分馏系统工艺流程及操作要点77页PPT
焦化反应分馏部分工艺流程说明
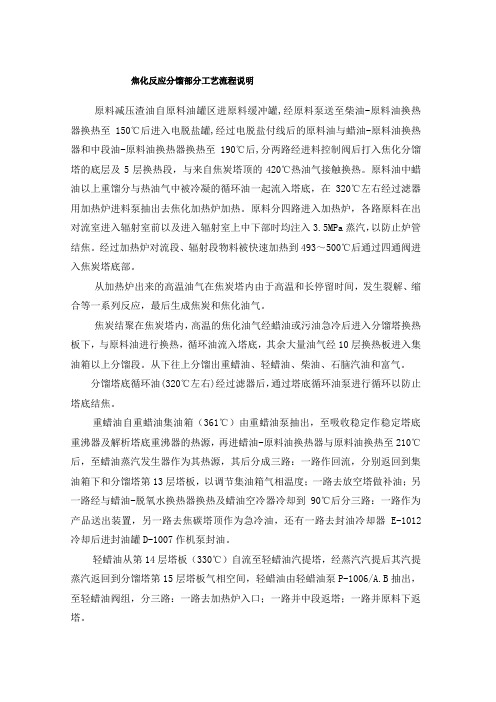
焦化反应分馏部分工艺流程说明原料减压渣油自原料油罐区进原料缓冲罐,经原料泵送至柴油-原料油换热器换热至150℃后进入电脱盐罐,经过电脱盐付线后的原料油与蜡油-原料油换热器和中段油-原料油换热器换热至190℃后,分两路经进料控制阀后打入焦化分馏塔的底层及5层换热段,与来自焦炭塔顶的420℃热油气接触换热。
原料油中蜡油以上重馏分与热油气中被冷凝的循环油一起流入塔底,在320℃左右经过滤器用加热炉进料泵抽出去焦化加热炉加热。
原料分四路进入加热炉,各路原料在出对流室进入辐射室前以及进入辐射室上中下部时均注入3.5MPa蒸汽,以防止炉管结焦。
经过加热炉对流段、辐射段物料被快速加热到493~500℃后通过四通阀进入焦炭塔底部。
从加热炉出来的高温油气在焦炭塔内由于高温和长停留时间,发生裂解、缩合等一系列反应,最后生成焦炭和焦化油气。
焦炭结聚在焦炭塔内,高温的焦化油气经蜡油或污油急冷后进入分馏塔换热板下,与原料油进行换热,循环油流入塔底,其余大量油气经10层换热板进入集油箱以上分馏段。
从下往上分馏出重蜡油、轻蜡油、柴油、石脑汽油和富气。
分馏塔底循环油(320℃左右)经过滤器后,通过塔底循环油泵进行循环以防止塔底结焦。
重蜡油自重蜡油集油箱(361℃)由重蜡油泵抽出,至吸收稳定作稳定塔底重沸器及解析塔底重沸器的热源,再进蜡油-原料油换热器与原料油换热至210℃后,至蜡油蒸汽发生器作为其热源,其后分成三路:一路作回流,分别返回到集油箱下和分馏塔第13层塔板,以调节集油箱气相温度;一路去放空塔做补油;另一路经与蜡油-脱氧水换热器换热及蜡油空冷器冷却到90℃后分三路:一路作为产品送出装置,另一路去焦碳塔顶作为急冷油,还有一路去封油冷却器E-1012冷却后进封油罐D-1007作机泵封油。
轻蜡油从第14层塔板(330℃)自流至轻蜡油汽提塔,经蒸汽汽提后其汽提蒸汽返回到分馏塔第15层塔板气相空间,轻蜡油由轻蜡油泵P-1006/A.B抽出,至轻蜡油阀组,分三路:一路去加热炉入口;一路并中段返塔;一路并原料下返塔。
分馏系统工艺流程及操作要点课件

煤油
• 煤油自分馏塔第11#集油箱馏出,进入煤油汽提塔T404。煤油汽提塔 共设10层塔盘,顶部气相返回分馏塔第10#塔盘上部。煤油汽提塔底 部用分馏塔中段回流作热源,由煤油汽提塔底重沸器E407加热至 225℃。煤油自汽提塔底由煤油泵P408抽出,经低温热水冷却至108℃ 分两路,一路经煤油空冷A406、煤油冷却器E408、煤油加药设施,作 为煤油产品出装置,另一路返回裂化原料油缓冲罐。
压力对塔操作的影响
• 压力对全塔组分的沸点有影响,随着塔压的升高,产品的沸点也会 升高,以致给组分的分离带来更大的困难。如果塔的压力降低,在塔 温不变的情况下,拨出率就会上升,产品容易变重,排出气体的流率 就会增加。因此不要随意改变压控的给定值,正常的塔压不宜改变。 压力的平稳与否直接影响到产品的质量、系统的热平衡和物料平衡, 甚至威胁到装置的安全生产。
