封装工艺流程
第二章 封装工艺流程
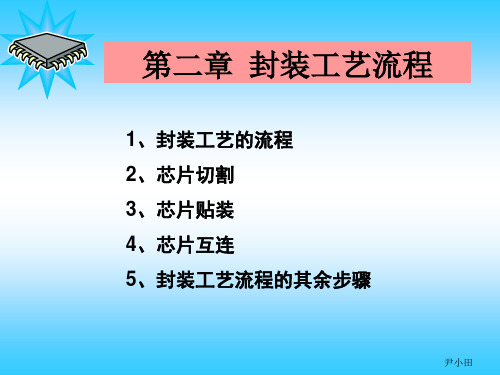
封装工艺的基本流程:
硅片减薄 芯片切割 硅片贴装 芯片互连
打码
上焊锡 切筋成形
成型技术即 (塑料封装) 去飞边毛刺
尹小田
硅片的尺寸越来越大,为了方便制 造、测试和运送过程,厚度增加。
硅片减薄 芯片切割 硅片贴装 芯片互连
成型技术即
打码 上焊锡 切筋成形
(塑料封装) 去飞边毛刺
背面减薄技术有: 磨削、研磨、干式抛光(Dry Polishing)、 化学机械抛光(chemical mechanicai polishing,CMP)、 电化学腐蚀(Electrochemical Etching)、 湿法腐蚀(Wet Etching,WE)、 等离子增强化学腐蚀(Plasma-Enhanced Chemical Etching,PECE) 常压等离子腐蚀(Atmosphere Downstream Plasma
尹小田
(4)玻璃胶粘贴法
方法:用高分子材料聚合物玻璃胶进行芯片粘贴。 工艺:先以盖印、网印、点胶的技术把胶原料涂布在基
板的芯片座中,再把芯片置于玻璃胶上粘贴。
1、多用于陶瓷封装中 2、冷却过程谨慎控制降温的速度以免造成应力破 裂
优3、点增:加可热以、得点到传无导空性隙能、,热可稳以定加性金优属良如的:、箔低、结银合应力、 低湿气含量的芯片粘贴;
尹小田
4、芯片互连
硅片减薄 芯片切割 硅片贴装 芯 切筋成形
(塑料封装) 去飞边毛刺
定义:把电子外壳的I/O引线或基板上的金线焊区与芯片的 焊区相连。
涂布合适的厚度和轮廓的芯片焊盘上进行固化。
1、各向同性材料。
不精确会怎样?
2、导电硅橡胶。
3、各向异性导电聚合物。 导电胶的缺点:热稳定性不好、高温时容易劣化和引发导 目电用的胶于导是中高电:有可胶改机靠中善物度填胶气要充的体求银导充的颗热分封粒性泄装或,漏。银增而薄强降片散低,热产因能品此力的都。 可是靠是度导,电因的此。不
封装工艺流程简介 (3)
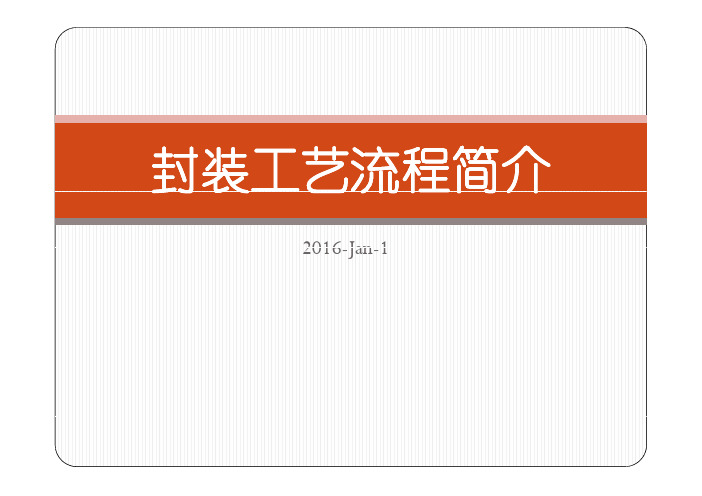
设备:
封装工艺流程简介
Tape and reel 编带
设备:
描述:
使用卷带包装设备,将单 颗产品用编带材料(卷带+盖 带)进行打卷包装。
封装工艺流程简介
Packing 包装
描述:
通过捆绑/包装以确 保产品在操作,运输的过 程中不受湿气, ESD的侵 袭,同时也确保产品在运 输过程中不受损伤。
封装工艺流程简介
2016-Jan-1
封装工艺流程简介
FOL
IQA SMT Pre-bake
基板收取Βιβλιοθήκη 来料检验IQA表面贴装* 可选 基板烘烤
Taping BG W/M
De-tape
D/S
2/O Fail
QA Pass
DA
DAC
Plasma
圆片收取 来料检验 贴保护膜 背部研磨 圆片装载 去掉保护膜
芯片切割 第二次光学检查
封装工艺流程简介
Baking 烘烤
描述:
PCB需要在做DA之 前做一下烘烤,以去 除PCB中的水分,提高 产品的可靠性能。
设备:
N2以防止PCB氧化
N2 inlet
Carrier Carrier
Outlet
125oC
封装工艺流程简介
Die Attach 装片
描述:
利用银浆或Film的 粘性将切割好的好的 晶粒吸取并粘贴于基 板上,以便于后制程作 业。
等离子清洗示意图
封装工艺流程简介
MD 包封
描述:
将前道完成后的产品 ,使用塑封料把芯片 塑封起来,免受外力损 坏。同时加强器件的 物理特性便于使用。
设备:
封装工艺流程简介
PMC 包封后烘
集成电路封装技术-封装工艺流程介绍

第二章 封装工艺流程
2.4.2 载带自动键合技术
TAB的关键技术
芯片凸点制作技术
TAB载带制作技术
载带引线与芯片凸点的内引线焊接和载带外引线 焊接技术
第二章 封装工艺流程
2.4.2 载带自动键合技术
TAB的关键技术--芯片凸点制作技术
一般工艺方法 将芯片反面淀积一定厚度的Au或Ni,同时在焊盘上淀积
Au-Pd-Ag和Cu的金属层。然后利用合金焊料将芯片焊接在 焊盘上。焊接工艺应在热氮气或能防止氧化的气氛中进行。
硬质焊料
合金焊料
软质焊料
第二章 封装工艺流程
2.3.3 导电胶粘贴法 导电胶是银粉与高分子聚合物〔环氧树脂〕的混合物。银
第二章 封装工艺流程
2.3.1共晶粘贴法 预型片法,此方法适用于较大面积的芯片粘贴。优点是
可以降低芯片粘贴时孔隙平整度不佳而造成的粘贴不完全 的影响。
第二章 封装工艺流程
2.3.2 焊接粘贴法
变形方式的不同,继而产生的各种应力。当材料在外力作用下不能产生位移时,它的几何形状和尺寸将发
