GFRP风机叶片结构设计的二级优化方法
风力发电机组叶片设计与性能优化

风力发电机组叶片设计与性能优化风力发电是一种可再生能源,利用风的动能转换为电能。
其中,风力发电机组的叶片是最关键的组件之一。
本文将重点讨论风力发电机组叶片的设计与性能优化。
1. 叶片设计原理风力发电机组的叶片主要用于捕获风能并转化为机械旋转能,并通过传动装置将机械能转化为电能。
叶片的设计原理包括以下几个方面:1.1 叶片的形状与曲率分布:叶片的形状和曲率分布对于风能的捕获和转化至关重要。
适当的曲率分布可以使风能转化效率最大化。
1.2 叶片长度和宽度比例:叶片的长度和宽度比例也会影响风能转化的效果。
适当的长度和宽度比例可以提高叶片的刚性和稳定性。
1.3 叶片材料选择:叶片的材料应具备一定的刚度、强度和耐腐蚀性能。
常用的材料包括玻璃纤维复合材料、碳纤维和铝合金等。
2. 叶片性能优化叶片的性能优化旨在提高风能转化效率,并降低噪音和振动。
以下是一些常见的叶片性能优化策略:2.1 气动外形优化:通过改变叶片的气动外形,如叶片的弦长、厚度以及前缘和后缘的形状等,可以提高叶片的气动效率和动态响应特性。
2.2 叶片结构优化:通过优化叶片的结构设计,如采用空心叶片、增强支撑结构和减小叶片质量等,可以提高叶片的刚度和稳定性,减小叶片的振动和噪音。
2.3 材料优化:选择合适的材料以提高叶片的强度和刚度。
同时,考虑材料的成本和可持续性,如选择可再生材料或回收材料。
2.4 控制系统优化:通过优化叶片的控制系统,实现叶片角度的调整和适应不同风速条件,进一步提高风能转化的效率。
3. 叶片性能测试与验证为了验证叶片的设计和性能优化效果,需要进行相应的测试和验证。
常见的测试方法包括:3.1 静态试验:对叶片进行材料强度和刚度等性能测试,以验证设计的可行性。
3.2 动态试验:通过在不同风速下对叶片进行负载测试,来评估叶片的动态性能和气动效率。
3.3 实地试验:在实际的风力发电场中,对叶片的性能进行实测,以验证设计的可靠性和有效性。
风机叶片结构设计与优化研究
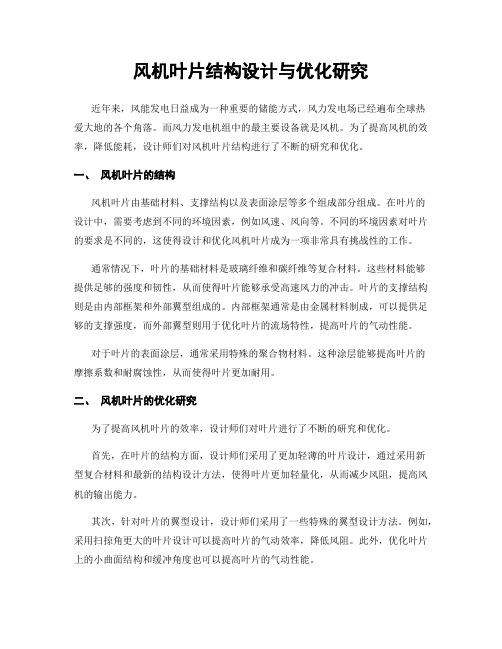
风机叶片结构设计与优化研究近年来,风能发电日益成为一种重要的储能方式,风力发电场已经遍布全球热爱大地的各个角落。
而风力发电机组中的最主要设备就是风机。
为了提高风机的效率,降低能耗,设计师们对风机叶片结构进行了不断的研究和优化。
一、风机叶片的结构风机叶片由基础材料、支撑结构以及表面涂层等多个组成部分组成。
在叶片的设计中,需要考虑到不同的环境因素,例如风速、风向等。
不同的环境因素对叶片的要求是不同的,这使得设计和优化风机叶片成为一项非常具有挑战性的工作。
通常情况下,叶片的基础材料是玻璃纤维和碳纤维等复合材料。
这些材料能够提供足够的强度和韧性,从而使得叶片能够承受高速风力的冲击。
叶片的支撑结构则是由内部框架和外部翼型组成的。
内部框架通常是由金属材料制成,可以提供足够的支撑强度,而外部翼型则用于优化叶片的流场特性,提高叶片的气动性能。
对于叶片的表面涂层,通常采用特殊的聚合物材料。
这种涂层能够提高叶片的摩擦系数和耐腐蚀性,从而使得叶片更加耐用。
二、风机叶片的优化研究为了提高风机叶片的效率,设计师们对叶片进行了不断的研究和优化。
首先,在叶片的结构方面,设计师们采用了更加轻薄的叶片设计,通过采用新型复合材料和最新的结构设计方法,使得叶片更加轻量化,从而减少风阻,提高风机的输出能力。
其次,针对叶片的翼型设计,设计师们采用了一些特殊的翼型设计方法。
例如,采用扫掠角更大的叶片设计可以提高叶片的气动效率,降低风阻。
此外,优化叶片上的小曲面结构和缓冲角度也可以提高叶片的气动性能。
另外,为了降低风机的噪音,设计师们还采用了一些新型材料和表面涂层。
通过改变叶片表面的形态或者采用新型涂层,来减少噪音的产生。
综上所述,设计师们对风机叶片的结构进行了不断的优化和改进,不仅可以提高风机的效率,还可以降低风机的能耗。
未来的研究方向则是进一步降低风机的噪音,并采用更加环保的新型材料。
风力发电机组叶片设计优化
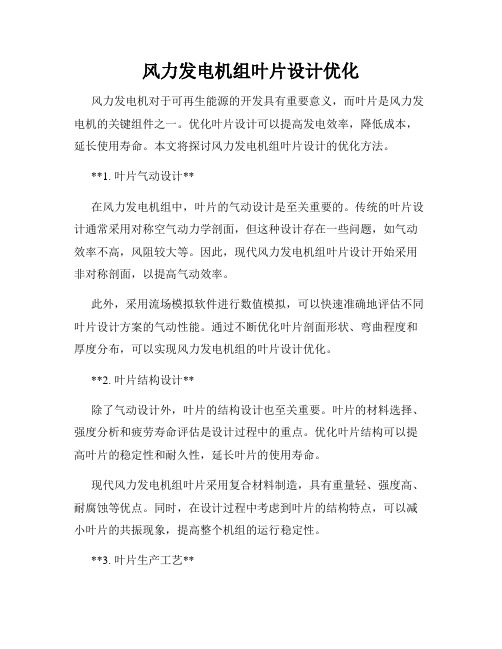
风力发电机组叶片设计优化风力发电机对于可再生能源的开发具有重要意义,而叶片是风力发电机的关键组件之一。
优化叶片设计可以提高发电效率,降低成本,延长使用寿命。
本文将探讨风力发电机组叶片设计的优化方法。
**1. 叶片气动设计**在风力发电机组中,叶片的气动设计是至关重要的。
传统的叶片设计通常采用对称空气动力学剖面,但这种设计存在一些问题,如气动效率不高,风阻较大等。
因此,现代风力发电机组叶片设计开始采用非对称剖面,以提高气动效率。
此外,采用流场模拟软件进行数值模拟,可以快速准确地评估不同叶片设计方案的气动性能。
通过不断优化叶片剖面形状、弯曲程度和厚度分布,可以实现风力发电机组的叶片设计优化。
**2. 叶片结构设计**除了气动设计外,叶片的结构设计也至关重要。
叶片的材料选择、强度分析和疲劳寿命评估是设计过程中的重点。
优化叶片结构可以提高叶片的稳定性和耐久性,延长叶片的使用寿命。
现代风力发电机组叶片采用复合材料制造,具有重量轻、强度高、耐腐蚀等优点。
同时,在设计过程中考虑到叶片的结构特点,可以减小叶片的共振现象,提高整个机组的运行稳定性。
**3. 叶片生产工艺**叶片生产工艺也是影响叶片质量和性能的重要因素。
采用先进的生产工艺可以提高叶片的一致性和精度,减小生产误差,确保叶片的性能稳定性。
现代风力发电机组叶片生产通常采用模具成型工艺,利用自动化设备进行加工和装配,提高生产效率和产品质量。
同时,通过建立完善的质量控制体系和监测手段,可以及时发现生产过程中的问题,确保叶片的质量符合设计要求。
**结语**风力发电机组叶片设计的优化是提高风力发电效率和降低成本的关键。
通过气动设计、结构设计和生产工艺的优化,可以实现叶片设计的全面提升,为风力发电行业的发展做出贡献。
希望本文可以为相关领域的专业人士提供一些思路和参考,推动风力发电技术的进步与发展。
风机叶片结构分析与性能优化研究
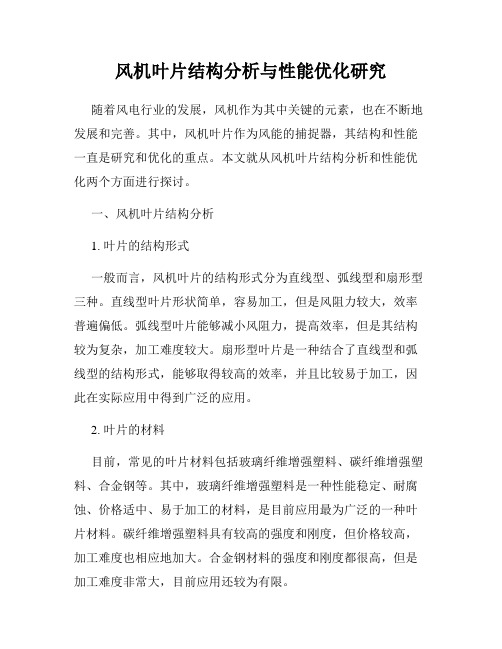
风机叶片结构分析与性能优化研究随着风电行业的发展,风机作为其中关键的元素,也在不断地发展和完善。
其中,风机叶片作为风能的捕捉器,其结构和性能一直是研究和优化的重点。
本文就从风机叶片结构分析和性能优化两个方面进行探讨。
一、风机叶片结构分析1. 叶片的结构形式一般而言,风机叶片的结构形式分为直线型、弧线型和扇形型三种。
直线型叶片形状简单,容易加工,但是风阻力较大,效率普遍偏低。
