AZ9481-1A-9D中文资料
A4931 datasheet 中文+总结

本人使用过程中翻译了本文,水平有限难免有误,欢迎纠正:tyooo@A49313-Phase Brushless DC Motor Pre-Driver三相无刷直流电机前置驱动器4931-DS, Rev. 4下载::/~/media/Files/Datasheets/A4931-Datasheet.ashx下载翻译:2012-11-15▪ ▪ ▪ ▪▪▪ ▪▪本人使用过程中翻译了本文,水平有限难免有误,欢迎纠正: tyooo@A4931 三相无刷直流电机前置驱动器Absolute Maximum RatingsThermal Characteristics*For additional information, refer to the Allegro website.CharacteristicSymbolNotes RatingUnits供电电压Load Supply Voltage V BB38 V 电机输出Motor Phase Output S X t w < 500 ns –3 V 霍尔输入 V Hx DC–0.3 to 7 V 逻辑输入电压范围 V IN–0.3 to 7 V 工作环境温度 T A Range M–20 to 105ºC 最大结温度 T J (max) 150 ºC 储藏温度T stg–40 to 150ºCCharacteristicSymbolTest Conditions*RatingUnits封装内阻,结点到外面(Junction to Ambient )R θJA 4-layer PCB based on JEDEC standard32 ºC/W 封装内阻,结点到焊盘(Junction to Exposed Pad )R θJP2ºC/W本人使用过程中翻译了本文,水平有限难免有误,欢迎纠正: tyooo@A4931 三相无刷直流电机前置驱动器Functional Block DiagramTerminal List0.1 μFNumber 1Name HA+ Description Hall input A 2 HA - Hall input A 3 HB+ Hall input B 4 HB Hall input B 5 HC+ Hall input C 6 HC- Hall input C 7 GND Ground8 HBIAS Hall bias power supply output 9 CP1 Charge pump capacitor terminal 10 CP2 Charge pump capacitor terminal 11 VBB Supply voltage12 VCP Reservoir capacitor terminal 13 SENSE Sense resistor connection 14GLCLow side gate drive CNumber 15 Name GLB Description Low side gate drive B 16 GLA Low side gate drive A 17 GHC High side gate drive C18 SC High side source connection C 19 GHB High side gate drive B20 SB High side source connection B 21 GHA High side gate drive A22 SA High side source connection A 23 FG1 FG 1 speed control output (3 Φ inputs)24 FG2 FG 2 speed control output (ΦA input) 25 CLD Locked rotor detect timing capacitor 26 DIR Logic input – motor direction27 ENABLE Logic input – external PWM control 28BRAKEZLogic input – motor brake (active low)本人使用过程中翻译了本文,水平有限难免有误,欢迎纠正: tyooo@A4931 三相无刷直流电机前置驱动器ELECTRICAL CHARACTERISTICS *Valid at T A= 25°C, V BB= 24 V, unless noted otherwise*Typical data are for initial design estimations only, and assume optimum manufacturing and application conditions. Performance may vary for individualunits, within the specified maximum and minimum limits. For input and output current specifications, negative current is defined as coming out of (sourcing) the specified device pin. Specifications throughout the allowed operating temperature range are guaranteed by design and characterization.本人使用过程中翻译了本文,水平有限难免有误,欢迎纠正:tyooo@ A4931 三相无刷直流电机前置驱动器本人使用过程中翻译了本文,水平有限难免有误,欢迎纠正:tyooo@固定断开时间Fixed Off-Time 理论上A4931的固定断开本人使用过程中翻译了本文,水平有限难免有误,欢迎纠正:tyooo@ A4931 三相无刷直流电机前置驱动器ET Package, 28-Contact QFNFor Reference Only (reference JEDEC MO-220VHHD-1) Dimensions in millimeters Exact caseand lead configuration at supplier discretion within limits shown0.55 +0.20 –0.10Terminal #1 mark area 3.15Exposed thermal pad (reference only, terminal #1 identifier appearance at supplier discretion)Reference land pattern layout (reference IPC7351 QFN50P500X500X100-29V1M); All pads a minimum of 0.20 mm from all adjacentpads; adjust as necessary to meet application process requirements and PCB layout tolerances; when mounting on a multilayer PCB,thermal vias at the exposed thermal pad land can improve thermal dissipation (reference EIA/JEDEC Standard JESD51-5)Coplanarity includes exposed thermal本人使用过程中翻译了本文,水平有限难免有误,欢迎纠正:tyooo@总结1.BREAK:低电平进入刹车状态。
SAE AS 85049(conn accessories)

SAE Technical Standards Board Rules provide that: “This report is published by SAE to advance the state of technical and engineering sciences. The use of this report is entirely voluntary, and its applicability and suitability for any particular use, including any patent infringement arising therefrom, is the sole responsibility of the user.”SAE reviews each technical report at least every five years at which time it may be reaffirmed, revised, or cancelled. SAE invites your written comments and suggestions. Copyright 1998 Society of Automotive Engineers, Inc.All rights reserved.Printed in U.S.A. QUESTIONS REGARDING THIS DOCUMENT:(724) 772-8510FAX: (724) 776-02431.SCOPE:1.1Scope:This specification covers connector accessories for use with electrical connectors underenvironmental or non-environmental conditions. Applicable connector accessories defined in this specification are delineated for the suppression of Electromagnetic Interference (EMI) and Radio Frequency Interference (RFI).1.1.1Connector accessory categories:Connector accessories covered in this specification shall includebut are not limited to the following categories:-- || | | | | || ||||| |||| || ||| || || | ||| |----- || | | | | || ||||| |||| || ||| || || | ||| |----- || | | | | || ||||| |||| || ||| || || | ||| |---1.2Classification:Connector accessories shall be of the size, style, finish, and class as specified on the applicable military specification sheet (see 3.1).2.APPLICABLE DOCUMENTS:2.1Government documents:2.1.1Specifications and standards:The following specifications and standards form a part of this specification to the extent specified herein. Unless otherwise specified, the issues of thesedocuments shall be those listed in the issue of the Department of Defense Index of Specifications and Standards (DODISS) and supplement thereto, cited in the solicitation.SPECIFICATIONS FEDERAL QQ-P-35Passivation Treatments for Austentic, Ferretic, and Corrosion Resisting Steel QQ-A-225Aluminum and Aluminum Alloy Bar, Rod, Wire, or Shapes; Rolled, Drawn, or Cold FinishedQQ-A-250Aluminum and Aluminum Alloy Plate and Sheet QQ-A-591Aluminum Alloy Die Castings QQ-A-601Aluminum Alloy Sand CastingsQQ-P-416Plating, Cadmium (Electrodeposited)QQ-S-763Steel Bars, Wires, Shapes, and Forgings, Corrosion-Resisting-- || | | | | || ||||| |||| || ||| || || | ||| |----- || | | | | || ||||| |||| || ||| || || | ||| |---SAE AS850492.1.1 (Continued):MILITARYMIL-C-915Cable and Cord, Electrical, for Shipboard UseMIL-C-5015Connectors, Electrical, Circular Threaded, AN TypeMIL-S-7742Screw Threads, Standard, Optimum Selected SeriesMIL-A-8625Anodic Coating, for Aluminum and Aluminum AlloysMIL-C-22992Connectors, Plugs and Receptacles, Electrical, Waterproof, Quick Disconnect,Heavy Duty Type, General Specification forMIL-C-24308Connectors, Electric, Rectangular, Miniature Polarized Shell, Rack and Panel MIL-R-25988Rubber, Fluorosilicone Elastomer, Oil and Fuel Resistant, Sheets, Strips,Molded Parts, and Extruded ShapesMIL-C-26074Coatings, Electroless Nickel, Requirements forMIL-C-26482Connectors, Electrical (Circular, Miniature, Quick Disconnect, EnvironmentResisting), Receptacles and PlugsMIL-C-27599Connector, Electrical, Miniature, Quick Disconnect (for Weapons Systems),Established ReliabilityMIL-C-28804Connector, Electric, Rectangular, High Density, Polarized Center Jackscrew,General Specification forMIL-C-38999Connectors, Electrical, Circular, Miniature, High Density, Quick Disconnect(Bayonet, Threaded, and Breech Coupling), Environment Resistant,Removable Crimp and Hermetic Solder ContactsMIL-C-55330Connectors, Electrical and Fiber Optic, Packaging ofMIL-C-81703Connectors, Electric, Circular, Miniature, Rack and Panel or Push-PullCoupling, Environment ResistingMIL-C-83723Connectors, Electrical, Circular (Environment Resisting), Receptacles andPlugsMIL-C-83733Connectors, Electrical, Miniature, Rectangular Type, Rack to Panel,Environment Resisting, 200°C T otal Continuous Operating Temperature,General Specification forSTANDARDSFEDERALFED-STD-H28Federal Standards, Screw-Thread Standards for Federal Services2.1.1 (Continued):MILITARYMS20995Wire, Safety or LockMIL-STD-105Sampling Procedures and Tables for Inspection by AttributesMIL-STD-167-1Mechanical Vibrations of Shipboard Equipment (Type I - Environmental andType II - Internally Excited)MIL-STD-202Test Methods for Electronic and Electrical Component PartsMIL-STD-454Standard General Requirements for Electronic EquipmentMIL-STD-790Reliability Assurance Program for Electronic Parts SpecificationsMIL-STD-1285Marking of Electrical and Electronic PartsMIL-STD-1344Test Methods for Electrical ConnectorsMIL-STD-45662Calibration Systems Requirements(Copies of applicable specifications, standards and handbooks listed in the Department of Defense Index of Specifications and Standards (DODISS) and required by the contractor in connection with specific procurement functions may be obtained upon application to the Standardization Documents Order Desk, Building 4D, 700 Robbins Avenue, Philadelphia, PA 19111-5094.)List of superseded documents is delineated in Table V of MIL-C-85049A.SPECIFICATION SHEETSMIL-C-85049/1Connector Accessories, Electrical, Backshell, Nonenvironmental, CableSealing, Straight, Grounding (Without Strain Relief), Category 1C (ForMIL-C-5015 Solder Type, MS310X, Connectors)MIL-C-85049/2Connector Accessories, Electrical, Backshell, Nonenvironmental, CableSealing, Straight, Category 1C (For MIL-C-5015 Solder Type, MS310X,Connectors)MIL-C-85049/3Connector Accessories, Electrical, Backshell, Cable Sealing, Straight,Category 1A (For MIL-C-22992 Connectors, Classes C, J and R)MIL-C-85049/4Connector Accessories, Electrical, Backshell, Cable Sealing, Straight, Step-Up, Category 1A (For MIL-C-22992 Connectors, Classes C, J and R)MIL-C-85049/5Connector Accessories, Electrical, Backshell, Cable Sealing, Straight, Step-Down, Category 1A (For MIL-C-22992 Connectors, Classes C, J and R)MIL-C-85049/6Connector Accessories, Electrical, Backshell, Environmental, Cable Sealing, 45°, Shield Termination, Category 1A (For MIL-C-5015 Crimp, MIL-C-26482Series 2, MIL-C-81703 Series 3, and MIL-C-83723 Series III)MIL-C-85049/7Connector Accessories, Electrical, Backshell, Environmental, Cable Sealing, 45°, Category 1A (For MIL-C-5015 Crimp, MIL-C-26482 Series 2,MIL-C-81703 Series 3, and MIL-C-83723 Series III)MIL-C-85049/8Connector Accessories, Electrical, Backshell, Environmental, Cable Sealing, 90°, Shield Termination, Category 1A (For MIL-C-5015 Crimp, MIL-C-26482Series 2, MIL-C-81703 Series 3, and MIL-C-83723 Series III Connectors)--| | | | | | | | | | | | | | | | | | | | | | | | | | | | | | | ---2.1.1 (Continued):MIL-C-85049/9Connector Accessories, Electrical, Backshell, Environmental, Cable Sealing,90°, Category 1A (For MIL-C-5015 Crimp, MIL-C-26482 Series 2,MIL-C-81703 Series 3, and MIL-C-83723 Series III Connectors) MIL-C-85049/10Connector Accessories, Electrical, Backshell, Environmental, Cable Sealing,Straight, Shield Termination, Category 1A (For MIL-C-5015 Crimp,MIL-C-26482 Series 2, MIL-C-81703 Series 3, and MIL-C-83723 Series IIIConnectors)MIL-C-85049/11Connector Accessories, Electrical, Backshell, Environmental, Cable Sealing,Straight, Category 1A (For MIL-C-5015 Crimp, MIL-C-26482 Series 2,MIL-C-81703 Series 3, and MIL-C-83723 Series III Connectors) MIL-C-85049/14Connector Accessories, Electrical, Backshell, Straight, Self-Locking, Category3B (For MIL-C-38999 Series III and IV Connectors)MIL-C-85049/15Connector Accessories, Electrical, Strain Relief, 45°, Self-Locking, Category4C (For MIL-C-38999 Series III and IV Connectors)MIL-C-85049/16Connector Accessories, Electrical, Strain Relief, 90°, Self-Locking, Category4C (For MIL-C-38999 Series III and IV Connectors)MIL-C-85049/17Connector Accessories, Electrical, Backshell, Environmental, Straight, EMI/RFI Shield Termination, Category 2B (For MIL-C-38999 Series I and IIConnectors)MIL-C-85049/18Connector Accessories, Electrical, Backshell, Environmental, Straight, RFI/EMI, Category 2B (For MIL-C-38999 Series III and IV Connectors) MIL-C-85049/19Connector Accessories, Electrical, Backshell, Nonenvironmental, Straight,RFI/EMI, Category 3B (For MIL-C-38999 Series III and IV Connectors) -- || | | | | || ||||| |||| || ||| || || | ||| |---MIL-C-85049/20Connector Accessories, Electrical, Backshell, Straight, RFI, EMI, Category 3B(For MIL-C-38999 Series III and IV Connectors)MIL-C-85049/21Connector Accessories, Electrical, Backshell, Nonenvironmental, Straight,Category 3B (For MIL-C-38999 Series III and IV Connectors) MIL-C-85049/23Connector Accessories, Electrical, Backshell, Nonenvironmental, 45°, ShieldTermination, Category 3A (For MIL-C-5015 Crimp, MIL-C-26482 Series 2,MIL-C-81703 Series 3, and MIL-C-83723 Series III Connectors) MIL-C-85049/24Connector Accessories, Electrical, Backshell, Nonenvironmental, 90°, ShieldTermination, Category 3A (For MIL-C-5015 Crimp, MIL-C-26482 Series 2,MIL-C-81703 Series 3, and MIL-C-83723 Series III Connectors) MIL-C-85049/25Connector Accessories, Electrical, Backshell, Nonenvironmental, Straight,Shield Termination, Category 3A (For MIL-C-5015 Crimp, MIL-C-26482 Series2, MIL-C-81703 Series 3, and MIL-C-83723 Series III Connectors) MIL-C-85049/26Connector Accessories, Electrical, Backshell, Nonenvironmental, Straight,Shield Termination, Category 3A (For MIL-C-5015 Crimp, MIL-C-26482 Series2, MIL-C-81703 Series 3, and MIL-C-83723 Series III Connectors) MIL-C-85049/27Connector Accessories, Electrical, Backshell, Nonenvironmental, Straight,Self-Locking and Nonself-Locking, Category 3B (For MIL-C-38999 Series Iand II Connectors)-- || | | | | || ||||| |||| || ||| || || | ||| |---SAE AS850492.1.1 (Continued):MIL-C-85049/28Connector Accessories, Electrical, Backshell, Nonenvironmental, Straight,Shield Termination, Category 3B (For MIL-C-83733 Connectors) MIL-C-85049/29Connector Accessories, Electrical, Backshell, Nonenvironmental, Straight,Category 3B (For MIL-C-38999 Series I and II Connectors)MIL-C-85049/30Connector Accessories, Electrical, Backshell, Nonenvironmental, Straight,Individual Shielded Wire Termination, Category 3B (For MIL-C-38999 Series Iand II Connectors)MIL-C-85049/31Connector Accessories, Electrical, Backshell, Nonenvironmental, Straight,Self-Locking and Non-Self-Locking, Category 3B (For MIL-C-5015 Crimp,MIL-C-26482 Series 2, MIL-C-81703 Series 3, and MIL-C-83723 Series IIIConnectors)MIL-C-85049/32Connector Accessories, Electrical, Backshell, Nonenvironmental, 90°, ShieldTermination, Category 3C (For MIL-C-38999 Series I and II