沟槽凸轮的机加工工艺分析
凸轮零件的机械加工工艺规程及夹具设计精品

凸轮零件的机械加工工艺规程及夹具设计.零件的分析凸轮共有两组加工表面,它们之间有一定的位置关系,现分析如下:1.以①28mm孔加工中心的表面这一组加工的表面包括①28mm孔及其倒角,尺寸为30mm的键槽,两个①6mm的工艺孔和宽度为16± 0.1mm凸轮槽,其中①28mm孔和键槽为主要加工表面。
2.以大端面为加工对象的表面,这组加工表面包括孔①28mm的大小两个端面。
这两组加工表面之间有着一定的位置精度要求,主要是①28mm孔大端面相对于①28mm 孔垂直度公差为0.05mm由以上分析可知,对这两组加工表面,要先加工其中一组表面,然后借助于专用夹具加工另一组表面,并且保证它们之间的相对位置精度要求。
二.工艺规程设计(一).确定毛坯的制造形式零件材料为45钢,考虑到凸轮在使用时反复冲击小,因此选用铸件,就能满足工作需要,由于零件的年产量为大批大量生产,形状较简单,尺寸不大,可采用沙箱铸造。
(二).基面的选择1.粗基准的选择:由于零件大端是以孔心为基准的,则应在保证①28mm孔心精度的基础上加工大端面,所以以大端面为粗基准是合理的。
2 .考虑到大端面相对①28mm孔的位置关系,取①28mm孔为精基准。
(三).制订工艺路线工艺路线工序1粗铳上端面,精铳上端面保证Ra3.2。
粗铳下端面,精铳下端面,保证Ra3.2。
以孔外圆为基准,选用数控式升降台铳床KX5012工序2扩孔至①27.7mm绞孔,保证尺寸①28 00.021mm以大端面为粗基准,选用数控式升降台铳床KX5012。
工序3加工键槽,保证尺寸60°.022mm 300°.013mm和粗糙度Ra6.3。
以①28 00.021mm孔外圆为基准,选用拉床。
工序4 钻通孔^<6mm 保证尺寸55 ± 0.1mm, R47± 0.1mm, 10°± 1°。
以① 28 語021mm 孔外圆为基准,选用ZF5132。
大型双向沟槽圆柱凸轮专机设计与研究
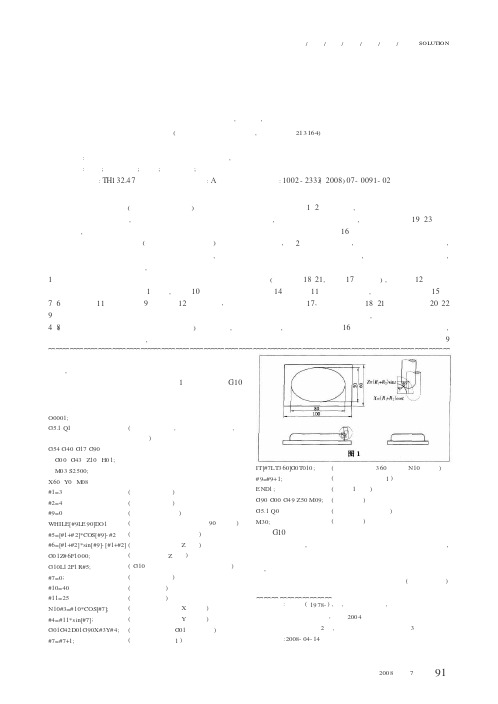
4、8( 与圆 柱 凸轮 沟 槽接 触 一 头是 尼 龙滑 块) 定轴 转 动, 构 经丝 内 , 织 造 成由 尺码 环 16 确 定规 格大 小 的筒 布。可 见 ,
成 圆 柱凸 轮 摆杆 从 动 件机 构 , 摆 杆 通 过铰 链 带动 内 、外两 梭 穴的 形 状 、亦 梭子 的 结 构 形状 、数 量 主要 由 圆 柱 凸轮 9 ! !! !! !! !! !! !! !!! !! !! !! !!! !! !! !! !!! !! !! !! !!! !! !! !!! !! !! !! !
关键 词: 摆杆; 圆柱凸轮; 梭穴; 五轴联动; 靠模凸轮
中图 分类 号: TH1 32.4 7
文献 标识 码: A
文章 编号 : 1002 - 2333( 2008) 07- 0091- 02
摆 杆式 塑 料 圆 织 机( 以 下 简 称圆 织 机) 是 以 聚 丙 烯 、 圈几 十 根 棕杆 1、2 上 下滑 动 , 每 根 棕杆 上 固 定有 几 十 根
便、快 捷、灵 活多 了。
( 编辑 启 迪)
!!! !!!!!!! 作者简介: 曾福辉( 19 78- ) , 男, 实习指导教师 , 多年从事 数控实训教
学、培训等工作, 曾获 200 4 年第一届全国数控大赛数控车
工职 工组 第 2 名, 多次获广东省数控大赛前 3 名。
收稿日期: 2008- 04- 14
于 其 大型 双 向沟 槽 圆 柱凸 轮( 以 下 简 称圆 柱 凸轮) 等 关键 间 梭 穴 , 图 2 为 梭 穴 展 开 图 , 图 中交 点 为 摆 杆 水 平 位 置 ,
件 的 运 动 规 律 、结 构 形状 的 设 计 、制 造 比 较 复 杂, 曾 一 度 每条 曲 线 圆周 方 向有 四 个周 期 , 两条 曲 线合 成 八 个梭 穴 ,
沟槽凸轮的设计与加工

6.1 沟槽凸轮的零件图
图6-1
沟槽凸轮的设计与加工
6.2 项目1 沟槽凸轮的绘制
6.2.1 引导问题 要求在阅读相关知识后,回答下述问题。 1. 绘制沟槽凸轮模型与工程图有什么异同? 2. 沟槽凸轮模型加工中,高度8mm,15mm怎样处理? 3. 绘制圆弧有哪几种方法? 4. 圆弧的绘制的不够长或有多余,怎样办? 5. 怎样标注圆弧半径、直径的尺寸? 6. 怎样标注文字? 7. 怎样标注尺寸公差? 8. 请描述沟槽凸轮模型的绘图思路。
沟槽凸轮的设计与加工
4. 加工步骤
凸轮加工工艺步骤如图6-30所示。
图6-30 凸轮加工工艺流程
沟槽凸轮的设计与加工
6.3.3制定加工工艺计划
表6-2 凸轮加工工艺卡片
沟槽凸轮的设计与加工
6.3.4 加工凸轮外形刀具路径的实施
1.外形铣削对话框 2. 选择刀具参数 3. 选择2D外形铣削参数 4. 产生刀具路径 5. 刀具路径模拟 6. 实体切削验证
沟槽凸轮的设计与加工
6.2.6检查
沟槽凸轮的设计与加工
6.3 项目2沟槽凸轮的加工工艺制定
任务要求:沟槽凸轮加工工艺方案的讨论与讲述。 6.3.1 引导问题 要求在阅读相关知识后,回答下述问题。 1.采用的是什么材料?铸造毛坯有什么优点?
2. 25mm及 12mm的孔采用什么机床来加工?