弧线型叶片能够减小风阻力,提高效率,但是其结构较为复杂,加工难度较大。
扇形型叶片是一种结合了直线型和弧线型的结构形式,能够取得较高的效率,并且比较易于加工,因此在实际应用中得到广泛的应用。
2. 叶片的材料目前,常见的叶片材料包括玻璃纤维增强塑料、碳纤维增强塑料、合金钢等。
其中,玻璃纤维增强塑料是一种性能稳定、耐腐蚀、价格适中、易于加工的材料,是目前应用最为广泛的一种叶片材料。
碳纤维增强塑料具有较高的强度和刚度,但价格较高,加工难度也相应地加大。
合金钢材料的强度和刚度都很高,但是加工难度非常大,目前应用还较为有限。
3. 叶片的结构优化为了提高叶片的效率和稳定性,可以通过结构优化的方式进行改进。
其中,一些常见的叶片结构优化方式包括增加叶片长宽比、增加弯曲度、改变叶片厚度分布、增加翼尖扭曲等。
通过这些方式的改进,可以提高叶片的捕风效率,减小噪声和振动,并且提高叶片的寿命和稳定性。
二、风机叶片性能优化针对不同的应用需求,对风机叶片进行性能优化也是非常重要的。
下面,我们从叶片的风力拟合性、捕风效率、稳定性等方面进行分析和探讨。
1. 风力拟合性风力拟合性是叶片性能的重要指标之一,它反映了叶片对于波动风速的适应性。
在设计叶片时,需要考虑到风能资源的特点,以及叶片运行过程中可能会遇到的风速变化等因素,通过对风力拟合性进行优化,可以提高叶片的适应能力和稳定性。
2. 捕风效率捕风效率是另一个重要的性能指标,它表示了叶片能够捕集风能的能力。
在叶片设计中,需要考虑到波动风速、风角变化等因素,以及叶片的形状、材料、转速等因素,通过对这些因素的综合考虑和优化,可以提高叶片的捕风效率。
风机结构优化设计方法综述与实例分析

风机结构优化设计方法综述与实例分析引言风机是一种广泛应用于工程领域的设备,利用风力进行动力转换。
在现代工业生产中,风机被广泛应用于通风、空调、冷却、加热等领域。
为了提高风机的性能和效率,风机结构优化设计成为一个重要的研究方向。
本文将综述风机结构优化设计的方法,并通过实例分析来展示这些方法的应用。
一、风机结构优化设计方法的分类风机结构优化设计方法可以分为传统方法和计算机辅助设计方法两大类。
1.传统方法传统方法通常基于试验和经验公式,其使用范围较为有限。
其中,试验方法通过实验来确定风机的参数和结构设计,具有较高的精度;经验公式方法则基于经验公式进行设计,速度较快,但精度较低。
2.计算机辅助设计方法计算机辅助设计方法采用数值模拟和优化算法,可以实现对风机结构的精确优化设计。
这些方法包括计算流体力学(CFD)模拟、有限元分析(FEA)和多目标优化算法等。
二、风机结构优化设计方法的具体应用接下来,将通过两个实例来介绍风机结构优化设计方法的具体应用。
1.示例一:风轮叶片优化设计风轮叶片的设计对风机的性能至关重要。
在优化设计过程中,可以采用计算机辅助设计方法来实现。
首先,通过计算流体力学(CFD)模拟来分析叶片的流场特性,包括气动特性和压力分布等。
然后,利用有限元分析(FEA)来评估叶片的结构强度和刚度。
最后,使用多目标优化算法来优化叶片的形状,以提高风能的转换效率和降低噪音。
2.示例二:风机外壳结构优化设计风机的外壳结构也对风机的性能和效率有重要影响。
在优化设计过程中,可以采用计算机辅助设计方法来实现。
首先,利用有限元分析(FEA)来评估外壳的结构强度和刚度,以及对风机运行时的振动和噪音的影响。
然后,使用多目标优化算法来优化外壳的结构,以提高风机的工作效率和降低振动和噪音。
三、结论与展望风机结构优化设计是提高风机性能和效率的关键措施。
本文综述了风机结构优化设计方法的分类,并通过两个实例分析展示了这些方法的具体应用。
风机叶片结构设计与优化

风机叶片结构设计与优化随着现代工业的快速发展,风力发电作为一种可再生的可持续能源形式也逐渐成为了人们关注的焦点。
而在风力发电的核心部件,风能转换系统中,风机叶片的设计和优化也十分关键。
风机叶片的结构设计风机叶片是风力发电机组的重要部分,主要作用是将风能转化为机械能,进而驱动发电机发电。
对于风机叶片的结构设计,需要考虑到以下几个方面。
首先,要充分考虑风速和风向的变化,以及风场的特性,从而设计出符合实际工作环境的叶片结构。
在设计叶片的根部、中部和尖部等位置时,还需要根据不同的受力情况进行合理的加强设计。
其次,叶片的长度和宽度也需要充分考虑。
如果叶片长度过短,那么就不能充分利用风能进行转换,从而影响到风力发电机组的发电效率。
而如果叶片长度过长,对于材质和生产成本的要求将会更高,也会带来更大的制造难度。
此外,叶片的形状也是设计的重要方面。
对于一般的三叶片风机叶片来说,需要考虑到叶片弯曲度、扭曲度、翼型等因素。
这些因素将直接影响到叶片的起飞速度、最大风速以及噪音等问题。
风机叶片的优化针对风机叶片的结构设计,优化也是设计的一个重要方面。
对于现有的风机叶片,需要进行深入的研究和优化,以提高风力发电机组的整体效率。
首先,要优化叶片的气动性能。
通过研究叶片的气动流场等问题,可以进一步改善叶片的气动性能,提高叶片的起飞速度和最大功率输出。
此外,还可以利用附面效应和扭曲设计等技术手段,改善叶片的空气动力学特性。
其次,要针对叶片的材质和结构进行优化。
目前常用的叶片材料主要为玻璃钢、碳纤维复合材料等。
但是,在复杂环境中,这些材料容易受到外界环境和受力情况的影响,导致叶片的损坏和破坏。
因此,需要对叶片的材料进行深入研究,开发出更加适合风力发电场景下的叶片材料。
最后,还需要对叶片的生产和装配进行优化。
对于现有的生产和装配工艺来说,需要考虑到生产成本、制造难度和效率等因素,进一步提高叶片的生产效率和质量水平。
结语风机叶片的结构设计和优化是风力发电系统中重要的研究内容。
风力发电机叶片材料参数优化设计研究
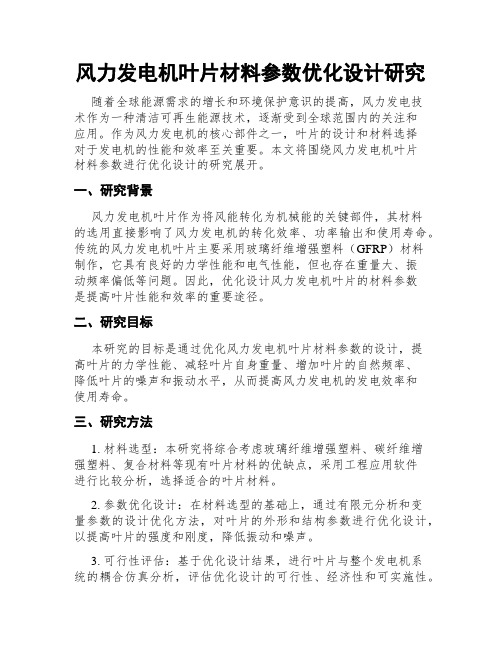
风力发电机叶片材料参数优化设计研究随着全球能源需求的增长和环境保护意识的提高,风力发电技术作为一种清洁可再生能源技术,逐渐受到全球范围内的关注和应用。
作为风力发电机的核心部件之一,叶片的设计和材料选择对于发电机的性能和效率至关重要。
本文将围绕风力发电机叶片材料参数进行优化设计的研究展开。
一、研究背景风力发电机叶片作为将风能转化为机械能的关键部件,其材料的选用直接影响了风力发电机的转化效率、功率输出和使用寿命。
传统的风力发电机叶片主要采用玻璃纤维增强塑料(GFRP)材料制作,它具有良好的力学性能和电气性能,但也存在重量大、振动频率偏低等问题。
因此,优化设计风力发电机叶片的材料参数是提高叶片性能和效率的重要途径。
