DCS系统概念及结构
DCS系统原理和结构
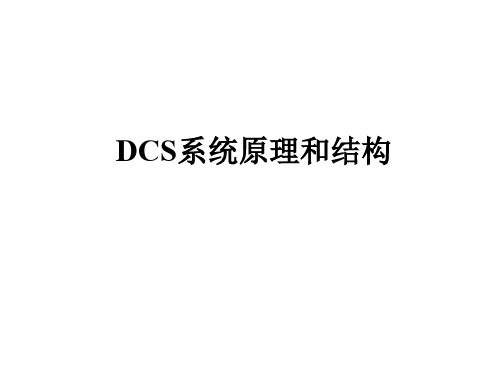
系统操作方便、显示直观,提供了装置运行下的可监视性。
控制功能齐全,控制算法丰富,连续控制、顺序控制和批量控制集 中于一体,还可实现串级、前馈、解耦和自适应等先进控制,提高了系 统的可控性。
2.5 在线性
•
通过人机接口和I/0接口,对过程对象的数据进行实时采集、
分析、记录、监视、操作控制,并包括对系统结构和组态回路的
在线修改、局部故障的在线维护等,提高了系统的可用性。
2.6 可靠性
•
高可靠性、高效率和高可用性是集散型控制系统的生命力所
在,制造厂商在确定系统结构的同时,进行可靠性设计,采用可
•
硬件和软件采用开放式、标准化和模块化设计,系统积木式
结构,具有灵活的配置,可适应不同用户的需要。
• 可根据生产要求,改变系统的大小配置,在工厂改变生产工 艺、生产流程时,只需要改变某些配置和控制方案。
• 以上的变化都不需要修改或重新开发软件,只是使用组态软 件,填写一些表格(或绘出控制组态图)即可实现。
2.DCS的主要特点
• 集散型控制系统是采用标准化、模块化和系列化设计,由过程控制级、 控制管理级和生产管理级所组成的一个以通信网络为纽带的集中显示操 作管理,控制相对分散,具有灵活配置、组态方便的多级计算机网络系 统结构。集散型控制系统具有以下的主要特点:
• 2.1.自主性
系统上各工作站是通过网络接口链接起来的,各工作站独立自主地完 成合理分配给自己的规定任务,如数据采集、处理、计算、监视、操作 和控制等。
DCS系统原理和结构
集散型(分布式)计算机控制系统简称集散型(分布式)控制系统 (Distributed Control System ),即我们通常说的DCS。
DCS的体系结构及构成
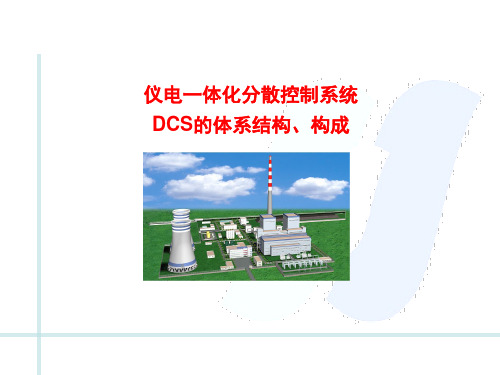
电气监控系统
• FSSS furnace safeguard supervisory system 炉膛安全监控系统
• BMS burner management system 燃烧器管理系统
• SOE sequence of event recorder 事件顺序记录仪
• MFT main fuel trip
4、热控常用术语缩写:
• DCS distributed control system
分散控制系统
• DAS data acquisition system
数据采集系统
• SCS sequence control system
顺序控制系统
• ECS electrical control system
工业总线I/OBus 10Mb/s Modbus+
现场总线F-Net 1Mb—10Mb/s IEC802.3u,第三方协议
信息管理级
中央监控级
过程控制级 现场设备级 传感器,执行器级
2.2 过程控制级 过程控制级主要由现场控制站DPU(Distributed Control Unit)和I/O数
据采集站构成。一般在电厂中,把现场控制站和数据采集站集中安装在位于主 控室后的电子设备室中。
•
逻辑加法器
•
High/Low Limiter
•
高/低限幅
•
Time Function Generator
•
时间函数发生器
•
High Selector
•
高选
•
Low Selector
•
低选
•
High Signal Limiter
•
DCS的基本结构及原理
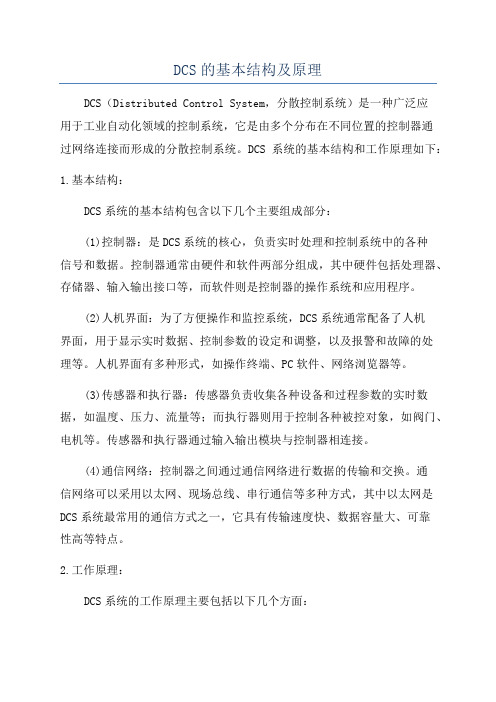
DCS的基本结构及原理DCS(Distributed Control System,分散控制系统)是一种广泛应用于工业自动化领域的控制系统,它是由多个分布在不同位置的控制器通过网络连接而形成的分散控制系统。
DCS系统的基本结构和工作原理如下:1.基本结构:DCS系统的基本结构包含以下几个主要组成部分:(1)控制器:是DCS系统的核心,负责实时处理和控制系统中的各种信号和数据。
控制器通常由硬件和软件两部分组成,其中硬件包括处理器、存储器、输入输出接口等,而软件则是控制器的操作系统和应用程序。
(2)人机界面:为了方便操作和监控系统,DCS系统通常配备了人机界面,用于显示实时数据、控制参数的设定和调整,以及报警和故障的处理等。
人机界面有多种形式,如操作终端、PC软件、网络浏览器等。
(3)传感器和执行器:传感器负责收集各种设备和过程参数的实时数据,如温度、压力、流量等;而执行器则用于控制各种被控对象,如阀门、电机等。
传感器和执行器通过输入输出模块与控制器相连接。
(4)通信网络:控制器之间通过通信网络进行数据的传输和交换。
通信网络可以采用以太网、现场总线、串行通信等多种方式,其中以太网是DCS系统最常用的通信方式之一,它具有传输速度快、数据容量大、可靠性高等特点。
2.工作原理:DCS系统的工作原理主要包括以下几个方面:(1)数据采集和处理:根据控制策略和设定参数,控制器通过输入输出模块从传感器和执行器中采集实时数据,并对其进行处理和分析。
(2)控制策略和算法:控制器根据设定的控制策略和算法,对采集到的数据进行逻辑运算和计算,生成相应的控制命令。
(3)信号传输和执行控制:生成的控制命令通过通信网络传输给执行器,执行器根据控制命令调整对应的工作状态,控制被控对象的运行。
(4)监控和调节:DCS系统通过人机界面实时显示各种参数和数据,并根据实际情况进行监控和调节。
当系统出现异常或故障时,系统会产生相应的报警信号,提醒操作员及时处理。
DCS的体系结构
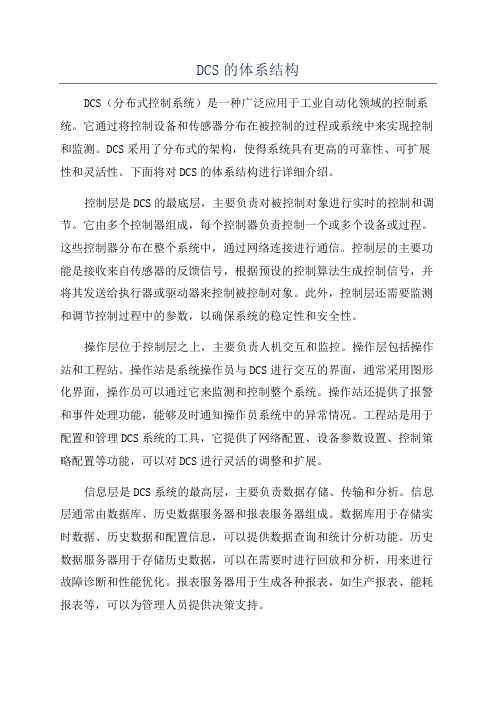