• 在操作中压力不能作为一种调节产品质量的手段,应保持恒定为好。 在对塔压进行调节时,要进行全面而周密的分析,尽力找出影响塔压 的主要因素进行准确而合理的调节,使操作平稳下来,当需要借助塔 顶容器的排气阀来调节塔压时要缓慢进行,不要猛开猛关,也不要随 便改变控制的给定值,以免造成大幅度的波动或冲塔事故。
石脑油分馏塔
• 石脑油分馏塔T406共设40层塔盘,来自分馏塔顶和脱丁烷塔底的石脑 油进料至第17#塔盘上部。塔顶控0.13MPa 、82℃,塔顶流出物经石脑 油分馏塔塔顶空冷A407、后冷E410,冷凝冷却至40℃,进入石脑油分 馏塔顶回流罐V405,罐顶由燃料气保压0.1MPa,塔顶油由石脑油分馏 塔顶回流泵P411AB抽出,一部分作为回流返塔,另一部分作为轻石脑 油出装。石脑油分馏塔底控148℃,用蒸汽作热源,由石脑油分馏塔 底重沸器E411加热。塔底油经重石脑油泵P410AB加压,经重石脑油脱 硫罐V406、重石脑油空冷A408、重石脑油冷却器E412,冷至40℃,作 为重石脑油产品出装。
实验三分馏PPT课件
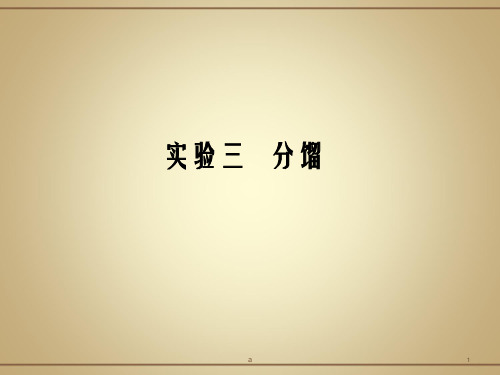
a
19
5、在分馏时通常用水浴或油 浴加热,它比直接火加热有什 么优点?
答:在分馏时通常用水浴或油浴 ,使液体受热均匀,不易产生 局部过热,这比直接火加热要 好得多。
a
5
在分馏柱内,当上升的蒸气与下降的冷凝液互 凝相接触时,上升的蒸气部分冷凝放出热量使 下降的冷凝液部分气化,两者之间发生了热量 交换,其结果,上升蒸气中易挥发组分增加, 而下降的冷凝液中高沸点组分(难挥发组分) 增加,如果继续多次,就等于进行了多次的气 液平衡,即达到了多次蒸馏的效果。这样靠近 分馏柱顶部易挥发物质的组分比率高,而在烧 瓶里高沸点组分(难挥发组分)的比率高。这 样只要分馏柱足够高,就可将这种组分完全彻 底分开。工业上的精馏塔就相当于分馏柱。
下降液体充分进行热交换,使易挥发组分量上升,难挥发组分尽量下降,分馏效 果更好。
a
14
3)必须尽量减少分馏柱的热量损失和波动。柱的外围可用石棉绳包住,这样可以减 少柱内热量的散发,减少风和室温的影响也减少了热量的损失和波动,使加热均 匀,分馏操作平稳地进行。分馏时将各组分倒入烧瓶时,必须熄火,冷却后进行 。
作业:1
a
20
馏出液总体积。继续蒸馏,记录每增加1ml馏出液时的温度及馏分总体积。
4、换瓶B接受T=750C -900C馏分,>900C馏分用瓶C接受,当柱顶温度达到950C时停止 ,使馏分回流至烧瓶中。
(A T<750C馏分, B T=750C -900C C >900C)
a
10
5、记录三个馏分的体积;待分馏柱内液体流到烧瓶时倒入C瓶记录体积。 以柱顶温度为纵坐标,馏出液体积为横坐标,将实验结果绘成温度-体积曲线,讨 论分馏效率。
《分馏系统》课件
