阳极氧化完整实用工艺流程
阳极氧化处理工艺

阳极氧化处理工艺引言阳极氧化(Anodic Oxidation)是一种常见的金属表面处理工艺,主要应用于铝和其合金的表面处理。
它通过在酸性电解液中通电的方式,使金属表面形成一层致密、均匀并具有一定硬度的氧化膜,提高金属材料表面的耐腐蚀性、硬度和装饰性。
本文将详细介绍阳极氧化处理工艺及其工艺流程。
工艺流程阳极氧化处理工艺主要包括以下几个步骤:1.表面清洗:将待处理的铝材表面进行清洗,去除表面的油污、灰尘及其他杂质,以确保处理后的氧化膜质量。
2.阳极化:将清洗后的铝材置于电解液中,通过通电的方式使其成为阳极,与电解液发生化学反应,形成氧化膜。
3.色彩处理(可选):根据需求,能够对氧化膜进行着色处理,以增加金属表面的装饰性。
4.封闭处理:通过热水封闭或冷水封闭的方式,对氧化膜进行涂层封闭,提高其耐腐蚀性和硬度。
电解液的选择阳极氧化处理工艺的核心是选取合适的电解液。
电解液的化学成分和操作参数对于形成的氧化膜的性质和质量有着重要影响。
常用的电解液有硫酸、草酸和磷酸等。
1.硫酸电解液:常用于工业生产中,具有成本低、氧化速度快、成膜厚度均匀等特点。
但硫酸电解液对操作要求高,容易腐蚀设备和制造环境。
2.草酸电解液:具有氧化速度适中、成膜均匀、可着色性好等优势。
但草酸电解液的操作要求较为严格,需要控制好温度和草酸浓度等参数。
3.磷酸电解液:具有成本低、韧性好、耐腐蚀性强的特点,通常应用于航空航天等高要求的领域。
根据不同的实际需求,选取合适的电解液进行阳极氧化处理是十分重要的。
影响因素阳极氧化处理的质量和效果受到许多因素的影响。
以下是影响因素的一些常见例子:1.温度:电解液的温度对氧化速度和氧化膜的性质有很大影响。
一般来说,温度越高,氧化速度越快,但同时也可能导致膜层厚度不均匀。
2.电流密度:电流密度决定了电解液中的氧化产物的生成速率。
如果电流密度过高,可能会导致氧化膜过厚,加剧表面的缺陷。
3.电解液浓度:电解液浓度与氧化速度和氧化膜厚度密切相关。
阳极氧化完整工艺流程
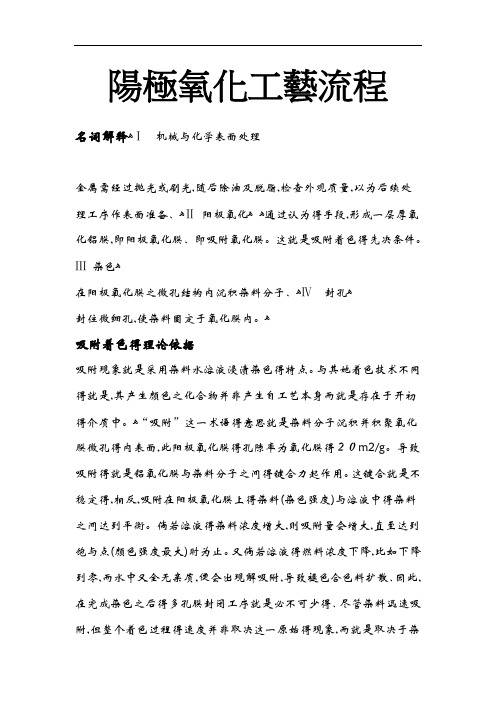
陽極氧化工藝流程名词解释ﻫⅠ机械与化学表面处理金属需经过抛光或刷光,随后除油及脱脂,检查外观质量,以为后续处ﻫ通过认为得手段,形成一层厚氧理工序作表面准备、ﻫⅡ阳极氧化ﻫ化铝膜,即阳极氧化膜、即吸附氧化膜。
这就是吸附着色得先决条件。
Ⅲ染色ﻫ在阳极氧化膜之微孔结构内沉积染料分子、ﻫⅣ封孔ﻫ封住微细孔,使染料固定于氧化膜内。
ﻫ吸附着色得理论依据吸附现象就是采用染料水溶液浸渍染色得特点。
与其她着色技术不同得就是,其产生颜色之化合物并非产生自工艺本身而就是存在于开初得介质中。
ﻫ“吸附”这一术语得意思就是染料分子沉积并积聚氧化膜微孔得内表面,此阳极氧化膜得孔隙率为氧化膜得20m2/g。
导致吸附得就是铝氧化膜与染料分子之间得键合力起作用。
这键合就是不稳定得,相反,吸附在阳极氧化膜上得染料(染色强度)与溶液中得染料之间达到平衡。
倘若溶液得染料浓度增大,则吸附量会增大,直至达到饱与点(颜色强度最大)时为止。
又倘若溶液得燃料浓度下降,比如下降到零,而水中又全无亲质,便会出现解吸附,导致褪色合色料扩散、因此,在完成染色之后得多孔膜封闭工序就是必不可少得、尽管染料迅速吸附,但整个着色过程得速度并非取决这一原始得现象,而就是取决于染料分子随后怎样进入狭窄得微孔内、这一过程以略低得速率进行。
分子得直径平均为0.0025µm,而用硫酸直流氧化法制备得阳极氧化膜得微孔平均直径为0.02µm。
ﻫﻫ***********************************************************ﻫ铝得级别与铝得阳极氧化ﻫ铝材得物理成分以及级别就是吸附着色就是否成功得重要因素、铝材分为高纯铝、纯铝与合金铝。
高纯铝只含不超过痕量(不超过0。
05%,依次排级)得亲质金属;纯铝得亲质金属含量不超过1%。
ﻫ由于铝本身得强度不足以应付各种用途,因而相当多就是与其她金属形成合金,主要得就是镁、锌、锰、铜等。
阳极氧化处理工艺过程及注意事项
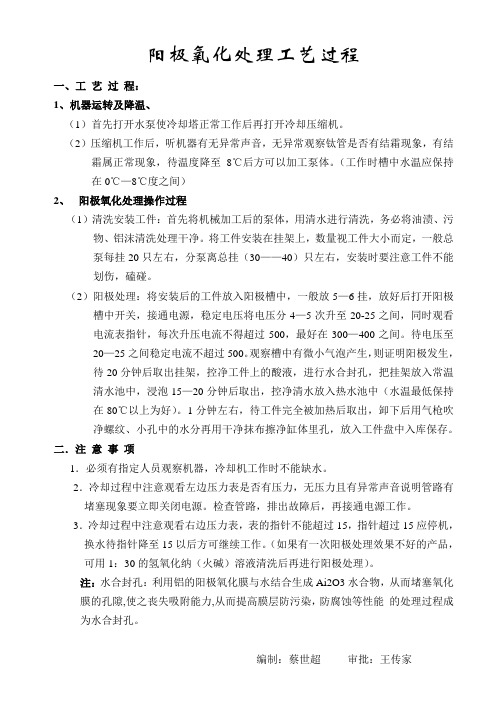
阳极氧化处理工艺过程一、工艺过程:1、机器运转及降温、(1)首先打开水泵使冷却塔正常工作后再打开冷却压缩机。
(2)压缩机工作后,听机器有无异常声音,无异常观察钛管是否有结霜现象,有结霜属正常现象,待温度降至8℃后方可以加工泵体。
(工作时槽中水温应保持在0℃—8℃度之间)2、阳极氧化处理操作过程(1)清洗安装工件:首先将机械加工后的泵体,用清水进行清洗,务必将油渍、污物、铝沫清洗处理干净。
将工件安装在挂架上,数量视工件大小而定,一般总泵每挂20只左右,分泵离总挂(30——40)只左右,安装时要注意工件不能划伤,磕碰。
(2)阳极处理:将安装后的工件放入阳极槽中,一般放5—6挂,放好后打开阳极槽中开关,接通电源,稳定电压将电压分4—5次升至20-25之间,同时观看电流表指针,每次升压电流不得超过500,最好在300—400之间。
待电压至20—25之间稳定电流不超过500。
观察槽中有微小气泡产生,则证明阳极发生,待20分钟后取出挂架,控净工件上的酸液,进行水合封孔,把挂架放入常温清水池中,浸泡15—20分钟后取出,控净清水放入热水池中(水温最低保持在80℃以上为好)。
1分钟左右,待工件完全被加热后取出,卸下后用气枪吹净螺纹、小孔中的水分再用干净抹布擦净缸体里孔,放入工件盘中入库保存。
二.注意事项1.必须有指定人员观察机器,冷却机工作时不能缺水。
2.冷却过程中注意观看左边压力表是否有压力,无压力且有异常声音说明管路有堵塞现象要立即关闭电源。
检查管路,排出故障后,再接通电源工作。
3.冷却过程中注意观看右边压力表,表的指针不能超过15,指针超过15应停机,换水待指针降至15以后方可继续工作。
(如果有一次阳极处理效果不好的产品,可用1:30的氢氧化纳(火碱)溶液清洗后再进行阳极处理)。
注:水合封孔:利用铝的阳极氧化膜与水结合生成Ai2O3水合物,从而堵塞氧化膜的孔隙,使之丧失吸附能力,从而提高膜层防污染,防腐蚀等性能的处理过程成为水合封孔。
阳极氧化工艺流程图