DCS的体系结构DCS(分布式控制系统)是一种广泛应用于工业自动化领域的控制系统。
它通过将控制设备和传感器分布在被控制的过程或系统中来实现控制和监测。
DCS采用了分布式的架构,使得系统具有更高的可靠性、可扩展性和灵活性。
下面将对DCS的体系结构进行详细介绍。
控制层是DCS的最底层,主要负责对被控制对象进行实时的控制和调节。
它由多个控制器组成,每个控制器负责控制一个或多个设备或过程。
这些控制器分布在整个系统中,通过网络连接进行通信。
控制层的主要功能是接收来自传感器的反馈信号,根据预设的控制算法生成控制信号,并将其发送给执行器或驱动器来控制被控制对象。
此外,控制层还需要监测和调节控制过程中的参数,以确保系统的稳定性和安全性。
操作层位于控制层之上,主要负责人机交互和监控。
操作层包括操作站和工程站。
操作站是系统操作员与DCS进行交互的界面,通常采用图形化界面,操作员可以通过它来监测和控制整个系统。
操作站还提供了报警和事件处理功能,能够及时通知操作员系统中的异常情况。
工程站是用于配置和管理DCS系统的工具,它提供了网络配置、设备参数设置、控制策略配置等功能,可以对DCS进行灵活的调整和扩展。
信息层是DCS系统的最高层,主要负责数据存储、传输和分析。
信息层通常由数据库、历史数据服务器和报表服务器组成。
数据库用于存储实时数据、历史数据和配置信息,可以提供数据查询和统计分析功能。
历史数据服务器用于存储历史数据,可以在需要时进行回放和分析,用来进行故障诊断和性能优化。
报表服务器用于生成各种报表,如生产报表、能耗报表等,可以为管理人员提供决策支持。
整个DCS系统的各个层次通过网络连接起来,形成一个完整的系统。
因为采用了分布式的架构,DCS具有很高的可靠性和可扩展性。
如果一些控制器或传感器发生故障,系统可以自动切换到备用设备,保证系统的正常运行。
此外,DCS还支持远程访问和管理,可以通过网络连接远程监控和控制系统,方便维护人员对系统进行远程配置和故障排查。
DCS系统原理和结构

DCS系统原理和结构DCS(分布式控制系统)是一种在工业过程控制领域中被广泛应用的自动化控制系统。
它的原理和结构是通过集中管理和控制分布在整个系统中的分散设备,实现对工业过程的自动化控制。
1.可分布性:DCS系统的设备分布在整个系统范围内,通过分布式的结构和网络连接,实现各个设备之间的信息交互和共享。
这种可分布性的特点使得DCS系统具备高度的灵活性和可扩展性。
2.分散性:DCS系统采用模块化的设计方式,将整个系统划分为多个功能模块,每个模块对应一个具体的任务。
这样可以降低系统的复杂性,提高系统的可靠性和可维护性。
3.高可用性:DCS系统采用冗余设计,通过多个相同的设备并行工作,保证系统在一些设备发生故障时能够自动切换到备用设备。
这种冗余设计可以降低系统的停机时间,提高系统的可用性。
4.分层结构:DCS系统采用分层的结构,将整个系统划分为多个层次,每个层次对应不同的功能和责任。
常见的DCS系统通常包括控制层、运行层、管理层和信息层。
控制层负责对过程进行实时监测和控制,运行层负责对过程进行计划和调度,管理层负责系统的管理和维护,信息层负责采集和存储过程数据。
5.数据共享:DCS系统通过网络连接将各个设备连接在一起,实现数据的共享和交换。
各个设备可以实时获取和传递数据,以便进行控制决策和调度操作。
这种数据共享的机制可以保证整个系统各个部分之间的协调和一致性。
硬件部分包括传感器、执行器、PLC(可编程逻辑控制器)、DCS控制器、通信模块等。
传感器用于将过程中的各种参数(温度、压力、流量等)转换为电信号,以便进行监测和控制。
执行器用于接收控制指令,并对过程进行调节和控制。
PLC是一种专用的计算机设备,负责对设备进行控制和监测。
DCS控制器是DCS系统的核心设备,负责整个系统的控制和管理。
通信模块用于设备之间的数据传输和通信。
软件部分包括操作系统、HMI(人机界面)、控制逻辑编程、数据存储等。
操作系统负责整个DCS系统的运行和管理。
DCS系统概念及结构
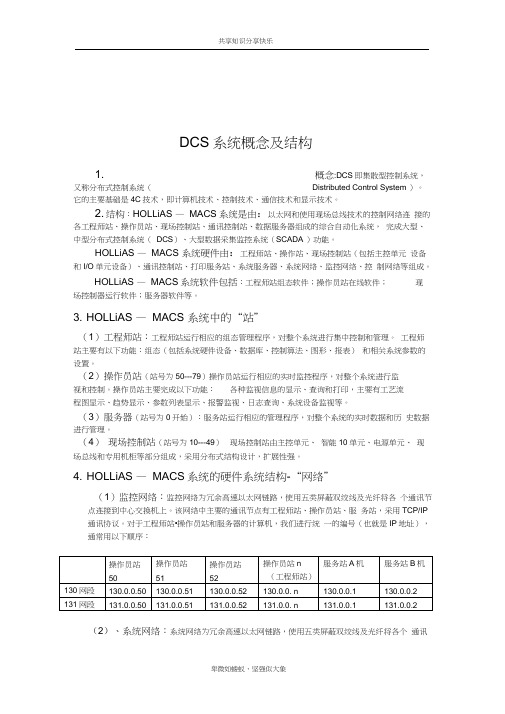
DCS系统概念及结构1. 概念:DCS即集散型控制系统,又称分布式控制系统(Distributed Control System )。
它的主要基础是4C技术,即计算机技术、控制技术、通信技术和显示技术。
2. 结构:HOLLiAS —MACS系统是由:以太网和使用现场总线技术的控制网络连接的各工程师站、操作员站、现场控制站、通讯控制站、数据服务器组成的综合自动化系统,完成大型、中型分布式控制系统(DCS)、大型数据采集监控系统(SCADA )功能。
HOLLiAS —MACS 系统硬件由:工程师站、操作站、现场控制站(包括主控单元设备和I/O单元设备)、通讯控制站、打印服务站、系统服务器、系统网络、监控网络、控制网络等组成。
HOLLiAS —MACS系统软件包括:工程师站组态软件;操作员站在线软件;现场控制器运行软件;服务器软件等。
3. HOLLiAS —MACS 系统中的“站”(1)工程师站:工程师站运行相应的组态管理程序,对整个系统进行集中控制和管理。
工程师站主要有以下功能:组态(包括系统硬件设备、数据库、控制算法、图形、报表)和相关系统参数的设置。
(2)操作员站(站号为50---79)操作员站运行相应的实时监控程序,对整个系统进行监视和控制。
操作员站主要完成以下功能:各种监视信息的显示、查询和打印,主要有工艺流程图显示、趋势显示、参数列表显示、报警监视、日志查询、系统设备监视等。
(3)服务器(站号为0开始):服务站运行相应的管理程序,对整个系统的实时数据和历史数据进行管理。
