板卡驱动CH38XDRV安装说明书
德克德车载存储系统安装指南说明书
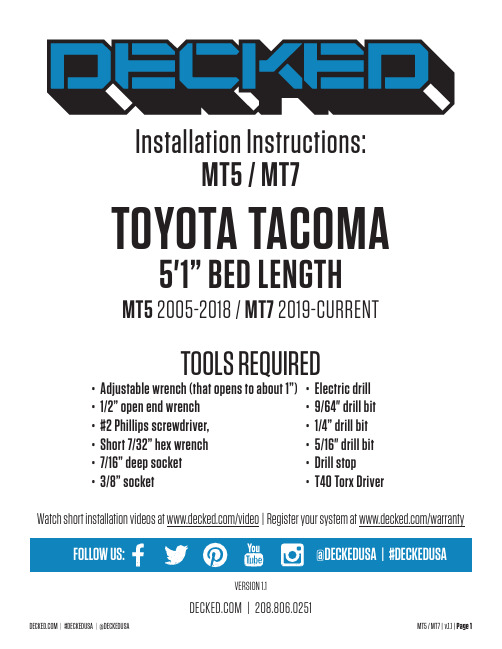
Watch short installation videos at /video | Register your system at /warrantyInstallation Instructions:MT5 / MT7TOOLS REQUIREDTOYOTA TACOMA5'1” BED LENGTHMT5 2005-2018 / MT7 2019-CURRENTVERSION 1.1 | 208.806.0251• Adjustable wrench (that opens to about 1”)• 1/2” open end wrench • #2 Phillips screwdriver, • Short 7/32” hex wrench • 7/16” deep socket • 3/8” socket• Electric drill • 9/64" drill bit • 1/4” drill bit • 5/16" drill bit • Drill stop • T40 Torx DriverCONTENTSDECKED carton LEFT deck half - 1RIGHT deck half - 1Center vert - 1Cabside vert - 1Drawer - 2Left ammo can - 1Right ammo can - 1Left stud - 1Right stud - 1Ammo can lid - 2C-channel - 2Ruler - 1Hardware box - 1Bottle opener - 1Torsion brace - 1Hardware box - unbagged components(inside DECKED carton):Shims - 4Weather strips - 2HARDWARE box - bagged componentsPREP-MT5 or MT7 - 1S1 - 1S2 - 1N1 - 1J4 - 2DRAWER 1 - 1DRAWER 2 - 1WHEELS - 1FINAL MID - 1PREP-EXTRA - 1MS WASHERS - 1(MT7 ONLY) TACOMA TD - 1▼ HEY! TORQUE BOY: READ BEFORE YOU INSTALL DECKED ▼1. DON’T be an idiot read the instructions.2. DON'T over tighten bolts, get em' hand-tight.3. DON'T use power tools.4.I f you don't follow directions and do use power tools:1). Set clutch at a very low setting. 2). If you blow it, see NOTE.*NOTE* T wo extra threaded inserts are included in BAG PREP-EXTRA . That’s all you get. The inserts will replace anystripped inserts in the tailgate ammo cans, but NOT THE CENTER VERT, so hand tighten until snug only! You can also screw the inserts back in if dislocated. There is a straight screwdriver slot on the underside of the insert.5. Start all bolts with fingers to avoid cross-threading6. DON'T over tighten J-hooks during installation. Make 'em good and snug enough to keep the system from moving in the bed.7. Nice job if you’re still reading .Prevent abusive, expletitive-filled language, watch our detailed installation videoor give us a call. We’re happy to help!208.806.0251 | /INSTALLVIDEOPREP BED: SHIMSNOTE: You will need to grab a pal for this step (or have incredibly long and flexible arms).• Remove top rear factory compartment bolt from the passenger side with a T40 Torx Driver. Keep bolt.• L oosely attach passanger side tailgate bracket with factory bolt in top hole. Make sure the tie down opening is angled toward the driver, not the tailgate ; BAG PREP-MT5 or MT7.• Align bracket so it's parallel with vertical edge of compartment. Tighten factory bolt at last!• Using the bottom hole in bracket as a guide, drill a 5/16" hole with a 1/2" drill stop through compartment and bed wall.• I nstall a 1" bolt through the bracket and bed wall. Install 1" washer and flanged nut and tighten securely ; BAG PREP-MT5 or MT7.• R epeat driver side unless you don't have a driver's side cubby. If not, follow the instructions for driver's side on next page. NOTE: On passenger side ONLY, you will need to add a washer; BAG PREP-MT5 or MT7... We know it's strange, trust us.(FOR TACOMAS WITH NO DRIVER SIDE TAILGATE CUBBY)NOTE: Disregard this page if you HAVE a driver's side tailgate cubby.• R eferencing dimensional info in DETAIL A mark hole locations and drill (2) 5/16" holes (with drill stop set at .62").• R eferencing DETAIL A install J-hook mounting bracket as shown with bolts, backing plate and nuts. Tighten bolts securely. BAG PREP-MT7, BAG TACOMA TD.DETAIL A DRIVER'S SIDE ONLYHOLE DRILLINGBOLT INSTALLATIONDRILL STOP.62"7.5" TO BOTTOM OF BED 5.75" FROM REAR OF BEDBOLTPLATEDETAIL AASSEMBLY: CENTER VERT + CABSIDE VERT NOTE: Perform the next few steps on a flat surface like a garage floor.• Attach center vert to cabside vert with four bolts. Alternate to tighten;BAG S1.ASSEMBLY: LOOSELY ATTACH STUDS (YUP)•LOOSELY attach studs to cabside vert with six bolts; BAG S1.ASSEMBLY: ALIGN & TIGHTEN STUDS (YUP) NOTE: This step ensures the studs are properly located before tightening bolts. It's important.• Place ammo cans to support tailgate end of deck panels.• Lift deck panels on center vert + stud + cabside vert assembly.• Slide studs around L-R until deck panels are seated.• DETAIL A: Loosely secure four bolts to hold decks onto studs; BAG S1.• Now you can securely tighten the bolts that hold the studs to the cabside vert.• Unbolt deck from studs, remove deck panels, save bolts, remove ammo cans and set aside for later assembly.STUD BRACKETTOP HOLECABSIDE BRACKET (GREY)STEP 1STEP 2NOTE: Make sure centerline arrows on cabside vert are aligned with your centerline mark (blue).STEP 3KEEP LOOSETIGHTENTHREE3 1/2"BOLTS3/4" BOLTCAB➡➡CABASSEMBLY: BRACKETS + MOUNTING• STEP 1: Securely attach stud bracket to driver side stud using three 3 1/2" bolts and three flanged nuts; BAG PREP-MT5 or MT7.• STEP 2: Loosely attach cabside bracket to the top hole in stud bracket with 3/4" bolt and flanged nut; BAG PREP-MT5 or MT7. KEEP LOOSE.• Repeat STEP 1 and STEP 2 on passenger side.• STEP 3: While supporting both ends, lift center vert + stud + cabside vert assembly in truck bed.FLANGED NUT➡CABFLANGED NUTSRECOMMENDED TORQUE: For all fasteners - 27 in-lb.INSTALL: CABSIDE BRACKET DRILL • Place driver side cabside bracket flush against truck bed wall, now tighten securely to stud bracket.• While keeping assembly on centerline, drill three 1/4" diameter holes into bed using cabside bracket as a guide (green holes). Make sure to use a drill stop set to 1/2" depth.1/4” DRILL BITDRILL STOP1/2”RECOMMENDED TORQUE:53 in-lb.INSTALL: BACKING PLATENOTE: If your pal left, clank some cans together to get them to come back.• Install three 1" bolts through holes in cabside bracket and pickup bed; BAG PREP-MT5 or MT7.• Play Rock Paper Scissors with your pal. The loser needs to hold the backing plate inside the wheel well and attach three flanged nuts; BAG PREP-MT5 or MT7. Securely tighten.• Repeat passenger side.INSTALL: C-CHANNEL• Loosely place driver side ammo can at tailgate corner of bed. The axles should be on the tailgate side of the truck.•INSTALL: DECK HALVES• Loosely place driver side deck panel on driver side stud, center vert and ammo can.• Shift tailgate ammo can forward, rearward, L-R, as necessary to align with fully seated deck panel.• Loosely assemble:• Five bolts (without washers) through deck panel into center vert; BAG S1.• Four bolts with nylon and rubber washers installed in order shown in DETAIL A through deck panel intostud; BAG S1,BAG MS WASHERS.• Eight bolts with nylon and rubber washers installed in order shown in DETAIL A through deck panel into tailgate ammo can; BAG S1,BAG MS WASHERS.• Tighten all S1 bolts.•Securely tighten driver side C-Channel/ammo can nut and bolt.• Repeat passenger side (make sure you don't forget to securely tighten passenger side C-Channel/ammo canINSTALL: J-HOOKS•Loosely assemble driver side J-hook assembly in order shown through tailgate side hole in ammo can; BAG J4.• Repeat passenger side.DRIVER SIDE AMMO CAN PASSENGER SIDE AMMO CANKEEP LOOSEKEEP LOOSEDRAWERS: BRACKETS + WHEELS • E ach drawer has a left and a right bracket. Bolt brackets into place via bottom two holes in bracket with 3/4"length bolts. Use the 2" length bolt for the upper cabside wall hole in bracket; BAG DRAWER 1.• Install a tube brace in each drawer with two 3/4" length bolts; BAG DRAWER 1, BAG DRAWER 2.DRAWERS: AXLE WHEELS + WEATHERSTRIPS • Slide narrow drawer into driver side drawer cavity. NOTE: It is easier to fully install narrow drawer first.➡FINAL STEPS: TORSION BRACE + BOTTLEOPENER• S lide torsion brace under center vert and tailgate ammo cans.NOTE: If you jumped the gun and tightened the J-hooks when installing, loosen them.• L oosely install:• T wo bolts with nylon washers through the end holes in torsion brace into ammo cans; BAG S1.• T wo bolts with nylon washers through the bottom bottle opener holes and torsion brace into center vert; BAG S1.• Two 1/2" length bolts through upper holes in bottle opener into center vert; BAG FINAL MID.• Align bottle opener to edges of center vert and tighten four bottle opener bolts.• T ighten end bolts into tailgate ammo cans.• F inally.....Tighten the J-hooks! DO NOT OVER TIGHTEN, just make snug. Make sure the gap between the sidewall of the bed and the deck is equal on both sides.9/64” DRILLBITDRILL STOP1/2”FINAL STEPS: AMMO CAN LIDS•DETAIL A: Ammo can lids are driver (marked L) and passenger (marked R) side specific.•DETAIL B: Holding lid in orientation shown, insert tab on tailgate end of ammo can lid and push the cabside end of lid down to secure. Don't be afraid to give'r the Fonzi to close, it's rugged.• Insert lock hole plugs, unless you ordered drawer locks! Install drawer locks now (instructions with locks); BAG FINAL MID.IMPORTANT: Grab your favorite beverage, crack 'er open in the bottle opener and christen this ship! You did it. Immediately post a photo of your significant other, child or canine (in no order of significance) a ppreciating your accomplishment. Add hashtag #DECKEDUSA | @DECKEDUSA .DETAIL A DRIVER SIDE AMMO CAN LID PASSENGER SIDE AMMO CAN LIDDECKED 3-YEAR LIMITED WARRANTY(a.k.a. LEGAL MUMBO JUMBO)DECKED LLC warrants to the original purchaser of this product that the product will be free from manufacturing defects in workmanship and materials for a period of three (3) years from the date of the original purchase. If within three (3) years from the original date of purchase this product fails due to defect in materials or workmanship, DECKED LLC will replace any defective part at its option.The original purchaser must contact the DECKED LLC customer service team and provide a description of the defective part, including digital pictures if requested, with the original purchase documentation as validation of warranty coverage or have previously activated their warranty online.This warranty DOES NOT cover or apply to:• Damage to the product due to misuse, mishandling and abuse.• Products not used in accordance with the manufacturer’s instructions or recommendations.• Product not assembled or installed according to manufacturer’s instructions.• Normal wear and tear.•U ndeclared damage to the system during shipping, acts of God. In addition, consequential damage and incidentaldamages (including lost time) such as damage to persons or property are not covered under this warranty.REGISTER YOUR PRODUCT FOR ANY FUTURE WARRANTY NEEDS. /REGISTER#DECKEDUSA | @DECKEDUSA | #DECKEDUSA | @DECKEDUSA MT5 / MT7 | v.1.1 | Page 21。