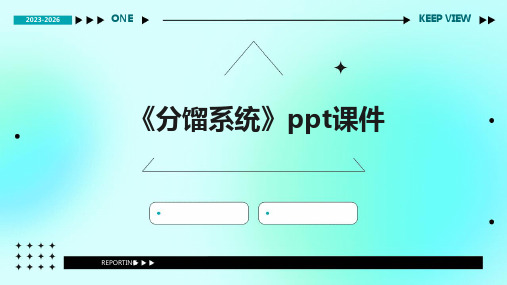
PART 03
分馏系统的操作流程
原料的预处理
原料的预处理
在进入分馏系统之前,原料需要 经过严格的预处理,包括清洁、 过滤和脱水等步骤,以确保原料
的纯净度和稳定性。
预处理的必要性
预处理可以去除原料中的杂质和水 分,避免它们对分馏过程产生干扰 ,影响产品的质量和产量。
预处理的方法
预处理的方法包括物理方法和化学 方法,如过滤、蒸馏、萃取等,具 体方法的选择取决于原料的性质和 要求。
程提供所需的热量。
预热器的设计应考虑传热效率、 热损失、操作稳定性和可靠性等 因素,以确保分馏过程的顺利进
行。
预热器通常采用管壳式结构,通 过加热介质(如蒸汽、导热油等 )与原料油进行热交换,以达到
预热的目的。
汽提塔
汽提塔是分馏系统中的关键设备之一,其主要作用是将原料油中的轻组分和部分重 组分分离出来。
保持现场秩序,确保 人员安全,防止事故 扩大。
启动紧急预案,通知 相关人员处理,并向 上级汇报。
环保要求与排放控制
分馏系统的设计和运行应符合国家和地 方环保法规要求。
选用低污染、低能耗的设备和工艺,减 对排放的废气、废水等污染物进行治理
少污染物排放。
,确保达标排放。
2023-2026
END
THANKS
分馏系统的应用
应用领域
分馏系统广泛应用于石油、化工、制药、食品等领域,用于分离液体混合物中 的不同组分,如石油的分馏可以得到汽油、柴油、润滑油等产品。
优势
分馏系统具有分离效果好、产品纯度高、操作稳定等优点,能够满足各种不同 的分离需求。
PART 02
分馏系统的组成
预热器
预热器是分馏系统中的重要组成 部分,其主要作用是将原料油加 热至所需温度,为后续的分馏过
分馏操作规程及流程
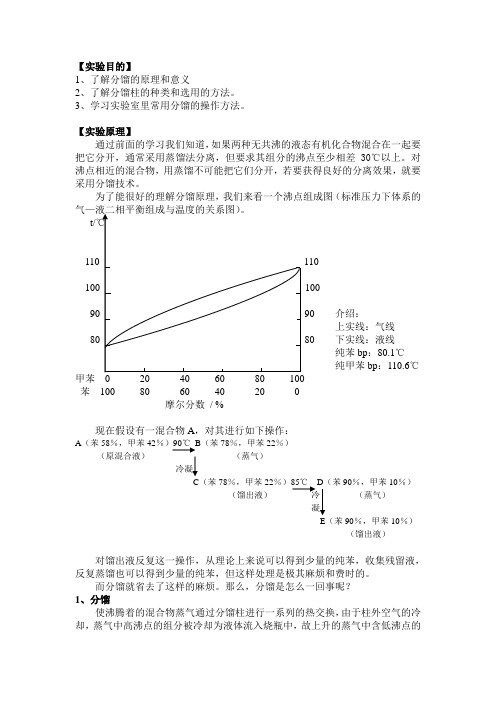
【实验目的】1、了解分馏的原理和意义2、了解分馏柱的种类和选用的方法。
3、学习实验室里常用分馏的操作方法。
【实验原理】通过前面的学习我们知道,如果两种无共沸的液态有机化合物混合在一起要把它分开,通常采用蒸馏法分离,但要求其组分的沸点至少相差30℃以上。
对沸点相近的混合物,用蒸馏不可能把它们分开,若要获得良好的分离效果,就要采用分馏技术。
为了能很好的理解分馏原理,我们来看一个沸点组成图(标准压力下体系的t/100介绍:上实线:气线下实线:液线纯苯bp:80.1℃纯甲苯bp:110.6℃甲苯苯100 80 60 40 20 0摩尔分数/ %现在假设有一混合物A,对其进行如下操作:A(苯58%,甲苯42%)90℃B(苯78%,甲苯22%)(原混合液)(蒸气)冷凝C(苯78%,甲苯22%)85℃D(苯90%,甲苯10%)(馏出液)冷(蒸气)凝E(苯90%,甲苯10%)(馏出液)对馏出液反复这一操作,从理论上来说可以得到少量的纯苯,收集残留液,反复蒸馏也可以得到少量的纯苯,但这样处理是极其麻烦和费时的。
而分馏就省去了这样的麻烦。