Connectors) MIL-C-85049/33Connector Accessories, Electrical, Backshell, Nonenvironmental, Straight,Shield Termination, Category 3C (For MIL-C-38999 Series I and IIConnectors)MIL-C-85049/34Connector Accessories, Electrical, Backshell, Nonenvironmental, ThreadedAdapter, Category 3C (For MIL-C-26482 Series I Jam Nut ReceptacleConnector) (Inactive for New Design Equipment or Modification of ExistingEquipment)MIL-C-85049/36Connector Accessories, Electrical, Backshell, Nonenvironmental, Straight,EMI/RFI Shield Termination, Category 3B (For MIL-C-38999 Series I and IIConnectors)MIL-C-85049/37Connector Accessories, Electrical, Backshell, Nonenvironmental, Split 90°,EMI/RFI Shield Termination, Category 3B (For MIL-C-38999 Series I and IIConnectors)MIL-C-85049/38Connector Accessories, Electrical, Strain Relief, Straight, Category 4B (ForMIL-C-38999 Series III and IV Connectors)MIL-C-85049/39Connector Accessories, Electrical, Strain Relief, 90°, Category 4B (ForMIL-C-38999 Series III and IV Connectors)MIL-C-85049/41Connector Accessories, Electrical, Nonenvironmental, Strain Relief, Straight,Category 4C (For MIL-C-5015 Solder Type, MS310X Connectors) MIL-C-85049/42Connector Accessories, Electrical, Nonenvironmental, Strain Relief, Straight,Category 4A (For MIL-C-5015 Solder Type, MS310X Connectors) MIL-C-85049/43Connector Accessories, Electrical, Strain Relief, Nonenvironmental, 45°,Category 4B (For MIL-C-5015 Crimp, MIL-C-26482 Series 2,MIL-C-81703 Series 3, and MIL-C-83723 Series III Connectors) MIL-C-85049/44Connector Accessories, Electrical, Strain Relief, Straight, Category 4C (ForMIL-C-83733 Connectors)MIL-C-85049/45Connector Accessories, Electrical, Strain Relief, Straight, Nonmetallic,Category 4C (For MIL-C-27599 Series I and MIL-C-38999 Series I and IIConnectors)SAE AS850492.1.1 (Continued):MIL-C-85049/46Connector Accessories, Electrical, Strain Relief, 90°, Nonmetallic, Category4C (For MIL-C-27599 Series I and MIL-C-38999 Series I and II Connectors) MIL-C-85049/47Connector Accessories, Electrical, Strain Relief, 90°, Self-Locking andNonself-Locking, Category 4B (For MIL-C-38999 Series I and II Connectors) MIL-C-85049/48Connector Accessories, Electrical, Strain Relief, Straight, Category 4C (ForMIL-C-24308 Connectors)MIL-C-85049/49Connector Accessories, Electrical, Strain Relief, Straight, Self-Locking andNonself-Locking, Category 4B (For MIL-C-38999 Series I and II Connectors) MIL-C-85049/50Connector Accessories, Electrical, Strain Relief, 90°, Category 4C (ForMIL-C-24308 Connectors)MIL-C-85049/51Connector Accessories, Electrical, Strain Relief, Nonenvironmental, 90°, Self-Locking and Non-Self-Locking, Category 4B (For MIL-C-5015 Crimp,MIL-C-26482 Series 2, MIL-C-81703 Series 3, and MIL-C-83723 Series IIIConnectors)MIL-C-85049/52Connector Accessories, Electrical, Strain Relief, Nonenvironmental, Straight,Self-Locking and Non-Self-Locking, Category 4B (For MIL-C-5015 Crimp,MIL-C-26482 Series 2, MIL-C-81703 Series 3, and MIL-C-83723 Series IIIConnectors)MIL-C-85049/53Connector Accessories, Electrical, Strain Relief, Nonenvironmental, Straight,Category 4C (For MIL-C-5015 Crimp, MIL-C-26482 Series 2, MIL-C-81703Series 3, and MIL-C-83723 Series III Connectors) (Inactive for New Design.For New Design Use MIL-C-85049/52)MIL-C-85049/54Connector Accessories, Electrical, Strain Relief, Nonenvironmental, 45°,Category 4C (For MIL-C-5015 Crimp, MIL-C-26482 Series 2, MIL-C-81703Series 3, and MIL-C-83723 Series III Connectors) (Inactive for New Design.For New Design Use MIL-C-85049/43)MIL-C-85049/55Connector Accessories, Electrical, Strain Relief, Nonenvironmental, 90°, Self-Locking and Non-Self-Locking, Category 4C (For MIL-C-5015 Crimp,MIL-C-26482 Series 2, MIL-C-81703 Series 3, and MIL-C-83723 Series IIIConnectors) (Inactive for New Design. For New Design Use MIL-C-85049/55) MIL-C-85049/56Connector Accessories, Electrical, Strain Relief, Straight, Category 4C (ForMIL-C-38999 Series I and II Connectors)MIL-C-85049/57Connector Accessories, Electrical, Strain Relief, 45°, Self-Locking andNonself-Locking, Category 4C (For MIL-C-38999 Series I and II Connectors) MIL-C-85049/58Connector Accessories, Electrical, Ring, Potting Boot, Category 5 (ForMIL-C-38999 Series I and II Connectors)MIL-C-85049/59Connector Accessories, Electrical, Adapter, Shrink Boot, Category 5 (ForMIL-C-22992 Connectors, Classes C, J and R)MIL-C-85049/60Connector Accessories, Electrical, Adapter, Shrink Boot, Category 5 (ForMIL-C-5015 Crimp, MIL-C-26482 Series 2, MIL-C-81703 Series 3, andMIL-C-83723 Series III Connectors)MIL-C-85049/61Connector Accessories, Electrical, Ring, Potting Boot, Category 5 (ForMIL-C-27599 Connectors)MIL-C-85049/62Connector Accessories, Electrical, Adapter, Shrink Boot, Category 5 (ForMIL-C-38999 Series I and II Connectors)2.1.1 (Continued):MIL-C-85049/63Connector Accessories, Electrical, Strain Relief, 90°, Self-Locking andNonself-Locking, Category 4C (For MIL-C-38999 Series I and II Connectors) MIL-C-85049/64Connector Accessories, Electrical, Strain Relief, Split, Straight, Category 4C(For MIL-C-38999 Series I and II Connectors)MIL-C-85049/65Connector Accessories, Electrical, Strain Relief, Split 90°, Category 4C (ForMIL-C-38999 Series I and II Connectors)MIL-C-85049/69Connector Accessories, Electrical, Adapter, Shrink Boot, Category 5 (ForMIL-C-38999 Series III and IV Connectors)MIL-C-85049/74Connector Accessories, Electrical, Potting Boot, Category 7 (For Use WithMIL-C-85049/61 Potting Boot Ring)MIL-C-85049/75Connector Accessories, Electrical, Potting Boot, Category 7 (For Use WithMIL-C-85049/58 Potting Boot Ring)MIL-C-85049/76Connector Accessories, Electrical, Backshell, Environmental, 90°, ShieldTermination, Category 2B, Nonself-Locking (MIL-C-38999 Series I and IIConnectors)MIL-C-85049/77Connector Accessories, Electrical, Backshell, Environmental, 45°, ShieldTermination, Category 2B, Nonself-Locking (MIL-C-38999 Series I and IIConnectors)MIL-C-85049/78Connector Accessories, Electrical, Backshell, Environmental, 45°, ShieldTermination, Category 2B, Nonself-Locking (MIL-C-38999 Series III and IVConnectors)MIL-C-85049/79Connector Accessories, Electrical, Backshell, Environmental, 90°, ShieldTermination, Category 2B, Nonself-Locking (MIL-C-38999 Series III and IVConnectors)2.2Other publications:The following document(s) form a part of this specification to the extent specified herein. Unless otherwise specified, the issues of the documents which are Department of Defense (DOD) adopted shall be those listed in the issue of the DODISS specified in the solicitation. Unless otherwisespecified, the issues of documents not listed in the DODISS shall be the issue of the nongovernment documents which is current on the date of the solicitation.ASTMASTM D 4066Nylon, Injection and Extrusion Materials (PA)(Application for copies should be addressed to the American Society for Testing Materials,1916Race Street, Philadelphia, PA 19103.)SD-6Provisions Governing Qualification(Application for copies should be addressed to the Standardization Documents Order Desk, Building4D, 700 Robbins Avenue, Philadelphia, PA 19111-5094.)--| | | | | | | | | | | | | | | | | | | | | | | | | | | | | | | ---2.3Order of precedence:In the event of a conflict between the text of this specification and the references cited herein (except for associated detail specifications, specification sheets, or MS standards), the text of thisspecification shall take precedence. Nothing in this specification, however, shall supersedeapplicable laws and regulations unless a specific exemption has been obtained.3.REQUIREMENTS:3.1Specification sheets:The individual item requirements shall be as specified herein and in accordance with the applicable -- || | | | | || ||||| |||| || ||| || || | ||| |---specification sheet. In the event of any conflict between the requirements of this specification and the specification sheet, the latter shall govern.3.2Qualification:The connector accessories furnished under this specification shall be products which are authorized by the qualifying activity for listing on the applicable qualified products list at the time set for opening of bids (see 4.3 and 6.6).3.2.1Provisions governing qualification:The provisions governing qualification are specified in SD-6.3.2.2Reliability:The contractor’s reliability program for assembled connector accessories andassembly procedures shall meet the requirements of MIL-STD-790.3.3Materials:Materials shall be suitable for the purpose intended and as specified (see 3.1), however, when a definite material is not specified, a material shall be used which will enable the connector accessory to meet the performance requirements of this specification. Acceptance or approval of anyconstituent material shall not be construed as a guarantee for acceptance of the finished product.3.3.1Corrosion resisting steel:Where applicable, corrosion resisting steel shall be 300 series, inaccordance with QQ-S-763.3.3.2Composite:Corrosion resistant, high performance resins with or without filler materials. Theresins must be defined by specifications listed in the DODISS or published by professionalmaterials associations. Exceptions may be granted by the preparing activity.3.3.3Aluminum:Aluminum alloy shall be in accordance with QQ-A-225, QQ-A-250, QQ-A-591, orQQ-A-601.3.3.4Elastomers:Unless otherwise specified (see 3.1), elastomers shall be silicone or fluorosilicone.Connector accessories which utilize elastomers shall meet the fluid immersion requirements (see3.5.12).3.3.5Nylon:Nylon shall be in accordance with ASTM D 4066, shall be fungus inert in accordance withRequirement 4 of MIL-STD-454 (see 4.6.14), shall be self-extinguishing in accordance withMIL-STD-454, Requirement 3, and shall be non-toxic.3.3.6Dissimilar metals:When dissimilar metals are employed in intimate contact with each other,suitable protection against electrolytic corrosion shall be provided as specified inMIL-STD-454, Requirement 16.3.3.7Finish:Finish for aluminum connector accessories shall be as follows:A -Black Anodize - In accordance with Class 2 of MIL-A-8625, Type II.N -Electroless Nickel - In accordance with MIL-C-26074, Class 3 or 4, Grade B. Restricted to space applications only.1/W -Cadmium - Olive drab over suitable underplate, 1000 hour salt spray (see 3.5.3).1/W is not for use in space application.Finish for corrosion resisting steel accessories shall be as follows:B -Black Cadmium - In accordance with QQ-P-416, Type II, Class 3.S -Passivate - In accordance with QQ-P-35.Finish for composite accessories shall be as follows:J -Olive drab cadmium plate in accordance with QQ-P-416 over a suitable underplate to withstand 2000 hour salt spray (see 3.5.3). Final finish shall be electrically conductive.M -Electrically conductive electroless nickel plating. Finish shall withstand 2000 hour salt spray (see 3.5.3). Use of a suitable underplate is permissible.3.4Design and construction:Connector accessories shall be designed and constructed to withstand normal handling incident to installation and maintenance in service.3.4.1Configuration:The configuration and dimensions of connector accessories shall be as specified(see 3.1).--| | | | | | | | | | | | | | | | | | | | | | | | | | | | | | | ---3.4.2Screw threads:English unit screw threads intended to mate with connectors, unless otherwisespecified, shall be unified 2A or 2B, conforming to MIL-S-7742. Metric unit screw threads intended to mate with connectors shall be in accordance with FED-STD-H28. Screw threads shall bechecked after plating by means of ring and plug gages only, in accordance with FED-STD-H28.Out of roundness is not objectionable if the threads can be checked without forcing the threadgage.3.4.3Safety wiring:When specified threaded coupling connector interfaces shall be designed for safetywiring. A minimum of two holes shall be provided for shell size 14 or smaller, and at least three equally spaced holes for sizes 16 and larger. Holes shall be of a diameter sufficient toaccommodate .020 inch wire. For non-self-locking accessories safety wire holes shall not beoptional. Self-locking accessories shall not have safety wire holes on the coupling nut.3.4.4Interchangeability:All connector accessories having the same military part number shall becompletely interchangeable with each other with respect to installation and performance asspecified herein.3.4.5Intermateability:Unless otherwise specified (see 3.1), the intermateability control dimensions forthe threaded mating end of the connector accessories shall conform to the interface dimensions specified in Figures 2 - 4 and Tables VIII - X.3.4.6Spin coupling:Unless otherwise specified (see 3.1), for all circular connector accessoryapplications the coupling nut shall have spin coupling. The coupling nut shall be captivated to, and free to rotate on, the follower of the circular connector accessory. Unless otherwise specified (see3.1), the spin coupling nut will be either non-self-locking or self-locking. The self-locking couplingdevices may exhibit some mechanical resistance while captivated to the follower.3.4.6.1Self-locking devices:The self-locking devices within the coupling nut shall be a corrosion-resistant material and shall provide a positive detent. Couplings with self-locking devices shallmeet all the performance requirements specified herein for the accessories specific category. 3.4.7Dummy connector test fixture:When specified for applicable tests in this specification, a dummyconnector test fixture which duplicates the connector interfacing features may be used in place of the applicable connector. The dummy connector test fixture material shall be aluminum alloy in accordance with 3.3.2 for aluminum connector accessory testing and corrosion resistant steel in accordance with 3.3.1 for corrosion resistant steel connector accessory testing. The dummyconnector test fixture shall have the same plating as the connector accessory being tested. The dummy connector test fixture configuration and dimensions for MIL-C-38999 Series I and IIconnectors; for MIL-C-38999 Series III and IV connectors; and MIL-C-5015 crimp, MIL-C-26482 Series 2, MIL-C-81703 Series 3, and MIL-C-83723 Series III are defined in Figures 5 - 7 and Table XI - XIV, respectively.