VOL. 39 Automatic Activity in Depolarized Guinea Pig
PCE-322A 类 II 声音级表 分贝表说明书

PCE Americas Inc.711 Commerce Way Suite 8JupiterFL-33458USAFrom outside US: +1 Tel: (561) 320-9162 Fax: (561) 320-9176*********************PCE Instruments UK Ltd.Units 12/13 Southpoint Business ParkEnsign way Hampshire / Southampton United Kingdom, SO31 4RF From outside UK: +44Tel: (0) 2380 98703 0Fax: (0) 2380 98703 9 ************************/englishTechnical Environmental Tester PCE-322APCE-322A Sound Level MeterClass II decibel (dB) meter with data-logging functionality / Measuring range: 30 ... 130 dB / Memory stores up to 32,700 readings / USB port / Microsoft Excel compatible / AnalogoutputPCE-322A is a handheld, portable, professional Class II sound level meter or decibel meter with built-in data-logging or data-recording functionality. Thus, PCE-322A is ideal for real-time noise measurement as well as for long-term noise exposure monitoring over time. A mini tripod is included in the delivery contents, as is a wind noise suppressor. The recorded decibel readings help users determine if and what protective measures need to be taken to ensure overall health, safety and productivity in industrial, commercial, occupational, educational and residential environments. The sound level meter can also be used to evaluate acoustics for audio installations.The sound level meter can be connected to a PC via the USB port. This allows the recorded decibel readings to be transferred to a PC for detailed analysis using Microsoft Excel or the included downloadable proprietary software. The sound level meter also features an analog output for connecting to a frequency analyzer or X-Y shaft recorder.- IEC 61672-1 Class II sound level meter- USB port for data transfer- Memory stores up to 32,700 readings- Fast and slow time weighting- A and C frequency weightings- Max, min, hold and alarm functions- Date- and time-stamped measurements- Analog output- Heavy-duty ABS plastic enclosure- Large, easy-to-read, 4-digit LCD screen- Power-saving automatic shutoff > 15 min. inactivity- Battery allows approx. 30 hours continuous use- ISO calibration available as an option - see accessories for detailsTechnical specifications:Noise levels Low 30 ... 80 dB Medium 50 ... 100 dB High 80 ... 130 dB Auto 30 ... 130 dBDynamic range 50 dBDisplay 4-digit LCD Resolution 0.1 dB Accuracy ±1.4 dB Sampling rate 2 x per second Frequency 31.5 Hz ... 8 kHz Storage capacity 32,700 readings Frequency weighting A and CTime weighting Fast (125 ms) Slow (1 sec.)Microphone type Electret condenser Functions MIN, MAX, HOLD, ALARMAnalog output AC/DC HeadphoneData interface USB portAutomatic shutdown After 15 minutes inactivityOperating conditions 0 ... +40 °C / +32 ... +104 °F, < 90 % RH Storage conditions -10 ... +60 °C / +14 ... +140 °F, 10 ... 75 % RHPower supply 9 V block battery (for approx. 30 h continuous operation) AC powerDimensions 280 x 95 x 45 mm / 11.02 x 3.74 x 1.77" Weight Approx. 350 g / 0.78 lbStandards IEC 61672-1 Class IIPlease see user manual for complete technical specifications. Delivery contents:1 x PCE-322A sound level meter1 x wind noise suppressor1 x USB cable1 x mini tripod1 x calibration screwdriver1 x battery1 x power adapter1 x carrying case1 x user manual。
Autolab 电位器和 NOVA 控制器程序的电化学测量说明书
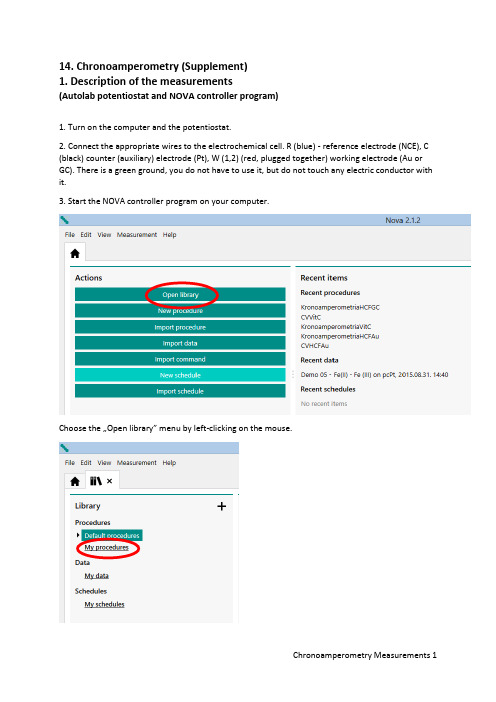
14. Chronoamperometry (Supplement)1. Description of the measurements(Autolab potentiostat and NOVA controller program)1. Turn on the computer and the potentiostat.2. Connect the appropriate wires to the electrochemical cell. R (blue) - reference electrode (NCE), C (black) counter (auxiliary) electrode (Pt), W (1,2) (red, plugged together) working electrode (Au or GC). There is a green ground, you do not have to use it, but do not touch any electric conductor with it.3. Start the NOVA controller program on your computer.Choose the …Open library” menu by left-clicking on the mouse.Clicking on the …My procedures” menu, you could find the procedures (programs) used in the measurements.Choose the appropriate procedure to what you want to do. Read the …Remarks” field also to choose the right program.For Chronoamperometric measurements, the parameters given in the measurement description are already set. The procedure looks like this.Each icon indicates "Commands", which makes the measurement happen. The first icon, "Autolab control" is used to detect the measuring instrument, to set the potentiostatic mode, and to select the current range. The second icon, "Apply", sets the initial electrode potential at the input of the potentiostat. The third icon, "Cell on", connects the potentiostat to the electrochemical cell. The fourth icon, "Wait", keeps the working electrode for the specified time at the initial potential. The fifth icon, "Apply", indicates the potential step to the specified value. The sixth icon, "Record signals", performs the measurement of the time depending current after the potential step. The seventh icon, "Cell Off" turns the cell off from the potentiostat, finishes the measurement. The measurement procedure and the measured data are automatically saved in a .nox file that can be found later on the "My data" menu in the "Library" menu. The data file name is the file name of the "Procedure" plus a "Timestamp", i.e. when the measurement was made. Therefore, it is important to note the order of measurements so that their results can easily be found later.The measurement can be started by clicking on the "Run" command in the "Measurement" menu on the top of the screen or by clicking the Play ( ) icon above the Procedure.During the measurement, instead of the Play icon, the Pause ( ) and Stop ( ) icons will be displayed. If you notice a problem, stop the measurement.During the measurement, the computer automatically plots the measured data in the Plots window in the lower left corner of the screen.Physically, the data files are stored in the Dokumentumok Library in the NOVA 2.1 folder in the Data subfolder. From there, you can make a copy, e.g. to a pendrive.…Behind” each Command icon you could find "Subcommands", shown on the right side of the Procedure pane, or you can see the details with the "More" command by clicking on the corresponding icon. If it is possible, do not change the parameters, or if this happened, DO NOT SAVE THE ALTERED PROCEDURE WITH ITS ORIGINAL NAME.For cyclic voltammetric measurements, the "Procedure" looks like this:Each icon indicates "Commands", which makes the measurement happen. The first icon, "Autolab control" (Autolab control) is used to detect the measuring instrument, to set the potentiostatic mode, and to select the current range. The second icon, "Message", asks for the applicable scan rate ("Scan rate (V/s)"). Once the measurement is started, it must be set to the desired value. The third icon, "Apply", sets the initial electrode potential at the input of the potentiostat. The fourth icon, "Cell on", switches the potentiostat to the electrochemical cell. The fifth icon, "Wait", keeps the working electrode for the specified time at the initial potential. The sixth icon, "CV staircase", represents the cyclic measurement between the lower and upper potential limits with the scan rate given in the …Message". The seventh icon, "Cell Off" turns the cell off from the potentiostat, finishes the measurement. The measurement procedure and the measured data are automatically saved in a .nox file that can be found later on the "My data" menu in the "Library" menu. The data file name is the file name of the "Procedure" plus a "Timestamp", i.e. when the measurement was made. Therefore, it is important to note the order of measurements so that their results can easily be found later.The measurement can be started by clicking on the "Run" command in the "Measurement" menu on the top of the screen or by clicking the Play ( ) icon above the Procedure.During the measurement, instead of the Play icon, the Pause ( ) and Stop ( ) icons will be displayed. If you notice a problem, stop the measurement.During the measurement, the computer automatically plots the measured data in the Plots window in the lower left corner of the screen.Physically, the data files are stored in the Dokumentumok Library in the NOVA 2.1 folder in the Data subfolder. From there, you can make a copy, e.g. to a pendrive.…Behind” each Command icon you could find "Subcommands", shown on the right side of the Procedure pane, or you can see the details with the "More" command by clicking on the corresponding icon. If it is possible, do not change the parameters, or if this happened, DO NOT SAVE THE ALTERED PROCEDURE WITH ITS ORIGINAL NAME.The only parameter you have to set is "Scan rate (V/s)". For sequential runs, use the order that is described in the measurement description. (For example HCF solutions 0.320 V/s, 0.160 V/s, 0.080V/s, etc.)IMPORTANT! NOVA uses Windows default decimal separator. See that the "Message" contains the default value, and that the entered value is also correct! (For example, 0,08 or 0.08!) The data exported from the NOVA also uses the same decimal separator. If necessary, change it to the settings in the Excel Options menu in accordance with the Windows setup!2. Description of evaluation(Autolab potentiometer and NOVA controller program)The NOVA software used for the measurements can be applied for many purposes, but the User's manual is 1196 pages, which is a bit tiring in a lab to read. Therefore, only the most important functions are highlighted.For the evaluation of voltammograms, it is necessary to determine the peak potentials (E p), half peak current potentials (E p/2) and the background corrected peak currents (I p). This can be done in Excel after exporting the measurement data. To do this, double-click the "Plots" pane.Instead of the procedure, the measured plot is displayed in the main window.Clicking on the …Show data” icon you could see a table.In the top right corner there is a marker leading to the export function.Select Excel Export from "File Format", and Windows Explorer will save the file to the desired name and location.ATTENTION! The Excel file contains only the measured data (maybe calculated data, as well), not the description of the Procedure! It's still in the .nox files, do not delete them.IMPORTANT! NOVA uses Windows default decimal separator. The data exported from the NOVA also uses the same decimal separator. If necessary, change it to the settings in the Excel Options menu in accordance with the Windows setup!For Excel files, you can get the desired data, graphics, where needed.For the evaluation of voltammograms, it is necessary to determine the peak potentials (E p), half peak current potentials (E p/2) and the background corrected peak currents (I p). This can be done in Excel after exporting the measurement data, but (perhaps) simpler in NOVA with an "Analysis" function.Click the microscope icon to see a menu. Select "Peak search" analysis.Then, a submenu "Properties" opens in the right window, which offers different versions of the peak search. The default setting is "Automatic", and the figure (or the table) also shows this result, but this is usually good for nothing!Select "Manual", and "Linear free cursor" option.Returning to the plot in the main window with the mouse, you could see a cross. Set this to the initial part of the voltammogram, and fix it with a click. Drag a straight line with the mouse that best fits thefirst part of the voltammogram. The end of the line does not have to be on the curve (free cursor). You can fix the straight line with another click, and the results of the peak search appear in the "Properties" window on the right. (Another voltammogram is illustrated because there will be many peaks on the earlier example.)The same can also be done for the cathodic peak, however from the other end of the curve, the straight line must be fitted backwards.All of these can go in succession, the peaks are included in the right table ("Peaks"). If you are not satisfied with the fitting, you can resume the search at any time by pressing the "Reset" button.The values in the table are:1 Number of found peaks"Peak position" is the electrode potential of the found peak in Volt"Peak height" is the corrected value of the peak current in Amper"Peak (1/2)" is the difference between the potential at the peak current and the potential at the half peak current, i.e. Peak (1/2) = E p– E P/2. (Signed!) (The other columns are not interesting now!)Data can not be exported directly, but when the data is marked with the mouse you can use Ctrl-C to put those on the clipboard, and then use the command Ctrl-V, for example, to copy those to Excel. Only the data, the header will not pass! Afterwards, you can delete unnecessary parts. IMPORTANT! NOVA uses Windows default decimal separator. The data exported (or copied) from NOVA also uses the same decimal separator. If necessary, change it to the settings in the Excel Options menu in accordance with the Windows setup!For chronoamperometric measurements it is recommended to integrate (calculate the charge-time function) in NOVA (you could spare an Excel programming). In the "Plot" window, call up the "Integrate" analysis command!The result is a new figure and the extension of the data file with integrated values.Exporting the measurement results to Excel will include the measured currents and the calculated charge as well.The rest are just time, patience and lots of work, and the evaluation is ready!14. Chronoamperometry1. Description of the measurements(Autolab potentiostat and NOVA controller program)IMPORTANT SUPPLEMENTAfter each electrode exchange and / or solution change, the first thing is a cell control!To do this, select "OCPMeasurement" from the "My procedures" list. The procedure looks like this.The first icon, "Autolab control", is used to detect the measuring instrument and to set the potentiostatic mode. The second icon, "Cell on", connects the potentiostat to the electrochemical cell. The third icon "OCP" (Open Circuit Potential) begins to measure the potential difference between the working and reference electrodes (OCP) when no current flows (the electric circuit is open between the working and the counter electrode). The fourth icon "Cell Off" turns the cell off the potentiostat, finishes the measurement.If, after starting the measurement, it is found that the difference between the Minimum and Maximum Potential is too high, or the blue line indicating the time dependence of the time derivative of the electrode potential (dE/dt) shows too high values (V/s and not μV/s), interrupt the measurement with the "Abort" command. THERE IS SOME TROUBLE!It is likely that the working and / or the reference electrode is not properly connected, the system can not be used! (The system did not damage yet because there was no current during the measurement!) Check the connections and run the procedure again.R (blue) reference electrode (NCE), C (black) counter (auxiliary) electrode (Pt), W (1,2) (red, plugged together) working electrode (Au or GC). There is a green ground, you do not have to use it, but do not touch any electric conductor with it.If, after starting the measurement, it is found that the deviation between the Minimum and Maximum Potential is small max. 10-20 mV, and the blue line indicating the time dependence of the time derivative of the electrode potential (dE/dt) shows normal (mV/s or μV/s) values, you can interrupt the measurement with the "Abort" command. The cell connection is OK!The measurement procedure and the measured data are automatically saved in a .nox file that can be found later in the "My data" menu in the "Library" menu. The data file name is called "OCPMeasurement" plus a "Timestamp", i.e. when the measurement was made. These files should normally not be used at the time of evaluation, but only for diagnostic purposes.。
Sennheiser ew 系列无线麦克风系统用户手册说明书

