塑胶产品结构设计案例
塑胶件通用结构设计

Rev.A
P17
壁厚:
壁厚影响收缩
Rev.A
P18
壁厚:
Rev.A
壁厚影响收缩
前后模温度差异大时,冷却效率所影响,冷面先收缩,但很快固化,收缩量 固定,但热面缓慢收缩,分子有较长时间重排,收缩量会更大,所以产品会 向热的一面弯曲(产品各处温度差 大于10 ̊C以上)
P19
Rev.A
壁厚:
壁厚影响收缩
PC 6485 UL.pdf
P25
肋骨:
肋骨厚度:
Rev.A
P26
Rev.A
肋骨:
肋骨厚度推荐值:
高光泽面, 可以选择更薄的厚度: <1.5mm, 厚度推荐值 <=1.0mm, 等于壁厚
P27
Rev.A
肋骨:
加强筋厚度与塑件壁厚的关系:
P28
肋骨:
薄壁肋骨问题:
-难填充 -靠近浇口比远处更难填充 -当壁厚在填充时,薄壁滞流冻结
圆角加大,应力集中减少。 内圆角R <0.3T----应力剧增。 内圆角R >0.8T----几乎无应力集中
Rev.A
P33
肋骨:
常见加强肋设计:
Rev.A
P34
肋骨:
常见加强肋设计:
Rev.A
P35
肋骨:
常见加强肋设计:
Rev.A
P36
肋骨:
常见加强肋设计:
Rev.A
P37
Rev.A
肋骨:
Rev.A
P2
Rev.A
壁厚:
壁厚的影响: 机械性能,感观,模塑性,成本
- 壁厚的选择是各方面的平衡 *强度 VS 减轻重量 *耐久性 VS 成本
塑料模具设计实例
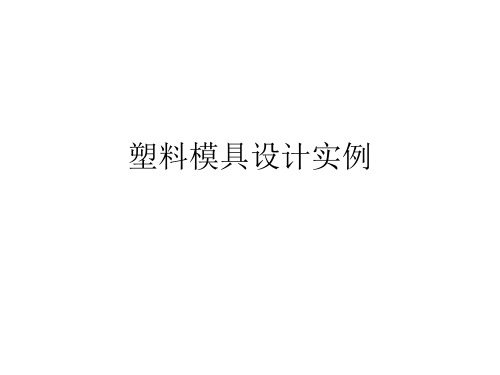
塑料件结构图
模具图
模具图-卸ቤተ መጻሕፍቲ ባይዱ图
模具设计特点
• 制品为薄壁件,内腔相对较深且有一定的精度要求。该模具采 用点浇口,并设计了点浇口自动切断脱落机构;采用摆块式二 级机构,确保了制品不发生推出变形。模具结构紧凑,工作安 全、可靠。 • 工作原理:开模时,在弹簧20的作用下I-I面首先分型,拉料杆 13拉断点浇口,流道凝料脱出流道板14,保留在拉料杆上。流 道板14运行至定距拉杆17端部时受定距拉杆17的阻挡而停止。 接着Π-Π面分型。当Ι-Ι面分型之后,脱浇板11在弹簧15的作用下, 将流道凝料推离拉料杆13,继而弹簧8推动拉料杆9,使流道凝 料脱离浇口套10和脱浇板11而掉落。定距螺钉5限定脱浇板11的 推出高度。当Π-Π面分型到一定距离时,机床开始推动推板37, 安装在推板两侧的顶板26推动顶块25向上转动(以轴钉29为转 轴),从而推动推件板23和凹模板22上行,由于凸模21不动, 故制品与凸模脱松,完成第一级推出动作。继续推出,顶板26 失去对顶块25的作用,故推件板和凹模板不在上行,而推杆36 继续上行将制品推出凹模,完成第二级推出动作。
再例如-零件图
模具结构
模具结构
花盆及模具设计
花盆结构图
模具结构——一次注塑两件
模具结构——一次注塑两件
花盆模具特点
• 特点:制品为深腔圆桶形状。该模具设计了2个型腔; 采用流道浇注系统,使用塑料能够较好地充模并节约原 料;型腔、型芯设计均设计了螺旋式冷却水路,使冷却 和冷却效率提高;定、动模合模时除了导柱导身装置外, 增加了圆锥定位面,确保了制品壁厚的均匀性;镶块31 的装配面要留有适当间隙(必要时开设气道),避免制 品与型芯之间产生真空状态。推件采用推件板,同气吹 结合的方式。 • 工作原理:开模后,制品脱离型腔镶件7留在型芯10上。 推出时,连接推杆36和环形推件板9在推板13的作用下, 将制品上推出一小段高度,然后高压空气经过进气管接 头11进入制品与型芯脱松的空隙中,制品即补吹起,最 后由人工取出制品。连接推杆36上套有弹簧37可使推件 板9复位。
塑胶件结构设计方案(PPT 50页)

从产品设计角度来看: 过厚的产品增加导致产生 ”空穴” 气孔的可能性, 大大削弱产品的刚性及强度 .
1. 由厚胶料的地方过渡到薄胶料的地方应尽可能顺滑, 太突然的壁厚过渡转变 会导致因冷却速度不同和产生乱流而造成尺寸不稳定和表面问题, 并且此處 模具易產生磨損.