(4)现场控制站(站号为10---49)现场控制站由主控单元、智能10单元、电源单元、现场总线和专用机柜等部分组成,采用分布式结构设计,扩展性强。
4. HOLLiAS —MACS系统的硬件系统结构-“网络”(1)监控网络:监控网络为冗余高速以太网链路,使用五类屏蔽双绞线及光纤将各个通讯节点连接到中心交换机上。
该网络中主要的通讯节点有工程师站、操作员站、服务站,采用TCP/IP 通讯协议。
(完整版)DCS系统介绍
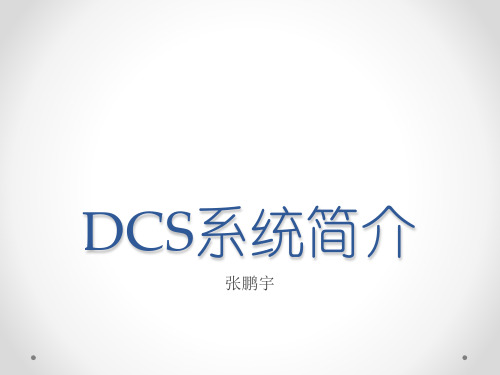
5.2 监控画面组态
5.3 工作站组态
• 用于监视控制显示画面及部分组态功能。
5.4 通讯组态
• 用于组态工作站,打印机及第三方控制器。
六、DCS的基础知识
• I/O信号 • 系统冗余 • DCS系统的特点
6.1 IO信号
• I/O:控制系统需要建立信号的输入和输出通道,这就是 I/O。DCS中的I/O一般是模块化的,一个I/O模块上有一 个或多个I/O通道,用来连接传感器和执行器。
2.2 1940~1970年
• 第三次科技革命开始后,随着计算机技术的发展,人们开 始尝试将计算机用于过程控制。但当时采用的办法是用一 台计算机控制几十甚至上百个回路,这样做的危险性很高, 如果计算机出现故障,会导致很严重的后果,这造成了危 险集中。
2.3 1970~1990年
• 直到上世纪70年代,随着计算机技术的日渐成熟,人们才 开始将危险分散。就是原来靠一台大计算机完成的任务, 现在用几十台微处理器来完成,从而大大降低了危险系数。 至此DCS就诞生了。
• 3.2管理级别分类:现场控制级、过程控制级、过程管理 级、经营管理级
• 3.3网络结构分类:一级网络、二级网络、三级网络
3.1硬件组成
3.2.1现场控制级
• 又称数据采集装置,主要是将过程非控变量进行数据采集 和预处理,而且对实时数据进一步加工处理,供操作站显 示和打印,从而实现开环监视,并将采集到的数据传输到 监控计算机。输出装置在有上位机的情况下,能以开关量 或者模拟量信号的方式,向终端元件输出计算机控制命令。 这一个级别直接面对现场,跟现场过程相连。比如阀门、 电机、各类传感器、变送器、执行机构等等。
3.2.2过程控制级
dcs的结构组成

dcs的结构组成【原创实用版】目录1.DCS 的定义和作用2.DCS 的结构组成部分3.DCS 的应用领域正文1.DCS 的定义和作用DCS,即分散控制系统,是一种应用于工业自动化领域的计算机控制系统。
其主要作用是实现对生产过程中的各个参数进行实时监控和调整,以确保生产过程的安全、稳定和高效运行。
DCS 具有较强的可靠性、开放性和易操作性,广泛应用于石油化工、电力、冶金、建材等各个工业领域。
2.DCS 的结构组成部分DCS 主要由以下几个部分组成:(1)控制器:DCS 的核心部分,负责对各个控制回路进行闭环控制。
控制器通常采用高档工业控制计算机,具有较高的运算速度和可靠性。
(2)I/O 板:负责与现场仪表和设备进行数据交换,采集模拟量和数字量信号,并将这些信号传输给控制器。
同时,I/O 板还能根据控制器发出的指令,对现场设备进行控制。
(3)操作站:DCS 的人机交互界面,提供给操作人员实时的数据监控、报警处理、设备控制等功能。
操作站通常采用触摸屏或鼠标键盘操作,界面友好,操作简便。
(4)通讯网络:负责各个部件之间的信息传输。
DCS 通常采用高速、可靠的工业以太网作为通讯网络,以保证数据传输的实时性和稳定性。
(5)现场仪表和设备:DCS 控制的对象,包括各种传感器、执行器、阀门等。
现场仪表和设备与 I/O 板通过信号线相连,共同构成了 DCS 的控制回路。
3.DCS 的应用领域DCS 在工业自动化领域具有广泛的应用,尤其在以下领域表现突出:(1)流程工业:如石油化工、化纤、化肥、制药等行业,DCS 能够实现对连续性生产过程的自动化控制,提高生产效率和产品质量。
(2)热能动力:如火电、核电、热力发电等,DCS 可以实现对锅炉、汽轮机等设备的监控和控制,确保能源供应的稳定和安全。
(3)冶金建材:如钢铁、有色金属、水泥等行业,DCS 可以实现对熔炼、轧制、窑炉等设备的自动化控制,降低生产成本,提高产品质量。
dcs分级结构
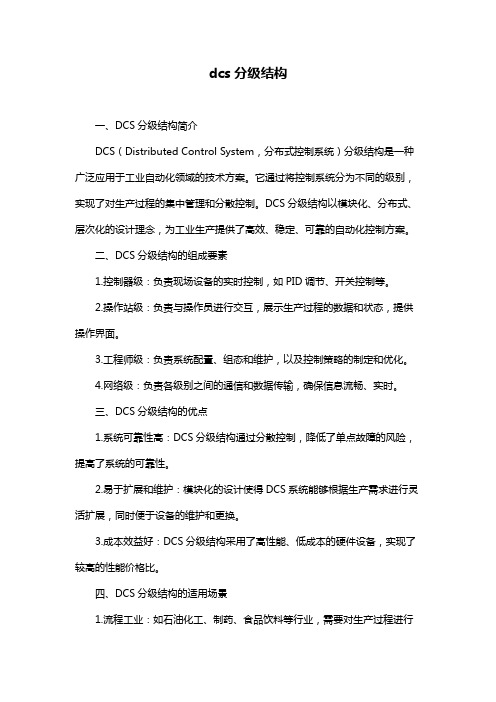
dcs分级结构一、DCS分级结构简介DCS(Distributed Control System,分布式控制系统)分级结构是一种广泛应用于工业自动化领域的技术方案。
它通过将控制系统分为不同的级别,实现了对生产过程的集中管理和分散控制。
DCS分级结构以模块化、分布式、层次化的设计理念,为工业生产提供了高效、稳定、可靠的自动化控制方案。
二、DCS分级结构的组成要素1.控制器级:负责现场设备的实时控制,如PID调节、开关控制等。
2.操作站级:负责与操作员进行交互,展示生产过程的数据和状态,提供操作界面。
3.工程师级:负责系统配置、组态和维护,以及控制策略的制定和优化。
4.网络级:负责各级别之间的通信和数据传输,确保信息流畅、实时。
三、DCS分级结构的优点1.系统可靠性高:DCS分级结构通过分散控制,降低了单点故障的风险,提高了系统的可靠性。
2.易于扩展和维护:模块化的设计使得DCS系统能够根据生产需求进行灵活扩展,同时便于设备的维护和更换。
3.成本效益好:DCS分级结构采用了高性能、低成本的硬件设备,实现了较高的性能价格比。
四、DCS分级结构的适用场景1.流程工业:如石油化工、制药、食品饮料等行业,需要对生产过程进行实时监控和控制。
2.离散制造:如汽车制造、电子制造等行业,适用于生产线自动化控制。
3.基础设施管理:如电力、水处理、燃气等行业,用于设施运行与维护管理。
