KBR合成氨工艺的节能省气新技术
KBR的煤制合成氨新工艺(NH3)

KBR的煤制合成氨新工艺摘要KBR传愉床气化炉(也称之为TRIG)是一种先进的煤气化技术,可提供干净、无颗拉的合成气。
TRIG是一种紧凑的加压循环流化床反应器,无内部或移动部件。
其运行和机械设计源自KBR的流化催化裂化(FCC)技术,该技术已有60多年的成功商业运营经验。
描述了煤制合成氛的KBR新工艺,其中TRIG作为KBR合成氛装里流程中的一部分,向一个典型的1500t/d的合成氨回路提供氮气。
论述了基于TRIG 特性的工艺整合和优化要素,以实现稳定高效的煤制合成氛工厂设计。
关键词:KBR传输床,气化炉,煤气化,新工艺0前言煤气化是指在高温、高压、蒸汽以及有限的氧气存在的情况下,将煤炭分解气化的过程。
通过限制氧气的量,可避免煤的完全燃烧,使煤炭分解成更有价值的合成气(主要成分是一氧化碳和氢气)。
在合成氨生产工艺中,煤要尽量多地转化为氢气;煤气化产生的粗合成气与蒸汽发生催化变换反应,将其中的一氧化碳转化为二氧化碳,同时产生更多的氢气用于氨合成。
煤气化的实际化学原理相当复杂,目前其基本依据是煤炭的非催化部分氧化反应,通常在高温耐火衬里容器内进行。
在煤气化过程中会产生多种副产品,煤中的硫大多转化为硫化氢和氧硫化碳,氮转化为氨和氰化氢。
煤的燃烧程度取决于输送至气化炉的氧气量。
气化炉一般在绝热状态下工作,放热反应产生的热必须与吸热反应消耗的热以及原料升温至反应温度所需热量保持平衡。
反应温度通常通过向气化炉内添加水或蒸汽来进行控制。
1 KBR传输床气化炉KBR传输床气化炉(也称之为TRIG'')是一种先进的循环流化床反应器,没有内部或移动部件,可在空气和氧气两种模式下工作。
TRIG的机械设计和操作是基于KBR 的流化催化裂化(FCC)技术,已有60多年的成功商业运行经验。
与传统的循环流化床相比,TRIG的固体循环速率和气体流速要快很多,提升管密度要大很多,因此具有较高的生产能力和碳转化率、混合均匀、传热和传质速率较快等特点。
化工合成氨工艺分析及节能改造措施

化工合成氨工艺分析及节能改造措施摘要:本论文旨在对化工合成氨工艺进行分析,并提出相应的节能改造措施。
首先,通过对合成氨的重要性和应用领域的介绍,强调了提高合成氨工艺的能源效率的重要性。
然后,详细分析了传统合成氨工艺的工艺流程及其能耗特点。
接着,提出了一些有效的节能改造措施,包括催化剂的改良、反应器的优化和废热回收利用等。
最后,总结了这些改造措施对于提高合成氨工艺的能源效率和可持续发展的意义。
关键字:化工;合成氨;节能改造;能源效率;可持续发展引言:合成氨是化工领域中重要的中间体和气体产品,在农业、化肥、医药和能源等多个领域有广泛的应用。
然而,传统的合成氨工艺存在能耗高、环境污染严重等问题,不利于可持续发展的要求。
因此,通过对合成氨工艺的分析和改造,提高其能源效率成为亟待解决的问题。
本文将对传统合成氨工艺进行深入分析,并提出相应的节能改造措施,以期为化工行业提供可持续发展的解决方案。
一、传统合成氨工艺的分析传统的合成氨工艺是通过哈伯-博士过程进行合成氨的方法。
该工艺主要包括三个步骤:氮气和氢气的制备、氮氢混合气的合成、合成氨的分离和提纯。
然而,传统工艺存在一些问题,如能耗高、原料利用率低、废热排放等,限制了工艺的能源效率和生产效率。
首先,传统合成氨工艺中的能耗问题主要体现在高温高压的工艺条件下。
由于反应需要较高的温度和压力,导致能源消耗较大。
此外,传统工艺中催化剂的活性较低,需要更高的温度和压力来促进反应,进一步增加了能源的消耗。
其次,传统工艺中的原料利用率较低。
在传统合成氨工艺中,氮气和氢气是主要的原料。
然而,由于反应条件不理想,导致原料的利用率较低,大量原料被浪费。
原料的低利用率不仅增加了生产成本,还对资源的可持续利用造成了压力。
此外,传统合成氨工艺中存在废热排放问题。
在反应过程中,产生大量的废热,其中一部分以冷却水或空气形式排放,导致能源的浪费。
废热的排放不仅造成了能源资源的浪费,还对环境造成了污染。
KBRs 新工艺PURIFIERplus