那么,分馏是怎么一回事呢?1、分馏使沸腾着的混合物蒸气通过分馏柱进行一系列的热交换,由于柱外空气的冷却,蒸气中高沸点的组分被冷却为液体流入烧瓶中,故上升的蒸气中含低沸点的组分就相对地增加;当冷凝回流途中遇到上升地蒸气,两者之间又进行热交换,上升的蒸气中高沸点的组分又被冷凝,低沸点的组分仍然继续上升,易挥发的组分又增加了。
如此在分馏柱内反复进行着气化——冷凝——回流等程序,最终低沸点的组分从分馏柱的顶部蒸馏出来,高沸点组分留在容器中,从而将不同沸点的物质分离开来。
需要指出的是,分馏也不能分离共沸混合物。
2、影响分馏效率的因素(1)理论塔板:分馏柱中的混合物,经过一次汽化和冷凝的热力学平衡过程,相当于一次普通蒸馏所达到的理论浓缩效率,当分馏柱达到这一浓缩效率时,那么分馏柱就具有一块理论塔板。
c第二章 第二节 分馏系统操作法
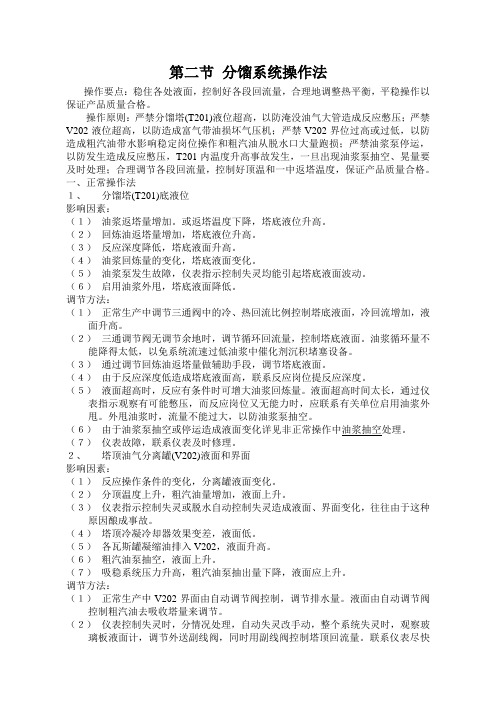
第二节分馏系统操作法操作要点:稳住各处液面,控制好各段回流量,合理地调整热平衡,平稳操作以保证产品质量合格。
操作原则:严禁分馏塔(T201)液位超高,以防淹没油气大管造成反应憋压;严禁V202液位超高,以防造成富气带油损坏气压机;严禁V202界位过高或过低,以防造成粗汽油带水影响稳定岗位操作和粗汽油从脱水口大量跑损;严禁油浆泵停运,以防发生造成反应憋压,T201内温度升高事故发生,一旦出现油浆泵抽空、晃量要及时处理;合理调节各段回流量,控制好顶温和一中返塔温度,保证产品质量合格。
一、正常操作法1、分馏塔(T201)底液位影响因素:(1)油浆返塔量增加。
或返塔温度下降,塔底液位升高。
(2)回炼油返塔量增加,塔底液位升高。
(3)反应深度降低,塔底液面升高。
(4)油浆回炼量的变化,塔底液面变化。
(5)油浆泵发生故障,仪表指示控制失灵均能引起塔底液面波动。
(6)启用油浆外甩,塔底液面降低。
调节方法:(1)正常生产中调节三通阀中的冷、热回流比例控制塔底液面,冷回流增加,液面升高。
(2)三通调节阀无调节余地时,调节循环回流量,控制塔底液面。
油浆循环量不能降得太低,以免系统流速过低油浆中催化剂沉积堵塞设备。
(3)通过调节回炼油返塔量做辅助手段,调节塔底液面。
(4)由于反应深度低造成塔底液面高,联系反应岗位提反应深度。
(5)液面超高时,反应有条件时可增大油浆回炼量。
液面超高时间太长,通过仪表指示观察有可能憋压,而反应岗位又无能力时,应联系有关单位启用油浆外甩。
外甩油浆时,流量不能过大,以防油浆泵抽空。
(6)由于油浆泵抽空或停运造成液面变化详见非正常操作中油浆抽空处理。
(7)仪表故障,联系仪表及时修理。
2、塔顶油气分离罐(V202)液面和界面影响因素:(1)反应操作条件的变化,分离罐液面变化。
(2)分顶温度上升,粗汽油量增加,液面上升。
(3)仪表指示控制失灵或脱水自动控制失灵造成液面、界面变化,往往由于这种原因酿成事故。
分馏部分培训教材
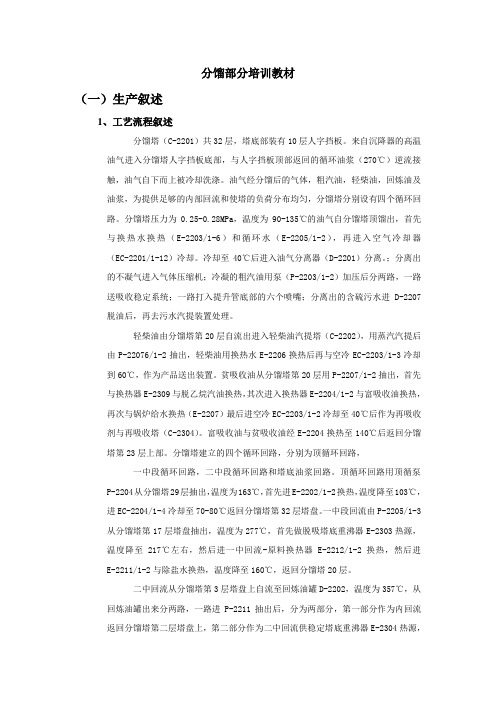