五、如何选择合适的DCS分级结构1.确定应用需求:根据生产过程的复杂性、实时性、安全性等需求,选择适合的控制级别和功能。
2.评估系统性能要求:考虑控制器的处理速度、通信带宽、存储容量等性能指标。
3.考虑设备兼容性和投资成本:确保DCS系统与现有设备兼容,同时兼顾投资成本,实现经济效益最大化。
六、DCS分级结构的未来发展趋势1.智能化:借助人工智能技术,提高DCS系统的智能水平,实现更高效的自动化控制。
2.云计算与大数据应用:将DCS系统与云计算、大数据技术相结合,实现数据共享与分析,提升生产过程的管理水平。
DCS系统介绍

DCS 发展历史
第二阶段:1980—1985.,在这个时期集散控 制系统的技术特点表现为: 1)微处理器的位数提高,CRT显示器的分辨 率提高 2)强化的模块化系统 3)强化了系统信息管理,加强通信功能
DCS 发展历史
第三阶段,1985年以后,集散系统进入第三 代,其技术特点表现为: 1)采用开放系统管理 2)操作站采用32位微处理器 3)采用实时多用户多任务的操作系统
DCS 发展历史
第一阶段:1975-1980年,在这个时期集散控 制系统的技术特点表现为: 1)采用微处理器为基础的控制单元,实现 分散控制,有各种各样的算法,通过组态独立 完成回路控制,具有自诊断功能 2)采用带CRT显示器的操作站与过程单元分 离,实现集中监视,集中操作 3)采用较先进的冗余通信系统
DeltaV I/O Card Types
Outputs
- AO, 8 Channel, 4 to 20 mA, HART – AO, 8 Channel, 4 to 20 mA – I.S. AO, 8 Channel, 4 to 20 mA – DO, 8 Channel, 120/230 VAC, Isolated – DO, 8 Channel, 120/230 VAC, High Side – DO, 8 Channel, 24 VDC, Isolated – DO, 8 Channel, 24 VDC, High Side – High Density DO, 32 Channel, 24 VDC, High Side – I.S. DO, 4 Channel, 12 VDC I.S. Power
DCS 特点
1) 高可靠性。由于DCS将系统控制功能分散在各台计 算机上实现,系统结构采用容错设计,因此某一台计算 机出现的故障不会导致系统其他功能的丧失。此外,由 于系统中各台计算机所承担的任务比较单一,可以针对 需要实现的功能采用具有特定结构和软件的专用计算机, 从而使系统中每台计算机的可靠性也得到提高。 2) 开放性。DCS采用开放式,标准化、模块化和系列 化设计,系统中各台计算机采用局域网方式通信,实现 信息传输,当需要改变或扩充系统功能时,可将新增计 算机方便地连入系统通信网络或从网络中卸下,几乎不 影响系统其他计算机的工作。
DCS体系结构分析
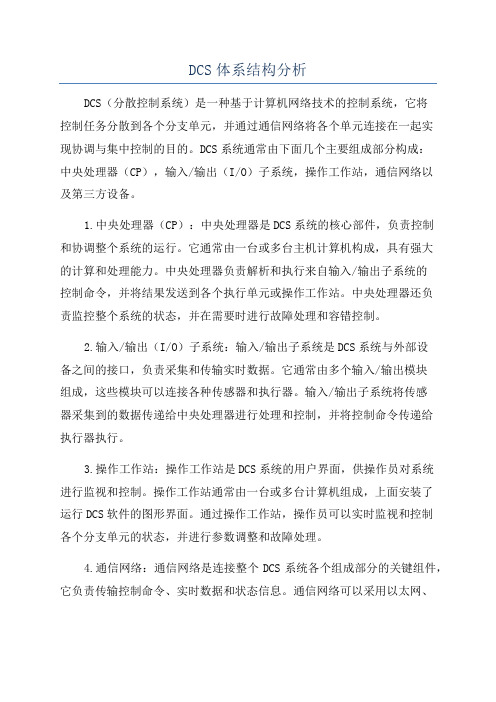
DCS体系结构分析DCS(分散控制系统)是一种基于计算机网络技术的控制系统,它将控制任务分散到各个分支单元,并通过通信网络将各个单元连接在一起实现协调与集中控制的目的。
DCS系统通常由下面几个主要组成部分构成:中央处理器(CP),输入/输出(I/O)子系统,操作工作站,通信网络以及第三方设备。
1.中央处理器(CP):中央处理器是DCS系统的核心部件,负责控制和协调整个系统的运行。
它通常由一台或多台主机计算机构成,具有强大的计算和处理能力。
中央处理器负责解析和执行来自输入/输出子系统的控制命令,并将结果发送到各个执行单元或操作工作站。
中央处理器还负责监控整个系统的状态,并在需要时进行故障处理和容错控制。
2.输入/输出(I/O)子系统:输入/输出子系统是DCS系统与外部设备之间的接口,负责采集和传输实时数据。
它通常由多个输入/输出模块组成,这些模块可以连接各种传感器和执行器。
输入/输出子系统将传感器采集到的数据传递给中央处理器进行处理和控制,并将控制命令传递给执行器执行。
3.操作工作站:操作工作站是DCS系统的用户界面,供操作员对系统进行监视和控制。
操作工作站通常由一台或多台计算机组成,上面安装了运行DCS软件的图形界面。
通过操作工作站,操作员可以实时监视和控制各个分支单元的状态,并进行参数调整和故障处理。
4.通信网络:通信网络是连接整个DCS系统各个组成部分的关键组件,它负责传输控制命令、实时数据和状态信息。
通信网络可以采用以太网、现场总线等各种标准协议。
通信网络需要具备高可靠性和实时性,以保证控制命令的实时性和准确性。
5.第三方设备:DCS系统通常与其他辅助设备和系统进行集成,例如数据库系统、报警系统、电力系统等。
这些第三方设备通过各种接口与DCS系统连接,实现数据共享和功能交互。
DCS体系结构的核心思想是将控制任务分散到各个单元,实现多级控制和分布式决策。
借助于中央处理器和通信网络的支持,DCS系统能够实现快速、准确的控制和协调,提高生产效率和质量,并具备灵活性和可扩展性。
DCS系统基础知识
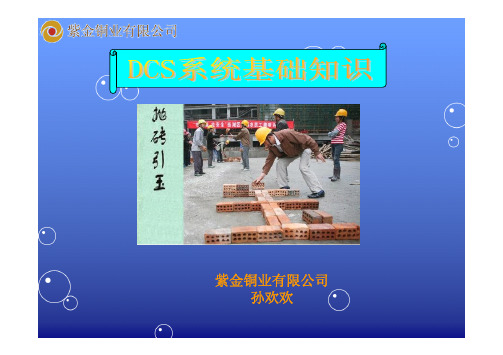
紫金铜业有限公司孙欢欢1.DCS系统的基本概念2.DCS系统的结构3.DCS系统的硬件4.DCS系统的软件5.DCS系统的操作DCS即集散型控制系统,又称分布式控制系统(Distributed Control System)。
DCS系统通过某种通信网络将分布在工业现场附近的现场控制站和控制中心的操作员站及工程师站等连接起来,以完成对现场生产设备的分散控制和集中操作管理。
