SST6838T216;中文规格书,Datasheet资料
AEMC PowerPad III Model 8336产品说明书

Transient Capture on theAEMC PowerPad III Model 8336Transients are short-term current and voltage phenomena that occur in the system under measurement. The process the AEMC PowerPad III Model 8336 uses for recording transients is as follows:•The instrument sampling rate is a constant256 samples per cycle.•When a transient search is started on theinstrument, each sample is compared to thecorresponding sample from the precedingcycle.•The transient threshold is the user-definedamount of volts or amps for any datapoint todiffer from the corresponding datapointexactly 1 cycle earlier. The preceding cycledefines the mid-point of the trigger envelopeand is used as reference.•As soon as a sample is outside the envelope,the triggering event occurs; the transient datais then captured by the instrument.•The cycle preceding the event and the threefollowing cycles are saved to memory.The following explains how to configure, schedule,and view a transient recording session on the Model8336. These instructions assume you are using theModel 8336 as a standalone instrument.Note that you can also perform these tasks by connecting the instrument to a computer running AEMC’s DataView software. For more information, see the PowerPad III Model 8336 User Guide.Transient Recording Configuration1. With the instrument turned ON, press the button to display the Waveform Capturescreen.2. Ensure Transient is highlighted, then press .●If there are no transient detection sessions stored in the instrument, the DetectionSchedule screen appears.●If there are recordings in the instrument, the Detection List screen is displayed. In thiscase, press to display the Detection Schedule screen.3. Press the function button under the icon to display the Voltage Thresholdsscreen. At the top of the screen is the Threshold Set-up field. Options are:●4V: The same voltage difference threshold applies to all phases and the neutral in theelectrical hook-up●3V+VN: One threshold applies to the phases and one applies to neutral●V1+V2+V3+V4: Each phase and neutral has its own assigned thresholdDepending on the electrical hook-up currently under measurement, not all these options may be available.4. The setting in this field determines which of the four fields below it (1, 2, 3, and N) areeditable:●4V: a single field is active for 1, 2, 3, and N.●3V+VN: one field is active for 1, 2, and 3; and another is active for N.●V1+V2+V3+N: each field is active.To edit a voltage threshold field, highlight it using the up and down arrow buttons, thenconfirm the selection by pressing . Use the left and right arrows to select a digit, and the up and down arrows to change it. You can also use these buttons to select units (V or kV).Press to confirm the edited field.5. Press the A button to display the Current Thresholds screen. This is similar to the VoltageThreshold screen. You can select which thresholds apply to which phases, and specify the value of the threshold (1mA through 9999kA). As with the voltage thresholds, not all these options may apply to all electrical hook-up types.Note that current transients typically occur frequently. We recommend performing a current transient search only when looking for a specific type of transient. At other times, such as when you are primarily interested in voltage transients, you can effectively disable current transient searching by setting the threshold to its maximum value.Scheduling Transient Detection1. Press the button to display the Waveform Capture screen.2. Ensure Transient is highlighted, then press .●If there are no transient detection sessions stored in the instrument, the DetectionSchedule screen appears.●If there are recordings in the instrument, the Detection List screen is displayed. In thiscase, press the button to display the Detection Schedule screen.3. This screen displays four input fields:●Start defines the time and date when the recording starts. This must be later than thecurrent date and time.●Stop specifies when the recording ends. This must be later than the start date and time.●Transient Count defines the maximum number of transients that you want to capturebefore stopping the session.●Name allows you to name the test. This can be 8 characters long.4. Use the arrow and buttons to highlight, select, and edit these fields.5. Press the button to write the settings to the instrument and start the session.6. If not enough memory is available, an error message appears informing you of this.Otherwise, the transient detection session will begin at the scheduled start time and date.If a session is scheduled but not yet started, the message DETECTION ON STANDBY appears on the screen until the start time is reached, at which point the message changes to DETECTION IN PROGRESS.When the session is active, the icon blinks at the top of the screen, along with a status bar showing the progress of the session. In addition, the (stop) button appears in place of .During the session, the Transient Count number is reduced by 1 every time a transient is recorded. If this number counts down rapidly and appears as though it will reach zero well before stop time is reached, we recommend stopping the session and setting the threshold to a higher, less sensitive value. The session will continue until: (1) you press , (2) the Transient Count limit is reached (see Step 3), or (3) the stop time/date is reached.7. When the transient detection session is finished, it appears in the Detection List screen. Youcan now open the session and view its contents, as explained in the following.Viewing a Transient Detection Session1. At the Detection Schedule screen, press the button.For all other displayed screens, press the button, and then select Transient.Either action displays the Detection List screen.2. If more than one transient detection recording is stored, use the arrows to select thedesired recording, then press to open it.In the preceding illustration:1 Location in the record of the zonedisplayed.4 Move cursor to transient triggering time.2 Instantaneous value of the signalsaccording to the position of the cursor on the scale. Use ◄ and ► to move cursor.5 Number assigned to displayed graph (e.g.1 is highlighted indicating channel V1 triggered capture of the transient)3 Move cursor to one period of the signalbefore transient triggering time. 6 Zoom In/Out。
NCP1015AP100G;NCP1015AP065G;NCP1015ST100T3G;NCP1015ST65T3G;中文规格书,Datasheet资料

1
8
2
7
3
4
5
GND Figure 1. Typical Application Example
PIN FUNCTION DESCRIPTION
Pin No.
SOT−223
PDIP−7
Pin Name
1
1
VCC
−
2
NC
−
3
GND
2
4
FB
3
5
DRAIN
−
−
−
−
7
GND
4
8
GND
Function Powers the Internal Circuitry
MARKING DIAGRAMS
8 1
PDIP−7 CASE 626A AP SUFFIX
P1015APyy AWL
YYWWG
1
4
4
SOT−223
CASE 318E
1
ST SUFFIX
AYW 1015y G
G
1
yy y A WL YY WW G or G
= 06 (65 kHz), 10 (100 kHz) = A (65 kHz), B (100 kHz) = Assembly Location = Wafer Lot = Year = Work Week = Pb−Free Package
1
Publication Order Number:
NCP1015/D
NCP1015
Indicative Maximum Output Power from NCP1015
RDS(on) − Ip
230 Vac
安捷伦8163 光波万用表说明书
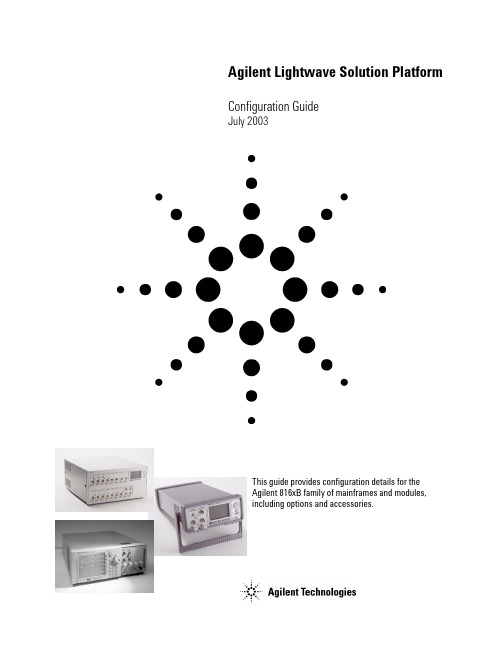
Page 2 of 14
Module compatibility
81600B TLS family #200, #160, #150, #140 low SSE #142, #132 high power
81980A compact TLS 81940A compact TLS 81989A compact TLS 81949A compact TLS
page 4 page 4
page 5 page 5 page 5 page 5
page 6 page 6
7 page 7 page 7
page 8 page 8 page 8 page 8
page 9/10 page 9/10
page 9 page 9 page 9
81662A dfb source module 81663A dfb source module
81650A fp source module 81651A fp source module 81654A fp source module
81655A fp source module 81656A fp source module 81657A fp source module
Note: 81600B - 072 is highly recommended over 81600B - 071 to reduce front-panel reflections, which will greatly reduce interference noise and spectral ripple in the test setup.
High Power Compact Tunable Laser module
TM1638规格书
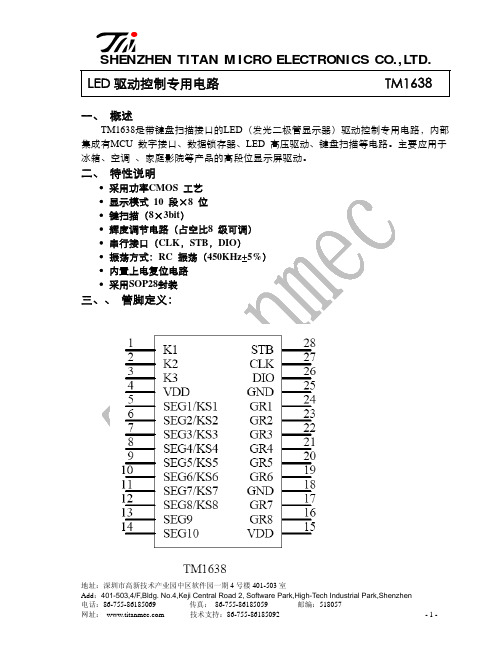
Add:401-503,4/F,Bldg. No.4,Keji Central Road 2, Software Park,High-Tech Industrial Park,Shenzhen
电话:86-755-86185069
传真: 86-755-86185059
邮编:518057
网址:
℃
储存温度
Tstg
-65 ~+150
℃
正常工作范围(Ta = -20 ~ +70℃,Vss = 0 V)
参数
符号
最小
典型 最大 单位
逻辑电源电压
VDD
5
V
高电平输入电压
VIH
0.7 VDD
-
VDD
V
测试条件 -
低电平输入电压
VIL
0
-
0.3 VDD
V
-
电气特性(Ta = -20 ~ +70℃,VDD = 4.5 ~ 5.5 V, Vss = 0 V
技术支持:86-755-86185092
-1-
深圳市天微电子有限公司
SHENZHEN TITAN M ICRO ELECTRONI CS CO.,LTD.
