工程曲面理论在风机叶片设计中的应用研究
风力发电机组的叶轮设计优化与性能分析

风力发电机组的叶轮设计优化与性能分析1. 引言风力发电作为一种可再生能源的重要形式,被广泛应用于电力供应系统。
叶轮作为风力发电机组中的核心部件,直接影响着发电机组的性能和效率。
本文旨在通过对风力发电机组叶轮的设计优化与性能分析,提出一种能够提高发电效率的叶轮设计方案。
2. 风力发电机组的工作原理风力发电机组利用风能将风动能转化为机械能,然后通过发电机将机械能转化为电能。
叶轮作为风力发电机组中的核心部件,承担着捕捉和利用风能的重要任务。
叶轮优化设计的目标是最大化风能的转化效率,提高发电机组的发电量。
3. 叶轮设计优化3.1 叶片数目和形状设计叶片数目和形状直接影响着风力发电机组的功率转化性能。
一般而言,叶片数目越多,转化效率越高。
然而,叶片数目过多会增加制造成本并增加风力发电机组的重量。
因此,需要综合考虑叶片数目和形状的设计,找到一个平衡点。
3.2 叶片长度和宽度设计叶片长度和宽度的设计也是叶轮设计中的重要因素。
叶片长度越长,捕捉风能的面积越大,风力发电机组的转化效率越高。
然而,过长的叶片会增加风力发电机组的叶轮重量,并对叶轮结构造成一定的负荷。
因此,需要对叶片长度和宽度进行优化设计。
3.3 叶片材料选择叶轮受到来自空气流动的巨大压力和弯曲力的影响,因此在叶片材料的选择上需要考虑其强度、轻量化和耐腐蚀性。
目前常用的叶片材料有玻璃纤维增强塑料(GFRP)和碳纤维增强塑料(CFRP)等。
在叶片材料的选择中,需要综合考虑材料的力学性能和经济性,以实现叶轮结构的优化设计。
4. 叶轮性能分析4.1 基于流体动力学的模拟分析通过建立风力发电机组的叶轮流体动力学模型,可以对叶轮的流场分布和压力分布进行模拟分析,了解叶轮在风力作用下的性能表现。
这可以为叶轮的优化设计提供有力的依据。
4.2 发电机组的发电量模拟叶轮是风力发电机组中能量转化的关键部件,其性能的优化直接影响发电机组的发电效率。
通过基于叶轮性能和风能资源的数据,可以进行发电量的模拟计算,评估叶轮优化设计的效果。
叶片设计技术在风力发电中的应用
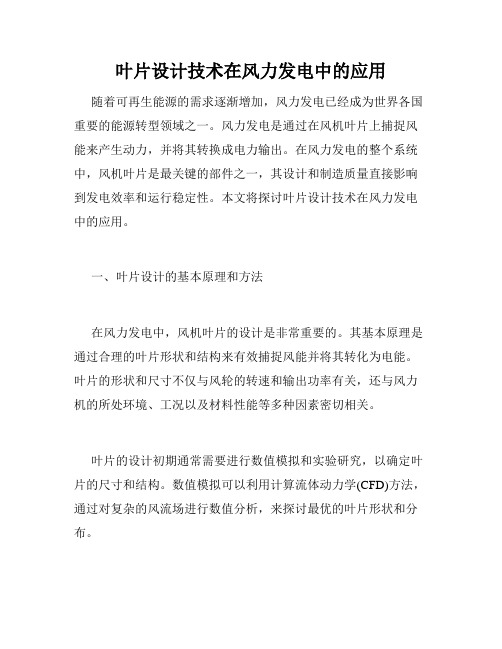
叶片设计技术在风力发电中的应用随着可再生能源的需求逐渐增加,风力发电已经成为世界各国重要的能源转型领域之一。
风力发电是通过在风机叶片上捕捉风能来产生动力,并将其转换成电力输出。
在风力发电的整个系统中,风机叶片是最关键的部件之一,其设计和制造质量直接影响到发电效率和运行稳定性。
本文将探讨叶片设计技术在风力发电中的应用。
一、叶片设计的基本原理和方法在风力发电中,风机叶片的设计是非常重要的。
其基本原理是通过合理的叶片形状和结构来有效捕捉风能并将其转化为电能。
叶片的形状和尺寸不仅与风轮的转速和输出功率有关,还与风力机的所处环境、工况以及材料性能等多种因素密切相关。
叶片的设计初期通常需要进行数值模拟和实验研究,以确定叶片的尺寸和结构。
数值模拟可以利用计算流体动力学(CFD)方法,通过对复杂的风流场进行数值分析,来探讨最优的叶片形状和分布。
二、叶片设计技术的应用1. 叶片形状的改进叶片的形状和尺寸对风力机的效率有重要的影响。
对于传统的风力机叶片,其钝角比较大,容易使风能流失,降低风力机的效率。
而采用先进的叶片形状设计,如S型、D型、倒卵形等,可以提高风力机的效率,并降低风力机的风速截止速度。
2. 叶片材料的优化叶片材料的性能直接影响到叶片的疲劳寿命、耐久性和可靠性。
不同的叶片材料可以有不同的强度、韧性和质量,选择合适的叶片材料可以在不降低发电效率的前提下提高叶片的使用寿命,降低维护和更换成本。
3. 叶片表面涂层技术通过对叶片表面进行涂层处理,可以有效地改善叶片的防污、抗氧化、抗紫外线等性能,提高其寿命和维护成本。
同时,通过增加叶片表面的光滑度,还可以有效地降低风力机的风阻力,增加发电量。
4. 特殊叶片结构设计目前,一些新型叶片结构设计,如蠕行型、可展叶片、弯曲叶片等正在逐渐发展和应用。
这些特殊的叶片设计可以增加风力机的转速,提高叶片的捕风效率,并增加其适应各种风力工况的能力,从而提高了整个风力发电系统的效率和稳定性。
TRIZ理论技术矛盾的实践应用——风力发电叶片的分析与改进

时, 可能 引起 叶片断 裂 。而 当风 速小 、 叶片较 大时 , 风 车发 电不足 或无 法发 电。 因此 , 根据 动态特 性原 理 在 叶片两侧 或单 一某侧 给 叶片添加 一伸缩 翼 , 当 风 速较小 时 , 翼拉 伸 ; 侧 当风速较 大时 , 侧翼 收缩 。
的强度问题。因此 , 可以把运动物体的面积和强度
3 个部分 : 根部、 外壳和龙骨。查阅资料后发现 , 大 部分的风车叶片损坏都是被折断的, 而且断裂的部 位很有规律 , 总是在靠近叶片根部 , 或者是离叶尖
收稿 日期 :0 1 6—1 2 1 —0 3 作者简介 : 豆玉龙( 9 7 , , 淮北人 , 18 一)男 安徽 昆明理工 大学硕 士研究生 , 主要从事数字化制造技术等方面的研究工作
C e nvt nS i 是一套简单、结构化 、 r xI oa o u e a n i t 系统 化及 可预 测 性 的创 新 流 程分 析 软 件 ,可 用来 处理 问题 及找 出创 新 方 案 ,让 使 用 者 更 系 统地 处 理工程方面的问题 ,其对扩大产 品研发 、产 品的
的作用不言而喻 。要提高风能发 电的效率 , 改进的 第一级就是对叶片的改进 , 可以从增加叶片长度和 叶片宽 度来 实现 。如 果从 增加 叶片 长度来 说 , 的 它 实现受 到一 定 的 限制 , 因为 叶片 的长 度 越 长 , 2个 风车发 电 塔 之 间 的 距 离 就 越 大 , 占地 面积 也 就 越 大 , 大 地 浪 费 了土 地 资源 。 因此 , 者考 虑 从增 极 笔 加 叶片 宽度来 分 析 。叶 片宽 度 的增加 同样 可 以使 叶片得到更多的风 的推力 , 同时提高发电效率 , 但 是 同时也对 叶 片 造成 很 大 的 压力 。 由于风 力 强度 的增 加 , 叶片 的危 害也 是 显 而 易见 的 , 容 易造 对 很 成 风车 叶 片的断 裂 , 也是 现在 风力发 电中叶片最 这 易出现的问题 。风力发 电机叶片的机构可以分为
基于无动力排风扇叶片曲面逆向工程技术研究
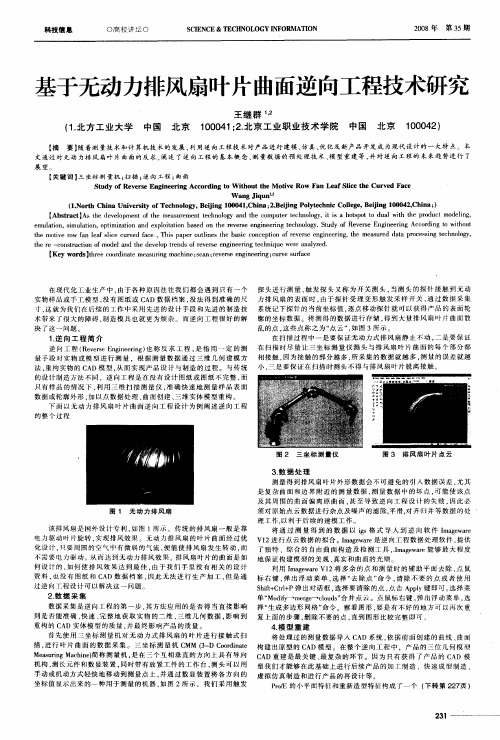
W a g Jq n n iu
(. r hn ies yo eh ooy B in 0 0 1 ia2Be igP l eh i Col e B in 0 0 2C i ; 1 t C iaUnvri f c n lg , e ig10 4 , n ;. in oy cnc lg , ej g1H 4, h衄 ) No h t T j Ch j t e i 0
【 yw rstrecodnt mesr gmahn ; a ;ee eegneig CIesr c Ke o d 】 e oriae aui c ies n rvr n ier ;HV uf e h n c s n a
触 当 在现 代 化 工业 生产 中 , 由于 各种 原 因往 往 我 们 都 会 遇 到 只 有 一 个 探 头 进 行 测 量 , 发 探 头 又 称 为 开关 测 头 , 测 头 的 探 针 接 触 到无 动 由于 探 针 受 理 变形 触 发 采 样 开 关 , 过 数 据 采 集 通 实 物样 品 或 手 工模 型 , 有 图 纸 或 C 没 AD数 据 档 案 , 法 得 到 准 确 的 尺 力 排 风 扇 的 表 面 时 , 没 逐 寸 , 就 为 我 们 在后 续 的工 作 中 采用 先 进 的 设 计 手 段 和 先 进 的 制 造 技 系 统 记 下探 针 的 当前 坐 标值 , 点 移 动 探 针 就 可 以 获得 产 品 的 表面 轮 这 术带 来 了很 大 的 障碍 , 造 模 具 也就 更 为 烦 杂 。 而 逆 向 工 程 很 好 的 解 廓 的 坐 标数 据 。将 测 得 的数 据 进 行 存 储 , 到 大 量排 风 扇 叶 片 曲 面散 制 得 乱 的 点 . 些 点 称 之 为 “ 云 ”如 图 3所示 。 这 点 , 决 了这 一 问 题 在 扫描 过 程 中 一 是 要保 证 无 动 力 式 排 风 扇静 止 不 动 , 是 要 保 证 二 1逆 向工 程 简 介 .
