基于hyperworks的车身碰撞
整车碰撞后处理作业指导书Hyperview

1 正面刚性墙,偏置碰撞后处理以下后处理主要是基于hyperview和hypergraph完成。
其中hyperview可对图像做处理,而hypergraph可对曲线做处理。
打开hyperview:在hyperview模式下,读入d3plot文件:播放动画,使得所有相关的d3pllot文件都读入到hyperview中来。
之后,动画进度条会从undeformed更新为时间。
1.1总体变形图正碰中,一般截取0ms,20ms,40ms,60ms,80ms,100ms这六个时刻的整车变形图。
偏置碰撞中,一般截取0ms,20ms,40ms,60ms,80ms,100ms,120ms这七个时刻的整车变形图。
通过改变该值来输出不同时刻的图片。
参考:1.2 前纵梁变形图正碰中,一般截取0ms,20ms,40ms,60ms,80ms,100ms这六个时刻的纵梁变形图。
偏置碰撞中,一般截取0ms,20ms,40ms,60ms,80ms,100ms,120ms这七个时刻的纵梁变形图。
用这些命令,把纵梁单独显示出来。
(注意按住shift可以片选)参考:1.3 能量曲线(1)切换到hypergraph模式,读入glstat文件(2)选择需要输出的能量(动能,内能,滑移能,总能),点击apply。
(3)沙漏能:在ls-dyna自带的前后处理软件lsprepost里处理,如下:打开lsprepost程序:读入glstat文件:选择沙漏能hourglass energy,点击plot在弹出的对话框,点击save。
在弹出的对话框中,选择输出类型为msoft csv格式,浏览路径,输入文件名,再点击save即可。
同上,可以在hypergraph模式下打开上面保存的沙漏能文件,然后输出曲线。
(4)需要输出的五个能量:(5)沙漏能和总能比例:点击以下图标,切换到曲线编辑。
用Add新增曲线,切换到math,选择横坐标(时间)和纵坐标(沙漏能/总能),点击apply即可。
应用Hypermesh软件进行汽车座椅强度及碰撞仿真分析

应用Hypermesh软件进行汽车座椅强度及碰撞仿真分析随着汽车工业现代化技术的发展,汽车广泛的进入人们生活中,而汽车座椅做为与人体直接接触的部件,其舒适性和安全性的重要程度是不言而喻的。
本文应用Hypermesh软件对汽车座椅静强度及碰撞及逆行有限元仿真分析,以供参考。
标签:汽车座椅;强度;碰撞;有限元仿真分析引言近年来,随着汽车保有量的增加,汽车道路交通事故呈逐年上升趋势。
在这些事故中,座椅作为减少损伤的安全部件对乘员起到了决定性的保护作用,使其成为汽车安全性研究中的重要部件。
采用有限元仿真技术,对座椅靠背进行静强度以及碰撞冲击强度分析,可减少开发过程中设计、试验、分析和评价循环的成本,缩短研究时间。
GB15083-2006标准中要求:当座椅处于制造厂所规定的正常使用位置时,构成行李舱的座椅靠背或头枕应具有足够的强度以保护乘员不因行李的前移而受到伤害。
试验的过程中及试验后,如果座椅及其锁止装置仍保持在原位置,则认为满足此要求。
一、汽车座椅有限元模型的建立(一)、搭建模型:用Hypermesh中的提取中面功能,抽取中面建立有限元模型,搭建被测汽车座椅骨架模型和地板模型,在不影响正常分析结果的前提下适当简化了运算模型,见图1。
图1 座椅强度分析的有限元模型其中座椅骨架采用壳单元进行网格划分,采用单元长度基准为10mm、最小单元长度不小于5mm、最大单元长度不大于13mm的规则来划分网格。
各钣金件之间的焊点和螺栓用刚性连接模拟。
建立的有限元模型共有节点个28640,壳单元23477个,体单元7718个,刚性连接694个。
利用ANSA软件LS-DYNA 模块对图1所示模型进行边界条件的加载及其属性(材料参数和厚度)定义,其中座椅骨架所用材料及厚度、直径见表1。
模型的加载过程按照标准GB15083-2006中的要求进行,发生碰撞前,行李箱模块以50km/h的初速度做减速运动,减速度为20g。
表1 座椅骨架材料(二)、边界条件的确定在进行座椅强度分析时,根据座椅与车身地板的连接形式和安装位置,在座椅骨架中锁柄连接处以及靠背与车身地面的铰接处施加约束。
基于HyperWorks/LS—Dyna的车辆事故原因分析

· 19 ·
设 计 一礤 究
汽车科技第1期2010年1月
1 模 型 建 立
目前 成 熟 的 CAE技 术 已经 贯 穿 汽 车领 域 整 个 生产 链 ,包 括前 期 的产 品开 发 ,零 件 静 强度 、模 态 分 析 ,车 辆被 动安 全设计 以及 后期产 品检 验 、改进
力模 型建 立 与 分析 :(6)驾驶 员操 作 策 略 与 行 为推 定。 其 中 (2)、(4)、(5)为研 究热 点 ,事 故再 现模 型 的 建立 是技 术难 点
本文 在 HyperWorks软 件 平 台中搭 建事 故模 型 . 从 有 限元模 拟 的 角度 出发 .利用 LS—Dyna软 件动 态 仿 真达 到 事故再 现 的 目的 。为事故 鉴定 提供 一种 新 的 方 法 。 事 故 再 现 仿 真 方 法 流 程 如 图 1所 示 。
ment model in HyperWorks,using the 一Oyna nonlinear large deformation f inite element simulation technolog y ,the dy— namic process o f reproduction traffic accidents,to analyze why the passive sa f ety devices failure, provide a theoretical basis for Identif ication of accidents.This method can provides a new thread about the identification of trafic accidents. K ey w ords:HyperW orks;I5一Dyna;simulation of vehicle accident
Hyperstudy在轿车正面碰撞优化分析中的应用
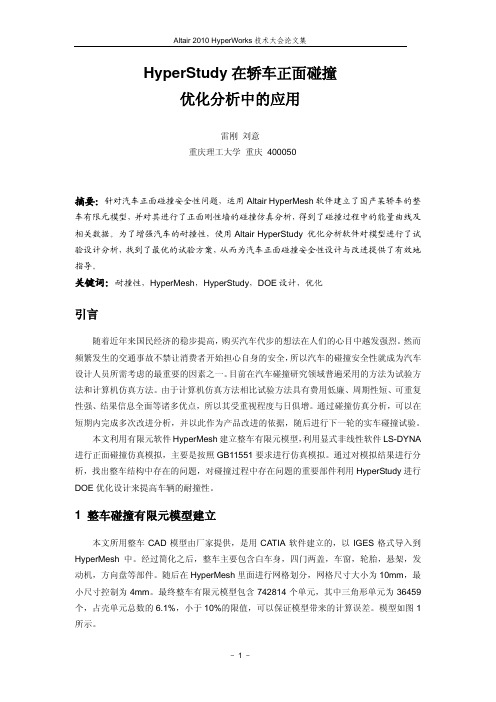
HyperStudy在轿车正面碰撞优化分析中的应用雷刚刘意重庆理工大学重庆400050摘要:针对汽车正面碰撞安全性问题,运用Altair HyperMesh软件建立了国产某轿车的整车有限元模型,并对其进行了正面刚性墙的碰撞仿真分析,得到了碰撞过程中的能量曲线及相关数据。