在一点的集度焊称为接应粘力〔贴St法res是s〕利。物用体合由于金外反因而响变进形时行,芯在物片体粘内各贴局的部之方间法产生。相优互作点用是的内力, 应变方向平热行,传而导切应性力好的方。向与应变垂直。按照载荷〔Load〕作用的形式不同,应力又可以分为拉伸压
这三种连接技术对于不同的封装形式和集成电路芯片集成度的限制各有 打线键合适用引脚数为3-257;载带自动键合的适用引脚数为12-600;
第二章 封装工艺流程
2.4.1 打线键合技术
打线键合技术
超声波键合(Ultrasonic Bonding ,U/S bonding)
IC封装测试工艺流程

IC封装测试工艺流程1.芯片准备:在IC封装测试工艺流程开始之前,需要对待封装的芯片进行准备工作。
这包括将芯片切割成单个的小尺寸芯片,然后对其进行清洗、去除尘埃等净化处理。
2.焊接:在将芯片封装前,需要在芯片上焊接金线。
这些金线用于将芯片内部的各个功能单元与外界的引线相连。
这个过程需要使用特殊的焊接设备,确保焊接质量。
3.封装:接下来,将芯片放置在封装材料中。
封装材料可以是塑料、陶瓷等,不同的材料可以提供不同的保护性能。
芯片与封装材料之间还需要使用金线或焊膏进行连接。
封装过程可以是手工操作,也可以是自动化机器进行。
4.封装测试:在完成封装后,需要对封装好的芯片进行测试以确保其质量和性能。
这些测试可以包括外观检查、尺寸测量、电气性能测试等。
测试过程需要使用专业的测试设备和工艺流程。
5.校准:如果芯片测试结果不符合要求,可能需要对测试设备进行校准,以确保测试的准确性和一致性。
校准可以通过标准器件或其他校准设备进行。
6.封装精调:如果芯片测试结果仍然不达标,可能需要对封装工艺进行精细调整。
这意味着需要调整封装材料的配方、焊接参数、封装温度等。
精细调整可以通过试验和实验确定最佳的封装工艺参数。
7.标识与包装:在完成封装测试后,需要对封装好的芯片进行标识和包装。
标识可以包括芯片型号、生产日期、批次号等信息。
包装可以是常规的芯片包装方式,如管装、带装等。
包装后的芯片可以进行存储或运输。
8.品质管理:在整个封装测试工艺流程中,需要对每个步骤进行严格的品质管理。
这包括设立合理的工艺流程、制定工艺参数标准、对工艺设备和材料进行检验等。
品质管理可以通过ISO9001等质量管理体系认证。
总结:IC封装测试工艺流程是将芯片封装为成品集成电路的关键过程。
通过逐步进行焊接、封装、测试、校准、精细调整、标识和包装等步骤,可以确保封装好的芯片的品质和性能。
并且通过切合实际的品质管理措施,可以提高封装工艺的稳定性和一致性。
微电子封装技术第2章 封装工艺流程

2.4芯片贴装
焊接粘贴法工艺是将芯片背面淀积一定厚度的 Au或Ni,同时在焊盘上淀积Au-Pd-Ag和Cu的金属 层。
其优点是热传导好。工艺是将芯片背面淀积一 定厚度的Au或Ni,同时在焊盘上淀积Au-Pd-Ag和 Cu的金属层。这样就可以使用Pb-Sn合金制作的合 金焊料将芯片焊接在焊盘上。焊接温度取决于PbSn合金的具体成分比例。
微电子封装技术
董海青 李荣茂
第2章 封装工艺流程
2.1 流程概述 2.2 芯片减薄 2.3 芯片切割 2.4 芯片贴装 2.5 芯片互连技术 2.6 成形技术 2.7 后续工艺
2.1 流程概述
芯片封装工艺流程一般可以分为两个部分:前 段操作和后段操作。前段操作一般是指用塑料封装 (固封)之前的工艺步骤,后段操作是指成形之后 的工艺步骤。
2.4芯片贴装
导电胶粘贴法不要求芯片背面和基板具有金属 化层,芯片座粘贴后,用导电胶固化要求的温度时 间进行固化,可以在洁净的烘箱中完成固化,操作 起来比较简便易行。
导电胶进行芯片贴装的工艺过程如下:用针筒 或注射器将黏着剂涂布在芯片焊盘上,然后将芯片 精确地放置到焊盘的黏着剂上面。
导电胶粘贴法的缺点是热稳定性不好,容易在 高温时发生劣化及引发黏着剂中有机物气体成分泄 露而降低产品的可靠度,因此不适用于高可靠度要 求的封装。
2.4芯片贴装
玻璃胶粘贴芯片时,先以盖印、网印、点胶等 技术将玻璃胶原料涂布在基板的芯片座上,将IC芯 片放置在玻璃胶上后,再将封装基板加热至玻璃熔 融温度以上即可完成粘贴。
玻璃胶粘贴法的优点是可以得到无空隙、热稳 定性优良、低结合应力与低湿气含量的芯片粘贴; 其缺点是玻璃胶中的有机成分与溶剂必须在热处理 时完全去除,否则对封装结构及其可靠度将有所损 害。
封装工艺流程
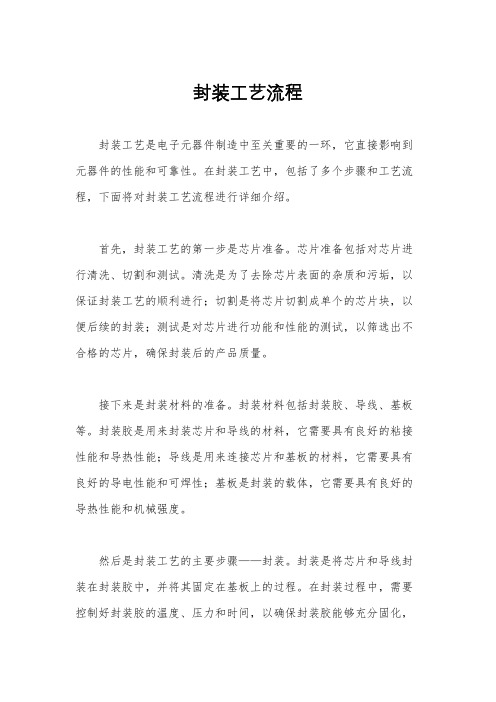
封装工艺流程
封装工艺是电子元器件制造中至关重要的一环,它直接影响到元器件的性能和可靠性。
