OLP-3x操作指南
VIAVI SmartClass OLP-8x 光学功率计操作指南说明书
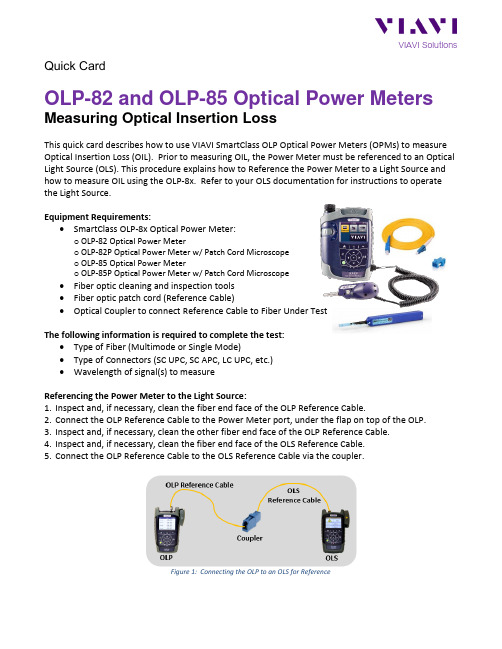
VIAVI Solutions Quick CardOLP-82 and OLP-85 Optical Power Meters Measuring Optical Insertion LossThis quick card describes how to use VIAVI SmartClass OLP Optical Power Meters (OPMs) to measure Optical Insertion Loss (OIL). Prior to measuring OIL, the Power Meter must be referenced to an Optical Light Source (OLS). This procedure explains how to Reference the Power Meter to a Light Source and how to measure OIL using the OLP-8x. Refer to your OLS documentation for instructions to operate the Light Source.Equipment Requirements:•SmartClass OLP-8x Optical Power Meter:o OLP-82 Optical Power Metero OLP-82P Optical Power Meter w/ Patch Cord Microscopeo OLP-85 Optical Power Metero OLP-85P Optical Power Meter w/ Patch Cord Microscope•Fiber optic cleaning and inspection tools•Fiber optic patch cord (Reference Cable)•Optical Coupler to connect Reference Cable to Fiber Under TestThe following information is required to complete the test:•Type of Fiber (Multimode or Single Mode)•Type of Connectors (SC UPC, SC APC, LC UPC, etc.)•Wavelength of signal(s) to measureReferencing the Power Meter to the Light Source:1.Inspect and, if necessary, clean the fiber end face of the OLP Reference Cable.2.Connect the OLP Reference Cable to the Power Meter port, under the flap on top of the OLP.3.Inspect and, if necessary, clean the other fiber end face of the OLP Reference Cable.4.Inspect and, if necessary, clean the fiber end face of the OLS Reference Cable.5.Connect the OLP Reference Cable to the OLS Reference Cable via the coupler.Figure 1: Connecting the OLP to an OLS for ReferenceFigure 2: OLP-82P Layout Figure 3: Power Meter Results screen6.Press the Power button to turn on the OLP and display the Home screen.7.Tap the Power Meter icon to launch the power meter.8.Tap the dBm/dB Display Unit soft key and set the Display Units to dB.The soft key will be labeled dBm, when the unit is set to dB in the Results Display.9.Tap the Wavelength soft key and select the wavelength to measure.10.Confirm that the OLS laser is on, and tap the SET REF soft key to reference the PowerMeter to the OLS. The signal level will change to 00.00 dB.11.Repeat steps 9 and 10 for all wavelengths to be tested.12.Disconnect the Reference Cable from the coupler. Do not disconnect the Reference Cable from theOLP port or power off the OLP until all OIL testing is complete. If the OLP is powered off or the fiber is disconnected from the OLP, you must reference the OLP and OLS again.VIAVI SolutionsContact Us +1 844 GO VIAVI (+1 844 468 4284) To reach the VIAVI office nearest you, visit /contacts.© 2018 VIAVI Solutions Inc.Product specifications and descriptions in this document are subject to change without notice.Measuring Insertion Loss:If you are performing an Optical Insertion Loss test and the OLP-8x has been referenced to an OLS, the Reference Cable should already be connected to the OLP-8x and the OLP-8x should be powered on and in the Power Meter Results view.1. If the interface to the Fiber under Test (FUT) is a patch cord, connect the patch cord to an opticalcoupler with the same connector type. 2. Inspect and, if necessary, clean the FUT connected to the coupler or OPP. 3. Inspect and, if necessary, clean the fiber end face of the Reference Cable.4. Connect the OLP Reference Cable to the coupler or OPP leading to the light source.Figure 4: Connecting the OLP to an OPP or coupler5. Tap the Wavelength soft key and select the wavelength to measure.6. View the Relative Power Level (dB) in the Results Display at the top of the screen.Figure 5: Optical Insertion Loss Results7. Repeat steps 5 and 6 for all wavelengths to be tested.8. Disconnect the Reference Cable from the FUT. Do not disconnect the Reference Cable from theOLP or power off the OLP until all testing is complete. If the fiber is disconnected, you must reference the Power Meter again. 9.Repeat steps 1 through 8 for all fibers to be tested.。
depolo lus余氯分析仪操作手册

IM 50.177AC UA (C/9-02)
1.010-42
简介
Depolox3plus分析仪
D+分析仪包括一个与样水流量组连接的电子控制模块,可适用于安装测量自由氯或总 氯探头及可选的 pH 值或氟探头。本系统可保证精确的测量(依照德国 DIN19643 标 准),本分析仪采用水质分析中最新德发展技术在线氯测量单元长期使用稳定且无需 维护。
Depolox3plus分析仪
1.2 自由氯测量单元
测量室:恒电势三电极测量室 精度:0.01 mg/l 或 2%满量程 灵敏度:0.01 mg/l 或 1%满量程 重量性:0.01 mg/l 或 2%满量程 稳定性:± 2%满量程达一个月运行(条件良好状况下) 响应时间:20 秒(当样水进入测量室 20 秒内,90%的余氯改变可反应出) 输出信号:µA 电流 尺寸:260(宽)×350(长)×160(高)(mm) 重量:3.8kg 材料:电极,铂;其它为不锈钢 样水温度:0 ~ 50°C 样水 PH 值:PH4 ~ PH8 电导率:> 280µs/cm 样水水压:0 ~ 15kg/cm2 ~ 4kg/cm2 样水排泄压力:无压 样水流量:33 升/小时 ± 5 升
非常重要的安全事项-----------------------------SP-1,-2, 技术数据--------------------------------------------第一部分 安装--------------------------------------------------第二部分 操作--------------------------------------------------第三部分 维修--------------------------------------------------第四部分 插图--------------------------------------------------第五部分 备件清单--------------------------------------------第六部分 索引--------------------------------------------------第七部分
ICOP技术股份有限公司的VDX3-ETX用户手册说明书

VDX DM&P1GH VDX3-ETXwithDM&P Vortex86DX31GHz processorVersion 6.0X3CopyrightThe information in this manual is subject to change without notice for continues improvement in the product. All rights are reserved. The manufacturer assumers no reasonability for any inaccuracies that may be contained in this document and makes no commitment to update or to keep current the information contained in this manual.No part of this manual may be reproduced, copied, translated or transmitted, in whole or in part, in any form or by any means without the prior to written permission of ICOP Technology Inc.ⓒCopyright 2016 ICOP Technology IncTrademarks Acknowledgement Vortex86DX3TM is the registered trademark of DM&P Electronics Inc. Other brand names and product names that appear in this document are the properties and registered trademarks of their respective owners. All names mentioned herewith are served for identification purpose only.Revision HistoryTable of Contents1 General Information (5)1.1 Overview (5)1.2 Block diagram (6)1.3 Specifications (7)1.4 Ordering Information (8)2 Hardware Information (10)2.1 Board Dimension (10)2.2 Dimension with heatsink/heatspreader (12)2.3 Connector and Jumper Location (14)2.4 Connector and Jumper Summary (15)2.5 Pin Assignments & Jumper Settings (15)J1: JTAG (15)J2&J6: SATA DOM (15)J3: SATA DOM Power (16)J4: LVDS Switch (16)J5: Giga Ethernet (16)X1: PCI, USB & Audio (17)X2: ISA (19)X3: VGA, LVDS, COM x2, PS/2 and Printer(Optional) (21)X4: IDE, Ethernet, Power and others (23)2.6 System Mapping (25)3 Software Resources (28)3.1 ICOP Technical Resource Website (28)4 Basic BIOS Setting (29)4.1 Introduction (29)4.2 IDE Configuration (29)4.3 Advanced PCI-PnP Setting (30)4.4 ACPI Enable (30)5 Basic LCD Panel Setting (31)5.1 Introduction (31)5.2 Pin Assignment of LVDS (31)5.3 Basic BIOS Setting for LCD (32)Technical Support Directly from ICOP (34)User Manual Feedback (34)Appendix (35)Warranty (36)1 General Information1.1OverviewThe VDX3-ETX is a low-power CPU module which compliant with ETX standard. It takes the advantage of Vortex86DX3 1GHz x86 CPU which integrate the PCIe, IDE, I2C, VGA, LVDS, PS/2, USB, HD Audio and even with 16-bit ISA bus support.The VDX3-ETX is designed as a plug in replacement, with backward compatibility to support legacy software to help extend existing product life cycle without heavy re-engineering.1.2Block diagram1.3Specifications1.4Ordering Informationrequired, please contact ICOP (*************.tw).**24-bit Signal channel LVDS running with VDX3-ETX module as default. If 24-bit Dual channel LVDS is required, please contact ICOP (*************.tw).Heatsink (For detail, please see Chapter 2.3):Accessories:2 Hardware Information 2.1Board DimensionTop ViewBottom View2.2 Dimension with heatsink/heatspreaderWith heatsink (item number: Heatsink-ETX-D3T)With heatspreader (item number: Heatspreader-ETX-D3T)2.3Connector andTop ViewBottom ViewJ6J5J3X2X1r and Jumper LocationJ2J1X4X32.4Connector and Jumper Summary2.5Pin Assignments & Jumper Settings J1: JTAGFor ICOP use only.J2&J6: SATA DOMJ6 is an optional SATA DOM horizontal connector.J3: SATA DOM PowerJ4: LVDS Switch18-Bit LVDS Support 24-Bit LVDS SupportJ5: Giga EthernetX1: PCI, USB & AudioPin Signal Voltage 5V I/O tolerant Pin Signal Voltage 5V I/O Tolerant A1 GND - - A2 GND - - A3 PCICLK2 VCC3 - A4 PCICLK3 VCC3 - A5 GND - - A6 GND - - A7 PCICLK0 VCC3 - A8 PCICLK1 VCC3 - A9 REQ3# VCC3 - A10 GNT3# VCC3 -A11 GNT2# VCC3 - A12 3V - -A13 REQ2# VCC3 - A14 GNT1# VCC3 -A15 REQ1# VCC3 - A16 3V - -A17 GNT0# VCC3 - A18 RESERVED - -A19 VCC - - A20 VCC - -A21 Not supported - - A22 REQ0# VCC3 -A23 AD0 VCC3 - A24 3V - -A25 AD1 VCC3 - A26 AD2 VCC3 -A27 AD4 VCC3 - A28 AD3 VCC3 -A29 AD6 VCC3 - A30 AD5 VCC3 -A31 CBE0# VCC3 - A32 AD7 VCC3 -A33 AD8 VCC3 - A34 AD9 VCC3 -A35 GND - - A36 GND - -A37 AD10 VCC3 - A38 AUXAL VCC -A39 AD11 VCC3 - A40 MIC VCC -A41 AD12 VCC3 - A42 AUXAR VCC -A43 AD13 VCC3 - A44 ASVCC VCC -A45 AD14 VCC3 - A46 SNDL VCC -A47 AD15 VCC3 - A48 ASGND .- -A49 CBE1# VCC3 - A50 SNDR VCC -Pin Signal Voltage 5V I/O tolerant Pin Signal Voltage 5V I/O Tolerant A51 VCC - - A52 VCC - -A53 PAR VCC3 - A54 SERR# VCC3 -A55 GPERR# VCC3 - A56 RESERVED - -A57 PME# VCC3 - A58 USB2- VCC3 -A59 LOCK# VCC3 - A60 DEVSEL# VCC3 -A61 TRDY# VCC3 - A62 USB3- VCC3 -A63 IRDY# VCC3 - A64 STOP# VCC3 -A65 FRAME# VCC3 - A66 USB2+ VCC3 -A67 GND - - A68 GND - -A69 AD16 VCC3 - A70 CBE2# VCC3 -A71 AD17 VCC3 - A72 USB3+ VCC3 -A73 AD19 VCC3 - A74 AD18 VCC3 -A75 AD20 VCC3 - A76 USB0- VCC3 -A77 AD22 VCC3 - A78 AD21 VCC3 -A79 AD23 VCC3 - A80 USB1- VCC3 -A81 AD24 VCC3 - A82 CBE3# VCC3 -A83 VCC - - A84 VCC - -A85 AD25 VCC3 - A86 AD26 VCC3 -A87 AD28 VCC3 - A88 USB0+ VCC3 -A89 AD27 VCC3 - A90 AD29 VCC3 -A91 AD30 VCC3 - A92 USB1+ VCC3 -A93 PCIRST# VCC3 - A94 AD31 VCC3 -A95 INTC# VCC3 - A96 INTD# VCC3 -A97 INTA# VCC3 - A98 INTB# VCC3 -A99 GND - - A100 GND - -X2: ISAPin Signal Voltage 5V I/O tolerant Pin Signal Voltage 5V I/O Tolerant B1 GND - - B2 GND - - B3 SD14 VCC B4 SD15 VCCB5 SD13 VCC B6 MASTER# - - B7 SD12 VCC B8 DREQ7 VCCB9 SD11 VCC B10 DACK7# VCC3 YB11 SD10 VCC B12 DREQ6 VCCB13 SD9 VCC B14 DACK6# VCC3 YB15 SD8 VCC B16 DREQ5 VCCB17 MEMW# VCC B18 DACK5# VCC3 YB19 MEMR# VCC B20 DREQ0 VCCB21 LA17 VCC B22 DACK0# VCC3 YB23 LA18 VCC B24 IRQ14 VCCB25 LA19 VCC B26 IRQ15 VCCB27 LA20 VCC B28 IRQ12 VCCB29 LA21 VCC B30 IRQ11 VCCB31 LA22 VCC B32 IRQ10 VCCB33 LA23 VCC B34 IOCS16# VCCB35 GND - B36 GND - -B37 SBHE# VCC3 Y B38 MEMCS16# VCCB39 SA0 VCC B40 OSC VCCB41 SA1 VCC B42 BALE VCC3 YB43 SA2 VCC B44 TC VCC3 YB45 SA3 VCC B46 DACK2 # VCC3 YB47 SA4 VCC B48 IRQ3 VCCB49 SA5 VCC B50 IRQ4 VCCPin Signal Voltage 5V I/O tolerant Pin Signal Voltage 5V I/O Tolerant B51 VCC - - B52 VCC - -B53 SA6 VCC B54 IRQ5 VCCB55 SA7 VCC B56 IRQ6 VCCB57 SA8 VCC B58 IRQ7 VCCB59 SA9 VCC B60 SYSCLK VCCB61 SA10 VCC B62 REFSH# VCC3 YB63 SA11 VCC B64 DREQ1 VCCB65 SA12 VCC B66 DACK1# VCC3 YB67 GND - - B68 GND - -B69 SA13 VCC B70 DREQ3 VCCB71 SA14 VCC B72 DACK3# VCC3 YB73 SA15 VCC B74 IOR# VCCB75 SA16 VCC B76 IOW# VCCB77 SA18 VCC B78 SA17 VCCB79 SA19 VCC B80 SMEMR# VCCB81 IOCHRDY VCC B82 AEN VCC3 YB83 VCC - - B84 VCC - -B85 SD0 VCC B86 SMEMW# VCCB87 SD2 VCC B88 SD1 VCCB89 SD3 VCC B90 OWS# VCC3 YB91 DREQ2 VCC B92 SD4 VCCB93 SD5 VCC B94 IRQ9 VCCB95 SD6 VCC B96 SD7 VCCB97 IOCHK# VCC B98 RSTDRV VCC3 YB99 GND - - B100 GND - -X3: VGA, LVDS, COM x2, PS/2 and Printer(Optional)Pin Signal Voltage 5V I/O tolerant Pin Signal Voltage 5V I/O Tolerant C1 GND - - C2 GND - - C3 R - - C4 B - - C5 HSY VCC - C6 G - - C7 VSY VCC - C8 DDCK VCC3 - C9 DETECT# VCC3 - C10 DDDA VCC3 -C11 TXLCK1- VCC1.8 - C12 TXOUT13- VCC1.8 -C13 TXLCK1+ VCC1.8 - C14 TXOUT13+ VCC1.8 -C15 GND - - C16 GND - -C17 TXOUT11+ VCC1.8 - C18 TXOUT12+ VCC1.8 -C19 TXOUT11- VCC1.8 - C20 TXOUT12- VCC1.8 -C21 GND - - C22 GND - -C23 TXOUT3- VCC1.8 - C24 TXOUT10+ VCC1.8 -C25 TXOUT3+ VCC1.8 - C26 TXOUT10- VCC1.8 -C27 GND - - C28 GND - -C29 TXOUT2- VCC1.8 - C30 TXLCK+ VCC1.8 -C31 TXOUT2+ VCC1.8 - C32 TXLCK- VCC1.8 -C33 GND - - C34 GND - -C35 TXOUT0+ VCC1.8 - C36 TXOUT1+ VCC1.8 -C37 TXOUT0- VCC1.8 - C38 TXOUT- VCC1.8 -C39 VCC - - C40 VCC - -C41 Not supported - - C42 Not supported - -C43 Not supported - - C44 BLON# - -C45 BIASON - - C46 DIGON# - -C47 COMP VCC3 - C48 Y VCC3 -C49 Not supported - - C50 C VCC3 -:First Channel LVDS:Second Channel LVDSPin Signal Voltage 5V I/O tolerant Pin Signal Voltage 5V I/O Tolerant C51 LPT VCC3 Y C52 Not supported - -C53 VCC - - C54 GND - -C55 STB# VCC3 - C56 AFD# VCC3 -C57 Not supported - - C58 PD7 VCC3 YC59 Not supported C60 ERR# VCC3 YC61 Not supported C62 PD6 VCC3 YC63 RXD2 VCC3 Y C64 INT# VCC3 -C65 GND - - C66 GND - -C67 RTS2# VCC3 - C68 PD5 VCC3 YC69 DTR2# VCC3 - C70 SLIN# VCC3 -C71 DCD2# VCC3 Y C72 PD4 VCC3 YC73 DSR2# VCC3 Y C74 PD3 VCC3 YC75 CTS2# VCC3 Y C76 PD2 VCC3 YC77 TXD2 VCC3 - C78 PD1 VCC3 YC79 RI2# VCC3 Y C80 PD0 VCC3 YC81 VCC - - C82 VCC - -C83 RXD1 VCC3 Y C84 ACK# VCC3 YC85 RTS1# VCC3 - C86 BUSY# VCC3 YC87 DTR1# VCC3 - C88 PE VCC3 YC89 DCD1# VCC3 Y C90 SLCT# VCC3 -C91 DSR1# VCC3 Y C92 MSCLK VCC3 YC93 CTS1# VCC3 Y C94 MSDAT VCC3 YC95 TXD1# VCC3 - C96 KBCLK VCC3 YC97 RI1# VCC3 Y C98 KBDAT VCC3 YC99 GND - - C100 GND - -X4: IDE, Ethernet, Power and othersPin Signal Voltage 5V I/O tolerant Pin Signal Voltage 5V I/O Tolerant D1 GND - - D2 GND - -D3 5V_SB - - D4 PWGIN VCC -D5 PS_ON# VSB5 - D6 SPEAKER VCC3 -D7 PWRBTN# VSB5 - D8 BATT VCC3 -D9 Not supported - - D10 LILED VCC3 -D11 Not supported - - D12 ACTLED VCC3 -D13 Not supported - - D14 Not supported - -D15 Not supported - - D16 I2CLK VCC3 YD17 VCC - - D18 VCC - -D19 Not supported - - D20 GPCS# VCC3 YD21 Not supported - - D22 I2DAT VCC3 YD23 Not supported - - D24 Not supported - -D25 Not supported - - D26 Not supported - -D27 Not supported - - D28 Not supported - -D29 Not supported - - D30 PIDE_CS3# VCC3 YD31 Not supported - - D32 PIDE_CS1# VCC3 YD33 GND - - D34 GND - -D35 Not supported - - D36 PIDE_A2 VCC3 YD37 Not supported - - D38 PIDE_A0 VCC3 YD39 Not supported - - D40 PIDE_A1 VCC3 YD41 Not supported - - D42 Not supportedD43 Not supported - - D44 PIDE_INTRQ VCC3 YD45 Not supported - - D46 PIDE_AK# VCC3 YD47 Not supported - - D48 PIDE_RDY VCC3 YD49 VCC - - D50 VCC - -Pin Signal Voltage 5V I/O tolerant Pin Signal Voltage 5V I/O Tolerant D51 Not supported - - D52 PIDE_IOR# VCC3 YD53 Not supported - - D54 PIDE_IOW# VCC3 YD55 Not supported - - D56 PIDE_DRQ VCC3 YD57 Not supported - - D58 PIDE_D15 VCC3 YD59 Not supported - - D60 PIDE_D0 VCC3 YD61 Not supported - - D62 PIDE_D14 VCC3 YD63 Not supported - - D64 PIDE_D1 VCC3 YD65 GND - - D66 GND - -D67 Not supported - - D68 PIDE_D13 VCC3 YD69 Not supported - - D70 PIDE_D2 VCC3 YD71 Not supported - - D72 PIDE_D12 VCC3 YD73 Not supported - - D74 PIDE_D3 VCC3 YD75 Not supported - - D76 PIDE_D11 VCC3 YD77 Not supported - - D78 PIDE_D4 VCC3 YD79 Not supported - - D80 PIDE_D10 VCC3 YD81 VCC - - D82 VCC - -D83 Not supported - - D84 PIDE_D5 VCC3 YD85 Not supported - - D86 PIDE_D9 VCC3 YD87 Not supported - - D88 PIDE_D6 VCC3 YD89 Not supported - - D90 CBLID_P VCC3 YD91 RXD- VCC3 - D92 PIDE_D8 VCC3 YD93 RXD+ VCC3 - D94 SIDE_D7 VCC3 YD95 TXD- VCC3 - D96 PIDE_D7 VCC3 YD97 TXD+ VCC3 - D98 HDRST# VCC3 YD99 GND - - D100 GND - -2.6System Mapping3 Software Resources3.1ICOP Technical Resource WebsiteIn the following website, you will find our latest user manuals, including OS support resources systems such as evaluation images for Windows Embedded Compact 7, Windows Embedded CE6.0, and Windows XP Embedded (Win XPe), etc. For details, please visit the link below:/4 Basic BIOS Setting4.1IntroductionFeaturing AMI BIOS, the VDX3-ETX module is a one stable module board for your applications. In this section, we will introduce you some basic AMI BIOS setting such as CPU speed adjusting, console redirection, and IDE configuration, etc.4.2IDE ConfigurationThe default IDE configuration is for Windows Operating System, and the setting as below:Onboard IDE Operate Mode: [Legacy Mode]IDE Compatibility:[Disabled].If you would like to use Linux on VDX3-ETX, please follow below instructions:Onboard IDE Operate Mode:[Native Mode]IDE Compatibility:[Enabled].Path of Onboard IDE Operate Mode:Advanced >IDE Configuration >Onboard IDE Operate Mode [Native Mode]4.3Advanced PCI-PnP SettingTwo statuses for IRQ setting:[Reserved]: IRQ will free to be allocated by PnP BIOS.[Available]: IRQ will not free to be allocated by PnP BIOS.Path: PCIPnP >IRQ4.4ACPI EnableTo install Windows 7 on ICOP computer boards, please enable ACPI as the following instruction.Path: Advanced >Power Management Configuration >ACPI Configuration >ACPI Aware O/S5 Basic LCD Panel Setting5.1 IntroductionThe VDX3-ETX offers two different interfaces which support maximum resolution up to 1920 x 1080 (at 60 MHz) connecting to VGA and LCD Flat Panel with 18-bit/24bit LVDS.The default setting of Boot Display Device[VBIOS] and LCD Panel Index[VBIOS] with Clone Display [ENBALED] support dual display (LCD and VGA) on VDX3-ETX.If your VGA display shifts because of the above setting, please switch Boot Display Device[VBIOS] to [CRT] as the following image:**Boot Display Device [VBIOS]: LCD and VGA display supported with display setting basedon your required LCD specification.[CRT]: VGA display supported5.2 Pin Assignment of LVDSPlease refer Page 20 for LVDS pin assignment.5.3 Basic BIOS Setting for LCDIf you would like to use LCD panel with VDX3-ETX, please follow below instruction: Boot Display Device [VBIOS]LCD Panel Index according to your LCD resolution from VBIOS to 5.Path of Boot Display Device setting:Boot >Boot Settings Configuration >Boot Display Device[VBIOS]Path of LCD Panel Index setting:Boot >Boot Settings Configuration >LCD Panel Index [ ]***The [VBIOS] difference between Boot Display Device and LCD Panel Index:Boot Display Device [VBIOS]: Display Output SettingLCD Panel Index [VBIOS]: Display Resolution SettingTechnical Support Directly from ICOP To offer you more accurate and specific solutions for the technical situations you have, please prepare the information below before contacting ICOP:—Product name and serial number—Description of the H/W environment ( i.e.: working temperature, I/O board information, information of connection between main boardand IO boards, and/or other devices, etc)—Description of the S/W environment (i.e: operating system, version,application software, and/or other related information, etc.)—A detailed description and photos of the technical situation—Any complement or technical situations you want ICOP morefocusing onUser Manual FeedbackTo make this user manual more complete, if you have any comments or feedbacks to this manual, please feel free to write to *************.tw or contact your ICOP sales representative.WarrantyThis product is warranted to be in good working order for a period of one year (12 months) from the date of purchase. Should this product fail to be in good working order at any time during this period, we will, at our option, replace or repair it without additional charge except as set forth in the following terms. This warranty does not apply to products damaged by misuse, modifications, accident or disaster. Vendor assumes no liability for any damages, lost profits, lost savings or any other incidental or consequential damage resulting from the use, misuse of, originality to use this product. Vendor will not be liable for any claim made by any other related party. Return authorization must be obtained from the vendor before returned merchandise is accepted. Authorization can be obtained by calling or faxing the vendor and requesting a Return Merchandise Authorization (RMA) number. Returned goods should always be accompanied by a clear problem description. Should you have questions about warranty and RMA service, please contact us directly.ICOP Technology Inc.Address: No. 15 Wugong 5th Road, Xinzhuang Dist.New Taipei City, Taiwan (R.O.C.) 24890TEL: +886-2-8990-1933FAX: +886-2-8990-2045Mail: *************.twWebsite: 。
VIAVI Solutions OLP-3xV2 宽带功率计产品说明书
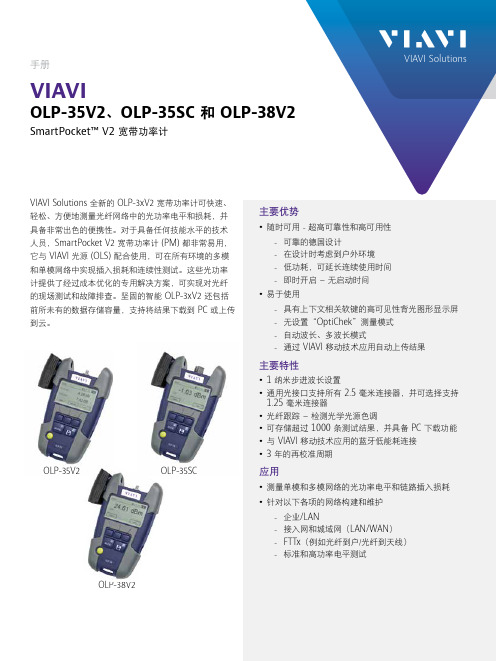
OLP-35V2OLP-38V2VIAVI Solutions 全新的 OLP-3xV2 宽带功率计可快速、轻松、方便地测量光纤网络中的光功率电平和损耗,并具备非常出色的便携性。
对于具备任何技能水平的技术人员,SmartPocket V2 宽带功率计 (PM) 都非常易用,它与 VIAVI 光源 (OLS) 配合使用,可在所有环境的多模和单模网络中实现插入损耗和连续性测试。
这些光功率计提供了经过成本优化的专用解决方案,可实现对光纤的现场测试和故障排查。
坚固的智能 OLP-3xV2 还包括前所未有的数据存储容量,支持将结果下载到 PC 或上传到云。
主要优势y 随时可用 - 超高可靠性和高可用性-可靠的德国设计 -在设计时考虑到户外环境 -低功耗,可延长连续使用时间 -即时开启 – 无启动时间 y 易于使用-具有上下文相关软键的高可见性背光图形显示屏 -无设置“OptiChek ”测量模式 -自动波长、多波长模式-通过 VIAVI 移动技术应用自动上传结果主要特性y 1 纳米步进波长设置y 通用光接口支持所有 2.5 毫米连接器,并可选择支持 1.25 毫米连接器y 光纤跟踪 – 检测光学光源色调y 可存储超过 1000 条测试结果,并具备 PC 下载功能 y 与 VIAVI 移动技术应用的蓝牙低能耗连接 y 3 年的再校准周期应用y 测量单模和多模网络的光功率电平和链路插入损耗 y 针对以下各项的网络构建和维护-企业/LAN-接入网和城域网(LAN/WAN ) -FTT x (例如光纤到户/光纤到天线) -标准和高功率电平测试手册VIAVIOLP-35V2、OLP-35SC 和 OLP-38V2SmartPocket™ V2 宽带功率计OLP-35SC产品:y OLP-35V2 是标准电信网络和多模或单模应用的最佳设备 y OLP-35SC 提供与 OLP-35V2 相同的功能,并附带固定 SC 适配器y OLP-38V2 是高功率版本(最高 +26 dBm ),适合有线电视 HFC (带模拟射频传输)或放大的 DWDM 系统应用Instant On – 易于使用 – 随时可用Instant On 意味着只要您准备好,SmartPocket V2 就准备好了,无需等待仪器启动,它在您需要的时候就随时可用。
Gamewell s3系列操作手册说明书

OMRON(OMRONMX3Plus)电子血压计使用说明书课件.doc

1 如何获得血压计的读数概要此款OMRON MX3 Plus 电子血压计不适合去测量心脏跳动的频率。
怀孕期间、脉搏无规律和动脉异常等类似影响测量的,请求教你的医生。
测量前避免吃饭、饮酒、吸烟、运动和洗澡。
测量前和测量中应保持平静、放松。
你决不能不听从医生的吩咐而改变所服用的药剂剂量。
将此款血压计保存于温度–20℃至60℃ 之间的干燥、封闭的地方。
如果 3 个月或更长时间不使用,请将所有电池从电子血压计中取出。
使用时的劝告一天至少检查你的血压两次(早餐前、工作后)。
当你在车上时,不要测量你的血压。
请始终在同一个手臂上测量血压。
在测量前,将“布袖口”缠好在手臂上。
警告使用环境温度在10℃至40℃。
使用中避免剧烈振动、撞击、磁场、电器干扰及其它。
不可在强烈日光下测量。
测量期间与移动电话保持至少 5 米远。
不要将“布袖口”缠绕在除手臂之外的其它物品上。
不要将“布袖口”和管子折叠。
不要将OMRON MX3 Plus 血压计摔落。
共13 页,第 1 页2 视图A 显示屏B 记忆按钮C 开始按钮D 开关按钮E 交流电源插口F 布袖口G 气管H 气管插头J 电池盒K 气管插口3 准备工作⑴滑开电池盖。
⑵按照图示插四节电池进电池盒,并合上电池盒。
注意!必须是四节相同的AALR61.5V 碱性电池!共13 页,第 2 页连接布袖口使布袖口缠绕好注意!当布袖口没有缠绕好手臂时,不要使布袖口膨胀!如上图,将H(气管插头)插入K( 气管插口)⑴除去手臂上衣物注意!卷起袖子时,切勿压迫血液流动!⑵将布袖口一端穿过H(金属环)注意!不要将气管裹入⑶手臂穿过布袖口布袖口内!注意!如测量左臂,使气管与手臂、中指保持平行!如上图;如测量右臂,则将气管与右手的小手指保持平行!如左图。
布袖口下端与肘关节保持 1 至2 厘米!共13 页,第 3 页⑷捏住布袖口末端,将它绕在手臂上,如左图。
注意!确信布袖口很好的裹住、粘好,否则不得膨胀布袖口压迫手臂!4 Operation 操作过程控制程序P 低压数值( 毫米汞柱) B 记忆按钮Q 记忆显示:存储中的记录C开始按钮数据D开关按钮R 脉搏:每分钟心跳次数测量屏幕S没电:电力太弱或耗尽M 高压数值T 泄压: 布袖口压力降低、( 毫米汞柱) 测量完毕N心脏符号:U 膨胀:布袖口膨胀、测闪烁-仪器测量量仪器启动长亮-测量完毕V 记忆位置: 1 至14共13 页,第 4 页注意!在连续两次测量中,应有最短三分钟的一个间隔!1坐在舒适的桌子2放松你的手臂,并将旁,双脚平放在地手掌心朝上。
PG0703P_C02B 编程手册:SSA3000X Plus频谱分析仪、SSA3000X-R实时频

目录1.远程控制概述 (1)1.1如何远程控制 (1)1.2通信协议 (3)1.3远程控制功能 (5)2.SCPI简介 (10)2.1命令格式 (10)2.2符号说明 (10)2.3参数类型 (11)2.4命令缩写 (12)3.模式共用命令 (13)3.1IEEE公用命令子系统 (13)3.2系统命令 (15)3.3存储命令 (20)3.4显示控制 (21)3.5模式命令 (22)3.6扫描命令 (22)4.频谱分析模式 (24)4.1仪器模式命令 (24)4.2Initiate命令子系统 (24)4.3Sense命令子系统 (25)4.4Calculate命令系统 (43)4.5Measurement命令系统 (58)4.6触发 (72)4.7TG (73)4.8调制解调 (75)5.矢量网络分析模式 (77)5.1频率控制 (77)5.2幅度控制 (78)5.3带宽控制 (80)5.4扫描控制 (80)5.5TG (81)5.6迹线 (81)5.7光标 (85)6.故障定点分析模式 (98)6.1频率控制 (98)6.2幅度控制 (99)6.3扫描控制 (100)6.4迹线 (101)6.5光标 (102)6.6测量 (105)7.调制分析模式 (110)7.1频率控制 (110)7.2幅度控制 (111)7.3带宽控制 (112)7.4扫描控制 (113)7.5迹线 (114)7.6光标 (117)7.7测量 (119)7.8触发 (124)8.实时频谱分析模式 (126)8.1频率控制 (126)8.2幅度控制 (129)8.3带宽控制 (131)8.4扫描控制 (132)8.5迹线 (134)8.6光标 (137)8.7触发 (139)8.8测量 (142)9.EMI测量 (145)9.1频率控制 (145)9.2幅度控制 (147)9.3带宽控制 (150)9.4扫描控制 (151)9.5迹线 (153)9.6光标 (155)9.7限制 (159)10.编程示例 (168)10.1使用VISA的编程示例 (168)10.2Sockets/Telnet示例 (182)SIGLENT 1. 远程控制概述分析仪支持通过USB、LAN、GPIB-USB接口与计算机进行通信。
1738 ArmorPOINT I O 系列产品连接线图指南说明书
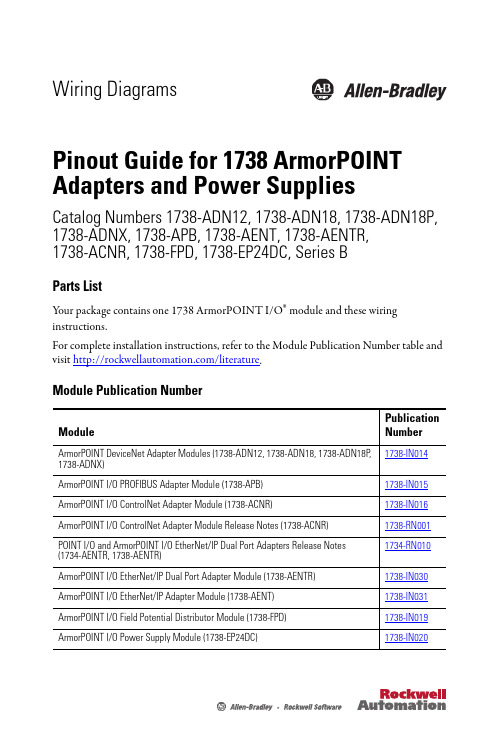