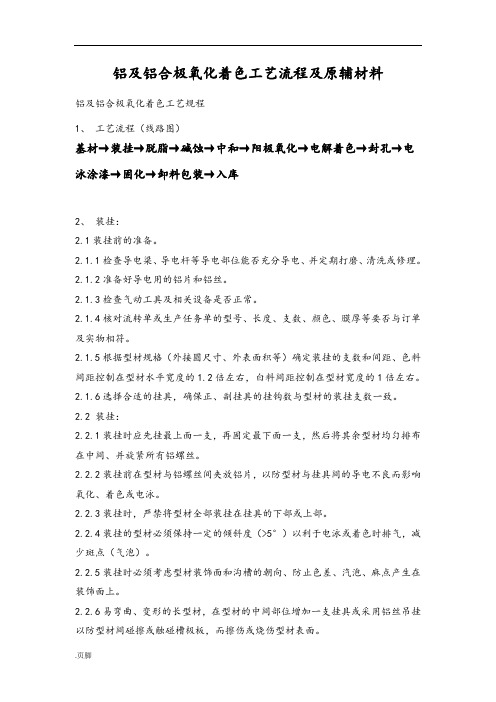
铝及铝合极氧化着色工艺流程及原辅材料铝及铝合极氧化着色工艺规程1、工艺流程(线路图)基材→装挂→脱脂→碱蚀→中和→阳极氧化→电解着色→封孔→电泳涂漆→固化→卸料包装→入库2、装挂:2.1装挂前的准备。
2.1.1检查导电梁、导电杆等导电部位能否充分导电、并定期打磨、清洗或修理。
2.1.2准备好导电用的铝片和铝丝。
2.1.3检查气动工具及相关设备是否正常。
2.1.4核对流转单或生产任务单的型号、长度、支数、颜色、膜厚等要否与订单及实物相符。
2.1.5根据型材规格(外接圆尺寸、外表面积等)确定装挂的支数和间距、色料间距控制在型材水平宽度的1.2倍左右,白料间距控制在型材宽度的1倍左右。
2.1.6选择合适的挂具,确保正、副挂具的挂钩数与型材的装挂支数一致。
2.2 装挂:2.2.1装挂时应先挂最上面一支,再固定最下面一支,然后将其余型材均匀排布在中间、并旋紧所有铝螺丝。
2.2.2装挂前在型材与铝螺丝间夹放铝片,以防型材与挂具间的导电不良而影响氧化、着色或电泳。
2.2.3装挂时,严禁将型材全部装挂在挂具的下部或上部。
2.2.4装挂的型材必须保持一定的倾斜度(>5°)以利于电泳或着色时排气,减少斑点(气泡)。
2.2.5装挂时必须考虑型材装饰面和沟槽的朝向、防止色差、汽泡、麻点产生在装饰面上。
2.2.6易弯曲、变形的长型材,在型材的中间部位增加一支挂具或采用铝丝吊挂以防型材间碰擦或触碰槽极板,而擦伤或烧伤型材表面。
2.2.7选用副杆挂具时,优先选用插杆,采用铝丝绑扎时,一定要间隔均匀,露头应小于25mm。
2.2.8截面大小、形状悬殊的型材严禁装挂在同一排上。
2.2.9装挂或搬运型材,必须戴好干净手套,轻拿轻放、爱护、防护好型材表面,严禁野蛮操作。
2.2.10装挂或搬运型材时必须加强自检和互检,不合格的型材严禁装挂,表面沾有油污或铝屑(毛刺)的型材必须采取适当的措施处理干净。
2.2.11剔除不合格型材后,必须按订单支数及时补足。
阳极氧化的工艺流程
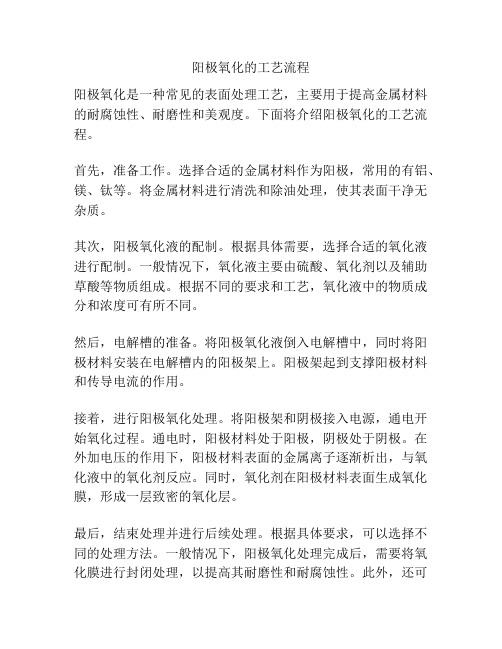
阳极氧化的工艺流程
阳极氧化是一种常见的表面处理工艺,主要用于提高金属材料的耐腐蚀性、耐磨性和美观度。
下面将介绍阳极氧化的工艺流程。
首先,准备工作。
选择合适的金属材料作为阳极,常用的有铝、镁、钛等。
将金属材料进行清洗和除油处理,使其表面干净无杂质。
其次,阳极氧化液的配制。
根据具体需要,选择合适的氧化液进行配制。
一般情况下,氧化液主要由硫酸、氧化剂以及辅助草酸等物质组成。
根据不同的要求和工艺,氧化液中的物质成分和浓度可有所不同。
然后,电解槽的准备。
将阳极氧化液倒入电解槽中,同时将阳极材料安装在电解槽内的阳极架上。
阳极架起到支撑阳极材料和传导电流的作用。
接着,进行阳极氧化处理。
将阳极架和阴极接入电源,通电开始氧化过程。
通电时,阳极材料处于阳极,阴极处于阴极。
在外加电压的作用下,阳极材料表面的金属离子逐渐析出,与氧化液中的氧化剂反应。
同时,氧化剂在阳极材料表面生成氧化膜,形成一层致密的氧化层。
最后,结束处理并进行后续处理。
根据具体要求,可以选择不同的处理方法。
一般情况下,阳极氧化处理完成后,需要将氧化膜进行封闭处理,以提高其耐磨性和耐腐蚀性。
此外,还可
以进行染色和封闭处理,以增加材料的美观度和耐候性。
总结来说,阳极氧化的工艺流程可以简单概括为准备工作、阳极氧化液的配制、电解槽的准备、阳极氧化处理和后续处理。
通过这一工艺流程,可以获得具有较高耐蚀性和耐磨性的氧化层,提高材料的使用寿命和美观度。
阳极氧化工艺广泛应用于各个行业,如建筑、汽车、航空等领域。
阳极氧化工艺流程

阳极氧化工艺流程阳极氧化工艺流程悬赏分:10 - 解决时间:2007-11-24 21:06请告诉我一下阳极氧化工艺流程,1,需要知道它的原理和 2,氧化后的产品特征,3,工艺流程,4,每一个流程的处理方法和每一个流程的原理和每一个流程的时间。
最重要的,怎样来看阳极氧化后的质量好坏,怎样检验,哪们兄弟正确回复后,我愿意也会追加30-50分,随便乱找的不算~问题补充:Why no person answer this question?、、提问者: xy791123 - 二级最佳答案阳极氧化已经慢慢淘汰了,现在已经升级到了微弧氧化,可以做镁和铝合金产品,原理都是一样,通过有机溶剂做为介质,采用尖端放电,在产品表面生成保护膜,类似於陶瓷层。
外观除了一些起跑引起的颜色问题,是很难看出来的,主要通过,盐雾、耐摩擦、电导率、电击穿等测试来判定膜层的好坏。
工艺:除油--水洗--水洗--阳极反应--水洗--封闭--烘烤铝制品阳极氧化工艺流程2009-06-10 08:19铝制品阳极氧化通用的工艺流程如下:铝工件?上挂具?脱脂?水洗?碱蚀?水洗?出光?水洗?阳极氧化?水洗?去离子水洗?染色或电解着色?水洗?去离子水洗?封闭?水洗?下挂具对于要求高光亮度的铝制品,可采用如下的工艺流程:铝工件?机械抛光?脱脂?水洗?中和?水洗?化学或电化学抛光?水洗?阳极氧化?水洗?去离子水洗?染色或电解着色?水洗?去离子水洗?封闭?水洗?机械光亮铝及铝合金阳极氧化着色工艺流程(图) 标签:铝合金阳极氧化着色工艺流程时间:2008-12-25 10:08:41 点击:2710 回帖:5 上一篇:成功领袖10大思维方式下一篇:业务员是什么意思呀,and pump installation engineering construction and acceptance specification for lifting 6 HG20201-2000 construction installation engineering construction standard 7, HG ... Pressure gauges, using an installed spark arrestor for acetylene cylinders, illegal carrying, using gas cylinders, each operator fined 20 Yuan. Gas bottle without the hot sun exposure measures, responsibilities of team a fine of 50 Yuan.