OEE基础入门
OEE培训资料
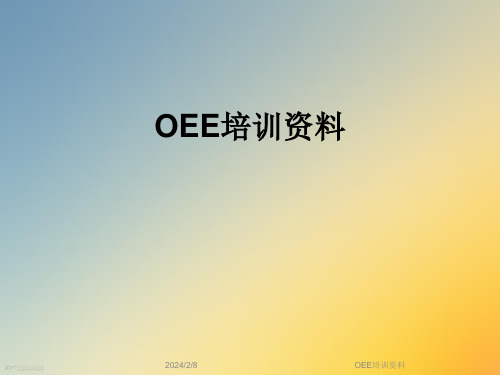
6. 启动稳定的损失 设备从启动到正常工作所需要的时间。
其原因有:
–设备要平缓加速到标准速度 –料筒需升温到设定温度 –去除多余的材料 –处理相关原料O的EE短培缺训资料
重庆光能荣能汽车配件有限公司
3. 设备综合效率的计算
稼动=开动=运转
工作时间 Total operating time A 负荷时间 Loading time
OEE培训资料
重庆光能荣能汽车配件有限公司
设
备
6大损失
设备综合效率的计算公式
工作时间
计
负荷时间
划 损
失
停
稼动时间
止 损
失
性
实 际能
稼动时间 损
失
不
价值稼 良
动时间 损
失
PPT文档演模板
0-1 计 划 停 机 0-2 教育、 早会
① 停工、故障 ② 换装、调整 ③ 空转、瞬停 ④ 速 度 降低 ⑤ 废品、返工 ⑥ 启 动 稳定
2. 设备效率损失的分类
大分类 计划损失 停止损失 性能损失 不良损失
中分类 交班时间/就餐/休息/生产中断/预防维修 设备故障/动力事故/换产/流量不足 流量调节/资材短缺/品质问题
瞬间停止/速度降低/空转
不良/再作业
公司认可的损失
影响OEE 的损失
PPT文档演模板
OEE培训资料
重庆光能荣能汽车配件有限公司
OEE就是用来表现实际的生产能力相对于理论产能的比率,它 是一个独立的测量工具 。
OEE也是一种简单实用的生产管理工具,设备效率指数已成为 衡量企业生产效率的重要标准,也是TPM实施的重要手法之一。
设备综合效率(OEE)是衡量一台设备按计划速度生产出合格产品 的时间占全部时间的百分比.
OEE设备综合效率管理培训教材(工业工程)

计算公式
公式说明: 1.人员操作周期=(3600/((合格品数+废品数)/(生产时间-换产时间-异常时间))) *模腔数 2.人员操作实际工时 =(合格品数+废品数)*人员操作周期 3.额定工时 =(合格品数+废品数)*额定生产周期 4.实际工时 =(合格品数+废品数)*实际生产周期 5.理论工时 = 合格品数*额定周期/一模几腔 6.废品损失工时 = 废品数*额定周期 7.产出工时 = 合格品数/(3600/额定生产周期)*标准定员/模腔数 8.节拍达标率(单个产品)= 额定周期/实际周期 9.节拍达标率(合计)= ∑额定工时/ ∑实际工时
标准作业组合表制定及运营
作业顺序变更运营
Quick Change 方法开发
SET UP 尺寸化
改善作业 BALANCE
作业顺序合理化
模具待机时间增加
Cleanning 效果增大
适用高压 Spray
模
小车上部加铁板盖
模具移动小车进行维修
作业 LEADER 运营
计划停机时间 =日常维护保养时间+交接班时间+一级保养时间+换模试模时间+计划维修时 间+达产的停机时间+其它计划中规定的时间
计划外停机时间(异常停机) =故障时间+工装及模具故障时间+工艺调试时间+待料时间+其它计划外停机 时间.
时间开动率相关关系
最新OEE培训讲义

I.OEE 的组成
OEE=Availability ×Performance efficiency ×Quality rate
设备综合效率=时间稼动率×性能稼动 率×合格品率
焦点:它衡量的目的在设备及制程的改 善,而不是对人的评价。
OEE培训讲义
2017-10-16
注意事项
欢迎大家参加本次课程,本课程将为您 打下一个基本的OEE知识基础,提高您的能 力和水平.请提前5分钟到场签到;
请注意以下的几点: 1、手机 上课期间请将您的手机开为振动
或关闭. 2、吸烟 在课堂内请不要吸烟. 3、其它
上课期间请不要大声喧哗, 举手提问, 不要随意走动.