2. 采用固化成型的生产方法时, 流道, 浇口和部件的设计应使塑料由厚胶料的 地方流向薄胶料的地方, 这样使模腔内有适当的压力以减少在厚胶料的地方 出现缩水及避免模腔不能完全充填的现象; 若塑料的流动方向是从薄胶料的 地方流向厚胶料的地方, 则应采用结构性发泡的生产方法来减低模腔压力.
加强筋的一般設計形式 角支撑的形式
材料厚度与加強筋的尺寸关系(一)
PC,PPO PA,PE PMMA,ABS PS
T’<0.6T T’<0.5T T’<0.5T T’<0.6T
肋根部厚度约为(0.5~0.7)T 肋间间距>4T 肋高L<3T
不同材质的加强筋细节有所区别 ABS
材料厚度与加強筋的关系(三)
2、在制品形状方面:能满足使用要求,有利于充模,排气,补缩,同时能适应高效冷 却硬化(热塑性塑料制品)或快速受热固化(热固性塑料制品)等.
3、在模具方面:应考虑它的总体结构,特别是抽芯与脱出制品的复杂程度;同时应 充分考虑模具零件的形状及其制造工艺,以便使制品具有较好的经济性.
4、在成本方面:要考虑注射制品的利润率,年产量,原料价格,使用寿命和更换期 限,尽可能降低成本.
材料厚度与加強筋的关系(二)
材料厚度与加強筋的关系(四)
如果对外观要求不是很严格的话可以在此处 加一个槽防止缩水和产生气泡
三 塑胶零件及产品设计---卡扣篇
塑胶产品结构 BOSS柱 螺丝柱 较全

2.6,BOSS柱的设计2.6.1,BOSS柱即凸出的柱子,通常指螺丝柱及紧配柱,是固定导向结构.螺丝柱有两种:自攻牙及机牙.a.自攻牙为自攻螺钉+塑胶BOSS柱,结构见图2.6.1aSD:螺钉外径;WD:螺帽外径;D:塑胶柱子外径;d:塑胶柱子底孔直径;自攻螺丝的BOSS柱设计原则:D=3*SD,[柱子壁厚≥(0.5-0.7)T]d=0.85*SD(质碎取0.9倍,质软取0.8倍)螺丝过孔一般为SD+0.4即可。
图2.6.1a图中两种固定方式,第一种:两塑胶件固定;第二种为PCB固定;b.机牙第一种方式为机牙螺钉+铜螺母+塑胶BOSS柱,铜螺母装入BOSS柱有热熔和直接成型两种.热熔见图2.6.1b-1CD:铜螺母直径,Cd:铜螺母螺牙公称直径D:塑胶柱子外径;d:塑胶柱子底孔直径;热压铜螺母的BOSS柱设计原则:D=CD+1.5(质硬+1,质软+2)d=CD-0.6(质硬-0.5,质软-0.8)螺钉及安装方式2.6.1a中有说明如为直接成型结构,取消热压空隙及溢胶槽深图2.6.1b-1图2.6.1b-2图2.6.1b-2中为铜螺母常见样式及热压加工方式,热压方式是用熔压铜棒装入铜螺母,电加热压入塑胶柱中;直接成型是将其作为镶件装入模具中注塑成型,通过模具螺丝机定位.这两种方式成本类似,但热熔增加了周转加工成本,且加工后容易造成溢胶,铜螺母歪斜等异常;直接成型则增加了单壳体成型周期(增加安装铜螺母时间,一般为手工安装),但结构牢固,设计上优选.铜螺母设计原则:防脱落,防转动,锁牙牢靠.常见铜螺母有直纹滚花+凹槽,网纹滚花,斜纹滚花+凹槽. c.机牙第二种方式为机牙螺钉+标准螺母.这种方式常见机械锁紧,在塑胶制品中用于高受力强度壳体,如电池固定,结构手臂,灯具,电机底座,吹风机手臂固定等等.螺母采用标准螺母,采用套筒或扳手夹紧,用螺丝刀锁紧.在结构上为了方便,常会在胶壳上开槽,将螺母放置其中管住锁紧.d.紧配柱为柱孔配合结构,可做紧配拉紧及导向结构.常用在小壳件配合(U盘,读卡器,蓝牙等零件);PCB 定位,壳体防翘曲拉紧等.