KRESTM 经验 (续)
♦ Methanex的日产量为350吨的装置于1994年在加 拿大投产,并且一直无故障运行。 ♦ KBR优化了其KRES装置的设计,将成本降低了 40%-60%。 ♦ 第二台日产量为1100公吨的KRES装置于2003年 在中国投产
© 2009 KBR. 保留所有权利.
辽河 KRESTM 改造项目
议程
♦ 什么是 PURIFIERplusTM 工艺? ♦ 工艺特点 ♦ PURIFIERplus 工艺的优势 ♦ KRESTM 和 PurifierTM工艺方面的经验 ♦ 总结
© 2009 KBR. 保留所有权利.
KBR 换热式转化系统 (KRESTM)
过量空气
去废锅 ~ 600 - 800oC
原料和 蒸汽 工艺加热炉 自热式转化炉 (ATR)
♦ 氨厂
20世纪70年代的KBR传统设计 原设计的日生产能力为1000公吨/天 实际运行日产量为1070公吨
♦ KBR的工作范围
可行性研究 工艺包和扩充基础设计
♦ 非-KBR的工作范围
由中国寰球工程公司进行详细工程设计 由辽河进行采购和项目管理 由中建九局施工
© 2009 KBR. 保留所有权利.
♦ 已证实是耗能最低的工艺
中海油 6.5 Gcal/公吨
© 2009 KBR. 保留所有权利.
PURIFIERplusTM 工艺总结
♦ 由经工业实施验证且切实可靠的 KRESTM 和 PurifierTM 工艺技术组合而成 ♦ 由于这一最佳组合,不再需要空分装置 ♦ 取替了一段转化炉,降低了设备成本 ♦ 可靠性提高,因为换热式转化炉比转化炉更可靠
© 2009 KBR. 保留所有权利.
浅析合成氨工艺节能措施

浅析合成氨工艺节能措施摘要:合成氨的生产能耗分为原料能耗和燃料能耗两局部,布朗公司正是基于降低合成氨过程燃料能耗方面的构思以及在这方面的努力,形成了温和的一段转化、二段炉参加过量空气、深冷净化的布朗根本工艺。
这就是布朗合成氨技术在合成氨的过程中,有诸多节能工艺,与其它的节能工艺相比,布朗合成氨工艺在甲烷化的净化根底上又添加了一道被称为"大冰箱";的深冷净化工艺。
关键词:煤制合成氨;装置;布朗合成氨;深冷净化工艺;节能是我国未来开展的重要内容,以现阶段煤制合成氨装置应用情况为根底,结合近年来能源消耗特点,分析煤制合成氨装置能源消耗特点,并结合我国未来开展需求提出全新的节能方向,基于此,主要探讨分析煤制合成氨装置的节能措施。
一、布朗合成氨工艺和其他合成氨技术根本相同,布朗合成氨生产工艺主要包括压缩原料气体,对原料气体进行脱硫处理、转化与压缩以及一氧化碳的上下温变换和对于气体的吸收〔主要是二氧化碳,两个时期的变换〕,甲烷化,枯燥的合成,低温净化合成气压缩、氨合成和冰冻等工序。
其中布朗合成氨技术的核心所在就是深冷净化工艺。
低温净化的效果是完全别离制备新鲜气体和合成氨,在很大程度上提高了操作的灵活性。
生产过程中,深冷净化技术可以有效地解决转化,净化局部等不可预料的波动操作,所以对合成局部根本没有影响,增加了操作弹性,使得操作更容易、更便捷。
另一个主要作用是去除杂质,主要是一些杂质气体〔一氧化碳、甲烷氩气等〕,使得H2与N2的比率维持在3∶1。
布朗公司在生产过程中的重要的措施是降低能源消耗〔降低燃气消耗〕,减少一段转化炉负荷,增加二段转化炉负荷。
其中重要的一个步骤是保证二段转化炉中含有过量气体,这可以使得参加的多于气体和氢、甲烷反响产生大量的热量,从而满足工艺生产中所需的热量。
甲烷化工序的过程后,深冷别离装置可以用来去除多余氮,同时也能得到浓度较高的H2和N2〔大约含有0.2%的Ar〕。
低热值天然气合成氨工艺中的节能技术

低热值天然气合成氨工艺中的节能技术郑厚超【摘要】Zhonghai Petrochemical Co.,Ltd.Phase II(referred to as Fudao Phase II)1500t/d ammonia plant,designed with a methane content of about 60.7% in the feed gas,which is a typical low calorific value natural gas,using KBR combined ammonia synthesis technology.The KBR process is the only synthetic ammonia process capable of treating low-calorie natural gas containing high concentrations of N2 and CO2.Its cryogenic technology has many advantages,such as high gas elasticity,stable operation,convenient operation and high efficiency.Good energy saving and so on.In this paper,the KBR process is compared with the other two processes to some extent,and the energy saving measures of the KBR process are studied and analyzed.%中海石油化学股份有限公司二期(简称富岛二期)1 500t/d合成氨装置,设计原料气中甲烷含量为60.7%左右,为典型的低热值天然气,采用KBR组合合成氨工艺技术.KBR工艺能够处理原料气为含高浓度N2和CO2的低热值天然气的合成氨工艺,其深冷技术具有诸多方面的优势,突出表现在原料气弹性大、运行稳定、操作便捷、效率高以及节能性好等方面.将KBR工艺与其他两项工艺进行一定程度的对比分析,并对KBR工艺的节能措施进行研究分析.【期刊名称】《化工设计通讯》【年(卷),期】2019(045)009【总页数】2页(P5-5,18)【关键词】合成氨;低热值;天然气;节能技术【作者】郑厚超【作者单位】中海石油化学股份有限公司,海南东方 572600【正文语种】中文【中图分类】TQ113.21 低热值天然气合成氨工艺对比分析当前状况下,常用的合成氨工艺主要有凯洛格工艺、布朗工艺以及KBR工艺,这三种合成氨工艺运行过程中的主要参数主要如下:①凯洛格工艺:在一段转化阶段,其水碳比为3.2,温度为805℃、压力达到了3.6MPa,炉型主要采用了顶烧炉,转化的温度相对较高;在二段转化阶段,运用凯洛格工艺处理残余的甲烷低于0.5%,在净化方面采用低热耗苯菲尔法、四级闪蒸;在氨合成阶段,在合成气压缩机段间设置了分子筛脱水,氨冷气选择组合式,并运用中空纤维管对氢气进行回收,在这一阶段压力达到了14.5MPa。
浅析合成氨工艺节能措施

