基于故障树的复杂机械设备排故策略设计
基于Petri网的复杂制造系统故障树分析
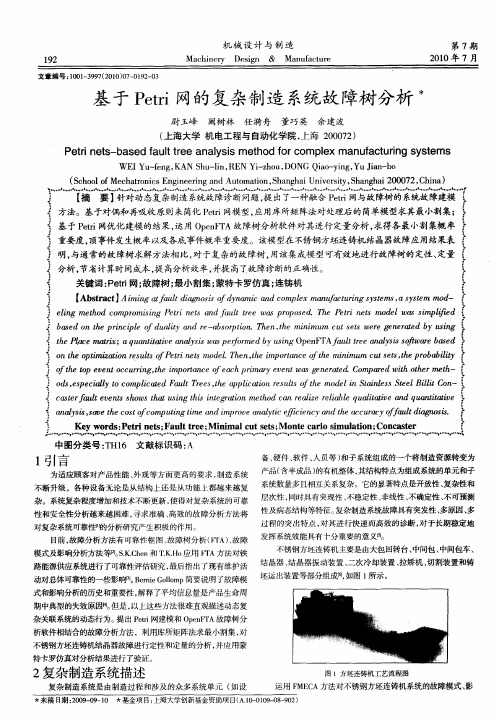
j
【 要】 摘 针对动态复杂制造 系 统故障诊断问 , 题 提出了一种融合 Pt 网与故障树的系统故障建模 t ei r
方法。基于对偶和再吸收原则来 简化 Pt 网模型 , ei r 应用库 所矩 阵法对 处理后的 简单模 型求其 最小割集 ; 基 于 P t 网优化 建模 的结果 , er i 运用 O eF A故障树 分析软件对其进行定量分析 , pnT 求得各 最小割 集概 率
a a s ,t e otf o p t gt e dip oe n yie cec dte c uay f a ldan s . nl i sv t so cm ui i ry a t f iny n h c r of t i oi ys oe h c n m a m n al c f i a a c u g s
WE u fn , A h —i, E izo , O G Qa -igY i - o I -e gK N S u l R NY -h u D N i y , uJ n b Y n o n a (c ol f carnc n ier ga dA tm t n S a g a U iesy S a ga 2 0 7 , hn ) Sh o o h t is gnei n uo a o ,h nh i nvri ,hn h i 0 0 2 C ia Me o E n i t
关键词 : er网 ; Pt i 故障树 ; 小割集 ; 最 蒙特卡 罗仿 真 ; 连铸机
基于故障树的故障诊断

基于故障树的故障诊断故障树分析是一种可靠性工程中常用的一种方法,用于识别和分析故障原因。
它可以帮助工程师识别系统发生故障的可能原因,通过构建故障树,分析故障树结构中的故障模式和故障主要原因,确定实际发生故障的根本原因,从而制定优化的维修方案。
故障树分析的基本步骤如下:1. 确定故障对象和故障目标首先需要明确故障对象和故障目标,即需要分析和诊断的设备或系统,和对该设备或系统所期望实现的功能要求。
2. 识别顶事件顶事件是指系统中的故障点,即需要分析和诊断的根本原因。
例如:电路短路、机器故障等。
3. 构建故障树通过逐层分解,将顶事件分解成一个个故障因素,形成故障树的结构。
通常采用的是与门、或门、非门等逻辑元件符号,在故障树上构建出故障因素的逻辑关系图。
4. 确定故障树中的故障模式在故障树结构中发现具有类似的故障因素,通过消融或剖析等手段,确定故障模式。
5. 确定故障树中的故障主要原因对于故障模式,通过进行合理的归纳和分析,确定故障的主要原因。
6. 制定维修方案综合分析并确定故障原因后,制定出相应的维修方案,并通过实现该方案,消除故障。
在进行故障树分析时,还需要注意以下几点:1. 指定适当的重要性指标在构建故障树时,需要根据实际情况指定一些重要性指标,以帮助分析和评价各个故障因素的重要程度。
2. 建立逻辑关系矩阵通过逻辑关系矩阵,可以将故障因素和设备之间的逻辑关系完整地表达出来,为故障树的构建提供更加清晰和准确的信息。
3. 进行故障树的验证和修正在故障树构建完成后,需要对其进行验证和修正,以确保它能够准确地表达故障因素的确切关系,从而减少实施方案的失误。
总之,故障树分析是一种非常有效的故障诊断方法,可帮助工程师迅速定位设备或系统的故障原因,并制定出正确的维修方案,以确保设备或系统能够按照预期功能正常运行。
故障树分析法在工程机械维修中的应用
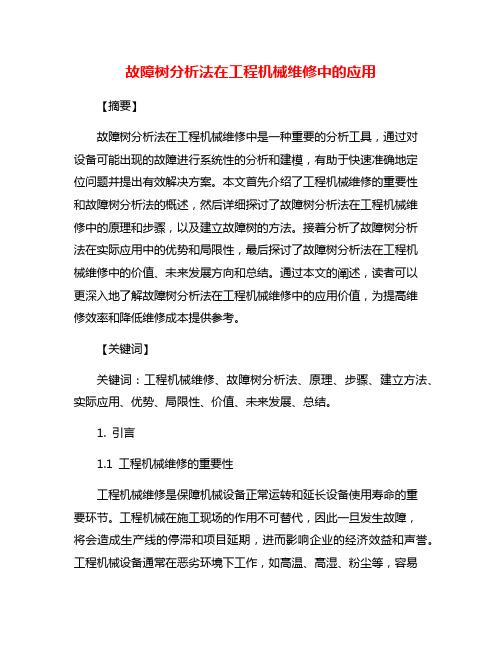
故障树分析法在工程机械维修中的应用【摘要】故障树分析法在工程机械维修中是一种重要的分析工具,通过对设备可能出现的故障进行系统性的分析和建模,有助于快速准确地定位问题并提出有效解决方案。
本文首先介绍了工程机械维修的重要性和故障树分析法的概述,然后详细探讨了故障树分析法在工程机械维修中的原理和步骤,以及建立故障树的方法。
接着分析了故障树分析法在实际应用中的优势和局限性,最后探讨了故障树分析法在工程机械维修中的价值、未来发展方向和总结。
通过本文的阐述,读者可以更深入地了解故障树分析法在工程机械维修中的应用价值,为提高维修效率和降低维修成本提供参考。
【关键词】关键词:工程机械维修、故障树分析法、原理、步骤、建立方法、实际应用、优势、局限性、价值、未来发展、总结。
1. 引言1.1 工程机械维修的重要性工程机械维修是保障机械设备正常运转和延长设备使用寿命的重要环节。
工程机械在施工现场的作用不可替代,因此一旦发生故障,将会造成生产线的停滞和项目延期,进而影响企业的经济效益和声誉。
工程机械设备通常在恶劣环境下工作,如高温、高湿、粉尘等,容易受到外部环境的影响导致故障频发。
对工程机械设备进行定期维护和及时修复故障显得尤为重要。