基于无动力排风扇的叶片曲面重构分析
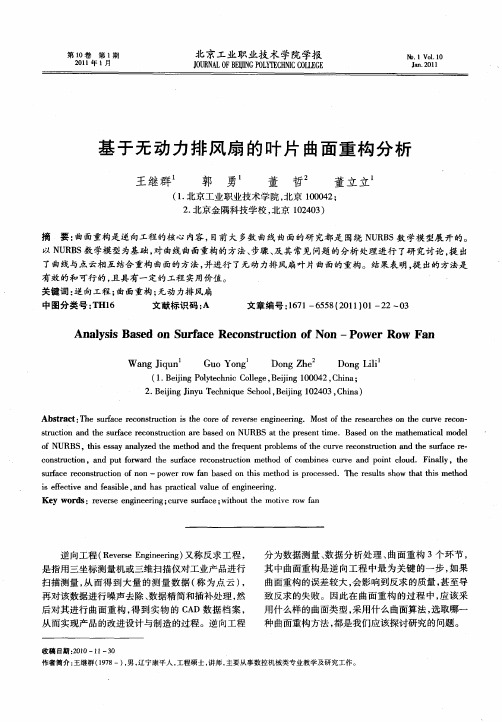
Wa g Jq n n iu
Gu n oYo g
Do gZ e n h
D n i o gL l i
ቤተ መጻሕፍቲ ባይዱ
( . e i oy cncC l g , e ig10 4 , hn ; 1 B in P l eh i o ee B in 0 0 2 C ia jg t l j 2 B in n uT c n u c olB in 0 4 3 C ia . e i J y eh i eS ho, e ig1 2 0 , hn ) jg i q j
王 继群 郭 勇 董 哲 董 立 立
(. 1 北京 工业 职业技 术学 院 , 京 10 4 ; 北 0 0 2 2 北京 金隅科 技学 校 , 京 12 0 ) . 北 0 4 3 摘 要 : 面重构是 逆 向工程 的核 心 内容 , 曲 目前 大 多数 曲线 曲面 的研 究都 是 围绕 N R S数 学模 型展 开 的 。 UB
逆 向工程 ( ees nier g 又称反 求 工 程 , R vreE gnei ) n 是 指用 三坐标 测量 机或三 维扫 描仪 对工业 产 品进行
扫 描测量 , 而得 到 大 量 的 测量 数 据 ( 为 点 云 ) 从 称 ,
分 为数 据测量 、 据 分 析处 理 、 数 曲面 重 构 3个 环 节 ,
其 中曲面重构是逆 向工程中最为关键的一步 , 如果
曲面重 构 的误 差较 大 , 影 响到反求 的质 量 , 至导 会 甚 致 反求 的失败 。因此 在 曲面 重构 的过 程 中 , 应该 采 用 什么 样 的曲面类 型 , 用什 么 曲面算法 , 采 选取 哪一 种 曲面 重构方 法 , 都是我 们应 该探讨 研究 的 问题 。
空气动力学中的叶片轮廓曲面设计与优化分析

空气动力学中的叶片轮廓曲面设计与优化分析在各种飞机和车辆的设计过程中,空气动力学是一个至关重要的领域。
叶片是其中一个重要的元素,充当了机翼、螺旋桨、涡轮机等设备中关键的作用。
叶片的轮廓曲线设计和优化可以有效地提高设备的性能和使用寿命,同时减少燃油消耗和废气排放。
在这篇文章中,将会讨论叶片轮廓曲面设计和优化的一些方法和技术。
1. 叶片轮廓曲线的形式和特征在叶片的设计和制造中,轮廓曲线是关键的设计因素。
通过轮廓曲线的设计,可以控制空气动力学和机械性能,从而提高叶片的效率和使用寿命。
叶片轮廓曲线通常由一系列基本曲线和控制点组成。
在基本曲线中,常用的有贝塞尔曲线、NURBS曲线、B 样条曲线等,而控制点则用于控制曲线的形状和位置。
叶片轮廓曲线的形状和特征与叶片的作用有关。
比如,在飞机的机翼中,轮廓曲线的形状和位置将影响到机翼的升力和阻力,而在涡轮机中,轮廓曲线的形状和位置则将影响到叶轮的压力和流量。
同时,轮廓曲线也需要考虑到叶片的结构特点,如叶片的厚度、材料和支撑结构等。
2. 叶片轮廓曲线设计的方法为了设计出高效的叶片轮廓曲线,通常需要采用逐步优化的方法。
首先需要考虑的是叶片的基本形态,即决定叶片长度、形状和位置的因素。
这可以通过风洞实验、数值模拟和经验公式等方法进行分析和评估。
在基本形态确定后,接下来需要考虑叶片轮廓曲线的具体形状和特征。
这时可以采用手动设计或计算机辅助设计的方法。
手动设计依赖于设计人员的经验和直觉,以及基于手绘图或模型的简单分析。
计算机辅助设计则采用了CAD和CAE等工具,能够更准确地计算和评估轮廓曲线的效果和性能。
在设计过程中,需要考虑到叶片的工作条件和使用环境。
比如在高速旋转的涡轮机叶片中,轮廓曲线的形状和位置需要考虑到离心力和惯性力等因素。
而在低速输送机的叶片中,则需要考虑轮廓曲线的适应性和耐用性。
3. 叶片轮廓曲线优化的方法在设计出初步的叶片轮廓曲线后,还需要进行优化。
这可以采用多种不同的方法和技术。
基于NURBS的风机叶片造型研究

S u y o a l d li g b s d o t d ff n ba e modn a e n NURBS
Z HANG — e , U u z u S Gu — h n Yu w i F Xi —h o, U o s e g
meh o l r v h u l y o e d sg f a ld f cie . to c ud i o e t e q a i ft e in o b a e ef t l d mp t h f n e v y Ke r s ba e N B ; o t ly p it S L y wo d : ld ; UR S c n r b n ; T o o
维普资讯
第 2 卷 第 3期 0
20 0 6定
山 东
轻 工
业
学
院 学
报
V 12 N . o .0 o3
9月
J R A O S A D N ISIU E F IM' I UT Y OU N L F H N O G N TT T 0 LG ND S R
cu igcnrln e es ons s r c it c mp tt n a d te d s n o T x h g l . T i ldn o t l g rv re p it, uf e p ns o uai h ei fS L ec a e fe oi a o o n g n i hs
“ + = + =… = + + =1且 曲 线 定 义域 “ 1 2 k1 , ∈
的一种 , 它有诸多优点 , C D C M与计算机 图形 在 A /A 学领域 得 到了广泛 的应 用 。本文 以扭 变风机 叶 片为
500W风力机叶片建模与仿真技研究
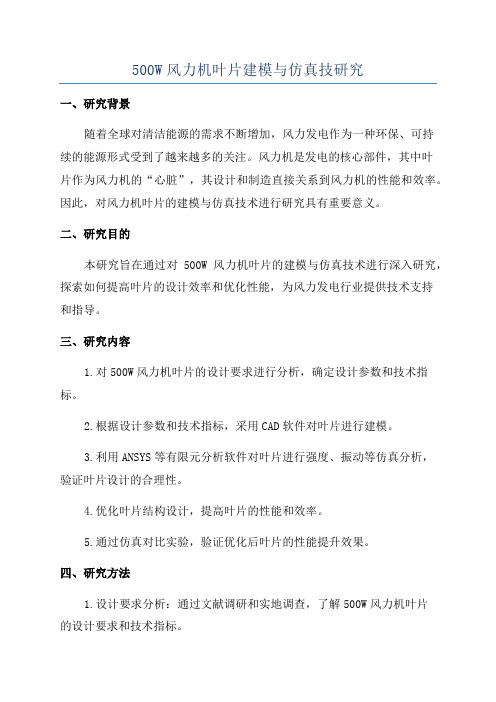