在封装工艺中,包括了多个步骤和工艺流程,下面将对封装工艺流程进行详细介绍。
首先,封装工艺的第一步是芯片准备。
芯片准备包括对芯片进行清洗、切割和测试。
清洗是为了去除芯片表面的杂质和污垢,以保证封装工艺的顺利进行;切割是将芯片切割成单个的芯片块,以便后续的封装;测试是对芯片进行功能和性能的测试,以筛选出不合格的芯片,确保封装后的产品质量。
接下来是封装材料的准备。
封装材料包括封装胶、导线、基板等。
封装胶是用来封装芯片和导线的材料,它需要具有良好的粘接性能和导热性能;导线是用来连接芯片和基板的材料,它需要具有良好的导电性能和可焊性;基板是封装的载体,它需要具有良好的导热性能和机械强度。
然后是封装工艺的主要步骤——封装。
封装是将芯片和导线封装在封装胶中,并将其固定在基板上的过程。
在封装过程中,需要控制好封装胶的温度、压力和时间,以确保封装胶能够充分固化,
并且芯片和导线能够被牢固地固定在基板上。
最后是封装产品的测试和包装。
测试是对封装后的产品进行功能和性能的测试,以确保产品符合规定的标准和要求;包装是将测试合格的产品进行包装,以便于存储和运输。
总的来说,封装工艺流程包括芯片准备、封装材料的准备、封装和封装产品的测试和包装。
每个步骤都至关重要,任何一环节的问题都可能导致产品的质量不合格。
因此,在封装工艺中,需要严格控制每个步骤的工艺参数,以确保产品的质量和可靠性。
一文详解封装制程工艺

点就是制程能力。
SIP封装制程按照芯片与基板的连接方式可分为引线键合封装和倒装焊两种。
引线键合封装工艺工艺流程圆片→圆片减薄→圆片切割→芯片粘结→引线键合→等离子清洗→液态密封剂灌封→装配焊料球→回流焊→表面打标→分离→最终检查→测试→包装。
圆片减薄圆片减薄是指从圆片背面采用机械或化学机械(CMP)方式进行研磨,将圆片减薄到适合封装的程度。
随着系统朝轻薄短小的方向发展,芯片封装后模块的厚度变得越来越薄,因此在封装之前一定要将圆片的厚度减薄到可以接受的程度,以满足芯片装配的要求。
圆片切割圆片减薄后,可以进行划片。
较老式的划片机是手动操作的,现在一般的划片机都已实现全自动化。
无论是部分划线还是完全分割硅片,目前均采用锯刀,因为它划出的边缘整齐,很少有碎屑和裂口产生。
芯片粘结已切割下来的芯片要贴装到框架的中间焊盘上。
焊盘的尺寸要和芯片大小相匹配,若焊盘尺寸太大,则会导致引线跨度太大,在转移成型过程中会由于流动产生的应力而造成引线弯曲及芯片位移现象。
贴装的方式可以是用软焊料(指Pb-Sn 合金,尤其是含Sn 的合金)、Au-Si 低共熔合金等焊接到基板上,在塑料封装中最常用的方法是使用聚合物粘结剂粘贴到金属框架上。
引线键合在塑料封装中使用的引线主要是金线,其直径一般为0.025mm~0.032mm。
引线的长度常在1.5mm~3mm之间,而弧圈的高度可比芯片所在平面高 0.75mm。
键合技术有热压焊、热超声焊等。
这些技术优点是容易形成球形(即焊球技术),并防止金线氧化。
为了降低成本,也在研究用其他金属丝,如铝、铜、银、钯等来替代金丝键合。
热压焊的条件是两种金属表面紧紧接触,控制时间、温度、压力,使得两种金属发生连接。
表面粗糙(不平整)、有氧化层形成或是有化学沾污、吸潮等都会影响到键合效果,降低键合强度热压焊的温度在300℃~400℃,时间一为40ms(通常,加上寻找键合位置等程序,键合速度是每秒二线)。
超声焊的优点是可避免高温,因为它用20kHz~60kHz的超声振动提供焊接所需的能量,所以焊接温度可以降低一些。
封装工艺流程
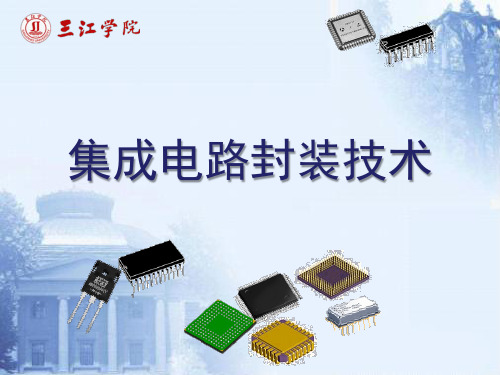
银粉起导电作用,而环氧树脂起粘接作用。
导电胶有三种配方: (1)各向同性材料,能沿所有方向导电。 (2)导电硅橡胶,能起到使器件与环境隔 绝,防止水、汽对芯片的影响,同时还可 以屏蔽电磁干扰。 (3)各向异性导电聚合物,电流只能在一 个方向流动。在倒装芯片封装中应用较多。 无应力影响。
芯片凸点金属材料:一般包括金属Au、Cu、Au/Sn、 Pd/Sn。
第二章 封装工艺流程
2.4.2 载带自动键合技术
TAB的关键技术
芯片凸点制作技术
TAB载带制作技术
载带引线与芯片凸点的内引线焊接和载带外引 线焊接技术
第二章 封装工艺流程
2.4.2 载带自动键合技术
TAB的关键技术--芯片凸点制作技术
第二章 封装工艺流程
2.2 芯片切割
2.2.1、为什么要减薄
半导体集成电路用硅片4吋厚度为520μm,6吋厚度为 670μm。这样就对芯片的切分带来困难。因此电路层制作完 成后,需要对硅片背面进行减薄,使其达到所需要的厚度, 然后再进行划片加工,形成一个个减薄的裸芯片。