沟槽凸轮的设计与加工
绘制圆弧
6. 绘制切弧 绘制R97mm的圆弧, 7. 圆弧的修剪 8. 三点画弧 绘制R40的圆弧 9. 两点画圆弧 绘制R25的圆弧
沟槽凸轮的设计与加工
绘制凸轮
10. 串联补正
沟槽凸轮的设计与加工
6.2.5 尺寸标注的实施
平面槽形凸轮的工艺浅析
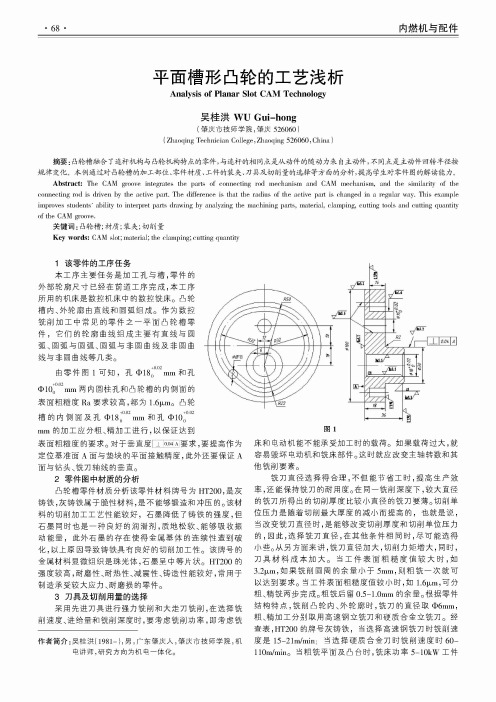
• 68•内燃机与配件平面槽形凸轮的工艺浅析Analysis of Planar Slot CAM Technology吴桂洪W U G u i-h o n g(肇庆市技师学院,肇庆526060)(Zhaoqing Technician College,Zhaoqing526060, C hina)摘要:凸轮槽融合了连杆机构与凸轮机构特点的零件,与连杆的相同点是从动件的随动力来自主动件,不同点是主动件回转半径按 规律变化。
本例通过对凸轮槽的加工部位、零件材质、工件的装夹、刀具及切削量的选择等方面的分析,提高学生对零件图的解读能力。
Abstract:T he C A M groove in tegrates th e p a rts of connecting rod m echanism and C A M m echanism,and th e sim ilarity of th e connecting rod is driven by th e active part.The difference is th a t th e radiu s of th e active p a rt is changed in a regular w ay.T his exam ple im proves students'ability to in terpret p a rts draw in g by analyzing th e m achining parts,m aterial,clam ping,cutting tools and cutting qu an tity of th e C A M groove.关键词:凸轮槽;材质;装夹;切削量Key words:C A M slot;m aterial;th e clam ping;cutting qu an tityi该零件的工序任务本工序主要任务是加工孔与槽,零件的外部轮廓尺寸已经在前道工序完成,本工序所用的机床是数控机床中的数控铣床。
槽凸轮的加工工艺规划及数控加工
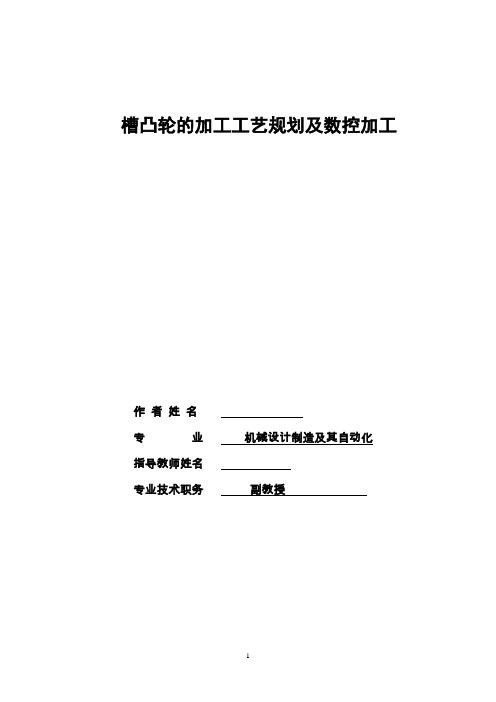
槽凸轮的加工工艺规划及数控加工作者姓名专业机械设计制造及其自动化指导教师姓名专业技术职务副教授目录摘要 (4)第一章绪论 (4)1.1 课题内容 (4)1.2 选题意义 (5)1.3 与课题内容相关的现状及发展趋势 (5)第二章零件的工艺分析 (5)2.1 零件的图样分析 (5)2.1.1 零件的结构特点 (5)2.1.2 零件的技术条件分析 (5)2.2 零件的工艺分析 (6)第三章毛坯的粗加工 (7)3.1 毛坯的选择 (7)3.1.1 毛坯的种类 (7)3.1.2 毛坯选择应考虑的因素 (7)3.2 加工余量的确定 (7)3.2.1 加工余量的概念 (7)3.2.2 影响加工余量的因素 (7)3.2.3确定加工余量的方法 (8)3.3 毛坯的加工方案 (8)3.3.1 确定毛坯的加工方案 (8)3.3.2 确定各工序所用的设备 (9)3.3.3 表面加工方法的选择 (9)3.3.4 各工序的切削用量 (10)第四章零件的数控加工 (10)4.1数控机床 (10)4.1.1数控机床简介 (11)4.1.2数控加工 (11)4.1.3数控加工的过程 (12)4.2零件的数控加工工艺 (12)4.2.1确定工艺路线 (11)4.2.2确定各工序所用设备 (11)4.2.3工件的装夹 (11)4.2.4定位基准的选择 (11)4.2.5方案的具体实施 (12)4.3零件的数控编成 (14)4.3.1加工编成概述 (15)4.3.2加工编成的分类 (15)4.3.3程序 (16)第五章小结及参考文献 (19)摘要本文首先进行了墙板右内凸轮椭圆校订包本机的工艺分析,规划出零件的工艺加工路线:毛坯的粗加工(零件材料的选择,加工余量的确定等);零件的数控加工包括工件的工艺方案(外围轮廓的加工,方孔的加工,中心孔的加工,凸轮槽的加工等)和数控编程。
这就必须介绍数控机床和数控加工过程,然后根据已确定的零件的工艺路线,进行数控编成——用G代码把零件的各工序用数控语言编写出来。
槽形凸轮加工工艺及夹具设计
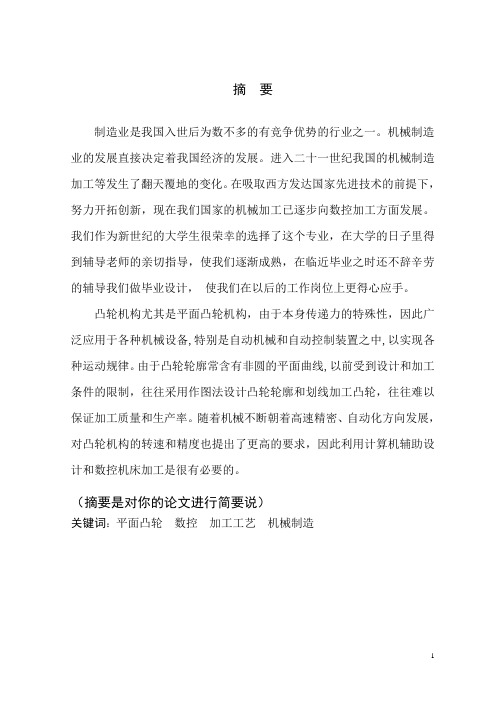
摘要制造业是我国入世后为数不多的有竞争优势的行业之一。
机械制造业的发展直接决定着我国经济的发展。
进入二十一世纪我国的机械制造加工等发生了翻天覆地的变化。
在吸取西方发达国家先进技术的前提下,努力开拓创新,现在我们国家的机械加工已逐步向数控加工方面发展。
我们作为新世纪的大学生很荣幸的选择了这个专业,在大学的日子里得到辅导老师的亲切指导,使我们逐渐成熟,在临近毕业之时还不辞辛劳的辅导我们做毕业设计,使我们在以后的工作岗位上更得心应手。
凸轮机构尤其是平面凸轮机构,由于本身传递力的特殊性,因此广泛应用于各种机械设备,特别是自动机械和自动控制装置之中,以实现各种运动规律。
由于凸轮轮廓常含有非圆的平面曲线,以前受到设计和加工条件的限制,往往采用作图法设计凸轮轮廓和划线加工凸轮,往往难以保证加工质量和生产率。
随着机械不断朝着高速精密、自动化方向发展,对凸轮机构的转速和精度也提出了更高的要求,因此利用计算机辅助设计和数控机床加工是很有必要的。
(摘要是对你的论文进行简要说)关键词:平面凸轮数控加工工艺机械制造第一章凸轮零件的加工工艺分析及设计1.1凸轮加工工艺分析1.1.1零件图及其结构工艺性分析图1-1所示为槽形凸轮零件图,该零件是一个外部轮廓经过加工的圆盘,圆盘直 ,这次的任务是在铣床上加工槽与孔及使外部轮廓达到尺寸要求,零件径为280mm的材料为HT200,切削加工性能较好,其数控铣床加工工艺分析如下。
图1-1 平面槽形凸轮(零件图怎么会有这么多辅助线?这是编程用确定基点的图另外画零件图,零件图尺寸看不清)①分析零件的形状、结构及尺寸的特点,确定零件上是否有妨碍刀具运动的部位,是否有会产生加工干涉或加工不到的区域,零件的最大形状尺寸是否超过机床的最大行程,零件的刚性随着加工的进行是否有太大的变化等。
