关于前处理药剂槽液控制和清理周期的说明
前处理液槽管理规范讲解
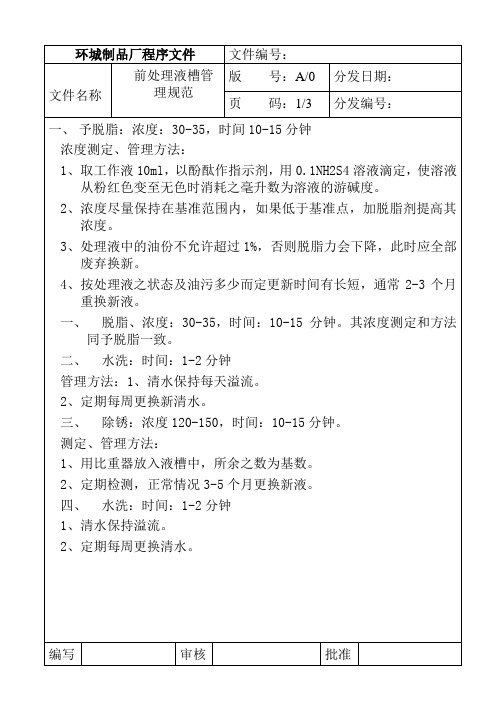
8、作业结束,清理现场工具和物品保持作业场所整洁干净。
编写:
审核:
批准:
环城制品厂程序文件
文件编号:
文件名称
前处理作业要求及岗位职责
版号:A/0
分发日期:
页码:1/1
分发编号:
1、按照上司生产指令,开始生产准备工作。抽查来料数目及质量。
2、除锈除油的工件摆放时,工件之间留有间隙。同时保持轻微倾斜,
3、促进剂、将工作液装满发酵管内,再以指示剂(粉状)氨基磺酸2-5g添加摇动成气体,视其产生之气体量为基准值。
4、日常维持方法:
A、日常维持方法:
B、促进剂除生产性消耗剂,在液槽中有自耗特性。正常每天上班前由技术员检测、添加。
编写:
审核:
批准:
环城制品厂程序文件
文件编号:
文件名称
前处理液槽管理规范
版号:A/0
编写:
审核:
批准:
环城制品厂程序文件
文件编号:
文件名称
电动打磨工作业要求及岗位职责
版号:A/0
分发日期:
页码:1/1
分发编号:
1、根据生产安排,抽查待磨工件腻子的干燥程度及待喷表面未刮油灰
的缺陷。
2、针对工件刮油灰的厚薄,选择与之相适应的砂纸号数,合理使用砂
低。
3、作业过程中,所有工件应轻放,应避免乱扔、乱丢、导致相互磕碰,
引起刮伤,划痕的野蛮作业方法。
4、打磨至刮油灰边缘处形成毛絮状为适宜。
5、工件槽孔位及边缘处不允许有油灰渣应清除干净。
6、每批作业结束,记录完成工件数目,并作标识。
7、作业结束,下班前,清洁作业现场保持整齐干净。关闭电、气源。
编写:
前处理药品使用说明书
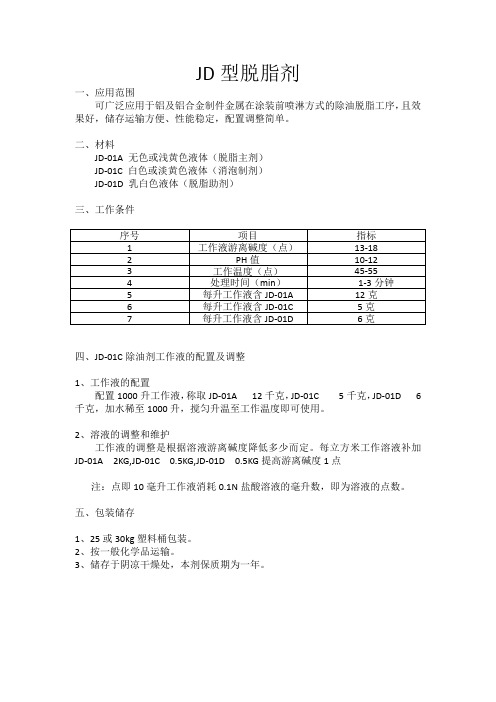
JD型脱脂剂一、应用范围可广泛应用于铝及铝合金制件金属在涂装前喷淋方式的除油脱脂工序,且效果好,储存运输方便、性能稳定,配置调整简单。
二、材料JD-01A 无色或浅黄色液体(脱脂主剂)JD-01C 白色或淡黄色液体(消泡制剂)JD-01D 乳白色液体(脱脂助剂)三、工作条件四、JD-01C除油剂工作液的配置及调整1、工作液的配置配置1000升工作液,称取JD-01A 12千克,JD-01C 5千克,JD-01D 6千克,加水稀至1000升,搅匀升温至工作温度即可使用。
2、溶液的调整和维护工作液的调整是根据溶液游离碱度降低多少而定。
每立方米工作溶液补加JD-01A 2KG,JD-01C 0.5KG,JD-01D 0.5KG提高游离碱度1点注:点即10毫升工作液消耗0.1N盐酸溶液的毫升数,即为溶液的点数。
五、包装储存1、25或30kg塑料桶包装。
2、按一般化学品运输。
3、储存于阴凉干燥处,本剂保质期为一年。
JD-02B型铝件出光剂一、产品简介JD-02B型铝件出光剂是一种由多种表面活性剂复配而成的酸性出光剂,它具有极强的去污、分散、乳化、增溶能力。
处理过程中,去污彻底迅速,工件不会存在过腐蚀现象,生产安全可靠。
二、主要特点1、主要由弱酸组成,且加有缓蚀成分,不易产生过腐蚀。
2、有助于铝件涂装,提高涂膜附着力。
3、用量少,速度快,效果好。
三、适用范围适用于各种铝、镁合金件的浸渍,喷淋去污和出光。
五、配置和调整1、配置工作液时,按每吨加JD-02B型铝件出光剂50-70kg计算,缓慢加入后搅拌摇匀。
2、工作液使用一段时间后,其去污和出光能力会下降,应及时添加,每吨工作液提高一个游离点,需添加JD-02B铝件脱脂剂约2升。
如游离点高出控制范围,表面反应速度会加快,工作一段时间后,待指标降至控制范围内,即可恢复正常。
3、当溶液中油污过多时,溶液的去无效果会下降,应考虑清除表面油脂或者更换工作液。
