铸铁件氮气孔产生的原因分析及特征
分析铸造过程气孔生成的原因及对策

分析铸造过程气孔生成的原因及对策铸造过程中气孔生成的原因及对策分析铸造是一种重要的金属加工方法,可用于生产各种形状的金属制品。
然而,在铸造过程中,气孔的生成是一个常见的问题,它可能会影响到铸件的质量和性能。
本文将分析铸造过程中气孔生成的原因,并提出相关的对策。
一、原因分析1. 铸造材料的问题在铸造过程中,铸造材料的纯度、含气量和化学成分会直接影响气孔的生成。
杂质和气体在熔融金属中的存在可能会形成气泡,并在凝固过程中被包裹在铸件内部。
此外,如果铸造材料中的挥发性成分含量过高,也容易导致气孔的生成。
2. 模具设计和制造的问题模具的设计和制造不当也是气孔生成的原因之一。
设计不合理的浇口和冷却系统会导致金属在流动过程中吸入空气,形成气孔。
模具的材质和表面处理也会对气孔的生成产生影响,表面粗糙度过高或使用粘结性差的涂料可能会导致铸件表面气孔的形成。
3. 浇注工艺的问题浇注工艺是影响气孔生成的关键因素之一。
浇注温度、浇注速度和浇注角度等工艺参数的控制不当可能导致金属流动不畅,气泡无法完全排出,从而形成气孔。
此外,如果铸件内部存在复杂的几何形状,也会增加气泡在凝固过程中的积累和无法排出的可能性。
二、对策措施1. 提高铸造材料的质量为了减少气孔的生成,需要选用高纯度的铸造材料,并控制好化学成分和气体含量。
可以通过加入脱气剂来减少金属中的气体含量,同时加入合适的合金元素可以改善金属的流动性和凝固性能。
2. 优化模具设计和制造合理的模具设计可以改善金属流动状态,减少气体吸入的可能性。
浇口的设计应考虑到金属的流动路径和速度,确保金属在流动过程中尽量少吸入空气。
此外,模具的材质应选用适合的材料,并进行表面处理以提高其抗粘性和耐腐蚀性能。
3. 控制好浇注工艺参数合理控制浇注温度、浇注速度和浇注角度等参数可以使金属流动顺畅,减少气泡的生成。
同时,在铸造过程中可采用自动浇注系统和真空吸气设备来排除金属中的气体。
对于复杂几何形状的铸件,可以采用分次浇注或采用喷浇工艺来减少气孔的生成。
氮气孔
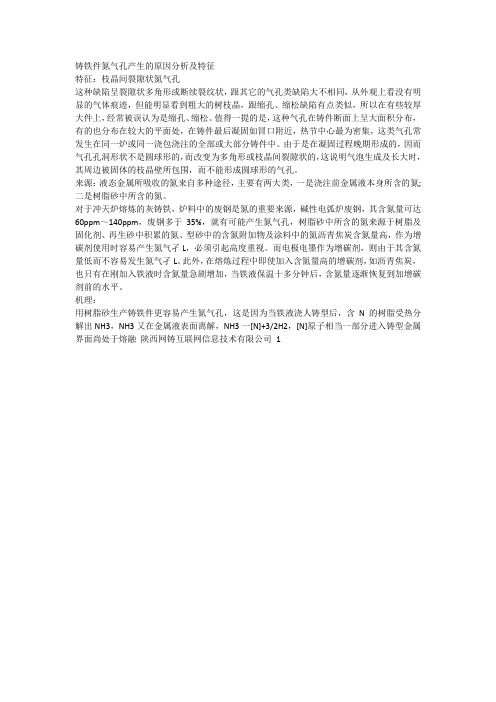
铸铁件氮气孔产生的原因分析及特征
特征:枝晶间裂隙状氮气孔
这种缺陷呈裂隙状多角形或断续裂纹状,跟其它的气孔类缺陷大不相同,从外观上看没有明显的气体痕迹,但能明显看到粗大的树枝晶,跟缩孔、缩松缺陷有点类似,所以在有些较厚大件上,经常被误认为是缩孔、缩松。
值得一提的是,这种气孔在铸件断面上呈大面积分布,有的也分布在较大的平面处,在铸件最后凝固如冒口附近,热节中心最为密集,这类气孔常发生在同一炉或同一浇包浇注的全部或大部分铸件中。
由于是在凝固过程晚期形成的,因而气孔孔洞形状不是圆球形的,而改变为多角形或枝晶间裂隙状的,这说明气泡生成及长大时,其周边被固体的枝晶壁所包围,而不能形成圆球形的气孔。
来源:液态金属所吸收的氮来自多种途径,主要有两大类,一是浇注前金属液本身所含的氮;二是树脂砂中所含的氮。
对于冲天炉熔炼的灰铸铁,炉料中的废钢是氮的重要来源,碱性电弧炉废钢,其含氮量可达60ppm~140ppm,废钢多于35%,就有可能产生氮气孔,树脂砂中所含的氮来源于树脂及固化剂、再生砂中积累的氮、型砂中的含氮附加物及涂料中的氮沥青焦炭含氮量高,作为增碳剂使用时容易产生氮气孑L,必须引起高度重视。
而电极电墨作为增碳剂,则由于其含氮量低而不容易发生氮气孑L。
此外,在熔炼过程中即使加入含氮量高的增碳剂,如沥青焦炭,也只有在刚加入铁液时含氮量急剧增加,当铁液保温十多分钟后,含氮量逐渐恢复到加增碳剂前的水平。
机理:
用树脂砂生产铸铁件更容易产生氮气孔,这是因为当铁液浇人铸型后,含N的树脂受热分解出NH3,NH3又在金属液表面离解,NH3一[N]+3/2H2,[N]原子相当一部分进入铸型金属界面尚处于熔融陕西网铸互联网信息技术有限公司1。
铸件气孔产生的原因
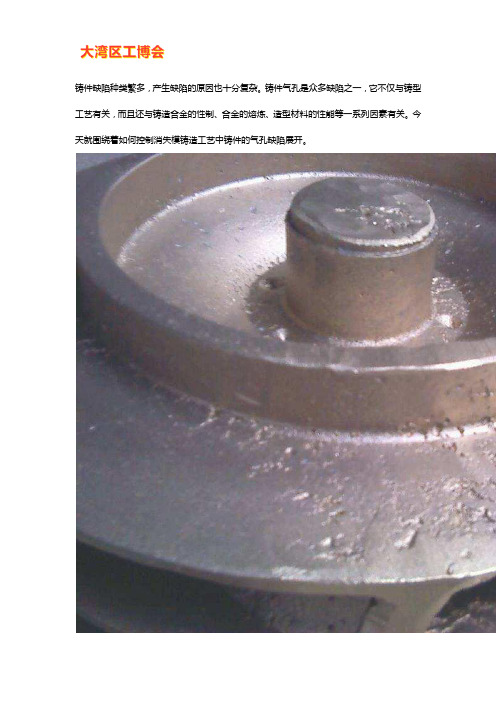
铸件缺陷种类繁多,产生缺陷的原因也十分复杂。
铸件气孔是众多缺陷之一,它不仅与铸型工艺有关,而且还与铸造合金的性制、合金的熔炼、造型材料的性能等一系列因素有关。
今天就围绕着如何控制消失模铸造工艺中铸件的气孔缺陷展开。
1、选择适宜的模型材料采用共聚泡沫模型材料,由于共聚物是拉链式分解,一次性气化程度高,液相比例小,小分子气体很容易从涂层溢出,白模密度在强度和光洁度保证的前提下尽可能小一些,减少发气总量,浇注系统采用空心直浇道并加设过滤器,对金属液进行机械挡渣、吸附梳流,使充型更平稳。
2、浇注系统及保温冒口的使用内浇道的开设要利于合金的顺利平稳快速充型,不形成死角区,在铸件的顶部设置大气压力保温冒口,集渣补缩于一体,相关部位设置随形隔砂冷铁,实现铸件的顺序凝固,把金属液内的气体、渣质及气化残留物快浮到冒口部位,减少气孔、渣孔、缩孔产生的几率。
3、提高涂料的透气性耐火骨料的粒度要适宜,采用复合粘结剂悬浮剂,配制的涂料具有高低温强度好、耐磨损、易涂刷、不开裂、排气能力强、透气性好、烧结均匀、开箱易脱落剥离,不与金属液润湿剂及化学反应,一般铸件涂刷2遍,涂层厚度2mm左右。