The ew 322 G3 consists of the same components as ew 312 G3but with a compact cardioid clip-on microphone.The ew 352 G3 consists of the same components as ew 312 G3but with a headworn cardioid microphone.FEATURESSturdy metal housing(transmitter and receiver)42 MHz bandwidth: 1,680 tunable UHF frequencies for interference-free reception20 frequency banks with up to 24 compatible frequenciesEthernet port for connecting to theWireless Systems Manager (WSM) software for control via computer High-quality true diversity receptionPilot tone squelch for eliminating RF inter- ference when transmitter is turned off Automatic frequency scan feature searches for available frequencies Enhanced AF frequency rangeIncreased range for audio sensitivity Wireless synchronization of transmitter parameter from receiverUser-friendly menu operation with more control optionsIlluminated graphic display, receiver also shows transmitter settingsAuto-Lock function avoids accidental changing of settingsHDX compander for crystal-clear sound Transmitter feature battery indicatation in 4 steps, also shown on receiver display Programmable Mute function Integrated Equalizer and Soundcheck modeContacts for recharging BA 2015 accupack directly in the transmitter Wide range of accessories adapts the system to any requirementThe ew 312 G3 is a wireless microphone set, consisting of a True Diversityreceiver, a bodyworn transmitter, a compact omni directional clip-on micropho-ne plus accessories.The bodypack transmitter features charging contacts for the optional recharge-able battery. Sync up the bodypack to the receiver wirelessly with the new wireless sync. Backlit graphic displays make them easy to read under all lighting conditions.ew 300 Setsew 312 G3 Presentation Set ew 322 G3 Presentation Set ew 352 G3 Head Setew 335/345/365 G3 Vocal SetsFEATURESew 335 G3/ew 345 G3/ew 365 G3 Vocal SetsSee above mentioned list of features plus Programmable Mute switch, easyaccessableHandheld transmitter with easy-exchangeable microphone heads from evolution series The ew 335 G3 is a wireless microphone set, consisting of a True Diversity receiver, a handheld transmitter with e 835 microphone head plus accessories. It is versatile for every style of music and presentations. A wireless link from receiver to the transmitter allows synchronization of frequencies for easy setup. Backlit graphic displays make them easy to read under all lighting conditions. The ew 345 G3 consists of the same components as ew 335 G3but with an e 845 microphone head.The ew 365 G3consists of the same components as ew 335 G3but with an e 865 microphone head.ARCHITECT’S SPECIFICATIONSew 312 G3 Presentation SetComplete plug & play wireless microphone set with clip-on microphone (condenser, omni-directional) from Sennheiser evolution series for multi-purpose application. The devices shall have metal housings for rugged use. 42 MHz bandwidth with 1,680 tunable frequencies. 20 banks with up to 24 compatible frequencies, 1 bank for individual selectable frequencies, scan function and wireless synchronization to the transmitter for easy setup. HDX compander delivers high-quality sound performance. All parameters of transmitter and receiver can be monitored and controlled via Wireless Systems Manager (WSM) software from PC. The transmitter shall have a sensitivity range of 48 dB. The receiver offers a maximum output level of +18 dBu (+6 dB gain). True Diversity and pilot tone squelch for interference-free reception. Charging contacts on transmitter for recharging BA 2015 accupack directly in the transmitter shall be available. 3-step battery + LowBattery indication on transmitter and receiver shall give reliable information on operation time.Menu operation, auto-lock function and illuminated graphic displays on transmitter and receiver for user-friendly operation.A RF Mute function on transmitter and receiver allows offline settings.An easy accessable Mute switch on the transmitter can be programmed for AF on/off, RF on/off.A suitable Remote Mute Switch option also allows push-to-talk and push-to-muteAn equalizer and soundcheck mode is inte g rated in the receiver.ew 322 G3 Presentation SetComplete plug & play wireless microphone set with clip-on microphone (electret, cardioid) from Sennheiser evolution series for multi-purpose application. Further discription see paragraph ew 312 G3.ew 352 G3 Head SetComplete plug & play wireless microphone set with headworn microphone (condenser, cardioid) for hands-free application. Further discription see paragraph ew 312 G3.ew 335 G3 Vocal SetComplete plug & play wireless microphone set with easy-exchangeable e 835 microphone head (dynamic, cardioid) from Sennheiser evolution series for multi-purpose application. Further discription see paragraph ew 312 G3.ew 345 G3 Vocal SetComplete plug & play wireless microphone set with easy-exchangeable e 845 microphone head (dynamic, supercardioid) from Sennheiser evolution series for multi-pur p ose application. Further discription see paragraph ew 312 G3.ew 365 G3 Vocal SetComplete plug & play wireless microphone set with easy-exchangeable e 865 microphone head (electret-condenser, supercardioid) from Sennheiser evolution series for multi-purpose application. Further discription see paragraph ew 312 G3.SySTEMRF frequency range ................................................516.....865 MHzTransmission/receiving frequencies ...................1,680Frequency banks ..................................................... 20 (factory presets)6 (user presets)Presets .......................................................................24 max.Switching bandwidth .............................................42 MHzCompander ...............................................................HDXSignal-to-noise ratio ..............................................> 115 dB(A)THD, total harmonic distortion ............................< 0.9 %RECEIvERAF Frequency response..........................................25…18,000 HzAntenna connectors ...............................................BNC, 50 OhmAudio outputs .......................................................... X LR: +18 dBu max6.3 mm jack: +10 dBu maxDimensions ...............................................................212 x 202 x 43 mmWeight .......................................................................980 gTRANSMITTERRF output power .....................................................10/30 mW switchableOperating time ........................................................typ. 8hInput voltage range ................................................1.8 v lineInput voltage range ................................................2.4 v lineDimensions ...............................................................82 x 64 x 24 mmWeight .......................................................................~ 160 gMICROPHONETransducer; Microphone type ...............................permanent polarizedAF sensitivity ...........................................................1.6 mv/PaFrequency response ...............................................80.....18,000 HzPick-up pattern ........................................................omni-directionalContinued on page 5EM 300Modulation ...............................................................wideband FMRF frequency range ................................................ 516 – 558, 566 – 608, 626 – 668, 734 –776, 780 – 822, 823 – 865 MHz Transmission/receiving frequencies ...................1,680, tuneable in steps of 25 kHzReceiving frequencies ............................................ 1,680 frequencies, tuneable in steps of 25 kHz20 frequency banks, each with up to 24 factory-preset channels,intermodulation-free20 frequency banks with up to 24 user programmable channelsSwitching bandwidth .............................................42 MHzNominal/peak deviation .......................................±24 kHz/±48 kHzReceiver principle ....................................................true diversitySensitivity (with HDX, peak deviation) .............< 2 μv for 52 dBA rms S/NAdjacent channel rejection ...................................typ. ≥ 75 dBIntermodulation attenuation ...............................typ. ≥ 70 dBBlocking .....................................................................≥ 75 dBSquelch ...................................................................... O ff, 5 to 25 dBμv, adjustable in steps of 2 dBPilot tone squelch ...................................................can be switched offAntenna inputs .......................................................2 BNC socketsCompander system .................................................Sennheiser HDXEQ presets (switchable, affect the line and monitor outputs):Preset 1: “Flat”Preset 2: “Low Cut” ................................................–3 dB at 180 HzPreset 3: “Low Cut/High boost” .......................... –3 dB at 180 Hz+6 dB at 10 kHzPreset 4: “High Boost” ...........................................+6 dB at 10 kHzS/N ratio (1 mv, peak deviation) ........................≥ 115 dBATHD .............................................................................≤ 0.9 %AF output voltage (at peak deviation,1 kHz AF) .................................................................. ¼” (6.3 mm) jack socket (unbalanced): +12 dBuXLR socket (balanced): +18 dBuAdjustment range of audio output level ........... 48 dB, adjustable in steps of 3 dB +6 dB gain reserveTemperature range .................................................–10 °C to +55 °CPower supply............................................................12 vPower consumption:...............................................350 mADimensions ...............................................................approx. 202 x 212 x 43 mmWeight (incl. batteries) .........................................approx. 980 gIn compliance with .................................................. C E, FCC, ETS 300422, ETS 300445MAINS UNITInput voltage............................................................100 to 240 v~, 50/60 HzPower/current consumption ................................max. 120 mAOutput voltage ........................................................12 vSecondary output current .....................................400 mATemperature range .................................................–10 °C to +40 °CIn compliance with .................................................. C E, FCC, IC, ETS 300422, ETS 300445Continued on page 6SK 300 and SKM 300Modulation ...............................................................wideband FMRF frequency range ................................................ 516 – 558, 566 – 608, 626 – 668, 734 –776, 780 – 822, 823 – 865 MHz Transmission/receiving frequencies ...................1,680, tuneable in steps of 25 kHzReceiving frequencies ............................................ 1,680 frequencies, tuneable in steps of 25 kHz20 frequency banks, each with up to 24 factory-preset channels, intermodulation-free6 frequency banks with up to 24 user programmable channelsSwitching bandwidth .............................................42 MHzNominal/peak deviation .......................................±24 kHz/±48 kHzFrequency stability .................................................≤ ±15 ppmRF output power at 50 O......................................typ. 10/30 mW, switchablePilot tone squelch ...................................................can be switched offAF characteristicsCompander system .................................................Sennheiser HDXAF frequency responseSK ................................................................................ m icrophone: 80 –18,000 Hzline: 25 –18,000 HzSKM ............................................................................80 –18,000 HzS/N ratio (1 mv, peak deviation) ........................≥ 115 dBATHD .............................................................................≤ 0.9 %Max. input voltage (SK) microphone/line ........3 vrmsInput impedance (SK) microphone/line ...........40 k O, unbalanced/1 M OInput capacitance (SK) ..........................................switchableAdjustment range of input sensitivity .............. S K: 60 dB, adjustable in steps of 3 dBSKM: 48 dB, adjustable in steps of 6 dBIn compliance with .................................................. C E, FCC, IC, ETS 300422, ETS 300445OvERALL DEvICETemperature range .................................................−10 °C to + 55 °CPower supply ........................................................... 2 AA size batteries, 1.5 v orBA 2015 accupackNominal voltage .....................................................2.4 vCurrent consumption: at nominal voltage ........typ. 180 mA (30 mW)with switched-off transmitter .............................≤ 25 μAOperating time .......................................................typ. 8 hrsDimensions ............................................................... S K: approx. 82 x 64 x 24 mmSKM: approx. Ø 50 x 265 mmWeight (incl. batteries) ......................................... S K: approx. 160 gSKM: approx. 450 gIn compliance with .................................................. C E, FCC, IC, ETS 300422, ETS 300445Continued on page 7Microphones (SK 300)ME 2ME 3-ew ME 4Microphone type .............................condenser condenser condenserSensitivity .........................................20 mv/Pa 1.6 mv/Pa40 mv/PaPick-up pattern ................................omni-directional cardioid cardioidMax. SPL ............................................130 dB SPL150 dB SPL120 dB SPL Microphone heads (SKM 300)MMD 835-1MMD 845-1MMK 865-1Radio microphone type .................dynamic dynamic condenserSensitivity ......................................... 2.1 mv/Pa 1.6 mv/Pa 1.6 mv/PaPick-up pattern ................................cardioid super-cardioid cardioid/super-cardioid,switchableMax. SPL ............................................154 dB SPL154 dB SPL152 dB SPL Frequency response .......................80.....18,000 Hz80.....18,000 Hz80.....18,000 HzDELIVERY INCLUDES for ew 312 / ew 322 / ew 352 G31 EM 300 G3 rack-mount receiver1 SK 300 G3 bodypack transmitter1 ME2 clip-on microphone (omni-directional) or1 ME 4 clip-on microphone (cardioid) or1 ME 3-ew headset microphone (cardioid)1 GA 3 rack mount1 NT2 power supply unit2 Antennas2 AA batteries1 Instruction manualDELIVERY INCLUDES for ew 335 / ew 345 / ew 365 G31 S KM 300-835 handheld transmitterwith cardioid dynamic head or1 S KM 300-845 handheld transmitterwith super-cardioid dynamic head or1 S KM 300-865 handheld transmitterwith super-cardioid condenser head1 EM 300 G3 rack receiver1 MZQ 1 microphone clip1 NT2 power supply unit2 Antennas1 GA 3 Rack mount kit2 AA batteries1 Instruction ManualPOLAR PATTERN0510152025dB30°30°60°60°90°90°120°150°120°150°0°180°125 Hz 250 Hz 500 Hz 1000 Hz2000 Hz 4000 Hz 8000 Hz 16000 HzMMD 835-1MME 865-1MMD 845-10510152025dB30°30°60°60°90°90°120°150°120°150°0°180°125 Hz 250 Hz 500 Hz 1000 Hz2000 Hz 4000 Hz 8000 Hz 16000 Hz0510152025dB30°30°60°60°90°90°120°150°120°150°0°180°125 Hz 250 Hz 500 Hz 1000 Hz2000 Hz 4000 Hz 8000 Hz 16000 HzME 3-ewME 4-ew0510152025dB30°30°60°60°90°90°120°150°120°150°0°180°125 Hz 250 Hz 500 Hz 1000 Hz2000 Hz 4000 Hz 8000 Hz 16000 Hz0510152025dB30°30°60°60°90°90°120°150°120°150°0°180°125 Hz 250 Hz 500 Hz 1000 Hz2000 Hz 4000 Hz 8000 Hz 16000 HzPRODUCT VARIANTSew 312 G3 Presentation Set Cat. No. ew 312 G3-A-EU 516 – 558 MHz 503112 ew 312 G3-A-US 516 – 558 MHz 503330 ew 312 G3-G-EU 566 – 608 MHz 503331 ew 312 G3-G-US 566 – 608 MHz 503332 ew 312 G3-B-EU 526 – 668 MHz 503333 ew 312 G3-B-US 526 – 668 MHz 503334 ew 312 G3-C-EU 734 –776 MHz 503335 ew 312 G3-C-US 734 –776 MHz 503336 ew 312 G3-D-EU 780 – 822 MHz 503337 ew 312 G3-D-EU-X 780 – 822 MHz 503338 ew 312 G3-D-UK 780 – 822 MHz 503339 ew 312 G3-E-EU 823 – 865 MHz 503340 ew 312 G3-E-EU-X 823 – 865 MHz 503341 ew 312 G3-E-UK 823 – 865 MHz 503342 ew 312 G3-GB 606 – 648 MHz 504649 ew 322 G3 Presentation Set Cat. No. ew 322 G3-E-UK 823 – 865 MHz 503357 ew 322 G3-A-EU 516 – 558 MHz 503113 ew 322 G3-A-US 516 – 558 MHz 503345 ew 322 G3-G-EU 566 – 608 MHz 503346 ew 322 G3-G-US 566 – 608 MHz 503347 ew 322 G3-B-EU 626 – 668 MHz 503348 ew 322 G3-B-US 626 – 668 MHz 503349 ew 322 G3-C-EU 734 –776 MHz 503350 ew 322 G3-C-US 734 –776 MHz 503351 ew 322 G3-D-EU 780 – 822 MHz 503352 ew 322 G3-D-EU-X 780 – 822 MHz 503353 ew 322 G3-D-UK 780 – 822 MHz 503354 ew 322 G3-E-EU 823 – 865 MHz 503355 ew 322 G3-E-EU-X 823 – 865 MHz 503356 ew 322 G3-GB 606 – 648 MHz 504650 ew 352 G3 Presentation Set Cat. No. ew 352 G3-A-EU 516 – 558 MHz 503114 ew 352 G3-A-US 516 – 558 MHz 503360 ew 352 G3-G-EU 566 – 608 MHz 503361 ew 352 G3-G-US 566 – 608 MHz 503362 ew 352 G3-B-EU 526 – 668 MHz 503363 ew 352 G3-B-US 526 – 668 MHz 503364 ew 352 G3-C-EU 734 –776 MHz 503365 ew 352 G3-C-US 734 –776 MHz 503366 ew 352 G3-D-EU 780 – 822 MHz 503367 ew 352 G3-D-EU-X 780 – 822 MHz 503368 ew 352 G3-D-UK 780 – 822 MHz 503369 ew 352 G3-E-EU 823 – 865 MHz 503370 ew 352 G3-E-EU-X 823 – 865 MHz 503371 ew 352 G3-E-UK 823 – 865 MHz 503372 ew 352 G3-GB 606 – 648 MHz 504651ew 335 G3 Vocal Set Cat. No. ew 335 G3-A-EU 516 – 558 MHz 503115 ew 335 G3-A-US 516 – 558 MHz 503375 ew 335 G3-G-EU 566 – 608 MHz 503376 ew 335 G3-G-US 566 – 608 MHz 503377 ew 335 G3-B-EU 526 – 668 MHz 503378 ew 335 G3-B-US 526 – 668 MHz 503379 ew 335 G3-C-EU 734 –776 MHz 503380 ew 335 G3-C-US 734 –776 MHz 503381 ew 335 G3-D-EU 780 – 822 MHz 503382 ew 335 G3-D-EU-X780 – 822 MHz 503383 ew 335 G3-D-UK 780 – 822 MHz 503384 ew 335 G3-E-EU 823 – 865 MHz 503385 ew 335 G3-E-EU-X823 – 865 MHz 503386 ew 335 G3-E-UK 823 – 865 MHz 503387 ew 335 G3-GB 606 – 648 MHz 504652 ew 345 G3 Vocal Set Cat. No. ew 345 G3-A-EU 516 – 558 MHz 503116 ew 345 G3-A-US 516 – 558 MHz 503390 ew 345 G3-G-EU 566 – 608 MHz 503391 ew 345 G3-G-US 566 – 608 MHz 503392 ew 345 G3-B-EU 526 – 668 MHz 503393 ew 345 G3-B-US 526 – 668 MHz 503394 ew 345 G3-C-EU 734 –776 MHz 503395 ew 345 G3-C-US 734 –776 MHz 503396 ew 345 G3-D-EU 780 – 822 MHz 503397 ew 345 G3-D-EU-X780 – 822 MHz 503398 ew 345 G3-D-UK 780 – 822 MHz 503399 ew 345 G3-E-EU 823 – 865 MHz 503400 ew 345 G3-E-EU-X823 – 865 MHz 503401 ew 345 G3-E-UK 823 – 865 MHz 503402 ew 345 G3-GB 606 – 648 MHz 504653 ew 365 G3 Vocal Set Cat. No. ew 365 G3-A-EU 516 – 558 MHz 503117 ew 365 G3-A-US 516 – 558 MHz 503405 ew 365 G3-G-EU 566 – 608 MHz 503406 ew 365 G3-G-US 566 – 608 MHz 503407 ew 365 G3-B-EU 526 – 668 MHz 503408 ew 365 G3-B-US 526 – 668 MHz 503409 ew 365 G3-C-EU 734 –776 MHz 503410 ew 365 G3-C-US 734 –776 MHz 503411 ew 365 G3-D-EU 780 – 822 MHz 503412 ew 365 G3-D-EU-X780 – 822 MHz 503413 ew 365 G3-D-UK 780 – 822 MHz 503414 ew 365 G3-E-EU 823 – 865 MHz 503415 ew 365 G3-E-EU-X823 – 865 MHz 503416 ew 365 G3-E-UK 823 – 865 MHz 503417 ew 365 G3-GB 606 – 648 MHz 504654RECOMMENDED ACCESSORIESCat. No. ME 4-ew – Clip-on microphone,cardioid, black 503156 AM 2 – Antenna Mount kit 009912 CC 3 – System Case 503168L 2015 – Charging unit 009928 BA 2015 – Rechargeable battery pack 009950 ASA 1 – Active antenna splitter 503165 NT 1-1 – plug-in mains unit forASA 1 & L 2015 E U: 503158US: 503873UK: 503874 NT 3-1 – Plug-in mains unit for L 2015 E U: 503159US: 503876UK: 503877 A 1031-U – Antenna 004645A 2003-UHF – Directional Antenna 003658 AB 3 – Antenna booster 505550 Ear Set 1-ew – Ear-worn microphone,omni, black 504232 Ear Set 1-ew-3 – Ear-worn microphone,omni, beige 504237 Ear Set 4-ew – Ear-worn microphone,cardioid, black 504236 Ear Set 4-ew-3 – Ear-worn microphone,cardioid, beige 504234 MKE 1-ew – Clip-on microphone,omni-directional, black 502876 MKE 1-ew-1 – Clip-on microphone,omni, white 502877 MKE 1-ew-2 – Clip-on microphone,omni, brown 502878 MKE 1-ew-3 – Clip-on microphone, beige 502879 MKE 2-ew Gold – Clip-on microphone,omni, black 009831 MKE 2-ew-3 Gold – Clip-on microphone,omni, beige 009832 MKE 40-ew – Clip-on microphone,cardioid, black 500527Cat. No. HSP 4-ew – Headworn microphone,cardioid, black 009864 HSP 4-ew-3 – Headworn microphone,cardioid, beige 009867 HSP 2-ew – Headworn microphone,omni, black 009866 HSP 2-ew-3 – Headworn microphone,omni, beige 009872 CI 1 – Instrument cable 503163ew 335 / ew 345 / ew 365 G3 Vocal SetsMMD 835-1 – evolution microphone head 502575 MMD 845-1 – evolution microphone head 502576 MME 865-1 – evolution microphone head 502581 MZW 1 – Windshield 004839 KEN 2 – Identification rings 530195 LA 2 – Charging adapter forhandheld microphones 503162 CC 3 – System case 503168Sennheiser electronic GmbH & Co. KG Am Labor 1, 30900 Wedemark, Germany 0 4 / 1 3 S e n n h e i s e r i s a r e g i s t e r e d t r a d e m a r k o f S e n n h e i s e r e l e c t r o n i c G m b H & C o . K G . w w w . s e n n h e i s e r . c o m . C o p y r i g h t ©0 4 / 2 0 1 3 . A l l r i g h t s r e s e r v e d . E r r o r s a n d o m i s s i o n s e x c e p t e d .Contact your local Service Partner:。
SDRplay ADS-B (dump1090) User Guide

Radio Spectrum Processor ADS-B (dump1090) User GuideOverviewThe SDRplay Radio combines together the Mirics flexible tuner front-end and USB Bridge to produce a SDR platform capable of being used for a wide range of worldwide radio and TV standards. This document provides an overview of the installation process and operation of the SDRplay ADS-B(dump1090) application.Dump1090 was originally written by Salvatore Sanfilippo ***************** in 2012 and is released under the BSD three clause license.Malcolm Robb *********************** made a number of improvements in 2014. In this revision of the application, support has been added for the RSP.Oliver Jowett ********************.uk created mutability version including oversampled demod in 2016. Contents1.Installation (2)2.Getting Started (11)3.RSP Command Line Options (13)4.Legal Information (14)1. InstallationDownload the SDRplay ADS-B (dump1090) installer from the Windows section of the website (/downloads)Run the downloaded installation file and you will see this, click Yes to continue.Click Next to continue past the welcome screen.Please read and accept the license agreement.The next screen will display important information about these early releases. Read and then click Next.The next screen shows the installation directory. Check you have enough disk space and then click NextThe next screen confirms where the software will be installed to. If correct, click Install.After the software has installed, there will be some quick tips in the next screen, after you have reviewed these click Next.This completes the installation, clicking Finish will close the installer.This software works well with the Virtual Radar Server software. Virtual Radar Server will collect the data from dump1090 and produce a clickable map that shows all of the aircraft found by dump1090 in real time. You can download it from here: /Download.aspxAfter downloading the software, run it to start the installation.Click Next to continue past the welcome screen.Review and accept the license agreement, then click Next.You can review the change log and then click Next to continue.Review the installation directory and click NextThe next screen allows you to change the port number that the server listens on to receive web requests. You can normally leave this as the default (80) but if it conflicts with another web server you may have on your system, you can change it, then click Next.You can choose which folder to store the programs shortcuts or leave it as the default and click NextThis screen allows you to automatically configure the firewall to allow remote connections. Review this information and then click Next once you have decided on the correct setting.After reviewing the summary of what will be installed, click Install to begin.After the software has installed, click Finish to close the installer.2. Getting StartedThe easiest way to get started is to click on Start dump1090 from the Stat Menu (underSDRplay/dump1090). This will start dump1090 with settings to output the received plane information to the network ports.A receiver should be setup in Virtual Server with the following information:Format: BeastIP: 127.0.0.1 (if dump1090 and virtual server running on the same machine) or set to the IP address of the machine running dump1090Port: 30005 (this is the default output port for beast data)Please note: there are more Start options from the menu, these are 2MHz mode (interactive or quiet) and 8MHz mode (interactive or quiet). Interactive will show the plane information as received but will require more CPU than the quiet mode that just outputs the data to the network port.Whilst this is running, start Virtual Radar Server from the Start Menu. It should automatically connect to the dump1090 application and start to process incoming data.You can now click on the link in blue inside the Virtual Radar window (shown in blue) and it will open up a browser window showing the aircraft being detected on a map.You can change some of the command line options to try to improve the performance to capture more aircraft data. Below are some of the options that relate directly to the operation of the RSP.3. RSP Command Line Options--dev-sdrplay – Must be set for ANY RSP--net – enable networking--modeac – enable decoding of SSR modes 3/A & 3/C--oversample – use the 8MHz demodulator (default: 2MHz demodulator)--rsp-device-serNo <serNo> Used to select between multiple devices when more than one RSP device is present--rsp2-antenna-portA Select Antenna Port A on RSP2 (default Antenna Port B)--rspduo-tuner1 Select Tuner 1 on RSPduo (default Tuner 2 if Master or Single Tuner)--rspduo-single Use Single Tuner mode for RSPduo if available (default Master/Slave mode)--adsbMode Set SDRplay ADSB mode (default 1 for ZIF and 2 for LIF)--enable-biasT Enable BiasT network on RSP2 Antenna Port B or RSP1A or RSPduo Tuner 2--disable-broadcast-notch Disable Broadcast notch filter (RSP1A/RSP2/RSPduo)--disable-dab-notch Disable DAB notch filter (RSP1A/RSPduo)--interactive – display aircraft data in a table in the command prompt--quiet – Disable output to the command promptFor more information contact /support4. Legal Information********************************************************(2012)andisreleasedunderthefollowingBSDthreeclause license.**********************************(2014)madeanumberofimprovements******************************(2016)addedRSPsupportCopyright(c)2012,************************************All rights reserved.Redistribution and use in source and binary forms, with or without modification, are permitted provided that the following conditions are met:1. Redistributions of source code must retain the above copyright notice, this list of conditions and the following disclaimer.2. Redistributions in binary form must reproduce the above copyright notice, this list of conditions and the following disclaimer in the documentation and/or other materials provided with the distribution.3. Neither the name of the copyright holder nor the names of its contributors may be used to endorse or promote products derived from this software without specific prior written permission.THIS SOFTWARE IS PROVIDED BY THE COPYRIGHT HOLDERS AND CONTRIBUTORS "AS IS" AND ANY EXPRESS OR IMPLIED WARRANTIES, INCLUDING, BUT NOT LIMITED TO, THE IMPLIED WARRANTIES OF MERCHANTABILITY AND FITNESS FOR A PARTICULAR PURPOSE ARE DISCLAIMED. IN NO EVENT SHALL THE COPYRIGHT HOLDER OR CONTRIBUTORS BE LIABLE FOR ANY DIRECT, INDIRECT, INCIDENTAL, SPECIAL, EXEMPLARY, OR CONSEQUENTIAL DAMAGES (INCLUDING, BUT NOT LIMITED TO, PROCUREMENT OF SUBSTITUTE GOODS OR SERVICES; LOSS OF USE, DATA, OR PROFITS; OR BUSINESS INTERRUPTION) HOWEVER CAUSED AND ON ANY THEORY OF LIABILITY, WHETHER IN CONTRACT, STRICT LIABILITY, OR TORT (INCLUDING NEGLIGENCE OR OTHERWISE) ARISING IN ANY WAY OUT OF THE USE OF THIS SOFTWARE, EVEN IF ADVISED OF THE POSSIBILITY OF SUCH DAMAGE.SDRPlay modules use a Mirics chipset and software. The information supplied hereunder is provided to you by SDRPlay under license from Mirics. Mirics hereby grants you a perpetual, worldwide, royalty free license to use the information herein for the purpose of designing software that utilizes SDRPlay modules, under the following conditions:There are no express or implied copyright licenses granted hereunder to design or fabricate any integrated circuits or integrated circuits based on the information in this document. Mirics reserves the right to make changes without further notice to any of its products. Mirics makes no warranty, representation or guarantee regarding the suitability of its products for any particular purpose, nor does Mirics assume any liability arising out of the application or use of any product or circuit, and specifically disclaims any and all liability, including without limitation consequential or incidental damages. Typical parameters that may be provided in Mirics data sheets and/or specifications can and do vary in different applications and actual performance may vary over time. All operating parameters must be validated for each customer application by the buyer’s technical experts. SDRPlay and Mirics products are not designed, intended, or authorized for use as components in systems intended for surgical implant into the body, or other applications intended to support or sustain life, or for any other application in which the failure of the Mirics product could create a situation where personal injury or death may occur. Should Buyer purchase or use SDRPlay or Mirics products for any such unintended or unauthorized application, Buyer shall indemnify and hold both SDRPlay and Mirics and their officers, employees, subsidiaries, affiliates, and distributors harmless against all claims, costs, damages, and expenses, and reasonable attorney fees arising out of, directly or indirectly, any claim of personal injury or death associated with such unintended or unauthorized use, even if such claim alleges that either SDRPlay or Mirics were negligent regarding the design or manufactu re of the part. Mirics FlexiRF™, Mirics FlexiTV™ and Mirics™ are trademarks of Mirics .SDRPlay is the trading name of SDRPlay Limited a company registered in England # 09035244.Mirics is the trading name of Mirics Limited a company registered in England # 05046393。
Ovation I O Reference Manual