4、六、注意事项1、出光后的工件在转入下到工序前,应充分水洗,保持水洗槽的清洁。
前处理投槽操作指导

如果低于 40℃时喷淋,表面活性剂会产生泡沫。
检测方法:
将 10ml 槽液样品放入锥型瓶,加纯水至 50 ml;加入 3-5 滴酚酞指
示剂;使用 0.05 M H2SO4 滴定由红色变成无色,每消耗 1 ml 0.05 M H2SO4
相当于 1.0 游离碱点。
槽液的补充
每消耗 1 游离碱点加入 2 g/L Gardoclean 10037/2,加入 0.5g/L
Gardoclean H7354/1
南京凯密特尔表面技术有限公司
NANJING CHEMETALL SURFACE TECH. CO., LTD.
槽液更换: 2-4 个月(根据生产量及槽液含油量而定) 设备要求
· 配备槽液搅拌泵,使槽液循环达到 2-4 次/小时 · 油水分离装置 · 热水介质热交换装置 · 主脱脂槽→预脱脂槽能溢流 · 推荐采用专用过滤系统,脱脂槽底部有锥面,便于清除脏物。
1.预脱脂阶段:
作用:
脱脂,阶段 1(D1)
成分:
Gardolean 10037/2 +Gardoclean H7354/1
浓度
Gardoclean 10037/2
20g/L
+Gardoclean H7354/1
5g/L
温度:
45-55℃
总碱点:
10-20 点
喷淋压力:
0.1-0.2MPa
处理时间:
0.5min
配制过程(新槽液)
把容器排空,清洗后,加入自来水
加入 Gardoclean 10037/2 加热槽液,,等待温度达到 50℃,然后
打开喷淋
再加入表面活性剂 Gardoclean H7354/1
喷涂前处理药剂、槽液检测操作指引

规范喷涂车间所使用之前处理药剂/槽液检测标准及操作方法,指导相关检测作业。
2. 适用范围
适用于本公司喷涂生产所使用的前处理药剂/槽液检测。
3. 抽样标准
按QSI-077《抽样检验作业指引》进行抽样检验。
4.前处理工艺流程
4.1铁件前处理工艺:除油 清洗 除锈 清洗 表调 清洗 磷化 清洗
4.2非铁件前处理工艺:除油 清洗 出光 清洗 钝化 清洗
6.5、生产过程中,所有的检测指标、原材料的添加都做好原始记录(包括取样时间、日期、指标、添加量、生产产量等);
6.6、“皮膜剂”添加建议采用“勤加少加”的原则,这样可以维持皮膜槽液的总酸度指标在工艺范围内,保持槽液的稳定性。
6.7、车间品管人员应不定时对各槽液进行抽检并记录数据,并结合日常喷涂产品的品质进行判定,发现上述情况要及时反馈并开出《质量异常报告》知会相关单位处理。
先取槽液10ml滴入锥形瓶中;其次滴入3-5滴溴酚蓝,摇均匀呈蓝色;再滴入稀硫酸试剂(0.1NH2SO4)轻摇,直到液体变为黄色时停止,此时滴入的稀硫酸试剂的数值即为总碱值。
5.3.2、游离碱值(FAL)
先取槽液10ml滴入锥形瓶中;其次滴入3-5滴酚酞,加入3-5ml蒸馏水,摇均匀呈粉红色;再滴入稀硫酸试剂(0.1NH2SO4)轻摇,直到液体呈无色透明时停止,此时滴入的稀硫酸试剂的数值即为游离碱值。
7.3、使用检测工具时,需轻拿轻放,尽量减少碰撞、以免损坏,正确使用。
7.4、在检测药剂槽液时,严格遵守检验的方法,不可随意变换。
8.参考文件
《前处理安全操作及药剂检验指引》WI-456
《监控和测量仪器管理程序》QEP-009
9.相关表单
【质量异常报告】FQ002-04保存部门: 品保部保存期限: 6年
前处理安全操作规程
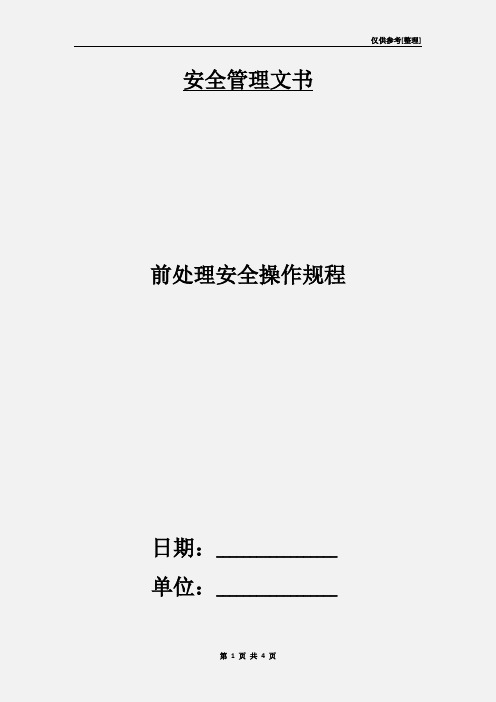