消失模涂料的质量管理十分关键。
在大量生产时,定期检查涂料的透气性,及时调整骨料的粒度。
由于涂料的粘结剂、悬浮剂中含有机物质,夏秋季节特别应该注意涂料的发酵酶变,合格的铸件离不开最佳的涂料,控制涂料的质量不可轻心。
4、浇注温度要适宜由于消失模的充型过程中药放热汽化泡沫,钢铁的浇注温度较砂型铸造高30-50℃。
金属液与泡沫的热作用受热浇注温度的制约,浇注温度适宜热解充分,模样的热解产物主要呈小分子气态,在负压场的作用下容易排除型腔,当浇注温度低时,模样的热解不充分,液相残留物会堵塞涂料层,热解气体排出受阻,型腔内形成反压力,充型流动性由此下降,再加上凝固速度快,液体附近的气渣来不及浮集到冒口内,生成气孔的几率增大,当然浇注温度要与冶炼的材料匹配,以避免因温度高或底而产生的其他铸造缺陷。
氮气孔_Nitrogen_Fissures
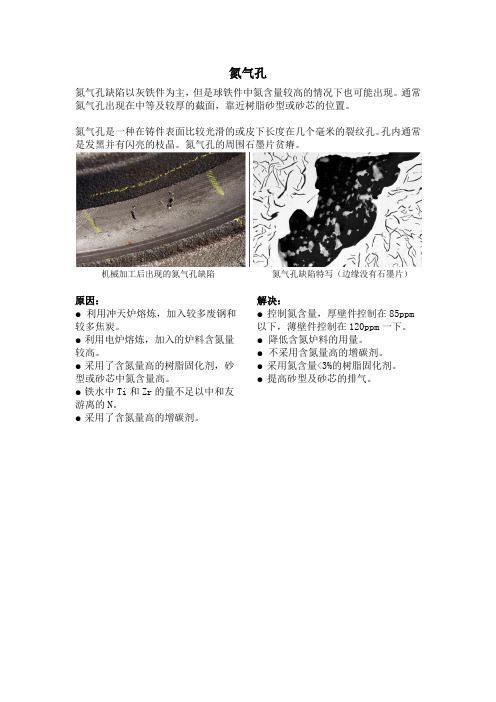
氮气孔
氮气孔缺陷以灰铁件为主,但是球铁件中氮含量较高的情况下也可能出现。
通常氮气孔出现在中等及较厚的截面,靠近树脂砂型或砂芯的位置。
氮气孔是一种在铸件表面比较光滑的或皮下长度在几个毫米的裂纹孔。
孔内通常是发黑并有闪亮的枝晶。
氮气孔的周围石墨片贫瘠。
机械加工后出现的氮气孔缺陷氮气孔缺陷特写(边缘没有石墨片)
原因:
●利用冲天炉熔炼,加入较多废钢和较多焦炭。
●利用电炉熔炼,加入的炉料含氮量较高。
●采用了含氮量高的树脂固化剂,砂型或砂芯中氮含量高。
●铁水中Ti和Zr的量不足以中和友游离的N。
●采用了含氮量高的增碳剂。
解决:
●控制氮含量,厚壁件控制在85ppm 以下,薄壁件控制在120ppm一下。
●降低含氮炉料的用量。
●不采用含氮量高的增碳剂。
●采用氮含量<3%的树脂固化剂。
●提高砂型及砂芯的排气。
铸造气孔解决方法
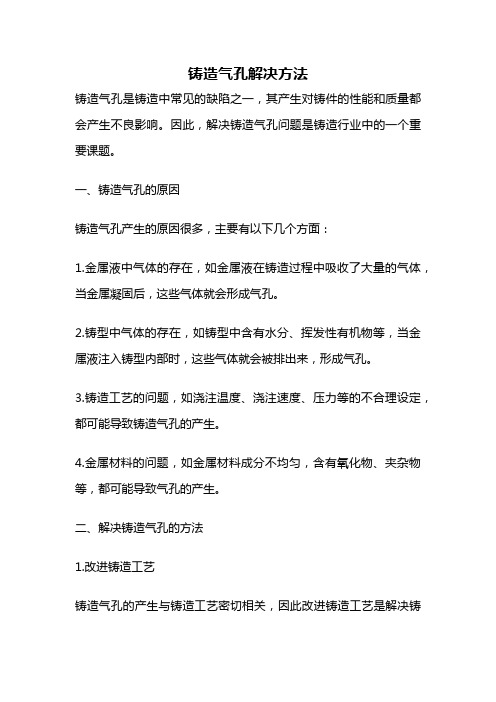
铸造气孔解决方法铸造气孔是铸造中常见的缺陷之一,其产生对铸件的性能和质量都会产生不良影响。
因此,解决铸造气孔问题是铸造行业中的一个重要课题。
一、铸造气孔的原因铸造气孔产生的原因很多,主要有以下几个方面:1.金属液中气体的存在,如金属液在铸造过程中吸收了大量的气体,当金属凝固后,这些气体就会形成气孔。
2.铸型中气体的存在,如铸型中含有水分、挥发性有机物等,当金属液注入铸型内部时,这些气体就会被排出来,形成气孔。
3.铸造工艺的问题,如浇注温度、浇注速度、压力等的不合理设定,都可能导致铸造气孔的产生。
4.金属材料的问题,如金属材料成分不均匀,含有氧化物、夹杂物等,都可能导致气孔的产生。
二、解决铸造气孔的方法1.改进铸造工艺铸造气孔的产生与铸造工艺密切相关,因此改进铸造工艺是解决铸造气孔问题的首要措施。
具体来说,可以采取以下措施:(1)提高浇注温度,减少金属液中气体的溶解度,从而减少气孔的产生。
(2)控制浇注速度和压力,使金属液充分填充铸型,减少气孔的产生。
(3)改进浇注系统,减少金属液的冲击和喷溅,从而减少气孔的产生。
2.改进金属材料金属材料的成分和质量对铸造气孔的产生也有很大的影响。
因此,改进金属材料也是解决铸造气孔问题的重要措施。
具体来说,可以采取以下措施:(1)改进金属材料的制备工艺,减少夹杂物、氧化物等的产生。
(2)优化金属材料的成分和配比,使其成分均匀,减少气孔的产生。
3.改进铸型和模具铸型和模具的质量对铸造气孔的产生也有很大的影响。
因此,改进铸型和模具也是解决铸造气孔问题的重要措施。
具体来说,可以采取以下措施:(1)优化铸型设计,使其能够充分填充金属液,减少气孔的产生。
(2)加强铸型的密封性,减少铸型中气体的存在,从而减少气孔的产生。
(3)采用高质量的模具材料,减少模具中气体的存在,从而减少气孔的产生。
4.采用热处理技术热处理技术可以改变铸件中的组织结构,从而减少气孔的产生。
具体来说,可以采用以下热处理技术:(1)固溶处理:将铸件加热到一定温度,使其中的溶质均匀分布,从而减少气孔的产生。
压铸件气孔产生的原因

压铸件气孔产生的原因产生气孔的原因有以下几点:一、氢气残留。
原材料里面还有氢气,坩埚及环境还有湿气,导致气体加热产生氢气夹裹在原材料里面,容易产生针状气孔。
二、压射室充满度不高。
压射室充满度不高会导致压射室内含空间过大,铝汤在压射前,出现回流撞击,产生涡流。
气泡是模具温度及铝温太高,容易产生气泡。
氢气,压射缸卷起,流道卷起,型腔内压力卷起,水蒸气产生气孔这些都是模具气孔的主因。
产生原因:1、金属液在压射室充满度过低(控制在45%~70%),易产生卷气,初压射速度过高。
2、模具浇注系统不合理,排气不良。
3、熔炼温度过高,含气量高,熔液未除气。
4、模具温度过高,留模时间不够,金属凝固时间不足,强度不够过早开模,受压气体膨胀起来。
5、脱模剂、注射头油用量过多。
6、喷涂后吹气时间过短,模具表面水未吹干。