500W风力机叶片建模与仿真技研究一、研究背景随着全球对清洁能源的需求不断增加,风力发电作为一种环保、可持续的能源形式受到了越来越多的关注。
风力机是发电的核心部件,其中叶片作为风力机的“心脏”,其设计和制造直接关系到风力机的性能和效率。
因此,对风力机叶片的建模与仿真技术进行研究具有重要意义。
二、研究目的本研究旨在通过对500W风力机叶片的建模与仿真技术进行深入研究,探索如何提高叶片的设计效率和优化性能,为风力发电行业提供技术支持和指导。
三、研究内容1.对500W风力机叶片的设计要求进行分析,确定设计参数和技术指标。
2.根据设计参数和技术指标,采用CAD软件对叶片进行建模。
3.利用ANSYS等有限元分析软件对叶片进行强度、振动等仿真分析,验证叶片设计的合理性。
4.优化叶片结构设计,提高叶片的性能和效率。
5.通过仿真对比实验,验证优化后叶片的性能提升效果。
四、研究方法1.设计要求分析:通过文献调研和实地调查,了解500W风力机叶片的设计要求和技术指标。
2.建模:利用CAD软件对500W风力机叶片进行三维建模,包括叶片的外形、内部结构等。
3.仿真分析:利用有限元分析软件对叶片进行强度、振动等仿真分析,获取叶片在不同工况下的力学性能。
4.优化设计:根据仿真分析结果,对叶片结构进行优化设计,提高其性能和效率。
5.仿真对比实验:对比优化前后叶片的性能指标,验证优化效果。
五、研究意义1.提高500W风力机叶片设计的效率和准确性,节约设计时间和成本。
2.优化叶片结构,提高风力机的能量利用率和发电效率。
3.为未来更大功率风力机叶片设计提供参考和借鉴。
4.促进清洁能源行业的发展和技术进步。
六、结论通过对500W风力机叶片的建模与仿真技术研究,可以提高叶片设计的效率和准确性,优化叶片结构,提高风力机的性能和效率,为清洁能源领域的发展提供技术支持和指导。
希望本研究能够为风力发电行业的进一步发展做出贡献。
基于CATIA的叶片曲面造型技术研究

基于CATIA的叶片曲面造型技术研究CATIA是一款领先的计算机辅助设计软件,它广泛应用于航空航天、汽车、机械制造等领域。
本文将介绍CATIA在叶片曲面造型方面的应用。
叶片曲面造型是涉及到航空发动机、汽车发动机、涡轮机等领域的重要工作。
曲面造型技术是利用软件进行成型、设计,从而对复杂的物体进行快速、准确的建模。
由于该技术对几何表面的精度和控制面的数量有着非常高的要求,因此在研制和生产领域得到越来越广泛的应用。
CATIA在叶片曲面造型方面具有很多优点。
首先,CATIA支持大规模的叶片曲面造型任务,同时提供了众多的工具和功能,例如创建曲线、剖面、旋转曲面、平移曲面等等。
其次,CATIA具有灵活的设计模块,可以帮助工程师更轻松地进行二次开发和修改。
最后,CATIA的数据管理系统也是非常强大的,能够处理大量的设计数据,并确保数据的安全性和完整性。
CATIA的曲面造型工具主要包括以下几种:1. 构建几何曲线:该工具可用于创建曲线以实现几何图形的建模,例如圆曲线、椭圆曲线、贝塞尔曲线等。
2. 剖面设计:该工具可用于创建各种形状的剖面,并将其转换为曲面。
3. 旋转形状:该工具可用于将一个剖面旋转成一个曲面。
4. 平移形状:该工具可用于将一个平移体,也就是一个几何图形在另一个几何图形上平移,从而形成一个曲面。
上述工具中,剖面设计和旋转形状是CATIA中最常用的曲面造型工具。
具体来说,剖面设计工具可以根据特定的截面快速创建叶片,而旋转形状工具则可以通过旋转剖面来创建整个叶片外形。
此外,CATIA的曲面造型工具还支持以下一些重要的功能:1. 模型分析:该功能可以分析和优化曲面模型,检查其是否符合设计规范。
2. 精度工具:该工具可用于精确测量曲面模型中的点、线和面,并且可以根据需要调整曲面的精度。
3. 模型编辑工具:该工具可以帮助工程师进行二次设计和修改,包括切割、拉伸、挤压等操作。
总之,CATIA在叶片曲面造型方面的应用非常广泛,其强大的工具和功能以及灵活的设计模块可以大大提高工程师的效率和精度。
风力机叶轮设计解析
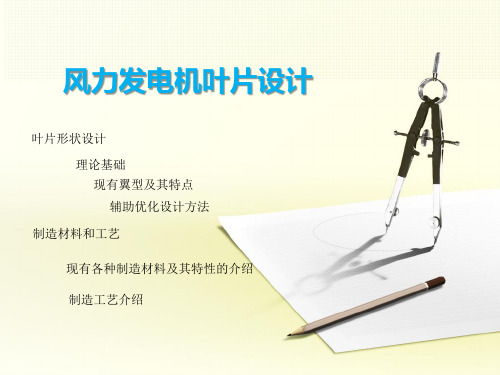
ldr cos
将上式投影到转轴上,设叶片数为n,则轴向推力为
dT
1 2
Cln
v2
sin2
cos( cos
) ldr
与上文相同的式子等同,则得到
Clnl
4r
sin2 cos( )
已知在最佳运行条件下
v
2 3
v1
,则
cot
r v
3 r 2 v1
3
2
为叶尖速比---------叶尖圆周速度与风速的比值
-----攻角,是来流速度方向与弦线间的夹角 0 -----零升力角,弦线与零升力线之间的夹角 -----升力角,来流速度方向与零升力线间的夹角
理论基础
风能计算
由一般的流体力学可知,气流的动能可以表示为:
E
1 mv 2
2
设单位时间内气流流过的单位面积 S 的气体体积为 V ,气体密度为
则气流所具有的动能表示为
E
1 2
Sv 3
其中密度和风速随着地理位置,海拔高度,地形等因素而改变, 速度为主要因素
贝茨理论
假设条件 叶轮没有轮毂,具有无限多叶片 气流通过风轮时没有阻力 气流经过整个风轮面时是均匀的 气流速度方向在风轮前后通过风轮时是沿风轮轴线方向 气体为不可压缩气体
连续性条件 S1v1 S2v 2
作用在风机上的力
风力发电机叶片设计
叶片形状设计 理论基础 现有翼型及其特点 辅助优化设计方法
制造材料和工艺
现有各种制造材料及其特性的介绍 制造工艺介绍
叶片和翼型的几何形状与空气动力特性
翼型的参数
l -----翼型的弦长,A点到B点的长度 C -----最大厚度,即弦长法线方向之翼型最大厚度 f -----翼型中线最大弯度
风电机叶轮设计数学模型的工程应用分析
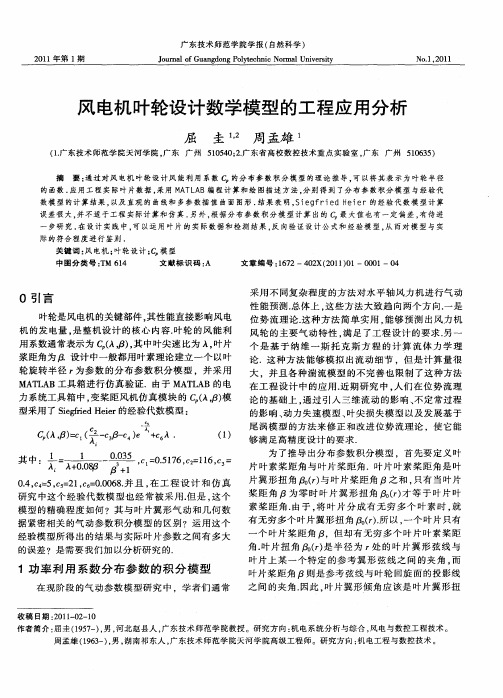
际的符 合程度 进 行鉴别 .