PCI7488板卡安装说明

PCI-7488 12位32路高速光隔A/D转换板一﹑概述PCI-7488是带高速光电隔离器件面向工业过程而设计的12位32路A/D转换模板,符合PCI +5V总线标准,适合在所有PC机中运行。
PCI-7488 A/D转换芯片采用高性能的AD1764(BB774),它具有100KHz(10μS)转换速率,自带采样保持、参考电源等功能。
外部模拟量信号经过A/D转换后的数字量与计算机接口之间采用高速光电隔离芯片(光隔通过率1MHz),确保本板A/D转换的高可靠性和对计算机的安全性。
板上带有DC-DC隔离电源模块,用户无需从外部接入电源。
PCI-7488模拟量输入信号由37芯D型孔头接入的,可输入单端32路或双端16路模拟量信号,信号输入范围广,通过改变跳线器就可选择不同的电压范围。
本板占用4个物理I/O端口地址,可采用查询或中断方式工作。
PCI-7488出厂时提供Win95/98/2000/NT下测试程序和动态链接程序(DLL)及编程指导(DEMO程序),有VB/VC 采集程序例程,并提供两年的质保服务。
由于是PCI总线,用户不必关心板卡的实际地址,安装板卡时,PCI协议自动分配该板的基地址PCI-7488采用查询或中断两种方式工作,中断方式由A/D转换完成信号作为中断的触发信号,接到PCI INTA 上。
由于本板路数多,建议用户用查询方式工作。
在实际使用时,A/D转换时间一定,计算机运行速度越快,I/O延时需加大。
本板为四层模板,采用表贴芯片。
技术指标及性能特点:·分辩率:12位·通道数:单端32路/差分16路·A/D芯片:AD1674/BB774·A/D转换时间:10μS·单通道采集速率:100KHZ·输入电压量程:单极性:0~5V;0~10V双极性:±2.5V;±5V;±10V ·物理I/O端口地址:出厂时:BASE+0H~3H·工作方式:软件查询;中断(INTA)·光电隔离器件:一分钟可耐压5000V·电源:DC-DC电源隔离模块,无需外接电源·地线:不共地,数字地与模拟地分离·最大差动输入值:20V(±10V)·输出码制:单极性时为二进原码双极性时为二进制偏移码·总误差:<2‟·可在Win95/98/2000/NT下运行,支持VB、VC·电源功耗:350mA·总线接口:符合PCI总线+5V标准·尺寸大小:165mm×116mm二﹑工作原理1. 原理框图图1:PCI-7488原理框图2.工作原理PCI-7488板由通道多选开关、A/D转换、光电隔离、地址译码、逻辑控制及数据缓冲、PCI-ISA桥等几大部分组成。
Geeetech Prusa I3 X 用户使用手册说明书
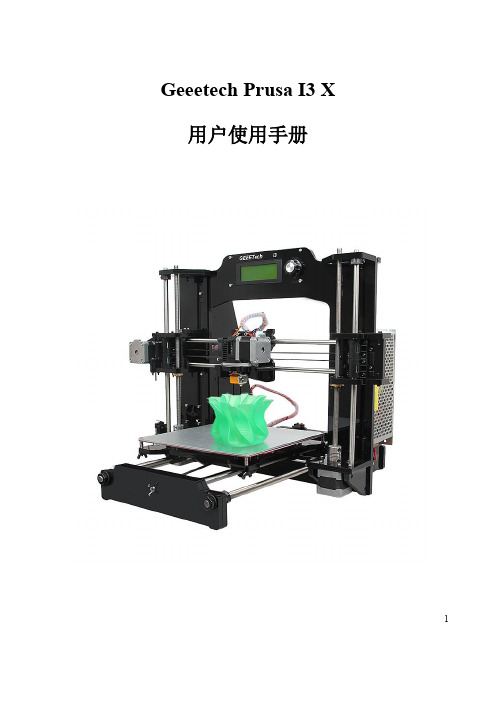
Geeetech Prusa I3 X用户使用手册1版权声明本手册版权归属深圳市捷泰技术有限公司(以下简称“捷泰技术”)所有, 并保留一切权力。
非经捷泰技术同意(书面形式),任何单位及个人不得擅自摘录本手册部分或全部,违者我们将追究其法律责任。
技术支持如果您对3D打印、飞控、智能家居等系列产品的成品、开发主板及模块感兴趣,希望获取相关资料或者技术支持,欢迎光临本公司网站进行了解,需要了解或想购买产品的客户请访问 或者,我们将竭诚为您服务。
安全声明安装此打印机要求安装人员具备较强的动手能力、一些基本常识以及对于接下来要进行的安装工作的充分理解。
我们提供此详细说明来帮助您,以使您的安装工作变得更加容易。
我们不会最终对因安装或者操作行为而导致的您的健康或安全问题负责,所以请您务必清楚地知道这一点,请确认自己是否能够开始安装或者购买。
请您仔细阅读整个手册来做出知情条件下的决策。
安装及操作涉及到用电,因此请做好所有必要的防范措施,打印机的运行由一个合格的12V电源提供动力,因此您的所有操作都应该在12V电压以下,但是不排除因为一些原因可2能会产生12V或者12V以上的电压,因此请谨慎操作。
使用前请检查电源的输入电压。
根据国家电源使用标准选择110V 或者220V。
(中国一般为220V)。
使用前请检查电源的输入电压。
根据国家电源使用标准选择110V 或者220V。
(中国一般为220V)。
3D打印过程涉及到高温,热端挤出喷嘴温度可高达230℃,加热后的热床温度高达110℃,挤出的融化塑料初始温度在200℃左右,因此在操作打印机的这些部位时需要格外小心与注意。
我们不推荐您在无人看管的情况下运行您的打印机,即便您足够自信这样做。
如果因为此种情况在安装或是使用打印机时造成任何损失、破坏、危险、受伤或者其他过失,本公司概不负责。
3 Tel: +86 755 2658 4110Fax: +86 755 2658 4074 -8581软件资源1.1 打印机控制软件Repetier-Host我们使用最新的Repetier hostV 1.6.0作为打印机的控制软件,下载地址为: /wiki/index.php/Repetier-Host#Download 下载完成后安装即可使用。
WCH38X系列串口卡驱动安装说明

WCH38X系列驱动安装说明
1、驱动安装
关机 插入CH38x卡 开机进系统 运行PCISETUP.EXE →
可以采用默认的“自动识别卡”或下拉列表选择对应的CH38x PCIe板卡类型→"安装驱动"
安装过程中出现这个提示不用理睬,系统反应和驱动安装进程不同步而已,
驱动正在正常安装。
驱动安装成功
2、驱动卸载
运行 PCISETUP.EXE —可以采用默认的“自动识别卡”或下拉列表选择对应要卸载的的CH38x板卡类型 "卸载驱动"
3、查看设备ID
运行PCISETUP.exe 点击“遇到问题请点击”按钮→点击“查看设备列表” 选择“所有PCI 设备” 找到相应硬件后,查看硬件ID即可。
该功能可用于驱动安装异常时检查硬件是否正常、系统是否找到硬件等。
4.修改串口/并口卡
运行pcisetup,点击“遇到问题请点击”按钮,点击修改“串并口卡”按钮,检测到CH38X的
串并口后,指定需要改动的COM口和LPT口号。
修改并口LPT 口号:
修改串口COM 口号:(支持多个串口同时修改)
如果串口号已经被占用或未释放,会有如下显示,可根据串口实际使用情况选择是否继续更改。
修改成功显示,有些机型需要重启才显示设置成功。
【用户手册】CAN卡驱动安装指导(Windows)
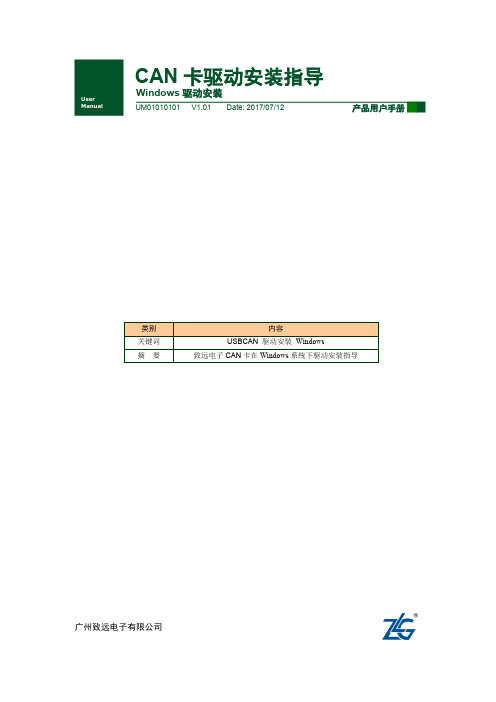
图 1.4 从计算机的设备驱动列表中选择
产品用户手册
©2017 Guangzhou ZHIYUAN Electronics Co., Ltd.. 2
广州致远电子有限公司
CAN 卡驱动安装指导
Windows 系统下驱动安装
图 1.5 直接点击下一步
图 1.6 从磁盘安装
产品用户手册
©2017 Guangzhou ZHIYUAN Electronics Co., Ltd.. 3
User Manual
CAN 卡驱动安装指导
Windows 驱动安装
UM01010101 V1.01 Date: 2017/07/12
产品用户手册
类别 关键词 摘要
内容 USBCAN 驱动安装 Windows 致远电子 CAN 卡在 Windows 系统下驱动安装指导
广州致远电子有限公司
广州致远电子有限公司
产品用户手册
©2017 Guangzhou ZHIYUAN Electronics Co., Ltd.. 4
广州致远电子有限公司
1.2 卸载驱动
同样可以通过设备管理器卸载驱动。
CAN 卡驱动安装指导
Windows 系统下驱动安装
图 1.9 设备驱动卸载
勾选“删除此设备的驱动程序软件”,然后点击“确定”按钮。ZLG USBCAN 的驱动将会 被卸载。“设备管理器”会自动刷新并显示该设备已经被移除。
MOXA UC-7408-CE 二代快速安装指南说明书

UC-7408-CEQuick Installation GuideSecond Edition, June 20081. OverviewMOXA UC-7408 features eight RS-232/422/485 serial ports, an 8-ch digital input, an 8-ch digital output, dual 10/100 Mbps Ethernet ports, PCMCIA, and a CompactFlash interface for wireless LAN communication and flash disk expansion, making UC-7408 ideal for embedded applications.2. Package ChecklistBefore installing UC-7408, verify that the package contains the following items:y 1 UC-7408y Wall-Mounting Kity DIN-Rail Mounting Kity UC-7408 Quick Installation Guide (this guide)y UC-7408 Documentation & Software CDy Cross-over Ethernet cabley CBL-RJ45M9-150: 150 cm, 8-pin RJ45 to Male DB9 serial port cable y CBL-RJ45F9-150: 150 cm, 8-pin RJ45 to Female DB9 console port cabley Universal Power Adaptory Product Warranty StatementPlease notify your sales representative if any of the above items are missing or damaged.3. UC-7408 Panel LayoutNOTE: UC-7420 (shown in the figures) has a CF slot, PCMCIA slot, and two USB 2.0 Host ports (circled below). UC-7410 does NOT have these three features.Rear View4. Installing UC-7408Wall or CabinetThe two metal brackets included with UC-7408 can be used to attach itto a wall, or the inside of a cabinet. Using two screws per bracket, firstattach the brackets to the bottom of the UC-7408. Next, use two screwsper bracket to attach the UC-7408 to a wall or cabinet.DIN-Rail MountingThe aluminum DIN-Rail attachment plate is included in the package.To attach the plate to UC-7408, situate the stiff metal spring towardsthe top.STEP 1: Insert the top of theDIN-rail into the slot just below thestiff metal spring.STEP 2: The DIN-Rail attachmentunit will snap into place as shownbelow.To remove UC-7408 from the DIN-Rail, simply reverse Steps 1 and 2above.5. Connector DescriptionPower ConnectorConnect the 12-48 VDC power line to UC-7408’s terminal block. If thepower is properly supplied, the Ready LED will will show a solid greencolor when the OS is ready.Grounding UC-7408Grounding and wire routing help limit the effects of noise due toelectromagnetic interference (EMI). Run the ground connection from theground screw to the grounding surface prior to connecting the power.ATTENTIONThis product is intended to be mounted to a well-grounded mountingsurface such as a metal panel.SG: The Shielded Ground (sometimes called ProtectedGround) contact is the left most contact of the3-pin power terminal block connector whenviewed from the angle shown here. Connect theSG wire to an appropriate grounded metal surface.Ethernet PortsThe 10/100 Mbps Ethernet ports (LAN 1 and LAN 2) use RJ45connectors.Pin Signal1 ETx+2 ETx-3 ERx+6 ERx-Serial PortsThe eight serial ports (P1 to P8) use RJ45 connectors. Each port can beconfigured by software for RS-232, RS-422, or RS-485. The pinassignments are shown in the following table:Pin RS-232RS-422 RS-4851 DSR --- ---2 RTS TXD+ ---3 GND GND GND4 TXD TXD- ---5 RXD RXD+ Data+6 DCD RXD- Data-7 CTS --- ---8 DTR --- ---D/I, D/OThe eight Digital Input channels andeight Digital Output channels useseparate terminal blocks.PCMCIAThe PCMCIA slot supports the CardBus (Card-32) Card standard and16-bit (PCMCIA 2.1/JEIDA 4.2) Card standard. It supports +3.3V, +5V,and +12V at a working voltage of 120 mA.CompactFlashUC-7408 provides one CompactFlash slot that supports CompactFlashtype I/II card expansion. Currently, MOXA provides a CompactFlashdisk for plug & play expansion. You may also use flash disks availablefrom most computer supply outlets. The CompactFlash will bemounted at\> CFFolderConsole PortThe console port is an RJ45 RS-232 port. It is designed for serial console, and can be connected to a V90 or GPRS modem via PPP. The pin definitions are the same as for the eight serial ports (P1 to P8). Reset to Default ButtonPress the “Reset to Default” button continuously for at least 5 seconds to load the factory default configuration. After the factory default configuration has been loaded, the system will reboot automatically. The Ready LED will blink on and off for the first 5 seconds, and then maintain a steady glow once the system has rebooted.Reset ButtonPress the “Reset” button to activate the hardware reset function. You should only use this function if the software does not function properly. To reset a system, you should reboot the operating system to avoid deleting important data.USBThe USB 1.1 Client port is reserved for future enhancement.Real Time ClockUC-7408’s real time clock is powered by a lithium battery. We strongly recommend that you do not replace the lithium battery without help from a qualified MOXA support engineer. If you need to change the battery, contact the Moxa RMA service team.ATTENTIONThere is a risk of explosion if the battery is replaced by an incorrect type.6. Powering on UC-7408To power on UC-7408, connect the “terminal block to power jack converter” to the UC-7408’s DC terminal block (located on the left back panel), and then connect the power adaptor. Note that the Shielded Ground wire should be connected to the right most pin of the terminal block. It takes about 30 seconds for the system to boot up. Once the system is ready, the Ready LED will light up, and UC-7408’s network settings will appear on the LCM display.7. Connecting UC-7408 to a PCThere are two ways to connect UC-7408 to a PC, through the serial console port or by Telnet over the network. The COM settings for the serial console port are: Baudrate = 115200 bps, Parity = None, Data bits = 8, Stop bits = 1, Flow Control = None.ATTENTIONRemember to choose the “VT100” terminal type. Use theCBL-RJ45F9-150 cable included with the product to connect a PC to UC-7408’s serial console. To use Telnet you will need to know UC-7408’s IP address andnetmask. The default LAN settings are shown below. For first-timeconfiguration, you may find it convenient to use a cross-over Ethernetcable to connect the PC directly to the UC-7408.DefaultIPAddressNetmaskLAN 1 192.168.3.127 255.255.255.0LAN 2 192.168.4.127 255.255.255.0Once the UC-7408 is powered on, the Ready LED will light up, and alogin page will open. Use the following default Login name andPassword to proceed.Login: adminPassword: admin8. Configuring the Network SettingNormally, you are required to change the IP address of UC-7400-CEbecause it is located in a different local network from that of yourdevelopment workstation. Use the netconfig utility to complete the task.Before using this utility, type netconfig -h to examine the usage of thecommand.\> netconfig –hUsage: netconfig –n <“LAN1” or “LAN2”> [-m <netmask>] [-d<DNS server>] [-g <gateway>] [-i <IP address>]For example, your development workstation has a LAN port at192.168.1.x and the Domain Name Server (DNS) is at 192.168.2.6.Execute the following command.\> netconfig –n LAN1 –i 192.168.1.5 –m 255.255.255.0 –g192.168.1.254 –d 192.168.2.6Type netconfig to view the new settings.