(7) at height and the opening and provisional protective measures have been taken, the responsible unit fined 200 Yuan, construction person in charge a fine of 50 Yuan. (8) no permit to work and the job in accordance with the provisions, on the job unit fined 300 yuan, the unit will charge a fine of 100 Yuan. 7.5.3 accident penalties (1) injuries fatalities directly punished 1~2 million. Direct responsibility for the accident and have the corresponding responsibility of leadership, such as concerning administrative sanctions, should be brought to the company or the relevant Department. (2) personal injury accident occurred, the direct punishment 0.5-10,000 yuan, responsible for the direct responsibility for the accident and the responsibility of leadership, such as concerning administrative sanctions should be dealt with by thepersonnel Department of the company. (3) personal injury accident occurs, the direct punishment 500-1000, who is directly responsible for the铝及铝合金阳极氧化着色工艺规程1、主题内容与适用范围:本规程规定了铝及铝合金阳极氧化、着色、电泳生产的工艺和操作的技术要求及规范。
阳极氧化完整工艺流程

陽極氧化工藝流程名词解释Ⅰ机械与化学表面处理金属需经过抛光或刷光,随后除油及脱脂,检查外观质量,以为后续处理工序作表面准备。
Ⅱ阳极氧化通过认为的手段,形成一层厚氧化铝膜,即阳极氧化膜。
即吸附氧化膜。
这是吸附着色的先决条件.Ⅲ染色在阳极氧化膜之微孔结构内沉积染料分子。
Ⅳ封孔封住微细孔,使染料固定于氧化膜内。
吸附着色的理论依据吸附现象是采用染料水溶液浸渍染色的特点。
与其他着色技术不同的是,其产生颜色之化合物并非产生自工艺本身而是存在于开初的介质中。
“吸附"这一术语的意思是染料分子沉积并积聚氧化膜微孔的内表面,此阳极氧化膜的孔隙率为氧化膜的20m2/g。
导致吸附的是铝氧化膜与染料分子之间的键合力起作用。
这键合是不稳定的,相反,吸附在阳极氧化膜上的染料(染色强度)与溶液中的染料之间达到平衡。
倘若溶液的染料浓度增大,则吸附量会增大,直至达到饱和点(颜色强度最大)时为止.又倘若溶液的燃料浓度下降,比如下降到零,而水中又全无亲质,便会出现解吸附,导致褪色合色料扩散。
因此,在完成染色之后的多孔膜封闭工序是必不可少的。
尽管染料迅速吸附,但整个着色过程的速度并非取决这一原始的现象,而是取决于染料分子随后怎样进入狭窄的微孔内。
这一过程以略低的速率进行.分子的直径平均为0。
0025µ;m,而用硫酸直流氧化法制备的阳极氧化膜的微孔平均直径为0.02µm.***********************************************************铝的级别和铝的阳极氧化铝材的物理成分以及级别是吸附着色是否成功的重要因素。
铝材分为高纯铝、纯铝和合金铝。
高纯铝只含不超过痕量(不超过0.05%,依次排级)的亲质金属;纯铝的亲质金属含量不超过1%。
由于铝本身的强度不足以应付各种用途,因而相当多是与其他金属形成合金,主要的是镁、锌、锰、铜等。
合金中的这些成分越高。
耐机械磨损性便越强,但对装饰性着色的适应性则相对的越差。
阳极氧化完整工艺流程

陽極氧化工藝流程名词解释Ⅰ机械与化学表面处理金属需经过抛光或刷光,随后除油及脱脂,检查外观质量,以为后续处理工序作表面准备。
Ⅱ阳极氧化通过认为的手段,形成一层厚氧化铝膜,即阳极氧化膜。
即吸附氧化膜。
这是吸附着色的先决条件。
Ⅲ染色在阳极氧化膜之微孔结构内沉积染料分子。
Ⅳ封孔封住微细孔,使染料固定于氧化膜内。
吸附着色的理论依据吸附现象是采用染料水溶液浸渍染色的特点。
与其他着色技术不同的是,其产生颜色之化合物并非产生自工艺本身而是存在于开初的介质中。
“吸附”这一术语的意思是染料分子沉积并积聚氧化膜微孔的内表面,此阳极氧化膜的孔隙率为氧化膜的20m2/g。
导致吸附的是铝氧化膜与染料分子之间的键合力起作用。
这键合是不稳定的,相反,吸附在阳极氧化膜上的染料(染色强度)与溶液中的染料之间达到平衡。
倘若溶液的染料浓度增大,则吸附量会增大,直至达到饱和点(颜色强度最大)时为止。
又倘若溶液的燃料浓度下降,比如下降到零,而水中又全无亲质,便会出现解吸附,导致褪色合色料扩散。
因此,在完成染色之后的多孔膜封闭工序是必不可少的。
尽管染料迅速吸附,但整个着色过程的速度并非取决这一原始的现象,而是取决于染料分子随后怎样进入狭窄的微孔内。
这一过程以略低的速率进行。
分子的直径平均为0.0025µm,而用硫酸直流氧化法制备的阳极氧化膜的微孔平均直径为0.02µm。
***********************************************************铝的级别和铝的阳极氧化铝材的物理成分以及级别是吸附着色是否成功的重要因素。
铝材分为高纯铝、纯铝和合金铝。