Wiring DiagramsPinout Guide for 1738 ArmorPOINT Adapters and Power SuppliesCatalog Numbers 1738-ADN12, 1738-ADN18, 1738-ADN18P, 1738-ADNX, 1738-APB, 1738-AENT, 1738-AENTR,1738-ACNR, 1738-FPD, 1738-EP24DC, Series BParts ListY our package contains one 1738 ArmorPOINT I/O® module and these wiring instructions.For complete installation instructions, refer to the Module Publication Number table and visit /literature.Module Publication NumberModule Publication NumberArmorPOINT DeviceNet Adapter Modules (1738-ADN12, 1738-ADN18, 1738-ADN18P,1738-ADNX)1738-IN014 ArmorPOINT I/O PROFIBUS Adapter Module (1738-APB)1738-IN015ArmorPOINT I/O ControlNet Adapter Module (1738-ACNR)1738-IN016 ArmorPOINT I/O ControlNet Adapter Module Release Notes (1738-ACNR)1738-RN001POINT I/O and ArmorPOINT I/O EtherNet/IP Dual Port Adapters Release Notes(1734-AENTR, 1738-AENTR)1734-RN010 ArmorPOINT I/O EtherNet/IP Dual Port Adapter Module (1738-AENTR)1738-IN030 ArmorPOINT I/O EtherNet/IP Adapter Module (1738-AENT)1738-IN031 ArmorPOINT I/O Field Potential Distributor Module (1738-FPD)1738-IN019 ArmorPOINT I/O Power Supply Module (1738-EP24DC)1738-IN0202 Pinout Guide for 1738 ArmorPOINT Adapters and Power SuppliesPublication 1738-WD011A-EN-P - July 20131738-ADN12 and 1738-ADNX 1738-ADN18 and 1738-ADN18PATTENTION: This equipment is considered Group 1, Class A industrialequipment according to IEC/CISPR 11. Without appropriate precautions, there may be difficulties with electromagnetic compatibility in residential and other environments due to conducted and radiated disturbance.ATTENTION: Two sets of mounting holes are used to mount the moduledirectly to a panel or machine. Mounting holes accommodate #8 (M4) machineor self-tapping screws. The torque specification is 0.8 Nm (7 lb-in).(view into connector)Pin 1DrainPin 2+ VPin 3- VPin 4CAN_HighPin 5CAN_LowFemale Out Connector(view into connector)Pin 1 DrainPin 2 + VPin 3 - VPin 4 CAN_HighPin 5 CAN_LowFemale Out Connector (1738-ADN18P only)Male In ConnectorPinout Guide for 1738 ArmorPOINT Adapters and Power Supplies 3Publication 1738-WD011A-EN-P - July 20131738 ArmorPOINT DeviceNet, ControlNet, EtherNet/IP Auxiliary Power (1)1738-AENT and 1738-AENTR1738-APB(1)Auxiliary power cable: standard cordset (single-ended), for example Allen-Bradley part number 889N-F4AFC-6F or 889N-R4AFC-6F; or standard patchcord (double-ended), for example, Allen-Bradley part number 889N-F4AFNU-6F or 889N-F4AFNV-6F. Refer to publication M117-CA001A-EN-Pfor more information.(view into connector)Pin 1User Power +Pin 2Adapter Power +Adapter/Subnet + (1738-ADNX only)Pin 3Adapter Power -Adapter/Subnet - (1738-ADNX only)Pin 4User Power -Mini Style 4-Pin in Male Connector(view into connector)Pin 1Tx +Pin 2Rx +Pin 3Tx -Pin 4Rx -M12 Female In Connector(view into connector)Pin 1+5VBUSPin 2A-LinePin 3GNDBUSPin 4B-LinePin 5ShieldFemale In Connector4 Pinout Guide for 1738 ArmorPOINT Adapters and Power SuppliesPublication 1738-WD011A-EN-P - July 20131738-APB Male Auxiliary1738-FPD and 1738-EP24DC Power SupplyEthernet Connector Pinout GuideD-Code M12 Micro Network Female Connector(view into connector)Pin 1User Power -Pin 2Adapter Power -Pin 3Protective GNDPin 4Adapter Power +Pin 5User Power +Male In Connector(view into connector)Pin 1User Power +Pin 2No Connect (1738-FPD)Adapter + (1738-EP24DC)Pin 3No Connect (1738-FPD)Adapter - (1738-EP24DC)Pin 4 User Power -Male In Connector44808(View into connector)Pin 1Tx+Pin 2 Rx+Pin 3 Tx-Pin 4 Rx-Pin 5 ShellPinout Guide for 1738 ArmorPOINT Adapters and Power Supplies 5Publication 1738-WD011A-EN-P - July 2013SpecificationsGeneral Specifications Attribute1738-FPD 1738-EP24DC 1738-AENT 1738-AENTR Backplane output currentPass-Through ***************************Operating voltage 12/24V DC120/240V AC 10...28.8V DC Environmental SpecificationsAttribute1738-FPD 1738-EP24DC 1738-AENT 1738-AENTRTemperature, operating -20...60° C (-4...140 °F)CertificationsCertification (whenproduct is marked)(1)(1)See the Product Certification link at /products/certification/ for Declaration of Conformity, Certificates, and other certification details.Value c-UL-usUL Listed Industrial Control Equipment, certified for US and Canada. See UL File E322657.CE European Union 2004/108/EC EMC Directive, compliant with:EN 61326-1; Meas./Control/Lab., Industrial RequirementsEN 61000-6-2; Industrial ImmunityEN 61000-6-4; Industrial EmissionsEN 61131-2; Programmable Controllers (Clause 8, Zone A & B)For 1738-FPD OnlyEuropean Union 2006/95/EC LVD, compliant with:EN 61131-2; Programmable Controllers (Clause 11)C-TickAustralian Radiocommunications Act, compliant with: AS/NZS CISPR11; Industrial Emissions EtherNet/IPODVA conformance tested to EtherNet/IP specifications6 Pinout Guide for 1738 ArmorPOINT Adapters and Power Supplies Notes:Publication 1738-WD011A-EN-P - July 2013Pinout Guide for 1738 ArmorPOINT Adapters and Power Supplies 7 Notes:Publication 1738-WD011A-EN-P - July 2013Rockwell Automation SupportRockwell Automation provides technical information on the Web to assist you in using its products. At , you can find technical manuals, a knowledge base of FAQs, technical and application notes, sample code and links to software service packs, and a MySupport feature that you can customize to make the best use of these tools.For an additional level of technical phone support for installation, configuration, and troubleshooting, we offer TechConnect support programs. For more information, contact your local distributor or Rockwell Automation representative, or visit .Installation AssistanceIf you experience a problem within the first 24 hours of installation, please review the information that's contained in this manual. You can also contact a special Customer Support number for initial help in getting your product up and running.New Product Satisfaction ReturnRockwell Automation tests all of its products to ensure that they are fully operational when shipped from the manufacturing facility. However, if your product is not functioning and needs to be returned, follow these procedures.Allen-Bradley, Rockwell Automation, ArmorPOINT and T echConnect are trademarks of Rockwell Automation, Inc.T rademarks not belonging to Rockwell Automation are property of their respective companies.United States1.440.646.3434 Monday – Friday, 8 a.m. – 5 p.m. EST Outside United States Please contact your local Rockwell Automation representative for any technical support issues.United States Contact your distributor. You must provide a Customer Support case number (see phone number above to obtain one) to your distributor in order to complete the return process.Outside United StatesPlease contact your local Rockwell Automation representative for the return procedure.Publication 1738-WD011A-EN-P - July 2013PN-204031Copyright © 2013 Rockwell Automation, Inc. All rights reserved. Printed in Singapore.。
ICOP Vortex86SX 300MHz 设备说明书
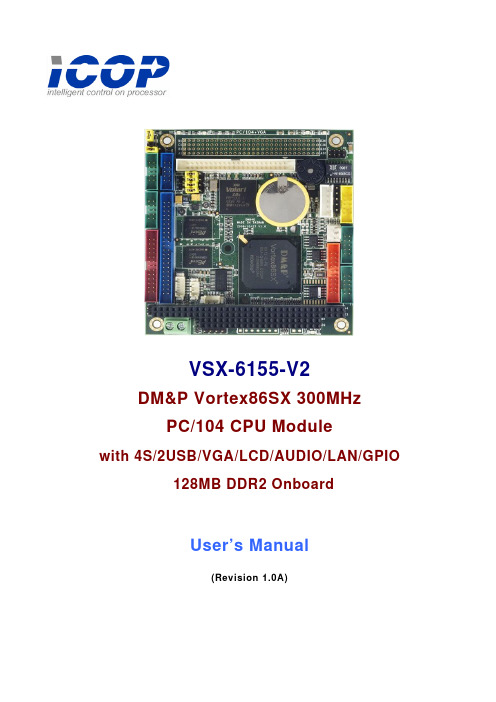
VSX-6155-V2DM&P Vortex86SX 300MHzPC/104 CPU Modulewith 4S/2USB/VGA/LCD/AUDIO/LAN/GPIO 128MB DDR2 OnboardUser’s Manual(Revision 1.0A)CopyrightThe information in this manual is subject to change without notice for continuous improvement in the product. All rights are reserved. The manufacturer assumes no responsibility for any inaccuracies that may be contained in this document. And makes no commitment to update or to keep current the information contained in this manual.No part of this manual may be reproduced, copied, translated or transmitted, in whole or in part, in any form or by any means without the prior written permission of the ICOP Technology Inc..©Copyright 2007 ICOP Technology Inc.Manual No. IUM6155-V2000-01 Ver.1.0A July, 2010Trademarks AcknowledgmentVortex86SX™ is the registered trademark of ICOP Technology Inc.Other brand names or product names appearing in this document are the properties and registered trademarks of their respective owners. All names mentioned herewith are served for identification purpose only.T a b l e o f C o n t e n t sT a b l e o f C o n t e n t s (iii)C h a p t e r 1 Introduction (1)1.1 Packing List (1)1.2 Product Description (2)1.3 Specifications (3)1.4 Board Dimension (5)C h a p t e r 2 Installation (6)2.1 Board Outline (6)2.2 Connectors & Jumpers Location (7)2.3 Connectors & Jumpers Summary (9)2.4 Pin Assignments & Jumper Settings (11)2.5 System Mapping (23)2.6 Watchdog Timer (26)2.7 GPIO (27)2.8 SPI flash (28)C h a p t e r 3 Driver Installation (29)Appendix (30)A. TFT Flat Panel Data Output (30)B. TFT Flat Panel Support List (31)C. LVDS Flat Panel Support List (33)D. Flat Panel Hardware Setting (34)E. Flat Panel Wiring and Lighting (35)F. TCP/IP library for DOS real mode (36)G. BIOS Default Setting (37)Warranty (38)C h a p t e r 1 Introduction1.1 Packing ListProduct NamePackageVSX-6155-V2Embedded Vortex86SX CPU All-in-One Board Manual & Drivers CD x 1 RS232 cable x 4PRINT cable x1 IDE cable x 1USB cable x 1 (USB port x 2) VGA cable x 1 LAN cable x 1 GPIO cable x 1 AUDIO Line x2 PS/2 Mouse cable x 1 PS/2 Keyboard cable x 1 Screw Kit x 11.2 Product DescriptionThe VSX-6155-V2 family of low-power x86 embedded controller is designed to meet PC/104 specification, and integrated with the following features.300 MHz Vortex86SX System-On-ChipVGA, TFT LCD support up to1280x1024 resolution128 / 256MB DDR2 system memory Enhanced IDE10/100Mbps Ethernet2 USB 2.0 (host)Up to 4 serial portsParallel port16-bit GPIOs Onboard 2MB SPI Flash PC/104-Plus expansion busMeet PC/104 stacking spec.2 watchdog timerJTAG interfaceAMI BIOSSingle voltage +5V DCSupport extended operatingtemperature range of -20°C to +70°CThe VSX-6155-V2 PC/104 family of embedded controller is designed with backward compatibility in mind, to provide migration path for projects facing end-of-life challenges with their existing x86 based PC/104 controller. The VSX-6155-V2 family of controller is designed as a plug in replacement, with backward compatibility to support legacy software to help extend existing product life cycle without heavy re-engineering.VSX-6155-V2 is suitable for broad range of data-acquisition, Industrial automation, Process control, Automotive controller, AVL, Intelligent Vehicle management devic,Medical device, Human machine interface, Robotics, machinery control And more…application that required small footprint, low-power and low-cost hardware with open industry standard such as PC/104.1.3 SpecificationsFeatures VSX-6155-V2 CPU DM&P SoC CPU Vortex86SX- 300MHzReal Time Clock with Lithium Battery Backup Cache L1:16K I-Cache, 16K D-CacheBIOS AMI BIOSBus Interface PC/104 Standard Compliant (Optional: PCI-104)System Memory 128 / 256MB DDR2 OnboardWatchdog Timer Software programmable from 30.5 us to 512 seconds x2sets(Watchdog 1 fully compatible with M6117D) VGA XGI Volari Z9s ChipsetVGA and TFT Flat Panel Interface SupportLVDS Flat Panel Interface Support (Optional)Onboard 32MB VGA MemorySupport resolution up to 1280 x 1024,16MB colors LAN Integrated 10/100M EthernetAUDIO CM119 USB Audio controllerI /O Interface Enhanced IDE port x1RS-232 port x3RS-232/422/485 port x1 (RS485: Auto Direction)Parallel port x1USB port x2 (USB 2.0 version)16-bit GPIO port x110/100Mbps Ethernet port x1Connectors 2.00 mm ∅ 44-pin box header for IDE x12.00 mm ∅ 44-pin box header for LCD x 12.00 mm ∅ 10-pin box header for VGA x12.00 mm ∅ 10-pin box header for USB x12.00 mm ∅ 26-pin box header for Print x12.00 mm ∅ 20-pin box header for 16-bit GPIO x12.00 mm ∅ 10-pin box header for RS-232 x42.00 mm ∅ 8-pin header for Ethernet x 12.54 mm ∅ 5-pin box header for Keyboard x12.54 mm ∅ 5-pin header for Mouse x12.54 mm ∅ 4-pin header for DC-in x12.54 mm ∅ 3-pin header for RS-485 x12.54 mm ∅ 2-pin header for Reset x12.54 mm ∅ 7-pin header for Redundancy x1(Opt)2.54 mm ∅ 2-pin header for SYS-Fail-SW- x1(Opt)1.25 mm ∅ 6-pin Wafer for JTAG x11.25 mm ∅ 4-pin Wafer for Line-out/MIC-in x2Flash Disk Support Onboard 2MB SPI Flash Disk (Driver: A)44-pin IDE Flash Disk( EmbedDisk 16MB or above)Power Requirement Single Voltage +5V@ 620mADimension 90 X 96mm (3.54 x 3.77 inches)Weight 90gOperating Temperature -20o C ~ +70o C-40°C ~ +85°C (Optional)1.4 Board DimensionC h a p t e r 2Installation2.1 Board Outline(Note1: COM2 RS232/422/485 is selected by BIOS setting) (Note2: PCI-104 connector is optional)(Note3: VI/O Default setting of PCI-104 connector is +5V) (Note4: Redundancy Signal and System-Fail-SW are optional)2.2 Connectors & Jumpers Location ConnectorsJumpers & LEDs2.3 Connectors & Jumpers SummarySummary TableIDE-IDE Active LED (Green ) LED-SMD LEDMTBF-MTBF-Out (Orange) LED-SMDLEDLED 3 LAN Link/Active LED (Green) LED-SMD LED 4 LAN Duplex LED ( Yellow ) LED-SMD SP1 BUZZER2.4 Pin Assignments & Jumper SettingsJ1: IDE (44 Pins)J2: USB Pin # Signal Name Pin # Signal Name1 VCC2 VCC3 LUSBD3-4 LUSBD2-5 LUSBD3+6 LUSBD2+7 GND8 GND9 GGND 10 GGND Pin # Signal Name Pin # Signal Name1 IDERST2 GND3 IDED74 IDED85 IDED6 6 IDED97 IDED58 IDED109 IDED4 10 IDED11 11 IDED3 12 