解决压铸件气孔的办法:先分析出师什么原因导致的气孔,再来取相应的措施。
(1)干燥、干净的合金料。
(2)控制熔炼温度,避免过热,进行除气处理。
(3)合理选择压铸工艺参数,特别是压射速度。
调整高速切换起点。
(4)顺利填充有利于型腔气体排出,直浇道和横浇道有足够的长度(>50mm),有利于合金液平稳流动和气体有机会排出。
可改变浇口厚度、浇口方向、在形成气孔的位置设置溢流槽、排气槽。
溢流品截面积总和不能小于内浇口截面积总和的60%,否则排渣效果差。
(5)选择性能好的涂料及控制喷涂量。
预防措施:1、调整压铸工艺参数、压射速度和高压射速度的切换点。
2、修改模具浇道,增设溢流槽、排气槽。
3、降低缺陷区域模温,从而降低气体的压力作用。
4、调整熔炼工艺、5、延长留模时间,调整喷涂后吹气时间。
6、调整脱模剂、压射油用量。
气孔是压铸件中常见多发的缺陷之一。
气孔呈圆形或扁平椭圆形气泡状,直径为1mm至20mm不等,内表面光滑,覆有一层氧化层,通常分散在加工表面下。
一、气孔缺陷的成因01 金属杂质过多原材料或回收料中含有较多的氧化物和其他杂质,一些杂质(如氧化物、氢化物、油脂)在熔炼过程中会释放气体。
检测铸件气孔的方法

检测铸件气孔的方法一、引言在我国的铸造行业中,铸件气孔是一个常见的问题。
气孔的存在不仅影响铸件的外观质量,还会对其使用性能产生严重影响。
为了确保铸件的质量,对铸件气孔的检测至关重要。
本文将对铸件气孔的成因、危害以及常用的检测方法进行介绍,以帮助大家更好地了解和解决这一问题。
二、铸件气孔的成因及危害铸件气孔主要是由于铸造过程中,金属液与型砂、芯砂等固体粒子发生反应产生的气体在凝固过程中无法及时排出而在铸件内部形成的。
铸件气孔的存在会使铸件的强度、硬度、耐磨性等性能降低,同时还容易导致铸件在使用过程中出现裂纹、变形等现象。
三、检测铸件气孔的常用方法1.肉眼观察:通过肉眼直接观察铸件表面和断面,观察是否存在气孔。
这种方法适用于较大型的铸件,但对于微小气孔和内部气孔难以发现。
2.低倍显微镜检测:使用低倍显微镜观察铸件的表面和断面,可以较准确地检测到微小气孔。
但低倍显微镜检测仍然难以发现内部气孔。
3.超声波检测:利用超声波在铸件中的传播特性,检测铸件内部是否存在气孔。
这种方法无损检测,适用于各种类型的铸件,但对于形状复杂、厚度变化的铸件检测效果有所降低。
4.射线检测:通过射线对铸件进行透射,观察射线底片上是否存在气孔。
这种方法适用于厚壁、大型铸件的检测,但射线对人体有一定危害,需采取防护措施。
5.渗透检测:将渗透剂涂抹在铸件表面,通过检测气孔处渗透剂的扩散情况来判断气孔的存在。
这种方法适用于表面光滑、无油污的铸件,但对于内部气孔和微小气孔检测效果较差。
四、各种检测方法的优缺点对比1.肉眼观察和低倍显微镜检测:优点是操作简便、成本低,适用于大型铸件的表面气孔检测。
缺点是难以发现微小气孔和内部气孔。
2.超声波检测:优点是无需破坏铸件,可以检测到内部气孔。
缺点是对形状复杂、厚度变化的铸件检测效果有所降低,且对微小气孔检测效果较差。
3.射线检测:优点是适用于厚壁、大型铸件的检测,检测精度较高。
缺点是射线对人体有一定危害,需采取防护措施。
铸铁件N2孔的原因分析及防止
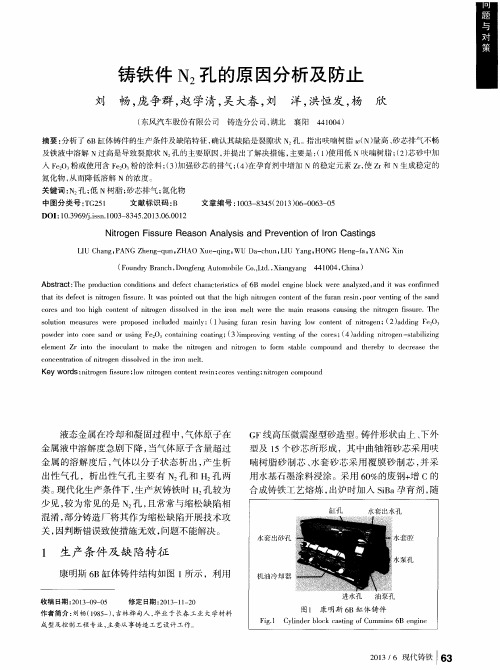
s o l u t i o n n l e a s u r e s w e r e p r o p o s e d i n c l u d e d ma i n l y :( 1 ) u s i n g f u r a n r e s i n h a v i n g l o w c o n t e n t o f n i t r o g e n: ( 2) a d d i n g F e 2 0 3
e l e me n t Z r i n t o t h e i n o e u l a n t t o ma k e t h e n i t r o g e n a n d n i t r o g e n t o f o r m s t a b l e c o mp o u n d a n d t h e r e b y t o d e c r e a s e t h e
铸铁件 N 2 孑 L 的原 因分析及 防止
刘 畅 , 庞争群 , 赵 学清 , 吴大春 , 刘 洋, 洪恒发 , 杨 欣
( 东风汽车股份有限公司 铸造分公司 , 湖北 襄阳 4 4 1 0 0 4 )
摘要 : 分析 了 6 B缸体铸件的生产 条件及缺 陷特征 , 确认其 缺陷是裂 隙状 N 孔。 指 出呋 喃树脂 ( N) 量高 、 砂芯排气不畅 及铁液 中溶解 N过高是导致裂隙状 N 孔的主要原 因 , 并提出了解决措施 , 主要是 : ( 1 ) 使用低 N呋喃树脂 ; ( 2 ) 芯砂 中加
L 1 U Ch a n g , P ANG Z h e n g — q u n, Z HAO Xu e - q i n g , WU Da - e h u n, L I U Ya n g , HONG He n g — f a , YA NG Xi n