结束语:
谢谢大家
重点:掌握造成OEE低下的各类型损失, 并加以改善。
II.OEE挂图
III.OEE的损失结构图
IV.OEE的计算---Availability时间稼动率
Availability的计算练习
Availability = B / A [练习] 某公司每班上班总时间为540分钟,其中用餐时间与
IV.OEE的计算---Performance性能稼动率
Performance的计算练习C
Performance = D / C [练习] 某公司每班上班总时间为540分钟,其中用餐时间与休
息为60分钟,上班前的交接班为10分钟,每班操作前 点检时间额定为10分钟。A=540-60-10-10=460 7月5日每班订单量为10k,每个的生产标准时间为2.76 秒,当日切换工程与调整总共花了30分钟,设备中途 故障与修复总时间为15分钟。另外这一班生产过程中 小停止10次,每次额定估算值为2分钟15=415, C=B*60/2.76=9021, D=9000, D/C=9000/9021=0.997 请计算这一班的Performance.
经典OEE培训教材

• 应对措施
– 了解损坏的原因及发生的时间和地点,然后运用根源问题解决 办法来解决
– 使用SMED技术来减少甚至消除设置调整的必要,并实现标准 化的第一轮通过流程
– 如果因为进线部件和原材料的变化而导致损坏,从而需要进行
调整来补偿就要建立部件质量拒收的限制,并使供应商质量管
理也参与到此管理流程
12
6. 质量缺陷
16
质量缺陷
计划外停 机
机器故障
速度下降
换线
损坏
4
OEE计算 – 模型
可编辑
六种重大损失降低机器效能说明
一班总工作时
可使用总工时
操作时间(停工时间 损失)
机器运转时间 (速度损失)
增值 (缺陷损失)
* 计划内停工排除在OEE计算之外
计划内停工*
机器故障 换线 计划外停工 速度降低 损坏 质量缺陷
可用时间 = (可使用总工时) - (窝工时间损失) (可使用总工时)
• 由PLC控制器衡量
• 应对措施 – 明确实际设计速度,最大速度,以及造成速度受限的物理原因 – 请工程人员进行程序检查并进行修改 – 应用Machine Kaizen来查找低速的原因并对设计速度提出质 疑
11
5. 损坏
可编辑
• 定义:工艺处理流程中,即“线上”即被查出的部件
• 由手写废品记录登记测量(注:假设每个部件的损坏造成生产该 部件全部时间的损失,从而将损坏部件数量转化为时间损失)
• 除机器故障或换线的所有计划 管理 外的停产 • 问题根源解决方法
• 由于机器运行速度较设计速度 慢而造成的时间损失 • 问题根源解决方法
• 在组装或调整中的损坏部件 • 问题根源解决方法
OEE运作
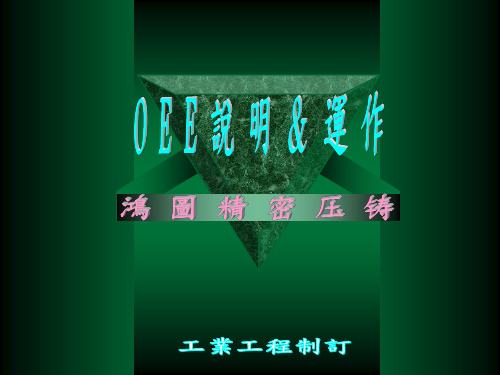
备注 1.一般情况由左表 所列单位主导负责 原因与对策,特情况 不能区分时由直接 责仸单位负责; 2.IE负责主导整个 提升OEE各项进度 跟进,其中涉及IE改 善项目由IE直接负 责,如切换类,环境 类..)
