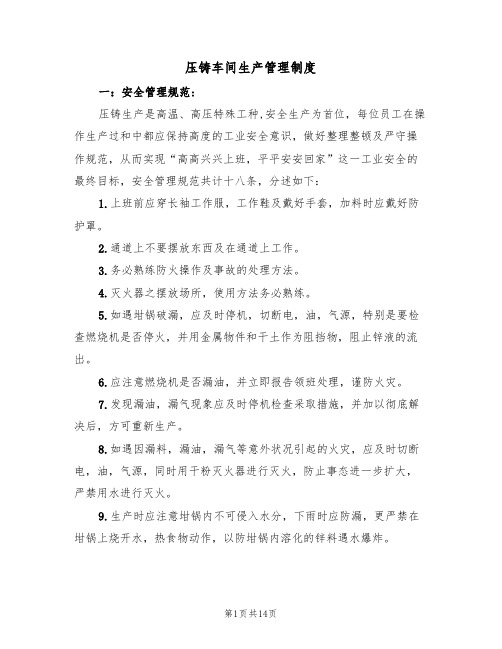
压铸车间生产管理制度一:安全管理规范:压铸生产是高温、高压特殊工种,安全生产为首位,每位员工在操作生产过和中都应保持高度的工业安全意识,做好整理整顿及严守操作规范,从而实现“高高兴兴上班,平平安安回家”这一工业安全的最终目标,安全管理规范共计十八条,分述如下:1.上班前应穿长袖工作服,工作鞋及戴好手套,加料时应戴好防护罩。
2.通道上不要摆放东西及在通道上工作。
3.务必熟练防火操作及事故的处理方法。
4.灭火器之摆放场所,使用方法务必熟练。
5.如遇坩锅破漏,应及时停机,切断电,油,气源,特别是要检查燃烧机是否停火,并用金属物件和干土作为阻挡物,阻止锌液的流出。
6.应注意燃烧机是否漏油,并立即报告领班处理,谨防火灾。
7.发现漏油,漏气现象应及时停机检查采取措施,并加以彻底解决后,方可重新生产。
8.如遇因漏料,漏油,漏气等意外状况引起的火灾,应及时切断电,油,气源,同时用干粉灭火器进行灭火,防止事态进一步扩大,严禁用水进行灭火。
9.生产时应注意坩锅内不可侵入水分,下雨时应防漏,更严禁在坩锅上烧开水,热食物动作,以防坩锅内溶化的锌料遇水爆炸。
10.料头锌锭应确保在干燥状态下投入使用,未经许可不可带有油分,水分的料头料屑倒入坩锅。
11.从坩锅中打捞出来的锌渣等,必须放于干燥的铸铁槽中,不得置于地板上,避免爆炸危险。
12.如因电气系统故障应关掉总开关后提出报告,不得私自拆卸。
13.每套压铸机中间应使用挡屏,以防溅料伤人。
14.走过压铸机旁应注意溅料危险。
15.操作人员,加料人员,应分清工作,加料作业时应进行招呼互相配合,同时劝阻非生产人员进入不安全区域。
16.换模具应两人配合,吊换模具时应仔细确认安全后方可搬迁吊装,谨慎作业,锁模时应用____个以上螺丝,并注意检查锁模螺丝的螺纹是否完好,严禁模具撞击或伤人。
17.整理整顿模具应停机后方可进行。
18.工具,配件使用后应放置于工具箱内,以防随意放置伤人,更严禁置放于机台内。
压铸车间生产管理制度范本

压铸车间生产管理制度范本第一章总则一、为了规范压铸车间的生产管理,提高生产效率,确保产品质量,保障员工安全,制定本制度。
二、本制度适用于压铸车间的生产管理活动。
三、所有压铸车间的员工都应严格按照本制度的要求执行。
四、压铸车间主管有责任监督员工执行本制度,并及时对其进行指导和培训。
第二章生产计划管理一、车间主管负责组织编制月度生产计划,并按照计划进行调整。
二、生产计划应考虑每台设备的生产能力、人员的实际工作效率、原材料的供应情况等因素。
三、生产计划应提前确定,确保生产线的连续运转。
第三章生产过程管理一、生产前准备工作:1.设备的检查与保养:每天生产前,设备操作人员应对设备进行检查与保养,确保设备正常运转。
2.原材料准备:生产前,原材料管理人员应根据生产计划,保证原材料的及时供应,并确保原材料的质量。
二、生产操作规范:1.设备操作人员应按照操作规程进行操作,严禁违规操作。
2.生产过程中,设备操作人员应定期检查设备的运行状态,发现问题及时报告。
三、生产记录的填写与保管:1.设备操作人员应按照规定填写生产记录,并保留至少半年。
2.生产记录应包括生产日期、生产数量、设备运行状态等信息。
第四章产品质量管理一、质检员应按照质量控制方案中的要求进行抽样检测,并对检测结果进行记录。
二、质检员应对不合格品进行分类,及时通知生产部门进行调查处理。
三、生产部门应对不合格品进行追溯分析,找出原因,并以此为依据改进生产工艺。
四、质管部门应组织对产品的抽样检测和深入检查,确保产品质量符合要求。
第五章安全生产管理一、所有员工应定期参加岗位安全培训,掌握安全操作规程。
二、车间主管应对现场进行安全巡检,及时发现并整改安全隐患。
三、设备操作人员应穿戴防护用品,严禁违规操作,确保自身安全。