工程机械维修的重要性体现在以下几个方面:及时维修可以减少故障对生产造成的影响,保障生产进程的顺利进行。
定期维护可以延长机械设备的使用寿命,降低企业的运营成本。
良好的维护工作还可以提高设备的工作效率和安全性,保障操作人员的工作安全。
工程机械维修在现代工程建设中扮演着不可或缺的角色,其重要性不言而喻。
1.2 故障树分析法的概述故障树分析法(FTA)是一种通过逻辑推理来分析系统可能发生故障的方法。
它是一种系统性分析方法,旨在找出系统中可能导致故障的所有可能组合,并通过结构化的分析方法来识别和评估这些组合的重要性。
故障树分析法可帮助工程师确定系统中可能出现的故障模式,从而提前采取预防措施或及时修复问题。
机械设计中的故障树和事件树分析

机械设计中的故障树和事件树分析在机械设计领域,故障树和事件树分析是常用的方法,用于识别和评估机械系统中可能发生的故障和事故事件。
这两种分析方法通过图形化的方式,帮助工程师们系统地分析和理解机械系统的可靠性,并提供相应的改进措施。
一、故障树分析故障树分析(Fault Tree Analysis, FTA)是一种定性和定量分析方法,用于识别导致系统故障的各种可能性。
它基于布尔代数的原理,通过将不同的事件与逻辑门连接,形成一棵树状结构,给出导致特定故障的所有可能故障事件的逻辑关系。
这样可以帮助工程师们深入分析系统的瓶颈,并提供改进的方向。
故障树分析通常从顶事件(Top Event)开始,这是所关注的主要系统故障。
然后,通过逆向推导分析,将顶事件分解为导致该事件发生的一系列基本事件或故障模式。
基本事件可以是硬件故障、人为失误、环境因素等。
当所有的基本事件都被识别出来,并通过逻辑门进行逻辑关系的连接后,故障树就构建完成了。
故障树分析的优点在于可以清晰地揭示系统故障的根本原因,并提供改进方案。
然而,它也存在一些限制,比如需要大量的数据支持和专业知识,以及难以处理复杂系统的问题。
二、事件树分析事件树分析(Event Tree Analysis, ETA)是一种定性和定量分析方法,用于评估机械系统中的事件发生概率和严重程度。
它通过图形化的方式,展示了系统事件的发展过程和结果,并提供了相应的风险评估。
事件树分析主要从一个初始事件(Initiating Event)开始,这是导致系统事件链的第一个事件。
然后,通过逻辑门的组合,确定出各种可能的事件序列和结果。
在每个逻辑门的选择中,考虑了不同的事件发生概率和条件。
最后,事件树形成了一个树状结构,直到最终事件(Final Event)为止。
事件树分析可以帮助工程师们全面了解系统事件的发展过程,并评估事件链中各个事件的发生概率和影响程度。
这有助于制定相应的风险控制策略和预防措施。
基于故障树分析的汽车机械故障诊断模型及系统构建

基于故障树分析的汽车机械故障诊断模型及系统构建作者:张士轩来源:《电脑知识与技术》2019年第26期摘要:现代汽车技术越来越复杂,机械故障的表现多种多样,机械故障诊断定位成为汽车维修工作的难题,故障树分析法是对现代复杂系统设备进行故障诊断的安全可靠方法。
本文分析了汽车机械故障发生的原因,总结了汽车机械故障诊断的方法,构建了汽车机械故障诊断故障树分析模型,设计了汽车机械故障诊断系统,提出了汽车机械故障的预防措施。
本文的研究成果,对于提高汽车机械故障诊断平和汽车维修工作效率等方面具有重要作用。
关键词:故障树分析;汽车机械故障;诊断模型;系统构建中图分类号:U472, TP311; ; ; ; ; ; ;文献标识码:A文章编号:1009-3044(2019)26-0259-03开放科学(资源服务)标识码(OSID):汽车作为一种交通运输工具,给人们出行带来了极大便利,在人们的日常工作和生产生活中发挥着极其重要的作用。
汽车由成百上千个机械零部件构成,结构复杂,工作条件差,由于使用不当和零部件磨损等原因,发生机械故障不可避免。
机械故障是指机械系统因偏离设计状态而丧失部分或全部功能的显现,机械故障是汽车比较常见的一种故障。
由于汽车零部件的寿命是有限的,虽然机械故障发生具有随机性,但随着汽车使用年限增长,机械故障发生总体呈增加趋势。
因此,必须对汽车机械故障引起足够的重视。
故障诊断是对设备运行状态和异常情况做出诊断,并确定故障大体发生部位的过程。
诊断出汽车机械故障的部位和原因后,运用维修技术进行处理,将机械故障及时消除,使汽车运行稳定性及效率得到提升,运行寿命得以延长。
现代汽车技术越来越复杂,机械故障的表现多种多样,机械故障诊断定位成为汽车维修工作的难题,传统的人工诊断排查技术越来越不适应汽车工业发展的需要。
故障树分析(FaultTree Analysis)是安全系统工程最重要的技术之一,已经成为设备故障诊断和预测的有效手段。
基于故障树分析法的飞机垃圾车液压系统故障分析

基于故障树分析法的飞机垃圾车液压系统故障分析飞机垃圾车液压系统故障分析是以故障树分析方法为基础的。
故障树分析是一种定性定量的方法,用于分析系统故障的引发原因,通过构建故障树来推断系统的失效概率和可靠性。