二、研究目标本研究的目标是通过优化风力发电机叶片材料参数的设计,提高叶片的力学性能、减轻叶片自身重量、增加叶片的自然频率、降低叶片的噪声和振动水平,从而提高风力发电机的发电效率和使用寿命。
三、研究方法1. 材料选型:本研究将综合考虑玻璃纤维增强塑料、碳纤维增强塑料、复合材料等现有叶片材料的优缺点,采用工程应用软件进行比较分析,选择适合的叶片材料。
2. 参数优化设计:在材料选型的基础上,通过有限元分析和变量参数的设计优化方法,对叶片的外形和结构参数进行优化设计,以提高叶片的强度和刚度,降低振动和噪声。
3. 可行性评估:基于优化设计结果,进行叶片与整个发电机系统的耦合仿真分析,评估优化设计的可行性、经济性和可实施性。
四、研究内容1. 材料特性分析:对玻璃纤维增强塑料、碳纤维增强塑料和复合材料等叶片材料的力学性能、电气性能、耐久性等进行综合分析,找出适合风力发电机叶片的材料。
2. 叶片外形优化设计:基于叶片的结构和气动特性,通过参数优化设计方法,优化叶片的尺寸、形态和布局,以实现最佳的机械性能和气动性能。
3. 叶片结构优化设计:采用有限元分析方法,在现有材料基础上,探索合理的叶片结构设计,包括筋骨布置、厚度分布等方面的优化,以提高叶片的强度和刚度。
GFRP风机叶片结构设计的二级优化方法
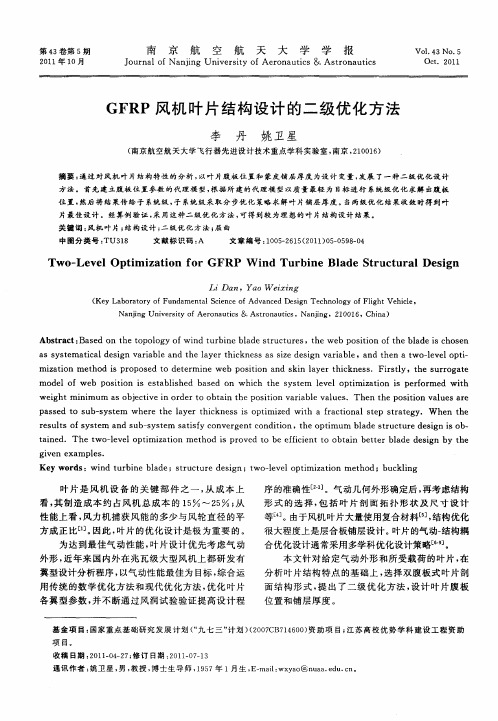
基 金 项 目 : 家 重 点 基 础 研 究 发 展 计 划 (九 七 三 ” 划 ) 2 0C 7 4 0 ) 助 项 目; 苏 高 校 优 势 学 科 建 设 工 程 资 助 国 “ 计 ( 07 B 16 0 资 江
项 目。 收稿 日期 :0 10 — 7 修 订 日期 :0 10 — 3 2 1- 42 ; 2 1 - 7 1
面结 构形 式 , 出 了二 级 优化 方法 , 计 叶 片腹 板 提 设
位 置 和铺 层 厚 度 。
方 成正 比[ 。 1 因此 , 片的优化 设计 是极 为重要 的 。 ] 叶 为达到 最佳气 动 性能 , 叶片设计 优 先考 虑气 动 外形, 近年来 国内外在 兆瓦级 大 型风机 上都研 发 有 翼型设计分析程序 , 以气动性 能最佳为 目标 , 综合 运 用 传统 的数 学优化 方法 和现代 优化 方法 , 优化 叶片 各 翼 型参数 , 并不 断通 过风洞 试验 验证 提高设 计 程
Na jn ie st fAeo a tc nig Unv r i o r n u is& Asr n u is 1 ,Chn ) ia
Absr c : s d o h o ol g n u b n a e s r c u e t a t Ba e n t e t p o y ofwi d t r i e bl d t u t r s,t b p ii ft e b a sc s n he we oston o h l dei ho e
风力发电机组叶片结构优化与性能研究

风力发电机组叶片结构优化与性能研究随着能源危机的日益严重和环境保护意识的增强,风力发电作为一种可再生清洁能源得到了广泛关注。
而风力发电机组的叶片作为直接受风力作用的部分,其结构优化和性能研究对于提高风力发电效率至关重要。
本文将就风力发电机组叶片的结构优化和性能进行研究。
一、风力发电机组叶片的结构优化风力发电机组叶片的结构优化是提高风能利用效率的关键,常见的结构优化方法有以下几种:1. 材料优化风力发电机组叶片常用的材料有复合材料、玻璃纤维、碳纤维等。
通过选用合适的材料,可以提高叶片的强度和刚度,减轻叶片自重。
2. 外形参数优化风力发电机组叶片的外形参数如叶片长度、扭转角度、弯曲程度等直接影响着叶片的风能捕获和转化效率。
通过合理调整这些参数,可以使叶片更好地适应不同的风速和风向,提高叶片的截风能力。
3. 结构设计优化风力发电机组叶片的结构设计包括叶片翼型设计、翼型内部结构设计等。
通过对叶片翼型进行优化设计,可以提高叶片的气动性能;通过合理设计叶片内部结构,可以提高叶片的刚度和耐久性。
二、风力发电机组叶片性能研究风力发电机组叶片的性能研究是为了评估叶片的工作能力和工作状态,常见的研究内容包括以下几个方面:1. 气动性能研究气动性能是评估风力发电机组叶片的重要指标,包括叶片的风阻特性、升力特性和流线型等。
通过数值模拟或实验测量,可以得到叶片在不同风速下的气动性能曲线,从而选择合适的叶片设计。
2. 力学性能研究风力发电机组叶片在工作过程中会受到风压力、离心力等多种力的作用,因此力学性能研究对于确保叶片的结构安全和可靠运行至关重要。
通过有限元分析等方法,可以研究叶片的应力分布、变形情况等。
3. 声学性能研究风力发电机组叶片在运行时会产生一定的噪音,而这对于附近居民的生活和健康是有一定影响的。
因此,研究叶片的声学性能,通过优化设计降低噪音的产生,对于提高叶片的使用环境非常重要。
结论通过对风力发电机组叶片的结构优化和性能研究,可以提高叶片的风能转化效率,进一步提高风力发电机组的发电效率。
风机叶片结构优化与维修技术研究
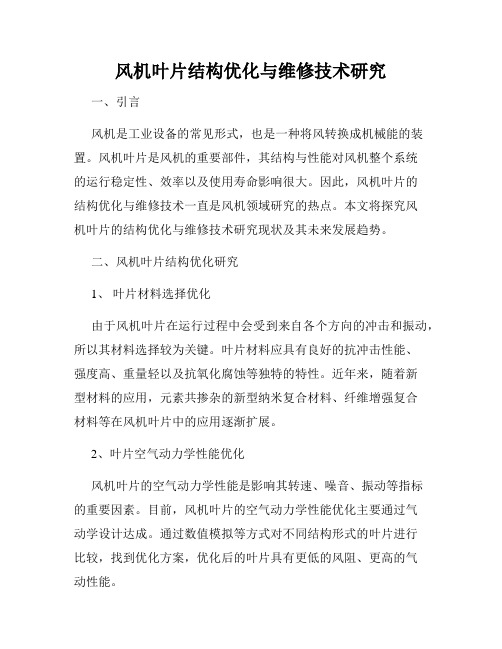
风机叶片结构优化与维修技术研究一、引言风机是工业设备的常见形式,也是一种将风转换成机械能的装置。
风机叶片是风机的重要部件,其结构与性能对风机整个系统的运行稳定性、效率以及使用寿命影响很大。
因此,风机叶片的结构优化与维修技术一直是风机领域研究的热点。
本文将探究风机叶片的结构优化与维修技术研究现状及其未来发展趋势。
二、风机叶片结构优化研究1、叶片材料选择优化由于风机叶片在运行过程中会受到来自各个方向的冲击和振动,所以其材料选择较为关键。
叶片材料应具有良好的抗冲击性能、强度高、重量轻以及抗氧化腐蚀等独特的特性。
近年来,随着新型材料的应用,元素共掺杂的新型纳米复合材料、纤维增强复合材料等在风机叶片中的应用逐渐扩展。
2、叶片空气动力学性能优化风机叶片的空气动力学性能是影响其转速、噪音、振动等指标的重要因素。
目前,风机叶片的空气动力学性能优化主要通过气动学设计达成。
通过数值模拟等方式对不同结构形式的叶片进行比较,找到优化方案,优化后的叶片具有更低的风阻、更高的气动性能。
三、风机叶片维修技术研究1、叶片断裂修复技术一旦叶片发生断裂,会对风机的稳定性和运行效率造成较大影响。
因此,如何及时修复叶片断裂成为了研究的重点。
主流的修复方法有焊接、粘接、复合材料修补等。
复合材料修补是目前较为普遍的方法之一,特别是针对一些较小的开裂或者裂纹。
目前,研究人员正在进行针对大面积叶片断裂的修复技术的探究。
2、各个部位的维护和检测技术风机叶片的维护和检测非常重要,对于叶片的各个部位,如叶片根部、叶片中心等,我们需要定期进行检查和维护。
对于这些部位,有专门的维护和检测技术。
