TPS讲义
TPS讲义

4、库存是万恶之源
库存 的浪费
库存的浪费
寻找浪费
他在做什么? 有浪费存在吗?
寻找浪费
寻找浪费
寻找浪费
你能识别是那些浪费吗?
四、TPS的两大支柱
• 准时化:在必要时间按必需的数量,生产必要的合格产品,
基本原则1 工序流程化(水流不能断开) 基本原则2 根据需求数制定生产节拍( 基本原则3 取货制____后道工序领取 (1、看板方式 2、搬运)
按步骤实施自主保全
人才培养 ⇒ 提高职场能力
自主保全活动内容
一、防止劣化 1、基本条件整备
(清扫、给油、锁紧)
二、发现劣化 1、测试劣化 2、日常点检
三、改善劣化 1、迅速处置异常 (救火)
(简单零件替换等应急 处置)
2、正确操作
用五感检查 发现潜在缺陷
2、援助突发性修理 3、记录异常 4、排除人为的强制 劣化 3、早期发现异常
此后,精益生产方式已被运用到一切 经营领域,引起全世界的瞩目,各国企业
纷纷学习和效仿。
4、从精益生产到精益思想
• 从精益生产到精益企业,从精益企业到精益思想
– 《机器)一书阐述了精益生产方式的形态,却没能说 明怎么能做成这样的企业——关键 – 为了说明怎么能做成精益企业, 美 国人又利用四年多的时间,通过对 众多推行精益生产的企业进行研究, 出版了《精益思想》一书。确立了 做成精益企业的原则和一些行动案 例。企图用此来指导工厂建立精益 企业。
6、对TPS的最新认识
• TPS之所以被称为丰田生产方式,是继泰勒制(Taylor System )和福 特制(Fordism)之后的第三个生产管理里程碑。他继承了泰勒制的优 点,创造了标准作业前提下,在福特式的流水生产线上,如何低成本地 进行小批量多品种的规模化生产。 • TPS是一种制造技术,它不是简单的工业工程(IE),更具有深刻的管理 内涵和理念的外延。也是员工能力的具体体现。与传统生产技术的区别, 在于它不仅仅是一种技术,同时也是一种管理,一种意识,一种思维方 法,一种文化。在追求持续改善这一管理本质的前提下,最大限度地发 挥每个员工智慧,提高思考力、执行力和创造力。
TPS培训资料

製程分析改善技術—TPS基礎篇一、TPS之概念(一)TPS之意義TPS源出自於豐田,亦就是全公司上下打成一片,合作無間之生產方式。
生產期間=加工期間+停滯期間,故需縮短停滯時間(二)TPS之目的1、每一人單位附加價值提高2、庫存日數、量縮減3、生產期間縮短(三)TPS達成途徑1、硬體ATÆ機械化技術2、軟體JITÆ協力工廠3、省人化生產線Æ現場幹部安排二、F公司等號型併排生產線等號型生產線:兩種不同生產線併排原生產線是是一人一機,產生待加工件效益:人員、半成品數、不良率、SPH(一日目標生產量)每個產品平均生產時間CT週期時間=一日運轉時間/一日目標生產量三、TPS與傳統生產方式比較1、現場幹部的職責傳統:人海戰術TPS:縮減人員、改善生產流程2、生產計劃的擬訂傳統:主導型生產計劃以長程、中程、短程的生產計劃為主導,以銷售預測為主,預測有誤則產生存貨。
TPS:利用裝配生產線,直接反應市場需求3、生產線的佈置傳統:以機種別為主,產生待加工件TPS:以零件加工週期為主,減少生產時間,準時交貨4、生產形態傳統:按照生產計劃、大批量生產、系列生產方式;優點:單一製程效率、缺點:整體性製程無效率TPS:小批量生產、單件製造(一件完成後,才開始下一件生產方式)、混合生產;提昇整體性製程效率。
5、在製品與庫存管理傳統:必需的,以訂購點決定TPS:問題產生之根源;設置直接聯接於裝配生產線的產品供應站6、換模作業準備的次數、時間傳統:換模次數(一周)、準備、撤換Æ積待加工件、存貨TPS:三分鐘「零換模」作業7、機械化的目標傳統:主力艦巨炮式大型專用機械TPS:通用型小型設備、綜合日工機8、作業姿勢傳統:坐姿作業、皮帶輸送固定化站立作業TPS:可移動式作業9、效率管理傳統:依作業執行能力管理TPS:重視生產目標之達成(每小時預定生產量)四、製程分析改善--七項程序之關鍵及設置U型生產線之十項法則程序一:掌握現狀關鍵1、發掘隱藏中的浪費Æ應用四種資料:PQ分析、加工路徑分析表、裝配製程圖、標準作業流程線形圖2、顯現型浪費至現場實地觀察即可程序二:否定現狀同時排除浪費1、找出TPS七項浪費Æ生產過剩、手等待、輸送、製程不當、庫存、動作不當、產製不良品2、探究浪費產生的原因Æ制作製成別排除浪費表程序三:探討製程目的1、探討製程目的,消除以往工作陋習2、「為什要這樣做?」