轴承套圈车削加工用弹簧胀卡的改进
HZC20车床弹簧内夹盘前拉杆结构的改进

( nh er gS bF coy ri er gG o pC roain ri10 5 ,hn ) Naz i ai u -atr, bnb a n ru op rt , bn 0 6 ia B n Ha i o Ha 5 C
Ab t a t T h u s o fs o tl e o r n e so a f i t r a h c n s rn flt e HZC2 , t e sr cu e wa s r c : o t e q e t n o h r i f fo tt n i n b r o e n lc u k i p i g o h i f n a 0 h tu t r s
第 1 期
贾淑晖:H C 0 Z 2车床弹簧内夹盘前拉杆ห้องสมุดไป่ตู้构的改进
连接处强度下降 ,使拉杆在A 处易出现裂纹 ,造 成断裂。在实际生产加工过程 中需要经常拆卸和 更 换前 拉 杆 ,造 成 了很 大 浪费 ,同时 生产 效 率 下 降。 ( )由于机床原前拉杆结构不合理 ,强度 2 低 ,造 成拉 杆 不 断报 废 ,它 就成 了机床 夹 紧机 构 的易 损 部件 ,需要 不 断地 重新 加 工 ,加 工 时 ,因 为 头部 直 径 为  ̄4 mm,而 杆部 直 径 只 有  ̄1mm 1 6 直径相差大 ,如 图 2。要保证头部的尺寸必须用 外 圆直径  ̄ 5 m以上的棒料来加工 ,把 q 5 m 4m  ̄m 4 棒 料加 工成 1 mm 杆 ,得 加工 多 次才 能完 6 拉 成 ,加 工 时 间较 长 ,同时又 浪 费 了加 工原 料 。由
( 哈尔滨轴 承集 团公 司 南直 轴承分厂 ,黑龙江 哈尔滨 10 5 50 6)
摘
要 :针对 H C 0 Z 2 车床 弹簧 内卡 盘前拉杆使用 寿命短 的 问题 ,对其结构加 以分析 ,提 出改进措 施 ,由原 来
轴承套圈工艺改进技术专题报告1
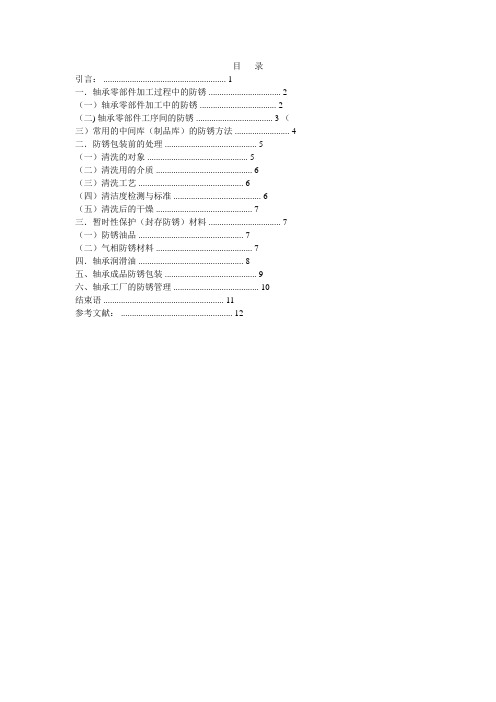
目录引言: (1)一.轴承零部件加工过程中的防锈 (2)(一)轴承零部件加工中的防锈 (2)(二) 轴承零部件工序间的防锈 ................................... 3 (三)常用的中间库(制品库)的防锈方法 . (4)二.防锈包装前的处理 (5)(一)清洗的对象 (5)(二)清洗用的介质 (6)(三)清洗工艺 (6)(四)清洁度检测与标准 (6)(五)清洗后的干燥 (7)三.暂时性保护(封存防锈)材料 (7)(一)防锈油品 (7)(二)气相防锈材料 (7)四.轴承润滑油 (8)五、轴承成品防锈包装 (9)六、轴承工厂的防锈管理 (10)结束语 (11)参考文献: (12)深沟球轴承轴承内外圈磨加工工艺过程改进作者:刘圣斌指导老师:余军合宁波大学科学技术学院摘要:通过改进轴承内外圈磨工工艺过程和使用的设备,可以使产品磨加工工艺过程和在制品周转更加合理,解决了冷却水、精研油、清洗煤油交叉相混现象,降低了生产成本,降低社会劳动生产时间的同时提高了社会劳动生产率和产品质量。
进一步扩大了轴承产品的竞争优势。
关键字:深沟球轴承;内圈、外圈、磨削、工艺一、轴承介绍:轴承是一种精度高、互换性很强的标准零件,因此,为获得高的生产效率和产品质量,常采用专用加工设备。
达克公司公司专业化生产深沟球轴承,对内外圈的磨加工工艺过程进行了多次改进,提高了工效和产品质量。
1原设备及工艺存在的问题原内、外圈磨超工艺如下:外圈:磨端面(MB7480)→退磁、清洗→磨外径(M1080,MG10200)→支外径磨外沟道(3MZ146)→退磁、清洗→支外径超精外沟道(四轴超精机)。