IDED12 13 IDED2 14 IDED13 15 IDED1 16 IDED14 17 IDED0 18 IDED15 19 GND 20 NC 21 IDEREQ 22 GND 23 IDEIOW 24 GND 25 IDEIOR 26 GND 27 ICHRDY 28 GND 29 IDEACK 30 GND 31 IDEINT 32 NC 33 IDESA1 34 IDECBLID 35 IDESA0 36 IDESA2 37 IDECS-0 38 IDECS1 39 IDELED 40 GND 41 VCC 42 VCC 43 GND 44 NCJ4: LANPin # Signal Name Pin # Signal Name1 ATX+2 ATX-3 ARX+4 LED05 LED0+6 ARX-7 LED1+ 8 LED1J5: JTAGPin # Signal Name Pin # Signal Name1 VCC2 GND3 TCK4 TDO5 TDI6 TMSJ6: RESETPin # Signal Name Pin # Signal Name1 RST_SW2 GNDJ7: Redundancy (Optional)Pin # Signal Name Pin # Signal NameSYS-FAIL-OUT1 GND 23 SYS-FAIL-IN4 GPCS05 SYS-GPCS-IN6 TXD9\7 RXD9\J8: System-Fail-Switch (Optional)Pin # Signal Name1 SYS-SW-IN2 GNDJ9: PS/2 KeyboardPin # Signal Name Pin # Signal Name1 KBCLK2 KBDAT3 NC4 GND5 VCCJ10: PS/2 MousePin # Signal Name Pin # Signal Name1 MSCLK2 MSDATA3 NC4 GND5 VCCJ11: COM 1 (Optional TTL/ GPIO-P4)Pin # SignalNamePin #SignalName1 DCD12 RXD13 TXD14 DTR15 GND6 DSR17 RTS1 8 CTS19 RI1 10 NCJ12: COM2 RS232 / 422 / 485 (Optional: TTL)Pin # Signal Name Pin # Signal Name1 DCD2/ 422TX- / RS485-2 RXD2 / 422TX+ / RS485+3 TXD2/422RX+ 4 DTR2/422RX-5 GND6 DSR27 RTS28 CTS29 RI2 10 NCJ13: GPIO (Port 0 / 1)Pin # Signal Name Pin # Signal Name1 GND2 VCC3 GP004 GP105 GP016 GP117 GP02 8 GP129 GP03 10 GP1311 GP04 12 GP1413 GP05 14 GP1515 GP06 16 GP1617 GP07 18 GP1719 VCC 20 GNDJ15: RS485 (Auto direction)Pin # Signal Name1 RS485+2 RS485-3 GNDJ16: Power Connector (Terminal Block 5.0mm) Pin # Signal Name1 +5V2 GNDJ17: COM3 (Optional: TTL)Pin # Signal Name Pin # Signal Name1 DCD32 RXD33 TXD34 DTR35 GND6 DSR37 RTS3 8 CTS39 RI3 10 NCJ18: PRINTPin # Signal Name Pin # Signal Name1 STB- 14 AFD-2 PD0 15 ERR-3 PD1 16 INIT-SLIN-4 PD2 175 PD3 18 GND6 PD4 19 GND7 PD5 20 GND8 PD6 21 GND9 PD7 22 GND10 ACK- 23 GND11 BUSY 24 GND12 PE 25 GND13 SLCT 26 NCJ19: COM4 (Optional: TTL)Pin # Signal Name Pin # Signal Name1 DCD42 RXD43 TXD4 4 DTR45 GND6 DSR47 RTS4 8 CTS49 RI4 10 NCJ20: PC104 Connector – 64pinPin # Signal Name Pin # Signal Name* 2 GND1 IOCHCHKRESETDRV3 SD7 45 SD6 6 VCC7 SD5 8 IRQ99 SD4 10 -5V 11 SD3 12 DRQ2 13 SD2 14 -12V 15 SD1 16 OWS 17 SD0 18 +12V 19 IOCHRDY 20 GNDSMEMW*21 AEN 22*SMEMR 23 SA19 24* 25 SA18 26 IOW* 27 SA17 28 IOR* 29 SA16 30 DACK3 31 SA15 32 DRQ3* 33 SA14 34 DACK1 35 SA13 36 DRQ1*REFRESH 37 SA12 3839 SA11 40 SYSCLK 41 SA10 42 IRQ7 43 SA9 44 IRQ6 45 SA8 46 IRQ5 47 SA7 48 IRQ4 49 SA6 50 IRQ3DACK2* 51 SA5 5253 SA4 54 TC 55 SA3 56 BALE 57 SA2 58 VCC 59 SA1 60 OSC 61 SA0 62 GND 63 GND 64 GNDJ21: PC104 Connector – 40pinJ22: 4P Power Source (Interconnect to PC/104 – J20) Pin # Signal Name1 -5V2 -12V3 +12V4 GNDPin # Signal Name Pin # Signal Name1 GND2 GND3 MEMCS16 *4 SBHE *5 IOCS16 * 6 SA237 IRQ10 8 SA229 IRQ11 10 SA2111 IRQ12 12 SA2013 IRQ15 14 SA1915 IRQ14 16 SA1817 DACK0 * 18 SA1719 DRQ0 20 MEMR *21 DACK5 * 22 MEMW *23 DRQ5 24 SD825 DACK6 * 26 SD927 DRQ6 28 SD1029 DACK7 * 30 SD1131 DRQ7 32 SD1233 VCC 34 SD1335 MASTER * 36 SD1437 GND 38 SD1539 GND 40 NCJ23: PC/104 + (Optional)VI/O Default setting: +5VIf you need to use VI/O as +3.3V, please see the page 19. Pin # A B C D1 GND NC +5V AD002 VI/O(+5V) AD02 AD01 +5V3 AD05 GND AD04 AD034 C/BE0# AD07 GND AD065 GND AD09 AD08 GND6 AD11VI/O(+5V) AD10 GND7 AD14 AD13 GND AD128 +3.3V C/BE1# AD15 +3.3V9 SERR# GND NC PAR10 GND PERR# +3.3V NC11 STOP# +3.3V LOCK# GND12 +3.3V TRDY# GND DEVSEL#13 FRAME# GND IRDY# +3.3V14 GND AD16 +3.3V C/BE2#15 AD18 +3.3V AD17 GND16 AD21 AD20 GND AD1917 +3.3V AD23 AD22 +3.3V18 IDSEL0 GND IDSEL1 IDSEL2VI/O(+5V) IDSEL319 AD24 C/BE3#20 GND AD26 AD25 GND21 AD29 +5V AD28 AD2722 +5V AD30 GND AD3123 REQ0# GND REQ1# VI/O(+5V)24 GND REQ2# +5V GNT0#25 GNT1# VI/O(+5V) GNT2# GND26 +5V CLK0 GND CLK127 CLK2 +5V CLK3 GND28 GND INTD# +5V RST#29 +12V INTA# INTB# INTC#30 -12V NC NC GNDPlease remove the 0 ohm (1206 type) of R212 and add 0 ohm (1206 type) on R213J24: VGAPin # SignalNamePin #SignalName1 ROUT 2 GND3 GOUT 4 GND5 BOUT 6 GND7 HSYNC 8 GND9 VSYNCD 10 GNDJ25: LCD (DVO) ConnectorPin # Signal Name Pin # Signal Name1 +3.3V2 +3.3V3 LG24 LG35 LG46 LG57 NC 8 NC9 LR0 10 LR111 LR2 12 LR313 LR4 14 LR515 GND 16 NC17 NC 18 NC19 NC 20 GND21 NC 22 NC23 LB0 24 LB125 LB2 26 LB327 LB4 28 LB529 NC 30 NC31 LG0 32 LG133 GND 34 GND35 NC 36LCLK37 NC 38 LDE39 NC 40LHSYNC41 NC 42LVSYNC43 LBACKL 44 LVDDEN(Please refer to Appendix A, for TFT Flat Panel Data Output)J26~J31: Display type setup (CRT /LCD) Connector Pin # Signal Name1 VCCJ262 GPIOA3 GND1 VCCJ272 GPIOB3 GND1 VCCJ282 GPIOC3 GND1 VCCJ292 GPIOD3 GND1 VCCJ302 GPIOE3 GND1 VCCJ312 GPIOF3 GND(Please refer to Appendix D, for Display type setup)J33: LINE OUTPin # Signal Name1 LOUTR2 GND3 GND4 LOUTLJ34: MIC-INPin # Signal Name1 MICVREF2 GND3 GND4 MIC-IN2.5 System Mapping2.6 Watchdog TimerThere are two watchdog timers in Vortex86SX/DX CPU. One is compatible with M6117D watchdog timer and the other is new. The M6117D compatible watchdog timer is called WDT0 and new one is called WDT1.We also provide DOS, Linux and WinCE example for your reference. For more technical support, please visit: /tech or download the PDF file:/tech/vortex86dx/2.7 GPIO (General Purpose Input / Output)40 GPIO pins are provided by the Vortex86SX/DX for general usage in the system. All GPIO pins are independent and can be configured as inputs or outputs, with or without pull-up/pull-down resistors.We also offer DOS, Linux and WinCE example for your reference. For more technical support, please visit: /tech or download the PDF file:/tech/vortex86dx/2.8 SPI flash (Serial Peripheral Interface)As SPI Flash (Serial Peripheral Interface) offers many benefits including: reduced controller pin count, smaller and simpler PCBs, reduced switching noise, less power consumption, and lower system costMany of users may consider using a formatted SPI flash to boot for the system or emulate SPI flash as Floppy (A: Driver or B: Driver). Then you must know how to set for this condition in CMOS Setup and boot up under DOS 6.22, X-DOS, DR-DOS and Free DOS.For more technical support, please visit: /tech or download the PDF file: /tech/vortex86dx/C h a p t e r 3Driver InstallationVGAThe Vortex86DX processor also use external Display chip ““Volari™ Z9s” which is an ultra low powered graphics chipset with total power consumption at around 1-1.5 W. It is capable in providing VGA display output upto 1600x1200. With DVO interface, developers could easily connect flat Panel to support TFT and LVDS output.LANThe Vortex86DX processor also integrated 10/100Mbps Ethernet controller that supports both 10/100BASE-T and allows direct connection to your 10/100Mbps Ethernet based Local Area Network for full interaction with local servers, wide area networks such as the Internet.The controller supports: Half / Full-Duplex Ethernet function to double channel bandwidth, auto media detection.AUDIOCM119 is a highly integrated single chip USB audio controller specifically for VoIP (Voice over internet protocol) application. All essential analog modules are embedded in CM119, including dual DAC and earphone driver, ADC, microphone booster, PLL, regulator, and USB transceiver.8 GPIO pins can constitute a 24 key matrix directly support keypad control function without MCU.Many features are programmable with jumper pins or external EEPROM. Vender can customize unique USB VID/PID to EEPROM for VoIP software authentication. Moreover, individual unique phone number for each device is possible via serial number stored in external EEPROM.Operating system supportThe Vortex86SX-6155-V2 PC/104 CPU board supports Embedded software: Free DOS, DOS 6.22, PCDOS 7.1, DR-DOS, x-DOS, OS/2, Windows CE 5.0 / 6.0Please get the drivers from the Driver CD which attached with the standard packing ofVortex86SX-6155-V2 board or please get it from DMP official website:/tech/vortex86sx/Vortex86SX-6155-V2 also supports most of the popular Linux distributions, for more detail information, please visit DMP official website: /tech/vortex86sx/Appendix A. TFT Flat Panel Data OutputB. TFT Flat Panel Support ListSize Brand Resolution Model No.image 320x240 FG050701DSSWBG015.7” Data5.7” Optrex 320x240 55264GD057J-FW-ABN5.7” TOSHIBA 320x240 LTA057A343F5.7” Sharp 320x240 (QVGA / VGA) LQ057Q3DC02(QVGA / VGA) TCG057QV1AC-G105.7” Kyocera 320x240(QVGA / VGA) PD057VU4 /U55.7” PVI 320x240image 640x480 FG050710DSSWJG01/DG015.7” Data5.7” Ampire 640x480 AM-640480GTMQW-T00H5.7” URT 640x480 UMSH-8004MD-T5.7” Sharp 640x480 LQ057V3DG015.7” CPT 640x480 CLAA057VA016.4” PVI 640x480 V16C6448AC6.4” LG-PHILIPS 640x480 LB064V02/VT5/VT46.4” PVI 640x480 PD064VT26.4” Sharp 640x480 LQ064V3DG017” AUO 800x480 C070VW02V0image 800x480 FG0700A0DSSWBG01 7” Data7” LG-PHILIPS 800x480 (TFT 24 bits) LB070WV17” HITACHI 800x480 TX18D57VM2BAA 7” Samsung 800x480 LMS700KF057” PVI 800x480 PM070WL4 7” URT 800x480 UMSH-8173MD-1T HSIN 800x480 LW700AT9309 7” CHI8” Sharp 640x480 LQ080V3DG01Size Brand Resolution Model No.V024bits) A080SN01(TFT8” AUO 800x6008.4” Sharp 800x600 LQ084S3DG01 10.4” PVI 640x480 PD104VT1/VT2 10.4” NEC 640x480 NL6448AC33-18 10.4” NEC 640x480 NL6448AC33-29 10.4” NEC 640x480 NL6448BC33-59 10.4” Sharp 640x480 LQ104V1DG51/DG61 10.4” Sharp 640x480 LQ10d368 11” Sharp 800x480 LQ110Y3DG01 12.1” NEC 800x600 NL8060BC31-01C. LVDS Flat Panel Support ListIf you would like to use LVDS Flat Panel with Vortex86SX / Vortex86DX series, please contact our regional sales to get ICOP-0096 information or visit ICOP website:/pddetail.aspx?id=65&pid=4ICOP–0096: 18-bit TFT to LVDS converter and Cable-LVDS-30: LVDS Cable 30cmApproved LVDS Flat Panel ListSize Brand Resolution Model No.3.5” PVI 640x480 PD035VL15” PVI 640x480 PD050VL16.5” AUO 640x480 G065VN018.4” AUO 800x600 G084SN038.9” AUO 1024x600 A089SW018.9” CPT 1024x600 CLAA089NA0ACW10.4” AUO 800x600 G104SN0212.1” AUO 800x600 G121SN0115” AUO 1024x768 G150XG01D. Flat Panel Hardware Setting:The Vortex86SX-6155-V2 offers the Hardware setting for the various TFT LCD Flat Panels support and please make sure the jumper setting (J26~J31) before you connect the LCD.Display type setupConnector LCD 1-2 2-3J26 C J27 CJ28 X XJ29 X XJ30 CJ31 CNote: "C" means close; "X" means openE. Flat Panel Wiring and LightingHardwareBefore you connect the TFT LCD Flat Panel with Vortex86SX-6155-V2, please make sure that the input Voltage of LCD is +3.3V or NotBIOSPlease contact or e-mail our regional sales to get the special BIOS for the any TFT LCD Flat Panels.Wiring LCD CablePlease refer to Page 20 (J25: LCD connector) and Page 30~35. Or for more LCD lighting and integration service, please contact our regional sales or mail to *************.tw ,if you have any questions.F. TCP/IP library for DOS real modeDSock is a TCP/IP library for DOS real mode, which is used by RSIP. It provides simple C functions for programmer to write Internet applications. ICOP also provide Internet examples using DSock: BOOTP/DHCP, FTP server, SMTP client/server, HTTP server, TELNET server, Talk client/server, etc.DSock provides a lot of example source code. Programmer can add Internet functions to their project easily and save development time. With a utility "MakeROM”, programmer also can make a ROM image to fit their application, those examples can be seen in the following Application systems: Mity-Mite Serial Server,Web Camera Tiny Server and RSIP Serial Server.DSock is free for All ICOP products using M6117D/Vortex86/Vortex86SX/Vortex86DX CPU and ICOP also provide the business version of DSock for those customers who are using other x86 CPUs.If you would like to use DSock or business version of DSock, Please mail to *************.tw or contact your regional sales.Please download the trial DSock software and Utilities from our website:/tech/dmp-lib/dsock/G. BIOS Default settingIf the system cannot be booted after BIOS changes are made, Please follow below procedures in order to restore the CMOS as default setting.Press “End” Key, when the power onPress <Del> to enter the AMI BIOS setupPress “F9” to Load Optimized DefaultsPress “F10” to Save configuration changes and exit setupWarrantyThis product is warranted to be in good working order for a period of one year from the date of purchase. Should this product fail to be in good working order at any time during this period, we will, at our option, replace or repair it at no additional charge except as set forth in the following terms. This warranty does not apply to products damaged by misuse, modifications, accident or disaster. Vendor assumes no liability for any damages, lost profits, lost savings or any other incidental or consequential damage resulting from the use, misuse of, originality to use this product. Vendor will not be liable for any claim made by any other related party. Return authorization must be obtained from the vendor before returned merchandise will be accepted. Authorization can be obtained by calling or faxing the vendor and requesting a Return Merchandise Authorization (RMA) number. Returned goods should always be accompanied by a clear problem description.Vortex86SX-6155-V2 Vortex86SX™PC/104 CPU Module 38。