反覆探討其目的程序四:找出改善重點1、找出改善問題之關鍵2、由停頓(待工件)製程分析—等待情形、輸送、動作運用CT計算表、生產線別編組效率表、製程別餘力調查別程序五:構思製程形態1、應採用L型、U型、直線型或是等號型生產線2、儲存站的位置、形態(最高、最低、平均存量)、存量3、應採用小型容器程序六:設置「試製生產線」並親自動手試製1、由加工路徑分析表彙集相關類屬製程佈置設備2、訂出專用、共同生產線3、由現場幹部率先試製操作利用TPS三種利器零件別加工能力表、標準作業編組表、標準作業書程序七:讓部屬參與試製,並多次反覆追蹤改善1、詳盡說明工作目的與意義2、一同操作並改善不妥之處3、以部屬名義,提出改善提案(移轉技術)五、設置U型生產線之十項法則法則1:配合CT逐件製造生產方式法則2:可移動式站立作業法則3:進料、出口段都由同一人員負責(品質)法則4:SPH達成率100%法則5:製程中發生問題時先停止運轉,並會同領人員調查原因,並排除之法則6:責令遵守,並執行標準作業書(步行圖)指示法則7:韻律化之CT生產法則8:以HT(手工)改成MT化以便實現連貫作業方式法則9:加裝「防呆裝置」法則10:三分鐘內完成「零換模」作業,裝配則是順序更換作業請說明何謂TPS及其作法,任舉一真實企業(服務業亦可),目前您認為該公司應如何改善為TPS。
TPS讲义

库存太多是万恶之源
• 为什么库存太多是万恶之源? • • • • • • • • • 一、有形损失 ① 产生不必要的搬运、防护、处理、寻找 ② 先进先出困难 ③ 占用资金,损失利息 ④ 增加管理费用 ⑤ 物品损耗、物品价值减低 ⑥ 变成呆滞品 ⑦ 占用厂房空间 ⑧ 仓库建设投资效益低
库存太多是万恶之源
认识工厂常见烧钱现象
库存的浪费 制造太多的浪费 不良修理的浪费 搬运的浪费 停滞的浪费 管理的浪费 动作的浪费 过分加工的浪费
J I T 要 改 善
丰田公司:为了彻底排除浪费,首先建立JIT生产方式
降低成本与排除浪费2(改善提案 制度)
• 凡在制造现场中使生产增加成本的,均为浪费。 如用人过多、库存过剩、多出之设备、超出不必
• 二、无形损失 • ① 造成生产没有紧迫感,阻碍改善和提高 生产效率 • ② 造成对设备能力及人员需求的误判
浪费的产生与固化过程
问题发生
真正解决问题 的长久对策 逃避产生浪费 领导说的认可浪费 没办法应付了事 好象应该有必要 即成事实 长期存在谁也不认 为不合理 回避问题 暂时增加库存应 对一下 应该保持库存 库存已成习惯 与应该 形成浪费
放区域等,均有状况之指示板(KPI)。甚至有
些工厂设立零件供应中心,当加工线或组立
线用完料时,按下开关,供应中心之各零件
指示灯会亮,指示何站缺何料件,以使零件
补给人员正确补给零件。
• 生产管理最忌讳负荷变化过大,如季节性产品。 而TPS管理强调将工作负荷之全年量加以平均, 使各月份之负荷平均一致,再平均至每月每小时, 进而平均负荷至每分。此项平准化生产为求平均 的负荷,可采不同机种之混线生产,于同一生产 线加工或组立。但由于制造过程不一致,宜采取 群体技术,将类似之制程群组化,并以中央控制 之计算机控制器,以调整各制程之负荷,以使各 制程顺利、负荷及产量能平准化。
TPS理念讲义
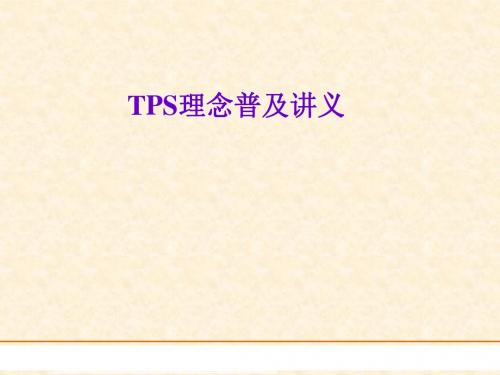
2、制造不良的浪费 是指企业内发生不良品,造成的各种质量成本。 主要现象如下: 材料、设备、人员、工时的损失; 额外的修复、挑选、追加检查; 额外的检查预防人员; 质量缺陷未被发现流入市场,造成用户索赔退货 企业信誉下降;
20
3、搬运的浪费 产品的搬运,在企业生产制造过程中不可缺少, 但搬运不产生附加价值,因平面布置和物流组织等 原因。常带来以下现象: 产品搬运纺织、堆积、移动等动作浪费; 搬运路线过长的浪费; 中转环节过多带来产品在搬运过程中造成的损失 和丢失的浪费; 产品移动所要的空间浪费; 时间的损耗;
10
2、丰田喜一郎(1894---1962)
丰田佐吉的儿子,丰田汽车的创始 人,毕业于东京帝国大学。为了完成父 亲临终前的遗愿。1932年4月份,丰田 喜一郎托人买了雪弗兰发动机开始仿 制,经过整整2年的艰苦努力,第一台 使用发动机制造成功了。1935年10月完成了第一台 A1型轿车的试制工作。
11
22