常见为圆形,一般紧配直径有1.0,1.2,1.5,1.8,2.0,2.5,3.0等等,值自定义.还有方形,椭圆形等其他异形结构.导向柱则需要单边留0.1-0.3mm间隙即可.H≥3mm(直径小于3)C≥R避空2.6.2,螺钉的选用:螺钉选用根据所使用的安装方式,2.6.1a/b/c中有介绍自攻及机牙安装结构,螺钉分自攻和机牙,自攻即螺距较大的螺钉在材料预留孔中挤压推进的固定咬合方式;机牙即按标准公制或英制牙加工处理的内外螺丝(同规格)相配合固定咬合方式.常用自攻螺钉尾部有平头,尖头等,螺帽有扁圆头,圆头,P盘头,C平头,K沉头.槽型可自定义,常用十字. BOSS柱锁牙达到3圈以上即可.尖头牙在BOSS柱锁牙足够情况下选用,具有导正牙的作用;平头牙在BOSS柱锁牙不够,高度偏低情况下选用,容易牙偏;C平头帽在压缩厚度情况下用,最薄可以做到1.0厚;P圆头:对厚度没要求常用的标准螺丝螺头;K沉头:常用在不超过平面的板件固定.机牙的牙距较小,不做挤压推进,所以仅有平头;螺帽除了自攻常用螺帽,还有内/外六角头,方头等,机牙锁牙达到2圈以上即可.因为机牙牙距较小,锁的圈数越多牢固.通常相同的长度,牙距越小锁牙越紧,强度越强.因此牙也有粗牙和细牙之分.粗牙即普通螺牙,细牙常见管螺纹.机牙的规格型号,请参考标准.2.6.3,塑胶预留自攻螺丝底孔设计参考值如下表所示.常用自攻螺丝装配及测试(10次)时所要用的扭力参考值,如下表所示.。
塑胶产品结构设计

塑胶产品结构设计要点1.胶厚(胶位):塑胶产品的胶厚(整体外壳)通常在0.80-3.00左右,太厚容易缩水和产生汽泡,太薄难走满胶,大型的产品胶厚取厚一点,小的产品取薄一点,一般产品取1.0-2.0为多。
而且胶位要尽可能的均匀,在不得已的情况下,局部地方可适当的厚一点或薄一点,但需渐变不可突变,要以不缩水和能走满胶为原则,一般塑料胶厚小于0.3时就很难走胶,但软胶类和橡胶在0.2-0.3的胶厚时也能走满胶。
2.加强筋(骨位):塑胶产品大部分都有加强筋,因加强筋在不增加产品整体胶厚的情况下可以大大增加其整体强度,对大型和受力的产品尤其有用,同时还能防止产品变形。
加强筋的厚度通常取整体胶厚的0.5-0.7倍,如大于0.7倍则容易缩水。
加强筋的高度较大时则要做0.5-1的斜度(因其出模阻力大),高度较矮时可不做斜度。
3.脱模斜度:塑料产品都要做脱模斜度,但高度较浅的(如一块平板)和有特殊要求的除外(但当侧壁较大而又没出模斜度时需做行位)。
出模斜度通常为1-5度,常取2度左右,具体要根据产品大小、高度、形状而定,以能顺利脱模和不影响使用功能为原则。
产品的前模斜度通常要比后模的斜度大0.5度为宜,以便产品开模事时能留在后模。
通常枕位、插穿、碰穿等地方均需做斜度,其上下断差(即大端尺寸与小端尺寸之差)单边要大于0.1以上。
4.圆角(R角):塑胶产品除特殊要求指定要锐边的地方外,在棱边处通常都要做圆角,以便减小应力集中、利于塑胶的流动和容易脱模。
最小R通常大于0.3,因太小的R模具上很难做到。
5.孔:从利于模具加工方面的角度考虑,孔最好做成形状规则简单的圆孔,尽可能不要做成复杂的异型孔,孔径不宜太小,孔深与孔径比不宜太大,因细而长的模具型心容易断、变形。
孔与产品外边缘的距离最好要大于1.5倍孔径,孔与孔之间的距离最好要大于2倍的孔径,以便产品有必要的强度。
与模具开模方向平行的孔在模具上通常上是用型心(可镶、可延伸留)或碰穿、插穿成型,与模具开模方向不平行的孔通常要做行位或斜顶,在不影响产品使用和装配的前提下,产品侧壁的孔在可能的情况下也应尽量做成能用碰穿、插穿成型的孔。