浅析合成氨工艺节能措施1. 引言1.1 研究背景合成氨是一种重要的化工产品,广泛应用于农业和工业领域。
随着社会经济的发展和人们对资源利用效率的要求越来越高,合成氨工艺节能措施成为研究的热点之一。
在合成氨生产过程中,能源消耗大、设备复杂、工艺流程繁琐,因此如何有效减少能源消耗,提高生产效率,已成为工程技术人员急需解决的问题之一。
当前,我国合成氨工业正处于转型升级的关键时期,节能减排已成为企业的必修课。
研究合成氨工艺的节能措施具有重要的现实意义。
本文旨在通过对合成氨生产工艺的概述,以及对节能措施的分析和探讨,探讨如何在合成氨生产中实施节能措施,提高工艺设备的能源利用效率,降低生产成本,促进我国合成氨工业的可持续发展。
1.2 研究目的本文旨在探讨合成氨工艺节能措施的相关问题,通过对合成氨生产工艺的概述和各种节能措施的分析,旨在为工程技术人员提供一些有益的启示和参考。
具体来说,本研究旨在通过优化催化剂配方、改进循环系统、提高装置热效率和优化工艺操作等方式,探讨如何在合成氨生产过程中降低能耗,提高生产效率,减少资源浪费,实现可持续发展。
通过本研究的展开,希望可以为合成氨工艺的节能改造提供一些实用的技术和经验,促进我国化工行业节能减排工作的开展,为环保和可持续发展贡献一份力量。
1.3 研究意义合成氨是一种重要的化工产品,广泛应用于农业、医药、化肥等领域。
在当前能源紧缺和环境污染日益严重的情况下,合成氨工艺的节能措施显得尤为重要。
通过对合成氨工艺的节能研究,可以有效降低生产成本,减少能源消耗,减少排放物,提高工艺效率,从而实现可持续发展的目标。
合成氨工艺的节能研究对于推动我国化工产业的可持续发展具有重要意义。
随着我国经济的不断发展,合成氨工业正处于快速发展阶段,然而高能耗、高排放的问题亟待解决。
通过对节能措施的研究,可以有效提升合成氨工业的生产效率,降低生产成本,减少对环境的影响,提高企业的竞争力,从而实现可持续发展。
kbr天然气合成氨工艺流程
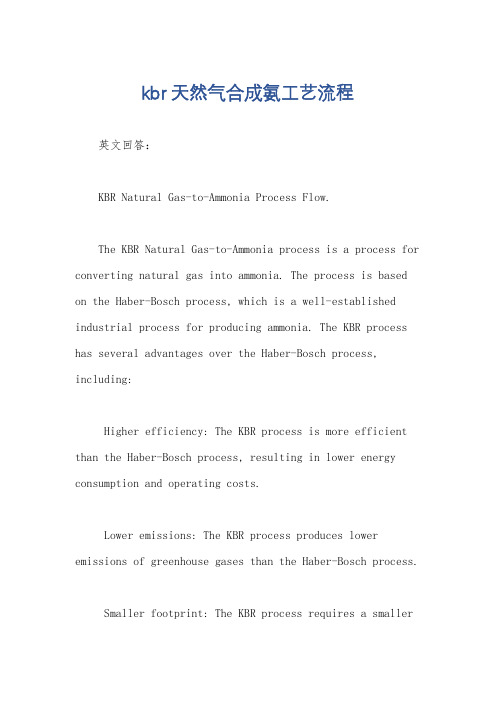
kbr天然气合成氨工艺流程英文回答:KBR Natural Gas-to-Ammonia Process Flow.The KBR Natural Gas-to-Ammonia process is a process for converting natural gas into ammonia. The process is based on the Haber-Bosch process, which is a well-established industrial process for producing ammonia. The KBR process has several advantages over the Haber-Bosch process, including:Higher efficiency: The KBR process is more efficient than the Haber-Bosch process, resulting in lower energy consumption and operating costs.Lower emissions: The KBR process produces lower emissions of greenhouse gases than the Haber-Bosch process.Smaller footprint: The KBR process requires a smallerfootprint than the Haber-Bosch process, making it more suitable for smaller-scale production facilities.The KBR process consists of the following steps:1. Natural gas reforming: The natural gas is reformed with steam in a reforming furnace to produce a mixture of hydrogen and carbon monoxide.2. Shift conversion: The hydrogen and carbon monoxide mixture is converted to hydrogen and carbon dioxide in a shift converter.3. Ammonia synthesis: The hydrogen and nitrogen are compressed and passed through a catalyst bed to produce ammonia.4. Product recovery: The ammonia is recovered from the reaction gases by condensation and separation.The KBR process is a highly efficient and environmentally friendly process for producing ammonia. Theprocess is well-suited for small-scale productionfacilities and can be used to produce ammonia from a variety of natural gas sources.中文回答:凯伯莱天然气制氨工艺流程。
浅析合成氨工艺节能措施

