汽轮机油系统故障分析及对策详细版
火力发电厂汽轮机油系统常见故障分析及防治措施

火力发电厂汽轮机油系统常见故障分析及防治措施汽轮机简单来讲就是蒸汽能量向机械功转换的动力机械,其油系统主要是由润滑油系统和液压油系统构成,对确保汽轮机正常运行具有重要意义。
然而,受汽轮机油系统稳定性不佳这一特点的影响,使得油系统故障引发的汽轮机发电机组断油烧瓦事故发生几率大大增加,甚至整个汽轮机组都无法正常使用。
对此,想要确保汽轮机的正常运转,那么就要从维护汽轮机油系统着手,注重对其故障的分析和检修,避免因油系统故障引发的汽轮机组损坏情况。
标签:火力发电厂;汽轮机油系统;故障;防治措施一、汽轮机概述发电厂在运行过程中,通常会使用汽轮机来驱动发电机进行发电,有一套固有的流程,相关工作人员首先需要开启锅炉设备,在锅炉内加水,然后进行不断的加热,使水变成水蒸气,水在加热的过程中,逐步向水蒸气演变的时候,其体积会不断的扩大,最后导致水蒸气沿着管道进入到汽轮机,这时汽轮机就可以通过喷嘴向汽轮机表面的叶片进行喷射,这样就能够促使叶片不断的旋转,从而带动发电机进行发电,通过水蒸气的热能转化为机械能在这一过程中有着非常大的能量转化以及消耗。
然而在汽轮机实际的运行过程中,仍然会存在很多的设备故障以及能耗大的问题,影响发电机组的正常运行,甚至威胁到整个发电厂的生产效率。
所以电厂的工作人员需要对汽轮机的运行状况进行不断的优化,降低运行过程中产生的能耗减少,运行过程中出现的故障,保证起轮机处于正常稳定的运行状态,确保发电机组能够正常运行,提高发电厂的生产效率,保证电厂的经济效益降低,在发电过程中产生的能源消耗。
此外,电厂在运行过程中保证生产过程中的安全性也是非常重要的,各种生产环节都应该以保证安全为前提进行,如果汽轮机在运行过程中出现故障,很有可能会影响到工作人员的生命财产安全,也不利于电厂的安全,所以需要对汽轮机的运行状态进行不断的优化,保证汽轮机安全运行,提高电厂生产的安全性,促进电厂各项生产活动的有序进行。
二、汽轮机油系统的常见故障原因(一)油系统内存在管路杂质(1)汽轮机油系统在制造安装过程中,油系统设备及管路中会滞留一些杂质,如纤维、焊渣、铁屑、漆皮、铁锈等;(2)油系统在负压运行时有入侵的污染物,如粉尘、泥沙;(3)润滑油长时间高温高压运行产生胶质、积碳等;(4)系统在检修维护或补油时会带入一些杂质、垃圾;(5)油系统涂层脱落物以及金属表面产生腐蚀物,如氧化铁、硫化铁等。
汽轮机油系统常见问题及处理措施分析

汽轮机油系统常见问题及处理措施分析摘要:在我国能源生产过程中,电能的生产主要由火力发电厂完成。
在发电过程中,使用蒸汽轮机可以将蒸汽能转换为机械能。
其油系统主要包括液压油和润滑油系统。
系统的稳定运行是汽轮机安全运行的重要保证。
然而,由于油系统的频繁故障,该装置被切断、烧毁和报废。
因此,应做好油系统维护工作,降低运行中的故障概率,确保汽轮机的运行安全和电厂的效益。
关键词:汽轮机油系统;问题;处理措施1润滑油系统常见问题分析及处理措施1.1润滑油温度异常升高汽轮机运行时,需要控制润滑油温度。
在具体的运行过程中,受润滑油温度影响的故障也非常频繁。
润滑油系统温度高的原因很多,与润滑油的功能密切相关。
润滑油的主要作用是润滑轴承,同时降低轴承温度。
如果汽轮机运行时温度过高,油膜承载能力将直接降低,高温润滑油将与轴承表面发生干摩擦,造成设备损坏。
如果长时间运行,会再次摩擦,减少油量,影响设备运行。
这些问题的主要原因是机油冷却器中的污渍和管道堵塞。
如果设计不符合标准,则总面积不足,油冷却器排出的气体不能及时冷却。
汽轮机油冷却器故障是一种常见故障,应及时发现并解决,以充分保证设备的安全稳定运行。
一般来说,常见故障是冷油器使用不规范,高温回油未及时冷却。
设备在长期运行过程中会产生污垢,导致管道结垢堵塞,影响设备制冷效果。
设备受热面越小,润滑油温度越高。
冷却循环水的温度不是自动设计的,通常不能满足运行中的制冷需要。
异常油温故障对季节敏感,特别是夏季室外温度较高时,制冷效果较弱。
1.2润滑油压力汽轮机是否正常运行直接关系到润滑油压力。
因此,必须全面有效地控制润滑油压,确保润滑油压合理。
一般来说,润滑油压力的设定需要与汽轮发电机组的主要参数保持一致,以维持系统的正常运行。
如果润滑油压过低,无法支持系统运行,则无法在轴颈和轴瓦之间建立油膜。
当部件运行时,会产生干摩擦并损坏部件。
如果润滑油油压过高,则会发生漏油,有设备起火的危险。
汽轮机检修中油系统常见故障与应对措施

汽轮机检修中油系统常见故障与应对措施摘要:在电力生产工作中,汽轮机有着极为重要的作用,而汽轮机在检修过程当中,非常容易碰到油系统故障问题。
基于此,本文以汽轮机检修过程中常见的油系统故障为立足点,分析相应的EH系统故障以及DEH系统故障,并针对这两个故障问题,提出对应的解决策略,希望对广大读者有所帮助。
关键词:汽轮机;检修;油系统;常见故障引言:汽轮机作为电力生产工作重要的组成部分,在检修进程中会经过长期运作,其油系统也非常容易发生问题与故障,进而对汽轮机整体机组状况产生负面影响。
基于此,为了有效保障汽轮机运行的稳定性与可靠性,顺利推进电力生产工作,相关工作人员应当对汽轮机检查维修进程中,油系统的常见故障以及其解决策略加强重视。
一、分析汽轮机检修过程中常见的油系统故障(一)EH系统故障EH系统故障主要分为两种,分别是油压过低与油温过高。
一般来说,汽轮机EH油压有相应的标准值,如果油压过低,实际参数就会与定值发生偏移,这时,主机为了保护相关设备,就会自动采取动作,借此保障汽轮机油系统机组安全。
而电力生产是一项系统化的工作,主动采取保护工作会对电力生产工作产生极大的不良影响。
其次,EH油温过高会导致油质量发生变化,出现酸值超标等情况,同时还会对油管产生结垢问题,进而导致EH回油管发生堵塞等障碍。