内圈:磨端面(MB7480)→退磁、清洗→磨内圈挡边(M1050,MGT1050)→支内沟道磨内沟道(3MZ133)→退磁、清洗→支内沟道磨内径(3MZ203)→退磁、清洗→支内圈挡边超精内沟道(四轴超精机)。
立轴圆台平面磨床(MB7480)弊端:此磨床分磨削套圈两个端面,套圈磨第一端面后需要退磁清洗,再磨第二端面,再退磁清洗。
老师傅经验分享:预防和控制轴承套圈淬火变形、开裂、胀缩

老师傅经验分享:预防和控制轴承套圈淬火变形、开裂、胀缩作者:范仲和,在洛阳轴承厂技术中心从事金属材料和热工工艺研究及轴承失效分析工作,有着40多年的工作经验。
《金属加工》资深专家、作者。
来源:《金属加工(热加工)》杂志这篇文章主要分析了轴承套圈淬火变形、开裂、胀缩的产生原因和预防措施。
轴承钢套圈淬、回火后的变形和尺寸胀缩一直影响着热处理产品质量。
近年来,轴承行业热处理应用了贝氏体、马氏体与贝氏体的复合淬火新工艺,因淬火后套圈变形、开裂及胀缩量难以控制,同一批产品胀缩量忽大忽小差别较大,产品合格率较低,只能采取增大下一工序磨削加工的留量来满足产品的胀缩量,这样既浪费了材料也消耗了人工工时,所以有些企业只能放弃先进的贝氏体淬火工艺改回原马氏体淬火。
轴承钢套圈淬火变形、开裂、胀缩量产生的原因受很多因素影响,是一个相当复杂的问题。
下面分别讨论这些缺陷的产生原因及其应采取的解决办法。
1.淬火变形、开裂和尺寸胀缩轴承钢套圈在淬火时材料中的应力未达到弹性极限,材料只发生弹性变形,应力超过弹性极限而低于材料的强度极限时,则发生塑性变形;应力达到强度极限,材料就发生断裂。
因此,材料的变形和开裂是在应力大小和材料的性能指标两个因素作用下发生的。
淬火过程不可避免要出现淬火应力,包括热应力和组织应力。
在操作过程中还可能带来零件机械的碰撞产生应力,这些应力分布不均匀,在应力集中处可能比平均应力大许多倍;同时,由于材质的不均匀性和材料缺陷,使其各部位的强度指标也能悬殊许多倍,而且在材质薄弱处也往往正是应力集中处,因此,应力超过材料强度极限则发生局部断裂,亦即裂纹。
由于淬火应力和体积变化,引起零件各部分尺寸均匀变化而不改变零件形状,称尺寸胀缩。
由于不均匀的淬火应力,而使零件形状改变者,即常说的淬火变形。
套圈的径向不均匀变形大小(长、短轴之差值),通常叫套圈的椭圆度;套圈的轴向不均匀变形,通常叫翘曲变形(见图1),轴向均匀变形叫蝶形变形(见图2)。
车加工滚子弹簧夹头结构的改进

Rm 5 m增至 R 0 m,这样有 利于 车刀刃部 的磨 削 ,增 1m
理淬火后应力集中 ,这是造成 夹头过早疲劳损坏 的主要
原因 。原来弹簧夹头在淬火时端 部 6个弹簧瓣 开 口没有
加了车刀的寿命 , 最大限度减少车刀的磨损,更重要的
是减少 了弹簧夹头应力过 于集 中问题。由于弹簧夹 头尾 部直径  ̄4 m偏 大 ,弹簧夹 头经 淬火后 尺寸胀 大 ,工 9m
()由于弹簧夹头结构 形式的不合理 ,导致 弹簧夹 2
头淬火应 力过 于集 中 ,当内应 力 大 于材料 的 断裂 强度
时,就会出现裂纹 ,多年来一 直被人们沿袭使用。弹簧
缸板 一冷工 l: ‘加
星 笪 堡曼 口
维普资讯
圈
型
‰ 一 ,Ix A iF ei s
面有时出现批 量废 品。另外 ,在 加工滚 子硬 车倒 角时 , 原来弹簧夹头 内部有横向齿形和纵 向齿形 ,由于横 向齿 形的存在 ,弹簧夹头一般 夹住 23 / 滚子长 度 ,减少 了滚 子与夹头 内接触面积 ,也会导致滚子在夹 头内定位不稳 定 , 而减小夹头对滚子的夹紧力 ,同样 由于反复使用 从
裂纹 。由于夹 头弹 性变 形 区直 径壁 厚 4 m 尺寸 偏 小 , m
2 改进后弹簧夹头结构及淬火方式 .