四、管脚功能说明:
符号
管脚名称
说明
DIN
数据输入
在时钟上升沿输入串行数据,从低位开始
DOUT STB
数据输出
在时钟下降沿输出串行数据,从低位开始。输出 为N-ch open drain
二、 特性说明
• 采用功率CMOS 工艺 • 显示模式 10 段×8 位 • 键扫描(8×3bit) • 辉度调节电路(占空比8 级可调) • 串行接口(CLK,STB,DIO) • 振荡方式:RC 振荡(450KHz+5%) • 内置上电复位电路 • 采用SOP28封装
FGD4536TM;中文规格书,Datasheet资料

I CES Collector Cut-Off Current V CE = V CES, V GE = 0V--100µA I GES G-E Leakage Current V GE = V GES, V CE = 0V --±400nAOn CharacteristicsV GE(th)G-E Threshold Voltage I C = 250µA, V CE = V GE 2.4 3.3 4.0VV CE(sat)Collector to EmitterSaturation Voltage I C = 20A, V GE = 15V- 1.19-V I C = 30A, V GE = 15V- 1.33-V I C = 50A, V GE = 15V,T C = 25o C- 1.59 1.8V I C = 50A, V GE = 15V,T C = 125o C- 1.66-VDynamic CharacteristicsC ies Input CapacitanceV CE = 30V, V GE = 0V,f = 1MHz -1295-pFC oes Output Capacitance-56-pF C res Reverse Transfer Capacitance-43-pFSwitching Characteristicst d(on)Turn-On Delay TimeV CC = 200V, I C = 20A,R G = 5Ω, V GE = 15V,Resistive L oad, T C = 25o C -5-nst r Rise Time-20-ns t d(off)Turn-Off Delay Time-41-ns t f Fall Time-182-nst d(on)Turn-On Delay TimeV CC = 200V, I C = 20A,R G = 5Ω, V GE = 15V,Resistive Load, T C = 125o C -5-nst r Rise Time-21-ns t d(off)Turn-Off Delay Time-43-ns t f Fall Time-249-nsQ g Total Gate ChargeV CE = 200V, I C = 20A,V GE = 15V -47-nCQ ge Gate to Emitter Charge- 5.4-nC Q gc Gate to Collector Charge-15-nCDimensions in Millimeters*Trademarks of System General Corporation, used under license by Fairchild Semiconductor.DISCLAIMERFAIRCHILD SEMICONDUCTOR RESERVES THE RIGHT TO MAKE CHANGES WITHOUT FURTHER NOTICE TO ANY PRODUCTS HEREIN TO IMPROVE RELIABILITY, FUNCTION, OR DESIGN. FAIRCHILD DOES NOT ASSUME ANY LIABILITY ARISING OUT OF THE APPLICATION OR USE OF ANY PRODUCT OR CIRCUIT DESCRIBED HEREIN; NEITHER DOES IT CONVEY ANY LICENSE UNDER ITS PATENT RIGHTS, NOR THE RIGHTS OF OTHERS.THESE SPECIFICATIONS DO NOT EXPAND THE TERMS OF FAIRCHILD’S WORLDWIDE TERMS AND CONDITIONS, SPECIFICALLY THE WARRANTY THEREIN, WHICH COVERS THESE PRODUCTS.LIFE SUPPORT POLICYFAIRCHILD’S PRODUCTS ARE NOT AUTHORIZED FOR USE AS CRITICAL COMPONENTS IN LIFE SUPPORT DEVICES OR SYSTEMS WITHOUT THE EXPRESS WRITTEN APPROVAL OF FAIRCHILD SEMICONDUCTOR CORPORATION.As used here in:1. Life support devices or systems are devices or systems which, (a) areintended for surgical implant into the body or (b) support or sustain life,and (c) whose failure to perform when properly used in accordance with instructions for use provided in the labeling, can be reasonably expected to result in a significant injury of the user.2.A critical component in any component of a life support, device, or system whose failure to perform can be reasonably expected to cause the failure of the life support device or system, or to affect its safety or effectiveness.PRODUCT STATUS DEFINITIONS Definition of TermsDEUXPEED ®Dual Cool™EcoSPARK ®EfficentMax™ESBC™Fairchild ®Fairchild Semiconductor ®FACT Quiet Series™FACT®FAST ®FastvCore™FETBench™FlashWriter ® *FPS™ISOPLANAR™MegaBuck™MICROCOUPLER™MicroFET™MicroPak™MicroPak2™MillerDrive™MotionMax™Motion-SPM™OptiHiT™OPTOLOGIC ®OPTOPLANAR ®®PDP SPM™Power-SPM™Saving our world, 1mW/W/kW at a time™SignalWise™SmartMax™SMART START™SPM ®STEALTH™SuperFET ®SuperSOT™-3SuperSOT™-6SuperSOT™-8SupreMOS ®SyncFET™Sync-Lock™ ®*TINYOPTO™TinyPower™TinyPWM™TinyWire™TriFault Detect™TRUECURRENT™*µSerDes™UHC ®Ultra FRFET™UniFET™VCX™VisualMax™XS™®Datasheet Identification Product Status DefinitionAdvance Information Formative / In Design Datasheet contains the design specifications for product development. Specifications ANTI-COUNTERFEITING POLICYFairchild Semiconductor Corporation’s Anti-Counterfeiting Policy. Fairchild’s Anti-Counterfeiting Policy is also stated on our external website,, under Sales Support .Counterfeiting of semiconductor parts is a growing problem in the industry. All manufactures of semiconductor products are experiencing counterfeiting of their parts. Customers who inadvertently purchase counterfeit parts experience many problems such as loss of brand reputation, substandard performance, failed application, and increased cost of production and manufacturing delays. Fairchild is taking strong measures to protect ourselves and our customers from the proliferation of counterfeit parts. Fairchild strongly encourages customers to purchase Fairchild parts either directly from Fairchild or from Authorized Fairchild Distributors who are listed by country on our web page cited above. Products customers buy either from Fairchild directly or from Authorized Fairchild Distributors are genuine parts, have full traceability, meet Fairchild’s quality standards for handing and storage and provide access to Fairchild’s full range of up-to-date technical and product information. Fairchild and our Authorized Distributors will stand behind all warranties and will appropriately address and warranty issues that may arise. Fairchild will not provide any warranty coverage or other assistance for parts bought from Unauthorized Sources. Fairchild is committed to combat this global problem and encourage our customers to do their part in stopping this practice by buying direct or from authorized distributors.分销商库存信息: FAIRCHILDFGD4536TM。
742863160;中文规格书,Datasheet资料

3.1 3.0 2.02012-06-272012-03-292009-08-13SStSStSMuSStSMu-Würth Elektronik eiSos GmbH & Co. KGEMC & Inductive SolutionsMax-Eyth-Str. 174638 WaldenburgGermanyTel. +49 (0) 79 42 945 - 0A Dimensions: [mm]F Typical Impedance Characteristics:Test Equipment: E4991A or equivalentF Derating Curve:H1: Classification Reflow Profile for SMT components:H2: Classification Reflow ProfilesProfile FeaturePreheat- Temperature Min (T smin ) - Temperature Max (T smax ) - Time (t s ) from (T smin to T smax )Ramp-up rate (T L to T P )Liquidous temperature (T L )Time (t L ) maintained above T L Peak package body temperature (T p )Time within 5°C of actual peak temperature (t p )Ramp-down rate (T P to T L )Time 25°C to peak temperature Pb-Free Assembly 150°C 200°C60-180 seconds 3°C/ second max.217°C60-150 seconds See Table H320-30 seconds 6°C/ second max.8 minutes max.refer to IPC/JEDEC J-STD-020DH3: Package Classification Reflow TemperaturePB-Free Assembly PB-Free Assembly PB-Free Assembly Package Thickness< 1.6 mm 1.6 - 2.5 mm ≥ 2.5 mmVolume mm³<350260°C 260°C 250°CVolume mm³350 - 2000260°C 250°C 245°CVolume mm³>2000260°C 245°C 245°Crefer to IPC/JEDEC J-STD-020DH Soldering Specifications:I Cautions and Warnings:The following conditions apply to all goods within the product series of WE-CBF HFof Würth Elektronik eiSos GmbH & Co. KG:General:All recommendations according to the general technical specifications of the data-sheet have to be complied with.The disposal and operation of the product within ambient conditions which probably alloy or harm the component surface has to be avoided.If the product is potted in customer applications, the potting material might shrink during and after hardening. Accordingly to this the product is exposed to the pressure of the potting material with the effect that the ferrite body and termination is possibly damaged by this pressure and so the electrical as well as the mechanical characteristics are endanger to be affected. After the potting material is cured, the ferrite body and termination of the product have to be checked if any reduced electrical or mechanical functions or destructions have occurred.The responsibility for the applicability of customer specific products and use in a particular customer design is always within the authority of the customer. All technical specifications for standard products do also apply for customer specific products.Washing varnish agent that is used during the production to clean the application might damage or change the characteristics of the plating. The washing varnish agent could have a negative effect on the long term function of the product.Direct mechanical impact to the product shall be prevented as the ferrite material of the ferrite body could flake or in the worst case it could break.Product specific:Follow all instructions mentioned in the datasheet, especially:•The solder profile has to be complied with according to the technical reflow soldering specification, otherwise no warranty will be sustai-ned.• Wave soldering is only allowed after evaluation and approval.•All products are supposed to be used before the end of the period of 12 months based on the product date-code, if not a 100% solderabi-lity can´t be warranted.•Violation of the technical product specifications such as exceeding the nominal rated current will result in the loss of warranty.1. General Customer ResponsibilitySome goods within the product range of Würth Elektronik eiSos GmbH & Co. KG contain statements regarding general suitability for certain application areas. These statements about suitability are based on our knowledge and experience of typical requirements concerning the are-as, serve as general guidance and cannot be estimated as binding statements about the suitability for a customer application. The responsibi-lity for the applicability and use in a particular customer design is always solely within the authority of the customer. Due to this fact it is up to the customer to evaluate, where appropriate to investigate and decide whether the device with the specific product characteristics described in the product specification is valid and suitable for the respective customer application or not.2. Customer Responsibility related to Specific, in particular Safety-Relevant ApplicationsIt has to be clearly pointed out that the possibility of a malfunction of electronic components or failure before the end of the usual lifetime can-not be completely eliminated in the current state of the art, even if the products are operated within the range of the specifications.In certain customer applications requiring a very high level of safety and especially in customer applications in which the malfunction or failure of an electronic component could endanger human life or health it must be ensured by most advanced technological aid of suitable design of the customer application that no injury or damage is caused to third parties in the event of malfunction or failure of an electronic component.3. Best Care and AttentionAny product-specific notes, warnings and cautions must be strictly observed.4. Customer Support for Product SpecificationsSome products within the product range may contain substances which are subject to restrictions in certain jurisdictions in order to serve spe-cific technical requirements. Necessary information is available on request. In this case the field sales engineer or the internal sales person in charge should be contacted who will be happy to support in this matter.5. Product R&DDue to constant product improvement product specifications may change from time to time. As a standard reporting procedure of the Product Change Notification (PCN) according to the JEDEC-Standard inform about minor and major changes. In case of further queries regarding the PCN, the field sales engineer or the internal sales person in charge should be contacted. The basic responsibility of the customer as per Secti-on 1 and 2 remains unaffected.6. Product Life CycleDue to technical progress and economical evaluation we also reserve the right to discontinue production and delivery of products. As a stan-dard reporting procedure of the Product Termination Notification (PTN) according to the JEDEC-Standard we will inform at an early stage about inevitable product discontinuance. According to this we cannot guarantee that all products within our product range will always be available. Therefore it needs to be verified with the field sales engineer or the internal sales person in charge about the current product availability ex-pectancy before or when the product for application design-in disposal is considered.The approach named above does not apply in the case of individual agreements deviating from the foregoing for customer-specific products.7. Property RightsAll the rights for contractual products produced by Würth Elektronik eiSos GmbH & Co. KG on the basis of ideas, development contracts as well as models or templates that are subject to copyright, patent or commercial protection supplied to the customer will remain with Würth Elektronik eiSos GmbH & Co. KG.8. General Terms and ConditionsUnless otherwise agreed in individual contracts, all orders are subject to the current version of the “General Terms and Conditions of Würth Elektronik eiSos Group”, last version available at .J Important Notes:The following conditions apply to all goods within the product range of Würth Elektronik eiSos GmbH & Co. KG:分销商库存信息: WURTH-ELECTRONICS 742863160。
si823x中文数据手册
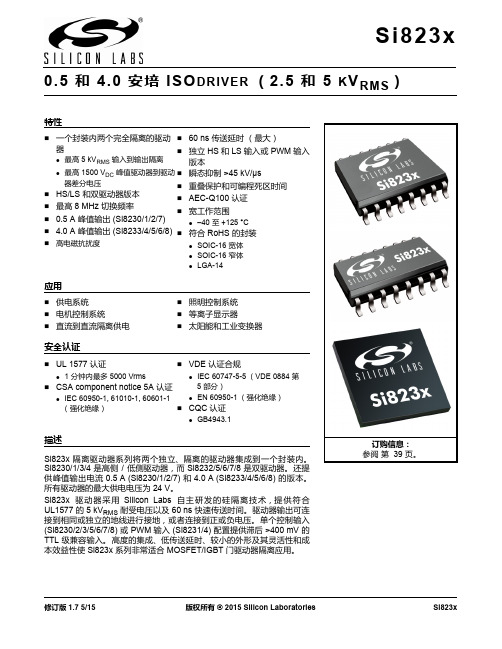
0.5 和 4.0 安 培 I S O D R I V E R ( 2. 5 和 5
特性
KVRMS)
一个封装内两个完全隔离的驱动 60 ns 传送延时 (最大) 器 独立 HS 和 LS 输入或 PWM 输入 最高 5 kVRMS 输入到输出隔离 版本 最高 1500 VDC 峰值驱动器到驱动 瞬态抑制 >45 kV/µs
宽体 SOIC-16 窄体 LGA-14
SOIC-16
应用
供电系统 电机控制系统 直流到直流隔离供电
照明控制系统 等离子显示器 太阳能和工业变换器
安全认证
UL 1577 认证
1
VDE 认证合规
60747-5-5 (VDE 0884 第 5 部分) EN 60950-1 (强化绝缘)
IEC
分钟内最多 5000 Vrms
CSA component notice 5A 认证
IEC
60950-1, 61010-1, 60601-1 CQC 认证 (强化绝缘) GB4943.1
描述
Si823x 隔离驱动器系列将两个独立、隔离的驱动器集成到一个封装内。 Si8230/1/3/4 是高侧 / 低侧驱动器,而 Si8232/5/6/7/8 是双驱动器。 还提 供峰值输出电流 0.5 A (Si8230/1/2/7) 和 4.0 A (Si8233/4/5/6/8) 的版本。 所有驱动器的最大供电电压为 24 V。 Si823x 驱 动 器 采 用 Silicon Labs 自 主 研 发 的 硅 隔 离 技 术,提 供 符 合 UL1577 的 5 kVRMS 耐受电压以及 60 ns 快速传送时间。 驱动器输出可连 接到相同或独立的地线进行接地,或者连接到正或负电压。 单个控制输入 (Si8230/2/3/5/6/7/8) 或 PWM 输入 (Si8231/4) 配置提供滞后 >400 mV 的 TTL 级兼容输入。 高度的集成、低传送延时、较小的外形及其灵活性和成 本效益性使 Si823x 系列非常适合 MOSFET/IGBT 门驱动器隔离应用。
DMG4466SSSL-13;中文规格书,Datasheet资料