浅析合成氨工艺节能措施1. 引言1.1 合成氨工艺的重要性合成氨是一种重要的化工原料,被广泛用于制造化肥、农药、燃料等产品。
合成氨工艺的重要性在于其在现代社会中的广泛应用,为农业生产、工业生产以及能源生产提供了必要的原料。
合成氨不仅可以提高农作物的产量,还可以满足工业生产对氮肥的需求,同时也可以用作燃料和化工原料。
合成氨的生产工艺一直是工业界关注的焦点之一,因为其生产过程中会消耗大量的能源。
采取节能措施对于合成氨工艺的持续发展至关重要。
通过提高能源利用效率,优化设备设计,改进余热回收系统以及应用先进的控制技术,可以有效降低合成氨生产过程中的能源消耗,实现更加高效、环保的生产过程。
合成氨工艺的重要性体现在其在各个领域的广泛应用以及对现代生产体系的贡献。
为了实现可持续发展,节能减排已经成为全球工业界的共同目标,合成氨工艺的节能措施也需要不断完善和深化。
1.2 能源消耗与节能意义合成氨工艺是工业生产中非常重要的一项工艺,其生产过程需要消耗大量的能源。
能源消耗不仅会增加生产成本,还会对环境造成负面影响。
节能对于合成氨工艺来说至关重要。
合成氨工艺的能源消耗主要来自于压缩、制冷和反应等环节。
压缩机是能源消耗的重要组成部分,压缩机效率的提高可以有效降低能源消耗。
反应器设计的优化和余热回收系统的改进也能有效减少能源消耗。
采用先进的控制技术可以使工艺运行更加稳定高效,也可以进一步减少能源消耗。
节能在合成氨工艺中具有重要的意义,不仅可以降低生产成本、提高生产效率,还可以减少能源消耗对环境的负面影响。
未来的发展方向应当是在不断提高工艺效率的进一步优化能源利用,实现合成氨工艺的可持续发展。
通过不断探索创新,合成氨工艺节能措施将有更广阔的发展前景。
2. 正文2.1 合成氨工艺中的能源消耗主要来源合成氨工艺中最主要的能源消耗来源是氮气的制备。
在合成氨的过程中,氮气与氢气通过催化剂反应生成氨气,而氮气的制备通常涉及空分设备和氧氮分离设备,这些设备消耗大量能源。
合成氨工艺及节能改造分析

·1·合成氨与尿素化 工 设 计 通 讯Ammonia and UreaChemical Engineering Design Communications第45卷第10期2019年10月1 工程案例近年来我国的煤化行业技术在不断更新发展,其中山西煤化工有限公司采用了目前比较先进的技术与相应的设备对合成氨系统不断优化改良,使合成氨系统可以极大减少对能源的消耗,同时可以更加稳定安全的运行,在实际运用后取得了较高的经济效益。
2 对于合成氨工艺步骤的介绍2.1 制造生产工艺所需要的原料在进行合成氨的工艺步骤中,第一,要制备氮气和氢气,并将这些气体加入到原料气体中,其中制造氢气的时候,要使用到的原料是天然气和石脑油等。
将这些原料投入到高温的条件中,跟水蒸气发生化学反应,制造出相应的合成气体,合成气体要含有氢元素和一氧化氮。
通过将原料煤与相应的焦炭固体材料发生变化来制备所需要的合成气体,同时相应的合成气要使用渣油来制作,使用部分催化来进行相应的氧化反应制作所需要的氢气。
除此之外,在制造氮气的过程中,主要运用的原料是空气,把空气实施物理液化或者是采用其他的化学方式,能够得到比较纯净的氨气,然后利用物理的方法来降低温度,使得空气液化之后,再把空气中的温度加大,由于氮气的沸点比较低,通过这种方式来得到纯度较高的氮气,同时也可使用其他的方式可以得到氮气,例如通过一些化学方法。
通过燃烧空气中的可燃碳物质将空气中的二氧化碳排出来,通过这样的方法得到纯度较高的氮气。
2.2 对于原料气体的进化方法在通常的合成氨工艺步骤中,首先就是要对所得的原料气体进行净化,第一,将一氧化氮实施变化和转换,对于原料气体来说,一氧化碳在原料气体中占比较高,需要将这些一氧化碳全部转化为氢气和二氧化碳,只有这样才能更好地消除掉一氧化碳,从而增大氢气的含量。
将一氧化碳进行转化的过程中,所需要的能源是很多的,因此需要通过科学合理的手段来减小能源方面的损失,从而控制生产成本,最大限度地防止出现能源浪费的现象。
合成氨工艺及节能改造措施的分析