四、车间主管应制定应急预案,并进行员工培训,提高应急处理能力。
第六章绩效考核与激励机制一、车间主管应根据生产计划完成情况、产品质量、成本控制等指标对员工进行绩效考核。
铸造生产过程的质量控制范文精简处理

铸造生产过程的质量控制铸造生产过程的质量控制引言铸造生产过程概述铸造是通过将熔融金属或合金注入预先制作好的模具中,然后进行冷却凝固得到所需形状的工艺。
铸造生产过程主要包括模具制作、熔炼与浇注、冷却凝固和后处理等环节。
质量控制措施铸造生产过程中的质量控制可以分为以下几个方面:1. 模具制作的质量控制模具的准确度要求高,尺寸精确、表面光滑,以保证最终产品的尺寸精度和表面质量。
模具的材料选择和加工工艺要合理,以保证模具的耐磨性和寿命。
2. 熔炼与浇注的质量控制熔炼时要严格控制熔炼温度和熔炼时间,保证金属或合金的成分均匀,不产生气体和夹杂物。
浇注时要控制浇注温度和速度,避免产生气孔、夹渣和缩松等缺陷。
3. 冷却凝固的质量控制控制冷却速度和冷却方式,以避免产生组织缺陷,如晶粒过大、晶界不清晰等。
控制凝固过程中的温度变化,以避免产生应力和变形。
4. 后处理的质量控制清理杂质和缺陷,如夹渣、气孔等。
进行热处理、表面处理或机械加工,以改善产品的性能和表面质量。
质量控制方法为了有效控制铸造生产过程中的质量,可以采取以下几种方法:1. 设计质量控制在产品设计阶段,就应考虑产品的铸造性,合理设计产品的几何形状和壁厚,减少可能出现的缺陷和变形。
2. 工艺参数控制对每个工艺环节中的关键参数进行严格控制,如熔炼温度、浇注温度和速度等。
在铸造过程中,通过实时监测温度、压力和流速等参数,进行及时调整和控制。
3. 检测和检验使用各种检测设备和仪器,如X射线探伤仪、超声波检测仪等,对产品进行无损检测,以发现和排除可能存在的缺陷。
进行物理和化学性能的检验,如拉伸试验、硬度测试和成分分析等。
4. 信息化管理建立完善的质量管理体系,进行全过程的质量记录和数据分析,发现问题并采取措施进行改进。
运用信息化技术,实现数据的实时监控和追溯,提高生产过程的透明度和可控性。
结论铸造生产过程的质量控制是确保最终产品质量的重要环节。
通过合理的质量控制措施和方法,可以有效避免铸造过程中可能出现的缺陷和变形,提高产品的质量和性能。
压铸厂车间品质管理制度

一、总则为了加强压铸厂车间的品质管理,确保产品质量,提高企业竞争力,特制定本制度。
本制度适用于压铸厂车间所有员工及相关部门。
二、品质管理目标1. 提高产品一次合格率,降低不良品率;2. 确保产品符合国家相关标准和客户要求;3. 优化生产流程,提高生产效率;4. 培养员工品质意识,提升整体素质。
三、品质管理体系1. 质量管理体系:建立健全质量管理体系,包括质量策划、质量控制、质量保证和质量改进等方面。
2. 品质管理组织:成立品质管理小组,负责组织实施本制度,协调各部门工作。
3. 品质管理职责:(1)品质管理小组:① 负责制定、修订和完善本制度;② 组织开展品质培训,提高员工品质意识;③ 监督检查各部门执行本制度情况;④ 分析品质问题,提出改进措施;⑤ 定期向上级汇报品质管理情况。
(2)生产部门:① 负责按照工艺要求组织生产;② 加强过程控制,确保产品质量;③ 及时反馈品质问题,配合品质管理小组进行分析和改进;④ 组织员工参加品质培训。
(3)技术部门:① 负责制定生产工艺,优化生产流程;② 提供技术支持,协助解决生产过程中的品质问题;③ 参与品质管理小组,共同分析品质问题,提出改进措施。
四、品质管理措施1. 原材料管理:(1)严格按照采购要求采购原材料,确保原材料质量;(2)对进厂原材料进行检验,不合格原材料不得投入使用;(3)对原材料进行标识、分类存放,防止混淆。