piezobrush PZ3 冷激光手持设备说明书
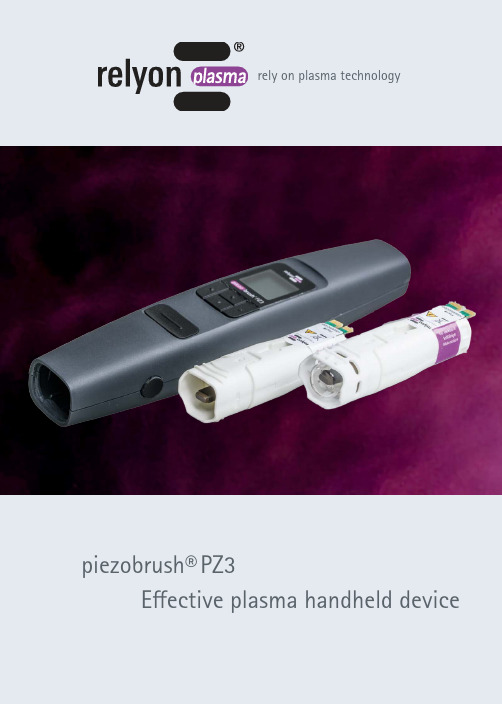
piezobrush® PZ3Effective plasma handheld devicerely on plasma technologyEffective plasma device for manual usePiezobrush® PZ3 has been designed as a compact plasma handheld device for use in laboratories, pre- development and assembly of small series. With a maximum power consumption of 18 W, the Piezoelectric Direct Discharge (PDD®) technology is used to generate cold active plasma at a temperature of less than 50°C. Plasma is used to increase the surface energy of many materials with high efficiency, as well as to reduce germs and odors.Fields of application◊Joining technology◊Development and optimization of production processes ◊Research facilities and laboratories◊Microbiology, microfluidics and food technology ◊Medical and dental technology◊Prototype and architectural model making ◊Small-scale productionPossible use cases◊Activation and functionalization of surfaces of various materials ◊Improvement of wettability◊Optimization of bonding, painting, printing and coating processes◊Surface treatment of plastics, glass, ceramics, metals, semiconductors, natural fibres and composite materials ◊Ultra-fine cleaning and odor reductionTechnical dataElectrical connection: 110-240 V / 50-60 Hz Power consumption: max. 18 W Weight: 110 gSound pressure level: 45 dB Plasma temperature: < 50 °C Treatment speed: 5 cm²/sTypical treatment distance: 2 - 10 mm Typical treatment width: 5 - 29 mmDesign: Handheld unit with plug-in power supply, integrated fanIntroduction to surface treatmentFor processing and end use of materials, their surface properties are of vital importance. These can be positively influenced by selective surface treatment with plasma to achieve an ideal end result. For example, the cleanliness and wettability of a surface are of decisive importance for adhesion in bonding, printing, painting or coating processes.Even in a clean state, many surfaces exhibit insufficient wettability, which is further worsened by contamination. As a result, liquids such as glue or ink will bead off and cannot adhere. This state is referred to as a low surface energy state of the solid. If this surface energy is lower than the surface tension of the liquid, the wetting and thus the adhesion is insuf-ficient. Plasma activation of a surface increases its surface energy and molecular anchor groups are formed which react with those of the liquid. This leads to improved wetting and consequently to an optimized adhesion of suitable liquids.◊Round droplet ◊Low surface energy◊Insufficient wettability of liquids ◊Poor adhesion of glue, inks, etc. ◊Very flat droplet ◊High surface energy◊Increased wettability of adhesives ◊Strong adhesion and bondingContact angle analysis as a method to determine the effectiveness of plasma treatmentTo prove the effectiveness of plasma treatment, a contact angle analysis is often performed: A drop of a liquid with known surface tension is applied to the surface before the plasma treatment and the contact angle between liquid and solid is measured with a contact angle measuring device. The surface is then treated with plasma and a contact angle measurement is carried out accordingly. By determining the contact angle of a polar and a non-polar liquid, the surfaceenergy is calculated and thus the effectiveness of the plasma treatment is quantified.LiquidLiquidSolid body - untreated Solid body - plasma treatedPlasma treatment Untreated surfacePlasmatreated surfacePlasma treatment Contact angleContact anglePlasma activation with piezobrush® PZ3Optimized adhesive bonding with plasmaIf a surface is functionalized with plasma before bonding, the following bonds show a significantly improved adhesion. Plasma can be used on a variety of materials: Metals, glass, ceramics and even natural materials such as wood, natural fibres and textiles react very well to plasma treatment. The adjoining table shows a comparison of the ultimate tensile strength of 2K epoxy bonds between untreated plastics and bonds between the same plastics with previous plasma treatment. The comparison shows a significantly improved adhesion.Application example: Bonding of PA 12In 3D printing, large parts are often manufactured as individual parts made of PA 12 and subsequently bonded - however, often with considerable adhesion problems. By means of a plasma pre-treatment, up to three times the strength of the adhesive joints is achieved without the use of environmentally harmful chemicalprimers.Plasma treatment before labelingA coated metal cover is plasma treated with the piezobrush® PZ3 and the module earfield. The plasma treatment significantly improves the subsequent labeling on the cover. This is partly due to the fine cleaning and part-ly to the activation of the surface, both effects of the plasma pre-treatment.Improved wettability by plasma treatmentFor many industrial processes it is important that materials, e.g. plastics, have a specific surface energy in order to achieve a certain quality of the subsequent processes. For this reason, plasma is often used as a pre-treatment to remove the finest contaminants and also to compensate any differences between material batches. The chart shows that the surface energy of the variousplastics can be increased significantly.24681012plasma treateduntreatedGFK/GFK ABS/ABSPEEK/PEEK U l t i m a t e t e n s i l e s t r e n g t h [N /m m ]1020304050607080plasma treateduntreated GFKTeflon /PTFEPOM PVCA-PETPPPEPMMAPA 6.6 ABSS u r a c e e n e r g y [m N /m ]Plasma activation with piezobrush® PZ3Application example: Printing on PTFEMany plastics such as Polytetrafluoroethylene (PTFE) are difficultto print on. In the photo only the right side has been treated withplasma before printing. The comparison clearly shows that theplasma pre-treatment of the substrate not only leads to an evenprint image, but also to a considerably better adhesion of the ink.Plasmatreatment prior to printingPlasma treatment improves adhesion of printing inks and varnisheson the surface, thus significantly enhances the print quality. The il-lustration shows a droplet of ink applied to a surface and below thesubsequent print result. The first droplet has a high contact angleof more than 90° and therefore wets the surface poorly, which cau-ses the ink to contract on the surface and is not distributed evenly.The best result is achieved when the contact angle is 0° - the inkwets the surface optimally and creates an even print image.Application example: PDMS and glassIn microfluidic chip manufacturing, PDMS chips are often connec-ted to glass carriers, which is not possible without pre-treatment.Only through plasma pre-treatment of the surfaces of both ma-terials a bond can be formed between PDMS and glass. With thepiezobrush® PZ3 the treatment is simple, fast and straightforward.Activation with plasmaThe plasma activation of a surface increases its surface energy andpolar molecular end groups are generated. These act as depositionsites for liquids applied to the surface and ensure that they canadhere better. Plasma activation modifies the surface and increasessurface energy, resulting in a significantly better wettability.Solid - plasma treatedPlasma treatmentSolid - untreatedIn principle, all materials can be treated with atmospheric pressure plasma from the piezobrush® PZ3 handheld plasma device. This surface treatment with atmospheric-pressure plasma hardly causes any temperature input on the material, which also has the advantage that there is no risk of overtreatment even with temperature-sensitive materials such as plastics.Typical materials◊Plastics and composites ◊Metals and metal alloys◊Glass, ceramics, natural stone ◊Natural leather, artificial leather◊Natural fibre, wood, paperThe following diagrams give an overview which materials are typically treated with piezobrush® by our customers.The first diagram shows that plastics represent the majority share of materials treated with the plasma handheld device. Since there is a large variety of plastics, the second diagram shows the different types of plastics that are typically trea-ted with this cold atmospheric pressure plasma.Which materials can be treated?MaterialsPlasticsPolybutylene terephthalate (PBT)Polystyrene (PS)Silicones, Silicone rubber (VMQ)Polyurethane (PUR)Exchangeable modules and displayModule StandardThis module is designed for the surface treatment of non-conductive substra-tes such as plastics, ceramics or glass. For effective treatment, a module-sub-strate-distance of 1 to 5 mm is recommended. If uncontrolled arcing occurs on the substrate during use, the device switches off automatically. In this case the surface is at least partially conductive and should therefore be treated with the Nearfield module.Module NearfieldThis module is used to treat (partially) electrically conductive materials such as metals, CFRP, lead glass or conductive plastics. However, this module may also be necessary for the ideal treatment of materials with conductive coatings or assemblies with conductive components. With this module, the plasma only ignites when it is close enough to a conductive surface (this may also be hidden under a thin insulating layer). At a distance of a few millimeters, a violet glow is visible in the gap between module and substra-te indicating that the treatment is being performed.Different surfaces have to be activated with the appropriate accessories to achieve an ideal result. Currently two different exchangeable modules are available for the piezobrush® PZ3 plasma handheld device. The PDD technology used to generate the cold plasma in piezobrush® PZ3 is based on the discharge of high electric fields. Therefore, the electricalconductivity of the component to be treated is of decisive importance when choosing the modules.The device automatically detects which module is currently in the device and automatically adjusts the parameters accordingly.DisplayFor process control of plasma treatment, the piezobrush® PZ3 is equipped with various features that can be selected and modified via the display. ◊Process control:◊Stopwatch: For monitoring the treatment time◊Countdown: Time setting with automatic switch-off function ◊Metronome: Acoustic feedback after defined treatment time ◊Power adjustment: Reduction of plasma power in several incrementsDo you have questions about our products or about plasma technology in general? Our team will be more than happy to help you with support and advice.relyon plasma GmbHA TDK Group Company Osterhofener Straße 693055 Regensburg, Germany Phone: +49 941 60098 0 Fax: +49 941 60098 100 Email: **********************More application examples: Application videos:rely on plasma technology。
Bitstream3X控制器使用说明-乐声音频

BitStream 3X MIDI控制器快速入门成都乐声科技王昕<一> 连接将Bitstream 3X 加入到电脑音乐系统中:以下是Bitstream 3X以及其他MIDI设备接入电脑的示意图:a.Bitstream 3X可以通过随机附送的USB线接入电脑。
b.也可通过MIDI电缆或者SYNC24电缆将其他MIDI设备接入系统中来。
(例如:MIDI主键盘,SYNC24 设备…)<二> 驱动安装与硬件重置Bitstream 3X也属于“即插即用”设备,因为其兼容USB-MIDI协议,在Windows XP、OS X和Linux中,Bitstream 3X 不需要安装任何特殊驱动,插上识别一次之后就可以使用。
a.首次插入Bitstream 3X请注意,当Bitstream 3X插入电脑后,电脑将自动安装所需要的常规驱动,以后连入Bitstream 3X直接将被电脑识别。