(二)DEH系统故障1.伺服阀故障在汽轮机油系统运行进程的当中,为了满足电力生产的要求,需要在特定时刻借助职工或者是器械进行调控,这就导致现阶段运行状态的平衡即将被打破,因此,DEH系统在应用进程中,可能会对汽轮机转动速度以及平稳性能产生影响,进而导致其无法固定在一个点,造成波动等情况出现。
而伺服阀一旦出现问题,那么就无法传输完整指令,最终就会造成汽轮机启动时出现故障情况。
1.EH油控问题对于DEH系统来说,EH油占据极为重要的地位,由于新旧EH油在酸值方面有很大差距性,所以,如果酸值产出相关标志,那么就会导致油在长期应用进程当中,产生沉淀物,最终导致油质出现巨大影响,汽轮机也无法正常运行。
汽轮机油系统故障分析及预防措施
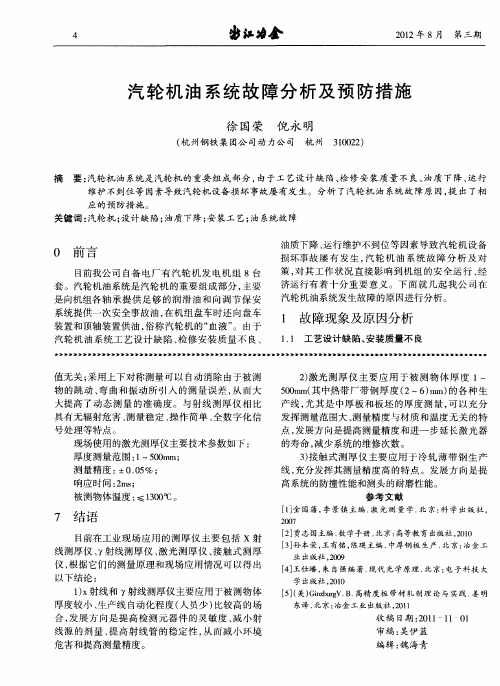
7 结 语
目前 在工业 现 场应 用 的测 厚 仪 主要 包 括 x射 线测厚 仪 、 了射线测 厚 仪 、 光 测厚 仪 、 触 式 测 厚 激 接
[] 2 贾志 国主编 . 数学手册 . 北京 : 高等教 育出版社 ,00 2 1 [] 3 孙本荣 , 王有铭 , 陈瑛主编 . 中厚钢板 生产 . 京: 北 冶金 8 第 期 0年 月 三 1
汽 轮 机 油 系统 故 障 分 析 及 预 防措 施
徐 国荣 倪 永 明
( 州钢铁 集 团公 司动 力公 司 杭 州 30 2 ) 杭 10 2
摘
要: 汽轮机 油 系统是 汽轮 机 的 重要 组成 部 分 , 由于 工艺设 计 缺 陷、 修 安 装 质 量 不 良、 质 下 降 、 行 检 油 运
1 故障现象及原 因分析
1 1 工艺设 计缺 陷 、 . 安装 质量 不 良
值无 关 ; 采用 上下 对称测 量 可 以 自动 消 除 由于被 测 物 的跳 动 、 曲和振 动 所 引 入 的测 量 误差 , 而 大 弯 从 大提高 了 动 态测 量 的准 确 度 。与 射 线 测厚 仪 相 比
编辑 : 海青 魏
21 02年 8月 第三期
汽轮 机 油 系统故 障分析 及预 防措 施
5
如果 机 组 工 艺设 计 缺 陷 、 装 质 量 不 良, 安 必然 造成 油系统 故 障 。如 油 管 由于 工 艺 布 置 不合 理 或 安装 不 良 , 行 中管 道发 生振 动 ; 管 法 兰 与 某些 发 热 运 油 体 无 隔离装 置等 。20 年 1 02 2月公 司某 热 电厂 3号 1MW 机组 , 5 因油管 工 艺 布 置不 合 理 加 上 安装 质量 不 良 , 运 行 中油管 振 动 较 大 , 成 供 油 管法 兰结 在 造 合 面漏 油 , 上 油 管 法 兰 与 主蒸 汽 管 道 无 隔 离 装 加 置 , 高 压 油 直 接 喷 到 主蒸 汽 管 道 上造 成 着 火 , 使 由 于处理 过程 中运 行人 员能 及 时破 坏 真空 紧 急停 机 , 并 立 即把油 放至 事故 油箱 , 免 了油 箱爆 炸事 故 的 避
汽轮机润滑油系统的常见故障和原因探究
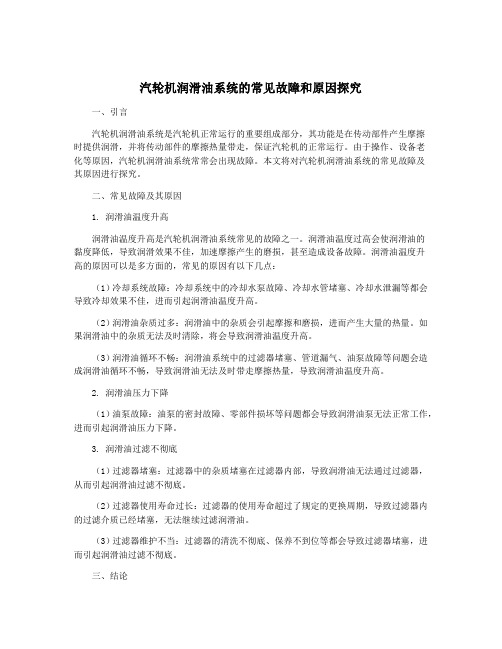
汽轮机润滑油系统的常见故障和原因探究一、引言汽轮机润滑油系统是汽轮机正常运行的重要组成部分,其功能是在传动部件产生摩擦时提供润滑,并将传动部件的摩擦热量带走,保证汽轮机的正常运行。
由于操作、设备老化等原因,汽轮机润滑油系统常常会出现故障。
本文将对汽轮机润滑油系统的常见故障及其原因进行探究。
二、常见故障及其原因1. 润滑油温度升高润滑油温度升高是汽轮机润滑油系统常见的故障之一。
润滑油温度过高会使润滑油的黏度降低,导致润滑效果不佳,加速摩擦产生的磨损,甚至造成设备故障。
润滑油温度升高的原因可以是多方面的,常见的原因有以下几点:(1)冷却系统故障:冷却系统中的冷却水泵故障、冷却水管堵塞、冷却水泄漏等都会导致冷却效果不佳,进而引起润滑油温度升高。
(2)润滑油杂质过多:润滑油中的杂质会引起摩擦和磨损,进而产生大量的热量。
如果润滑油中的杂质无法及时清除,将会导致润滑油温度升高。
(3)润滑油循环不畅:润滑油系统中的过滤器堵塞、管道漏气、油泵故障等问题会造成润滑油循环不畅,导致润滑油无法及时带走摩擦热量,导致润滑油温度升高。
2. 润滑油压力下降(1)油泵故障:油泵的密封故障、零部件损坏等问题都会导致润滑油泵无法正常工作,进而引起润滑油压力下降。
3. 润滑油过滤不彻底(1)过滤器堵塞:过滤器中的杂质堵塞在过滤器内部,导致润滑油无法通过过滤器,从而引起润滑油过滤不彻底。
(2)过滤器使用寿命过长:过滤器的使用寿命超过了规定的更换周期,导致过滤器内的过滤介质已经堵塞,无法继续过滤润滑油。
(3)过滤器维护不当:过滤器的清洗不彻底、保养不到位等都会导致过滤器堵塞,进而引起润滑油过滤不彻底。
三、结论汽轮机润滑油系统的常见故障及其原因主要有润滑油温度升高、润滑油压力下降和润滑油过滤不彻底。
润滑油温度升高的原因可以是冷却系统故障、润滑油杂质过多和润滑油循环不畅等。
润滑油压力下降的原因可以是油泵故障、润滑油泄漏和润滑油污染等。
润滑油过滤不彻底的原因可以是过滤器堵塞、过滤器使用寿命过长和过滤器维护不当等。
汽轮机油系统故障分析及改进措施施

汽轮机油系统故障分析及改进措xxxx工技术总结汽轮机的润滑油系统是汽轮机系统的重要组成部分,也是汽轮机组重要的调节保安系统,负责可靠地向汽轮发电机组的各轴承、盘车装置提供合格的润滑油。
如果汽轮机的润滑油系统工作异常,将直接威胁汽轮机设备的安全运行。
处理不及时就会导致汽轮机烧瓦、大轴弯曲、转子动、静磨擦甚至整机损坏等恶性事故的发生,特别是在基建调试阶段,此类事故更易出现。