DCS自1975年问世以来已经历了近三十年的时间,其可靠性、实用性不断提高,功能日益增强。
如控制器的处理能力、网络通讯能力、控制算法、画面显示及综合管理能力等。
DCS系统过去只应用在少数大型企业的控制系统中,但随着4C技术及软件技术的迅猛发展,到目前已经在电力、石油、化工、制药、冶金、建材等众多行业得到了广泛的应用,特别是电力、石化这样的行业。
右图以一个水位调节的例子简单地说明DCS 系统在实际生产中的应用过程:我们可以把上述过程引申如下:从整体上,可以将DCS系统分为硬件和软件两大部分。
硬件部分主要包括工程师站、操作员站、现场控制站(包括主控单元设备和I/O单元设备)、通讯控制站、系统服务器、网络等。
系统软件主要包括:工程师站组态软件、操作员站在线监控软件、现场控制器运行软件和服务器软件等。
HOLLIAS-MACS 系统的硬件体系结构:DeltaV系统的结构:DCS系统的硬件主要包括:1.现场控制站:电源模块、主控单元、各种I/O卡件和功能模块(DI卡、DO卡、AI卡、AO卡和各种通讯卡);2.工程师站、操作员站;3.通讯网络:控制网络、监控网络和系统网络;4.通讯控制站、系统服务器等;右图是DeltaV 系统的部分硬件:电源模块右图是西门子DCS系统的现,场控制站:S7-400(CPU)通讯控制器电源模块网关I/O卡件右图是和利控制器时DCS系统的现场控制站:电源模块I/O卡件DCS系统的软件主要包括:1.工程师站组态软件;2.操作员站在线监控软件;3.现场控制器运行软件;4.服务器软件。
什么是DCS系统
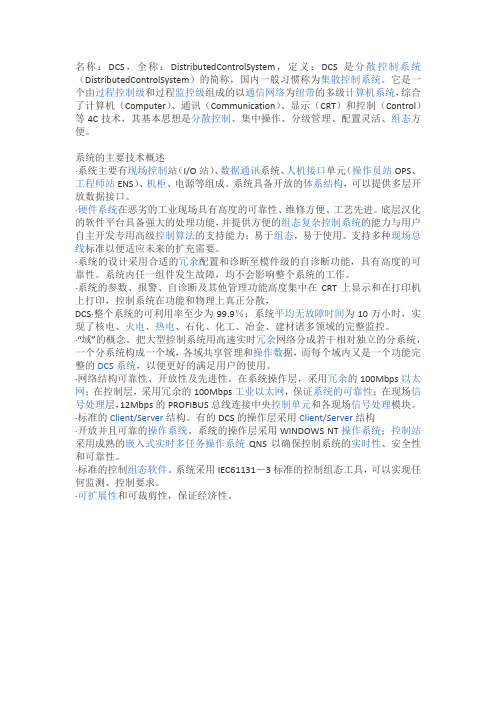
名称:DCS,全称:DistributedControlSystem,定义:DCS是分散控制系统(DistributedControlSystem)的简称,国内一般习惯称为集散控制系统。
它是一个由过程控制级和过程监控级组成的以通信网络为纽带的多级计算机系统,综合了计算机(Computer)、通讯(Communication)、显示(CRT)和控制(Control)等4C技术,其基本思想是分散控制、集中操作、分级管理、配置灵活、组态方便。
系统的主要技术概述·系统主要有现场控制站(I/O站)、数据通讯系统、人机接口单元(操作员站OPS、工程师站ENS)、机柜、电源等组成。
系统具备开放的体系结构,可以提供多层开放数据接口。
·硬件系统在恶劣的工业现场具有高度的可靠性、维修方便、工艺先进。
底层汉化的软件平台具备强大的处理功能,并提供方便的组态复杂控制系统的能力与用户自主开发专用高级控制算法的支持能力;易于组态,易于使用。
支持多种现场总线标准以便适应未来的扩充需要。
·系统的设计采用合适的冗余配置和诊断至模件级的自诊断功能,具有高度的可靠性。
系统内任一组件发生故障,均不会影响整个系统的工作。
·系统的参数、报警、自诊断及其他管理功能高度集中在CRT上显示和在打印机上打印,控制系统在功能和物理上真正分散,DCS·整个系统的可利用率至少为99.9%;系统平均无故障时间为10万小时,实现了核电、火电、热电、石化、化工、冶金、建材诸多领域的完整监控。
·“域”的概念。
把大型控制系统用高速实时冗余网络分成若干相对独立的分系统,一个分系统构成一个域,各域共享管理和操作数据,而每个域内又是一个功能完整的DCS系统,以便更好的满足用户的使用。
·网络结构可靠性、开放性及先进性。
在系统操作层,采用冗余的100Mbps以太网;在控制层,采用冗余的100Mbps工业以太网,保证系统的可靠性;在现场信号处理层,12Mbps的PROFIBUS总线连接中央控制单元和各现场信号处理模块。
DCS控制系统

第三章 DCS的控制站
功能 控制站是DCS的核心,直接与生产过程的 信号传感器,变送器和执行器连接,具有 信号输入,输出,运算,控制和通信功能
DCS控制站硬件
◆输入输出单元(IOU) 直接与生产过程的输入输出信号连接,主要 由输入输出处理器板(IOP),信号调理板和端 子板(FTA)组成. ◆过程控制单元(PCU) 是控制站的核心,主要由控制处理器,输入 输出接口处理器,通信处理器和冗余处理器组成. 一般都有两个PCU,互为冗余热备用,具有自动诊 断和自动切换功能. ◆电源:一般都有两个电源,互为冗余
DCS的主要特点 的主要特点
(4)适应性,灵活性和易扩展性 DCS硬件采用积木式结构,可灵活配置成小,中,大 各类系统,还可根据生产要求,逐步扩展系统,改变系统 配置. 软件采用模块化设计,提供各类功能模块,可灵活组 态. (5)自治性和协调性 DCS自治性是指系统中各个控制站,操作站均可独立 地工作. DCS协调性指系统中各台计算机用通信网络互连在一 起,相互传送信息,相互协调工作. (6)界面友好性
DCS工程师站
DCS的工程师站功能 工程师站的主要功能就是组态,建立 DCS系统,控制系统和人机界面. ★作为DCS控制工程师的人机界面,工程师 站组态的主要内容包括系统设备组态,控 制功能组态和操作画面组态
�
集散控制系统( 第二篇 集散控制系统(DCS) )
第一章 DCS概述 第二章 DCS的体系结构 第三章 DCS的控制站 第四章 DCS的操作站和工程师站
第一章 DCS概述
概念 DCS(Distributed Control System)分散控 制系统,也称集散控制系统.是以应用微处 理器为基础,结合计算机技术,信号处理技 术,测量控制技术,通信网络技术和人机接 口技术,实现过程控制和工厂管理的控制系 统. 也可以说综ห้องสมุดไป่ตู้了计算机(Computer),通信 (Communication),屏幕显示(CRT)和 控制(Control)技术,简称"4C"技术.