为了增强汽车的耐撞性,使用Altair HyperStudy 优化分析软件对模型进行了试验设计分析,找到了最优的试验方案,从而为汽车正面碰撞安全性设计与改进提供了有效地指导。
关键词:耐撞性,HyperMesh,HyperStudy,DOE设计,优化引言随着近年来国民经济的稳步提高,购买汽车代步的想法在人们的心目中越发强烈。
然而频繁发生的交通事故不禁让消费者开始担心自身的安全,所以汽车的碰撞安全性就成为汽车设计人员所需考虑的最重要的因素之一。
目前在汽车碰撞研究领域普遍采用的方法为试验方法和计算机仿真方法。
由于计算机仿真方法相比试验方法具有费用低廉、周期性短、可重复性强、结果信息全面等诸多优点,所以其受重视程度与日俱增。
通过碰撞仿真分析,可以在短期内完成多次改进分析,并以此作为产品改进的依据,随后进行下一轮的实车碰撞试验。
本文利用有限元软件HyperMesh建立整车有限元模型,利用显式非线性软件LS-DYNA 进行正面碰撞仿真模拟,主要是按照GB11551要求进行仿真模拟。
通过对模拟结果进行分析,找出整车结构中存在的问题,对碰撞过程中存在问题的重要部件利用HyperStudy进行DOE优化设计来提高车辆的耐撞性。
1 整车碰撞有限元模型建立本文所用整车CAD模型由厂家提供,是用CATIA软件建立的,以IGES格式导入到HyperMesh中。
经过简化之后,整车主要包含白车身,四门两盖,车窗,轮胎,悬架,发动机,方向盘等部件。
随后在HyperMesh里面进行网格划分,网格尺寸大小为10mm,最小尺寸控制为4mm。
最终整车有限元模型包含742814个单元,其中三角形单元为36459个,占壳单元总数的6.1%,小于10%的限值,可以保证模型带来的计算误差。
基于HyperWorks—Radioss的轿车前保险杠100%正面碰撞仿真分析
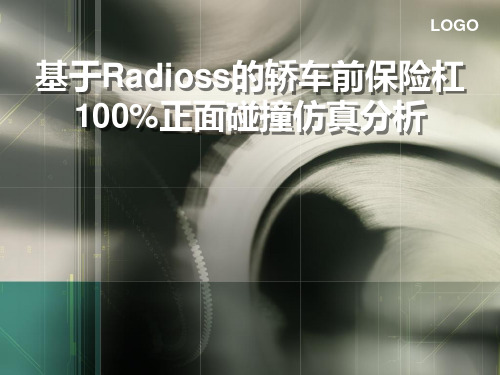
4.设置仿真计算和结果输出参数
4.1 设置仿真计算参数
4.设置仿真计算和结果输出参数
4.2 设置结果输出参数
5.求解并查看碰撞仿真分析结果
5.1 Radioss求解器及求解过程
5.求解并查看碰撞仿真分析结果
5.2 动态可视化保险杆100%正面碰撞过程
5.求解并查看碰撞仿真分析结果
5.3 动态可视化塑性应变云图
5.求解并查看碰撞仿真分析结果
5.6 动态可视化等效应力云图(单型的建立
1.2 导入模型有限元单元文件
此处导入的是包含模型网格单元信息的*nas文件
1.有限元分析模型的建立
1.3 定义分析模型的材料和属性
2.定义保险杠在正碰过程中的工况
2.1 创建保险杠基部刚体
创建连接保险杠基部的刚体,并对刚体的运动方向进行约束, 用来模拟正碰过程中车身与保险杠连接的力学关系特性。
2.3 定义碰撞过程中的速度
为了更加真实的模拟保险杆100%正面碰撞过程,在仿真分析 中引入实车碰撞过程中的碰撞速度。根据实车碰撞情况创建速 度变化曲线来定义保险杆在碰撞仿真过程中的碰撞速度大小
2.定义保险杠在正碰过程中的工况
2.3 定义碰撞过程中的速度
根据实车碰撞情况来定义保险杆正碰的速度方向
2.定义保险杠在正碰过程中的工况
2.1 创建保险杠基部刚体
根据保险杠在正碰过程中的实际运动方向来对基部刚体的运动 方向进行约束
2.定义保险杠在正碰过程中的工况
2.2 创建刚性连接
创建防撞横梁与吸能盒之间的刚性连接,用来定义部件之间的 焊接关系,来模拟实际碰撞过程中不同部件之间的力学关系
2.定义保险杠在正碰过程中的工况
LOGO
12_基于恶劣工况下的纯电动车碰撞安全仿真与评估
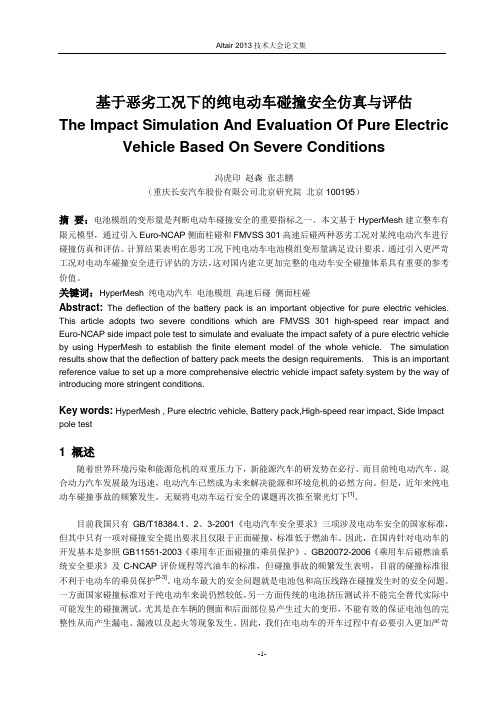
基于恶劣工况下的纯电动车碰撞安全仿真与评估The Impact Simulation And Evaluation Of Pure Electric Vehicle Based On Severe Conditions冯虎印赵森张志鹏(重庆长安汽车股份有限公司北京研究院北京100195)摘要:电池模组的变形量是判断电动车碰撞安全的重要指标之一。
本文基于HyperMesh建立整车有限元模型,通过引入Euro-NCAP侧面柱碰和FMVSS 301高速后碰两种恶劣工况对某纯电动汽车进行碰撞仿真和评估。
计算结果表明在恶劣工况下纯电动车电池模组变形量满足设计要求。
通过引入更严苛工况对电动车碰撞安全进行评估的方法,这对国内建立更加完整的电动车安全碰撞体系具有重要的参考价值。
关键词:HyperMesh 纯电动汽车电池模组高速后碰侧面柱碰Abstract: The deflection of the battery pack is an important objective for pure electric vehicles. This article adopts two severe conditions which are FMVSS 301 high-speed rear impact and Euro-NCAP side impact pole test to simulate and evaluate the impact safety of a pure electric vehicle by using HyperMesh to establish the finite element model of the whole vehicle. The simulation results show that the deflection of battery pack meets the design requirements. This is an important reference value to set up a more comprehensive electric vehicle impact safety system by the way of introducing more stringent conditions.Key words: HyperMesh , Pure electric vehicle, Battery pack,High-speed rear impact, Side Impact pole test1 概述随着世界环境污染和能源危机的双重压力下,新能源汽车的研发势在必行。
74-基于HyperMesh的车身模态分析[1]
![74-基于HyperMesh的车身模态分析[1]](https://img.taocdn.com/s3/m/759f5b8da0116c175f0e4843.png)