5、加工过程本身的浪费 亦称‘过分加工的浪费’一方面指多余的加工, 另一方面指过分精确的加工。带来以下现象: 需要多余的作业时间和辅助设备; 生产用电、气、油等能源,材料及工具耗用过量 的浪费; 管理工时的增加; 造成产品功能过剩,加工工时过多,设备损耗增 加的浪费;
23
6、动作的浪费 由于工位布置、操作顺序的不合理,造成使用工 具工具和操作方法不得当,产生的浪费。带来以下 现象: 单手、双手空闲; 作业动作不连贯停顿; 步行过多、转身角度大; 寻找东西; 重复不必要的动作
32
8、合理化建议
合理化建议主要是针对班组的。 班组的职能:①质量;②成本③合理化建议④安全⑤培训
33
9、推进TPS的方法
㈠以人员为中心,以现场为依据进行分析,最后形成改善 点; ㈡在操作过程中发现的问题详细记录。分析最好是在现场 进行,将记录内容现场操作一遍。 ㈢班组长或员工对现场的观察,用合理化建议的方式反应 出来。
TPS培训课件

所谓降低本钱
4
在消费≥需求的市场下,应该思索 销售价钱是由顾客决议
TPS的基本方针
利润
①降低本钱,利润添加 ②降低售价,添加利润
降低售价
①
② 降低本钱
售价相反
现状 利润确保方案 = 企业的努力是必要的 =
①
②
TPS的基本方针
5
降低本钱…推进彻底消弭糜费的活动
〔1〕本钱的构成
其他 动力 劳务费 零件推销 资料
间)T.T是每月会发作变化的
规范作业
◎以人的举措为中心,用没有MUDA(不用要)的 顺序有效地消费的做法.
◎规范作业三要素 -----T.T -----作业顺序 -----规范手持 (工序内最少限制的待加工品)
后工序支付
• 看板方式
• ----信息流:从最后一道工序向上 传递
• 么,
1)指示何时消费,何时搬运什
ANDON
应用ANDON完成就近可视化
36
信号机
运用三色,改换颜色
人流 车流
调好!!
停下
留意 行走 商定俗成〔规范〕
大家都知道的,所以经过颜色的改动来停止有规那么活动
假设发作缺点或许由于不守规那么的人在招致
发作事故,十字路口就会发作混乱
可视化要实现简单易懂
集中表示型ANDON
37
停线 呼叫
○○车间
规范手持
效果
①人从4人
2人〔▲省2人〕
②库存方面消弭工序间库存啊
制造方法中存不存在糜费直接招致本钱差的发生
〔3〕关于糜费(MUDA)的思索
7
①糜费的定义…一切不发生附加价值的东西
正味作业… 发生附加价值的作业
作业
TPS讲义

提 问
有怎样的浪费 有怎样的浪费?
提 问
ムダの種類 ムダの種類
最坏的浪费是什么? 最坏的浪费是什么
工序内的各种问题 工序内的各种问题点&浪费 种问题点 全都被隐 全都被隐藏起来了
浪 费
问 题 点
浪费 ムダ
消除制造过 消除制造过剩
把工序内的各种问题点 把工序内的各种问题点 种问题 &浪费显在化
如果无论 如果无论在谁眼里都是浪 费的话就清楚表明
中间品
浪 费
B先生
浪 费
运 搬 浪 费
浪 费
完 成
C先生
完成品
使工序流动起来的生产方法
1工序 2工序 3工序
1个个生産完成品 个个生産完成品
完 成
半成品
生产周期短
材料 A先生 B先生 C先生
完成品 完成品
6
提 问 生产量减少(减少1/3)、达不到3个人到定时 量减少(减少1 )、达不到3 达不到 到定时 (7.5H)的生产量。如果2个人做的话,达到到定 H)的生产 如果2 做的话 H)的生 的生产 能省1 时的生产量。能省1个人吗? 运 搬
2.作业顺序
・在既加工部品又进行组装的情况下,技能员搬运物品,在机器上进行 在既加工部品又进行组装的情况下,技能员搬运物品, 安装,卸除,组装部品的顺序。 安装,卸除,组装部品的顺序。
3.标准手持
・为了能在相同的顺序下重复进行作业而必要的最少限度的压线用工件
标 准 作 业 和 改 善
“没有标准的地方就没有改善 ” 没有标准的地方就没有改善” 没有标准的地方就没有改善
標準作業に づく改 標準作業に基づく改 善
(2) 半成品在库的递减
减少工序内的半成品, 减少工序内的半成品,把接合改善的慢性不良和故障显在化
TPS基础知识课件

一般防错装置具备如下功能: • 作业忘记或失误时,制品无法装入 机器的模具内. • 发现产品不良,机器无法启动. • 加工失误时,在滑道上就会停止,不 会流到下一个制程. • 加工失误时,警报器或蜂鸣器会启 亮鸣叫. • 即使加工异常的产品流入生产线, 也不会被误装.