例如,采用超声波检测技术可以检测叶片表面是否有裂纹,避免叶片在工作时出现过多的振动,引发风机失灵等问题。
此外,还需要核查叶片是否处于正确的位置,叶片间距是否足够,以及是否存在叶片变形等情况。
四、结论风机叶片的结构优化和维修技术研究是风机领域的重要方向,主流的研究方案包括叶片材料选择、空气动力学性能优化、断裂修复技术、叶片各个部位的维护和检测等内容。
风力发电机组的叶片设计与优化策略
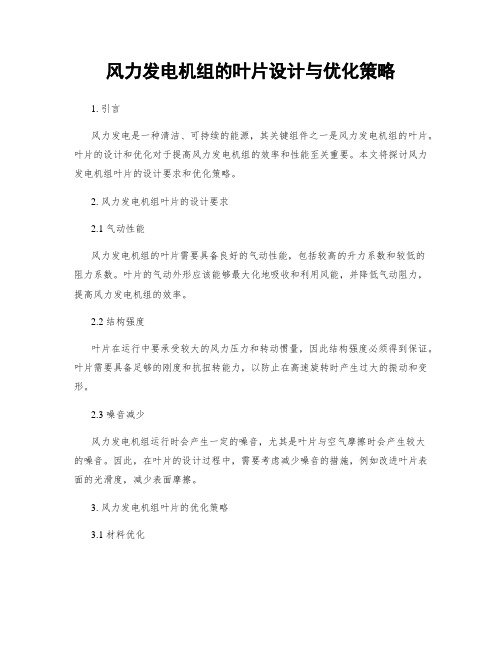
风力发电机组的叶片设计与优化策略1. 引言风力发电是一种清洁、可持续的能源,其关键组件之一是风力发电机组的叶片。
叶片的设计和优化对于提高风力发电机组的效率和性能至关重要。
本文将探讨风力发电机组叶片的设计要求和优化策略。
2. 风力发电机组叶片的设计要求2.1 气动性能风力发电机组的叶片需要具备良好的气动性能,包括较高的升力系数和较低的阻力系数。
叶片的气动外形应该能够最大化地吸收和利用风能,并降低气动阻力,提高风力发电机组的效率。
2.2 结构强度叶片在运行中要承受较大的风力压力和转动惯量,因此结构强度必须得到保证。
叶片需要具备足够的刚度和抗扭转能力,以防止在高速旋转时产生过大的振动和变形。
2.3 噪音减少风力发电机组运行时会产生一定的噪音,尤其是叶片与空气摩擦时会产生较大的噪音。
因此,在叶片的设计过程中,需要考虑减少噪音的措施,例如改进叶片表面的光滑度,减少表面摩擦。
3. 风力发电机组叶片的优化策略3.1 材料优化叶片的材料选择对于提高叶片的结构强度和抗扭转能力至关重要。
常见的叶片材料有玻璃纤维复合材料和碳纤维复合材料,这些材料具有较高的强度和轻量化的特点,是叶片制造中常用的选择。
3.2 叶片外形的优化叶片外形的优化是叶片设计中的核心问题。
一般来说,叶片的长度和弯曲度对于风力发电机组的性能有着重要的影响。
通过合理地设计叶片的曲线和扭转分布,可以达到提高风能捕捉效率的目的。
此外,还可以采用翼型优化算法,如遗传算法、粒子群算法等,来求解最佳的叶片外形。
3.3 运行参数的优化风力发电机组叶片的运行参数也可以通过优化来提高风能转化效率。
例如,通过调整叶片的旋转速度、倾斜角度和叶片的扭转分布,可以使叶片在不同风速下都能以最佳状态运行,从而最大限度地提高风能转化效率。
4. 风力发电机组叶片设计与优化的案例研究国内外许多研究人员和工程师都对风力发电机组叶片的设计和优化进行了深入研究。
例如,瑞典乌普萨拉大学的研究团队通过数值模拟和实验验证,优化了风力发电机组叶片的扭转角度分布,提高了转化效率。
风力发电机组叶片结构设计与优化

风力发电机组叶片结构设计与优化随着可再生能源的重要性逐渐凸显,风力发电作为一种清洁、可持续的能源形式,受到越来越多的关注。
而风力发电机组的叶片是转化风能为机械能的关键元件,其结构设计与优化对于提高风力发电机组的性能至关重要。
本文将对风力发电机组叶片的结构设计与优化进行探讨。
一、风力发电机组叶片结构设计风力发电机组叶片的结构设计是指确定叶片的长度、宽度、形状等参数的过程。
叶片的结构设计需要考虑以下几个方面:1. 材料选择:叶片的材料需要具备足够的强度和刚度,同时要尽量减小自重以降低风力发电机组的启动风速。
常见的材料包括复合材料、玻璃钢等。
2. 叶片长度:叶片长度的选取需要考虑风场的平均风速、叶片的强度以及噪音和振动的限制要求。
较长的叶片能够提高风力发电机组的发电效率,但同时也会增加叶片的自重和制造成本。
3. 叶片形状:叶片的形状对于风力发电机组的性能具有重要影响。
常见的叶片形状包括平直型、过渡型和弯曲型。
不同形状的叶片在不同风速下的性能表现也有所差异。
4. 附加设备:叶片上还可以添加一些附加设备,如流场修型装置、结构缓冲装置等,以进一步提高风力发电机组的性能。
二、风力发电机组叶片结构优化叶片结构的优化是指在满足风力发电机组性能要求的前提下,通过设计优化方法,改善叶片的结构以提高发电效率、降低噪音和振动等。
以下是一些常见的叶片结构优化方法:1. 气动外形优化:通过改变叶片的气动外形,如增加扭曲、增加前缘粗度等,可以改善叶片的气动性能,提高风力发电机组的发电效率。
2. 结构优化:通过优化叶片的结构设计,如增加纤维层数、调整纤维布局等,可以提高叶片的强度和刚度。
此外,结构优化还可以减小叶片的自重,降低风力发电机组的启动风速。
3. 材料优化:选择适当的材料,如复合材料等,可以在不影响叶片强度的情况下,减小叶片的自重,进一步提高发电效率。
4. 多目标优化:针对叶片结构的多个性能指标,如发电效率、噪音和振动等,采用多目标优化方法,通过权衡不同指标之间的矛盾关系,寻找最优解。
风机叶片结构优化研究

风机叶片结构优化研究随着清洁能源的重要性日益提升,风力发电作为一种环保、可再生能源,成为了当今世界的热门话题。
在风力发电中,风机叶片是最为重要的一个部分,其结构和性能的优化直接影响着整个风力发电系统的效率和稳定性。
因此,风机叶片结构优化研究已成为了近年来风能行业中的一个热点。
一、风机叶片结构分析风机叶片的主要结构是由根部、尖部、前缘和后缘四个部分组成。
在评估叶片结构性能时,需要考虑的参数有:1. 叶片面积:叶片面积越大,单位面积上的风能转化效率越高。
2. 叶片厚度:叶片厚度影响着叶片的刚度和强度。
3. 叶片扭曲度:叶片扭曲度是指叶片在旋转时呈现的弯曲形态,影响着叶片的空气动力学性能和噪音特性。
4. 叶片弯曲度:叶片弯曲度是指叶片在其长度方向上呈现的弯曲形态,影响着叶片的空气动力学性能和重量分布。
5. 叶片材料:叶片材料的选择直接影响着叶片的刚度、强度以及生命周期。
6. 风机叶片尺寸:根据风机的输出功率需求和生产成本等因素,需要优化叶片尺寸。
在考虑了这些因素之后,我们可以进行一些叶片结构优化的尝试。
二、风机叶片结构优化方法1. 叶片多种材料复合结构为了提高叶片的强度、剛度和防腐蚀性等性能,多种材料的复合结构已经成为了一个研究热点。
比如,叶片根部可以使用高强度钢板,叶片尖部可以使用轻质材料,如碳纤维等。
2. 叶片形状优化叶片的形状对风能转化效率和噪音特性都有很大影响。
对于传统的三叶式风机而言,叶片朝向风的宽面应该被设计为凸面,而背风面则应设计成凹面,以便更好地利用风能。
同时,对于桨叶的设计也可以参考鸟翼等自然界中的弯曲形态,来减少气动阻力和噪音。
3. 叶片空气动力学优化在叶片旋转的同时,空气动力学力学效应会影响着叶片的性能。
由于每个点处叶片上的力都会互相影响,因此需要通过计算流体力学等方法来进行叶片空气动力学分析。
同时,在进行叶片设计时,需要考虑风的入射角度、旋转角速度等因素,以最大化叶片的风能转化效率。