This publication adds the Eight Channel RTD module to the Ovation I/O Reference Manual. It should be placed between Sections 19 and 20.Date: 04/03IPU No.243Ovation ® Interim Publication UpdatePUBLICATION TITLEOvation I/O Reference ManualPublication No. R3-1150Revision 3, March 2003Section 19A. Eight Channel RTDModule19A-1. DescriptionThe Eight (8) channel RTD module is used to convert inputs from Resistance Temperature Detectors (RTDs) to digital data. The digitized data is transmitted to the Controller.19A-2. Module Groups19A-2.1. Electronics ModulesThere is one Electronics module group for the 8 channel RTD Module:n5X00119G01 converts inputs for all ranges and is compatible only with Personality module 5X00121G01 (not applicable for CE Mark certified systems).19A-2.2. Personality ModulesThere is one Personality module groups for the 8 channel RTD Module:n5X00121G01 converts inputs for all ranges and is compatible only with Electronics module 5x00119G01 (not applicable for CE Mark certified systems).19A-2.3. Module Block Diagram and Field Connection WiringDiagramThe Ovation 8 Channel RTD module consists of two modules an electronics module contains a logic printed circuit board (LIA) and a printed circuit board (FTD). The electronics module is used in conjunction with a personalty module, which contains a single printed circuit board (PTD). The block diagram for the 8 channel RTD moduleis shown in Figure 19A-1.Table 19A-1. 8 Channel RTD Module Subsystem ChannelsElectronic Module Personality Module85X00119G015X00121G01Figure 19A-1. 8 Channel RTD Module Block Diagram and Field Connection Wiring Diagram19A-3. SpecificationsElectronics Module (5X00119)Personality Module (5X00121)Table 19A-2. 8 Channel RTD Module SpecificationsDescription ValueNumber of channels8Sampling rate50 HZ mode: 16.67/sec. normally. In 3 wire mode, leadresistance measurement occurs once every 6.45 sec.during which the rate drops to 3/sec.60 HZ mode: 20/sec. normally. In 3 wire mode, leadresistance measurement occurs once every 6.45 sec.during which the rate drops to 2/sec.Self Calibration Mode: Occurs on demand only. The ratedrops to 1/sec. once during each self calibration cycle.RTD ranges Refer to Table 19A-3.Resolution12 bitsGuaranteed accuracy (@25°C)0.10% ±[0.045 (Rcold/Rspan)]% ± [((Rcold + Rspan)/4096 OHM)]% ± [0.5 OHM/Rspan]% ±10 m V ± 1/2LSBwhere:Rcold and Rspan are in Ohms.Temperature coefficient 10ppm/°CDielectric isolation:Channel to channel Channel to logic 200V AC/DC 1000 V AC/DCInput impedance100 M OHM50 K OHM in power downModule power 3.6 W typical; 4.2 W maximumOperating temperature range0 to 60°C (32°F to 140°F)Storage temperature range-40°C to 85°C (-40°F to 185°F)Humidity (non-condensing)0 to 95%Self Calibration On Demand by Ovation ControllerCommon Mode Rejection120 dB @ DC and nominal power line frequency+/- 1/2%Normal Mode Rejection100 dB @ DC and nominal power line frequency+/- 1/2%Table 19A-3. 8 Channel RTD RangesScale #(HEX)Wires Type Tempo FTempo CRcold(ohm)Rhot(ohm)Excitationcurrent(ma)Accuracy± ±countsAccuracy± ±% ofSPAN1310OhmPL0 to1200–18 t o6496106.3 1.090.222310OhmCU 0 to302–18 t o1508.516.5 1.0 130.32D350OhmCU 32 to2840 to1405080 1.0110.2711350OhmCU 32 to2300 to1105378 1.0120.30193100Ohm PL –4 to334–16 t o16892163.671.0110.27223100Ohm PL 32 to5200 to269100200 1.0100.25233100Ohm PL 32 to10400 to561100301 1.0100.25253120Ohm NI –12 t o464–11 t o240109360 1.0100.25263120Ohm NI 32 to1500 to70120170 1.0130.32283120Ohm NI 32 to2780 to122120225 1.0110.27804100Ohm PL 32 to5440 to290100 208 1.0100.25814100Ohm PL 356 t o446180 t o230168 186 1.0300.74824200Ohm PL 32 to6980 to370200 473 1.0120.30834200Ohm PL 514 t o648268 t o342402452 1.0290.71844100Ohm PL 32 to1240 to51100120 1.0190.47854100Ohm PL 32 to2170 to103100 140 1.0130.3286 4100Ohm PL 32 to4120 to211100 180 1.0110.27874100Ohm PL 32 to7140 to379100 240 1.0100.25884120Ohm PL 511 t o662266 t o350200230 1.0240.5919A-4. 8 Channel RTD Terminal Block Wiring Information19A-4.1. Systems Using Personality Module 5X00121G01 Each Personality module has a simplified wiring diagram label on its side, which appears above the terminal block. This diagram indicates how the wiring from the field is to beconnected to the terminal block in the base unit. The following table lists and defines the abbreviations used in this diagram.Table 19A-4. Abbreviations Used in the DiagramAbbreviation Definition+IN, -IN Positive and negative sense input connectionEarth ground terminal. Used for landing shields when the shield is to begrounded at the module.PS+, PS-Auxiliary power supply terminals.RTN Return for current source connection.SH Shield connector. used for landing shields when the shield is to begrounded at the RTD.SRC Current source connection.Note:PS+ and PS- are not used by this module.19A-5. 8 Channel RTD Module Address Locations19A-5.1. Configuration and Status RegisterWord address 13 (D in Hex) is used for both module configuration and module status. The Module Status Register has both status and diagnostic information. The bit information contained within these words is shown in Table 19A-5.Definitions for the Configuration/Module Status Register bits:Bit 0:This bit configures the module (write) or indicates the configuration state of the module (read). A “1” indicates that the module is configured. Note that until the module is configured, reading from addresses #0 through #11 (B in Hex) will produce an attention status.Bit 1:This bit (write “1”) forces the module into the error state, resulting in the error LED being lit. The read of bit “1” indicates that there is an internal module error,or the controller has forced the module into the error state. The state of this bit is always reflected by the module’s Internal Error LED. Whenever this bit is set,an attention status is returned to the controller when address #0 through #11(B in Hex) are read.Table 19A-5. 8 Channel RTD Configuration/Status Register (Address 13 0xD in Hex)Bit Data Description -Configuration Register (Write)Data Description -Status Register (Read)0Configure Module Module Configured(1 = configured; 0 = unconfigured)1Force errorInternal or forced error(1 = forced error; 0 = no forced error)250/60 Hz select (0 = 60Hz, 1 = 50Hz)50/60 Hz System (1 = 50Hz) d(read back)3SELF_CAL (Initiates Self Calibration)Warming bit (set during power up or configuration)40050060Module Not Calibrated 708CH.1 _ 3/4 Wire.CH.1 _ 3/4 Wire - Configuration (read back)9CH.2 _ 3/4 Wire.CH.2 _ 3/4 Wire - Configuration (read back)10CH.3 _ 3/4 Wire.CH.3 _ 3/4 Wire - Configuration (read back)11CH.4 _ 3/4 Wire.CH.4 _ 3/4 Wire - Configuration (read back)12CH.5 _ 3/4 Wire.CH.5 _ 3/4 Wire - Configuration (read back)13CH.6 _ 3/4 Wire.CH.6 _ 3/4 Wire - Configuration (read back)14CH.7 _ 3/4 Wire.CH.7 _ 3/4 Wire - Configuration (read back)15CH.8 _ 3/4 Wire.CH.8 _ 3/4 Wire - Configuration (read back)Bit 2:The status of this bit (read) indicates the conversion rate of the module, write to this bit configures the conversion rate of A/D converters as shown below.see Table 19A-6.Bit3:Write: This bit is used to initiate self-calibration. Read: This bit indicates that the module is in the “Warming” state. this state exists after power up and ter-minates after 8.16 seconds. the module will be in the error condition during the warm up period.Bit4 & 5:These bits are not used and read as “0” under normal operation.Bit 6:This bit (read) is the result of a checksum test of the EEPROM. A failure of this test can indicate a bad EEPROM, but it typically indicates that the module has not been calibrated. A “0” indicates that there is no error condition. If an error is present, the internal error LED is lit and attention status will be returned for all address offsets 0-11 (0x0 - 0xB). The “1” state of this bit indicates an unre-coverable error condition in the field.Bit 7:This bits is not used and read as “0” under normal operation.Bit 8 - 15:These bits are used to configure channels 1 - 8 respectively for 3 or 4 wire op-eration. A “0” indicates 3 wire and a “1” indicates 4 wire operation, see Table 19A-7 and Table 19A-8).Word address 12 (0xC) is used to configure the appropriate scales for Channels 1 - 4 (refer to Table 19A-7 and Table 19A-8).Table 19A-6. Conversion Rate Conversion Rate (1/sec.)Bit 260 (for 60Hz systems)050 (for 50Hz systems)1Table 19A-7. Data Format for the Channel Scale Configuration Register(0xC)Bit Data Description Configuration (Write)Data Description Status (Read)0 Configure Channel #1scale - Bit 0Channel #1 scale configuration (read back) - Bit 01Configure Channel #1scale - Bit 1Channel #1 scale configuration (read back) - Bit 12Configure Channel #1scale - Bit 2Channel #1 scale configuration (read back) - Bit 23Configure Channel #1scale - Bit 3Channel #1 scale configuration (read back) - Bit 34Configure Channel #2 scale - Bit 0Channel #2 scale configuration (read back) - Bit 05Configure Channel #2 scale - Bit 1Channel #2 scale configuration (read back) - Bit 16Configure Channel #2 scale - Bit 2Channel #2 scale configuration (read back) - Bit 27Configure Channel #2 scale - Bit 3Channel #2 scale configuration (read back) - Bit 38Configure Channel #3 scale - Bit 0Channel #3 scale configuration (read back) - Bit 09Configure Channel #3 scale - Bit 1Channel #3 scale configuration (read back) - Bit 1Caution:Configuring any or all channel scales while the system is running will cause all channels to return attention status for up to two seconds following the reconfiguration.Caution:Configuring any or all channel scales while the system is running will cause all channels to return attention status for up to two seconds following the reconfiguration.10Configure Channel #3 scale - Bit 2Channel #3 scale configuration (read back) - Bit 211Configure Channel #3 scale - Bit 3Channel #3 scale configuration (read back) - Bit 312Configure Channel #4 scale - Bit 0Channel #4 scale configuration (read back) - Bit 013Configure Channel #4 scale - Bit 1Channel #4 scale configuration (read back) - Bit 114Configure Channel #4 scale - Bit 2Channel #4 scale configuration (read back) - Bit 215Configure Channel #4 scale - Bit 3Channel #4 scale configuration (read back) - Bit 3Table 19A-8. Data Format for the Channel Scale Configuration Register(0xE)Bit Data Description Configuration (Write)Data Description Status (Read)0 Configure Channel #5 scale - Bit 0Channel #5 scale configuration (read back) - Bit 01Configure Channel #5 scale - Bit 1Channel #5 scale configuration (read back) - Bit 12Configure Channel #5 scale - Bit 2Channel #5 scale configuration (read back) - Bit 23Configure Channel #5 scale - Bit 3Channel #5 scale configuration (read back) - Bit 34Configure Channel #6 scale - Bit 0Channel #6 scale configuration (read back) - Bit 05Configure Channel #6 scale - Bit 1Channel #6 scale configuration (read back) - Bit 16Configure Channel #6 scale - Bit 2Channel #6 scale configuration (read back) - Bit 27Configure Channel #6 scale - Bit 3Channel #6 scale configuration (read back) - Bit 38Configure Channel #7 scale - Bit 0Channel #7 scale configuration (read back) - Bit 09Configure Channel #7 scale - Bit 1Channel #7 scale configuration (read back) - Bit 110Configure Channel #7 scale - Bit 2Channel #7 scale configuration (read back) - Bit 211Configure Channel #7 scale - Bit 3Channel #7 scale configuration (read back) - Bit 312Configure Channel #8 scale - Bit 0Channel #8 scale configuration (read back) - Bit 013Configure Channel #8 scale - Bit 1Channel #8 scale configuration (read back) - Bit 114Configure Channel #8 scale - Bit 2Channel #8 scale configuration (read back) - Bit 215Configure Channel #8 scale - Bit 3Channel #8 scale configuration (read back) - Bit 3Table 19A-7. Data Format for the Channel Scale Configuration Register(0xC)19A-6. Diagnostic LEDsTable 19A-9. 8 Channel RTD Diagnostic LEDsLED DescriptionP (Green)Power OK LED. Lit when the +5V power is OK.C (Green)Communications OK LED. Lit when the Controller is communicatingwith the module.I (Red)Internal Fault LED. Lit whenever there is any type of error with themodule except to a loss of power. Possible causes are:n - Module initialization is in progress.n - I/O Bus time-out has occurred.n - Register, static RAM, or FLASH checksum error.n - Module resetn - Module is uncalibrated.n - Forced error has been received from the Controllern - Communication between the Field and Logic boards failedCH1 - CH 8 (Red)Channel error. Lit whenever there is an error associated with a channel or channels. Possible causes are:n - Positive overrangen - Negative overrangen Communication with the channel has failed。
嵌入式固件开发手册说明书