中图分 类 号 :M 1 T 64
文 献标 识 码 : A
文章 编 号 :6 2—4 2 2 1 ) 1—0 0 17 0 X(0 1 0 0 l一0 4
0 引 言
叶轮是风 电机的关键部件 , 其性能直接影 响风电
采 用 不 同复 杂 程 度 的方 法 对 水 平 轴 风 力 机 进 行 气 动
性 能预测. 总体上 。 这些 方法大致趋 向两个方 向. 一是 位 势 流 理 论 . 种 方 法 简单 实用 . 够 预 测 出风 力 机 这 能
风 轮 的 主 要 气 动 特 性 。 足 了工 程 设 计 的要 求 . 一 满 另 个 是 基 于 纳 维 一 斯 托 克 斯 方 程 的 计 算 流 体 力 学 理 论 .这 种 方 法 能够 模 拟 出 流 动 细 节 ,但 是 计 算 量 很 大 ,并 且 各 种 湍 流 模 型 的 不 完 善 也 限制 了 这 种 方法
桨 距 角 为 零 时 叶 片 翼 形 扭 角 () 等 于 叶 片 叶 r才 有无 穷 多 个 叶 片 翼 形 扭 角 () 以 , 个 叶 片 只有 r. 所 一
一
为 了 推 导 出 分 布 参 数 积 分 模 型 ,首 先要 定 义 叶
片 翼 形 扭 角 () 叶 片 桨距 角 之 和 , r与 只有 当 叶 片 素桨 距角 . 于 , 叶 片分 成有无 穷 多个 叶素时 , 由 将 就
广 东技 术 师范 学院 学报 ( 自然科 学 ) 2 1 年第 l 01 期
J un lo a g o gP ltc ncNoma iest o r a fGu n d n oye h i r l Unv ri y No 1 2 1 .,0 1
工程力学在风力发电设备设计中的应用
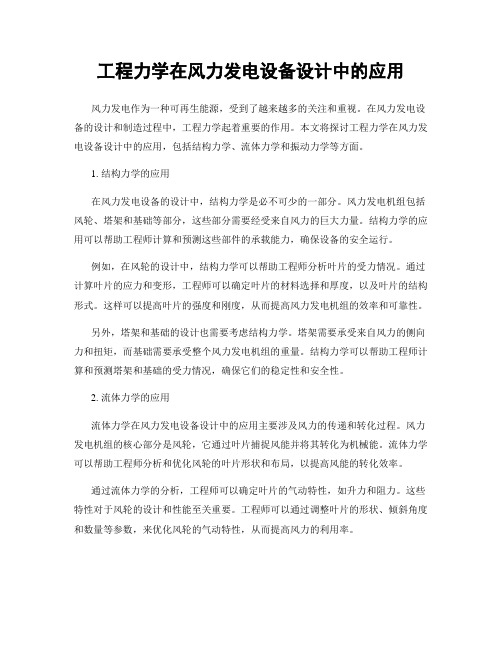
工程力学在风力发电设备设计中的应用风力发电作为一种可再生能源,受到了越来越多的关注和重视。
在风力发电设备的设计和制造过程中,工程力学起着重要的作用。
本文将探讨工程力学在风力发电设备设计中的应用,包括结构力学、流体力学和振动力学等方面。
1. 结构力学的应用在风力发电设备的设计中,结构力学是必不可少的一部分。
风力发电机组包括风轮、塔架和基础等部分,这些部分需要经受来自风力的巨大力量。
结构力学的应用可以帮助工程师计算和预测这些部件的承载能力,确保设备的安全运行。
例如,在风轮的设计中,结构力学可以帮助工程师分析叶片的受力情况。
通过计算叶片的应力和变形,工程师可以确定叶片的材料选择和厚度,以及叶片的结构形式。
这样可以提高叶片的强度和刚度,从而提高风力发电机组的效率和可靠性。
另外,塔架和基础的设计也需要考虑结构力学。
塔架需要承受来自风力的侧向力和扭矩,而基础需要承受整个风力发电机组的重量。
结构力学可以帮助工程师计算和预测塔架和基础的受力情况,确保它们的稳定性和安全性。
2. 流体力学的应用流体力学在风力发电设备设计中的应用主要涉及风力的传递和转化过程。
风力发电机组的核心部分是风轮,它通过叶片捕捉风能并将其转化为机械能。
流体力学可以帮助工程师分析和优化风轮的叶片形状和布局,以提高风能的转化效率。
通过流体力学的分析,工程师可以确定叶片的气动特性,如升力和阻力。
这些特性对于风轮的设计和性能至关重要。
工程师可以通过调整叶片的形状、倾斜角度和数量等参数,来优化风轮的气动特性,从而提高风力的利用率。
此外,流体力学还可以帮助工程师分析风力发电机组与周围环境的相互作用。
例如,当风力发电机组安装在海上时,海洋流体力学的知识可以帮助工程师预测风力发电机组在海浪和海流的作用下的受力情况,从而提高设备的稳定性和可靠性。
3. 振动力学的应用振动力学在风力发电设备设计中的应用主要涉及设备的振动特性和振动控制。
风力发电机组在运行过程中会受到风力的激励,从而产生振动。
基于无动力排风扇叶片曲面的逆向设计及关键技术研究
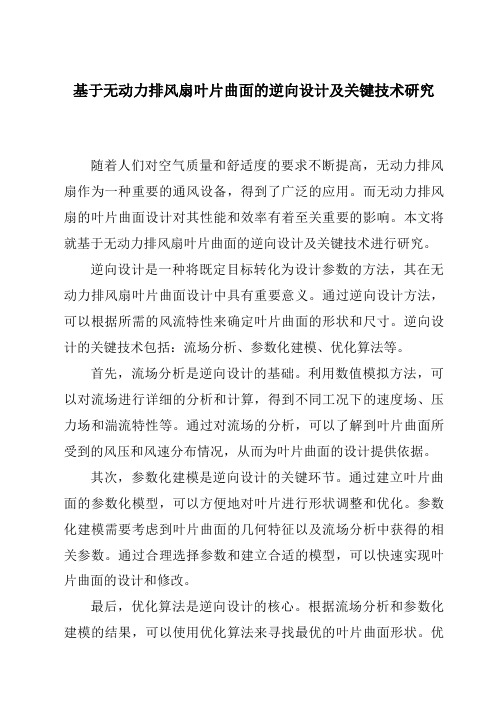
基于无动力排风扇叶片曲面的逆向设计及关键技术研究随着人们对空气质量和舒适度的要求不断提高,无动力排风扇作为一种重要的通风设备,得到了广泛的应用。
而无动力排风扇的叶片曲面设计对其性能和效率有着至关重要的影响。
本文将就基于无动力排风扇叶片曲面的逆向设计及关键技术进行研究。
逆向设计是一种将既定目标转化为设计参数的方法,其在无动力排风扇叶片曲面设计中具有重要意义。
通过逆向设计方法,可以根据所需的风流特性来确定叶片曲面的形状和尺寸。
逆向设计的关键技术包括:流场分析、参数化建模、优化算法等。
首先,流场分析是逆向设计的基础。
利用数值模拟方法,可以对流场进行详细的分析和计算,得到不同工况下的速度场、压力场和湍流特性等。
通过对流场的分析,可以了解到叶片曲面所受到的风压和风速分布情况,从而为叶片曲面的设计提供依据。
其次,参数化建模是逆向设计的关键环节。
通过建立叶片曲面的参数化模型,可以方便地对叶片进行形状调整和优化。
参数化建模需要考虑到叶片曲面的几何特征以及流场分析中获得的相关参数。
通过合理选择参数和建立合适的模型,可以快速实现叶片曲面的设计和修改。
最后,优化算法是逆向设计的核心。
根据流场分析和参数化建模的结果,可以使用优化算法来寻找最优的叶片曲面形状。
优化算法可以基于遗传算法、粒子群算法等,通过不断地调整参数和评估目标函数,寻找到最优的叶片曲面形状,从而提高无动力排风扇的性能和效率。
综上所述,基于无动力排风扇叶片曲面的逆向设计及关键技术研究是提高无动力排风扇性能和效率的重要手段。
通过流场分析、参数化建模和优化算法的综合应用,可以实现叶片曲面的精确设计和优化,进而提高无动力排风扇的风量和通风效果。
这对于改善室内空气质量、提高人们的舒适度具有重要意义。
基于偏微分方程的风力机叶片优化设计

基于偏微分方程的风力机叶片优化设计一、引言随着全球气候变化的加剧和对可再生能源需求的不断增长,风能已成为发电领域中备受青睐的一种清洁能源。
在风能利用的过程中,风力机叶片是最为关键的部件之一。
优化风力机叶片的设计对提高风力发电系统的效率、降低成本和增强可靠性等方面具有重要意义。
本文将基于偏微分方程的方法探讨风力机叶片优化设计的相关问题。
二、风力机叶片的结构和工作原理风力机叶片是由多个带有逐渐变细、逐渐扭曲和逐渐充实的气动剖面组成的。
在运行过程中,叶片通过受力转动,将风能转换为机械能并传递给发电机,最终产生电能。
因此,风力机叶片的性能将直接影响整个风力发电系统的性能。
三、偏微分方程的基本概念在叶片的优化设计过程中,偏微分方程技术被广泛应用。
偏微分方程是描述物理系统的一种方程形式,通常与时间和空间相关。
在数学上,偏微分方程可以用来求解连续介质的运动、电磁场、热传导、流体力学、波动等问题。
四、偏微分方程在叶片设计中的应用1. 流体力学模拟在风力机叶片的设计中,流体力学模拟是非常重要的一环。
基于Navier–Stokes方程的CFD模拟可以帮助设计师准确地掌握风力机叶片的气动特性。
CFD模拟可以考虑气流的不同速度、湍流、粘性以及叶片结构的影响等多种因素,以此来预测风力机叶片的性能。
2. 多物理场协作仿真除流体力学模拟之外,叶片的优化设计还需要考虑机械力学、热力学、材料力学等因素。
因此,必须进行多物理场协作仿真来实现整体叶片性能的优化设计。
通过将CFD、结构力学、热力学等多种物理场协同模拟,设计师可以综合考虑叶片的动态响应、材料的热膨胀以及叶片结构的强度等因素,得到最优设计方案。
五、结论偏微分方程技术已经成为研究风力机叶片的优化设计的重要工具。
流体力学模拟和多物理场协作仿真都是利用偏微分方程技术的重要应用。
经过对叶片结构、气动特性等多方面进行优化设计,将能够提高风力机的效率,降低成本,并延长整个风力发电系统的使用寿命,为全球环境保护和经济发展做出积极的贡献。
风机叶片检测的研究现状及进展

风机叶片检测的研究现状及进展摘要:叶片是风力单位的关键组成部分,在能量转换中发挥作用。
在风扇运行期间,必须确保叶片的安全和可靠性,以便有效地提高吸收的风力发电的转换效率,并对整个风力发电系统产生积极影响。