铸件气孔案例分析报告

铸件气孔案例分析报告1. 引言铸造是一种常见的金属加工方法,用于生产各种复杂形状的金属零件。
然而,在铸造过程中,气体存在的问题是一个常见的挑战。
气孔是铸件中最常见的缺陷之一,它们对铸件的力学性能和表面质量都会造成负面影响。
因此,对铸件气孔现象进行分析,并采取相应的措施来减少气孔产生,是提高铸件质量和性能的关键。
2. 气孔的成因气孔的形成是由于铸造过程中存在的气体无法完全逸出,而被困在铸件内部形成的。
气体在金属液态状态下溶解度较低,在凝固过程中会析出。
以下是几种常见的气孔成因:a) 液态金属中溶解的气体:液态金属中可溶解的气体,在固化过程中会分解,产生气体泡沫形成气孔。
b) 铸型气体:在铸造过程中,砂型或其他铸型材料中的挥发物会被加热并释放出气体,形成气孔。
c) 内部形成的气体:在凝固过程中,疏松的金属结构或其他元素的分解反应会生成气体,形成气孔。
3. 气孔的影响气孔对铸件性能和表面质量产生以下负面影响:a) 降低强度和韧性:气孔导致铸件内部存在弱点和孔洞,会降低铸件的强度和韧性。
b) 引起裂纹和漏洞:气孔是裂纹和漏洞形成的起点,它们可能在应力作用下扩展,导致铸件的损坏和失效。
c) 影响铸件外观:气孔会在铸件表面形成小孔或凹陷,影响铸件的外观质量,降低其市场竞争力。
4. 案例分析以下是一个关于铸件气孔案例的分析,以展示如何识别和解决气孔问题的过程:案例背景:一家汽车制造公司的铝合金发动机块铸件出现了气孔问题,导致部分铸件在测试中出现弯曲和断裂现象,严重影响了发动机的可靠性。
分析步骤:a) 气孔检测:使用X射线或CT扫描等非破坏性检测方法,对铸件进行全面的检测,确定气孔的位置和数量。
b) 气孔成因分析:通过对铸造工艺参数、金属合金成分和砂型材料等进行分析,确定气孔产生的可能原因。
c) 工艺优化:针对气孔成因,通过调整铸造温度、压力和保温时间等工艺参数,优化铸造过程,减少气孔的形成。
d) 砂型改进:对砂型材料进行优化,选择低挥发性和低含气量的材料,减少砂型气体的释放。
氮气孔的产生及预防
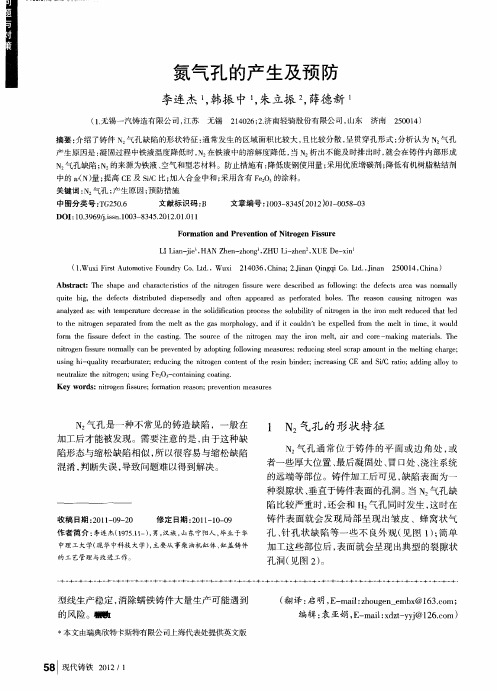
( 译 : 明 , — alzo gn e x@1 3.o ; 翻 启 E m i hu e mb : 6 cm
—
编辑 : 亚娟 , - i:dtyj 2 . r) 袁 E ma xz y@16cn l — o
5 代 铁 21/ 8 现 铸 02 1 l
2 N 气孔 产 生 的原 因 ,
一 一
() a 缺陷部位 的金相组织 () b 正常区域的金相组织
废 钢 ; 一方 面 , 另 可通 过增 碳剂 调 整铁 液成 分 , 以 相 对 于缩 松 而 言 , , 通 常 发 生 的 区域 面 N孔
达 到 降低 生 产成本 及 提高铸 件材 料 的 目的。 由 但
积 比较 大 , 而且 比较 分散 , 陷呈贯 穿 孔 , 铸 件 缺 对
于废钢 中的奥氏体相可溶解和容纳不少 N, ,同时 低s 条件有利于 N 的溶解 , : 导致铁液中 N 含量 : 显 著上 升 。增 碳剂 中也 含有 N, 质增 碳 剂 中的 劣 () N 量更高。所以, 感应 电炉熔炼大比例使用废 钢和增碳剂 , 使得铁液中的 N 量显著提升 , ( ) M
Ab t a t h h p n h r ce it s o h i o e s u e w r e ci e s fl w n :t e d f cs a e a o mal sr c :T e s a e a d c a a t s c ft e n t g n f s r e e d s r d a ol i g h e e t r a w s n r l r i r i b o y q i i,t e ee t it b t d d s e s d y n f n a p a e s e fr t d o e .T e r a o a s g i o e s u t b g h d f cs sr u e i r e l a d o e p e r d a p r a e h l s h e s n c u i nt g n wa e d i p t o n r
关于精密铸造气孔的形成原因和防止措施

关于精密铸造气孔的形成原因和防止措施
作者:admin 发布时间:2012-12-28 11:03:14 点击次数: 45
气孔是精密铸造上存在着光滑孔眼缺陷。
气孔往往出现在铸件个别部位,以单个或几个尺寸较大的孔存在,又称集中气孔。
孔眼有时呈氧化颜色。
通常是在加工后才会发现。
1、形成原因:这种气孔主要是因为精密铸造型壳焙烧不充分,浇注时型壳产生大量气体侵入金属液中;或型壳透气性太差,型腔中气体难于排出,进入金属液中;或浇注时卷入气体未能排出金属液而造成的铸件气孔。
属本书第四章介绍的侵入性气孔或裹携气孔。
2、防止措施
1)对复杂的薄壁铸件,为提高精密铸造型壳透气性,在可能情况下,在最高处可设排气孔。