b.当电脑识别Bitstream 3X后,在Bitstream 3X上也将做出被识别的反映,显示屏右上方将显示USB图形。
(如下图显示)c.类同与其他的USB AUDIO DEVICE,当电脑识别Bitstream 3X后,它所附带的MIDI外围也将在系统以及SONAR等音序软件中列出,对应识别列表如下图显示:(注:Bitstream 3X接入电脑后如果不习惯电脑识别的USB AUDIO DEVICE名称,Wave Idea 公司还在Bitstream 3X所附送的光盘中带有安装信息文件---Waveidea_usb_driver.zip。
将该安装信息文件装入系统后,在Windows XP设备管理器中就会出现Wave Idea Bitstream 3X的名字。
)<三> 硬件对应软件操作快速入门Bitstream 3X提供的控制功能包括:8个推子、1个Crosse Fader、32个旋钮和14个按钮统统可以自定义参数,并且允许将定义的情况编组,可以方便地记忆和唤出场景。
Olimex TMS320-XDS100-V3 数字信号处理器和 ARM 仿真器和适配器用户手册说明
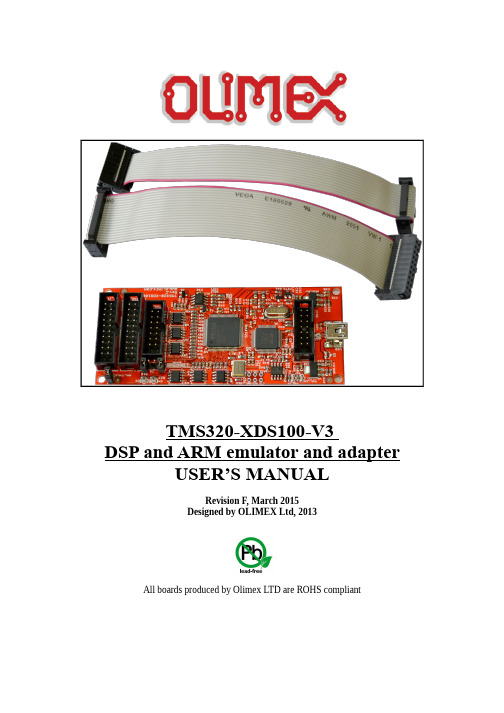
TMS320-XDS100-V3DSP and ARM emulator and adapter USER’S MANUALRevision F, March 2015Designed by OLIMEX Ltd, 2013All boards produced by Olimex LTD are ROHS compliantDISCLAIMER© 2015 Olimex Ltd. Olimex®, logo and combinations thereof, are registered trademarks of Olimex Ltd. Other product names may be trademarks of others and the rights belong to their respective owners.The information in this document is provided in connection with Olimex products. No license, express or implied or otherwise, to any intellectual property right is granted by this document or in connection with the sale of Olimex products.It is possible that the pictures in this manual differ from the latest revision of the board.The product described in this document is subject to continuous development and improvements. All particulars of the product and its use contained in this document are given by OLIMEX in good faith. However all warranties implied or expressed including but not limited to implied warranties of merchantability or fitness for purpose are excluded. This document is intended only to assist the reader in the use of the product. OLIMEX Ltd. shall not be liable for any loss or damage arising from the use of any information in this document or any error or omission in such information or any incorrect use of the product.This evaluation board/kit is intended for use for engineering development, demonstration, or evaluation purposes only and is not considered by OLIMEX to be a finished end-product fit for general consumer use. Persons handling the product must have electronics training and observe good engineering practice standards. As such, the goods being provided are not intended to be complete in terms of required design-, marketing-, and/or manufacturing-related protective considerations, including product safety and environmental measures typically found in end products that incorporate such semiconductor components or circuit boards.Olimex currently deals with a variety of customers for products, and therefore our arrangement with the user is not exclusive. Olimex assumes no liability for applications assistance, customer product design, software performance, or infringement of patents or services described herein.THERE IS NO WARRANTY FOR THE DESIGN MATERIALS AND THE COMPONENTS USED TO CREATE TMS320-XDS100-V3.THEY ARE CONSIDERED SUITABLE ONLY FOR TMS320-XDS100-V3.Table of Contents DISCLAIMER (2)CHAPTER 1 OVERVIEW (4)1. Introduction to the chapter (4)1.1 Features (4)1.2 Target market and purpose of the board (5)1.3 Organization (5)CHAPTER 2 SETTING UP THE TMS320-XDS100-V3 (6)2. Introduction to the chapter (6)2.1 Electrostatic warning (6)2.3 Requirements (6)2.4 Cables, layouts, connection (6)2.5 Powering the board and installation procedure for CCS v5 and CCS v6 (8)2.6 Powering the board and installation procedure for IAR EW for ARM 6 (9)CHAPTER 3 TMS320-XDS100-V3 DESCRIPTION (10)3. Introduction to the chapter (10)3.1 Layout (top view) (10)CHAPTER 4 INTERFACES AND HARDWARE (11)4. Introduction to the chapter (11)4.1 JTAG connectors (11)4.1.1 JTAG (11)4.1.2 TI_JTAG_14 (11)4.1.3 TI_JTAG_20 (11)4.1.4 ARM_JTAG_20 (11)4.2 USB mini (12)4.3 Test pads (12)4.4 LEDs (12)4.4.1 Power LEDs (12)4.4.2 D3 and D4 (12)4.5 Jumpers (12)4.5.1 Jumper ARM_JTAG_E (12)4.5.2 Jumpers J4 and J5 (12)CHAPTER 5 REVISION HISTORY AND SUPPORT (13)5. Introduction to the chapter (13)5.1 Document revision (13)5.2 Hardware revision (14)5.3 Useful web links and purchase codes (15)5.4 Product support (16)CHAPTER 1 OVERVIEW1. Introduction to the chapterThank you for choosing the TMS320-XDS100-V3 emulator from Olimex!TMS320-XDS100-V3 is an implementation of the Texas Instruments' ultra-low-cost USB-interface JTAG hardware reference design. This emulator provides JTAG access to Texas Instruments' JTAG-based devices.This document provides a user’s guide for the Olimex TMS320-XDS100-V3. As an overview, this chapter gives the scope of this document and lists the board’s features. The document’s organization is then detailed.1.1 FeaturesAmong the features of the Olimex implementation of the XDS100v3 design are:•TMS320-XDS100-V3 hardware is designed to work with CCS5 or CCS6 software•Grants free license for TI's Code Composer Studio 5 and TI's Code Composer Studio 6•Supported in IAR EW for ARM (for IAR versions after 6.40)•Equipped with three JTAG connectors for different JTAG layouts: TI 14-pin JTAG; TI 20-pin JTAG and standard ARM 20-pin JTAG layout•All plastic headers have 0.1" pin step for easier access•Two compatible female-female cables included – 14-pin and 20-pin ones.•Works with targets in 1.65V-5.0V range•No need for external power supply, all power is taken from USB and the target•IEEE 1149.7 capable emulator with a USB interface•Can function as an 1149.7 adapter for use with existing scan controllers.•Software compatible with XDS100v2 (except link delay and IEEE 1149.7 modes)•Physical jumper to select emulator or adapter mode•Operates in 1149.7 Class 4, up to 25MHz•LED to indicate IEEE 1149.7 Class 4 operation•LED to indicate operation in adapter mode•Supported devices: TMS320C28xx, TMS320C54xx, TMS320C55xx, TMS320C674x, TMS320C64x+, TMS320C66x, ARM9, ARM Cortex A9, ARM Cortex A8, ARM CortexM3, ARM Cortex R4•Board dimensions (4.15×1.8)" ~ (10.5×4.6)cmFor full list of XDS100v3 design features visit the TI's wiki address:/index.php/XDS100#What_is_the_XDS100.3F1.2 Target market and purpose of the boardThe main purpose of the board is programming and debugging Texas Instruments' JTAG-based devices. Typically, these are DSP (digital signal processing) targets AND high-speed ARM targets. The board can also act as adapter to existing scan controllers.The design of the board follows the schematics and the recommendations provided by Texas Instruments.1.3 OrganizationEach section in this document covers a separate topic, organized as follow:–Chapter 1 is an overview of the board usage and features–Chapter 2 provides a guide for quickly setting up the board–Chapter 3 contains the general board diagram and layout–Chapter 4 mentions the main software tools used with TMS320-XDS100-V3–Chapter 5 is an explanation of the interfaces, the LEDs, the jumpers position–Chapter 6 contains the revision history, useful links and support informationCHAPTER 2 SETTING UP THE TMS320-XDS100-V32. Introduction to the chapterThis section helps you set up the Olimex TMS320-XDS100-V3 emulator/adapter for the first time. Please consider first the electrostatic warning to avoid damaging the board, then discover the hardware and software required to operate the board.The procedure to power up the board is given, and a description of the default board behavior is detailed.2.1 Electrostatic warningTMS320-XDS100-V3 is shipped in a protective anti-static package. The board must not be exposed to high electrostatic potentials. A grounding strap or similar protective device should be worn when handling the board. Avoid touching the component pins or any other metallic element.2.3 RequirementsIn order to set up the TMS320-XDS100-V3 optimally, the following items are required:- USB-A to mini-USB cable- Set of software tools (preferably Code Composer Studio v5 or Code Composer Studio v6 – check the table – /index.php/XDS100#XDS100_Installation_Instructions)- a TARGET from the supported list (can be found here:/index.php/XDS100#Installation_for_Code_Composer_Studio_v5.1.x) Note that there are two ribbon cables included in the package – for the TI_JTAG_14 and theTI_JTAG_20 (or ARM_JTAG) connectors.2.4 Cables, layouts, connectionInitially there might be a slight confusion for the proper cable setup which is caused by the number of different connectors you might meet working with Texas Instruments ARM processors.The TMS320-XDS100-V3's 14pin JTAG connector named “TI_JTAG_14” has the exact layout of TI's 14pin JTAG. Both connectors have 0.1'' step.The 20pin TI JTAG connector is named “TI_JTAG_20”. It might be found next to the 14pin JTAG of TMS320-XDS100-V3. TI_JTAG_20 follows the signal layout proposed by Texas Instruments but it uses bigger connector with pin holes with 0.1'' step again (the original CTI design suggests 0.05''). The 20pin ARM JTAG connector is named “ARM_JTAG”. It is located at the edge of the top side of the board. ARM_JTAG is the official ARM 20-way 0.1'' pitch connector. The signal layout also follows the ARM recommendations. It can be used in either standard JTAG (IEEE 1149.1) mode or Serial Wire Debug (SWD) mode.Refer to the table below for the proper connections. The first 4 columns represent the TI layout of TI_JTAG_14 and TI_JTAG_20 connectors of TMS320-XDS100-V3, the last 2 show the 20-pin ARM_JTAG layout.*The entries NA means the standard signal was not routed (was not used for the JTAG connection). **The value of TDIS is controlled by the ARM_JTAG_E jumper. If you use ARM_JTAG connector keep the jumper closed. If you use TI_JTAG_14 or TI_JTAG_20 – open the ARM_JTAG_E jumper.A useful table for the relations of the signals might be found at the following web address: /index.php/JTAG_Connectors#Pinout2.5 Powering the board and installation procedure for CCS v5 and CCS v6 The XDS100v3 board is powered via the mini USB.A. Install Code Composer Studio 5.1.x (or newer) before connecting XDS100 USB hardware.B. Install the EmuPack with XDS100v3 support. It is usually downloaded via the update button.C. Connect the XDS100 hardware1. Make sure the Code Composer Studio v5.1.x (or newer) and EmuPack with XDS100v3support is installed FIRST before plugging in the XDS100 HW to the PC.2. Connect USB cable from the PC to the XDS100 hardware. Connect the JTAG to thetarget board (be careful to plug it in correctly: pin 1 should go to pin 1. Red strip usually indicates the side of pin 1)3. You will notice small popups to inform user that USB hardware is recognized andinstalled correctly. No input are required.D. Setup Code Composer Studio v5.1.x4. Start Code Composer Studio and create a new target configuration.5. Select XDS100v3 as connection type6. Select device (target).E. The configuration of the emulator in CCS v5.1.x is shown below (the one in CCS v6 is quite similar):2.6 Powering the board and installation procedure for IAR EW for ARM 6A. Install IAR EW for ARM (version 6.40 or newer) before connecting XDS100 USB hardware.B. Connect the TMS320-XDS100-V3 to the mini USB of a computer.C. Install the drivers for XDS100v3 hardware – there is an executable typically located in“C:\Program Files (x86)\IAR Systems\Embedded Workbench for ARM 6\arm\drivers\ti-xds”D. Load a demo project and right-click over the project in the “Workspace” window. Select “Options” and click the “Debugger” group then choose “TI XDS100” from the drop-down menu. Then in the tab under the “Debugger” group go to “TI XDS100” and from the emulator menu select “TI XDS100v3 USB Emulator”.E. You are now ready to debug your project!CHAPTER 3 TMS320-XDS100-V3 DESCRIPTION3. Introduction to the chapterHere you get acquainted with the main parts of the board. Note the names used on the board differ from the names used to describe them. For the actual names check the TMS320-XDS100-V3 board itself.3.1 Layout (top view)CHAPTER 4 INTERFACES AND HARDWARE4. Introduction to the chapterIn this chapter the connectors function will be pointed, the meaning of the LEDs states will be explained, and the function of the jumpers would be clarified.4.1 JTAG connectorsThere are four JTAG connectors on this board. Each of them has 0.1'' step between