轮胎的等压变温硫化工艺
轮胎硫化压力

轮胎硫化压力一、背景介绍轮胎硫化是指将橡胶制品在高温和高压下进行加热处理,使其产生交联反应,从而形成具有强度和弹性的物质。
而轮胎硫化则是指将橡胶轮胎进行硫化处理,以提高其耐磨性、耐老化性和抗裂性等性能。
二、硫化过程中的压力在轮胎硫化过程中,压力是一个非常重要的参数。
一方面,适当的压力可以促进橡胶材料之间的交联反应,从而提高轮胎的强度和耐久性;另一方面,过高或过低的压力则会影响硫化效果,并可能导致轮胎内部出现气泡或缺陷等问题。
三、硫化压力的测量方法为了保证轮胎硫化过程中的压力符合要求,必须对其进行实时监测。
目前常用的方法有以下几种:1. 基于传感器的测量方法:通过在模具上安装压力传感器来实时监测模具内部的压力变化。
2. 基于液位计的测量方法:在模具中加入一定量的液体,通过监测液位变化来计算出压力大小。
3. 基于气压计的测量方法:在模具中加入一定量的气体,通过监测气压变化来计算出压力大小。
四、硫化压力的控制方法为了保证轮胎硫化过程中的压力稳定在合适范围内,必须采取相应的控制措施。
常用的方法有以下几种:1. 控制硫化温度:适当提高硫化温度可以促进橡胶材料之间的交联反应,从而提高轮胎硫化效果;但是过高的温度则会导致轮胎内部出现气泡或缺陷等问题。
2. 调整硫化时间:适当延长硫化时间可以保证橡胶材料之间充分反应,从而提高轮胎硫化效果;但是过长的时间则会影响生产效率和产品质量。
3. 调整模具结构:合理设计模具结构可以保证轮胎内部受到均匀的压力作用,从而提高硫化效果;但是不合理的模具结构则会导致轮胎内部出现不均匀的硫化情况。
4. 优化硫化工艺:通过对硫化工艺进行优化,如调整硫化温度、时间、压力等参数,可以提高轮胎的硫化效果,并保证产品质量和生产效率的平衡。
五、结论轮胎硫化压力是影响轮胎硫化效果和产品质量的重要参数之一。
为了保证轮胎硫化过程中的压力稳定在合适范围内,必须采取相应的测量和控制措施,并逐步优化硫化工艺,以提高产品质量和生产效率。
轮胎-硫化基础知识分析

硫化基础知识
6、胎里漏线与胎体帘线弯曲 (1)机头宽度与帘线假定伸张值选取不合理 (2)胎胚周长大小选取不合理,周长小,伸张大,造成 胎里漏线,反之出现帘线弯曲。 (3)成型机传递环和机头扇形块出现故障可以造成胎圈 定位出现偏差 (4)成型时局部拉伸,造成尺寸变小;部件接头脱开。 (5)带束层偏歪 (6)硫化定型压力过大、时间过长,造成胎体帘线发生 弯曲,胎体反包高度降低,硫化后产生帘线弯曲。 (8)压辊压力过大 (9)硫化过程中,硫化胶囊渗漏,导致胶囊内热水渗到 胎里,压迫内衬层胶料内渗。 (10)内衬层厚度偏薄造成胎里漏线
硫化基础知识
第二讲:硫化工艺要点及注意事项
1、胎坯检查: (1)胎坯倒放:标识线在上侧。 (2)胎坯要放正:减少变形。 ( 3 )胎坯修整:胎圈和子口处均匀扎眼,不得扎透,为 排气和进一步整修胎坯。 2、吊胎坯:启模前3—5分钟,主要为恢复胎胚的形状, 如时间过长,则胎坯部件移位、变形过大。 3、硫化记录确认: (1) 异常硫化条件的轮胎要单独存放 ( 2 )按要求正常对硫化工艺参数记录,确保记录真是可 靠、可追溯。
硫化基础知识
5、气密层气泡、脱层 (1)成型中超定型压力低或组合压辊压力小、组合滚压 各段压力及轨迹设置有问题; (2)半成品部件不粘、喷霜; (3)垫胶定位偏歪,胎体与带束层之间产生孔隙 (4)内衬层胶料含水过多,硫化时形成气泡。 (5)内衬层压延时贴合不实,层间存在气泡。 (6) 成型时有水或胶浆未干。 (7) 胎坯气泡未按标准修理。 (8)胶囊砂眼造成轻微漏水、汽。
T90=ML+(MH-ML)×90%
硫化基础知识
硫化条件的选取和确定
一般来讲,测定出正硫化时间后,并不等于找到了具体产品的最 适宜硫化条件,还必须考虑以下因素: 产品的厚度、胶料的导热系数、制品材料中其它材料对导热的影响、 模型尺寸、模型材料、产品具体形状、硫化介质(油、蒸汽、水、 气、射线) 硫化三要素:时间、温度、压力 1、硫化压力 (1)施加硫化压力的目的:通过水胎或胶囊传递热量,达到内外硫 化的目的;使胶料易于流动和充满模腔;提高胶料的致密性;提 高硫化橡胶的物理机械性能;提高胶料与骨架材料的粘合性能。 但不是越大越好,还应考虑生产成本和设备的承受能力。 (2)硫化压力的选取:随胶料配方、可塑性、产品结构不同而不同, 在工艺上遵循:塑性大压力小,产品厚、层数多、结构复杂压力 大。 2、硫化时间:交联反应完成的时间;与温度有相应的关系。
载重子午线轮胎氮气硫化工艺