-)合理设置浇注系统,防止浇注卷气,并有利于型腔中气体排出。
2)适当提高浇注温度,尽量降低浇包嘴至浇口杯距离,降低浇注速度,使金属液能平稳充型,防止卷入气体,使型腔中及液体金属中气体能顺利排出。
3)脱蜡时应将模料排除干净,残余模料应尽量少。
4)型壳焙烧要充分,应有足够高的温度;硅溶胶和硅酸乙酯型壳950~1100摄氏度,水玻璃型壳850~900摄氏度;保温时间大于&,,以保证精密铸造型壳焙烧透,发气物质充分排除。
焙烧完全的型壳为白色或淡灰色,不应有黑斑。
铸件氮气孔和气孔的区别

铸件氮气孔和气孔的区别摘要:一、引言二、铸件氮气孔的定义与特点1.氮气孔的形成原因2.氮气孔对铸件质量的影响三、气孔的定义与特点1.气孔的形成原因2.气孔对铸件质量的影响四、氮气孔与气孔的区别1.成因上的区别2.形态上的区别3.对铸件质量影响上的区别五、如何预防和控制氮气孔和气孔的出现1.优化铸造工艺2.选用合适的熔炼设备和方法3.控制氮气和气体含量4.提高铸件表面质量六、结论正文:一、引言在铸造行业中,氮气孔和气孔是常见的缺陷,它们对铸件质量产生严重影响。
为了提高铸件质量,减少缺陷,我们需要深入了解氮气孔和气孔的区别,以及如何预防和控制它们的出现。
二、铸件氮气孔的定义与特点1.氮气孔的形成原因氮气孔主要是由于熔融金属中氮含量过高,在凝固过程中氮气析出并在铸件中形成孔洞。
氮来源于金属原材料、熔炼设备、炉气及保护气体等。
2.氮气孔对铸件质量的影响氮气孔的存在会导致铸件内部产生缺陷,降低铸件的力学性能和耐磨性,严重时会影响铸件的使用寿命。
三、气孔的定义与特点1.气孔的形成原因气孔主要是由于熔融金属在凝固过程中,气体不能及时排出,从而在铸件中形成孔洞。
气孔的成因包括金属原材料中的气体、熔炼过程中的气体、浇注系统和铸型材料等。
2.气孔对铸件质量的影响气孔同样会导致铸件内部产生缺陷,降低铸件的力学性能和耐磨性。
此外,气孔还会影响铸件的加工性能,增加后续加工的难度。
四、氮气孔与气孔的区别1.成因上的区别氮气孔的形成主要与氮含量过高和熔炼过程中氮气的析出有关,而气孔的形成则与熔融金属中气体含量过高和凝固过程中气体的排出不畅有关。
2.形态上的区别氮气孔一般呈现圆孔状,孔洞较干净,多分布在铸件的内部;气孔则呈现不规则形状,孔洞内可能有夹杂物,分布较为分散。
3.对铸件质量影响上的区别氮气孔和气孔都对铸件质量产生负面影响,但氮气孔对铸件的力学性能和耐磨性的影响更为严重。
五、如何预防和控制氮气孔和气孔的出现1.优化铸造工艺,降低氮气和气体含量。
树脂砂铸铁件氮气孔缺陷的产生原因及对策
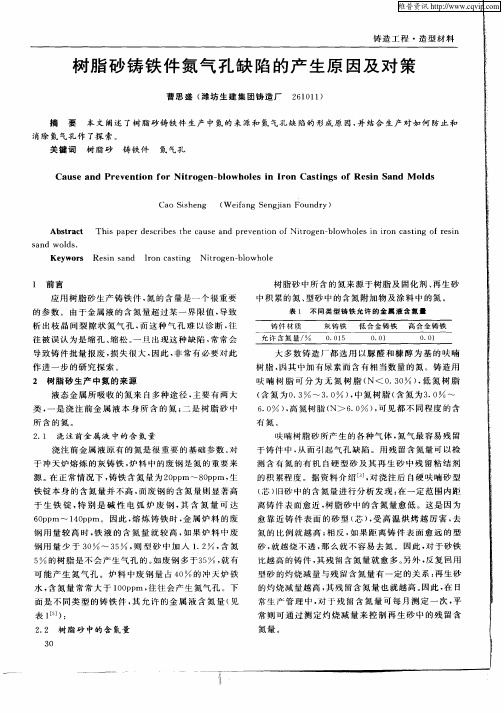
采用 H。 P O 作 自硬 树 脂砂 的催 化剂 时 , 由于 形成
( NH ) 。 P O 会 增 加 残 留含 氮 量 , 因 而 规 定 磷 酸 盐 的
但 是在 生 产线 上 生产 车 体 铸件 时也 发现 类 似缺 陷 , 而 且 是 成批 的 , 发生部位多在浇注位置的底面 , 形 状 如
6 . 0 ) , 高 氮树 脂 ( N> 6 . 0 ) , 可 见 都 不 同程 度 的 含
有氮 。 呋 喃树 脂砂 所 产 生 的各 种气 体 , 氮 气 最 容易 残 留 于铸件中, 从 而 引 起气 孔 缺 陷 。用 残 留 含氮 量 可 以检 测 含 有 氮 的有 机 自硬 型 砂 及 其 再 生 砂 中残 留粘 结 剂
Ke y wor s Re s i n s an d I r o n c a s t i ng Ni t r o ge n — bl owh ol e
1 前 言
树 脂 砂 中所 含 的 氮来 源 于树 脂 及 固化 剂 、 再 生砂 中积 累 的氮 、 型 砂 中 的含 氮 附加 物 及涂 料 中的氮 。
的积 累程度 。据 资料 介 绍 _ 3 ] , 对浇 注 后 自硬 呋 喃砂 型
( 芯) 旧砂 中 的含 氮量 进 行 分析 发 现 : 在 一定 范 围内距
离铸 件 表 面 愈近 , 树 脂 砂 中 的含 氮量 愈 低 。这 是 因 为 愈 靠 近 铸 件 表 面 的砂 型 ( 芯) , 受高温烘烤越厉害 , 去 氮 的 比例 就 越 高 ; 相反 , 如果 距 离 铸 件 表 面 愈 远 的 型
浇 注 前金 属 液 原 有 的氮 是 很重 要 的 基础 参 数 。 对
于 冲天 炉熔 炼 的灰 铸 铁 , 炉 料 中的 废钢 是氮 的 重要 来 源 。在正 常 情 况 下 , 铸铁含氮量为2 0 p p m ̄8 0 p p m, 生 铁 锭本 身 的含 氮量 并 不 高 , 而废 钢 的 含 氮量 则 显 著 高 于 生铁 锭 , 特别 是碱 性 电弧 炉废 钢 , 其 含 氮 量 可 达
铸铁形成氮气孔的原因

铸铁形成氮气孔的原因
铸铁是一种基础材料,被广泛应用于机械、汽车制造、航空航天和建
筑等领域。
然而,铸铁在铸造过程中可能会出现氮气孔,这对其力学
性能和表面质量产生不利影响。
那么,铸铁形成氮气孔的原因是什么呢?