工时 模具故障 利用 率(A) 模具切换 亊务管理 等待时间
试作时间 其它时间
各相关单位 PJE
故障 设备故障及维修所引起的
建立完整的设备管理制度,加快 故障对应速度
计 切换 生产两种不同型号产品 划 订单 因订单不足而引起的
准备 外因
其他
生产开如前的准备过程
外界因素引起(如停电\水..) 无法归纳上列各点
8
三 OEE 2.計算公式: 概念 計劃停 機時間 之设 總 备工 計 净 作業 劃 利 時間 用 时利 時 間 時 間 其他 用率 停机
5
设备损失结构 休息时间 停 计划停机时间 机 时 亊务管理时间 间 无负荷时间 停机 故障 时间 切换
定义 生产计划觃定的休息时间 计划5S\TPM\保养\保全 朝会\教育培训\盘点\体检\试作\引 起设备之停机时间 待料/待检 突发故障 模具\治工具切换、调试
三 OEE 出 勤 概念 工 时 之工 时组 成
性能效率=
作業時間
實際產能(pcs/台/h)
=
960
=75.00%
11
1.含義:它是良品數與總生產數比 值,反映出制程質量狀況,也是 就我們通常說的良品率。
三 OEE 概念 之质 量率
2.組成、公式、例子:
=1350
生 总 產 數
良 品 數
不良品數 返工數 報廢數
質量率=
1350
1350+50+40 =83.75%
OEE基础(汇总)
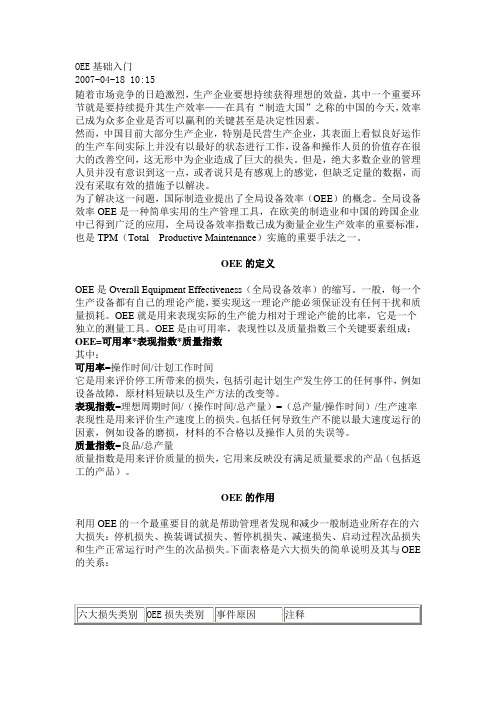
OEE基础入门2007-04-18 10:15随着市场竞争的日趋激烈,生产企业要想持续获得理想的效益,其中一个重要环节就是要持续提升其生产效率——在具有“制造大国”之称的中国的今天,效率已成为众多企业是否可以赢利的关键甚至是决定性因素。
然而,中国目前大部分生产企业,特别是民营生产企业,其表面上看似良好运作的生产车间实际上并没有以最好的状态进行工作,设备和操作人员的价值存在很大的改善空间,这无形中为企业造成了巨大的损失。
但是,绝大多数企业的管理人员并没有意识到这一点,或者说只是有感观上的感觉,但缺乏定量的数据,而没有采取有效的措施予以解决。
为了解决这一问题,国际制造业提出了全局设备效率(OEE)的概念。
全局设备效率OEE是一种简单实用的生产管理工具,在欧美的制造业和中国的跨国企业中已得到广泛的应用,全局设备效率指数已成为衡量企业生产效率的重要标准,也是TPM(Total Productive Maintenance)实施的重要手法之一。
OEE的定义OEE是Overall Equipment Effectiveness(全局设备效率)的缩写。
一般,每一个生产设备都有自己的理论产能,要实现这一理论产能必须保证没有任何干扰和质量损耗。
OEE就是用来表现实际的生产能力相对于理论产能的比率,它是一个独立的测量工具。
OEE是由可用率,表现性以及质量指数三个关键要素组成:OEE=可用率*表现指数*质量指数其中:可用率=操作时间/计划工作时间它是用来评价停工所带来的损失,包括引起计划生产发生停工的任何事件,例如设备故障,原材料短缺以及生产方法的改变等。
表现指数=理想周期时间/(操作时间/总产量)=(总产量/操作时间)/生产速率表现性是用来评价生产速度上的损失。
包括任何导致生产不能以最大速度运行的因素,例如设备的磨损,材料的不合格以及操作人员的失误等。
质量指数=良品/总产量质量指数是用来评价质量的损失,它用来反映没有满足质量要求的产品(包括返工的产品)。
OEE基础入门

OEE的定义OEE是Overall Equipment Effectiveness(全局设备效率)的缩写。
一般,每一个生产设备都有自己的理论产能,要实现这一理论产能必须保证没有任何干扰和质量损耗。
OEE就是用来表现实际的生产能力相对于理论产能的比率,它是一个独立的测量工具。
OEE是由可用率,表现性以及质量指数三个关键要素组成:OEE=可用率*表现指数*质量指数其中:可用率=操作时间/计划工作时间它是用来评价停工所带来的损失,包括引起计划生产发生停工的任何事件,例如设备故障,原材料短缺以及生产方法的改变等。