301© Jacob Beningo 2017J. Beningo, Reusable Firmware Development , https:///10.1007/978-1-4842-3297-2IndexAAbstract Data Types (ADTs)abstractions, 80definition, 81implementation data structure, 82initialization function, 83interface specification, 81operations, 81pop method, 84stack method initialization, 83Stack_Push, 85Abstractions, see Abstract DataTypes (ADTs)Application Programming Interfaces(APIs), 23architecture, 24characteristics, 49consistent look and feel, 53const keyword, 49documentation, 53flexible and configuration, 53Micrium uc/OS-III, 54naming conventions, 50uOS III, 52comparison (API and HAL), 58designing process, 53embedded-software developers, 49FreeRTOS TaskCreate, 54HAL design, 57scope, 48ThreadX tx_thread_create, 55wrappers, 55Assertion fundamentals assert.h header file, 68definition, 68input and pre-condition, 69macro implementation, 69Automating tests, 269BBoogeymanintegration issues, 35issues, 33microcontroller vendors, 34peripheral technique, 35ramifications, 34readability issues, 35Bootloaders framework, 252CCallback functionsArrayInit function, 88definition, 86elements to random numbers, 89implementation, 87initialization code, 87instances, 86lower-level code, 87signal handler, 87Classes definition, 80Cohesion, 11Commercial off-the-shelf (COTS), 1 Coupling method, 11C programming languagebit fields, 15conditional compilation, 18data type, 13demonstration code, 13preprocessor directives, 16structures and unions, 14DData hiding, 86Designing APIapplication framework, 246creation, 247embedded applicationsadvantages, 244application framework, 244disadvantages, 244hardware abstraction layer, 243implementation, 243modifications, 245modules, 245software frameworksbootloaders, 252console applications, 250FAT file system, 254parsers, 251RTOS and schedulers, 248 Design patterns, 90–91Device driver models, 70blocking driver, 70non-blocking driver, 70polling, 71Documentation, 121C codecoding style guide, 144commenting code, 143consistent commentlocation, 146Doxygen tags, 144explanation, 143file header, 145line command, 146mathematical typeidentification, 146template creation, 145update comments, 147 Doxygen (see Doxygen) DoxyWizarddiagrams setup, 131folder structure, 127mode setup, 129output setup, 130project setup, 127run tab, 128wizard tab, 129embedded software, 121enum and struct, 132 functions, 133code block, 136description block, 135factors, 133parameter and return block, 135 pre-condition/post-conditionblock, 135related block, 136revision log, 137start block, 134load operation, 122approaches, 123single source, 123software spectrum, 123Index302main.c file, 122main page, 140modules, 137@Addtogroup comment block, 139header file, 137source files, 138reusable template, 139Doxygen, 124comment fundamentals, 131control and develop documentation, 125 installation, 126Driversabstraction and ADT, 80component definition, 76component organization, 77components, 77–78expected results andrecommendations, 91files, 77fundamental unit, 76interface, 64, 78component identification, 66design contract, 66–67hardware abstraction layer, 65lasagna software architecture, 65outputs, 67pre-conditions, 67modules, 78naming convention, 78object-oriented programming, 79procedural language, 79EEEPROM devices, See alsoMemory devicesdatasheet, 221EepromErase_t, 239EepromRegister_t definition, 226extending HAL, 237_ext file, 239feature comparison, 222files, 238interface, 224memory devices, 221repeat, 237stubs and documentation templates functions, 227Init(), 228–229Read(), 229–230Write(), 230–231target processor, 231functions, 232initialization function, 232read function, 235write function, 233testing, 237write state enumeration, 226 Embedded-software processes/codebase, 295Encapsulation, 80, 86Error handling, 89FFAT file systems, 254Firmware projectadvantages, 4benefits, 4code reuse, 1development team, 3disadvantages, 4embedded-software, 5–6architecture, 20dependencies and interactions, 19design/reuse, 18Index303formal models, 21functional boundary, 19interfaces, 19low-level driver, 19portable firmware creation, 19three-layer model, 20features, 3HAL (see Hardware AbstractionLayers (HAL))microcontrollers, 2modularity, 9module coupling and cohesion, 10project development time, 2portability issues (see C programming language)qualities of, 8software, 3smart solar panel, 7standard revisions, 12Functional testingblack-box/white-box testingmethods, 264test-driven development, 265testing process, 264GGeneral-purpose input/output (GPIO) datasheet, 167HAL interface, 169microcontrollers, 168overview, 167peripheral features, 168stubs and documentation templates, 172 Dio.c, 182Dio_Config.c, 178Dio_Config.h, 174Dio.h, 180HAL organization, 174target processor, 192ChannelRead, 195ChannelWrite, 196Dio_ChannelToggle function, 196Dio_ChannelWrite function, 196GPIO initialization, 194pointer array memory map, 193RegisterRead, 197RegisterWrite, 197repeat option, 198test harnesses, 198HHardware abstraction layer (HAL), 21, 149 application layer, 22APIs, 30 (see also ApplicationProgramming Interfaces (APIs)) architecture, 23board-support package, 22benefits, 21, 33characteristics, 36, 150C99, 38coding standards, 36debugging software, 43deterministic and well-understoodbehavior, 41error-handling and diagnosticcapabilities, 42evaluation, 44extensible, 40hardware features, 39integrated regression testing, 43integration server, 43modern compiler, 38modular and adaptable, 40Firmware project (cont.) Index304reasonable documentation andcomments, 37well-defined coding standard, 37 configuration layer, 22 comparison list, 152design process, 151all-encompassing HAL, 161core features identification, 161Doxygen, 162initialization, 164iterate, 163multiple development kits, 164naming conventions, 164register-access hooks, 162second set of eyes, 162view, 163driver layer, 22factors, 46Good, Bad, and Ugly, 33GPIO peripheral, 47interfacecallback interface, 154creation, 153developers, 155generic definition, 154peripheral features, 153 landscape, 31microcontroller peripheraldatasheet, 46, 152 middleware, 22peripheral identification, 152, 160 platform, 31potential issues (see Boogeyman) software terminology, 22stubs and documentationtemplates, 155target processor(s), 158testing, 158Hardware in-loop (HIL) testing, 266 automating tests, 269COMM port, 267components, 267debugger, 267factors, 268Python scripts, 268regression, 268I, J, K, LInheritance, 80Internet of Things (IoT), 6Invariants, 68M, NMemory devicesflash and EEPROM devices, 219internal and external devices, 220issues, 220overview, 219Memory mapCPU, 63EEPROM, 63flash memory regions, 62generic microcontroller memory, 64memory, 64microcontroller, 62peripheral memory, 63RAM, 62–63ROM, 62Memory-mapping methodologiesarrays, 106controls, 101declaration, 104direct register access, 102methods, 101Index305non-constant pointer, 104pointers, 102register bit, 103structures, 105volatile keyword, 103–104Module coupling, 11OObject-Oriented Programming (OOP), 79 Objects definition, 80P, QPolling vs. Interrupt-driven drivers, 71 attitude determination and control, 76 DMA-controlled data transfer, 75Hello World, 72interrupts, 74printf statement, 72, 74transmit interrupt frequency, 73UART transmit interrupt duration, 74 Portable firmware see Firmwareprojectcharacteristics, 27code evaluation, 26portability, 27reuse software, 25,Post- c onditions, 68Practical approachdefinition, 284desired results and outcomesbusiness perspective, managementand shareholders, 281development costs, 282identification, 280quality increases, 283time to market, 281evaluation, 284metrics, 285phases, 278recognizing design patterns, 288results, 288software practice improvement, 280templates and checklists creation, 289tracking metrics, 285unpractical environment, 277VCS (see Version-control systems (VCS)) Pre-conditions, 68Project organization, 24RReal-Time Operating System (RTOS), 249 advantages, 249compiler optimizations, 249microchip, 249scheduler, 248scheduling algorithm, 250wrapper layer, 249Regression testing, 257, 268Renesas Synergy™ platform, 272 Reusable drivers, 95const keyword, 99extern and static keywords, 95explicit, 97function and variable scope, 97global variables, 96implicit, 96programming language, 96implementation, 117memory-mapping (see Memory-mapping methodologies)timer (see Timer driver)volatile keyword, 98Memory-mapping methodologies (cont.) Index306location, 99optimization, 98prevent code optimization, 99UART Tx, 98SScheduler, see Real-Time OperatingSystem (RTOS)Serial Peripheral Interface bus (SPI) advantages, 201architecture, 202datasheet, 202features, 203hardware level, 201interface, 204repeat, 216stubs and documentation templates design patterns, 205init function, 206module files, 206transfer function, 207target processorarray mapping, 209flow chart, 213initialization function, 210Spi_Transfer function, 212–213 testing, 215Side effects, 68Standard tests, 263TTest-Driven Development (TDD), 265 Testingapplication software, 270block diagram, 270deadlock, 272events, 271reusable firmware, 271task statistics, 271automation and regression, 258development teams, 258embedded system, 257functional testing (see Functionaltesting)HIL testing, 266regression testing, 257renesas Synergy™ platform, 272standard tests, 263unit test, 258Timer driverchannel definition, 110configuration structure, 109configuration table, 108, 110design pattern, 116driver interface, 116initialization function, 112init loop code, 115overview, 107peripheral channels, 109pointer arrays, 111steps, 108UUnit testing, 258cyclomatic complexityfunction, 261if/else statements, 262linearly independent paths, 261measurements, 260nodes (program statements), 262parameters, 261tools, 263function, 259harness test, 259Index307V, W, X, Y, ZVersion-control systems (VCS) add files, 294code-comparison tools, 295commit frequently, 293log information, 293–294 process definition, 294 lock modules, 294 merging code branches, 295Index308。
ADL5541 RF IF Gain Block数据手册说明书

20 MHz to 6 GHzRF/IF Gain Block Data Sheet ADL5541FEATURESFixed gain of 15 dBOperation up to 6 GHzInput/output internally matched to 50 Ω Integrated bias control circuitOutput IP344 dBm at 500 MHz40 dBm at 900 MHzOutput 1 dB compression: 19.7 dBm at 900 MHz Noise figure of 3.5 dB at 900 MHzSingle 5 V power supplySmall footprint 8-lead LFCSPPin compatible with 20 dB gain ADL55421 kV ESD (Class 1C) FUNCTIONAL BLOCK DIAGRAMGNDRFOUTGNDVPOS6877-1Figure 1.GENERAL DESCRIPTIONThe ADL5541 is a broadband 15 dB linear amplifier that operates at frequencies up to 6 GHz. The device can be used in a wide variety of CATV, cellular, and instrumentation equipment. The ADL5541 provides a gain of 15 dB, which is stable over frequency, temperature, power supply, and from device to device. The device is internally matched to 50 Ω with an input return loss of 10 dB or better up to 6 GHz. Only input/output ac coupling capacitors, power supply decoupling capacitors, and an external inductor are required for operation. The ADL5541 is fabricated on an InGaP HBT process and has an ESD rating of 1 kV (Class 1C). The device is packaged in a3 mm × 3 mm LFCSP that uses an exposed paddle for excellent thermal impedance.The ADL5541 consumes 90 mA on a single 5 V supply andis fully specified for operation from −40°C to +85°C.A fully populated RoHS-compliant evaluation board is available.The ADL5542 is a companion part that offers a gain of 20 dB in a pin-compatible package.Rev. B Document Feedback Information furnished by Analog Devices is believed to be accurate and reliable. However, noresponsibility is assumed by Analog Devices for its use, nor for any infringements of patents or other rights of third parties that may result from its use. Specifications subject to change without notice. No license is granted by implication or otherwise under any patent or patent rights of Analog Devices. T rademarks and registered trademarks are the property of their respective owners. O ne Technology Way, P.O. Box 9106, Norwood, MA 02062-9106, U.S.A. Tel: 781.329.4700 ©2007–2015 Analog Devices, Inc. All rights reserved. Technical Support ADL5541 Data Sheet TABLE OF CONTENTSFeatures (1)Functional Block Diagram (1)General Description (1)Revision History (2)Specifications (3)Typical Scattering Parameters (5)Absolute Maximum Ratings (6)ESD Caution (6)Pin Configuration and Function Descriptions ............................. 7Typical Performance Characteristics . (8)Operating to 20 MHz (10)Basic Connections (11)Soldering Information and Recommended PCB Land Pattern (11)Evaluation Board (12)Outline Dimensions (13)Ordering Guide (13)REVISION HISTORY2/15—Rev. A to Rev. BChanged Frequency Range from 50 MHz to 6000 MHz to20 MHz to 6000 MHz (Throughout) (1)Changes to Table 1 (3)Added Figure 14 to Figure 19; Renumbered Sequentially (10)Changes to Basic Connections Section and Table 5; AddedFigure 21 and Figure 22 (11)Updated Outline Dimensions (13)Changes to Ordering Guide (13)11/13—Rev. 0 to Rev. AChanges to Figure 2 (7)Added Figure 13, Renumbered Sequentially (9)Added Exposed Pad Notation to Outline Dimensions (12)7/07—Revision 0: Initial VersionRev. B | Page 2 of 13Data Sheet ADL5541 SPECIFICATIONSVPOS = 5 V and T A = 25°C, unless otherwise noted.Table 1.Parameter Test Conditions/Comments Min Typ Max Unit OVERALL FUNCTIONFrequency Range 20 6000 MHz Gain (S21) 900 MHz 15.2 dB Input Return Loss (S11) Frequency 500 MHz to 5 GHz −12 dB Output Return Loss (S22) Frequency 500 MHz to 5 GHz −10 dB Reverse Isolation (S12) −19 dB FREQUENCY = 20 MHzGain 17.6 dB Output 1 dB Compression Point 18.3 dBm Output Third-Order Intercept Δf = 1 MHz, output power (P OUT) = 0 dBm per tone 38 dBm Noise Figure 3.3 dB FREQUENCY = 100 MHzGain 15.7 dB Output 1 dB Compression Point 19 dBm Output Third-Order Intercept Δf = 1 MHz, output power (P OUT) = 0 dBm per tone 37 dBm Noise Figure 3.9 dB FREQUENCY = 500 MHzGain 14.7 15.1 15.5 dB vs. Frequency ±50 MHz ±0.15 dB vs. Temperature −40°C ≤ T A ≤ +85°C ±0.1 dB vs. Supply 4.75 V to 5.25 V ±0.01 dB Output 1 dB Compression Point 19.9 dBm Output Third-Order Intercept Δf = 1 MHz, output power (P OUT) = 3 dBm per tone 44 dBm Noise Figure 3.5 3.7 dB FREQUENCY = 900 MHzGain 14.9 15.2 15.4 dB vs. Frequency ±50 MHz ±0.03 dB vs. Temperature −40°C ≤ T A ≤ +85°C ±0.15 dB vs. Supply 4.75 V to 5.25 V ±0.01 dB Output 1 dB Compression Point 19.7 dBm Output Third-Order Intercept Δf = 1 MHz, output power (P OUT) = 0 dBm per tone 40.8 dBm Noise Figure 3.5 3.7 dB FREQUENCY = 2000 MHzGain 13.9 14.7 15.4 dB vs. Frequency ±50 MHz ±0.03 dB vs. Temperature −40°C ≤ T A ≤ +85°C ±0.17 dB vs. Supply 4.75 V to 5.25 V ±0.01 dB Output 1 dB Compression Point 16.3 dBm Output Third-Order Intercept Δf = 1 MHz, output power (P OUT) = 0 dBm per tone 39.2 dBm Noise Figure 3.8 4.0 dB FREQUENCY = 2400 MHzGain 13.9 14.5 15.1 dB vs. Frequency ±50 MHz ±0.03 dB vs. Temperature −40°C ≤ T A ≤ +85°C ±0.19 dB vs. Supply 4.75 V to 5.25 V ±0.02 dB Output 1 dB Compression Point 14.9 dBm Output Third-Order Intercept Δf = 1 MHz, output power (P OUT) = 0 dBm per tone 38.6 dBm Noise Figure 4.0 4.2 dBRev. B | Page 3 of 13ADL5541 Data Sheet Parameter Test Conditions/Comments Min Typ Max Unit FREQUENCY = 3500 MHzGain 13.6 14.3 14.9 dB vs. Frequency ±50 MHz ±0.03 dB vs. Temperature −40°C ≤ T A ≤ +85°C ±0.19 dB vs. Supply 4.75 V to 5.25 V ±0.02 dB Output 1 dB Compression Point 12.1 dBm Output Third-Order Intercept Δf = 1 MHz, output power (P OUT) = 0 dBm per tone 30.7 dBm Noise Figure 4.2 4.5 dB FREQUENCY = 5800 MHzGain 9.1 11.2 13.5 dB vs. Frequency ±50 MHz ±0.15 dB vs. Temperature −40°C ≤ T A ≤ +85°C ±0.9 dB vs. Supply 4.75 V to 5.25 V ±0.02 dB Output 1 dB Compression Point 5.8 dBm Output Third-Order Intercept Δf = 1 MHz, output power (P OUT) = 0 dBm per tone 21.9 dBm Noise Figure 6.0 7.0 dB POWER INTERFACE Pin VPOSSupply Voltage (VPOS) 4.5 5 5.5 V Supply Current 90 100 mA vs. Temperature −40°C ≤ T A ≤ +85°C ±12 mA Power Dissipation VPOS = 5 V 0.5 WRev. B | Page 4 of 13Data Sheet ADL5541TYPICAL SCATTERING PARAMETERSVPOS = 5 V and T A = 25°C, the effects of the test fixture have been de-embedded up to the pins of the device.Table 2.Freq. (MHz)S11 S21 S12 S22 Magnitude (dB) Angle (°) Magnitude (dB) Angle (°)Magnitude (dB) Angle (°)Magnitude (dB) Angle (°)50 −18.11 −134.53 16.29 +166.36 −19.15 +3.84 −17.89 −134.08 100 −20.84 −161.29 15.93 +168.53 −18.82 +2.26 −22.24 −155.22 500 −27.69 +115.36 15.58 +154.53 −18.70 −13.59 −24.96 +176.64 900 −27.48 +101.79 15.52 +136.22 −18.70 −26.33 −22.38 +173.92 1000 −26.87 +91.91 15.56 +131.64 −18.64 −29.43 −23.15 +174.28 1500 −29.18 −107.74 15.50 +108.03 −18.64 −44.69 −19.35 +167.80 2000 −17.88 −153.68 15.51 +84.72 −18.43 −60.42 −14.13 +176.19 2500 −9.87 +169.30 15.57 +59.74 −18.32 −75.48 −9.89 +161.55 3000 −7.92 +142.75 15.49 +35.05 −17.93 −92.29 −8.69 +138.18 3500 −7.74 +117.57 15.21 +9.15 −18.14 −110.62 −11.02 +100.39 4000 −10.85 +116.84 14.82 −16.13 −18.11 −125.08 −15.70 +6.37 4500 −13.25 +136.93 15.23 −41.75 −17.54 −142.99 −7.83 −80.59 5000 −13.97 +143.02 14.56 −68.15 −17.64 −161.24 −6.87 −112.39 5500 −13.68 −121.08 13.89 −96.10 −17.47 +178.77 −11.66 −102.32 6000 −4.52 −138.62 12.07 −123.56 −18.61 +157.35 −7.66 −54.40Rev. B | Page 5 of 13ADL5541 Data Sheet ABSOLUTE MAXIMUM RATINGSESD CAUTIONTable 3.Parameter RatingSupply Voltage, VPOS 6.5 VInput Power (re: 50 Ω)10 dBmInternal Power Dissipation (Paddle Soldered) 650 mWθJC (Junction to Paddle)28.5°C/WMaximum Junction Temperature 150°COperating Temperature Range −40°C to +85°CStorage Temperature Range −65°C to +150°CStresses at or above those listed under Absolute MaximumRatings may cause permanent damage to the product. This is astress rating only; functional operation of the product at theseor any other conditions above those indicated in the operationalsection of this specification is not implied. Operation beyondthe maximum operating conditions for extended periods mayaffect product reliability.Rev. B | Page 6 of 13Data SheetADL5541PIN CONFIGURATION AND FUNCTION DESCRIPTIONS06877-002GND CB RFIN NOTES1. EXPOSED PADDLE. INTERNALLY CONNECTED TO GND. SOLDER TO A LOW IMPEDANCE GROUND PLANE.GND GND VPOSRFOUT GNDFigure 2. Pin ConfigurationTable 4. Pin Function DescriptionsPin No. Mnemonic Description1RFIN RF Input. Requires a dc blocking capacitor.2, 3, 6, 7 GND Ground. Connect these pins to a low impedance ground plane.4 CB Low Frequency Bypass. A 1 µF capacitor should be connected between this pin and ground.5 VPOS Power Supply for Bias Controller. Connect directly to external power supply.8RFOUT RF Output and Supply Voltage. DC bias is provided to this pin through an inductor that is tied to the external power supply. RF path requires a dc blocking capacitor.Exposed PaddleExposed Paddle. Internally connected to GND. Solder to a low impedance ground plane.Rev. B | Page 7 of 13ADL5541Data SheetRev. B | Page 8 of 13TYPICAL PERFORMANCE CHARACTERISTICSVPOS = 5 V and T A = 25°C, unless otherwise noted. C1 = 33 pF, C2 = 33 pF, L1 = 47 nH.45FREQUENCY (GHz)G A I N , P 1d B , O I P 3, N F (d B , d B m )403530252015105.75.34.94.54.13.73.32.92.52.11.71.30.90.506877-003Figure 3. Gain, P1dB, OIP3, and Noise Figure vs. Frequency1610FREQUENCY (GHz)G A I N (d B )5.75.34.94.54.13.73.32.92.52.11.71.30.90.5151413121106877-004Figure 4. Gain vs. Frequency and Temperature–4506FREQUENCY (GHz)S 11, S 22, S 12 (d B )–5–10–15–20–25–30–35–401234506877-005Figure 5. Input Return Loss (S11), Output Return Loss (S22), andReverse Isolation (S12) vs. Frequency450FREQUENCY (GHz)O I P 3 A ND P 1d B (d B m )4035302520151055.75.34.94.54.13.73.32.92.52.11.71.30.90.5Figure 6. OIP3 and P1dB vs. Frequency and Temperature5010–515P OUT (dBm)O I P 3 (d B m )45403530252015–3–1135791113Figure 7. OIP3 vs. Output Power (P OUT ) and Frequency820 6.0FREQUENCY (GHz)N O I S E F I G U R E (d B )765430.5 1.0 1.5 2.0 2.5 3.0 3.5 4.0 4.5 5.0 5.5Figure 8. Noise Figure vs. Frequency and TemperatureData SheetADL55413037.0OIP3 (dBm)P E R C E N T A G E (%)25201510538.540.041.543.006877-009Figure 9. OIP3 Distribution at 900 MHz2519.4P1dB (dBm)P E R C E N T A G E (%)201510519.519.619.719.819.920.020.106877-010Figure 10. P1dB Distribution at 900 MHz2515.08GAIN (dB)P E R C E N T A G E (%)201510515.1115.1415.1715.2015.2315.2606877-011Figure 11. Gain Distribution at 900 MHz3003.303.36 3.42 3.48 3.54 3.60 3.66 3.72 3.78NOISE FIGURE (dB)P E R C E N T A G E (%)252015105Figure 12. Noise Figure Distribution at 900 MHz100707580859095–6–4–2024681012141618202206877-100S U P P L Y C U R R EN T (m A )P OUT (dBm)Figure 13. Supply Current vs. P OUT and TemperatureRev. B | Page 9 of 13ADL5541Data SheetOPERATING TO 20 MHzVPOS = 5 V and T A = 25°C, unless otherwise noted. C1 = 0.1 µF, C2 = 0.1 µF, L1 = 1 µH.0510********354020406080100120140G A I N , P 1d B , O I P 3, N F (d B , d B m )FREQUENCY (MHz)06877-114Figure 14. Gain, P1dB, OIP3, and Noise Figure vs. Frequency15.015.516.016.517.017.518.020406080100120140G AI N (d B )FREQUENCY (MHz)06877-115Figure 15. Gain vs. Frequency and Temperature–30–25–20–15–10–52030405060708090100110120130140S 11,S 22, S 12 (d B )FREQUENCY (MHz)06877-116Figure 16. Input Return Loss (S11), Output Return Loss (S22), andReverse Isolation (S12) vs. Frequency51015202530354045O I P 3A N D P 1d B (d B m )FREQUENCY (MHz)06877-117Figure 17. OIP3 and P1dB vs. Frequency and Temperature2022242628303234363840–5–3–11357911131506877-118O I P 3 (d B m )P OUT (dBm)Figure 18. OIP3 vs. Output Power (P OUT ) and Frequency2.02.53.03.54.04.55.020406080100120140N O I S E F I G U R E (d B )FREQUENCY (MHz)+25°C–40°C+85°C06877-119Figure 19. Noise Figure vs. Frequency and TemperatureRev. B | Page 10 of 13Data SheetADL5541BASIC CONNECTIONSThe basic connections for operating the ADL5541 are shown in Figure 20. Recommended components are listed in Table 5. The input and output should be ac-coupled with appropriately sized capacitors (device characterization was performed with 33 pF capacitors). A 5 V dc bias is supplied to the amplifier via GND (Pin 6) and through a biasing inductor connected to RFOUT (Pin 8). The bias voltage should be decoupled using a 1 µFRFIN RFOUT06877-013Figure 20. Basic ConnectionsFor operation below 500 MHz, a larger biasing choke and ac coupling capacitors are necessary (see Table 5). Figure 21 shows input return loss, output return loss, and gain for frequencies between 200 MHz and 500 MHz. The noise figure performance for operation from 200 MHz to 500 MHz is shown in Figure 22.–30–25–20–15–10–512.012.513.013.514.014.515.015.516.016.517.0200250300350400450500R E T U R N L O S S (d B )G A I N (d B )FREQUENCY (MHz)06877-121Figure 21. Input Return Loss (S11), Output Return Loss (S22), andGain (S21) vs. Frequency2.02.53.03.54.04.5200250300350400450500N O I S E F I G U R E (d B )FREQUENCY (MHz)06877-122Figure 22. Noise Figure vs. Frequency from 200 MHz to 500 MHzSOLDERING INFORMATION AND RECOMMENDED PCB LAND PATTERNFigure 23 shows the recommended land pattern for the ADL5541. To minimize thermal impedance, the exposed paddle on the package underside should be soldered down to a ground plane along with Pin 2, Pin 3, Pin 6, and Pin 7. If multiple ground layers exist, they should be stitched together using vias (aminimum of five vias is recommended). For more information on land pattern design and layout, refer to Application Note AN-772, A Design and Manufacturing Guide for the Lead Frame 06877-016Figure 23. Recommended Land PatternTable 5. Recommended Components for Basic ConnectionsFrequencyC1 C2 C3 L1C4 C5 C6 C7 20 MHz to 200 MHz 0.1 µF 0.1 µF 1 µF 1 µH (Coilcraft 0805LS-102XJL_ or equivalent) 68 pF 1.2 nF 1 µF 68 pF 200 MHz to 500 MHz 0.1 µF 0.1 µF 1 µF 470 nH (Coilcraft 0603LS-471-NX or equivalent) 68 pF 1.2 nF 1 µF 68 pF 500 MHz to 6000 MHz33 pF33 pF1 µF47 nH (Coilcraft 0603CS-47-NX or equivalent)68 pF1.2 nF1 µF68 pFRev. B | Page 11 of 13ADL5541Data SheetRev. B | Page 12 of 13EVALUATION BOARDFigure 26 shows the schematic for the ADL5541 evaluation board. The board is powered by a single 5 V supply.The components used on the board are listed in Table 6. Power can be applied to the board through clip-on leads (VCC and GND) or through a 2-pin header (W1).06877-017Figure 24. Evaluation Board Layout (Bottom)06877-018Figure 25. Evaluation Board Layout (Top)RFIN06877-019Figure 26. Evaluation Board SchematicTable 6. Evaluation Board ConfigurationComponent Fun c tion Default ValueDUT1 Gain block ADL5541 C1, C2 AC coupling capacitors 33 pF, 0402 C3 Low frequency bypass capacitor 1 μF, 0805C4, C5, C6, C7, C8, C9 Power supply decoupling capacitors C4 and C7 = 68 pF, 0603 C5 = 1.2 nF, 0603 C6 = 1 μF, 0805 C8 and C9 = openL1 DC bias inductor 47 nH, 0603 (Coilcraft 0603CS-47-NX or equivalent) VCC and GND Clip-on terminals for power supply W1 2-pin header for connection of ground and supply via cableData SheetADL5541Rev. B | Page 13 of 13OUTLINE DIMENSIONSPIN 10.80FOR PROPER CONNECTION OF THE EXPOSED PAD,REFER TO THE PIN CONFIGURATION AND FUNCTION DESCRIPTIONSSECTION OF THIS DATA SHEET.0.08COMPLIANT TO JEDEC STANDARDS MO-229-WEED12-07-2010-AFigure 27. 8-Lead Lead Frame Chip Scale Package [LFCSP_WD]3 mm × 3 mm Body, Very Very Thin, Dual Lead(CP-8-13)Dimensions shown in millimetersORDERING GUIDEModel 1 Temperature Range Package DescriptionPackage OptionBranding ADL5541ACPZ-R7 −40°C to +85°C 8-Lead LFCSP_WD, 7” Tape and Reel CP-8-13 Q13 ADL5541-EVALZEvaluation Board1Z = RoHS Compliant Part.©2007–2015 Analog Devices, Inc. All rights reserved. Trademarks and registered trademarks are the property of their respec tive owners. D06877-0-2/15(B)。
西门子电机参数
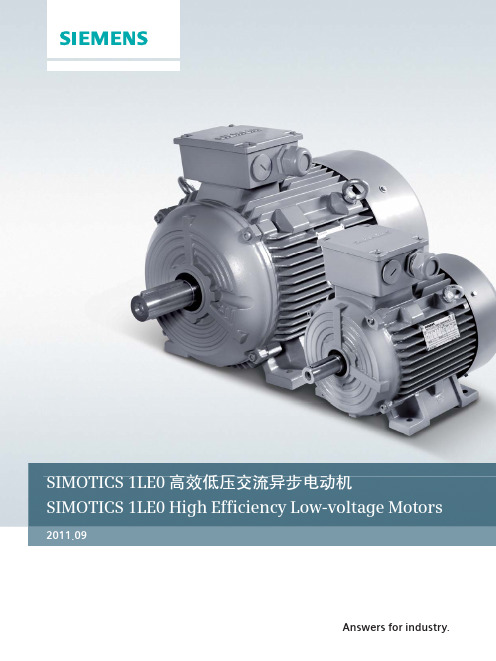
选型技术数据表 Technical data table ............................................................. 22
■ Available in 2, 4, 6 pole variants with efficiency grade 2. according to GB18613-2006 and efficiency class IE2 according to IEC 60034-30.
■ 额定功率:0.55 kW ~ 315 kW(50 Hz);
■ Insulation system is designed for temperature class 155 (F). At rated output with line-fed operation, the motors can be used in temperature class 130 (B).
Padm = Prated • kHT
对于不同高度和(或)不同环境温度的功率换算系数 kHT Factor kHT for different side altitudes and / or coolant temperature
海拔高度 Site altitude above see level
对应海拔高度的环境温度 Site altitude above see level Coolant temperature
55 ºC 0.87 0.84 0.82 0.78 0.75 0.71 0.67
俄罗斯分光光度计PHOTON RT说明书