铸铁形成氮气孔的原因可以归结为两个方面:一是原料中杂质的存在;二是铸造过程中的操作不当。
在铸造过程中,氮气的来源主要有两种:空气和铸造物表面的氮化物。
其中,铸造物表面的氮化物主要来源于
原料和沙子中的氮和铝,这些杂质进入到铸件中后,在液态金属的凝
固过程中会形成氮气孔。
除了杂质的影响,铸造过程中的操作不当也会导致氮气孔的产生。
在
铸造过程中,如果液态金属的流动不顺畅,就会在铸件中形成气孔。
另外,在浇注过程中,如果液态金属与空气接触过多,也容易导致气
孔的产生。
此外,铸造过程中的钢渣、沙砾等杂质也可能会在铸件中
形成气孔。
为了避免铸铁中出现氮气孔,有以下几点建议:
首先,应该选择高纯度的原材料,并注意杂质的去除和净化工作。
其次,要提高操作水平和技术水平,确保液态金属的流动顺畅,并加
强对铸造过程中氧化和挥发的控制。
此外,在铸造过程中应注意控制
浇注速度和浇注角度,以免产生气孔。
最后,要加强铸造过程的监控和检测,及时发现并处理存在的问题,
确保铸件的质量和性能。
总之,铸铁形成氮气孔的原因是多方面的,需要综合考虑材料、制造
工艺和操作等因素。
通过选择高质量的原材料、加强技术培训和管理,加强铸造过程的控制和检测以及及时处理存在的问题,我们可以有效
避免铸铁中氮气孔的产生,提高产品的质量和性能。
压铸件内部气孔产生的原因

压铸件内部气孔产生的原因
压铸件内部气孔的产生原因可以有多种,下面列举了几种常见的原因:
1. 模具设计不合理:模具的进气和排气系统设计不合理,导致在铸件充型过程中无法有效地排出空气,从而形成气孔。
2. 原材料含气量高:铸件采用的原材料中含气量较高,当材料在充型过程中受到高压挤压时,气体会被压入铸件内部形成气孔。
3. 润滑剂残留:在模具内涂抹润滑剂时,如果残留过多或没有合适地分布均匀,会在铸件内形成气孔。
4. 入砂速度过快:当铸模进沙速度过快时,砂芯内的空气没有足够时间流出,造成铸件内部气孔。
5. 砂芯设计不合理:砂芯的结构设计不合理,或者砂芯制作过程中存在缺陷,会导致充型过程中无法排出空气,形成气孔。
6. 炉前处理不当:在熔化和浇铸过程中未能有效去除熔融金属中的杂质和气体,导致铸件内产生气孔。
这些都是可能导致压铸件内部气孔产生的常见原因,通过优化设计、改进工艺和加强质量管理,可以减少气孔的产生。
铸件气孔形成的原因及解决的措施

铸件气孔形成的原因及解决的措施在工厂的生产实践中,人们对气孔的叫法不一样。
有的叫气眼、气泡、气窝,丛生气孔,划为一体统称为“气孔”。
气孔是铸件最常见的缺陷之一。
在铸件废品中,气孔缺陷占很大比例,特别是在湿模砂铸造生产中,此类缺陷更为常见,有时会引起成批报废。
球墨铸铁更为严重。
气孔是在铸件成型过程中形成的,形成的原因比较复杂,有物理作用,也有化学作用,有时还是两者综合作用的产物。
有些气孔的形成机理尚无统一认识,因为其形成的原因可能是多方面的。
各类合金铸件,产生气孔缺陷有其共性,但又都是在特定条件下生成的,因此又都具有特殊性。
所以要从共性中分析产生气孔的一般规律,也要研究特性中的特有规律,以便采取有效的针对性措施,防止气孔缺陷的产生。
一、气孔的特征气孔大部分产生在铸件的内表面或内部、砂芯面以及靠近芯撑的地方。
形状有圆形的、长方形的以及不规则形状,直径有大的、小的也有似针状丛生孔形。
气孔通常具有干净而光滑的内孔面,有时被一层氧化皮所覆盖。
光滑的孔内颜色一般是白色,或带有一层暗蓝色,有的气孔内壁还有一个或几个小铁豆豆,常把这种气孔称作“铁豆气孔”。
距铸件表面很近的气孔,又叫“皮下气孔”,往往通过热处理、清滚或者机械加工后才被发现。
还有一种常见的气孔,叫做“气缩孔”,是气体和铸件凝固时的收缩而共同促使其产生的,形状又有其特殊性。
铸钢和高牌号铸铁都常出这种名称的缺陷,但形成的机理有所差异。
气孔和缩孔是可以区别开的,一般说来气孔是圆形或梨形的孔洞,内壁光滑。
而不像缩孔那样内表面比较粗糙。
二、气体的来源各类铸造合金在熔炼及成型过程中,总要和气体相接触的,气体就会进入并以各种形式存在于合金中,气体来源是多方面的,归纳起来,主要来自以下几个方面:1、原材料带进的。
各种铁类、铁合金、燃料、熔剂等,自身就含有气体,有的带有雨雪潮湿,有的锈蚀,有的带有浊污,在熔炼过程中都有可能产生气体,其中一部分就会滞留在合金液中。
有人提出:炉料上带的雨水、雪湿、浊污随炉料进入炉内,在炉料还是固态仅发红时,它们就已蒸发或烧掉,怎么会留存在铁水里呢?在资料里,用语言详细解释的不多,但在实践中,只要炉料(生铁、废钢、回炉料)受雨雪淋湿,湿着入炉,铁水一定会氧化,这确是事实。
氮气孔的产生及预防
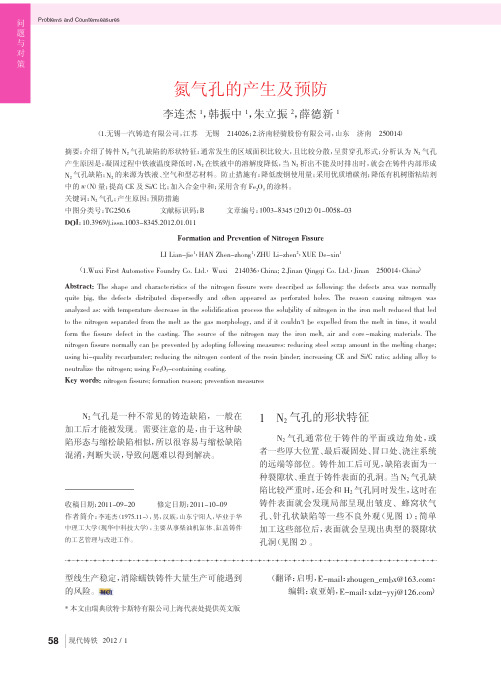
200 μm
200 μm
(a)缺陷部位的金相组织 (b)正常区域的金相组织
目前,随着国内树脂砂造型制芯技术的普 及、废钢在炉料配比中的比重不断加大以及增碳 剂使用的普及与推广,N2 气孔发生的概率大大增 加。因此,如何正确地判断、了解 N2 气孔产生的 原因及防止措施是解决 N2 气孔问题的关键。