--| | | | | | | | | | | | | | | | | | | | | | | | | | | | | | | ---3.4.7.1Dummy connector test plug:When specified for applicable tests in this specification, a dummycable test plug made of metal core and coated with neoprene, polychloroprene or fluorocarbonpolymer. The test plug diameter shall be equal or not more than 0.016 (.406 mm) smaller thanthe minimum cable sealing diameter being tested.3.5Performance requirements:Connector accessories shall meet the performance requirements specified herein when tested in accordance with the specified methods of Section 4.3.5.1Magnetic permeability:When tested as specified in4.6.2, the relative permeability of theconnector accessory shall be less than 2.0 for aluminum accessories and 5.0 for stainless steel. 3.5.2Shell conductivity:When tested as specified in 4.6.3, the counterpart connector and connectoraccessory assembly shall be electrically conductive. The overall resistance shall not exceed 0.025 ohms for aluminum connector accessories and 0.05 ohms for stainless steel connectoraccessories.3.5.3Salt spray (corrosion):When tested as specified in4.6.4, connector accessories shall show noexposure of basis material due to corrosion, which could affect performance. For finish J, after 500 hours salt spray, inspect connector accessories for cadmium (inspection method optional). Nounderplate or basis material shall be exposed. Return to chamber for completion of test.3.5.4Vibration:When tested as specified in4.6.5, connector accessories shall not be damaged, norshall there be any loosening of parts during vibration. Monitoring for electrical conductivity shall not be utilized for pass fail criteria.3.5.5Shock:When tested as specified in4.6.6, connector accessories shall not be damaged, nor shallthere be any loosening of parts during exposure to shock.3.5.6Humidity (category 2):After being subjected to the humidity test specified in4.6.7, connectoraccessories mated to counterpart connectors (or dummy connectors, see 3.4.7) shall be examined and there shall be no evidence of water entrance.3.5.7Water pressure (categories 1 and 8A only):After being subjected to the test specified in4.6.8,connector accessories shall be examined and shall show no evidence of internal water entrance.3.5.8Cable pullout:When tested as specified in4.6.9, the test plug shall not pull out nor shall slippageexceed .125 inch. The cable pullout requirement is not applicable to categories 1C, 2C, 3C and 4C.--| | | | | | | | | | | | | | | | | | | | | | | | | | | | | | | ---。
STA800 SmartLine绝对压力变送器产品说明书
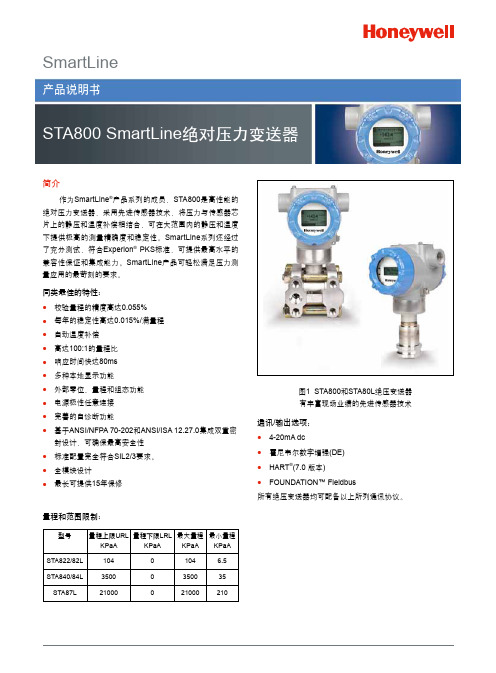
SmartLine简介作为SmartLine ®产品系列的成员,STA800是高性能的绝对压力变送器,采用先进传感器技术,将压力与传感器芯片上的静压和温度补偿相结合,可在大范围内的静压和温度下提供极高的测量精确度和稳定性。
SmartLine 系列还经过了充分测试,符合Experion ® PKS 标准,可提供最高水平的兼容性保证和集成能力。
SmartLine 产品可轻松满足压力测量应用的最苛刻的要求。
同类最佳的特性:● 校验量程的精度高达0.055%● 每年的稳定性高达0.015%/满量程● 自动温度补偿● 高达100:1的量程比● 响应时间快达80ms ● 多种本地显示功能● 外部零位、量程和组态功能● 电源极性任意连接● 完善的自诊断功能●基于ANSI/NFPA 70-202和ANSI/ISA 12.27.0集成双重密封设计,可确保最高安全性● 标准配置完全符合SIL2/3要求。
● 全模块设计●最长可提供15年保修量程和范围限制:型号量程上限URL KPaA 量程下限LRL KPaA 最大量程KPaA 最小量程KPaASTA822/82L 1040 104 6.5 STA840/84L 35000 350035STA87L2100021000210图1 STA800和STA80L 绝压变送器有丰富现场业绩的先进传感器技术通讯/输出选项:●4-20mA dc●霍尼韦尔数字增强(DE)●HART ®(7.0 版本)●FOUNDATION™ Fieldbus所有绝压变送器均可配备以上所列通讯协议。
描述SmartLine系列的压力变送器均基于高性能的传感器设计。
这一个传感器实际集成了多个传感器,将过程压力测量与静态压力(DP型号)及温度补偿测量相结合,从而实现了最佳的总体性能。
这一性能使得SmartLine成为几乎可以替代任何现有变送器的竞争产品。
独特的显示表头选项SmartLine的模块化设计,可采用基本型字母数字LCD 显示表头,或者带有独特的无与伦比的高级图形LCD显示表头。
PCF8591中文数据手册

PCF8591 8位A/D和D/A转换器1、特性单电源供电工作电压:2.5 V ~ 6 V待机电流低✍ I2C总线串行输入/输出通过3个硬件地址引脚编址采样速率取决于I2C总线速度✍ 4个模拟输入可编程为单端或差分输入自动增量通道选择模拟电压范围:VSS~VDD片上跟踪与保持电路✍ 8位逐次逼近式A/D转换带一个模拟输出的乘法DAC 2、应用闭环控制系统用于远程数据采集的低功耗转换器电池供电设备在汽车、音响和TV应用方面的模拟数据采集3、概述PCF8591是单片、单电源低功耗8位CMOS数据采集器件,具有4个模拟输入、一个输出和一个串行I2C总线接口。
3个地址引脚A0、A1和A2用于编程硬件地址,允许将最多8个器件连接至I2C总线而不需要额外硬件。
器件的地址、控制和数据通过两线双向I2C总线传输。
器件功能包括多路复用模拟输入、片上跟踪和保持功能、8位模数转换和8位数模拟转换。
最大转换速率取决于I2C总线的最高速率。
4、订货信息5、内部框图图 1 内部框图6、引脚图2 引脚图(DIP16).7、功能描述7.1 地址I2C总线系统中的每一片PCF8591通过发送有效地址到该器件来激活。
该地址包括固定部分和可编程部分。
可编程部分必须根据地址引脚A0、A1和A2来设置。
在I2C总线协议中地址必须是起始条件后作为第一个字节发送。
地址字节的最后一位是用于设置以后数据传输方向的读/写位。
(见图4、16、17)图4 地址7.2 控制字发送到PCF8591的第二个字节将被存储在控制寄存器,用于控制器件功能。
控制寄存器的高半字节用于允许模拟输出,和将模拟输入编程为单端或差分输入。
低半字节选择一个由高半字节定义的模拟输入通道(见图5)。
如果自动增量(auto-increment)标志置1,每次A/D转换后通道号将自动增加。
如果自动增量(auto-increment)模式是使用内部振荡器的应用中所需要的,那么控制字中模拟输出允许标志应置1。
施耐德 A9D93610 A9 SLIM 4.5kA 10A TypeA 数据表

Product data sheetCharacteristicsA9D93610A9 SLIM 4.5kA 10A TypeA主要信息断路器应用配电保护产品系列Acti 9产品类型剩余电流动作保护断路器产品短名iDPNa Vigi+极数1P + N 中性线位置左侧保护极数量1额定电流 [In]10 A 电网类型AC 脱扣曲线C 剩余电流灵敏度 [IΔn]30 MA 漏电流保护等级A类分断能力4500 A Icn 隔离功能适用补充信息配电系统位置下游配电出线电网频率50 Hz 额定工作电压 [Ue]230 V AC 50 Hz 磁脱扣限制5...10 x In 额定绝缘电压 [Ui]400 V 额定冲击耐受电压 [Uimp]4 KV 触点位置指示有控制类型手柄本地信号指示开/关指示安装方式DIN 导轨安装宽度 (9mm的倍数)2高度96.1 Mm 宽度18 Mm 深度65.8 Mm 净重136 Kg 机械寿命20000 次电气寿命10000 次接线能力隧道式端子 (上接线) - <= 16 mm² - 单股硬线 不带接线端子 隧道式端子 (下接线) - <= 10 mm² - 单股硬线 不带接线端子紧固扭矩电源回路: 2.5 N.m 上接线 电源回路: 2 N.m 下接线环境符合标准GB/T 16917.1 GB/T 16917.22 EN/IEC 61009-1产品认证CCCIP 保护等级IP20IP40抗湿热性2相对湿度95 % 在…上 55 °C运行温度-25…55 °C贮存环境温度-30…70 °CT h e i n f o r m a t i o n p r o v i d e d i n t h i s d o c u m e n t a t i o n c o n t a i n s g e n e r a l d e s c r i p t i o n s a n d /o r t e c h n i c a l c h a r a c t e r i s t i c s o f t h e p e r f o r m a n c e o f t h e p r o d u c t s c o n t a i n e d h e r e i n .T h i s d o c u m e n t a t i o n i s n o t i n t e n d e d a s a s u b s t i t u t e f o r a n d i s n o t t o b e u s e d f o r d e t e r m i n i n g s u i t a b i l i t y o r r e l i a b i l i t y o f t h e s e p r o d u c t s f o r s p e c i f i c u s e r a p p l i c a t i o n s .I t i s t h e d u t y o f a n y s u c h u s e r o r i n t e g r a t o r t o p e r f o r m t h e a p p r o p r i a t e a n d c o m p l e t e r i s k a n a l y s i s , e v a l u a t i o n a n d t e s t i n g o f t h e p r o d u c t s w i t h r e s p e c t t o t h e r e l e v a n t s p e c i f i c a p p l i c a t i o n o r u s e t h e r e o f .N e i t h e r S c h n e i d e r E l e c t r i c I n d u s t r i e s S A S n o r a n y o f i t s a f f i l i a t e s o r s u b s i d i a r i e s s h a l l b e r e s p o n s i b l e o r l i a b l e f o r m i s u s e o f t h e i n f o r m a t i o n c o n t a i n e d h e r e i n .包装单位Unit Type of Package 1PCENumber of Units in Package 11Package 1 Height9.61 CmPackage 1 Width 1.8 CmPackage 1 Length 6.58 CmPackage 1 Weight125 GUnit Type of Package 2BB1Number of Units in Package 212Package 2 Height7.8 CmPackage 2 Width9.5 CmPackage 2 Length21.8 CmPackage 2 Weight 1.548 KgUnit Type of Package 3CARNumber of Units in Package 372Package 3 Height20 CmPackage 3 Width27.8 CmPackage 3 Length37.6 CmPackage 3 Weight9.831 Kg可持续性产品类型Green Premium 产品REACh法规REACh 声明欧盟ROHS指令符合豁免条件Mercury free支持可持续的包装YesRoHS exemption information支持中国 ROHS 管理办法中国 ROHS 声明环境披露产品环境文件流通资料无需具体的回收操作合同保修保修单18 个月Product Life Status :Commercialised。
ADCLK948BCPZ-REEL7 产品说明书
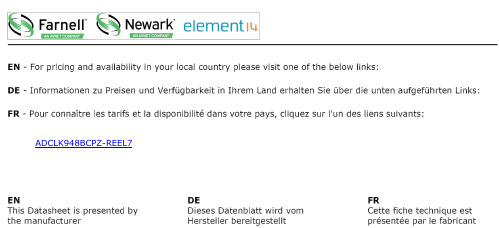
ADCLK948BCPZ-REEL7Two Selectable Inputs, 8 LVPECL Outputs,SiGe Clock Fanout Buffer Data Sheet ADCLK948Rev. B Document FeedbackInformation furnished by Analog Devices is believed to be accurate and reliable. However, noresponsibility is assumed by Analog Devices for its use, nor for any infringements of patents or other rights of third parties that may result from its use. Specifications subject to change without notice. No license is granted by implication or otherwise under any patent or patent rights of Analog Devices. T rademarks and registered trademarks are the property of their respective owners. One Technology Way, P.O. Box 9106, N orwood, MA 02062-9106, U.S.A. Tel: 781.329.4700 ©2009–2016 Analog Devices, Inc. All rights reserved. Technical Support FEATURES2 selectable differential inputs4.8 GHz operating frequency75 fs rms broadband random jitterOn-chip input terminations3.3 V power supplyAPPLICATIONSLow jitter clock distributionClock and data signal restorationLevel translationWireless communicationsWired communicationsMedical and industrial imagingATE and high performance instrumentationGENERAL DESCRIPTIONThe ADCLK948 is an ultrafast clock fanout buffer fabricated on the Analog Devices, Inc., proprietary XFCB3 silicon germanium (SiGe) bipolar process. This device is designed for high speed applications requiring low jitter.The device has two selectable differential inputs via the IN_SEL control pin. Both inputs are equipped with center tapped, differential, 100 Ω on-chip termination resistors. The inputs accept dc-coupled LVPECL, CML, 3.3 V CMOS (single-ended), and ac-coupled 1.8 V CMOS, LVDS, and LVPECL inputs. AV REF x pin is available for biasing ac-coupled inputs.The ADCLK948 features eight full-swing emitter coupled logic (ECL) output drivers. For LVPECL (positive ECL) operation, bias V CC to the positive supply and V EE to ground. For ECL operation, bias V CC to ground and V EE to the negative supply. The output stages are designed to directly drive 800 mV each side into 50 Ω terminated to V CC − 2 V for a total differential output swing of 1.6 V.The ADCLK948 is available in a 32-lead LFCSP and specified for operation over the standard industrial temperature range of −40°C to +85°C. FUNCTIONAL BLOCK DIAGRAM828-1Figure 1.ADCLK948Data SheetRev. B | Page 2 of 12TABLE OF CONTENTSFeatures .............................................................................................. 1 Applications ....................................................................................... 1 General Description ......................................................................... 1 Functional Block Diagram .............................................................. 1 Revision History ............................................................................... 2 Specifications ..................................................................................... 3 Electrical Characteristics ............................................................. 3 Absolute Maximum Ratings ............................................................ 5 Determining Junction Temperature .......................................... 5 ESD Caution .................................................................................. 5 Thermal Performance .................................................................. 5 Pin Configuration and Function Descriptions ..............................6 Typical Performance Characteristics ..............................................7 Functional Description .....................................................................9 Clock Inputs ...................................................................................9 Clock Outputs ................................................................................9 Clock Input Select (IN_SEL) Settings...................................... 10 PCB Layout Considerations ...................................................... 10 Input Termination Options ....................................................... 11 Outline Dimensions ....................................................................... 12 Ordering Guide .. (12)REVISION HISTORY8/2016—Rev. A to Rev. BChanged CP-32-8 to CP-32-21 .................................... Throughout Changes to Figure 2 and Table 7 ..................................................... 6 Updated Outline Dimensions ....................................................... 12 Changes to Ordering Guide . (12)6/2010—Rev. 0 to Rev. AChanged Output Voltage Differential Parameter to OutputVoltage, Single Ended Parameter, Table 1 ..................................... 3 Changes to Output Voltage, Single Ended Parameter, Table 1 (3)7/2009—Revision 0: Initial VersionData SheetADCLK948Rev. B | Page 3 of 12SPECIFICATIONSELECTRICAL CHARACTERISTICSTypical (Typ column) values are given for V CC − V EE = 3.3 V and T A = 25°C, unless otherwise noted. Minimum (Min column) and maximum (Max column) values are given over the full V CC − V EE = 3.3 V ± 10% and T A = −40°C to +85°C variation, unless otherwise noted. Table 1. Clock Inputs and OutputsParameterSymbol Min Typ Max Unit Test Conditions/Comments DC INPUT CHARACTERISTICSInput Common Mode Voltage V ICM V EE + 1.5 V CC − 0.1 VInput Differential Range V ID 0.4 3.4 V p-p ±1.7 V between input pins Input Capacitance C IN 0.4 pF Input ResistanceSingle-Ended Mode 50 Ω Differential Mode 100 ΩCommon Mode 50 kΩ Open V T x Input Bias Current 20 µA Hysteresis10 mV DC OUTPUT CHARACTERISTICSOutput Voltage High Level V OH V CC − 1.26 V CC − 0.76 V 50 Ω to (V CC − 2.0 V) Output Voltage Low Level V OL V CC − 1.99 V CC − 1.54 V 50 Ω to (V CC − 2.0 V) Output Voltage, Single Ended V O 610 960 mV V OH − V OL , output static Reference Voltage V REFOutput Voltage (V CC + 1)/2 V −500 µA to +500 µA Output Resistance235ΩTable 2. Timing CharacteristicsParameterSymbol Min Typ Max Unit Test Conditions/Comments AC PERFORMANCEMaximum Output Frequency 4.5 4.8 GHz See Figure 4 for differential output voltage vs. frequency, >0.8 V differential output swing Output Rise Time t R 40 75 90 ps 20% to 80% measured differentially Output Fall Time t F 40 75 90 psPropagation Delayt PD 175 210 245 ps V ICM = 2 V, V ID = 1.6 V p-p Temperature Coefficient 50 fs/°C Output-to-Output Skew 1 9 25 psPart-to-Part Skew 45 ps V ID = 1.6 V p-p Additive Time JitterIntegrated Random Jitter 28 fs rms BW = 12 kHz − 20 MHz, CLK = 1 GHz Broadband Random Jitter 2 75 fs rms V ID = 1.6 V p-p, 8 V/ns, V ICM = 2 V Crosstalk-Induced Jitter 3 90 fs rms CLOCK OUTPUT PHASE NOISEAbsolute Phase NoiseInput slew rate > 1 V/ns (see Figure 11, the phase noise plot, for more details) f IN = 1 GHz −119 dBc/Hz @100 Hz offset −134 dBc/Hz @1 kHz offset −145 dBc/Hz @10 kHz offset −150 dBc/Hz @100 kHz offset−150dBc/Hz >1 MHz offset1 The output skew is the difference between any two similar delay paths while operating at the same voltage and temperature. 