基于HyperMesh 的车身模态分析王得刚 赵春雨 闻邦椿(东北大学机械工程与自动化学院 辽宁沈阳 110004)摘要摘要::应用先进的有限元前后处理软件HyperMesh,采用全新的建模方法,对车身结构进行有限元建模,用MSC.Nastran 软件对模型求解,然后用HyperMesh 对计算结果进行后处理分析。
通过对车身的结构进行有限元模态分析,得到在低频范围内与试验结果基本一致的模态频率和振型,有利于控制车身的固有特性,从而可以对车身设计方案进行全面的评价和改进。
关键词关键词::HyperMesh;车身;模态分析Modal Analysis of Car-body on the Basis of HyperMeshAbstract :Adopted a new modeling method, the finite element modal of car-body is established by HyperMesh, which is an advanced preprocess and postprocess software to finite element. The modal is calculated by MSC.Nastran software. Calculated result is post-progressed by HyperMesh. The modal frequency and mode shape can be gained through the modal analysis of the car-body. The result using FEM is consistent with test result in low frequencies, so it can help controlling the inherent performance of the car-body. Consequently, the result can be used in estimating and improving the design project of the car-body.Key words :HyperMesh ;car-body ;modal analysis1 1 前前言对于实际结构进行模态分析,可从固有频率和振型中得到其发生共振的频率信息和振动形态信息,这对合理地设计车身结构,使其具有良好的动态性能指标,以及解决结构上出现的动态性能缺陷问题具有重要的指导意义。
基于HyperMesh的行人保护碰撞区域划分方法

基于HyperMesh的行人保护碰撞区域划线方法冯亚玲高鹏飞苏成谦天津一汽夏利汽车股份有限公司产品开发中心摘要:行人保护碰撞法规中的碰撞区域由几条重要基准线组成。
本文以某款车为例,详细阐述了运用HyperMesh相关命令手动划线的方法,并介绍了自主开发的自动划线程序。
碰撞区域基准线是空间连续曲线,在HyperMesh中操作必须曲线离散化,分析基准线的几何关系,定制辅助线模板文件,通过正确的操作命令,可以提高划线的效率。
基于手动划线方法的思路,开发的自动划线程序可以简化划线操作。
关键词:行人保护碰撞区域,HyperMesh,侧面基准线,WAD,发动机罩后面基准线1 概述2009年我国发布了汽车对行人的碰撞保护法规(GB/T 24550-2009),行人保护已成为汽车安全领域发展的一个热点。
在行人碰撞CAE分析中,碰撞区域的准确划分是一项关键技术。
在车身造型设计阶段,必须基于精确的碰撞区域进行造型评估,快速绘制碰撞区域基准线成为CAE分析的前提条件。
法规定义的基准线包括:发动机罩前缘基准线、发动机罩后面基准线、侧面基准线、保险杠上部基准线、保险杠下部基准线、包络线(WAD1000及WAD1700)。
其中有几条基准线的划线方法一致。
本文结合某款车区域划分实例,重点介绍HyperMesh软件绘制侧面基准线、WAD和后面基准线的方法,并对比了手动划线和自动划线的结果。
研究表明,基于HyperMesh可以实现用程序自动划线,采用正确方法也可以用手动方法快速划分区域。
2 手动划线方法截取车身前部结构的模型,包括发动机罩外板、翼子板、保险杠、大灯表面、散热器罩、通风盖板、风挡玻璃等等,可以用Surface模型或是Mesh模型(需偏置到外表面)。
建议采用rigid body mesh划分的网格模型,特征能完整保留、而且在HyperMesh操作快捷。
为提高划线操作的效率,根据基准线定义,创建统一的辅助线模板文件。
以下分别详解侧面基准线、包络线(WAD线)和发动机罩后面基准线的划线步骤。
基于hyperworks的校车车身骨架结构分析
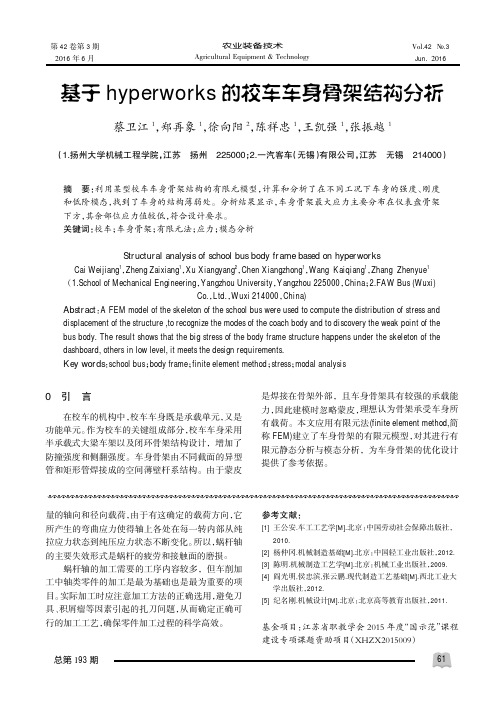
量的轴向和径向载荷,由于有这确定的载荷方向,它所产生的弯曲应力使得轴上各处在每一转内部从纯拉应力状态到纯压应力状态不断变化。
所以,蜗杆轴的主要失效形式是蜗杆的疲劳和接触面的磨损。
蜗杆轴的加工需要的工序内容较多,但车削加工中轴类零件的加工是最为基础也是最为重要的项目。
实际加工时应注意加工方法的正确选用,避免刀具、积屑瘤等因素引起的扎刀问题,从而确定正确可行的加工工艺,确保零件加工过程的科学高效。
参考文献:[1]王公安.车工工艺学[M].北京:中国劳动社会保障出版社,2010.[2]杨仲冈.机械制造基础[M].北京:中国轻工业出版社,2012.[3]陈明.机械制造工艺学[M].北京:机械工业出版社,2009.[4]阎光明,侯忠滨,张云鹏.现代制造工艺基础[M].西北工业大学出版社,2012.[5]纪名刚.机械设计[M].北京:北京高等教育出版社,2011.基金项目:江苏省职教学会2015年度“国示范”课程建设专项课题资助项目(XHZX2015009)0引言在校车的机构中,校车车身既是承载单元,又是功能单元。
作为校车的关键组成部分,校车车身采用半承载式大梁车架以及闭环骨架结构设计,增加了防撞强度和侧翻强度。
车身骨架由不同截面的异型管和矩形管焊接成的空间薄壁杆系结构。
由于蒙皮是焊接在骨架外部,且车身骨架具有较强的承载能力,因此建模时忽略蒙皮,理想认为骨架承受车身所有载荷。
本文应用有限元法(finite element method,简称FEM)建立了车身骨架的有限元模型,对其进行有限元静态分析与模态分析,为车身骨架的优化设计提供了参考依据。
基于hyperworks 的校车车身骨架结构分析蔡卫江1,郑再象1,徐向阳2,陈祥忠1,王凯强1,张振越1(1.扬州大学机械工程学院,江苏扬州225000;2.一汽客车(无锡)有限公司,江苏无锡214000)摘要:利用某型校车车身骨架结构的有限元模型,计算和分析了在不同工况下车身的强度、刚度和低阶模态,找到了车身的结构薄弱处。
石朝亮_基于HyperWorks白车身灵敏度分析及结构优化