PHOTON RTUniversal Scanning SpectrophotometerOperation ManualPKTH.033.000.0001IMPORTANT NOTICECopyright InformationThis document contains proprietary information that is protected by copyright. All rights are reserved. Neither the whole document nor any part of this document may be reproduced in any form or by any means or translated into any language without the prior and written permission of EssentOptics Ltd. Copyright © 2012-2016 EssentOptics Ltd.TrademarksAll brand names, trademarks, etc. used in this document, even when not specifically marked as such, are protected by law. EssentOptics and PHOTON RT are trademarks of EssentOptics Ltd.Contents1 SAFETY MEASURES (4)2 DESCRIPTION AND OPERATION OF PHOTON RT SPECTROPHOTOMETER (5)2.1 P URPOSE (5)2.2 P RODUCT S PECIFICATIONS (6)2.3 C OMPLETE SET OF SPECTROPHOTOMETER (6)2.4 C ONFIGURATION OF SPECTROPHOTOMETER (7)2.5 M ARKING AND SEALING (9)2.6 P ACKING (9)3 INSTALLATION (10)3.1 P REPARING FOR OPERATION (10)3.2 P HOTON S OFT I NSTALLATION (11)3.2.1 PC REQUIREMENTS (11)3.2.2 S OFTWARE INSTALLATION (11)3.3 O PERATION OF THE SPECTROPHOTOMETER (12)3.3.1 M EASUREMENT OF TRANSMITTANCE. (13)3.3.2 M EASUREMENT OF ABSOLUTE SPECULAR REFLECTANCE. (14)3.3.3 M EASUREMENT OF ABSORPTANCE SPECTRA (15)3.3.4 P OLARIZATION-DEPENDENT MEASUREMENTS AT VARIABLE ANGLES IN PS MODE. (16)3.3.5 T RANSMITTANCE MEASUREMENT OF THICK SAMPLES AT HIGH ANGLES OF INCIDENCE. (18)3.3.6 M EASUREMENT OF COMPLEX REFRACTIVE INDEX AND LAYER THICKNESS (19)3.3.7 B ATCH MEASUREMENTS (21)3.3.8 V ERIFICATION OF WAVELENGTH CALIBRATION OF THE SPECTROPHOTOMETER (22)3.4 P HOTON S OFT S OFTWARE (24)3.4.1 C ONTROL COMMANDS (24)3.4.2 S ETTINGS OF MEASURING PARAMETERS (26)3.4.3 S PECTRAL GRAPHS (27)3.4.4 S AVING OF SPECTRA (28)3.4.5 O PTICAL DENSITY (29)3.4.6 K INETIC MEASUREMENT (29)3.4.7 P RINTING OF REPORT (32)3.4.8 B EAM DISPLACEMENT CALCULATOR (36)3.4.9 M EASUREMENT OF COMPLEX REFRACTIVE INDEX AND LAYER THICKNESS. (37)3.4.10 M ETHODS (39)3.4.11 B ATCH MEASUREMENTS (40)3.4.12 I NTERFACE SETTINGS (44)4 MAINTENANCE AND REPAIRS (46)4.1 R EPLACEMENT OF LIGHT SOURCES (46)4.1.1 R EPLACEMENT OF HALOGEN LAMP (46)4.1.2 R EPLACEMENT OF DEUTERIUM LAMP (48)5 STORAGE (50)6 TRANSPORTATION (50)7 UTILIZATION (50)8 ACCEPTANCE CERTIFICATE (51)9 PACKING CERTIFICATE (52)10 WARRANTY (53)11 APPENDIX 1. PRODUCT SPECIFICATION (54)12 APPENDIX 2. COMPLETE SET OF SPECTROPHOTOMETER (56)13 APPENDIX 3. WAVELENGTH CALIBRATION TABLE (57)1Safety measuresThe spectrophotometer complies with the safety standard IР STB 14254-96 standard.Prior to the operation, read the safety rules and regulations for electric equipment carefully and follow the necessary instructions for operation of the spectrophotometer. One should be clearly aware of danger of hazardous internal and external voltages.CAUTION!It is PROHIBITED to operate the spectrophotometer with the removed housing.It is PROHIBITED to operate the spectrophotometer after ingress of water.It is PROHIBITED to operate the spectrophotometer without proper grounding.2Description and operation of Photon RT spectrophotometer2.1PurposeThe Photon RT universal scanning spectrophotometer (further referred to as spectrophotometer) is designed to measure optical characteristics of absolute specular reflectance, transmittance, absorptance, and optical density of planar optical samples with thin film coatings at variable angles and in the polarized light.The spectrophotometer is developed on the basis of the Czerny-Turner monochromator. The spectrophotometer is intended for operation in laboratory conditions in accordance with the following requirements:∙ambient temperature – from +10 0С to +28 0С;∙relative humidity – below 80 % at the temperature + 25 оС;∙atmospheric pressure – from 84 kPa to 106.7 kPa∙proper grounding at the connection point of spectrophotometer and computer2.2Product SpecificationsSee Appendix 1for specifications of your individual spectrophotometer.2.3Complete set of spectrophotometerSee Appendix 2 for complete set of your individual spectrophotometer.2.4Configuration of spectrophotometerFigure 2.4.1 shows the spectrophotometer (front view) with an open lid.The lid of the measuring compartment 1 ensures protection against ambient illumination. In the process of measurement a sample is placed on the sample holder 3 of the sample stage 2 and is fastened with clamps 4. When the spectrophotometer is switched on, red-color flickering of indicator light-emitting diode (LED) 7 continues until the end of the spectrophotometer initialization and self-check procedure. When the spectrophotometer is in the off-measuring mode (“ready” mode), flickering of the indicator LED is green. The indicator LED 7 flickers red during the measurement process, and red-yellow during the change of diffraction gratings. The spectrophotometer is switched on and off by switch 6.Photodetector unit 5 is positioned at a supporting holder of the photodetector drive. The drive provides for positioning of photodetectors along the optical axis for the angles from 16˚ to 183˚: in the case of reflectance measuring -synchronously or non-synchronously with the stage rotation, in the case of transmittance measuring - photodetectors are positioned at normal angle of incidence or any angle within 0˚ - 75˚ range selected by the user.Rotation of stage 2 in the horizontal plane around the optical axis is realized from 0˚ to 75˚. Both rotations are executed with 0,10 step.The value of the incidence angle on the measured surface is set in the field «Measuring parameters» (see Subsection 2.4.2). The position of photodetector is adjusted automatically with the measuring mode («TRANSMITTANCE» or «REFLECTANCE») and depending on the rotation angle of sample stage 2. Rotation angles of sample stage 2 and photodetector unit 5 can be also realized independently in the manual mode for measurement of complex prismatic units. The motorized displacement of photodetector unit perpendicular to the axis of the light beam allows measuring the transmittance of thick samples at high angles up to 75˚. Operation of the beam displacement calculator is described in section 2.4.For the adequate measurement of reflectance, the sample’s surface must be pressed to the stage surface. The measuring area is at the opening center of stage 2.1. Lid of measuring compartment;2. Sample stage;3. Holder;4. Clamps;5. Photodetector unit;6. Power switch;7. Indicator LED;Figure 2.4.1 Photon RT spectrophotometer, front view, with open lid.Figure 2 shows a rear view of the spectrophotometer. The rear panel has USB connector 1 for connection of PC, power supply connector 2, and fuse 3 (including the spare fuse inside). Cover 4 of the compartment with light sources is fastened to the side surface of the instrument by screws 5. The procedure for replacement of the light sources is described in Subsection 4.11. USB connector;2. Power supply connector;3. Fuse (including spare fuse inside);4. Cover;5. Screws.Figure 2.4.2 Photon RT spectrophotometer, rear view.2.5Marking and sealingMarking of the spectrophotometer includes:∙brand name (description) of the device;∙manufacturer’s trademark;∙legends for the elements of connection to external devices are given on the rear panel of the spectrophotometer;∙serial number of the tool is provided on the rear panel;∙marking on the shipment package2.6PackingThe spectrophotometer is packed in accordance with the manufacturer’s requirements and specifications.3Installation3.1Preparing for operation1)Open the packing container, take out the operation manual (OM), take out the spectrophotometer. Whentransportation of the spectrophotometer is handled at temperature below 5оС, leave it unpacked for no less than 24 hours.2)Install the spectrophotometer on the solid horizontal surface.3)Check for the set completeness (see Subsection 2.3).4)Inspect the instrument to make sure that there is no mechanical damage.5)Install «PhotonSoft» Software using PC in accordance with Subsection 3.2.6)Provide effective grounding of the spectrophotometer and PC.7)Connect the spectrophotometer to power mains using the power cable.8)Connect the spectrophotometer to PC with the help of USB cable (see Figure 2.4.2).9)Switch-on the spectrophotometer.10)Start «PhotonSoft» Software.IMPORTANT NOTE:After “PhotonSoft” software starts, the instrument runs self-check and initialization procedure of all controlled elements. This may take about 1 minute.It is PROHIBITED to switch off / switch on the instrument, close / open the software or activate any elements of the software during the self-check and initialization procedure. Otherwise this may damage the instrument.3.2PhotonSoft Installation3.2.1PC requirements∙Microsoft Windows XP/ Windows7/Windows 8operating system;∙SVGA monitor with the resolution no less than 1024x768 (optimum 1280х1024) dots;∙Video adapter memory capacity no less than 32Мb (optimum 64Мb) and color depth no less than 16 bit; ∙No less than 128 Мb of memory (RAM);∙Keyboard, mouse-type manipulator;∙Hard disk (HDD) with free capacity no less than 10 Gb.3.2.2 Software installationTo install the Software, perform the following operations:∙make sure the spectrophotometer is NOT connected to PC∙insert the Software CD-disk (or USB-flash) into CD-ROM (or USB port) of PC ;∙start the installation software setup.exe and follow its instructions;∙press the «Next» button in the installation window ;∙press «Next» in the installation window;∙after successful installation of the software, press the «Finish» button in the window;∙find quick start tag of «PhotonSoft» on the desktop of your PC;∙connect the spectrophotometer to PC;The spectrophotometer is ready for operation.3.3Operation of the spectrophotometer3.3.1Measurement of transmittance.∙Switch on the spectrophotometer.∙Start «PhotonSoft» from your desktop.IMPORTANT NOTE:After “PhotonSoft” software starts, the instrument runs self-check and initialization procedure of all controlled elements. This may take about 1 minute.It is PROHIBITED to switch off / switch on the instrument, close / open the software or activate any elements of the software during the self-check and initialization procedure. Otherwise this may damage the instrument.∙The warm-up time of the spectrophotometer shall be no less than 30 minutes.∙Select «TRANSMITTANCE» from the drop-down menu.∙Set the necessary measuring parameters (see Subsection 3.4.1).1) scanning range;2) sampling pitch;3) averaging count;4) smoothing mode;5) sample stage angle setting;6) polarization.∙Open the lid and make sure that the optical channel in the measuring compartment has no objects.∙Close the lid.∙Press the button «Apply».∙Press the button «Calibration» for baseline calibration. When scanning of a spectrum is finished, the screen displays the horizontal spectral graph serving as 100% transmittance level.∙Open the lid. Place a sample to be measured on the sample stage. Close the lid.∙Start the measuring process by pressing the button «MEASUREMENT». When the process is finished, the screen displays the graph for a transmittance spectrum of the sample.IMPORTANT NOTES:1)When starting the instrument on the new day, it is recommended to repeat baseline calibration beforeactual measurements for breaking-in after 30 minutes warm-up time. This ensures small bit adjustments of the moving parts after idle time.Recommended parameters:∙Staring wavelength: 400 nm;∙Ending wavelength: 1600 nm;∙Sampling pitch: 10 nm;∙Averaging count: 10;∙Smoothing mode: 0;2)Select the wavelength scanning range applicable to the measured sample.3)For more precise measurements in UV-VIS or VIS range, set scanning range and run baselinecalibration up to 990 nm. (For example, 180-990 nm or 380-990 nm respectfully.)4)For more precise measurements in IR range, set scanning range and run baseline calibration starting1000 nm. (For example, or 1000-1600 nm or 1000-3000 nm etc).5)When measurements are conducted over the complete effective wavelength range of thespectrophotometer, it is recommended to perform the baseline calibration directly before measuring the spectrum of the sample.Figure 3.3.1 Transmittance and optical density spectrum.Figure 3 illustrates transmittance and optical density spectrum. The transmittance scale is on the left and the optical density scale is on the right. The optical density graph may be displayed or hidden (see Subsection2.4.4).3.3.2Measurement of absolute specular reflectance.∙Switch on the spectrophotometer.∙Start «PhotonSoft».IMPORTANT NOTE:After “PhotonSoft” software starts, the instrument runs self-check and initialization procedure of all controlled elements. This may take about 1 minute.It is PROHIBITED to switch off / switch on the instrument, close / open the software or activate any elements of the software during the self-check and initialization procedure. Otherwise this may damage the instrument.∙The warm-up time of the spectrophotometer shall be no less than 30 minutes.∙Select «TRANSMITTANCE» from the drop-down menu.∙Set the required measuring parameters (see Subsection 3.4.1)1) scanning range;2) sampling pitch;3) averaging count;4) smoothing mode;5) polarization.∙Make sure that the optical channel in the measuring compartment has no objects.∙Press the button«Apply».∙Press the button «Calibration» for baseline calibration. When scanning of a spectrum is finished, the screen displays the horizontal spectral graph serving as 100% transmittance level.∙Select «REFLECTANCE» from the drop-down menu to change for measurement of absolute specular reflectance.∙Open the lid. Place a sample to be measured on the sample stage. The coated surface shall be facing the sample stage for measurement of absolute specular reflectance. Close the lid.∙Set the angle for sample stage.∙Press the button«Apply».∙Start the measuring process by pressing the button «MEASUREMENT». When the process is finished, the screen displays the graph for the absolute reflectance spectrum of the sample.IMPORTANT NOTES:1)When starting the instrument on the new day, it is recommended to repeat baseline calibration beforeactual measurements for breaking-in after 30 minutes warm-up time. This ensures small bit adjustments of the moving parts after idle time.Recommended parameters:∙Staring wavelength: 400 nm;∙Ending wavelength: 1600 nm;∙Sampling pitch: 10 nm;∙Averaging count: 10;∙Smoothing mode: 0;2)Select the wavelength scanning range applicable to the measured sample.3)For more precise measurements in UV-VIS or VIS range, set scanning range and run baselinecalibration up to 990 nm. (For example, 180-990 nm or 380-990 nm respectfully.4)For more precise measurements in IR range, set scanning range and run baseline calibration starting1000 nm. (For example, 1000-3000 nm, 1000-1650 nm etc.)5)When measurements are conducted over the complete effective wavelength range of thespectrophotometer, perform baseline calibration directly before measuring the spectrum of the sample.3.3.3Measurement of absorptance spectraThe Photon RT spectrophotometer provides the possibility to measure absorptance spectra of the unknown transparent substrate. The measurement of the absorptance spectra is realized by sequential measurements of transmittance and reflectance, and subsequent processing of the measurement results.∙Switch on the spectrophotometer.∙Start «PhotonSoft».IMPORTANT NOTE:After “PhotonSoft” software starts, the instrument runs self-check and initialization procedure of all controlled elements. This may take about 1 minute.It is PROHIBITED to switch off / switch on the instrument, close / open the software or activate any elements of the software during the self-check and initialization procedure. Otherwise this may damage the instrument.∙The warm-up time of the spectrophotometer shall be no less than 30 minutes.∙Select «TRANSMITTANCE» from the drop-down menu.∙Set the required measuring parameters (see Subsection 3.4.1)1) scanning range;2) sampling pitch;3) averaging count;4) smoothing mode;5) polarization.∙Make sure that the optical channel in the measuring compartment has no objects.∙Press the button«Apply».∙Press the button «Calibration» for baseline calibration. When scanning of a spectrum is finished, the screen displays the horizontal spectral graph serving as 100% transmittance level.∙Select «ABSORPTANCE» from the drop-down menu to change for measurement of absorptance.∙Place a sample to be measured on the sample stage.NOTE: One can use the same sample to measure both transmittance and reflectance, if the sample has thickness of 40 mm and above. Otherwise, for reflectance measurementone should prepare and use a 50 wedge sample made of the same material.∙Input the value of the sample thickness in the line “Sample thickness, mm” (See Fig. 3.4.4).∙Press the button«Apply».∙Start the measuring process by pressing the button «MEASUREMENT». When the process is finished, the screen displays the graph for the transmittance spectrum of the sample. After that, thedetectors unit and sample stage will synchronously rotate for reflectance measurement at 80.∙Start the measuring process by pressing the button «MEASUREMENT». When the process is finished, the screen displays the graph for the internal attenuation DA which represents the value of total internal losses for absorptance and scattering of the signal in the measured sample.3.3.4Polarization-dependent measurements at variable angles in PS mode.The spectrophotometer has built-in high-contrast polarizers that operate unattended. This configuration provides for polarization-dependent measurement of transmittance, absolute specular reflectance at variable angles of incidence, and measurement/calculation of optical constants (refractive index, layer thickness and extinction coefficient).During the PS mode of measurement, the spectrum is measured subsequently for S polarization and for P polarization without any involvement of operator. Next, the (S+P)/2 value of random polarization is calculated and displayed instantly for transmittance or absolute specular reflectance.∙Switch on the spectrophotometer.∙Start the «PhotonSoft».IMPORTANT NOTE:After “PhotonSoft” software starts, the instrument runs self-check and initialization procedure of all controlled elements. This may take about 1 minute.It is PROHIBITED to switch off / switch on the instrument, close / open the software or activate any elements of the software during the self-check and initialization procedure. Otherwise this may damage the instrument.∙The warm-up time of the spectrophotometer shall be no less than 30 minutes.∙Set the required measuring parameters (see Subsection 3.4.1)(1) scanning range;(2) sampling pitch;(3) averaging count;(4) smoothing mode;(5) polarization - PS.(6) slid width∙Open the lid, make sure that the optical channel in the measuring compartment has no objects. Close the lid.∙Press the button«Apply».∙Press the button «CALIBRATION».∙Open the lid. Place a sample to be measured on the sample stage. The coated surface shall be facing the sample table for measurement of reflectance. Close the lid.∙Select «TRANSMITTANCE» or “REFLECTANCE” measurement mode from the drop-down menu. ∙Set the angel for the sample stage.∙Press the button«Apply».∙To start the measuring process, press the button «MEASUREMENT».In the «PS» polarization mode the baseline calibration is performed twice: in «S» position of the polarizer and in «P» position of the polarizer. The displayed spectrum for «S» polarization is dark blue and that for «P» polarization is dark green in color. The calculation of average polarization «(S+P)/2» is performed after completion of subsequent measurements for the spectra associated with «S» and «P» polarizations. The resultant spectrum is displayed in white color on the screen immediately.∙When the process is finished, the screen displays a transmittance or reflectance spectrum at the specified angle of incidence at (S+P)/2 average polarization.IMPORTANT NOTES:1)When starting the instrument on the new day, it is recommended to repeat baseline calibration beforeactual measurements for breaking-in after 30 minutes warm-up time. This ensures small bit adjustments of the moving parts after idle time.Recommended parameters:2)Staring wavelength: 400 nm;3)Ending wavelength: 1600 nm;4)Sampling pitch: 10 nm;5)Averaging count: 10;6)Smoothing mode: 0;7)Select the wavelength scanning range applicable to the measured sample.8)For more precise measurements in UV-VIS or VIS range, set scanning range and run baselinecalibration up to 990 nm. (For example, 180-990 nm or 380-990 nm respectfully.)9)For more precise measurements in IR range, set scanning range and run baseline calibration starting1000 nm. (For example, 1000-3000 nm, 1000-1650 nm etc.)10)W hen measurements are conducted over the complete effective wavelength range of thespectrophotometer, perform calibration directly before measuring the spectrum for a sample.11)S elect the slit width approximately 1.5 times bigger compared to regular (not PS) measurementprocedure. Make sure the maximum signal value does not exceed 65 000 units after baseline calibration (refer to the Signal window of the main interface).Figure 3.3.2 Transmittance spectrum in «PS» mode.Figure 3.3.2 shows a transmittance spectrum of the optical coating at the 45˚ angle of incidence in «PS» mode. The spectra for «S» and «P» polarizations are displayed in darkened colors.3.3.5Transmittance measurement of thick samples at high angles of incidence.When measuring transmittance of thick optical samples at high angles of incidence, the parallel displacement of transmitted beam occurs. The value of beam displacement depends on three factors: angle of incidence, physical thickness of the sample and refractive index of the sample material.The PHOTON RT spectrophotometer offers a possibility for correct transmittance measurement of thick sample at high angles using the built-in “Beam displacement calculator” option (See also Section 3.4.8). The actual value of beam displacement can be within 0-10 mm range.∙Switch on the spectrophotometer.∙Start the «PhotonSoft».IMPORTANT NOTE:After “PhotonSoft” software starts, the instrument runs self-check and initialization procedure of all controlled elements. This may take about 1 minute.It is PROHIBITED to switch off / switch on the instrument, close / open the software or activate any elements of the software during the self-check and initialization procedure. Otherwise this may damage the instrument.∙The warm-up time of the spectrophotometer shall be no less than 30 minutes.∙Set the required measuring parameters (see Subsection 3.4.1)(1) scanning range;(2) sampling pitch;(3) averaging count;(4) smoothing mode;(5) sample table angle setting(6) polarization - PS.∙Open the lid. Make sure that the optical channel in the measuring compartment has no objects. Close the lid.∙Press the button«Apply».∙Press the button «Calibration» for baseline calibration. When scanning of a spectrum is finished, the screen displays the horizontal spectral graph serving as 100% transmittance level.∙Open the lid. Place a sample to be measured on the sample stage.∙Select desired angle of incidence. Close the lid.∙Select «BEAM DISPLACEMENT CALCULATOR» from the drop-down menu «Tools”. The “Beam displacement calculator” window opens (see Figure 3.4.21).∙In the “Beam displacement calculator” window, fill in appropriate fields “Thickness” (in mm) and “Refractive index” for the measured sample. The angle of sample table is uploaded from the “Sample table angle setting” field (see Figure 3.4.4).∙The value of beam displacement (in mm) is calculated immediately.∙Press the button«APPLY» in the “Beam displacement calculator” window. The value of beam displacement (in mm) will be immediately displayed in the “Detector displacement, mm” field of the “Display options” menu (see Figure 3.4.4).∙Press the button«APPLY» in the “Display options” menu (see Figure 3.4.4).∙Start the measuring process by pressing the button «MEASUREMENT». When the process is finished, the screen displays the graph for transmittance spectra of the sample at a user-selected angle of incidence.∙Change the beam displacement value for “0” in the “Detector displacement, mm” field of the “Display options” menu (see Figure 3.4.4) if no further transmittance measurements of thick samples at highangles of incidence are required.∙Press the button«APPLY» in the “Display options” menu (see Figure 3.4.4).The beam displacement of the detectors can also be realized by setting the check box in the field "Detector autodisplacement" (see. Figure 3.4.3). The following lines become active: "Sample thickness, mm" and "Refractive index n”. The value of the sample thickness and the average refractive index of the sample material for the selected wavelength range shall be indicated in the appropriate fields. After clicking the "Apply" button, the value of detector displacement will be displayed in the "Detector displacement, mm" field. The detectors will immediately move at the calculated value of displacement.3.3.6Measurement of complex refractive index and layer thicknessOptical constants of the material layers are characterized with a number of parameters. Several of them are important for experts involved in optical design of the multilayer coatings – refractive index (n), layer thickness (d) and extinction coefficient (k).The NKD calculation software is designed to calculate the refractive index (n), extinction coefficient (k) and layer thickness (d) of the single homogenous layers on the known substrate using the photometric reverse engineering method. Calculations of optical parameters of the thin film layers is based on measuring the reflectance of the coated substrate in a polarized light (Rp and Rs values) for several angles of incidence. Typically, 3 to 8 angles of incidence are sufficient for correct measurement and calculation. Recommended sampling pitch is from 5 to 20 nm. The wedged substrate (with not less than 5 deg wedge angle) must be used for correct measurement to exclude reflectance from the back surface. BK7 and SiO2 substrates are recommended as test substrates for described measurement. It is necessary to increase the slid with 1,5 times to compensate for decreased signal in the PS measurement mode.∙Switch on the spectrophotometer.∙Start the «PhotonSoft».。
petapoco 多参存储过程 -回复