表现指数=理想周期时间/(操作时间/总产量)=(总产量/操作时间)/生产速率表现性是用来评价生产速度上的损失。
包括任何导致生产不能以最大速度运行的因素,例如设备的磨损,材料的不合格以及操作人员的失误等。
质量指数=良品/总产量质量指数是用来评价质量的损失,它用来反映没有满足质量要求的产品(包括返工的产品)OEE基础入门——OEE系列知识培训之一随着市场竞争的日趋激烈,生产企业要想持续获得理想的效益,其中一个重要环节就是要持续提升其生产效率——在具有“制造大国”之称的中国的今天,效率已成为众多企业是否可以赢利的关键甚至是决定性因素。
然而,中国目前大部分生产企业,特别是民营生产企业,其表面上看似良好运作的生产车间实际上并没有以最好的状态进行工作,设备和操作人员的价值存在很大的改善空间,这无形中为企业造成了巨大的损失。
但是,绝大多数企业的管理人员并没有意识到这一点,或者说只是有感观上的感觉,但缺乏定量的数据,而没有采取有效的措施予以解决。
为了解决这一问题,国际制造业提出了全局设备效率(OEE)的概念。
全局设备效率OEE是一种简单实用的生产管理工具,在欧美的制造业和中国的跨国企业中已得到广泛的应用,全局设备效率指数已成为衡量企业生产效率的重要标准,也是TPM(Total Productive Maintenance)实施的重要手法之一。
OEE_精品文档

体现设备的开动时间中有多少时间是进行产品生产的。
净开动率= 生产数量×实际Cycle Time ×100(%) 开动时间
OEE中性能开动率的计算公式
(5)性能开动率: 速度开动率和净开动率相乘得出的设备的性能发挥情况。
性能开动率=速度开动率×净开动率=
理论Circle Time×生产数量 开动时间
444 365,653 118,750
理论加工 时间(分钟/吨)
所需生产时间
0.138
13,350
0.120
41,740.4
0.114
58,316.3
0.108
36,734.1
0.105
152,371.2
0.095 0.089
34,683 10,581.2 5796小时
多品种生产线计算OEE举例
产品列表及性能开动率
A 时间开动率 Availability P 性能开动率 Performance Rate Q 合格品率 Quality Rate
设备利用率的计算公式(计算TEEP时用)
(1)设备利用率: 在整个日历时间中去除休止时间后的可利用时间所占的比例。
设备利用率
日历时间-休止时间 ×100 = 日历时间
负荷时间 日历时间
☆原则上,理论加工时间不大于实际加工周期,即速 度开动率是不大于100%的统计结果。 ☆国内企业经过不断升级改造或为超产拼速度,许多 设备当前加工运转速度超出了设计速度。 ☆这样如果仍使用原有数据为基准,则使速度开动率 超过100%,进而使性能开动率超过100%。
性能开动率为什么不能大于1?
﹡如果设备开动速度超过了设计速度,就如同设计 负荷5吨的大桥车开过8吨的汽车一样,是掠夺性的 使用设备,是不可取、不科学的做法,不应提倡。
OEE培训教材资料
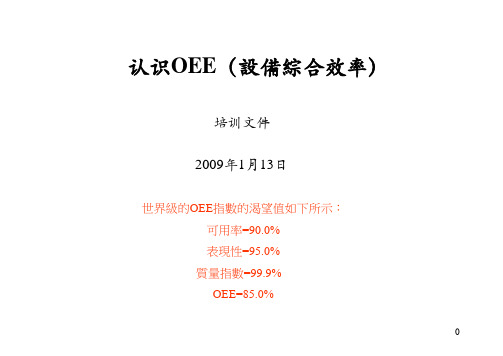
2、分析說明
根據OEE系統所提供的資料,你可以方便的知道自己工廠存在什麼問題,例如, 如果你的可用率在某一個時間段很低,說明在六大損失中和OEE可用率損失有關的 故障太多,那麼,顯而易見,你應該把改善重點放在這些方面了!同樣,如果質量 指數或者生產率導致你的OEE水準降低,那麼你就應該把目光放在和它們有關的問 題點上。在表一中,我們只列舉了一些事件原因,其實它可以包括和生產有關的任 何方面,因此,你可以對生產做到全面的管理和改善。
設備預熱,調試等生產正式運行之前產 • 问题根源解决方法 生的次品 生產穩定進行時產生的次品
■
• 问题根源解决方法
十三、使用OEE时的注意事项
!