飞机垃圾车液压系统是保障垃圾车正常运行的重要组成部分,涉及到液压泵、液压油箱、液压马达等多个关键部件。
故障树分析可以帮助我们识别系统的故障模式和主要故障原因,并制定相应的维修和改进措施。
首先,我们需要确定液压系统的顶事件,即系统不能正常运行的故障状态。
常见的液压系统故障包括液压泵失效、液压油箱漏油、液压马达性能下降等。
以液压泵失效为例,我们可以将其作为故障树的顶事件。
然后,我们需要确定导致液压泵失效的基本事件。
基本事件是故障树中无法继续拆解为其他事件的最小单位。
在液压泵失效的情况下,可能的基本事件包括泵内部零件损坏、液压油温度过高等。
接下来,我们可以采用与顶事件相反的方式,将基本事件和逻辑门连接起来,构建故障树的逻辑关系。
逻辑门有与门、或门和非门,用于描述事件之间的关系。
在液压泵失效的情况下,可能需要考虑泵内部零件同时损坏或液压油温度过高的情况。
在构建完故障树后,我们可以通过定量分析来评估系统的失效概率和可靠性。
定量分析可以通过故障概率数据和逻辑关系计算得出。
根据故障树分析的结果,我们可以确定导致飞机垃圾车液压系统故障的主要原因,并采取相应的措施进行维修和改进。
例如,如果发现泵内部零件损坏是主要原因,我们可以制定定期检查和更换零件的计划;如果发现液压油温度过高是主要原因,我们可以考虑增加散热设备或改进液压油循环系统。
总之,基于故障树分析方法的飞机垃圾车液压系统故障分析可以帮助我们识别故障模式和主要故障原因,并采取相应的措施提高系统的可靠性和安全性。
这种分析方法是一种有力的工具,可以应用于各种类型的系统故障分析和优化。
基于故障树分析法在工程机械维修中的应用 张侃
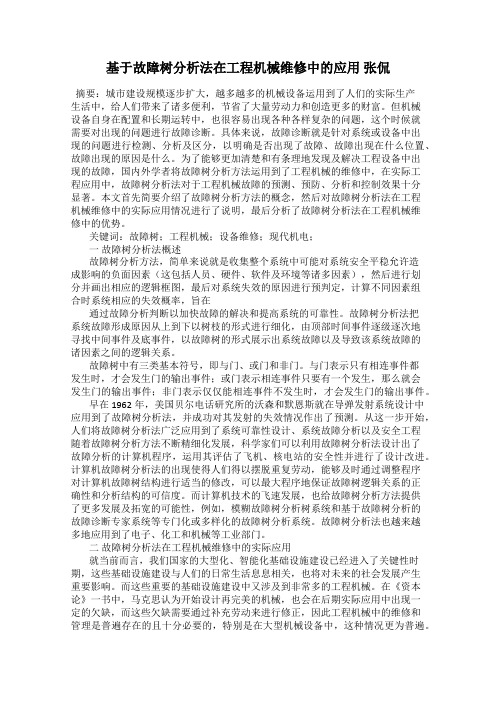
基于故障树分析法在工程机械维修中的应用张侃摘要:城市建设规模逐步扩大,越多越多的机械设备运用到了人们的实际生产生活中,给人们带来了诸多便利,节省了大量劳动力和创造更多的财富。
但机械设备自身在配置和长期运转中,也很容易出现各种各样复杂的问题,这个时候就需要对出现的问题进行故障诊断。
具体来说,故障诊断就是针对系统或设备中出现的问题进行检测、分析及区分,以明确是否出现了故障、故障出现在什么位置、故障出现的原因是什么。
为了能够更加清楚和有条理地发现及解决工程设备中出现的故障,国内外学者将故障树分析方法运用到了工程机械的维修中,在实际工程应用中,故障树分析法对于工程机械故障的预测、预防、分析和控制效果十分显著。
本文首先简要介绍了故障树分析方法的概念,然后对故障树分析法在工程机械维修中的实际应用情况进行了说明,最后分析了故障树分析法在工程机械维修中的优势。
关键词:故障树;工程机械;设备维修;现代机电;一故障树分析法概述故障树分析方法,简单来说就是收集整个系统中可能对系统安全平稳允许造成影响的负面因素(这包括人员、硬件、软件及环境等诸多因素),然后进行划分并画出相应的逻辑框图,最后对系统失效的原因进行预判定,计算不同因素组合时系统相应的失效概率,旨在通过故障分析判断以加快故障的解决和提高系统的可靠性。
故障树分析法把系统故障形成原因从上到下以树枝的形式进行细化,由顶部时间事件逐级逐次地寻找中间事件及底事件,以故障树的形式展示出系统故障以及导致该系统故障的诸因素之间的逻辑关系。
故障树中有三类基本符号,即与门、或门和非门。
与门表示只有相连事件都发生时,才会发生门的输出事件;或门表示相连事件只要有一个发生,那么就会发生门的输出事件;非门表示仅仅能相连事件不发生时,才会发生门的输出事件。
早在1962年,美国贝尔电话研究所的沃森和默恩斯就在导弹发射系统设计中应用到了故障树分析法,并成功对其发射的失效情况作出了预测。
从这一步开始,人们将故障树分析法广泛应用到了系统可靠性设计、系统故障分析以及安全工程随着故障树分析方法不断精细化发展,科学家们可以利用故障树分析法设计出了故障分析的计算机程序,运用其评估了飞机、核电站的安全性并进行了设计改进。
基于故障树的复杂机械设备排故策略设计

研究目的与意义
02
故障树分析理论基础
VS
故障树是一种逻辑关系图,以系统故障为顶事件,自上而下逐层分解,直至不能继续分解为止。它能够清晰地描述系统故障与各子系统故障之间的逻辑关系。
故障树原理
故障树原理基于布尔代数和逻辑运算,通过对系统故障的分析,找出最小割集,即导致系统故障的最小子系统组合。
故障树定义
故障树定义与原理
故障树的建立与计算
首先需要明确系统故障和各子系统故障之间的逻辑关系,然后绘制故障树图,逐步分解至最小割集。
建立故障树
通过对故障树中的最小割集进行计算,找出导致系统故障的最小子系统故障组合。
故障树计算
优势
故障树分析能够清晰地描述系统故障与各子系统故障之间的逻辑关系,有助于快速定位故障点;同时具有较高的可靠性、灵活性和可扩展性。
智能化故障诊断与排故技术
故障树分析与其他方法的融合
将故障树分析结果与专家系统知识库相结合,提供更加准确和高效的故障诊断解决方案。