力 的高 纯氮气增 压 , 以达到 高温高 压 的硫 化条件 。 近 年来 , 汽/ 气 介 质硫 化 方 式 发 展很 快 , 蒸 氮
定 。生产 轮胎 的质量较 好 , 观合格 率较 高 , 外 不足
的是 蒸 汽耗 量 大 、 能耗 高 , 由于硫化 温 度低 , 且 硫 化 时间 长 , 生产效 率较 低 。
同时 , 硫化 工序是 轮胎制 造过程 中能 耗最大 、 投资
数额很 大 的一个 工 序 , 因此 对 新 型硫 化 工 艺进 行
目前在 美 国和 E本等 主要 轮胎生 产 国新建 项 目已 t 基 本采 用这种硫 化方 式 。 与过热水 硫化 工 艺相 比 , 气 硫化 工 艺 具 有 氮 下述优 点 。
第 2 期
朱 军 超 等 . 重 子 午 线 轮 胎 氮 气 硫 化 工 艺 载
( ) 化 周 期 缩 短 近 1 , 化 机 的利 用 率 1硫 0 硫
肩 部位胶 料较 厚 , 造成 局部压 力不 足 , 易产生钢 容
丝 带束层 端点 松散 , 而 影 响 轮胎 的 速度 和 耐久 从 性 能 。 由于 内压低 , 还会造 成外 观合格率 下降 。 这 两种硫 化工艺 分别 为高压 低温和 低压高 温 工艺 , 各有优 缺点 。
2 氮 气 硫 化 工 艺 介 绍
提高 8 , 降低设 备投 资 。 () 2 降低 轮胎成本 。 () 3 变水~ 汽一 蒸 过热 水 两 次 换 热 过 程 为水一 蒸
硫化工艺对成品轮胎性能的影响

硫化工艺对成品轮胎性能的影响发布时间:2021-08-09T15:05:02.750Z 来源:《探索科学》2021年7月13期作者:贾肖阳邓龙齐林连刚邓龙[导读] 目前,我国的综合国力的发展迅速,硫化是轮胎生产中的重要环节之一,需要消耗大量的能量,约占轮胎生产总能耗的60%。
为了提高轮胎生产效率,加大产出,需要对硫化工艺进行优化。
全钢载重子午线轮胎的胎圈、胎肩等部件容易出现硫化程度不均匀,这些关键部件出现欠硫或过硫,将严重影响轮胎的使用性能,同时各部件的不同硫化程度也将在一定程度上影响轮胎的使用性能。
八亿橡胶有限责任公司贾肖阳邓龙齐林连刚邓龙山东枣庄 277000摘要:目前,我国的综合国力的发展迅速,硫化是轮胎生产中的重要环节之一,需要消耗大量的能量,约占轮胎生产总能耗的60%。
为了提高轮胎生产效率,加大产出,需要对硫化工艺进行优化。
全钢载重子午线轮胎的胎圈、胎肩等部件容易出现硫化程度不均匀,这些关键部件出现欠硫或过硫,将严重影响轮胎的使用性能,同时各部件的不同硫化程度也将在一定程度上影响轮胎的使用性能。
关键词:硫化工艺;成品轮胎性能;影响引言随着工业的发展,能源的消耗越来越快,这是地球难以承受的负担。
在政策的积极响应下,更多的工厂创新技术,生产低耗能产品,以降低能源的使用,保障自然环境的可持续性。
在汽车领域中,由于汽车长时间的行驶,对轮胎的损坏更高,所以轮胎的质量需要达到更高的水平,如耐磨损性、高耐热性、稳定性等。
其中轮胎硫化过程是轮胎生产中最重要的一步,轮胎的质量取决于硫化程度的高低。
但硫化耗能也是最高,并存在严重的过硫问题,所以怎样优化配方、改善工业硫化是一项重要的研究课题,亟待解决。
1硫化温度分布为对比两种硫化工艺下轮胎硫化升温情况,选取具有代表性的测温点数据作温度曲线。
胎圈及肩部测温点中分别选取升温速度较慢的测温点,缓冲部位测温点选取通入内冷水后降温最快的测温点。
内冷却硫化工艺测温后期胎冠表面中心及胎侧表面温度开始下降;通入冷却水后气密层中心、缓冲层中心、下模胎圈部位温度下降明显。
热硫化工艺问题回答

热硫化工艺
热硫化是一种将橡胶加热并与硫化剂反应的工艺,它可以使橡胶变得更加耐用和强韧。
这种工艺在制造轮胎、密封件、管道等橡胶制品中广泛应用。
热硫化的工艺流程包括以下几个步骤:
1.混炼:将橡胶和其他添加剂混合在一起,以形成所需的化学配方。
2.压延:将混合物压成薄片或条形,以便于后续加工。
3.模压:将压延后的混合物放入模具中,并施加高温高压,使其形成所需形状。
4.硫化:在高温下对模具中的橡胶进行硫化反应。
硫化剂可以是硫或其它有机硫化合物。
5.冷却:待反应完成后,取出模具并冷却。
6.修整:对制品进行修整、打磨等处理,以便于使用。
热硫化工艺的优点是可以使橡胶材料变得更加耐用和强韧,并且能够
生产出各种不同形状和尺寸的橡胶制品。
此外,热硫化还可以提高橡
胶的耐热性、耐寒性和耐化学腐蚀性。
不过,热硫化也有一些缺点。
首先,它需要较长的时间来完成反应,
因此生产效率相对较低。
其次,高温和高压环境下可能会导致橡胶材
料变形或出现气泡等问题。
此外,在硫化过程中还会产生有害气体和
废水等污染物。
为了解决这些问题,近年来出现了一些新型的硫化工艺,如微波硫化、紫外线光固化等。
这些工艺具有反应时间短、能耗低、环保等优点,
并且可以用于对特殊材料进行处理。
总之,热硫化是一种重要的橡胶加工工艺,在现代工业生产中得到广
泛应用。
随着技术的不断发展和创新,相信未来会出现更多高效、环
保的硫化工艺。
硫化的工艺参数