第二章 封装工艺流程
2.2.2减薄工艺
打线键合适用引脚数为3-257;载带自动键合的 适用引脚数为12-600;倒装芯片键合适用的引脚数为 6-16000。可见C4适合于高密度组装。
第二章 封装工艺流程
2.4.1 打线键合技术
打线键合技术
超声波键合(Ultrasonic Bonding ,U/S bonding)
热压键合(Thermocompression Bonding T/C bonding) 热超声波键合(Thermosonic Bonding,T/S bonding)
IC芯片封装测试工艺流程

IC芯片封装测试工艺流程一、封装前的准备工作1、确定封装器件的封装类型和尺寸。
不同的封装类型和尺寸需要不同的工艺流程和设备。
2、准备封装器件所需的封装模具和模具夹具。
3、准备封装器件所需的封装材料,如封装胶水、封装粘合剂等。
二、封装工艺流程1、胶水涂布:将封装胶水涂布在封装模具的底部。
2、芯片定位:将芯片放置在封装模具的底部,确保芯片与模具中的引脚对齐。
3、封装胶水固化:将封装模具放入固化设备中,对胶水进行固化处理,确保芯片与封装器件之间有良好的粘合性。
4、封装粘合:将封装粘合剂涂布在封装模具的顶部,确保芯片与封装器件之间的连接紧密。
5、封装器件密封:将封装模具的顶部与底部进行紧密封闭,确保封装器件的内部空间不受外界环境影响。
6、焊线连接:根据封装类型的不同,将引脚连接器件板上的焊点,通常使用焊锡或焊膏进行焊接。
7、焊接固化:对焊接点进行固化处理,确保焊接点的稳定性和可靠性。
8、封装器件外观检查:对封装器件的外观进行检查,确保封装质量符合要求。
9、封装器件的包装、存储和标识:对封装器件进行包装,以便于存储和识别。
三、封装后的测试工作1、外观检查:对封装器件的外观进行检查,包括封装是否完整、无明显裂纹等。
2、尺寸测量:对封装器件的尺寸进行测量,确保尺寸符合要求。
3、引脚测试:对封装器件的引脚进行测试,包括引脚间的连接性、引脚的电气特性等。
4、性能测试:对封装器件的性能进行测试,包括电气性能、温度特性等。
5、可靠性测试:对封装器件的可靠性进行测试,包括高温老化、低温老化、湿热老化等。
6、功能测试:对封装器件的功能进行测试,确保其能够正常工作。
7、包装、存储和标识:对已测试完成的封装器件进行包装、存储和标识,以便于后续的使用和销售。
以上是一个相对完整的IC芯片封装测试工艺流程,通过这个流程,可以确保封装器件的质量和性能符合要求,并满足客户的需求。
封装测试过程中的每一个环节都非常重要,任何一个环节的差错都可能导致封装器件的质量问题,因此需要严密的工艺控制和严格的质量管控。
半导体封装主要工艺流程
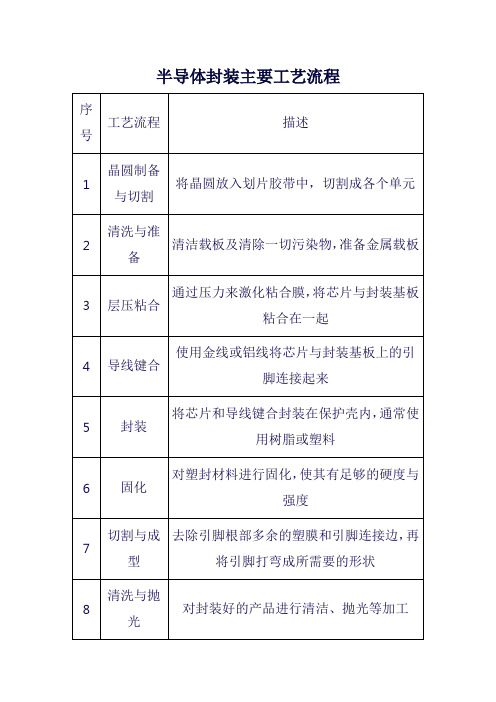
序号
工艺流程
描述
1
晶圆制备与切割
将晶圆放入划片胶带中,切割成各个单元
2
清洗与准备
清洁载板及清除一切污染物,准备金属载板
3
层压粘合
通过压力来激化粘合膜,将芯片与封装基板粘合在一起
4
导线键合
使用金线或铝线将芯片与封装基板上的引脚连接起来
5
封装
将芯片和导线键合封装在保护壳内,通常使用树脂或塑料
6
固化
对塑封材料进行固化,使其有足够的硬度与强度
7
切割与成型
去除引脚根部多余的塑膜和引脚连接边,再将引脚打弯成所需要的形状
8
清洗与抛光
对封装好的产品进行清洁、抛光等加工
9
标识与打印
根据客户需要,在封装器件表面进行打印,用于识别
10
测试
对封装好的半导体器件进行测试,检验其性能和可靠性
lga封装工艺流程步骤
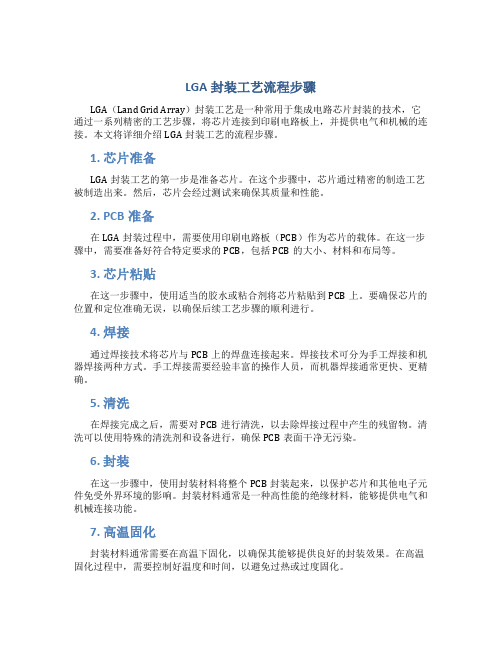
LGA封装工艺流程步骤LGA(Land Grid Array)封装工艺是一种常用于集成电路芯片封装的技术,它通过一系列精密的工艺步骤,将芯片连接到印刷电路板上,并提供电气和机械的连接。
本文将详细介绍LGA封装工艺的流程步骤。
1. 芯片准备LGA封装工艺的第一步是准备芯片。
在这个步骤中,芯片通过精密的制造工艺被制造出来。
然后,芯片会经过测试来确保其质量和性能。
2. PCB准备在LGA封装过程中,需要使用印刷电路板(PCB)作为芯片的载体。
在这一步骤中,需要准备好符合特定要求的PCB,包括PCB的大小、材料和布局等。
3. 芯片粘贴在这一步骤中,使用适当的胶水或粘合剂将芯片粘贴到PCB上。
要确保芯片的位置和定位准确无误,以确保后续工艺步骤的顺利进行。
4. 焊接通过焊接技术将芯片与PCB上的焊盘连接起来。
焊接技术可分为手工焊接和机器焊接两种方式。
手工焊接需要经验丰富的操作人员,而机器焊接通常更快、更精确。