2Measured at the rising edge of the clock signal; calculated using the SNR of the ADC method. 3This is the amount of added jitter measured at the output while two related, asynchronous, differential frequencies are applied to the inputs.ADCLK948Data SheetRev. B | Page 4 of 12Table 3. Input Select Control PinParameter Symbol Min Typ Max Unit Logic 1 Voltage V IH V CC − 0.4 V CC V Logic 0 Voltage V IL V EE 1 V Logic 1 Current I IH 100 μA Logic 0 Current I IL 0.6 mA Capacitance2pFTable 4. PowerParameter Symbol Min Typ Max Unit Test Conditions/Comments POWER SUPPLYSupply Voltage Requirement V CC − V EE 2.97 3.63 V 3.3 V + 10% Power Supply CurrentStaticNegative Supply Current I VEE 96 120 mA V CC − V EE = 3.3 V ± 10% Positive Supply Current I VCC 288 330 mA V CC − V EE = 3.3 V ± 10% Power Supply Rejection 1PSR VCC <3 ps/V V CC − V EE = 3.3 V ± 10% Output Swing Supply Rejection 2PSR VCC28 dBV CC − V EE = 3.3 V ± 10%1 Change in t PD per change in V CC .2Change in output swing per change in V CC .Data SheetADCLK948Rev. B | Page 5 of 12ABSOLUTE MAXIMUM RATINGSStresses at or above those listed under Absolute Maximum Ratings may cause permanent damage to the product. This is a stress rating only; functional operation of the product at these or any other conditions above those indicated in the operational section of this specification is not implied. Operation beyond the maximum operating conditions for extended periods may affect product reliability.DETERMINING JUNCTION TEMPERATURETo determine the junction temperature on the application printed circuit board (PCB), use the following equation:T J = T CASE + (ΨJT × P D )where:T J is the junction temperature (°C).T CASE is the case temperature (°C) measured by the customer at the top center of the package. ΨJT is from Table 6.P D is the power dissipation.Values of θJA are provided for package comparison and PCB design considerations. θJA can be used for a first-order approxi-mation of T J by the equationT J = T A + (θJA × P D )where T A is the ambient temperature (°C).Values of θJB are provided in Table 6 for package comparison and PCB design considerations.ESD CAUTIONTHERMAL PERFORMANCETable 6.ParameterSymbol Description Value 1 Unit Junction-to-Ambient Thermal Resistance θJAStill AirPer JEDEC JESD51-20 m/sec Air Flow49.8 °C/W Moving AirθJMA Per JEDEC JESD51-61 m/sec Air Flow 43.5 °C/W 2.5 m/sec Air Flow39.0 °C/W Junction-to-Board Thermal Resistance θJBMoving AirPer JEDEC JESD51-81 m/sec Air Flow30.7 °C/W Junction-to-Case Thermal Resistance θJCMoving AirPer MIL-STD 883, Method 1012.1Die-to-Heatsink8.8 °C/W Junction-to-Top-of-Package Characterization Parameter ΨJTStill AirPer JEDEC JESD51-20 m/sec Air Flow0.7 °C/W1Results are from simulations. The PCB is a JEDEC multilayer type. Thermal performance for actual applications requires careful inspection of the conditions in the application to determine if they are similar to those assumed in these calculations.ADCLK948Data SheetRev. B | Page 6 of 12PIN CONFIGURATION AND FUNCTION DESCRIPTIONSNOTES1. NC = NO CONNECT.2. THE EPAD MUST BE SOLDERED TO THE V EE POWER PLANE.CLK0CLK0V REF 0V T 0CLK1CLK1V T 1V REF 1Q2Q2Q3Q3Q4Q4Q5Q5N C V C CQ 7Q 7Q 6Q 6V C CV C CI N _S E L V C CQ 0Q 0Q 1Q 1V C CV C C11111112109876508280-002Figure 2. Pin ConfigurationData SheetADCLK948Rev. B | Page 7 of 12TYPICAL PERFORMANCE CHARACTERISTICSV CC = 3.3 V , V EE = 0 V , V ICM = V REF x , T A = 25°C, clock outputs terminated at 50 Ω to V CC − 2 V , unless otherwise noted.08280-003Figure 3. LVPECL Output Waveform @ 200 MHz1.80.40.50.60.70.80.91.01.11.21.31.41.51.61.7010002000300040005000D I F F E R E N T I A L O U T P U T V O L T A G E (V )FREQUENCY (MHz)08280-004Figure 4. Differential Output Voltage vs. Frequency, V ID > 1.1 V p-p2251801851901952002052102152200 1.81.61.41.21.00.80.60.40.2P R O P A G A T I O N D E L A Y (p s )DIFFERENTIAL INPUT VOLTAGE SWING (V)08280-005Figure 5. Propagation Delay vs. Differential Input Voltage08280-006Figure 6. LVPECL Output Waveform @ 1000 MHz214213212211************–40806040200–20P R O P A G A T I O N D E L A Y (p s )TEMPERATURE (°C)08280-007Figure 7. Propagation Delay vs. Temperature, V ID = 1.6 V p-p2301902002102200.93.12.92.72.52.32.11.91.71.51.31.1P R O P A G A T I O N D E L A Y (p s )DC COMMON-MODE VOLTAGE (V)08280-008Figure 8. Propagation Delay vs. DC Common-Mode Voltage vs. Temperature,Input Slew Rate > 25 V/nsADCLK948Data SheetRev. B | Page 8 of 121.561.541.521.501.481.461.441.422.752.85 2.953.05 3.15 3.25 3.35 3.45 3.55 3.65 3.75D I F FE R E N T I A L O U T P U T V O L T A G E S W I N G (V )POWER SUPPLY (V)08280-009Figure 9. Differential Output Voltage Swing vs. Power Supply Voltage vs.Temperature, V ID = 1.6 V p-p08280-0103503002502001501005002.753.753.503.253.00S U P P L Y C U R R E N T (m A )SUPPLY VOLTAGE (V)Figure 10. Power Supply Current vs. Power Supply Voltage vs. Temperature,All Outputs Loaded (50 Ω to V CC − 2 V).–90–170–160–150–140–130–120–110–100101001k10k100k1M10M100MP H A S E N O I S E (d B c /H z )FREQUENCY OFFSET (Hz)08280-011Figure 11. Absolute Phase Noise Measured @1 GHz300250200150100500252015105R A N D O M J I T T E R (fS r m s )INPUT SLEW RATE (V/ns)08280-012Figure 12. RMS Random Jitter vs. Input Slew Rate, V ID MethodData SheetADCLK948Rev. B | Page 9 of 12FUNCTIONAL DESCRIPTIONCLOCK INPUTSThe ADCLK948 accepts a differential clock input from one of two inputs and distributes the selected clock to all eight LVPECL outputs. The maximum specified frequency is the point at which the output voltage swing is 50% of the standard LVPECL swing (see Figure 4). See the functional block diagram (Figure 1) and the General Description section for more clock input details. See Figure 19 through Figure 23 for various clock input termination schemes.Output jitter performance is degraded by an input slew rate below 4 V/ns, as shown in Figure 12. The ADCLK948 is specifically designed to minimize added random jitter over a wide input slew rate range. Whenever possible, clamp excessively large input signals with fast Schottky diodes because attenuators reduce the slew rate. Input signal runs of more than a few centimeters should be over low loss dielectrics or cables with good high frequency characteristics.CLOCK OUTPUTSThe specified performance necessitates using proper transmission line terminations. The LVPECL outputs of the ADCLK948 are designed to directly drive 800 mV into a 50 Ω cable or into microstrip/stripline transmission lines terminated with 50 Ω referenced to V CC − 2 V , as shown in Figure 14. The LVPECL output stage is shown in Figure 13. The outputs are designed for best transmission line matching. If high speed signals must be routed more than a centimeter, either the microstrip or the stripline technique is required to ensure proper transition times and to prevent excessive output ringing and pulse width depen-dent propagation delay dispersion.V EE Qx Qx08280-013Figure 13. Simplified Schematic Diagram of the LVPECL Output StageFigure 14 through Figure 17 depict various LVPECL output termination schemes. When dc-coupled, V S of the receiving buffer should match VS_DRV .Thevenin-equivalent termination uses a resistor network to provide 50 Ω termination to a dc voltage that is below V OL of the LVPECL driver. In this case, VS_DRV on the ADCLK948 should equal V S of the receiving buffer. Although the resistor combination shown (in Figure 15) results in a dc bias point of VS_DRV − 2 V , the actual common-mode voltage is VS_DRV − 1.3 V because there is additional current flowing from the ADCLK948 LVPECL driver through the pull-down resistor. LVPECL Y-termination is an elegant termination scheme that uses the fewest components and offers both odd- and even-mode impedance matching. Even-mode impedance matching is an important consideration for closely coupled transmission lines at high frequencies. Its main drawback is that it offers limited flexibility for varying the drive strength of the emitter follower LVPECL driver. This can be an important consideration when driving long trace lengths but is usually not an issue.08280-014Figure 14. DC-Coupled, 3.3 V LVPECL08280-015Figure 15. DC-Coupled, 3.3 V LVPECL Far-End Thevenin Termination08280-016Figure 16. DC-Coupled, 3.3 V LVPECL Y-Termination08280-017Figure 17. AC-Coupled, LVPECL with Parallel Transmission LineADCLK948Data SheetRev. B | Page 10 of 12CLOCK INPUT SELECT (IN_SEL) SETTINGSA Logic 0 on the IN_SEL pin selects the Input CLK0 andInput CLK0. A Logic 1 on the IN_SEL pin selects Input CLK1 and Input CLK1.PCB LAYOUT CONSIDERATIONSThe ADCLK948 buffer is designed for very high speed applica-tions. Consequently, high speed design techniques must be used to achieve the specified performance. It is critically important to use low impedance supply planes for both the negative supply (V EE ) and the positive supply (V CC ) planes as part of a multilayer board. Providing the lowest inductance return path for switching currents ensures the best possible performance in the target application.The following references to the GND plane assume that the V EE power plane is grounded for LVPECL operation. Note that, for ECL operation, the V CC power plane becomes the ground plane. It is also important to adequately bypass the input and output supplies. Place a 1 µF electrolytic bypass capacitor within several inches of each V CC power supply pin to the GND plane. In addition, place multiple high quality 0.001 µF bypass capacitors as close as possible to each of the V CC supply pins, and connect the capacitors to the GND plane with redundant vias. Carefully select high frequency bypass capacitors for minimum induc-tance and ESR. To improve the effectiveness of the bypass at high frequencies, minimize parasitic layout inductance. Also, avoid discontinuities along input and output transmission lines that can affect jitter performance.In a 50 Ω environment, input and output matching have a significant impact on performance. The buffer provides internal 50 Ωtermination resistors for both CLKx and CLKx inputs. Normally, the return side is connected to the reference pin that is provided. Carefully bypass the termination potential using ceramic capacitors to prevent undesired aberrations on the input signal due to parasitic inductance in the termination return path. If the inputs are dc-coupled to a source, take care to ensure that the pins are within the rated input differential and common-mode ranges. If the return is floated, the device exhibits a 100 Ω cross termi-nation, but the source must then control the common-mode voltage and supply the input bias currents.There are ESD/clamp diodes between the input pins to prevent the application from developing excessive offsets to the input transistors. ESD diodes are not optimized for best ac perfor-mance. When a clamp is required, it is recommended thatappropriate external diodes be used.Exposed Metal PaddleThe exposed metal paddle on the ADCLK948 package is both an electrical connection and a thermal enhancement. For the device to function properly, the paddle must be properly attached to the V EE power plane.When properly mounted, the ADCLK948 also dissipates heat through its exposed paddle. The PCB acts as a heat sink for the ADCLK948. The PCB attachment must provide a good thermal path to a larger heat dissipation area. This requires a grid of vias from the top layer down to the V EE power plane (see Figure 18). The ADCLK948 evaluation board (ADCLK948/PCBZ) pro-vides an example of how to attach the part to the PCB.VIAS TO V EE POWERPLANE08280-018Figure 18. PCB Land for Attaching Exposed PaddleData SheetADCLK948Rev. B | Page 11 of 12INPUT TERMINATION OPTIONSCONNECT V T x TO V CC .08280-019Figure 19. DC-Coupled CML Input TerminationV 08280-0200.01µF(OPTIONAL)50Figure 20. DC-Coupled LVPECL Input Termination CONNECT V T x TO V REF x.08280-021Figure 21. AC-Coupled Input Termination, Such as LVDS and LEVPECLCONNECT V T x, V REF x, AND CLKx. PLACE A BYPASS CAPACITOR FROM V T x TO GROUND.ALTERNATIVELY, V T x, V REF x, AND CLKx CAN BE CONNECTED, GIVING A CLEANER LAYOUT ANDA 180º PHASE SHIFT.08280-022Figure 22. AC-Coupled Single-Ended Input Termination08280-023Figure 23. DC-Coupled 3.3 V CMOS Input TerminationADCLK948Data SheetRev. B | Page 12 of 12OUTLINE DIMENSIONS0.080.800.75THE EXPOSED PAD, REFER TO THE PIN CONFIGURATION AND FUNCTION DESCRIPTIONSSECTION OF THIS DATA SHEET.COMPLIANT TO JEDEC STANDARDS MO-220-WHHD-2.08-22-2013-A00Figure 24. 32-Lead Lead Frame Chip Scale Package [LFCSP]5 mm × 5 mm Body and 0.75 mm Package Height(CP-32-21)Dimensions shown in millimetersORDERING GUIDEModel 1Temperature Range Package DescriptionPackage Option ADCLK948BCPZ−40°C to +85°C 32-Lead Lead Frame Chip Scale Package [LFCSP] CP-32-21 ADCLK948BCPZ-REEL7 −40°C to +85°C 32-Lead Lead Frame Chip Scale Package [LFCSP] CP-32-21 ADCLK948/PCBZEvaluation Board1Z = RoHS Compliant Part.©2009–2016 Analog Devices, Inc. All rights reserved. Trademarks and registered trademarks are the property of their respective owners. D08280-0-8/16(B)ADCLK948BCPZ-REEL7。
DS9481R USB-到-1-Wire适配器商品说明书