高纯铝只含不超过痕量(不超过0.05%,依次排级)的亲质金属;纯铝的亲质金属含量不超过1%。
由于铝本身的强度不足以应付各种用途,因而相当多是与其他金属形成合金,主要的是镁、锌、锰、铜等。
合金中的这些成分越高。
耐机械磨损性便越强,但对装饰性着色的适应性则相对的越差。
阳极氧化工艺流程图

阳极氧化工艺流程阳极氧化已经慢慢淘汰了,现在已经升级到了微弧氧化,可以做镁和铝合金产品,原理都是一样,通过有机溶剂做为介质,采用尖端放电,在产品表面生成保护膜,类似於陶瓷层。
外观除了一些起跑引起的颜色问题,是很难看出来的,主要通过,盐雾、耐摩擦、电导率、电击穿等测试来判定膜层的好坏。
工艺:除油--水洗--水洗--阳极反应--水洗--封闭--烘烤铝制品阳极氧化工艺流程铝制品阳极氧化通用的工艺流程如下:铝工件→上挂具→脱脂→水洗→碱蚀→水洗→出光→水洗→阳极氧化→水洗→去离子水洗→染色或电解着色→水洗→去离子水洗→封闭→水洗→下挂具对于要求高光亮度的铝制品,可采用如下的工艺流程:铝工件→机械抛光→脱脂→水洗→中和→水洗→化学或电化学抛光→水洗→阳极氧化→水洗→去离子水洗→染色或电解着色→水洗→去离子水洗→封闭→水洗→机械光亮铝及铝合金阳极氧化着色工艺流程(图) 铝及铝合金阳极氧化着色工艺规程 1、主题内容与适用范围:本规程规定了铝及铝合金阳极氧化、着色、电泳生产的工艺和操作的技术要求及规范。
2、工艺流程(线路图)基材→装挂→脱脂→碱蚀→中和→阳极氧化→电解着色→封孔→电泳涂漆→固化→卸料包装→入库 3、装挂: 3.1装挂前的准备。
3.1.1检查导电梁、导电杆等导电部位能否充分导电、并定期打磨、清洗或修理。
3.1.2准备好导电用的铝片和铝丝。
3.1.3检查气动工具及相关设备是否正常。
3.1.4核对流转单或生产任务单的型号、长度、支数、颜色、膜厚等要求是否与订单及实物相符。
3.1.5根据型材规格(外接圆尺寸、外表面积等)确定装挂的支数和间距、色料间距控制在型材水平宽度的1.2倍左右,白料间距控制在型材宽度的1倍左右。
3.1.6选择合适的挂具,确保正、副挂具的挂钩数与型材的装挂支数一致。
3.2 装挂: 3.2.1装挂时应先挂最上面一支,再固定最下面一支,然后将其余型材均匀排布在中间、并旋紧所有铝螺丝。
阳极氧化工艺流程

阳极氧化工艺流程阳极氧化是一种常用的表面处理工艺,通过电化学的方法,在金属表面形成一层氧化膜,以提高金属的耐腐蚀性、硬度和装饰性。
这种工艺广泛应用于铝、镁、钛等金属材料的表面处理中,下面将详细介绍阳极氧化的工艺流程。
1. 预处理在进行阳极氧化之前,首先需要对金属材料进行预处理。
通常包括去油、除锈、除氧化膜等步骤,以确保金属表面干净、光滑,有利于氧化膜的形成和质量。
2. 清洗清洗是预处理的重要环节,主要是利用碱性或酸性溶液清洗金属表面,去除表面的杂质和氧化物。
清洗后,要进行充分的水洗,确保金属表面不含任何清洗剂残留。
3. 阳极处理将经过预处理和清洗的金属材料作为阳极,放置在含有适当添加剂的电解液中。
电解液通常是硫酸、氧化铝或硫酸铝等,添加剂包括氟化物、硅酸盐等。
在一定的电压和电流密度下,金属表面将开始氧化,形成氧化膜。
4. 形成氧化膜在阳极处理的过程中,金属表面会逐渐形成氧化膜。
氧化膜的厚度和颜色取决于电解液的成分、温度、电压和电流密度等因素。
一般来说,较厚的氧化膜具有较好的耐腐蚀性和硬度,而颜色则可以根据客户的需求进行定制。
5. 密封形成氧化膜后,需要进行密封处理,以提高氧化膜的密封性和耐腐蚀性。
密封处理通常采用热水、热蒸汽或镉盐溶液浸渍等方法。
通过密封处理,可以使氧化膜更加坚固和耐用。
6. 检测最后,需要对阳极氧化后的金属材料进行检测,以确保氧化膜的质量符合要求。
常用的检测方法包括厚度测量、耐蚀性测试、外观检查等。
只有经过严格的检测合格后,才能进行后续的加工和使用。
总结阳极氧化是一种重要的金属表面处理工艺,通过预处理、清洗、阳极处理、形成氧化膜、密封和检测等步骤,可以在金属表面形成一层坚固耐用的氧化膜,提高金属的耐腐蚀性、硬度和装饰性。
这种工艺广泛应用于航空航天、汽车、电子、建筑等领域,对于提高产品质量和性能具有重要意义。
阳极氧化完整工艺流程图
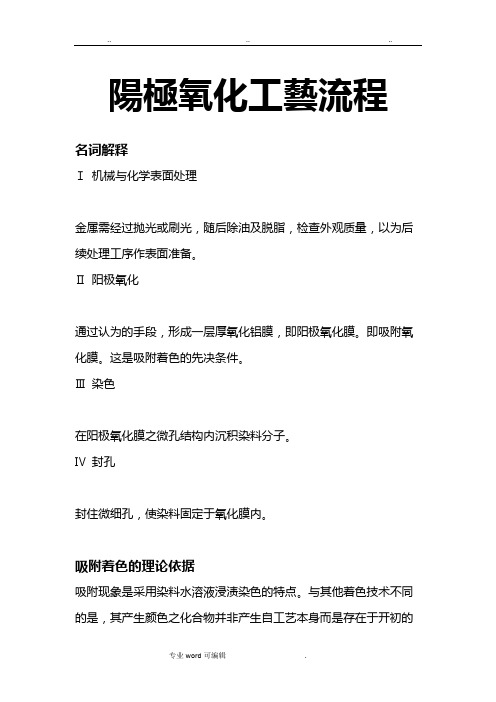
陽極氧化工藝流程名词解释Ⅰ 机械与化学表面处理金属需经过抛光或刷光,随后除油及脱脂,检查外观质量,以为后续处理工序作表面准备。
Ⅱ 阳极氧化通过认为的手段,形成一层厚氧化铝膜,即阳极氧化膜。
即吸附氧化膜。
这是吸附着色的先决条件。
Ⅲ 染色在阳极氧化膜之微孔结构内沉积染料分子。
Ⅳ 封孔封住微细孔,使染料固定于氧化膜内。
吸附着色的理论依据吸附现象是采用染料水溶液浸渍染色的特点。
与其他着色技术不同的是,其产生颜色之化合物并非产生自工艺本身而是存在于开初的介质中。
“吸附”这一术语的意思是染料分子沉积并积聚氧化膜微孔的内表面,此阳极氧化膜的孔隙率为氧化膜的20m2/g。
导致吸附的是铝氧化膜与染料分子之间的键合力起作用。
这键合是不稳定的,相反,吸附在阳极氧化膜上的染料(染色强度)与溶液中的染料之间达到平衡。
倘若溶液的染料浓度增大,则吸附量会增大,直至达到饱和点(颜色强度最大)时为止。
又倘若溶液的燃料浓度下降,比如下降到零,而水中又全无亲质,便会出现解吸附,导致褪色合色料扩散。
因此,在完成染色之后的多孔膜封闭工序是必不可少的。
尽管染料迅速吸附,但整个着色过程的速度并非取决这一原始的现象,而是取决于染料分子随后怎样进入狭窄的微孔内。
这一过程以略低的速率进行。
分子的直径平均为0.0025µm,而用硫酸直流氧化法制备的阳极氧化膜的微孔平均直径为0.02µm。
***********************************************************铝的级别和铝的阳极氧化铝材的物理成分以及级别是吸附着色是否成功的重要因素。
铝材分为高纯铝、纯铝和合金铝。
高纯铝只含不超过痕量(不超过0.05%,依次排级)的亲质金属;纯铝的亲质金属含量不超过1%。
由于铝本身的强度不足以应付各种用途,因而相当多是与其他金属形成合金,主要的是镁、锌、锰、铜等。
合金中的这些成分越高。