仅供参考[整理] 安全管理文书前处理安全操作规程日期:__________________单位:__________________第1 页共4 页前处理安全操作规程为确保生产安全,吐绝一切安全隐患,稳定产品质量,特对前处理操作者及进入本车间的人员制定以下安全操作规范章程:一、物料存放1.前处理用药液及空桶应置于专用仓库集中存放装并由专人保管员,车间根据生产需要按需领用。
2.物料在装装卸、搬运过程中应小心轻放,防止包装破裂;若桶破裂,破桶溢出药液须用专用桶收集。
操作过程中须做好防护措施,避免药液接触眼睛、皮肤,若身体不慎触药液,立即用清水冲洗,并及时就医。
二、药济添加1.在进行药液添加操作前须做好安全防护措施:穿戴耐酸胶手套,戴安全防护面罩及胶围裙。
2.在添加工作药水时,应每一放、二避的操作进行,保证操作人员的每次生产安全三、加工操作工艺1.操作人员每天上岗前须穿戴好个人防护用品,检查各液槽的水位及液池周边情况,判断是否有泄漏现象,并用PH值试纸检测各槽液酸碱度,确保各项指标合格后方可进行生产操作。
2.合理控制吊机运行情况,吊笼入池、出池过程要慢速、匀速起降,防止工作液飞溅及吊笼碰撞池壁损坏液槽。
3.吊笼升起后在移至下一槽位之前应稍停留2~3分钟后待工件上的药液滴干后方可移于下一槽位。
4.操作作业过程中每隔两小时检测一次工作液的浓度及加工产品第 2 页共 4 页的质量情况,及时添加药液原料。
四、污水(泥)收集处理与回收要点:前处理生产过程中产生的所有液体(包括地板上的积水)、固体污泥沉淀渣一律不允对外排放,对全部污水(泥)进行集中安全处理。
1.清水池溢出污水及地板面收集的污水统一抽至中和池处理并回收利用(见流程图).2.污水处理池及工作液槽中的固体沉淀物收集后临时存放在贮渣池中,至一定数量后交由有资质的回收公司(柳州金太阳工业废物处理有限公司)定点回收处理。
五、安全应急议案1.非前处理车间工作人员尽量不靠近工作液池,任何人不得在池中洗手,洗衣服等做与工作无关的事情,车间人员有向不知者作提醒的义务。
前处理投槽操作指导

D. 槽液损失后的补充,如除渣后:总酸点每下降一点,每1000L磷化液 中加入0.96 kg H7211,1.4L(2 kg)Gardodond 2600 TA 和170ml(0.21 kg) H7256。将 H7211在充分搅拌下加入槽液。然后加入 2600TA ,H7256。工作前需测促进剂点,并补充 H7001至通常水平。
6.两次水洗阶段
作用: 产品成分: 处理时间: 压力: 滴定总酸点:
R3 水洗 自来水 0.5min 0.1-0.2 MPa E3< 2.0
R4 水洗 自来水 浸入即出 0.1-0.2 MPa E4< 1.5
检测方法 名称:水洗阶段-滴定总酸点
数目 1 1 1 1 1
器皿名称 椎形烧瓶 移液管 试管 滴定管 滴瓶
南京凯密特尔表面技术有限公司
NANJING CHEMETALL SURFACE TECH. CO., LTD.
3.两次水洗阶段+新鲜工业水洗
R1
作用:
水洗
产品成分:
自来水
温度:
<40℃
时间:
1min
压力:
0.10-0.20 M水洗 自来水 <40℃ 1min 0.10-0.2 MPa
检测方法 : A.总酸点测定 : 移取10ml槽液于锥形瓶中,用100ml蒸馏水稀释,加 2-3滴酚酞指示剂,用0.1N NaOH标准液滴定溶液颜色由无色变为粉红 色,所耗用的0.1N NaOH的毫升数即总酸点。 B.游离酸点的测定 : 移取10ml槽液于锥形瓶中, 用100ml蒸馏水稀 释,加2-3滴溴酚蓝指示剂,用0.1N NaOH标准液滴定溶液颜色由淡黄 色转兰紫色,所耗用的0.1N NaOH的毫升数即游离酸点。 C.促进剂点测定 :移取槽液至发酵气管,加入 2-4g 工业级氨基磺酸; 快速倒置发酵气管,使尽量多的氨基磺酸进入发酵气管的顶部,然后 立即将发酵气管静置 1-2min。发酵气管上的读数即促进剂点.