\> netconfigLAN1 Interface Configuration:IP Address: 192.168.1.5SubNet Mask: 255.255.255.0Gateway: 192.168.1.254DNS: 192.168.2.6LAN2 Interface Configuration:IP Address: 192.168.4.127SubNet Mask: 255.255.255.0Gateway:DNS:9. Developing Your ApplicationApplication development on the UC-7400-CE computer takesadvantage of a number of well-known tools that are provided by theWindows environment in programmers’ workstations. These tools aretrouble-free to use for Windows programmers. Check the followingdevelopment tools for Windows Embedded Application Development.y /C# Applications: Use Visual Studio 2005y /C# Applications: Use Visual Studio .NET 2003y C/C++ Applications: Use eMbedded Visual C++ (eVC) 4.0Visual Studio 2005You do not need to install additional packages.Visual Studio .NET 20031.Install Visual Studio .NET 20032.Install Windows® CE Utilities for Visual Studio .NET 2003 Add-onPack (550KB) for VB .NET3.Import Compact .NET Framework SDKeMbedded Visual C++ (eVC) 4.01.Install eMbedded Visual C++ 4.0 (230 MB)2.Install Service Pack 4 for eVC 4.0 (68 MB)3.Install MOXA Windows® CE 5.0 C/C++ SDKsDeveloping applications with eVC 4.0 and MOXA SDKs1.Open Microsoft® eMbedded Visual C++ 4.0.2.From the File menu, choose New.3.Choose the Projects tab and then select the type of application.4.In the Project name box, type project name, then click OK.5.Choose the application type you want to create and click Finish.6.On the Build toolbar, choose the MOXA UC-7400-CE SDK, thetype of run-time image (Release or Debug), and the UC-7400-CEdevice.7.Write your application code.8.From the Build menu, choose Rebuild All to build the application.9.When you complete your application, use the web-basedmanagement system to upload it to the target computer.Developing a / C# application with .NET CompactFramework1.Open Microsoft® Visual Studio .NET 2003.2.From the File menu, choose New Æ Project.3.Choose the Project Type and then select the Smart DeviceApplication type of application.4.In the Project name box, type a name for the project, and then clickOK.5.Choose the Windows CE target platform.6.Select the project type and click OK.7.Write your application code.8.From the Device toolbar, choose Windows Device.9.From the Build menu, choose Build Project or Rebuild Project.10.When you complete your application, use the web-basedmanagement system to upload it to the target computer.Click here for online support:/supportThe Americas:+1-714-528-6777 (toll-free: 1-888-669-2872)Europe:+49-89-3 70 03 99-0Asia-Pacific: +886-2-8919-1230China: +86-21-5258-9955 (toll-free: 800-820-5036)© 2008 Moxa Inc., all rights reserved.Reproduction without permission is prohibited.。
Super Saver HSI CE Heater Fenwal板卡改装安装说明书

Date: 07-09-21 V4.0PNEG-2335Instructions1004 East Illinois Street • Assumption, IL 62510 • 1-217-226-4421Page 1 of 7Printed in the USARetrofit Kit Installation for Super Saver HSI CE Heater (3591-5001)These instructions cover replacing a Pektron board with Fenwal board in a SUPER SAVER HSICE HEATER. For in-field service, you will need twelve (3006-0107) spade terminals for Fenwal blade connections.All the bottom wires, #8 and #9, gray wire on the terminal connection block stays the same. (See Figure 1.)Figure 1 Bottom Terminal ConnectionsSee Figure 8 on Page 7 for the completed wiring connections. See Figure 5-7 on Pages 4-6 only highlight the wires for steps called out in that section.Before You BeginUse the normal shut down procedure.1. Close all the manual fuel supply valves.2. With the heater lit, allow the heater to burn off the excess fuel in the gas supply line.3. Disconnect the main power supply.Cut the wires from 4, 5 and 7 pin connection plugs and use the same for instructions later in this manual.Retrofit Kit Installation for Super Saver HSI CE Heater (3591-5001)Figure 2 Pektron BoardNOTE: Remove the filter and filter wires.Figure 3FilterFilterRetrofit Kit Installation for Super Saver HSI CE Heater (3591-5001) Heater and Igniter ConnectionHeater• Remove the heavy DSI cord from the heater.• Replace with one orange wire (1901-4017) connected with one yellow wire (1901-0144) and one brown wire (1901-4018) connected with one yellow wire (1901-0144).• Add 1/2" split loom (1044-2606) to these wires or zip tie them to existing hi-limit and flameprobe wires.Igniter• Replace the existing igniter with one hot surface 24V igniter (3002-3008).• Igniter bracket needs the vertical hole drilled out using a 7/16" drill bit to accommodate the igniter.• After the igniter is placed in the drilled hole, mark and drill igniter mounting hole in bracket with 1/8" drill bit for self-tapping screw (1004-5007).• Connect the orange wire (1901-0144) and the brown wire (1901-4018) to the igniter.Figure 4 Heater and Igniter ConnectionsRetrofit Kit Installation for Super Saver HSI CE Heater (3591-5001)Transformer ConnectionsLeft Side1. Remove the left 230 transformer terminal wire (brown) from the bottom of the left fuse and then remove the left fuse.2. Connect the left 230 transformer wire (brown) into the ON-OFF switch.3. Connect the right 24 transformer terminal wire (black) to the L1 on the Fenwal board.4. Connect the left 0 transformer terminal wire (black) to the #6 top terminal block.Right Side (Stays the same)5. The right 24 transformer terminal wire (black) should be connected to the top of right fuse.6. The right 0 transformer terminal wire (GN/YW) should be connected to the grounding screw.7. The ground wire (GN/YW) should be connected from the grounding screw to the #5 top terminal block.Figure 5 Transformer Connections0c .8Retrofit Kit Installation for Super Saver HSI CE Heater (3591-5001) Terminal Block Connections8. Connect the red wire (1901-0042) from the bottom of the right fuse to the #9 top terminal block.9. Connect the gray wire between the top terminal blocks #9 and #2.10. Connect the gray wire from the top terminal block #8 to the Fenwal W.11. Connect the purple wire (1901-3259) from the top terminal block #8 to Fenwal R.12. The brown wire should be connected between the top terminal block #7 to the right side of theON-OFF switch.13. Connect the blue wire between the top terminal blocks #6 and #3.14. Connect the brown wire between the top terminal block #4 to Fenwal F2.15. Connect the black wire between the top terminal block #1 to Fenwal PSW..8Figure 6 Terminal Block ConnectionsRetrofit Kit Installation for Super Saver HSI CE Heater (3591-5001)Fenwal Connections16. Connect the orange wire from the Fenwal GND to the grounding screw.17. Connect the red wire (1901-3366) from the top terminal block #7 to Fenwal F1.18. Connect the yellow flame probe wire to the Fenwal S2/FS.19. The green ground wire from the DSI should be connected to the grounding screw.20. Connect the black Hi-Limit wire to the Fenwal MV1.21. Connect orange wire (1901-4017) to Fenwal S1/120.22. Connect brown wire (1901-4018) to top terminal block #6.Figure 7 Fenwal ConnectionsRetrofit Kit Installation for Super Saver HSI CE Heater (3591-5001) Wiring DiagramEN298Figure 8 Completed Wiring。
Moxa Universal PCI Smart Serial Board 快速安装指南说明书
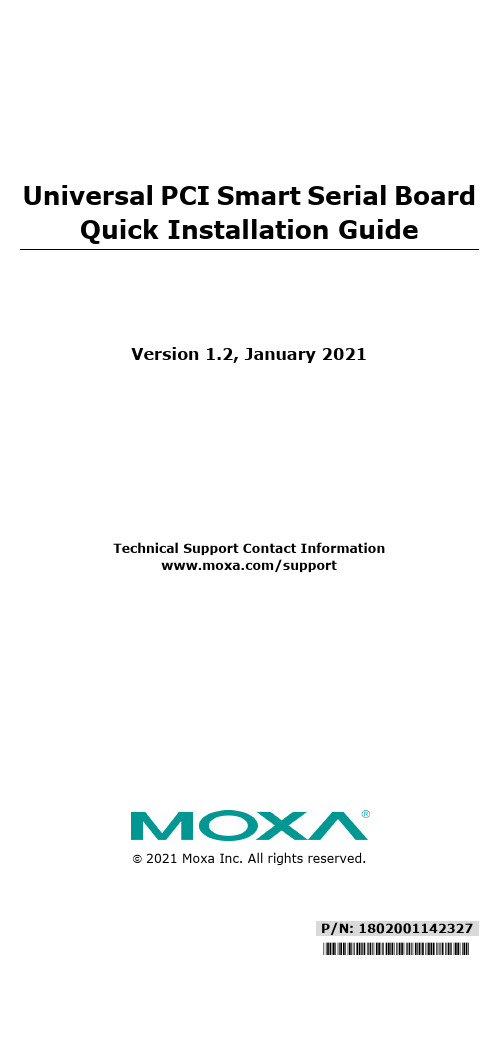
P/N: 1802001142327 *1802001142327*Universal PCI Smart Serial BoardQuick Installation GuideVersion 1.2, January 2021Technical Support Contact Information/support2021 Moxa Inc. All rights reserved.OverviewMoxa’s Universal PCI (UPCI) multiport serial boards can be installed in PCI or PCI-X slots and support both 3.3V and 5V PCI/PCI-X.Package ChecklistUPCI board are shipped with the following items:• 1 Moxa UPCI multiport serial board•Low-profile bracket (low-profile models only)•Quick installation guide (printed)•Warranty cardNOTE Notify your sales representative if any of the above items are missing or damaged.Hardware Installation ProcedureThe Universal PCI board MUST be plugged into the PC before the driver is installed.Follow the steps below:1.Select serial transmission mode. This step is for certain modelslisted below. If your product on hand is not included, please directly go to step2.If your model is CP-112UL Series/CP-114UL Series/CP-118U Series/ CP-132UL Series/CP-134U Series/CP-138U Series, you will need to set onboard DIP switches for each port.(Refer to “Dip Switch Settings” section to complete the DIPswitches setting)2.Install the board. Power off the PC and then plug the board firmlyinto any open PCI or PCI-X expansion slot.3.Plug the connection cable into the board’s connector. (Refer to“Pin Assignments” section for the cable pin assignment).4.Start system and verify the driver initialization. Software Installation Information1.Get the driver at . Based on the OS type, choosethe corresponding driver.2.Installing the driver:•For Windows OS (Take the installation of Win7 as an example)2.1. Unzip and execute the .exe file2.2. Follow the instructions to install the drivers•For LinuxExecute the following commands from the Linux prompt:2.1. Get the driver at and unzip the file:#cd /#mkdir moxa#cd moxa#cp /<driverdirectory>/driv_linux_smart_<version>_build_<build_date>.tgz .