Features• Low On-Resistance • Low Input Capacitance • Fast Switching Speed • Low Input/Output Leakage • Low Gate Resistance • Lead Free By Design/RoHS Compliant (Note 1) • "Green" Device (Note 2) • Qualified to AEC-Q101 Standards for High ReliabilityMechanical Data• Case: SO-8 • Case Material: Molded Plastic, “Green” Molding Compound.UL Flammability Classification Rating 94V-0 • Moisture Sensitivity: Level 1 per J-STD-020 • Terminal Connections: See Diagram Below • Marking Information: See Page 5 • Ordering Information: See Page 5 • Weight: 0.072 grams (approximate)Maximum Ratings @T A = 25°C unless otherwise specifiedCharacteristicSymbol Value UnitDrain-Source Voltage V DSS 30 V Gate-Source VoltageV GSS±20 V Continuous Drain Current (Note 3)Steady StateT A = 25°C T A = 85°CI D 106APulsed Drain Current (Note 4) I DM 60 A Avalanche Current (Notes 4 & 5)I AR16 A Repetitive Avalanche Energy (Notes 4 & 5) L = 0.1mH E AR12.8 mJThermal CharacteristicsCharacteristic Symbol Value UnitPower Dissipation (Note 3) P D 1.42 W Thermal Resistance, Junction to Ambient @T A = 25°C (Note 3) R θJA 88.4 °C/W Operating and Storage Temperature Range T J , T STG-55 to +150 °C Notes:1. No purposefully added lead.2. Diodes Inc.'s "Green" policy can be found on our website at .3. Device mounted on FR-4 substrate PC board with minimum recommended pad layout in a still air environment @ T A = 25°C. The value in any given application depends on the user's specific board design.4. Repetitive rating, pulse width limited by junction temperature.5. I AR and E AR rating are based on low frequency and duty cycles to keep T J = 25°CSO-8TOP VIEW Internal SchematicTOP VIEWS D D GD DS SElectrical Characteristics @T A = 25°C unless otherwise specifiedCharacteristicSymbol Min Typ Max Unit Test ConditionOFF CHARACTERISTICS (Note 6) Drain-Source Breakdown Voltage BV DSS 30 - - V V GS = 0V, I D = 250μA Zero Gate Voltage Drain Current I DSS - - 1 μA V DS = 30V, V GS= 0V Gate-Source LeakageI GSS - - ±100 nA V GS = ±20V, V DS = 0V ON CHARACTERISTICS (Note 6) Gate Threshold VoltageV GS(th) 1.0 1.45 2.4 V V DS = V GS , I D = 250μAStatic Drain-Source On-Resistance R DS (ON) -15 25 2333 m Ω V GS = 10V, I D= 10A V GS = 4.5V, I D = 7.5AForward Transfer Admittance |Y fs | - 2.5 - S V DS = 5V, I D = 10A Diode Forward VoltageV SD - 0.69 1 V V GS = 0V, I S = 1A DYNAMIC CHARACTERISTICS (Note 7) Input Capacitance C iss - 478.9 - pFV DS = 15V, V GS = 0V,f = 1.0MHzOutput CapacitanceC oss - 96.7 - pFReverse Transfer Capacitance C rss - 61.4 - pF Gate ResistanceR g 0.4 1.1 1.6 Ω V DS = 0V, V GS = 0V, f = 1MHz Total Gate Charge (V GS = 4.5V) Q g - 5.0 8 nC V DS = 15V, V GS = 10V, I D = 10ATotal Gate Charge (V GS = 10V) Q g - 10.5 17 nCGate-Source Charge Q gs - 1.8 - nC Gate-Drain Charge Q gd - 1.6 - nC Turn-On Delay Time t D(on) - 2.9 - ns V GS = 10V, V DS = 15V, R G = 3Ω, R L = 1.5Ω Turn-On Rise Time t r - 7.9 - ns Turn-Off Delay Time t D(off) - 14.6 - ns Turn-Off Fall Timet f- 3.1 - nsNotes: 6. Short duration pulse test used to minimize self-heating effect. 7. Guaranteed by design. Not subject to production testing.Fig. 1 Typical Output CharacteristicV , DRAIN-SOURCE VOLTAGE (V)DS I , D R A I N C U R R E N T (A )D 05Fig. 2 Typical Transfer CharacteristicV , GATE-SOURCE VOLTAGE (V)GS I , D R A I N C U R R E N T (A )DFig. 3 Typical On-Resistance vs. Drain Current and Gate VoltageI , DRAIN-SOURCE CURRENT (A)D R , D R A I N -S O U R C E O N -R E S I S T A N C E ()D S (O N )ΩI , DRAIN CURRENT (A)D Fig. 4 Typical On-Resistance vs. Drain Current and Temperature0.010.020.04R , D R A I N -S O U R C E O N -R E S I S T A N C E ()D S (O N )Ω0.03Fig. 5 On-Resistance Variation with T emperature T , AMBIENT TEMPERATURE (°C)A R , D R A I N -S O U R C E O N -R E S I S T A N C E (N O R M A L I Z E D )D S O NFig. 6 On-Resistance Variation with Temperature T , AMBIENT TEMPERATURE (°C)A R , D R A I N -S O U R C E O N -R E S I S T A N C E ()D S O N ΩFig. 7 Gate Threshold Variation vs. Ambient TemperatureT , AMBIENT TEMPERATURE (°C)A V , G A T E T H R E S H O L D V O L T A G E (V )G S(T H )Fig. 8 Diode Forward Voltage vs. CurrentV , SOURCE-DRAIN VOLTAGE (V)SD I , S O U R C E C U R R E N T (A )SFig. 9 Typical T otal CapacitanceV , DRAIN-SOURCE VOLTAGE (V)DS 101,000C , C A P A C I T A N C E (p F )100Fig. 10 Typical Leakage Currentvs. Drain-Source VoltageV , DRAIN-SOURCE VOLTAGE (V) DS I , L E A K A G E C U R R E N T (n A )D S SFig. 11 Gate-Charge CharacteristicsQ , TOTAL GATE CHARGE (nC) g V , G A T E -S O U R C E V O L T A G E (V )G SFig. 12 Transient Thermal Responset , PULSE DURATION TIME (s)1r (t ), T R A N S I E N T T H E R M A L R E S I S T A N C EOrdering Information (Note 8)Part Number Case Packaging DMG4466SSSL-13SO-8 2500 / Tape & ReelNotes:8. For packaging details, go to our website at /datasheets/ap02007.pdf.Marking InformationPackage Outline Dimensions Suggested Pad LayoutSO-8Dim Min Max A - 1.75 A1 0.10 0.20 A2 1.30 1.50 A3 0.15 0.25 b 0.3 0.5 D 4.85 4.95 E 5.90 6.10 E1 3.85 3.95 e 1.27 Typ h - 0.35 L 0.62 0.82θ0° 8° All Dimensions in mmDimensionsValue (in mm)X 0.60 Y1.55 C15.4 C2 1.27Gauge PlaneSeating PlaneDetail ‘A’XC2YTop ViewG4466SS YY WWIMPORTANT NOTICEDIODES INCORPORATED MAKES NO WARRANTY OF ANY KIND, EXPRESS OR IMPLIED, WITH REGARDS TO THIS DOCUMENT, INCLUDING, BUT NOT LIMITED TO, THE IMPLIED WARRANTIES OF MERCHANTABILITY AND FITNESS FOR A PARTICULAR PURPOSE (AND THEIR EQUIVALENTS UNDER THE LAWS OF ANY JURISDICTION).Diodes Incorporated and its subsidiaries reserve the right to make modifications, enhancements, improvements, corrections or other changes without further notice to this document and any product described herein. Diodes Incorporated does not assume any liability arising out of the application or use of this document or any product described herein; neither does Diodes Incorporated convey any license under its patent or trademark rights, nor the rights of others. Any Customer or user of this document or products described herein in such applications shall assume all risks of such use and will agree to hold Diodes Incorporated and all the companies whose products are represented on Diodes Incorporated website, harmless against all damages.Diodes Incorporated does not warrant or accept any liability whatsoever in respect of any products purchased through unauthorized sales channel. Should Customers purchase or use Diodes Incorporated products for any unintended or unauthorized application, Customers shall indemnify and hold Diodes Incorporated and its representatives harmless against all claims, damages, expenses, and attorney fees arising out of, directly or indirectly, any claim of personal injury or death associated with such unintended or unauthorized application.Products described herein may be covered by one or more United States, international or foreign patents pending. Product names and markings noted herein may also be covered by one or more United States, international or foreign trademarks.LIFE SUPPORTDiodes Incorporated products are specifically not authorized for use as critical components in life support devices or systems without the express written approval of the Chief Executive Officer of Diodes Incorporated. As used herein:A. Life support devices or systems are devices or systems which:1. are intended to implant into the body, or2. support or sustain life and whose failure to perform when properly used in accordance with instructions for use provided in thelabeling can be reasonably expected to result in significant injury to the user.B. A critical component is any component in a life support device or system whose failure to perform can be reasonably expected to cause the failure of the life support device or to affect its safety or effectiveness.Customers represent that they have all necessary expertise in the safety and regulatory ramifications of their life support devices or systems, and acknowledge and agree that they are solely responsible for all legal, regulatory and safety-related requirements concerning their products and any use of Diodes Incorporated products in such safety-critical, life support devices or systems, notwithstanding any devices- or systems-related information or support that may be provided by Diodes Incorporated. Further, Customers must fully indemnify Diodes Incorporated and its representatives against any damages arising out of the use of Diodes Incorporated products in such safety-critical, life support devices or systems.Copyright © 2010, Diodes Incorporated分销商库存信息: DIODESDMG4466SSSL-13。
iw3616、3617、3630datasheet中文翻译(绝对真实)

产品特色大幅简化离线式LED驱动器设计●单级功率因数校正(PFC)与精确恒流(CC)输出相结合●输入/输出电容和变压器体积小●一次侧反馈控制,无需光耦电路,简化了电路设计●简化初级侧PWM调光接口●符合IEC61000-3-2标准高效节能和高兼容性●大幅提升效率,可达到85%以上●减少元件数量●总谐波失真<15%且PF>0.95●前沿、后沿和数字调光器●传感器和定时器精确稳定的性能●LED负载恒流精度不低于±5%●支持LED负载热插拔●1%-100%宽范围调光,调光无闪烁先进的保护及安全特性●通过自动重启动提供短路保护●开路故障检测模式●自动热关断重启动无论在PCB板上还是在封装上,都保证高压漏极引脚与其他所有信号引脚之间满足高压爬电要求应用●LED离线固态照明说明G7617 是一款的适用于LED调光控制的离线式两级交流/直流电源控制器,是适用于25W 输出功率的可调光LED 灯具的最优之选。
G7617符合电磁兼容性(EMC) IEC61000-3-2 标准,在120V AC或230V AC输入电压下其功率因数(PF) 可达到0.95 以上。
采用先进的数控技术来检测调光器的类型和相位,为调光器提供动态阻抗的同时可调节LED发光亮度,自动检测调光器类型和相位,从而实现了业内与模拟及数字调光器最广泛的兼容性。
G7617工作于准谐振工作模式,工作效率高,可工作于前沿后沿调光模式,也可工作于R 型、R-C型或R-L型调光控制模式。
G7617 符合热插拔LED 模块的固态照明行业标准Zhaga,同时还集成了调光功能的映射选项(位于白炽灯替代灯的NEMA SSL6 调光曲线内)。
G7617 系列有两个版本:针对120V AC输入应用进行优化的G7617-00 和针对230V AC 应用进行优化的G7617-01。
订购信息应用框图图1典型应用内部框图Vcc VinVcbVT CFGASU BisenseBdrvFdrvFisensePGNDAGND C O R E图2 内部框图引脚功能描述BV SENSE V IN BI SENSE B DRV CFG ASU V CCV CBV TFV SENSEFI SENSEF DRVAGNDPGND 图3. 引脚布局BV SENSE引脚:PFC电感电压反馈点,用于感知Boost电感的磁通状态。
STTH8S06D;STTH8S06FP;中文规格书,Datasheet资料
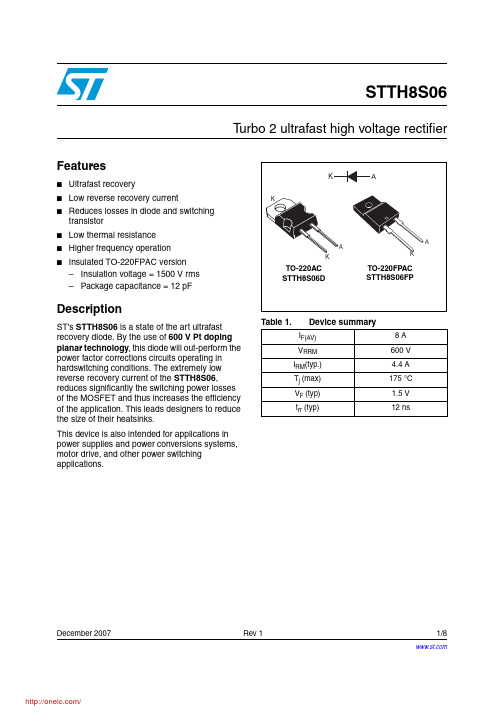
December 2007 Rev 11/8STTH8S06Turbo 2 ultrafast high voltage rectifierFeatures■Ultrafast recovery■Low reverse recovery current■Reduces losses in diode and switching transistor■Low thermal resistance ■Higher frequency operation ■Insulated TO-220FPAC version –Insulation voltage = 1500 V rms –Package capacitance = 12 pFDescriptionST's STTH8S06 is a state of the art ultrafast recovery diode. By the use of 600 V Pt doping planar technology , this diode will out-perform the power factor corrections circuits operating in hardswitching conditions. The extremely low reverse recovery current of the STTH8S06,reduces significantly the switching power losses of the MOSFET and thus increases the efficiency of the application. This leads designers to reduce the size of their heatsinks.This device is also intended for applications in power supplies and power conversions systems, motor drive, and other power switching applications.Table 1.Device summaryI F(AV)8 A V RRM 600 V I RM (typ.) 4.4 A T j (max)175 °C V F (typ) 1.5 V t rr (typ)12 nsCharacteristics STTH8S062/81 CharacteristicsTo evaluate the maximum conduction losses use the following equation:P = 1.20 x I F(AV) + 0.087 I F 2(RMS)Table 2.Absolute ratings (limiting values)Symbol ParameterValue Unit V RRM Repetitive peak reverse voltage 600V I F(AV)Average forward current8A I FSM Surge non repetitive forward current t p = 10 ms60A T stg Storage temperature range-65 to + 175°C T jMaximum operating junction temperature175°CTable 3.Thermal parameterSymbol ParameterMaximumUnit R th(j-c)Junction to caseTO-220AC 3.0°C/WTO220FP AC5.5Table 4.Static electrical characteristicsSymbol ParameterTest conditions Min.TypMax.Unit I RReverse leakage currentT j = 25 °C V R = 600 V20µAT j = 125 °C 25200V FForward voltage dropT j = 25 °C I F = 8 A3.4VT j = 125 °C1.51.9Table 5.Dynamic electrical characteristicsSymbol ParameterTest conditionsMin.Typ Max.Unit t rr Reverse recovery time I F = 1 A, dI F /dt = - 200 A/µs, V R = 30 V1218ns I RM Reverse current T j = 25 °CI F = 8 A, dI F /dt = - 200 A/µs, V R = 200 V 1.6 2.2A S factor Softness factor1-Q rr Reverse recovery charges 17nC I RM Reverse current T j = 125 °CI F = 8 A, dI F /dt = - 200 A/µs, V R = 200 V4.4 6.0A S factor Softness factor0.3-Q rrReverse recovery charges90nCSTTH8S06Characteristics3/8Figure 1.Forward voltage drop versus forward currentFigure 2.Relative variation of thermalimpedance junction to case versusFigure 3.Relative variation of thermal impedance junction to case versus Figure 4.Peak reverse recovery current versus dI F /dt (typical values)Tδ=tp/TtpCharacteristics STTH8S06 Figure 5.Reverse recovery time versus dI F/dt Figure 6.Reverse recovery charges versus4/8STTH8S06Package information5/82 Package information●Epoxy meets UL94, V0●Cooling method: by conduction (C)●Recommended torque value: 0.4 to 0.6 N·mIn order to meet environmental requirements, ST (also) offers these devices in ECOPACK®packages. ECOPACK® packages are Lead-free. The category of second level Interconnect is marked on the package and on the inner box label, in compliance with JEDEC Standard JESD97. The maximum ratings related to soldering conditions are also marked on the inner box label.ECOPACK is an ST trademark. ECOPACK specifications are available at: .Package information STTH8S066/8STTH8S06Ordering information7/83 Ordering information4 Revision historyTable 8.Ordering informationOrder code Marking Package Weight Base qtyDelivery modeSTTH8S06D STTH8S06D TO-220AC 1.9 g 50Tube STTH8S06FPSTTH8S06FPTO-220FP AC1.64 g50TubeTable 9.Document revision historyDate RevisionDescription of changes18-Dec-20071First issue.STTH8S068/8Please Read Carefully:Information in this document is provided solely in connection with ST products. STMicroelectronics NV and its subsidiaries (“ST”) reserve the right to make changes, corrections, modifications or improvements, to this document, and the products and services described herein at any time, without notice.All ST products are sold pursuant to ST’s terms and conditions of sale.Purchasers are solely responsible for the choice, selection and use of the ST products and services described herein, and ST assumes no liability whatsoever relating to the choice, selection or use of the ST products and services described herein.No license, express or implied, by estoppel or otherwise, to any intellectual property rights is granted under this document. If any part of this document refers to any third party products or services it shall not be deemed a license grant by ST for the use of such third party products or services, or any intellectual property contained therein or considered as a warranty covering the use in any manner whatsoever of such third party products or services or any intellectual property contained therein.UNLESS OTHERWISE SET FORTH IN ST’S TERMS AND CONDITIONS OF SALE ST DISCLAIMS ANY EXPRESS OR IMPLIED WARRANTY WITH RESPECT TO THE USE AND/OR SALE OF ST PRODUCTS INCLUDING WITHOUT LIMITATION IMPLIED WARRANTIES OF MERCHANTABILITY, FITNESS FOR A PARTICULAR PURPOSE (AND THEIR EQUIVALENTS UNDER THE LAWS OF ANY JURISDICTION), OR INFRINGEMENT OF ANY PATENT, COPYRIGHT OR OTHER INTELLECTUAL PROPERTY RIGHT. UNLESS EXPRESSLY APPROVED IN WRITING BY AN AUTHORIZED ST REPRESENTATIVE, ST PRODUCTS ARE NOT RECOMMENDED, AUTHORIZED OR WARRANTED FOR USE IN MILITARY, AIR CRAFT, SPACE, LIFE SAVING, OR LIFE SUSTAINING APPLICATIONS, NOR IN PRODUCTS OR SYSTEMS WHERE FAILURE OR MALFUNCTION MAY RESULT IN PERSONAL INJURY, DEATH, OR SEVERE PROPERTY OR ENVIRONMENTAL DAMAGE. ST PRODUCTS WHICH ARE NOT SPECIFIED AS "AUTOMOTIVE GRADE" MAY ONLY BE USED IN AUTOMOTIVE APPLICATIONS AT USER’S OWN RISK.Resale of ST products with provisions different from the statements and/or technical features set forth in this document shall immediately void any warranty granted by ST for the ST product or service described herein and shall not create or extend in any manner whatsoever, any liability of ST.ST and the ST logo are trademarks or registered trademarks of ST in various countries.Information in this document supersedes and replaces all information previously supplied.The ST logo is a registered trademark of STMicroelectronics. All other names are the property of their respective owners.© 2007 STMicroelectronics - All rights reservedSTMicroelectronics group of companiesAustralia - Belgium - Brazil - Canada - China - Czech Republic - Finland - France - Germany - Hong Kong - India - Israel - Italy - Japan - Malaysia - Malta - Morocco - Singapore - Spain - Sweden - Switzerland - United Kingdom - United States of America分销商库存信息:STMSTTH8S06D STTH8S06FP。
BAS21W,115;BAS21AW,115;BAS21SW,115;中文规格书,Datasheet资料

6. Thermal characteristics
Table 7. Thermal characteristics
Symbol Parameter
Per device
Rth(j-a)
thermal resistance from junction to ambient
[1] * = -: made in Hong Kong * = p: made in Hong Kong * = t: made in Malaysia * = W: made in China
5. Limiting values
Marking code[1] X4* X6* X5*
Table 6. Limiting values In accordance with the Absolute Maximum Rating System (IEC 60134).