根据近几年我公司所施火电厂发生的油系统的相关故障,从设备安装、管道安装、焊接工艺、油循环冲洗等各方面做了如下总结:1、油系统的常见故障及主要表现1.1密封材料损坏,系统泄露1.2电液伺服阀故障,调节异常1.3油质劣化,油品指标不合格其中润滑油质量问题是油系统故障的主要问题,在云南工地因机组在安装结束后进行大油量循环时,其冲洗时间不足,未将焊渣及硬质颗粒清洗干净而发生过轴承处轴颈和轴瓦损伤、拉伤的情况,后来经过堆焊处理。
润滑油不合格的原因主要是:其主要来源有:(1)设备制造安装过程中滞留的杂质,如焊渣、铁锈、铁屑等;(2)系统运转,流体变质生成的杂质;(3)油箱及系统在微负压运行时外侵的污染物;(4)系统在安装或补油的过程中带人的杂质。
润滑油中的固体颗粒物会导致系统管道及设备的磨损,磨损产生的固体颗粒物使油质进一步劣化,如果得不到有效的控制,如此恶性循环,会使油质急剧下降,设备严重磨损。
其主要来源有:(1)轴封漏汽进入油系统;(2)冷油器泄漏时水压高于油压而侵入的水;(3)潮湿空气冷凝时产生的水;(4)补油时带人的水。
研究显示,当水分和微小颗粒杂质并存于油液中时,油液的氧化速度加快10倍以上。
水分还会引起油液中添加剂的分解和沉淀,形成黏性化合物,使油液呈酸性。
油中的酸性物质在水分的作用下与金属表面形成电化学反应而腐蚀设备,主要表现为生锈,进而加剧磨损和油液变质。
油中的空气主要是油系统在排烟风机作用下负压运行吸入的,系统中的空气使不被油淹没的管道部分和元件产生氧化腐蚀,增加系统中杂质污染。
汽轮机检修中油系统常见故障的处理分析

汽轮机检修中油系统常见故障的处理分析摘要:汽轮机是电力生产的主要机组设备,在电力企业中,汽轮机主要发挥着电能转换的作用,其运行状况直接影响着电力的供应以及城市居民的生产与生活用电。
因此,汽轮机的正常、稳定运行显得尤为重要。
而在实际运转过程中,汽轮机不可避免地都会发生故障,特别是汽轮机中的油系统,其故障发生率尤为突出。
这就需要电力企业加强对汽轮机中油系统的检修与保养工作,在检修过程中及时对故障进行排除,以确保汽轮机得以安全、稳定运行。
为此,结合自身实践经验,对汽轮机检修中油系统的常见故障进行分析,并提出相应的处理策略。
关键词:汽轮机;检修;油系统;故障;处理;一、汽轮机检修中油系统的常见故障根据多年的汽轮机故障处理经验以及众多汽轮机研究成果发现,当前在我国的汽轮机的油系统中普遍存在的故障主要有EH油系统故障和DEH油系统故障。
1.汽轮机的EH油系统故障E H油系统故障作为汽轮机的油系统中较为常见的故障类型,在实际工作中经常出现,包括EH油系统的油动机开调门失效、EH油系统油箱的油压及油位下降和油温超出正常范围。
导致EH油系统这些故障产生的原因,主要包括复阀堵死或卡涩、AST系统带电的不正常、DEH控制系统故障、油箱进油阀故障、溢油阀卡死、油加热器故障以及EH油系统冷却水系统故障等。
2.汽轮机的DEH油系统故障该故障也是汽轮机的油系统故障中最常见的类型之一,其故障类型通常包括DEH油系统的AST电磁阀与隔膜阀关闭故障、EH油系统油箱油温或者油位低于正常运行值以及DEH油系统储能器故障等。
导致这些故障产生的原因主要有OPC电磁阀没有送电或没有关严、EH油箱油阀或冷却水系统出现故障等。
二、汽轮机油系统常见故障现象及原因分析1)汽轮机在运行过程中,往往会产生许多蒸汽,而发电的水质并未进行有效的过滤,长久以往,水中杂质不断增多,从而容易结垢,导致通汽部位极易发生腐蚀,从而降低管道的畅通性。
2)汽轮机前轴承出现局部烧损。
汽轮机检修中油系统故障与对策探析

汽轮机检修中油系统故障与对策探析摘要:汽轮机油在电力体系中起着重要的润滑作用,若是缺乏足够的机油,极易导致汽轮机在使用过程中由于摩擦力较大,或者由于机油使用性不强等问题,最终出现磨损、衔接问题,导致其难以充分发挥作用。
随着我国工业的不断发展,汽轮机油体系的质量对这个生产过程都有着重要影响。
本文简要阐述了油系统相关内容以及常见故障,并在此基础上详细分析了针对常见故障的应对策略。
关键词:机油系统;常见故障;对策引言随着我国工业的不断发展,油系统在社会生产中的运用越来广泛,其在工业生产中也起着重要作用。
整体上讲,目前汽轮机的油系统在使用过程中仍旧具有一定的不稳定特征。
因此,为了提高油系统的使用率,充分发挥其在汽轮机使用过程中的作用,有必要对其常见故障进行分析,并提出解决建议。
1油系统的主要构成1.1油箱概述顾名思义,油箱即是储存机油的设备,包含汽轮机所需要的润滑油、调节油等。
同时,该设备也是对油中的水、油进行分离,清除其中含有的杂质等的重要设备。
在整个供油体系中,该设备都起着十分重要的作用。
通常情况下,油箱主要是由碳钢构成,其能够容纳的油量一般根据实际需要而定,主要目的是能够满足油在持续循环时有足够的停留时间。
此外,在具体的使用过程中,还应保证油箱所处的环境,不能有明火等容易引发安全事故的因素存在。
1.2冷油器概述一般情况下,在使用过程中会准备2个冷油器,除了投入使用之外,另外一个主要拿来备用。
该设备的主要功能是能够控制冷却水及油的温度,保证其的进水温度不超过37摄氏度的范围,润滑油的温度保持在47摄氏度的范围以内。
该设备的主要运行方式,是水的管道内部进行流动,而油则在管道外部通过。
温度较高的油从外部进入,隔板可以改变油的流动方向,以提高其流动速度,提高工作效率,再促使水与油进行热量交换。
通过这样的方式,以达到对两者的温度进行控制的目的。
1.3滤油器概述所谓滤油器,简单来说就是对液压油进行过滤的器材。
汽轮机油系统故障分析及对策(正式)
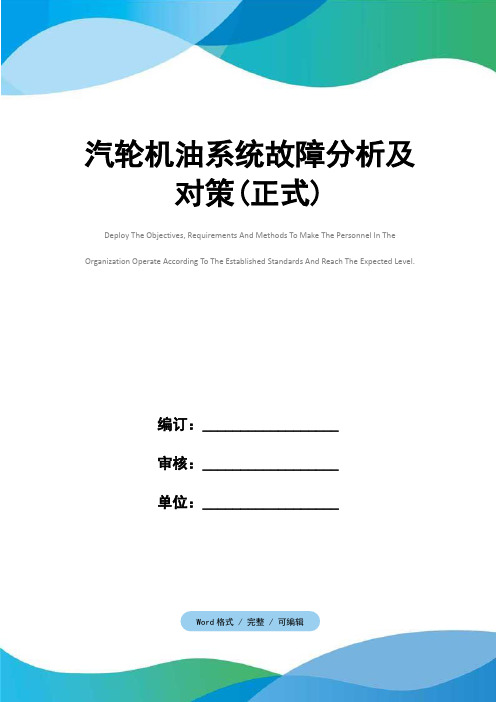