硫化历程
橡膠不同厚度的溫升图
• 橡胶为不良导热 体,表层与内层 的温差随着厚度 的增加而增大。 • 正硫化時间只适 用于厚度6mm以內 之制品。 • 厚度每增加1mm, 硫化时间需增加 约47sec.。
硫化温度与时间
• 温度每差10℃,时间差一倍。 • 硫化温度系数 1.8 ~ 2.5 随胶料配方而有差异。
14.886 15.204 15.528 15.857
气胎硫化
• • • • 1、模温:160℃左右。 2、内硫化介质:空气。 3、压力:一般17±1kgf/cm² 缺点:气胎整形劳动强度大;硫化时间长;气胎 内部容易氧化发粘、发烂。) • 优点:可多层模硫化。
胶囊隔膜硫化
• 1、模温: 160℃左右。 • 2、内硫化介质: ※过热水,一般采用20kgf/cm² 左右的压力,热水温度 一般在160~170 ℃,对轮胎硫化质量来讲是较好的硫 化工艺。 ※氮气,有二种,液氮(成本较高,但纯度高);制氮 装置直接从空气中分离制取氮气(纯度不稳定),一 般采用20kgf/cm² 左右的压力。氮气硫化工艺在理论 上是较为理想的一种工艺,但由于氮气制取纯度不稳 定、对设备和管道密封性要求很高等因素,目前在国 内还未被大部分轮胎企业采用。
胶囊隔膜硫化
4.50-12 双向导热硫化测温 2012.12.28
内压蒸汽约11kgf/cm²
胶囊隔膜硫化
※空气,胶囊隔膜硫化内压使用空气,业内基本没 有厂家使用。此工艺就轮胎质量而言,是可行的, 业内不采用的原因是:内压采用空气时,空气中 含有的大量氧分子会加快胶囊的老化,胶囊的使 用寿命会很短(只有正常的1/4~1/3),也会增加 废胶囊导致的废胎,对生产成本增加明显;更大 的问题是,由于胶囊很容易氧化,发粘、发烂会 损坏硫化机的中心机构,到一定程度时甚至有使 整个硫化管道堵塞瘫痪的风险。
华东高温硫化半钢子午线轮胎外观质量缺陷的原因分析及解决措施

(上)橡胶行业节能技术和设备介绍来源:中国化工信息网 2007年8月3日0 前言橡胶行业是国民经济中消耗能源较大的行业之一,一个年产100万套轮胎的传统轮胎企业每小时消耗蒸汽约40 t,消耗电量约7000 kW·h。
目前轮胎企业用机械式轮胎硫化机硫化1100R20子午胎时,根据轮胎硫化机采取节能措施情况,每硫化一条轮胎可消耗蒸汽约110-180 kg。
因此,减少能耗,节约能源,降低生产成本,一直是橡胶企业所关心的问题。
研究开发节能型橡胶加工设备及利用节能技术改造设备,提高设备使用性能,是目前降低橡胶行业能耗的主要措施之一。
由于我国国民经济整体生产水平比较落后,属国际上能源消耗大国,也是能源浪费大国。
为此中央提出在“十一五”期间降低能耗20%。
橡胶行业响应中央号召,为实现中央降耗目标而努力,多年来开发了不少行之有效的降耗节能设备和节能新措施,为橡胶行业的节能降耗工作作出了贡献。
为便于了解行业节能技术情况,根据个人水平将有关资料收集汇总如下,供同行参考。
1 炼胶设备节能措施炼胶是橡胶加工中消耗电能最多的一道工序,一台F270密炼机的装机功率达1000-1500 kW,因此做好炼胶设备的节能工作极为重要,在设计新机型和提高使用效率方面,出现了许多好经验。
提高密炼机转子转速和压砣压力提高密炼机转子转速和压砣压力可以提高生产效率,节约电能。
当采用过去压砣对物料压力≤ MPa,转子转速20 r/min的250 L低压低速密炼机炼胶时,每千克混炼胶能耗高达 kW·h;而当采用压砣对物料压力≥ MPa,转子转速40r/min的270L高压快速密炼机炼胶时,每千克混炼胶耗能 kW·h。
因此,每加工1000 kg混炼胶,至少比老式密炼机要少消耗100 kW·h电能。
国内过去大量生产的低压低速密炼机如果不进行改造,就应该淘汰,推广采用高效节能密炼机,以减少电能消耗。
利用智能密炼机控制系统节能青岛高校软控和浙江大学共同开发的两栖智能密炼机上辅机系列利用统计学理论、人工智能和专家系统,解决混炼质量的波动。
轮胎硫化罐参数

轮胎硫化罐参数轮胎硫化罐是一种用于轮胎制造过程中的重要设备。
它起着将轮胎胶料加热硫化的作用,使轮胎具有良好的强度和耐磨性能。
本文将从轮胎硫化罐的结构、工作原理、优点和应用等方面进行介绍。
一、轮胎硫化罐的结构轮胎硫化罐通常由罐体、加热系统、控制系统、密封系统等部分组成。
罐体采用优质的耐高温材料制造,具有良好的热传导性能和稳定性。
加热系统通常采用电加热或蒸汽加热方式,能够提供稳定的加热温度。
控制系统则负责监测和调节加热温度,确保轮胎在硫化过程中得到适当的加热。
密封系统则起到密封罐体的作用,防止热量和硫化气体的泄漏。
二、轮胎硫化罐的工作原理轮胎硫化罐的工作原理是通过加热将轮胎胶料中的硫化剂加热至一定温度,使其发生化学反应,从而使胶料变成固态。
在硫化过程中,罐体内的温度和压力会逐渐升高,使轮胎胶料中的硫化剂与橡胶发生交联反应,增强轮胎的强度和耐磨性能。
三、轮胎硫化罐的优点轮胎硫化罐具有以下几个优点:1. 加热温度可调节:通过控制系统可以灵活调节加热温度,适应不同轮胎的硫化需求。
2. 硫化效果好:轮胎硫化罐能够提供均匀的加热,使轮胎胶料中的硫化剂充分交联,确保轮胎具有良好的性能。
3. 操作简便:轮胎硫化罐的操作相对简单,只需设置加热温度和硫化时间,即可完成硫化过程。
4. 节能环保:轮胎硫化罐采用的加热方式能够提高能源利用效率,减少能源浪费,对环境友好。
四、轮胎硫化罐的应用轮胎硫化罐广泛应用于轮胎制造行业。
无论是乘用车轮胎、商用车轮胎还是工程机械轮胎,都需要经过硫化过程,以提高轮胎的强度和耐磨性能。
轮胎硫化罐能够满足不同规格和型号的轮胎硫化需求,是轮胎制造过程中不可或缺的设备。
轮胎硫化罐是轮胎制造过程中必不可少的设备之一。
它通过加热将轮胎胶料中的硫化剂加热至一定温度,使其发生化学反应,从而使轮胎具有良好的性能。
轮胎硫化罐具有加热温度可调节、硫化效果好、操作简便和节能环保等优点,广泛应用于轮胎制造行业。
半钢子午线轮胎全氮气硫化工艺研究