150
200
250
VR (V)
(1) Tamb = 150 °C (2) Tamb = 85 °C (3) Tamb = 25 °C (4) Tamb = −40 °C
Fig 3. Reverse current as a function of reverse voltage; typical values
1.3 Applications
I High-speed switching I General-purpose switching
I Voltage clamping I Reverse polarity protection
1.4 Quick reference data
Table 2. Quick reference data
力仕 3086 G.SHDSL 集线器使用说明书
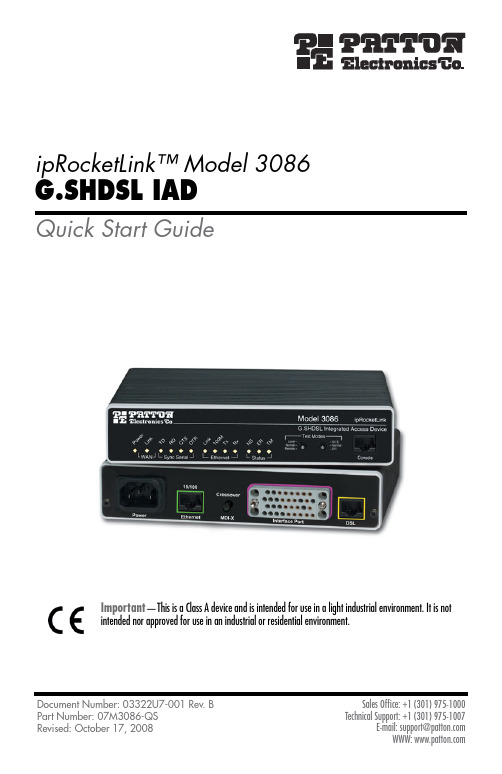
ipRocketLink™ Model 3086G.SHDSL IADQuick Start GuideImportant—This is a Class A device and is intended for use in a light industrial environment. It is notintended nor approved for use in an industrial or residential environment.Document Number: 03322U7-001 Rev. B Sales Office: +1 (301) 975-10001.0 Power up the IADYour IAD comes with one of the following power supply options:•Internal AC power supply with detachable power cord•External AC adaptor with detachable power cord•Internal DC power supply—no power accessories are included1.1 Models with internal AC power supply1.Insert the female end of the AC power cord into the internal power supply connector.2.Connect the male end of the power cord into an AC power outlet (100–240 VAC).1.2 Models with external AC adaptor1.Connect female plug of the AC power cord to the AC adaptor provided.•This device contains no user serviceable parts. The equipment shall bereturned to Patton Electronics for repairs, or repaired by qualifiedservice personnel.•Mains Voltage: Do not open the case the when the power cord isattached. Line voltages are present within the power supply whenthe power cords are connected. The mains outlet that is utilized topower the devise shall be within 10 feet (3 meters) of the device,shall be easily accessible, and protected by a circuit breaker.•For AC powered units, ensure that the power cable used meets allapplicable standards for the country in which it is to be installed, andthat it is connected to a wall outlet which has earth ground.•For units with an external power adapter, the adapter shall be alisted Limited Power Source.•Hazardous network voltages are present in WAN ports regardless ofwhether power to the unit is ON or OFF. To avoid electric shock, usecaution when near WAN ports. When detaching the cables, detach theend away from the device first.•Do not work on the system or connect or disconnect cables during periods of lightning activity.The interconnecting cables shall be acceptable for external use and shall be rated forthe proper application with respect to voltage, current, anticipated temperature, flam-mability, and mechanical serviceability.WARNING CAUTION2.Connect the barrel-type connector of the AC adaptor to the barrel-type power jack on the ipRocketLink.3.Insert the male plug of the AC power cord into an AC power outlet (100–240 VAC).1.3 Models with internal DC power supply1.Strip insulation 1/4-inch from the electrical wires that will connect the DC power source tothe ipRocketLink.2.Connect the ground terminal from the power source to the ground terminal on the ipRocketLink.3.Connect the negative (-) terminal from the power source with to the negative (-) terminal onthe ipRocketLink.4.Connect the positive (+) terminal from the power source with to the positive (+) terminal onthe ipRocketLink.1.4 Power-up indicationThe Power LED blinks as the ipRocketLink is powering up. When the Power LED stops blinking and remains lit, the ipRocketLink is ready for you to configure.2.0 Configure the IP addressThe ipRocketLink is shipped with a factory-configured IP address assigned to the Ethernet LAN port (green out-line). The address is 192.168.200.10/24. In most cases, you must change the address to be on the same subnet as your PC, as described in the procedures below. If you are not sure which IP address to use for your installa-tion, contact your network administrator.2.1 Connect a PC and log ining the included combination RS232/Ethernet cable and DB9-RJ45 adapter, connect a PC’s serial portFigure 1. Connecting ipRocketLink to the PC’s serial port2.Start a HyperTerminal session on the PC using the settings:9600 bps, 8 data bits, 1 stop bit, no parity, no flow control3.Log in to the ipRocketLink using the factory-default login and password:Login: superuserPassword: superuserLogin successful2.2 Modify the IP address1.Display current IP interface settings for the ipRocketLink Ethernet LAN port.→ip list interfaces <enter>IP Interfaces:ID | Name | IP Address | DHCP | Transport---|------|----------------|----------|--------------1 | ip1 | 192.168.200.10 | disabled | <bridge>----------------------------------------------------2.Modify the IP address for the LAN port according to your network requirements.→ip set interface ip1 ipaddress 10.10.10.5 255.255.255.0Note The above IP address (10.10.10.5/24) is only an example. You must choose an IP address on the same subnet as your PC.3.Verify the new address is correct and save it in system boot memory.→ip list interfaces <enter>→system config save <enter>→3.0 Connect to the local IP networkNow you can connect the ipRocketLink to your local IP network and complete the remaining configuration from your PC using a standard web browser.Connect the ipRocketLink’s Ethernet port (green) to the same Ethernet segment as your PC (see figure 2). The front-panel Ethernet Link LED should turn on. If it does not, press the rear-panel MDI-X switch so that the Ethernet Link LED illuminates.You can check the connection with the ping command. For example shown in figure 2, you would ping 10.10.10.5 from a PC on the IP network.Figure 2. Connecting the ipRocketLink to the local IP network (Model 3086/RIC shown)4.0 Log onto the web management interface You will now access the web management graphical user interface (GUI) to configure the ipRocketLink using a standard web browser (such as Internet Explorer or Netscape browser).1.At your PC, open a web browser and enter the IP address you assigned to the ipRocketLink’s Ethernet LANport in step 2 of section 2.2 “Modify the IP address” on page 4.2.Log in to the web management home page using the username superuser and the password superuser .Figure 3. ipRocketLink web management home page5.0 Connect the G.SHDSL Port1.Obtain single-twisted-pair cable with an RJ-11 plug connector at each end.2.Plug one end of the cable into the (yellow) RJ-11socket (labelled DSL) on the ipRocketLink IntegratedAccess Device.3.Plug the other end of the cable into the RJ-11 wall socket that provides your G.SHDSL service.4.When a DSL link is established the front-panel WAN LINK LED will turn on.6.0 Connect the serial portYour ipRocketLink is equipped with one of the following serial WAN ports for connection to an NTU:•V.35 (M/34 or DB-25)—Model 3086/RIC, Model 3086/RICA•X.21 (DB-15)—Model 3086/RID•T1/E1(RJ-48C and dual BNC)—Model 3086/RIKConnect the serial cable to the ipRocketLink serial port as follows:1.Attach the male connector of the serial cable to the female serial connector on the IAD.2.Attach the other end of the cable to the serial connector on local serial NTU.Note The IAD’s V.35 interface is wired as a DCE. No DTE configuration is possible. If you are directly connect-ing the IAD’s V.35 interface to third-party equipment that cannot be configured as a DTE, you must usea tail-circuit cable. You can purchase a tail-circuit cable from a datacom-supply vendor. A tail-circuitcable will cross-over the necessary V.35 signals so that the two DCE interfaces can communicate.Note The IAD’s X.21 interface is wired as a DCE. No DTE configuration is possible. The IAD’s X.21 interface requires a cable with a male DB-15 connector.7.0 Additional InformationRefer to the ipRocketLink 3086 User Guide located on the CD-ROM shipped with your 3086 Integrated Access Device and available online at /manuals for detailed information about:•Installing, configuring, operating, and troubleshooting,•Warranty, trademark, & complianceA.0 Customer and Technical SupportToll-Free VoIP support: call sip:****************** with a VoIP SIP phoneOnline support: E-mail support: ******************—answered within 1 business dayTelephone support:•Standard: +1 (301) 975-1007 (USA), Monday–Friday: 8:00 am to 5:00 pm EST (1300 to2200 UTC/GMT)•Alternate: +41 (0)31 985 25 55 (Switzerland), Monday–Friday: 8:00 am to 5:00 pm CET (0900 to 1800 UTC/GMT)Fax: +1 (253) 663-5693 (USA) or +41 (0)31 985 25 26 (Switzerland)B.0 Compliance InformationB.1 ComplianceEMC:•FCC Part 15, Class A•EN55022, Class A•EN55024Safety:•UL60950-1/CSA C22.2 No. 60950-1•IEC/EN 60950-1•AS/NZS 60950-1PSTN Regulatory:•FCC Part 68•CS-03•AS/ACIF S043B.2 Radio and TV Interference (FCC Part 15)This equipment generates and uses radio frequency energy, and if not installed and used properly—that is, in strict accordance with the manufacturer's instructions—may cause interference to radio and television recep-tion. This equipment has been tested and found to comply with the limits for a Class A computing device in accor-dance with the specifications in Subpart B of Part 15 of FCC rules, which are designed to provide reasonable protection from such interference in a commercial installation. However, there is no guarantee that interference will not occur in a particular installation. If the equipment causes interference to radio or television reception, which can be determined by disconnecting the cables, try to correct the interference by one or more of the fol-lowing measures: moving the computing equipment away from the receiver, re-orienting the receiving antenna, and/or plugging the receiving equipment into a different AC outlet (such that the computing equipment and receiver are on different branches).B.3 CE Declaration of ConformityProduct Description: ipRocketLink 3086We certify that the apparatus identified in this document conforms to the requirements of Council Directive 1999/5/EC on the approximation of the laws of the member states relating to Radio and Telecommunication Terminal Equipment and the mutual recognition of their conformity.The safety advice in the documentation accompanying this product shall be obeyed. The conformity to the above directive is indicated by the CE sign on the device.The signed Declaration of Conformity can be downloaded from /certifications/.B.4 Authorized European RepresentativeD R M GreenEuropean Compliance Services Limited.Avalon House, Marcham RoadAbingdon,Oxon OX14 1UD, UKB.5 FCC Part 68 (ACTA) StatementThis equipment complies with Part 68 of FCC rules and the requirements adopted by ACTA. On the bottom side of this equipment is a label that contains—among other information—a product identifier in the format US: AAAEQ##TXXXX. If requested, this number must be provided to the telephone company.The method used to connect this equipment to the premises wiring and telephone network must comply with the applicable FCC Part 68 rules and requirements adopted by the ACTA.If this equipment causes harm to the telephone network, the telephone company will notify you in advance that temporary discontinuance of service may be required. But if advance notice isn’t practical, the telephone com-pany will notify the customer as soon as possible. Also, you will be advised of your right to file a complaint with the FCC if you believe it is necessary.The telephone company may make changes in its facilities, equipment, operations or procedures that could affect the operation of the equipment. If this happens, the telephone company will provide advance notice in order for you to make necessary modifications to maintain uninterrupted service.If trouble is experienced with this equipment, for repair or warranty information, please contact our company. If the equipment is causing harm to the telephone network, the telephone company may request that you discon-nect the equipment until the problem is resolved.Connection to party line service is subject to state tariffs. Contact the state public utility commission, public ser-vice commission or corporation commission for information.The safety advises in the documentation accompanying the products shall be obeyed. Theconformity to the above directive is indicated by the CE sign on the device.B.6 Industry Canada NoticeThis equipment meets the applicable Industry Canada Terminal Equipment Technical Specifications. This is con-firmed by the registration number. The abbreviation, IC, before the registration number signifies that registra-tion was performed based on a Declaration of Conformity indicating that Industry Canada technical specifications were met. It does not imply that Industry Canada approved the equipment.This Declaration of Conformity means that the equipment meets certain