编订:__________________审核:__________________单位:__________________汽轮机油系统故障分析及对策(正式)Deploy The Objectives, Requirements And Methods To Make The Personnel In The Organization Operate According To The Established Standards And Reach The Expected Level.Word格式 / 完整 / 可编辑文件编号:KG-AO-2822-31 汽轮机油系统故障分析及对策(正式)使用备注:本文档可用在日常工作场景,通过对目的、要求、方式、方法、进度等进行具体的部署,从而使得组织内人员按照既定标准、规范的要求进行操作,使日常工作或活动达到预期的水平。
下载后就可自由编辑。
油系统是汽轮机的重要组成部分,其工作状况直接影响到机组的安全经济运行。
因汽轮机油系统导致机组故障、设备损坏的事故屡有发生,特别是在基建调试阶段,此类事故更易出现。
下面介绍几起基建调试阶段发生的汽轮机油系统故障现象及原因。
1 故障现象及原因1.1 油质不良造成故障油质不良主要是指油中的水份、颗粒度等指标超过规定标准。
如1996年1月某电厂1号机组(300MW)调试阶段停机消缺期间,将主油箱内的油倒入储油箱中,因储油箱内未清理干净引起润滑油污染造成设备损伤。
同年11月该厂2号机组(300 MW)调试中因油质不良多次造成中压主汽门伺服阀及DUMP阀卡死、伺服机构节流孔堵等故障。
1997年1月某电厂13号机组(125 MW)在带负荷调试中出现中联门卡、润滑油压低等现象,经检查均为油脏所致,揭瓦后还发现机组轴颈拉伤、轴瓦拉毛。
油质不良的原因主要有两个方面:一是制造质量不好,油出厂时就存在油质不合格的问题;二是受外界污染。
1.2 设备质量不良造成故障设备质量不良是指设备及附件在加工、制造过程中工艺未按有关规定执行,致使质量不符合标准要求。
汽轮机油系统的常见故障及解决对策

汽轮机油系统的常见故障及解决对策摘要:汽轮发电机润滑油系统基本都采用主油泵—射油器的供油方式,主油泵由汽轮机主轴直接驱动,其出口压力油驱动射油器投入工作。
润滑油系统主要用于向汽轮发电机组各轴承提供润滑油,向汽轮机危急遮断系统供油,向发电机氢密封装置提供油源,以及为主轴顶起装置提供入口油。
本文根据作者多年工作经验,对汽轮机检修中油系统的常见故障进行了详细的分析,并提出了相关的解决对策,共大家学习和借鉴。
关键词:汽轮机;检修;油系统;常见故障;解决对策1、引言汽轮机油系统故障分析及对策油系统是汽轮机的重要组成部分,其工作状况直接影响到机组的安全经济运行。
因汽轮机油系统导致机组故障、设备损坏的事故屡有发生。
在机组基建阶段和运行阶段都会出现故障。
严重影响汽轮机机转子的寿命。
甚至引起汽轮机转子报废。
2、汽轮机油系统的组成汽轮机油系统主要由主油泵,射油器,交流电动油泵,直流电动油泵,集装油箱,溢流阀。
冷油器,切换阀,油烟风机,顶轴油泵,密封油泵及集装油管的附件组成。
2.1 主油泵主油泵为单级双吸离心式油泵,由汽轮机转子直接驱动,它为射油器提供动力油,向调节保安系统提供压力油。
2.2 射油器射油器安装在油箱内油面以下,工作时,主油泵来的压力油以很高的速度从喷嘴射出,在混合室中造成一个负压区,油箱中的油被吸入混合室。
同时由于油粘性,高速油流带动吸入混合室的油进入射油器喉部,从油箱中吸入的油量基本等于主油泵供给喷嘴进口的动力油量。
2.3 交流和直流电动油泵交流润滑油泵、直流事故油泵,交流润滑油泵、直流事故油泵一般都安装在润滑油箱盖板上。
当机组在起动和停机工况时,交流润滑油泵代替主油泵向保安系统提供压力油。
代替供润滑油射油器,向机组各轴承及盘车装置、顶轴装置提供充足的润滑油,同时也为氢密封油泵提供油源,直流事故油泵在机组处于事故状态时,代替交流润滑油泵,在机组发生交流失电时为机组提供必要的润滑油,以保证机组安全停运,但直流事故油泵不能用于机组起动或正常运行。
汽轮机检修中油系统的常见故障及处理方法

汽轮机检修中油系统的常见故障及处理方法摘要:许多因素都会对电网的稳定性产生影响,而汽轮机是最主要的转化电能的设备,它的工作状态一定要维持在一个较好的状态,才能供应高品质和稳定的电能。
为了确保汽轮机的正常运转,需要对油系统进行良好的控制,本文对汽轮机检修中油系统的常见故障及处理方法进行了详细的论述。
关键词:汽轮机;油系统;故障1汽轮机油系统的几种常见故障及其成因由于汽轮机的工作原理,它在运转时会释放出很多的水蒸气,在进行发电工作时,所用的水都没有经过过滤,久而久之,水里的杂质就会在里面形成固态,使得汽轮机的部件被这些杂质所侵蚀,从而对汽轮机的正常运转造成影响。
由于部件损伤引起的汽轮机部分燃烧问题,在长时间的运转中,汽轮机的各部分都会有一定的损耗,特别是联结部分,在损耗过后容易出现松动,若得不到及时的替换和维护,将会对汽轮机的相关性能造成一定的影响。
在机油系统中,前、中、后三个部位都有一个密封,由于某些特定的因素,密封的缝隙太大,会引起汽轮机的热能问题。
由于汽轮机油系统长期工作在较高的温度下,使其内部的非金属构件极易发生磨损,同时在热量的影响下,又加快了金属构件的磨损,所以油系统的故障是汽轮机工作中比较普遍的一种故障,如果油路管路中的油质达不到规范的要求,则会造成油路不畅通,因此,必须在生产中对油路管路中储存的油质进行监控,以保证其满足规范的要求,油系统体系在长时间的运转中,其内部的支承构件发生摩擦是一种必然的现象,如果其内壁的厚度降低到某一程度,其间隙就会增大,汽轮机在使用过程中,由于机油系统存在漏油、漏气或高温等问题,导致汽轮机出现不正常的振动。
2汽轮机油系统中几种常见故障的解决方法基于上述问题,逐一对上述几种常见的故障问题提出了相应的解决措施:针对汽轮机中出现的污渍,我们可以采用改进汽轮机所用的水质来减轻污渍,目的是从根源上保证汽轮机的正常运转。