分馏部分培训教材(一)生产叙述1、工艺流程叙述分馏塔(C-2201)共32层,塔底部装有10层人字挡板。
来自沉降器的高温油气进入分馏塔人字挡板底部,与人字挡板顶部返回的循环油浆(270℃)逆流接触,油气自下而上被冷却洗涤。
油气经分馏后的气体,粗汽油,轻柴油,回炼油及油浆,为提供足够的内部回流和使塔的负荷分布均匀,分馏塔分别设有四个循环回路。
分馏塔压力为0.25-0.28MPa,温度为90-135℃的油气自分馏塔顶馏出,首先与换热水换热(E-2203/1-6)和循环水(E-2205/1-2),再进入空气冷却器(EC-2201/1-12)冷却。
冷却至40℃后进入油气分离器(D-2201)分离。
;分离出的不凝气进入气体压缩机;冷凝的粗汽油用泵(P-2203/1-2)加压后分两路,一路送吸收稳定系统;一路打入提升管底部的六个喷嘴;分离出的含硫污水进D-2207脱油后,再去污水汽提装置处理。
轻柴油由分馏塔第20层自流出进入轻柴油汽提塔(C-2202),用蒸汽汽提后由P-22076/1-2抽出,轻柴油用换热水E-2206换热后再与空冷EC-2203/1-3冷却到60℃,作为产品送出装置。
贫吸收油从分馏塔第20层用P-2207/1-2抽出,首先与换热器E-2309与脱乙烷汽油换热,其次进入换热器E-2204/1-2与富吸收油换热,再次与锅炉给水换热(E-2207)最后进空冷EC-2203/1-2冷却至40℃后作为再吸收剂与再吸收塔(C-2304)。
富吸收油与贫吸收油经E-2204换热至140℃后返回分馏塔第23层上部。
分馏塔建立的四个循环回路,分别为顶循环回路,一中段循环回路,二中段循环回路和塔底油浆回路。
顶循环回路用顶循泵P-2204从分馏塔29层抽出,温度为163℃,首先进E-2202/1-2换热,温度降至103℃,进EC-2204/1-4冷却至70-80℃返回分馏塔第32层塔盘。
一中段回流由P-2205/1-3从分馏塔第17层塔盘抽出,温度为277℃,首先做脱吸塔底重沸器E-2303热源,温度降至217℃左右,然后进一中回流-原料换热器E-2212/1-2换热,然后进E-2211/1-2与除盐水换热,温度降至160℃,返回分馏塔20层。
石油的分馏课件
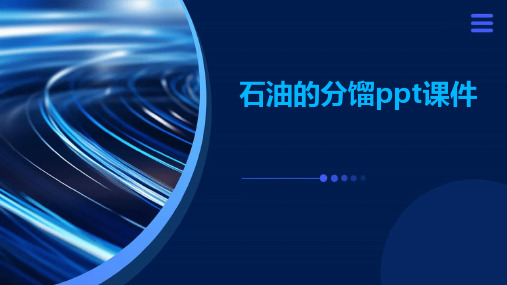
建立自动化控制系统,实现分馏过程的自动化控 制,减少人工干预,提高生产效率。
3
远程监控和故障诊断
通过远程监控和故障诊断系统,实时监测设备的 运行状态,及时发现并处理故障,确保生产安全 和稳定。
THANKS
感谢观看
生产过程
石油分馏过程中,通过控制温度和压力, 将石蜡和沥青从石油中分离出来,再经过 进一步加工得到最终产品。
05
CATALOGUE
石油分馏的挑战与解决方案
能耗和污染问题
石油分馏过程中能耗和污染问题严重,亟待解决。
石油分馏是石油加工的重要环节,但在实际操作过程中,会产生大量的能耗和污染。这是因为石油分馏需要在高温高压条件 下进行,同时还需要消耗大量的能源,如电、蒸汽等。此外,分馏过程中产生的废气、废水和固废也对环境造成了严重的影 响。