前处理液槽管理规范

文件编号:
文件名称
前处理液槽管理规范
版号:A/0
分发日期:
1/3码:页
分发编号:
一、予脱脂:浓度:30-35,时间10-15分钟
浓度测定、管理方法:1、取工作液10ml,以酚酞作指示剂,用0.1NH2S4溶液滴定,使溶液从粉红色变至无色时消耗之毫升数为溶液的游碱度。
2、浓度尽量保持在基准范围内,如果低于基准点,加脱脂剂提高其浓度。
三、除锈:浓度120-150,时间:10-15分钟。
测定、管理方法:
1、用比重器放入液槽中,所余之数为基数。
2、定期检测,正常情况3-5个月更换新液。
四、水洗:时间:1-2分钟
1、清水保持溢流。
2、定期每周更换清水。
编写
审核
批准
环城制品厂程序文件
文件编号:
文件名称
前处理液槽管理规范
版号:A/0
分发日期:
划痕至基体形成九个方块。方格边长为1毫米,用手指轻轻触摸,
方格脱落不超过2个以内为合格。或用粘贴法进行胶带试验。
编写:
审核:
批准:
环城制品厂程序文件
文件编号:
文件名称
喷涂车间制程检验作业指导
版号:A/0
分发日期:
页码:1/2
分发编号:
1、目的
喷涂工序作为工件表面处理的一个特殊过程,对工件最终是否合格,起到关键的作用。因此对每一质量控制点及过程参数必须进行控制和监督,以确保满足规定要求。
要求:1、喷涂完成的工件经过十分钟时间流平。
2、温度与速度(时间)保持控制在标准的范围内。
九:检验:
要求:1、色差与样板一致,表面必须平整,光滑、无砂粒,无疙瘩,
前处理工艺槽液的日常管理

前处理工艺槽液的日常管理一、脱脂槽:1.开新槽,按每吨水添加脱脂粉50㎏,脱脂剂1﹪即达到游离碱度40点。
为了增加除油效果,减少除油时间,采用加温方法来提高脱脂速度。
槽液温度控制在60-70°C之间。
2.检测与添加,首先用试管吸入10ml槽夜放入锥形瓶中加入酚酞指示剂3-4滴,再用试管吸入0.1N HCL标准液滴定由红色变为无色时为终点,所消耗0.1N HCL标准液(ml)即为游离碱度。
添加方法:每吨槽液添加脱脂粉1.8㎏,游离碱会提高3度。
二、除锈槽:开新槽:按每吨水加31﹪的浓盐酸180㎏,即得18﹪的槽液浓度。
添加方法一般按坯件除锈效果作适量添加。
三、表调槽:新开槽按每吨水加入表调剂(胶肽)2㎏即达到PH值8。
日常管理:生产时防止酸性、碱性污染表调槽,影响表调效果。
PH值应保持在8-9,正常生产一段时间后应更换槽液。
四、磷化槽:新开槽按每吨水加入磷化剂60㎏,促进剂2㎏充分搅拌均匀,即符合规定的槽液。
日常管理,每天总酸度控制在25-35度之间,促进剂点数在1.5-3.0之间检测与添加。
总酸度:用试管吸入槽液10ml放入锥形瓶中加入酚酞指示剂3-4滴再用试管吸入0.1N NaOH标准液加入由无色变为红色时为止,所消耗NaOH溶液ml数即为总酸度。
促进剂:用发酵管装满磷化剂再加入1g左右发酵粉上下振动静止后发酵管所显示的即为促进剂点数。
当槽液总酸度低于规定值时,每吨槽液添加磷化液1.5升总酸度提高1度。
促进剂:低于规定值时按每吨槽液添加促进剂2.5㎏,度数上升1度。
日常每天1-2次磷化渣打捞。
五、水洗槽:生产时每道水洗槽保持溢流水,平时有计划的轮流清洗洗水槽。
脱脂后水洗槽PH值控制在7-8之间。
酸洗后的水洗槽PH值控制在6-7之间。
磷化后的水洗槽PH值控制在7。
六、按GB/T601-2002《化学试剂标准滴定溶液的制备》规定:量取9ml盐酸,注入1000ML水中,所得为0.1mol/l,因盐酸的当量浓度与摩尔浓度相同,也就是0.1N的盐酸了。
前处理作业指导书

3.5.1用10ml吸管取10ml加工液置于三角烧杯中。
3.5.2滴加3~5滴BPB指示剂,摇匀。
3.5.3以0.1N NaOH进行滴定,边滴定边晃动烧杯。
3.5.4溶液由黄色变为淡蓝色为终止点,滴定过程中所消耗至0.1NNaOH毫升即为浓度,1ml=1piont。
降到规定温度
皮膜槽促进剂过高
调节降低
酸比过高
调节降低酸比
3.皮膜不均匀,甚至不上膜
脱脂不彻底
检测浓度后添加脱脂剂
表调液浓度偏低或老化
调整或更新
酸洗槽浓度太低
检测浓度后补充浓H2SO4
皮膜槽全酸度偏低或促进剂浓度偏高
检测浓度后进行调整
4.皮膜有水痕
烘干温度不足
升温
工件内水未流干净
改变挂具
5.皮膜发黑
酸洗槽浓度过高或浸泡时间过久
版本
制定日期
2012年8月6日
3.4槽液全酸度(TA)的测试方法:
3.4.1用10ml吸管取10ml加工液置于三角烧杯中。
3.4.2滴加3~5滴PP指示剂,摇匀。
3.4.3以0.1N NaOH进行滴定,边滴定边晃动烧杯。
3.4.4溶液由无色变为粉红色为终止点,滴定过程中所消耗至0.1NNaOH毫升即为浓度,1ml=1piont。
3.4.4溶液由黃色变为藍色为终止点,滴定过程中所消耗之0.1NNaOH毫升数即为浓度,1ml=1piont