proe塑胶产品柱和孔结构设计
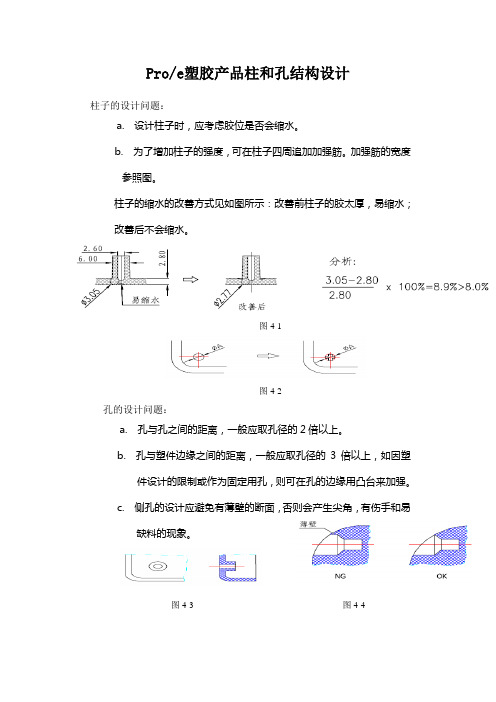
Pro/e塑胶产品柱和孔结构设计
柱子的设计问题:
a. 设计柱子时,应考虑胶位是否会缩水。
b. 为了增加柱子的强度,可在柱子四周追加加强筋。
加强筋的宽度
参照图。
柱子的缩水的改善方式见如图所示:改善前柱子的胶太厚,易缩水;
改善后不会缩水。
图4-1
图4-2
孔的设计问题:
a. 孔与孔之间的距离,一般应取孔径的2倍以上。
b. 孔与塑件边缘之间的距离,一般应取孔径的3倍以上,如因塑
件设计的限制或作为固定用孔,则可在孔的边缘用凸台来加强。
c. 侧孔的设计应避免有薄壁的断面,否则会产生尖角,有伤手和
易缺料的现象。
图4-3 图4-4 “减胶”的问题:
螺丝柱的设计:
5.1 通常采取螺丝加卡扣的方式来固定两个壳体,螺丝柱通常还起
着对PCB板的定位作用。
5.2 用于自攻螺丝的螺丝柱的设计原则是为:其外径应该是Screw
外径的2.0~2.4倍。
图6-2为M1.6×0.35的自螺丝与螺柱的尺寸关系。
设计中可以取:螺丝柱外径=2×螺丝外径;螺柱内径(ABS,ABS+PC)=螺丝外径-0.40mm;螺柱内径(PC)=螺丝外径-0.30mm 或-0.35mm(可以先按0.30mm来设计,待测试通不过再修模加胶);
两壳体螺柱面之间距离取0.05mm。
5.3 不同材料、不同螺丝的螺丝柱孔设计值如表5-2、表5-3所示。
更多关于Proe分享,请参看:。
塑料零件设计实例
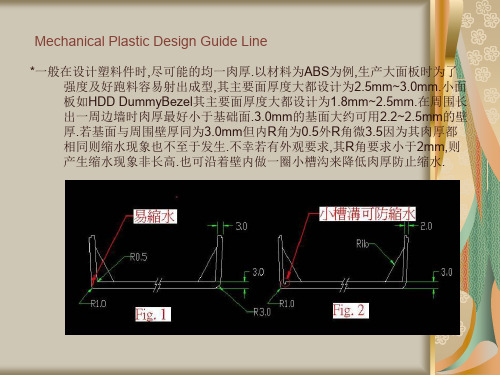
Mechanical Plastic Design Guide Line
*常在塑料件的结构上可看到运用塑料的韧性设计卡勾来结合其他的配合件.但往 往在材料的特性,卡勾的厚度,被组合件的重量,多重变异因素下,无法精确的 计算出要多大的强度时,常用Try anderr的方式达到所要的感觉.
在此情况下卡勾的长度先设计模补肉的动作.会比卡勾做太短,强度太大,不易组装 时再做补模去肉的动作来得容易.
Mechanical Plastic Design Guide Line
*常在塑料件的结构上可看到运用塑料的韧性设计卡勾来结合其他的配合 件.而卡勾在开合模上有UnderCut的特征.因此在模具上必须有其他 机构才能启闭模具而不至于剪断卡勾.一般都在公模上做斜梢或滑块, 但因其是滑动件,久而久之容易磨损而产生间隙影响尺寸,公差或毛 边产生或滑动件间的润滑油渗出污染成品.故除非会影影响外观,如 下右图面板.否则设计为公母模靠破方式,模具较经济也坚固.也无以 上之缺点.
Mechanical Plastic Design Guide Line
在固定塑料件(如面板)最常见的是以锁螺丝方式,而螺丝又常用的有自攻牙 与机械牙两种.采用机械螺丝者必须在塑料柱(Boss)上再insert铜柱.设计采 用机械螺丝固定组装是希望可多次的拆装动作. 需先选定适当的铜柱.再从铜柱的外径设计boss的尺寸,boss内径要比铜柱 的外径小约0.5mm.其boss肉厚约1.5mm.例如:PSM生产的M3铜柱外径有 4.6mm,4.4mm,4.2mm,三种.就必须配合着boss设计内径为4.1mm,3.9mm, 或3.7mm.
可在Lens的表面设计适当的咬花(Texture),让光线漫射.模糊了光原.效果就像 透明玻璃和毛玻璃的差异.