()对滚子弹簧夹头结构进 行 了改进设 计 ,同时改 1
变弹簧夹头热处理淬火方式 。通过增 加弹簧夹头 弹性 变
形 区壁厚 、增大工作部位 与弹性变形 区 善弹簧夹 头的性能 。
种滚 子外 径表 面时 ,采用弹簧夹具定 位 ,因其定位精度
温少英
容易造成夹头磨钝 ,导致 滚子存在一定 的偏 心 ,就造成 滚子倒角偏差 ,出现 废品。
滚动轴承套圈数控车削缺陷分析及改进措施

序言目前,国内轴承行业的轴承套圈已经采用先进的数控车削加工技术。
生产实践中发现,轴承套圈在数控车削加工过程中,由于受到各种因素的影响,加工出来的工件不仅达不到规定的技术要求,还会出现各种各样的质量问题,从而造成不合格品甚至废品。
因此,必须进行质量分析,找出质量问题产生的原因,采取相应的纠正预防措施。
滚动轴承套圈数控车削加工过程中的常见缺陷有:车刀纹粗大、垫伤、漏工序、工件放偏、车削瘤、滚道留筋、振纹、倒角异常、挡边低及崩刀等。
有些缺陷出现在表面,很容易被发现,例如车刀纹粗大、漏工序等,可以将缺陷件挑出来后进行返工,经检验合格后流转至下道工序;有些缺陷如垫伤、倒角异常及挡边低等,必须将缺陷件挑出来做报废处理;另外一些缺陷,例如工件放偏、车削瘤及滚道留筋等,不容易被发现,若流入下道工序,则会带来质量隐患,甚至会导致产品报废。
下面以实例分析方式,对滚动轴承套圈数控车削加工过程中产生的缺陷进行原因分析并加以整理归纳,提出相应的改进措施。
缺陷分析与改进措施2.1 工件车刀纹粗大轴承套圈车削完成后,发现端面有非常明显的粗大车刀纹(见图1)。
产生这种缺陷的主要原因是车削刀具选用不合理,如刃口形状、角度不正确(如刀头太尖等),甚至刃口有缺陷;进刀速度快,进给量选择不合理;主轴的间隙大,车削过程中产生振动;材料硬度不合格,如果套圈锻件太硬或太软,则也会出现刀纹粗大问题。
图1端面车刀纹粗大针对该问题采取的改进措施如下。
1)选择合适的车削刀具、合理的进刀速度,调整机床主轴间隙在合适的范围。
2)要求轴承套圈锻件球化退火后硬度在合格范围之内(如GCr15轴承钢退火硬度为8 8~94HRB),这样可避免因硬度不合格而导致的车削刀纹粗大问题。
3)改善机床的刚度,避免机床、工件及刀具在车削过程中产生振动。
4)对于端面有明显车刀纹的轴承套圈,挑出来做报废处理,决不能流入下道工序。
2.2 工件垫伤数控车削后的轴承套圈端面或外径某部位有明显的凹坑,称为车削垫伤。
轴承厂改善提案

轴承厂改善提案随着工业及科学技术的高速发展,国内外数控、伺服机械产品普遍向高精度、重负荷、少振动、低噪声、高速、高寿命等方向发展,滚动轴承也不列外。
滚动轴承的制造技术、质量及精度要求也在不断地提高,对于轴承制造的母机一轴承加工的专用设备,在加工精度、生产效率、自动化控制程度等方面提出了更高的要求1轴承加工中存在的问题1.1轴承外圈的加工难点以某型铝合金材料关节轴承外圈(图1所示)为例,此套圈外径较大,壁厚最小处仅3.5mm,且尺寸及形位公差要求较高,加工过程中存在以下难点:1)只能采用车削加工,对机床精度要求较高;2)外圈薄壁、尺寸较大且精度要求高,由于薄壁本身有一定的弹性,加工过程中的切削力容易导致加工面产生振动,零件的尺寸及形位公差无法控制;3)切削夹紧力可能引起铝合金材料的冷变形;4)铝合金材料的塑性、韧性好,刀具在切削过程中使零件受到挤压,材料表面在切削方向上产生塑性变形,内部组织应力平衡被打破,导致零件发生变形而达不到预期的加工精度;5)铝合金材料线膨胀系数大(约为钢的2.4倍),车加工中产生的大量热易使零件变形。