重质油品,如燃料油、润滑油等 ,沸点较高。
分馏塔的维护与优化
定期检查
对分馏塔进行定期检查,确保设 备正常运行。
清洗与维修
根据需要清洗和维修分馏塔,清除 积垢和腐蚀物。
参数优化
根据实际运行情况,调整工艺参数 ,提高分馏效率和产品质量。
04
CATALOGUE
石油分馏的应用
燃料油的生产
燃料油种类
石油分馏可以生产多种燃料油, 如汽油、柴油和重油等。
生产过程
石油经过加热和压力作用,按照 沸点不同分离成不同组分,再经 过进一步加工精制,得到符合标
准的燃料油。
重要性
燃料油是现代工业和交通领域的 重要能源,石油分馏为全球能源
供应提供了稳定的基础。
润滑油的生产
润滑油种类
石油分馏可以生产各种润滑油,如内燃机油、齿轮油、液压油等 。
石油的分馏PPT课件人教版原创
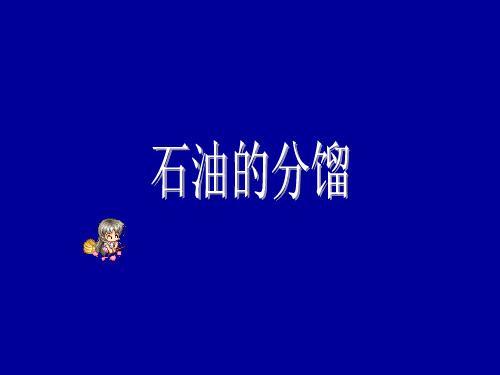
主要组成元素: 主要组成元素 碳 氢
组成物质: 组成物质: 主要是由各种烷烃、 主要是由各种烷烃、环烷烃和芳香烃组成 的混和物,大多数是液态烃, 的混和物,大多数是液态烃,同时溶有气态烃和 固态烃
二 石油的炼制
1.蒸馏和分馏 蒸馏和分馏 蒸馏: 蒸馏:
通过加热、冷凝,把液态混和物中沸点低的成分 通过加热、冷凝,把液态混和物中沸点低的成分 沸点低 先分离出来的操作。 先分离出来的操作。
石油
常压 加热炉 分馏塔
4.裂化和催化裂化 裂化和催化裂化
定义:P138 定义
裂化和催化裂化是化学变化--------链烃的断链分解反应 链烃的断链分解反应 裂化和催化裂化是化学变化
分馏 石 油 裂化
直馏汽油
烷烃 环烷烃
裂化汽油
烷烃 烯烃
5.裂解 裂解
定义:P138 定义 裂解是深度的裂化------也是化学变化 也是化学变化 裂解是深度的裂化
3)实验产物 实验产物
60度到 度到150度--------汽油 ~11 汽油C5~ 度到 度 汽油 150度到 度到300度---------煤油 煤油C11~16 度到 度 煤油 ~ 分馏出来的各种成分叫馏分 仍是混合物 分馏出来的各种成分叫馏分(仍是混合物 馏分 仍是混合物)
3.工业上的分馏 工业上的分馏 石油气 汽油: ~ 直馏汽油 直馏汽油) 汽油 C5~11(直馏汽油 煤油: 煤油 C11~16 ~ 柴油: 柴油 C15~18 重柴油 ~ 润滑油 减压 重油: 重油 石蜡 C20 以上 加热炉 渣油(制沥青 制沥青) 分馏塔 渣油 制沥青 燃料油
返回
2.实验室蒸馏石油 实验室蒸馏石油
1)仪器名称 仪器名称: 仪器名称
石油的分馏解析PPT课件
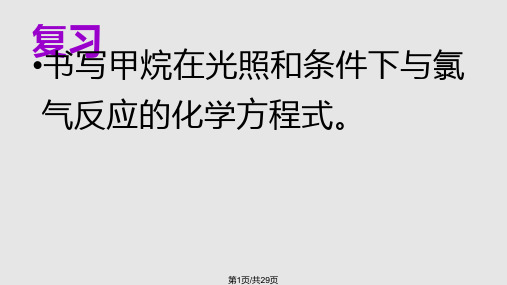
化学变化与物理变化
(3)分类:高温干馏和低温干馏 第21页/共29页
煤焦油再经分馏后可得: •170℃以下是苯、甲苯、二甲苯 和其它苯的同系物 •170~230℃是酚和萘 •剩下的是沥青
第22页/共29页