塑胶壳体设计优秀案例

塑胶壳体设计优秀案例## Excellent Examples of Plastic Enclosure Design.Plastic enclosures are an essential part of many electronic devices. They protect the internal components from damage and provide a finished look to the product. When designing a plastic enclosure, there are a number of factors to consider, including the size, shape, and material.Size and Shape:The size and shape of the enclosure will be determined by the size and shape of the internal components. It is important to leave enough space for the components to fit comfortably inside the enclosure, but not so much space that the enclosure is too bulky or unwieldy.Material:There are a variety of different materials that can be used to make plastic enclosures. The most common materials are ABS, polycarbonate, and acrylic. Each material has its own advantages and disadvantages. ABS is a durable and inexpensive material that is resistant to impact and chemicals. Polycarbonate is a clear material that is more expensive than ABS but is more durable and scratch-resistant. Acrylic is a lightweight and transparent material that is easy to mold and shape.Design Considerations:In addition to the size, shape, and material, there are a number of other design considerations to keep in mind when designing a plastic enclosure. These include:Ventilation: It is important to provide adequate ventilation for the internal components. This will help to prevent the components from overheating.EMI/RFI shielding: If the enclosure will be used to house electronic components that are sensitive toelectromagnetic interference (EMI) or radio frequency interference (RFI), it is important to provide EMI/RFI shielding.Gaskets: Gaskets can be used to seal the enclosure and prevent dust and moisture from entering.Assembly: The enclosure should be easy to assemble and disassemble. This will make it easier to service the internal components.Examples of Excellent Plastic Enclosure Design:There are a number of excellent examples of plastic enclosure design. Some of these examples include:The Apple iPhone: The iPhone is a well-designed electronic device that features a plastic enclosure. The enclosure is made of polycarbonate, which is a durable and scratch-resistant material. The enclosure is also lightweight and easy to grip.The Dyson Air Multiplier: The Dyson Air Multiplier is a fan that features a plastic enclosure. The