式中,X=x1,x2,...,xn 是设计变量, f ( X ) 是目标函数, g ( X ) 是不等式约束函数, h( X ) 是等式约束函数,上角标 L 指 Lower Limit,即下限,上角标 U 指 Upper Limit,即上限。
-6-
-1-
Altair 2012 HyperWorks 技术大会论文集
2 优化分析理论
灵敏度分析与计算是结构优化设计中时常面临的问题。灵敏度作为导数信息,反映出结构 设计变量或参数的改变对目标或约束函数的影响程度,利用它可以确定最优解的搜索方向,建立 近似方程或构造优化迭代计算公式以及进行结构设计修改。 对于有限元方程 两边对设计变量 X 求偏导数:
5 结论
(1)通过优化,实现材料在车身上的重新分布,在扭转刚度和一阶扭转模态略有提高的 情况下白车身实现减重 5.8kg; (2)结构优化设计可以为设计人员提供全新的设计和最优的材料分布方案,尤其在设计 早期,可以得到更好的设计基础和更短的设计周期; (3)通过灵敏度分析,可以避免结构修改的盲目性,找出对结构性能影响较大的结构参 数作为优化的设计变量,对应提高结构性能具有十分重要的意义。 (4)有限元方法在结构设计方面占有很重要的位置,并应该贯穿整个设计和制造的全过 程,将有限元方法应用于汽车白车身开发是缩短新型车开发周期、降低产品成本、提高汽车品 质的必由之路。
KU P
式中,K 是刚度矩阵;U 是单元节点位移矢量;P 是单元节点载荷矢量。
K U P U K X X X
则
U P K U K 1 X X X
一般,结构相应(如约束函数 g)可以描述为位移矢量 U 的函数:
g QTU
HyperWorks 在车身结构胶优化中的应用
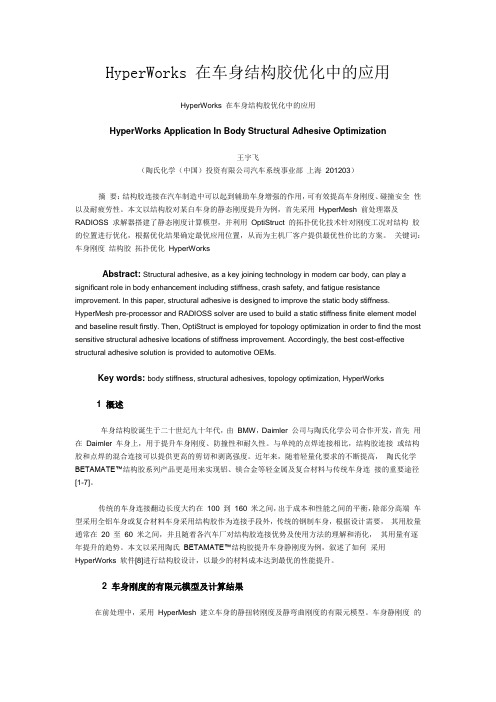
HyperWorks 在车身结构胶优化中的应用HyperWorks 在车身结构胶优化中的应用HyperWorks Application In Body Structural Adhesive Optimization王宇飞(陶氏化学(中国)投资有限公司汽车系统事业部上海201203)摘要:结构胶连接在汽车制造中可以起到辅助车身增强的作用,可有效提高车身刚度、碰撞安全性以及耐疲劳性。
本文以结构胶对某白车身的静态刚度提升为例,首先采用HyperMesh 前处理器及RADIOSS 求解器搭建了静态刚度计算模型,并利用OptiStruct 的拓扑优化技术针对刚度工况对结构胶的位置进行优化,根据优化结果确定最优应用位置,从而为主机厂客户提供最优性价比的方案。
关键词:车身刚度结构胶拓扑优化HyperWorksAbstract: Structural adhesive, as a key joining technology in modern car body, can play a significant role in body enhancement including stiffness, crash safety, and fatigue resistance improvement. In this paper, structural adhesive is designed to improve the static body stiffness. HyperMesh pre-processor and RADIOSS solver are used to build a static stiffness finite element model and baseline result firstly. Then, OptiStruct is employed for topology optimization in order to find the most sensitive structural adhesive locations of stiffness improvement. Accordingly, the best cost-effective structural adhesive solution is provided to automotive OEMs.Key words: body stiffness, structural adhesives, topology optimization, HyperWorks1 概述车身结构胶诞生于二十世纪九十年代,由BMW,Daimler 公司与陶氏化学公司合作开发,首先用在Daimler 车身上,用于提升车身刚度、防撞性和耐久性。
基于HyperWorks的某电动汽车TB车身强度分析
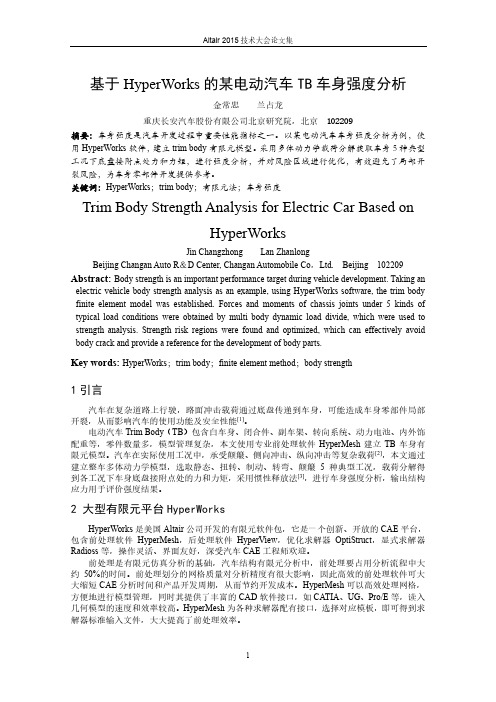
基于HyperWorks的某电动汽车TB车身强度分析金常忠兰占龙重庆长安汽车股份有限公司北京研究院,北京 102209摘要:车身强度是汽车开发过程中重要性能指标之一。
以某电动汽车车身强度分析为例,使用HyperWorks软件,建立trim body有限元模型。
采用多体动力学载荷分解获取车身5种典型工况下底盘接附点处力和力矩,进行强度分析,并对风险区域进行优化,有效避免了局部开裂风险,为车身零部件开发提供参考。
关键词:HyperWorks;trim body;有限元法;车身强度Trim Body Strength Analysis for Electric Car Based onHyperWorksJin Changzhong Lan ZhanlongBeijing Changan Auto R&D Center, Changan Automobile Co,Ltd. Beijing 102209 Abstract: Body strength is an important performance target during vehicle development. Taking an electric vehicle body strength analysis as an example, using HyperWorks software, the trim body finite element model was established. Forces and moments of chassis joints under 5 kinds of typical load conditions were obtained by multi body dynamic load divide, which were used to strength analysis. Strength risk regions were found and optimized, which can effectively avoid body crack and provide a reference for the development of body parts.Key words: HyperWorks;trim body;finite element method;body strength1引言汽车在复杂道路上行驶,路面冲击载荷通过底盘传递到车身,可能造成车身零部件局部开裂,从而影响汽车的使用功能及安全性能[1]。