集散控制系统(DCS)
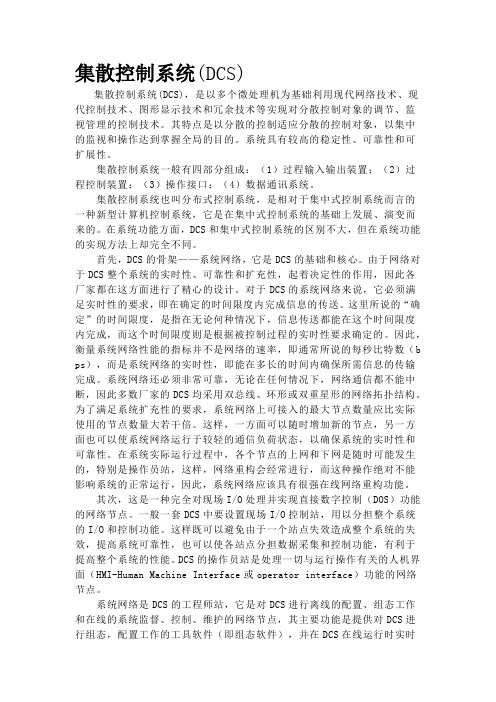
集散控制系统(DCS)集散控制系统(DCS),是以多个微处理机为基础利用现代网络技术、现代控制技术、图形显示技术和冗余技术等实现对分散控制对象的调节、监视管理的控制技术。
其特点是以分散的控制适应分散的控制对象,以集中的监视和操作达到掌握全局的目的。
系统具有较高的稳定性、可靠性和可扩展性。
集散控制系统一般有四部分组成:(1)过程输入输出装置;(2)过程控制装置;(3)操作接口;(4)数据通讯系统。
集散控制系统也叫分布式控制系统,是相对于集中式控制系统而言的一种新型计算机控制系统,它是在集中式控制系统的基础上发展、演变而来的。
在系统功能方面,DCS和集中式控制系统的区别不大,但在系统功能的实现方法上却完全不同。
首先,DCS的骨架——系统网络,它是DCS的基础和核心。
由于网络对于DCS整个系统的实时性、可靠性和扩充性,起着决定性的作用,因此各厂家都在这方面进行了精心的设计。
对于DCS的系统网络来说,它必须满足实时性的要求,即在确定的时间限度内完成信息的传送。
这里所说的“确定”的时间限度,是指在无论何种情况下,信息传送都能在这个时间限度内完成,而这个时间限度则是根据被控制过程的实时性要求确定的。
因此,衡量系统网络性能的指标并不是网络的速率,即通常所说的每秒比特数(b ps),而是系统网络的实时性,即能在多长的时间内确保所需信息的传输完成。
系统网络还必须非常可靠,无论在任何情况下,网络通信都不能中断,因此多数厂家的DCS均采用双总线、环形或双重星形的网络拓扑结构。
为了满足系统扩充性的要求,系统网络上可接入的最大节点数量应比实际使用的节点数量大若干倍。
这样,一方面可以随时增加新的节点,另一方面也可以使系统网络运行于较轻的通信负荷状态,以确保系统的实时性和可靠性。
在系统实际运行过程中,各个节点的上网和下网是随时可能发生的,特别是操作员站,这样,网络重构会经常进行,而这种操作绝对不能影响系统的正常运行,因此,系统网络应该具有很强在线网络重构功能。
DCS系统原理和结构

DCS系统原理和结构DCS系统(分布式控制系统)是一种用于控制工业过程的计算机系统。
它通过多个分散的控制器和数据采集设备组成,实现对工业过程的自动化控制。
DCS系统通常由下面几个部分构成:中央控制器、工作站、输入/输出模块、通信网络和现场设备。
1.中央控制器:中央控制器是DCS系统的核心。
它负责接收从工作站或其他控制器发送的指令,并对所控制的设备进行控制。
中央控制器通常由一台或多台工控机组成,可以通过各种通信协议与其他设备进行通信。
2.工作站:工作站是DCS系统的操作界面,用于设置和监控控制系统。
工作站通常由一台或多台高性能计算机组成,提供人机界面,使操作人员可以方便地对过程进行控制和监测。
3.输入/输出模块:输入/输出模块是DCS系统与现场设备之间的接口。
它负责将来自现场传感器的信号转换为数字信号,并将数字信号转换为控制信号发送给执行器。
输入/输出模块通常由数字量输入模块、模拟量输入模块、数字量输出模块和模拟量输出模块组成。
4.通信网络:通信网络是DCS系统中各个组件之间进行数据传输的介质。
它通常由以太网、现场总线和串行接口等组成,用于实现控制系统中数据的交换和共享。
通过通信网络,DCS系统可以实现分布式控制,使各个控制设备之间可以进行数据共享和协作。
5.现场设备:现场设备是指DCS系统中需要进行控制的各种设备,包括传感器、执行器等。
传感器负责将现场的物理量转换为电信号输入给输入/输出模块,执行器根据输入控制信号执行相应的动作。
现场设备的种类和数量根据具体的工业过程和控制需求而定。
1.数据采集:DCS系统通过连接各种传感器和执行器,实时采集现场设备的状态和操作数据。
2.数据处理和控制算法:中央控制器接收到采集到的数据后,会进行数据处理和控制算法的计算。
控制算法根据设定的控制目标和现场数据,计算出相应的控制策略和控制信号。
3.控制信号输出:经过计算后的控制信号将通过通信网络发送给相应的执行器,执行器根据控制信号进行相应的操作。
dcs的结构组成

dcs的结构组成【原创实用版】目录1.DCS 的定义与应用2.DCS 的结构组成3.DCS 的主要功能4.DCS 的发展趋势正文1.DCS 的定义与应用分布式控制系统(Distributed Control System,简称 DCS)是一种计算机控制系统,广泛应用于工业生产过程、设备运行管理等领域。
DCS 通过将控制功能分散到各个子系统,实现对整个工艺过程的集中监控、操作和管理。
相较于传统的集中式控制系统,DCS 具有更高的可靠性、实时性和灵活性。
2.DCS 的结构组成DCS 的结构组成主要包括以下几个方面:(1)管理层:管理层主要包括操作员站、工程师站和主管站。
操作员站负责实时监控生产过程,工程师站负责系统配置和维护,主管站则负责对整个系统的运行进行监督和管理。
(2)控制层:控制层主要包括各种控制模块、PID 控制器和逻辑控制器。
控制模块负责实现对现场设备的实时控制,PID 控制器负责对控制过程进行调节,逻辑控制器则负责实现各种复杂的控制逻辑。
(3)现场设备层:现场设备层主要包括各种传感器、执行器和现场总线设备。
传感器负责采集现场数据,执行器负责实现对设备的动作控制,现场总线设备则负责实现各个设备之间的数据通信。
3.DCS 的主要功能DCS 的主要功能包括:实时控制、过程监控、报警管理、数据记录、趋势分析、设备维护等。
通过这些功能,DCS 能够实现对整个生产过程的自动化管理,提高生产效率和产品质量。
4.DCS 的发展趋势随着科技的不断发展,DCS 也在不断地更新换代。
未来的 DCS 将更加智能化、网络化和一体化。
具体表现在以下几个方面:(1)智能化:未来的 DCS 将具备更强大的人工智能,能够自主学习和优化控制策略。
(2)网络化:DCS 将与企业内部的其他信息系统实现无缝集成,实现数据的共享和交流。
(3)一体化:DCS 将与生产设备的设计、制造和运行等环节实现紧密结合,形成一个完整的产业链。
DCS系统概念及结构
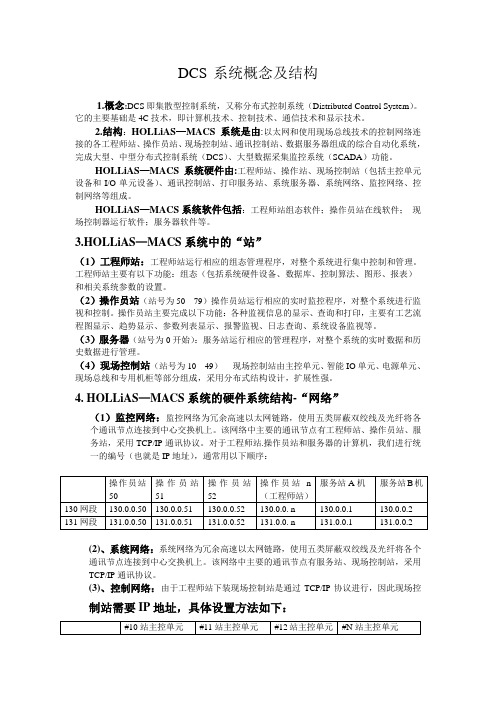
DCS 系统概念及结构1.概念:DCS即集散型控制系统,又称分布式控制系统(Distributed Control System)。
它的主要基础是4C技术,即计算机技术、控制技术、通信技术和显示技术。
2.结构:HOLLiAS—MACS系统是由:以太网和使用现场总线技术的控制网络连接的各工程师站、操作员站、现场控制站、通讯控制站、数据服务器组成的综合自动化系统,完成大型、中型分布式控制系统(DCS)、大型数据采集监控系统(SCADA)功能。
HOLLiAS—MACS系统硬件由:工程师站、操作站、现场控制站(包括主控单元设备和I/O单元设备)、通讯控制站、打印服务站、系统服务器、系统网络、监控网络、控制网络等组成。
HOLLiAS—MACS系统软件包括:工程师站组态软件;操作员站在线软件;现场控制器运行软件;服务器软件等。