3.4.5检验完毕。清洗所使用的测试工具,并放入指定位置。
3.4.6记录所测试浓度
★注意:1.轻拿轻放,小心打碎玻璃仪器(如三角烧杯、试管等)。
2.小心药水溅到眼睛(如溅到立即用水冲洗)。
3.切记清洗试管、烧杯,防止试药被污染。
前处理工艺介绍

前处理工艺介绍前处理工序:除油清洗除锈清光中和粉磷化清洗1.除油:比例。
除油粉50%。
脱脂剂50%。
PH值。
13-14总碱度35-50。
处理时间:5-20分钟。
技术要求:每天打捞厚油。
更换时间:半年全池更换一次。
开槽配制:水(4500㎏)+除油粉(225㎏)+脱指(225㎏)+搅拌均匀体测方法:吸取槽液20ML于200ML锥形瓶中。
加入酸酞(H2S04)3-4滴,用0.1NH2S04滴定红色消失为终点,所耗0.1NH2S04毫开数为总碱度点数,每吨槽液添加1㎏除油粉总碱提高017点(615K 开开1点)2.清洗:比例:自来水.PH值7-8处理时间:1-2分钟,技术要求:使用连续循环清水,更换时间:半月全池更换.开槽配制:清池清水.3.除锈:比例:酸性脱脂剂1-2%盐酸度31%PH值:2-3.处理时间:5-10分钟,技术要求:管类铁板2件处理后2件不能酸洗.更换时间:半年会地更换一次..开槽配制(容积计算):31%的盐酸4400㎏.酸性脱脂剂1-2%.氧化皮去除添加剂22.5㎏.0.5%.检测方法:1.取中性脱指剂注入500ML量简中.八分满放入比重升后至清洗止后,读界面比重计之读数为此重值(1。
02±0.02)2.用PH值试纸入溶液1分钟后,取对照色板(7±0.5)1.清洗:比例:自来水PH值4-5.处理时间:0.5-1分钟,技术要求:使用连续循环清水,更换时间:半月全池更换一次.开槽配制:清槽清水.2.中和:比例:中和粉0.5-10%.PH值:8-9.处理时间:1-2分钟.技术要求:使用连续循环清水,更换时间:半月全池更换一次.开槽配制(容积计算):先将中和粉50㎏在意小器中溶解后加入放满水的水池中溶解(0.5-1%)检测方法:用PH底纸测量.PH值要求为8-9.3.磷化:比例:鋅系磷化50%.促进剂.PH值:总酸度25-35点,游离酸度:1.1-1.9点,促进剂AC2-5点处理时间;半月全池更换一次.开槽配制:水(5000㎏)一锌系磷化剂(250㎏)+促进剂(15㎏)+中和粉(4㎏)促进剂需用水稀释数位后加入水中和粉用水完成溶解.检测方法:A.总酸度的检测方法:取槽液10ML置于锥形瓶中加3-5滴酸酞指指示剂.再用0.1NaOH标准液滴颜色.由无色变成粉红色.且轻摇荡不再消失为终点所耗NaOH,溶液毫开数即为总酸度。
汽车涂装前处理槽液的工艺管理.doc

汽车涂装前处理槽液的工艺管理作者:尚中萍来源:万方数据时间:2009-3-11 9:53:09在钢铁的制造、冲压成型中,会使用各种保护油、润滑油、冲压油、粘合剂、焊接助剂等,而要得到光滑平整、耐腐蚀好、附着力好的涂层取决于工件表面的清洁程度及磷化膜的质量。
刖处理就是对铁板、钢板、镀锌板等金属的表面进行清洗、化学处理而使底材易于电泳涂装,从而得到所需的防腐蚀涂层。
本文针对汽车涂装前处理在实际生产过程中存在的工艺管理问题,结合结口本公司实际从技术角度阐述了其对涂装质量的影响。
在钢铁的制造、冲压成型中,会使用各种保护油、润滑油、冲压油、粘合剂、焊接助剂等,而要得到光滑平整、耐腐蚀好、附着力好的涂层取决于工件表面的清洁程度及磷化膜的质量。
前处理就是对铁板、钢板、镀锌板等金属的表面进行清洗、化学处理而使底材易于电泳涂装,从而得到所需的防腐蚀涂层。
本文针对汽车涂装前处理在实际生产过程中存在的工艺管理问题,结合本公司实际从技术角度阐述了其对涂装质量的影响。
0引言涂装是汽车耐腐蚀和装饰最经济有效的方法。
而涂装前处理是涂装中不可缺少的重要工序,是提高涂膜附着力、耐蚀性的关键环节,其目的是为了去除被涂件构成物之外的所有异物,提供适合于涂装要求的良好基底,以保证涂层具有良好的防腐蚀性能和装饰性能。
它直接关系到涂装质量的优劣,而且关系到涂装产品寿命的长短,甚至关系到涂装产品价值的高低。
本文结合实际工作探讨了涂装前处理槽液的工艺管理对涂装质量的影响。
1 工艺管理要点涂装前处理工艺管理必须从脱脂到干燥的全工艺过程进行细致而又认真的管理,而脱脂、表面调整、磷化、水洗工序既是重点又是难点,其工序管理主要是下述几个因素。
(1)脱脂、表面调整-时间、温度、浓度、更新周期;(2)磷化-时间、温度、浓度、渣;(3)水洗-污染度、水质;(4 )其他钢板表面状态、各工艺之间的问题。
其中最关键的因素是浓度、温度和时间三大要素,如果发生磷化膜不良等问题时,在考虑到十分复杂的推定原因之前,首先要调整和确认浓度、温度和时间这些因素,这是十分重要的。
前处理表调槽工艺说明

前处理表调槽工艺说明
一、胶钛产品用途:
本产品为胶体磷酸酞盐表面调整剂,具有调整能力强,槽液长期稳定,抗硬水性强,可用任何自来水,井水,河水配制,适合于大部份中温、常温磷化前的表面调整,经本品处理的工件,可加快磷化成膜速度,减少磷化沉渣,形成更细致、密实、均匀的磷化膜。
二、产品使用法:
三、产品说明:
1.将计量好的胶钛先用少量水(最好热水),使之充分溶解,然后加入槽中,
搅拌均匀,测定总碱度,PH值8-10即可使用。
2.每天开工前应将槽液充分搅拌,且测量PH值,然后根据需要补加表调剂,
如前面工序带入杂质,尤其是酸,容易使本品老化,一般槽液呈污黑或污黄色,应弃去槽液,重新开槽。
四、溶液的日常管理:
1.以1000L水计,每补加2KG表调,PH值上升1点。
2.PH值测试方法:取一条广泛测纸放入槽液中半秒钟取出,对照广泛纸上之
PH值。
一般为8-10。
汽车涂装前处理槽液的工艺管理

汽车涂装前处理槽液的工艺管理作者:尚中萍来源:万方数据时间:2009-3-11 9:53:09 在钢铁的制造、冲压成型中,会使用各种保护油、润滑油、冲压油、粘合剂、焊接助剂等,而要得到光滑平整、耐腐蚀好、附着力好的涂层取决于工件表面的清洁程度及磷化膜的质量。
前处理就是对铁板、钢板、镀锌板等金属的表面进行清洗、化学处理而使底材易于电泳涂装,从而得到所需的防腐蚀涂层。
本文针对汽车涂装前处理在实际生产过程中存在的工艺管理问题,结合本公司实际从技术角度阐述了其对涂装质量的影响。
在钢铁的制造、冲压成型中,会使用各种保护油、润滑油、冲压油、粘合剂、焊接助剂等,而要得到光滑平整、耐腐蚀好、附着力好的涂层取决于工件表面的清洁程度及磷化膜的质量。
前处理就是对铁板、钢板、镀锌板等金属的表面进行清洗、化学处理而使底材易于电泳涂装,从而得到所需的防腐蚀涂层。
本文针对汽车涂装前处理在实际生产过程中存在的工艺管理问题,结合本公司实际从技术角度阐述了其对涂装质量的影响。
0 引言涂装是汽车耐腐蚀和装饰最经济有效的方法。
而涂装前处理是涂装中不可缺少的重要工序,是提高涂膜附着力、耐蚀性的关键环节,其目的是为了去除被涂件构成物之外的所有异物,提供适合于涂装要求的良好基底,以保证涂层具有良好的防腐蚀性能和装饰性能。
它直接关系到涂装质量的优劣,而且关系到涂装产品寿命的长短,甚至关系到涂装产品价值的高低。
本文结合实际工作探讨了涂装前处理槽液的工艺管理对涂装质量的影响。
1 工艺管理要点涂装前处理工艺管理必须从脱脂到干燥的全工艺过程进行细致而又认真的管理,而脱脂、表面调整、磷化、水洗工序既是重点又是难点,其工序管理主要是下述几个因素。
(1)脱脂、表面调整-时间、温度、浓度、更新周期;(2)磷化-时间、温度、浓度、渣;(3)水洗-污染度、水质;(4 )其他钢板表面状态、各工艺之间的问题。
其中最关键的因素是浓度、温度和时间三大要素,如果发生磷化膜不良等问题时,在考虑到十分复杂的推定原因之前,首先要调整和确认浓度、温度和时间这些因素,这是十分重要的。
前处理药水用量优化提案资料

更改后单套 用量(kg)
0.03 0.028 0.0173 0.0003 0.0024
单套降低用 用量下 单价 量(kg) 降比率 (元/kg)
0.001
3.23%
4
0.002
6.67%
4
0.0023 11.73% 4.4
0.0001
25%
20
0.0016
40%
2
单套机箱节省成本: 0.02732
月节省成本: 3278.4
磷化液处理槽在经过处理产品一段时间后槽内会有残渣物, 使得槽液过脏及老化过快,一般每隔3个月需对槽液进行 更换。
磷化槽
问题分析
主脱脂槽和磷化槽都因槽内的残渣物而影响了处 理产品的效果和槽液药水的利用率。
两个槽的残渣物存在方式不同: 主脱脂槽残渣物(主要为油脂)漂浮于液面; 而磷化槽内的残渣物沉淀于槽内底部。
前处理药水用量优化
2011-04
目录
问题描述 问题分析 改善方案 改善前后对比
总结
问题描述
主脱脂槽的经过使用一段时间后,药水表面会附上一层油 脂,使得产品在脱离主脱脂槽进入下一工序时表面附上一 些油脂。为清理这些油脂,每隔3-4个月需更换主脱脂槽 液,使得水资源和药水浪费。
主脱脂 槽
问题描述
前处理药水用量变更前后对比:
物料名称
中性脱脂剂 环保脱脂剂 特效锌系磷化液 表调 促进剂
物料编号
更改前单套 用量(kg)
390-0800001R2 0.031
390-0800000R2 0.03
390-1200000R2 0.0196
390-1400000R2 0.0004
390-2300000R2 0.004
槽液的调整及控制

槽液的调整及控制1、如除油速度减缓时,可适当投入1/3份量的各型号的固体铬合剂,在添加时应先用10倍以上重量的原液再适当加酸溶解呈澄清状后再混入槽液中,工作能量又即可上升复原。
2、如除锈速度减缓时,可分析总酸度和游离酸度,按当时的差额添加磷酸或盐酸、或硫酸、或按生产时使用经验加适当量。
3、本厂生产的磷化液一般不会衰减,但由于蒸发及被部件带走,将使槽液不断减少,届时可加同样浓度本溶液使之恢复到原来容量。