2. 生产过程管理:(1)严格按照生产工艺进行生产,确保生产过程稳定;(2)加强过程控制,及时发现和纠正生产过程中的问题;(3)对关键工序进行重点监控,确保产品质量;(4)对生产设备进行定期维护保养,确保设备正常运行。
3. 产品检验:(1)严格执行产品检验标准,确保产品符合质量要求;(2)对检验过程中发现的不良品进行隔离,防止混入合格品;(3)对检验数据进行统计分析,为品质改进提供依据。
4. 质量改进:(1)对品质问题进行分析,找出原因,制定改进措施;(2)对改进措施进行跟踪验证,确保措施有效;(3)对改进成果进行总结,形成标准化文件,指导生产。
- 1、下载文档前请自行甄别文档内容的完整性,平台不提供额外的编辑、内容补充、找答案等附加服务。
- 2、"仅部分预览"的文档,不可在线预览部分如存在完整性等问题,可反馈申请退款(可完整预览的文档不适用该条件!)。
- 3、如文档侵犯您的权益,请联系客服反馈,我们会尽快为您处理(人工客服工作时间:9:00-18:30)。
压铸车间生产过程质量控制办法工序名称:熔化→装模→模具调试→压铸→脱模一、熔铝合金(作业人员:熔化工)1、熔炉的温度要控制在630℃-680℃。
2、观察熔化后的铝液,适于生产的铝液呈亮白色,如果铝液显红色,说明炉温过高,如铝液呈冰淇淋状则说明温度过低.3、严禁熔铝过程中,混入杂质,禁止操作人员私自将不合格品投入熔炉回炼,如有产品需回炉重炼,必须经过组长检验确认,方可投入回炼.4、保持铝液液面平稳,无浮渣和气泡冒出,在舀取铝液进行压铸时,必须将铝液表面的氧化层及杂质刮去。
5、生产过程中,每一班次必须在熔炉中加注两次粉状精炼剂及去渣剂,平均每4小时加注一次,整个加注过程,必须在组长的指导下进行,作业完成后,须把精炼产生的杂质清理干净后方能进行铸件生产。
6、生产过程中,每一班次必须至少两次清理炉底铝渣,至少平均每4小时清理一次。
7、所有接触铝液的工具,必先烘干,要保持绝对的干燥与干净,不能附带杂质进入铝液。
8、在熔铝过程中,如发现铝锭或回炉料中杂质过多,应立既停止将同类铝锭或回炉料再投入熔炉中,并及时向班长及车间主任进行汇报。
二、装模(作业人员:操作工、维修工、班组长)1、首先要确定模具型号的准确性,确保模具的完好性。
2、装配模具时要在操作工,维修工及组长的共同协助下完成。
3、模具装配时,要保证各坚固件的牢固性,确保模具在生产过程中的安全。
三、模具调试(作业人员:操作工、维修工、带班长)(重点工序)1、模具装配完成,可进行试机(点动),自动低压空运转一周次,以确保所装配模具之灵活性。
1检查螺丝是否有松动。
2检查设备是否有漏油或其它异常情况。
3检查压铸机和模具的活动部位是否回加注润滑油工序名称:熔铝→装模→模具调试→压铸→脱模2、模具的温度(模具预热)1)模具表面温度升温至180℃-220℃。
2)检查冷却水运行是否正常。
3、试压铸1)班组长设定压铸参数。
2)检查所要浇铸的铝液是否适用。
3)压铸时观察设备及模具运转是否正常。
4)检查脱模剂喷雾压力及水量是否正常。
5)检查所压铸之产品尺寸,外观是否符合图纸及检验卡片之要求,有无产品缺陷。
6)试压铸产品必须在50件以上(必须打低速压射20模后,再开高速压射试压)。
7)最终确认合格的压铸件,可作为首检品予以保留,并填写《首件检验单》。
四、压铸(作业人员:操作工)1、压铸产品经确认合格后,应确定所设定的参数,操作工不得擅自改变所设定的参数。
2、生产过程中如发现设备异响等不正常现象或铸件滞留在模具中,应立即停机并通知维修人员,严禁操作工私自维修。
3、生产过程中,操作工要确保模具的可靠性。
1 由于分型面不平整或磨损多,锁模力不够,导致铸件飞边多。
2由于冲头磨损导致射料位置铝液飞溅。
3 由于误操作导致模腔、滑块等损坏。
4 由于长期使用模具,促使模具材料疲劳,产生崩损,影响产品质量。
4 生产过程中,操作工要做到产品自检,规定每压铸成型20件产品,即对产品进行一次自检,如发现产品异常,应立即停止生产,查找原因。