#tar -zxvfdriv_linux_smart_<version>_build_<build_date>.tgz2.2. Install the driver:#cd mxser#./mxinstall2.3. Verify the driver statusUse the Moxa diagnostic utility to verify the driver status:#cd /moxa/mxser/utility/diag#./msdiag2.4. Test the tty portUse the Moxa terminal utility to test the tty ports:#cd /moxa/mxser/utility/term#./mstermDIP Switch SettingsCP-112UL Series/CP-112UL-I SeriesMode S1 S2 S3RS-232 ON – –RS-422 OFF ON –4-Wire RS-485 OFF OFF ON2-Wire RS-485 OFF OFF OFFCP-114UL Series/CP-114UL-I SeriesMode S1 S2 S3RS-232 – – ONRS-422 – ON OFF4-Wire RS-485 ON OFF OFF2-Wire RS-485 OFF OFF OFFCP-118U Series/CP-118U-I SeriesMode S1 S2 S3RS-232 – – ONRS-422 – ON OFF4-Wire RS-485 ON OFF OFF2-Wire RS-485 OFF OFF OFFCP-132UL SeriesMode S1 S2 Illustration RS-422 – OFF2-Wire RS-485 ON ON4-Wire RS-485 OFF ONCP-134U Series/CP-134U-I SeriesRS-422 or RS-485 mode: Use the jumper to cover the two columns on the left of the jumper pins.RS-232 mode: Use the jumper to cover the two columns on the right of the jumper pins. CP-138U Series/CP-138U-I SeriesMode S1 S2 RS-422– ON 4-Wire RS-485 ON OFF 2-Wire RS-485OFFOFFPin AssignmentsCP-102U SeriesMale DB9 RS-232 PinSignal 1 DCD 2 RxD 3 TxD 4 DTR 5 GND 6 DSR 7 RTS 8CTSCP-102UL SeriesFemale DB25 RS-232 Pin Signal Pin Signal 1 – 14 – 2 DCD1 15 DTR1 3 GND 16 DSR1 4 CTS1 17 RTS1 5 RxD1 18 TxD1 6 – 19 – 7 – 20 – 8 – 21 DCD0 9 DTR0 22 GND 10 DSR0 23 CTS0 11 RTS0 24RxD0 12 TxD0 25 – 13–––CP-104JU SeriesRJ45 (RS-232) Pin Signal 1 DSR 2 RTS 3 GND 4 TxD 5 RxD 6 DCD 7 CTS 8CTRCP-104ULMale DB25 (CBL-M44M25x4-50) Pin Signal 2 TxD 3 RxD 4 RTS 5 CTS 6 DSR 7 GND 8 DCD 20DTR(CBL-M44M9x4-50) (OPT4-M9A) Pin Signal 1 DCD 2 RxD 3 TxD 4 DTR 5 GND 6 DSR 7 RTS 8 CTS Male DB9RJ45 (OPT4-RJ45A)Pin Signal 1 DSR 2 RTS 3 GND 4 TxD 5 RxD 6 DCD 7 CTS 8DTR8-pin RJ45CP-112UL SeriesMale DB9 (CBL-M25M9x2-50) Pin RS-232 RS-422/RS-485-4W RS-485-2W1 DCD TxD-(A) –2 RxD TxD+(B) –3 TxD RxD+(B) Data+(B)4 DTR RxD-(A) Data-(A)5 GND GND GND6 DSR – –7 RTS – –8 CTS – – 9–– –CP-114UL SeriesMale DB9 (CBL-M44M9x4-50)PinRS-232 RS-422/RS-485-4W RS-485-2W1DCD TxD-(A) – 2 RxD TxD+(B) – 3 TxD RxD+(B) Data+(B) 4 DTR RxD-(A) Data-(A) 5 GND GND GND 6 DSR – – 7 RTS – – 8 CTS – – 9–– –Male DB25 (CBL-M44M25x4-50)Pin RS-232RS-422/RS-485-4WRS-485-2W2 TxD RxD+(B) Data+(B)3 RxD TxD+(B) –4 RTS – –5 CTS – –6 DSR – –7 GND GND GND8 DCD TxD-(A) –20 DTR RxD-(A) Data-(A) CP-118UI Series/CP-138U-I Series Male DB9 (CBL-M78M9x8-100)Pin RS-232RS-422/RS-485-4WRS-485-2W1 DCD TxD-(A) –2 RxD TxD+(B) –3 TxD RxD+(B) Data+(B)4 DTR RxD-(A) Data-(A)5 GND GND GND6 DSR – –7 RTS – –8 CTS – –9 – –– *CP-118U-I Series onlyMale DB25 (CBL-M78M25x8-100)Pin RS-232RS-422/RS-485-4WRS-485-2W2 TxD RxD+(B) Data+(B)3 RxD TxD+(B) –4 RTS – –5 CTS – –6 DSR – –7 GND GND GND8 DCD TxD-(A) –20 DTR RxD-(A) Data-(A) *CP-118U-I Series onlyCP-118U Series/CP-138U SeriesMale DB9(CBL-M62M9x8-100, OPT8-M9 is for CP-118U and CP-138U) (CBL-M78M9x8-100 is for CP-118U-I and CP-138U-I)Pin RS-232RS-422/RS-485-4WRS-485-2W1 DCD TxD-(A) –2 RxD TxD+(B) –3 TxD RxD+(B) Data+(B)4 DTR RxD-(A) Data-(A)5 GND GND GND6 DSR – –7 RTS – –8 CTS – –9 – – –Male DB25(CBL-M62M25x8-100, OPT8B is for CP-118U and CP-138U) (CBL-M78M25x8-100 is for CP-118U-I and CP-138U-I)Pin RS-232RS-422/RS-485-4WRS-485-2W2 TxD RxD+(B) Data+(B)3 RxD TxD+(B) –4 RTS – –5 CTS – –6 DSR – –7 GND GND GND8 DCD TxD-(A) –20 DTR RxD-(A)Data-(A) Female DB25 (OPT8A/S)Pin RS-232RS-422/RS-485-4WRS-485-2W2 RxD TxD+(B) –3 TxD RxD+(B) Data+(B)4 CTS – –5 RTS – –6 DTR RxD-(A) Data-(A)7 GND GND GND8 DCD TxD-(A) –20 DSR – –*CP-118U Series onlyRJ45 (OPT8-RJ45) Pin Signal 1 DSR 2 RTS 3 GND 4 TxD 5 RxD 6 DCD 7 CTS 8 DTR*CP-118U Series onlyCP-132UL Series/CP-132UL-I SeriesMale DB9 Connector: Device-side Pin Assignments Pin RS-232 RS-422/RS-485-4W RS-485-2W1 TxD-(A) TxD-(A) –2 TxD+(B) TxD+(B) –3 RxD+(B) RxD+(B) Data+(B)4 RxD-(A) RxD-(A) Data-(A)5 GND RxD-(A) GND6 RTS-(A) GND –7 RTS+(B) – –8 CTS+(B) – – 9CTS-(A)– –CP-134U SeriesMale DB9 (CBL-M44M9x4-50) Pin RS-232RS-422 RS-485-4W RS-485-2W1 DCD TxD-(A) TxD-(A) –2 RxD TxD+(B) TxD+(B) –3 TxD RxD+(B) RxD+(B) Data+(B)4 DTR RxD-(A) RxD-(A) Data– (A)5 GND GND GND GND6 DSR RTS-(A) – –7 RTS RTS+(B) – –8 CTS CTS+(B) – –9 –CTS-(A) – –Male DB25 (CBL-M44M25x4-50)PinRS-232 RS-422 RS-485- 4W RS-485-2W 2TxD RxD+(B) RxD+(B) Data+(B) 3 RxD TxD+(B) TxD+(B) –4 RTS RTS+(B) – –5 CTS CTS+(B) – –6 DSR RTS-(A) – –7 GND GND GND GND8 DCD TxD-(A) TxD-(A) – 20 DTR RxD-(A) RxD-(A) Data-(A)22–CTS-(A)– –CP-168U SeriesRS-232 Cable Wiring for OPT8A/B/C/D/S OPT8A/S (DCE, DB25 Female) Pin Signal 2 RxD 3 TxD 4 CTS 5 RTS 6 DTR 7 GND 8 DCD 20 DSROPT8-RJ45 (8-pin)Pin Signal 1 DSR 2 RTS 3 TxD 4 GND 5 RxD 6 DCD 7 CTS 8 DTROPT8B/C (DCE, DB25 Male)Pin Signal 2 TxD 3 RxD 4 RTS 5 CTS 6 DSR 7 GND 8 DCD 20 DTROPT8-M9, OPT8D (DTE, DB9 Male)PinSignal 1 DCD 2 RxD 3 TxD 4 DTR 5 GND 6 DSR 7 RTS 8CTS- 11 - RS-422 Cable Wiring for OPT8F OPT8F/Z (DB25 Female)Pin Signal2 RxD+(B)3 TxD+(B)14 RxD-(A)16 TxD-(A)7 GNDRS-422/485 Cable Wiring for OPT8K Pin RS-422/RS-485-4W Pin RS-485-2W 2 RxD+(B) 2 Data+(B) 3 TxD+(B) 14 Data-(A) 14 RxD-(A) 7 GND 16 TxD-(A) 7 GNDPOS-104UL SeriesMale DB9 (CBL-M44M9x4-50) Pin Signal1 DCD2 RxD3 TxD4 DTR5 GND6 DSR7 RTS8 CTS9 RI/5V/12V。
PowerFlex DC Drive 帧A SCR模块安装指南说明书

Installation InstructionsPowerFlex ® DC Drive - Frame A SCR Modules for Drives with a Power Traces Circuit BoardWhat This Kit Includes•SCR modules (3 for non-regenerative drives, 6 for regenerative drives)•Mounting screws and washers (6 for non-regenerative drives, 12 for regenerative drives)•Gate leads (6 for non-regenerative drives, 12 for regenerative drives)•Thermal Grease •Static strapImportant:The SCR Modules supplied with this kit should only be used inthe following Frame A drives:!ATTENTION: Only qualified personnel familiar with DC drives and associated machinery should plan or implement the installation, start-up and subsequent maintenance of the system. Failure to comply may result in personal injury and/or equipment damage.!ATTENTION: To avoid an electric shock hazard, ensure that all power to the drive has been removed before performing the following.!ATTENTION: This drive contains ESD (Electrostatic Discharge) sensitive parts and assemblies. Static controlprecautions are required when installing, testing, servicing or repairing this assembly. Component damage may result if ESD control procedures are not followed. If you are not familiar with static control procedures, reference A-B publication 8000-4.5.2, “Guarding Against Electrostatic Damage” or any other applicable ESD protection handbook.230V AC Input 460V AC Input Drive CurrentRating Code DC Amps AC LineAmps HPDrive Current Rating Code DC Amps AC LineAmps HP 7P07 5.7 1.54P1 4.1 3.329P097.426P06 4.93012129.83010108.25020201650141411.47.502929247.50191915.5100383831100272722.1150555545150353528.6200454536.8250525242.5302PowerFlex® DC Drive - Frame A SCR Modules for Drives with a Power Traces Circuit BoardTools That You Need•Phillips® screwdriver•Flathead screwdriver•Nut driver or wrench for hex stand-offs•Torque wrenchPhillips® is a registered trademark of Phillips Screw Company.What You Need to Do The SCR modules are located on the heat sink of the drive chassis, below allcircuit boards and components. To install the SCR modules:❐ Step 1:Remove power from the drive❐ Step 2:Remove the protective covers❐ Step 3:Remove the Control EMI shield and Control board❐ Step 4:Remove the Pulse Transformer and Switching Power Supplyboards❐ Step 5:Remove the Power Traces board and AC CurrentTransducers❐ Step 6:Remove the existing SCR modules❐ Step 7:Install the new SCR modules❐ Step 8:Install the Power Traces board and AC Current Transducers❐ Step 9:Install the Pulse Transformer and Switching Power Supplyboards❐ Step 10:Install the Control EMI Shield and Control board❐ Step 11:Replace the protective covers and document the changePowerFlex® DC Drive - Frame A SCR Modules for Drives with a Power Traces Circuit Board3 Step 1:Remove Powerfrom the Drive1.Remove and lock-out all incoming power to the drive.Step 2:Remove the Protective Covers 1.Remove the two screws that secure the power terminal cover to thedrive and slide the cover down and off the drive chassis.!ATTENTION: Remove power before making or breaking cableconnections. When you remove or insert a cable connector withpower applied, an electrical arc may occur. An electrical arc cancause personal injury or property damage by:•sending an erroneous signal to your system’s field devices, causing unintended machine motion•causing an explosion in a hazardous environmentElectrical arcing causes excessive wear to contacts on both themodule and its mating connector. Worn contacts may createelectrical resistance.4PowerFlex® DC Drive - Frame A SCR Modules for Drives with a Power Traces Circuit Board2.Disconnect the DPI cable from the HIM assembly (if present).3.Remove the screws that secure the bottom cover to the drive, then slidethe cover down and off the drive chassis.4.Press in on the sides at the bottom edge of the top cover and at the sametime pull the cover toward you to pull it partially off the drive chassis.5.At the top of the drive, pull the cover forward, away from the drive,until the pins fit in the keyhole in the top of the cover, then carefully lift the cover off of the drive chassis.Important:The HIM assembly is connected via a cable to theControl board and therefore will not pull free from the drive until disconnected. See page 5for instructions.lift cover off drive chassis.4.PowerFlex® DC Drive - Frame A SCR Modules for Drives with a Power Traces Circuit Board 56.Disconnect the HIM Communication cable from the connector on theupper right corner of the Control board and set the cover aside.Pull tabs out to disconnect cable.6PowerFlex® DC Drive - Frame A SCR Modules for Drives with a Power Traces Circuit BoardStep 3:Remove the Control EMI Shield and Control BoardNote : The SCR Modules are located on the heat sink of the drive, behind the Control, Pulse Transformer, Switching Power Supply and Power Traces boards. All of these boards must be removed in order to replace the SCR Modules.1.Carefully disconnect the cables from connectors XA, XR and XFCD onthe Control board.2.Remove all appropriate I/O and control wiring including:–digital and analog I/O plug-in terminal blocks on the Control board –analog tachometer terminal block on the Control board –encoder terminal block on the Control board–cable shields that are grounded to the Control EMI shield –I/O terminal blocks on the I/O Expansion board–I/O terminal blocks on the 115V AC to 24V DC I/O Converter boardPowerFlex® DC Drive - Frame A SCR Modules for Drives with a Power Traces Circuit Board 73.Remove the four screws (and ground wire on the lower left corner ofboard) that secure the Control EMI shield and Control board to the chassis and slide the Control EMI shield and Control board up and out of the drive.Important:Be careful when removing the EMI shield not to pull freeany of the gate leads or other cables on the PulseTransformer circuit board below the EMI shield.Remove screwsRemove screw and ground wire8PowerFlex® DC Drive - Frame A SCR Modules for Drives with a Power Traces Circuit BoardStep 4:Remove the Pulse Transformer and Switching Power Supply Boards Note: The Switching Power Supply circuit board is secured to the back of the Pulse Transformer circuit board.1.Remove the slotted air flow plate from the top of the drive.