根据图1-1所示该零件凸轮轮廓由HA、BC、DE、FG和直线AB、HG以及过渡圆弧CD、EF所组成。
组成轮廓的各几何元素关系清楚,条件充分,所需要基点坐标容易求得。
凸轮轴机械加工工艺和标准
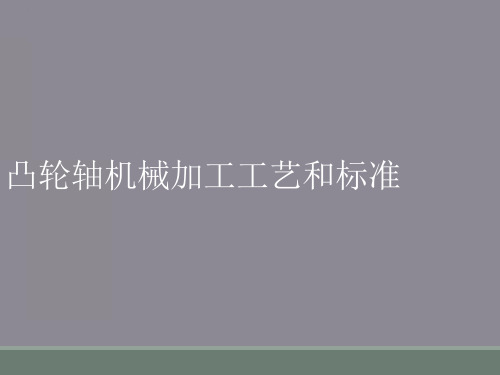
二、加工阶段的划分与工序顺序的安 排
(二)工序顺序的安排 各支承轴颈、凸轮、偏心轮: 车——粗磨——精磨——抛光 从粗到精,主要表面与次要表面的加工工序交叉进
行。 淬火工序安排在各主要表面的半精加工之前 防止工件经淬火后变形过大造成精加工困难
三、主要表面的加工
(一)凸轮形面的加工
1. 凸轮形面的粗加工 凸轮传统的粗加工方法是采用靠模车床及液压
工序3: 车1、2支承轴颈外圆等 凸轮轴轴颈车床
工序4: 车3、4支承轴颈外圆等 凸轮轴轴颈车床
工序5:钻φ7孔 钻床
工序6:校直 压床
工序7:磨第2、3轴颈外圆 外圆磨床
工序8:车凸轮侧面和连接轴颈等 凸轮轴车床
工序8:车凸轮侧面和连接轴颈等 凸轮轴车床
工序9:校直 压床
工序10:磨正时齿轮轴颈和螺纹轴颈外圆等 外圆端面磨床
第四节 凸轮轴的检验
中间检验 1)由加工阶段和中间检验的性质 、目的、作用所决定,每项检验内容的 中检数量所占百分比不同。 2) 对于单项检验,多使用专用定值量具(如量规),以保证检验的效率 和精度。 3)对于综合检验,(如齿轮的检验), 多使用检验夹具,以保证迅速准确 的反映多参数的测量结果。
最终检验
以CA 6102 发动机为例, 凸轮的升程偏差 为: A、 D 段为±0 . 015mm; B段为±0 . 05mm; C 段为±0 . 025mm。
二、凸轮轴的材料与毛坯
材料: 铸铁:冷硬铸铁、可淬硬的低合金铸铁、球墨铸铁等。 钢: 中碳钢、渗碳钢。
毛坯制造方法: 精铸和精锻。 直接用棒料加工。
a) 车刀
b)工具的安装
2.凸轮形面的精加工
凸轮轴切点跟踪磨削加工
凸轮形面磨削的新技术
凸轮加工工艺流程
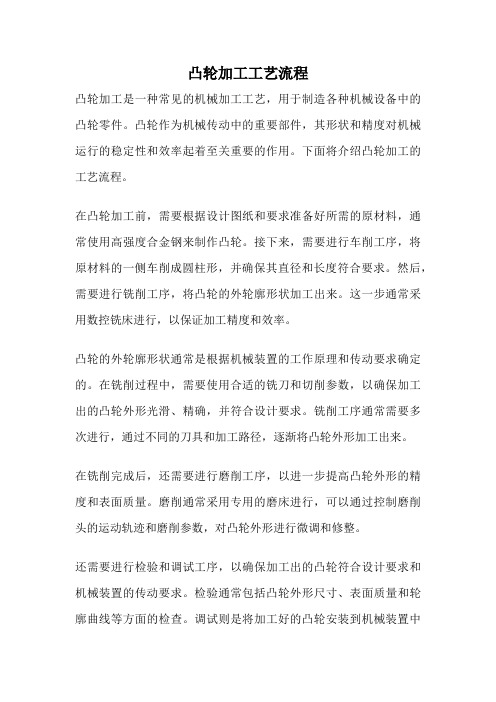
凸轮加工工艺流程凸轮加工是一种常见的机械加工工艺,用于制造各种机械设备中的凸轮零件。
凸轮作为机械传动中的重要部件,其形状和精度对机械运行的稳定性和效率起着至关重要的作用。
下面将介绍凸轮加工的工艺流程。
在凸轮加工前,需要根据设计图纸和要求准备好所需的原材料,通常使用高强度合金钢来制作凸轮。
接下来,需要进行车削工序,将原材料的一侧车削成圆柱形,并确保其直径和长度符合要求。
然后,需要进行铣削工序,将凸轮的外轮廓形状加工出来。
这一步通常采用数控铣床进行,以保证加工精度和效率。
凸轮的外轮廓形状通常是根据机械装置的工作原理和传动要求确定的。
在铣削过程中,需要使用合适的铣刀和切削参数,以确保加工出的凸轮外形光滑、精确,并符合设计要求。
铣削工序通常需要多次进行,通过不同的刀具和加工路径,逐渐将凸轮外形加工出来。
在铣削完成后,还需要进行磨削工序,以进一步提高凸轮外形的精度和表面质量。
磨削通常采用专用的磨床进行,可以通过控制磨削头的运动轨迹和磨削参数,对凸轮外形进行微调和修整。
还需要进行检验和调试工序,以确保加工出的凸轮符合设计要求和机械装置的传动要求。
检验通常包括凸轮外形尺寸、表面质量和轮廓曲线等方面的检查。
调试则是将加工好的凸轮安装到机械装置中进行试运行,检查其传动效果和稳定性,并根据实际情况进行调整和修正。
凸轮加工是一项复杂而精密的工艺,需要经过多个工序的加工和调试。
通过合理的工艺流程和精确的操作,可以加工出符合设计要求的凸轮零件,为机械装置的正常运行提供保障。
凸轮加工的工艺流程可以根据具体的需求和装备的不同,进行适当的调整和优化,以提高加工效率和质量。
槽凸轮的数控加工

槽凸轮的数控加工槽凸轮的数控加工引导语:下面是店铺为大家整理出来的一些关于槽凸轮的数控加工的资料,希望可以帮助到大家哦!下面以我厂生产的XKH714数控立式加工中求,将曲线部分细化得更密。
此凸轮由于曲线精度心机械手自动换刀部位的槽凸轮为例,介绍数控加要求在±。
以内,所以在编程时数控铣削半工工艺过程,其工艺流程为:凸轮曲线部分的粗加精加工按照凸轮每转动。
5°计算出一组坐标值的方工一数控铣削半精加工一曲线表面热处理一数控磨法编程,数控磨削精加工按凸轮每转动。
25°计算削精加工。
A、/按正弦加速度曲线(外凸轮曲线)变化。
0.02mm加工,凸轮曲线必须光滑。
按照要求及凸轮传动机构参数(凸轮回转中心到摆杆中心的距离、摆杆长度、升程、滚子半径、基圆半径等等),用解析法建立凸轮轮廊线方出一组坐标值的方法编程。
因为整个凸轮曲线是由各个点的坐标连接而成的,所以在编程时凸轮转动的角度与角度之间越小,则点集越密,数控编程精度越篼,从而才能保证加工曲线精度达到设计要求。
这一计算过程都由计算机自动来完成。
由于这种凸轮结构复杂,内外曲线具有一定的角度要求,为保证技术要求,对其定位安卡、工件坐标系设定、进刀、走刀路线及退刀点是这样安排的。
数控铣、数控磨共采用同一定位基准及同一工件坐标系,这样在编程时铣、磨同在一个起刀点完成。
走刀路线,外凸轮首先将刀具移动到K点,在iC'点完成刀偏并落刀,直线运动到a点,然后工件加工a―b一c―d―e一a一K"点,在K"点退刀。
槽凸轮采用理论曲线编程,对槽凸轮走刀路线是在A点落刀,然后由A―B一C一D―E―A抬刀。
槽的宽度由G41刀具左偏及G42刀具右偏控制。
在铣削结束后要对曲线留有一定的磨量,一般留0.4~0.6mm,槽凸轮留0.1~0.15mm,然后进行热处理,凸轮表面淬火,最后进人凸轮磨削加工。
槽凸轮的磨削,数控磨削与数控铣削定位基准、走刀路线采用同一基准的方法进行加工。
凸轮槽板类零件数控铣削工艺分析及数控加工编程
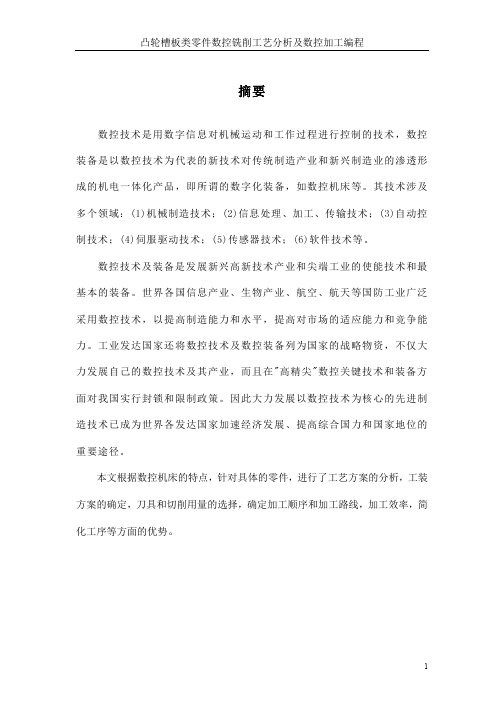