4 全精馏提氩在实际生产中的应用某公司28000m 3/h 空分设备全精馏制氩系统已经投入运行。
该装置提氩流程采用的是全精馏无氢提氩。
具体步骤是从主塔的适当位置抽取氩馏分进粗氩塔I ,粗氩塔内冷凝器的冷源采用的是液空,然后在粗氩塔II 的顶部获得含量适中的粗氩,其中粗氩中含氧量应低于3ppm ,含氩量必须大于98%。
从主塔的中部逐步进入液化器内进行冷却,经过冷却后的粗氩从纯氩塔的中部进入塔内参与精馏,最后在纯氩塔的底部可以获取纯度极高的液氩。
整个操作过程中,粗氩液化器与纯氩冷凝器所利用的冷源始终是过冷的污液氮,而纯氩蒸发器采用的热源是中压液氮。
具体操作指标规定如下:(1)抽取氩馏分中的含氩量应为9%~11%,抽取数量应为30000~32000Nm 3/h 。
(2)粗氩的产量为850~950Nm 3/h 。
(3)由于该操作过程的弹性较大,目前实际生产量已超出了设计量。
据操作人员估算,最高产出量可达1000Nm 3/h 。
(4)通过对主塔的污液氮纯度进行控制来实现对氩馏分含量的控制,效果非常明显。
(5)粗氩塔和纯氩塔的压力分别控制在30kPa 和40kPa 为最好。
(6)纯氩塔和粗氩塔之间的压力差必须符合规定的标准。
一般情况下,粗氩塔I 内的指标应控制在4~5kPa ,粗氩塔内的指标应控制在8~10kPa ,纯氩塔内的指标应控制在5~8kPa 。
5 对全精馏提氩操作的思考通过实践,对操作进行了一些改进和设想,具体有三个方面。
(1)粗液氩泵应采用变速调节电机,这样对操作过程有三方面的好处。
①预冷启动比较方便,可以利用低转速启动后,等待设备运行正常后,再逐步提高转速。
②对氧气纯度有稳定作用,因为,从目前实际提氩的操作中发现,当粗液氩泵开始启动时,粗氩将会进入粗氩塔I 内完成精馏,此时,下部出现了过量的回流液进入上塔中,这样一来,很容易降低氧气的纯度,然而,当变速实施调节后,通过逐步缓慢的调节,可以避免因上塔工况受到破坏而引发恶性循环。
合成氨工艺分析及节能改造

合成氨工艺分析及节能改造摘要:合成氨工艺在我国的应用具有重要意义。
合成氨生产过程将消耗大量的煤能源,因此有必要加强合成氨工艺的分析,并改造其工艺技术,实现节能降耗,这对我国能源节约和可持续发展具有重要意义。
本文对合成氨工艺及节能改造措施进行了详细的分析。
关键词:合成氨;工艺流程;节能改造措施氨是人们日常生活中不可缺少的一种化工产品,主要用于农业生产。
合成氨不仅是氮肥生产的基础,并且氨本身就是重要的化肥原料,因氨不仅是重要的无机化学原料,而且是有机化学的基本原料。
由于合成氨需要大量的能源,如果合成氨工艺流程不够科学与环保,这将导致每年由于合成氨而造成的大量资源浪费,因此合成氨工艺需改进。
一、合成氨的工艺流程1、原料气的制取。
该工序的主要目的是制取含有氮和氢的原料气。
氢气主要由天然气、石脑油、重质油、煤、焦炭、焦炉气等原料制取。
工业上通常先在高温下将这些原料与水蒸气作用制得含氢、一氧化碳等组分的合成气,这个过程称为造气。
具体而言,对固体原料煤和焦炭,通常采用固体燃料气化法制取合成气;渣油可用非催化部分氧化法获得合成气;对于气态烃和石脑油,工业上采用两段蒸汽转化法制取合成气。
氮气则主要来源于空气,可通过物理方法空气液化或化学方法得到。
第一种物理方法即首先降低温度使空气液化,再升高温度,沸点低的氮气先逸出,从而获得高纯度氮气。
而化学方法是让碳在空气中燃烧,再用脱除气体中的二氧化碳,即得到氮气。
2、净化原料气。
净化处理原料气是合成氨工艺的重要流程。
这一流程相对复杂,包含以下几个环节:1)变换-氧化碳。
由于通过煤气化制取的原料气内含较大比重的一氧化碳,而在合成氨生产过程中需要将水蒸气、一氧化碳向氢气、二氧化碳进行转变,将一氧化碳向二氧化碳进行转变可降低其脱除的难度,同时可增加氢气含量。
在工业生产过程中,变换一氧化碳是一个需要消耗大量能量的工序,因此应使这一工序的能耗降低,以解决能源浪费问题。
2)原料气脱碳脱硫。
节能新技术在合成氨技术改造中的应用