基于HyperWorks的特种车辆车身有限元分析
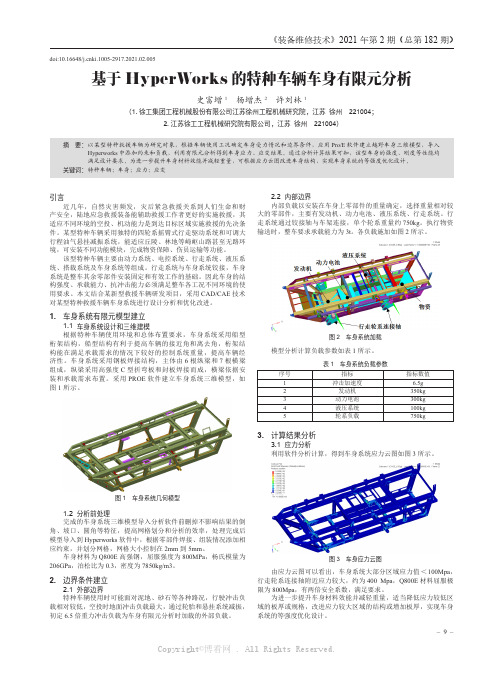
《装备维修技术》2021年第2期(总第182期)doi:10.16648/ki.1005-2917.2021.02.005基于HyperWorks的特种车辆车身有限元分析史富增1 杨增杰2 许刘林1(1.徐工集团工程机械股份有限公司江苏徐州工程机械研究院,江苏徐州 221004;2.江苏徐工工程机械研究院有限公司,江苏徐州 221004)摘要:以某型特种救援车辆为研究对象,根据车辆使用工况确定车身受力情况和边界条件,应用Pro/E软件建立越野车身三维模型,导入Hyperworks中添加约束和负载,利用有限元分析得到车身应力、应变结果。
通过分析计算结果可知,该型车身的强度、刚度等性能均满足设计要求。
为进一步提升车身材料效能并减轻重量,可根据应力云图改进车身结构,实现车身系统的等强度优化设计。
关键词:特种车辆;车身;应力;应变引言近几年,自然灾害频发,灾后紧急救援关系到人们生命和财产安全,陆地应急救援装备能辅助救援工作者更好的实施救援,其适应不同环境的空投、机动能力是到达目标区域实施救援的先决条件。
某型特种车辆采用独特的四轮系摇臂式行走驱动系统和可调大行程油气悬挂减振系统,能适应丘陵、林地等崎岖山路甚至无路环境,可安装不同功能模块,完成物资保障、伤员运输等功能。
该型特种车辆主要由动力系统、电控系统、行走系统、液压系统、搭载系统及车身系统等组成。
行走系统与车身系统铰接,车身系统是整车其余零部件安装固定和有效工作的基础。
因此车身的结构强度、承载能力、抗冲击能力必须满足整车各工况不同环境的使用要求。
本文结合某新型救援车辆研发项目,采用CAD/CAE技术对某型特种救援车辆车身系统进行设计分析和优化改进。
1. 车身系统有限元模型建立1.1 车身系统设计和三维建模根据特种车辆使用环境和总体布置要求,车身系统采用船型桁架结构,船型结构有利于提高车辆的接近角和离去角,桁架结构能在满足承载需求的情况下较好的控制系统重量,提高车辆经济性。
基于hyperworks的车身碰撞
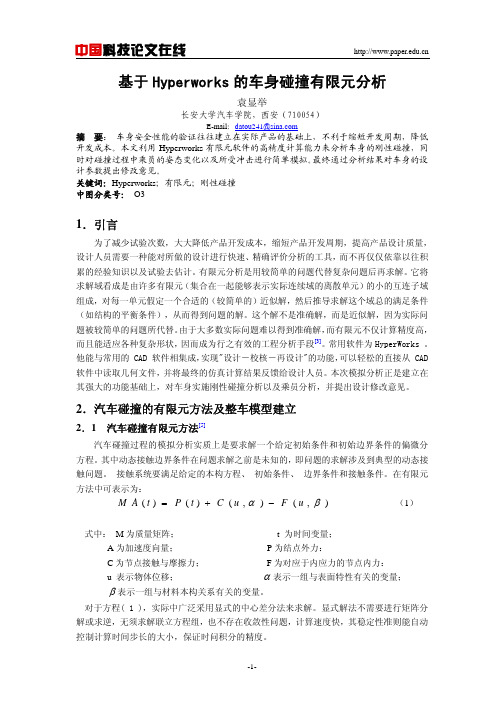
基于Hyperworks 的车身碰撞有限元分析袁显举长安大学汽车学院,西安(710054)E-mail :datou241@摘 要: 车身安全性能的验证往往建立在实际产品的基础上,不利于缩短开发周期,降低开发成本。
本文利用Hyperworks 有限元软件的高精度计算能力来分析车身的刚性碰撞,同时对碰撞过程中乘员的姿态变化以及所受冲击进行简单模拟。
最终通过分析结果对车身的设计参数提出修改意见。
关键词:Hyperworks ;有限元;刚性碰撞中图分类号: O31.引言为了减少试验次数,大大降低产品开发成本,缩短产品开发周期,提高产品设计质量,设计人员需要一种能对所做的设计进行快速、精确评价分析的工具,而不再仅仅依靠以往积累的经验知识以及试验去估计。
有限元分析是用较简单的问题代替复杂问题后再求解。
它将求解域看成是由许多有限元(集合在一起能够表示实际连续域的离散单元)的小的互连子域组成,对每一单元假定一个合适的(较简单的)近似解,然后推导求解这个域总的满足条件(如结构的平衡条件),从而得到问题的解。
这个解不是准确解,而是近似解,因为实际问题被较简单的问题所代替。
由于大多数实际问题难以得到准确解,而有限元不仅计算精度高,而且能适应各种复杂形状,因而成为行之有效的工程分析手段[3]。
常用软件为HyperWorks 。
他能与常用的 CAD 软件相集成,实现"设计-校核-再设计"的功能,可以轻松的直接从 CAD 软件中读取几何文件,并将最终的仿真计算结果反馈给设计人员。
本次模拟分析正是建立在其强大的功能基础上,对车身实施刚性碰撞分析以及乘员分析,并提出设计修改意见。
2.汽车碰撞的有限元方法及整车模型建立2.1 汽车碰撞有限元方法[5]汽车碰撞过程的模拟分析实质上是要求解一个给定初始条件和初始边界条件的偏微分方程。
其中动态接触边界条件在问题求解之前是未知的,即问题的求解涉及到典型的动态接触问题。
某乘用车的车身正面碰撞性能仿真分析

造成车身变形。
因此A 柱会更容易发生变形,此变形形式以折弯为主。
这样的变形会使驾驶舱内的乘客受伤概率增加、受伤程度加重。
同时A 柱变形过大的话,会造成驾乘人员无法打开车门逃生或由于腿部挤压无法离开事故现场的情况。
因此从保护驾乘人员生命安全的角度出发,对A 柱进行折弯变形分析意义重大。
图2所示为A 柱变形后折弯角度测量图,选取A 柱上3
个点,可以测量其角度变化。
图1 正面碰撞模型
图2 A 柱变形折弯角度测量图
图3 A柱碰撞角度变曲线
图5 前纵梁位移云图
图4 保险杠位移变化云图
终角度约为175.2°。
对比碰撞前后状态,A柱所测角度最终变化
3 仿真变形结果对比分析
针对本车型的仿真结果与执行同样碰撞标准的同车型实车碰
撞试验结果进行比对。
通过对碰撞试验车发动机舱内部和对应底盘部分观察,可以看出发动机缸盖罩和油底壳部分依然保持完好
(图7)。
发动机舱内零部件位置与正常发动机舱内布置相比,可
图6 前围板位移云图
图7 正面100%碰撞试验发动机舱变形情况
程,主要涉及的都是一些非线性大位移变形。
车辆本身包含很多零部件,本文主要针对在100%正面碰撞过程中A 柱的变化、保广告。
车辆正面碰撞中的耐撞性能仿真分析

车辆正面碰撞中的耐撞性能仿真分析刘翔;刘俊杰;罗方赞【摘要】为了评价汽车在正面碰撞事故中耐撞性能,应用HyperWorks仿真软件建立了车辆正面100%碰撞有限元模型.后处理利用HyperView对B柱下端加速度、A柱上部最大折弯角、前围板侵入量以及前门铰链变形量4项重要评价指标进行仿真分析,以此评估正面碰撞中车体的耐撞性能.结果表明:B柱下端最大加速度小于3ms合成加速度72g的要求,A柱上部最大折弯角对乘员伤害程度在允许范围内,前围板变形云图小范围超出目标值,前门铰链变形量不影响碰撞后车门的正常开启,车体耐撞性能良好.类比2017年C-NCAP实车正面碰撞结果,表明仿真试验具有较高的可信性,为车体耐撞性优化设计提供依据.【期刊名称】《汽车实用技术》【年(卷),期】2019(000)009【总页数】4页(P149-152)【关键词】正面100%碰撞;有限元;耐撞性能;仿真分析【作者】刘翔;刘俊杰;罗方赞【作者单位】衢州职业技术学院,浙江衢州 324000;衢州职业技术学院,浙江衢州324000;衢州职业技术学院,浙江衢州 324000【正文语种】中文【中图分类】TP399;U661.93汽车已成当今社会人们出行的主流交通工具,但随着汽车保有量的日益增加,道路通行效率呈现下滑趋势,导致道路交通碰撞事故的频发。