凸轮槽板类零件数控铣削工艺分析及数控加工编程 6-4 凸轮槽板加工程序的编制......................................21 第七章 UGNX8.0 软件介绍.............................................22 7-1 UGNX8.0 界面................................................22 7-2 UG 建模模块介绍.............................................23 7-3UGNX/CAM 模块介绍............................................24 第八章凸轮槽板 UG 编程及刀具轨迹路线图模拟..........................26 8-1 刀具创建....................................................26 8-2 坐标系以及几何体的创建......................................26 8-3 创建操作....................................................27 第九章工艺设计总结................................................. 31 参考文献........................................................... 32
数控技术及装备是发展新兴高新技术产业和尖端工业的使能技术和最 基本的装备。世界各国信息产业、生物产业、航空、航天等国防工业广泛 采用数控技术,以提高制造能力和水平,提高对市场的适应能力和竞争能 力。工业发达国家还将数控技术及数控装备列为国家的战略物资,不仅大 力发展自己的数控技术及其产业,而且在"高精尖"数控关键技术和装备方 面对我国实行封锁和限制政策。因此大力发展以数控技术为核心的先进制 造技术已成为世界各发达国家加速经济发展、提高综合国力和国家地位的 重要途径。
车铣技术凸轮轴加工工艺分析
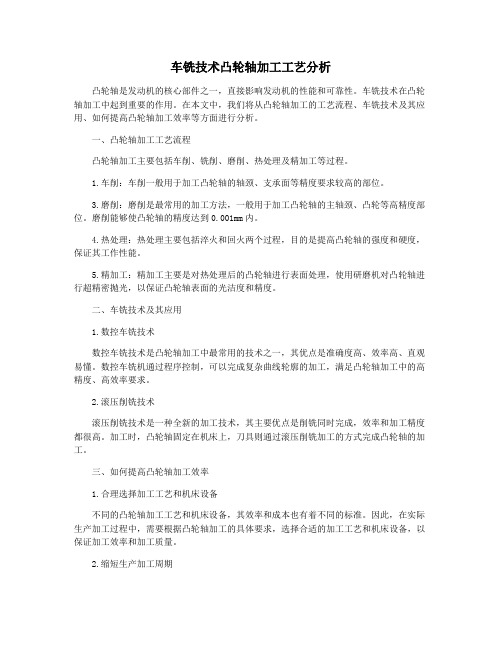
车铣技术凸轮轴加工工艺分析凸轮轴是发动机的核心部件之一,直接影响发动机的性能和可靠性。
车铣技术在凸轮轴加工中起到重要的作用。
在本文中,我们将从凸轮轴加工的工艺流程、车铣技术及其应用、如何提高凸轮轴加工效率等方面进行分析。
一、凸轮轴加工工艺流程凸轮轴加工主要包括车削、铣削、磨削、热处理及精加工等过程。
1.车削:车削一般用于加工凸轮轴的轴颈、支承面等精度要求较高的部位。
3.磨削:磨削是最常用的加工方法,一般用于加工凸轮轴的主轴颈、凸轮等高精度部位。
磨削能够使凸轮轴的精度达到0.001mm内。
4.热处理:热处理主要包括淬火和回火两个过程,目的是提高凸轮轴的强度和硬度,保证其工作性能。
5.精加工:精加工主要是对热处理后的凸轮轴进行表面处理,使用研磨机对凸轮轴进行超精密抛光,以保证凸轮轴表面的光洁度和精度。
二、车铣技术及其应用1.数控车铣技术数控车铣技术是凸轮轴加工中最常用的技术之一,其优点是准确度高、效率高、直观易懂。
数控车铣机通过程序控制,可以完成复杂曲线轮廓的加工,满足凸轮轴加工中的高精度、高效率要求。
2.滚压削铣技术滚压削铣技术是一种全新的加工技术,其主要优点是削铣同时完成,效率和加工精度都很高。
加工时,凸轮轴固定在机床上,刀具则通过滚压削铣加工的方式完成凸轮轴的加工。
三、如何提高凸轮轴加工效率1.合理选择加工工艺和机床设备不同的凸轮轴加工工艺和机床设备,其效率和成本也有着不同的标准。
因此,在实际生产加工过程中,需要根据凸轮轴加工的具体要求,选择合适的加工工艺和机床设备,以保证加工效率和加工质量。
2.缩短生产加工周期生产加工周期不仅直接影响成本和效率,还会影响到生产中的实时监控和生产安排。
因此,缩短生产加工周期对于凸轮轴加工具有重要的意义。
3.设计满足自动化加工的凸轮轴结构在设计凸轮轴结构时,需要考虑到自动化加工:保证各个关键尺寸精度,适当增大轴承支承直径,从而提高轴承支承精度和生产加工效率。
总之,在凸轮轴加工中,需要选择适当的工艺和机床设备,尽可能缩短生产加工周期,设计合理的凸轮轴结构,以提高加工效率和成本优势,从而提升凸轮轴的工作性能和可靠性。
典型零件的加工工艺分析案例
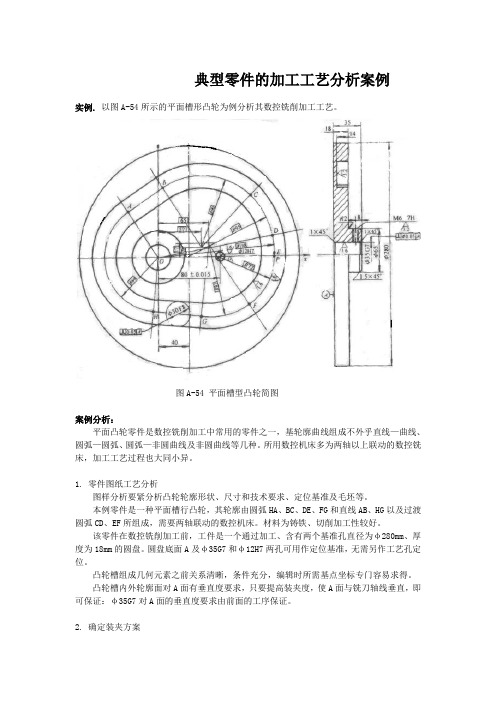
典型零件的加工工艺分析案例实例. 以图A-54所示的平面槽形凸轮为例分析其数控铣削加工工艺。
图A-54 平面槽型凸轮简图案例分析:平面凸轮零件是数控铣削加工中常用的零件之一,基轮廓曲线组成不外乎直线—曲线、圆弧—圆弧、圆弧—非圆曲线及非圆曲线等几种。
所用数控机床多为两轴以上联动的数控铣床,加工工艺过程也大同小异。
1. 零件图纸工艺分析图样分析要紧分析凸轮轮廓形状、尺寸和技术要求、定位基准及毛坯等。
本例零件是一种平面槽行凸轮,其轮廓由圆弧HA、BC、DE、FG和直线AB、HG以及过渡圆弧CD、EF所组成,需要两轴联动的数控机床。
材料为铸铁、切削加工性较好。
该零件在数控铣削加工前,工件是一个通过加工、含有两个基准孔直径为φ280mm、厚度为18mm的圆盘。
圆盘底面A及φ35G7和φ12H7两孔可用作定位基准,无需另作工艺孔定位。
凸轮槽组成几何元素之前关系清晰,条件充分,编辑时所需基点坐标专门容易求得。
凸轮槽内外轮廓面对A面有垂直度要求,只要提高装夹度,使A面与铣刀轴线垂直,即可保证:φ35G7对A面的垂直度要求由前面的工序保证。
2. 确定装夹方案一样大型凸轮可用等高垫块垫在工作台上,然后用压板螺栓在凸轮的孔上压紧。
外轮廓平面盘形凸轮的垫板要小于凸轮的轮廓尺寸,不与铣刀发生干涉。
对小型凸轮,一样用心轴定位,压紧即可。
依照图A-54所示凸轮的结构特点,采纳〝一面两孔〞定位,设计一〝一面两销〞专用夹具。
用一块320mm×320mm×40mm的垫块,在垫块上分别精镗φ35mm及φ12mm两个定位销孔的中心连接线与机床的x轴平行,垫块的平面要保证与工作台面平行,并用百分表检查。
图A-55为本例凸轮零件的装夹方案示意图。
采纳双螺母夹紧,提高装夹刚性,防止铣削时因螺母松动引起的振动。
图A-55凸轮装夹示意图3. 确定进给路线进给路线包括平面内进给和深度进给两部分路线。
对平面内进给,对外凸轮廓从切线方向切入,对内凹轮廓从过渡圆弧切入。
凸轮工件的数控加工工艺分析

摘要:凸轮轴作为汽车发动机配气机构中的关键部件,其性能直接影响着发动机整体性能。
因此凸轮轴的加工工艺有特殊要求,合理的加工工艺对于降低加工成本、减少生产环节以及合理布置凸轮轴生产线具有很大的现实意义。