用情 况 。使 用 三废 混 燃 锅 炉 后 , 蒸 汽 煤 耗 下 降 至 10 k , 蒸 汽 节 约 用 煤 8 g 且 尾 气 达 标 排 放 ; 原 吨 0 g吨 0k, 将
税 6Om 造气炉改造为 高炉体锥形管式 夹套副产 中压蒸汽煤气炉后 , O m 副产蒸汽温度提 高了8 0℃ , 单炉发气量
第3 8卷
第 3期
化 肥工 业
2 1 年 6月 01
节 能 新 技 术 在 合 成 氨 技 术 改 造 中 的 应 用
,
娄 勇
( 肃金 昌化 学工 业集 团有 限公 司 7 7 0 ) 甘 3 00
摘要 介绍三废流化混燃锅炉 、 高炉体锥形 管式夹套 副产 中压蒸汽煤 气炉 、 热功 电联 产汽轮 机等技 术的应
增加 了 l o o~150/ / ( 态 ) 达 到 600~650m / 标 态 ) 吨氨 煤 耗 由 15t 至 、. , o 0 / h 标 1 , 0 0 h( , . 降 13t炉渣 含 碳 质 量
分数 由 2 % 降 至 1% ; 用 热 功 电联 产 汽轮 机技 术后 , 气风 机 每 小 时节 电 4 0k ・ , 动 贫 液 泵 每 小 时 节 电 0 5 采 造 4 W h 拖
batu aeb d dat e ie ak t r eeaig y rd c s a teb po u tta r e y l r c o ya pr p c e f n rt pou t t m,h y rd c s m ss s fn n a p j g o n b e e i b
21 kW ・
技 术 改 造
Us fNe Te h lg o e o w c noo y f r Ene g Sa i n Re v to r y- vng i no a in
合成氨节能降耗改造措施

合成氨节能降耗改造措施2009-01-11 23:14 作者:来源:合成氨是重要的煤化工产品,2007年国内产能已达5700万t/a,产量5159万t。
目前我国76.5%的合成氨生产以煤为原料,年消耗无烟煤超过4200万t,约占国内无烟煤总产量的22%。
鉴于我国“缺油少气富煤”的能源结构,今后煤仍将在合成氨生产中占主导地位。
能源消耗指标差距大合成氨生产中能源消耗约占生产成本的60%左右,目前全国共有氮肥企业560多家,其中有大型合成氨装置的仅有40多家,其他小型装置的能耗远远高于大型先进装置水平。
单机效率低工艺技术落后目前国内大型引进装置使用高效的单系列设备,其压缩机、风机和水泵等装置节能效果显著。
而小型厂造气炉技术虽经不断改进,但仍有气化率、碳利用率低等缺点;另外压缩机技术相对落后,能量利用率低;工艺过程的单元操作还是上世纪五、六十年代的传统方法,虽经过近几年改造有所进步,但与大型企业仍然有较大差距。
“三废”综合利用不足①合成氨生产会产生大量的污水。
目前我国部分企业已经实行了废水闭路循环,实现了冷却循环水和污水零排放,但行业总体污水处置状况并不理想。
②合成氨生产中产生大量的造气吹风气、合成弛放气、脱碳放空气等。
废气中含有大量CO、氢、氨、甲烷,目前仍未得到有效利用。
③以煤为原料的合成氨生产中,每生产1t合成氨约产生500kg废渣,全国每年产生废渣1500万t以上。
面对合成氨生产“三废”排放高、资源利用率低的现状,企业应积极进行“三废“的综合利用,变废为宝,以实现经济和环保的双赢。
推广节能措施提高企业竞争力根据我国石油和化工行业“十一五”规划建议,合成氨行业在“十一五”期间的节能目标是:到2010年,全国合成氨能耗(大、中、小规模加权平均)降为1570kg标煤/t NH3,能源利用效率由目前的42.0%提高到45.5%,实现节能570万~585万t标煤;至2010年,氮肥行业争取吨产品节水10%,节电200 kW·h。
氨碱法蒸氨系统节能降耗的改造

氨碱法蒸氨系统节能降耗的改造氨碱法蒸氨系统是工业生产中常用的一种合成氨方法,其主要原理是利用高温下氨酐与氨水的反应生成氨气。
传统的氨碱法蒸氨系统由于存在能耗高、热效率低、环境污染等问题,亟需进行节能降耗的改造。
对氨碱法蒸氨系统的换热装置进行改造是节能降耗的重要措施之一。
传统的氨碱法蒸氨系统中常采用的换热方式是通过蒸发室与冷凝室之间的传热,然而这种方式热量的传递效率低下,导致能耗较高。
改进的方法是引入新的换热设备,如翅片换热器或换热管,在蒸发室和冷凝室之间增加传热面积,提高热量传递效率,从而降低热能消耗。
改进氨碱法蒸氨系统的循环泵也是节能降耗的重要环节。
传统的氨碱法蒸氨系统中常采用的是钢制离心泵,其耗能较高。
而现代化的节能循环泵采用了新型的材料和结构设计,通过降低泵的转速和使用电动机频率变频控制,能够有效降低能耗,提高泵的效率。
对于氨碱法蒸氨系统的废热利用也是节能降耗的重要手段。
在传统的氨碱法蒸氨系统中,很多废热直接排放到环境中,造成了能源的浪费。
而通过废热回收系统,收集并利用这些废热,可以为其他工艺或生活提供热能,减少能源的消耗。
改进氨碱法蒸氨系统的自动控制装置也是节能降耗的一项重要措施。
传统的氨碱法蒸氨系统往往存在控制不准确、操作复杂等问题,导致运行能耗较高。
而通过引入先进的自动控制技术,实现对系统的精确控制,可以降低系统的能耗,提高生产效率。
通过对氨碱法蒸氨系统的换热装置、循环泵、废热利用和自动控制装置的改造,可以有效地降低系统的能耗,提高能源利用效率。
这不仅符合节能减排的要求,还能够降低生产成本,提高企业的竞争力。
氨碱法蒸氨系统节能降耗的改造对于促进工业发展、减少能源消耗具有重要意义。
KBR的煤制合成氨新工艺(NH3)