General DescriptionThe DS9481R is a USB-to-1-Wire ® adapter for easy PC connectivity to 1-Wire devices. The adapter provides an RJ11 connector with the signals to communicate with all 1-Wire and iButton ® devices that support a 3.3V data I/O level. Additionally, the adapter provides the support and signaling to program 1-Wire/iButton EEPROM and one-time programmable (OTP)/EPROM devices. To provide a total hardware solution, the DS9481R can readily be used with the DS9120 socket adapter to create a 1-Wire PC programmer for 1-Wire peripheral devices (contact factory for more information). The equivalent peripheral hardware solution for the iButton is the DS1402D-DR8.Features●Driver Support for Windows ® 11 and Windows 10Operating Systems●Enumerates as a Virtual PC COM Port by Use of theProlific PL-2303GC USB-to-UART Bridge IC ●Emulates the DS2480B 1-Wire Line DrivingFunctionality●1-Wire OTP/EPROM Programming Provided Withoutthe Need of an External Power Supply (12V on OW,7V on PULSE)● 3.3V Read/Write Operation to 1-Wire/iButton Devices ●RJ11 Interface for Standard Connectivity Accessoriessuch as the DS9120 Socket Adapter●Supports Standard and Overdrive 1-WireCommunication●Provides Strong Pullup to 3.3V●Fully Compliant with USB 2.0 SpecificationDS9481R USB-to-1-Wire/iButton Adapter19-5608; Rev 1; 3/23Ordering Information+Denotes lead(Pb)-free and RoHS compliant.Adapter Contents1-Wire and iButton are registered trademarks of Maxim Integrated Products, Inc.Windows is a registered trademark of Microsoft Corporation.QTY DESCRIPTION1USB-to-1-Wire adapterAnalog Devices DS9481R-3C7+1USB Type A-to-USB Mini-Type B cable Qualtek Electronics Corp. 3021003-03PARTTYPEDS9481R-3C7+Adapter Evaluates: 1-Wire Peripheral and i Button DevicesDS9481R USB-to-1-Wire/i Button AdapterOne Analog Way, Wilmington, MA 01887 U.S.A. | Tel: 781.329.4700 | © 2023 Analog Devices, Inc. All rights reserved.© 2023 Analog Devices, Inc. All rights reserved. Trademarks and registered trademarks are the property of their respective owners.Click here to ask an associate for production status of specific part numbers.Quick StartRecommended Equipment• Analog Devices DS9481R (included in adapter)• USB type-A to USB Mini type-B cable (included in adapter)• RJ11 cable assembly (not included)• PC with a Windows 11 or Windows 10 OS and a spare USB portNote: In the following sections, software-related items are identified by bolding. Text in bold refers to items directly from the adapter software. Text in bold and underlined refers to items from the Windows operating system. Procedure1) Do the following to install the PL-2303GC Prolific driver:a) Download the latest driver version from Prolific.b) Open and Run the latest version of the DriverInstaller.c) Follow the directions of the Install Wizard untilFinish is reached for the PL-2303 USB-to-serialdriver installation. Close by clicking the Finishbutton.2) Do the following to install the 1-Wire drivers:a) Go to the Download 1-Wire/iButton Drivers forWindows webpage..b) From the Choose Operating System drop-downlist, select your OS.c) From the Select File drop-down list, select 32-bitor 64-bit 1-Wire drivers for the architecture beingused by your OS.d) Click the Download button.e When prompted by the question Do you want torun or save this file?, select Run.f) When you get a security warning that says Doyou want to run the software?, select Run.g) Read and check the box if you accept the licenseagreement and click Install.h) Click the Finish button to exit the Setup Wizard.3) The DS9481R USB-to-1-Wire adapter uses boththe Prolific PL-2303GC and the Analog Devices MAXQ610 to emulate a virtual COM-to-1-Wire port on any PC. Find the enumeration of the virtual COM port by inserting the DS9481R into a spare USB port on the computer. Determine the COM port by look-ing in Control Panel→System→Hardware→Device Manager and expand Ports (COM & LPT). The port is COM5 in the example shown in Figure 2.Figure 1. DS9481R USB-to-1-Wire/iButton Adapter and CableiButton Adapter i Button DevicesYou have now completed the installation of the DS9481R adapter. Obtain the adapter software and directions for installation for your 1-Wire/iButton peripheral device by contacting the Analog Devices online Technical Support Portal.RJ11 PinoutTable 1 and Figure 3 show the RJ11 pinout mounted on the DS9481R PCB at J1. The RJ11 pin 1 can supply 3.3V and can be used for auxiliary board power. The GND is the ground of the 3.3V supply. The signal OW (DATA) stands for the 1-Wire data bus. The ground return for OW (DATA) is the signal OWGND. The PULSE signal is to be used as the VCC power supply for OTP 1-Wire peripheral parts. The PULSE signal is typically 3.3V, but also canprovide the needed programming pulse for OTP parts.The GP signal is reserved for future general-purposeusage and is functionally not used by the DS9481R.Mini-USB PinoutThe 5-position Mini-USB type AB connector is mounted atCN1 of the DS9481R PCB, as shown in Table 2.Hardware/Firmware CapabilitiesThe DS9481R uses both the Prolific PL-2303GC andthe Analog Devices MAXQ610. The PL-2303GC is fullycompliant with the USB 2.0 specification for the Windows11 and Windows 10 OS and provides a bridge for theUSB-to-UART connection. The MAXQ610 is loaded withfirmware that emulates the functionality of the DS2480Bserial-to-1-Wire line driver at a lower 3.3V operationvoltage. The MAXQ610 functions as a UART-to-1-Wirebridge and can serve custom application needs with firm-ware programmability.Table 1. 1-Wire RJ11 PinoutTable 2. Mini-USB Type AB USB PinoutCONNECTOR PIN SIGNAL NAME1 3.3V2GND3OW (DATA)4OWGND5PULSE6GPCONNECTOR PIN SIGNAL NAME1 5.0V2DMCN3DPCN4NC5GND6-9GND_EARTH iButton Adapter i Button DevicesDS9481R EV Kit Bill of MaterialsDESIGNATIONQTY DESCRIPTION4.7uF, 16V Y5V ceramic capacitors (0805) TDK Corp. C2012Y5V1C475Z2 2.2uF, 16V Y5V ceramic capacitors (0805) Murata GRM21BF51C225ZA01L20.22uF Q10%, 16V X7R ceramic capacitors (0603) TDK Corp. C1608X7R1C224K310nF ±5%, 16V X7R ceramic capacitors (0603) AVX 06035C103JAT2A60.1uF, 16V X7R ceramic capacitors (0603) KEMET C0603C104K4RACTU110uF, 10V Y5V ceramic capacitor (0805) TDK Corp. C2012Y5V1C106Z 0Do not populate,470pF ceramic capacitor (0603)21uF, 10V X7R ceramic capacitor (0603) Taiyo Yuden LMK107B7105KA-TC261 2.2uF, 16V X5R ceramic capacitors (0603)110pF, 16V NP0 ceramic capacitor (0603) TDK Corp. C1608C0G1H100D C9, C24, C25 0Do not populate, capacitorsCN1 1USB Mini-AB connector, right-angle, SMD, 5-position JAE Electronics DX3R005HN2E700 130V, 200mA Schottky diode (SOT23) Diodes Inc./Zetex BAT54TA115V, 350mA zener diode (SOT23) Diodes Inc. MMBZ5245B-7-F 1Orange LED (TSS type) (0603) Panasonic/SSG LNJ812R83RA 1Dual CC Schottky diode (SOT23) Diodes Inc./Zetex BAT54CTA2220W, 2000mA ferrite chips (0805) Murata BLM21PG221SN1D16-position, right-angle, PCB-mounted jack Tyco 5520425-3J2 0Do not populate, JTAG connector2130mA, 50V p-channel MOSFETs (SOT23-3) Fairchild Semiconductor BSS844115mA, 60V n-channel MOSFETs (SOT23) Diodes, Inc. 2N7002-7-F1 3.9A, 20V p-channel MOSFET (SOT23) NXP PMV65XP,215 0Do not populate, resistors0Do Not Populate Resistors3 1.5kOHM Q1%, 1/10W SMD resistors (0603) Panasonic ECG ERJ-3EKF1501V210kOHM Q1%, 1/10W SMD resistors (0603) Yageo RC0603FR-0710KL31kOHM Q1%, 1/10W SMD resistors (0603) Yageo RC0603FR-071KL5100kOHM Q1%, 1/10W SMD resistors (0603) Yageo RC0603FR-07100KLC1, C6, C21 3C2, C3 C4, C7 D1 C16 C17, C18 C19C5, C15, C22C8, C12, C13, C14, C20, C23 C10 R6, R24 R7, R14, R26R8, R13, R17, R20, R27, R30R1, R29 R2, R3, R5 R4, R16, R21 Q2, Q4, Q5, Q7 Q6 D2 D3 FB1, FB2 J1 Q1, Q3 D4 iButton Adapteri Button DevicesDS9481R EV Kit Bill of Materials (continued)DESIGNATIONQTY DESCRIPTION1979Ohm Q5%, 1/10W SMD resistor (0603) Yageo RC0603FR-07750RL10Ohm Q1%, 1/10W SMD resistor (0603) Panasonic ECG ERJ-3GEY0R00V133Ohm Q1%, 0.1W SMD resistor (0603) Rohm MCR03EZPFX33R034.99Ohm Q1%, 1/10W SMD resistors (0603) Yageo RC0603FR-074R99L1 2.2kOHM Q5%, 1/10W SMD resistor (0603) Stackpole Electronics RMCF 1/16 2.2K 1% R R191 4.7k OHM Q5% (0603)151kOHM Q0.1%, 1/10W SMD resistor (0603) Panasonic ECG ERA-3AEB513V111kOHM Q0.1%, 1/10W SMD resistor (0603) Vishay/Dale TNPW060311K0BEEA110Ohm Q1%, 1/10W SMD resistor (0603) Yageo RC0603FR-0710RL132.4kOHM Q1%, 1/10W SMD resistor (0603) Vishay/Dale TNPW060332K4BEEA130.1kOHM Q0.1%, 1/10W SMD resistor (0603) Panasonic ECG ERJ-3EKF3012V150kOHM Q1%, 1/10W SMD resistor (0603) Panasonic ECG ERJ-3EKF4992V R36127 Ohm Q1%, 1/10W SMD (0603)10.12A, 30V PTC resettable fuse (1206) Bourns MF-NSMF012-2 SW1 0Do not populate, switch1Low-dropout, 300mA linear regulator (5 SOT23) Analog Devices MAX8887EZK33+T (Top Mark: ADPZ)112V, 30mA Flash memory programming supply (8 SO) Analog Devices MAX662ACSA+ 1TinyLogicM UHS inverter (5 SOT23) Fairchild NC7SZ04M5XU4 0Do not populate, Silicon oscillator1USB-to-serial bridge controller (28 SSOP) Prolific PL-2303GC SSOP116-bit microcontroller with infrared module (32 TQFN-EP*) Analog Devices MAXQ610A-9410+ 12-channel ESD protector (6 FDFN) Analog Devices MAX13204EALT+ (Top Mark: BV)1High-voltage, low-power linear regulators (5 SOT23) Analog Devices MAX1616EUK+ (Top Mark: ABZD)U9 1 1.8V comparator (5 SOT23) STMicroelectronics TS3021ILT —1PCB: DS9481R REV A5R18 R23 R9 R10, R29 R11U6 U7U8 U3 U1 U2 U5 R32 R33 RT1 R25 R28 R31 R12, R15, R22iButton Adapteri Button DevicesiButton Adapter i Button DevicesiButton Adapter i Button DevicesFigure 5. DS9481R Adapter Enclosure DimensionsiButton Adapter i Button Devices DS9481R EV Kit PCB LayoutDS9481R Adapter Board—Top Assembly DS9481R Adapter Board—Bottom AssemblyDS9481R Adapter Board—Top SilkscreenDS9481R Adapter Board—Top Assembly DS9481R Adapter Board—Bottom AssemblyDS9481R Adapter Board—Top SilkscreeniButton Adapteri Button DevicesRevision HistoryREVISION NUMBER REVISIONDATEDESCRIPTIONPAGESCHANGED010/10Initial release—13/23Updated for hardware changes All iButton Adapter i Button DevicesInformation furnished by Analog Devices is believed to be accurate and reliable. However, no responsibility isassumed by Analog Devices for its use, nor for any infringements of patents or other rights of third parties thatmay result from its use.Specifications subject to change without notice. No license is granted by implication orotherwise under any patent or patent rights of Analog Devices. Trademarks and registered trademarks are theproperty of their respective owners.。
XC-009 Mechanical Key Cutting Machine User Manual

CONDOR Mechanical Key Cutting MachineXC-009 User ManualXC-009 Mechanical Key Cutting MachineCONTENTS1 Safety Precautions (5)2 General Information (6)2.1 Machine Description (6)2.2 Characteristics (6)3 Product Packaging Checklist (7)4 Overview (10)4.1 Schematic (10)4.2 Specifications (11)4.3 Main Parts and Function Declaration (13)4.3.1 Hand Wheel (13)4.3.2 Skid Platform (14)4.3.3 Micro-adjust slide (15)4.3.4 Clamp (16)4.3.5 Power Parts (17)5 Equipment Installing and Debugging (18)5.1 Handle Installing (18)5.2 Cutter Installing (19)5.3 Micro-adjust Slide Calibration (20)5.3.1 Lateral Micro-adjust Slide Calibration (21)5.3.2 Longitudinal Micro-adjust Slide Calibration (22)5.4 Clamp Installing (23)6 Use of Equipment (24)6.1 Key Alignment (24)6.1.1 Head spacing (24)6.1.2 Shoulder spacing (25)6.2 Clamp cutting surface selection (26)6.3Use of needle (27)7 Maintenance (28)8 Quality assurance and after-sales instructions (28)9 Appendix (30)1 Safety PrecautionsTo prevent personal injure or machine damage, users should carefully observe the instructions provided by this operation manual and adopt the following safety precautions:●Use the machine under the safe condition●Place the machine on a horizontal surface, which should be firm enough to carrythe weight of the machine.●Do not exposure machine in scorching sun or place the machine in any wet, oily,dusty area.●Keep the machine clean and dry and keep a distance of 30cm from the wall forventilation.●Wear safety glass that meets ANSI standards.●When the machine is working, keep clothing, hair, etc. away from all movingparts.●Do not leave the machine while it is operating.●Do not place anything on the machine while it is operating.●Power plug with ground wire must be connected when charging. Do not usepower plug that is out of power and loose.●Turn off the switch when the machine is not in use or in service.●Shut down the machine immediately when any exception occurs. The switch onthe left side of the machine.●Keep the machine out of reach of children.2 General Information2.1 Machine DescriptionThank you for choosing CONDOR XC-009 Mechanical Key Cutting machine.CONDOR XC-009 Mechanical Key Cutting machine is a portable special device specially designed for global locksmiths. It is small in volume, light in weight and easy to carry.It can quickly and accurately copy and process variety of automobile and resident mechanical key types.Please read it carefully before use. It is crucially important if you wish to operate the machine safely and efficiently.2.2 CharacteristicsCONDOR XC-009 is a new generation of mechanical Key Cutting machine with the following characteristics:●Beautifully designed, full of modernity and technology.●Integrated Casting, Aluminum structure, Durable.●Small volume, Light weight, Easy to carry●Ergonomics designed, More comfortable, simple and convenient.●Micro-adjusted guide for high-precision cutting requirements.●Built-in lithium battery, Super long endurance ability3 Product Packaging ChecklistMain BodyKey spacer2.5mm Allen3mm Allen4mm Allen5mm Allen Tool change 19mm open))))certificate and Product Packaging Checklist(Take4 Overview4.1 SchematicMicro-adjust slideHand wheelHandrailPower display4.2 SpecificationsMachine DimensionsPacking Dimensions175mm285mm200mm4.3 Main Parts and Function Declaration4.3.1 Hand WheelUnscrew the small hand wheel and turn the small hand wheel to achieve cutting feed. By rotating the hand wheel, the clamp slide can be controlled to move left and right, so as to achieve lateral feed during the cutting of the key. The hand wheel adopts a concealed structure, which opens outward when in use and can be hidden after use.4.3.2 Skid PlatformThe clamp Skid Platform can be rotated about the axis of rotation and moved axially to achieve lateral and longitudinal feed of the key. Rotating the hand wheel to realize the lateral feed of the s Skid Platform, holding the handrail and rotating around the axis to realize the key longitudinal feed, the Skid Platform has a lateral stroke of 46mm and the clamp spacing is 95mm.4.3.3 Micro-adjust slideAdjust the Micro-adjust slide to align the cutter with key cutting guide.4.3.4 ClampAllocation and clamp the key, the four-side (A、B、C、D)can be used to copy different key types. The left side is accessory clamp, placed original key, the right side is main clamp, placed blank key. Ensure that left and right clamp use the same cutting surface. Select the proper cutting surface according to different types (refer to chapter 6.2 clamp cutting surface selection and chapter 9 appendix). Be sure to clamp the key before cutting.4.3.5 Power Parts●There is a battery capacity indicator in front of the machine. When the power is low, the indicator is red. Please charge it in time. When power is fully, please unplug the power cord in time. It can be filled about 3-4 hours. After it is full, the machine can be cut the keys 60-100 continuously.