在汽轮机的生产过程中,都会发出相应的安装规范,汽轮机在投入使用前,必须按照安全规范来进行安装,特别是对各轴承零件的拧紧情况,要做好相应的规范,并在调节好各轴承之间的间隙后,才能开始工作,以确保轴承的正常运转。
汽轮机检修中油系统的常见故障分析以及处理

汽轮机检修中油系统的常见故障分析以及处理摘要:汽轮机是一种重要的机组设备,维持汽轮机的稳定、正常运行是企业生产过程中的重点。
为了保证汽轮机正常运行,必须要定期对其进行检查,在检修过程中,油系统是很容易出现故障的部分,本文对汽轮机检修中油系统的常见故障进行分析,并且提出解决策略,旨在提高汽轮机的工作效率。
关键词:汽轮机;检修;油系统;故障;解决措施一、汽轮机的工作原理以及油系统常见故障1.1汽轮机的工作原理汽轮机主要应用作发电用的原动机,同时,也可以对各种泵、风机、压缩机以及船舶螺旋桨等。
汽轮机是将蒸汽机的能量转换为机械功的旋转式动力机械,也被称之为蒸汽透平。
汽轮机的组成比较简单,主要是由两大部分组成,一部分是转动部分,另一部分为固定部分。
通长,转动部分被称之为转子,而固定部分被成为静子。
汽轮机的转动部分的部件包括:叶栅、叶轮或者是转子,主轴和联轴器以及紧固件等一些旋转部件。
而固定部分包括气缸、蒸汽室、喷嘴室、隔板、以及隔板套,汽封、轴承和轴承座、机座、滑销系统等一些有关的紧固的部件。
汽轮机在正常的工作当中,以蒸汽为主要的动力,将蒸汽的热能转化为机械功的旋转机械。
汽轮机被现代的诸多火力发电厂广泛的应用,它自身具有单机功率大,工作效率高,寿命比较长的优点。
这些特点决定了汽轮机在工作的过程中工作效率比较高。
1.2油系统中的常见故障(1)DEH油系统的常见故障汽轮机工作的过程中,油系统出现故障,通产个都是因为EH油箱油位已经低于450毫米,油温低于20摄氏度;在油泵正常运行之后,油压低于11.2MPa:;另外,又系统的隔膜阀、OPC电磁阀以及AST电磁阀没有严密的关闭,或者OPC电磁阀失去了电源或本身就没有送电;也有可能是油系统中任一伺服阀发生了故障,油系统中两支以上的蓄能器没有投入运行;另外,油系统中的主要指示以及压力开关动作出现异常,或者连锁保护失常等。
这些都是导致汽轮机中油系统故障频发的原因。
(2)EH系统的常见故障导致EH系统出现故障的原因有很多,在正常工作过程中,EH油箱的油位下降;EH油压下降;也有可能EH的油温超过了正常的油温所致;更有可能在挂闸后,油动机没能按照指令开调门。
试述汽轮机检修中油系统的常见故障及处理
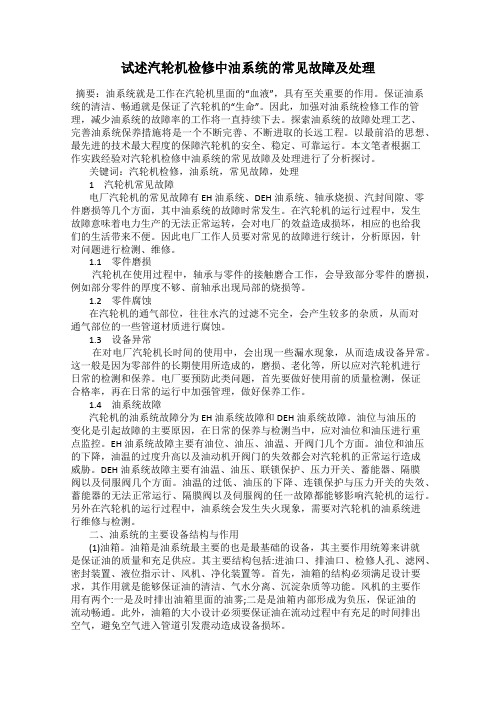
试述汽轮机检修中油系统的常见故障及处理摘要:油系统就是工作在汽轮机里面的“血液”,具有至关重要的作用。
保证油系统的清洁、畅通就是保证了汽轮机的“生命”。
因此,加强对油系统检修工作的管理,减少油系统的故障率的工作将一直持续下去。
探索油系统的故障处理工艺、完善油系统保养措施将是一个不断完善、不断进取的长远工程。
以最前沿的思想、最先进的技术最大程度的保障汽轮机的安全、稳定、可靠运行。
本文笔者根据工作实践经验对汽轮机检修中油系统的常见故障及处理进行了分析探讨。
关键词:汽轮机检修,油系统,常见故障,处理1汽轮机常见故障电厂汽轮机的常见故障有 EH 油系统、DEH 油系统、轴承烧损、汽封间隙、零件磨损等几个方面,其中油系统的故障时常发生。
在汽轮机的运行过程中,发生故障意味着电力生产的无法正常运转,会对电厂的效益造成损坏,相应的也给我们的生活带来不便。
因此电厂工作人员要对常见的故障进行统计,分析原因,针对问题进行检测、维修。
1.1零件磨损汽轮机在使用过程中,轴承与零件的接触磨合工作,会导致部分零件的磨损,例如部分零件的厚度不够、前轴承出现局部的烧损等。
1.2零件腐蚀在汽轮机的通气部位,往往水汽的过滤不完全,会产生较多的杂质,从而对通气部位的一些管道材质进行腐蚀。
1.3设备异常在对电厂汽轮机长时间的使用中,会出现一些漏水现象,从而造成设备异常。
这一般是因为零部件的长期使用所造成的,磨损、老化等,所以应对汽轮机进行日常的检测和保养。
电厂要预防此类问题,首先要做好使用前的质量检测,保证合格率,再在日常的运行中加强管理,做好保养工作。
1.4油系统故障汽轮机的油系统故障分为 EH 油系统故障和 DEH 油系统故障。
油位与油压的变化是引起故障的主要原因,在日常的保养与检测当中,应对油位和油压进行重点监控。
EH 油系统故障主要有油位、油压、油温、开阀门几个方面。
油位和油压的下降,油温的过度升高以及油动机开阀门的失效都会对汽轮机的正常运行造成威胁。
汽轮机油系统故障原因分析及改进措施解析
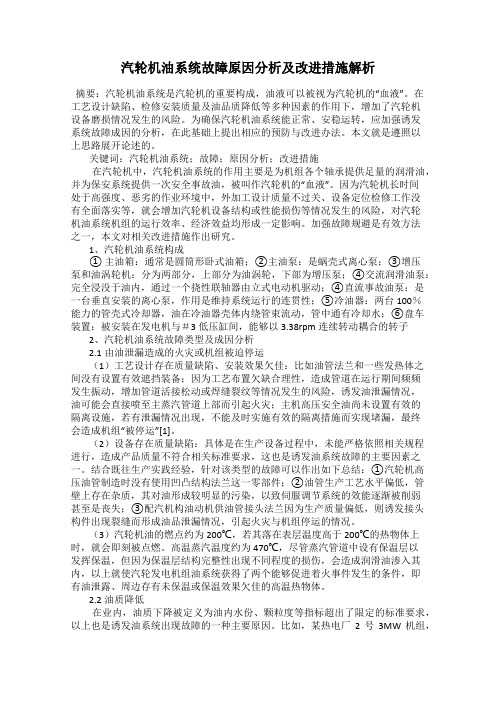
汽轮机油系统故障原因分析及改进措施解析摘要:汽轮机油系统是汽轮机的重要构成,油液可以被视为汽轮机的“血液”。
在工艺设计缺陷、检修安装质量及油品质降低等多种因素的作用下,增加了汽轮机设备磨损情况发生的风险。
为确保汽轮机油系统能正常、安稳运转,应加强诱发系统故障成因的分析,在此基础上提出相应的预防与改进办法。
本文就是遵照以上思路展开论述的。
关键词:汽轮机油系统;故障;原因分析;改进措施在汽轮机中,汽轮机油系统的作用主要是为机组各个轴承提供足量的润滑油,并为保安系统提供一次安全事故油,被叫作汽轮机的“血液”。
因为汽轮机长时间处于高强度、恶劣的作业环境中,外加工设计质量不过关、设备定位检修工作没有全面落实等,就会增加汽轮机设备结构或性能损伤等情况发生的风险,对汽轮机油系统机组的运行效率、经济效益均形成一定影响。
加强故障规避是有效方法之一,本文对相关改进措施作出研究。