1.2加工效率存在问题目前,通用型数控车床出厂标准配置附件为三爪自定心手动卡盘、手动尾座。
在生产过程中,零件装夹、尾座套筒的移动和顶紧零件都需要靠手动完成。
据笔者测算,就目前的通用型数控机床来说,批量加工一个轴承外圈内外径平均需要85秒,其中装夹零件的辅助时间约为60秒。
此种轴承零件在通用型数控车床上的装夹过程完全由手工完成,自动化程度低,操作者耗费大量的工作时间,用工成本大,无疑增加了企业的生产成本,降低了市场竞争力2改造措施2.1主轴夹紧部件改造1)根据轴承加工零件以轴线、对称中心为工序基准的特点,采用定心夹紧机构。
定心夹紧机构是以外圆柱面为定位基准线装夹零件的弹簧夹头构成的弹簧筒夹。
将弹性夹筒设计成一个锥型套筒,表面开出4~6条轴向槽,在结构上分成卡爪A、簧片B和导向部分C三个部分。
印刷机轴承车加工偏心夹具设计

印刷机轴承车加工偏心夹具设计发布时间:2022-06-26T03:21:44.578Z 来源:《城镇建设》2022年第4期第2月作者:李鹏孙传新[导读] 滚动轴承圈滚道的磨削加工使用夹具是电磁式无心夹具,这种模式特征是工件中心不与主轴中心重合,李鹏孙传新天津长荣科技集团股份有限公司天津市 300400摘要:滚动轴承圈滚道的磨削加工使用夹具是电磁式无心夹具,这种模式特征是工件中心不与主轴中心重合,加工精度备不受到主轴旋转精度的影响。
偏心轴承是一种使用非常广泛的轴承类型,优势显著,如结构简单使用方便,同时还具备的不需要偏心轴承就能实现偏心功能的特征,常常运用在印刷机和减速机等重型机械设备。
现阶段国内轴承行业磨削使用的偏心夹具,普遍使用通用磨床,利用偏心夹具本身偏心来让轴承偏心相对应来加工出合格的产品,实际生产中偏心夹具本身存在加工困难,工装精度低的情况。
文章通过对其进行优化、改进,解决了夹具设计存在的问题。
关键词:偏心轴承;偏心夹具;设计偏心轴承振动是一种十分复杂的物理现象,最大特征是轴承的内径和滚动不同心,偏心轴承的使用不仅仅和轴承零件的形位偏差和滚动表面形态特征、结构等相关,同时也因为工作条件的不同而产生变化。
因此使用常规的轴承加工方式来加工,则无法满足偏心轴承加工的需要,实际加工工艺也比实际轴承更复杂,实际加工难度也极大。
1.原偏心轴承夹具原有偏心轴承磨加工夹具是夹具本身具备偏心定位,通过夹具本体偏心和轴承偏心相抵消,偏心夹具内叫做偏心内圆,接触轴承内外径。
让夹具的外径和轴承的内径同心,通过装夹夹具的外径来加工轴承确定内径。
偏心夹具的加工:偏心夹具本身有偏心的特殊性,自身结构不对称,因此在加工夹具的时候主要难度在于加工偏心圆,使用坐标镗来加工,利用设备本身的精度来保证偏心加工的顺利完成。
在偏心轴承的加工使用中,加工偏心轴承的时候将夹具偏心内径和轴承圈套外径装紧固定和定位给适,以夹具的偏心来抵消轴承的偏心,则夹具外径、轴承内径同心[1]。
中大型轴承套圈高效车削解决方案

控制信号, 保存加工程序及参数 , 是整个控制系统 的核 心 。E S 2具 备 D D R V I 相 对定位 、 D D R V A绝对 定位 指令 , 方便 运 动程 序 编制 , 满 足 车床 控 制 系统