petapoco 多参存储过程-回复微软的Petapoco是一个轻量级的ORM框架,它允许开发人员使用.NET 语言来访问和操作数据库。
Petapoco提供了强大的对象到关系模型的映射功能,使开发人员能够以面向对象的方式进行数据库操作,提高了代码的可读性和可维护性。
在使用Petapoco进行数据库操作时,存储过程是一种常见的技术选择。
存储过程是一组预编译的SQL语句,可以接受参数并返回结果。
Petapoco提供了丰富的支持,使开发人员能够方便地与存储过程进行交互。
本文将一步一步地介绍如何使用Petapoco与多参数存储过程交互。
第一步:创建存储过程首先,我们需要在数据库中创建一个存储过程。
存储过程是在数据库中预先编译的一组SQL语句,可以接受参数并返回结果。
我们可以使用数据库管理工具(如SQL Server Management Studio)来创建存储过程。
以下是一个简单的示例存储过程:CREATE PROCEDURE GetProductsByCategoryCategoryId INTASBEGINSELECT * FROM Products WHERE CategoryId = CategoryIdEND上面的存储过程名为`GetProductsByCategory`,它接受一个`CategoryId`参数,并在`Products`表中查询指定`CategoryId`的产品。
这只是一个简单的示例,你可以根据实际需求编写更复杂的存储过程。
第二步:定义实体类在使用Petapoco与存储过程交互之前,我们需要定义一个实体类来表示存储过程的结果。
实体类是一个普通的.NET类,它的属性对应着存储过程返回的结果列。
以下是一个使用Petapoco和存储过程的实体类示例:[PetaPoco.TableName("Products")][PetaPoco.PrimaryKey("Id")]public class Product{public int Id { get; set; }public string Name { get; set; }public decimal Price { get; set; }}在上面的示例中,我们使用了`PetaPoco.TableName`和`PetaPoco.PrimaryKey`特性来指定表名和主键列。
Bosch Serie 4 积分式洗衣机说明书

Serie 4, Lavastoviglie integrabile, 60 cm, acciaio inox, XXLSBI4HCS48EAccessori specialiSGZ0BI11 Kit di adattamento e fissaggio NiroSGZ0IC00 :SGZ1010 Prolunga acqua-stop sgs/gi/gv/guSMZ1051EU :SMZ2014 Cestello per bicchieri a stelo lungoSMZ5000 Set completo spazio 51SMZ5003 Cerniera ribaltabile per dimensioni alte SMZ5045 :SMZ5100 Cestello porta posateSMZ5300 Accessorio lavastoviglie da incasso Caricare facilmente le stoviglie e gestirela lavastoviglie tramite l'app Home Connect.• ExtraDry: opzione selezionabile per un'ulteriore asciugatura.• CestelloVario - Flessibilità nel terzo livello di carico• Home Connect: elettrodomestici interconnessi di Bosch per unapiù facile gestione della quotidianità• AquaStop: protezione antiallagamento, con una garanzia a vita al 100%.Dati tecniciClasse di efficienza energetica: ........................................................D Consumo energetico del programma Eco per 100 cicli : .........85 kWh Numero massimo di coperti: .. (14)Consumo di acqua del programma eco in litri per ciclo: ..............9.5 l Durata del programma: .............................................................4:55 h Emissioni di rumore aereo: ......................................44 dB(A) re 1 pW Classe di emissioni di rumore aereo: ................................................B Da incasso / a libera installazione: .....................................Da incasso Altezza senza piano di lavoro: ....................................................0 mm Dimensioni (lxp): ................................................865 x 598 x 573 mm Dimensioni del vano per l'installazione: .......865-925 x 600 x 550 mm Profondità con porta aperta a 90 gradi: ...............................1200 mm piedini regolabili: ...................................................Yes - all from front Regolazione massima dei piedini: ............................................60 mm Zoccolo regolabile: ..........................................verticale ed orizontale Peso netto: ..............................................................................37.6 kg Peso lordo: ..............................................................................39.5 kg Potenza: ..................................................................................2400 W Corrente: .....................................................................................10 A Tensione: .............................................................................220-240 V Frequenza: ...........................................................................50; 60 Hz Lunghezza del cavo di alimentazione elettrica: .....................175.0 cm Tipo di spina: ..........................................................................Schuko Lunghezza tubo entrata: ..........................................................165 cm Lunghezza tubo uscita: ............................................................190 cm Codice EAN: (4242005184019)Installazione: ......................................................................IntegrabileSerie 4, Lavastoviglie integrabile, 60cm, acciaio inox, XXLSBI4HCS48ECaricare facilmente le stoviglie e gestire la lavastoviglie tramite l'app Home Connect.Prestazioni e consumo- Classe di efficienza energetica¹: D- Energia² / Acqua³: 85 kWh / 9.5 litri- Capacità: 14 coperti- Durata del programma⁴: 4:55 (h:min)- Livello sonoro: 44 dB(A) re 1 pW- Livello di rumore programma Silence: 41(A) re 1 pW- Classe di efficienza di rumore: BProgrammi e opzioni- 6 Programmi: Eco 50 °C, Auto 45-65°, Intensive 70 °C, Express 65°, Silence- Prelavaggio- 4 Programmi supplementari: Home Connect, Asciugatura extra, Mezzo carico, SpeedPerfect+- Home Connect-capibile via WLAN- Programma manutenzione- Silence on demand (tramite App)Tecnologia lavaggio- Scambiatore di calore.- DosageAssist- EcoSilence Drive- Automatismo di pulizia- Sistema di filtri autopulenti con ondulazione a 3 livelli- Contenitore interno: Materiale della vasca interna in acciaio inox Sistema Cestelli- Cestelli Flex- VarioCestello- Ruote con scorrimento facile nel cestello inferiore e nel terzo cestello- Cestello inferiore con blocco (rackStopper) per evitare che fuoriesca dalle guide.- Cestello superiore regolabile in altezza con Rackmatic (3 livelli)- Griglie abbattibili nel cestello superiore (2x)- Griglie abbattibili nel cestello inferiore (2x)- Ripiani per tazze nel cestello superiore (2x)- Carrello inferiore con ripiani per tazze (2x)Indicazione e funzionamento- Iscrizioni di testo in chiaro (inglese)- Indicazione tempo residuo (min.)- Programmatore inizio lavaggio (1-24 h)Sicurezza- AquaStop: una garanzia Bosch per danni causati dall'acqua - durata del dispositivo*- Sicurezza bambini (Tasti)- Tecnologia di protezione del vetro - Aiuto per il riempimento del sale (Imbuto)- Protezione contro il vaporeDimensioni- Dimensioni del prodotto (HxLxP): 86.5 x 59.8 x 57.3 cm¹ In una scala di classi di efficienza energetica da A a G² Consumo di energia in kWh per 100 cicli (nel programma Eco 50°C)³ Consumo di acqua in litiri per ciclo (nel programma Eco 50 °C)⁴ Durata del programma Eco 50 °C* Verificare i termini di garanzia al link/ch/it/condizioni-generali-di-garanziaSerie 4, Lavastoviglie integrabile, 60 cm, acciaio inox, XXLSBI4HCS48E。
PIC32MX Trace Interface 连接指南说明书
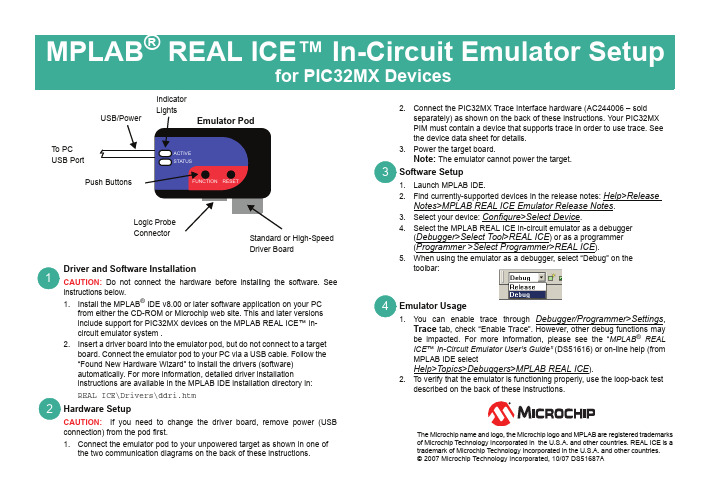
2.Connect the PIC32MX Trace Interface hardware (AC244006 – soldseparately) as shown on the back of these instructions. Your PIC32MX PIM must contain a device that supports trace in order to use trace. See the device data sheet for details.3.Power the target board.Note: The emulator cannot power the target.Software Setupunch MPLAB IDE.2.Find currently-supported devices in the release notes: Help>ReleaseNotes>MPLAB REAL ICE Emulator Release Notes .3.Select your device: Configure>Select Device .4.Select the MPLAB REAL ICE in-circuit emulator as a debugger(Debugger>Select Tool>REAL ICE ) or as a programmer (Programmer >Select Programmer>REAL ICE ).5.When using the emulator as a debugger, select “Debug” on thetoolbar:Emulator Usage1.You can enable trace through Debugger/Programmer>Settings ,Trace tab, check “Enable Trace”. However, other debug functions may be impacted. For more information, please see the “MPLAB ® REAL ICE ™ In-Circuit Emulator User’s Guide” (DS51616) or on-line help (from MPLAB IDE selectHelp>Topics>Debuggers>MPLAB REAL ICE ).2.To verify that the emulator is functioning properly, use the loop-back testdescribed on the back of these instructions.34Driver and Software InstallationCAUTION: Do not connect the hardware before installing the software. See instructions below.1.Install the MPLAB ® IDE v8.00 or later software application on your PCfrom either the CD-ROM or Microchip web site. This and later versions include support for PIC32MX devices on the MPLAB REAL ICE™ in-circuit emulator system .2.Insert a driver board into the emulator pod, but do not connect to a targetboard. Connect the emulator pod to your PC via a USB cable. Follow the “Found New Hardware Wizard” to install the drivers (software) automatically. For more information, detailed driver installationinstructions are available in the MPLAB IDE installation directory in:REAL ICE\Drivers\ddri.htmHardware SetupCAUTION: If you need to change the driver board, remove power (USB connection) from the pod first .1.Connect the emulator pod to your unpowered target as shown in one ofthe two communication diagrams on the back of these instructions.21USB/PowerEmulator PodLogic Probe ConnectorIndicatorLightsPush ButtonsStandard or High-Speed Driver BoardTo PC USB PortThe Microchip name and logo, the Microchip logo and MPLAB are registered trademarks of Microchip T echnology Incorporated in the U.S.A. and other countries. REAL ICE is a trademark of Microchip T echnology Incorporated in the U.S.A. and other countries.© 2007 Microchip Technology Incorporated, 10/07 DS51687AEmulator PodTarget BoardPIC32MX PIMStandard Driver BoardStandard CommunicationEmulator PodTarget BoardHigh-Speed Driver BoardPIC32MX PIMHigh-Speed Receiver BoardHigh-Speed CommunicationExternal Triggersor TraceExternal Triggersor TraceDebug/Programmer InterfaceDebug/Programmer InterfacePerformance PakP I C 32trace portPIMPIC32MX Trace InterfaceTarget BoardEmulatorPodStandard Driver Board Loop-Back Test B oardModular Cable Logic Probe Connector Driver Board Slot Loop-Back TestT o verify that the emulator is function-ing properly, use the loop-back test board. Disconnect the emulator fromthe target and PC, plug in the stan-dard driver board and loop-back test board as shown, reconnect the emu-lator to the PC, and select the emula-tor as in “Software Setup”, Step 3, on the front of these instructions toautomatically run the loop-back test.Trace Adaptertrace cableEmulator Podlogic probe connectorDebug/Programmer InterfaceOR。
acitivity monitor 参数的解释
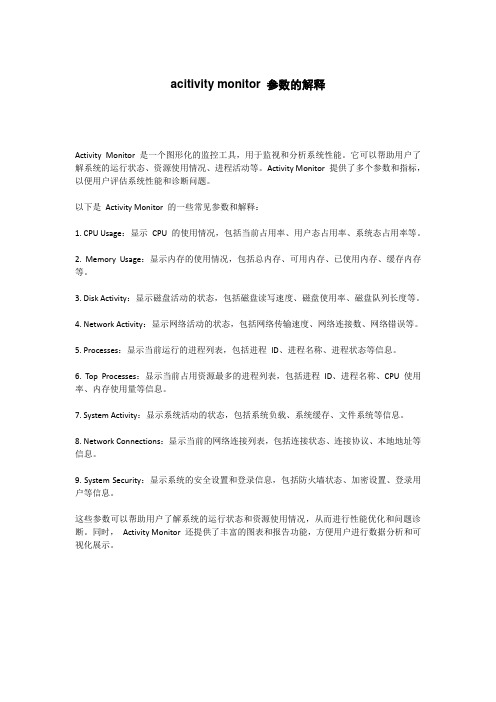
acitivity monitor 参数的解释Activity Monitor 是一个图形化的监控工具,用于监视和分析系统性能。
它可以帮助用户了解系统的运行状态、资源使用情况、进程活动等。
Activity Monitor 提供了多个参数和指标,以便用户评估系统性能和诊断问题。
以下是Activity Monitor 的一些常见参数和解释:1. CPU Usage:显示CPU 的使用情况,包括当前占用率、用户态占用率、系统态占用率等。
2. Memory Usage:显示内存的使用情况,包括总内存、可用内存、已使用内存、缓存内存等。
3. Disk Activity:显示磁盘活动的状态,包括磁盘读写速度、磁盘使用率、磁盘队列长度等。
4. Network Activity:显示网络活动的状态,包括网络传输速度、网络连接数、网络错误等。
5. Processes:显示当前运行的进程列表,包括进程ID、进程名称、进程状态等信息。
6. Top Processes:显示当前占用资源最多的进程列表,包括进程ID、进程名称、CPU 使用率、内存使用量等信息。
7. System Activity:显示系统活动的状态,包括系统负载、系统缓存、文件系统等信息。
8. Network Connections:显示当前的网络连接列表,包括连接状态、连接协议、本地地址等信息。
9. System Security:显示系统的安全设置和登录信息,包括防火墙状态、加密设置、登录用户等信息。
这些参数可以帮助用户了解系统的运行状态和资源使用情况,从而进行性能优化和问题诊断。
同时,Activity Monitor 还提供了丰富的图表和报告功能,方便用户进行数据分析和可视化展示。
acitivity monitor 参数的解释