enclosure is made of ABS, which is a durable and inexpensive material. The enclosure is also aerodynamically designed to help improve the airflow.The Bose SoundLink Mini II: The Bose SoundLink Mini II is a portable speaker that features a plastic enclosure. The enclosure is made of polycarbonate, which is a durable and lightweight material. The enclosure is also water-resistant, which makes it ideal for use in outdoor environments.These are just a few examples of excellent plastic enclosure design. When designing a plastic enclosure, it is important to consider the size, shape, material, and design considerations. By following these guidelines, you can create an enclosure that is both functional and aesthetically pleasing.## 杰出的塑料外壳设计案例。
塑胶产品结构设计案例
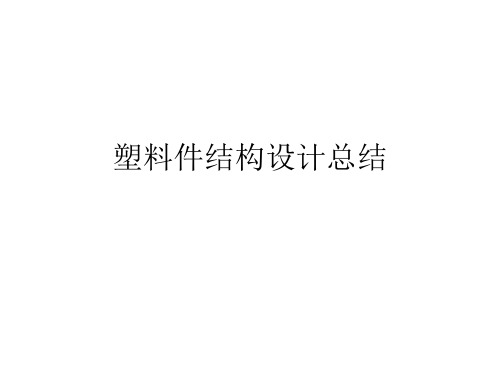
• POM 聚甲醛
– 用途:机械零件、齿轮、家电外壳
– 特性:耐磨、坚硬但脆弱,损坏时容易有利边出 现。
– 应用:多数用于胶齿轮、滑轮、一些需要传动, 承受大扭力或应力的地方。
• Nylon(尼龙,PA)
– 用途:齿轮、滑轮、纺织品
– 特性:坚韧、吸水、耐磨、吸震、耐热,但当 水份完全挥发后会变得脆弱。
3M螺丝
虚位设计(间隙)
一般零件与零件间的虚位(非活动 件) 零件与零件间的虚位(活动件) 电池门周边与壳身的虚位 电池门轴与壳身的擦穿坑虚位单边 需要与其它零件相配的擦穿坑 齿轮及滑轮与牙箱外壳的内壁
齿轮与齿轮之间的虚位(大齿轮半 径+小齿轮半径+虚位)=PCD 电池与电箱的骨位及电池门的虚位
电池与电池箱底部平面的虚位
2mm
Rib thickness 1.1~1.2mm
1.4~1.5mm
2.5mm
1.8mm
3mm
2.1mm
Height of Rib (x) x≦5mm
5<x≦10mm 10<x≦15mm
x≦5mm 5<x≦10mm 10<x≦15mm 15<x≦20mm 20<x≦25mm 25<x≦30mm
x≦5mm 5<x≦10mm 10<x≦15mm 15<x≦20mm 20<x≦25mm 25<x≦30mm
波在成品内发生Leabharlann 鸣,扩大音量。止口• 真止口
– 用途: 生产装配时作较对之用,而且可作涂胶水之用。
• 假止口
– 用途: 在外形上可作遮丑之用。
• 半假止口
– 用途: 如平均料厚有2.0mm或以上时,因为凹 槽太深的关系,所以需要在止口的位置加多一 层料,保持成品外形的美观。
塑胶产品结构设计卡扣
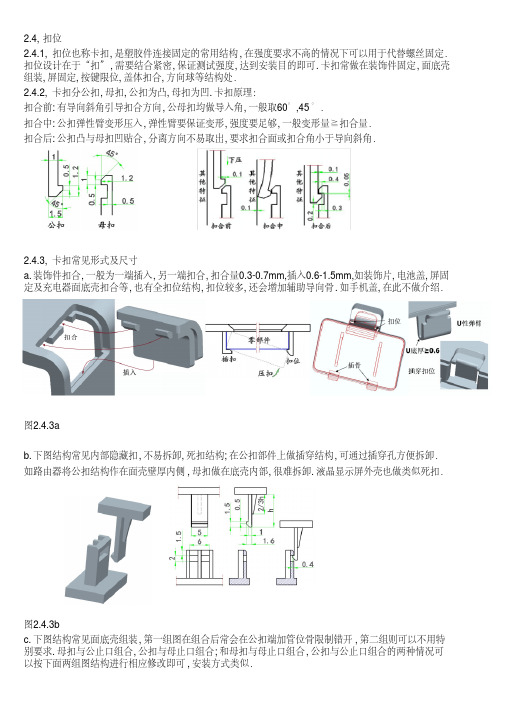
2.4,扣位2.4.1,扣位也称卡扣,是塑胶件连接固定的常用结构,在强度要求不高的情况下可以用于代替螺丝固定.扣位设计在于“扣”,需要结合紧密,保证测试强度,达到安装目的即可.卡扣常做在装饰件固定,面底壳组装,屏固定,按键限位,盖体扣合,方向球等结构处.2.4.2,卡扣分公扣,母扣,公扣为凸,母扣为凹.卡扣原理:扣合前:有导向斜角引导扣合方向,公母扣均做导入角,一般取60°,45°.扣合中:公扣弹性臂变形压入,弹性臂要保证变形,强度要足够,一般变形量≧扣合量.扣合后:公扣凸与母扣凹贴合,分离方向不易取出,要求扣合面或扣合角小于导向斜角.2.4.3,卡扣常见形式及尺寸a.装饰件扣合,一般为一端插入,另一端扣合,扣合量0.3-0.7mm,插入0.6-1.5mm,如装饰片,电池盖,屏固定及充电器面底壳扣合等,也有全扣位结构,扣位较多,还会增加辅助导向骨.如手机盖,在此不做介绍.图2.4.3ab.下图结构常见内部隐藏扣,不易拆卸,死扣结构;在公扣部件上做插穿结构,可通过插穿孔方便拆卸.如路由器将公扣结构作在面壳壁厚内侧,母扣做在底壳内部,很难拆卸.液晶显示屏外壳也做类似死扣.图2.4.3bc.下图结构常见面底壳组装,第一组图在组合后常会在公扣端加管位骨限制错开,第二组则可以不用特别要求.母扣与公止口组合,公扣与母止口组合;和母扣与母止口组合,公扣与公止口组合的两种情况可以按下面两组图结构进行相应修改即可,安装方式类似.图2.4.3cd.强脱扣位,由材质,韧性决定,材质越软可以强脱越多.一般单边强脱ABS:0.3mm,PC:0.5,PP:0.8, TPE:1.5等,强脱同所承载的壁厚韧性有关,韧性足可以稍微加大强脱深度.具体依结构实际情况定.图2.4.3de.手感扣,通常作在滑动结构上,如电池盖,旋转环等结构.一端为弹扣状,另一端为齿或圆柱.另一种不作弹扣,直接强扣强出,扣合量一般在0.3-0.8之间.F.其他常见扣:2.4.4,卡扣设计考虑要素卡扣需要考虑布局数量位置,安装形式,安装强度,注意事项:a.规则外形,布局按右图方形圆形卡扣分布,方形壳体宽度≤20,宽度不做扣位;20<壳体宽度≤50,作1至2个扣位;圆形壳体一般扣位会均布,如做防呆,可以将扣位稍微移动,保证扣位分布均匀.b.不规则外形,按装配方向选择安装形式,曲线边凸凹处易出现翘曲,受力错位脱开问题,常做扣位+管位骨结构;c.扣位位置尽量靠近转角,防止翘曲,并与螺钉配合组装;卡扣一般在保证强度情况下尽量作少.d.卡扣安装形式与正反扣,要考虑组装,拆卸的方便,考虑模具的制作;e.卡扣处注意防止缩水与熔接痕;f.卡扣斜顶运动空间不小于5,一般取值8,退位不能有干涉,最好为平面,;g.在卡扣上非安装边做R角,不要干涉扣合过程.h.扣位导正,特征:止口,管位骨等,止口,管位骨在上述有说明.。