因此提高汽车耐撞性能,最大限度地降低乘员在碰撞事故中的伤害程度,已成为汽车制造企业主要的研方向。
正面碰撞试验是检验一辆汽车耐撞性能非常正要的指标。
在中国新车安全评价体系C-NCAP中正面100%刚性壁碰撞试验占18分,占比约30%,凸显了正面100%碰撞的重要性。
传统实车碰撞试验破坏性大、成本高、重复性差,对于前期汽车耐撞性设计阶段的反馈效率低且周期长[1]。
但计算机仿真技术的应用很好地克服了这些缺陷,其采用显示非线性有限元法能够准确地分析在碰撞中汽车结构和材料的非线性问题,且随着建模精度的不断提高,碰撞仿真结果的准确度也在提供。
基于hypermesh的整车正碰分析

10.16638/ki.1671-7988.2020.02.014基于Hypermesh的整车正碰分析*胡珀,余强*,宋若旸,赵轩(长安大学,陕西陕西710000)摘要:文章构建车辆的有限元模型,进行正面100%刚性壁障碰撞的模拟仿真,来分析车辆结构的潜在缺陷和合理性,主要内容为:(1)介绍整车中各个铰链以及加速度传感器的建立,对整车各个结构部件进行了连接设置,对整车的接触设置进行了说明,对材料的设置、刚性墙的建立以及控制卡片的导入进行说明。
(2)利用Hypermesh 和LS-DYNA对模型进行计算,利用HyperView查看输出结果。
(3)根据仿真计算的数据,对模型的合理性进行评价分析,发现前围板入侵量和B柱右侧加速度的指标偏大,影响了汽车的安全性能。
关键词:正面100%碰撞;有限元;Hypermesh;LS-DYNA中图分类号:U467 文献标识码:A 文章编号:1671-7988(2020)02-40-05Analysis of Vehicle Frontal Collision Based on Hypermesh*Hu Po, Yu Qiang*, Song Ruoyang, Zhao Xuan(Chang’an University, Shaanxi Xi’an 710000 )Abstract:Full-text finite element model, 100% self-confrontation, wall-fault-like imitation, future analysis, implicit latent rationality. Main contents: (1) The theoretical basis of the finite element method is introduced, and the establishment of each hinge and acceleration sensor in the whole vehicle is introduced. The structural components of the whole vehicle are connected and set, and the contact setting of the whole vehicle is explained. The establishment of a rigid wall and the introduction of control cards are described. (2) Calculate the model using Hypermesh and LS-DYNA, and use HyperView to view the output consequence. (3) According to the data calculated by the simulation, the rationality of the model is evaluated and found that the intrusion of the dash panel and the acceleration of the right side of the B-pillar are too large, which affects the safety performance of the car.Keywords: Positive 100% collision; Finite element; Hypermesh; LS-DYNACLC NO.: U467 Document Code: A Article ID: 1671-7988(2020)02-40-05前言针对当今严重的交通事故,各国的工程技术人员都在努力提高汽车的安全性能。
基于HyperMesh驾驶室碰撞结构优化

基于HyperMesh驾驶室碰撞结构优化作者:文/ 陈崇山邱宗金路云飞来源:《时代汽车》 2020年第23期陈崇山邱宗金路云飞东风柳州汽车有限公司广西柳州市 545000摘要:本文利用HyperWorks对某商用车驾驶室本体进行结构优化,提升驾驶室结构强度,优化其传递路径,降低驾驶室在各种碰撞工况下入侵量,以保证驾驶室有足够的生存空间;最终实现驾驶室满足ECE R29-03碰撞法规要求。
关键词:商用车驾驶室碰撞 HyperWorks ECE R29-03Optimization of Cab Collision Structure based on HyperMeshChen Chongshan,Qiu Zongjin,Lu YunfeiAbstract: This paper uses HyperWorks to optimize the structure of a commercial vehicle cab body, enhance the strength of the cab structure, optimize its transmission path, and reduce the amount of cab intrusion under various collision conditions to ensure that the cab has enough living space, so that the cab meetsthe requirements of ECE R29-03 collision regulations.Key words: commercial vehicle, cab, collision, HyperWorks, ECE R29-031 引言随着GB 26512-2011《商用车驾驶室乘员保护》强制法规的实施,法规中关于驾驶室碰撞要求完全与欧洲ECE R29-03版碰撞法规要求一致,对国内现有市场上在售的商用车驾驶室是个极大的挑战。