1 由于模具温度过低,铝液温度低或铝液充填速度过慢,导致铸件出现冷隔。
2 由于保压时间不够,铸件拔模斜度过小,导致铸件裂纹甚至拉裂。
3 由于铝液材质有偏差,模腔表面粗糙,脱模剂量不足或失效,导致铸件粘模。
5 在生产过程中,如发现模具有轻微崩缺的,而铸件只需要进行外观修理,不影响性能的,需及时向班组长及车间主任进行报告,处理方法如下:1)根据实际情况,可以不终止生产,但铸件产品必须全部进行维修处理,在该批产品压铸完成后,必须对模具进行维修,该情况适用于批量不大的产品。
2)立即停止生产,拆卸有问题的模具进行维修,在维修后及试压铸确认其完好性后,方可继续投入生产。
五、脱模(作业人员:操作工)1、在生产过程中进行压铸前,必须向模具喷洒脱模剂。
2、检查脱模剂喷射气压是否适于压铸生产。
3、检查脱模剂流量是否适合生产4、检查脱模剂是否失效。
5、如出现上述问题,应立即通知班组长及车间主任,及时对喷射气压、流量和脱模剂配比进行调整,适用于生产为止。
工序名称:带班长检验(作业人员:带班长)一、模具的确认与装配1、带班长必须确认所要使用装配的模具型号的符合性,其产品型号要有生产单一致。
2、带班长必须确认模具的完好性,避免崩缺及损伤的模具装机生产。
3、对于已装配好的模具,要检查其紧固性,要加注润滑油,保证模具运转的灵活性。
4、必须要确认模具试压铸品的符合性。
二、产品首检1、带班长必须确认所生产的首件压铸件是否符合图纸要求。
2、带班长在进行产品首检时,一定要确认压铸件尺寸外观等条件是否满足图纸及检验卡片之要求。
3、带班长在进行产品首检时,一定要确认压铸设备及模具运行的良好性。
三、巡检1、带班长每小时至少对每台机正在运行的设备进行一次巡检,以纠正操作工的不良操作。
2、对每一部机台进行巡检,对其正在生产的产品进行抽检,以确认产品即时的符合性。
3、带班长应及时处理所发生的生产异常情况,重大质量问题应及时向车间主管汇报。
四、其他1、带班长在每次交接班时,应核实交接班程序,并记录。
2、带班长需填写工作日记,记录当班的质量问题及生产情况,并对下一班进行工作提示。
工序名称:全检(作业人员:全检员)一、产品的全检1、全检员对所压铸的产品实施全检。
2、主要检测产品的外观、缺损等项目。
3、在全检过程中,如发现产品存在有许多的质量问题,应及时将情况向压铸带班长及品质主管反映。
4、全检员要对所检产品存在的质量问题,进行分类记录。
二、产品的分选1、全检员要对所全检的产品进行分选,坚决从中剔除不合格品。
2、全检过程中所剔除的不合格品,在按不同的质量问题进行分类,隔离及标识。
3、不同种类、不同型号的产品,一定区别摆放,防止不同产品互混。
三、产品的标识1、已全检的产品一定要进行标识,不同种类,不同型号的产品一定要进行区分。
2、产品的标识中,一定要注明产品的型号、种类、数量、压铸机的台号、操作人员的姓名、全检员的姓名。
3、不合格品一定要标识并隔离,防止已选出的不合格品再次混入合格品中。
工序名称:抽检(作业人员:巡检员)一、产品的首检1、巡检员必须参与首件产品的首检工作并记录。
2、巡检员必须确认首检产品完全符合《压铸工艺卡》或《检验指导书》要求,方可继续生。
3、对于首检不合格的产品,巡检员有责任要求操作工及带班长对设备及模具进行调整或维修,直至生产出合格品为止。
二、产品的巡检1、巡检员每2小时至少对每台机正在生产的产品进行一次巡检,以确认正在生产的产品是否符合《压铸工艺卡》或《检验指导书》要求并记录。
2、巡检员每小时对全检员正在全检分选的产品进行一次巡检,以确认正在全检的产品是否符合《外观检验指导书》要求。
3、在巡检过程中,所发现的不合格品,应立即标识隔离,巡检员有责任督促操作工、带班长对此加以纠正。
4、在巡检过程中,如发现重大质量问题,或发现严重隐患,应立即向车间主管和品质部门进行汇报,以便于进行及时处理。