本文针对凸轮轴的加工特点,结合工厂的实际,从前期规划开始,对凸轮轴的加工工艺进行了深入的分析、研究。
建立了用数控无靠模方法。
对凸轮廓形进行计算和推倒,对凸轮轮廓的加工进行了探讨并提出适用于发动机凸轮轴的加工方法。
关键词:发动机;凸轮轴;工艺分析目录摘要: (1)目录 (2)1 引言 (1)2 凸轮轴生产线前期规划 (1)2.1产品规格 (1)2.2工艺设计原则及凸轮轴加工工艺分析 (2)2.3小结 (3)3 凸轮轴生产线工艺分析 (3)3.1生产线布置 (3)3.2工艺设计 (4)3.3工艺分析 (5)3.4工艺特点 (7)3.5工艺难点 (9)4 凸轮廓形理论计算及加工控制参数 (10)4.1凸轮轴凸轮的廓形要求 (10)4.2包络线理论 (13)4.3凸轮廓形坐标 (14)4.4砂轮的中心坐标 (17)4.5磨削圆周进给量计算 (18)4.6等周速曲线 (20)4.7砂轮座加速度 (20)4.8光顺处理 (21)4.9工件主轴转速配置 (21)4.10磨削用量数据 (22)5结论 (23)参考文献 (23)1 引言随着现代行业的不断发展,再加上配件的需求,使得凸轮轴的需求量一直高居不下。
建立一条集先进性与经济性为一体的凸轮轴生产线是非常必要的。
面对国外汽车行业的冲击,我们国产汽车业应该加紧研究、建立符合中国国情的,我们自己的基础制造业,提高质量、降低成本,这样才能保住我们国产汽车的市场。
凸轮轴在发动机中的重要地位决定了国内发动机生产厂家都建有自己的凸轮轴生产线,这样可以在保证整机质量的前提下,尽可能的降低成本,提高竞争力。
本文主要围绕汽车凸轮轴生产线的工艺分析,从前期准备、工艺设计、理论计算、生产实践、和产品检测这几个方面,阐述了凸轮轴加工的一整套设计思路和方法,对发动机制造业中的零部件加工具有重要的参考作用。
凸轮轴加工工艺

凸轮轴加工工艺凸轮轴是一种重要的机械传动装置,用于将来自引擎的旋转运动转化为线性运动,驱动汽车等机械设备的运行。
凸轮轴的加工工艺对于其性能和质量起着重要的影响。
本文将详细介绍凸轮轴加工的工艺过程和注意事项。
1.工艺流程凸轮轴加工的工艺流程包括以下几个关键步骤:1.1 材料准备:选择适合的材料对凸轮轴的性能和耐用性至关重要。
常见的材料有碳钢、合金钢等。
在材料准备阶段,需要对材料进行检验和筛选,确保其质量符合要求。
1.2 成品设计:根据汽车或机械设备的需求,通过CAD软件进行凸轮轴的设计。
设计包括凸轮的形状、凸轮的数量和位置等。
1.3 粗加工:将材料锯断成合适的长度,并进行外形修整。
粗加工通常采用车床等机床进行,以确保凸轮轴的整体形状和尺寸符合设计要求。
1.4 精加工:精加工是凸轮轴加工的重要环节。
其中包括车削、铣削、钻孔等工艺。
通过这些工艺,将凸轮轴的各个部位进行加工,使其形成凸轮和轴颈等特殊结构。
1.5 热处理:热处理是为了提高凸轮轴的硬度和强度,以增加其使用寿命和耐磨性。
常见的热处理方法包括淬火、回火等。
1.6 表面处理:为了提高凸轮轴的表面质量和耐腐蚀性,常常需要进行表面处理。
常见的表面处理方法有镀铬、喷涂等。
1.7 检验和调整:在加工完成后,需要对凸轮轴进行检验和调整,以确保其质量和性能符合要求。
常见的检验方法有尺寸测量、硬度测试等。
2.注意事项凸轮轴加工过程中需要注意以下几个方面:2.1 切削参数的选择:切削参数的选择直接影响凸轮轴的加工质量和效率。
不同的材料和工艺要求需要选择不同的切削速度、进给量和切削深度等参数。
2.2 工具的选择和磨具的修整:工具的选择和磨具的修整对于凸轮轴的加工精度和表面质量起着决定性的作用。
需要选择适合的工具和磨具,并进行定期的修整和更换。
2.3 温度控制:加工过程中需要控制好温度,避免过热或过冷对凸轮轴的影响。
特别是热处理过程中,需要控制好加热温度和冷却速度,以确保凸轮轴的性能和硬度符合要求。
车铣技术凸轮轴加工工艺分析

车铣技术凸轮轴加工工艺分析车铣技术是一种将工件放置在机床上,通过车铣刀具的切削力和机床的移动来加工工件的技术。
凸轮轴是一种具有复杂曲线轮廓的机械零件,其加工工艺分析对于保证产品质量和提高生产效率具有重要意义。
本文将从工艺流程、工艺参数和工艺装备三个方面对凸轮轴的加工工艺分析进行详细阐述。
一、工艺流程:凸轮轴的加工工艺流程一般包括零件的选择、工艺设计、工艺装备准备、加工工序和质量检验等几个主要环节。
工艺设计是关键的环节,它直接决定了后续加工工序的选择和加工工艺的确定。
1、零件的选择:凸轮轴的加工工艺分析首先需要根据设计要求选择合适的零件。
在选择零件时,应考虑到凸轮轴所承受的载荷、工作环境及材料的性能等因素,以确保最终产品的质量和可靠性。
2、工艺设计:在工艺设计环节中,需要对凸轮轴的加工工艺进行规划和组织。
根据凸轮轴的结构特点和加工要求,确定凸轮轴的加工工序、加工顺序和加工方法,并确定对应的切削参数和加工配方。
3、工艺装备准备:准备好所需的加工设备和工装夹具,对机床进行调整和检修,确保其正常工作状态。
还需准备好所需的刀具、测量工具和辅助设备,以便进行加工和检测。
4、加工工序:根据工艺设计确定的加工工序和工艺流程进行加工。
一般来说,凸轮轴的加工工序包括车削、铣削、钻削、砂轮修整等。
在每个工序中,都需要合理选择刀具、确定切削速度和进给量,控制切削力和加工精度,以确保加工质量和降低生产成本。
5、质量检验:在加工完成后,需要对凸轮轴进行质量检验,以确保其满足设计要求和产品标准。
质量检验的内容主要包括尺寸精度、表面质量、材料性能和装配性能等。
根据检验结果,可对加工工艺进行调整和改进,以提高产品的质量和性能。
二、工艺参数:凸轮轴的加工工艺分析还需要确定一系列的加工参数,包括切削速度、进给量、切削厚度和切削角度等。
这些参数直接影响到加工效率和加工质量。
1、切削速度:切削速度是指切削刀具在加工过程中的移动速度。
它是决定切削力大小和切削温度高低的主要参数之一。
机械毕业设计(论文)-平面槽形凸轮零件的加工工艺设计与数控编程【全套图纸】

本科毕业设计(论文)题目:平面槽形凸轮零件的加工工艺设计与数控编程系别:机电信息系专业:机械设计制造及其自动化班级:学生:学号:指导老师:2013年5月摘要平面槽形凸轮零件的加工工艺设计与数控编程摘要此设计主要是对典型零件进行图形绘制、工艺设计和程序的编制及加工,通过对平面槽型凸轮的外形尺寸分析,应用CAD以及Pro/E软件绘制出二维和三维的图形并进行标注说明,注明图纸的公差要求、技术要求等。