故障树分析与专家系统的结合
通过仿真技术模拟设备运行状态,结合故障树分析,找出设备潜在故障及故障原因。
故障树分析与仿真技术的结合
数据驱动的故障树分析
通过对大量数据进行分析和学习,建立基于数据驱动的故障树模型,提高故障诊断的精度和效率。
简化故障树
优化故障树
故障树的简化与优化
制定预防性维护计划
监控运行状态
培训与演练
基于故障树分析的预防性维护策略
04
工程应用案例
总结词
高效、准确
详细描述
航空发动机故障树分析以可靠性为中心,针对发动机性能衰退和故障进行深入分析,通过定性和定量分析,确定故障原因,制定相应的预防和维修措施,提高发动机的可靠性和使用寿命。
基于故障树的机车故障诊断系统设计

第37卷第6期 计算机应用与软件Vol 37No.62020年6月 ComputerApplicationsandSoftwareJun.2020基于故障树的机车故障诊断系统设计梁 杰1 饶天贵21(中国铁路武汉局集团有限公司机务部 湖北武汉430070)2(株洲中车时代电气股份有限公司 湖南株洲412001)收稿日期:2019-02-22。
梁杰,高工,主研领域:机车检修与诊断。
饶天贵,高工。
摘 要 给出基于故障树的机车故障诊断系统设计方案。
采用公式形式将故障树的结构信息保存在文本文件中,在运用故障树进行推理诊断时,提出基于Java语言SWING包中JTree控件解析保存故障树的结构与节点信息的方法,从而方便快速完成故障推理。
给出基于模块化故障树及割集计算方法,为大型故障树诊断与定性分析提供了较好的解决方案。
关键词 故障树 故障诊断 割集中图分类号 TP302.1 文献标志码 A DOI:10.3969/j.issn.1000 386x.2020.06.056DESIGNOFTRAINFAULTDIAGNOSISSYSTEMBASEDONFAULTTREELiangJie1 RaoTiangui21(ChinaRailwayWuhanBureauLocomotiveDepartment,Wuhan430070,Hubei,China)2(ZhuzhouCRRCTimesElectricCo.,Ltd.,Zhuzhou412001,Hunan,China)Abstract Thispaperpresentsthedesignschemeoftrainfaultdiagnosissystembasedonfaulttree.Thestructureinformationofthefaulttreewassavedinthetextfilebyusingequation.Whenusingfaulttreeforreasoningdiagnosis,weproposedamethodtoanalyzeandsavethestructureandnodeinformationoffaulttreebasedonJTreeoftheSWINGpackageinJava,soastofacilitatetherapidcompletionoffaultreasoning.Basedonthemodularfaulttreeandcutsetcalculationmethod,thispaperalsoprovidesabettersolutionforlarge scalefaulttreediagnosisandqualitativeanalysis.Keywords Faulttree Faultdiagnosis Cutset0 引 言故障树分析法(FaultTreeAnalysis,FTA)[1]是目前国际上公认的一种简单有效的可靠分析和故障诊断的方法,也是指导系统最优化设计、薄弱环节分析和运行维护的有力工具。
系统可靠性设计中的故障树分析案例分享(八)

系统可靠性设计中的故障树分析案例分享一、引言在工程设计与管理中,系统可靠性是一个至关重要的问题。
无论是汽车、飞机、电子设备还是工业生产线,都需要保证系统的可靠性。
故障树分析作为一种系统可靠性设计的方法,在工程领域得到了广泛的应用。
本文将分享一个实际案例,介绍故障树分析在系统可靠性设计中的应用。
二、案例介绍某高端数控机床在运行过程中出现了频繁的故障,导致生产进度延误和设备维护成本增加。
经过初步排查,发现故障可能涉及多个系统组件,包括液压系统、电气系统和控制系统。
为了找出故障的根本原因,工程团队决定进行故障树分析,并邀请了专业的可靠性工程师进行指导。
三、故障树分析1. 事件识别首先,工程团队对可能导致机床故障的事件进行了识别。
这些事件包括液压系统压力异常、电气系统短路、控制系统指令错误等。
通过对这些事件的分析,确定了可能导致机床故障的根本原因。
2. 逻辑关系建立在确定了可能的故障事件之后,工程团队开始建立故障树的逻辑关系。
他们首先确定了各个故障事件之间的逻辑关系,然后将这些事件按照逻辑关系进行了组织和排列。