阳极工艺流程

阳极工艺流程阳极工艺是一种用于金属表面处理的工艺,主要是通过阳极氧化的方式,使金属表面形成一层氧化膜,从而提高金属的耐腐蚀性、硬度和耐磨性。
阳极工艺在航空航天、汽车制造、建筑等领域有着广泛的应用。
下面将详细介绍阳极工艺的流程。
1. 原料准备阳极工艺的原料主要包括金属制品、酸性溶液、阳极氧化设备等。
在进行阳极氧化处理之前,首先需要对金属制品进行清洗和除油处理,以确保金属表面干净无油污。
2. 阳极氧化设备准备阳极氧化设备主要包括电解槽、阳极、阴极、电源等。
在进行阳极氧化处理之前,需要对设备进行检查和调试,确保设备正常运行。
3. 阳极氧化处理首先将清洁的金属制品放入电解槽中,然后将阳极氧化设备连接电源,调节电流和电压,使金属制品成为阴极,阳极为铝板或铅板。
在酸性溶液中,通过电解作用,金属表面会形成一层氧化膜。
氧化膜的厚度和颜色可以通过控制电流密度和处理时间来调节。
4. 封孔处理经过阳极氧化处理后,金属表面会形成微孔,为了提高氧化膜的耐蚀性,需要进行封孔处理。
封孔处理通常是将金属制品浸入热水或热镁盐溶液中,使氧化膜中的微孔得到封闭。
5. 清洗和干燥经过封孔处理后,金属制品需要进行清洗和干燥,以去除表面的残留溶液和水分。
6. 检验最后,对经过阳极氧化处理的金属制品进行检验,包括外观检查、厚度测量、耐蚀性测试等,确保产品符合要求。
通过以上流程,金属制品经过阳极氧化处理后,表面会形成一层坚固耐用的氧化膜,从而提高了金属的耐蚀性、硬度和耐磨性,延长了使用寿命。
阳极工艺不仅可以改善金属制品的性能,还可以美化产品外观,因此在各个领域都有着广泛的应用。
阳极氧化工艺流程图

铝及铝合极氧化着色工艺流程及原辅材料铝及铝合极氧化着色工艺规程1、工艺流程(线路图)基材→装挂→脱脂→碱蚀→中和→阳极氧化→电解着色→封孔→电泳涂漆→固化→卸料包装→入库2、装挂:2.1装挂前的准备。
2.1.1检查导电梁、导电杆等导电部位能否充分导电、并定期打磨、清洗或修理。
2.1.2准备好导电用的铝片和铝丝。
2.1.3检查气动工具及相关设备是否正常。
2.1.4核对流转单或生产任务单的型号、长度、支数、颜色、膜厚等要否与订单及实物相符。
2.1.5根据型材规格(外接圆尺寸、外表面积等)确定装挂的支数和间距、色料间距控制在型材水平宽度的1.2倍左右,白料间距控制在型材宽度的1倍左右。
2.1.6选择合适的挂具,确保正、副挂具的挂钩数与型材的装挂支数一致。
2.2 装挂:2.2.1装挂时应先挂最上面一支,再固定最下面一支,然后将其余型材均匀排布在中间、并旋紧所有铝螺丝。
2.2.2装挂前在型材与铝螺丝间夹放铝片,以防型材与挂具间的导电不良而影响氧化、着色或电泳。
2.2.3装挂时,严禁将型材全部装挂在挂具的下部或上部。
2.2.4装挂的型材必须保持一定的倾斜度(>5°)以利于电泳或着色时排气,减少斑点(气泡)。
2.2.5装挂时必须考虑型材装饰面和沟槽的朝向、防止色差、汽泡、麻点产生在装饰面上。
2.2.6易弯曲、变形的长型材,在型材的中间部位增加一支挂具或采用铝丝吊挂以防型材间碰擦或触碰槽极板,而擦伤或烧伤型材表面。
2.2.7选用副杆挂具时,优先选用插杆,采用铝丝绑扎时,一定要间隔均匀,露头应小于25mm。
2.2.8截面大小、形状悬殊的型材严禁装挂在同一排上。
2.2.9装挂或搬运型材,必须戴好干净手套,轻拿轻放、爱护、防护好型材表面,严禁野蛮操作。
2.2.10装挂或搬运型材时必须加强自检和互检,不合格的型材严禁装挂,表面沾有油污或铝屑(毛刺)的型材必须采取适当的措施处理干净。
2.2.11剔除不合格型材后,必须按订单支数及时补足。
阳极氧化工艺技术详解

阳极化阳极氧化工艺流程为:表面整平——除油——浸蚀或抛光——阳极氧化——着色处理——封闭处理——干燥(三个主要过程:阳极氧化、着色、封孔),本色氧化就是少了着色处理这一过程,阳极氧化后直接封孔。
1.阳极氧化(1)硫酸阳极化(5-20um)物色氧化膜,易于染色,硬度高,是铝和铝合金主要的防护和装饰方法,工艺简单,操作方便,应用最广。
(2)铬酸阳极化(2-5um)氧化膜不透明,未浅灰色或乳白色,孔隙率低,所以零件仍能保持原来的精度和表面粗糙度,丐工艺适用于精密零件,膜比较薄。
(3)草酸阳极化(8-20um,最厚达60um)草酸阳极化易于制取较厚膜层,氧化膜硬度高,孔隙率低,耐蚀性高,有良好的电绝缘性。
但成本较高,是硫酸阳极化的3-5倍,一般用于特殊要求的表面,如制作电器绝缘保护层、日用品的表面装饰。
(4)硬质阳极化(又称厚膜氧化,250-300um)硬度很高,一般为400-600HV,电流密度为普通阳极氧化的2-3倍。
(5)瓷质阳极化(6-20um)氧化膜具有不透明的灰色外观,类似瓷釉、搪瓷,也被称之为仿釉氧化膜。
一般不会改变零件的表面粗糙度,也不影响其尺寸精度,适用于仪器、仪表等精密零件和日用品的表面防护和装饰。
2.阳极氧化膜染色(1)整体着色法采用特定成分的铝合金或在特殊的电解液中阳极氧化时,获得氧化膜的同时,而着上不同颜色,也成自然着色法。
(阳极氧化和染色同时进行)能耗较大,成本高,着色膜色泽不鲜艳,逐渐被电解着色所取代。
(2)吸附着色法将阳极氧化后的铝制品浸渍到带有染料的溶液中,则多孔层外表能吸附各种染料而呈现出染料的色彩。
(3)电解着色铝制品经阳极氧化后,再在含金属盐的电解溶液中进行交流电解,则在多孔层孔隙底部沉积金属或金属化合物而显色。
3.封孔(1)热水封闭法(2)重铬酸盐封闭法防护性封孔,封孔后氧化膜呈黄色,耐蚀性较好,不适用于以装饰为目的着色氧化膜的封闭。
(3)水解封闭法(4)填充封闭法采用有机质如透明清漆、熔融石蜡、各种树脂和干性油等进行封闭。
阳极氧化工艺流程
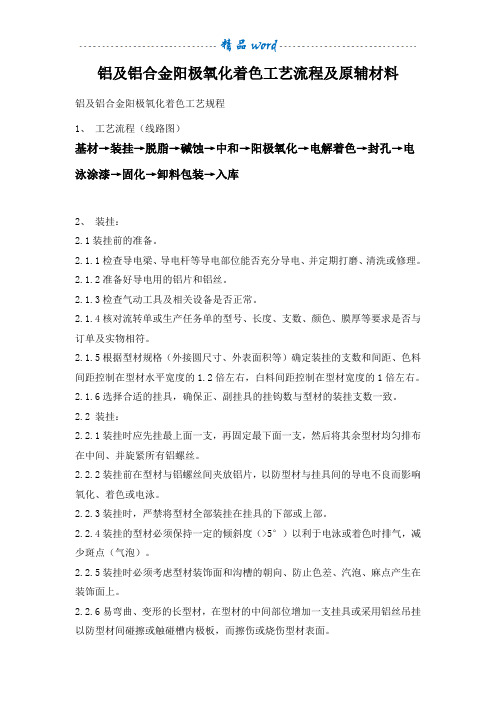
铝及铝合金阳极氧化着色工艺流程及原辅材料铝及铝合金阳极氧化着色工艺规程1、工艺流程(线路图)基材→装挂→脱脂→碱蚀→中和→阳极氧化→电解着色→封孔→电泳涂漆→固化→卸料包装→入库2、装挂:2.1装挂前的准备。
2.1.1检查导电梁、导电杆等导电部位能否充分导电、并定期打磨、清洗或修理。
2.1.2准备好导电用的铝片和铝丝。
2.1.3检查气动工具及相关设备是否正常。