●Please use original power cord and adapter.●Please use power socket with ground wire.●Do not cut the key when charging.5 Equipment Installing and Debugging5.1 Handle InstallingIn order to save space, the handrail is separately from the whole machine in the package. Please open the box and install the handrail according to above picture.5.2 Cutter Installing1)While the machine is stopped, slowly rotate the spindle, align the spindle pin hole with the host pin hole, and then insert the tool change rod into the end.2)Installing the cutter on the spindle. Pay Attention to the front and back surface of cutter (with the word facing left), install the cutter block and lock nut (anti-nut).3)Use the 19mm open spanner to tighten the lock screw counterclockwise. Then pull out the tool change rod. After installing the cutter, please refer to chapter 5.3 Fine Adjustment Slide Calibration.5.3 Micro-adjust Slide CalibrationMicro-adjust slide calibration has been finished at the factory. If deviation or incorrect operations are found, please adjust it as follows.Firstly, both clamps are screw to A side, and clamp the Key spacer on both clamps. Closed the Key spacer to clamp, the clamp is tightened. And adjust the lateral and longitudinal adjustment of the slide separately.5.3.1 Lateral Micro-adjust Slide CalibrationPerform lateral adjustment. After clamping the Key spacer, rotate and slide the clamp slide,the left side of cutter is close to the Key spacer, loosen the slide fixing screw slightly, and slowly adjust the left adjustment screw with an Allen wrench. The left side of the key cutting guide is just close to the Key spacer, and the fixing screw is tightened.5.3.2 Longitudinal Micro-adjust Slide CalibrationWhen the longitudinal direction adjusting, slowly rotates the clamp skid platform, align the cutter with the key holder v groove, then rotates the Micro-adjust slide dial, align the key cutting guide with the key holder v groove, rotates the dial 1 small lattice, the key cutting guide moves 0.02mm than before.5.4 Clamp InstallingDo not remove the clamp under normal condition. If it is accidentally disassembled, please install according to the above figure. Pay attention to the clamp surface, otherwise it will not work normally.6 Use of Equipment6.1 Key Alignment6.1.1 Head spacingWhen the key head is spacing, use the alignment block, insert the positioning block into the spacing slot, slowly push the key until it touches the key spacer, the clamp is tightened to remove the key spacer.6.1.2 Shoulder spacingThe original key is fixed on the accessory clamp, the shoulder spacer is aligned, then the blank key is aligned to the shoulder spacer, clamped, and finally the shoulder spacer isrotated to the initial state.If it is found that the distance between the shoulder position and the fixture is inconsistent, it is necessary to calibrate the shoulder spacer. As shown in the following figure, installed the alignment block (refer to chapter 5.3), rotating the shoulder spacing axis, make the left and right shoulder spacer just close to the alignment block A angle, if there is deviation, release the set screw. Slowly move the shoulder spacer, and adjusted the spacer in correct position, then lock the set screw tightly. Remove the key spacer that it can be used normally.6.2 Clamp cutting surface selectionClamp have A, B, C, D on all sides, different types of keys according to the above image to select the appropriate clamping surface, or reference appendix.6.3Use of needleWhen using A or B surface, the clamping depth too deep, cutting less than the complete , you can use the needle, change the clamping depth to ensure normal processing, as shown in the following figure:7 Maintenance●Before cutting the key, please use the brush to clean up the debris of the parts ofthe processing area to avoid the impurity damage and corrosion the machine parts, affecting the key processing accuracy.●Do not use any oily products and detergents to clean all parts of the machine toavoid damage or corrosion the machine parts.●Do not wash machine and parts with water directly, do not wipe the machine withwet cloth, in case of leakage of machine or rust of metal parts●In order to avoid the debris blown into the machine inside, causing safetyproblems,please do not use air guns, hair dryers and other cleaning equipment cleaning processing area.8 Quality assurance and after-sales instructionsCONDOR XC-009 warranty period is one year, subject to the date on the transaction voucher, if no transaction voucher or transaction voucher is lost, the factory record date shall prevail.The following conditions are not free warranty:●Failure to use the instructions as required●Machine damage caused by self repair or modification●Machine failure due to drop, collision or improper voltage●Machine damage caused by force majeure●Used for a long time in harsh environments or on vehicles or ships, causingmachine malfunctions or damage.●The normal use of the machine causing the daily wear.Product After-sale repair and technical support, please contact the dealer or use WeChat scanning QR code, attention to the official WeChat public accounts of the Xhorse (WeChat: SZ-Xhorse).Xhorse leagueXhorse reserve all rights to this manual. No person or organization is allowed to copy and disseminate any part of this manual in any form without permission. Due to product improvement, the contents of this manual may be changed without prior notice。
XC8111AA010R Evaluation Board User Manual

XC8111AA010R Evaluation Board
6Vmax, 1A Load switch IC with ideal diode function
Evaluation Board Picture
Evaluation Board SPEC
PARAMETER
SYMBOL
・ Input Voltage Range
・・・・・・・・・・・・・・・・・・
・ Max Output Current
・・・・・・・・・・・・・・・・・・
1.5V ~ 6.0V 1000mA
・ Ideal Diode function Forward Voltage Quiescent Current Stand-by Current
Iin Vin
A
Multimeter
V
Multimeter
Active Stand-by
: CE="H" (1.2V~6.0V) : CE="L" (0V~0.3V)
Vout
A Iout
Multimeter
V
Multimeter
Rout
XC8111AA010-EVB-01
2/5
www.torex.co.jp
VOUT
1.5V ~ 6.0V
Output Current
1.5V ≦ VIN ≦ 1.7V
(Ta =25℃ )
1.7V < VIN ≦ 6.0V
IOUT
MIN. 1.5
0.0
1.5
0.0 -
TYP. -
-
-
-
MAX. 6.0 6.0
ZETTLER继电器选型

DPDT Bifurcated
Ag Alloy, Au clad 60W / 125VA
250VDC / 300VAC 3A
1A @ 120VAC 2A @ 30VDC
3………48VDC 0.14W
1000MΩ (at 500VDC) 1000 Vrms 1 min 1000 Vrms 1 min
FEATURES
Approvals
Contact Ratings
Contact Arrangement
Contact Material Max Switching Power Max Switching Voltage Max Switching Current
Safety Approved Contact Ratings
CQC
SPDT Ag (Au clad)
30W / 62.5VA 60 VDC / 125VAC
1A
0.5A @ 125VAC 1A @ 30VDC 0.3A @ 60VDC
SPDT
Ag + Au plated 30W / 62.5VA 60 VDC / 125VAC
1A
0.5A @ 125VAC 1A @ 30VDC 0.3A @ 60VDC
12A
E
AZ763
1A, 1C 12
12A
R
AZ766
1A
12
13.5A
AZ943
1A, 1C 13
15A
R
AZ9432
1A, 1C 13
15A
E
AZ943S
1A, 1C 13
15A
L
AZ770
74AHC9541A八位缓冲线驱动器产品数据手册说明书

74AHC9541AOctal buffer/line driver; 3-stateRev. 1 — 28 June 2017Product data sheet1General descriptionThe 74AHC9541A is an 8-bit buffer/line driver with 3-state outputs and Schmitt triggerinputs. The device features an output enable input (OE) and select input (S). A HIGH onOE causes the associated outputs to assume a high-impedance OFF-state. A LOW onthe select input S causes the buffer/line driver to act as an inverter.Inputs are overvoltage tolerant. This feature allows the use of these devices astranslators in mixed voltage environments.The data (An), select (S) and output enable (OE) inputs include Schmitt trigger inputs,capable of transforming slowly changing input signals into sharply defined, jitter-freeoutput signals.This device is fully specified for partial Power-down applications using I OFF. The I OFFcircuitry disables the output, preventing the damaging backflow current through thedevice when it is powered down.2Features and benefits•Wide supply voltage range from 1.8 V to 5.5 V•Typical t pd of 5.1 ns at 5 V•Typical V OL(p) < 0.8 V at V CC = 3.3 V, T amb = 25 °C•Typical V OH(v) > 2.3 V at V CC = 3.3 V, T amb = 25 °C•Supports mixed-mode voltage operation on all ports•I OFF circuitry provides partial Power-down mode operation•Latch-up performance exceeds 250 mA per JESD 78 Class II•ESD protection:–HBM ANSI/ESDA/JEDEC JS-001 Class 2 exceeds 3 kV–MM JESD22-A115-A exceeds 150 V–CDM JESD22-C101E exceeds 2 kV•Specified from -40 °C to +85 °C and from -40 °C to +125 °C3Ordering informationOctal buffer/line driver; 3-state4Functional diagram5Pinning information5.1Pinning74AHC9541AS V CC A0OE A1Y0A2Y1A3Y2A4Y3A5Y4A6Y5A7Y6GND Y7aaa-0268941234567891012111413161518172019Figure 2. Pin configuration TSSOP20Octal buffer/line driver; 3-state5.2Pin description6Functional descriptionTable 3. Functional tableH = HIGH voltage level; L = LOW voltage level; X = don’t care; Z = high-impedance OFF-state.Octal buffer/line driver; 3-state 7Limiting valuesTable 4. Limiting valuesIn accordance with the Absolute Maximum Rating System (IEC 60134). Voltages are referenced to GND (ground = 0 V).[1]The minimum input voltage ratings may be exceeded if the input current ratings are observed.[2]The output voltage ratings may be exceeded if the output current ratings are observed.[3]This value is limited to 7.0 V maximum.[4]For TSSOP20 package: above 100 °C the value of P tot derates linearly with 10 mW/K.8Recommended operating conditionsTable 5. Recommended operating conditionsVoltages are referenced to GND (ground = 0 V).Octal buffer/line driver; 3-state 9Static characteristicsTable 6. Static characteristicsVoltages are referenced to GND (ground = 0 V).Octal buffer/line driver; 3-state9.1Transfer characteristics waveformsOctal buffer/line driver; 3-stateaaa-023439V IN (V)00.5 1.5 2.53211.51.2510.750.50.25I CC (mA)0aaa-023440V IN (V)0123453I CC (mA)00.511.522.5a. V CC = 3.0 Vb. V CC = 4.5 Vaaa-023441V IN (V)013564223145I CC (mA)c. V CC = 5.5 VFigure 4. Typical transfer characteristicsOctal buffer/line driver; 3-state 10Dynamic characteristicsTable 7. Dynamic characteristicsGND = 0 V. For test circuit see Figure 7.Octal buffer/line driver; 3-state[1]Typical values are measured at T amb = 25 °C and V CC = 2.5 V, 3.3 V, and 5 V respectively, unless otherwise specified.[2]t pd is the same as t PLH and t PHL.t en is the same as t PZL and t PZH.t dis is the same as t PLZ and t PHZ.[3]C PD is used to determine the dynamic power dissipation P D (μW).P D = C PD x V CC2 x f i + ∑ (C L x V CC2 x f o) where:f i = input frequency in MHz;f o = output frequency in MHz;C L = output load capacitance in pF;V CC = supply voltage in Volts.Octal buffer/line driver; 3-stateTable 8. Noise characteristicsGND = 0 V. For test circuit see Figure 7.10.1Waveforms and test circuitOctal buffer/line driver; 3-stateOctal buffer/line driver; 3-stateOctal buffer/line driver; 3-state 11Package outlineOctal buffer/line driver; 3-state 12Abbreviations13Revision historyOctal buffer/line driver; 3-state 14Legal information14.1 Data sheet status[1]Please consult the most recently issued document before initiating or completing a design.[2]The term 'short data sheet' is explained in section "Definitions".[3]The product status of device(s) described in this document may have changed since this document was published and may differ in case of multipledevices. The latest product status information is available on the Internet at URL .14.2 DefinitionsDraft — The document is a draft version only. The content is still under internal review and subject to formal approval, which may result in modifications or additions. Nexperia does not give any representations or warranties as to the accuracy or completeness of information included herein and shall have no liability for the consequences of use of such information.Short data sheet — A short data sheet is an extract from a full data sheet with the same product type number(s) and title. A short data sheet is intended for quick reference only and should not be relied upon to contain detailed and full information. For detailed and full information see the relevant full data sheet, which is available on request via the local Nexperia sales office. In case of any inconsistency or conflict with the short data sheet, the full data sheet shall prevail.Product specification — The information and data provided in a Product data sheet shall define the specification of the product as agreed between Nexperia and its customer, unless Nexperia and customer have explicitly agreed otherwise in writing. In no event however, shall an agreement be valid in which the Nexperia product is deemed to offer functions and qualities beyond those described in the Product data sheet.14.3 DisclaimersLimited warranty and liability — Information in this document is believed to be accurate and reliable. However, Nexperia does not give any representations or warranties, expressed or implied, as to the accuracyor completeness of such information and shall have no liability for the consequences of use of such information. Nexperia takes no responsibility for the content in this document if provided by an information source outside of Nexperia. In no event shall Nexperia be liable for any indirect, incidental, punitive, special or consequential damages (including - without limitation -lost profits, lost savings, business interruption, costs related to the removal or