通过这一步骤,他们建立了一个完整的故障树结构。
3. 概率分析在建立了故障树结构之后,工程团队对每个事件的发生概率进行了分析。
他们通过实际数据和专业知识,确定了每个事件发生的概率,并将这些概率值应用到了故障树的分析中。
4. 根本原因分析最后,工程团队对故障树进行了综合分析,找出了机床故障的根本原因。
通过故障树分析,他们发现机床故障的根本原因是液压系统的压力异常,导致了电气系统的短路和控制系统的指令错误。
基于这一分析结果,工程团队制定了相应的改进方案,解决了机床故障问题。
四、结论与展望通过故障树分析,工程团队找出了机床故障的根本原因,并制定了相应的改进方案。
这不仅解决了机床故障问题,还提高了机床的可靠性和稳定性。
未来,工程团队将继续运用故障树分析方法,提高系统的可靠性,并不断优化产品设计和生产管理流程。
解析工程机械维修中故障树分析法应用
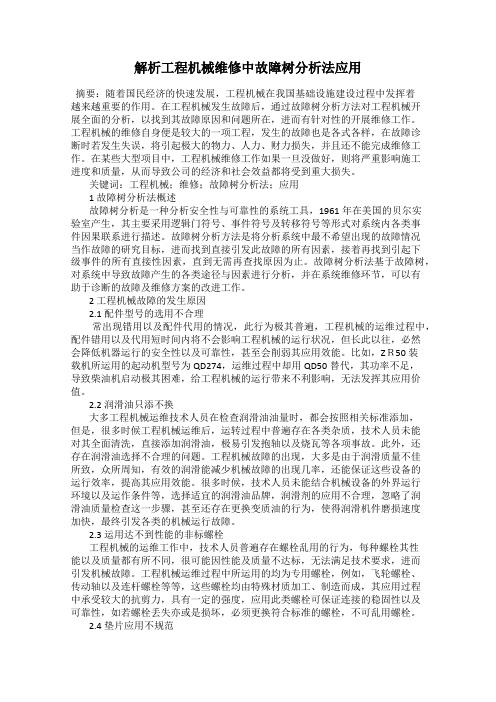
解析工程机械维修中故障树分析法应用摘要:随着国民经济的快速发展,工程机械在我国基础设施建设过程中发挥着越来越重要的作用。
在工程机械发生故障后,通过故障树分析方法对工程机械开展全面的分析,以找到其故障原因和问题所在,进而有针对性的开展维修工作。
工程机械的维修自身便是较大的一项工程,发生的故障也是各式各样,在故障诊断时若发生失误,将引起极大的物力、人力、财力损失,并且还不能完成维修工作。
在某些大型项目中,工程机械维修工作如果一旦没做好,则将严重影响施工进度和质量,从而导致公司的经济和社会效益都将受到重大损失。
关键词:工程机械;维修;故障树分析法;应用1 故障树分析法概述故障树分析是一种分析安全性与可靠性的系统工具,1961年在美国的贝尔实验室产生,其主要采用逻辑门符号、事件符号及转移符号等形式对系统内各类事件因果联系进行描述。
故障树分析方法是将分析系统中最不希望出现的故障情况当作故障的研究目标,进而找到直接引发此故障的所有因素,接着再找到引起下级事件的所有直接性因素,直到无需再查找原因为止。
故障树分析法基于故障树,对系统中导致故障产生的各类途径与因素进行分析,并在系统维修环节,可以有助于诊断的故障及维修方案的改进工作。
2 工程机械故障的发生原因2.1 配件型号的选用不合理常出现错用以及配件代用的情况,此行为极其普遍,工程机械的运维过程中,配件错用以及代用短时间内将不会影响工程机械的运行状况,但长此以往,必然会降低机器运行的安全性以及可靠性,甚至会削弱其应用效能。
比如,ZR50装载机所运用的起动机型号为QD274,运维过程中却用QD50替代,其功率不足,导致柴油机启动极其困难,给工程机械的运行带来不利影响,无法发挥其应用价值。
2.2 润滑油只添不换大多工程机械运维技术人员在检查润滑油油量时,都会按照相关标准添加,但是,很多时候工程机械运维后,运转过程中普遍存在各类杂质,技术人员未能对其全面清洗,直接添加润滑油,极易引发抱轴以及烧瓦等各项事故。
设备故障分析方法—故障树分析法

设备故障分析方法—故障树分析法1.故障树分析法的产生与特点从系统的角度来说,故障既有因设备中具体部件(硬件)的缺陷和性能恶化所引起的,也有因软件,如自控装置中的程序错误等引起的。
此外,还有因为操作人员操作不当或不经心而引起的损坏故障。
20世纪60年代初,随着载人宇航飞行,洲际导弹的发射,以及原子能、核电站的应用等尖端和军事科学技术的发展,都需要对一些极为复杂的系统,做出有效的可靠性与安全性评价;故障树分析法就是在这种情况下产生的。
故障树分析法简称FTA (Failute Tree Analysis),是1961年为可靠性及安全情况,由美国贝尔电话研究室的华特先生首先提出的。
其后,在航空和航天的设计、维修,原子反应堆、大型设备以及大型电子计算机系统中得到了广泛的应用。
目前,故障树分析法虽还处在不断完善的发展阶段,但其应用范围正在不断扩大,是一种很有前途的故障分析法。
总的说来,故障树分析法具有以下一些特点。
它是一种从系统到部件,再到零件,按“下降形”分析的方法。
它从系统开始,通过由逻辑符号绘制出的一个逐渐展开成树状的分枝图,来分析故障事件(又称顶端事件)发生的概率。
同时也可以用来分析零件、部件或子系统故障对系统故障的影响,其中包括人为因素和环境条件等在内。
它对系统故障不但可以做定性的而且还可以做定量的分析;不仅可以分析由单一构件所引起的系统故障,而且也可以分析多个构件不同模式故障而产生的系统故障情况。
因为故障树分析法使用的是一个逻辑图,因此,不论是设计人员或是使用和维修人员都容易掌握和运用,并且由它可派生出其他专门用途的“树”。
例如,可以绘制出专用于研究维修问题的维修树,用于研究经济效益及方案比较的决策树等。
由于故障树是一种逻辑门所构成的逻辑图,因此适合于用电子计算机来计算;而且对于复杂系统的故障树的构成和分析,也只有在应用计算机的条件下才能实现。
显然,故障树分析法也存在一些缺点。