telecommunications network protective, operational and safety requirements. The Department does not guarantee the equipment will operate to the user's satisfaction. Before installing this equipment, users should ensure that it is permissible to be connected to the facilities of the local telecommunications company. The equipment must also be installed using an acceptable method of connection. In some cases, the company's inside wiring associated with a single line individual service may be extended by means of a certified connector assembly (telephone extension cord). The customer should be aware that compliance with the above condition may not prevent degradation of service in some situations. Repairs to some certified equipment should be made by an authorized maintenance facility designated by the supplier. Any repairs or alterations made by the user to this equipment, or equipment malfunctions, may give the telecommunications company cause to request the user to disconnect the equipment. Users should ensure for their own protection that the ground connections of the power utility, telephone lines and internal metallic water pipe system, are connected together. This protection may be particularly important in rural areas.Copyright statementCopyright © 2008, Patton Electronics Company. All rights reserved.The information in this document is subject to change without notice. Patton Electronics assumes noliability for errors that may appear in this document.Trademarks statementThe term ipRocketLink is a trademark of Patton Electronics Company. All other trademarks presented in this doc-ument are the property of their respective owners.Warranty, Trademark, & Compliance InformationFor warranty, trademark and compliance information, refer to the Models 3086 ipRocketLink User Guide located on the CD-ROM that came with your IAD or available online at .In accordance with the requirements of council directive 2002/96/EC on Waste ofElectrical and Electronic Equipment (WEEE), ensure that at end-of-life you separatethis product from other waste and scrap and deliver to the WEEE collection system inyour country for recycling.____________________________________________________________________ ____________________________________________________________________ ____________________________________________________________________ ____________________________________________________________________ ____________________________________________________________________ ____________________________________________________________________ ____________________________________________________________________ ____________________________________________________________________ ____________________________________________________________________ ____________________________________________________________________ ____________________________________________________________________ ____________________________________________________________________ ____________________________________________________________________ ____________________________________________________________________ ________________________________________________________________________________________________________________________________________ ____________________________________________________________________ ____________________________________________________________________ ____________________________________________________________________ ____________________________________________________________________ ____________________________________________________________________ ____________________________________________________________________ ____________________________________________________________________ ____________________________________________________________________ ____________________________________________________________________ ____________________________________________________________________ ____________________________________________________________________ ____________________________________________________________________ ____________________________________________________________________ ____________________________________________________________________。
PBSS4160T中文资料

handbook, halfpage
500
MLE128
Ptot (mW)
400
(1)
300
(2)
200
100
0 0 40 80 120 160 Tamb (°C)
(1) Device mounted with 1 cm2 collector tab. (2) Device mounted on standard footprint.
CHARACTERISTICS Tamb = 25 °C unless otherwise specified. SYMBOL ICBO ICES IEBO hFE PARAMETER collector-base cut-off current collector-emitter cut-off current emitter-base cut-off current DC current gain CONDITIONS VCB = 60 V; IE = 0 A VCB = 60 V; IE = 0 A; Tj = 150 °C VCE = 60 V; VBE = 0 A VEB = 5 V; IC = 0 A VCE = 5 V; IC = 1 mA VCE = 5 V; IC = 500 mA; note 1 VCE = 5 V; IC = 1 A; note 1 VCEsat collector-emitter saturation voltage IC = 100 mA; IB = 1 mA IC = 500 mA; IB = 50 mA IC = 1 A; IB = 100 mA; note 1 VBEsat RCEsat VBEon fT Cc Note 1. Pulse test: tp ≤ 300 µs; δ ≤ 0.02. base-emitter saturation voltage equivalent on-resistance base-emitter turn-on voltage transition frequency collector capacitance IC = 1 A; IB = 50 mA IC = 1 A; IB = 100 mA; note 1 VCE = 5 V; IC = 1 A IC = 50 mA; VCE = 10 V; f = 100 MHz MIN. − − − − 250 200 100 − − − − − − 150
AD8386资料

10-Bit, 12-Channel OutputDecimating LCD DriverAD8386 Rev. 0Information furnished by Analog Devices is believed to be accurate and reliable. However, noresponsibility is assumed by Analog Devices for its use, nor for any infringements of patents or other rights of third parties that may result from its use. Specifications subject to change without notice. No license is granted by implication or otherwise under any patent or patent rights of Analog Devices. T rademarks and registered trademarks are the property of their respective owners. One Technology Way, P.O. Box 9106, N orwood, MA 02062-9106, U.S.A. Tel: 781.329.4700 Fax: 781.461.3113 © 2005 Analog Devices, Inc. All rights reserved.FEATURESHigh voltage driveTo within 1.3 V of supply railsOutput short-circuit protectionHigh update ratesFast, 100 Ms/s 10-bit input data update rateStatic power dissipation: 1.4 WVoltage-controlled video reference (brightness), offset,and full-scale (contrast) output levelsINV bit reverses polarity of video signal3.3 V logic, 9 V to 18 V analog suppliesHigh accuracy voltage outputsLaser trimming eliminates the need for adjustments orcalibrationFlexible logicXFR allows parallel AD8386 operationFast settling into capacitive loads35 ns settling time to 0.25% into 150 pF loadSlew rate 400 V/μsAvailable in 64-lead 9 mm × 9 mm LFCSP_VQGENERAL DESCRIPTIONThe AD8386 provides a fast, 10-bit, latched, decimating digital input that drives 12 high voltage outputs. Input words with10 bits are loaded sequentially into 12 separate high speed, bipolar DACs. Flexible digital input format allows severalAD8386s to be used in parallel in high resolution displays. The output signal can be adjusted for dc reference, signal inversion, and contrast for maximum flexibility.The AD8386 is fabricated on ADI’s fast bipolar, 26 V XFHV process, which provides fast input logic, bipolar DACs with trimmed accuracy and fast settling, high voltage, precision drive amplifiers on the same chip.The AD8386 dissipates 1.4 W nominal static power.The AD8386 is offered in a 64-lead 9 mm × 9 mm LFCSP_VQ package and operates over the commercial temperature range of 0°C to 85°C. FUNCTIONAL BLOCK DIAGRAMVID0VID1VID2VID3VID4VID5VID6VID7VID8VID9VID10VID11VAO5687-1Figure 1.AD8386Rev. 0 | Page 2 of 20TABLE OF CONTENTSFeatures..............................................................................................1 General Description.........................................................................1 Functional Block Diagram..............................................................1 Revision History...............................................................................2 Specifications.....................................................................................3 DecDriver® Section.......................................................................3 Serial Interface Section................................................................5 Absolute Maximum Ratings............................................................6 Maximum Power Dissipation.....................................................6 Overload Protection.....................................................................6 Exposed Paddle.............................................................................6 ESD Caution..................................................................................6 Operating Temperature Range...................................................7 Pin Configuration and Function Descriptions.............................8 DecDriver Block Diagram and Timing........................................10 Serial Interface Block Diagram and Timing...............................12 Functional Description..................................................................13 Reference and Control Input Descriptions.............................13 Transfer Function and Analog Output Voltage......................13 Accuracy......................................................................................14 3-Wire Serial Interface...............................................................14 Output Operating Modes..........................................................14 Overload Protection...................................................................14 Applications.....................................................................................15 Optimized Reliability with the Thermal Protection Circuit 15 Operation in High Ambient Temperature..............................15 Power Supply Sequencing.........................................................15 Grounded Output Mode During Power-Off..........................15 Typical Application Circuits.....................................................16 PCB Design for Optimized Thermal Performance...............17 AD8386 PCB Design Recommendations...............................17 Outline Dimensions.......................................................................19 Ordering Guide.. (19)REVISION HISTORY8/05—Revision 0: Initial VersionAD8386Rev. 0 | Page 3 of 20SPECIFICATIONSDECDRIVER® SECTIONAt 25°C, AVCC = 15.5 V , DVCC = 3.3 V , T A MIN = 0°C, T A MAX = 85°C, VRH = 9.5 V , VRL = 7 V , unless otherwise noted. Table 1.Parameter Conditions Min Typ Max Unit VIDEO DC PERFORMANCE 1T A MIN to T A MAX VDE DAC Code 450 to 800 −7.5 +7.5 mV VCME DAC Code 450 to 800 −3.5 +3.5 mV VIDEO OUTPUT DYNAMIC PERFORMANCE T A MIN to T A MAX , C L = 150 pF Data Switching Slew Rate 20% to 80%, V O = 5 V step 400 V/μs Invert Switching Slew Rate 20% to 80%, V O = 10 V step 560 V/μs Data Switching Settling Time to 1% 24 35 ns Data Switching Settling Time to 0.25% 35 50 ns Invert Switching Settling Time to 1% 80 130 ns Invert Switching Settling Time to 0.25% 250 500 ns Invert Switching Overshoot 10 V Step 100 200 mVCLK and Data Feedthrough 215 mV p-p All-Hostile Crosstalk 3 Amplitude 50 mV p-p Glitch Duration 30 ns DAC Transition Glitch Energy DAC code 511 to 512 0.6 nV-s VIDEO OUTPUT CHARACTERISTICS Output Voltage Swing AVCC − VOH, VOL − AGND 1.1 1.3 V Output Voltage—Grounded Mode 200 mVData Switching Delay: t 945 V step 12 14 16 ns INV Switching Delay: t 10510 V step 15 17 19 ns Output Current 100 mA Output Resistance 29 Ω REFERENCE INPUTS VRL Range VRH ≥ VRL 5.25 AVCC − 4 V VRH Range VRH ≥ VRL VRL AVCC V VRH – VRL Range VFS = 2 × (VRH − VRL) 0 2.75 V VRH Input Resistance To VRL 20 kΩ VRL Input Current −45 μA VRH Input Current 125 μA RESOLUT ON Coding Binary 10 Bits DIGITAL INPUT CHARACTERISTICS C IN 3 pF I IH 0.05 μA I IL −2 μA V IH 2 V V IL 0.8 V V TH 1.65 V I IH TSW 330 μA I IL TSW −2 μA TSW R PULLDOWN 10 kΩAD8386Rev. 0 | Page 4 of 20Parameter Conditions Min Typ Max Unit DIGITAL TIMING CHARACTERISTICS T A MIN to T A MAX Maximum Input Data Update Rate 100 Ms/s Data Setup Time: t 1 1 ns XFR Setup Time: t 3 0 ns INV Setup Time: t 11 0 ns Data Hold Time: t 2 3.5 ns XFR Hold Time: t 4 4.5 ns INV Hold Time: t 12 4 ns CLK High Time: t 7 6 ns CLK Low Time: t 8 4 ns1 VDE = differential error voltage. VCME = common-mode error voltage. Full-scale output voltage = VFS =2 × (VRH − VRL). See the Accuracy section. 