3.HOLLiAS—MACS系统中的“站”(1)工程师站:工程师站运行相应的组态管理程序,对整个系统进行集中控制和管理。
工程师站主要有以下功能:组态(包括系统硬件设备、数据库、控制算法、图形、报表)和相关系统参数的设置。
(2)操作员站(站号为50---79)操作员站运行相应的实时监控程序,对整个系统进行监视和控制。
操作员站主要完成以下功能:各种监视信息的显示、查询和打印,主要有工艺流程图显示、趋势显示、参数列表显示、报警监视、日志查询、系统设备监视等。
(3)服务器(站号为0开始):服务站运行相应的管理程序,对整个系统的实时数据和历史数据进行管理。
(4)现场控制站(站号为10---49)现场控制站由主控单元、智能IO单元、电源单元、现场总线和专用机柜等部分组成,采用分布式结构设计,扩展性强。
4. HOLLiAS—MACS系统的硬件系统结构-“网络”(1)监控网络:监控网络为冗余高速以太网链路,使用五类屏蔽双绞线及光纤将各个通讯节点连接到中心交换机上。
该网络中主要的通讯节点有工程师站、操作员站、服务站,采用TCP/IP通讯协议。
DCS系统原理和结构

DCS系统原理和结构DCS系统(Distributed Control Systems)是一种用于工业自动化控制的系统,用于监测和控制生产过程中的各种参数和设备。
它由一系列连接在一起的分布式控制器组成,这些控制器可以独立工作,同时又可以相互通信,形成一个整体系统。
DCS系统的原理和结构是其运行和功能的基础,下面将详细介绍。
1.数据采集:DCS系统通过连接各种传感器、执行器等设备,实时采集生产过程中的各种参数数据,如温度、压力、流量等。
这些数据被传输到控制器中进行处理。
2.数据处理:控制器接收到采集的数据后,进行处理分析,根据预设的控制策略和算法,生成控制命令,并将其发送给执行器,调节系统的状态。
3.控制:控制器根据接收到的数据进行控制,维持系统在设定的工作状态,确保生产过程稳定运行。
4.通信:DCS系统通过网络连接各个控制器,实现信息的共享和互通,从而实现全系统的集中监控和控制。
1.控制器:控制器是DCS系统的核心部件,通常由主控制器和分散控制器组成。
主控制器负责整个系统的整体控制和监控,而分散控制器负责对具体的设备和过程进行控制。
2.I/O模块:I/O模块是连接控制器和各种传感器、执行器的接口设备,负责采集和输出数据。
它将传感器采集到的信号转换为数字信号,并发送给控制器进行处理。
3.通信网络:通信网络是连接各个控制器和外部设备的媒介,通常采用以太网、现场总线等通信协议。
它实现了各个控制器之间的数据传输和共享。
4.人机界面:人机界面是工程师和操作人员与DCS系统交互的窗口,通常包括监控屏幕、操作面板等设备。
通过人机界面,操作人员可以对系统进行监控和控制。
5.数据存储设备:数据存储设备用于记录和保存系统运行过程中的数据,例如历史数据、故障记录等。
这些数据可以用于分析系统运行状态和优化控制策略。
总的来说,DCS系统是一个由多个控制器组成的分布式自动化控制系统,采用数据采集、处理、控制和通信等原理实现对生产过程的监控和控制。
- 1、下载文档前请自行甄别文档内容的完整性,平台不提供额外的编辑、内容补充、找答案等附加服务。
- 2、"仅部分预览"的文档,不可在线预览部分如存在完整性等问题,可反馈申请退款(可完整预览的文档不适用该条件!)。
- 3、如文档侵犯您的权益,请联系客服反馈,我们会尽快为您处理(人工客服工作时间:9:00-18:30)。
DCS 系统概念及结构1.概念:DCS即集散型控制系统,又称分布式控制系统(Distributed Control System)。
它的主要基础是4C技术,即计算机技术、控制技术、通信技术和显示技术。
2.结构:HOLLiAS—MACS系统是由:以太网和使用现场总线技术的控制网络连接的各工程师站、操作员站、现场控制站、通讯控制站、数据服务器组成的综合自动化系统,完成大型、中型分布式控制系统(DCS)、大型数据采集监控系统(SCADA)功能。
HOLLiAS—MACS系统硬件由:工程师站、操作站、现场控制站(包括主控单元设备和I/O单元设备)、通讯控制站、打印服务站、系统服务器、系统网络、监控网络、控制网络等组成。
HOLLiAS—MACS系统软件包括:工程师站组态软件;操作员站在线软件;现场控制器运行软件;服务器软件等。
3.HOLLiAS—MACS系统中的“站”(1)工程师站:工程师站运行相应的组态管理程序,对整个系统进行集中控制和管理。
工程师站主要有以下功能:组态(包括系统硬件设备、数据库、控制算法、图形、报表)和相关系统参数的设置。
(2)操作员站(站号为50---79)操作员站运行相应的实时监控程序,对整个系统进行监视和控制。
操作员站主要完成以下功能:各种监视信息的显示、查询和打印,主要有工艺流程图显示、趋势显示、参数列表显示、报警监视、日志查询、系统设备监视等。
(3)服务器(站号为0开始):服务站运行相应的管理程序,对整个系统的实时数据和历史数据进行管理。
(4)现场控制站(站号为10---49)现场控制站由主控单元、智能IO单元、电源单元、现场总线和专用机柜等部分组成,采用分布式结构设计,扩展性强。
4. HOLLiAS—MACS系统的硬件系统结构-“网络”(1)监控网络:监控网络为冗余高速以太网链路,使用五类屏蔽双绞线及光纤将各个通讯节点连接到中心交换机上。
该网络中主要的通讯节点有工程师站、操作员站、服务站,采用TCP/IP通讯协议。
对于工程师站.操作员站和服务器的计算机,我们进行统一的编号(也就是IP地址),通常用以下顺序:(2)、系统网络:系统网络为冗余高速以太网链路,使用五类屏蔽双绞线及光纤将各个通讯节点连接到中心交换机上。
该网络中主要的通讯节点有服务站、现场控制站,采用TCP/IP通讯协议。
(3)、控制网络:由于工程师站下装现场控制站是通过TCP/IP协议进行,因此现场控制站需要IP地址,具体设置方法如下:HOLLiAS—MACS系统的硬件介绍FM801 主控单元主控单元是现场控制站的中央处理单元,主要承担本站的部分信号处理、控制运算、与上位机及与上位机及其它单元的通讯等任务。
它是一个与PC兼容的高性能的工业级中央处理单元,采用模块化结构,主控单元可以热备份方式冗余使用,在出现故障时能够自动无扰切换,并保证不会丢失数据。
拨码开关的设置:从下到上依次是第1—6位,用于设置主控单元站号,ON为0,OFF 为1,对于双机系统,两个拨码开关要设成一致。
换算方法如下:站号=20*K1+21*K2+22*K3+23*K4+24*K5+25*K6其中,Ki=0表示第I位的开关拨到ON位置,Ki=1表示第i位的开关拨到OFF位置。
FM910、FM920电源模块电源单元为单元式模块化结构,用来对现场控制站的主控单元、I/O模块及现场仪表供电,可构成无扰切换的冗余配电方式。
输出电压为DC24V或DC48VFM300、FM301机笼单元机笼单元是主控单元FM801和电源模块FM910、FM920的安装机笼,实现主控单元、电源模块的冗余配置和电源模块间的均流。