acitivity monitor 参数的解释Activity monitor(活动监视器)是一款用于监控电脑系统活动和性能的实用工具。
它可以提供关于CPU、内存、硬盘、网络等方面的信息,帮助用户了解系统的运行情况并及时采取相应的措施。
本文将详细解释Activity monitor的参数,并介绍其在不同操作系统中的使用方法和功能。
一、Activity monitor 参数的解释Activity Monitor中有许多参数可以帮助用户了解系统的运行情况,以下是一些常见的参数及其解释:1. CPU(中央处理器)参数- % CPU:显示每个进程(包括应用程序和背景进程)使用CPU的百分比。
可以提供关于CPU使用情况的概览。
- Idle %:显示CPU处于空闲状态的百分比。
当该值过高时,表示CPU资源空闲,当该值过低时,表示CPU资源繁忙。
2. Memory(内存)参数- Memory Used:显示已使用的物理内存量。
当该值过高时,表示内存资源不足,可能会导致系统运行缓慢。
- Swap Used:显示用于虚拟内存的磁盘空间。
当该值过高时,表示系统正在频繁地使用磁盘空间作为内存的延伸区域,可能会导致系统响应速度下降。
3. Disk(硬盘)参数- Read/Write:显示磁盘读取和写入速度(除非特别指定,否则以字节为单位)。
可以帮助用户了解硬盘的活动情况。
- Read/Write Errors:显示磁盘读取和写入过程中发生的错误数量。
当该值过高时,可能存在硬盘故障或其他问题。
4. Network(网络)参数- Sent/Received:显示已发送和接收的数据量。
可以帮助用户了解系统的网络流量情况。
- Connection Status:显示当前系统的网络连接状态。
可以帮助用户了解网络是否正常连接和运行。
5. Energy(能源)参数- Energy Impact:显示各个进程对电池寿命的影响程度。
可以帮助用户了解哪些应用程序会消耗更多的电能。
uepactivationvol子程序调用
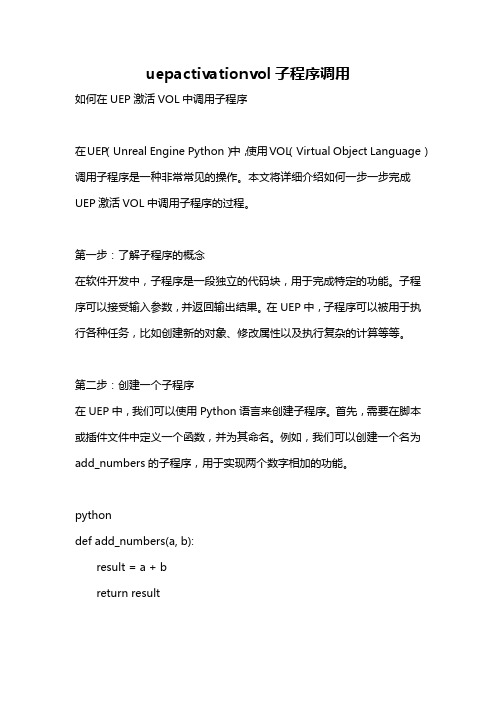
uepactivationvol子程序调用如何在UEP激活VOL中调用子程序在UEP(Unreal Engine Python)中,使用VOL(Virtual Object Language)调用子程序是一种非常常见的操作。
本文将详细介绍如何一步一步完成UEP激活VOL中调用子程序的过程。
第一步:了解子程序的概念在软件开发中,子程序是一段独立的代码块,用于完成特定的功能。
子程序可以接受输入参数,并返回输出结果。
在UEP中,子程序可以被用于执行各种任务,比如创建新的对象、修改属性以及执行复杂的计算等等。
第二步:创建一个子程序在UEP中,我们可以使用Python语言来创建子程序。
首先,需要在脚本或插件文件中定义一个函数,并为其命名。
例如,我们可以创建一个名为add_numbers的子程序,用于实现两个数字相加的功能。
pythondef add_numbers(a, b):result = a + breturn result上述代码定义了一个名为add_numbers的函数,该函数接受两个参数a 和b,并返回它们的和。
第三步:导入子程序一旦我们定义好了子程序,就可以在其他脚本中导入并调用它了。
在UEP 中,可以使用import语句来导入子程序。
假设我们的add_numbers函数定义在一个名为math_utils.py的脚本文件中,我们可以在其他脚本中使用以下方式导入该函数:pythonfrom math_utils import add_numbers上述代码将会导入math_utils.py文件中的add_numbers函数。
第四步:调用子程序一旦我们成功导入了子程序,就可以在UEP中调用它了。
调用子程序的方式与调用任何其他函数类似。
我们只需提供所需的参数,并处理返回的结果。
以下是一个使用add_numbers函数的示例:pythonresult = add_numbers(2, 3)print(result) # 输出结果为5上述代码将传入参数2和3给add_numbers函数,并将其返回的结果赋值给变量result。
evosuite 实例

evosuite 实例什么是evosuite实例?Evosuite是一个自动化测试工具,它使用遗传算法来生成测试用例。
Evosuite实例是指使用Evosuite工具生成的具体测试用例。
通过Evosuite 实例,可以检验和评估被测试对象的功能和性能。
步骤一:Evosuite实例的生成生成Evosuite实例的第一步是选择被测试的目标代码。
可以选择已有的Java代码或jar包作为目标。
Evosuite实例生成的目标是构建一个最小的测试用例集,以覆盖被测试代码的所有分支和逻辑路径。
步骤二:配置Evosuite工具在生成Evosuite实例之前,需要配置Evosuite工具。
配置的目的是指定测试套件的路径、生成测试用例的时间限制、是否生成断言和其他选项。
配置完成后,可以启动Evosuite工具。
步骤三:执行Evosuite工具启动Evosuite工具后,它会根据配置信息开始生成测试用例。
Evosuite使用遗传算法的思想,从初始种群中不断进化,生成新的测试用例,并且评估每个测试用例的适应值。
适应值较高的测试用例将保留并用于生成更多的测试用例。
步骤四:评估Evosuite实例生成的Evosuite实例需要通过一系列评估指标来评估其质量和效能。
常见的评估指标包括代码覆盖率、故障检出率、执行时间、测试用例的有效性等。
借助这些指标,可以评估Evosuite实例的效果和可行性。
步骤五:修改和优化Evosuite实例根据评估结果,可以对Evosuite实例进行修改和优化。
可能需要调整配置选项,例如测试用例生成的时间限制、生成测试用例的数量等。
也可以通过修改目标代码的内容,来改进Evosuite实例的生成效果。
经过多轮的修改和优化,Evosuite实例可以不断改善,并达到更好的测试目的。
步骤六:应用Evosuite实例生成并优化的Evosuite实例可以用于多个方面。
首先,它可以作为质量保证的手段,验证被测试代码的正确性和稳定性。
Leica Spatial Analyzer User Manual

106L eicaAT9x0Prerequisites■All Leica trackers are shipped with 192.168.0.1 as the IP address as default. The Leica AT960/930 also off er a wireless connectionoption.■The current version of Tracker Pilot can be downloaded directly from the Laser Tracker Controller. To do so, open a web browser and type http://192.168.0.1 in the search bar. This will open a link to the tools saved on the tracker controller. To learn more about confi guring IP addresses, see the IP Address Basics pensationThe AT960/930 trackers and accessories can be compensated within Tracker Pilot (if you need the current Tracker Pilot you can browse di-rectly to http://192.168.0.1 (or the trackers IP) and download Tracker Pilot from the controller).■Compensation Password: Expert (Full and Intermediate, ADM, Refl ector Defi nition, Camera Compensation, etc.)■Server Settings Password: Administrator (TCP/IP address, Time/Date, etc.)Starting the Interface1. Select Instrument > Add and choose the respective Leica Trackerfrom the Add Instrument to SA dialog.1072. Figure 3-96. A dding a LeicaAT960/930 tracker.Now run the instrument interface module under Instrument > Run Interface Module and choose Laser Trackers .3. Enter the tracker’s IP address and use the Ping button to test the connection if needed. Once satisfi ed, press OK . The next time the interface is started, you can simply click the Run In-terface and Connect icon. This will use the last saved set-tings and automatically connect the instrument. The AT960/930 also off ers an IP discover utility.4. Figure 3-97. T he Leica Trackerconnection window.v The interface is now connected and ready for use. Please refer to the Laser Tracker section for details on the laser tracker in-terface (”Laser Tracker Interface ” on page 10).Tracker Settings To access the custom settings, use Settings > Tracker > General Settings orpress the button. Then press the tracker specifi c button at the bot-tom.6D Shank MeasurementsWith a calibrated shank tip attached to a T-probe (calibration is per-formed within Tracker Pilot), shank measurements can be taken forsheet metal applications, providing an edge measurement solution.Shank Points is a new Operation that can be used with any measure-ment acquisition mode(discrete, stable or scan). But two new mea-surement profi les have been added to support this application(Figure3-98):■Discrete Shank Point. This mode is the standard measure-ment of a point on an edge.■Discrete Bottom Shank Point. This operation provides thesame shank measurement option with the addition of a speci-fi ed shift relative to the reference plane, designed to accountfor material thickness.Figure 3-98. S hank Measurement Profile OperationsShank Plane - measurements require a projection plane to be defi nedand use this plane defi nition to defi ne the intersection point of theshank axis and the plane. The tilt of the probe relative to the plane isused to determine the point’s off set in combination with the probediameter.This means that the cleanest off set is obtained by holding the probeperpendicular to the edge. Tilting the probe is fi ne but leaning it suchthat it trails along the edge (into or out of the paper in (Figure 3-99)should be avoided and could cause an overestimate of the off set.Override Radius- the radius of the shank probe should be set as partof the calibration process but its default value can be changed withinthe measurement profi le if needed, using this control.Shank Measurements in SpatialAnalyzer -https://youtu.be/hXnoj4ov1GA108Figure 3-99. P roper orientation ofthe probe for accurate shank measure-mentsProximity Measurements with a Shank ProbeShank measurements can also be used with proximity triggers. Thismakes edge measurements easy to perform by allowing you to trig-ger points along an edge as you slide a shank probe along it.To do so perform the following steps:1. Build a vector group to be used for the proximity trigger pro-cess. Each vector in this vector group will be used as a triggersuch that as the probe’s axis crosses the vector a point will betriggered for you.2. Navigate to Instru ment>Au tomatic Measu rement>Au to-Correspondwith Proximity Triggers>Vectors. Specify a tolerance zone to con-sider and a resulting group name and begin the operation.Double check that the option to measure each point more than oncewithin the proximity dialog is Enabled. If you don’t, it will simply takethe fi rst point that is within the proximity tolerance…on the approachand will not fi nd the closest point to the vector intersection.3. Slide the shank probe along the edge of the part to triggermeasurements at each of the reference vector locations.The point that is recorded is the closest point on the shank to the vec-tor origin. Its important, therefore to have a good alignment. If themeasure feature deviations signifi cantly from the nominal the com-pensation can be aff ected.External Trigger Confi gurationThe external trigger settings are defi ned within a “Custom Triggers”measurement profi le. These settings are shown conceptually in Fig-ure 3-100 and as they appear in the measurement profi le settings dia-log in Figure 3-100.109Figure 3-100. E xternal Trigger ConfigurationFigure 3-101. C ustom Profi leused to Enable External TriggeringMeasurement Profi le SettingsExternal Trigger measurements can be performed using either of twobasic methods:1. Set the Clock Source to “Internal” and use the external trigger tocontrol the start and stop of a scan at a give rate.2. Set the Clock Source to “External” and trigger measurements ex-clusively with the external trigger.Clock Source:■Internal (Internal Clock with External Start/Stop Signal).110Measurements will be triggered by the external start/stop sig-nal on the trigger board. However, the measurement rate willbe taken based on internal settings and is not synchronized toan external signal.■External (External Clock with Start/Stop Signal). The mea-surement will be controlled by a start/stop signal on the trig-ger board. One transition of the clock signal (positive or nega-tive depends on the confi guration) triggers a measurement ifthe Start/Stop signal is active.Start / Stop Active Level■Low/High. The start/stop signal can be set either low or highactive (for example, low active means that events are beinggenerated as long as the start/stop signal remains low).Start / Stop Source■Ignored/Active. This setting controls the subsequent responseto the external trigger after a measurement operation hasstarted. If ignored, the measurement will continue regardlessof other triggers until the profi le is stopped, while if active, thefollowing trigger changes will start / stop the measurement.Clock Transmission■Negative/Positive. This defi nes the change in clock signalused for the trigger (negative transition or positive transition).Minimal Time Delay■Delay Value. This defi nes the maximum rate at which mea-surements can be taken (minimal delay between two consecu-tive measurements). Additional trigger signals sent faster thanthis preset delay will be ignored.Running the Tracker Interface SeparatelyOne of the unique features about SA’s architecture is that the instru-ment interface can be run separately from SA. This provides a meansto run multiple trackers independently on diff erent machines whileconnect to a single SA for data storage. Doing so also provides theability to separate the persistence fi les for individual trackers, as thepersistence fi le will be saved in the directory as where the tracker in-terface is launched, as opposed to the C:\Analyzer Data\Persistencefolder.In order to run the SA Laser Tracker process separately some addition-al support fi les are required. These include the following fi les (Figure3-102):111to run the SA Laser Tracker processindependently from SA.Additional ConnectionsThe AT960 can be used with a number of peripheral devices. For moreinformation refer to the following quickstart guides:■“Hexagon AS1 Scanner” on page 121■“Leica Absolute Scanner (LAS) 20-8” on page 128■“Leica T-Scan Interface” on page 131112。
MPLAB Harmony 2016用户手册说明书

2016 Microchip Technology Inc.page 1STANDARD FEATURES•MPLAB ® Harmony is a flexible, abstracted, fully integrated firmware development platform for PIC32 microcontrollers•Broad range of Middleware Stack/Libraries, including: USB, TCP/IP , Wi-Fi™, File System, Graphics, Bootloaders, Bluetooth™, Audio, DSP , Math, Cryptography, Drivers, System Services, and more•Over 160 Application Demonstrations with up to 600 application configurations to accelerate application development•Seamlessly integrates third-party solutions (RTOS, Middleware, Drivers, etc.) into the software frame-work•RTOS support, which includes: FreeRTOS™, OPENRTOS, Express Logic Thread X, SEGGER embOS ®, Micriµm ® µC/OS-II™, Micriµm µC/OS-III™ •Middleware support, which includes: SEGGERemWin ®, InterNiche Technologies, Inc., wolfSSL, and PubNub ®•Both free and enabling license terms provided For a detailed list of features, please visit the MPLAB Harmony Web page at:/harmonyFrom the landing page, scroll down and select the Features tab.DESCRIPTIONMPLAB Harmony is a flexible, abstracted, fully integrated firmware development platform for PIC32microcontrollers. MPLAB Harmony's modular architec-ture allows drivers and libraries to work together with minimal effort. It is scalable across PIC32 Microchip devices to custom fit customers’ requirements.MPLAB Harmony takes key elements of modular and object oriented design, adding an Operating System Abstraction Layer (OSAL) that provides the flexibility to use a Real-Time Operating System (RTOS) or work without one, and provides a framework of software modules that are easy to use, configurable for your specific needs, and that work together in complete har-mony.In addition, the MPLAB Harmony Configurator (MHC)and code development format allows for maximum reuse and reduces time to market.COMPLIANCECompliant with MISRA-C:2012 Mandatory Standards:•MPLAB Harmony Drivers, System Services, and Peripheral LibrariesDEVELOPMENT TOOLS•MPLAB X IDE v3.30 or later is required•MPLAB XC32 C/C++ Compiler v1.42 (ISO 26262)•MPLAB X IDE plug-ins:-MPLAB Harmony Configurator (MHC) v2.00.xxTHIRD-PARTY DEVELOPERSMicrochip offers a range of documentation to assist you with the design of your own software offerings for MPLAB® Harmony. These documents, which are pro-vided with the installation Help, are also available for download from the MPLAB Harmony website (see “Download Information” for details). •MPLAB Harmony Overview•MPLAB Harmony Compatibility Guide •MPLAB Harmony Tutorial•MPLAB Harmony Driver Development Guide •MPLAB Harmony Configurator User's Guide•MPLAB Harmony Configurator Developer's Guide •MPLAB Harmony Graphics Composer User's Guide •MPLAB Harmony Test Harness User's Guide•MPLAB Harmony Compatibility Checklist WorksheetS o f t w a r e F r a m e w o r kIntegrated Software Framework v2.00bMPLAB HARMONY v2.00bpage 2 2016 Microchip Technology Inc.v2.00b FEATURE UPDATES AND ADDITIONS0MPLAB Harmony v2.0b includes the following updates and additions:•Board Support Package (BSP) Creation tool (Alpha)•Application templates (Beta)•Initial microMIPS™ ISA support •PIC32MZ DA MCU family support•MISRA-C: 2012-compliant optimized peripheral libraries for all PIC32 MCUs•TCP/IP Stack Library updates for Static drivers •New applications for microphone support:-usb_headset -usb_microphone•Updated Audio Codec drivers (microphone support and dynamic I 2C)•Updated applications for PIC32MZ audio •Integrated Touch and Audio applications•Tighter coupling between SEGGER emWin Pro and MPLAB Harmony:-SEGGER emWin tool suite-SEGGER emWin functional demonstration and user’s guide•AR1021 Resistive Touch Display Driver•Revised JPEG decoder with integrated support for external media and display resize•New application for SD card JPEG, BMP , and GIF decoding to display•New application for MSD JPEG decoding, low-cost graphics board•Updated touch drivers (MTCH6301, MTCH6303); improved touch system service•Opus codec in universal decoders framework •Support for double buffering (up to WQVGAresolution) in MPLAB Harmony Graphics Composer •Updated support for WVGA display (LCCG Graphics Driver) on PIC32MZ family devicesUtilities:•MHC and MPLAB Harmony Graphics Composer -Configuration Import/Export/Move/Copy -Updated pin management features Please refer to the v2.00b Release Notes for additional information (see “Download Information”).DOWNLOAD INFORMATIONMPLAB Harmony, including the current release notes and Software License Agreement, is available for download by visiting:/mplabharmonyADDITIONAL RESOURCESMPLAB Harmony TV offers a wide range of getting started and training videos. The video content is avail-able by scrolling to the bottom of the MPLAB Harmony webpage at:/mplabharmony The Microchip Developer Site provides short introductory videos, self-paced training modules, and answers to frequently asked questions./harmony:startNote the following details of the code protection feature on Microchip devices:•Microchip products meet the specification contained in their particular Microchip Data Sheet.•Microchip believes that its family of products is one of the most secure families of its kind on the market today, when used in the intended manner and under normal conditions.•There are dishonest and possibly illegal methods used to breach the code protection feature. All of these methods, to our knowledge, require using the Microchip products in a manner outside the operating specifications contained in Microchip’s Data Sheets. Most likely, the person doing so is engaged in theft of intellectual property.•Microchip is willing to work with the customer who is concerned about the integrity of their code.•Neither Microchip nor any other semiconductor manufacturer can guarantee the security of their code. Code protection does not mean that we are guaranteeing the product as “unbreakable.”Code protection is constantly evolving. We at Microchip are committed to continuously improving the code protection features of our products. Attempts to break Microchip’s code protection feature may be a violation of the Digital Millennium Copyright Act. If such acts allow unauthorized access to your software or other copyrighted work, you may have a right to sue for relief under that Act.。
西部数据HP 33120A波形生成器说明书