通过提高叶片性能,还可以保证风扇稳定运行。
但是,叶片的工作环境相对复杂,面临离心力、空气功率、热应力和弯曲应力,甚至雨雪冰侵蚀和闪电积聚破坏等现象。
在此基础上,我们必须重视风扇叶片的检测和分析,以确保准确快速地确定其疲劳程度,这是保持风扇安全运行、降低成本和提高风力利用率的有效途径。
关键词:风机叶片检测;研究现状;进展引言叶片是风力发电的关键组成部分之一。
在运行过程中可能受到强风、冲洗、空气氧化和潮湿空气腐蚀的影响。
可能会出现空气孔、裂纹、磨损和腐蚀等问题。
否则叶片可能断裂,严重威胁设备的安全运行。
因此,对风力发电机叶片进行状态检测和故障排除非常重要。
风扇叶片检测有助于避免潜在的叶片故障,减少意外丢失和停机。
降低叶片维护成本,直接影响整体稳定性和整体效率。
风力棒状态检测分为结构损伤检测和运行状态诊断,叶片结构损伤检测方法包括复制方法、电位法、显微镜直接观察和各种无损检测方法;叶片状态诊断包括监测风力发电机运行过程中产生的振动、冲击和噪声信号,用各种动态驱动器性能参数描述信号,提取故障信息,并将其用作诊断基础,以确定故障的类型、位置和原因。
与复印方法、电子定位方法、显微镜直接观察等其他传统试验方法相比,无损检测方法不需要停机,检测成本低,可以方便地在工程中使用。
1风机叶片损伤机理风机叶轮是风力发电机组中最重要的部件,造价较高,而叶片是其中的关键组成部分,长期处于复杂工作环境下,容易遇到静力风、气动力、重力和离心力等作用的影响,并形成挥舞、摆振、扭转等复杂运动,同时叶片内部也容易发生多个区域、程度不一的损伤。
在叶片上长期作用的荷载存在交变性与随机性等特点,从而导致叶片出现疲劳破坏。
此外,叶片使用中也面临沙粒冲刷、紫外线照射等影响,并存在大气氧化和腐蚀、海洋潮湿空气腐蚀等问题。
离心式风机叶轮曲面

离心式风机叶轮曲面
离心式风机的叶轮曲面是指其叶片的形状和曲线。
离心式风机的叶轮通常由一系列弯曲的叶片组成,这些叶片可以通过一定的设计来实现所需的风流控制和效率。
离心式风机的叶轮曲面有不同的设计形式,常见的包括:
1. 直流曲线(Forward-curved):叶片的曲线呈现向前凸出的形状,类似向前弯曲的弯刀。
这种设计适用于低风阻、低静压和大流量的应用,如通风系统。
2. 后流曲线(Backward-curved):叶片的曲线呈现向后凸出的形状,类似向后弯曲的弯刀。
这种设计通常用于高风阻、高静压和中等流量的应用,如工业风机。
3. 前后流曲线(Mixed-flow):叶片的曲线同时包含前流曲线和后流曲线的特点,类似于前两者的结合。
这种设计适用于中等风阻、中等静压和大流量的应用,如空调系统。
这些不同的叶轮曲线形式影响着离心式风机的性能、风量和压力特性。
在选择离心式风机时,需要根据具体的应用场景和要求,选择合适的叶轮曲线形式。
风力发电机组设计制造中的叶片优化与动态平衡控制
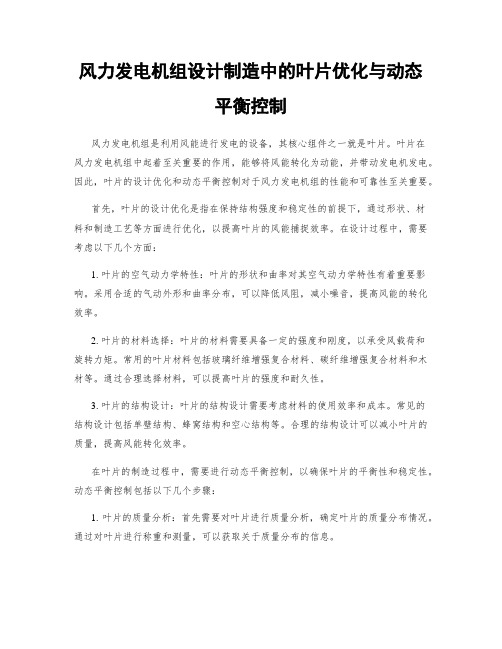
风力发电机组设计制造中的叶片优化与动态平衡控制风力发电机组是利用风能进行发电的设备,其核心组件之一就是叶片。
叶片在风力发电机组中起着至关重要的作用,能够将风能转化为动能,并带动发电机发电。
因此,叶片的设计优化和动态平衡控制对于风力发电机组的性能和可靠性至关重要。
首先,叶片的设计优化是指在保持结构强度和稳定性的前提下,通过形状、材料和制造工艺等方面进行优化,以提高叶片的风能捕捉效率。
在设计过程中,需要考虑以下几个方面:1. 叶片的空气动力学特性:叶片的形状和曲率对其空气动力学特性有着重要影响。
采用合适的气动外形和曲率分布,可以降低风阻,减小噪音,提高风能的转化效率。
2. 叶片的材料选择:叶片的材料需要具备一定的强度和刚度,以承受风载荷和旋转力矩。
常用的叶片材料包括玻璃纤维增强复合材料、碳纤维增强复合材料和木材等。
通过合理选择材料,可以提高叶片的强度和耐久性。
3. 叶片的结构设计:叶片的结构设计需要考虑材料的使用效率和成本。
常见的结构设计包括单壁结构、蜂窝结构和空心结构等。
合理的结构设计可以减小叶片的质量,提高风能转化效率。
在叶片的制造过程中,需要进行动态平衡控制,以确保叶片的平衡性和稳定性。
动态平衡控制包括以下几个步骤:1. 叶片的质量分析:首先需要对叶片进行质量分析,确定叶片的质量分布情况。
通过对叶片进行称重和测量,可以获取关于质量分布的信息。
2. 动平衡试验:在动平衡试验中,需要将叶片安装在平衡机上,并在旋转的条件下进行试验。
通过试验,可以检测叶片的不平衡情况。
3. 调整平衡:根据动平衡试验的结果,可以确定叶片不平衡的具体位置。
通过在不平衡位置上增加或减少质量,可以实现叶片的动平衡。
4. 动态平衡控制系统:动态平衡控制系统可以实时监测叶片的不平衡情况,并通过自动调整质量分布来实现叶片的动平衡。
该系统可以提高叶片的稳定性和寿命。
总的来说,在风力发电机组设计制造中,叶片的设计优化和动态平衡控制是影响风力发电机组性能和可靠性的关键因素。
叶片的曲面加工
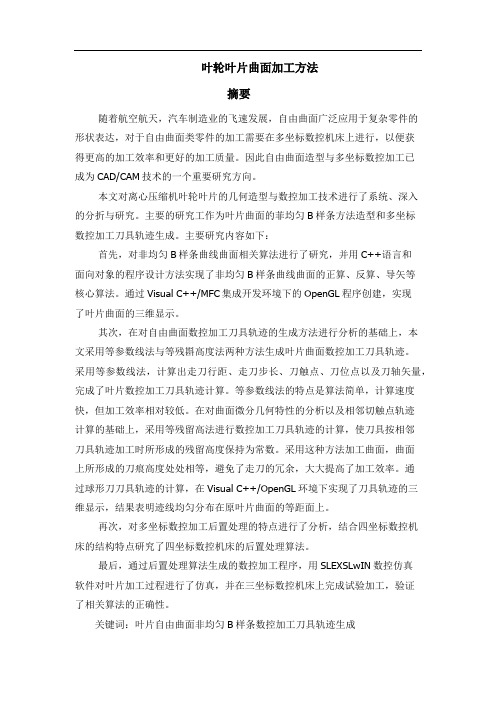
随着航空航天,汽车制造业的飞速发展,自由曲面广泛应用于复杂零件的 形状表达,对于自由曲面类零件的加工需要在多坐标数控机床上进行,以便获 得更高的加工效率和更好的加工质量。因此自由曲面造型与多坐标数控加工已 成为 CAD/CAM 技术的一个重要研究方向。 本文对离心压缩机叶轮叶片的几何造型与数控加工技术进行了系统、深入 的分折与研究。主要的研究工作为叶片曲面的菲均匀 B 样条方法造型和多坐标 数控加工刀具轨迹生成。主要研究内容如下: 首先,对非均匀 B 样条曲线曲面相关算法进行了研究,并用 C++语言和 面向对象的程序设计方法实现了非均匀 B 样条曲线曲面的正算、反算、导矢等 核心算法。通过 Visual C++/MFC 集成开发环境下的 OpenGL 程序创建,实现 了叶片曲面的三维显示。 其次,在对自由曲面数控加工刀具轨迹的生成方法进行分析的基础上,本 文采用等参数线法与等残斟高度法两种方法生成叶片曲面数控加工刀具轨迹。 采用等参数线法,计算出走刀行距、走刀步长、刀触点、刀位点以及刀轴矢量, 完成了叶片数控加工刀具轨迹计算。等参数线法的特点是算法简单,计算速度 快,但加工效率相对较低。在对曲面微分几何特性的分析以及相邻切触点轨迹 计算的基础上,采用等残留高法进行数控加工刀具轨迹的计算,使刀具按相邻 刀具轨迹加工时所形成的残留高度保持为常数。采用这种方法加工曲面,曲面 上所形成的刀痕高度处处相等,避免了走刀的冗余,大大提高了加工效率。通 过球形刀刀具轨迹的计算,在 Visual C++/OpenGL 环境下实现了刀具轨迹的三 维显示,结果表明迹线均匀分布在原叶片曲面的等距面上。 再次,对多坐标数控加工后置处理的特点进行了分析,结合四坐标数控机 床的结构特点研究了四坐标数控机床的后置处理算法。 最后,通过后置处理算法生成的数控加工程序,用 SLEXSLwIN 数控仿真 软件对叶片加工过程进行了仿真,并在三坐标数控机床上完成试验加工,验证 了相关算法的正确性。 关键词:叶片自由曲面非均匀 B 样条数控加工刀具轨迹生成
风机叶片的几何展开和程序化设计
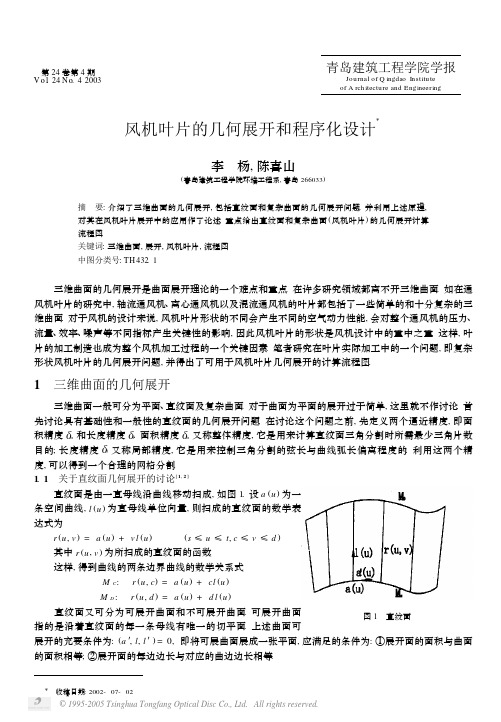