2.1.4核对流转单或生产任务单的型号、长度、支数、颜色、膜厚等要求是否与订单及实物相符。
2.1.5根据型材规格(外接圆尺寸、外表面积等)确定装挂的支数和间距、色料间距控制在型材水平宽度的1.2倍左右,白料间距控制在型材宽度的1倍左右。
2.1.6选择合适的挂具,确保正、副挂具的挂钩数与型材的装挂支数一致。
2.2 装挂:2.2.1装挂时应先挂最上面一支,再固定最下面一支,然后将其余型材均匀排布在中间、并旋紧所有铝螺丝。
2.2.2装挂前在型材与铝螺丝间夹放铝片,以防型材与挂具间的导电不良而影响氧化、着色或电泳。
2.2.3装挂时,严禁将型材全部装挂在挂具的下部或上部。
2.2.4装挂的型材必须保持一定的倾斜度(>5°)以利于电泳或着色时排气,减少斑点(气泡)。
2.2.5装挂时必须考虑型材装饰面和沟槽的朝向、防止色差、汽泡、麻点产生在装饰面上。
2.2.6易弯曲、变形的长型材,在型材的中间部位增加一支挂具或采用铝丝吊挂以防型材间碰擦或触碰槽内极板,而擦伤或烧伤型材表面。
2.2.7选用副杆挂具时,优先选用插杆,采用铝丝绑扎时,一定要间隔均匀,露头应小于25mm。
2.2.8截面大小、形状悬殊的型材严禁装挂在同一排上。
2.2.9装挂或搬运型材,必须戴好干净手套,轻拿轻放、爱护、防护好型材表面,严禁野蛮操作。
2.2.10装挂或搬运型材时必须加强自检和互检,不合格的型材严禁装挂,表面沾有油污或铝屑(毛刺)的型材必须采取适当的措施处理干净。
2.2.11剔除不合格型材后,必须按订单支数及时补足。
阳极氧化工艺操作规程

阳极氧化工艺操作规程阳极氧化(Anodizing)是一种将金属表面氧化后形成氧化膜的工艺。
它具有增强耐腐蚀性、装饰性和机械性能的功能,被广泛应用于金属制品行业。
下面是阳极氧化工艺操作规程的详细介绍。
一、工艺前准备1. 确保设备和工具的清洁与正常运行,包括阳极氧化槽、电源、阴极和阳极等。
2. 准备氧化液,根据金属种类和要求调整氧化液的成分和浓度。
3. 清洁工件表面,确保无油污、灰尘和氧化膜。
二、工艺步骤1. 工件预处理将要进行阳极氧化的工件进行预处理,包括去油、去污和表面处理等。
确保工件表面光洁,无杂质。
2. 设定工艺参数根据金属种类和工件要求,设定适当的工艺参数,包括氧化液温度、电压、电流密度和氧化时间等。
3. 工件固定将工件固定在阳极上,确保与阳极之间的接触良好,避免电流不稳定和漏电现象。
4. 开始氧化将阳极浸入氧化液中,开启电源,让电流通过阳极和工件,开始氧化过程。
根据工艺参数,控制电流密度和氧化时间,使得工件表面形成所需的氧化膜。
5. 膜冲洗将工件从氧化槽中取出,用清水冲洗,去除残留的氧化液。
确保工件表面干净。
6. 封孔处理(可选)根据需要,进行封孔处理,形成封孔层,提高氧化膜的密封性能。
7. 接着进行除静电和干燥处理。
将工件置于除静电设备中,去除静电。
然后进行干燥处理,确保工件表面干燥。
8. 检验和包装对工件进行检验,包括氧化膜的厚度、颜色和质量等方面进行检查。
然后进行包装,确保工件安全运输。
三、安全注意事项1. 操作人员应穿戴好防护装备,包括手套、眼镜、口罩和工作服等。
2. 阳极氧化液有一定的腐蚀性,操作时要避免直接接触皮肤和吸入气体。
3. 严禁在阳极氧化过程中离开现场,避免发生安全事故。
4. 定期检查设备和电源,确保正常运行。
5. 阳极氧化过程涉及高温和高电压,操作人员应具备相关的安全知识和技能。
总结:阳极氧化工艺操作规程主要包括工艺前准备、工艺步骤和安全注意事项等方面。
通过正确操作和控制工艺参数,可以获得符合要求的氧化膜,提高金属制品的性能和质量。
铝及铝合金阳极氧化着色工艺流程及原辅材料
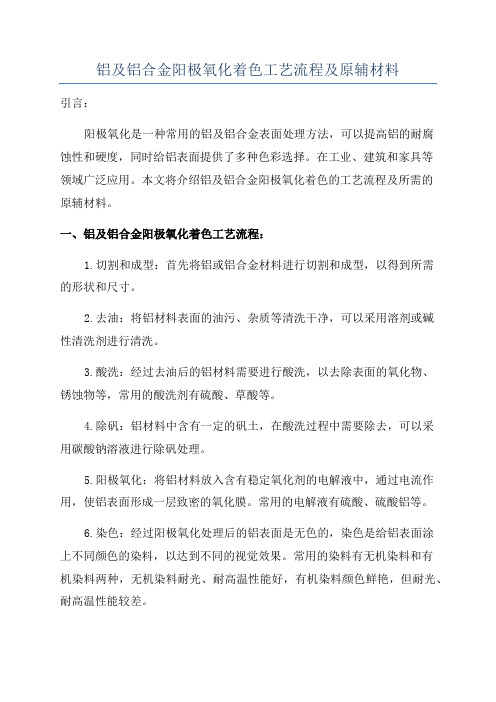
铝及铝合金阳极氧化着色工艺流程及原辅材料引言:阳极氧化是一种常用的铝及铝合金表面处理方法,可以提高铝的耐腐蚀性和硬度,同时给铝表面提供了多种色彩选择。
在工业、建筑和家具等领域广泛应用。
本文将介绍铝及铝合金阳极氧化着色的工艺流程及所需的原辅材料。
一、铝及铝合金阳极氧化着色工艺流程:1.切割和成型:首先将铝或铝合金材料进行切割和成型,以得到所需的形状和尺寸。
2.去油:将铝材料表面的油污、杂质等清洗干净,可以采用溶剂或碱性清洗剂进行清洗。
3.酸洗:经过去油后的铝材料需要进行酸洗,以去除表面的氧化物、锈蚀物等,常用的酸洗剂有硫酸、草酸等。
4.除矾:铝材料中含有一定的矾土,在酸洗过程中需要除去,可以采用碳酸钠溶液进行除矾处理。
5.阳极氧化:将铝材料放入含有稳定氧化剂的电解液中,通过电流作用,使铝表面形成一层致密的氧化膜。
常用的电解液有硫酸、硫酸铝等。
6.染色:经过阳极氧化处理后的铝表面是无色的,染色是给铝表面涂上不同颜色的染料,以达到不同的视觉效果。
常用的染料有无机染料和有机染料两种,无机染料耐光、耐高温性能好,有机染料颜色鲜艳,但耐光、耐高温性能较差。
7.封闭:染色后的铝材料需要通过封闭处理来提高色彩稳定性和耐腐蚀性,常用的封闭剂有热水封闭、冷水封闭、热气封闭等。
二、铝及铝合金阳极氧化着色所需的原辅材料:1.铝或铝合金材料:作为阳极氧化的基材。
2.去油剂:用于去除铝材料表面的油污、杂质等,常用的去油剂有溶剂或碱性清洗剂。
3.酸洗剂:用于去除铝材料表面的氧化物、锈蚀物等,常用的酸洗剂有硫酸、草酸等。
4.除矾剂:用于除去铝材料中的矾土,常用的除矾剂有碳酸钠溶液。
5.电解液:用于进行阳极氧化,常用的电解液有硫酸、硫酸铝等。
6.染料:用于给阳极氧化后的铝表面涂上不同颜色的染料,常用的染料有无机染料和有机染料。
7.封闭剂:用于提高染色后的铝表面的色彩稳定性和耐腐蚀性,常用的封闭剂有热水封闭、冷水封闭、热气封闭等。
阳极氧化完整工艺流程

陽極氧化工藝流程名词解释Ⅰ机械与化学表面处理ﻫ金属需经过抛光或刷光,随后除油及脱脂,检查外观质量,以为后续处理工序作表面准备。
Ⅱ阳极氧化通过认为得手段,形成一层厚氧化铝膜,即阳极氧化膜。
即吸附氧化膜.ﻫ在阳极氧化膜之微孔结构这就是吸附着色得先决条件.ﻫⅢ染色ﻫ内沉积染料分子.ﻫ封住微细孔,使染料固定于氧化膜内。
Ⅳ封孔ﻫﻫ吸附着色得理论依据ﻫ吸附现象就是采用染料水溶液浸渍染色得特点。