风机叶片结构的优化组合设计

风机叶片结构的优化组合设计随着风能发电技术的日益成熟,风电设备的性能和效率备受关注。
而作为风力发电机组的核心部件之一,风机叶片的结构设计也越来越重要。
如何设计出更为优化的风机叶片结构,提高其效率和性能,是当前风电行业亟待解决的问题之一。
1. 风机叶片的基本结构和设计原理风机叶片一般由前缘、背缘、表面、厚度等多个结构参数组成。
其中,前缘是叶片前部呈锥形的部分,起到引向风的作用;背缘是在进风面后方的部分,对流场的倒流和升力产生作用;表面是叶片的外表面,决定了空气在叶片表面的流动特性;厚度则决定了叶片的强度和稳定性。
风机叶片的设计原理是在牢记风力机的机械特性的基础上,尽可能地提高叶片的性能,使叶片能够在不同的工况下运行,并保持高效率。
在设计叶片时需要考虑到以下几个方面:(1) 叶片气动特性的影响因素:在设计叶片的过程中,需要细致地分析气动学问题,探究风对叶片的冲击作用,以及叶片背面的气流和压力分布等问题。
(2) 叶片材料的优化选择:叶片材料的选用是叶片设计中最为重要的因素之一。
优选材料需要具备良好的机械性能、稳定性、抗风能力以及低温性能。
(3) 叶片形状和数量:叶片形状和数量是设计叶片的另外两个关键因素。
通过设计叶片的形状和数量,可以有效地优化叶片的气动性能、增加叶片的扭矩和升力等。
2. 风机叶片结构的优化设计方法在风机叶片的优化设计过程中,需要综合考虑叶片的材料、结构、气动特性等多个因素,并采取合适的设计方法。
下面简单介绍几种优化设计方法:(1) 基于计算流体力学的优化设计方法:计算流体力学是一种数值计算方法,可以模拟液体和气体的流动过程,对风机叶片进行流体力学分析,优化叶片厚度、弯曲情况等参数,提高叶片的效率和稳定性。
(2) 基于能量分析的优化设计方法:能量分析是一种分析方法,适用于计算风机叶片的能量转化效率。
通过对风机叶片的能量分析,确定叶片的气动特性和材料性能,从而实现优化设计。
(3) 基于人工智能的优化设计方法:人工智能技术逐渐被引入到工程设计领域,能够帮助设计师实现智能化设计。
风力发电机的叶片设计与优化
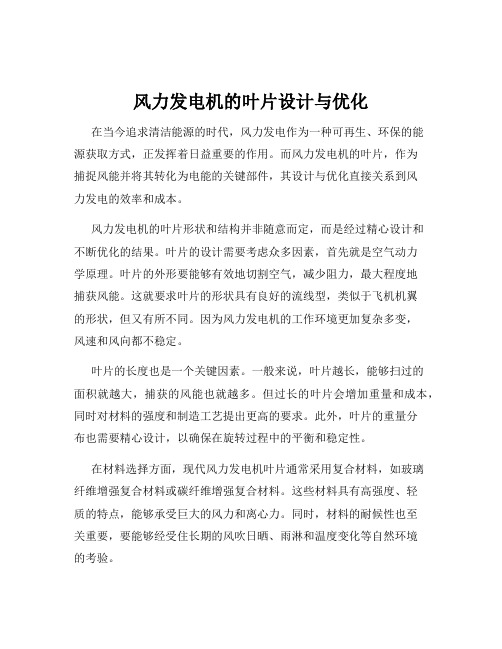
风力发电机的叶片设计与优化在当今追求清洁能源的时代,风力发电作为一种可再生、环保的能源获取方式,正发挥着日益重要的作用。
而风力发电机的叶片,作为捕捉风能并将其转化为电能的关键部件,其设计与优化直接关系到风力发电的效率和成本。
风力发电机的叶片形状和结构并非随意而定,而是经过精心设计和不断优化的结果。
叶片的设计需要考虑众多因素,首先就是空气动力学原理。
叶片的外形要能够有效地切割空气,减少阻力,最大程度地捕获风能。
这就要求叶片的形状具有良好的流线型,类似于飞机机翼的形状,但又有所不同。
因为风力发电机的工作环境更加复杂多变,风速和风向都不稳定。
叶片的长度也是一个关键因素。
一般来说,叶片越长,能够扫过的面积就越大,捕获的风能也就越多。
但过长的叶片会增加重量和成本,同时对材料的强度和制造工艺提出更高的要求。
此外,叶片的重量分布也需要精心设计,以确保在旋转过程中的平衡和稳定性。
在材料选择方面,现代风力发电机叶片通常采用复合材料,如玻璃纤维增强复合材料或碳纤维增强复合材料。
这些材料具有高强度、轻质的特点,能够承受巨大的风力和离心力。
同时,材料的耐候性也至关重要,要能够经受住长期的风吹日晒、雨淋和温度变化等自然环境的考验。
除了上述的基本设计要素,叶片的优化也是提高风力发电效率的重要手段。
优化可以从多个方面入手。
例如,通过优化叶片的表面粗糙度,可以减少空气阻力,提高风能的利用效率。
叶片的翼型优化也是常见的方法之一,通过不断调整翼型的参数,找到最佳的升阻比,从而提高风能的捕获能力。
在实际的设计和优化过程中,数值模拟技术发挥着重要作用。
工程师们可以利用计算机软件对不同的叶片设计方案进行模拟分析,预测其在不同风速和风向条件下的性能表现。
通过对比不同方案的结果,选择最优的设计方案。
但数值模拟也有其局限性,实际的风场环境非常复杂,模拟结果与实际情况可能存在一定的偏差。
因此,实验测试也是必不可少的环节。
实验测试可以在风洞中进行,也可以在实际的风电场中进行。
风力发电机组叶片设计及优化
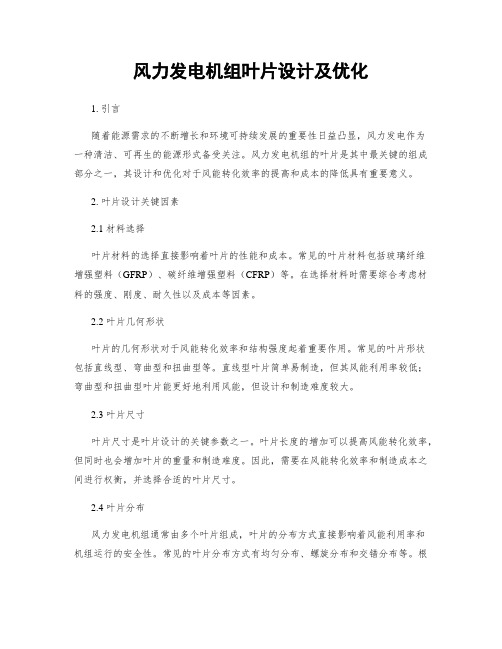
风力发电机组叶片设计及优化1. 引言随着能源需求的不断增长和环境可持续发展的重要性日益凸显,风力发电作为一种清洁、可再生的能源形式备受关注。
风力发电机组的叶片是其中最关键的组成部分之一,其设计和优化对于风能转化效率的提高和成本的降低具有重要意义。
2. 叶片设计关键因素2.1 材料选择叶片材料的选择直接影响着叶片的性能和成本。
常见的叶片材料包括玻璃纤维增强塑料(GFRP)、碳纤维增强塑料(CFRP)等。
在选择材料时需要综合考虑材料的强度、刚度、耐久性以及成本等因素。
2.2 叶片几何形状叶片的几何形状对于风能转化效率和结构强度起着重要作用。
常见的叶片形状包括直线型、弯曲型和扭曲型等。
直线型叶片简单易制造,但其风能利用率较低;弯曲型和扭曲型叶片能更好地利用风能,但设计和制造难度较大。
2.3 叶片尺寸叶片尺寸是叶片设计的关键参数之一。
叶片长度的增加可以提高风能转化效率,但同时也会增加叶片的重量和制造难度。
因此,需要在风能转化效率和制造成本之间进行权衡,并选择合适的叶片尺寸。
2.4 叶片分布风力发电机组通常由多个叶片组成,叶片的分布方式直接影响着风能利用率和机组运行的安全性。
常见的叶片分布方式有均匀分布、螺旋分布和交错分布等。
根据具体的场地条件和工程要求选择适合的叶片分布方式,以实现最佳的风能转化效率和机组运行稳定性。
3. 叶片设计流程3.1 需求分析在进行叶片设计之前,需要对工程需求进行全面分析,并明确设计目标。
包括风速范围、功率输出、机组尺寸等方面的要求。
3.2 叶片初始设计根据需求分析的结果,进行叶片的初始设计。
在设计中需要考虑叶片形状、尺寸和材料等因素,并使用适当的工具和软件进行建模和计算。
3.3 叶片力学分析对叶片的力学性能进行分析,包括受力分析、变形分析和疲劳寿命评估等。
这可以通过有限元分析等工具进行计算和模拟。
3.4 叶片优化设计根据叶片力学分析的结果,对叶片进行优化设计。
优化的目标包括提高风能利用率、减小叶片重量、增强叶片结构强度等方面。
风机叶片结构优化设计及性能分析

风机叶片结构优化设计及性能分析风机是一种将风能转化为机械能的装置,广泛应用于能源产业、环境保护和建筑领域。
风机的叶片结构是其重要组成部分,直接影响着风机的性能和效率。
因此,风机叶片结构的优化设计及性能分析是提高风机效率的关键。