77_基于加速度和侵入量的整车正面碰撞对标分析方法_梁永
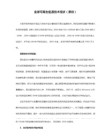
基于加速度和侵入量的整车正面碰撞对标分析方法梁永 李碧浩 杜汉斌上海汽车集团乘用车公司技术中心 上海 201804摘要:本文针对整车结构碰撞分析模型的精确度,从车体加速度及前舱侵入量两方面考察模型的精确度,通过采用HyperMesh建立碰撞分析模型,使用HyperView对分析结果进行处理,对分析结果与实车试验结果进行加速度、侵入量等关键指标的对比,探讨影响分析精确度的影响因素,最终不断提高正面碰撞分析模型与试验的吻合程度。
关键词:B柱加速度,侵入量,碰撞对标,HyperWorks1概述整车结构碰撞仿真分析一直是各大汽车企业着重发展的一个方面,整车碰撞分析模型的精确程度直接影响到后续整车开发中的碰撞试验数量。
一个好的碰撞分析模型能够精确地反映出实际碰撞试验中的车体加速度、乘员舱的侵入量等关键技术指标;为建立较为精确的碰撞分析模型,初始的整车对标碰撞分析模型是必须的基础,该模型建立于整车开发第一次碰撞摸底试验完成之后,与碰撞试验结果有较高的吻合度,使得在后续的开发中对碰撞分析结果有足够的可信度。
2模型建立本文所述的整车碰撞分析对标模型是基于整车第一版数据已经发布并完成首次碰撞试验后与试验结果进行对标。
初始的整车碰撞有限元模型采用HyperMesh前处理工具进行网格划分、材料厚度设置、接触设定、焊点及各种连接关系等建模工作,同时根据CAD数据中的分总成模块化设计的原则,将整车模型分成多个子模型,最后通过*INCLUDE的命令将所有子模型汇聚成一个树状结构的主模型。
整车碰撞模型的细分主要有以下:白车身BIW门盖系统动力总成系统(发动机、变速箱、排气系统、冷却模块、空调等)底盘(转向系统、悬架系统、悬置、行驶制动系统、燃油系统、轮胎等)内外饰(座椅、保险杠、仪表板、内外饰件、玻璃等)通过采用HyperMesh建立整车模型,并且通过配重达到与整车试验一致的总质量、整车质心、前后轴荷等关键参数,完成模型的建立,下图为完成的整车正面100%刚性墙碰撞模型的基本情况。
- 1、下载文档前请自行甄别文档内容的完整性,平台不提供额外的编辑、内容补充、找答案等附加服务。
- 2、"仅部分预览"的文档,不可在线预览部分如存在完整性等问题,可反馈申请退款(可完整预览的文档不适用该条件!)。
- 3、如文档侵犯您的权益,请联系客服反馈,我们会尽快为您处理(人工客服工作时间:9:00-18:30)。
基于Hyperworks 的车身碰撞有限元分析袁显举长安大学汽车学院,西安(710054)E-mail :datou241@摘 要: 车身安全性能的验证往往建立在实际产品的基础上,不利于缩短开发周期,降低开发成本。
本文利用Hyperworks 有限元软件的高精度计算能力来分析车身的刚性碰撞,同时对碰撞过程中乘员的姿态变化以及所受冲击进行简单模拟。
最终通过分析结果对车身的设计参数提出修改意见。
关键词:Hyperworks ;有限元;刚性碰撞中图分类号: O31.引言为了减少试验次数,大大降低产品开发成本,缩短产品开发周期,提高产品设计质量,设计人员需要一种能对所做的设计进行快速、精确评价分析的工具,而不再仅仅依靠以往积累的经验知识以及试验去估计。
有限元分析是用较简单的问题代替复杂问题后再求解。
它将求解域看成是由许多有限元(集合在一起能够表示实际连续域的离散单元)的小的互连子域组成,对每一单元假定一个合适的(较简单的)近似解,然后推导求解这个域总的满足条件(如结构的平衡条件),从而得到问题的解。
这个解不是准确解,而是近似解,因为实际问题被较简单的问题所代替。
由于大多数实际问题难以得到准确解,而有限元不仅计算精度高,而且能适应各种复杂形状,因而成为行之有效的工程分析手段[3]。
常用软件为HyperWorks 。
他能与常用的 CAD 软件相集成,实现"设计-校核-再设计"的功能,可以轻松的直接从 CAD 软件中读取几何文件,并将最终的仿真计算结果反馈给设计人员。
本次模拟分析正是建立在其强大的功能基础上,对车身实施刚性碰撞分析以及乘员分析,并提出设计修改意见。
2.汽车碰撞的有限元方法及整车模型建立2.1 汽车碰撞有限元方法[5]汽车碰撞过程的模拟分析实质上是要求解一个给定初始条件和初始边界条件的偏微分方程。
其中动态接触边界条件在问题求解之前是未知的,即问题的求解涉及到典型的动态接触问题。
接触系统要满足给定的本构方程、 初始条件、 边界条件和接触条件。
在有限元方法中可表示为:()()(,)(,)M A t P t C u F u αβ=+− (1)式中: M 为质量矩阵; t 为时间变量;A 为加速度向量; P 为结点外力:C 为节点接触与摩擦力; F 为对应于内应力的节点内力:u 表示物体位移; α表示一组与表面特性有关的变量; β表示一组与材料本构关系有关的变量。
对于方程( 1 ),实际中广泛采用显式的中心差分法来求解。
显式解法不需要进行矩阵分解或求逆,无须求解联立方程组,也不存在收敛性问题,计算速度快,其稳定性准则能自动控制计算时间步长的大小,保证时问积分的精度。
2.2整车模型建立对于类似车身这样的复杂模型,一般不直接采用Hyperworks建实体模型,可采用UG,等对车身建模。
按照设计意图建立好UG模型后,直接将实体模型导入Hyperworks进行有限元模型建立。
建立有限元模型时,整车包含许多的零部件,因而整车模型的单元通常比较多。
考虑到过大的整车模型会影响计算的成本(主要指计算时间),所以,结合侧面碰撞变形特点,在不影响计算要求和精度的前提下,尽可能地减少模型的单元数。
采用Hyperworks建立本次有限元模型需满足和注意以下事项:对于汽车这样复杂的薄壁板壳结构系统,其碰撞模拟分析中最常用的结构单元是二维壳单元,少量用到梁单元和体单元。
4节点壳单元(称BT单元)和4节点Hughes-Lio壳单元(称HL单元)是汽车碰撞模拟分析中常用的壳单元。
在划分网格前,应该对所划分网格的类型和参数,比如三角形,四边形网格,长度,角度翘曲度进行设置。
事先设置不合格网格显示颜色,即使调整网格宜保证所有网格满足参数要求。