接着对平面槽型凸轮的零件图进行工艺分析,确定加工方法、路线等,并设计好各切削参数自动编出加工刀路轨迹。
然后跟据图纸的工艺分析,选择合理的工艺路线及加工方法,根据零件形状、余量等选择适用形状大小的各种铣刀,最后将Pro/E软件绘制的三维图利用数控加工仿真软加工件Mastercam9.0进行仿真模拟加工,生产刀具轨迹;使用后置处理程序选取相应的配置文件,将刀具轨迹转换为数控机床可以识别的NC程序,为更加高速,快捷的造型,生产提供了一种切实可行的办法。
生成的NC程序可以利用DNC方式传输给数控机床进行三维加工。
关键词:平面槽型凸轮;加工工艺;数控加工毕业设计(论文)Planar slotted CAM parts processing design and NCprogrammingAbstractThis design is mainly focuses on the preparation, the process of graphics rendering, design and the typical parts, through the analysis of shape and size of plane cam groove by using CAD and Pro/E software to draw graphics, 2D and 3D to label instructions and annotate the drawings tolerance requirements and technical requirements.Then it comes to the analysis of plane groove cam parts , the determination of the method of producing,and routes for process as well as the design the cutting parameters, which will create tool’s path automatically.After the previous process, choosing suitable allowance cutter shape and size is determined by the analysis of pictures. According to the shape of parts, the NC machining simulation using Pro/E software rendering 3D map of the soft parts of Mastercam9.0 for simulation of processing and production tool path. Selecting the configuration file accordingly is determined by the use of post processing program, the tool path for CNC machine tool transformation can be identified by the NC program, for more rapid, efficient design,which provide a feasible solution.The generated NC program can be transmitted to the CNC machine tools for machining by using the DNC.Key words:Planar slot type cam;machining process;NC machining目录摘要 (I)1 绪论 (1)1.1 研究背景 (1)1.2 平面凸轮机构CAD/CAM的发展方向 (1)1.3课题内容及实施步骤 (3)2 零件的分析及工艺规程设计 (4)2.1零件的作用 (4)2.2工艺分析 (4)2.3毛坯的确定 (5)2.4基准的选择 (6)2.4.1粗基准的选择 (6)2.4.2 精基准的选用 (7)2.5制定加工工艺路线 (7)3 刀具的选择和切削用量的确定 (9)3.1 铣削用刀具及其选择 (9)3.2 刀具材料应该满足零件的加工要求 (9)4 加工参数的选择及时间定额计算 (11)5 夹具的设计 (19)5.1 机床夹具有三大功用 (19)5.2 机床夹具设计要求 (19)5.3 工件的装夹方法和装夹方式 (19)5.4 确定夹具的类型 (20)5.5 夹紧装置 (20)6 仿真加工 (24)6.1 图形处理 (24)6.2 走刀路线的确定及刀具选择 (24)6.3 后置处理(生成NC 程序) (30)总结 (31)参考文献 (32)致谢 (33)附录1 Master CAM仿真程序代码 (34)毕业设计(论文)知识产权声明 ................................................错误!未定义书签。
凸轮轴的工艺分析及生产类型的确定

凸轮轴的工艺分析及生产类型的确定凸轮轴是发动机中的重要部件,其主要作用是控制气门的开闭时机。
凸轮轴的工艺分析及生产类型的确定对提高发动机的性能和可靠性具有重要意义。
一、凸轮轴的工艺分析:1.材料选择:凸轮轴一般采用高强度合金钢材料,如40Cr、40CrNiMoA等。
材料应具有较高的强度、韧性和耐磨性,以满足凸轮轴在高温、高压和高速旋转环境下的工作要求。
2.凸轮形状设计:凸轮轴的凸轮形状直接影响气门的开闭时机和程度,对发动机的性能、经济性和排放等方面有重要影响。
通过对发动机的工作特性和工作条件的分析,确定凸轮的形状参数,如凸轮角度、凸轮升程、凸轮曲线等。
3.热处理工艺:凸轮轴在制造过程中需要进行热处理,以提高其强度和硬度。
常用的热处理方法有淬火和回火。
淬火可以增加凸轮轴的硬度,但容易导致脆性增加;回火可以减轻凸轮轴的脆性,但降低了其硬度。
通过对热处理工艺的优化,可以使凸轮轴具有较高的强度和良好的韧性。
4.加工工艺:凸轮轴的加工工艺包括车削、磨削、车磨联合加工等。
其中,磨削是保证凸轮轴精度和表面质量的重要工艺。