!
• OEE要应用在一台机器上(可视为一台机器的生产线) 而不能应用在整个生产线或全厂上,这样才有意义
• OEE要作为一系列一体化的综合关键业绩指标中的一部 分来运用而不能孤立使用,否则将造成生产批次规模加大 或有质量缺陷的产品 • OEE必须与精益原则相符,要确保对OEE的计算不会导 致浪费合理化、制度化,例如,绝不要允许给换线留出 时间
理系統。
2、能分析/跟蹤生產線設備的有效利用情況,以便最大
化挖掘設備生產潛力。
3、能分析/跟蹤產線上的潛在風險和六大損失,以便降
低生產成本、提高生產力。
4、能為企業精益生產管理提供可視化的生產報告。 設備:降低設備的故障以及維修成本,加強設備管理以延長設備 的使用壽命。 員工:通過明確操作程式和SOP,提高勞動者的熟練程度和有效 工作業績,從而 提高生產效率。 工藝:通過解決工藝上的瓶頸問題,提高生產力。 質量:提高產品直通率(FTT),降低返修率,減少質量成本,
认识OEE(設備綜合效率)
培训文件 2009年1月13日
OEE培训教材(ppt44张)

时
间
5大人力损失
11 12 13 14
3大原材料与能源损失
成
15 16
本
我们的近邻联合利华世界500强在经过近10年的OE 的管理,2010年才从12大损失向16大损失迈进。
其中它是先做6大损失到9大损失到12大损失不断的摸索 才有今天的成绩。数据显示联合利华洗衣粉的产量从2004 日产260T/D到2010年日产近1000T/D。其中生产机器只增 了50%。在OEE的数据支撑下结合一些优良的管理方法再 加上公司员工的群策群力下设备的效率平均提高了48.6%
…
OEE 表格
原来 修改制作 在修改的
你会选择那种表?
中国员工的画像
海尔总裁张瑞敏关于人的品质有一段精彩的论述; “如果训练一个日本人,让他每天擦六遍桌子,他一定 会这样做;而一个中国人开始会擦六遍,慢慢觉得五遍 四遍也可以,最后索性不擦了”,“中国人坐事最大毛 是不认真,做事不到位,每天工作欠缺一点,天长地久 成为落后的顽症”。
OEE表的填写标准
上班第一时间填写OEE表上的日期、班次 、机器号、包装机、设定速度 开班清理、点检、润滑后填写开停车时间 开机至机器正常运行时填写试车时间 运行过程中出现如故障、小停机调整等填 写相应项,吃饭停机后要填写吃饭时间 不得提前填写或推迟填写
【OEE】要注意的问题
设备综合效率 = 时间利用率 * 设备性能率 * 产品合格率
1. 时间利用率 = (负荷时间 - 停机损失) / 负荷时间 * 100%
2. 设备性能率 = 生产产品数 / (利用时间 * 设计速度) * 100
3. 质量缺陷率 = (生产产品数 - 不合格品) / 生产产品数 * 1
TPM与PAMCO OEE的差别
OEE基础

20
常见问题及注意事项
TDK Div Pts Operations - IE
常见问题
如何选择机器速度的标准? (铭牌产量/理想速度/数据统计) 如果缺原料所以做清洁设备, 我们该记录什么停机原因?(缺原料) OEE是否要统计预防维护和清洁?(是) 我的设备特殊,无法推行OEE或根本实现85%的目标
23
~End~
BU8 Module Group Confidential
24
故障
设备坏
Setup time
不同产品转换时的设备调整时间
BU8 Module Group Confidential
12
效能: 速度损失
运行速度减慢
设备实际运行速度经常低于其设计运行速度. 影响设备运行但不会导致长时期停机的异常
小停顿
BU8 Module Group Confidential
16
Example
设某设备某天工作时间为8h, 班前计划停机15min, 故障停机30min,设备调整 25min, 产品的理论加工周期为0.6 min/件, 一天共加工产品450件, 有20件废 品, 求这台设备的OEE。
根据上面可知: 计划运行时间=8x60-15=465 (min) 实际运行时间=465-30-25=410 (min) 可用性=410/465=0.881(88.1%) 生产总量=410(件) 理想速度x实际运行时间=410/0.6=683 性能=450/683=0.658(65.8%) 质量指数=(450—20)/450=0.955(95.5%) OEE=可用性x性能x质量指数=55.4% 5 Why分析 找到根本问题 和解决方案
OEE培训教材

产品缺陷分类的目的
让全体员工都可以去识别我们生产出来产 品是否合格,以及产品缺陷的严重类别指数 。
我们可以通过什么方法达到我们要的效果和目 的?