主从冗余的两个FM801和冗余联用的电源模块FM910、FM920插在机笼单元的相应槽位中,形成一个完整的冗余控制结构。
FM131A 端子模块FM131A 端子模块是与常规IO模块搭配使用的端子模块,实现功能模块与现场信号的连接。
拨码开关可以灵活简便地设置站地址,支持多个模块级联和DP 终端匹配器的挂接。
模块设有防混销,可以有效防止不同的功能模块与FM131A 底座模块的混装组合。
地址拨码开关的设置:按照预定的模块通讯地址的二进制值设定底座上的8 位拨码开关,当拨码开关的某位置于ON时,对应位的二进制值为0,置于OFF 则为1。
拨码开关的低位对应于模块地址二进制值的低位。
FM143 8路热电阻输入模块FM143型模块是智能型8路热电阻模拟量输入模块,是HollySys公司采用目前世界上先进的现场总线技术(ProfiBus-DP总线)而新开发的热电阻模拟量输入模块。
通过与配套的底座FM131A连接,用于处理从现场来的热电阻输入信号。
注:En、Sn 表示电阻式温度传感器的两端引线的接入端(n=0~7);Cn 表示电阻式温度传感器的一端引线的公共线的接入端(n=0~7);FM148A 8路大信号输入模块FM148A型模块是智能型8路大信号模拟量输入模块,通过与配套的端子底座FM131A 连接,用于处理从现场来的0~10V范围内的电压信号和0~20mA范围内的电流信号。
FM148A 端子信号的接线要求每路信号采用两根导线+24V (屏蔽电缆)接到FM131A 的端子上。
针对不同类型的信号和供电情况的不同,有三种端子接线方式:二线制电流信号的接线、四线制电流信号的接线、电压信号的接线FM151A 8路模拟量输出模块FM151A型模块是智能型8路4~20mA模拟量输出模块,是HollySys公司采用目前世界上先进的现场总线技术(ProfiBus-DP总线)而新开发的模拟量输出模块。
通过与配套的端子底座FM131A连接,输出8路4~20mA的电流信号。
FM161D 16路开关量输入模块FM161D型模块是智能型16路普通DI输入模块,是HollySys公司采用目前世界上先进的现场总线技术(ProfiBus-DP总线)而新开发的DI信号输入模块。
通过与配套的底座FM131A 连接,用于处理从现场来的触点型开关量输入信号,触点查询电压24VDC。
FM171 16路开关量输出模块FM171型模块是智能型16路继电器开关量输出模块,是HollySys公司采用目前世界上先进的现场总线技术(ProfiBus-DP总线)而新开发的DO信号输出模块。
通过与配套的底座FM131A、FM131-C、FM131-D连接,用于给现场提供无源触点型开关量输出信号,从而控制现场设备的开/关、启/停。
FM171 模块可以与FM131A 底座之间依靠64 针欧式连接器连接每路通道的输出信号通过FM131A 的接线端子硬接线到中间继电器构成完整I/O 单元FM171 模块还可以与FM131-C 连接再通过中间继电器端子板(FM137系列)从而构成完整的I/O 单元FM171 模块还可以与FM131-D 连接再通过中间继电器端子板(FM138系列)从而构成完整的I/O 单元FM192-TR DP总线终端匹配器模块FM192-TR DP总线终端匹配器是为FM系列硬件系统配套设计的,用于DP总线终端匹配。
模块为24VDC供电,利用电阻消除信号不匹配,以克服干扰,提高通讯质量。
它是与FM 系列硬件系统的I/O模块配套的一种产品。
PROFIBUS-DP重复器在FM系列硬件系统中的使用西门子公司的DP重复器视PROFIBUS-DP现场总线网络结构中的重要模块,它主要用于下列目的:*拓展总线的物理长度*改变总线的拓扑结构*增加总线的节点数目*两段总线间的关断与隔离MACSV系统软件介绍及组态实施过程一.MACSV系统软件主要包括:组态软件.操作员站软件.服务器软件和控制站软件1.组态软件包括:数据库总控.设备组态.服务器算法组态.控制器算法组态.报表组态.图形组态.工程师在线下装等组成。
2.操作员在线软件是安装在操作员站上,它完成拥护对于人机交互界面的监控。
3.服务器软件是安装在服务器上的,它完成对系统实时.历史数据的采集管理和监视,并为各站的数据请求提供服务。
4.控制站软件是安装在现场控制站中的主控单元中的,它完成数据采集.转换.控制运算等。
二.MACSV系统组态软件的组态实施过程1.新建工程(数据库总控)2.硬件设置(设备组态)3.数据库定义(数据库总控)4.服务器控制算法组态(服务器算法组态)5.控制器算法工程生成(数据库总控)6.控制器控制算法组态(控制器算法组态)7.制作报表(报表组态)8.绘制图形(图形组态)9.生成下装工程文件(数据库总控)10.登陆控制器.将工程下装到主控单元(控制器算法)11.下装服务器.操作员站(工程师在线下装)12.运行程序并在线调试三MACSV系统组态软件的介绍1.数据库总控:数据库总控组态软件是由三部分组成:数据库总控.数据库编辑.控制表编辑,其中在数据库编辑中我们最常用的点名为AI模拟量输入.AO模拟量输出.DI 开关量输入.DO开关量输出。
2.设备组态:设备组态分为系统设备组态和IO设备组态,系统设备组态是完成系统网和监控网上各网络设备的硬件配置,IO设备组态是以现场控制站为单位来完成每个站的IO单元配置。
3.服务器算法组态:服务器算法组态是用来编制服务器算法程序的,4.控制器算法组态:控制器算法组态的核心:创建程序型POU,采用合适的POU语言(一般CFC或FBD)编写它的运算内容,在编程时,对变量进行数据读.写操作,用变量传递运算结果,将某些变量值送到输出模块去作为控制现场设备动作的指令,或者不输出变量而将变量值传递到上层操作员站监控用。
(1)各类POU之间是可以调用的,调用关系为:程序可以调用功能块和函数;功能块可以调用功能块和函数;函数可以调用函数;需说明的是程序可以调用程序。
POU可以用六种编程语言,有FBD.CFC.LD.ST.IL.SFC,其中重点掌握FBD和CFC。
(2)POU的触发:可以通过任务配置触发POU或者用已触发的POU调用要被触发的POU。
(3)控制器算法支持的运算符有:ADD加法运算.MUL乘法运算.SUB减法运算.DIV除法运算.AND逻辑与运算.OR逻辑或运算.XOR异或运算.NOT逻辑非运算.SEL二选一运算.MAX两个取其最大值.MIN两个取其最小值.GT大于逻辑运算符.LT小于逻辑运算符.LE小于等于逻辑运算符.GE大于等于逻辑运算符.EQ相等逻辑运算符。
5.图形组态:图形组态软件是MACS系统生成应用系统所需的各种总貌图.流程图和工况图,通过图形,操作员可以对现场情况一目了然。
工业控制系统流程图形包括静态图形和动态图形。
6.工程师在线下装:下装是把控制方案文件从工程师站传送到主控单元.服务器和各操作员站的过程,下装主控单元时有两种下装:初始化下装和无扰下装。
7.报表组态:报表组态软件需要和EXCEL配合使用,利用EXCEL提供的各种功能,设定表格格式,在单元格中录入说明性文字,然后利用报表组态软件设置动态点,完成报表的编辑。