KBR的煤制合成氨新工艺摘要KBR传愉床气化炉(也称之为TRIG)是一种先进的煤气化技术,可提供干净、无颗拉的合成气。
TRIG是一种紧凑的加压循环流化床反应器,无内部或移动部件。
其运行和机械设计源自KBR的流化催化裂化(FCC)技术,该技术已有60多年的成功商业运营经验。
描述了煤制合成氛的KBR新工艺,其中TRIG作为KBR合成氛装里流程中的一部分,向一个典型的1500t/d的合成氨回路提供氮气。
论述了基于TRIG 特性的工艺整合和优化要素,以实现稳定高效的煤制合成氛工厂设计。
关键词:KBR传输床,气化炉,煤气化,新工艺0前言煤气化是指在高温、高压、蒸汽以及有限的氧气存在的情况下,将煤炭分解气化的过程。
通过限制氧气的量,可避免煤的完全燃烧,使煤炭分解成更有价值的合成气(主要成分是一氧化碳和氢气)。
在合成氨生产工艺中,煤要尽量多地转化为氢气;煤气化产生的粗合成气与蒸汽发生催化变换反应,将其中的一氧化碳转化为二氧化碳,同时产生更多的氢气用于氨合成。
煤气化的实际化学原理相当复杂,目前其基本依据是煤炭的非催化部分氧化反应,通常在高温耐火衬里容器内进行。
在煤气化过程中会产生多种副产品,煤中的硫大多转化为硫化氢和氧硫化碳,氮转化为氨和氰化氢。
煤的燃烧程度取决于输送至气化炉的氧气量。
气化炉一般在绝热状态下工作,放热反应产生的热必须与吸热反应消耗的热以及原料升温至反应温度所需热量保持平衡。
反应温度通常通过向气化炉内添加水或蒸汽来进行控制。
1 KBR传输床气化炉KBR传输床气化炉(也称之为TRIG'')是一种先进的循环流化床反应器,没有内部或移动部件,可在空气和氧气两种模式下工作。
TRIG的机械设计和操作是基于KBR 的流化催化裂化(FCC)技术,已有60多年的成功商业运行经验。
与传统的循环流化床相比,TRIG的固体循环速率和气体流速要快很多,提升管密度要大很多,因此具有较高的生产能力和碳转化率、混合均匀、传热和传质速率较快等特点。
合成氨原料气节能净化技术简介

合成氨原料气节能净化技术简介摘要:在分析传统合成氨工艺中原料气净化工艺流程的基础上,对合成氨净化工序提出以下节能净化技术:优化分子筛再生系统流程,即增加第三换热器,实现分子筛再生系统的节能改造;增加一种合成氨原料气节能净化装置,用以回收原料气中的甲烷并减少弛放气的排放;增加一种低压液氮洗节能净化装置,使得在合成气压力低的情况下不需要补充液氮提供冷量。
应用结果表明,上述净化技术可达到节能降耗、提产增效的目的。
关键词:合成氨;分子筛节能再生系统;原料气节能净化装置1 分子筛再生节能系统分子筛系统是合成气净化工艺装备中重要的部分,合成气经过分子筛吸附后,其 H 2 O、CO2和CH3OH含量显著下降,气体质量得到提高。
分子筛具有一定的吸附容量,采用合适的再生方法会延长其使用寿命。
而分子筛的吸附是放热过程,脱附是吸热过程,低温有利于吸附,高温有利于脱附。
温度转化再生法是其常用的分子筛再生方法,一般采用直接加热再生法,即采用热再生气直接加热分子筛。
但分子筛系统通常采用外部热源和冷源来控制氮气温度以对分子筛进行温度控制,需要对流程中每个换热器都配置外部热源和冷源,这势必会造成能耗较高。
传统的分子筛再生工艺系统需要配置 2 台换热器,且换热器需要额外配置外部热源或冷源,其工艺流程见图1。
30 ~50℃低温低压氮气在第一换热器中经外部热源加热至200~220℃后进入分子筛吸附器,完成分子筛再生;接着高温低压氮气进入第二换热器中,经外部冷源冷却至30~50℃后流出。
额外配置的外部热源和冷源会在一定程度上增大能耗,但通过改进,增加1台换热器,即第三换热器(该换热器无需配置外部热源或冷源)使完成再生的高温氮气和低温氮气在第三换热器中进行热量交换,达到各自所需的温度,从而实现节能的目的。
第三换热器的安装位置见图2。
第三换热器的高温氮气出口与第一换热器的低温氮气入口相连,第一换热器出口与分子筛吸附器入口相连,分子筛吸附器出口与第三换热器高温氮气入口相连,第三换热器低温氮气出口与第二换热器入口相连。
合成氨原料气体精制技术的节能与最佳选择