2Measured on two outputs differentially as CLK and DB (0:9) are driven and XFR is held low. 3Measured on two outputs differentially as the others are transitioning by 5 V. Measured for both states of INV. 4Measured from 50% of rising CLK edge to 50% of output change. Measurement is made for both states of INV. 5Measured from 50% of rising CLK edge, which follows a valid XFR, to 50% of output change. See Figure 6 for the definition.AD8386Rev. 0 | Page 5 of 20SERIAL INTERFACE SECTIONAt 25°C, AVCC = 15.5 V , DVCC = 3.3 V , T A MIN = 0°C, T A MAX = 85°C, VRH = 9.5 V , VRL = 7 V , unless otherwise noted. Table 2.Parameter Conditions Min Typ Max Unit SERIAL DAC DC PERFORMANCE DNL SVFS = 5 V −1 +1 LSB INL SVFS = 5 V −1.5 +1.5 LSB Output Offset Error −2.0 +2.0 LSB Scale Factor Error −3.0 +3.0 LSB SERIAL DAC OUTPUT DYNAMIC PERFORMANCE To 0.5% VAO Settling Time, t 26 C L = 100 pF 1 2 μs VAO Settling Time, t 26 C L = 33 μF 15 ms SERIAL DAC OUTPUT CHARACTERISTICS VAO Maximum SVRH − 1 LSB V VAO Minimum SVRL V VAO − Grounded Mode 150 mV VAO Output Resistance All supplies OFF 75 kΩ I OUT ±30 mAC LOAD Low Range 10.002 μFC LOAD High Range 10.047 μF REFERENCE INPUTS SVRH Range SVRL < SVRH SVRL + 1 AVCC − 3.5 V SVRL Range SVRL < SVRH AGND + 1.5 SVRH − 1 V SVFS Range 1 8 V SVRH Input Current SVRS = 5 V 0.1 μA SVRL Input Current SVRS = 5 V −1.6 −1.3 mA DIGITAL INPUT CHARACTERISTICS C IN 3 pF I IH 0.05 μA I IL −1 μA V IH 2.0 DVCC V V IL DGND 0.8 V V TH 1.65 V DIGITAL TIMING CHARACTERISTICS T A MIN to T A MAX SEN to SCL Setup Time, t 20 10 ns SCL, High Level Pulse Width, t 21 10 ns SCL, Low Level Pulse Width, t 22 10 ns SCL to SEN Hold Time, t 23 10 ns SDI Setup Time, t 24 10 ns SDI Hold Time, t 25 10 ns POWER SUPPLIES DVCC, Operating Range 3 3.3 3.6 V DVCC, Quiescent Current 54 75 mA AVCC Operating Range 9 18 V Total AVCC Quiescent Current 80 100 mA OPERATING TEMPERATURESAmbient Temperature Range, T A 2Still air, TSW = HIGH 0 70 °CAmbient Temperature Range, T A 2Still air, TSW = LOW 0 85 °C1Output VAO is designed to drive capacitive loads less than 0.002 μF or more than 0.047 μF. Load capacitances in the range 0.002 μF − 0.047 μF cause the outputovershoot to exceed 100 mV. 2Operation at high ambient temperature requires a thermally optimized PCB layout (see the Applications section). In systems with limited or no airflow, the maximum ambient operating temperature is limited to 70°C with the thermal protection enabled, VFS = 4 V, data update rate = 85 Ms/s. Operation at 85°C ambient temperature requires the thermal protection circuit turned disabled (TSW = LOW).AD8386Rev. 0 | Page 6 of 20ABSOLUTE MAXIMUM RATINGSTable 3.Parameter RatingSupply VoltageAVCCx − AGNDx 18 VDVCC − DGND 4.5 VInput VoltageMaximum Digital Input Voltage DVCC + 0.5 VMinimum Digital Input Voltage DGND − 0.5 VMaximum Analog Input Voltage AVCC + 0.5 VMinimum Analog Input Voltage AGND − 0.5 V Internal Power Dissipation 1 LFCSP @ T A = 25°C 3.7 WOperating Temperature Range 0°C to 85°CStorage Temperature Range –65°C to +125°CLead Temperature Range (Soldering 10 sec) 300°C Stresses above those listed under Absolute Maximum Ratings may cause permanent damage to the device. This is a stress rating only and functional operation of the device at these or any other conditions above those indicated in the operational section of this specification is not implied. Exposure to absolute maximum rating conditions for extended periods may affect device reliability.164-lead VQ_LFCSP:θJA = 27°C/W in still air (JEDEC STD, 4-layer PCB with 16 vias on Epad)θJA = 25°C/W @ 200 lfm airflow (JEDEC STD, 4-layer PCB with 16 vias on Epad) θJA = 24°C/W @ 400 lfm airflow (JEDEC STD, 4-layer PCB with 16 vias on Epad) ΨJT = 0.2°C/W in still air (JEDEC STD, 4-layer PCB with 16 vias on Epad) ΨJB = 13.8°C/W in still air (JEDEC STD, 4-layer PCB with 16 vias on Epad)MAXIMUM POWER DISSIPATIONThe maximum power that can be safely dissipated by theAD8386 is limited by its junction temperature. The maximumsafe junction temperature for plastic encapsulated devices, asdetermined by the glass transition temperature of the plastic, isapproximately 150°C. Exceeding this limit temporarily maycause a shift in the parametric performance due to a change inthe stresses exerted on the die by the package. Exceeding ajunction temperature of 175°C for an extended period canresult in device failure.OVERLOAD PROTECTION The AD8386 overload protection circuit consists of an outputcurrent limiter and a thermal protection circuit.When TSW is LOW , the thermal protection circuit is disabled,and the output current limiter is turned on. The maximumcurrent at any one output of the AD8386 is internally limited to 100 mA average. In the event of a momentary short circuit between a video output and a power supply rail (AVCC or AGND), the output current limit is sufficiently low to provide temporary protection.When TSW is HIGH, the output current limiter, as well as the thermal protection circuit, is turned on. The thermal protection circuit debiases the output amplifier when the junctiontemperature reaches the internally set trip point. In the event of an extended short circuit between a video output and a power supply rail, the output amplifier current continues to switch between 0 mA and 100 mA typical with a period determined by the thermal time constant and the hysteresis of the thermal trip point. The thermal protection circuit limits the average junction temperature to a safe level, which provides long-term protection.EXPOSED PADDLETo ensure optimal thermal performance, the exposed paddle must be electrically connected to an external plane, such as AVCC or GND, as described in the Applications section.ESD CAUTIONESD (electrostatic discharge) sensitive device. Electrostatic charges as high as 4000 V readily accumulate on the human body and test equipment and can discharge without detection. Although this product features proprietary ESD protection circuitry, permanent damage may occur on devices subjected to high energy electrostatic discharges. Therefore, proper ESD precautions are recommended to avoid performancedegradation or loss of functionality.AD8386Rev. 0 | Page 7 of 20OPERATING TEMPERATURE RANGEThe maximum operating junction temperature is 150°C. The junction temperature trip point of the thermal protection circuit is 165°C. Production tests guarantee a minimum junction temperature trip point of 125°C.Consequently, the maximum guaranteed operating junction temperature is 125°C when the thermal protection circuit is enabled and 150°C when the thermal protection circuit is disabled.To ensure operation within the specified operating temperature range, it is necessary to limit the maximum power dissipation as()()59.009.0lfm in Airflow T T P Air Still JA A JMAX DMAX ×−θ−≈M A X I M U M P O W E R D I S S I P A T I O N (W )AMBIENT TEMPERATURE (°C)OVERLOADFigure 2. Maximum Power Dissipation vs. TemperatureThe AD8386 is on a 4-layer JEDEC PCB with a thermally optimized landing pattern with 16 vias.The quiescent power dissipation of the AD8386 is 1.4 W . When driving a 12-channel 720p HDTV panel with an input capacitance of 150 pF, the AD8386 dissipates 1.66 W whendisplaying 1 pixel wide alternating white and black vertical lines generated by a standard 720p HDTV input video. Conditions include the following: • AVCC = 15.5 V • DVCC = 3.3 V • VFS = 5 V • C L = 150 pF• f PIXEL = 74.25 MHz• Black-to-white transition = 4 V • Active video time = 75%Figure 2 shows these power dissipations.AD8386Rev. 0 | Page 8 of 20PIN CONFIGURATION AND FUNCTION DESCRIPTIONS17181920212223242526272829303132G S W T S W D V C C D G N D A G N D S S V R L S V R L S V R H V A O A V C C S B Y P A G N D 11V I D 11A V C C 10, 11V I D 10A G N D 9, 1064636261605958575655545352515049D V C C D G N D C L K X F R I N V R /L T S T A A G N D D A V C C D V R H V R H V R L A G N D 0V I D 0A V C C 0, 1V I D 112345678910111213141516NC NC DB0DB1DB2DB3DB4DB5DB6DB7DB8DB9SDI SEN SCL GCTL AGND1, 2VID2AVCC2, 3VID3AGND3, 4VID4AVCC4, 5VID5AGND5, 6VID6AVCC6, 7VID7AGND7, 8VID8AVCC8, 9VID94847464544434241403938373635343305687-003Figure 3. 64-Lead LFCSP_VQ Pin ConfigurationAD8386Rev. 0 | Page 9 of 20Table 4. 64-Lead LFCSP_VQ Pin Function DescriptionsPin No. Mnemonic FunctionDescription1, 2 NCNo Connect No Internal Connection.3 to 12 DB0 to DB9 Data Input10-Bit Data Input. MSB = DB(9).13SDISerial Data InputWhile the SEN input is LOW, one 12-bit serial word is loaded into the serial DAC on the rising edges of the SCL.14 SEN Serial DAC Enable A falling edge of this input initiates a loading cycle. While this input is heldLOW, the serial DAC is enabled and data is loaded on every rising edge of SCL. The output is updated on the rising edge of a valid SEN. A valid SEN must remain LOW for at least three SCL cycles. While this input is held HIGH, the control DAC is disabled.15 SCL Serial Data Clock Serial Data Clock. 16 GCTL Output Mode Control When this input is HIGH, the output mode is determined by the functionprogrammed into the serial interface. When LOW, the output mode is controlled by the GSW input.17 GSW Output Mode Switch When GCTL is LOW and this input is HIGH, the video outputs and VAOoperate normally. When GCTL and this input are both LOW, the video outputs and VAO are asynchronously forced to AGND, regardless ofthe function programmed into the serial interface. This function operates when AVCC power is OFF but requires DVCC power supply to be ON.18 TSW Thermal Switch When this input is LOW, the thermal protection circuit is disabled. WhenHIGH, the thermal protection circuit is enabled. This pin has a 10 kΩ internal pull-down resistor.19, 64 DVCC Digital Power Supply Digital Power Supply. 20, 63 DGND Digital Ground Digital Supply Return. 21 AGNDS Analog Ground Analog Supply Return. 22, 23, 24 SVRL, SVRH Serial DAC Reference Voltage The voltage applied between these pins sets the serial DAC full-scale voltage. 25 VAO Serial DAC Output This output voltage is updated in the rising edge of the SEN input. 26 AVCCS Analog Power Supply Analog Power Supply. 27 BYP Bypass A 0.1 μF capacitor connected between this pin and AGND ensuresoptimum settling time. 28, 32, 36, 40, 44, 48, 52 AGND11 to AGND0Analog GroundAnalog Supply Returns. 29, 31, 33, 35, 37, 39, 41, 43, 45, 47, 49, 51VID11 toVID0 Analog Output These pins are directly connected to the analog inputs of the LCD panel. 30, 34, 38, 42, 46, 50 AVCC10, 11 to AVCC0, 1 Analog Power SupplyAnalog Power Supplies. 53 VRL Video Center Reference The voltage applied to this pin sets the video center voltage. The videooutputs are above this reference while the INV = HIGH and below this reference while INV = LOW.54, 55 VRH Full-Scale Reference The full-scale video output voltage is VFS = 2 × (VRH − VRL). 56 AVCCD Analog Power Supply Analog Power Supply. 57 AGNDD Analog Ground Analog Supply Return. 58 TSTA Test Pin Connect this pin to AGND. 59 R/L Right/Left Select A new data loading sequence begins on the left with Channel 0 whenthis input is LOW, and on the right with Channel 11 when this input is HIGH.60 I NV Invert When this input is HIGH, the VIDx output voltages are above VRL. WhenLOW, the VIDx outputs voltages are below VRL. The state of INV is latched on the first rising CLK edge after XFR is detected. The VIDx outputs change on the rising CLK edge after the next XFR is detected.61 XFR Transfer/Start Sequence The state of XFR is detected on the rising edge of CLK. Data is transferred tothe outputs and a new loading sequence begins on the next rising edge of CLK after XFR is detected HIGH.62 CLK Clock Video Data Clock.AD8386Rev. 0 | Page 10 of 20DECDRIVER BLOCK DIAGRAM AND TIMINGVID1VID3VID5VID7VID9VID11VID0VID2VID4VID6VID8VID10XFR CLK R/LBYPDB(0:9)VRH VRL05687-004Figure 4. AD8386 DecDriver Section05687-005Figure 5. Input Timing–VFSCLK DB(0:9)XFR INVVID(0:11)05687-006Figure 6. Output Timing (R/L LOW)Table 5.Parameter Conditions Min Typ Max Unit Data Setup Time, t 1 Input t r , t f = 2 ns 1 ns Data Hold Time, t 2 3.5 ns XFR Setup Time, t 3 0 ns XFR Hold Time, t 4 4.5 ns CLK High Time, t 7 6 ns CLK Low Time, t 8 4 ns Data Switching Delay, t 9 12 14 16 ns Invert Switching Delay, t 10 15 17 19 ns Invert Setup Time, t 11 0 ns Invert Hold Time, t 12 4 nsSERIAL INTERFACE BLOCK DIAGRAM AND TIMINGSVRH SVRL SDI SCL SENTSWGSWGCTLVAOVID(0:11)05687-007Figure 7. Serial Interface Block DiagramSCLSENSDI D11D10D9D8D7D6D5D4D3D2D1D0VAO05687-008Figure 8. Serial Interface Timing DiagramSENSCLSDIVAO05687-009Figure 9. Serial Interface Timing DiagramTable 6.Parameter Conditions Min Typ Max Unit SEN to SCL Setup Time, t 20 10 ns SCL, High Level Pulse Width, t 21 10 ns SCL, Low Level Pulse Width, t 22 10 ns SCL to SEN Hold Time, t 23 10 ns SDI Setup Time, t 24 10 ns SDI Hold Time, t 25 10 ns VAO Settling Time, t 26 SVFS = 5 V, to 0.5 %, C L = 100 pF 1 2 μs VAO