后工序必须在必需的时候,只按必须的数量, 从前工序领取必须的物品。 前工序仅生产被后工序领取数量的物品。
不合格品绝对不能送往后工序。
必须把看板枚数减小到最小程度。 看板必须适应小幅度地需求变化。
五、实现“准时化生产”的方式
1、看板方式——传递生产信息的工具, 实现准时化生产的有效手段。 2、后工序取用方式——拉动生产 3、单个流动方式——一个流
三、成本取决于生产方法
1、成本构成
在成本构成的各要素,各公司没有太大的 差别。只有制造工艺的差别会产生成本的 差别。
2、降低成本的办法 制造工艺不同,可以减少人员,降低在库。 丰田生产方式从多方面研究“生产技术”, 即产品的制造方法,探求制造方法的合理 性,彻底消除浪费,降低成本。
• 因此,丰田生产方式的基本思 想是通过改善活动彻底消除隐 藏在企业里的种种浪费现象.
这里的“自働化”,并非是所谓的“自动化”.而是 在“动”字旁边加“人”字的“自働化”. • “有人字旁自働化机械”的意义: 在丰田称做“有自働停止装置的机 械”.在丰田的任何工厂,几乎全部 的机械设备,不管新机械或是旧机 械均附有自动停止装置. • “自働化”有排除生产现场中制造 过多的重大浪费与防止生产不良品 的功能.
被取走的那部分就可以了.这种方
式被称为“拉动方式”.
• 准时化的基本原则 ⑪根据需求量确定生产节拍. ⑫用看板进行后工序领取的方式,实 现拉动式生产. ⑬按流程生产.是一个一个地按顺序 进行生产,根据后工序的领取状况 推进工序的进展的机制.
TPS系统知识讲座(WORD版)

DCS(HENEYWELL)系统知识讲座第一节H ENEYWELL系统概况美国HENEYWELL公司产品目前应用最广泛的是TPS系统,并且作为中油大赛中DCS的参赛项目之一。
我们以TPS系统为基础讲解,在过程中涉及到的TDC3000与TPS系统不同的地方会着重作出说明。
首先对仪电培训基地DCS(HENEYWELL)系统作一简单的介绍,该系统是由104厂拆回的一套TDC3000的系统,型号及版本为MICRO—TDC3000(R400)。
该系统保存完整,共有三个操作站,一个控制站,IOP卡件29块,其中HLAI(高电平模拟量输入卡)10块,AO(模拟量输出卡)9块,LLAI(低电平模拟量输入卡)2块,LLMUX(多路低电平模拟量输入卡)3块,PI(脉冲量输入卡)1块,DI(数字量输入卡)3块,DO(数字量输出卡)1块。
第二节硬件的组成及连接一、TPS和TDC系统结构图如下:TPS系统典型配置(以催化裂化装置为例)见图1TDC系统典型配置(以培训基地DCS为例)见图2TAPTAP图1 TPS3000典型配置图LCNA LCNBHMLM GUS3GUS2GUS1NIMNIM UCNBUCNAUCNBUCNA75终端电阻TAPTAPUCN INTER MODULE IOP 卡IOP 卡IOP 卡IOP 卡IOP 卡IOP 卡IOP 卡IOP 卡IOP 卡IOP 卡PAOY22AO (16)IOP 卡PALM02RTD (32)IOP 卡PLAM02TC (32)IOP 卡PAIH03AI (16)高性能I/O LINK 卡COM/CON PRO通讯/控制处理器-+FTATAOY22 AO(16)16132-31+......2-1+1A 1B 1C .........32A 32B32C132TAMR03 TRD(32)FTAT1A T1B ......10P 11+116TAMT03 TC(16)FTAFTATAIH12 AI(16)16112-11+10P .........3-2+1P 输出安全栅输入安全栅调节阀(4-20mADC)热电阻热电偶(MV)变送器(4-20mADC)312442卡件供电TB3TB2TB1TAPTAP图2 典型配置图(以基地DCS 为例)LCNA HMUS2US3US1NIMNIM UCNBUCNAUCNBUCNA75终端电阻TAP TAPIOP卡IOP卡IOP卡IOP卡IOP卡IOP卡IOP卡Advancedcontrol Advanced I/O Link interfaceIOP卡AOIOP卡LLMUXIOP卡LLAIAdvanced CommunMode m-+FTATAOY22 AO(16)16132-31+......2-1+1A 1B 1C .........32A 32B32C 132TAMR03 TRD(32)FTA13......IN1IN8TAIL02 AI(8)FTAFTATAIH02 AI(16)161.........TB3TB2TB1输出安全栅输入安全栅调节阀(4-20mADC)热电阻热电偶(MV)变送器(4-20mADC)LCNB二、硬件说明结合配置图,对各个部份作出说明● GUS (全局用户操作站):TPS 系统的人机接口,用于整个LCN 系统的信息访问。