308 轮 胎 工 业2024年第44卷半钢子午线轮胎全氮气硫化工艺研究吕国勤,夏代杰(山东昊华轮胎有限公司,山东寿光262700)摘要:对蒸汽/氮气硫化工艺与全氮气硫化工艺进行对比,并对205/55R16 91V半钢子午线轮胎采用两种硫化工艺进行硫化测温和分析。
结果表明,相对蒸汽/氮气硫化工艺,采用全氮气硫化工艺轮胎的上下模温差较低,硫化时间缩短,各部位硫化程度符合要求,成品轮胎性能提高,单胎硫化能耗成本降低40%。
关键词:半钢子午线轮胎;全氮气硫化工艺;蒸汽/氮气硫化工艺;工艺优化;低碳节能中图分类号:TQ336.1;TQ330.6+7 文章编号:1006-8171(2024)05-0308-04文献标志码:A DOI:10.12135/j.issn.1006-8171.2024.05.0308构建基于低碳经济的轮胎产业可以减少能源消耗、降低轮胎生产成本,低碳技术开发与创新也必将提升轮胎企业的竞争力。
硫化工序使用大量蒸汽能源,使轮胎胶料在硫化介质提供的温度、压力下发生复杂的化学反应,由线型结构变成体型网状结构,进而获得优良的物理性能。
传统硫化工序使用过热水或蒸汽硫化工艺,近几十年来蒸汽/氮气硫化工艺以较低的蒸汽消耗量、优异的能源利用率得到大面积应用。
随着设备的创新升级,电加热硫化机带来一种更加节能的全氮气硫化工艺。
本工作通过对205/55R16 91V半钢子午线轮胎采用蒸汽/氮气硫化工艺与全氮气硫化工艺进行硫化测温和对比分析,探索使用更加高效的全氮气硫化工艺,达到低碳节能的目的[1-4]。
1 蒸汽/氮气与全氮气硫化工艺的主要区别半钢子午线轮胎一般要求硫化结束时介质温度高于150 ℃,硫化介质中含有的热量对轮胎生产可利用价值较低,而同等条件下蒸汽的热焓远大于氮气,造成蒸汽/氮气硫化工艺在硫化程序结束时排放气体的余热较高,这也成为全氮气硫化工艺节能的主要原因。
1.1 工艺步骤蒸汽/氮气硫化工艺首先使用1.4~1.8 MPa高压蒸汽提供热量,若干分钟后切换通入2.2~2.8 MPa高压氮气,利用充氮硫化绝热压缩减小温度下降,最后空排、氮气回收、抽真空至硫化程序结束。
轮胎硫化机结构简介(三四)

液压式硫化机合模力的获得完全来源于油的压力。一般均用较低压力、较快速度、较长行程的油缸控制开合模。合模以后用一定的方式(插销、锁环、或锁紧块)将上下模部分锁住,组成一个闭环受力系统,然后再用高压、短行程的油缸使上下模受到合模力。PC-X硫化机获得合模力的方式有其结构特点,见图3。
2 氮气硫化站的组成原理
氮气硫化站的作用是提供一定压力的高纯度的氮气 , 作为轮胎硫化的内压介质。氮气硫化站主要是由制氮系统、氮气纯化系统、氮气加压系统和压力控制系统四部分组成 , 如附图所示。制氮系统的任务是将空气经过制氮设备 , 利用分子膜原理制出一定纯度的氮气 ; 氮气纯化系统的任务是利用氢气还原氧气的原理 , 将此氮气进行高纯度净化 , 使含氮量高达 99.99% 以上 ; 氮气加压系统和压力控制系统的任务是将此高纯度氮气用压缩机加压 , 并进行控制 , 以达到硫化工艺的要求。
采用日本横河新型的UR1000三针记录仪和UT35数字调节仪对硫化过程的外温,内温,内压参数进行记录,并对外温进行自动调节。
新型的三针记录仪和数字调节仪体积小,功能强、精度高,对外温进行数字控制,具有超温超压报警功能,能与上级计算机进行联网。
综上所述,在当前国际市场上可提供的各种型号的液硫化机中,日本三菱重工的产品具有较突出的优点。现产品除在日本销售外已销到韩国、马来西亚、中国、中国台湾、美国、巳西、南非和法国、英国、德国、波兰、葡萄牙、卢森堡、俄罗斯等欧洲国家。国际上一些知名的轮胎公司如桥石、固特异、米西林、大陆、邓录普都已较多地采用。
②故障指示:T/P ER.硫化温度/压力超过设定值;
COM ER MAC—LAN系统联网故障;
CPU ER CPU故障。
(6)步前进键
硫化罐变温变压硫化工艺

型硫 化仪 , 国埃 迩法科 技有 限公 司产 品 。 美
1 2 测 温 部 位 的选 取 及 成 型 .
阀 , 打 开 冷 水 回水 阀 , 内 压 保 持 硫 化 所 需 水 不 使
平, 利用 余 热继 续 硫 化 的工 艺 。 由于 橡 胶传 热 具
有 滞 后 的特性 , 胎 各 部位 的结 构 和 尺 寸 不 同造 轮
由于测试 结果 直接 影 响对 轮胎各 部位 硫化 程
度 的判定 和硫 化 工 艺 的调 整 , 此选 取 的测 温 点 因 必 须有代 表性 。在 关键 部位 或 温度场 梯度 较高 部 位 必须 多选 取测 温 点 , 以消 除 几何 结 构 和花 纹 变 化 对测试 结 果 的影 响 , 测试 结 果 更 真 实 。一 般 使 测 温部位 多 选取在 肩 部 和胎圈 区 。 按 照既 定 的部 位 在成 型机 上边 成型 边埋 线 , 埋 线时 热 电偶 补偿 导 线在 轮胎 内部 打弯 处应 涂上 少 许滑 石粉 , 并在 所经 之处 用粘 合胶 片 固定 , 以免 在 定型 时被 拉断 , 型时 热 电偶 测 温 头应 平 行 于 成 胎 圈或 花纹 方 向 。埋 线 结 束 后 , 有 补偿 导 线 集 所
丢失 的 问题 ; E型 测温热 电偶 补偿 导 线 , 江苏 杰 创 科技 有 限公 司 产 品 , 径 为 0 4 直 . 0 mm, 覆 聚 四 外
作 者简 介 : 世刚 (9 8) 男 , 沈 1 6_ , 黑龙 江牡 丹 江人 , 岛 双星 轮胎 工 青
在 上模 胎 圈外三 角胶 中心处 ; ~ 9 下 模肩 部 7 在
要求 其很 高 , 却水 的进水 压力 ( . ~2 4MP ) 冷 2 2 . a
热硫化工艺