首先,风机叶片结构的优化设计是指通过改进叶片的几何形状和构造参数,以达到最佳的风能利用效果。
优化设计应综合考虑叶片的强度、刚度和空气动力学性能等因素。
具体而言,优化设计可以从以下几个方面展开:1. 材料选择:风机叶片通常采用纤维增强复合材料制造。
不同的材料具有不同的强度和刚度特性,对叶片结构的优化设计产生重要影响。
在材料选择上,需要综合考虑成本、重量和力学性能等因素,以选择最合适的材料。
2. 几何形状设计:叶片的几何形状是影响风机性能的重要因素。
通常来说,叶片的横截面采用空气动力学优化曲线,如NACA翼型曲线。
此外,叶片的长度、扭转角度以及叶片的数量也需要根据具体的应用需求进行优化设计。
3. 加筋设计:为了增加叶片的强度和刚度,通常在叶片上设置加筋。
加筋的设计应考虑叶片的应力分布和受力情况,以提高叶片的抗弯、抗扭能力。
同时,在加筋的设计上还需注意减少结构的重量,以提高整体的轻量化效果。
其次,对风机叶片结构的性能进行分析是优化设计的重要环节。
通过性能分析,可以评估叶片在不同工况下的风能捕获能力、机械功率输出以及动力学响应等指标。
1. 流场分析:利用计算流体力学(CFD)方法,可以对风机叶片在流场中的行为进行数值模拟。
通过模拟结果,可以分析叶片的速度分布、压力分布和阻力分布等情况,从而优化叶片的气动设计。
2. 力学分析:在风机运行过程中,叶片会受到风荷载的作用,因此需要进行强度和刚度的力学分析。
通过有限元分析方法,可以模拟叶片的受力情况,预测叶片的应力分布和变形情况。
在分析中,还可以考虑动力学响应,以确保叶片在各种工况下的稳定性和可靠性。
综上所述,风机叶片结构的优化设计及性能分析是提高风能转化效率的关键。
某型风力发电机叶片结构优化设计
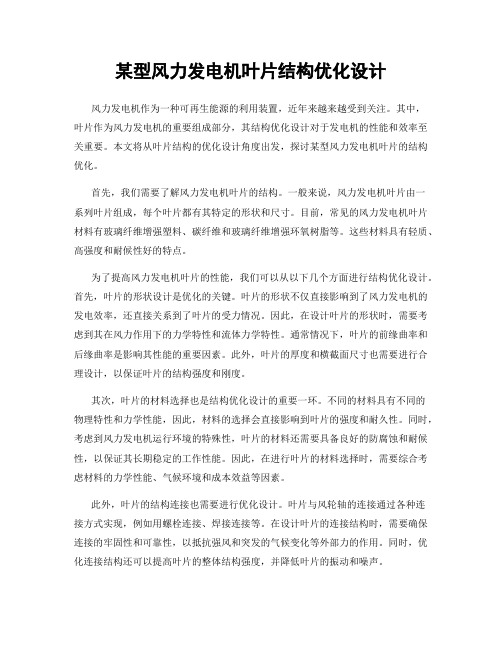
某型风力发电机叶片结构优化设计风力发电机作为一种可再生能源的利用装置,近年来越来越受到关注。
其中,叶片作为风力发电机的重要组成部分,其结构优化设计对于发电机的性能和效率至关重要。
本文将从叶片结构的优化设计角度出发,探讨某型风力发电机叶片的结构优化。
首先,我们需要了解风力发电机叶片的结构。
一般来说,风力发电机叶片由一系列叶片组成,每个叶片都有其特定的形状和尺寸。
目前,常见的风力发电机叶片材料有玻璃纤维增强塑料、碳纤维和玻璃纤维增强环氧树脂等。
这些材料具有轻质、高强度和耐候性好的特点。
为了提高风力发电机叶片的性能,我们可以从以下几个方面进行结构优化设计。
首先,叶片的形状设计是优化的关键。
叶片的形状不仅直接影响到了风力发电机的发电效率,还直接关系到了叶片的受力情况。
因此,在设计叶片的形状时,需要考虑到其在风力作用下的力学特性和流体力学特性。
通常情况下,叶片的前缘曲率和后缘曲率是影响其性能的重要因素。
此外,叶片的厚度和横截面尺寸也需要进行合理设计,以保证叶片的结构强度和刚度。
其次,叶片的材料选择也是结构优化设计的重要一环。
不同的材料具有不同的物理特性和力学性能,因此,材料的选择会直接影响到叶片的强度和耐久性。
同时,考虑到风力发电机运行环境的特殊性,叶片的材料还需要具备良好的防腐蚀和耐候性,以保证其长期稳定的工作性能。
因此,在进行叶片的材料选择时,需要综合考虑材料的力学性能、气候环境和成本效益等因素。
此外,叶片的结构连接也需要进行优化设计。
叶片与风轮轴的连接通过各种连接方式实现,例如用螺栓连接、焊接连接等。
在设计叶片的连接结构时,需要确保连接的牢固性和可靠性,以抵抗强风和突发的气候变化等外部力的作用。
同时,优化连接结构还可以提高叶片的整体结构强度,并降低叶片的振动和噪声。
此外,叶片的表面涂层和防污措施也是结构优化的重要组成部分。
叶片表面的涂层可以提高其抗风化和耐腐蚀性能,并减少静电积聚。
另外,采用防污措施可以防止叶片表面积聚尘土和沙尘等杂质,减少表面粗糙度,进一步提高风力发电机的转速和产能。
GFRP风机叶片结构设计的二级优化方法
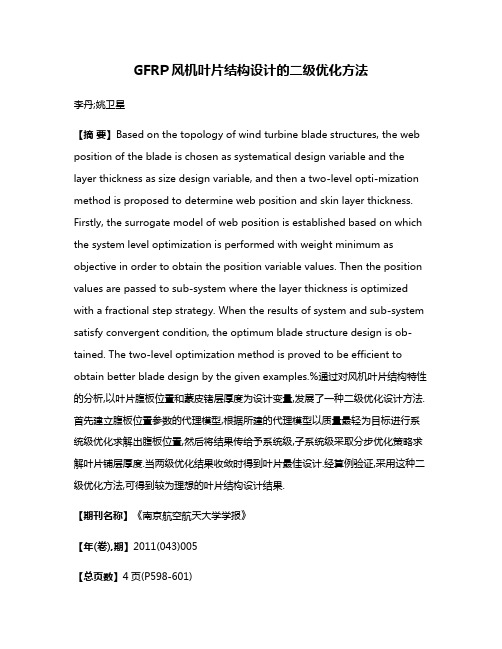
GFRP风机叶片结构设计的二级优化方法李丹;姚卫星【摘要】Based on the topology of wind turbine blade structures, the web position of the blade is chosen as systematical design variable and the layer thickness as size design variable, and then a two-level opti-mization method is proposed to determine web position and skin layer thickness. Firstly, the surrogate model of web position is established based on which the system level optimization is performed with weight minimum as objective in order to obtain the position variable values. Then the position values are passed to sub-system where the layer thickness is optimized with a fractional step strategy. When the results of system and sub-system satisfy convergent condition, the optimum blade structure design is ob-tained. The two-level optimization method is proved to be efficient to obtain better blade design by the given examples.%通过对风机叶片结构特性的分析,以叶片腹板位置和蒙皮锗层厚度为设计变量,发展了一种二级优化设计方法.首先建立腹板位置参数的代理模型,根据所建的代理模型以质量最轻为目标进行系统级优化求解出腹板位置,然后将结果传给予系统级,子系统级采取分步优化策略求解叶片铺层厚度.当两级优化结果收敛时得到叶片最佳设计.经算例验证,采用这种二级优化方法,可得到较为理想的叶片结构设计结果.【期刊名称】《南京航空航天大学学报》【年(卷),期】2011(043)005【总页数】4页(P598-601)【关键词】风机叶片;结构设计;二级优化方法;屈曲【作者】李丹;姚卫星【作者单位】南京航空航天大学飞行器先进设计技术重点学科实验室,南京,210016;南京航空航天大学飞行器先进设计技术重点学科实验室,南京,210016【正文语种】中文【中图分类】TU318叶片是风机设备的关键部件之一,从成本上看,其制造成本约占风机总成本的 15%~25%;从性能上看,风力机捕获风能的多少与风轮直径的平方成正比[1]。