5、在巡检过程中,如因设备、模具等问题,而造成的可修补的轻微质量问题,巡检员应及时通报车间主管与品质主管。
此类情况,如在事后可以通过修补可以解决的,可继续生产。
批量生产完成后,应通知相关人员及时对设备和模具进行维修。
三、产品的终检(入成品库前的抽检)1、巡检员对入成品库前的产品,进行最后的抽检。
2、产品性能尺寸、外观的检验按《出厂检验指导书》来进行。
3、对于不合格的批量产品,可根据实际情况作报废、返修、分选等处理。
四、其他1、负责压铸模具的检测、验收及检测记录的填写,并及时上报相关《质量日报表》。
2、负责车间的工序控制,负责产品的首检、巡检及入库检验,并填写相关的检验记录。
3、负责产品的终检入库(出厂)检验,不合格产品不得入库(出厂)。
4、监督检查全检员的工作,协助处理车间的质量问题。
5、负责保管车间的质量检验记录,协助车间处理客户退货。
6、协助车间提出产品质量改进方案,提高制成工艺水平。
工序名称:过程控制中应注意的其他问题一、重点工序应进行重点控制:二、对于因抽芯长而易引发产品变形的压铸件,操作工、带班长及巡检员应加强其检查力度,并列为重点,以确保合格产品流入下工序。
三、工序完成的半成品,在全检时不能堆放过高。
外形相似的不同规格的产品,不同产品之间需要进行有效的产品定置标识,防止不同产品之间因距离过近,在搬运、挪动、生产过程中出现重大混淆现象。
四、不合格品的控制1、在生产过程中,如发现所压铸产品不合格或模具损坏,发现者应立即上报。
带班长、巡检员或车间主管组织对不合格品进行标识并隔离,并将不合格品放置在指定区域内。
2、在检测环节中,出现的不合格品如可通过技术处理解决相关质量问题的,全检员及巡检员可要求生产现场做出技术处理,经过处理的产品必须经过重检。
3、发现的不合格品,由车间巡检员填写《质量报告单》,并上报品质主管。
由品质主管召集车间相关人员对不合格品进行分析,并做出书面的处理决定。
五、巡检员可一周或一个月对车间生产的质量状况进行一次总结,内容涉及产品质量、客户退货、客户质量投诉等内容,并上报品质主管,由品质主管做出最终的质量月报。
工序名称:原材料的化验、试验、批号管理及压铸件的时效性处理一、原材料(铝锭)的化验及试压铸1、所有进货的铝锭必须要经过理、化室的化验,只有化验合格的铝锭方可进入压铸车间进行试压铸。
2、新到的未经过化验的铝锭可先行入仓暂时存放,仓管员应将该批新入仓的铝锭与现正在使用的铝锭严格区分开来,并对该批新入仓暂时存放的铝锭进行标识,同一批不同堆数的铝锭进行相同的标识。
3、新入仓暂时存放的铝锭,未经许可不准发予生产车间使用。
该批铝锭的标识中。
应有明确的材料合金的代号、数量、进货日期及铝锭的受检状态(未经化验与试压铸的新入仓的铝锭必须悬挂待检标志)。
4、经过化验合格的铝锭,必须在压铸车间进行试压铸,试压铸产品不能低于小件不低于2000件,大件不低于800件,试压铸产品必须经过车间主任及质量管理科质检员的检验,且必须要经过时效处理后的检验,如裂纹、开裂、变形等方面的检验。
5、经过化验、试压铸及时效处理检验均合格的铝锭,质量管理科质检员填写《铝锭检验报告》方可确认为合格原材料。
质量管理科根据上述检测报告,在《入仓单》上签名确认,并注明该批铝锭已经过上述两项检验,此时材料方可正式入仓,仓管员正式悬挂已检标志,表明该材料可正式投入生产。
6、通过检验的铝锭,仓管员为其编制材料批号:列:ADC12——100831时间号:材料通过检验的时间,即2010年8月31日。
材料合金代号:工序名称:原材料的化验、试验、批号管理及压铸件的时效处理二、压铸件的时效性处理1、所有压铸件必须要经过时效性处理,以消除产品的压铸应力。
2、压铸车间所生产的压铸件,在经过全检后,必须要经过15-20天的堆放,以消除产品的压铸应力,在经过时效性处理的压铸件方可流入下工加工。