热硫化工艺热硫化工艺是一种在高温条件下进行的硫化反应,常用于橡胶制品的生产过程中。
热硫化工艺能够提高橡胶制品的耐磨性、耐老化性和耐用性,是现代橡胶工业中不可或缺的重要工艺之一。
热硫化工艺的原理是利用硫化剂(如硫)在高温下与橡胶分子中的双键发生反应,形成硫化键,从而使橡胶分子交联成网状结构。
这种交联结构使橡胶材料变得更加坚固和耐用,同时也提高了橡胶制品的弹性和抗拉伸性能。
在热硫化工艺中,首先需要将橡胶制品放入硫化炉中,然后加入硫化剂和辅助剂,通过加热使硫化剂与橡胶发生反应。
硫化的时间、温度和压力等参数都会影响硫化反应的效果和速度。
一般来说,硫化温度越高、硫化时间越长,橡胶制品的硫化程度就越高,性能也越优异。
热硫化工艺在橡胶制品的生产中起着至关重要的作用。
通过热硫化可以改善橡胶制品的物理性能,延长其使用寿命,提高产品质量和市场竞争力。
目前,热硫化工艺已经广泛应用于轮胎、密封件、管道、橡胶垫等各种橡胶制品的生产中。
虽然热硫化工艺在橡胶工业中有着重要的地位,但也存在一些问题和挑战。
比如,硫化过程中会产生硫化气体,对环境造成污染;硫化剂的使用可能会对人体健康造成危害;硫化温度和时间的控制要求较高,生产成本较高等。
因此,如何改进热硫化工艺,减少环境污染,提高生产效率,降低生产成本,是橡胶工业亟待解决的问题。
为了进一步推动热硫化工艺的发展和应用,需要加强科研力量,开展硫化反应机理的研究,优化硫化工艺参数,开发绿色环保的硫化剂,推广应用新型硫化技术等。
只有不断创新和改进,才能更好地利用热硫化工艺,提高橡胶制品的质量和市场竞争力,推动橡胶工业的可持续发展。
总的来说,热硫化工艺作为一种重要的橡胶硫化方法,在橡胶制品生产中具有不可替代的作用。
通过不断改进和创新,我们可以更好地利用热硫化工艺,提高橡胶制品的性能和品质,推动橡胶工业的发展,为社会经济的发展做出更大的贡献。
轮胎硫化方式及步骤