5. 清洗在焊接完成之后,需要对PCB进行清洗,以去除焊接过程中产生的残留物。
清洗可以使用特殊的清洗剂和设备进行,确保PCB表面干净无污染。
6. 封装在这一步骤中,使用封装材料将整个PCB封装起来,以保护芯片和其他电子元件免受外界环境的影响。
封装材料通常是一种高性能的绝缘材料,能够提供电气和机械连接功能。
7. 高温固化封装材料通常需要在高温下固化,以确保其能够提供良好的封装效果。
在高温固化过程中,需要控制好温度和时间,以避免过热或过度固化。
8. 检测与测试封装完成后,需要对封装后的芯片进行检测和测试,以确保其质量和性能。
这些测试可以包括外观检查、电气测试和功能测试等,以验证芯片的可靠性和稳定性。
9. 终检与包装在所有工艺步骤完成之后,进行终检与包装。
终检是最后一道工序,通过对封装好的芯片进行全面检测,确保其符合规定的标准和要求。
然后,芯片将被包装起来,以便运输和存储。
结论LGA封装工艺是一种常用的电子封装技术,通过精密的步骤将芯片连接到PCB 上,并提供电气和机械连接。
封装工艺流程
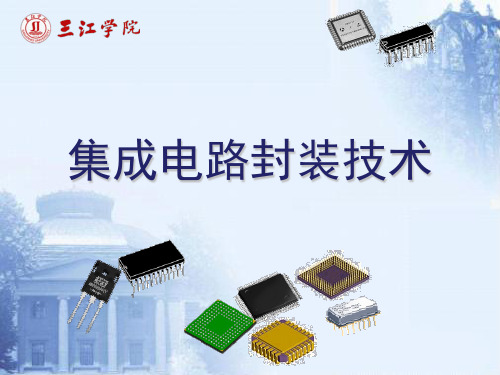
第二章 封装工艺流程
(3)热超声波键合
热超声波键合是热压键合与超声波键合的混合技术。在 工艺过程中,先在金属线末端成球,再使用超声波脉冲进行 金属线与金属接垫之间的接合。
此过程中接合工具不被加热,仅给接合的基板加热(温 度维持在100-150℃)。其目的是抑制键合界面的金属间化合 物(类似于化学键,金属原子的价电子形成键)的成长,和 降低基板高分子材料因高温产生形变。
第二章 封装工艺流程
2.2.2减薄工艺
先划片后减薄和减薄划片两种方法
DBG(dicing before grinding) 在背面磨削之前,将硅片 的正面切割出一定深度的切口,然后再进行磨削。
DBT(dicing by thinning) 在减薄之前先用机械的或化学 的方法切割出一定深度的切口,然后用磨削方法减薄到一 定厚度后,采用常压等离子腐蚀技术去除掉剩余加工量。。
这两种方法都很好地避免了或减少了减薄引起 的硅片翘曲以及划片引起的边缘损害,大大增强了 芯片的抗碎能力。
第二章 封装工艺流程
2.3 芯片贴装 芯片贴装,也称芯片粘贴,是将芯片固定于封装基板
或引脚架芯片的承载座上的工艺过程。
贴装方式
• 共晶粘贴法 • 焊接粘贴法 • 导电胶粘贴法 • 玻璃胶粘贴法
第二章 封装工艺流程
2.3.2 焊接粘贴法 焊接粘贴法是利用合金反应进行芯片粘贴的方法。优点
是热传导性好。 一般工艺方法
将芯片背面淀积一定厚度的Au或Ni,同时在焊盘上淀积 Au-Pd-Ag和Cu的金属层。然后利用合金焊料将芯片焊接在焊 盘上。焊接工艺应在热氮气或能防止氧化的气氛中进行。
硬质焊料
合金焊料
软质焊料
扇出式封装的工艺流程

扇出式封装的工艺流程一、基板准备扇出式封装的第一步是准备基板。
基板是封装过程中芯片的载体,其质量直接影响着封装成品的质量。
在这一步骤中,需要选择合适的基板材料,并进行清洗、切割等处理,确保基板的平整度和尺寸符合要求。
二、放置芯片在准备好基板后,需要将芯片放置在基板上。
这一步需要精确对位,确保芯片与基板之间的连接正确无误。
常用的放置方式有手动和自动两种,根据实际情况选择合适的放置方式。
三、固晶固晶是确保芯片在封装过程中保持稳定的关键步骤。
在这一步骤中,需要使用粘合剂将芯片粘贴在基板上,并确保粘合剂的厚度和均匀度符合要求。
同时,需要对芯片进行热压处理,增强芯片与基板之间的粘合力。
四、焊线焊线是扇出式封装的关键步骤之一,其目的是将芯片与基板之间的引脚进行连接。
在这一步骤中,需要使用焊接设备将引脚与对应的焊盘进行焊接,确保焊接点的质量符合要求。
焊线的质量直接影响着封装成品的质量和可靠性。
五、填充塑胶在完成焊线后,需要在芯片和基板之间填充塑胶材料,以保护芯片和引脚不受外界环境的影响。
填充塑胶时需要控制填充的量和均匀度,避免出现气泡、空洞等缺陷。
六、表面处理表面处理是扇出式封装过程中的重要环节,其目的是提高封装成品的美观度和耐久性。
在这一步骤中,需要对封装成品进行抛光、镀膜等处理,以提高其表面光洁度和抗腐蚀性能。
七、切筋成型切筋成型是将封装完成的基板进行切割和成型的过程。
在这一步骤中,需要使用切割设备和模具,将基板切割成所需形状,并对边缘进行倒角、磨光等处理,以确保封装成品的美观度和使用性能。
八、质量检测质量检测是扇出式封装过程中必不可少的环节。
在这一步骤中,需要对封装成品进行各种检测,如外观检测、电性能检测、环境试验等,以确保其质量和可靠性符合要求。
对于不合格的封装成品,需要进行返工或报废处理。