其中主要是构造故障树的多余量相当繁重,难度也较大,对分析人员的要求也较高,因而限制了它的推广和普及。
基于故障树分析法的挖掘机故障诊断知识库设计

器箱箱故 动 合速动盘 作 客耋翁釜 lll l I l I 《动 轴
故 I l l f 操 障l I l l l I l J 障l 故 故I 故 障l 障l 障
纵 故
工
障 组【 l I l 故l 】 l 清 故I l 达I _ l 头l 障l
障[ I l 】 障l { 】 I 故l 障I 故 器
液压 缸 达不 到 预定 的速 度 (
液压缸进油路泄漏( 。 一j )
l 液压缸损伤
压缸回油
7 太大 4 )
定 缸同i 压 l 力太大 (
l 压泵损伤 液
——丰 ~
E 回油、 ,一 压 缸 内 、、 / 内部 油 路 、、 / 吸 人 大 量 、、 /一转 速 太 低 、、 /一 侧 板 磨 损 缸 、 , r液 , , 一 r
蓁I If l l 菱藿 ll f f 薰藿 l调 f空 故 萎障
传
动 系 统 故
机 械
障
1 故 障 诊 断 模 型 建 立
1 1 故 障树模 型建 立 .
油 操 l l l 纵 I I 回l I 】 转l 】 l 缸 压I l 油 液l J 工 作 泵 故 阀l l l I 1 l 接l 故 马I 滤
墨 墨
! :
长春工程学院学报 ( 自然 科 学 版 )2 1 0 2年 第 l 卷 第 l 3 期
J C a g h n I s . c . Na . c. i ) 2 1 。 1 1 No 1 . h n c u n t Te h ( t S i Ed . , 0 2 Vo . 3. .
奎 兰 !
型 / 塾 /
墨 / 窒 ! / !
!
里! ! 翌
机械密封故障分析——故障树分析方法
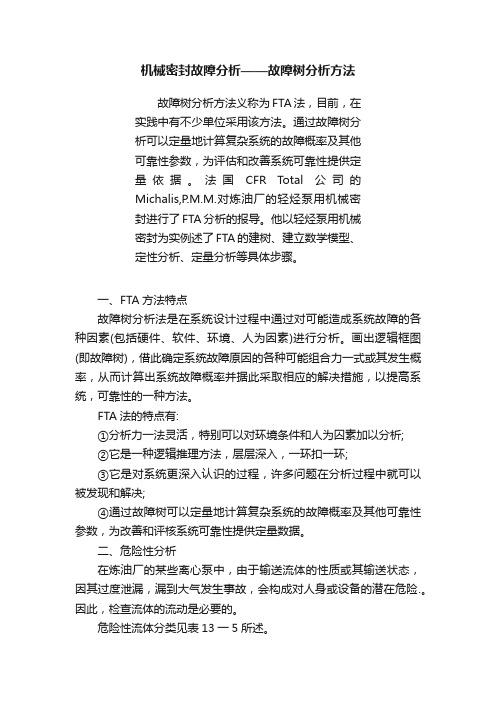
机械密封故障分析——故障树分析方法故障树分析方法义称为FTA法,目前,在实践中有不少单位采用该方法。
通过故障树分析可以定量地计算复杂系统的故障概率及其他可靠性参数,为评估和改善系统可靠性提供定量依据。
法国CFR Total公司的Michalis,P.M.M.对炼油厂的轻烃泵用机械密封进行了FTA分析的报导。
他以轻烃泵用机械密封为实例述了FTA的建树、建立数学模型、定性分析、定量分析等具体步骤。
一、FTA方法特点故障树分析法是在系统设计过程中通过对可能造成系统故障的各种因素(包括硬件、软件、环境、人为因素)进行分析。
画出逻辑框图(即故障树),借此确定系统故障原因的各种可能组合力一式或其发生概率,从而计算出系统故障概率并据此采取相应的解决措施,以提高系统,可靠性的一种方法。
FTA法的特点有:①分析力一法灵活,特别可以对环境条件和人为囚素加以分析;②它是一种逻辑推理方法,层层深入,一环扣一环;③它是对系统更深入认识的过程,许多问题在分析过程中就可以被发现和解决;④通过故障树可以定量地计算复杂系统的故障概率及其他可靠性参数,为改善和评核系统可靠性提供定量数据。
二、危险性分析在炼油厂的某些离心泵中,由于输送流体的性质或其输送状态,因其过度泄漏,漏到大气发生事故,会构成对人身或设备的潜在危险.。
因此,检查流体的流动是必要的。
危险性流体分类见表13一5所述。
炼油厂机械密封所发生故障级别分类及所导致的后果见表13一6所述。
对以上流体,根据机械密封最初发生过度泄漏的事故作一因/果示意图,可以判定九组可能发生的不同情况的后果C1至C9,见图13一28:这些后果取决于以下参数,如所采用的机械密封类刑、要堵住流体的类型、有无报警仪器系统、外部事件的作用等。
根据图13一2,可能引起严重后果和灾难性后果的情况.见表13一7所述。
三、故障树分析通过机械密封系统“故障树”的分析,有可能将导致带来不希望故障的原始事件加以分类。
分类的依据是:故障类型(腐蚀、热影响、机械影响……),故障原因(设计不良、工艺过程、泵、辅助流体),应负责任者(设计人员、维修人员、用户)。
基于故障树分析法的数控机床故障诊断

基于故障树分析法的数控机床故障诊断【摘要】故障树分析法可进行数控机床故障分析,寻找故障点和分析故障原因,是一种相当有效的数控机床故障诊断方法。
【关键词】数控机床;故障树;诊断数控机床是指应用了数控技术对其加工过程进行自动控制的机床,伴随着中国制造业的快速发展,数控机床已经广泛应用于几乎所有的制造行业。
为了提高生产效率,其中之一就是要提高机床有效度,即当机床出现故障时,就要采取科学合理的方法找出故障点并排除故障,减少故障时间。
故障树分析(Fault Tree Analysis,FTA)可进行故障分析,寻找故障点和分析故障原因,是一种相当有效的数控机床故障诊断方法。
1故障树分析法故障树分析法是一种由果到因的演绎分析方法,它是基于故障的层次特性及故障成因和后果的关系,将系统故障形成的原因由总体至部件按树枝状逐级细化的分析方法。
1.1故障树定义故障树分析中,把所研究系统最不希望发生的故障状态作为故障分析的目标,这个最不希望发生的系统故障事件称为顶事件。