轮胎硫化方式及步骤工艺技市上Z杖JIL1硫化方式1.1过热水硫化过热水硫化是比较传统的硫化方式,内温由过热水提供,外温由热板式或蒸鼓式设备提供.采用蒸鼓式供热,能耗较高,升温也较慢,但受热相对较均匀.采用热板式供热,外温较稳定且波动小,但热板不同部位可能受热不同,故热板中的蒸汽走向设计要科学合理,以使整个热板不同点的温差尽量小,同时模具和热板的接触面不能有杂质,模具背面的排气槽要尽量窄,以增大热板和模具的接触面积,即增大传热面积.此硫化工艺一般用于载重斜交轮胎和全钢载重子午线轮胎.1.2高温蒸汽和过热水硫化高温蒸汽和过热水硫化是目前较多采用的硫化方式,大部分轿车子午线轮胎采用此硫化工艺.胶囊在通过热水之前内部温度相对较低,为使胶囊快速升温,需先在胶囊中充入高温饱和蒸汽(压力一般为1.5MPa),一定时问后再充入压力较高的过热水.此工艺相对较简单,技术也易于得到保障.1.3全蒸汽硫化全蒸汽硫化是目前国际上一些大公司普遍采用的方法,主要用于硫化乘用子午线轮胎和轻载子午线轮胎.全蒸汽硫化可节省能源且生产效率高,但技术要求相对较高,须保证高温饱和蒸汽压力稳定,同时还须解决胶囊上下部分的温差硫化机动力水泄漏,内压偏低造成的轮胎外观瑕疵增多及胶料和部分骨架材料的耐高温性能等问题.1.4充氮气硫化充氮气硫化内压可控且稳定,因此可节省能源和提高轮胎质量,并能延长胶囊的使用寿命.充氮气硫化对设备的要求较高:(1)需购置制氮设备且设备维护成本高;(2)需使用氮气回收装置以降低成本;(3)为防止氮气泄漏,需采用专用阀门和氮气输送管路;(4)硫化机管路需重新设计和改造,特别是各阀门的泄漏问题必须解决,以免造成氮气的大量泄漏而对硫化内温造成影响.2硫化步骤的设定各轮胎公司采用的硫化步骤不尽相同,但主要由以下步骤组成:(1)通高温饱和蒸汽;(2)充填水(视情况而定);(3)通过热水;(4)热水回收;200%年第11期第1]页MoDERNRUBBER&PLASTICS(5)通冷却水(视情况而定);(6)主排;(7)抽真空;(8)开模.其中,第3步可采用3种方式:循环,半循环或不循环,需根据实际情况进行选取.第4步可采用两种方式:用高压蒸汽把胶囊中的过热水赶回除氧器或设置一热水回收罐.第6和7步可采用单路或双路.第8步的开模压力一般设置为O.03MPa.全蒸汽硫化一般有两种方式:高温蒸汽进加热排或高温蒸汽进,然后主排,再抽真空;高温蒸汽进加热排,然后低压蒸汽进,再主排,抽真空.其中热排是为了把胶囊中的冷凝水排出.充氮气硫化还需要增加两个步骤,即放气(排出胶囊下部的低温氮气)和查漏(关闭所有阀门,看内压有无下降,以观察有无阀门泄漏).由于主排时间的长短直接影响到硫化效率,因此主排管径的设定和走向以及辅助措施(如安装排空管)对主排的效果至关重要.抽真空可采用蒸汽或动力水,只需将胶囊从胎里脱出并适当收缩,以便轮胎能轻松取出即可.若抽真空过度,胶囊会紧贴中心机构,上环下降时容易夹破胶囊(B型硫化机).3匹配硫化机管路及选取测温点(1)选取高温蒸汽主管及支管管径主管管径选取要考虑硫化机台数及进蒸汽时对蒸汽压力波动的影响.若管径偏小,易导致饱和蒸汽压力偏低,从而使硫化温度波动较大.在设计i●,,tttI,,tt,●I,-市场信息主排管径时,要特别考虑热水主排时蒸发而引起的背压.(2)选取测温点内外温度,时间和内压是硫化三要素,为便于控制,各硫化机都要对三要素进行测定并记录.一般测温点选在回管上靠近胶囊的出口处较好,当然最好是将测温点选在胶囊内部,但难度较大.采用蒸汽硫化时还须在相应位置安装疏水阀,以免冷凝水积存过多影响测温结果.同时要定期校正热电阻及温度变送器,发现异常时应及时校正.4利用测温数据进行硫化速度匹配调节由于各配方胶料硫化速度不相同,各部件在硫化过程中的温升也不相同,只有当各部件在一定的硫化条件下基本同时达到正硫化点,轮胎的性能和硫化效率才是最佳的.因此,必须对每个配方的胶料进行测温,每个部件均须埋热电偶,对较厚的部件要在中间埋一些点.根据测得的温度,采用RPA2000硫化仪对不同部件的变温进行测定,通过对变温硫化仪曲线和恒温硫化仪曲线分析及各半成品制造的特点(挤出或压延等),对整个配方体系进行硫化速度匹配调整,以求各部件胶料基本同时达到正硫化.5选取合模力合模力太小,易造成轮胎合模处出边,引起带束层弯曲,影响轮胎质量;合模力太大,则会引起模具变形和硫化机损坏.因此要根据不同的轮胎规格选取相应的合模力,才能生产出高质量的轮胎.我国聚丙烯薄膜市场分析美国一家信息机构最近发布了其关于中国市场份额系列报告中的首份报告——"中国挤出塑料薄膜市场".该报告对成长中的中国塑料薄膜市场进行了深入分析,并提供了按供应商,地区和终端应用市场分类的详尽信息.该报告称,中国今年将要加工118.4万t聚丙烯薄膜,其中56%的原料由国内树脂生产商提供.中国两大聚丙烯薄膜生产中心是苏沪浙地区和广东省,分别占全国总生产能力的33%和32%.食品包装是聚丙烯薄膜最大的终端应用市场,约占42%.其中,包装袋,塑料编织袋和干货食品包装材料占食品包装的60%以上.非食品包装中,香烟包装,编织袋和防护膜是最大的细分市场,合计占55%.RP010-5第14页总第己口]期。
轮胎生产流程、生产工艺
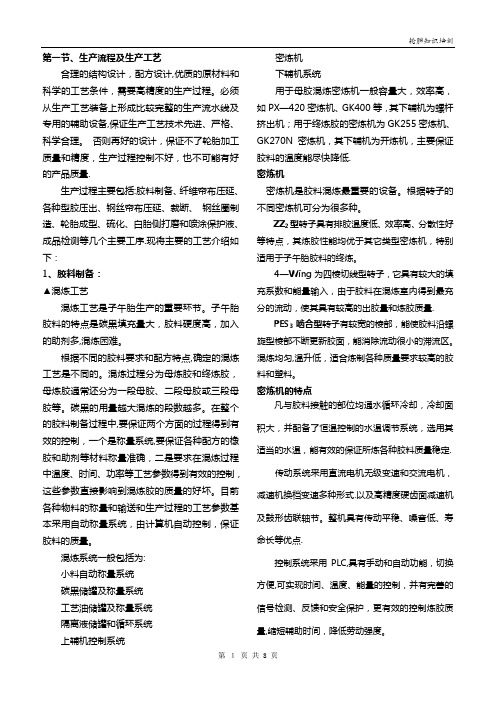
第一节、生产流程及生产工艺合理的结构设计,配方设计,优质的原材料和科学的工艺条件,需要高精度的生产过程。
必须从生产工艺装备上形成比较完整的生产流水线及专用的辅助设备,保证生产工艺技术先进、严格、科学合理。
否则再好的设计,保证不了轮胎加工质量和精度,生产过程控制不好,也不可能有好的产品质量.生产过程主要包括:胶料制备、纤维帘布压延、各种型胶压出、钢丝帘布压延、裁断、钢丝圈制造、轮胎成型、硫化、白胎侧打磨和喷涂保护液、成品检测等几个主要工序.现将主要的工艺介绍如下:1、胶料制备:▲混炼工艺混炼工艺是子午胎生产的重要环节。
子午胎胶料的特点是碳黑填充量大,胶料硬度高,加入的助剂多,混炼困难。
根据不同的胶料要求和配方特点,确定的混炼工艺是不同的。
混炼过程分为母炼胶和终炼胶,母炼胶通常还分为一段母胶、二段母胶或三段母胶等。
碳黑的用量越大混炼的段数越多。
在整个的胶料制备过程中,要保证两个方面的过程得到有效的控制,一个是称量系统,要保证各种配方的橡胶和助剂等材料称量准确,二是要求在混炼过程中温度、时间、功率等工艺参数得到有效的控制,这些参数直接影响到混炼胶的质量的好坏。
目前各种物料的称量和输送和生产过程的工艺参数基本采用自动称量系统,由计算机自动控制,保证胶料的质量。
混炼系统一般包括为:小料自动称量系统碳黑储罐及称量系统工艺油储罐及称量系统隔离液储罐和循环系统上辅机控制系统密炼机下辅机系统用于母胶混炼密炼机一般容量大,效率高,如PX—420密炼机、GK400等,其下辅机为螺杆挤出机;用于终炼胶的密炼机为GK255密炼机、GK270N密炼机,其下辅机为开炼机,主要保证胶料的温度能尽快降低.密炼机密炼机是胶料混炼最重要的设备。
根据转子的不同密炼机可分为很多种。
ZZ2型转子具有排胶温度低、效率高、分散性好等特点,其炼胶性能均优于其它类型密炼机,特别适用于子午胎胶料的终炼。
4—Wing为四棱切线型转子,它具有较大的填充系数和能量输入,由于胶料在混炼室内得到最充分的流动,使其具有较高的出胶量和炼胶质量.PES3啮合型转子有较宽的棱部,能使胶料沿螺旋型棱部不断更新胶面,能消除流动很小的滞流区。
不同变温硫化工艺下轮胎硫化效果分析