pins. They are in the sub-chapters below.4.1.1 JTAGThe JTAG connector (note the one WITHOUT any prefix or suffix to the name) is used during production to upload the firmware of TMS320-XDS100-V3. It has a 14-pin TI JTAG layout.You can not program targets using this connector! It is used to program the emulator itself!It can be used to restore the firmware of the the unit. The firmware is located inside the FPGA integrated circuit.4.1.2 TI_JTAG_14Used for 14-pin TI JTAG connection. The TI_JTAG_14 follows the JTAG layout of Texas Instruments. This interface might be used to communicate with Olimex TMS320-P28016 and Olimex TMX320-P28027. The interface might be used with any target that follows the 14-pin TI JTAG layout.Jumper ARM_JTAG_E has to be open to be able to use TI_JTAG_14 successfully!4.1.3 TI_JTAG_20Used for 20-pin TI JTAG connection. The TI_JTAG_20 follows the JTAG layout of Texas Instruments. Note that the step is different from the original TI JTAG connector. The original connector has a 0.05'' step connector, while the one used by Olimex has 0.1''. The interface might be used with any target that follows the 20-pin TI JTAG layout.Jumper ARM_JTAG_E has to be open to be able to use TI_JTAG_20 successfully!4.1.4 ARM_JTAG_20ARM_JTAG_20 connector was added in hardware revision C. It is used for 20-pin ARM JTAG connection. The interface might be used with any TI target that follows the 20-pin ARM JTAG layout. For example, boards like “Stellaris EKS-LM3S3748” can be debugged externally only using tools with ARM JTAG layout.Jumper ARM_JTAG_E has to be closed to be able use ARM_JTAG_20 successfully!4.2 USB miniStandard USB mini cable connector. Used to connect the emulator to a personal computer.4.3 Test padsThere are six testpads provided (CTS; RXD; GND; RTS; RXD; 3.3V). They allow access to the FTDI chip of the board. They can be used for debugging purposes and also for direct communication with the FT2232HL IC. The names are easily visible near each pad.4.4 LEDsThere are four LEDs on TMS320-XDS100v3. Two for indicating power input and power output and two for the current board-mode.4.4.1 Power LEDsThe PWR_LED shows whether the board is powered. The PWR_EN shows whether the board can power the target.4.4.2 D3 and D4The D3 and D4 LEDs show the state of, respectively, J4 and J5 jumpers.4.5 JumpersThere are three PTH jumpers on TMS320-XDS100-V3: ARM_JTAG_E, J4, and J5.4.5.1 Jumper ARM_JTAG_EThe value of pin 4 (signal “TDIS”) of every JTAG interface is controlled by ARM_JTAG_E jumper. Important:In the Texas JTAG layouts TDIS is used to detect when the target is disconnected from the emulator. It is usually a pull-up in the emulator and GND on the target. The emulator senses the removal of GND. If you use TI_JTAG_14 or TI_JTAG_20 – open the ARM_JTAG_E jumper.Pin 4 needs to be pulled-down in the ARM JTAG layout. If you use ARM_JTAG connector keep the jumper closed.4.5.2 Jumpers J4 and J5They are responsible for the emulation – adapter configuration. When J4 and J5 are open – the chosen mode is emulator mode. When J4 an J5 are closed the chosen mode is adapter.For general use of the TMS320-XDS100-V3 as emulator and debugger, please, keep jumpers J4 and J5 open.CHAPTER 5 REVISION HISTORY AND SUPPORT5. Introduction to the chapterIn this chapter you will find the current and the previous version of the document you are reading. Also the web-page for your device is listed. Be sure to check it after a purchase for the latest available updates and examples.5.1 Document revision5.2 Hardware revisionRemember to check the schematics and the board design files to compare the differences.5.3 Useful web links and purchase codesThe web page you can visit for more info on your device ishttps:///Products/DSP/Emulators/TMS320-XDS100-V3/.ORDER CODES:TMS320-XDS100-V3 – completely assembled and tested JTAG emulatorHow to purchase?You can purchase directly from our online shop or from any of our distributors. Note that usually it might be faster and cheaper to purchase Olimex products from our distributors. List of confirmed Olimex LTD distributors and resellers: https:///Distributors.Please visit https:/// for more info.5.4 Product supportFor product support, hardware information and error reports mail to: ******************. All document or hardware feedback is welcome. Note that we are primarily a hardware company and our software support is limited. Please consider reading the paragraph below about the warranty of Olimex products.All goods are checked before they are sent out. In the unlikely event that goods are faulty, they must be returned, to OLIMEX at the address listed on your order invoice.OLIMEX will not accept goods that have clearly been used more than the amount needed to evaluate their functionality.If the goods are found to be in working condition, and the lack of functionality is a result of lack of knowledge on the customers part, no refund will be made, but the goods will be returned to the user at their expense.******************************************************************************* number before shipping back any merchandise. Please include your name, phone number and order number in your email request.Returns for any unaffected development board, programmer, tools, and cables permitted within 7 days from the date of receipt of merchandise. After such time, all sales are considered final. Returns of incorrect ordered items are allowed subject to a10%restocking fee.What is unaffected? If you hooked it to power, you affected it. To be clear, this includes items that have been soldered to,or have had their firmware changed.Because of the nature of the products we deal with (prototyping electronic tools) we cannot allow returns of items that have been programmed, powered up, or otherwise changed post shipment from our warehouse.All returned merchandise must be in its original mint and clean condition. Returns on damaged, scratched, programmed, burnt, or otherwise 'played with' merchandise will not be accepted.All returns must include all the factory accessories which come with the item. This includes any In-Circuit-Serial-Programming cables, anti-static packing, boxes, etc.With your return, enclose your PO#. Also include a brief letter of explanation of why the merchandise is being returned and state your request for either a refund or an exchange. Include the authorization number on this letter, and on the outside of the shipping box.Please note: It is your responsibility to ensure that returned goods reach us. Please use a reliable form of shipping. If we do not receive your package we will not be held liable. Shipping and handling charges are not refundable.We are not responsible for any shipping charges of merchandise being returned to us or returning working items to you.The full text might be found at https:///wiki/GTC#Warranty for future reference.。
V3产品使用说明
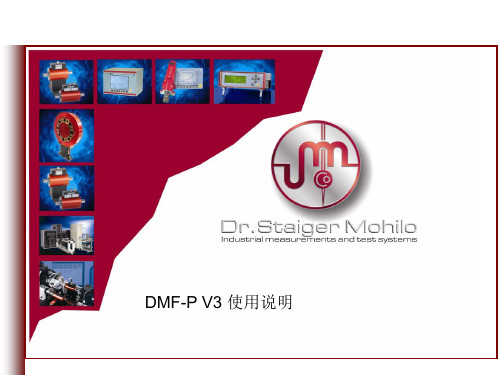
Parameter input Program no. 02 Smooth factor Trig. yTS, yTE Trig. xTE shut-off y,x Job no.: 3964 DW/OF Vel start end Vel min max Dircection X/Y Master sample 0 0,0 0,00 0,0 987654321 0/ 0 0,00 0,00 0 0,00 N mm N
评估结果, OK 或者NOK
单位
第一层 Graph
测量程序 标定压力值 压力窗口 压力位移窗口1 窗口号 位移窗口4 200,0 N
5 4
压力位移曲线
“ 曲线 ” 界面
这个曲线窗口显示压力、位移特性以及所有的公差窗口
通过 Tab(F1) 返回界面
Байду номын сангаасProg.2
通过 Hcopy(F2) 复制
1 3 2
窗口号 测量程序 (00 - 31) 最小实际值 最大实际值 最小设置值 最大设置值 Measured values : tabular form P02 wn1 wn2 wn3 wn4 wn5 wn6 wn7 wn8 OK Graph Servi F1 F2 F3 F4 Setpt Calib F5 F6 Docu F7 通过 Docu(F7) 进入文档 Docu(F7 文档界面 文档 actual values setpoint values min max min max 0,0 33,6 61,6 45,0 41,9 86,7 4,4 153,5 0,0 25,0 35,0 4,2 130,0 90,0 65,0 85,0 4,8 170,0 N N N mm N 通过 Graph(F2) 进入曲线 曲线界面 ( ) 曲线
Drawmer S3三带立方式真空管压缩器操作手册说明书

DRAWMERS3Three-Band Stereo Vacuum Tube CompressorOPERATOR’S MANUALCONTENTSWarranty Safety Consideration Chapter 1 - IntroductionIntroduction Installation Audio ConnectionsPower Connection Chapter 2 - Control DescriptionControl Description Quick Setup Procedure Chapter 3 - General InformationIf a fault developsContacting DrawmerSpecification Block Diagram . . . . . . . . . . . . . . . . . . . . . . . . . . . . . . . . . . . . . . . . . . . . . . . . . . . . . . . . . . . 2. . . . . . . . . . . . . . . . . . . . . . . . . . . . . . . . . . . . . . . . . . . . . . . . 2 . . . . . . . . . . . . . . . . . . . . . . . . . . . . . . . . . . . . . . . . . . . . . . . . . . . . . . . 3 . . . . . . . . . . . . . . . . . . . . . . . . . . . . . . . . . . . . . . . . . . . . . . . . . . . . . . . . 4. . . . . . . . . . . . . . . . . . . . . . . . . . . . . . . . . . . . . . . . . . . . . . . . . 5 . . . . . . . . . . . . . . . . . . . . . . . . . . . . . . . . . . . . . . . . . . . . . . . . . 5. . . . . . . . . . . . . . . . . . . . . . . . . . . . . . . . . . . . . . . . . . . . . . . . . 6. . . . . . . . . . . . . . . . . . . . . . . . . . . . . . . . . . . . . . . . . . . . . 9 . . . . . . . . . . . . . . . . . . . . . . . . . . . . . . . . . . . . . . . . . . . . . . . . . 10 . . . . . . . . . . . . . . . . . . . . . . . . . . . . . . . . . . . . . . . . . . . . . . . .10 . . . . . . . . . . . . . . . . . . . . . . . . . . . . . . . . . . . . . . . . . . . . . . . . . . . . .10. . . . . . . . . . . . . . . . . . . . . . . . . . . . . . . . . . . . . . . . . . . . . . . . . . . 112DRAWMER S3 O PERATOR’S M ANUAL3DRAWMER S3 O PERATOR’S M ANUALDRAWMERS3THREE-BAND STEREO VACUUM TUBE COMPRESSORThe new S3 Three-Band Stereo Vacuum Tube Compressor incorporates the very latest in Ivor Drawmer designs andthe aim from the very beginning was to create a 'no technical compromise' circuit using only the highest gradeCHAPTER 1INTRODUCTIONThe Key Features are as follows:• Fully balanced signal path class A design • Isolation transformers in and out • 20 x active tube stages• High power 'push/pull' output stage delivering up to +30dBu • Variable band split points• Switchable 'peak' or 'VU' metering to display transients, with +10dB or +20dB re-scaling • 'Air' mode for high band • 'Big' mode for low band• Switchable mute and bypass on each band • Individual gain reduction metering on all bandscomponents. The S3 forms the basis of a 'Signature Series'and offers previously unattainable control and tonality over each of the three bands - gain control at each stage provides precise spectral balancing.4DRAWMER S3 O PERATOR’S MANUALThe S3 is designed for standard 19" rack mounting and occupies 3U of rack space. Fibre or plastic washers may be used to prevent the front panel becoming marked by the mounting bolts. Always connect the mains earth to the unit.Because the S3 contains ten valves it will generate moreheat than a simple solid state unit. Avoid mounting the unit directly above power amplifiers or power supplies thatradiate significant amounts of heat. In addition it is advised that you leave at least 1U of space above to allow heat to dissipate. Alternatively, a fan should be fitted somewhere near to the rear of the unit to circulate cooler air and help expel any excess heat. (see fig. 1).It is also recommended to the S3 is mounted horizontally to allow heat to escape vertically through the vents on the lid. To mount at an angle may cause the S3 to overheat which will damage internal components (see fig. 2).INSTALLATIONfig.2 TYPICAL S3 SETUPfig.1 RACK MOUNT POSITIONINGfig.2 MOUNT HORIZONTALLY5DRAWMER S3 O PERATOR’S M ANUALThe unit will have been supplied with a power cable suitable for domestic power outlets in your country.For your own safety it is important that you use thiscable. The unit should alwaysbe connected to themains supply earth using this cable, and no other.If for some reason the unit is to be used at a mains input operating voltage which is different to that as supplied, the following procedure must be carried out.1: Disconnect the unit from the mains.2: Remove the two screws holding the voltage selection cover-plate.3: Remove the cover plate and slide the switch fully to its opposite end.4: Rotate the cover plate one half turn (180 degrees)and refit the two screws.5: Replace with a correctly rated fuse for the selected operation voltage in the IEC socket:230V-T500mA and 115V-T1Amp6: Re-connect to mains power source.Never disconnect the earth from the mains supplyAUDIO CONNECTIONSThe inputs and outputs are electronically balanced on conventionally wired XLRs (pin 1 screen, pin 2 hot, pin 3cold and XLR shell is connected to chassis). The operating level is nominally +4dBu. Balanced use is recommended.