TPS讲义
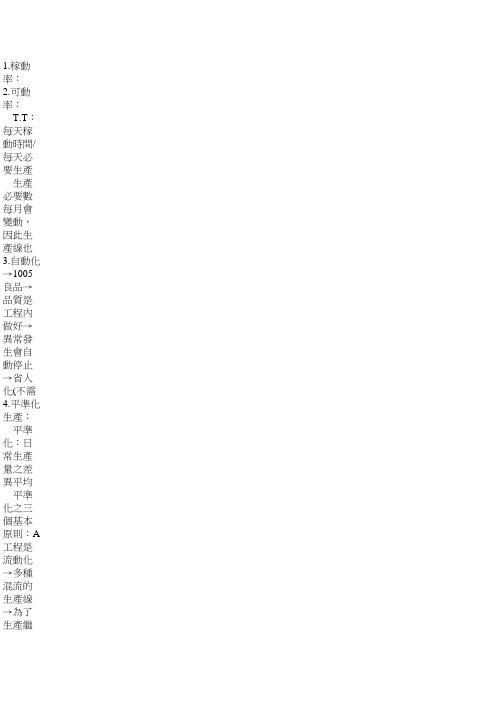
1.稼動率:
2.可動率:
T.T:每天稼動時間/每天必要生產數
生產必要數每月會變動,因此生產線也要隨之變動。
3.自動化→1005良品→品質是工程內做好→異常發生會自動停止→省人化(不需人工手動停止)
4.平準化生產:
平準化:日常生產量之差異平均化
平準化之三個基本原則:A工程是流動化→多種混流的生產線→為了生產繼續不斷的不同製品,需
要迅速對應之『人、物、設備』←流動化工程的三要素:物、人、設備物→一個流→加工物不是批量生產,而是一個一個流動(製品的加工順序不變)
→同期化→要做到工程的同期化
人→持多工程→作業者在節拍時間內可擔當範圍的工程→站立作業
→多能工
B以必要數來決定T/T(節拍時間)
C領取時由後工程向前工程領取。
TPS管理知识讲座3
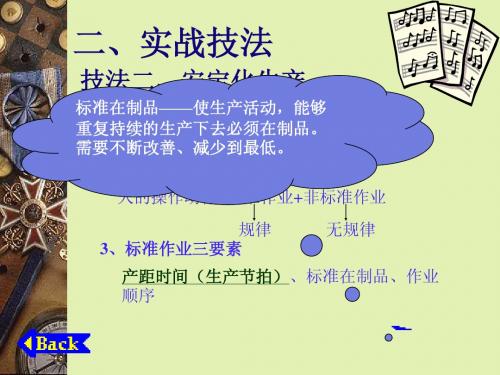
技法二、安定化生产(一)、人员的安定1、人员的安定取决于标准作业2、区分标准作业与非标准作业人的操作动作=标准作业+非标准作业规律无规律3、标准作业三要素产距时间(生产节拍)、标准在制品、作业顺序标准在制品——使生产活动,能够重复持续的生产下去必须在制品。
需要不断改善、减少到最低。
技法二、安定化生产(一)、人员的安定(续)4、少人化有利于生产的安定少人化是指要以顾客的需要量,用最少的人数最经济的成本来生产产品劳动生产率=需要数量/人数需要数量200台/10人=20台/人,需要数量200台/8人=25台/人,说明人员减少,劳动生产率提高了。
技法二、安定化生产(一)、人员的安定(续)4、少人化有利于生产的安定(续)培养多能工作业简单——改善作业动作,使之简单容易操作适当指导——现场管理人员标准作业——一目了然,易于新人培训制定计划——多能工技能训练计划表技法二、安定化生产(一)、人员的安定(续)5、由“水蜘蛛”来作非标准作业将非标准作业工作集中在一个头脑灵活、动作迅速的人身上,编制成标准作业。
进行此项作业的人是水蜘蛛。
实现水蜘蛛作业的好处:作业员的动作品质提高,作业时间缩短,作业速度稳定,生产线持续进行作业。
作业员从装配工——装置工有助于多能工化及行人的培训。
技法二、安定化生产(二)、设备的安定1、名词稼动率=实际负荷时间/最大负荷时间*100%稼动率是衡量设备运行效果的指标可动率=有效工作时间/需要工作时间*100%可动率是衡量设备运行效率的指标TPS不追求高稼动率,追求高可动率二、实战技法技法二、安定化生产(二)、设备的安定(续)2、提高可动率,该动则动,该停则停设备损失时间越少,可动率越高,设备越安定平稳。
目标:零故障首先要转变观念,不能只有修理没有保全,稼动率和可动率没有分别,一定要有救火的意识,打破操作者管操作,维修工管维修的界限。
3、全员自主保全(TPM)预防保全+改良保全+保全预防+事后保全二、实战技法技法二、安定化生产(二)、设备的安定(续)自主保全清扫点检——设备本身+死角(油箱盖、电机罩、油封等),发现不良进行改善。
TPS精益生产方式培训

TPS精益生产方式培训◆讲课内容:TPS不能元样照搬的导入所有企业。
但是,结合「均衡化生产(JIT)「自働化」、「看板系统(无库存生产)」的基本思想,根据自身企业的特色・特征,建立起一套自成体系的「独自的生产方式」是有必有的。
从顾客,外部供应商的对应;到以批量生产为前提的工程对应等等各种各样的情况下,如果都能按「独自的生产方式」去做的话,就会建立起一个强大的制造工程。