忌 Ae p 一 E/ ’ 一 x( R了) () 1
胎 , 变 内外 温 、 温 、 外 温 和 变 内温 等几 种 硫 在 恒 变
化工 艺情 况进 行 了 模 拟 , 对 这 几 种 不 同变 温 硫 并 化工 艺 下 的硫 化 效 果 进行 了分 析 比较 , 以期 对 工 程 中硫 化工艺 的 正确制 定 提供 一定 的 参考 。
量 概念 , 是指胶 料在 不 同硫 化 温 度 下达 到 相 同 它
质 量 的重要 因素 。不 同 的硫化 程度 ( 即交联 度 ) 对
橡 胶制 品 的使用 性 能 有 着 不 同的 影 响 , 胎 是 一 轮
种 橡胶 厚 制品 , 何 在硫 化 生 产 的过 程 中使 轮 胎 如 获 得恰 当 而均匀 的硫 化 程 度 , 提 高 轮 胎 的 行驶 对 质 量有 重要 意义 。文 献[ 曾对 斜 交 胎和 子 午线 1 q] 轮 胎在 变外 温硫 化条 件下 的硫 化程 度 进行 了实 验
温 同 时 变化 和 只 变 外 温 的 条 件 下 , 胎 的 硫 化 速 度 比在 变 内 温和 恒 温 条件 下 的硫 化 速 度 快 , 是 硫 化 均 轮 但 匀 程度 较 差 ; 而在 恒 温 和 变 内温 的 条 件 下 , 化 均 匀程 度 要 好 , 是 最 难 硫 化 点 达 到 正 硫 化 的 速 度 相 对 硫 但
式 中 : 硫化 反应 速率 常 数 ; 为 常数 ; 为 硫 最为 A E 化反 应活 化 能( J mo)R 为气体 常数 ; k/ 1; 丁为硫 化
温度 ( 。 K) 由式 ( ) 以 得 到 : 1可
巨型工程机械子午线轮胎的变温硫化工艺研究