第24卷第4期V o l .24N o .42003青岛建筑工程学院学报Journal of Q ingdao Instituteof A rch itecture and Engineering风机叶片的几何展开和程序化设计Ξ李 杨,陈喜山(青岛建筑工程学院环境工程系,青岛266033)摘 要:介绍了三维曲面的几何展开,包括直纹面和复杂曲面的几何展开问题.并利用上述原理,对其在风机叶片展开中的应用作了论述.重点给出直纹面和复杂曲面(风机叶片)的几何展开计算流程图.关键词:三维曲面,展开,风机叶片,流程图中图分类号:TH 432.1三维曲面的几何展开是曲面展开理论的一个难点和重点.在许多研究领域都离不开三维曲面.如在通风机叶片的研究中,轴流通风机、离心通风机以及混流通风机的叶片都包括了一些简单的和十分复杂的三维曲面.对于风机的设计来说,风机叶片形状的不同会产生不同的空气动力性能,会对整个通风机的压力、流量、效率、噪声等不同指标产生关键性的影响,因此风机叶片的形状是风机设计中的重中之重.这样,叶片的加工制造也成为整个风机加工过程的一个关键因素.笔者研究在叶片实际加工中的一个问题,即复杂形状风机叶片的几何展开问题,并得出了可用于风机叶片几何展开的计算流程图.1 三维曲面的几何展开三维曲面一般可分为平面、直纹面及复杂曲面.对于曲面为平面的展开过于简单,这里就不作讨论.首先讨论具有基础性和一般性的直纹面的几何展开问题.在讨论这个问题之前,先定义两个逼近精度,即面积精度∆a 和长度精度∆l .面积精度∆a 又称整体精度,它是用来计算直纹面三角分割时所需最少三角片数目的;长度精度∆l 又称局部精度,它是用来控制三角分割的弦长与曲线弧长偏离程度的.利用这两个精度,可以得到一个合理的网格分割.1.1 关于直纹面几何展开的讨论[1,2]图1 直纹面直纹面是由一直母线沿曲线移动扫成,如图1.设a (u )为一条空间曲线,l (u )为直母线单位向量,则扫成的直纹面的数学表达式为r (u ,v )=a (u )+v l (u ) (s ≤u ≤t ,c ≤v ≤d ) 其中r (u ,v )为所扫成的直纹面的函数.这样,得到曲线的两条边界曲线的数学关系式M C : r (u ,c )=a (u )+cl (u )M D : r (u ,d )=a (u )+d l (u ) 直纹面又可分为可展开曲面和不可展开曲面.可展开曲面指的是沿着直纹面的每一条母线有唯一的切平面.上述曲面可展开的充要条件为:(a ′,l ,l ′)=0,即将可展曲面展成一张平面,应满足的条件为:①展开面的面积与曲面的面积相等;②展开面的每边边长与对应的曲边边长相等.Ξ收稿日期:2002-07-02而另一种直纹面——不可展开曲面,它是工程实际应用中常遇到的,它展开后的平面与原曲面相比,不论从面积上还是各边的对应边长上都会有差别.这时只能用逼近法来求得展开,即利用前已述及的两个逼近精度:∆a 、∆l .对于不可展直纹面来说要展开成一平面所要满足的条件为:①展开面的面积与曲面的面积相对误差小于给定的面积精度∆a ;②展开面的每边边长与对应的曲面边长相对误差要小于给定的长度精度∆l .图2 直纹面的三角剖分不可展面展开时,要先将曲面作三角剖分,然后把所有小三角形平面展开在同一平面上,如图2所示.首先对该直纹面进行等参数分割,取一系列的等参数值u i =s +(t -s )i n (i =0,1,2,…,n ),在两条边界曲线上可分别得到一系列的等参数点,P c (u i )=r (u i ,c ),Pd (u i )=r (u i ,d ).图2中顺序地连接相邻分割点,便可形成不可展直纹面的三角平面逼近.接下来的工作是靠∆a 和∆l 的控制来确定三角网格分割所需要的平面数目.要分两步走.(1)考虑从整体上来逼近面积精度∆a ,设曲面展开面积为S 2D ,曲面实际面积为S 3D ,用S 2D 来从整体上逼近S 3D ,两者的相对误差设为Εa ,那么Εa = (S 3D -S 2D ) S 3D ≤∆a (1)或S 2D ≥ 1-∆a S 3D (2)而S 2D =∑n -1i =0(S ∃i +S ∃i ′)(3)其中 S ∃i 和S ∃i ′为如图2所示的小三角平面的面积.将(3)式代入式(2)得∑n -1i =0(S ∃i +S ∃i ′)≥ 1-∆a S 3D 图3 用弦长逼近弧长直纹面边界曲线的分割点数n 用迭代计算来确定,迭代初值设为n 0,可取作n 0=trunc[m ax (L (k ) l (k ))],k =c ,d其中 L (k )=∞t s r (u ,k )d u 为曲线r (u ,k )的弧长;l (k )=‖r (s ,k )r (t ,k )‖ 为曲线r (u ,k )的弦长;trunc 表示对小数取整.把n 0代入(2)式,若不成立,则令n 1=n 0+1,分割点数增加,分割细化,继续迭代,直至满足(2)式为止.图4 三角剖分加密在这步计算中,网格的等参数分割的优点是计算简单、快速;缺点是它没有从曲面的实际情况出发,也就是说这种分割方法没有反映出曲面的特点.一个比较合理的网格分割,应该是在同一精度条件下,用最少的三角平面去逼近曲面.这样就要考虑到曲面的几何特点,在曲率大的区域,网格划分比较细密,而曲率小的区域网格划分比较稀疏.这样就要利用下一步的方法来解决上述问题.(2)修正展开面积的边界逼近精度.就直纹面而言,可根据边界曲线的曲率,作为修正网格划分的依据.如图3所示,当用弦长逼近弧长时,这段弧的曲率反映了弧的弯曲程度.曲率越大,弧的弯曲程度就越大,弦长和弧长的差别就越大.因此,边界局部误差Ε(k )l i 可定义为:79第4期李杨等:风机叶片的几何展开和程序化设计图5 小三角平面的展开Ε(k )l i = L (k )i -l (k )i L (k )i ≤∆l(4)或l (k )i ≥ 1-∆l L (k )i (5)这里 l (k )i =‖p k (u i +1)p k (u i )‖,为p k (u i +1)p k (u i )两点间的弦长;L (k )i =∞u i +1u i r (u ,k )d u ,为p k (u i +1)p k (u i )两点间的弧长;i =0,1,2,3,…n -1, k =c ,d图6 直纹面几何展开计算流程图按(4)式逐段检查Ε(k )l i ,当Εl i =m ax {Ε(k )l i }超过∆l 的区间[u i ,u i +1]时,中间就再加密一点p k (u i +u i +12).由图2的曲面经过局部精度检查和插值后的结果可知在曲率大的地方网格密,反之则比较稀,如图4所示.将各三角片依次绕前一个三角片旋转,使所有三角片都落在同一平面上.最后,用曲线逼近由三角平面所确定的平面形状的外围点,即可得到直纹面的最终展开形状,如图5所示.直纹面有几种特例,如锥面的一条边界曲线退化为一点;柱面l (u )=常数;切线面l (u )=a (u ),这时算法相应作出一些修正.将上述步骤归纳为逻辑性较强的框图形式,即得直纹面几何展开程序化计算流程图(如图6所示).1.2 复杂曲面的展开讨论复杂曲面属于一类不可展开曲面.对于它分“三步走”来将其展成平面.(1)分割复杂曲面为一系列条状区域 利用逼近精度的办法来把一张曲面分割成若干条,所需条状分割的数目n 应该满足长度相对误差Εl ≤∆l ,这里∆l 仍为前已述及的长度逼近精度(或局部精度).设复杂曲面为s (u ,v )(0≤u ≤1,0≤v ≤1),其中的两条边界曲面为H (0):s (u ,0)和H (1):s (u ,1),假设分割方向取u 向,长度相对误差Εl 定义为Εl =m ax{Ε(k )l }≤∆l , k =0,1(6)其中 Ε(k )l = L(k )s -∑n -1i =0C (k )i L (k )s(7)L (k )s =∞10s (u i ,k )d u 为曲线H (k )的弧长;C (k )s =‖s (u i +1,k )s (u i ,k )‖为直线段s (u i +1,k )s (u i ,k )的长度.下面利用上述各式进行分析计算.根据(6)式、(7)式,可计算出所需条状区域的数目n .①设定一个初值n 0,由此计算出∑n -1i =0C (k )i ,代入(6)式、(7)式;②如果Εl ≤∆l ,则n =n 0,如果Εl >∆l ,则取n 1=n 0+1;③重复上述计算过程,直至求出n 满足Εl ≤∆l 为止.89青岛建筑工程学院学报第24卷其中初值n 0用n 0=trunc [m ax (C (k )L (k )s)]来确定,这里C (k )=s (0,k )s (1,k ),为曲线H (k )的弦长.