4、本产品可以浓缩成固体粉末形式出售,销售时按用户的要求当面议定。
总酸度及游离酸度的分析方法测定游离酸度和酸度是采用氢氧化钠中和法,中和时有两个当量点,可分别用甲基橙 (PH2.1-4.4)和酚酞(PH8.3-10.0)作指示剂显示出来,但由于测定过程中磷酸二氢盐水解沉淀,影响当量点的测定,所以终点不如一般酸碱滴定明显,只能测得它们的近似值。
测定游离酸的量为游离酸度。
游离酸和未离解的磷酸总量为总酸度,10毫升试样所需0.1NaOH溶液毫升数为基酸度值。
酸度值一般用点来表示,滴定10毫升试样至终点时所耗用0.1N氢氧化钠溶液的毫升数即为点数,但由于88-1型88-2型和88-4型88-5型溶液中含游离酸度及总酸度都很高,所以用来标定酸值的NaOH克当量应相当提高到1N,则计算酸值点数时,要比原规定的大几倍。
即消耗0.1NNaOH溶液1毫升称为“1点”,消耗1NNaOH溶液1毫升为1/0.1点,即为10点,测定游离酸度以甲基橙为指示剂,测定总酸度以酚酞为指示剂。
I 试剂:A)甲基橙指示,0.1克甲基橙溶解于100毫升蒸馏水中。
B)酚酞指示剂,1克酚酞溶解于100毫升酒精中。
C)1NNaOH标准溶液。
配制:称取化学纯氢氧化钠40克,溶于新鲜蒸馏水中释至1升。
称定:精确称取干燥的邻苯二甲酸氢钾约0.5克(四位有效数字)放在250毫升三角烧瓶中,加水100毫升及甲基橙指示剂3滴,用配制好的氢氧化钠溶液滴定至溶液由红色变为橙色即为终点。
前处理槽体清洗计划

河北中兴汽车有限公司宜昌分公司前处理线清洗计划南京凯密特尔表面技术有限公司2013.2一、工作计划时间表二.洗槽工作计划1.前处理工艺流2.洗槽工作计划时间表3.设备清洗具体步骤槽体清洗阶段:在确认设备之后没有任何问题下,开始进入槽体清洗。
1.洪流热水洗工段;a.加水至工作液位,升温至50℃;b.打开循环泵,加入0.5‰的Gardolean 10037/2,喷淋2小时;c.停止循环泵,排放掉槽中水;d.人工冲洗、清理槽中残留的铁屑以及其他杂物;f. 再加入清水,喷淋半小时,排空水槽;2.预脱脂工段:a.加水至工作液位,升温至50℃;b. 打开循环泵,加入0.5‰的Gardolean 10037/2,喷淋2小时;c.停止循环泵,排放掉槽中水;d.人工冲洗、清理槽中残留的铁屑以及其他杂物;e.再加入清水,喷淋半小时,排空水槽;3.脱脂槽工段:a.加水至工作液位,升温至50℃;b. 打开循环泵,加入0.5‰的Gardolean 10037/2,循环4小时;c.停止循环泵,排放掉槽中水;d.人工冲洗、清理槽中残留的铁屑以及其他杂物;e.再加入清水,循环1小时,排空水槽;4.第一、二水洗工段:a.加水至工作液位;b.打开循环泵,加入0.5‰的Gardolean 10037/2,第一水洗循环2小时,第一水洗循环4小时。
c.停止循环泵,排放掉槽中水;d.人工冲洗、清理槽中残留的铁屑以及其他杂物;e.再加入清水,循环1小时,排空水槽。
5.表调槽工段:a.加水至工作液位;b.打开循环泵,加入0.5‰的Gardolean 10037/2,循环4小时。
c.停止循环泵,排放掉槽中水;d.人工冲洗、清理槽中残留的铁屑以及其他杂物;e.再加入清水,循环1小时,排空水槽。
6.磷化槽工段:a.加水至工作液位,升温至40-45℃;b. 打开循环,加入0.5‰的Gardolean 10037/2,循环,4小时;c.停止循环泵,排放掉槽中水;d.人工冲洗、清理槽中残留的铁屑以及其他杂物;e.再加入清水,循环1时,排空水槽;7.第三、第四水洗工段:a.加水至工作液位;b.打开循环泵,加入0.5‰的Gardolean 10037/2,第三水洗循环2小时,第四水洗循环4小时;c.停止循环泵,排放掉槽中水;d.人工清理槽中残留的铁屑以及其他杂物;e.再加入清水,循环1小时,排空水槽;8.第1和2纯水洗工段:a.加水至工作液位;b. 打开循环,加入0.5‰的Gardolean 10037/2,第三水洗循环2小时,第四水洗循环4小时;c.停止循环泵,排放掉槽中水;d.人工冲洗、清理槽中残留的铁屑以及其他杂物;e.再加入清水,循环1时,排空水槽;f.再注满纯水洗、循环1小时,排空。
喷淋除油自动前处理作业指导书

4、 每立方米槽液提咼游离碱1个点约需添加
1.1kg ST-1015B
5、 新开槽加水至刚好淹没报警盒,需加9袋 (225kg)ST-1015B。
附
图
编制/日期
审核/日期
审批/日期
自动前处理作业指导书
工序号:
工 序 内 容
1、待生产线开线前先检测其溶液的总碱度、游离 碱度、温度、喷淋压力是否达到工艺要求,达 到工艺要求后方可开线。
2、槽液每两小时检测一次,若其浓度低于工艺要 求时,补加ST-1015B,并将其溶解后加入。
3、每7天检查清洗一次喷嘴,每1~2个月更新一 次槽液。
0.5~1.0kg/cm2
压力表读数
每两小时一次
化验员
5.