◆课程大纲:1.开始●对制造部门的期待●改善过的制造工程部门所带来的效果2.「独自的生产方式」必要性3.丰田生产方式(以下称TPS)概要●TPS的概念●TPS的基本思想「卖价」、「原价」、「利润」的理论顾客第一的生产使人充满干劲的工作●TPS的目的●TPS的构成―两大支柱―◇均衡化生产(JIT)◇自働化●浪费与改善●看板(无库存生产)系统◇看板系统的直接作用◇看板系统的类型◇看板系统的使用例◇看板系统的效用●现地现物主义●维持与向上●生产工程中的主人公4.自社流生产方式(TPS)导入的实际●自社的情况●导入方法●导入事例◇顾客、外部供应商的对应◇从复数的单项工程到工厂的合理化看板系统机能的窍门外部供应零部件交货用看板系统的简单化9精益生产与6SIGMA管理课程目标:了解精益生产的基本概念及其改善的思想;如何认识现场的浪费及排除浪费;了解6σ的基本理念及运作模式;6σ的推进对企业的巨大收益;精益生产与6σ如何做到完美结合;课程纲要:Unit 1 精益生产的基本理念及基础了解企业竞争主题的改变精益的基本概念精益思想的基本理念精益思想的哲理性降低成本的思路以满足客户的需求为导向为什么库存是罪恶彻底消除一切浪费改善的基础Unit 2 精益生产方式的介绍如何降低成本真效率与假效率最大的浪费是什么挑战传统的生产方式拉动生产的方式实施条件供应链的管理精益生产的评价指标推动客户、供应商的良性循环理想的同期化生产模式Unit 3 六西格玛的介绍6σ的介绍6σ的哲理性6σ起源与成功开展6σ的流程改进方法如何推进6σ6σ成功的关键因素建立高效团队成功的项目管理6σ对未来的巨大挑战Unit 4精益生产与六西格玛的完美结合精益生产推行中的困惑为什么精益生产与6σ能够完美结合企业管理中的完美模式实现管理的层次变化生产力的增强提升企业的竞争体质Unit 5如何在你的工厂开始打造超级企业起步推行精益生产的要诀推行的基本步骤著名企业推行经验(二)工业工程篇工业工程(IE--Industrial Engineering)是对人员、物料、设备、能源和信息所组成的集成系统进行设计、改善的一门学科。
TPS讲稿
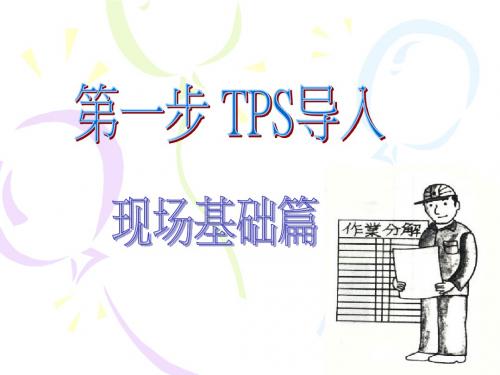
6.方便地观察到浪费
怎样的现场才能方便地观察到浪费?
客户要的是成品,我们要控制成品的数量,通 过后一道工序去前一道工序去工件的方式,就 同时控制了所有的工序产生不必要的积压品, 一定要作到超过规定的积压就停!最后,所有 的异常只会引起一个结果-----停工,所有的 作业人员和管理者就会马上意识到出问题了, 管理者就会马上赶到出问题的地方解决问题, 作业员也会积极配合。
經濟動作
1.機器與人的作業 的不明確 2.毫無意識地實施 了不產生附加價值 的動作 3.生產布局不合理 4.教育訓練不充分
1.生產工序流程化 2.U字型設備配置 3.教育和訓練經濟動作原 則,並且堅持貫徹這一 原則 4.善於發現和消除表面作 業 5.根據是否會產生附加價 值研究相應對策
續表
浪費
內容
續表
浪費
內容
種類
對策
加工 本身 的無 效勞 動和 浪費
1.為不必在的 工序和不需要 的作業增加人 員和工時數 2.生產性低下 3.次品增加 4.按照過去的 習慣操作,不 加以改善
1.生產工序設計不合 理 2.作業內容分析不足 3.對人和機器功能的 分析不完全 4.處理異常停止的對 策不完善 5.PM不完善 6.夾具工具不完善 7.標准化體制不完善 8.員工技術不熟練 9.缺乏原材料
產品質量
3.制訂培養相關意識的
3.檢查中心的管理檢查 對策
標准不完善(特別是功 4.通過不斷問為什麼的
能檢查)
對策,防止問題再次發
4.教育訓練體制不健全、 生
顧客對於產品質量要求 5.引進預防錯誤的措施
過多、缺乏標准作業管 6.確立產品質量保證體
理
制(ISO90001)有效融
合
- 1、下载文档前请自行甄别文档内容的完整性,平台不提供额外的编辑、内容补充、找答案等附加服务。
- 2、"仅部分预览"的文档,不可在线预览部分如存在完整性等问题,可反馈申请退款(可完整预览的文档不适用该条件!)。
- 3、如文档侵犯您的权益,请联系客服反馈,我们会尽快为您处理(人工客服工作时间:9:00-18:30)。
创造出独特的“丰田生产方式”(TPS)。靠着这种方
式,日本迅速发展了本国的汽车工业,并从70年代起,
以质量高、耗能少、价格低、污染少的优势产品,大
量进入美国市场。
计 No1 划 生 产 库 方 存 式 No2 生 产 流 程 库 存 库 存 No3 库 存