(2)用直纹面去逼近条状区域 对于每个条状区域可用一直纹面r i (t ,w )(u i )Φt Φu i +1,0Φw Φ1)去逼近.直纹面的两条边界曲线分别为Гi :r i (u i ,w )=s (u i ,w ) Гi +1:r i (u i +1,v )=s (u i +1,v ) u i =i n,i =0,1,2,…n -1,u n =1,0≤w ,v ≤1然后展开每一个直纹面r i (t ,w ).为了便于计算,这里假设所有的直纹面有相同的三角剖分,取三角平面数目m =m ax {m i },i =0,1,2,…n -1,其中m i 为第i 个直纹面的网格分割数.(3)把直纹面展开面转到同一平面上,方法同前.将上述步骤归纳为逻辑性较强的框图形式,即得复杂曲面几何展开程序化计算流程图(如图7所示).图7 复杂曲面几何展开计算流程图2 风机叶片曲面展开成平面对于离心风机、轴流风机以及混流风机叶片,不论是简单的三维曲面还是复杂的三维曲面都可以利用上述方法加以展开.对于简单曲面的风机叶片,虽然属于不可展曲面,但它仍属于基本的直纹面,完全可以采用前已述及的直纹面的逼近式展开法[3],即利用两个逼近精度(面积精度∆a 和长度精度∆l ),从整体上和局部来控制逼近效果,最后展成平面.对于其它复杂形状的风机叶片来说,完全可以利用关于复杂曲面展开问题的基本思想,利用从复杂曲面化为条状区域再逼近为直纹面的思路,在其中再利用长度精度∆l ,使长度相对误差Εl ≤∆l 来确定条状分割的数目实现平面展开.具体操作与复杂曲面展成平面相似.因此,完全可用复杂曲面几何展开计算流程图(如图7所示)来完成风机叶片的展开.这里就不再赘述.这里需要注意的一点是对于复杂曲面的风机叶片来说,由于其展开图形是不封闭的,即有缝隙和重叠.并且由于所取的展开方向不同(如沿参数U 向、V 向等),同一风机叶片的展开面不是唯一的,可能会有多种不同的解.而对于由直纹面所构筑的风机叶片,它的展开结果是唯一的.这是因为在展开计算中,将钣金件的几何外形作为展开计算的唯一依据,而忽略了材料特性及成形方式的影响.由图7可知,复杂曲面几何展开计算流程图的最后一步,接直纹面几何展开计算流程图,即可完成该曲面的几何展开.3 结束语笔者介绍的三维曲面的几何展开问题,是从基本曲面(直纹面)的展开到复杂曲面的几何展开的方法,最后到风机叶片曲面的展开.从简单到复杂,从理论到实际.其中突出了直纹面和复杂曲面几何展开的计算流程图及它对风机叶片展开问题的解决.这两个计算流程图的意义是重大的,在编制关于风机叶片几何展开的计算机软件上将发挥极其重要的作用,为下一步风机叶片几何展开的大规模程序化设计起到一个铺路石的作用,同时,在整个风机加工过程中也起着核心作用.利用前述的方式与方法在通风机叶片形状设计与加工中都起到一定的作用.在叶片的实际加工中,该展开法提供了一个简便易行的近似而实用的计算方法,在实际工作中可以减少确定下料外形的试验次数,降低成本,缩短生产周期.同时,避免了制造过多的模具,进一步降低了加工费用.另外,减少了设计中所要考虑的诸多因素,简化了设计.99第4期李杨等:风机叶片的几何展开和程序化设计001青岛建筑工程学院学报第24卷参 考 文 献[1] 席平.三维曲面的几何展开.计算机学报,1997(4):3152322[2] 李绍珍等.工程曲面.济南:山东大学出版社,1997[3] 张公升.轴流风机叶片展开下料及型线的CAD技术.风机技术,1996(3):23225D evelop m en t and Formal D esign of Fan BladeL i Yang and Chen X i2shan(Q ingdao In stitu te of A rch itectu re and Engineering,Q ingdao266033)Abstract:In th is p ap er,the developm en t of3D su rfaces,including the developm en t of ru led and non2 ru ledcom p lex su rfaces is p resen ted;T he developm en t of b lades is stated by the p rinci p les and the flow charts of the developm en t of ru led and non2ru ledcom p lex su rfaces are also p resen ted.Key words:3D su rface,developm en t,fan b lade,flow charts作者简介:李杨,男,28岁,硕士研究生。
- 1、下载文档前请自行甄别文档内容的完整性,平台不提供额外的编辑、内容补充、找答案等附加服务。
- 2、"仅部分预览"的文档,不可在线预览部分如存在完整性等问题,可反馈申请退款(可完整预览的文档不适用该条件!)。
- 3、如文档侵犯您的权益,请联系客服反馈,我们会尽快为您处理(人工客服工作时间:9:00-18:30)。
2000年 6月第30卷 第3期 山 东 工 业 大 学 学 报JOURNAL OF SHANDONG UN IVERSIT Y OF TECHNOLOG Y V o l.30 N o.3 June 2000工程曲面理论在风机叶片设计中的应用研究苑国强 王 岩①(250061 济南 山东工业大学机械工程学院)摘 要 针对工程曲面在混(斜)流式风机叶片中的应用问题,对其曲面进行了理论分析和数学建模,开发了叶片曲面CAD软件,该软件能精确快捷地设计、绘制出曲面的各种图样,从而在根本上解决了风机叶片在生产工艺中的难题,实现了复杂曲面的CAD1关键词 扭叶片;混流式鼓风机;计算机辅助设计;构形(数学)中图分类号 TH1220 引言按叶片的制造工艺,首先将叶片曲面展开,尔后将剪切好的板材再冲压成理想的空间形状,这是叶片制造的关键技术,也是确保风机性能的重要一环[1~5]1根据混(斜)流式风机的性能特点,其叶片截面以机翼型或圆弧形为好1从气动设计的要求出发,在叶轮中为避免流道中从叶顶到叶根产生涡流,减少能量损失,以保证沿叶片半径方向具有相同的压力,只有把叶片设计成扭变曲面的形状,才能符合三元流理论的要求1根据工程曲面理论,该叶片曲面属变截面扭变曲面,是不可展曲面,这给风机叶片的制造带来很大困难1从目前查阅的国内资料看,对该种曲面叶片还没有系统的研究,叶片的展开、下料也无完整、合理、准确的方法,因而使该类型风机叶片难以获得理论设计形状1本文以风机性能及气动设计要求为依据,对该类风机叶片进行了数学建模,提出了叶片展开及压模板的算法11 数学建模及算法1.1 叶片的数学模型扭曲变截面叶片曲面在不同高度位置上两对应点之间不存在线性关系1各截面曲率半径的大小是设计时由气动实验数据决定的1这样,就不能用一个确切的数学表达式进行描述1故运用了分解重构的原理,即将叶片分解为若干个截面叶型,建立起不同截面安装角、 收稿日期:2000203224 ①在济南联合大学机电系工作1作者简介 苑国强,男,1964年生,1985年7月,1997年10月分别获学士、硕士学位1主要研究方向:工程图学等1王 岩,女,实验师11989年毕业于山东矿业学院1曾参与“箱体类零件CA PP专家系统开发研究”、“地方高校工科(机电)专业实践教学模式的改革探讨”等工作1研究方向:机械专业实验的研究与开发1第3期苑国强等:工程曲面理论在风机叶片设计中的应用研究259弦长随叶片高度变化规律的表达式,这样就可建立整个叶片的数学模型1根椐风机性能及气动设计要求,叶片被焊接在一个圆锥形的轮毂上1因此,叶片样板型线应在相应锥面上弯曲成型1由于叶片是扭曲的,故叶片与轮毂的交线以及被圆锥截面截切后得到的型线均为空间曲线1图1 坐标系的设置F ig .1 T he po siti on of coo rdinate system 图1所示为数学建模而设立的坐标系,通过一系列的推导和变换,其平面圆弧型线上A (x 3,y 3)点的参数方程为:x 