水位
刚好淹没报警器即可
目测
每两小时一次
化验员
6.
燃烧机
运行情
况
当温度低于设定值时
可正常起动二段火
目测
每两小时一次
化验员
7.
棚体链
轨滴水
情况
不允许
目测
每班一次
化验员
注
意
事
项
1、游离碱和总碱检测方法同超声波除油注意事项
1。
2、喷淋除油有效长度19m。
4、每次停机时都要检查一次工件有无掉落。
5、每次调整压力时都要到棚顶上观察其挂具摇
摆情况。
检 测 内 容
序号
检测内
容
工艺要求
检测方法
频次
操作者
1.
游离碱
15~25点
酸碱滴定
每两小时一次
化验员
2.
总碱
20~40点
- 1、下载文档前请自行甄别文档内容的完整性,平台不提供额外的编辑、内容补充、找答案等附加服务。
- 2、"仅部分预览"的文档,不可在线预览部分如存在完整性等问题,可反馈申请退款(可完整预览的文档不适用该条件!)。
- 3、如文档侵犯您的权益,请联系客服反馈,我们会尽快为您处理(人工客服工作时间:9:00-18:30)。
关于前处理药剂槽液控制和清理周期的说明
单元板前处理工艺中包含预脱脂、脱脂、酸洗出光、无铬钝化四个药剂工作槽位。
其中预脱脂、脱脂工序的作用为清除工件表面的油脂及灰尘,同时对铝材表面进行碱腐蚀作用,以达到去除铝材表面的天然生成的氧化膜,便于下道工序的处理。
在处理过程中,处理药剂和铝材发生化学反应,不可避免的会产生一定量的衍生物和沉渣。
因此,在工作一定的周期后需要对处理槽内的槽液进行清渣或对槽液进行更换。
具体更换和清理周期的频率根据处理量的大小以及槽内沉渣量的多少而定。
一般情况下,当槽内沉渣厚度高于10cm,或者已经对喷淋室内的喷嘴及换热系统造成堵塞等现象时需及时进行清渣处理。
每连续工作60~90天或者槽液内杂质过多、色泽变深发暗时应考虑更换脱脂和预脱脂槽液。
酸洗出光槽液的作用是对铝材表面进行酸腐蚀,去除碱腐蚀后的残留物和铝材表面自身带有的硅类物质。
在生产过程中应及时清除槽液表面集聚的漂浮物,以维持槽液的清洁度。
酸洗出光液的更换周期一般为预脱脂和脱脂槽液更换周期的1.5~2倍无铬钝化槽液的作用是在铝材表面生成一种不含铬的钝化层,增加基体和涂层之间的结合能力,同时抑制涂层破裂后基体的腐蚀速度,提高产品的抗腐蚀能力。
无铬钝化槽液的维护类似于酸洗出光工序。
注意清除槽液表面的漂浮物。
更换周期为60~90
个工作日。
由于部分待处理工件长时间放置后表面已经产生腐蚀和氧化,所以在涂装前处理过程中需要尽可能多的去除氧化物,去除氧化物的方式主要为提高预脱脂和脱脂槽液的游离碱度,酸洗出光槽液的游离酸度也应适当提高。
处理发生氧化的板材预脱脂和脱脂的游离碱度应控制在15~18点之间,温度50~55℃。
处理正常板材时游离碱度应控制在4~6点之间为宜。
如游离碱度控制过高,槽液内会产生较多的沉淀物,堵塞喷嘴和热交换系统。
因此,在处理产生氧化的板材期间,应适当缩短预脱脂和脱脂槽液的清理间隔时间,以维持生产线的正常云状和处理效果。
酸洗出光液的控制指标为游离酸度50~100点之间。
处理发生氧化的板材时,实际操作数据应为规定范围的高位为宜。
江都市金属表面处理有限公司生产技术部
二0一一年七月一日。