与其她着色技术不同得就是,其产生颜色之化合物并非产生自工艺本身而就是存在于开初得介质中.“吸附”这一术语得意思就是染料分子沉积并积聚氧化膜微孔得内表面,此阳极氧化膜得孔隙率为氧化膜得20m2/g。
导致吸附得就是铝氧化膜与染料分子之间得键合力起作用.这键合就是不稳定得,相反,吸附在阳极氧化膜上得染料(染色强度)与溶液中得染料之间达到平衡。
倘若溶液得染料浓度增大,则吸附量会增大,直至达到饱与点(颜色强度最大)时为止。
又倘若溶液得燃料浓度下降,比如下降到零,而水中又全无亲质,便会出现解吸附,导致褪色合色料扩散。
因此,在完成染色之后得多孔膜封闭工序就是必不可少得。
尽管染料迅速吸附,但整个着色过程得速度并非取决这一原始得现象,而就是取决于染料分子随后怎样进入狭窄得微孔内。
这一过程以略低得速率进行。
分子得直径平均为0、0025µm,而用硫酸直流氧化法制备得阳极氧化膜得微孔平均直径为0、02µm。
ﻫ***********************************************************ﻫ铝得级别与铝得阳极氧化ﻫ铝材得物理成分以及级别就是吸附着色就是否成功得重要因素。
铝材分为高纯铝、纯铝与合金铝。
高纯铝只含不超过痕量(不超过0、05%,依次排级)得亲质金属;纯铝得亲质金属含量不超过1%.ﻫ由于铝本身得强度不足以应付各种用途,因而相当多就是与其她金属形成合金,主要得就是镁、锌、锰、铜等。
- 1、下载文档前请自行甄别文档内容的完整性,平台不提供额外的编辑、内容补充、找答案等附加服务。
- 2、"仅部分预览"的文档,不可在线预览部分如存在完整性等问题,可反馈申请退款(可完整预览的文档不适用该条件!)。
- 3、如文档侵犯您的权益,请联系客服反馈,我们会尽快为您处理(人工客服工作时间:9:00-18:30)。
陽極氧化工藝流程名词解释Ⅰ机械与化学表面处理金属需经过抛光或刷光,随后除油及脱脂,检查外观质量,以为后续处理工序作表面准备。
Ⅱ阳极氧化通过认为的手段,形成一层厚氧化铝膜,即阳极氧化膜。
即吸附氧化膜。
这是吸附着色的先决条件。
Ⅲ染色在阳极氧化膜之微孔结构内沉积染料分子。
Ⅳ封孔封住微细孔,使染料固定于氧化膜内。
吸附着色的理论依据吸附现象是采用染料水溶液浸渍染色的特点。
与其他着色技术不同的是,其产生颜色之化合物并非产生自工艺本身而是存在于开初的介质中。
“吸附”这一术语的意思是染料分子沉积并积聚氧化膜微孔的内表面,此阳极氧化膜的孔隙率为氧化膜的20m2/g。
导致吸附的是铝氧化膜与染料分子之间的键合力起作用。
这键合是不稳定的,相反,吸附在阳极氧化膜上的染料(染色强度)与溶液中的染料之间达到平衡。
倘若溶液的染料浓度增大,则吸附量会增大,直至达到饱和点(颜色强度最大)时为止。
又倘若溶液的燃料浓度下降,比如下降到零,而水中又全无亲质,便会出现解吸附,导致褪色合色料扩散。
因此,在完成染色之后的多孔膜封闭工序是必不可少的。
尽管染料迅速吸附,但整个着色过程的速度并非取决这一原始的现象,而是取决于染料分子随后怎样进入狭窄的微孔内。
这一过程以略低的速率进行。
分子的直径平均为0.0025µm,而用硫酸直流氧化法制备的阳极氧化膜的微孔平均直径为0.02µm。
***********************************************************铝的级别和铝的阳极氧化铝材的物理成分以及级别是吸附着色是否成功的重要因素。
铝材分为高纯铝、纯铝和合金铝。
高纯铝只含不超过痕量(不超过0.05%,依次排级)的亲质金属;纯铝的亲质金属含量不超过1%。
由于铝本身的强度不足以应付各种用途,因而相当多是与其他金属形成合金,主要的是镁、锌、锰、铜等。
合金中的这些成分越高。
耐机械磨损性便越强,但对装饰性着色的适应性则相对的越差。
吸附着色本身是不会改善阳极氧化膜的物理特性的。
Ⅰ质量要求必须选用阳极氧化级的铝材,才能保证在阳极氧化和着色后仍然能保持吸引人的外观。
这一级别的铝材是专门为阳极氧化和着色而特别制备并经过特别检测的。
Ⅱ合金成分对色泽和透明度的影响铝和铝合金原有的颜色分别随其纯度级别与所含成分不同而异。
而吸附着色的色调又受原来的底色所影响。
1镁量大于5%时,阳极氧化膜会暗哑;2含锰及铬量即使低至仅1%,氧化膜便带黄色,超过此含量时,金属色调便会变的暗黑;3硅有使氧化膜带灰色的趋向,不过,很大程度上取决于它存在于合金中的形式。
如果以固溶体形式存在而含量低于1%时,它不会使氧化膜明显暗哑。
超过此含量及以非固溶体形式存在时,金属就会呈浑浊的灰色。
有一种特别的含硅3%~6%的铝合金就被称为“灰色调和金”。
4含铜量不超过0.2%左右的铝合金对阳极氧化膜的颜色、透明度或硬度均无甚影响。
以其通常在一些合金(如铝、铜、镁类及其他)所用含量,铜往往会给合金带来不规则斑点、呈微棕色及微灰色外观。
此外,铝铜合金在染色过程中比其他合金更易于发生原电池腐蚀(点状腐蚀)。
5锌对氧化膜质量不产生影响。
倘若含量在2%左右或稍大,又假如合金不含其他成分,则在染色中不会产生明显的色调变化,也不会令染色膜变暗哑。
Ⅲ机械表面处理与化学表面处理未经预处理的铝是不能阳极氧化和着色的。
事实上,有控制的表面处理是染色完美和光滑均匀德必备条件。
机械的和化学的预处理决定了金属表面最终德外观,因为透明德阳极氧化膜或着色都是无助于光学性能德。
化学处理目的在于清除金属上的脂类、油污、夹杂的亲质、皂类德残余、以及自然氧化膜。
这些污染物质如果未得到彻底清除,就会妨碍氧化膜的生成,随而队染色产生明显不良的影响。
对准备阳极氧化并吸附着色德铝件作预处理时所遵循的准则,与阳极氧化而步着色德工艺准则相同。
Ⅳ硫酸直流电氧化工艺参数对阳极氧化膜着色性能的影响在阳极氧化膜的吸附着色工艺中,最终获得的色调不但取决于着色过程本身,而且在相等重要的程度上取决于氧化膜的性能。
而氧化膜的性能又取决于阳极氧化参数。
在工业生产中,这一点往往未受到注意。
当在追溯染色故障因由时,必须同时仔细检查阳极氧化的工艺条件。
在无色阳极氧化时未被发现的氧化膜上的某些变异在西服着色时变的明显,而且即使改进染色过程亦只能有限度的得到改正。
①、硫酸浓度提高硫酸浓度会增强其对金属的溶解作用,产生更显著锥性的微细孔,孔的平均直径更大些。