塑胶产品结构设计案例

加强筋
• 一般的设计方法 : 平均壁厚*0.65~0.7
加强筋的基本设计
加强筋的缩水情况
第十一页,编辑于星期六:二十一点 三十七分。
拔模斜度
• 出模角的大少是没有一定的准则,多数是依照产 品的深度来决定。
• 一般的出模角为0.5°~1.0°。 • 在深入或附有织纹的产品上,出模角的要求是视乎
加防水槽
第二十九页,编辑于星期六:二十一点 三十七 分。
电池门
• 加上加强筋作强化作用。
第三十页,编辑于星期六:二十一点 三十七分。
• 如电池门的位置是在成品的中央,而且在电池门的四周没 有凹坑的时候。必须加上一凹形的手指位,作方便开启电 池门之用。
第三十一页,编辑于星期六:二十一点 三十七 分。
效果不受操作人员的操作情况所影响。
强度高 将塑料熔合起来,因此能产生出无内 应力的高强的接合。
不需夹紧 当工件离开机器后便告完成,不需 进行焊接后加工。
用途较广 可用来焊接那些不能用任何其它 黏合剂的物料。
安全性 由于不需使用化学物品,因此不会产 生化学中毒。
若要超声焊接头达致所需要强度及美观程度, 那么接头必须设计恰当,以及就要个别应用 情况及个别塑料性质来设计。
5<x≦10mm 10<x≦15mm
x≦5mm 5<x≦10mm 10<x≦15mm 15<x≦20mm 20<x≦25mm 25<x≦30mm
x≦5mm 5<x≦10mm 10<x≦15mm 15<x≦20mm 20<x≦25mm 25<x≦30mm
x≦5mm 5<x≦10mm 10<x≦15mm 15<x≦20mm 20<x≦25mm 25<x≦30mm 30<x≦35mm 35<x≦40mm
塑胶件的结构设计:卡扣篇(下)

塑胶件的结构设计:卡扣篇(下)卡扣设计的原则卡扣设计的最终目标是要实现两个零件之间的成功连接固定,要达到连接固定的效果,卡扣设计时需要从以下几方面进行考虑:连接可靠性、约束完整性和装配协调性,它们是卡扣连接成功的关键要求,其他要求还应该包括制造工艺的可行性、成本的高低等。
1. 连接可靠性连接可靠性最核心的一点就是卡扣需要保证有足够的保持强度,以下为悬臂梁卡扣保持力的一般公式:由以上公式可知,保持力Fr 跟Wb、E、Tb、Lb、μs、βe有关;其中Wb:卡扣的宽度;E:卡扣的弹性模量;Tb:卡扣的厚度;Lb:卡扣的长度;Y:卡扣保持面的深度;μs:卡扣的摩擦系数;βe:卡扣的保持面角度。
上面参数,除了弹性模量E、摩擦系数μs跟卡扣所用的材料有关外,其他参数跟卡扣的结构设计相关;通过增大Wb、Tb/Lb的比值、Y、βe都可以增强卡扣的保持强度。
1)增大Wb增大卡扣的宽度Wb,可以增大梁的刚度以及卡扣保持面与配合件的面积,理论上卡扣宽度越大,卡扣的保持强度就越大,但是实际设计中,考虑到制造与装配,常常通过设计多个小卡扣代替一个大卡扣。
卡扣的排布:卡扣应均匀设置在零件的四周,以均匀承受载荷,对于容易变形的地方(如零件的角落),可以考虑尽量让卡扣靠近这些地方。
整圈卡扣一般用在卡合量不大的零件或设计在较软材料上的零件上,常常采用强脱出模,比如常见的一些日化产品的瓶盖。
对于一些宽度较大的卡扣,为了提高母扣的强度,可以在大卡扣中设计两个小卡扣,如下图。
2)增大Tb/Lb的比值增大Tb或减小Lb都可以增大Tb/Lb的比值,实际上也是增大梁的刚度,但是Tb不宜过大,否则会引起外观不良,合理的方式是通过增加加强筋或者局部淘胶,如下图。
Lb也不宜过小,否则难于装配(虽然保持强度增大了),如果因空间限制,Lb过小的情况下,需适当减小Tb,但为了兼顾卡扣的强度,可以考虑在卡扣根部添加加强筋,如下图。
3)增大YY这里指的是卡扣保持面的深度,实际上卡扣的保持强度应该是跟卡合量有关,理论上Y值可以等于卡合量,但是在实际结构设计中,为了便于装配以及后续的调整,一般预留一定的间隙或余量,比如以下某卡扣的设计,前后都预留了0.2-0.5的间隙,预留空间方便后续通过改模增大Y值。
- 1、下载文档前请自行甄别文档内容的完整性,平台不提供额外的编辑、内容补充、找答案等附加服务。
- 2、"仅部分预览"的文档,不可在线预览部分如存在完整性等问题,可反馈申请退款(可完整预览的文档不适用该条件!)。
- 3、如文档侵犯您的权益,请联系客服反馈,我们会尽快为您处理(人工客服工作时间:9:00-18:30)。
支柱
• 支柱高度一般不要超过支柱直径的两倍半。
支柱靠近外壁的基本设计
支柱远离外壁的基本设计
Screw Æ Ø 2.0 mm Ø 2.3 mm Ø 2.6 mm Ø 3.0 mm Ø 3.5 mm
Ød Ø 1.7 mm Ø 1.9 mm Ø 2.3 mm Ø 2.6 mm Ø 3.0 mm
支柱的出模角一般会以支柱顶部的平面为 中性面,而且角度一般为0.5º~1.0º。如支 柱的高度超过15.0mm的时候,为加强支柱 的强度,可在支柱连上些加强筋,作结构 加强之用。