100
利益 其他
•以设备的泛用 化提升设备家 动率(投资减 少) •适合多种少量 能源费
80
折旧费 能源&副资材 劳务费 购入零件费
60
•削减设备台数 以紧排方式减 少能源费
•物:每一工程都得要保持库存 •人:配置3名作业者
现场管理的工具
• 目视化:现场管理的基本工具
五、实施TPS的基础——现场管理
现场管理的基本任务
• 安全:使现场不发生伤害和疾病的管理和活动 • 环境:减少废弃物、降低能源消耗的管理和活动 • 质量:不制造不良的管理和活动 • 生产:保证准时化生产和准时交付的管理和活动
• 设备:保证设备在必要时可用的管理和活动
6、对TPS的最新认识
• TPS之所以被称为丰田生产方式,是继泰勒制(Taylor System )和福 特制(Fordism)之后的第三个生产管理里程碑。他继承了泰勒制的优 点,创造了标准作业前提下,在福特式的流水生产线上,如何低成本地 进行小批量多品种的规模化生产。 • TPS是一种制造技术,它不是简单的工业工程(IE),更具有深刻的管理 内涵和理念的外延。也是员工能力的具体体现。与传统生产技术的区别, 在于它不仅仅是一种技术,同时也是一种管理,一种意识,一种思维方 法,一种文化。在追求持续改善这一管理本质的前提下,最大限度地发 挥每个员工智慧,提高思考力、执行力和创造力。
2、生产线 的目视化
生产线 「异常」 之显在化
明灯化
明灯化
3、作业点 的目视化
加工时「加工 点」的目视化
加工点之 透明化
流量之 透明化
现场管理的基础——4S活动 整理——将没用的拿走
分开:(有用的和没用的、必要的和不必要的、有价值和无价值的) 清除:没用的,不必要的、没附加值的坚决离开现场
整顿——将有用的放好
TPS基础
中国第一汽车集团公司 姜连志
一、引言
• 提出的问题:丰田为什么
– 半个世纪没有亏损 – 利润相当于别人的三倍 – 能造就出公认的品质
• 直接的答案:实施了TPS
– 别具一格的生产方式
• 深层的原因:理念打造了团队、过程保证了结果
– 共同的The Toyota Way的价值观体系 – 共同的解决问题的工作方法和工作意识 – 全员参与(非少数精英)的文化理念
标准作业的三要素
1)生产节拍:组织生产的速度
生产节拍是指生产1个零件或1台份需要多长的时 间值 ( 总之 生产的速度 = 销售的速度 )
• 成本:把握现场使用量和不断消除浪费的管理和活动 • 人事:创造强状的职场,培育人,活用人附:现场Leabharlann 理的结构 育人的活动生产三要素
人 生产过程
有价值的商品
质量Q
物
交货期
D
设备
成本C
管理是必要的,但更重要的是改善活动
「目视管理」的活用
「目视管理」的内容
目视化项目
1、管理状态 的目视化 目 的 方针管理之 「异常」 目视化方法 部门管理板 内 容
+
利
益
=
价
格
(发生的成本)
(必要的利益)
(由企业来决定)
・价
格
-
成
本
=
利
益
(由市场决定)
(发生的成本)
(做为结果的利益)
商品的价格是由顾客(市场)来决定的, 利益包括社会贡献,是由企业生存的必要性来决定的 只有成本是通过企业努力可以自己把握的要素
制造方法会改变成本
成本构成〈制造成本〉
120
制造方法改善例 〈原来的生产方式〉
7、比较的结论
• 精益生产方式=TPS(部分) • 精益思想≠ The Toyota Way
形 神
从长期的观点看:全世界所有学习丰田的企 业,都只注重了“形”,而忽略了“神”,所以 都没有取得和丰田一样的管理业绩。
二、丰田生产方式的基本概念
TPS
实现没有浪费的制造过程
准 时 化
自 働 化
安全、品质、成本、生产、人才育成
5、从TPS到The Toyota Way
• 70年代中期后,丰田TPS获得了巨大的成果。为世人瞩目 • 在此基础上,丰田还在不断地完善自己。随着在全世界的 发展,将国内员工形成的管理思想、工作方法和文化理念 等内容向海外的工厂注入,丰田人开始自己总结自己,终 于在2001年,推出了代表丰田成功过程的“The Toyota Way”及一系列有关能指导员工工作和提高员工能力的教材, 知识和方法的文献。并将“The Toyota Way”作为丰田一 切工作的原点。
自働化:遇到异常,自动停止