–For 38A/10 HP and 55A/15 HP drives with 230V AC input and 35A/20 HP, 45A/25 HP, and 52A/30 HP drives with 460V ACinput, remove the four screws that secure the slotted air flow plateto the top of the drive, remove the fan cable from connector XV onthe Switching Power Supply board and remove the plate.PowerFlex® DC Drive - Frame A SCR Modules for Drives with a Power Traces Circuit Board9–For all other drives, remove the two screws that secure the slotted air flow plate to the top of the drive and remove the plate.Important:Mark all connections and wires before removal to avoidincorrect wiring during reassembly.10PowerFlex® DC Drive - Frame A SCR Modules for Drives with a Power Traces Circuit BoardFigure 1 Pulse Transformer Circuit Board LayoutComponents shown within dashed lines are only on the Pulse Transformer board for regenerative drives.F I R 1-X X r e v . “P ” a n d l o w e rF I R 1-X X r e v . “Q ” a n d h i g h e rPowerFlex® DC Drive - Frame A SCR Modules for Drives with a Power Traces Circuit Board 112.Remove the plug-in control power terminal block from the PulseTransformer circuit board (refer to Figure 1on page 10 for location).3.Remove the cables from connectors X3 and XP on the PulseTransformer board (refer to Figure 1on page 10 for location).4.For drives with a fan, remove the cable from connector X4 on the PulseTransformer board.5.For Pulse Transformer boards with an armature voltage feedbackterminal block, FIR1-XX, rev “Q” and higher, remove the connectorfrom XCD_IO on the upper left corner of the board.Removeplug-in terminalblock Remove cables from X3 and XPRemove cable from X4 for drives with a fan12PowerFlex® DC Drive - Frame A SCR Modules for Drives with a Power Traces Circuit Board6.Remove the appropriate gate leads (refer to Figure 1on page 10 forlocation):–For regenerative drives, remove each pair of (orange and yellow) gatelead cables from connectors KG01…KG06 and KG1…KG6 and pusheach lead through the appropriate opening in the board.–For non-regenerative drives, remove each pair of (orange and yellow)gate lead cables from connectors KG01…KG06 and push each leadthrough the appropriate opening in the board.Important:Remove the gate leads by grasping the connector andpulling up. DO NOT pull the gate leads off by pulling onthe wires.7.Remove the cable from connectors XTA on the Pulse Transformerboard (refer to Figure 1on page 10for location). Remove cable from XTAFor regenerativedrives, remove 12gate leads andpush through holesin boardRemove cablefrom XTAFor non-regenerativedrives, remove sixgate leads and pushthrough holes inboardPowerFlex® DC Drive - Frame A SCR Modules for Drives with a Power Traces Circuit Board 138.Remove the six screws that secure the Pulse Transformer board (andSwitching Power Supply board) to the drive and, while lifting upslightly on the board, slide the Pulse Transformer and Switching PowerSupply boards toward the top of the drive and out of the chassis.Important:The cables from connectors X4 (if present) and XTA mustslide through the openings in the board as it is lifted out ofthe drive chassis. Take care not to damage these cables andconnectors.Remove six screwsCarefully route cables through openings as the board is removed.Regenerative drive shown14PowerFlex® DC Drive - Frame A SCR Modules for Drives with a Power Traces Circuit BoardStep 5:Remove the Power Traces Board 1.Remove the screws that secure the terminal lugs (if present) and powerand ground wiring to terminals U, V, W, C, D and PE at the bottom of the drive.2.Remove the six stand-offs (and the ground wire) from the Power Tracescircuit board.PowerFlex® DC Drive - Frame A SCR Modules for Drives with a Power Traces Circuit Board15 3.Remove all screws and washers that secure the board to the SCRModules and power terminal isolation strip and remove the PowerTraces board from the drive.Non-Regenerative driveRemove allscrews andwashersRemove sixstand-offsand PEground wireRemove sixscrewsRemove sixstand-offsand PEground wireRemove allscrews andwashersRemove sixscrewsRegenerative drive16PowerFlex® DC Drive - Frame A SCR Modules for Drives with a Power Traces Circuit BoardStep 6:Remove the Existing SCR Modules 1.Remove the two screws and washers that secure each SCR Module tothe heatsink and remove the SCR Modules.Step 7:Install the New SCR Modules Install the new SCR modules in reverse order of removal as detailed in Step 6: Remove the Existing SCR Modules above.Important:Verify that each SCR Module is orientated in the same position as it was prior to removal.Important:Thermal grease must be applied to the bottom of the SCR modules before securing them to the heatsink.Use the following table to determine the proper tightening torque for theSCR Modules installed.Regenerative driveRemove screws230V AC Input460V AC InputPart Number Final Torque Part Number Final TorqueSK-20P-S7F44 2.5…4 N•m (22…35.4 lb•in)SK-20P-S7F73 2.5…4 N•m (22…35.4 lb•in) SK-20P-S7F45 2.5…4 N•m (22…35.4 lb•in)SK-20P-S7F74 2.5…4 N•m (22…35.4 lb•in)PowerFlex® DC Drive - Frame A SCR Modules for Drives with a Power Traces Circuit Board17Step 8:Install the Power Traces Board Install the Power Traces board in reverse order of removal as detailed in Step 5: Remove the Power Traces Board on page14.Verify that the connecting wire on the board is placed in the exact location as previously installed.Use the following table to determine the proper tightening torque for the Power Traces board to SCR Modules connections.Step 9:Install the Pulse Transformer and Switching Power Supply Boards Install the Pulse Transformer and Switching Power Supply boards in reverse order of removal as detailed in Step 4: Remove the Pulse Transformer and Switching Power Supply Boards on page8.Step 10:Install the Control EMI Shield and Control Board Install the Control EMI Shield and Control board in the reverse order of removal as detailed in Step 3: Remove the Control EMI Shield and Control Board on page6.230V AC Input460V AC InputPart NumberFinal Torque Part Number Final TorqueSK-20P-S7F442.5…4 N•m (22…35.4 lb•in)SK-20P-S7F73 2.5…4 N•m (22…35.4 lb•in) SK-20P-S7F45 2.5…4 N•m (22…35.4 lb•in)SK-20P-S7F74 2.5…4 N•m (22…35.4 lb•in)Regenerative driveNon-Regenerative drive!ATTENTION: Each gate lead cable must be connected to theexact connector from which it was removed on the PulseTransformer circuit board or damage to the drive may occur.Publication 20P-IN020B-EN-P - December 2009Supersedes 20P-IN020A-EN-P - March 2009Copyright © 2009 Rockwell Automation. All rights reserved. Printed in USA.Step 11:Replace theProtective Covers andDocumenting the Change 1.Replace the protective covers in the reverse order of removal as described in Step 2: Remove the Protective Covers on page 3.2.Install the DPI cable (if present).3.Record the installation of the new SCRs and date of installation on theField Installed Option label on the side of the drive (as shown below).Related Documentation Allen-Bradley publications are available on the internet at/literature .For . . .Read this document Publication Number In depth information regarding theoperation of PowerFlex Digital DC drives User Manual - PowerFlex Digital DC Drives 20P-UM001…。
CSR Harmony驱动安装和产品使用说明

CSR Harmony驱动安装和产品使用说明CSR Harmony4.0蓝牙的驱动安装和产品使用说明您好~欢迎您使用本产品~让我们一起尽情享受蓝牙的无线快乐吧~首先让我们先大概了解一下本产品的特色:1. CSR V4.0蓝牙适配器采用了CSR(Cambridge SiliconRadio)公司的最新的8510芯片。
2. 支持Bluetooth High Speed v3.0与low energy v4.0,并完全向下兼容v1.1/ v1.2/ v2.0/ v2.1的蓝牙设备;3. CSR蓝牙4.0芯片通过被称为Wideband Speech的技术进行音频编码解码,并进一步消除背景噪声和干扰,使无线音频的传输质量大幅提升,A2DP蓝牙立体声音频传输的音效极佳,可以媲美有线音频传输的音质;4. 蓝牙4.0技术拥有极低的运行和待机功耗,同时拥有跨厂商互操作性,3毫秒低延迟,AES-128加密,无线覆盖范围增强; 5. 是蓝牙3.0的升级增强版本,与3.0版本相比最大的不同就是低功耗。
speed up technology results into, active guide enterprise will mature technology results into for productivity, and Translate into economic benefits, efforts to solve economic and technological "two peels" phenomenon, says from the Dongping real, is to provide research institutions with more into place. Strengthening the agricultural scientific and technological achievements in the field to improveefforts to help farmers, crop planting, processing, animal husbandry and other agricultural products, increase the intensity of transforming scientific and technological innovation, science and technology to improve agricultural efficiency, improve the mass income and services immigrants safe haven siege works. Wuhan Institute of freshwater should give full play to the Chinese Academy of Sciences, and improving the added value of Dongping Lake aquatic products. 1th, in the middle ofthis yearProposed to increase the level of modernization in agriculture, hoping the county levels to seriously study the documents. 18 plenary session "storing food in, storing food in land", this requirement is very high, population, food is not enough, and not completely rely on imports, has to rely on technology to increase food production and limited land mass, relevant departments at the county level in particular, agricultural sector, active docking tertiary institutions, the Institute took the lead in the一:驱动部分本产品是支持免驱,即插即用的。
Mach3以太网控制卡 MKX-ET(以太网卡)说明书
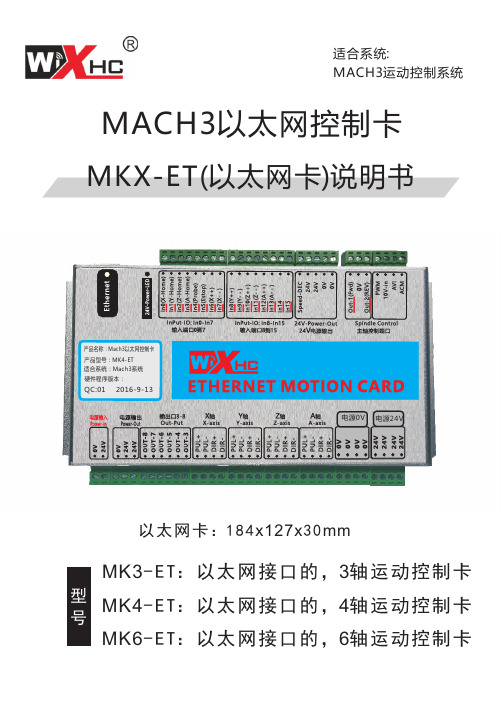
MACH3以太网控制卡适合系统:MACH3运动控制系统MK3-ET :以太网接口的,3轴运动控制卡MK4-ET :以太网接口的,4轴运动控制卡MK6-ET :以太网接口的,6轴运动控制卡型号以太网卡:184x127x 30mmMKX-ET(以太网卡)说明书QC :012016-9-13电源0V 电源24V适合系统:Mach 3系统产品型号:MK 4-ET 产品名称:Mach 3以太网控制卡硬件程序版本:特点描述支持Mach 3 所有版本,只适合Windows 操作系统,仅支持以太网接口,使用时需要进行IP 通讯地址设置(参考第20页)支持主轴速度反馈功能支持断电续传功能支持最大10米以太网线,无需安装驱动,即插即用;支持最多6轴联动,包括点动6轴联动。
(根据型号不同,支持轴数不同)拥有2000K Hz 的脉冲输出,支持差分信号输出,支持伺服/步进电机。
拥有状态指示灯,可提示连线状态,Mach 3连线状态,运行中,各类状态一目了然。
拥有16个输入口,8个输出口,支持扩展输入输出口所有IO 口全隔离,抗干扰强,性能稳定支持主轴PWM 调速输出;支持主轴脉冲+方向输出;支持主轴0到10V 模拟电压调速输出。
184x 127x 30 毫米,铝外壳,屏蔽干扰,稳定可靠。
★第1部分:控制卡硬件说明★★★★★★★★★-1-端口说明图变频器调速接口变频器调速信号模拟地变频器调速输入:0-10V 变频器10V 输出5V P W M 信号输出X 轴原点信号(输入0)Y 轴原点信号(输入1)Z 轴原点信号(输入2)A 轴原点信号(输入3)对刀信号输入(输入4)16个输入信号接口外接电源输入:24V外接电源输入:地线方向-脉冲+外接电源输入X 轴工作指示灯状态说明:常亮:表示工作运行正常输出:0V电源指示灯慢闪:表示控制卡与电脑 连接正常不亮:表示与电脑连接 不正常输出0V输出24V 输入5输入6输入7输入8输入9输入10输入11输入12输入13输入14输入15输出8输出3输出4输出5输出6输出76个输出口Y 轴Z 轴A 轴第1部分:控制卡硬件说明变频器正转信号变频器反转信号变频器数字信号地主轴速度反馈输出:24V-2-QC :012016-9-13脉冲-方向+方向-脉冲+脉冲-方向+方向-脉冲+脉冲-方向+方向-脉冲+脉冲-方向+电源0V电源24V输出:24V输出:0V适合系统:Mach 3系统产品型号:MK 4-ET 产品名称:Mach 3以太网控制卡硬件程序版本:应用接线图备注:如果出现开启变频器,控制卡工作不正常,是因为变频器干扰引起的;请更换变频器 根据我们的测试,推荐使用市场上的如下品牌变频器:贝斯特。
TS Performance MP-8 安装说明书