[1] [2](1) 对曲面和过渡部分采用弦差控制划分网格,以保证网格和几何模型有更好的吻合度,宜采用较密网格。
对于大平面,网格密度可以适当减小。
(2) 先对车身壳体,车前板制件,车门窗等划分网格,然后采用Hyperworks的焊接功能,形成车身整体有限元模型。
同时为了方便管理这些焊接约束点,将其置于统一的component中,命名Welds。
(3) 在建立模型过程中,事先建立各部分的集,比如材料集,并将模型置于集中,对集中的参数,如弹性模量,泊松比等进行设置。
否则分析不能成功。
(4) 本次模型建立了轮胎模型,并与车身实施作用连接,并建立了驾驶员模型。
本驾驶员模型主要考虑汽车碰撞过程中,安全气囊,人体臀部和座椅作用变化情况。
(5)车身主要通过焊点单元将零部件装配在一起。
车门与车身骨架的连接通过铰接单元和弹簧单元连接,用铰接单元模拟车门铰链,用带失效定义的一般弹簧单元模拟门锁的锁止作用。
车轮与车轴之间采用铰接单元连接,使车轮能够绕车轴转动。
座椅与车身通过刚性短梁固定[4]。
模型建立以后,加载Radioss环境以及查看编辑组件的材料和属性,更新点对点连接成无网络焊接。
本次建立的某轿车车身以及人体模型如图1、图2所示:[6]3.定义冲击车身正面碰撞的可移动刚性墙利用Analysis页面下的Rigid Walls功能面板定义可移动刚性墙。
创建刚性墙应遵循以下过程,否则容易出错。
[2](1) 创建焊接单元节点集合,且务必使Name为Welds,Card Image为GRNOD。
(2) 创建BOX卡,确定上下边界坐标,本次坐标如下:(3)表1 刚性墙位置坐标Lower Bound Upper BoundX 100 200600 Y -600Z 400 700(4) 创建刚性墙。
该步骤须定义刚性墙名称,类型,颜色。
(5) 定义刚性墙的位置和尺寸。
刚性墙的法向矢量尾端节点通过Base Node定义,用Creat Nodes的功能创建用于定义刚性墙的基点的临时节点。
本次采用位置点为:X=100,Y=0,Z=525。
(6) 定义刚性墙的从属节点和定义刚性墙的运动。
定义运动时,要注意其方向和法向的一致性,更该矢量模式设置X方向分量为1000.(7) 编辑组的卡片属性。
定义刚性墙的从属点,将焊接点从点集中排除,避免运动约束冲突。
同时定义摩擦系数,本次设置摩擦系数为0.2,设置刚性强质量为300。
4.后处理以及结果分析后处理包括查看控制卡片,导出计算控制文件,提交计算任务,查看结果。
查看控制卡片,选择图形界面中的关键点或者区域,并将有限元模型文件导入到工作目录。
导出计算控制文件,设置计算运行参数,算法状态,数据输出频率。
同时该过程将单元能量信息,单元塑性应变,沙漏能量写入结果动画文件。
提交计算任务前,要进行模型检查,将计算文件置于工作目录,然后确认没有错误后,提交计算。
等待计算完毕后,查看结果文件,分析结果[2]。
同时可以利用Hyperview的功能观察整个碰撞过程中车体变形,人体和座椅座椅作用变化情况,甚至可以观看安全气囊整个作用过程以及人体姿态的变化。
车体变形,人体姿态与座椅作用变化情况,碰撞过程刚性墙和车体作用力变化情况(某时刻)如图3、图4、图5所示:根据结果图,可以分析各设计元素的合理性,对整车的基本尺寸,质量,材料,厚度等参数提出修改,在继续进行模型碰撞,直碰撞结果达到安全要求。
这样就不需要经过多试制,试验,能大大减少成本和开发周期。
例如本次碰撞模型中,车身壳体采用钢材料,从结果可以看出,前围板在受到剧烈碰撞后,变形较合理,而发动机舱盖板变形相当严重,应修改其设计参数。
同时应该根据人体姿态变化以及约束系统,作用力变化甚至加速度变化来调整参数,汽车前部结构以及相应的安全结构措施。
5.结论可见,HyperWorks 在汽车各种有限元分析中都能发挥极大的作用,快速的建模,良好的可操作性,优秀的可视化效果都使我们在分析汽车部件时,更加省时省力。
HyperWorks 操作简单,对零部件的计算,精度比较高,它的应用将大大减少试验费用,提高分析效率,加快产品研发的进程。
本文主要介绍了利用HyperWorks 建立车身模型的关键方法,步骤以及注意事项,并介绍了利用HyperWorks 定义可移动刚性墙,分析后处理步骤。
并成功实施车身正面碰撞可移动刚性墙分析,得出车身变形,人体姿态变化,碰撞过程中刚性墙作用力变化的结论。
对利用HyperWorks 对汽车零部件,总成及整车分析提供一定参考价值。
参考文献[1] 张胜兰,等.基于HyperWorks的结构优化设计技术[M].北京:机械工业出版社,2007.[2] 李楚林,等.HyperWorks分析运用实例[M].北京:机械工业出版社,2008.[3] 潭继锦.汽车有限元法[M].北京:人民交通出版社,2005.[4] Gopalakrishnan R, Agrawal H N. Durability Analysis of Full Automotive Body Structures [ R ]. SAE Transaction, No. 930568, 1993:775 -791[5] 李博闻.有限元法在汽车碰撞研究中的应用.天津汽车,2008(3).[6] A car’s colliding with wall based on Hyperworks finiteelement softwareYuan XianjuAutomobile College of Chan’An University, Xi’an, PRC, (7100544)AbstractThe validity about a car’ security used to base on fact production,which must go against reducingthe amount of physical testing and create optimum designs with regard to weight, cost and strength. The paper addresses methods about a car’s colliding with wall based on Hyperworks finite element software .And,it simulates the process of the driver’s gesture and concussion.Finally, a perfect idea of mending design parameter will be put forward.Keywords: Hyperworks ; Finite Element; Rigidity Colliding。