复合材料风力机叶片结构设计2

c ss tn aoe su u suib d m s fp ns l sf e , r se i o bv to c r , l e sl sf e , t ns o - co f w t te n a a , t s a i s r t a i g t s n f e ad i sf e , etg ehn a pr e r b d o i s f s n a a t ns r cn m cail a t o l e ro t n s x l i i s e i l f c a m e f a sutap pr sw r c cle b Peo p e cd p g m i w tc r r ei, e u t y cm a e e r w c a r u l t e a ad r o e l r f o r a h h o s
的强度和刚度,有效降低了叶片的重量。同时也对复合材料叶片的结构设计起 到了良 好的指导作用。文中的方法同样适用于其它复合材料复杂结构的极限分 析与强度设计。 关键词:桥联模型,复合材料风机叶片,极限分析,强度设计
Ab sic at t a
uia fle li nt a fqec cl li ad bi a s o a l t au aa s a r r uny c ao n s i a l i f t e r n ys u l m i e a u tn t l n y s a t y 2k ad k cm oi wn t b e d. u aeya k cm oi 0W 60W pse d i b eS lni, 6 W pse n 6 o t i u n l r a i t t 60 m o t wn tb e d wtto c r w s nd aa zd O e s l i u i b e h sut e a d i e ad l e. o ihlw d n l i w t u s e g n n y r a r s n f oo
- 1、下载文档前请自行甄别文档内容的完整性,平台不提供额外的编辑、内容补充、找答案等附加服务。
- 2、"仅部分预览"的文档,不可在线预览部分如存在完整性等问题,可反馈申请退款(可完整预览的文档不适用该条件!)。
- 3、如文档侵犯您的权益,请联系客服反馈,我们会尽快为您处理(人工客服工作时间:9:00-18:30)。
序的准确性[ 2-3] 。气动几何外形确定后, 再考虑结构 形式的选择, 包括叶片剖面拓扑形状及尺寸设计 等[ 4] 。由于风机叶片大量使用复合材料[ 5] , 结构优化 很大程度上是层合板铺层设计。叶片的气动-结构耦 合优化设计通常采用多学科优化设计策略[ 6-9] 。
本文针对给定气动外形和所受载荷的叶片, 在 分析叶片结构特点的基础上, 选择双腹板式叶片剖 面结构形式, 提出了二级优化方法, 设计叶片腹板 位置和铺层厚度。
料密度分别为 , GFRP PVC , U D, 为使结构在满足稳定
性紧约束的同时不违背变形约束, 控制调整后各铺
层厚度不小于第一步变形约束优化所得各层厚度,
故准则法优化铺层厚度等效为解下述优化问题
m in m =
GFRPt′ 1 +
PVCt ′ 2 +
t′
UD 3
s . t . D ′= E UD t′ 33 + E GFRP[ ( t′ 1 + t ′ 2) 3 - t ′ 23] =
Abstract: Based on t he to polo gy o f w ind t ur bine blade st ructures, t he w eb po sit io n o f t he blade is chosen as sy st emat ical desig n variable and t he layer t hickness as size desig n v ariable, and t hen a t w o-level opt imizat ion met hod is pro posed to det ermine w eb positio n and skin layer t hickness. F ir st ly , t he surr ogat e model of web posit ion is est ablished based on w hich the system level opt imizat io n is perf orm ed w it h w eig ht minim um as object iv e in order t o o bt ain t he position variable v al ues. T hen t he posit ion values are passed t o sub-sy st em w here the layer t hickness is optim ized w it h a fract io nal step st rat eg y. When t he result s of syst em and sub-syst em sat isf y convergent conditio n, t he o pt imum blade st ruct ur e design is obtained. T he t w o-level o pt imizat ion m et hod is pr oved to be eff icient t o o bt ain bet t er blade design by t he given exam ples. Key words: w ind t urbine blade; st ruct ur e desig n; t w o-level opt im izat io n method; buckling
第 43 2 01 1
卷第 年 10
5月期
南 京 航 空 航 天 大 学 学 报
Journal of N anjing U niversit y of Aero nautics & Ast ronau
tics
V ol. O
43 ct .