1、汽轮机油系统构成① 主油箱:通常是圆筒形卧式油箱;②主油泵:是蜗壳式离心泵;③增压泵和油涡轮机:分为两部分,上部分为油涡轮,下部为增压泵;④交流润滑油泵:完全浸没于油内,通过一个挠性联轴器由立式电动机驱动;④直流事故油泵:是一台垂直安装的离心泵,作用是维持系统运行的连贯性;⑤冷油器:两台100%能力的管壳式冷却器,油在冷油器壳体内绕管束流动,管中通有冷却水;⑥盘车装置:被安装在发电机与#3低压缸间,能够以3.38rpm连续转动耦合的转子2、汽轮机油系统故障类型及成因分析2.1由油泄漏造成的火灾或机组被迫停运(1)工艺设计存在质量缺陷、安装效果欠佳:比如油管法兰和一些发热体之间没有设置有效遮挡装备;因为工艺布置欠缺合理性,造成管道在运行期间频频发生振动,增加管道活接松动或焊缝裂纹等情况发生的风险,诱发油泄漏情况,油可能会直接喷至主蒸汽管道上部而引起火灾;主机高压安全油尚未设置有效的隔离设施,若有泄漏情况出现,不能及时实施有效的隔离措施而实现堵漏,最终会造成机组“被停运”[1]。
汽轮机检修中油系统的常见故障及处理途径

汽轮机检修中油系统的常见故障及处理途径下载提示:该文档是本店铺精心编制而成的,希望大家下载后,能够帮助大家解决实际问题。
文档下载后可定制修改,请根据实际需要进行调整和使用,谢谢!本店铺为大家提供各种类型的实用资料,如教育随笔、日记赏析、句子摘抄、古诗大全、经典美文、话题作文、工作总结、词语解析、文案摘录、其他资料等等,想了解不同资料格式和写法,敬请关注!Download tips: This document is carefully compiled by this editor. I hope that after you download it, it can help you solve practical problems. The document can be customized and modified after downloading, please adjust and use it according to actual needs, thank you! In addition, this shop provides you with various types of practical materials, such as educational essays, diary appreciation, sentence excerpts, ancient poems, classic articles, topic composition, work summary, word parsing, copy excerpts, other materials and so on, want to know different data formats and writing methods, please pay attention!汽轮机检修中油系统的常见故障及处理途径在汽轮机检修过程中,油系统故障是常见的问题之一,正确的识别和处理可以有效提升设备的可靠性和效率。
汽轮机润滑油系统的常见故障和原因探究

汽轮机润滑油系统的常见故障和原因探究汽轮机润滑油系统在运行过程中,常常会出现一些故障,影响到汽轮机的正常运行。
本文将探究汽轮机润滑油系统的常见故障及其原因,并提出相应的解决方案。
1. 润滑油泵故障:润滑油泵是汽轮机润滑油系统的核心设备,当润滑油泵出现故障时,将导致油压不足,无法保证油膜的形成和润滑效果的达到,严重时可能会引起轴瓦焊接、轴承锈蚀等故障。
主要原因:1)润滑油泵叶轮磨损、变形或断裂;2)润滑油泵轴承损坏;3)润滑油泵进口阻力过大;4)润滑油泵进口管道堵塞。
解决方案:1)定期进行润滑油泵的检查和维护,及时更换磨损严重的叶轮;2)及时更换润滑油泵的轴承;3)清理润滑油泵进口管道。
2. 润滑油过滤器堵塞:润滑油过滤器是保证润滑油质量的重要设备,当润滑油过滤器堵塞时,将导致润滑油中的杂质和污染物无法得到有效过滤,影响到润滑油的质量和润滑效果。
主要原因:1)润滑油过滤器滤芯堵塞;2)润滑油中的杂质和污染物积聚过多;3)润滑油过滤器不定期清洗和更换。
主要原因:1)润滑油冷却器内部结垢;2)润滑油冷却器外部进风口被灰尘堵塞;3)润滑油冷却器进出口管道阻塞。
4. 润滑油质量下降:润滑油在运行过程中,会受到杂质、水分和氧化等因素的影响,从而导致润滑油质量下降。
解决方案:1)定期对润滑油进行脱水、净化和过滤处理,降低杂质和水分的含量;2)根据使用规定,定期更换润滑油;3)提高润滑油的贮存条件,避免氧化和污染。
汽轮机润滑油系统的常见故障包括润滑油泵故障、润滑油过滤器堵塞、润滑油冷却器堵塞和润滑油质量下降等问题。
解决这些故障的关键在于定期检查和维护润滑油系统的各个部分,并采取相应的处理措施,以确保润滑油的质量和润滑效果的达到。
分析电厂汽轮机检修中油系统常见故障与应对措施

分析电厂汽轮机检修中油系统常见故障与应对措施发布时间:2022-10-09T01:26:05.597Z 来源:《科技新时代》2022年第6期作者:王晓辉[导读] 汽轮机调节油系统为控制汽轮机进汽阀阀位的伺服执行机构和汽轮机超速保护控制器及自动停机脱扣装置提供油温王晓辉京能(锡林郭勒)发电有限公司内蒙古锡林郭勒盟 026200摘要:汽轮机调节油系统为控制汽轮机进汽阀阀位的伺服执行机构和汽轮机超速保护控制器及自动停机脱扣装置提供油温、油压稳定和油质合格的高压动力油,所使用的动力油为磷酸酯抗燃油。
在电厂运行操作期间,汽轮机运作可能会出现许多油系统问题。
必须修复才能彻底解决问题。
及时进行计划维护。
文章根据最新电厂汽轮机常见故障,做了数据分析,确定出常见的故障,制定了以下有效对策。
关键词:电厂汽轮机;油系统;常见故障;应对措施引言随着人类社会的飞速发展与科技进步,汽轮机逐渐取代了蒸汽机与内燃机,成为人类社会的主要动力来源,其以突出的大功率和低事故率被广泛应用于机械制造,是时下最普遍的动力机械。