培训
现场VCS
一点课程
现场活动
OEE 的时间利用表示图
720
690 660
总时间
操作时间
计划停 产时间
负荷时间 利用时间
净利用时间 有价值时间
不合格质量 停产时间 效率停 产时间 停产时 间
TPM与PAMCO OEE的差别
TPM OEE 基于由设备本身所带来的6大损失 ,强调负荷时间 PAMCO OEE 基于工厂业务/管理,前后工序 和设备本身等所带来的损失,强调总时间 PAMCO OEE < TPM OEE
PAMCO 设备效能指标
效率:
–生产效率PE –操作效率OE (E/P) (E/O)
产品合格率
6大损失的形象化
100% 速度损失
生产能力
时间
开车
小停车
质量 缺陷
故障
切换
停机
设备综合效率
设备综合效率 = 时间利用率 * 设备性能率 * 产品合格率
1. 时间利用率 = (负荷时间 - 停机损失) / 负荷时间 * 100% 2. 设备性能率 = 生产产品数 / (利用时间 * 设计速度) * 100% 3. 质量缺陷率 = (生产产品数 - 不合格品) / 生产产品数 * 100%
时
间
5大人力损失
11 12 13 14
成
3大原材料与能源损失
15 16
本
我们的近邻联合利华世界500强在经过近10年的OEE 的管理,2010年才从12大损失向16大损失迈进。 其中它是先做6大损失到9大损失到12大损失不断的摸索中 才有今天的成绩。数据显示联合利华洗衣粉的产量从2004年 日产260T/D到2010年日产近1000T/D。其中生产机器只增加 了50%。在OEE的数据支撑下结合一些优良的管理方法再 加上公司员工的群策群力下设备的效率平均提高了48.6%。 OEE对洽洽是一个陌生的管理方法,对我们来说OEE的 引进是对洽洽百利无一害的。同时联合利华给了我们一个很 好的启示和带头作用。
完整版OEE基本概念

设某设备某天工作时间为8h,班前计划停机15min,故障停机30min,设备调整25min,产品
的理论加工周期为0.6 min/件,一天共加工产品450件,有20件废品,求这台设备的OEE=根据上面可知:
计划运行时间=8x60-15=465 (mi n)
质量指数=(450—20)/450=0.955(95.5%)
OEE韦效率x表现性x质量指数=55.4%
另一种OEE算法:
OEE=符合质量要求的产品/最大理论产量
此例中最大理论产量=(8*60-15)/0.6件=775件
符合质量要求产品=450-20=430件
0EE=430/775*100%=55.4%
OEE损
失类别事Biblioteka 原因注释停机损失有效率
刀具损坏、设备突发 故障、原料短缺等
表示设备因为一些大的故障,或者突发 事件所引起的停工。
换装调试损 失
有效率
改变工具、设备预热 等
因改换工具,生产线调试等准备工作而 造成的损失,一般位于工位安排,生产 布置这一阶段
暂停机损失
表现性
不通畅的生产流、导 轨阻塞清洁,检查
•OE要作为一系列一体化的综合关键业绩指标中的一部分来运用而不能孤立使用,否则将 造成生产批次规模加大或有质量缺陷的产品。
•OE必须与精益原则相符,要确保对OEE的计算不会导致浪费合理化、制度化,例如,绝
不要允许给换线留出时间。
oee详细解释 编辑
OEE=^用率X表现性X质量指数。
其中:
可用率=操作时间/计划工作时间