No. 2 01
5 1
GFRP 风机叶片结构设计的二级优化方法
Two-Level Optimization for GFRP Wind Turbine Blade Structural Design
L i Dan, Y ao W ei x ing
( K ey Labo rat or y o f Fundamental Science of A dv anced Desig n T echno lo gy of F light Vehicle, N anjing U niver sity of A ero naut ics & A stro naut ics, N anjing , 210016, China)
复合材料, 为提高叶片截面刚度, 蒙皮从外向内的 铺 层 顺序 设 计为 单 向玻 璃纤 维 增强 复 合材 料/ P VC/ 双轴向玻璃纤维增强复合材料, 以减小结构 的弯曲变形。
( 2) 设计约束 结构约束包括变形、强度、稳定性和工艺性四 个方面: ( a) 叶尖最大变形不超过叶片展长的10% , 与腹板位置关系不大, 主要由叶片蒙皮整体铺层布 置 决定; ( b) 考虑载荷和材料的分散性, 叶片的屈 曲临界载荷不小于正常使用载荷的 1. 1 倍, 失稳一 般发生在局部, 叶片的屈曲因子除受腹板位置影响 外, 更多的由局部蒙皮铺层厚度决定; ( c) 工艺上要 求叶片沿展向相邻区域铺层厚度不宜相差过大, 可 通过增设叶片展向分区来满足; ( d) 各分区按最大 应力强度准则不发生失效。 ( 3) 设计目标 以风机叶片质量最轻为优化目标, 在腹板位置 变量 p 1 , p 2 确定的条件下, 风机质量为叶片各铺层 厚度的线性函数。 ( 4) 构造二级优化设计方法 根据以上对设计变量和约束的分析, 构造二级 优化方法如下: 首 先, 以腹板位置 p 1 , p 2 为系统设计变量, 采用 全因子设计试验法确定样本点, 应用参数化建模技术 建立结构尺寸优化的有限元模型, 求各腹板位置下满 足结构设计约束的叶片最轻质量, 建立系统级代理模 型; 然后根据所建的代理模型以质量最轻为目标进行 系统级优化求解腹板位置, 并将结果传给子系统级, 子系统级优化给定腹板位置下的叶片铺层厚度。其 次, 比较子系统级与系统级优化得到的叶片质量, 若 两者误差在5% 以内, 认为收敛, 迭代结束, 子系统级 所得结果即为最佳叶片设计; 若两者误差在5% 以上, 将子系统级结果作为新的样本点, 更新代理模型, 重 新进行系统级优化, 继续迭代至收敛。 在优化给定腹板位置下叶片最轻质量时, 根据 对各约束的分析, 采取分步优化策略。第一步, 以变 形为约束, 采用数学规划法-改进的可行方向法优 化叶片各铺层厚度; 第二步, 以第一步优化结果为 初值, 以稳定性为紧约束, 采用准则法优化叶片局 部失稳区域的铺层厚度。图 2 为优化流程图。 1. 2. 2 代理模型技术 为得到最佳叶片质量关于腹板位置变量的整 体 分 布关 系, 采用 均 匀全 因 子设 计 方法 取 实验 点[ 11] ; 且各特征量水平数较大, 故代理模型取插值 类代理模型。三次样条插值在给出的样本点之间具 有二阶连续导数, 光滑性较好, 故插值方法取样条 插值[ 12] 。
第5 期
李 丹, 等: G F RP 风机叶片结构设计的二级优化方法
59 9
1 二级优化设计方法
1. 1 叶片结构特点 风力机所受载荷比较复杂, 叶片作为转化风能 的主要部件, 承受大部分气动载荷和惯性载荷。从 整体上看, 叶片是一个细长的悬臂梁, 弯矩是其主 要载荷。为提高截面弯扭刚度, 防止局部失稳, 叶片 剖面主要采用主梁加气动外壳的三闭室结构形式, 见图 1。
叶片是风机设备的关键部件之一, 从成本上 看, 其制造成本约占风机总成本的 15% ~25% ; 从 性能上看, 风力机捕获风能的多少与风轮直径的平 方成正比[ 1] 。因此, 叶片的优化设计是极为重要的。
为达到最佳气动性能, 叶片设计优先考虑气动 外形, 近年来国内外在兆瓦级大型风机上都研发有 翼型设计分析程序, 以气动性能最佳为目标, 综合运 用传统的数学优化方法和现代优化方法, 优化叶片 各翼型参数, 并不断通过风洞试验验证提高设计程
图 1 叶片剖面形式
大型化是叶片发展的重要趋势。随着功率的增 大, 叶片越来越长, 自重越来越大。对 10~60 m 叶 片的统计研究表明, 叶片质量 按长度的三次方增 加。在风机运行时, 叶片自重会产生交变载荷, 对风 机运行、疲劳寿命和能量输出等有重要影响, 以致 传统材料不能满足大型机组对叶片强度和刚度的 要求。在这种情况下, 复合材料成为叶片材料的必 然选择。长度 50 m 以下的叶片结构材料一般以单 向玻璃纤维增强复合材料为主, 承受大部分弯曲载 荷, 并铺设部分双轴向玻璃纤维增强复合材料, 承 受扭转载荷。为增强屈曲稳定性, 夹芯材料PVC 泡 沫也有大量应用。当叶片长度大于50 m 时, 玻璃纤 维复合材料已不能满足叶片的强度和刚度要求而 改用碳纤维复合材料。目前全碳纤维的叶片应用较 少, 多以混杂复合材料应用为主[ 10 ] 。
60 0
南 京 航 空 航 天 大 学 学 报
第 43 卷
D=
E
U
Dt
3 3
+
EGFRP[ ( t 2 +
t1) 3 -
t32 ]
A = E U Dt3 + E GFR Pt 1
( 2)
式中 EU D、E GFRP 分别为 GF RP -U D 和 G FR P±45 的
材料模量。
设优化后此区域铺层厚度变为t ′ 1, t ′ 2, t ′ 3, 对应材
基金项目: 国家重点基础研究发 展计划( “九七三”计划) ( 2007CB714600) 资助项 目; 江 苏高校 优势学 科建设工 程资助 项目。
收稿日期: 2011-04-27; 修订日期: 2011-07-13 通讯作者: 姚卫星, 男, 教授, 博士 生导师, 1957 年 1 月生, E -mail: w x yao @ nuaa . edu. cn。