• Interference:If the S3 is to be used where it maybe exposed to high levels of disturbance such as found close to a TV or radio transmitter, we advise that it is operated in a balanced configuration. The screens of the signal cables should be connected to the chassis connection on the XLR connector as opposed to connecting to pin1. The S3 conforms to the EMC standards.• Ground Loops:If ground loop problems are encountered, never disconnect the mains earth, but instead, try disconnecting the signal screen on one end of each of the cables connecting the outputs of the S3 to the patchbay. If such measures are necessary, balanced operation is recommended.POWER CONNECTIONfig.4 Altering the Voltagefig.3 XLR WIRING6DRAWMER S3 O PERATOR’S M ANUALBAND SPLITThe 6dB per octave crossover frequencies determine the points within the frequency spectrum one band stops to process audio, and another band takes over.Low Split Frequency:60Hz - 1.4kHzSets the frequency point at which the split between low and mid bands occurs.High Split Frequency:1.4kHz - 14kHzSets the frequency point at which the split between mid and high bands occurs.The following diagram provides a good, but general, idea of some useful frequencies:CHAPTER 2127DRAWMER S3 O PERATOR’S M ANUALUse to brighten and enhance the high band detail. Cymbals sound more vibrant without becoming splashy, vocals all bandsControls the speed that the compressor responds to signals that exceed the level set by threshold. Six switchable Attack settings. All times are nominal, the actual attack time is further modified by the release setting chosen.all bandsGain:-10 - +20dBall bandsDuring compression the signal is attenuated, gain may be required to produce the required output level. In addition,as the S3 is multi-band, the three gain controls are used to adjust the levels of each band to obtain a desirable overall signal, or to bring out the bass, treble etc.all bandsRelease PresetsAttack PresetsMETERSVU Meter:Two moving coil VU meters monitor either the level of the input or output signal.Pad:Vu - +10dB - +20dBA three-position switch adjusts the meters to show either normal output level, (and for those working at ‘hot’ outputlevels) VU +10dB or VU +20dB modes. i.e. with the switch at VU +10dB - when the VU meter reads 0dB the actual level is +10dB.Response:Peak VU - VUOn smooth, gentle pieces of music the “VU” (average level) setting would be sufficient, however, on fast dynamic signals the “Peak VU” setting provides more accurate readings.Select:Output - InputSet to "Input" and adjust the level of the incoming signal: an optimal level of 0dB provides optimum headroom and signal-to-noise ratio. If the input level is too low little compression will occur (and, raising the overall output level of 8DRAWMER S3 O PERATOR’S M ANUAL9DRAWMER S3 O PERATOR’S M ANUALQUICK SETUP PROCEDUREPlease note that the following procedure is only a guide. All audio is different, requiring numerous settings, however,this should give a good staring point:1)Set the compressor settings to be the same on all bands - Threshold at “infinite”, Gain at 0dB, theAttack in a mid position (2 or 3) and Release set to F(ast). The overall Gain control should be set to 0dB,and the Balance at 0.2)Set the Meter Select switch to Input and adjust the incoming signal so that the meters read 0dB. Set the switch to output .3)With the Low Frequency Split set fully counter-clockwise, and the High Frequency Split set fullyclockwise, listen to the audio and bring in the two knobs to the positions that you think the cross-over points should be set - generally to separate the main bass and treble sounds from the mid-range. Using a combination of Mute and Bypass switches for the various bands allows the operator to monitor only the frequencies that are required and so tune the low, mid and high frequencies.4)Keeping an eye on the Gain Reduction Meters alter the Threshold level control for each band until the desired compression level is achieved - a G.R. level up to -10dB is acceptable.5)Adjust the Gain control of each band until 0dB is reached on the Output VU meter . To see only the band that is being adjusted on the VU meter Mute the other two bands.6)Set the Attack and Release settings of each band to suit the audio being compressed.7)The Threshold and Gain of each band can be modified to achieve the desired compression, levels and tonal balance to the overall signal.8)At this point the Bypass switches can be toggled to listen to the affect that the S3 is having on the audio.Adjust to suit.9)Once each band is setup correctly modify the overall Output Gain and Balance until the VU meters read 0dB (more if in +10dB VU or +20dB modes).Above is an example setup that could be used for a General Pop Mix, though, of course, as all music is diverse andvaried, will not be ideal elsewhere.10DRAWMER S3 O PERATOR’S M ANUALCHAPTER 3IF A FAULT DEVELOPSFor warranty service please call Drawmer Electronics Ltd. or their nearest authorised service facility, giving full details of the difficulty.A list of all main dealers can be found on the Drawmer webpages.On receipt of this information, service or shipping instructions will be forwarded to you.No equipment should be returned under the warranty without prior consent from Drawmer or their authorised representative.For service claims under the warranty agreement a service Returns Authorisation (RA) number will be issued.Write this RA number in large letters in a prominent position on the shipping box. Enclose your name, address, telephone number, copy of the original sales invoice and a detailed description of the problem.Authorised returns should be prepaid and must be insured.All Drawmer products are packaged in specially designed containers for protection. If the unit is to be returned, the original container must be used. If this container is not available, then the equipment should be packaged in substantial shock-proof material, capable of withstanding the handling for the transit.CONTACTING DRAWMERDrawmer Electronics Ltd., will be pleased to answer all application questions to enhance your usage of this equipment. Please address correspondence to:Drawmer (Technical Help line)Coleman Street Parkgate Rotherham S62 6EL UKAlternatively contact us by E-mail on :forsalesenquiries:*****************orfortechnicalissues:****************Further information on all Drawmer dealers, Authorised service departments and other contact information can be obtained from our web pages on:GENERAL INFORMATIONINPUTInput Impedance 600 Ohms or greater Maximum Input Level+30dBuOUTPUTOutput Impedance 600 OhmsMaximum Output Level+30dBu @ 10k Ohms Load +26dBu @ 600 Ohms LoadFREQUENCY RESPONSE<24Hz to 38kHz -1dB <10Hz to 60kHz -3dBCROSSTALK< -80dB @ 10kHz < -74dB @ 20kHzNOISE AT UNITY GAINwith flat EQ response switched in circuitWideband 22Hz - 22kHz A V-79dB -84dB -87dB-94dBS3 THREE-BAND STEREO VACUUM TUBE COMPRESSORDATA SPECIFICATION% DISTORTION (THD & NOISE) @ 1kHz0dB (ref +4)0.03%10dB (ref +4)0.1%20dB (ref +4)0.4%POWER REQUIREMENTS230Volt or 115V at 50-60hZ, 60VAFUSE RATINGT500mA for 230Volt, T1A for 115Volt Conforming to IEC 127-2FUSE TYPE20mm x 5mm, Class 3 Timed-Blo, 250Volt workingCASE SIZE482mm (W) x 132mm (H) x 315mm (D)WEIGHT9.7Kgs11DRAWMER S3 O PERATOR’S M ANUAL BLOCK DIAGRAMS3 ver 01 C 30/03/09。
OLP设备原理及应用培训
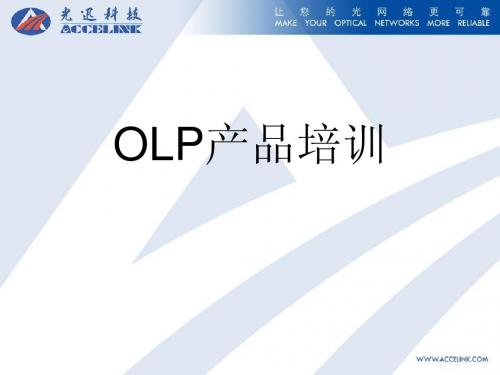
应急处理步骤
若业务运行在主用路由上,则
①.把两站点OLP单盘的TX和T1端口的尾纤拔下,用SCSC的适配器将2根尾纤对接。
应急处理步骤
②.再把两站点OLP单盘的RX和R1端口的尾纤拔 下,用SC-SC的适配器将2根尾纤对接。
分类故障处理 OLP设备故障
故障现象:本地\远程指示灯,单盘选择指示灯,单盘型号指示灯不亮
处理步骤:
可能属硬件故障。
分类故障处理 OLP设备故障
故障现象:工作模式/线路指示灯不亮或一个以上工作模式指示灯亮 /两个以上工作线路指示灯亮
处理步骤:
用笔或其他工具按复位键(RESET),看是否恢复正常 ; 改变工作模式,看是否恢复正常 ;
3.工作方式(1:1A)
主路由
光终端 设备
Tx Rx
R1 R2
Rx
Tx
光终端 设备
备用路由
PATENT 动态光线路同步切换保护 装置03254764.1
工作模式:
自动不返回模式 自动返回模式 手动 强制
特点 选发选收 切换速度快:<50ms 备纤监控 插入损耗小(<2.5dB) 可自动返回至主线路
DCM1&DCM2:色散补偿模块接口, 用于连接DCM的两个端口。
注意,在连接好输入端口和输出端口后,DCM1和 DCM2端口也必须连好,如果不接DCM的话则必须 用短跳线将这两个端口短接,否则EDFA没有光输出。
2.机盘介绍
Mon
O D F
Input Output DCM1 DCM2
O L P
DCM
• 在进行线路割接或线路维修后,一定要对 纤,确保每根纤芯用于正确的系统以及正 确的收/发方向,以免以后自动切换后产生 错环、收发交叉等不必要的问题
EOC_EMS_JIANGSU_V3网管使用手册
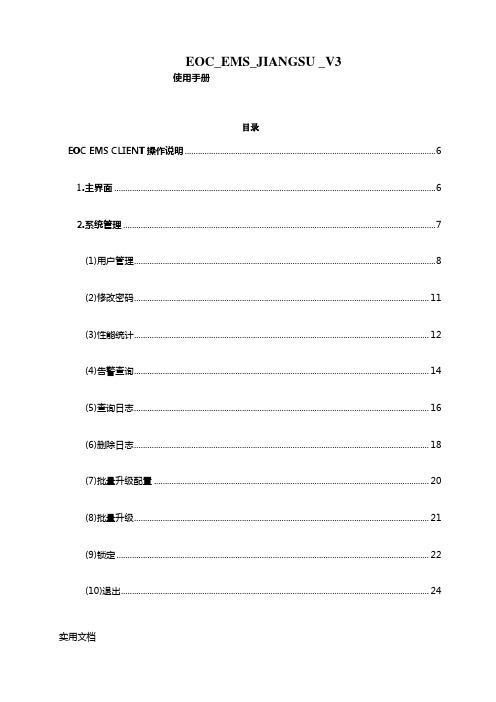
EOC_EMS_JIANGSU _V3使用手册目录EOC EMS CLIENT操作说明 (6)1.主界面 (6)2.系统管理 (7)(1)用户管理 (8)(2)修改密码 (11)(3)性能统计 (12)(4)告警查询 (14)(5)查询日志 (16)(6)删除日志 (18)(7)批量升级配置 (20)(8)批量升级 (21)(9)锁定 (22)(10)退出 (24)实用文档3.拓扑管理 (24)(1)禁止拖动 (25)(2)实时告警 (25)(3)查找设备 (26)(4)导出拓扑 (28)(5)导入拓扑 (31)(6)备份数据库 (32)4.窗口管理 (33)(1)层叠 (33)(2)平铺 (34)(3)窗口列表 (34)5.ROOT或子网节点右键菜单 (35)(1)增加子网 (35)(2)修改子网 (36)(3)增加设备 (38)(4)删除 (39)实用文档6.CBAT主控板右键业务操作 (41)(1)详细信息 (42)(2)修改设备基本信息 (43)(3)删除设备 (45)(4)cbat网络设置 (46)(5)复位操作 (48)(6)备份配置数据 (49)(7)在线CNU最大数设置 (50)(8)白名单信息登记 (51)(9)在线CLT信息 (56)(10)软件升级 (57)(11)全局配置 (60)(12)局端性能检测 (63)(13)设置性能统计任务 (64)(14)刷新 (66)实用文档(16)CNU端口配置模板管理 (71)(17)绑定CNU端口模板 (76)(18)CBAT自动配置开关 (77)(19)广播风暴设置 (79)7.CLT头端右键业务操作 (80)(1)详细信息 (81)(2)修改设备基本信息 (82)(3)在线CNU信息 (84)(4)VLAN配置 (85)(5)射频信道信息设置 (86)(6)IGMP Snooping (88)U终端右键业务操作 (89)(1)详细信息 (90)(2)修改设备基本信息 (91)(3)性能统计 (93)实用文档(5)调谐映射设置 (97)(6)MAC地址限制 (98)(7)CNU重启 (99)(8)删除CNU (100)(9)链路测试(暂不提供此功能) (101)9.帮助 (101)(1)图例 (102)(2)关于 (102)10.系统配置 (103)(1) AccessParam.xml (103)(2) AlarmParam.xml (103)(3) ConfigParam.xml (104)(4) CompCmdConf.xml (105)(5) Component.conf (105)(6) Ldcp.conf (105)实用文档(8) Process.conf (107)(9) Version.conf (108)EOC EMS CLIENT操作说明1.主界面登录EOC Client后,进入主界面。
EPON爱普生V33扫描仪使用说明(随意调整页面宽高)
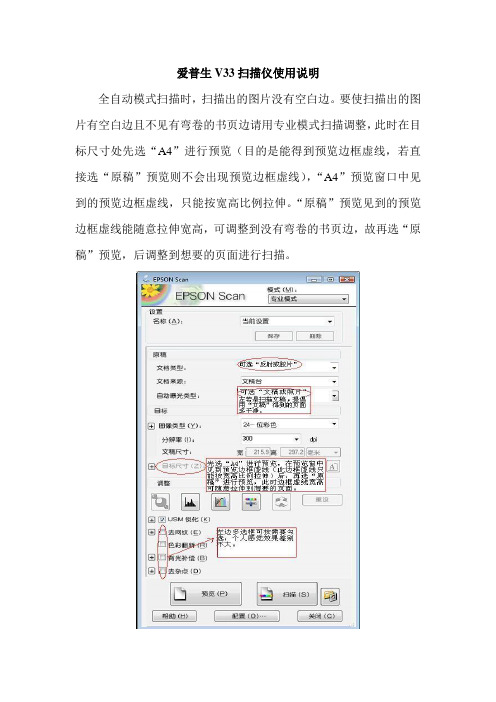
全自动模式扫描时,扫描出的图片没有空白边。
要使扫描出的图片有空白边且不见有弯卷的书页边请用专业模式扫描调整,此时在目标尺寸处先选“A4”进行预览(目的是能得到预览边框虚线,若直接选“原稿”预览则不会出现预览边框虚线),“A4”预览窗口中见到的预览边框虚线,只能按宽高比例拉伸。
“原稿”预览见到的预览边框虚线能随意拉伸宽高,可调整到没有弯卷的书页边,故再选“原稿”预览,后调整到想要的页面进行扫描。
一、扫描仪部件指南A、扫描仪部件a. 扫描仪文稿盖a. 文稿垫(仅Perfection V330 Photo)b. 文稿台c. 扫描头(在文稿台里边)a. USB接口b. 直流电入口B、指示灯和按钮此扫描仪有四个按钮用于扫描操作。
状态指示灯指示扫描仪操作是否正常a. 电子邮件按钮d. PDF按钮c. 复印按钮d. 电源/启动按钮e. 状态指示灯状态指示灯位于电源/启动按钮和PDF按钮之间。
颜色指示灯状态含义绿色亮准备扫描图像。
闪烁正在初始化或正在扫描。
橙色闪烁发生错误。
有关详细信息,参见状态指示灯闪烁。
(无)灭扫描仪关闭。
按钮功能电源/启动按钮电源如果按下一次可打开扫描仪电源。
当扫描仪电源打开时,按下此按钮3秒钟可关闭扫描仪。
(当扫描软件正在运行时,您不能关闭扫描仪。
)启动Epson Scan启动。
复印Copy Utility启动。
E-mail Epson Scan自动扫描,然后出现传送文件的邮件窗口。
PDF 扫描至PDF窗口出现。
二、扫描仪部件指南A、将文稿和照片放在文稿台上1、打开扫描仪盖2、将原始文稿或照片面朝下放置在扫描仪文稿台上。
确保将文稿或照片放置在文稿台的右下角且与箭头标记对齐。
3、轻轻地合上文稿盖,以免移动原始文稿。
注意:扫描多张照片,请将每张照片与其相邻照片之间至少距离20 毫米(0.8 英寸)放置保持文稿台干净请勿将照片在文稿台上放置过长时间,因为它们可能会粘在玻璃上B、放置大或厚的文稿扫描大的或厚的文稿时,可完全的打开扫描仪的文稿盖,使其平放在扫描仪的旁边1、打开扫描仪盖2、向上笔直地拉出文稿盖3、向下放置文稿盖使其平放在扫描仪的旁边。
- 1、下载文档前请自行甄别文档内容的完整性,平台不提供额外的编辑、内容补充、找答案等附加服务。
- 2、"仅部分预览"的文档,不可在线预览部分如存在完整性等问题,可反馈申请退款(可完整预览的文档不适用该条件!)。
- 3、如文档侵犯您的权益,请联系客服反馈,我们会尽快为您处理(人工客服工作时间:9:00-18:30)。
保持2 保持2秒
同时按住 保持2 保持2秒
所有测试 结果清空 退出调 用模式
OLP-3x操作指南 OLP-3x操作指南
外观
1. 防尘盖 2. 测试接口(通用2.5mm) 测试接口(通用 ) 3. 标签 4. 显示屏 5. 外部电源接口(需USB选项) 选项) 外部电源接口( 选项 6. 电池仓(背后) 电池仓(背后) 7. 操作键盘
存储测 试结果
按[STORE]键,存储测试结果。 键 存储测试结果。 按[STORE]键,并保持 秒,调用以 键 并保持2秒 前测试结果。 前测试结果。
保持2 保持2秒
调用测 试结果
确定存储位置
退出调 用模式
典型操作典型操作-删除所有存储结果
1. 长按 长按[STORE]键,并保持2秒,进入结果调用模式(RECALL) 键 并保持 秒 进入结果调用模式( ) 2. 同时按 入]键和 同时按[入 键和 键和[AUTO-入]键,并保持 秒,所有结果被清空。 入 键 并保持2秒 所有结果被清空。
显示Biblioteka 开机模式 PERM: PERM:长开机 ECON: ECON:自动关机 电池电量
存储位置 0到100
测量值
单位
波长 自动波长 检测显示 调制信号 检测显示
典型操作典型操作-变更波长
按[入]键,可变更测试波长 入 键 变更的测试波长在5个预制波长 变更的测试波长在 个预制波长 之间轮流切换。 之间轮流切换。
3. 通过[上/下]键,调整波长数值,直 通过 上 下 键 调整波长数值, 到所需波长。 到所需波长。 4. 按[入]键,存储波长。 入 键 存储波长。
完成波长存储
典型操作-存储/ 典型操作-存储/调用结果
OLP-3x系列可以存储 系列可以存储100个结果 系列可以存储 个结果
键盘定义
短按 开关 长按 短按 波长 长按 短按 自动波长 长按 短按 存储 长按 短按 单位切换 长按 清除当前存储 存储当前测量结果 调用存储结果 单位切换,dBm和W为绝对功率 单位切换, 和 为绝对功率 dB为相对功率 为相对功率 设定参考电平 更改校准波长,上下键调整波长 更改校准波长, 启动自动波长功能 ECON:开/关(无操作 分钟自动 : 关 无操作20分钟自动 关机) 关机) PERM:开/关(开机保持) : 关 开机保持) 波长切换( 个预制好的波长 个预制好的波长) 波长切换(5个预制好的波长)
波长显示
典型操作典型操作-编辑波长
1. 按[入]键,选择要编辑的测试波长 入 键 建议使用不常用的波长编辑, (建议使用不常用的波长编辑,如 850nm)。 )。 2. 按[入]键,保持 秒以上。进入波长 秒以上。 入 键 保持2秒以上 编辑状态。 编辑状态。
保持2 保持2秒