MP-8 2110201, 2110202, 4111002 98-05 Cat C7&31262000-07 C9Installation of TS Performance Power Play MP-8Caterpillar C-7, C9, & 3126Read all instructions and fully understand them before installing your TS Performance MP-8module. Disconnect the battery terminals and remove keys from the ignition beforeinstallation.Place Di-Electric Grease onto every electrical connection.1. Locate a place to mount the MP-8 module inside the engine compartm ent on the driver’s sidewhere it will be free from extreme heat and moisture. Use the supplied zip ties to securely mount the module.ICP Fuel Pressure SensorMAP/ Boost SensorTSP01CAT HARNESS1999-2005 - 3126 CAT / C7 CAT / 2000-2005 C91998-1999 CAT 3126 7.2L2006-2007 CAT C92.Locate the MAP/ Boost Sensor towards the back side of the engine on the driver’s side, next to thevalve cover in the intake manifold. The MAP/Boost sensor on the engine usually has white, green, and Pink wires on it. Unplug the factory harness from this sensor and plug the harness from the MP-8 into it. On our harness, the MAP connectors are the middle set of connectors having thegreen and orange wires.3.Locate the ICP sensor directly in front of the MAP Sensor toward the front of the engine. The ICPconnector on the engine usually has white, green, and brown wires. Unplug the factory harness from the ICP Sensor and plug the MP-8 harness into it which has the white and blue wires.4.From the inside of the cab, route the wire from the adjustable switch through the firewall to themodule in the engine compartment.5.Mount the switch in the dash in a location the driver can easily access.∙HP increase of 30%∙Decrease Fuel Consumption by up to 15%∙On-The-Fly Adjustable∙When removed leaves to trace of modification or foot printsPower increases as you turn the switch clockwise 0-30% over stock。
Synway AST Series Trixbox 2.8.0.4 安装手册说明书

Synway AST SeriesTrixbox2.8.0.4 Installation ManualSynway Information Engineering Co., LtdContentsContents (i)Copyright Declaration (ii)Software License Agreement (iii)Preface (iv)Chapter 1Preparation (1)1.1Hardware (1)1.2Software (1)Chapter 2Installation of Trixbox 2.8.0.4 System (2)2.1Brief Introduction to Trixbox System (2)2.2Installation of Trixbox System (2)Chapter 3Compilation and Installation of Dahdi and SynAST (7)3.1Compiling Environment Installation (7)3.2Driver Installation (7)Chapter 4Configuration and Management of Trixbox (10)Appendix A Technical/Sales Support (21)Copyright DeclarationThis manual is provided by Synway Information Engineering Co., Ltd (hereinafter referred to as ‘Synway’) as the support file for ‘Synway AST Series board driver software’. Both the software and this manual are copyrighted and protected by the laws of the People's Republic of China.All rights reserved; no part of this manual may be extracted, modified, copied, reproduced or transmitted in any form or by any means, electronic or mechanical, without prior written permission from Synway.Synway reserves the right to revise this manual without prior note. Please contact Synway for the latest version of this manual before placing an order.Synway has made every effort to ensure the accuracy of this manual but does not guarantee the absence of errors. Moreover, Synway assumes no responsibility in obtaining permission and authorization of any third party patent, copyright or product involved in relation to the use of this manual.Software License AgreementSynway Information Engineering Co., Ltd (hereinafter referred to as ‘Synway’) owns the copyright of ‘this software and its accessories, relative files and archives’ (hereinafter referred to as ‘this product’). Any company or person can download the corresponding driver software and other useful documents for free directly from our website after purchasing a board of Synway.PrefaceWhen you use the Synway AST series boards to set up a Trixbox application system, this file provides the help for software installation and configuration.Chapter 1 tells what to prepare before installing Trixbox.Chapter 2 introduces how to install the Trixbox 2.8.0.4 system.Chapter 3 unfolds how to compile and install the Dahdi and SynAST drivers.Chapter 4 shows how to configure and use the Trixbox system.Appendix A gives the contact way of technical support and sales department in Synway.Although Synway has scrupulously checked through this manual, but cannot guarantee the absence of errors and omissions. We sincerely apologize for any consequent inconvenience brought to you and will be very grateful if you kindly give your advice regarding amendments to this book.Chapter 1 Preparation1.1 HardwareFirst you shall prepare the following items: A PC with an empty HD (what we use herein is SAMSUNG, ATA/133 HDD 80GB), a Synway TEJ-1A/PCI board and a Synway FXM3201P board with two trunk modules (CH1 and CH2) and two station modules (CH3 and CH4).You can install the Synway AST series boards before or after the installation of the Trixbox system. All hardware manuals for the AST series boards can be downloaded from the following page./support.aspNote:We recommend you to use IE browser to open the links in this document.1.2 SoftwareMake sure you have these software: Trixbox 2.8.0.4 installation CD, Dahdi-2.4.0 and SynAst-1.9.0.0.Trixbox 2.8.0.4, about 672MB in size, can be downloaded from:http://58.100.228.233/download/3898250/4109637/4/iso/240/200/1322927635184_200/trixbox-2. 8.0.4.isoor/projects/asteriskathome/files/trixbox%20CE/trixbox%202.8/Burn the downloaded driver into a CD.dahdi-linux-complete-2.4.0+2.4.0, about 2.3MB in size, can be downloaded from:/pub/telephony/dahdi-linux-complete/releases/dahdi-linux-complete-2.4.0+2.4.0.tar.gzSynAst-1.9.0.0, about 37.4MB in size, can be downloaded from:/Download/Driver/Asterisk/AST1900/SynAST-1.9.0.0_en.tar.gzChapter 2 Installation of Trixbox 2.8.0.4 System2.1 Brief Introduction to Trixbox SystemThe Trixbox system is an integrated system which includes the operating system CentOS and other software like Asterisk, Dahdi, FreePBX. All necessary software can be installed well at one time, not requiring independent operation for any one of them. Asterisk and relative services will automatically start up upon installation.For detailed information about Trixbox, please go to the official website of Trixbox: .2.2 Installation of Trixbox SystemStep 1: Set the guide modeSet BIOS to boot from CD-ROM. Put the CD of Trixbox system burned already into CD-ROM and start the PC. Note: Don’t use the ISO image file to install the driver from HD, otherwise some functions may be unavailable.Step 2: Install Trixboxa) The system will go into the CD guide after the PC being started. Then the following interfacewill be shown on the screen. See Figure 1. Press Enter directly to select the default installation mode.Figure 1Note: When the Trixbox is installed in the default mode, it will format the entire HD. If you do not want the whole HD to be formatted, you should boot in the above interface following the CD start, then input ‘advanced’ and press Enter. Thus the system will give a prompt on how to partition the HD.b) Next, choose a keyboard type according to your requirement. Usually we choose ‘us’ asshown in Figure 2.Figure 2c) Next, select a time zone according to the real situation. Here we select ‘America/New_York’as shown in Figure 3.Figure 3d) Next, enter the root password as shown in Figure 4.Figure 4e) Then go into the installation process. Upon all files being installed successfully, the PC willbe restarted automatically.Note: You must take out the Trixbox CD before the PC restarts; or the system will go into the installation guide interface again.f) After the PC restarts, the system will go into the startup interface. By default, the system willboot up in trixbox-base mode. See Figure 5.Figure 5Step 3: Log in to the systemThere pops up the login prompt after the system startup. Please use the username “root” to log in, and the password is just the one set during the installation process.Step 4: Configure the networkAfter entering the Trixbox system, you should first configure the network to connect the system to Internet.To be exact, run the command ‘system-config-network’ to configure.# system-config-networkOn the displayed menu:Enter ‘Edit Devices’ to configure the basic information of network card;Enter ‘Edit DNS configuration’ to configure the DNS information;Save those configured settings and exit the interface. Then you need to restart the network service to put those settings into effect.# service network restartNote: During the following installation process, the system will automatically link to Internet to download some relative files. Therefore, if the network has not been well configured, all subsequent operations will fail. However, for some networks that haveDHCP servers to automatically allocate IP and gateway addresses, you need not do such network configuration.Step 5: When all the above steps are finished, the basic Trixbox system has been installed successfully.Chapter 3 Compilation and Installation of Dahdi and SynASTTo support the Synway AST series boards, you should install the SynAST driver based on the Trixbox system. Here take the Synway TEJ-1A/PCI and FXM3201P boards as an example. As the Trixbox system needs to be recompiled before installing other drivers, you should first install the compiling environment.3.1 Compiling Environment InstallationNote: Because the default installation does not involve installing the gcc compiler and the kernel source tree, the driver can not be compiled and installed directly. Only after you install the compiling environment can you install and use the third party boards and drivers. The commands are as follows.gcc # Install the gcc compilerinstall#yum# yum install kernel-devel-`uname -r` # Install the kernel source treeIf you cannot use the ‘yum’ command to find them, use the command ‘yum check-update’.3.2 Driver InstallationStep 1: Stop relative servicesstop # Stop Asterisk servicesamportal#Note: amportal commands include stop, start, restart and some other operations. See the command description for details.Note:1) When the board driver is being installed, the Dahdi driver will be recompiled beforethe configuration of Asterisk system. Hence, we suggest you install the driver and configure the board on the condition that all running services are stopped.2) Asterisk services will be automatically started once the Trixbox system is installed,and the driver installation will fail if it is performed while Asterisk services are running.In such situation, you should manually stop Asterisk services first.3) As using the ‘service’ mode to stop and start Asterisk may not be compatible withTrixbox 2.8.0.4 and later versions, we suggest you use ‘amportal’ to stop and start Asterisk.Step 2: Install the SynAST driverPut the prepared files under the /opt directory. Enter this directory and uncompress relativeinstallation packages.