九、包装入库最后一步是包装入库,即将检测合格的封装成品进行包装、标识和入库管理。
包装材料应具有良好的保护性能和运输性能,以确保封装成品在运输过程中不受损坏。
封装基板工艺流程
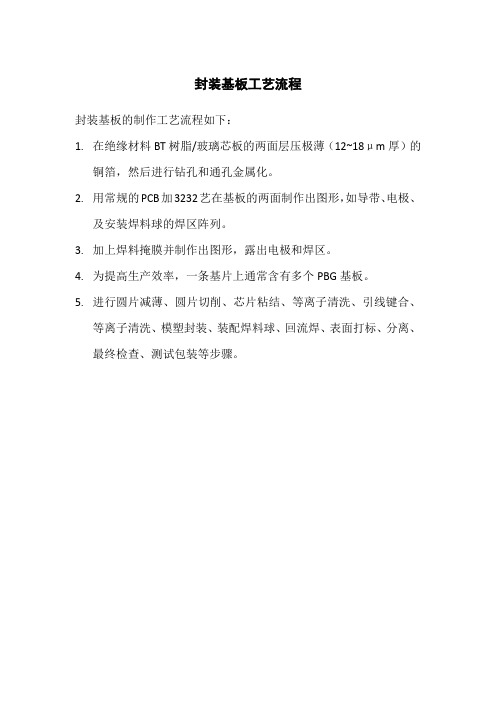
封装基板工艺流程
封装基板的制作工艺流程如下:
1.在绝缘材料BT树脂/玻璃芯板的两面层压极薄(12~18μm厚)的
铜箔,然后进行钻孔和通孔金属化。
2.用常规的PCB加3232艺在基板的两面制作出图形,如导带、电极、
及安装焊料球的焊区阵列。
3.加上焊料掩膜并制作出图形,露出电极和焊区。
4.为提高生产效率,一条基片上通常含有多个PBG基板。
5.进行圆片减薄、圆片切削、芯片粘结、等离子清洗、引线键合、
等离子清洗、模塑封装、装配焊料球、回流焊、表面打标、分离、最终检查、测试包装等步骤。
COB封装工流程

COB封装工流程COB(Chip on Board)封装工艺是一种将裸片芯片直接粘贴在基板上,并通过线缆和焊接技术进行连接的封装工艺。
它具有芯片与基板紧密结合、尺寸小、导热性能好等特点,已广泛应用于LED灯、光电子器件、传感器、电源模块等领域。
下面将详细介绍COB封装工艺的流程。
一、准备工作COB封装工艺的准备工作主要包括选材、基板处理和组织技术资料。
选材时要根据芯片的尺寸、功耗、工作温度等要求选择适合的基板材料和封装胶水。
基板处理主要包括表面清洁、去除氧化层和涂胶处理等。
组织技术资料主要包括芯片引线布局、焊盘设计、焊接参数等信息。
二、芯片粘贴芯片粘贴是COB封装的关键环节,主要包括基板对位、芯片定位和胶水涂布。
首先,通过光学显微镜和自动对位设备对基板进行对位。
然后,将芯片放置在基板上的粘合区域,并进行调整和定位。
最后,使用封装胶水均匀地涂布在芯片和基板之间,确保芯片与基板之间的粘合牢固。
三、导线连接导线连接是将芯片与基板进行电气连接的重要环节,主要包括连接线焊接和连接线切断。
连接线焊接使用线材将芯片引脚与基板焊盘连接起来,需要注意引脚位置和焊接质量。
连接线切断则是将多余的线材通过切断或烧断等方式进行处理,确保连接线的整洁和牢固。
四、灌胶固化灌胶固化是为了保护芯片和连接线,并提高封装的抗震、抗压能力。
首先,将灌胶胶水注入芯片和基板之间的间隙中,确保将所有空隙填满。
然后,通过高温或紫外线照射等方式使胶水固化,形成牢固的胶固层。
最后,对胶固层进行修整和除尘处理,提高封装的外观和品质。
五、测试和封装封装完成后,需要进行测试和封装。
测试主要包括芯片性能检测和连接线电性测试。
芯片性能检测通过电性能测试仪器检测芯片的电流、电压、亮度等参数,确保芯片能正常工作。
连接线电性测试则通过测试仪器检测连接线的焊接质量和电阻值等。
测试完成后,通过封装设备将COB封装好的芯片进行分割、切片或切断等处理,最终形成成品。
总结:COB封装工艺从芯片粘贴到灌胶固化再到测试和封装,是一个细致而复杂的过程。
- 1、下载文档前请自行甄别文档内容的完整性,平台不提供额外的编辑、内容补充、找答案等附加服务。
- 2、"仅部分预览"的文档,不可在线预览部分如存在完整性等问题,可反馈申请退款(可完整预览的文档不适用该条件!)。
- 3、如文档侵犯您的权益,请联系客服反馈,我们会尽快为您处理(人工客服工作时间:9:00-18:30)。
导电胶粘贴法的缺点是热稳定性不好,高温下会引 起粘接可靠度下降,因此不适合于高可靠度封装。
第二章 封装工艺流程
玻璃胶粘贴法
与导电胶类似,玻璃胶也属于厚膜导体材料( 后面我们将介绍)。不过起粘接作用的是低温玻璃 粉。它是起导电作用的金属粉(Ag、Ag-Pd、Au、Cu 等)与低温玻璃粉和有机溶剂混合,制成膏状。
硬质焊料
合金焊料
软质焊料
第二章 封装工艺流程
2.3.3 导电胶粘贴法 导电胶是银粉与高分子聚合物(环氧树脂)的混合物。 银粉起导电作用,而环氧树脂起粘接作用。
导电胶有三种配方: (1)各向同性材料,能沿所有方向导电。 (2)导电硅橡胶,能起到使器件与环境隔 绝,防止水、汽对芯片的影响,同时还可 以屏蔽电磁干扰。 (3)各向异性导电聚合物,电流只能在一 个方向流动。在倒装芯片封装中应用较多。 无应力影响。
第二章 封装工艺流程
2.4.2 载带自动键合技术
TAB技术的关键材料
基带材料:要求耐高温,与金属箔粘贴性好,热匹配性 好,抗化学腐蚀性强,机械强度高,吸水率低。例如,聚酰亚胺
(PI)、聚乙烯对本二甲酸脂(PET)和苯并环丁烯(BCB)