然后找出直接导致这一故障发生的全部因素,它可能是部件中硬件失效、人为差错、环境因素以及其它有关事件,把它们作为第二级。
再找出造成第二级事件发生的全部直接因素作为第三级,如此逐级展开,一直追溯到那些不能再展开或毋需再深究的最基本的故障事件为止。
这些不能再展开或毋需再深究的最基本的故障事件称为底事件,而介于顶事件和底事件之间的其它故障事件称为中间事件。
把顶事件、中间事件和底事件用适当的逻辑门自上而下逐级连接起来所构成的逻辑结构图就是故障树。
1.2建立故障树的步骤1)确定故障树的顶事件。
顶事件是系统级故障事件,对于数控机床故障,顶事件应满足:(1)顶事件的发生与否必须有明确的定义;(2)顶事件必须是能进一步分解的,即可以找出使顶事件发生的次级事件;(3)顶事件必须能够度量。
2)确定故障树的边界条件。
故障树边界条件应包括:(1)初始状态应指明与顶事件发生有关的部件的工作状态。
- 1、下载文档前请自行甄别文档内容的完整性,平台不提供额外的编辑、内容补充、找答案等附加服务。
- 2、"仅部分预览"的文档,不可在线预览部分如存在完整性等问题,可反馈申请退款(可完整预览的文档不适用该条件!)。
- 3、如文档侵犯您的权益,请联系客服反馈,我们会尽快为您处理(人工客服工作时间:9:00-18:30)。
基于故障树的复杂机械设备排故策略设计
摘要:复杂机械设备发生故障后的排故策略会影响到故障诊断的速度,进而影响到生产进度,工程中常用故障树(FTA)设计排故策略。
诊断重要度(DIF)是基于FTA故障诊断的关键因子,然而并未考虑诊断时间和费用。
通过修正故障判明效时比的定义,给出了时间诊断重要度的概念(TDIF)。
在综合诊断重要度、诊断时间和费用的基础上,提出了费用–时间诊断重要度(CTDIF)的概念,并给出了计算公式。
最后以某型采煤机的发动机为例,对基于DIF、CDIF、TDIF 和CTDIF的排故策略进行了对比计算。
关键词:故障树;费用-时间诊断重要度;故障诊断;复杂机械设备
引言
复杂机械设备一旦发生故障,极有可能会因为故障排查的复杂性而造成长时间的停机。
设计高效的复杂机械设备故障排查策略是解决这一问题的主要方法。
复杂机械设备故障诊断的目的是定位造成系统故障的根本原因,其思路可总结为:首先假定一组故障原因集;然后综合各种方法和数据对该组集合进行分析判断;最后通过排除法、推理法或其它方法判断出导致系统故障的原因。
故障树分析方法(Fault Tree Analysis,FTA)起源于系统安全分析领域,其核心思路是通过对顶事件的推演得到导致该事件发生的基本事件组合[1]。
由于该方法可从定性和定量两方面对系统进行分析,因此也广泛应用于故障诊断领域。
基于FTA 的故障诊断中,如何根据重要度确定部件的诊断顺序是关键。
1.术语定义
综合分析以上文献的优点和缺点,本文提出一种新的基本FTA的故障诊断方法。
为叙述方便,首先定义以下概念。
定义1:TDIF(Time and Diagnostics Importance Factor):时间诊断重要度,指单位时间内的诊断重要度。
定义2:CTDIF(Cost-Tme and Diagnostics Importance Factor):费用—时间诊断重要度,指单位时间内每单位成本的诊断重要度。
定义3:MCTD(Mean Cost to Detection):平均故障检测费用,产品从开始检测到检测完毕并给出是否故障的结论所产生的平均检测费用。
对于这三个定义的深入解释将在下文中结合算法和实例给出。
2.基于CTDIF的诊断方法设计
本文设计的基本FTA的故障诊断方法为:
2.1获取故障树定性、定量分析的结果数据。
针对某一故障现象,确定其对应的顶事件,查找有关该顶事件的故障树,获取关于该故障树的最小割集、底事件故障概率、已计算出的各最小割集概率以及顶事件的发生概率。
2.2计算各基本部件、最小割集的CTDIF,并进行排序。
2.2.1α和β的确定
公式n中,α和β分别被称为CDIF的权重因子和TDIF的权重因子,且α+β=1。
这两个参数表明了本次故障诊断中对时间和费用的度量程度,即若现实要求对时间较苛刻,则可取α>β;若对费用比较敏感,则可取α<β;若对费用和时间同等看待,则可取α=β=0.5。
特殊情况下,若取α=1且β=0,则退化为CTDIF=CDIF;若取α=0且β=1,则退化为CTDIF=TDIF。
2.2.2 基于MCTD的CDIF重定义
对于部件的诊断费用,本文通过MCTD进行定义。
对于该值的估算,可按以下原则进行:
(1)当部件或单元的测试费用固定时,按该费用做为其MCTD。
如一些设备的故障检测供货商(特别是进口设备)在保修期外是要收取固定诊断费用的,此时可令该费用做为其MCTD。
(2)定量计算。
假设在不考虑人工费的情况下,价格c万元,预计使用y 年,每年估计平均使用m次,则该设备的每次检测费用可估计为:。