合成氨原料气体精制技术的节能与最佳选择合成氨原料气体精制技术的节能与最佳选择近年来,我国合成氨厂不断采用新技术、新工艺使我国合成氨单位能耗大幅度下降,如采用三废混燃余热回收装置不仅回收了吹风气的显热、潜热,回收了弛放气减少环境污染,提高了原料煤的利用率,同时可以副产用于驱动汽轮机的高品位过热蒸汽。
变换采用低阻力的全低变或中低低的节能技术,降低了动力消耗、减少蒸汽用量。
脱碳节能技术更是不断推出。
原料气体的精制有南京敦先化工的节能环保深度转换工艺、国昌公司的非等压醇烷化工艺及湖南安淳公司的醇烃化工艺等节能技术,为我国合成氨节能降耗、节能减排作出了突出贡献!合成氨装置的运行压力也由原来的15.0MP降到11.0~14.5,31.4MPa降到22.0~25.0MPa,原料气压缩机、合成工段的循环机等运转设备电耗大幅度下降,合成氨的综合电耗基本上可以控制在1050~1200KWh/tNH3(针对电驱动)。
另外,氢回收、无动力氨回收、低温高活性的催化剂以及节能设备也为我国合成氨节能降耗作出了较大贡献。
本文主要对合成氨原料气体精制的节能技术进行客观、实事求是地分析和比较。
便于使用单位在选择技术方案时能够选择最适合自己的技术,使合成氨装置进一步节能降耗。
1、合成氨原料气净化总体流程简述无论南京敦先化工的节能环保深度转换工艺、国昌公司的非等压醇烷化工艺及湖南安淳公司的醇烃化工艺,对脱碳后气体的净化基本上分为三个阶梯:第一、二级为甲醇装置,第三级为甲烷化或烃化装置。
第一级甲醇装置以产醇为主,可以设置在4.5~5.5MPa,也可以设置在10.0~12.0MPa。
设置4.5~5. 5MPa采用水移走催化剂床层反应热,设置在10.0~12.0MPa压力等采用气体移走催化剂床层反应热;第二级净化装置以净化为主,可以使原料气中CO、CO2的含量净化到CO+CO2=200PPm~0.2%之间,装置可以设置在10.0~12.0MPa之间,也可以设置在22.0~31.4MPa之间;第三级净化装置是将原料气中200PPm~0.2%的CO、CO2净化到10PPm以下,装置大部分设置在22.0~31. 4MPa之间。
KBR气化炉-合成氨
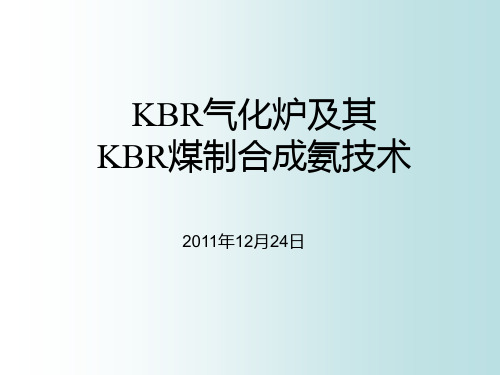
KBR煤制合成氨合成气变换净化流程
KBR煤制合成氨合成气变换净化流程
• » 来自高温烛式过滤器(PCD)合成气的水/气~0.2,经 合成气饱和塔加入蒸汽,使水/气达到~1.0 • »经酸气变换,合成气中CO含量由45-50mol%下降至2.04.0mol%,生成CO2 和H2;COS由10-100ppm降至110ppm,生成CO2 和H2S • » 经废热回收和脱汞后,脱除合成气中的酸性气体,主要 是H2S和CO2 , H2S回收制硫磺,CO2 用于生产尿素 • » 通过变压吸附分离氢气,使氢气含量达到99.5%以上, 分离氢后尾气用作燃料
• KBR煤制合成氨技术分为KBR输运床气 化制合成气、合成气净化和KBR氨合成 技术三部分。气化制气包括KBR气化制 气、热回收和细灰控制。合成气净化包 括酸气变换、酸气脱除、脱汞、变压吸 附制氢等。 KBR氨合成包括合成气压缩、 氨合成、氨冷冻等。
KBR煤制合成氨技术流程
KBR煤制合成氨气化制气流程
KBR煤制合成氨合成气变换净化流 程各节点典型合成气组分表
组分 CO H2 CO2 CH4 NH3 N2 H2S HCN COS 节点 来自PCD (mol%无水) 45.0-50.0 30.0-35.0 13.0-18.0 1-5 0.1-1.0 0.1-0.5 500-1000ppmv 50-300ppmv 10-100ppmv 出酸气变换 (mol%无水) 2.0-4.0 52.0-56.0 40.0-45.0 0.7-3.5 0.07-0.7 0.07-0.35 510-1100ppmv 50-300ppmv 1-10ppmv 出酸气脱除装置 (mol%无水) 4.0-5.0 85.0-88.0 2.0-5.0 2.0-4.0 0.1-1.0 0.1-1.0 0 — —