3=-R co s Ηco s <+R sin <sin Η+x 0y 3=-R sin <co s Η-R co s <sin Η+y0式中:R 为圆弧半径,Η,<为旋转角,(x 0,y 0)为坐标系X O Y 与X 1O 1Y 1的坐标差1因截面型线是由锥截面截切后得到的,故将圆弧上各点绕Y 轴旋转一角度p ,使截切圆锥的一条素线与展开后的对应素线重合,则有:[x y z 1]=[x 3y 3z 31]TT 为绕Y 轴逆时针旋转的矩阵1T =co s p 0-sin p00100sin p 0co s p00001图2 截切圆锥位置及关系F ig .2 T he po siti on and relater of cu tter cone 如图2所示;设该截切面圆锥的宽度为H ,端部两圆半径分别为r 1,r 2,偏心量为e ,则有:z 3=(r 1+r 22)r 1H r 2-r 1+(H 2-e )r 1H r 2-r 1+H 2绕Y 轴逆时针旋转角度p =Π 2-arctg (H(r 2-r 1))用参数形式表示为:x =x 3co s p +z 3sin py =y 3z =-x 3sin p +z 3co s p若将截切平面还原为截切圆锥,则截面叶型曲面上任意点A 的位置变为A ′,如图3所示,即A 点的y 值为A ′所在位置的弧度值1设A ′所在圆锥部位的半径为r ,则2Πr 360=y Α,Α=180y Πr260山 东 工 业 大 学 学 报2000年图3 叶型曲线上点的坐标变换F ig .3 T he coo rdinate conversi on of po in t on the secti on shape of fanA ′点坐标为: x ′=xy ′=r sin (y r )z ′=r co s (y r )其中:r =z 3+b =z 3x ′(r 2-z 3)H 2+e上述为叶片曲面上任意点的数学描述,计算得到若干个离散点,然后用B 样条曲面拟合方法,即可构造出叶片曲面11.2 叶片展开图的计算方法为得到准确的叶片展开图边界,首先准确求出叶片与轮毂的交线,其次借助于所描述的叶片型线,将曲面剖分成若干个小矩形,然后再采用三角型法求其展开图,即按给定的的步长,将相邻两曲线上的各点分别图4 叶片展开图原理F ig .4 T he develop ingp rinci p le of fan s 存贮在两个一维数组中,如图4所示,以四点为一循环单位调用数组中各点的坐标值,用空间两点的距离公式:d =(x 1-x 2)2+(y 1-y 2)2+(z 1-z 2)2可求出d 1,d 2,d 3,d 4,d 5的距离1固定A D 线的位置,分别以A 、D 两点为圆心,以d 2,d 3为半径,可得交点C 的展开位置1同样利用d 4,d 5可求得B 点的展开位置1把该步骤作为一个循环体进行循环,可得整个叶面曲面的展开图11.3 平面样板曲线的生成考虑到多品种、小批量生产的需要,开发的CAD 系统能够生成平面样板曲线,构造一种简易的压模板1若用一组平行的平面截切叶片,便可以得到一组平面曲线1任一平面与叶片曲面求交的方法如下:将叶片曲面表示为p (u ,w )=[u 3u 2u 1]・[S ]・[w 3w 2w 1]T 平面表示为ax +by +cz +d =0则交线为[u 3u 2u 1u 1](a [s ]x +b [s ]y +c [s ]z )[w 3w 2w 1w 1]T +d =0其中,[S ]x ,[S ]y ,[S ]z 为[S ]的坐标分量矩阵1给定一个特定的参数值u 3,便可得到一个关于w 的三次方程,反之,给定w 3,可得到u 的三次方程1方程在参数域(0,1)上的根,便是平面与叶片的交点1连续给出一系列参数值,求得一系列的交点,便得到一条样板曲线1给出一组平行平面,则得到一组样板曲线1由这一组样板曲线(可多层加密),即可构造为一个简易可行的压模板1第3期苑国强等:工程曲面理论在风机叶片设计中的应用研究2612 理论应用使用先进的VB 语言编程,以W indow s 98为平台,以操作方便、简捷,用交互式方式设计及绘制图样为宗旨,用以上算法编制了三维扭变曲面的CAD 软件,总体框图如图51(1)用该算法开发的CAD 软件绘出的叶片展开图(如图6)形状准确,叶片与轮毂的交线求解精度高,吻合性好,与以前的手工展开下料相比较,既提高了叶片的焊接精度,又节省了焊条1同时减少了钢板的浪费1(2)用该软件绘出的简易压模型线图,为下一步叶片的模具设计及制造提供了准确的截面型线(空间曲线),从而提高了叶片的扭曲精度,使叶片与风筒的间隙较小且均匀1特别适用于品种多、批量小的风机厂1图5 总体框图F ig .5 T he fram e of system 图6 叶片展开图F ig .6 T he develop of fan3 结论(1)混流式风机叶片的空间形状一般由若干截面图表达,这些截面图是由圆锥面截得,绘制成二维图形1本文即利用这些二维截面图转换到三维圆锥面上,得到叶片的三维空间形状1因此,本文虽然使用规则截面形状进行的求导,但由气动性能得到的不规则截面形状,也可利用相同原理得到叶片的空间形状1(2)本文所涉及的叶片为扭曲变截面的不可展曲面,为了获得叶片较精确的展开图,将相邻两叶型曲线间的四边形为微型基本单元,采用三角形逼近求得其展开图,因此叶型截面越密,得到的展开图就越精确1(3)利用重新构造的叶片空间曲面与一平面相交得到的压模型线图,因此,适应范围也较广泛1262山 东 工 业 大 学 学 报2000年参 考 文 献1 李绍珍,范波涛.共轭曲面接触线的生成与回转曲面轮廓线方程式的建立.山东工业大学学报,1997,27(1):55~582 张公升.引风机叶轮叶片的CAD技术.山东工业大学学报,1997,27(3):218~2213 范波涛,李绍珍,戴邦国.离心式风机叶片设计中的CAD软件技术,山东工业大学学报,1995,25(4): 377~3834 左 丽.子午加速风机叶片构型分析及其CAD.流体机械,1994,8:65 李绍珍,张爱平1叶轮叶片结构设计中交线的形成及算法1山东工业大学学报,1999,29(4):337ON THE APPL I CAT I ON OF ENGINEER ING SURFACETHEORY IN FAN B LAD ES D ESIGNY uan Guoqiang W ang Y an(Co ll.of M ech.Eng.,Shandong U n iv.of T ech.,J inan250061)ABSTRACT In the app licati on of engineering su rface in slan t flow fan b lades design, T he theo retical analysis and a m athem atical m odel fo r design ing fan b lade have been estab lished.T he CAD softw are of the su rface of b lades are also develop ed.It is easier and faster to design and draw all so rts of draw ings accu rately w ith the develop ed softw are. T herefo re,the difficu lties in design ing and m anufactu ring the fan b lades are overcom e and the CAD fo r com p licated su rface is realized.KEY WORD S Tw isted b lades;M ixed flow b low ers;Com p u ter aided design; Configu rati on s(m athem atics)。