replacement of any products or rework charges) whether or not such damages are based on tort (including negligence), warranty, breach of contract or any other legal theory. Notwithstanding any damages that customer might incur for any reason whatsoever, Nexperia's aggregate and cumulative liability towards customer for the products described herein shall be limited in accordance with the Terms and conditions of commercial sale of Nexperia.Right to make changes — Nexperia reserves the right to make changesto information published in this document, including without limitation specifications and product descriptions, at any time and without notice. This document supersedes and replaces all information supplied prior to the publication hereof.Suitability for use — Nexperia products are not designed, authorized or warranted to be suitable for use in life support, life-critical or safety-critical systems or equipment, nor in applications where failure or malfunctionof an Nexperia product can reasonably be expected to result in personal injury, death or severe property or environmental damage. Nexperia and its suppliers accept no liability for inclusion and/or use of Nexperia products in such equipment or applications and therefore such inclusion and/or use is at the customer’s own risk.Applications — Applications that are described herein for any of these products are for illustrative purposes only. Nexperia makes no representation or warranty that such applications will be suitable for the specified use without further testing or modification. Customers are responsible for the design and operation of their applications and products using Nexperia products, and Nexperia accepts no liability for any assistance with applications or customer product design. It is customer’s sole responsibility to determine whether the Nexperia product is suitable and fit for the customer’s applications and products planned, as well as for the planned application and use of customer’s third party customer(s). Customers should provide appropriate design and operating safeguards to minimize the risks associated with their applications and products. Nexperia does not accept any liability related to any default, damage, costs or problem which is based on any weakness or default in the customer’s applications or products, or the application or use by customer’s third party customer(s). Customer is responsible for doing all necessary testing for the customer’s applications and products using Nexperia products in order to avoid a default of the applications and the products or of the application or use by customer’s third party customer(s). Nexperia does not accept any liability in this respect.Limiting values — Stress above one or more limiting values (as defined in the Absolute Maximum Ratings System of IEC 60134) will cause permanent damage to the device. Limiting values are stress ratings only and (proper) operation of the device at these or any other conditions above thosegiven in the Recommended operating conditions section (if present) or the Characteristics sections of this document is not warranted. Constant or repeated exposure to limiting values will permanently and irreversibly affect the quality and reliability of the device.Terms and conditions of commercial sale — Nexperia products aresold subject to the general terms and conditions of commercial sale, as published at /profile/terms, unless otherwise agreed in a valid written individual agreement. In case an individual agreement is concluded only the terms and conditions of the respective agreement shall apply. Nexperia hereby expressly objects to applying the customer’s general terms and conditions with regard to the purchase of Nexperia products by customer.No offer to sell or license — Nothing in this document may be interpreted or construed as an offer to sell products that is open for acceptance orthe grant, conveyance or implication of any license under any copyrights, patents or other industrial or intellectual property rights.Export control — This document as well as the item(s) described herein may be subject to export control regulations. Export might require a prior authorization from competent authorities.Octal buffer/line driver; 3-stateNon-automotive qualified products — Unless this data sheet expressly states that this specific Nexperia product is automotive qualified, the product is not suitable for automotive use. It is neither qualified nor tested in accordance with automotive testing or application requirements. Nexperia accepts no liability for inclusion and/or use of non-automotive qualified products in automotive equipment or applications. In the event that customer uses the product for design-in and use in automotive applications to automotive specifications and standards, customer (a) shall use the product without Nexperia's warranty of the product for such automotive applications, use and specifications, and (b) whenever customer uses the product for automotive applications beyond Nexperia's specifications such use shall be solely at customer’s own risk, and (c) customer fully indemnifies Nexperia for any liability, damages or failed product claims resulting from customer design and use of the product for automotive applications beyond Nexperia's standard warranty and Nexperia's product specifications.Translations — A non-English (translated) version of a document is for reference only. The English version shall prevail in case of any discrepancy between the translated and English versions.14.4 TrademarksNotice: All referenced brands, product names, service names and trademarks are the property of their respective owners.Octal buffer/line driver; 3-statePlease be aware that important notices concerning this document and the product(s)described herein, have been included in section 'Legal information'.Contents1General description ............................................12Features and benefits .........................................13Ordering information ..........................................14Functional diagram .............................................25Pinning information ............................................25.1Pinning ...............................................................25.2Pin description ...................................................36Functional description ........................................37Limiting values ....................................................48Recommended operating conditions ................49Static characteristics ..........................................59.1Transfer characteristics waveforms ...................610Dynamic characteristics .....................................810.1Waveforms and test circuit ..............................1011Package outline .................................................1312Abbreviations ....................................................1413Revision history (1414)Legal information (15)Mouser ElectronicsAuthorized DistributorClick to View Pricing, Inventory, Delivery & Lifecycle Information:N experia:74AHC9541APWJ。
CDE电容型号,9D1C系列

Type 941C High dV/dt, Metallized Polypropylene Film CapacitorsRatingsType 941C flat, oval film capacitors are constructed with polypropylene film and dual metallized electrodes for both self healing properties and high peak current carrying capability (dV/dt). This series features low ESR characteristics, excellenthigh frequency and high voltage capabilities.Construction850 Vdc and HigherDouble MetallizedPolyesterPolypropyleneMetallized PolypropyleneOval Axial Leaded CapacitorsCapacitance Range: .01 µF to 4.7 µFVoltage Range: 600 to 3000 Vdc (275 to 750 Vac, 60 Hz)Capacitance Tolerance: ±10%Operating Temperature Range: –55 ºC to 105 ºCSpecifications1.625(41 mm) Min 1.625(41 mm) MinW MaxTMax L Max d*Full rated at 85 ºC, Derate linearly to 50% rated voltage at 105 ºCNOTE: Refer to Application Guide for test conditions. Contact us for other capacitance values, sizes and performance specificationsNote : Refer to Application Guide for test conditions. Contact us for other capacitance values, sizes and performance specificationsI RMSCatalogTypical Typical70 ºCCap.Part NumberTWLdESR ESL dV/dt I peak 100 kHz(µF)Inches (mm)Inches (mm)Inches (mm)Inches (mm)(mΩ)(nH)(V/µs)(A)(A)600 Vdc (275 Vac).10 941C6P1K-F .223(5.7).470(11.9) 1.339(34.0).032(0.8)281719620 2.8.15 941C6P15K-F .266(6.8).513(13.0) 1.339(34.0).032(0.8)131819629 4.4.22 941C6P22K-F .318(8.1).565(14.3) 1.339(34.0).032(0.8)121919643 4.9.33 941C6P33K-F .387(9.8).634(16.1) 1.339(34.0).032(0.8)91919665 6.1.47 941C6P47K-F .462(11.7).709(18.0) 1.339(34.0).032(0.8)720196927.6.68 941C6P68K-F .558(14.2).805(20.4) 1.339(34.0).040(1.0)6211961348.91.0 941C6W1K-F .680(17.3).927(23.5) 1.339(34.0).040(1.0)6231961969.91.5 941C6W1P5K-F .837(21.3) 1.084(27.5) 1.339(34.0).047(1.2)52419629512.12.0 941C6W2K-F .717(18.2) 1.088(27.6) 1.811(46.0).047(1.2)52812825513.13.3 941C6W3P3K-F .886(22.5) 1.253(31.8) 2.126(54.0).047(1.2)43410534617.34.7 941C6W4P7K-F 1.125(28.6) 1.311(33.3) 2.126(54.0).047(1.2)43610549218.7850 Vdc (450 Vac).15 941C8P15K-F .378(9.6).625(15.9) 1.339(34.0).032(0.8)819713107 6.4.22 941C8P22K-F .458(11.6).705(17.9) 1.339(34.0).032(0.8)8207131577.0.33 941C8P33K-F .562(14.3).810(20.6) 1.339(34.0).040(1.0)7217132358.3.47 941C8P47K-F .674(17.1).922(23.4) 1.339(34.0).040(1.0)52271333510.8.68 941C8P68K-F .815(20.7) 1.063(27.0) 1.339(34.0).047(1.2)42471348513.31.0 941C8W1K-F .679(17.2) 1.050(26.7) 1.811(46.0).047(1.2)52840040012.71.5 941C8W1P5K-F .847(21.5) 1.218(30.9) 1.811(46.0).047(1.2)43040060015.82.0 941C8W2K-F .990(25.1) 1.361(34.6) 1.811(46.0).047(1.2)33140080019.82.2 941C8W2P2K-F 1.042(26.5) 1.413(35.9) 1.811(46.0).047(1.2)33240088020.42.5 941C8W2P5K-F1.117(28.4)1.488(37.8)1.811(46.0).047(1.2)333400100021.2Complies with the EU Directive 2002/95/EC requirement restricting the use of Lead (Pb), Mercury (Hg), Cadmium (Cd), Hexavalent chromium (Cr(VI)), PolyBrominated Biphenyls (PBB) and PolyBrominated Diphenyl Ethers (PBDE).Type 941C High dV/dt, Metallized Polypropylene Film CapacitorsIRMS Catalog Typical Typical70 ºCCap.Part Number T W L d ESR ESL dV/dt I peak100 kHz(µF)Inches(mm)Inches(mm)Inches(mm)Inches(mm)(mΩ)(nH)(V/µs)(A)(A)1000 Vdc (500 Vac).15 941C10P15K-F.441(11.2).688(17.5) 1.339(34.0).032(0.8)7208561287.4 .22 941C10P22K-F.535(13.6).782(19.9) 1.339(34.0).040(1.0)7218561888.1 .33 941C10P33K-F.658(16.7).906(23.0) 1.339(34.0).040(1.0)6228562839.7 .47 941C10P47K-F.790(20.1) 1.037(26.3) 1.339(34.0).047(1.2)52485640211.7 .68 941C10P68K-F.955(24.2) 1.203(30.5) 1.339(34.0).047(1.2)52685658213.0 1.0 941C10W1K-F.803(20.4) 1.174(29.8) 1.811(46.0).047(1.2)52448048013.81.5 941C10W1P5K-F 1.001(25.4) 1.372(34.8) 1.811(46.0).047(1.2)43148072017.32.0 941C10W2K-F 1.169(29.7) 1.540(39.1) 1.811(46.0).047(1.2)33348096021.71200 Vdc (500 Vac).10 941C12P1K-F.462(11.7).709(18.0) 1.339(34.0).032(0.8)9201142114 6.7 .15 941C12P15K-F.568(14.4).815(20.7) 1.339(34.0).040(1.0)72111421718.3 .22 941C12P22K-F.691(17.5).938(23.8) 1.339(34.0).040(1.0)72311422519.2 .33 941C12P33K-F.575(14.6).946(24.0) 1.811(46.0).040(1.0)72164021110.0 .47 941C12P47K-F.698(17.7) 1.069(27.1) 1.811(46.0).047(1.2)72864030110.9 .68 941C12P68K-F.854(21.7) 1.225(31.1) 1.811(46.0).047(1.2)63064043513.0 1.0 941C12W1K-F 1.053(26.7) 1.423(36.1) 1.811(46.0).047(1.2)53264064015.9 1.5 941C12W1P5K-F 1.088(27.6) 1.582(40.2) 2.126(54.0).047(1.2)43650275419.71600 Vdc (630 Vac).10 941C16P1K-F.565(14.3).813(20.6) 1.339(34.0).040(1.0)72114271438.3 .15 941C16P15K-F.696(17.7).943(23.9) 1.339(34.0).040(1.0)523142721411.0 .22 941C16P22K-F.848(21.5) 1.095(27.8) 1.339(34.0).047(1.2)724142731410.3 .33 941C16P33K-F.715(18.2) 1.086(27.6) 1.811(46.0).047(1.2)72380026411.0 .47 941C16P47K-F.867(22.0) 1.238(31.4) 1.811(46.0).047(1.2)63080037613.1 .68 941C16P68K-F 1.059(26.9) 1.430(36.3) 1.811(46.0).047(1.2)63280054414.5 1.0 941C16W1K-F 1.303(33.1) 1.674(42.5) 1.811(46.0).047(1.2)53580080017.9 1.5 941C16W1P5K-F 1.358(34.5) 1.852(47.0) 2.126(54.0).047(1.2)43962894222.22000 Vdc (630 Vac).022 941C20S22K-F.313(7.9).561(14.2) 1.339(34.0).032(0.8)3518171238 2.8 .033 941C20S33K-F.382(9.7).629(16.0) 1.339(34.0).032(0.8)2019171257 4.1 .047 941C20S47K-F.456(11.6).703(17.8) 1.339(34.0).032(0.8)1220171280 5.7 .068 941C20S68K-F.550(14.0).797(20.2) 1.339(34.0).040(1.0)82117121167.7 .10 941C20P1K-F.670(17.0).917(23.3) 1.339(34.0).040(1.0)72217121719.1 .15 941C20P15K-F.557(14.1).928(23.6) 1.811(46.0).040(1.0)7219601449.8 .22 941C20P22K-F.686(17.4) 1.057(26.8) 1.811(46.0).040(1.0)82896021110.1 .33 941C20P33K-F.856(21.7) 1.227(31.2) 1.811(46.0).047(1.2)83096031711.3 .47 941C20P47K-F 1.037(26.3) 1.408(35.8) 1.811(46.0).047(1.2)63296045114.4 .56 941C20P56K-F.941(23.9) 1.436(36.5) 2.126(54.0).047(1.2)73175442213.9 .68 941C20P68K-F 1.050(26.7) 1.545(39.2) 2.126(54.0).047(1.2)63575451315.8 1.0 941C20W1K-F 1.303(33.1) 1.797(45.6) 2.126(54.0).047(1.2)53875475419.43000 Vdc (750 Vac).010 941C30S1K-F.308(7.8).555(14.1) 1.339(34.0).032(0.8)6018256826 2.2 .015 941C30S15K-F.375(9.5).622(15.8) 1.339(34.0).032(0.8)4019256839 2.9 .022 941C30S22K-F.454(11.5).701(17.8) 1.339(34.0).032(0.8)2520256857 4.0 .033 941C30S33K-F.558(14.2).805(20.4) 1.339(34.0).040(1.0)1421256885 5.8 .047 941C30S47K-F.446(11.3).817(20.7) 1.811(46.0).040(1.0)1420144068 6.3 .068 941C30S68K-F.545(13.8).916(23.3) 1.811(46.0).040(1.0)12261440987.4 .10 941C30P1K-F.673(17.1) 1.044(26.5) 1.811(46.0).047(1.2)102814401449.0 .15 941C30P15K-F.839(21.3) 1.210(30.7) 1.811(46.0).047(1.2)830144021611.2。
无线遥控器分析仪

背光模式设置(Backlight mode):选项是 AUTO<自动>、ON<常开>、OFF<常关>,“翻
页”键 选 择 ,“功能”键确定。
周期显示模式(Cycle display): 选项是 Resistance<振荡阻值>、Time<时间> ,“翻页”键选
择 ,“功能”键确定。
帮助(HELP):显示机器的机器型号、版本信息,方便用户在遇到问题时可以反馈得到
Save as..(另存为):将当前编辑好的内码另存为新的一组,存储器满时自动删除第一组 内码。
拷贝遥控子机:
● 按下遥控器发射键,成功收到信号后,用“#”键对信号转发,和改变键码发射测试, 观察接收机是否收到正确的信号。机器会自动识别芯片,但如果判断错误可以手动改变 芯片的类型再发射测试。
● 机器上显示“xx2262”表示 PT2262/2260/CS5211 等三态码系列: 信号内码的表示:0 代表接低电平,1 代表悬空,2 代表接高电平,LCD 显示左边对应 为芯片的“1 脚”,按显示把新遥控焊接好,换上对应的振荡电阻,完成拷贝。