由于空隙率增大而使内表面面积增大,吸附能力因而加强,可以染出较深的颜色。
在阳极氧化液使用期间,越来越多的游离硫酸消耗于溶解方面,随着其浓度因而下降,膜的吸附力亦随而降低。
为保证随后的染色能具有同等的强度,维持游离硫酸浓度于严格的允许范围内就显得十分重要。
②、铝含量当铝含量在5g/l以下时,染料吸附能力显著下降,但铝含量达到5g/l 以上时,吸附能力便维持接近稳定。
但当超过15g/l时,溶液便不能有效的起作用,阳极氧化膜会出现不规则。
因此,为使着色色泽高度均匀,宜将铝含量保持在5~15g/l。
③、电流密度在电流密度高而膜厚固定的情况下,由于金属受硫酸溶解的时间短些,所以染料吸附能力下降。
如果把成分不同的合金件放在一起进行阳极氧化,零件与零件之间便会出现电流密度上的变动,当这些零件着色时,便会反映为色泽上的差异。
因此,在同一批次内应只阳极氧化一种合金的零件;如果零件时要着色的,这一点尤其重要。
④、电压电压应根据阳极氧化工艺参数以及合金的成分来施加,通常为12~20V。
⑤、温度提高温度会加强硫酸的溶解作用,从而使氧化膜柔软些和有更多的微细孔,染料吸附能力便高。
但温度的影响非常明显,必须严格控制。
其允许的误差微+/-2℃。
在这方面,必须注意的是,倘若热对流步充分而出现局部温度差异,以后便会出现着色的不均匀的结果。
为避免出现局部过热现象,对阳极氧化液必须采取彻底搅拌和均匀冷却的措施。
⑥、阳极氧化时间与膜厚度阳极氧化膜的厚度几乎与电流密度和时间的乘积成正比。
当电流密度恒定时(在工厂生产时只是指接近恒定时),氧化膜的厚度及与厚度密切关联的染料吸附能力均与阳极氧化时间成正比关系。
由此可见,如需要着出深色,就必须有相当厚的膜,实际上,在厚度为12μm的标准氧化膜上,只要着色条件适当,一切需要的色调都可染出来。
不过,当要很高的颜色坚牢度时,阳极氧化膜就必须有超过12μm的厚度,以便获得最佳的耐光度,因为这一性能是由封闭在氧化膜内的染料量来确定的。
对于建筑物配件,氧化膜厚度还必须达到25μm。
基于成本及质量方面的考虑,建议厚度不超过30μm。
厚度在12μm以下的薄膜,其染出的色调不得不只限于淡色,因为其吸附能力有限。
Ⅴ阳极氧化后的清洗在精饰生产过程中,阳极氧化后的清洗是十分重要的。
黏在着色件上的酸的残留物如果未得到彻底清洗,染色时便会出现斑点。
它们还会污染染色液使之逐渐减弱染色能力,甚至会使染料产生化学变化。
因此,必须制订最优选的清洗处理程序,其处理过程还要尽量缩短滞留时间,以免氧化膜有被过早封闭的危险,而导致降低染料吸附力。
控制清洗效率的最佳方法是用溴甲酚紫指示剂。
酸/水发生迅速交换。
重要的是要让新鲜的清水尽快到达工件表面的每一个点。
如果工件的形状复杂,如有洞穴、焊接口等,就必须在清洗水中搅拌以产生嫘流。
Ⅵ阳极氧化后的工件在染色前的贮存阳极氧化出槽的工件在贮放一定时间后,其染料吸附能力便会减弱,在环境温度及湿度高时尤甚。
因此,氧化后的工件宜即作下一步处理或予以干燥,而不应过分迟缓。
如果工件经过干燥后,在进入下一步处理前,最好先用冷水湿透工件或者是用酸予以活化。
阳极氧化后的工件绝不允许沾上手指印。
只要有可能,在拿取这些工件时都需要戴上湿水的橡胶手套。
工件上凡被污物或油脂污染过的地方都不能吸附足够的染料来达到颜色深度的要求,也不能达到满意的封闭效果。
Ⅶ阳极氧化膜的活化阳极氧化后,在着色之前,可用酸液处理,把氧化膜活化。
所有有机酸、无机酸及酸性盐均适用于活化,不过,通常多选用硫酸或硝酸。
这一处理必会使一些阳极氧化膜的物质溶解,使空隙率增加,从而提高吸附染料能力。
如果工件曾存放一段时间,则酸的作用主要是溶解因大气水分反应而形成的水合物。
这样提高吸附染料能力会带来很多好处,这是有充分理由的。
但是,在最终厚度恒定的情况下,氧化膜的质量会有所下降,也是必须接受的事实。
用酸活化的方法主要应用在铭牌的制作上。
①、操作步骤直接在阳极氧化后或在经过贮放后(湿的或干的),氧化的铝品处理方法如下表所示:表中提供的数据只是典型的处理方法实例,还必须根据精饰方法的其他因素作相应的调整。
活化后还必须将工件再次彻底进行清洗。
②、氧化膜活化后的染色性能如果酸活化处理在比上述工件条件更为严格的条件下进行,则不但会有使阳极氧化膜的光泽和硬度下降的趋势,且其耐腐蚀性能亦会降低。
因此,对于建筑铝材,不推荐使用着色前酸活化的方法。
***********************************************************染色流程Ⅰ染色设备选择染色槽德尺寸以及染色液液量时,要考虑到使要处理的一槽工件完全浸没于溶液而不必对工件作重新排布。
若是采用喷淋染色法,则染色液的体积要小的多(约15%~20%)。
染色液用酸泵循环并通过喷嘴喷到工件上。
染色槽必须用符合下列要求的材料制造:①、有能经受80℃的热稳定性;②、对极度稀的非阳极氧化用之有机酸有耐酸能力;③、对低浓度的氯化物有稳定性;适用的材料包括有:①、耐酸不锈钢;②、具有中等至高的热稳定性之塑料,如聚烯烃类(聚乙烯、聚丙烯)、聚氯乙烯、聚丙烯腈、聚酯等;③、硬质橡胶。
染色槽经过使用一段时间出现裂纹或孔洞时,染色液会因裸露的槽体材料接触而致消弱染色能力。
Ⅱ染色液的加热最好的加热装置是以在水平方向安装于靠近染色槽底部的由电加热元件或蛇行管交换器组成的加热系统。
导热介质可以是水、蒸汽或油。
染色液也可以选用煤气燃烧器来加热,燃烧器安装在槽子下面。
制造加热装置的材料,其稳定性要与制造染色槽的材料稳定性标准相同。
加热系统宜配备温度控制装置。
Ⅲ染色液的搅拌适度的搅拌可使整槽染色液各处的染料浓度均匀。
倘若是给小零件染色的染色槽,通过热对流及工件运动产生的搅拌便可能足够了。
但是,一般情况下,必须透过多孔管打入经过过滤的压缩空气来增加染色液的运动。
搅拌器如螺旋浆或舵式的搅拌器之类都有很好的效果。
染色液也可以用循环泵来保证搅拌。
在这种情况下,可插上一个过滤网,把液中浮游物质隔住,保证染色液保持高纯净和着色件清洁。
由于染料吸附速率会随染色过程之持续而明显降低,因此,保持槽液搅拌就十分重要,特别是在开始阶段。
在把工件浸入时以及在染色的第一分钟,让工件动来动去往往可以增加色调均匀性,特别是在染淡色时。