在磨削过程中,需要控制加工参数,如磨削速度、进给量、磨料选用等,以保证凸轮轴的尺寸和几何精度。
5.表面处理:为了提高凸轮轴的耐磨性和耐蚀性,常常需要进行表面处理。
常用的表面处理方法有渗碳、镀铬、氮化等。
渗碳可以提高凸轮轴的表面硬度,镀铬和氮化可以形成硬度较高、抗蚀能力较强的层。
二、凸轮轴生产类型的确定:1.单体型凸轮轴:单体型凸轮轴即整体式凸轮轴,是将凸轮和轴体作为一个整体加工制造。
这种生产类型制造工艺较简单,但对材料的要求较高,需要选择强度和韧性兼备的合金钢材料。
2.组合式凸轮轴:组合式凸轮轴是将凸轮和轴体分别加工制造,再通过加热融合或机械连接等方式结合在一起。
这种生产类型相对于单体型凸轮轴,制造工艺更为复杂,但可以选择不同材料进行制造,以满足不同部位的要求。
在确定凸轮轴的生产类型时,需要考虑生产工艺的复杂性、材料的可选性以及成本等因素。
Mastercam9.1第6章 沟槽凸轮的设计与

4.注解文字
若直接点选R80,R90,R97,R250,R260,R267的圆弧,也可标注圆 弧的半径,但尺寸线通过圆心,造成尺寸线很长,图面较零乱。现采用引 导线加注解文字来标注。方法如下:
(1) 单击 绘图 → 尺寸标注 →引导线 → 中点 命令,过程如图6-18 所示。
(2) 点选 R97圆弧,拉动鼠标到合适位置,单击左键,再水平拉动 鼠标到合适位置,单击左键,按 Esc 键,可画好引导线。如图6-19所示。
图6-20
图6-21
5.两圆的中心距的标注
(1)单击 绘图 → 尺寸标注 → 标示尺寸 → 水平标示 → 圆心点 命令,点
选Ø 25的圆。
(2)单击 圆心点 命令,点选Ø 12的圆。移动鼠标到合适位置。
(3)从键盘输入字母“G”,出现如图6-22所示的对话框,填选如下:
• 小数位数:3 。
• 公差设定: 。
• 处理方式为:⊙复制。
• 补正 ⊙ 左补正,当串联的箭头方向为逆时针方向时,采用左补正, 保证向内补正。
• 补正距离为7。
图6-13
图6-14
6.3.8 串联补正
(4)点选 确定 按钮,得到“凸轮外轮廓”,结果如图6-15所示 。
(5)同样的方法,可得到内轮廓“凸轮内轮廓”,补正距离为
17,如图6-16所示。
(4)点选主菜单中的 执行 命令,进入外形铣削对话框。如图6-25所示。
2. 选择刀具参数
输入主要刀具参数如下:
·进给率: 1200 毫米/分。
·Z轴进给率: 1000毫米/分。
·提刀速率: 2000 毫米/分。
·主轴转速 1700 转/分。
·冷却液
喷气 。 其余为默认值。
- 1、下载文档前请自行甄别文档内容的完整性,平台不提供额外的编辑、内容补充、找答案等附加服务。
- 2、"仅部分预览"的文档,不可在线预览部分如存在完整性等问题,可反馈申请退款(可完整预览的文档不适用该条件!)。
- 3、如文档侵犯您的权益,请联系客服反馈,我们会尽快为您处理(人工客服工作时间:9:00-18:30)。
大 于 1 1 根据上述各因素 。 .. 6L m。 可查表确定该锻件的尺寸公差
2 确定 毛坯 的尺 寸公差 和机 械加 工余 量
毛 坯余 量 的确 定 , 工 余 量 可 以 由 《 械 制 造 技 术 基 础 课 加 机 程 设 计 指 导 教程 》查 到 。要 确 定 毛 坯 的 尺 寸 公 差 及 机 械 加 工
5
结论
在 进 行 沟 槽 凸 轮 零 件 沟 槽 粗 铣 加 工 工序 时 , 10外 圆端 q5  ̄
工工序和辅助加工工 序 , 些工序都直接 影响到零件 的加 工 这
质 、 生产效率和加工成本。 量 采 用普 通 的 机械 车床 加 工 方 法 :
⑤5 V稳压 电源 2 。 个
()硬件单元电路 : 2 ①振铃音检测 。 将本装置的输入线两
端 并 联 在 电 话 机 两 端 , 手 机 拨 打 本 舍 电话 , 用 当有 振 铃 音 时 ,
用 万 用 表 的 直 流 档 测 量 光 电耦 合 器 4 2 N 5的输 出端 ,有 明显
某 沟槽 凸轮 锻造 毛坯 图 。
28
压 件、 冲压 件 及 焊 接 组 合 件 等 , 同一 种 毛 坯 又 可 能 有 不 同的 制 造 方 法 。 最 常 用 的 毛 坯 是 铸 件 和 锻 件 , 而 本 文 所 研 究 的 对
象 — — 某 沟 槽 凸 轮 在 工作 中要 承 受 重 载 荷 、 击 载 荷 或 交 变 冲
的 。流 程 图 如 图 2所示 。
4 系统 调试
本 装 置 的 调试 主要 分 为 硬件 调 试 、软 件 调 试 和 联 机 调 试
等三大部分 。
() 仪器仪表 : 电话机 2台 ;)P 14 1测试 ① (L 52 单片机仿真  ̄
机 2 ③gn sP  ̄序读写器 2 ; F0 个; ei S + u 个 ④M 5 万用表 2 ; 个
1 确 定 毛坯 的制造 形式
5 9
提 高 毛 坯 的 制 造 质 量 , 以减 少 机 械 加 工 劳 动 量 , 可 降低 机
械 加 工 成 本 ,但 往 往 会 增 加 毛 坯 的 制 造 成本 。 因 此我 们 要 注
意 材 料 的工 艺 性 能 、 毛坯 的 尺 寸形 状 和精 度 要 求 、 件 的 生 产 零 纲 领 采 用 新 技 术 新 工 艺 新 材 料 的可 能 性 。
Ab t a t T i a e s man y o a g o v c i i g p o e s t t y n lz h c ia i t f p rs a d sr c hsp p ri i l f a c m r o e ma h nn r c s o s ud ,a ay e t e ma h n b l y o a t n i
摘
要: 文章主要是 对某沟槽 凸轮 的机加 工工艺进行研究 , 分析零件的可加 工性和 工序 的合理性 可以为产品建立
合理的设计结构 , 而为实现 并行设计打下基础 。 从 关键词 : 沟槽 凸轮 ; 机加工 ; 工艺 中图分类号 :H1 T 2 文献标识码 : A
文章编号 :0 7 82 (0 10 — 0 8 0 10 — 3 0 2 1 )9 0 5— 1