Settling Time, t 26 SVFS = 5 V, to 0.5 %, C L = 33 μF 15 msFUNCTIONAL DESCRIPTIONThe AD8386 is a system building block designed todirectly drive the columns of LCD microdisplays of the type popularized for use in projection systems. It has 12 channels of precision, 10-bit digital-to-analog converters (DACs) loaded from a single high speed serial input. Precision current feedback amplifiers, which provide well-damped pulse response and fast voltage settling into large capacitive loads, buffer the 12 outputs. Laser trimming at the wafer level ensures low absolute output errors and tight channel-to-channel matching. Tight part-to-part matching in high resolution systems is guaranteed by the use of external voltage references.REFERENCE AND CONTROL INPUT DESCRIPTIONS Data transfer/start sequence control—input data loading, data transfer.A valid XFR control input initiates a new six-clock loading cycle, during which data is transferred to the outputs, and 12 input data-words are loaded sequentially into the 12 internal channels. Data is loaded on both the rising and falling edges of CLK. Data loaded from the previous cycle is transferred to the outputs on the rising CLK edge when the XFR is held HIGH at the preceding rising CLK edge only. A new loading sequence begins on the current rising CLK edge when XFR is held HIGH at the preceding rising CLK edge only.Right/left control—input data loading.To facilitate image mirroring, the direction of the loading sequence is set by the R/L control.A new loading sequence begins at Channel 0 and proceeds to Channel 11 when the R/L control is held LOW. It begins at Channel 11 and proceeds to Channel 0 when the R/L control is held HIGH.VRH, VRL inputs—full-scale video reference inputs.The full-scale output voltage is VFS = 2 × (VRH − VRL).INV control—analog output inversion.The analog voltage equivalent of the input code is subtracted from (VRL + VFS) while INV is held HIGH, and added to (VRL − VFS) while INV is held LOW.The state of the INV input is latched on the first rising edge of CLK, immediately following a valid XFR. The VIDx outputs invert on the first rising CLK edge, immediately following the next valid XFR.TSW control—thermal switch control.When this input is HIGH, the thermal protection circuit is enabled. When LOW or left unconnected, the thermal protection circuit is disabled. An internal 10 kΩ pull-down resistor disables the thermal switch when this pin is left unconnected.GCTL, GSW controls—output mode control.Table 7. GTCL, GSW Truth TableGTCL GSW Action0 0 All video outputs and VAO are forced nearAGND. While the outputs are disabled, AVCC canbe removed.0 1 All video outputs and VAO operate normally.1 X Output operating mode is controlled by theserial interface.TRANSFER FUNCTION AND ANALOG OUTPUT VOLTAGEThe DecDriver has two regions of operation where the video output voltages are either above or below the reference voltage VRL. The transfer function defines the video output voltage as the function of the digital input code asVIDx(n) = VRL + VFS × (1 − n/1023), for INV = HIGHVIDx(n) = VRL − VFS × (1 − n/1023), for INV = LOW where:n = input codeVFS = 2 × (VRH − VRL)A number of internal limits define the usable range of the video output voltages, VIDx, shown in Figure 10.VIDx– VOLTS(VRLVIDx vs. INPUT CODE≤ AVCC18VINTERNAL LIMITS ANDUSABLE VOLTAGE RANGES05687-10 Figure 10. Transfer Function and Usable Voltage RangesACCURACYTo best correlate transfer function errors to image artifacts, the overall accuracy of the DecDriver is defined by two parameters, VDE and VCME.VDE, the differential error voltage, measures the difference between the rms value of the output and the rms value of the ideal. The defining expression is()()()[]VFS n n VOUTP n VOUTN n VDE ×⎟⎠⎞⎜⎝⎛−−−=102312VCME, the common-mode error voltage, measures ½ the dc offset of the output. The defining expression is()()()⎥⎦⎤⎢⎣⎡−+=VRL n VOUTP n VOUTN n VCME 13-WIRE SERIAL INTERFACEThe serial interface controls the 8-bit serial DAC and the videooutput operating mode via a 12-bit serial word. The two most significant bits (MSB) select the function and the eight least significant bits (LSB) are the data for the serial DAC. Table 8. Bit DefinitionsBit Name Bit Functionality SD (0:7) 8-Bit SDAC Data. MSB = SD7. SD8 Not Used. SD9 Not Used. SD10 VAO Load Selection. SD11Output Mode Selection When GCTL = 1.Table 9. Truth Table @ GCTL = HIGHSEN SD Action 11 10 9 80 0 X X Normal Output Mode. No change to VAO.0 1 X X Normal Output Mode. Load VAO.1 0 X X Grounded Output Mode. No change to VAO.1 1 X X Grounded Output Mode. Load VAO.X X X X Start a Serial Interface Loading Cycle. No change to VAO.Table 10. Truth Table @ GCTL = LOWSE N SD Action 111098X 0 X X No Change to VAO.X 1 X X Load VAO.X X X X Start a Serial Interface Loading Cycle. Nochange to VAO.Serial DACThe serial DAC is loaded via the serial interface. The output voltage is determined byVAO = SVRL + (SVRH − SVRL ) × n /256 where n is the SD (0:7) serial input code.Output V AO is designed to drive capacitive loads less than 0.002 μF or more than 0.047 μF. Load capacitances in the0.002 μF − 0.047 μF range cause the output overshoot to exceed 100 mV .OUTPUT OPERATING MODESIn normal operating mode, the voltage of the video outputs isdetermined by the inputs.In grounded output mode, the video outputs are forced to (AGND + 0.2 V) typ.OVERLOAD PROTECTIONThe overload protection employs current limiters and a thermal protection circuit to protect the video output pins against accidental shorts between any video output pin and AVCC or AGND. The junction temperature trip point of the thermal protectioncircuit is 165°C. Production tests guarantee a minimum junction temperature trip point of 125°C. Consequently, the operating junction temperature should not rise above 125°C when the thermal protection circuit is enabled.For systems that operate at high internal ambient temperatures and require large capacitive loads to be driven by the AD8386 at high frequencies, junction temperatures above 125°C may be required. In such systems, the thermal protection circuit should either be disabled or a minimum airflow of 200 lfm must be maintained.APPLICATIONSOPTIMIZED RELIABILITY WITH THE THERMAL PROTECTION CIRCUITThe AD8386 is designed for enhanced reliability through features that provide protection against accidental shorts that may occur during PCB assembly repair, such as solder bridging, or during system assembly, such as a misaligned flat panel cable in the connector.While internal current limiters provide short-term protection against temporary shorts at the outputs, the thermal shutdown provides protection against persistent shorts lasting for several seconds. To optimize reliability, the following sequence of operations is recommended.Initial Power-Up after PCB Assembly or RepairDisable grounded output mode and enable thermal protection. Ensure that the GCTL and GSW pins are LOW and the TSW pin is HIGH upon initial power-up and remains unchanged throughout this procedure.•Execute the initial power-up.•Identify any shorts at the outputs.•Power-down, repair shorts, and repeat the initial power-up sequence until proper system functionality is verified. Power-Up during Normal OperationDisable grounded output mode and disable the thermal protection circuit using either of the following two methods: •GCTL = HIGH, TSW = HIGH and serial code0XXXXXXXXXXX sent immediately following a power-up, places all outputs into normal operating mode and disables the thermal protection circuit.•TSW = LOW disables the thermal protection circuit. GCTL = LOW and GSW = HIGH puts all outputs into normal operating mode.OPERATION IN HIGH AMBIENT TEMPERATURETo extend the maximum operating junction temperature of the AD8386 to 150°C, keep the thermal protection circuit disabled (TSW = LOW) during normal operation. POWER SUPPLY SEQUENCINGAs indicated in the Absolute Maximum Ratings section, the voltage at any input pin cannot exceed its supply voltage by more than 0.5 V. Power-on and power-off sequencing may be required to comply with the Absolute Maximum Ratings.Failure to comply with the Absolute Maximum Ratings may result in functional failure or damage to the internal ESD diodes. Damaged ESD diodes may cause temporary parametric failures, which may result in image artifacts. Damaged ESD diodes cannot provide full ESD protection, reducing reliability.The following power supply sequencing ensures that the Absolute Maximum Ratings are not violated.Power-on sequence is:•Turn ON AVCC and analog reference voltages.•Turn ON DVCC and digital signals.Power-off sequence is:•Turn OFF AVCC and analog reference voltages.•Turn OFF DVCC and digital signals.GROUNDED OUTPUT MODE DURING POWER-OFF Certain applications require that the video outputs be held near AGND during power-down. The following power-off sequence ensures that the outputs are near ground during power-off and the Absolute Maximum Ratings are not violated.•Enable grounded output mode in one of two ways:GTCL = LOW and GSW = LOW, or GCTL = HIGHand code 1XXXXXXXXXXX sent via the serial interface.•Turn OFF AVCC and analog reference voltages.•Turn OFF DVCC and digital signals.。
TEL T836 传输器和 T837 激发器 PCB 说明书
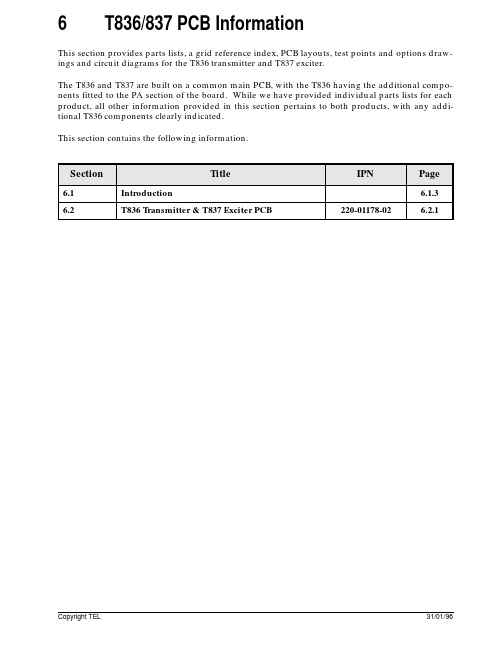
6T836/837 PCB InformationThis section provides parts lists, a grid reference index, PCB layouts, test points and options draw-ings and circuit diagrams for the T836 transmitter and T837 exciter.The T836 and T837 are built on a common main PCB, with the T836 having the additional compo-nents fitted to the PA section of the board. While we have provided individual parts lists for each product, all other information provided in this section pertains to both products, with any addi-tional T836 components clearly indicated.This section contains the following information.Section Title IPN Page 6.1Introduction 6.1.3 6.2T836 T ransmitter & T837 Exciter PCB220-01178-02 6.2.16.1IntroductionPCB IdentificationAll PCBs are identified by a unique 10 digit number, the last 2 digits of which define the issue status.The issue status starts at 00 and increments through 01, 02, 03, etc. as the PCB is updated. Some issue PCBs never reach full production status and are therefore not included in this manual. A let-ter following the 10 digit IPN has no relevance in identifying the PCB for service purposes.Parts ListsThe 10 digit numbers (000-00000-00) in this Parts List are “internal part numbers” (IPNs). Your spare parts orders can be handled more efficiently if you quote the IPN and provide a brief descrip-tion of the part.The components listed in this parts list are divided into two main types: those with a circuit refer-ence (e.g. C2, D1, R121, etc.) and those without (miscellaneous and mechanical).Those with a circuit reference are grouped in alphabetical order and then in numerical order within each group. Each component entry comprises three or four columns, as shown below:The miscellaneous and mechanical section lists the variant and common parts in IPN order.circuit reference -lists components in numerical ordervariant column -indicates that this component is fitted only to this variant Internal Part Number -order the component by this numberdescription -gives a brief description of the componentGrid Reference IndexTo assist in locating components and labelled pads on the PCB layouts and circuit diagrams, a com-ponent grid reference index has been provided. This index lists the components and pads in alpha-betical order, along with the appropriate alphanumeric grid references, as shown below:Using CAD Circuit DiagramsReading a CAD circuit diagram is similar to reading a road map, in that both have an alphanumeric border. The circuit diagrams in this manual use letters to represent the horizontal axis, and num-bers for the vertical axis. These circuit diagram “grid references” are useful in following a circuit that is spread over two or more sheets.When a line representing part of the circuitry is discontinued, a reference will be given at the end of the line to indicate where the rest of the circuitry is located. The first digit refers to the sheet number (printed on the bottom right hand corner of the CAD diagram) and the last two characters refer to the location on that sheet of the continuation of the circuit (e.g. 1-D4).If more than one line is represented (indicated by a double thickness line), a dot with a reference label will follow the route each individual line represents.circuit diagram reference PCB layout referencecomponents listed in numerical orderlayer number -1 = top side layer 2 = bottom side layercomponent location on the layersheet numbercomponent location on the sheet。