• POM 聚甲醛
– 用途:机械零件、齿轮、家电外壳
– 特性:耐磨、坚硬但脆弱,损坏时容易有利边出 现。
– 应用:多数用于胶齿轮、滑轮、一些需要传动, 承受大扭力或应力的地方。
• Nylon(尼龙,PA)
– 用途:齿轮、滑轮、纺织品
– 特性:坚韧、吸水、耐磨、吸震、耐热,但当 水份完全挥发后会变得脆弱。
3M螺丝
虚位设计(间隙)
一般零件与零件间的虚位(非活动 件) 零件与零件间的虚位(活动件) 电池门周边与壳身的虚位 电池门轴与壳身的擦穿坑虚位单边 需要与其它零件相配的擦穿坑 齿轮及滑轮与牙箱外壳的内壁
齿轮与齿轮之间的虚位(大齿轮半 径+小齿轮半径+虚位)=PCD 电池与电箱的骨位及电池门的虚位
– 一般最先选择的材料,壁厚通常为1, 1.2, 1.5, 2, 2.5, 3mm,视乎产品的大 小和功能而定。
• PP
– 因为比较软,而且基于缩水的问题,所以不能太厚,一般为1, 1.2, 1.5mm。 薄壁件壁厚0.6mm。
• PVC
– 因为多用由于外形,多是实心,所以限制不大。
• PS
– 1.5~5.0mm。
ØD Ø 4.3~4.4 mm Ø 4.7~4.8mm
Ø 5.0 mm Ø 5.5 mm Ø 6.0 mm
• 如支柱需要穿过PCB的时候,同样在支柱连上些加强筋,而且在加强 筋的顶部设计成平台形式,此可作承托PCB之用,而平台的平面与丝 筒项的平面必须要有2.0 ~ 3.0mm。
支柱套
• 跟据一般的安全规格标准,螺丝头必须收藏于不能触摸的 位置,所以高度必须有2.5mm或以上。由于加上支柱套后 会有锐边,所以在每一个支柱套上壳收螺丝的地方,必须 加上R1.0或以上的圆角。
• PC
– 1.0~4.0mm。
• POM
– 一般为1, 1.2, 1.5, 2, 2.5, 3mm视乎产品大小而定。
• Nylon
– 因为缩水率比较高,所以平均料厚和筋骨的比例可比较少。
• Kraton
– 因为多数用作摩打垫或不外露件,所以限制不大。
加强筋
• 一般的设计方法 : 平均壁厚*0.65~0.7
– 用途:玩具、日常用品、包装胶袋、瓶子
– 特性:有弹性、韧度强、延伸性大、但不可涂胶 水,工作温度-30℃~140℃ 。
– 应用:多数应用于一些因要接受跌落测试而拆件 的地方。
• PVC(聚氯乙烯)
– 用途:软喉管、硬喉管、软板、硬板、电线、玩 具
– 特性:柔软、坚韧而有弹性,工作温度-25℃~ 75℃ ;200 ℃ 易分解产生腐蚀、刺激性气体。
2.5mm
3mm
Rib thickness 1.1~1.2mm 1.4~1.5mm
1.8mm
2.1mm
Height of Rib (x) x≦5mm
5<x≦10mm 10<x≦15mm
x≦5mm 5<x≦10mm 10<x≦15mm 15<x≦20mm 20<x≦25mm 25<x≦30mm
x≦5mm 5<x≦10mm 10<x≦15mm 15<x≦20mm 20<x≦25mm 25<x≦30mm
– 应用:因为精准度比较难控制,所以大多用于 一些模数较大的齿轮
• Kraton(热塑性丁苯橡胶) • 用途:摩打垫,手工具把手 • 特性: 柔软,有弹性,韧度高,延伸性强。
• 设计上的应用:多数作为摩打垫,吸收摩 打震动,减低噪音。
不同材料的常用壁厚
• 一般不宜小于0.6~0.9mm,常选取2~4mm。 • ABS
加强筋的基本设计 加强筋的缩水情况
拔模斜度
• 出模角的大少是没有一定的准则,多数是依照 产品的深度来决定。
• 一般的出模角为0.5°~1.0°。 • 在深入或附有织纹的产品上,出模角的要求是
视乎织纹的深度而相应增加,一般为2°~3°。 • 一般的晒纹版上已清楚例出可供作参考之用的
要求出模角。
Wall thickness 1.5mm 2mm
– 特性:绝缘性好,硬而脆,无色透明,可染色, 耐热。发泡PS无法回;
• PC(聚碳酸酯)
– 用途:车辆前后灯、仪表板、冰箱抽屉、搅拌 机、网线水晶插头、一次性医疗器械;
– 特性:无色透明、无毒、可染色、抗冲击、耐 磨、耐腐蚀、抑制细菌、阻燃,耐高温和耐低 温(-60~120℃);
– 应用:多数应用于透明零件,代替玻璃。
x≦5mm 5<x≦10mm 10<x≦15mm 15<x≦20mm 20<x≦25mm 25<x≦30mm 30<x≦35mm 35<x≦40mm
Draft Angle 1.0°~1.5° 0.5°~0.8°
0.5° 1.0°~1.5° 1.0°~1.5° 0.5°~1.0°
0.8° 0.5° 0.5° 1.0°~1.5° 0.5°~1.0° 0.5°~1.0° 0.5° 0.5° 0.5° 1.0° 1.0° 1.0° 1.0° 0.5°~1.0° 0.5°~1.0° 0.5°~0.8° 0.5°~0.8°
– PVC电线、电缆在制造、使用及废弃处理时, 都会产生大量的二恶英、氯氢酸、铅等有害物 质。
– 设计上的应用:多数用于玩具,或一些需要避震 或吸震的地方。
• PS(聚苯乙烯)
– 用途:绝缘透明件、装饰件、化学仪器、光学仪 器;发泡PS(保丽龙),建筑隔音、隔热层, 冰箱保温层,一次性饭盒,头盔缓冲层;
塑料件结构设计总结
不同材料的特性
• ABS(丙烯腈-苯乙烯-丁二烯共聚物)
– 用途:玩具、机壳、日常用品、汽车配件(仪表 板、工具舱门、车轮盖、反光镜盒)、家电外壳;
– 特性:坚硬、不易碎、可涂胶水,工作温度50~+70℃,可燃烧,损坏时可能有利边出现。多 数应用于玩具外壳或不用受力的零件。
• PP(聚丙烯)