按键码([Data bit]),“翻页”键移动光标,“#”键改变该位的数值,“功能”键确定。 设置完成后,按“功能”键开始扫描,屏幕显示地址码不断在跳动,在扫描中按下“取
消”键暂停扫描,并发出提示,液晶屏显示当前地址码,按“翻页 ”键地址上翻减一 并 发射,按“#”键地址下翻加 一并发 射, 按 “功能 ”键继续扫描, 按 “S”键切换, ST 灯亮起,按“A、B、C、D”键改变按键位同时发射。
第 7 页 共 10 页
>,“翻页”键 选 择 ,“功能”键确定。
无线遥控分析仪 A890-RES/A890-EN
高压防闩锁型48通道多路复用器

修订历史
2013年3月—修订版B至修订版C 更改表5和表6 ................................................................................ 8 表7中ADG5408峰值电流从370 mA变为435 mA; ADG5409峰值电流从275 mA变为300 mA; 回流焊峰值温度(无铅)从260(+0/−5)°C变为“依据 JEDEC J-STD-020”........................................................................ 9 更改图25、图26和图29 ............................................................ 16
license is granted by implication or otherwise under any patent or patent rights of Analog Devices.
Trademarks and registered trademarks are the property of their respective owners.
±15 V双电源 ............................................................................. 3 ±20 V双电源 ............................................................................. 4 12 V单电源................................................................................ 5 36 V单电源................................................................................ 6 每通道连续电流,Sx或D ...................................................... 8
AZ2150-1A-12DE中文资料
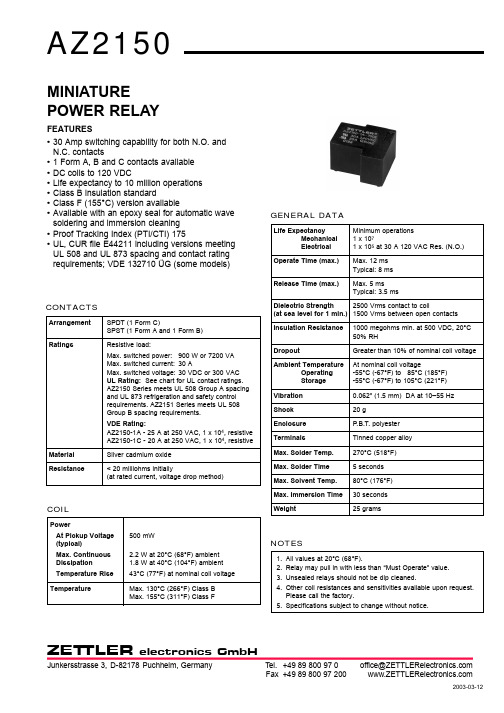
ZET TLERelectronics GmbHFax +49 89 800 97 200 office@ 0 97 800 89 +49 Tel. GermanyPuchheim, D-82178Junkersstrasse 3, 2003-03-12GENERAL DATALife ExpectancyMinimum operations Mechanical 1 x 107Electrical 1 x 105at 30 A 120 VAC Res. (N.O.)Operate Time (max.)Max. 12 ms Typical: 8 ms Release Time (max.)Max. 5 ms Typical: 3.5 msDielectric Strength 2500 Vrms contact to coil(at sea level for 1 min.)1500 Vrms between open contacts Insulation Resistance 1000 megohms min. at 500 VDC, 20°C 50% RHDropoutGreater than 10% of nominal coil voltage Ambient TemperatureAt nominal coil voltageOperating -55°C (-67°F) to 85°C (185°F)Storage -55°C (-67°F) to 105°C (221°F)Vibration 0.062" (1.5 mm) DA at 10–55 Hz Shock 20 gEnclosure P .B.T. polyester TerminalsTinned copper alloy Max. Solder Temp.270°C (518°F)Max. Solder Time 5 seconds Max. Solvent Temp.80°C (176°F)Max. Immersion Time30 seconds Weight25 gramsMINIATURE POWER RELAYFEATURES•30 Amp switching capability for both N.O. and N.C. contacts•1 Form A, B and C contacts available •DC coils to 120 VDC•Life expectancy to 10 million operations •Class B insulation standard•Class F (155°C) version available•Available with an epoxy seal for automatic wave soldering and immersion cleaning •Proof Tracking Index (PTI/CTI) 175•UL, CUR file E44211 including versions meeting UL 508 and UL 873 spacing and contact rating requirements; VDE 132710 ÜG (some models)CONTACTSArrangement SPDT (1 Form C)SPST (1 Form A and 1 Form B)RatingsResistive load:Max. switched power:900 W or 7200 VA Max. switched current: 30 AMax. switched voltage: 30 VDC or 300 VAC UL Rating:See chart for UL contact ratings.AZ2150 Series meets UL 508 Group A spacing and UL 873 refrigeration and safety control requirements. AZ2151 Series meets UL 508Group B spacing requirements.VDE Rating:AZ2150-1A - 25 A at 250 VAC, 1 x 104, resistive AZ2150-1C - 20 A at 250 VAC, 1 x 104, resistiveMaterial Silver cadmium oxideResistance< 20 milliohms initially(at rated current, voltage drop method)COILPowerAt Pickup Voltage 500 mW(typical)Max. Continuous 2.2 W at 20°C (68°F) ambient Dissipation 1.8 W at 40°C (104°F) ambient Temperature Rise 43°C (77°F) at nominal coil voltage TemperatureMax. 130°C (266°F) Class B Max. 155°C (311°F) Class FNOTES1.All values at 20°C (68°F).2.Relay may pull in with less than “Must Operate” value.3.Unsealed relays should not be dip cleaned.4.Other coil resistances and sensitivities available upon request.Please call the factory.5.Specifications subject to change without notice.2003-03-12ZET TLERelectronics GmbHFax +49 89 800 97 200 office@ 0 97 800 89 +49 Tel. GermanyPuchheim, D-82178 Junkersstrasse 3, RELAY ORDERING DATASTANDARD RELAYS: 1 Form A (SPST); 508 Group A; UL 873 VersionCOIL SPECIFICATIONS ORDER NUMBER*Nominal Max.CoilMust Coil Continuous Resistance Operate Unsealed SealedVDC VDC±10%VDC57.327 3.75AZ2150–1A–5D AZ2150–1A–5DE 68.940 4.5AZ2150–1A–6D AZ2150–1A–6DE 913.997 6.75AZ2150–1A–9D AZ2150–1A–9DE 1217.51559.0AZ2150–1A–12D AZ2150–1A–12DE 1522.525611.25AZ2150–1A–15D AZ2150–1A–15DE 1827.438013.5AZ2150–1A–18D AZ2150–1A–18DE 2436.166018.0AZ2150–1A–24D AZ2150–1A–24DE 4868.42,56036.0AZ2150–1A–48D AZ2150–1A–48DE 70104.45,50052.5AZ2150–1A–70D AZ2150–1A–70DE 110163.213,45082.5AZ2150–1A–110D AZ2150–1A–110DESTANDARD RELAYS: 1 Form A (SPST); UL 508 Group B VersionCOIL SPECIFICATIONS ORDER NUMBER*57.327 3.75AZ2151–1A–5D AZ2151–1A–5DE 68.940 4.5AZ2151–1A–6D AZ2151–1A–6DE913.997 6.75AZ2151–1A–9D AZ2151–1A–9DE1217.51559.0AZ2151–1A–12D AZ2151–1A–12DE1522.525611.25AZ2151–1A–15D AZ2151–1A–15DE1827.438013.5AZ2151–1A–18D AZ2151–1A–18DE2436.166018.0AZ2151–1A–24D AZ2151–1A–24DE4868.42,56036.0AZ2151–1A–48D AZ2151–1A–48DE70104.45,50052.5AZ2151–1A–70D AZ2151–1A–70DE 110163.213,45082.5AZ2151–1A–110DAZ2151–1A–110DE * Substitute “1B” or “1C” in place of the “1A” to indicate 1 Form B and 1 Form C respectively.To indicate Class F version, add suffix “F”.MECHANICAL DATA。
PCF8591中文数据手册
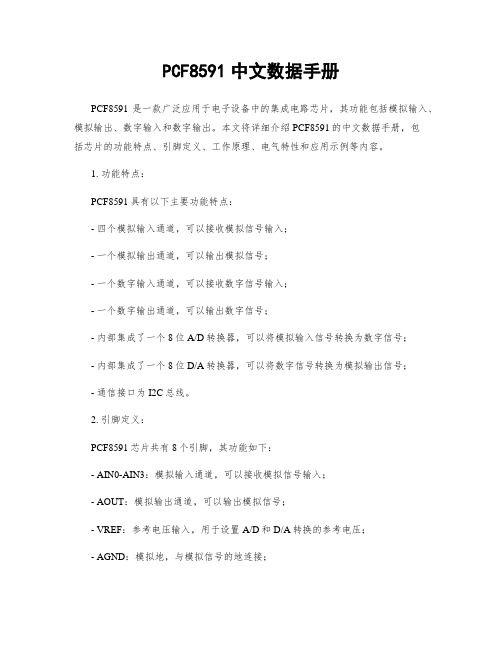
PCF8591中文数据手册PCF8591是一款广泛应用于电子设备中的集成电路芯片,其功能包括模拟输入、模拟输出、数字输入和数字输出。
本文将详细介绍PCF8591的中文数据手册,包括芯片的功能特点、引脚定义、工作原理、电气特性和应用示例等内容。
1. 功能特点:PCF8591具有以下主要功能特点:- 四个模拟输入通道,可以接收模拟信号输入;- 一个模拟输出通道,可以输出模拟信号;- 一个数字输入通道,可以接收数字信号输入;- 一个数字输出通道,可以输出数字信号;- 内部集成了一个8位A/D转换器,可以将模拟输入信号转换为数字信号;- 内部集成了一个8位D/A转换器,可以将数字信号转换为模拟输出信号;- 通信接口为I2C总线。
2. 引脚定义:PCF8591芯片共有8个引脚,其功能如下:- AIN0-AIN3:模拟输入通道,可以接收模拟信号输入;- AOUT:模拟输出通道,可以输出模拟信号;- VREF:参考电压输入,用于设置A/D和D/A转换的参考电压;- AGND:模拟地,与模拟信号的地连接;- VCC:供电电源,通常为+5V;- SDA:I2C总线数据线;- SCL:I2C总线时钟线。
3. 工作原理:PCF8591通过内部的A/D和D/A转换器实现模拟信号和数字信号之间的转换。
在模拟输入模式下,PCF8591将模拟输入信号转换为数字信号,并通过I2C总线输出给主控设备。
在模拟输出模式下,PCF8591将数字信号转换为模拟输出信号,并输出给外部设备。
同时,PCF8591还可以通过数字输入通道接收外部设备的数字信号,并通过I2C总线输出给主控设备。
4. 电气特性:PCF8591的电气特性包括供电电压、工作温度范围、输入输出电压范围等方面。
以供电电压为例,PCF8591的供电电压范围为2.5V至6V,通常为+5V。
在不同的工作温度范围内,PCF8591的电气特性可能会有所变化,具体请参考数据手册中的详细参数表。
ili9481 中文规格书

ili9481 中文规格书【实用版】目录1.引言2.概述3.功能特性4.物理特性5.工作环境6.安全特性7.测试方法8.结论正文1.引言本文档旨在介绍 ili9481 中文液晶显示屏的相关信息,包括其功能特性、物理特性、工作环境、安全特性以及测试方法等,以帮助用户更好地了解和使用这款产品。
2.概述ili9481 是一款中文液晶显示屏,具有显示中文字符的能力。
它采用了 TFT 技术,具有高对比度、高亮度和快速响应等特点,适合在各种场合使用。
3.功能特性ili9481 具有以下功能特性:- 可显示中文字符,支持简体和繁体;- 支持多种字体样式,如黑体、楷体等;- 可调节字体大小、颜色和显示效果;- 支持多种文本格式,如字符、数字和符号等;- 具有自动翻页和滚动显示等功能。
4.物理特性ili9481 的物理特性如下:- 显示屏尺寸:128x64 像素;- 显示屏分辨率:128x64 像素;- 显示颜色:16 级灰度;- 视角:60 度;- 工作温度:-20℃至 +70℃;- 存储温度:-30℃至 +80℃。
5.工作环境ili9481 适用于以下工作环境:- 温度:-20℃至 +70℃;- 湿度:5% 至 95%;- 电源:DC 3.3V 至 5V;- 功耗:小于 10mA;- 振动:10 至 55Hz,1mm 振幅;- 冲击:10g,10 至 55Hz。
6.安全特性为了确保产品安全可靠,请遵循以下注意事项:- 请勿在高温、高湿或低温环境中使用;- 请勿将产品暴露在阳光下或紫外线下;- 请勿在腐蚀性环境中使用;- 请勿在电源电压超过范围的情况下使用;- 请勿在产品上施加过大的力。
7.测试方法为了确保产品性能稳定,请按照以下方法进行测试:- 通电测试:连接电源,检查显示屏是否正常工作;- 功能测试:设置各种参数,检查显示屏是否正常显示;- 耐压测试:施加规定的电压,检查显示屏是否损坏;- 耐温测试:将产品放入规定的温度环境中,检查显示屏是否正常工作;- 振动和冲击测试:施加规定的振动和冲击,检查显示屏是否损坏。
CRT型号配件库存
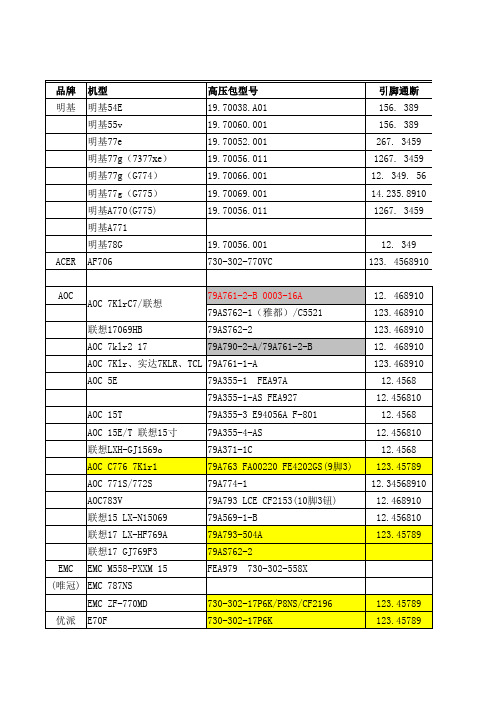
BSC24-N2374S 美格99P 美格XJ700T 菲利普 105G(裕安) 107S,107S51 107s67/107S66 107S(17C2622H)普平 107T(荣欣) (联想)LXH-769 (联想)LXH-GJ769F4 三星 三星450B 三星550B 三星510N 三星743DF/763DF 三星750S 753DF 三星 三星 三星 三星788DF 793DF 三星795MB 三星793DF 三星997MB 三星988MB+ HP TCL P9009 19寸 TCL M1502 TCL MF767 TCL MF786 方正 海洋 方向 海信 ? CM787Z 海洋 T171 海信HS-1728R HY现代 HY775 730-302-797N LCE CF1033A FEA888 LCE CF2091 FM-1077/FPH0213/2091 AT2097/20B AT2097 / LCE CF1880 730-302-P8NS 79A774 FKG-15A006 FQA-15A001 FQA-15A001 FQM-17B002/FQM-17B015/ PQB-17A001 FEA831 FSA0188 LCE CF1781 FQM-17B021 FQM-17A011 FQM-17A012 FQM-19A007 FQM-19A005 BH26-00205A Y268109B BSM35-3221 37SC25M0-2510X 25-0208M 730-302-P6SE BSM76-3709 (可以用730-302-770VC代换) BSC26-1461 BSC26-1453 BSM75-3707 BSM75-3708C BSM75-3709 12.35.46810 12345. 67810 1267.345810 12. 3489. 56 123.568910 BSM64-3803 1478. 35910 139.24678 139.24678 1478. 35910 14.27.358910 123.45789 12.34568910 1279. 345 12.36.579 12.36.579 12.3610.4579 12. 36. 4579 12.345679 12.345679 12.34610.579 12.410.579 12.410.579 12.35.489.610 12.46.579 12.46.579 12.3579.46 12.5681
JH9401EE

1 概述JH9401E电话机拨号/CID分析仪是专为测试电话机拨号特性(Pulse/Tone)、主叫号码显示(Caller ID)而设计的新一代智能测试仪表。
采用快速富里叶变换(FFT)算法分析电话机的双音频拨号特性,在测试功能、速度和精度上代表同类仪表最先进水平。
该仪器采用全数字式结构,具有高可靠性和稳定性,可以用来对电话机脉冲/音频拨号的全部性能和主叫号码(FSK/DTMF)的详细指标的测试,测试结果可以显示,亦可打印。
JH9401E采用10″LCD(640X480)作显示屏,使用户能同时看到更多的信息。
该类仪器是科研部门开发研制话机和工厂生产话机的必要设备,亦可用于行业质量检测、工厂流水线生产检测。
1.1 使用环境1、环境温度 0℃~40℃2、相对湿度 45%~75%3、大气压力 86kpa~106kpa4、使用环境内应无强磁场和化学腐蚀气体。
1.2 电源供电 AC 220V±22V1.3 功耗<50W1.4 外形尺寸 436×200×250(mm)1.5 质量≤9.2kg2 JH9401E主要技术性能2.1 测试仪能测试电话机脉冲拨号特性(包括脉冲个数、脉冲速率、断/续比、脉宽、脉冲串间隔时间、R/Flash键、导通电阻、断开电阻)。
精度:时间±1ms电阻±2%接收DTMF信号的动态范围:-37dBm~-3dBm2.2 测试仪能测试电话机双音频拨号特性(包括键号、高低频群的频率、高低频群的电平、高低频群的频偏、高低频群的电平差、非线性失真、DTMF持续时间、DTMF 间隔时间、双音频信号的功率谱)。
精度:频率±2‰电平±0.3dB2.2.1 仪器的噪声为白噪声,带宽为2.5s~50k2.2.2 信号源输出阻抗为600±1%Ω(美国标准为900±1%Ω)。
可按各国标准设置于仪表内存,用来判别被测电话机合格与否。
- 1、下载文档前请自行甄别文档内容的完整性,平台不提供额外的编辑、内容补充、找答案等附加服务。
- 2、"仅部分预览"的文档,不可在线预览部分如存在完整性等问题,可反馈申请退款(可完整预览的文档不适用该条件!)。
- 3、如文档侵犯您的权益,请联系客服反馈,我们会尽快为您处理(人工客服工作时间:9:00-18:30)。
.500 [12.7]
.500 [12.7]
.400 [10.16]
.400 [10.16]
.300 [7.62]
.701 [17.8]
WIRING DIAGRAM
2 1 2 1
0.5 [12.7]
2-Ø.036 [Ø0.9]
0.4 [10.2]
0.3 [7.62]
3-Ø.052 [Ø1.3]
ORDER NUMBER*
AgCdO Contacts AZ9481–1A–5D AZ9481–1A–6D AZ9481–1A–9D AZ9481–1A–12D AZ9481–1A–18D AZ9481–1A–24D AZ9481–1A–48D AgSnO2 Contacts AZ9481–1AE–5D AZ9481–1AE–6D AZ9481–1AE–9D AZ9481–1AE–12D AZ9481–1AE–18D AZ9481–1AE–24D AZ9481–1AE–48D
1 Form CRLeabharlann ted Load ULCOIL
Power At Pickup Voltage (typical) Max. Continuous Dissipation Temperature Rise Temperature 128 mW (Form A) 256 mW (Form C) 1.34 W at 20°C (68°F) 24°C (43°F) at nominal coil voltage (Form C) 13°C (23°F) at nominal coil voltage (Form A) Max. 155°C (333°F)
Material Resistance
NOTES
1. All values at 20°C (68°F). 2. Relay may pull in with less than “Must Operate” value. 3. Specifications subject to change without notice.
ORDER NUMBER*
AgNi Contacts AZ9481–1CB–5D AZ9481–1CB–6D AZ9481–1CB–9D AZ9481–1CB–12D AZ9481–1CB–18D AZ9481–1CB–24D AZ9481–1CB–48D AgSnO2 Contacts AZ9481–1CE–5D AZ9481–1CE–6D AZ9481–1CE–9D AZ9481–1CE–12D AZ9481–1CE–18D AZ9481–1CE–24D AZ9481–1CE–48D
Form A
.886MAX [22.5] .649MAX [16.5] .886MAX [22.5]
Form C
.649MAX [16.5]
.016 [0.4]
.449MAX [11.4]
.016 [0.4]
.449MAX [11.4]
.701 [17.8] 2-Ø.036 [Ø0.9]
.142 [3.7]
*Add suffix “E” for epoxy sealed version. Add suffix “A” for gold plated contacts.
12/14/05W
元器件交易网
AZ9481
MECHANICAL DATA OUTLINE DIMENSIONS PC BOARD LAYOUT
12/14/05W
元器件交易网
AZ9481
RELAY ORDERING DATA
COIL SPECIFICATIONS SPST-NO (1 Form A)
Nominal Coil VDC 5 6 9 12 18 24 48 Must Operate VDC 4 4.8 7.2 9.6 14.4 19.2 38.4 Max. Continuous VDC 13.4 16.1 24.1 32.2 48.3 64.4 128.8 Coil Resistance ±10% 125 180 405 720 1620 2880 11520
CONTACTS
Arrangement Ratings Standard 1 Form A
High Capacity 1 Form A
Dielectric Strength 2500 Vrms coil to contact (at sea level for 1 min.) 1000 Vrms contact to contact Insulation Resistance Dropout Ambient Temperature Operating Storage Vibration Shock Enclosure Terminals Max. Solder Temp. Max. Solder Time Max. Solvent Temp. Max. Immersion Time Weight 100 megohms min. at 20°C, 500 VDC, 50% RH Greater than 10% of nominal coil voltage At nominal coil voltage -40°C (-40°F) to 85°C (185°F) -40°C (-40°F) to 155°C (333°F) 0.062" DA at 10–55 Hz 10g operational, 100g destructive P.B.T. polyester Tinned copper alloy, P.C. 270°C (518°F) 5 seconds 80°C (176°F) 30 seconds 8 grams
*Add suffix “E” for epoxy sealed version. Add suffix “A” for gold plated contacts.
COIL SPECIFICATIONS SPST-NO (1 Form A) - HIGH CAPACITY
Nominal Coil VDC 5 6 9 12 18 24 48 Must Operate VDC 4 4.8 7.2 9.6 14.4 19.2 38.4 Max. Continuous VDC 13.4 16.1 24.1 32.2 48.3 64.4 128.8 Coil Resistance ±10% 125 180 405 720 1620 2880 11520
ORDER NUMBER*
AgCdO Contacts AZ9481–1AT–5D AZ9481–1AT–6D AZ9481–1AT–9D AZ9481–1AT–12D AZ9481–1AT–18D AZ9481–1AT–24D AZ9481–1AT–48D AgSnO2 Contacts AZ9481–1AET–5D AZ9481–1AET–6D AZ9481–1AET–9D AZ9481–1AET–12D AZ9481–1AET–18D AZ9481–1AET–24D AZ9481–1AET–48D
*Add suffix “E” for epoxy sealed version. Add suffix “A” for gold plated contacts.
COIL SPECIFICATIONS SPDT (1 Form C)
Nominal Coil VDC 5 6 9 12 18 24 48 Must Operate VDC 4 4.8 7.2 9.6 14.4 19.2 38.4 Max. Continuous VDC 9.5 11.4 17.1 22.8 34.2 45.5 91.1 Coil Resistance ±10% 63 90 203 360 810 1440 5760
元器件交易网
AZ9481
16 AMP LOW PROFILE POWER RELAY
FEATURES • • • • • • • • High power switching (4000 VA) High sensitivity, 128 mW pickup Low profile (less than .5" height) SPST (1 Form A) and SPDT (1 Form C) UL Class F (155°C) standard Epoxy sealed versions available DC coils up to 48 VDC UL file E43203, TÜV R50053055 GENERAL DATA
SPST (1 Form A) SPDT (1 Form C) Resistive load: Max. switched power: 300 W, 2500 VA Max. switched current: 10 A Max. switched voltage: 250 VAC / 30 VDC Max. switch power: 300 W, 4000 VA Max. switch current: 16 A Max. switched voltage: 250 VAC / 30 VDC Max. switched power: 300 / 180 W, 2500 / 1500 VA (N.O./N.C.) Max. switched current: 10 / 6 A (N.O./N.C.) Max. switched voltages: 250 VAC / 30 VDC Standard 1 Form A 10 A at 250 VAC Res. 100k cycles [1][2] 10 A at 30 VDC Res. 100k cycles [1][2] TV-5 [1][2] High Capacity 1 Form A 16 A at 125 VAC Res. 100k cycles [1][2] 10 A at 30 VDC Res. 100k cycles [1][2] TV-5 [1][2] Standard 1 Form C 10 / 6 A (N.O./N.C.) at 250 VAC Res. 100k cycles[2] 10 / 6 A (N.O./N.C.) at 250 VAC Res. 30k/100k cycles [3] TÜV High Capacity 1 Form A 16 A at 250 VAC Res. 100k cycles [1][2] 8 A at 250 VAC cos phi = 0.4 100k cycles [1][2] 10 A at 30 VDC Res. 100k cycles [1][2] Silver cadmium oxide [1], silver tin oxide [2] or silver nickel [3]. Gold plated contacts available. < 100 milliohms initially (6 V, 1 A voltage drop method) Life Expectancy Mechanical Electrical Operate Time (typical) Release Time (typical) Minimum operations 1 x 107 1 x 105 10 A 250 VAC Res. 10 ms at nominal coil voltage 5 ms at nominal coil voltage (with no coil suppression)