但低事故率不等于无事故,在汽轮机的日常运转过程中,仍需要对其进行及时检修,排除故障,确保其动力提供的稳定性。
1油系统故障原因分析汽轮机在运行过程中,还可能出现油系统故障。
一旦汽轮机发生油系统故障,不仅会导致汽轮机发生严重的漏油现象,造成资源的严重浪费,还会影响汽轮机的整个机组润滑系统,进而造成非常严重的危害,影响汽轮机的运行速度和运行效率。
在进行汽轮机安装的过程中,如果汽轮机的密封度不符合要求,或者是汽轮机在运行过程中密封面发生损坏,会导致汽轮机在运行过程中出现严重的漏油故障,影响汽轮机的正常运行。
除此之外,油是保障汽轮机正常运转的关键因素之一,我们需要保障汽轮机的优质符合汽轮机的运行条件。
如果油罐的清洁工作不到位,将会加速优质的恶化,影响汽轮机的正常运转。
2电厂汽轮机检修中油系统常见故障的应对措施2.1提高电厂汽轮机操作工艺水平,从而保证设备的安装质量在工作过程中,生产都需要精密的设备来保证生产的正常运行。
锅炉给水泵汽轮机油系统故障和处理模版

锅炉给水泵汽轮机油系统故障和处理模版锅炉给水泵是锅炉燃烧的关键组件之一,负责将给水输送到锅炉中进行加热。
而汽轮机油系统则是维持汽轮机正常运转的重要设备,负责润滑和冷却机械运动部件。
然而,由于各种因素,锅炉给水泵和汽轮机油系统在运行过程中可能会发生故障。
本文将介绍一些常见的故障现象,并探讨如何处理这些故障。
一、锅炉给水泵故障1. 给水泵无法启动故障现象:给水泵无法启动,没有水流送入锅炉。
处理方法:a. 检查电源供应是否正常,确保给水泵的电源接线没有松动或断裂。
b. 检查控制回路,确保给水泵的控制开关或继电器没有故障。
c. 检查给水泵的电机是否正常运转,如果电机有异响或发热现象,应立即停机检修。
d. 检查给水泵的吸入和排出管路,确保其中没有堵塞或泄漏。
2. 给水泵水流量不稳定故障现象:给水泵的水流量时大时小,无法保持稳定。
处理方法:a. 检查给水泵的叶轮和轴承,确保其没有磨损或堵塞。
b. 检查给水泵的进口和出口阀门,确保其完全打开或关闭。
c. 检查给水泵的吸入管路,确保其没有堵塞或泄漏。
d. 检查给水泵的注水管路,确保其中没有堵塞或漏水。
3. 给水泵噪音过大故障现象:给水泵运转时产生噪音过大,影响生产和工作环境。
处理方法:a. 检查给水泵的叶轮和轴承,确保其没有磨损或断裂。
b. 检查给水泵的基础和底座,确保其稳固牢固,没有松动或振动。
c. 检查给水泵的进口和出口管路,确保其没有漏水或漏气。
d. 检查给水泵的密封件,确保其没有损坏或老化。
二、汽轮机油系统故障1. 油温过高故障现象:汽轮机油温度升高超过正常范围。
处理方法:a. 检查油温传感器和温度控制装置,确保其准确可靠。
b. 检查油路管道和散热器,确保其畅通无阻。
2. 油压过低故障现象:汽轮机油压力下降到较低值,无法维持正常运转。
处理方法:a. 检查油压传感器和压力控制装置,确保其正常工作。
b. 检查油路管道和油泵,确保其正常工作和无泄漏。
3. 油质污染故障现象:汽轮机油中出现杂质、水分或颗粒物。
汽轮机油系统着火的原因现象和处理

汽轮机油系统着火的原因现象和处理
1.原因
(1)滑油温度升高:由于过高的运行工况或冷却系统的故障导致滑油温度升高,使滑油发生氧化反应,产生高分子沥青质和硅酸盐等易于沉积的物质,进而引起着火。
(2)受污染的滑油:当滑油被杂质或水分等污染时,会产生一系列的腐蚀和氧化反应,进而导致滑油的性能降低,增加着火的风险。
(3)润滑系统故障:当润滑系统中的滤油器、冷却器、油泵等部件发生故障时,会导致滑油循环不畅或滑油供应不足,进而提高了发生着火的可能性。
2.现象
(1)异常油温:油温过高是着火的常见现象,可能会导致严重的着火事故发生。
(2)油污:滑油系统出现异常的油污现象,如油黏度增大,沉积物增多等。
(3)噪声或振动:由于滑油系统的异常,可能导致汽轮机工作时出现噪声或振动等异常现象。
3.处理措施
(1)定期检查和更换滑油:定期检查和更换滑油是保持滑油系统状况良好的基本措施,能够有效减少滑油系统出现异常的可能性。
(2)加强润滑系统的维护和保养:对润滑系统中各个部件进行定期维护和保养,如清洗滤油器、冷却器,检查油泵等,以确保润滑系统正常运行。
(3)定期检查油品质量:定期检查滑油的质量,包括黏度、清洁度、含水率等,发现异常及时处理或更换滑油。
(4)安装温度和压力监测装置:安装温度和压力监测装置可以实时监测滑油温度和压力,及时发现异常,采取相应措施。
(5)提高运行监测的水平:通过合理的运行监测手段,及时发现滑油系统的异常情况,采取相应的控制措施,避免发生着火事故。
总之,汽轮机油系统着火是一种严重的安全隐患,通过定期检查和维护润滑系统,监测和控制滑油的质量,加强运行监测,可以有效降低着火的风险,确保汽轮机的安全运行。
- 1、下载文档前请自行甄别文档内容的完整性,平台不提供额外的编辑、内容补充、找答案等附加服务。
- 2、"仅部分预览"的文档,不可在线预览部分如存在完整性等问题,可反馈申请退款(可完整预览的文档不适用该条件!)。
- 3、如文档侵犯您的权益,请联系客服反馈,我们会尽快为您处理(人工客服工作时间:9:00-18:30)。
文件编号:GD/FS-3800
(安全管理范本系列)
汽轮机油系统故障分析及
对策详细版
In Order To Simplify The Management Process And Improve The Management Efficiency, It Is Necessary To Make Effective Use Of Production Resources And Carry Out Production Activities.