TAB金属材料:要求导电性能好,强度高,延展性、表 面平滑性良好,与各种基带粘贴牢固,不易剥离,易于用光 刻法制作出精细复杂的图形,易电镀Au、Ni、Pb/Sn焊接材 料,例如,Al、Cu。 芯片凸点金属材料:一般包括金属Au、Cu、Au/Sn、 Pd/Sn。
第二章 封装工艺流程
2.2.2减薄工艺
先划片后减薄和减薄划片两种方法
DBG(dicing before grinding) 在背面磨削之前,将硅片 的正面切割出一定深度的切口,然后再进行磨削。
DBT(dicing by thinning) 在减薄之前先用机械的或化学 的方法切割出一定深度的切口,然后用磨削方法减薄到一 定厚度后,采用常压等离子腐蚀技术去除掉剩余加工量。。 这两种方法都很好地避免了或减少了减薄引起 的硅片翘曲以及划片引起的边缘损害,大大增强了 芯片的抗碎能力。
第二章 封装工艺流程
2.4.1 打线键合技术介绍 (2)热压键合
第二章 封装工艺流程
(3)热超声波键合
热超声波键合是热压键合与超声波键合的混合技术。在 工艺过程中,先在金属线末端成球,再使用超声波脉冲进行 金属线与金属接垫之间的接合。
此过程中接合工具不被加热,仅给接合的基板加热(温 度维持在100-150℃)。其目的是抑制键合界面的金属间化合 物(类似于化学键,金属原子的价电子形成键)的成长,和 降低基板高分子材料因高温产生形变。
第二章 封装工艺流程
2.4.1 打线键合技术
打线键合技术
超声波键合(Ultrasonic Bonding ,U/S bonding) 热压键合(Thermocompression Bonding T/C bonding) 热超声波键合(Thermosonic Bonding,T/S bonding)
第二章 封装工艺流程
(2)影响打线键合可靠度因素
封胶和粘贴材料 与线材的反应
金属间化合物的形成
可靠度因素
可靠度常用拉力试验 和键合点的剪切试验 测试检查
第二章 封装工艺流程
2.4.2 载带自动键合技术
载带自动健合技术是在类似于135胶片的柔性载带粘结金属 薄片,(像电影胶片一样卷在一带卷上,载带宽度8-70mm。 在其特定的位置上开出一个窗口。窗口为蚀刻出一定的印刷线路 图形的金属箔片(0.035mm厚)。 引线排从窗口伸出,并与载带相连,载带边上有供传输带用 的齿轮孔。 当载带卷转动时,载带依靠齿孔往前运动,使带上的窗口精 确对准带下的芯片。再利用热压模将导线排精确键合到芯片上。 可见TAB技术与一般的压丝引线技术不同。 后者的特点是将一根、一根的引线先后分立的快速的键合到 搭接片上。TAB技术中内引线键合后还要作后道工序,包括电学 测试、通电老化,外引线键合、切下,最后进行封装工艺(。这 些都在载带上完成。
三种导电胶的特点是:化学接合、具有导电功能。
第二章 封装工艺流程
导电胶贴装工艺
膏状导电胶: 用针筒或注射器将粘贴剂涂布到芯 片焊盘上(不能太靠近芯片表面,否则 会引起银迁移现象),然后用自动拾片 机(机械手)将芯片精确地放置到焊盘 的粘贴剂上,在一定温度下固化处理 (150℃ 1小时或186℃半小时)。 固体薄膜: 将其切割成合适的大小放置于芯片 与基座之间,然后再进行热压接合。采 用固体薄膜导电胶能自动化大规模生产。
第二章 封装工艺流程
打线键合的线材与可靠度 (1)合金线材 铝合金线 因纯铝线材太软很少使用。铝合金线标准线材是铝1%硅。令你一种是含0.5-1%镁的铝导线。其优点是抗疲劳 性优良,生成金属间化合物的影响小。 金线 纯金线的纯度一般用4个9。为增加机械强度,往往在 金中添加5-10ppm 铍或铜。金线抗氧化性好,常由于超声 波焊接中。
第二章 封装工艺流程
2.3.1共晶粘贴法 预型片法,此方法适用于较大面积的芯片粘贴。优点 是可以降低芯片粘贴时孔隙平整度不佳而造成的粘贴不完 全的影响。
第二章 封装工艺流程
2.3.2 焊接粘贴法 焊接粘贴法是利用合金反应进行芯片粘贴的方法。优点 是热传导性好。 一般工艺方法 将芯片背面淀积一定厚度的Au或Ni,同时在焊盘上淀积 Au-Pd-Ag和Cu的金属层。然后利用合金焊料将芯片焊接在焊 盘上。焊接工艺应在热氮气或能防止氧化的气氛中进行。
集成电路封装技术
第二章 封装工艺流程
2.1.1 为什么要学习封装工艺流程
熟悉封装工艺流程是认识封装技术的前提,是 进行封装设计、制造和优化的基础。
芯片封装和芯片制造不在同一工厂完成 它们可能在同一工厂不同的生产区、或不同的地区,甚 至在不同的国家。许多工厂将生产好的芯片送到几千公里以 外的地方去做封装。芯片一般在做成集成电路的硅片上进行 测试。在测试中,先将有缺陷的芯片打上记号(打一个黑色 墨点),然后在自动拾片机上分辨出合格的芯片。
第二章 封装工艺流程
2.4.2 载带自动键合技术