计划运行时间=8*60-10=470(min) 实际运行时间=470-30-35=405(min) 有效率=405/470=0.86(86%)表现性=400/405=0.98(98%)质量指数=(400-20)/400=0.95(95%)OEE=
OEE基础入门

OEE的定义OEE是Overall Equipment Effectiveness(全局设备效率)的缩写。
一般,每一个生产设备都有自己的理论产能,要实现这一理论产能必须保证没有任何干扰和质量损耗。
OEE就是用来表现实际的生产能力相对于理论产能的比率,它是一个独立的测量工具。
OEE是由可用率,表现性以及质量指数三个关键要素组成:OEE=可用率*表现指数*质量指数其中:可用率=操作时间/计划工作时间它是用来评价停工所带来的损失,包括引起计划生产发生停工的任何事件,例如设备故障,原材料短缺以及生产方法的改变等。
表现指数=理想周期时间/(操作时间/总产量)=(总产量/操作时间)/生产速率表现性是用来评价生产速度上的损失。
包括任何导致生产不能以最大速度运行的因素,例如设备的磨损,材料的不合格以及操作人员的失误等。
质量指数=良品/总产量质量指数是用来评价质量的损失,它用来反映没有满足质量要求的产品(包括返工的产品)OEE基础入门——OEE系列知识培训之一随着市场竞争的日趋激烈,生产企业要想持续获得理想的效益,其中一个重要环节就是要持续提升其生产效率——在具有“制造大国”之称的中国的今天,效率已成为众多企业是否可以赢利的关键甚至是决定性因素。
然而,中国目前大部分生产企业,特别是民营生产企业,其表面上看似良好运作的生产车间实际上并没有以最好的状态进行工作,设备和操作人员的价值存在很大的改善空间,这无形中为企业造成了巨大的损失。
但是,绝大多数企业的管理人员并没有意识到这一点,或者说只是有感观上的感觉,但缺乏定量的数据,而没有采取有效的措施予以解决。
为了解决这一问题,国际制造业提出了全局设备效率(OEE)的概念。
全局设备效率OEE是一种简单实用的生产管理工具,在欧美的制造业和中国的跨国企业中已得到广泛的应用,全局设备效率指数已成为衡量企业生产效率的重要标准,也是TPM(Total Productive Maintenance)实施的重要手法之一。
设备OEE基础知识
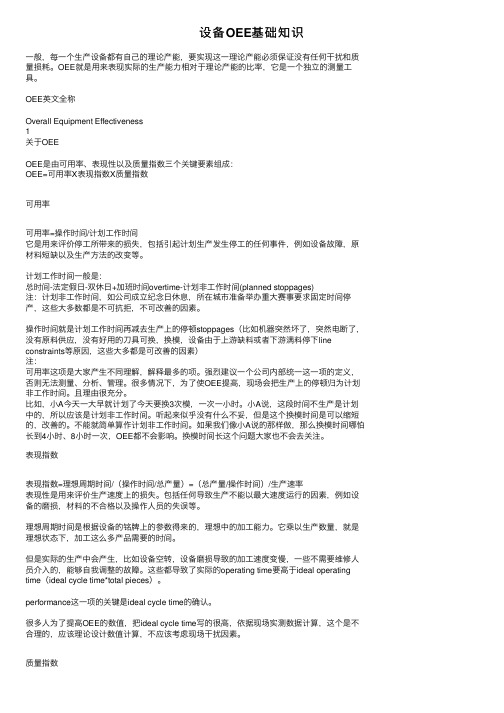
设备OEE基础知识⼀般,每⼀个⽣产设备都有⾃⼰的理论产能,要实现这⼀理论产能必须保证没有任何⼲扰和质量损耗。
OEE就是⽤来表现实际的⽣产能⼒相对于理论产能的⽐率,它是⼀个独⽴的测量⼯具。
OEE英⽂全称Overall Equipment Effectiveness1关于OEEOEE是由可⽤率、表现性以及质量指数三个关键要素组成:OEE=可⽤率X表现指数X质量指数可⽤率可⽤率=操作时间/计划⼯作时间它是⽤来评价停⼯所带来的损失,包括引起计划⽣产发⽣停⼯的任何事件,例如设备故障,原材料短缺以及⽣产⽅法的改变等。
计划⼯作时间⼀般是:总时间-法定假⽇-双休⽇+加班时间overtime-计划⾮⼯作时间(planned stoppages)注:计划⾮⼯作时间,如公司成⽴纪念⽇休息,所在城市准备举办重⼤赛事要求固定时间停产,这些⼤多数都是不可抗拒,不可改善的因素。