4、 煤的气化和液化 气化: 把煤中的有机物转化为可燃性气体的过程。 液化: 把煤转化为液体燃料的过程。
第23页/共29页
5、环境保护 大量燃烧煤燃料,会造成CO2、SO2等污染
煤作为化工原料又会引出“三废” ——废水、废气、废渣
—— 掺入氧化钙
—— 合理处理并重复利用各种产物 煤在运输和使用过程中的煤灰
—— 湿化
第24页/共29页
练习
汽油燃烧产生的汽车尾气中,所含的大气污染物主要是 A、碳的氧化物 B、硫的氧化物 C、氮的氧化物 D、磷的氧化物 C
第16页/共29页
随堂练习:
•1、如何鉴别:直馏汽油和裂化汽油? •答:采用溴水。能使溴水褪色的是裂 化汽油;不能使溴水褪色的为直馏汽 油。
第17页/共29页
2、1moL 某直链烷烃A可以直接裂解成1moL 气
态烷烃 B 和 1moL气态烯烃 C,经测定,裂解后
混合气体的密度是同温同压下氢气的 14.5倍,
2、C8H18经多步裂化,最后完全转
化为C4H8、C3H6、C2H4、C2H6、CH4
五种气体的混合物。该BC混合物的
平均相对分子质量可能是(
)
A、28 B、30 C、38 D、 40
第28页/共29页
谢谢您的观看!
第29页/共29页
沸点 混合
第5页/共29页
第6页/共29页
【正式版】蒸馏与分馏PPT
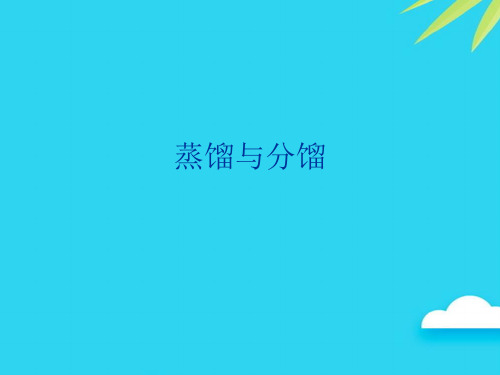
汽,再将蒸汽冷凝到液体的过程。用于分 1Mpa(即760mmHg柱)压力下液体的沸腾温度。
这时的温度称为液体的沸点 回流比--冷凝液流回蒸馏瓶的速度与分馏柱顶蒸汽通过冷凝管流出的速度的比值。
离沸点相差大于30度的液体。 例如水的沸点为100oC,即指大气压为760mmHg柱时,水在100oC时沸腾。
四、操作
❖ 向圆底烧瓶中加入15mL丙酮和15mL水的
混合液,再加2-3粒沸石 按蒸馏图安装
仪器 缓慢通冷凝水
打开电热套
加热 当有蒸汽产生时调整加热速度控
制馏出液每秒1-2滴 分别收集56-62、
62-72、27-98、98-100度的馏分
画出蒸馏曲线
❖ 分馏操作:
仪器安装❖:(圆先下底后上、烧先左后瓶右)中加入15mL丙酮和15mL水,再
确定热源(电炉、水浴、油浴或其它热源)→固定蒸馏瓶→装蒸馏头→安温度计(使温度计水银球的上限与蒸馏头侧管的下限同处一
换沸石。 水平线上)→装冷凝管(上端出水口向上,出水;
1Mpa(即760mmHg柱)压力下液体的沸腾温度。 回流比--冷凝液流回蒸馏瓶的速度与分馏柱顶蒸汽通过冷凝管流出的速度的比值。
前馏分--在需收集组分沸点前蒸出的液 例如水的沸点为100oC,即指大气压为760mmHg柱时,水在100oC时沸腾。
❖ 2、温度计位置要准确,否则影响收集组分 的纯度及数量。
❖ 3、不要将所有液体蒸干,以防起火或爆炸。
❖ 4、操作要轻,防止玻璃仪器破损,不用的 仪器及时放入原位。放置于桌面时要注意 不要碰倒或滚落地上。
六、思考题
❖ 1、加热后忘加沸石,应如何补加? ❖ 2、温度计位置对测量温度有何影响?