(3)定性估计。
在难以定量计算MCTD时,可结合专家建议和检测过程进行定性估值。
在确定MCTD之后,本文将公式n重新定义为:,其中i代表第i个基本部件。
2.2.3 割集重要度的计算方法
最小割集的诊断重要度DIFMCSi的公式为该割集发生概率P(MCSi)与系统故障概率P(S)的比值[7]。
最小割集的TDIF、CDIF和CTDIF与求基本部件的公式一致,只需把部件的DIF改为最小割集的DIF、把部件的测试时间和费用改为割集中各部件的测试时间和费用之和即可,此处不在敷述。
2.2.4将部件和割集的CDIF、TDIF归一化处理
为使CDIF和TDIF在计算CTDIF的过程中具有可比性,需要将计算结果进行归一化处理,即将各部件和各割集的CDIF和TDIF变为(0,1)之间的小数。
2.2.5 排序原则
系统故障是由最小割集引起的,因此首先应按最小割集的CTDIF进行排序,同一最小割集的各基本部件再按其各自的CTDIF从大到小排序[7]。
2.3根据排序结果生成决策诊断树DDT。
关于将故障树转换为DDT的方法可参见文献[3]。
3.实例分析
下面以某型采煤机的发动机故障诊断为例进行分析验证。
该故障树共有5个割集,分别为:C1={x1,x2},C2={ x1,x4},C3={ x1,x3,x5},C4={x2,x3,x5},C5={x3,x4,x5}。
顶事件T的发生概率为P(T)=6.93E-4
由于计算过程会用到P(T|C)、MIF,因此这里一并给出相关结果。
关于P (T|C)、MIF和DIF的定义、公式及其物理意义参见文献2。
为了对本文提出的方法进行评判,下面从系统诊断准确度、系统平均诊断时间和系统平均诊断费用三个方面对CTDIF法和DIF法进行比较。
为了计算方便,这里忽略割集间的相关性。
经比较可以得出以下结论:3.1由DIF可知,系统诊断准确度最小的诊断策略并不是最优的;
3.2最省时间的诊断策略其诊断费用最高,而费用最省的诊断策略其诊断时间最长(分别见表4TDIF和CDIF);
3.3CTDIF是一种折衷的诊断策略,可根据对时间和费用的重视程度调整参数α和β;
3.4诊断时若按DIF进行割集排序,尽管其系统诊断准确度(即平均要检测的割集数)要比按CTDIF的小,但其平均诊断时间和平均诊断费用都要高于CTDIF。
4.总结
针对复杂机械设备故障排查困难这一问题,研究了基于FTA的故障检测方法。
诊断重要度是应用FTA方法设计诊断策略的关键。
本文在此基础上,综合考虑了诊断时间和费用,提出了CTDIF的概念。
该方法适用于在无任何先验信息、无任何维修经验、且需要考虑诊断成本的维修诊断场合。
参考文献:
[1] Vesely W.E. Fault Tree Handbook[M],Technical Report NUREG-0492,US Nuclear Regulatory Committee,Washington,1981.
[2] Y. Dutuit,A. Rauzy. Efficient Algorithms to Assess Component and Gate Importance in Fault Tree Analysis[J],Reliability Engineering & System Safety,2001:213-221.
[3]T. Assaf,J.B. Dugan. Diagnosis Based on Reliability Analysis Using Monitors and Sensors[J],Reliability Engineering & System Safety,2007:509-521.
[4]T. Assaf,J.B. Dugan. Design For Diagnosis Using a Diagnostic Evaluation Measure[J],Instrumentation & Measurement Magazine,IEEE,2006:37-43.
[5]张超,马存宝,宋东,许家栋.基于动态故障树分析的容错系统机内测试诊断策略设计[J],兵工学报,2008:602-607.
[6]倪绍徐,张裕芳,易宏,梁晓锋.基于故障树的智能故障诊断方法[J],上海交通大学学报,2008:1372-1375.
[7]陶勇剑,董德存,任鹏.采用故障树分析诊断系统故障的改进方法[J],哈尔滨工业大学学报,2010:157-158.
[8]C.L. Smith,S.T. Wood,W.J. Galyean. Systems Analysis Programs for Hands-On Integrated Reliability Evaluations Technical Reference[M],Technical Report INL/EXT-05-00327,US Nuclear Regulatory Committee,Washington,2008.。