操作时间就是计划⼯作时间再减去⽣产上的停顿stoppages(⽐如机器突然坏了,突然电断了,没有原料供应,没有好⽤的⼑具可换,换模,设备由于上游缺料或者下游满料停下line constraints等原因,这些⼤多都是可改善的因素)注:可⽤率这项是⼤家产⽣不同理解,解释最多的项。
强烈建议⼀个公司内部统⼀这⼀项的定义,否则⽆法测量、分析、管理。
很多情况下,为了使OEE提⾼,现场会把⽣产上的停顿归为计划⾮⼯作时间。
且理由很充分。
⽐如,⼩A今天⼀⼤早就计划了今天要换3次模,⼀次⼀⼩时。
⼩A说,这段时间不⽣产是计划中的,所以应该是计划⾮⼯作时间。
听起来似乎没有什么不妥,但是这个换模时间是可以缩短的,改善的。
不能就简单算作计划⾮⼯作时间。
如果我们像⼩A说的那样做,那么换模时间哪怕长到4⼩时、8⼩时⼀次,OEE都不会影响。
换模时间长这个问题⼤家也不会去关注。
表现指数表现指数=理想周期时间/(操作时间/总产量)=(总产量/操作时间)/⽣产速率表现性是⽤来评价⽣产速度上的损失。
OEE基本概念(最新整理)

OEE(测量工具)OEE 是一个独立的测量工具,它用来表现实际的生产能力相对于理论产能的比率。
中文名全局设备效率外文名Overall Equipment Effectiveness关键要素可用率,表现性,质量指数目录1定义2采集方法3作用4应用范围5作用6效益7注意事项8详细解释9计算实例10采集方法11计算实例12水平对比oee 定义编辑一般,每一个生产设备都有自己的最大理论产能,要实现这一产能必须保证没有任何干扰和质量损耗。
当然,实际生产中是不可能达到这一要求,由于许许多多的因素,车间设备存在着大量的失效: 例如,除去设备的故障、调整,以及设备的完全更换之外,当设备的表现非常低时,可能会影响生产率,产生次品,返工等。
OEE 是一个独立的测量工具,它用来表现实际的生产能力相对于理论产能的比率。
国际上对OEE 的定义为:OEE 是Overall Equipment Effectiveness(全局设备效率)的缩写。
它由可用率,表现性以及质量指数三个关键要素组成,即:OEE=可用率X 表现性X 质量指数其中:可用率=操作时间/计划工作时间。
它是用来考虑停工所带来的损失,包括引起计划生产发生停工的任何事件,例如设备故障,原料短缺以及生产方法的改变等。
表现性=理想周期时间/ (操作时间/ 总产量)=总产量/ (操作时间X 理论生产速率)表现性考虑生产速度上的损失。
包括任何导致生产不能以最大速度运行的因素,例如设备的磨损,材料的不合格以及操作人员的失误等。
质量指数=良品/总产量质量指数考虑质量的损失,它用来反映没有满足质量要求的产品(包括返工的产品)。
利用OEE 的一个最重要目的就是减少一般制造业所存在的六大损失:停机损失、换装调试损失、暂停机损失、减速损失、启动过程次品损失和生产正常运行时产生的次品损失。
oee 采集方法编辑OEE 的计算虽然简单,但是,在实际的应用中,当与班次,员工,设备,产品等生产要素联系在一起时,便变得十分复杂,利用人工采集数据计算OEE 显得麻烦费事,为了更有效的利用OEE 这个工具,OEE 数据采集信息化越来越成为人们关心的话题,OEE IMPACT 是世界上最优秀的OEE 系统,它具有自动化数据采集模块,可以轻松地获取有关设备的生产信息,为OEE 提供最有价值的数据,同时,该系统也可以生成实时的生产信息报告,包括故障停工,在制品信息和OEE 等。