比也可以降低 N2 孔发生的概率。这同时也解释 了为什么 N2 孔多发生在灰铸铁中,特别是高牌 号灰铸铁中。
相对于缩松而言,N2 孔通常发生的区域面 积比较大,而且比较分散,缺陷呈贯穿孔,对铸件 的密封性及性能影响很大;而缩松缺陷基本位于 铸件热节的中心位置,相对集中,以局部独立热 节为主,缩松区域集中连续。
从缺陷部位的金相来看,N2 气孔缺陷的边 缘有脱 C 现象,而且铁素体量增加(见图 3a);而 正常区域的珠光体量则比较高(见图 3b)。
图 3 铸件金相组织 Fig.3 Microstructure of area with defec(t a)and
without defec(t b)
Problems and Countermeasures 问 题 与 对 策
2 N2 气孔产生的原因
铁液中 N 的溶解量随着温度升高而增加,随 温度下降而减少。气体在铁液中的溶解是一个可 逆过程:温度降低时,溶解的气体处于过饱和状 态,气体能向铁液表面扩散而脱离吸附状态。所 以凝固过程中,铁液温度降低,为 N2 析出提供了 动力,当 N2 析出并不能及时排出时,就会在铸件 内部形成 N2 孔缺陷。
铸件气孔分析及解决措施的建议
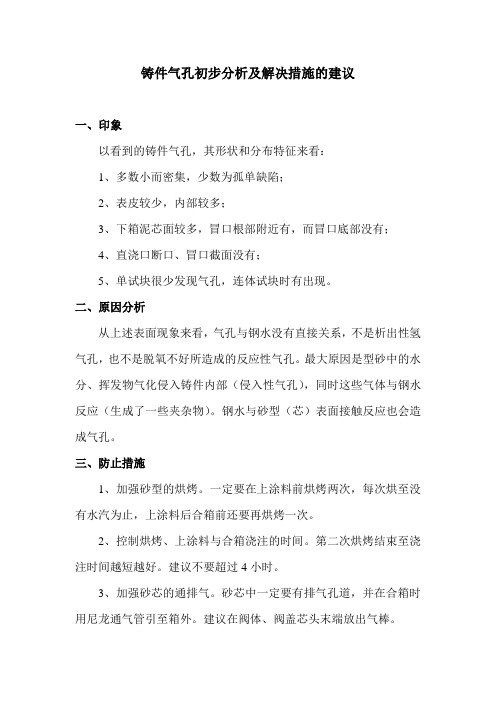
铸件气孔初步分析及解决措施的建议一、印象以看到的铸件气孔,其形状和分布特征来看:1、多数小而密集,少数为孤单缺陷;2、表皮较少,内部较多;3、下箱泥芯面较多,冒口根部附近有,而冒口底部没有;4、直浇口断口、冒口截面没有;5、单试块很少发现气孔,连体试块时有出现。
二、原因分析从上述表面现象来看,气孔与钢水没有直接关系,不是析出性氢气孔,也不是脱氧不好所造成的反应性气孔。
最大原因是型砂中的水分、挥发物气化侵入铸件内部(侵入性气孔),同时这些气体与钢水反应(生成了一些夹杂物)。
钢水与砂型(芯)表面接触反应也会造成气孔。
三、防止措施1、加强砂型的烘烤。
一定要在上涂料前烘烤两次,每次烘至没有水汽为止,上涂料后合箱前还要再烘烤一次。
2、控制烘烤、上涂料与合箱浇注的时间。
第二次烘烤结束至浇注时间越短越好。
建议不要超过4小时。
3、加强砂芯的通排气。
砂芯中一定要有排气孔道,并在合箱时用尼龙通气管引至箱外。
建议在阀体、阀盖芯头末端放出气棒。
4、浇注坑内潮湿的砂要清理掉,换成破碎机清除出来的陶口管碎屑。
5、改变浇口位置,如自封密式闸阀阀体中通道端有气孔在此处增加底注浇口。
6、树脂固化剂厂家的对比试验,某一时期固定用一家厂的树脂、固化剂,统计对比出现气孔的概率。
同一厂家的产品也要统计出现气孔的概率,看哪一家的产品好。
7、合金烘烤容易造成气孔的镍板、钼铁、金属铬等合金材料要脱氧,容易造成气孔的废钢,如不锈钢压块料要烘烤。
8、熔炼时不能用潮湿的造渣材料,吸了水的石灰一定不要用,熔炼后期加大渣量,减少功率,防止驼峰致使钢水外露吸气。
9、如有可能,弹性闸板砂芯试用水玻璃有机酯。
这种砂与碱酚醛砂不冲突,可以同时回用。
1.。
铸件,气孔,原因

铸件,气孔,原因导致铸件出现气孔的原因有哪些气孔是由于砂型(砂芯)的透气性不良,浇注时产生的大量气体不能及时排出,而在铸件内产生的孔洞。
气孔不仅减少铸件的有效截面积,且使局部造成应力集中,成为零件断裂的裂纹源,尤其是形状不规则的气孔,如裂纹状气孔和尖角形气孔,不仅增加缺口的敏感性,使金属强度下降,而且降低零件的疲劳强度。
气孔通常分为析出性气孔、反应性气孔和侵入性气孔。
1、析出性气孔。
金属液在冷却和凝固的过程中,因气体溶解度下降,析出的气体来不及排除,铸件由此而产生的气孔,称为析出性气孔。
这类气孔的特征是:在大型铸件截面上呈大面积分布,而靠近冒口、热节等温度较高区域则分布较密集。
通常金属含气量较多时,气孔形状呈裂纹状;含气量较多时,气孔较大,呈圆球状。
常发生在同一炉或同一浇包浇注的一批铸件中。
产生析出性气孔的气体,主要是氢气,其次是氮气。
铝合金最常出现析出性气孔,其次是铸钢件,铸铁件有时也会出现。
影响析出性气孔形成的因素有:1)、金属液原始含气量。
金属液原始含气量越高,气孔越易形成。
2)、冷却速度。
铸件冷却速度越快,气孔越不易形成。
3)、合金成分。
合金液态收缩大、结晶温度范围大的合金,则容易产生气孔或气缩孔。
4)、气体性质。
气体的扩散速度越快,气孔越不易形成。
2、反应性气孔。
金属液与铸型之间或在金属液内部发生化学反应产生的气体来不及排出,所产生的气孔,称为反应性气孔。
导致铸件产生反应性气孔的因素有:1)铸型水分含量过高及透气性太低;2)金属液原始气体含量高;3)合金中含有易氧化成分,如铁液中含有AL、Mg及稀土元素,钢液中含有Cr、Ca,铜液中含AL、Mn,Zn等;4)熔点较高的合金铸件(如铸钢件,铸铁件及铜合金铸件)中易出现反应性气孔。
3、侵入性气孔。
铸型在金属液的热作用下所产生的气体,侵入金属液后造成的气孔,称为侵入性气孔。
它的特征是气孔的数量较少,尺寸较大,孔壁光滑,表面有光泽或轻微的氧化色,形状多成椭圆形或梨形,一般位于铸件浇注位置的中上部或上部。