余量 . 应先 确定 如下 各 项 因素 。 ( ) 差 等 级 。 由 弹簧 吊耳 的功 用 及 其 技 术 要 求 , 定 该 1公 确 零 件 的公 差 等级 为 普 通 级 。 ( )锻 件 重 量 。 已 知 机 械 加 工 后 某 沟 槽 凸 轮 的重 量 为 2 26 g 由 此可 初 步 估 计 机 械 加 工 前 锻 件 毛 坯 的 重 量 为 3 k 。 . 。 k . g 2 ( ) 用 范 围 。 国标 规定 了 圆形 , 雷 和 盘类 自由 锻件 的 3适 柱 机 械 加 工 余 量 与 公 差 ,对 某 沟 槽 凸轮 零 件 图 进 行 分 析 计 算 , 可 大致 确定 适合 范 围 (.D≤H≤D) 01 盘类 。 ( ) 件 分 模 线 形 状 。 根 据某 沟槽 凸轮 的形 位 特 点 , 选 4锻 故 择 零 件 高 度 方 向 的对 称平 面为 分 模 面 , 平 直 分 模 线 , 1 属 图 为
凸 轮 的 两 端 面
4 某沟槽凸轮零件的工艺路线拟定
工 艺 路 线 的 拟 定 包 括 : 位 基 准 的 选 择 : 表 面 加 工 方 定 各 法 的确 定 ; 工 阶段 的划 分 ; 序 集 中程 度 的 确 定 ; 序 顺 序 加 工 工 的 安排 。 拟 定 工 艺 路 线 的 第 一 步 确 定 定 位 基 准 . 考 虑 精 基 先 准 来 加 工 各 表 面 。在 选 择 粗 基 准 把 精 基 准 的 表 面 先 加 工 出 来。
载 荷 , 选 用 锻 件 作 为 毛 坯 , 为锻 件 的 强 度 与 冲 击 韧 度 高 , 应 因 该 锻件 的 材料 选 用 合 金 钢 。 锻 造 方 法 有 自由锻 、 模锻 与 胎 膜锻 和精 密锻 造 等 几 种 。 其 中 . 由锻 生 产 效 率 低 、 造 精 度 低 、 面 质 量 差 、 工 余 量 自 锻 表 加 大 , 成本较低 , 用于单件小 批量生产及 大型锻件生产 ; 但 适 模 锻 生 产 效 率 高 、 造 精 度 高 、 面质 量 好 、 工 余 量 小 , 锻 造 锻 表 加 可 较 复 杂 的 锻 件 ,但成 本 较 高 ,适 用 于成 批 大 量 生 产 中小 型 锻 件 ; 膜 锻 介 于 自 由锻 与 模 锻 之 间 , 用 于 中小 批 生 产 小 型 锻 胎 适 件。
社 .9 9 19 .
() 2 用户 信 令 解 释 功 能 。对 收 到 的用 户信 号, 统 按 照 软 系
件 设 定 加 以解 释 , 设 语 音 提 示 电路 , 放 相 应 的系 统 提 示 音 , 可 播
( 上接 第 5 8页)差为 O 0 , 的配合精度为 H , . 6孔 0 7 表面粗糙度
为H , 7 表面粗糙度为 1 。 . 中心孔 的垂直度公 ( 6 下转第 6 0页)
6 0
湖 南 农 机
实现 用 户 和 电话 远 程 控 制 系 统 间 的 交 互 操 作 。
2 1 年 9月 0 1
话 线 发 送 到 电容 C 3 经 R 3 R 4衰 减 送 至 M 87 ( 整 的 2, 1、 1 T 80完
综 合 以上 两 种 因 素 来 考 虑 我们 生 产 的零 件 应 该 是 采 用 锻 造 的 方 式 生 产 锻 造 毛 坯 。确 定 该 零 件 的 材 料 为 K H30 0 , T 0 — 6 该
材 料具 有 良好 的 加工 切 削 性 能 。
图 1零件毛坯 图
由 沟槽 凸 轮 零 件 图 可 知 ,该 零 件 各 加 工 表 面 的 粗糙 度 R t e均
() 1 系统 身 份 认 证 功 能 。 为 了保 证 只 有 合 法 用 户 才 能操
作 系统 , 电话 远 程 控 制 系 统 上 线 以后 , 户 必 须 输 入 密 码 , 系 用 待 统确认后才具有对系统的操作权限。
行仿真 。
参
社 .0 0 20 .
考
文
献
[ 何 书森. 1 ] 实用数字电路 原理 与设计速成[ ] 州 : 建科 学技术 出版 M. 福 福 【 房小翠, 2 】 王金凤. 片机 实用 系统设计技术[ 】 单 M. : 北京 国防工业 出版
p o ess o ain ly c n b e s n be d sg o h rd c t cue n h sly te fu d t n frte raia rc se frt ai a e ara o a l e in frte po u ts u tr,a d tu a h o n ai o h e l - o t r o z
D MF接 收器)进行解码 ,把双音多频信号转换成 二进 制编 T
码 。 后输至单片机进行数据处理 , 而实现控制功能。 然 进
( ) 件定 时 功 能 。 3软 系统 软 件 设 定 系 统 自动 复 位 的 软 件定
时 器 。 时 器 的设 置 值 规 定 了 系 统 一 次 上 线 工 作 的 最 大 时 间 。 定 若 一 次 工 作 超 时 , 统 自动 离 线 , 入 待 机 状 态 , 非 常 重 要 系 进 是
功 能 比较 多 , 以软 件 程 序 的 调 试 显 得 相 当 的烦 琐 。 个 程 序 所 整
是 使 用 汇 编 语 言 ,在 L P O E下 编 写 调 试 完 成 后 ,先 用 gnu eis S+ 序读写器将 程序写入单片机 , 后在 L52 P程 然 P 14仿 真 机 进
3 系统 软件设 计
Ca g o v o e sn a h n n l ss m r o e pr c s i g m c i e a a y i
L o gfi /Yn -e
( nin oai a n eh i lC lg, ni gH nn4 3 0 ,hn) Xi ag V ct nlad Tc nc oe e Xi a e a 5 0 0C ia x o a l xn
为 1 。 他 部 位 的 表 面 粗 糙度 为 3 。 毛刺 , 圆 角 , 进 行 .其 6 .去 2 倒 并 热 处 理 , 零件 达 的综 合 性 能 达 到 零 件 的使 用 要 求 。 使
外 轮廓 工序 四 :  ̄ 5 以 o 0的外 轮 廓 为 粗 基 准 钻 、 、 孔 1 扩 铰 工 序 五 : q 2的 中 心 孔 为 精 基 准 半 精 铣 、 铣 某 沟 槽 以 o 1 精
t n o a al ld sg . i fp r l e in o e Ke wo d :c m r o e y r s a g o v ;ma h n n p o e s c ii ̄ rc s