橡 胶 工 业
2019年第66卷
巨型工程机械子午线轮胎的变温硫化工艺研究
武栴丞1,李文Leabharlann 1,杨茂林1,曾 季1,蔡 庆1,黄振华2,施大全2
(1. 北京橡胶工业研究设计院有限公司,北京 100143;2. 福建省海安橡胶有限公司,福建 莆田 351100)
摘要:研究巨型工程机械子午线轮胎的变温硫化工艺。结果表明:与传统硫化工艺相比,采用变温硫化工艺(加热时 间/保压时间比为1/1. 07)的巨型工程机械子午线轮胎胶料过硫化程度降低,物理性能提高;变温硫化工艺能提高巨型工 程机械子午线轮胎硫化均匀性,解决局部过硫严重的问题;采用变温硫化工艺,调整加热时间与保压时间比,有利于提高 巨型工程机械子午线轮胎性能和生产效率,节约能源。
于改善轮胎硫化均匀性有更显著的效果。
3 优化方案测温结果验证与分析 通 过 以 上 模 拟 计 算 和 理 论 分 析 可 知 ,优 化 方
案2更有助于改善巨型工程机械子午线轮胎部分 部 位 过 硫 严 重 问 题,因 此 选 择 优 化 方 案2进 行 埋 线测温试验,对测温结果进行分析。 3. 1 不同硫化方案排出保压热水时温度对比
图1。采用传统硫化工艺生产的轮胎多个部件处 于 较 严 重 过 硫 化 状 态,硫 化 均 匀 性 差。 通 过 分 析 可知,橡胶热传导性能差,各部件体积和厚度差异 显著,受热不均匀。针对现有问题,本工作提出两
作者简介:武栴丞(1992—),女,山西阳泉人,北京橡胶工业研 究设计院有限公司助理工程师,硕士,主要从事轮胎结构与配方设 计工作。
根 据 以 上 两 种 优 化 思 路 ,基 于 对 中 小 型 工 程 机 械 轮 胎 优 化 经 验 ,本 研 究 将 内 部 热 水 循 环 时 间 与 保 压 时 间 的 比 例 重 新 分 配 ,拟 定 两 种 优 化 工 艺 方案,并与原方案对比(见表1)。
- 1、下载文档前请自行甄别文档内容的完整性,平台不提供额外的编辑、内容补充、找答案等附加服务。
- 2、"仅部分预览"的文档,不可在线预览部分如存在完整性等问题,可反馈申请退款(可完整预览的文档不适用该条件!)。
- 3、如文档侵犯您的权益,请联系客服反馈,我们会尽快为您处理(人工客服工作时间:9:00-18:30)。
束, 硫化温度在硫化过程中缓慢下降。
由于 等压 变温硫 化 过程 大大 缩短 了过 热水 循 环时 间 , 节约 大量过 热 水及过 热 水循 环所 需能 量 ,
作者 简 介 : 魏荣 贺 ( 9 2 ) 男 , 宁 朝 阳 人 , 阳浪 马 轮 胎 有 17 一 , 辽 朝 限责 任 公 司工 程 师 , 要 从 事 工 艺 技 术 及 质 量 管 理 工 作 。 主
硫 化 结 束 , 缩 短 过 热 水 的 循 环 时 间 、 约 过 热水 及循 环 所 需 能 量 、 可 节 降低 生 产 能 耗 和 缩 短 硫 化 时 间 , 硫 化 轮 胎 的 质 量 且 与 传 统 硫 化 工 艺 无 差 别 。 在 提 高 生 产 效 率 的 同 时 降 低 了 生 产成 本 。 关 键 词 : 压 变 温 硫 化 ; 化 测 温 ; 久 性 试 验 等 硫 耐
艺和 正 常硫化 工艺 硫化测 温试 验结 果 分 别 如 图 1由 图 1和 2可 以看 出 , 化前 期 靠 近 硫 化介 硫
维普资讯
42 3
轮
胎 工
业
20 0 8年 第 2 8卷
4 硫 化 时 间 调 整 及 轮 胎 性 能 ( ) 化 工 艺 时 问 调 整 1硫
从 而 降低硫 化过 程 中的能 耗 。轮胎 硫化 时 间可缩
短 5 ~1 , 高 了设 备 利用 率 , 而 提 高 了生 2 提 从
产效率 。 2 实施等 压变 温硫 化工 艺 的准备 工作 为保证 硫化 蒸 汽压 力 不 低 于 1 6MP , 化 . a硫 管路及 分 配 阀需 按工 艺要 求进 行改 造 。 主要试 验设 备 : 硫化 仪 , 国台湾优 肯科 技股 中 份 有 限公 司产 品 ; 化 机 , 硫 桂林 橡 胶 机 械厂 产 品 ;
仪 软件 中 , 温过 程 中 由硫 化 测 温 仪 系统 采 用 阿 测 累尼 乌斯 公式 计算 出各 测 温点胶 料 的累计 等效 硫 化 时问 , 测温结 束 后 计 算 出 轮 胎 各测 温 点 胶 料 的
硫化 程度 。
不变 ; 化初 期 向胶 囊 内通 入 比常 规 硫 化 温度 高 硫 的蒸 汽 , 使硫 化 内温迅 速 升至 2 0℃ 以上 , 压一 0 保
经硫 化 测 温 结 果 数 据 分 析 , 1 O R2 8 R l. O 01P
规 格 轮 胎 硫 化 时 问 由 原 来 的 5 n 短 到 mi 缩 6
5 i 2 m n。
() 气 泡 点试验 2割
由于胎 肩在 轮 胎 结构 中 属最 厚 部 位 , 硫 化 若
中图 分 类 号 : TQ3 0 4 7 3. 文 献 标识 码 : B 文 章 编 号 : 0 6 8 7 ( 0 8 0 — 4 10 1 0 — 1 1 2 0 ) 70 3 — 3
轮胎 市场 竞争 , 不仅 是 质量 和服 务 的竞争 , 更
重要 的是 成本 和效 益竞 争 。
艺 实施 过程 。
3 硫 化 测 温
首 先通 过硫 化仪 测量 各种 胶料 在一定 温 度下
对 应 的硫化 时 间 , 然后 由硫 化 测 温 仪 软件 计 算 各
1 等压 变 温工 艺原理 等 压变 温硫 化 工 艺 的 原理 为 : 热板 式硫 化机 硫化 外 温适 当提 高 , 锅 式 硫 化 机 硫 化 外 温保 持 蒸 种 胶料 的活 化 能 。在 被 测 轮胎 的埋 线 点 埋 线 , 测 温前 将 每一 个测 温点胶 料 的活 化能输 入硫 化测 温
维普资讯
第 7 期
魏 荣 贺 . 胎 的 等 压 变 温 硫 化 工 艺 轮
41 3
轮 胎 的等 压 变 温 硫 化 工 艺
魏 荣 贺
( 阳浪 马 轮 胎 有 限 责 任 公 司 , 宁 朝 阳 12 0 ) 朝 辽 2 0 9
摘 要 : 过 采 用 等 压 变 温硫 化 工 艺 : 硫 化过 程 通 热 水 并 短 时 间循 环 后 , 持 过 热 水 压 力 、 止 热 水循 环并 持 续 到 通 在 保 停
段 时间 , 以提 高轮 胎 的硫化 温度 , 向胶囊 内通入 再 过热 水 , 持一 定 的温 度 和压 力 短 时问循 环后 , 保 保
采用 等压变 温硫 化 工 艺 , 化 外 温 比正 常 硫 硫
持 过 热水 内压 并 停 止过 热 水 循 环 , 续 到硫 化 结 持
化工 艺 高 1 ℃ , 次 过 热 水 循 环 时 间 缩 短 3 0 二 0
硫 化测 温 仪 , 南理 工大 学产 品 ; 胎耐 久性 试验 华 轮
机 , 国 申克公 司产 品 。 德
我公 司通过 实 施 等压 变 温 硫 化 工 艺 , 短 了轮 胎 缩
硫 化 时间 , 提高 了产 能 , 节约 了能 源 。本文 简单 介 绍 1 . 0 2 8 R规 格 轮 胎 的等 压 变 温 硫 化 工 1 0 R 0 1P
轮胎 传统 硫化 工艺 常用 的硫 化介 质是 蒸 汽及
过热 水 。在轮 胎 的整 个 正 硫 化 过程 中 , 热 水 保 过 持一 定 的压力 和 温 度 不 问断 地 循 环 流 动 , 即硫 化
过程 中始 终保 持 等 压 等 温 , 化 过程 消耗 大 量 能 硫
源 , 轮胎 只 吸取很 小 一部 分循 环过 热水 能量 , 但 大 量 的热能 被浪 费 掉 , 同时 硫 化 时 问过 长 时 还 会 影 响轮 胎产 品质 量 。等压 变温 硫化 工艺 因其 节 能效 果 显 著 , 为 轮 胎 生 产 新 的经 济 及 利 润 增 长 点 。 成