铸件气孔 -回复
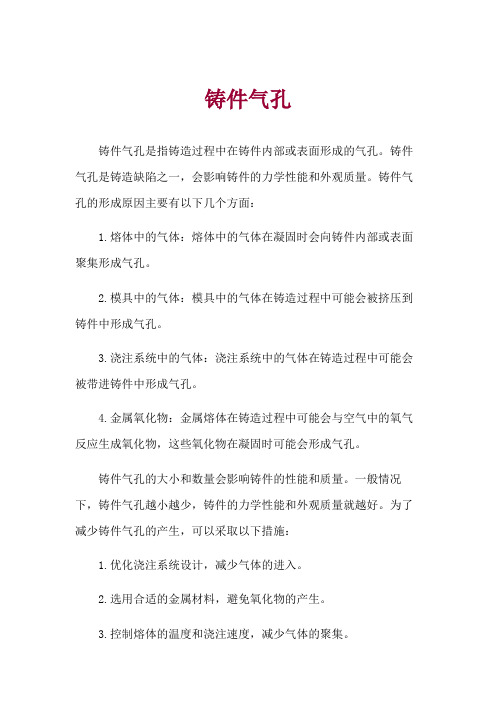
铸件气孔
铸件气孔是指铸造过程中在铸件内部或表面形成的气孔。
铸件气孔是铸造缺陷之一,会影响铸件的力学性能和外观质量。
铸件气孔的形成原因主要有以下几个方面:
1.熔体中的气体:熔体中的气体在凝固时会向铸件内部或表面聚集形成气孔。
2.模具中的气体:模具中的气体在铸造过程中可能会被挤压到铸件中形成气孔。
3.浇注系统中的气体:浇注系统中的气体在铸造过程中可能会被带进铸件中形成气孔。
4.金属氧化物:金属熔体在铸造过程中可能会与空气中的氧气反应生成氧化物,这些氧化物在凝固时可能会形成气孔。
铸件气孔的大小和数量会影响铸件的性能和质量。
一般情况下,铸件气孔越小越少,铸件的力学性能和外观质量就越好。
为了减少铸件气孔的产生,可以采取以下措施:
1.优化浇注系统设计,减少气体的进入。
2.选用合适的金属材料,避免氧化物的产生。
3.控制熔体的温度和浇注速度,减少气体的聚集。
4.采用真空铸造或压力铸造等先进工艺,减少气体的产生。
铸件气孔的检测方法包括目视检查、X射线检测、超声波检测等。
一旦发现铸件气孔,需要进行修补或重新铸造。
- 1、下载文档前请自行甄别文档内容的完整性,平台不提供额外的编辑、内容补充、找答案等附加服务。
- 2、"仅部分预览"的文档,不可在线预览部分如存在完整性等问题,可反馈申请退款(可完整预览的文档不适用该条件!)。
- 3、如文档侵犯您的权益,请联系客服反馈,我们会尽快为您处理(人工客服工作时间:9:00-18:30)。
铸铁件氮气孔产生的原因分析及特征
特征:枝晶间裂隙状氮气孔
这种缺陷呈裂隙状多角形或断续裂纹状,跟其它的气孔类缺陷大不相同,从外观上看没有明显的气体痕迹,但能明显看到粗大的树枝晶,跟缩孔、缩松缺陷有点类似,所以在有些较厚大件上,经常被误认为是缩孔、缩松。
值得一提的是,这种气孔在铸件断面上呈大面积分布,有的也分布在较大的平面处,在铸件最后凝固如冒口附近,热节中心最为密集,这类气孔常发生在同一炉或同一浇包浇注的全部或大部分铸件中。
由于是在凝固过程晚期形成的,因而气孔孔洞形状不是圆球形的,而改变为多角形或枝晶间裂隙状的,这说明气泡生成及长大时,其周边被固体的枝晶壁所包围,而不能形成圆球形的气孔。
来源:液态金属所吸收的氮来自多种途径,主要有两大类,一是浇注前金属液本身所含的氮;二是树脂砂中所含的氮。
对于冲天炉熔炼的灰铸铁,炉料中的废钢是氮的重要来源,碱性电弧炉废钢,其含氮量可达
60ppm~140ppm,废钢多于35%,就有可能产生氮气孔,树脂砂中所含的氮来源于树脂及固化剂、再生砂中积累的氮、型砂中的含氮附加物及涂料中的氮沥青焦炭含氮量高,作为增碳剂使用时容易产生氮气孑L,必须引起高度重视。
而电极电墨作为增碳剂,则由于其含氮量低而不容易发生氮气孑L。
此外,在熔炼过程中即使加入含氮量高的增碳剂,如沥青焦炭,也只有在刚加入铁液时含氮量急剧增加,当铁液保温十多分钟后,含氮量逐渐恢复到加增碳剂前的水平。
机理:
用树脂砂生产铸铁件更容易产生氮气孔,这是因为当铁液浇人铸型后,含N的树脂受热分解出NH3,NH3又在金属液表面离解,NH3一[N]+3/2H2,[N]原子相当一部分进入铸型金属界面尚处于熔融
状态的金属表层,并由表向里扩散,致使表层金属液为氮饱和。
而到金属凝固期间,氮的溶解度急剧下降,就会析出氮气,形成氮气孔
铁水中含氮量大于100ppm时,往往会产生氮气孔,凝固前金属液所含全氮量=浇注前金属液本身的全氮量+树脂砂分解侵入金属液的氮量
金属液内的含氮量主要靠控制原材料废钢进行
砂铁比过高,型砂烧不透,这是导致再生砂残留含N量过高的重要因素,检测烧灼减量是监控树脂砂里面残留N量的一个主要手段
熔炼方式对灰铸铁中含氮量有较大的影响。
即使是C、Si含量相同的铁液,用工频电炉熔炼比冲天炉熔炼时的白口倾向大,含氮量也高。
对于酚醛尿烷树脂中的聚异氰酸酯,在潮湿的环境下使用时,NCO与水强烈反应,产生NH2,则要确保聚异氰酸酯容器的密封,减少它与空气的接触。
铁液含氮量高引起的氮气孔的防止方法是:铁液中加入钛铁,降低铸铁白口倾向和正确选用增碳剂。
防止树脂砂含氮量高引起的氮气孔的方法是:选用低氮树脂,型砂或涂料中加入氧化铁粉和避免树脂受潮。
1)将废钢加入量由3O降至2O%;
2)在铁液中加入氮稳定剂——锆、钛以及硼、铝,和氮生成稳定的化合物,从而降低了溶解[N]的浓度,即减少了含N量,也起脱氮作用。
特别是低碳当量灰铸铁件,当含氮量过高时,会产生枝晶间裂隙状氮气孔,铁液中加人Ti可以消除这种氮气孔。
灰铸铁含碳、硅低,即碳当量低时,氮在铁液中的溶解度增大。
因此,高牌号灰铸铁件易产生裂隙状氮气孔。
当熔融状态的铸铁中含有Zr、Al、Ti、Mg等元素时,可能形成氮化物,使铁液中的含氮量减少。
3)选用含N量5的中氮树脂,减少粘结剂中含N量;
4)下大力气着重解决再生砂的含N量问题,通过加大除尘力度,增强再生效果,提高脱膜率等措施,降低再生砂中的灼烧减量来。