基本原则1 出现异常自动停止 出现异常能知道 基本原则2 人、机工作的分离
改变一人一机的做法(实现一人多机) ——在高效、廉价生产方面下功夫
五、实施TPS的基础——现场管理
现场管理的基础
• 5S:管理物的基本活动
• 自主保全:维护设备的基本活动
• 标准作业:对人的作业行为的基本管理
3、精益生产方式的形成
丰田的成就引起了西方国家的关注。 80年代中期,美国麻 省理工大学(詹姆斯 • P • 沃麦克和丹尼尔 • 鲁斯等)用5年的
时间,研究了日本的做法,把丰田生产方式称之为“瘦的生
产”,译作《精益生产方式》 。认为世界工业将进入日本所创 造的精益生产时代,这是管理上的又一次革命。 90年出版《改变世界的机器》一书。
消除浪费≠“节约”
1、什么是浪费
纯工作:可以提高附加价值的行为 • 组装零件 • 焊接零件等 行为发生了,但根本不需要 • 等待 • 不合格件的返 修等
A
人的 人的 行为 行为
C 浪费
C
B
必要的行为:没有附加价值的行为, 但在目前条件下还必须得做 • 搬运零件 • 包装零件等
B
改善的目的就是要不断地 消除C,减少B,增加A
你能识别是那些浪费吗?
四、丰田生产方式之基本原则
基本的想法
1. 不降低成本、 就无法提高利 益 2. 以制造方法改 变成本 3. 彻底排除浪费 4. 追求真正的效 率(更低成本 做出良好品质 的商品)
TPS 2大支柱
准时化 JIT
〈基本原则〉〈具体化的道具· 方策〉 物:同期化 人:多能工化 设备:工程顺序布局 标准作业 三要素 • 节拍时间(T/T) • 作业顺序 • 标准中间库存数 看板方式 · 搬运· 备料· 店面构成
放置:定址、定量、定时、分门别类 。 易于取放、“0”秒拿到
清扫——放好的东西保持完好
保持:放好的东西保持随时可用
清洁——养成一个好习惯
形成:3个S形成习惯,长期保持、自觉实行、雷打不动
素养——成为一名好员工
培养:守规则、使命感、修养(打造人品)
在 忙 , 你 就 不 刷 牙 洗 脸 了 吗
现场管理的基础——自主保全活动
异常会停止 异常会知道 〉设备
平准化 1. 工程流动化 2. 以必要数决定 节拍时间 3. 后工程引取
目视管理
100%良品 1. 品质在工程内 做好 2. 省人化
自働化
· 灯号表示· 防错装置 人的工作与机械的 工作要分开
TPS的两大支柱
• 准时化:在必要时间按必需的数量,生产必要的合格产品,
基本原则1 工序流程化(水流不能断开) 基本原则2 根据需求数制定生产节拍( 基本原则3 取货制____后道工序领取 (1、看板方式 2、搬运)
• 问题: 应该如何增加利润?(增加利润的着眼点在哪里?)
– 成本主义:成本是刚性的,不可能降低。 增加利润只能靠扩大规模。 – 降低成本:成本是可以降低的。降低成本 就能增加利润。
3、关于目标成本的思路
・价 格 - 利 益 = 成 本
(由市场决定) (必要的利益) (达到的成本)
○ × ×
・成
本
過剰に加工する事
3、最大的浪费——生产过剩 • 潜在的浪费——不易识别 • 多重的浪费
– 隐藏着等待和动作上的浪费 – 增加了搬运和库存的浪费 – 伴随器具、能源和资源的浪费等等
4、库存是万恶之源
“库存的浪费” 的浪费
寻找浪费
寻找浪费
他在做什么? 有浪费存在吗?
寻找浪费
寻找浪费
寻找浪费
1、丰田生产方式的起源
丰田佐吉提出
丰田佐吉
“赋予设备以人类的智慧。”
如果出现异常就立即停止
[G型自动纺机]经线、纬线在断线的瞬间动力自动停止。
丰田喜一郎提出 “改变必须有仓库的观念。” 在必要的时候,把必要数量的各种必要的零件送到生产线 旁边是最理想的。 推动式生产 拉动式生产
丰田喜一郎
2、丰田生产方式的发展
标准作业 \ 5S \ 自主保全
1、丰田生产方式追求的目的
最终目的:
“以彻底消除浪费降低成本来增加效益”
___用更低的成本,在必要时间按必需的 数量,生产必要的合格产品。
推进TPS的同时,必须输出以下三个成果:
对数量的管理、质量保证、尊重人性
2、成本主义与降低成本的区别
确保利润最大化是企业活动的目标之一 确保利润可以保证企业继续生存及职工的生活。
2、生产现场常见的七种浪费
機械が回っていて手が出せない 状態 造った物が不良になったり、手直しを 必要とする物・・・コストアップ