TAB的关键技术 芯片凸点制作技术 TAB载带制作技术
载带引线与芯片凸点的内引线焊接和载带外引 线焊接技术
第二章 封装工艺流程
2.4.2 载带自动键合技术 TAB的关键技术--芯片凸点制作技术
IC芯片制作完成后其表面均镀有钝化保护层,厚度高于 电路的键合点,因此必须在IC芯片的键合点上或TAB载带的 内引线前端先长成键合凸块才能进行后续的键合,通常TAB 载带技术也据此区分为凸块化载带与凸块化芯片TAB两大类。 地状金属凸块;单层载带可配合铜箔引脚的刻蚀制成凸 块,在双层与三层载带上,因为蚀刻的工艺容易致导带变形, 而使未来键合发生对位错误,因此双层与三层载带较少应用 于凸块载带TAB的键合。 凸块式芯片TAB,先将金属凸块长成于IC芯片的铝键合 点上,再与载带的内引脚键合。预先长成的凸块除了提供引 脚所需要的金属化条件外,可避免引脚与IC芯片间可能发生 短路,但制作长有凸块的芯片是TAN工艺最大的困难。
打线键合(WB wire bonding) 倒装芯片键合(FCB flip chip bonding,C4) 载带自动键合(TAB tape automate bonding)
这三种连接技术对于不同的封装形式和集成电 路芯片集成度的限制各有不同的应用范围。 打线键合适用引脚数为3-257;载带自动键合的 适用引脚数为12-600;倒装芯片键合适用的引脚数为 6-16000。可见C4适合于高密度组装。
第二章 封装工艺流程
2.3 芯片贴装 芯片贴装,也称芯片粘贴,是将芯片固定于封装基板 或引脚架芯片的承载座上的工艺过程。
贴装方式
• 共晶粘贴法
• 焊接粘贴法 • 导电胶粘贴法 • 玻璃胶粘贴法
第二章 封装工艺流程
2.3.1共晶粘贴法 共晶反应 指在一定的温度下,一定成分的液体同时结晶出两种 一定成分的固相反应。例如,含碳量为2.11%-6.69%的铁碳 合金,在1148摄氏度的恆温下发生共晶反应,产物是奥氏 体(固态)和渗碳体(固态)的机械混合物,称为“莱氏 体”。 一般工艺方法 陶瓷基板芯片座上镀金膜-将芯片放臵在芯片座上-热 氮气氛中(防氧化)加热并使粘贴表面产生摩擦(去除粘 贴表面氧化层)-约425℃时出现金-硅反应液面,液面移动 时,硅逐渐扩散至金中而形成紧密结合。
第二章 封装工艺流程
2.2 芯片切割
2.2.1、为什么要减薄
半导体集成电路用硅片4吋厚度为520μm,6吋厚度为 670μm。这样就对芯片的切分带来困难。因此电路层制作完 成后,需要对硅片背面进行减薄,使其达到所需要的厚度, 然后再进行划片加工,形成一个个减薄的裸芯片。
第二章 封装工艺流程
2.2.2减薄工艺
硅片背面减技术主要有: 磨削、研磨、化学抛光 干式抛光、电化学腐蚀、湿法腐蚀 等离子增强化学腐蚀、常压等离子腐蚀等
减薄厚硅片粘在一个带有金属环或塑料框架的薄膜 (常称为蓝膜)上,送到划片机进行划片。现在划片机都 是自动的,机器上配备激光或金钢石的划片刀具。切割分 部分划片(不划到底,留有残留厚度)和完全分割划片。 对于部分划片,用顶针顶力使芯片完全分离。划片时,边 缘或多或少会存在微裂纹和凹槽这取决于刀具的刃度。这 样会严重影响芯片的碎裂强度。
第二章 封装工艺流程
过去,TAB技术不受重视的原因: (1)TAB技术初始投资大; (2)开始时TAB工艺设备不易买到,而传统的引线工艺已 得到充分的发展,且其生产设备也容易买到; (3)有关TAB技术资料和信息少。但是随着芯片信息容量 及随之而来的引脚数的增加,传统的分立引线工艺显得力 不从心。为降低引线成本的需要,TAB技术越来越受到人 们的青睐,促使许多半导体厂家积极开发研究。
第二章 封装工艺流程
2.4.1 打线键合技术介绍 (1)超声波键合
优点: 键合点尺寸小,回 绕高度低,适合于键合 点间距小、密度高的芯 片连接。 缺点: 所有的连线必须沿 回绕方向排列(这不可 能),因此在连线过程 中要不断改变芯片与封 装基板的位置再进行第2 根引线的较之常用的引线工艺的优点: (1)对高速电路来说,常规的引线使用圆形导线,而且引线 较长,往往引线中高频电流的趋肤效应使电感增加,造成信号 传递延迟和畸变,这是十分不利的。TAB技术采用矩形截面的 引线,因而电感小,这是它的优点。 (2)传统引线工艺要求键合面积4mil2,而TAB工艺的内引线 键合面积仅为2mil2这样就可以增加I/O密度,适应超级计算机 与微处理器的更新换代。 (3)TAB技术中使用铜线而不使用铝线,从而改善器件的热耗 散性能。 (4)在芯片最终封装前可进行预测试和通电老化。这样可剔 除坏芯片,不使它流入下一道工序,从而节省了成本,提高了 可靠性。 (5)TAB工艺中引线的键合平面低,使器件薄化。