# cd /opt# tar -zxvf SynAST-1.9.0.0_en.tar.gz# tar -zxvf dahdi-linux-complete-2.4.0+2.4.0.tar.gzEnter SynAST-1.9.0.0_en to start auto installation:# cd SynAST-1.9.0.0_en# cd for_dahdi# ./Setup installPrompts on Screen:Install SynAST AST package now!You must install libpri and asterisk before this.Would you like to install SynAST AST package now? (y/n) Enter ‘y’.Please enter working dahdi directory [q](exit install) :Enter the directory to dahdi. Here please enter: /opt/dahdi-linux-complete-2.4.0+2.4.0If there are TEJ boards installed on your machine, the following prompts will pop up on the screen.SELECT TEJA MODE [t, e, j] : Select the TEJ board trunk working mode. Here select e which indicates working in E1 mode;SELECT TEJA [75, 120]ohm :Select the trunk impedance in E1 mode. Here input 120 which indicates working in Twisted Pair, 120Ω mode;Select OK to start installing. During the installation, the system will link to the network to download some relative files. When finished, the prompt Install Driver Completed appears. Then you will see the following line which reminds you of the board arrangement.Would you like to configure the cards order now? (y/n)If you have multiple boards of a same model, follow the section Configure Boards Order in the file SynAST_UserManual.pdf to handle. Here just input n and press ‘Enter’.Now both Dahdi and SynAST drivers are already installed.In the above step, these options ‘SELECT TEJA MODE [t, e, j]’, ‘SELECT TEJA [75, 120]ohm’ will appear only when the system is installed with TEJ series boards. In other words, they will not appear if the system is only installed with FXM series boards.Note: The system will automatically compile and install the Dahdi driver while installing the SynAST driver. Therefore, it is not necessary to compile and install the Dahdi driver separately.Step 3: Check if the driver module has been loadedInput the command:# lsmod | grep fxmIf properly installed, the first several lines of FXM will display on the screen. If they include the fxm32 line, it means the fxm32.ko module has been well loaded.To check TEJ boards, just replace the FXM in the above command with TEJ.Step 4: Configure the board channel and generate the following configuration file.# astcfg_dahdi trixboxStep 5: Start Trixbox# amportal start#Start Asterisk ServicesNow the SynAST driver installation is finished.Chapter 4 Configuration and Management of TrixboxIn the address bar of the browser, enter the Trixbox website to go into the initial interface of Trixbox (see Figure 6). User Mode is the default setting. First click on the ‘switch’ button at the top right corner and the login box pops up. Enter the admin username maint and the password password to reach the configuration and management interface.Then a dialog box will pop up for registration. Close it directly as you are not required to register so far.Figure 6On the upward side is the menu bar and on the left side is the navigation bar (see Figure 7).Figure 7Select the option PBX in the menu bar and click PBX Status to see the PBX information. Since there lists the channel information of our boards under ‘Dahdi driver info’ (see Figure 8), we canconfigure the PBX according to Trixbox explanation.Figure 8Next we will use an actual example to explain how to configure.Take the FXM3201P board as an example. Install an FXM3201P motherboard with an FXO module and an FXS module. Channel 1 and Channel 2 on the board are FXO (trunk) while Channel 3 and Channel 4 are FXS (station). You can see from the above figure that the corresponding trunks in the Trixbox system are Dahdi channel 1 and channel 2, the corresponding stations are Dahdi channel 3 and channel 4. If there are multiple boards in the system, the channels are arranged by board number.Here we demonstrate such functions as making a call from extension to extension, a call from extension to trunk, and a call from trunk to extension.First, select PBX in the menu bar and click on PBX Settings.Step 1: Configure extensionsIn this situation, there are two station channels on the FXM board respectively corresponding to Dahdi channel 3 and Dahdi channel 4. We need to add two Extensions whose numbers are supposed to be 2001 and 2002.Find the option Setup in the left navigation bar, select Basic and click Extensions. To add the information about the first extension 2001, choose Generic ZAP Device in the pull-down box for Device and press the Submit button to submit (see Figure 9). Then fill in some relative information on the page shown afterwards. Fill in 2001 for both options ‘User Extension’ and ‘Display Name’.Find the sentence ‘This device use technology. (Via DAHDI compatibility mode)’ (see Figure 10)and fill in 3 for the following option ‘Channel’. This indicates Extension 2001 uses Dahdi channel 3. Press Submit and the configuration of Extension 2001 is finished.Figure 9Figure 10After that, return to Add Extension at the top to add Extension 2002. Configure it to use Dahdi channel 4. Then both extensions are well configured.When the modified configuration is submitted, there appears a prompt ‘Apply Configuration Changes’ (see Figure 11) in orange on the top right corner of this page. Click it and an orange dialog pops up (see Figure 12). Click ‘Continue with reload’ to apply the modified configuration. Now we can make calls from extension to extension. Dial 2002 on the first extension to call the second extension.Figure 11Figure 12Step 2: Configure trunksNow there are two trunk channels on the FXM board respectively corresponding to Dahdi channel 1 and Dahdi channel 2.Find the option Setup in the left navigation bar, select Basic and click Trunks. We can see from the right side of this page (see Figure 13) that the default setting has included a trunk. Click ‘Trunk ZAP/g0’ and we can see the default value of ‘Zap Identifier (trunk name)’ is g0. Modify it to 1 which indicates this trunk uses Dahdi channel 1 and leave other parameters unchanged. Save thechange and the configuration of the first trunk is finished (see Figure 14).Figure 13Figure 14Then add the second trunk. Click ‘Add Trunk’ on the right and press ‘Add Zap Trunk (DAHDI compatibility mode)’. Fill in 2 for ‘Zap Identifier (trunk name)’ which indicates this trunk uses Dahdi channel 2. Click the Submit button to submit. Now both trunks are properly configured (see Figure 15).Figure 15Next, we shall manage to perform the call from extension to trunk.Step 3: Configure the outbound route for calls from extension to trunkFind the option Setup in the left navigation bar, select Basic and click Outbound Routes. We cansee from the right side of this page (see Figure 16) that the default setting has included a routewith the name of 9_outside which indicates the rule of dialing 9 before the phone number. The outbound call is routed on Dahdi/1. Actually, dial ‘9+phone number’ on the extension and the call will be routed out through Dahdi channel 1. You can modify the configuration and apply it tomake calls from extension to trunks.Figure 16Step 4: Configure to make calls from trunk to extensionTo make calls from trunk to extension, we shall configure ‘Inbound Routes’. Find the option Inbound Call Control and select Inbound Routes. Go to the bottom of the displayed page (see Figure 17) to find Set Destination. Select Extensions and designate some extension (see Figure 18). Thus, when a call comes in from a trunk, the specified extension rings directly. Just pick up the call and talk. Also you can set other inbound routes like IVR to complete corresponding flows. However, the IVR must be set beforehand.At last don’t forget to click ‘Apply Configuration Changes’ to make modified configurations effective; otherwise, no modification works. Then we can perform call tests based on the aboveconfigurations.Figure 17Now you are able to use the Synway FXM3201P board in the Trixbox system to make simple calls.To achieve more complicated functions, go to / to refer to relative documents.Appendix A Technical/Sales SupportThank you for choosing Synway. Please contact us should you have any inquiry regarding our products. We shall do our best to help you. However, our technicians and salesmen are mainly responsible for maintaining our boards and providing relative technical support. If there are problems about Asterisk, please keep in touch with Digium Inc. for help.HeadquartersSynway Information Engineering Co., Ltd/9F, Synway D&R Center, No.3756, Nanhuan Road, Binjiang District,Hangzhou, P.R.China, 310053Tel: +86-571-88860561Fax: +86-571-88850923Technical SupportTel: +86-571-88864579Mobile: +86-189********Email:***********************Email:**********************MSN:**************************Sales DepartmentTel: +86-571-88860561Tel: +86-571-88864579Fax: +86-571-88850923Email:****************。
HDX卡安装指南

Avid Core Audio 驱动程序功能 . . . . . . . . . . . . . . . . . . . . . . . . . . . . . . . . . . . . . . . . . . . . . . . . . . . 23 安装 Avid Core Audio 驱动程序 . . . . . . . . . . . . . . . . . . . . . . . . . . . . . . . . . . . . . . . . . . . . . . . . . . 23 CoreAudio 管理器 . . . . . . . . . . . . . . . . . . . . . . . . . . . . . . . . . . . . . . . . . . . . . . . . . . . . . . . . . . . . 24 配置用于第三方应用程序的 HD 音频接口 . . . . . . . . . . . . . . . . . . . . . . . . . . . . . . . . . . . . . . . . . . . . . . 26 配置 Apple 声音首选项或 Apple 音频 MIDI 设置 . . . . . . . . . . . . . . . . . . . . . . . . . . . . . . . . . . . . . . . 26
第 3 章 安装 HDX 卡 . . . . . . . . . . . . . . . . . . . . . . . . . . . . . . . . . . . . . . . . . . . . . . . . . . . . . . . . . . . . . . . . 9
板卡安装流程图TSDVR

点“是,仅这一次”然后单击“下一步”如下图:
出现如下界面后,点“从列表或指定位置安装(高级)”如下图:
点“下一步”后如下图:
点击浏览,找到驱动所在的目录,点击“下一步”:
点击“下一步”:
点击“完成”,驱动安装完毕。
特别注意:板卡注册文件不是压缩文件,不能通过解压缩打开,下载后需要改扩展名。
1、下载注册文件
2、修改注册文件扩展名:将注册文件名由“licence.zip”改为“licence.dat”。
(要先显示扩展名再修改,不能直接在后面加。
)
3、将改完扩展名的注册文件放到软件安装根目录下
4、注册完成
如何修改扩展名?