编辑:_________________
单位:_________________
日期:_________________
汽轮机油系统故障分析及对策详细
版
提示语:本安全管理文件适合使用于平时合理组织的生产过程中,有效利用生产资源,经济合理地进行生产活动,以达到实现简化管理过程,提高管理效率,实现预期的生产目标。
,文档所展示内容即为所得,可在下载完成后直接进行编辑。
油系统是汽轮机的重要组成部分,其工作状况直接影响到机组的安全经济运行。
因汽轮机油系统导致机组故障、设备损坏的事故屡有发生,特别是在基建调试阶段,此类事故更易出现。
下面介绍几起基建调试阶段发生的汽轮机油系统故障现象及原因。
1 故障现象及原因
1.1 油质不良造成故障
油质不良主要是指油中的水份、颗粒度等指标超过规定标准。
如1996年1月某电厂1号机组(300MW)调试阶段停机消缺期间,将主油箱内的油倒入储油箱中,因储油箱内未清理干净引起润滑油污
染造成设备损伤。
同年11月该厂2号机组(300 MW)调试中因油质不良多次造成中压主汽门伺服阀及DUMP阀卡死、伺服机构节流孔堵等故障。
1997年1月某电厂13号机组(125 MW)在带负荷调试中出现中联门卡、润滑油压低等现象,经检查均为油脏所致,揭瓦后还发现机组轴颈拉伤、轴瓦拉毛。
油质不良的原因主要有两个方面:一是制造质量不好,油出厂时就存在油质不合格的问题;二是受外界污染。
1.2 设备质量不良造成故障
设备质量不良是指设备及附件在加工、制造过程中工艺未按有关规定执行,致使质量不符合标准要求。
设备质量不良是油系统故障的主要原因之一。
如1996年1月某电厂1号机组(300 MW)调试期间停机检查中发现主油箱内壁油漆脱落造成油质恶化,磨
损汽机轴颈、轴瓦(主油箱内壁未按要求进行处理)。
同年11月该厂2号机组(300 MW)因密封油装置内部不清洁,其中14只阀门壳体严重锈蚀,引起油系统污染,不仅影响了密封油系统的正常运行和机组的调试工作,还造成设备损伤。
1996年10月某电厂5号机组(300 MW)首次整套启动后停机揭瓦发现4号轴瓦拉毛、轴颈拉伤,进一步检查发现密封油系统阀门质量低劣且内部残留较多杂质(锈蚀物、铁屑等),造成密封油和润滑油系统污染及设备损坏。
以上两例密封油系统引起的事故均是因设备出厂前未能认真进行质量检验,致使问题未能及时发现和解决所致。
1.3 其他原因造成故障
除油质和设备质量不良外,安装工艺不精、技术措施不完善等也是造成油系统故障的主要原因。
如
1989年9月某电厂1号机组(125MW)试运中“主油泵进、出口压力低”,检查发现为油系统防火门及注油器喷嘴装反所致。
1995年12月某电厂3号机组(300 MW)72 h试运结束后停机揭瓦发现2、3、4号轴颈和轴瓦均有不同程度损伤,均因在油系统管路的弯头处有一约1 cm2的残留金属片,在安装和滤油过程中未能及时发现和清理。
2 对策和措施通过以上故障现象可以看出要防止油系统事故的发生必须从设备的制造、安装、运行等多方面入手,既要有精良的制造、安装工艺,又要有完善的技术措施,才能保证设备的安全经济运行。
2.1 严把设备质量关确保设备安全运行
良好的设备质量是安全经济运行的基础,没有质量的保证无法谈及安全运行。
因此,一方面需要设备制造厂在加强内部管理的前提下,不断提高生产工
艺水平,严把设备质量关,杜绝不合格的产品投入生产运行;另一方面,用户也应在设备制造期间派人到厂监造,确保质量符合要求。
2.2 提高工艺水平保证设备安装质量
精良的安装工艺是设备安全运行的保证。
设备安装前必须在现场解体检查并清理,油管道还要进行化学清洗;设备安装过程中不仅要注意环境因素的影响,更要注重设备安装的工艺水平。
油系统的安装有着较高的工艺标准,例如油管道的焊接、油箱内壁的处理、油系统各类设备的安装等工艺要求在规程中都有明确规定,安装时必须严格执行并按部就班进行,决不能偷工减料、图省事,安装结束后须彻底清理设备及系统内部,避免残留杂物。
另外还要加强安装阶段的监理工作,坚持多级验收检查制度,保证安装质量。
2.3 完善技术措施加强油务监督
完善的技术措施是避免事故发生的保障。
油系统正式投运前必须要有完善的切实可行的技术措施进行油循环冲洗和过滤,以使油质达到规程标准,符合设备运行要求。
通常在油循环冲洗过程中采取以下措施:
(1) 分段循环,即按照系统的设备布置利用外置滤油机或本机油泵进行分段油循环冲洗。
如:首先将外置滤油机和油箱组成一个独立系统进行油循环,待油质合格后,再将油箱并入系统;而后将轴承进出口油管与轴承之间断开并用短管连接(轴承不参与循环回路)进行油循环冲洗(小循环),待油质合格后将短管拆除,恢复正常连接再进行油循环冲洗(大循环)。
油冲洗期间要注意检查轴承处是否有杂质,并用面团粘除。
(2) 油系统中加装临时滤网或磁棒,清除油中的颗粒物和铁磁性物质。
一般在每一个轴承的进油管上分别加装临时滤网(其面积稍大于进油管面积,其孔径小于油系统原设计滤网的孔径),以防油中的颗粒物进入轴承,要经常检查、清理或更换滤网,防止滤网堵塞或损坏;磁棒一般装置在油箱中,用以吸附油中的铁屑、锈皮等杂质并除之。
(3) 采取升降油温并击打管道等措施,提高油冲洗效果。
用电加热器将油温升至70℃左右再自然冷却到环境温度,如此反复多次,利用温度交变,使粘附在油箱、管道和设备内壁上的氧化物等杂质松动、脱落,同时击打管道加快杂质剥离、流动,以提高冲洗效果。
(4) 油循环冲洗过程中要有足够的油流量(正常运行的油流量)保证系统得到充分冲洗并带走杂质,
油循环期间要经常采样化验分析,只有待油质完全符合标准要求后才可将油倒入正常的系统中运行。
管道弯头、接口和设备内拐角是杂质的集中处,因此对系统中的弯头和死角等处更要认真检查,彻底清理系统内残留的杂质;还要防止外来因素的影响,如:周围环境的灰、水以及雨、雪等杂质进入油系统中污染油质。
油系统故障造成的损失是很大的,教训也是深刻的,如何减少和避免事故的发生,关键是要抓好质量管理工作,特别是设备的制造、安装质量;另外,运行管理也不可放松,要从每一个环节深入细致地抓起,疏忽了任一环节都有可能造成事故的发生,并带来不必要的损失。
可在这里输入个人/品牌名/地点
Personal / Brand Name / Location Can Be Entered Here。