SS-T资料

SS-T Series CS-2460 09/01/06Page 1 of 2Features•Sleek, low-profile, stylish design.•State-of-the-art thermistor technology for fast response.•SS-TR rate-of-rise model: 15°F (8.3°C)per minute.•SS-T fixed heat, Factory preset at 135°F (57°C).•SS-TH high temperature model of 190°F (88°C).•Addressable by devices via decade address switches.•Rotary, decimal addressing (1 – 99)•Two-wire SLC connection.•Visible LEDs “blink” every time the unit is addressed.•360°-field viewing angle of the visual alarm indicators (two bicolor LEDs).LEDs blink green in Normal condition and turn on steady red in Alarm.•Integral communications and built-in device-type identification.•Remote test feature from the panel.•Built-in functional test switch activated by external magnet.•Low standby current.•Built-in tamper-resistant feature.•Designed for direct-surface or electrical-box mounting.•Sealed against back pressure.•Plugs into separate base for ease of installation and maintenance. Separate base allows interchange of photoelec-tric, ionization and thermal sensors.•SEMS screws for wiring of the separate base.•Constructed of off-white Bayblend®,designed to commercial standards, and offers an attractive appearance.•94-5V plastic flammability rating.•Remote LED output connection tooptional RA400Z remote LED annuncia-tor.•Optional sounder, relay, and isolator bases.•Optional recessed (RMK400) or surface (SMK400) base mounting kits.ListingsListings and approvals below apply to the SS-T Series of intelligent, address-able thermal (heat) detectors. In some cases, certain detectors may not be listed by certain approval agencies, or listing may be in process. Consult factory for latest listing status.• UL Listed: file S2527.• CSFM approved: file 3240-1288:166.• MEA approved: file 383-02-E Vol. V.DescriptionGamewell’s Smart Scan TM intelli-gent plug-in smoke detectors with integral communication provide features that surpass conven-tional detectors. Detector sensi-tivity can be programmed in the control panel software. Sensitiv-ity is continuously monitored andreported to the panel. Point ID capability allows each detector’s address to be set with decadeaddress switches, providing exact detector locations for selective maintenance and troubleshooting. SS-T Series thermal detectors use an innovative ther-mistor sensing circuit to produce 135°F/57°C fixed-temperature (SS-T ) and rate-of-rise thermal detection (SS-TR ) in a low-profile package. SS-TH provides fixed high-temperature detection at 190°F/88°C in a low-profile package as well. These thermal detectors provide cost effective, intelligent property protection in a vari-ety of applications. SS-T Series addressable detectors are compatible with Gamewell’s 602, 610, 632, 654 and 658 addressable fire alarm control panels with a Smart Scan TM SLC.InstallationThe SS-T Series of plug-in intelligent, addressable thermal detectors use a sepa-rate base to simplify installation, service, and maintenance. Installation instruc-tions are shipped with each detector.Mount base (all base types) on an electrical backbox which is at least 1.5" (3.81cm) deep. Suitable back boxes include:• 4.0" (10.16 cm) square box.• 3.5" (8.89 cm) or 4.0" (10.16 cm) octagonal box.•Single-gang box (except relay or isolator base).•With B501BH or B501BHT base, use a 4.0" (10.16 cm) square box.•With B224RB or B224BI base, use a 3.5" (8.89 cm) or 4.0" (10.16 cm) oc-tagonal box, or a 4.0" (10.16 cm) square box.NOTES: 1) Because of the inherent supervision provided by the SLC loop, end-of-line resis-tors are not required. Wiring “T-taps” or branches are permitted for Style 4 (Class “B”) wiring.2) When using relay or sounder bases , consult the SS-LI data sheet for device limitations between isolator modules and isolator bases.ApplicationsUse thermal detectors for protection of property. For further information, go to for manual I56-407-00, Applications Manual for System Smoke Detectors, which provides detailed information on detector spacing, place-ment, zoning, wiring, and special applications.Bayblend® is a registered trademark of Bayer Corporation.6936pho1.jpgSS-T in SS-B6 baseSS-T SeriesIntelligent Addressable Plug-In Thermal (Heat) DetectorsSS-T Series CS-2460 09/01/06Page 2 of 2Gamewell-FCI 12 Clintonville Road Northford, CT 06472-1610Phone: 203-484-7161Fax: A Honeywell Company © 2006 Gamewell-FCIProduct Line InformationWiring DiagramsSize2.1" (5.3 cm) high x 4.1" (10.4 cm)diameter installed in B501 base, 6.1"(15.5 cm) diameter installed in SS-B6base.Shipping weight 4.8 oz. (137 g).Operating temperature rangeSS-T, SS-TR: –20°C to 38°C (–4°F to 100°F)SS-TH: –20°C to 66°C (–4°F to 150°F).Detector spacingUL approved for 50 ft. (15.24 m) centerto center. FM approved for 25 x 25 ft.(7.62 x 7.62 m) spacing.Relative humidity10% – 93% noncondensing.Thermal ratingsFixed-temperature setpoint 135°F (57°C),rate-of-rise detection 15°F (8.3°C) per minute, high temperature heat 190°F (88°C).ELECTRICAL SPECIFICATIONS:Voltage range15 - 32 volts DC peak.Standby current (max. avg.)200 µA @ 24 VDC (without communica-tion); 300 µA @ 24 VDC (one communi-cation every 5 seconds with LED en-abled).LED current (max.)6.5 mA @ 24 VDC (“ON”).BASES AVAILABLE:SS-B6: 6.1" (15.5 cm) diameter.B501: 4.1" (10.4 cm) diameter.B501BH or B501BHT: Sounder base assembly. Includes B501 base.B224RB Relay Base: Screw terminals:up to 14 AWG (2.0 mm²). Relay type:Form-C. Rating: 2.0 A @ 30 VDCresistive; 0.3 A @ 110 VDC inductive; 1.0A @ 30 VDC inductive. Dimensions: 6.2"(15.748 cm) x 1.2" (3.048 cm).B224BI Isolator Base: Dimensions: 6.2"(15.748 cm) x 1.2" (15.748 cm). Maxi-mum: 25 devices between isolatorbases. See Note 2 under Installation on page 1.SS-T : Intelligent, addressable thermal detector. Must be mounted to one of the bases listed below.SS-TR : Same as SS-T with rate-of-rise feature.SS-TH : Intelligent, addressable high-temperature thermal (190°F/88°C) detector.Bases:SS-B6: Standard U.S. low-profile base, UL Listing.B501BP : Standard European flangeless base, pkg. of 10.B501BH : Sounder base, includes B501base above.B501BHT : Same as B501BH, but includes temporal sounder.B224RB : Intelligent relay base.B224BI : Intelligent isolator base. Isolates SLC from loop shorts.Accessories:RA400Z : Remote LED annunciator. 3 – 32VDC. Fits U.S. single-gang electrical box.Supported by SS-B6 and B501 bases only.SMK400: Surface mounting kit provides for entry of surface wiring conduit. For use with B501 base only .RMK400: Recessed mounting kit. For use with B501 base only .SMB600: Surface mounting kit for use withAddress dial on back of detector.SS-B6.BCK-200B : Black detector covers, box of 10.M02-04-01: Test magnet.M02-09-00: Test magnet with telescope stick.XR2B : Detector removal tool. Allowsinstallation and/or removal of SS-T Series thermal detector heads from base in high ceiling installations.T55-127-000: Detector removal tool without pole.XP-4: Extension pole for XR2B. Comes in three 5-ft. sections.Detector Guards:NOTE: The following guards are not UL listed with the SS-T detectors. Consult with AHJ.STI 9601: Low-profile, flush-mount smoke detector guard, wire.STI 9602: Low-profile, surface-mount, smoke detector guard, wire.STI 9609: High-profile, flush-mount, smoke detector guard, wire.STI 9605: High-profile, surface-mount, smoke detector guard, wire.STI 9604: Flush-mount heat detector guard, wire.STI 9610: Surface-mount heat detector guard, wire.STI-8200-SS : Flush-mount stainless steel smoke detector guardSTI-8230-SS : Surface-mount stainless steel smoke detector guard。
河南省初级中学理科教学仪器配备标准(详细)

省初级中学理科教学仪器配备标准编制说明一、本标准是根据教育部发布的全日制义务教育数学(第三学段)、物理、化学、生物、地理课程标准(实验稿)及《初中理科教学仪器配备标准》(JY/T 0386—2006),结合实际情况制订的。
本标准作为指导本省义务教育阶段初级中学配备教学仪器的依据,亦可作为特殊教育学校配备常规教学仪器的参考。
二、本标准是按数学、物理、化学、生物、地理五科分学科编制的,分为“基本”和“选配”两种配备要求。
“配备数量”栏目中不加括号的数字为“基本”要求,加括号的数字为“选配”要求。
“基本”要求规定了初中完成上述课程标准所规定的教学任务应具备的常规仪器设备、教学软件、药品、材料、工具和必要的安全器材,所有开设初中理科课程的学校均应达到该栏目的配备要求。
有条件的学校在达到“基本”配备要求的基础上,可根据选用的教材、教师教学方法的多样性和仪器的多种类等实际情况,在“选配”栏目中有选择地配备相应的仪器设备,以满足教学的需要。
三、基于我省各地经济和教育发展的实际情况,本标准配备数量按学校规模为4轨(每年级4个平行班)、每班50人的标准计算,提出了二种配备方案。
省辖市所在地、县城所在地及市(县)直属初级中学按方案一配备。
乡(镇)初级中学(含乡以下)按方案二配备。
其他规模学校参照《省初级中学教育装备标准(试行)》的要求,每个室配备相应的仪器、设备;如果每班学生数较多,则应适当增加配备数量,达到分组活动每组人数不多于6人。
四、消耗性实验材料是保证教学实验活动顺利进行的重要条件,学校应根据需要及时补充。
五、各级装备部门应指导各类学校结合所选用的教材和教学活动的实际需要,对学校现有仪器进行清理,并对照本标准所列的品种和数量,制订积极的、切实可行的配备计划。
六、凡是进入学校的教学仪器设备产品,需取得通过计量认证的教学仪器设备产品质量检验机构出具的合格证书或符合相关标准的检测报告。
不得含有国家明令禁止的有毒材料,要符合国家相关安全和环保标准。
- 1、下载文档前请自行甄别文档内容的完整性,平台不提供额外的编辑、内容补充、找答案等附加服务。
- 2、"仅部分预览"的文档,不可在线预览部分如存在完整性等问题,可反馈申请退款(可完整预览的文档不适用该条件!)。
- 3、如文档侵犯您的权益,请联系客服反馈,我们会尽快为您处理(人工客服工作时间:9:00-18:30)。
Transistors Rev.A 1/3NPN general purpose transistorSST6838z Features z External dimensions (Unit : mm) 1) BV CEO minimum is 40V (I C = 1mA) SST6838ROHM : SST3(1) Emitter (2) Base (3) Collectorthe same dimensions All terminals have0~0.10.2Min.2.4±0.21.30.950.45±0.10.150.42.9±0.21.9±0.20.950.95+0.2−0.1−0.1+0.2+0.1−0.06+0.1−0.05(2)(1)(3)2) Complements the SST6839.z Package, marking and packaging specificationsPart No.SST6838SST3RBR T1163000Pacaging type MarkingCodeBasic ordering unit (pieces)z Absolute maximum ratings (T a=25°C)ParameterSymbol V CBO V CEO V EBO I C Tj TstgLimits 504050.2150−55 to +150Unit V V V A P C 0.2W °C °CCollector-base voltage Collector-emitter voltage Emitter-base voltage Collector currentJunction temperature Storage temperatureCollector power dissipationz Electrical characteristics (T a=25°C)ParameterSymbol Min.Typ.Max.Unit ConditionsBV CBO BV CEO I EBO5040−−−−−−−−0.55V V µAI C =10µA I C =1mA V EB =4V V EB =4VI CBO −−−−0.55µA V CB =30V V CB =30V 200−−−−0.7I C /I B =10mA/0.2mA V CE(sat)−−0.5V I C /I B =10mA/0.2mA V CE /I C =5V/1mA V CE /I C =5V/10mAh FE2150−−−−V CE /I C =5V/1mA −1000−V CE /I C =5V/1mA h FE1−800−f T Cob 50−1802−3.5MHz pF V CE =12V , I C =2mA , f =100MHz V CB =12V , f =1MHz Cib−17−pF V EB =0.5V , f =1MHz(Ta = −40°C to +125°C)(Ta = −40°C to +125°C)(Ta =85°C)(Ta =125°C)(Ta =85°C)(Ta =125°C)(Ta =85°C)−−0.4I C /I B =50mA/5mA (Ta =25°C)(Ta =125°C)(Ta = −40°C to +25°C)(Ta =85°C)(Ta =125°C)(Ta = −40°C to +25°C)(Ta =25°C)(Ta =25°C)(Ta =25°C)Collector-base breakdown voltage Collector-emitter breakdown voltage Emitter cutoff currentCollector cutoff current Collector-emitter saturation voltageDC current transfer ratio DC current transfer ratio Transition frequency Collector output capacitance Emitter input capacitanceTransistors Rev.A 2/3z Electrical characteristic curvesFig.1 Grounded emitter propagationcharacteristics C O L L E C T O R C U R R E N T : I C (m A )BASE TO EMITTER VOLTAGE : V BE (V)Fig.2 Grounded emitter outputcharacteristics ( Ι )C O L L E C T O R C U R R E N T : I C (m A )COLLECTOR TO EMITTER VOLTAGE : V CE (V)C O L L E C T O R C U R R E N T : I C(m A )COLLECTOR TO EMITTER VOLTAGE : V CE (V)Fig.3 Grounded emitter outputcharacteristics ( ΙΙ )Fig.4 DC current gain vs.collector current ( Ι )D C C U R R E N T G A I N : h F ECOLLECTOR CURRENT : I C (mA)Fig.5 DC current gain vs.collector current ( ΙΙ )D C C U R RE N T G A I N : hF ECOLLECTOR CURRENT : I C (mA)Fig. 6 Collector-emitter saturationvoltage vs. collector currentC O L L E C T O R S A T U R A T I O N V O L T A G E : V C E (s a t ) (V )COLLECTOR CURRENT : I C (mA)Fig.7 Collector-emitter saturationvoltage vs. collector current ( Ι )C O L L E C T O R S A T U R A T I O N V O L T A G E : V C E (s a t ) (V )COLLECTOR CURRENT : I C (mA)Fig.8 Collector-emitter saturationvoltage vs. collector current (ΙΙ)C O L L E C T O R S A T U R A T I O N V O L T A G E : V C E (s a t ) (V )COLLECTOR CURRENT : I C (mA)Fig.9 Gain bandwidth product vs.emitter current−EMITTER CURRENT : I E (mA)T R A N S I T I O N F R E Q U E N C Y : f T (M H z )Transistors Rev.A 3/3Fig.11 Base-collector time constantvs. emitter current − B A S E C O L L E C T O R T I M E C O N S T A N T : C c ·r b b (p s )EMITTER CURRENT : I E (mA)Fig.10 Collector output capacitance vs.collector-base voltageEmitter input capacitance vs.emitter-base voltageCOLLECTOR TO BASE VOLTAGE : V CB (V)EMITTER TO BASE VOLTAGE : V EB (V)C O L L E C T O R O U T P U T C A P A C I T AN C E : C o b (p F )E M I T T E R I N P U T C A P A C I T A N C E : C i b (p F )AppendixAbout Export Control Order in JapanProducts described herein are the objects of controlled goods in Annex 1 (Item 16) of Export T rade ControlOrder in Japan.In case of export from Japan, please confirm if it applies to "objective" criteria or an "informed" (by MITI clause)on the basis of "catch all controls for Non-Proliferation of Weapons of Mass Destruction.Appendix1-Rev1.1分销商库存信息: ROHMSST6838T216。