分馏系统操作法
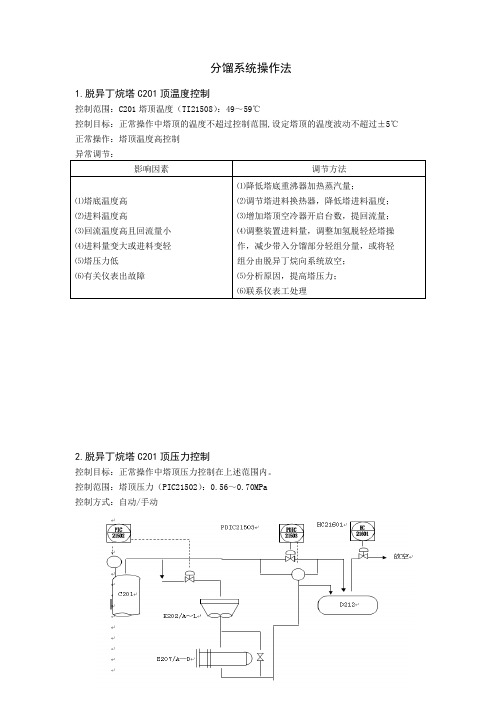
分馏系统操作法1.脱异丁烷塔C201顶温度控制控制范围:C201塔顶温度(TI21508):49~59℃控制目标:正常操作中塔顶的温度不超过控制范围,设定塔顶的温度波动不超过±5℃正常操作:塔顶温度高控制2.脱异丁烷塔C201顶压力控制控制目标:正常操作中塔顶压力控制在上述范围内。
控制范围:塔顶压力(PIC21502):0.56~0.70MPa控制方式:自动/手动影响因素调节方法⑴塔底温度高⑵进料温度高⑶回流温度高且回流量小⑷进料量变大或进料变轻⑸塔压力低⑹有关仪表出故障⑴降低塔底重沸器加热蒸汽量;⑵调节塔进料换热器,降低塔进料温度;⑶增加塔顶空冷器开启台数,提回流量;⑷调整装置进料量,调整加氢脱轻烃塔操作,减少带入分馏部分轻组分量,或将轻组分由脱异丁烷向系统放空;⑸分析原因,提高塔压力;⑹联系仪表工处理图2-20正常操作:脱异丁塔压力正常控制是将PIC21502投自控,通过直接改变流经E202/A ~L 和E207/A ~D 气体的冷凝量来调节塔顶压力。
气体热旁路调节阀PDV21503也投自控,通过此阀开度大小控制脱异丁烷塔顶不超压, 保持脱异丁烷塔顶和回流罐有一定的压力差,保证塔顶气、液体流动有一定的推动力。
3脱异丁烷塔C201底温度控制控制目标:正常操作中塔底温度控制在上述范围内, 设定塔底的温度波动不超过±5℃ 控制范围:塔底温度(TIC21503):120 ~132℃ 控制方式:自动/手动图2-21正常操作:正常操作时,设定塔底温度,通过塔重沸器蒸汽流量调节阀FV21502自动调节正常操作:正常操作时,设定塔底温度,通过塔重沸器蒸汽流量调节阀FV21502自动调节蒸汽流量控制塔底温度。
如果发现仪表出现故障自动控制失灵时,应改为手动调节,并联系仪表处理。
异常调节:脱异丁烷塔底温度过低会使脱异丁烷分离效果不好,导致循环异丁烷浓度和循环量下降,进而使烷基化反应器运行效果恶化 现象原因处理方法蒸汽系统的压力、温度下降 低压蒸气管网压力温度波动相应提蒸汽量,通知调度并联系管网车间查找原因塔底温度的控制原则是:根据塔进料量、塔顶压力、温度和产品控制指标来进行调节。