HUncompromising performance for standard waveformsThe HP 33120A function/arbitrary waveform generator uses direct digital-synthesis techniques to create a stable, accurate output signal for clean, low-distortion sine waves. It also gives you fast rise-and fall-time square wave, and linear ramp waveforms down to10mHz.Custom waveform generationUse the HP 33120A to generate complex custom waveforms such as a heartbeat or the output of a mechanical transducer. With 12-bit resolution, and a sampling rate of 40MSa/s, the HP 33120A gives you the flexibility to create any waveform you need. It also lets you store up to found 16,000-deep waveforms in nonvolatile memory. Easy-to-use functionalityFront-panel operation of theHP33120A is straightforward and intuitive. You can access any often major functions with a single key press or two, then use a simple knob to adjust frequency, amplitude and offset. To save time, you can enter voltage values directly in Vp-p, Vrms or dBm. Internal AM, FM,FSK and burst modulationmake it easy to modulatewaveforms without theneed for a separatemodulation source.Linear and log sweeps arealso built in, with sweeprates selectable from 1msto 500s. HP-IB and RS-232interfaces are both standard,plus you get full programmabilityusing SCPI commands.Optional phase-lock capabilityThe Option 001 phase lock/TCXOtimebase gives you the ability togenerate synchronized phase-offsetsignals. An external clockinput/output lets you synchronizewith up to three other HP 33120Asor with an external 10-MHz clock.Option 001 also gives you aTCXO timebase for increasedfrequency stability. With accuracyof 4 ppm/yr, the TCXO timebasemake an HP 33120A ideal forfrequency calibrations and otherdemanding applications.With Option 001, new commandslet you perform phase changes onthe fly, via the front panel or from acomputer, allowing precise phasecalibration and adjustment.Link the HP 33120A to your PCTo further increase yourproductivity, use the HP 33120A inconjunction with HP 34811ABenchLink Arb software. TheWindows®-based program lets youcreate and edit waveforms on yourPC and download them to yourHP33120A with the click of a mouse.Create complex waveforms in amath or statistics program--or usethe freehand drawing tool--then passthem into HP BenchLink Arb. Use inconjunction with HP BenchLinkScope, the software also lets youcapture a waveform with your HPoscilloscope or DMM and send it toyour HP 33120A for output.3-year warrantyWith your HP 33120A, you getoperating and service manuals, aquick reference guide, test date,and a full 3-year warranty, all forone low price.HP 33120A Function/ArbitraryWaveform GeneratorCreate custom waveforms easily and affordably • 15 MHz sine and square wave outputs• Sine, triangle, square, ramp, noise and more• 12-bit, 40MSa/s, 16,000-point deep arbitrary waveforms • Direct Digital Synthesis for excellent stabilityWaveformsStandard Sine, square, triangle,ramp, noise, sin(x)/x,exponential riseexponential fall, cardiac,dc volts.ArbitraryWaveform length8 to 16,000 points Amplitude resolution12 bits (including sign) Sample rate40 MSa/sNon-volatile memory Four (4) 16,000 waveforms Frequency CharacteristicsSine100 µHz - 15 MHz Square100 µHz - 15 MHz Triangle100 µHz - 100 kHz Ramp100 µHz - 100 kHz White noise10 MHz bandwidth Resolution10 µHz or 10 digits Accuracy10 ppm in 90 days,20 ppm in 1 year,18°C - 28°CTemp. Coeff< 2 ppm/°CAging< 10 ppm/yr Sinewave Spectral PurityHarmonic distortiondc to 20 kHz-70 dBc20 kHz to 100 kHz-60 dBc100 kHz to 1 MHz-45 dBc1 MHz to 15 MHz-35 dBcSpurious (non-harmonic)DC to 1 MHz< -65 dBc1 MHz to 15 MHz< -65 dBc + 6 dB/octave Total harmonic distortionDC to 20 kHz<0.04%Phase noise<-55 dBc in a 30 kHz band Signal CharacteristicsSquarewaveRise/Fall time< 20 nsOvershoot4%Asymmetry1% + 5nsDuty cycle20% to 80% (to 5 MHz)40% to 60% (to 15 MHz) Triangle, Ramp, ArbRise/Fall time40 ns (typical) Linearity<0.1% of peak output Setting Time<250 ns to 0.5% offinal valueJitter<25nsOutput CharacteristicsAmplitude (into 50Ω)50 mVpp - 10 Vpp [1]Accuracy (at 1 kHz)±1% of specified outputFlatness (sinewave relative to 1 kHz)< 100 kHz±1% (0.1 dB)100 kHz to 1 MHz±1.5% (0.15 dB)1 Mz to 15 MHz±2% (0.2 dB) Ampl≥3Vrms±3.5% (0.3 dB) Ampl<3VrmsOutput Impedance50Ω(fixed)Offset (into 50Ω) [2]+ 5 Vpk ac + dcAccuracy±2% of setting + 2 mVResolution 3 digits, amplitude andoffsetUnits Vpp, Vrms, dBmIsolation42 Vpk maximum to earthProtection Short circuit protected±15Vpk overdrive < 1 minuteModulationAMCarrier -3dB Freq.10 MHz (typical)Modulation any internal waveformincluding ArbFrequency10 mHz - 20 kHzDepth0% - 120%Source Internal/ExternalFMModulation any internal waveformincluding ArbFrequency10 mHz - 10 kHzDeviation10 mHz - 15 MHzSource Internal onlyFSKInternal rate10 mHz - 50 kHzFrequency Range10 mHz - 15 MHzSource Internal/External(1 MHz max.)BurstCarrier Freq. 5 MHz max.Count 1 to 50,000 cyclesor infiniteStart Phase-360°to +360°Internal Rate10 mHz - 50 kHz ±1%Gate Source Internal/External GateTrigger Single, External orInternal RateSweepType Linear or LogarithmicDirection Up or DownStart F/Stop F10 mHz - 15 MHzSpeed 1 ms to 500 s ±0.1%Trigger Single, External, or InternalRear Panel InputsExt. AM Modulation±5 Vpk = 100% modulation5kΩinput resistanceExternal Trigger/TTL low trueFSK/Burst GateSystem Characteristics[3]Configuration Times[4]Function Change:[5]80 msFrequency Change:[5]30 msAmplitude Change:30 msOffset Change:10 msSelect User Arb:100 msModulation ParameterChange:<350 msArb Download Times over HP-IBArb Length Binary ASCII Integer ASCII Real[6]16,000 points8 sec81 sec100 sec8,192 points 4 sec42 sec51 sec4,096 points 2.5 sec21 sec26 sec2,048 points 1.5 sec11 sec13 secArb Download Times over RS-232 at 9600 Baud:[7]Arb Length Binary ASCII Integer ASCII Real[8]16,000 points35 sec101 sec134 sec8,192 points18 sec52 sec69 sec4,096 points10 sec27 sec35 sec2,048 points 6 sec14 sec18 sec[1] 100 mVpp - 20 Vpp into open circuit[2] Offset ≤2x pk - pk amplitude[3] Times are typical. May vary based on controllerperformance[4] time to change parameter and output the new signal.[5] Modulation or sweep off.[6] Times for 5-digit and 12-digit numbers.[7] For 4800 baud, multiply the download times by two;For2400 baud, multiply the download times by four, etc.[8] Time for 5-digit numbers. For 12-digit numbers, multiplythe 5-digit numbers by two.2Option 001 Phaselock/TCXO TimebaseTimebase AccuracySetability< 0.01 ppmStability±1 ppm 0°- 50°Aging< 2ppm in first 30 days(continuous operation)0.1 pm/month(after first 30 days)External Reference InputLock Range10 MHz ±50 HzLevel-10 dBm to + 15 dBm+25 dBm or 10 Vpp maxinputImpedance50Ω±2%, 42 Vpk isolationto earthLock Time< 2 secondsInternal Reference OutputFrequency10 MHzLevel> 1 Vpp into 50 ΩPhase OffsetRange+ 360°to - 360°Resolution0.001°Accuracy25 nsTrigger OutputLevel5V zero-going pulse Pulse Width> 2µs typicalFanout Capable of driving up tothree 33120AsOrdering InformationHP 33120A Function/Arb GeneratorOpt. 001 Phase Lock/TCXO Timebase OptionGeneralPower Supply110V/120V/220V/240V ±10% Power Line Frequency45 Hz to 66 Hz and 360 Hzto 440 HzPower Consumption50VA peak (28 W average) Operating Environment0°C to 55°CStorage Environment-40°C to 70°CState Storage Memory Power Off stateautomatically saved, 3 UserConfigurable Stored States Interface IEEE-488 and RS-232standardLanguage SCPI - 1993, IEEE-488.2 Dimensions (W x H x D)Bench top254.4mm x 103.6mm x374mmRack mount212.6mm x 88.5mm x348.3mmWeight 4 kg (8.8 lbs)Safety Designed to UL-1244, CSA 1010,EN61010EMC Tested to MIL-461C, EN55011,EN50082-1Vibration and Shock MIL-T-28800, Type III,Class5Acoustic Noise30 dBaWarm-up Time 1 hourWarranty3 years standard3Ordering InformationHP 33120A Function/Arbitrary Waveform GeneratorAccessories includedOperating manual, service manual, quick reference guide, test data, and power cord.OptionsOpt. 001Phase lock/TCXO timebaseOpt. 106HP BenchLink Arb software (HP 34811A)Opt. 1CM Rack Mount Kit (P/N 5062-3972)*Opt. W50Additional 2-year warranty (5-year total)Opt. 910Extra manual setManual language options (please specify one)ABA US English ABD German ABE Spanish ABF French ABJ Japanese ABZ ItalianABO Taiwan Chinese AB1 KoreanAccessoriesHP 34161A Accessory pouchHP 34811A BenchLink Arb software*For racking two side-by-side, order both items below Lock-link Kit (P/N 5061-9694)Flange Kit (P/N 5062-3974)HData subject to change.Printed in the U.S.A. 8/98© Hewlett-Packard Company 1998Windows is a registered trademark of Microsoft Corporation.5968-0125ENFor more information about HP’s waveform generators and all other Hewlett-Packard basic instruments, and for a current sales office listing, visit our web site at /go/tmdir.You can also contact one of the following centers and ask for a test and measurement sales representative.United States:Hewlett-Packard CompanyTest and Measurement Call Center P.O. Box 4026Englewood, Colorado 80155-4026180****4844Canada:Hewlett-Packard Canada Ltd.5150 Spectrum Way Mississauga, Ontario L4W 5G1(905) 206 4725Europe:Hewlett-PackardEuropean Marketing Centre P.O. Box 9991180 AZ Amstelveen The Netherlands (31 20) 547 9900Japan:Hewlett-Packard Japan Ltd.Measurement Assistance Center 9-1, Takakura-Cho, Hachioji-Shi,Tokyo 192, Japan Tel: (81) 426 56 7832Fax: (81) 426 56 7840Latin America:Hewlett-PackardLatin American Region Headquarters 5200 Blue Lagoon Drive 9th FloorMiami, Florida 33126U.S.A.Tel: (305) 267-4245(305) 267-4220Fax: (305) 267-4288Australia/New Zealand:Hewlett-Packard Australia Ltd.31-41 Joseph StreetBlackburn, Victoria 3130Australia 1 800 629 485Asia Pacific:Hewlett-Packard Asia Pacific Ltd.17-21/F Shell Tower, Times Square,1 Matheson Street, Causeway Bay,Hong KongTel: (852) 2599 7777Fax: (852) 2506 9285。
国立工程实验室CDA-2990 8通道时钟分布系统用户手册说明书

Manufacturer: National InstrumentsBoard Assembly Part Numbers (Refer to Procedure 1 for identification procedure):Part Number and Revision Description140001A-03L or later CDA-2990, 8 CHANNEL CLOCK DISTRIBUTION SYSTEM 140001A-04L or later CDA-2990, 8 CHANNEL CLOCK DISTRIBUTION SYSTEM WITHINTEGRATED GPSDOVolatile MemoryTarget Data Type Size Backup1Accessible Accessible ProcedureNon-Volatile Memory (incl. Media Storage)Target Data Type Size BatteryBackupUserAccessibleSystemAccessibleSanitizationProcedureMicrocontroller Firmware Flash 128 KB No No Yes None GPSDO Parameter Data EEPROM 2 KB No No Yes None GPSDO Executable ProgramMemoryFlash 512 KB No No No None 1 Refer to Terms and Definitions section for clarification of User and System AccessibleProceduresProcedure 1 – Board Assembly Part Number Identification:To determine the Board Assembly Part Number and Revision, refer to the label applied to the surface of your product. The Assembly Part Number should be formatted as “P/N: 140001#-##L.Terms and DefinitionsCycle Power:The process of completely removing power from the device and its components and allowing for adequate discharge. This process includes a complete shutdown of the PC and/or chassis containing the device; a reboot is not sufficient for the completion of this process.Volatile Memory:Requires power to maintain the stored information. When power is removed from this memory, its contents are lost. This type of memory typically contains application specific data such as capture waveforms.Non-Volatile Memory:Power is not required to maintain the stored information. Device retains its contents when power is removed.This type of memory typically contains information necessary to boot, configure, or calibrate the product or may include device power up states.User Accessible:The component is read and/or write addressable such that a user can store arbitrary information to the component from the host using a publicly distributed NI tool, such as a Driver API, the System Configuration API, or MAX. System Accessible:The component is read and/or write addressable from the host without the need to physically alter the product. Clearing:Per NIST Special Publication 800-88 Revision 1, “clearing” is a logical technique to sanitize data in all User Accessible storage locations for protection against simple non-invasive data recovery techniques using the same interface available to the user; typically applied through the standard read and write commands to the storage device.Sanitization:Per NIST Special Publication 800-88 Revision 1, “sanitization” is a process to render access to “Target Data” on the media infeasible for a given level of effort. In this document, clearing is the degree of sanitization described.。
- 1、下载文档前请自行甄别文档内容的完整性,平台不提供额外的编辑、内容补充、找答案等附加服务。
- 2、"仅部分预览"的文档,不可在线预览部分如存在完整性等问题,可反馈申请退款(可完整预览的文档不适用该条件!)。
- 3、如文档侵犯您的权益,请联系客服反馈,我们会尽快为您处理(人工客服工作时间:9:00-18:30)。
Downloaded from by on April 14, 2008
Circulation Research
An Otticiui Journal of the American Heart Association
DECEMBER VOL. 39
The online version of this article, along with updated information and services, is located on the World Wide Web at:
ቤተ መጻሕፍቲ ባይዱ
Subscriptions: Information about subscribing to Circulation Research is online at /subscriptions/ Permissions: Permissions & Rights Desk, Lippincott Williams & Wilkins, a division of Wolters Kluwer Health, 351 West Camden Street, Baltimore, MD 21202-2436. Phone: 410-528-4050. Fax: 410-528-8550. E-mail: journalpermissions@ Reprints: Information about reprints can be found online at /reprints
1976 NO. 6
Automatic Activity in Depolarized Guinea Pig Ventricular Myocardium
Characteristics and Mechanisms
SUNAO IMANISHI, M . D . , AND BORYS SURAWICZ, M . D .
AUTOMATICITY of ventricular myocardial fibers has been observed after supervision with K+-free and Ca2+free solution,1 exposure to Ba2+ salts,1' 3 excessive mechanical stretch,4 and several other interventions (for references, see Antoni5 and Cranefield,6 p. 213). Common to all these interventions is the depolarization to levels of membrane potential at which the rapid inward sodium current is partly or completely inactivated. Automatic activity of ventricular myocardium also has been induced by depolarizing direct current pulses of several seconds' duration applied across a single sucrose gap in sodiumfree7 and regular Tyrode's solution .e- • Recently Katzung8'9 showed that Ca and Na ions influence automaticity of papillary muscles from guinea pigs and cats and dog trabeculae after depolarizations to membrane potentials less negative than —60 mV. Imanishi10 used the partition chamber method of Kamiyama and Matsuda" to study the effect of depolarizing currents on quiescent dog Purkinje fibers. In this preparation depolarization induced CaI+-sensitive oscillations
Circulation Research is published by the American Heart Association. 7272 Greenville Avenue, Dallas, TX 72514 Copyright © 1976 American Heart Association. All rights reserved. Print ISSN: 0009-7330. Online ISSN: 1524-4571
Automatic activity in depolarized guinea pig ventricular myocardium. Characteristics and mechanisms S Imanishi and B Surawicz Circ. Res. 1976;39;751-759
SUMMARY Membrane potential was changed uniformly in segments, 0.7-1.0 mm long, of guinea pig papillary muscles exdsed from the right ventricle by using extracellular polarizing current pulses applied across two electrically insulated compartments. Rhythmic automatic depolarizations (RAD) occurred in 90% of preparations superfused with Tyrode's solution at maximum dlastolic membrane potentials ranging from - 3 5 . 2 ± 7.5 (threshold) to +4.0 ± 9.2 mV. The average maximum dV/dt of RAD ranged from 17.1 to 18.0 V/sec within a membrane potential range of - 4 0 to +20 mV. Raising extracellular Ca'+ concentration [Ca1+]n from 1.8 to 6.8 ITIM, or application of isoproterenol (10-* g/ml) enhanced the rate of RAD, but lowering |Ca J+ ],, to 0.4 iuM or exposure to MnCl, (6 mix) abolished RAD. RAD
From the Cardiovascular Division, Department of Medicine, Univenity of Kentucky Medical Center, Lexington, Kentucky. Supported by NIHL Training Grant 203-60-7H350-A3BB6 and a grant from the Kentucky Heart Association. Dr. Imanishi is a Research Fellow of the Kentucky Heart Association. Address for reprints: Borys Surawicz, M.D., Department of Medicine, University of Kentucky Medical Center, Lexington, Kentucky 40506. Original manuscript received May 1975; accepted for publication July 15, 1976.
were enhanced by lowering extracellular K+ concentration | K + ] 0 from 5.4 to 1.5 DIM. RAD were suppressed in 40% of fibers by raising [K+]n to 15.4 raM, and hi all fibers by raising [K+]o to 40.4 HIM. This suppression was dne to increased |K + ],, and not to Kinduced depolarization because it persisted when membrane potential was held by means of a conditioning hyperpolarizing pulse at the level of control resting potential. The slope resistance increased gradually after maximum re polarization. These observations suggest that the development of RAD in depolarized myocardium is associated with a time-dependent decrease in outward current (probably K current) and with increase in the background inward current, presumably flowing through the stow channel carrying Ca or Na ions, or both.