请在打开一个文件夹的情况下,点击“工具---文件夹选项”,打开后选“查看”,看一下里面的项目,在“隐藏已知文件类型的扩展名”前面看一下,如果打“√”,去掉;选择完后点“应用”,确定即可。
这样就可以看到文件的扩展名。
修改:鼠标点在注册文件上,右键,选择“属性”,然后“重命名”更改文件名。
如果未注册会有很多影响:
1、录一段时间会自己停录
2、影响联网功能
3、不能实现录满清盘功能
软件打开后出现以下情况是未注册:
点击确定后方可进入监控界面。
USB数据采集卡V8.2使用说明书

全志板卡常用操作说明

全志板卡常用操作说明全志板卡常用操作说明USB线升级1.准备好一条usb线,一头插到电脑上;2.打开升级软件,选择好固件;3.将板卡里的电源线拔出,按住板卡上的UBOOT按钮,将usb线的另一头插到USB-OTG口(通常是USB0口)上,待升级工具识别到设备插入,方可松开UBOOT按钮;4.此时电脑上如果没有安装过驱动,将会在电脑的右下角提示发现未知usb设备,此时请安装AW_driver驱动(该驱动在升级软件的安装路径的driver目录下),如果电脑上之前安装过,则升级软件会做出反应,提示你是否格式化flash升级,点击是进行升级;5.等待升级完成。
sd卡改屏参1.准备好U盘,将屏参命名为display_param.cfg拷贝到U盘根目录;2.将sd卡插入板卡卡槽;3.拔插板卡电源线重启板卡即可。
U盘改屏参1.准备好U盘,将屏参命名为display_param.cfg拷贝到U盘根目录;2.在板卡开好机的状态下,将U盘插入板卡,系统识别到屏参文件,执行相应程序并自动重启系统;3.待重启后即可看到屏参修改效果。
sd卡升级1.打开PhoenixCard工具,将sd卡插到电脑上,工具自己识别到sd卡插入,在界面上选择好盘符;2.选择好固件;3.点击“恢复卡”,完成后点击“烧录”;4.等待sd卡烧录完成;5.待sd卡制作成功,拔出sd卡,插入板卡卡槽;6.插上板卡电源,指示灯亮,等待2-3分钟,指示灯灭,则升级成功,拔出sd卡,拔插电源线重启即可。
sd卡改屏参1.准备好一张sd卡,将屏参命名为display_param.cfg拷贝到sd 卡根目录;2.将sd卡插入板卡卡槽;3.拔插板卡电源线重启板卡即可。
M3X(A64)板卡 sd卡/U盘改屏参1.插上板卡电源启动系统;2.准备好sd卡或者U盘,将屏参命名为display_param.cfg拷贝到sd卡/U盘根目录;3.将sd卡/U盘插入板卡卡槽,系统识别到屏参文件,执行相应程序并自动重启系统;4.待重启后即可看到屏参修改效果。
C218 Turbo PCI智能串行板快速安装指南(第四版,2008年6月)说明书

C218 Turbo/PCI IntelligentSerial BoardQuick Installation GuideFourth Edition, June 20081. OverviewC218 Turbo/PCI is an 8-port RS-232 serial board that is ideal for connecting a wide range of serial devices—including terminals, modems, printers, scanners, cash registers, bar code readers, keypads, numeric displays, electronic scales, and data acquisition equipment—to a PC.C218 Turbo/PCI is a Moxa Green Product. Moxa’s Green Products satisfy the RoHS directive of the European Parliament, and accordingly, do not contain cadmium and cadmium compounds, hexavalent chromium compounds, lead and lead compounds, mercury and mercury compounds, PBBs (polybrominated biphenyls), or PBDEs (polybrominated diphenyl ethers).2. Package ChecklistBefore installing the C218 Turbo/PCI board, verify that the package contains the following items:y C218 Turbo/PCI async boardy Software CDy C218 Turbo/PCI Quick Installation GuideNotify your sales representative if any of the above items is missing or damaged.3. Hardware Installation ProcedureThe C218 Turbo/PCI board MUST be installed in the PC before installing the driver. The following directions explain how to install the board in the PC.STEP 1: Power off the PC.STEP 2:Insert the C218Turbo/PCI control board firmly into any free PCI or PCI-X slot.STEP 3:Fasten the holding screw to fix the control board in place. STEP 4:Use the cable to connect C218Turbo/PCI to the CPUmodule.STEP 5: Power on the PC.STEP 6:Enter the PC’s BIOS to reserve a specific IRQ forC218Turbo/PCI.STEP 7: Restart the PC. 4. Software Installation InformationThe board MUST be plugged in before installing the driver. See theprevious section for instructions on how to install the board in your PC.Refer to the C218Turbo User’s Manual for detailed instructions oninstalling the drivers for this board.Windows 2003/XP Driver Installation1.After powering on your PC, log into Win 2003/XP as Administrator.2.Insert the C218Turbo software CD in your CD-ROM drive.3.Select Add/Remove Hardware from Control Panel.4.Select Add a device.5.Select Add new device.6.Select No, I want to select the hardware from a list.7.Select Multi-port serial adapters.8.Select Have Disk, and then use the browse button to navigate to theCD’s C218Turbo\Software\Win2K-XP-2003 folder.9.Select the C218Turbo driver.10.Start the installation.11.Click Yes in response to any admonitions that the software doesn’tcontain a Microsoft digital signature.12.Click Finish to complete the driver installation.13.If your ISA board configuration is not set as the default, you will needto change the driver settings to match the hardware configuration.Use the Device Manager to check if I/O, IRQ, INT vector, etc. arecorrect.Windows 2000 Driver Installation1.After powering on your PC, log into Win 2000 as Administrator.2.Insert the C218Turbo software CD in your CD-ROM drive.3.Select Add/Remove Hardware from the Control Panel.4.Select Add a device.5.Select Add new device.6.Select No, I want to select the hardware from a list.7.Select Multi-port serial adapters.8.Select Have Disk, and then use the browse button to navigate to theCD’s C218Turbo\Software\Win2K-XP-2003 folder.9.Select C218Turbo driver.10.Start the installation.11.Click Yes in response to any admonitions that the software doesn’tcontain a Microsoft digital signature.12.Click Finish to complete the driver installation.13.If your ISA board configuration is not set as the default, you will needto change the driver settings to match the hardware configuration.Use the Device Manager to check if I/O, IRQ, INT vector, etc. arecorrect.Windows 95/98 Driver Installation1.After powering on your PC, log into 95/98 as Administrator.2.Insert the C218Turbo software CD in your CD-ROM drive.3.Run Setup95.exe for both Windows 95 and Windows 98. In bothcases, be sure to install the driver from the CD’sC218Turbo\Software\Win9x\Windows.95 folder.4.After the board has been installed, the installation wizard will openthe port configuration window.5.Configure the I/O, IRQ, INT vector, etc.6.Restart the OSWindows NT Driver Installation1.After powering on your PC, log into NT as Administrator.2.Copy the folder C218Turbo\Software\WinNT\Windows.nt to yourhard drive.3.Open the Control Panel, click on the Network icon, and select theAdaptors tab.4.Click the Add button, and then Have Disk… in the Select NetworkAdapter window.5.Specify the exact path to the folder created in Step 2 above.6.Select MOXA Intellio C218Turbo series multiport board in theSelect OEM Option window, and then click on OK to start installingthe driver.7.When the Moxa Configuration Panel dialog box appears, click onAdd to open the Property window to modify port settings andadvanced FIFO configuration done automatically by the system.8.Configure the I/O, IRQ, INT vector, etc.9.Restart the OS.Linux Driver Installation1.Execute the following commands from the Linux prompt:#mount /dev/cdrom /mnt/cdrom#cd /#mkdir moxa#cd moxa#cp /mnt/cdrom/<driver directory>/mxdrv.tgz .#tar xvfz mxdrv.tgz2.#cd mxdrv#make clean; make install3.#cd /moxa/mxdrv/driver#./mxmknod4.Load the Moxa Driver#insmod moxa5.Download the firmware#cd /moxa/mxdrv/driver#./moxaload –y6.You can use the Moxa diagnostic utility to verify the driver status:#cd /moxa/mxdrv/utility/diag#./mxdiag7.You can use the Moxa terminal utility to test the tty ports:#cd /moxa/mxdrv/utility/term#./mxtermP/N: 18020021827005. Pin AssignmentsThe C218Turbo board has one female DB62 connector on the board. To connect the board to your serial devices, you may use one of the connection cables or connection boxes available from Moxa. In the following figures, we give the pin assignments for the serial device side of the various connection options. CBL-M62M25x8-100Male DB62 to male DB25 x 8 Opt8BMale DB62 to male DB25 x 8Male DB25Pin RS-2322 TxD3 RxD4 RTS5 CTS6 DSR7 GND8 DCD20 DTROpt8A, Opt8SMale DB62 to female DB25 x 8Female DB25Pin RS-2322 RxD3 TxD4 CTS5 RTS6 DTR7 GND 8 DCD 20 DSRCBL-M62M9x8-100Male DB62 to male DB9 x 8 Opt8-M9Male DB62 to male DB9 x 8Male DB9Pin RS-2321 DCD2 RxD3 TxD4 DTR5 GND6 DSR7 RTS8 CTSOpt8-RJ45Male DB62 to 8-pin RJ45 x 8Pin RS-2321 DSR2 RTS3 GND4 TxD5 RxD6 DCD7 CTS8 DTROpt8F, Opt8Z (RS-422 Converters)Male DB62 to female DB25 x 8Female DB25Pin RS-422 2 RxD+(B)3 TxD+(B) 14 RxD-(A) 16 TxD-(A)7 GNDOpt8K (RS-422/485 Converter)Male DB62 to female DB25 x 8Female DB25PinRS-4224-wire RS-4852-wireRS-4852 RxD+(B)RxD+(B)Data+(B)3 TxD+(B)TxD+(B)--- 14RxD-(A)RxD-(A)Data-(A)16TxD-(A)TxD-(A)--- 7 GND GND GNDClick here for online support: /supportThe Americas: +1-714-528-6777 (toll-free: 1-888-669-2872)Europe: +49-89-3 70 03 99-0 Asia-Pacific: +886-2-8919-1230China: +86-21-5258-9955 (toll-free: 800-820-5036)© 2008 Moxa Inc., all rights reserved.Reproduction without permission is prohibited.。
研为 网络运动控制卡与WinCE平板电脑连接 使用说明说明书

以太网运动控制卡与WinCE平板电脑连接使用说明广州研为2014/3/13目录1安装VS2008和ActiveSync (2)2安装SDK (2)3驱动文件 (2)4建立项目 (3)5项目设置 (5)6WinCE系统设置 (7)7连接调试 (8)8程序自启动 (8)需求: 1、网络2、安装VS2008编程软件3、安装控制系统支持的SDK4、安装同步软件ActiveSync1安装VS2008和ActiveSync将光盘中的vs2008的ISO文件解压到硬盘中,完成后打开解压的目录,双击子目录VS中的setup.exe文件,然后按提示进行安装VS2008。
VS2008安装完毕后,还要安装其SP1补丁,以及VisualStudioDeviceWindowsEmbeddedCompact7.msi补丁。
最后将光盘中的ActiveSync4.5压缩包解压到电脑中,在解压目录中双击“ActiveSyncsetupchs.msi”安装ActiveSync。
2安装SDK当安装好VS2008后,在光盘中找到SDK安装文件“FLAM335xDSDK_zh.rar”(7寸屏)或者“McgsTpc_617_SDK.rar”(10寸屏),双击执行安装,全部选择默认安装,静等一段时间,SDK即可安装成功。
如果安装过程中出现上图类似的错误,请重新安装,在选择时把Documentation取消掉,其他两项Native Development Support和Common保留。
3驱动文件驱动:IMC_pktdrv.dll函数库:imcCENet.dll头文件:IMCnet.h、 ParamDef.h、 IMC_Def.h、 PackageFun.h、imcCENet.lib 注意,必须将IMC_pktdrv.dll和imcCENet.dll与主程序放在WinCE中的同一个目录下。
将头文件放在工程目录中。
4建立项目启动VS2008,在文件菜单中选择“新建—>项目”;在弹出的对话框中的“项目类型”中选择自己熟悉的编程语言,在这里我们选择的是“Visual C++”,在它的分类下选择“智能设备”,然后在右边的模版中选择“MFC智能设备应用程序”;在“名称”栏输入项目名称,在“位置”栏中输入项目保存目录。