的需 要 。因为 X1 , X 2轴 为独 立 拖 板 , 工 作 中要 求 分 时或 同时动 作 , 并 无 插 补需 求 , 一 般数 控 系 统不
( 1 ) 人机 界面选 用 T D 2 2 0文本 显 示器 , 其 具有 2 0个按 键 , 可代替 部分 控制 柜 的机械 按钮 , 可 显示
1 2× 4行 汉 字 , 具备 R S 2 3 2 / R S 4 8 5通 信 口 , 可 实现
为提 高生 产效 率 , 车床 采用 2套拖板 。1 拖板 由z 1 轴与 l 轴 组成 , z 1 轴 由汽缸 驱动 , 完成 拖板 快速移 进 ; X 1轴 由伺 服 电动 机 驱 动 , 实 现 切 削进
各检 测开 关 控 制 按 钮 信 号 , 输 出各 驱 动 部 件 的
切 削进 给 , 仅 作 纵 向运 动 。两 拖 板 可 同时 工 作 或 错 时 工作 , 加上 分 段进 刀 程 序设 计 , 一 次 装 夹 可完 成 多个 加 工 工 序 。考 虑 到 经 济 性 与操 作 习 惯 , 车 床 未设 置 机械 零位 而采 用 浮动零 点 。
给 。2 拖 板 由伺 服 电动 机 驱 动 的 轴 组成 , 实现
加工 程 序 设 置 、 参 数 设 置 和 运 行 状 态 监 控 等 功
能 ¨。 ( 2 )选 用 的 P L C配 置为 D V P 3 2 E S 2 0 0 T+
调心球轴承外圈车加工方法改进

调心球轴承外圈车加工方法改进发布时间:2022-09-13T02:28:16.992Z 来源:《科技新时代》2022年2月第4期作者:张朋[导读] 我们加入轴承这一零部件的目的主要就是为了调节轴旋转的润滑条件,让轴和支撑点直接的摩擦张朋南京轴承有限公司江苏南京 210000摘要:我们加入轴承这一零部件的目的主要就是为了调节轴旋转的润滑条件,让轴和支撑点直接的摩擦可以减少,从而达到避免或者减少器件的损坏,节约成本支出的效果。
调心球轴承的主要特点就是重量相对来说较轻,而且重要的是,它能够像自动调心球一样,进行自动调,性能较好。
当然,调心轴承也具有一定的局限性,比如我们在使用的过程中,专用车床对自可能会出现产生毛刺的情况,同时这也会影响到外圈的质量。
还有就是在很多时候,我们安装轴承的过程中,钢球会遭到刮擦,这就会破坏旋转功能,影响轴承进行的自调心的工作。
面对以上这些问题,接下来,我们将通过研究外圈与倒角加工之间的关系,对加工顺序和加工方法进行调整和改进,以防止上述不良情况的发生。
关键词:调心球;轴承加工;车加工;优化策略前言首先,需要我们了解的是,调心球轴承的主要结构和功能,它的外围是一个球形的滚道,内圈可以看成是两个深沟滚道,主要功能当然就是具有调心性能。
调心球轴承的运用一般是为了保证那些难以做到同轴的零件可以实现同轴,从而可以有效发挥器件的各项功能,为我们生活所用,以产生它们的经济价值和使用价值。
一、调心球轴承加工难点由于调心球轴承的结构比较特殊,所以也会受各种因素的制约,最终可能会影响到质量状况。
在组装过程中会发生诸如旋转不灵活和对中性能低下之类的质量问题,在很多情况下,还会产生较大程度的误差,影响调心球轴承的工作性能。
当然,我们在发现这些质量不达标的产品时,不能直接投入安装和使用,必须积极进行修检工作,坚决不做豆腐渣工程。
生活中也经常会出现因为一些零件不达标,而不能继续使用、失去价值,成为废物的情况,这也就造成了浪人力和物力成本的浪费。
我国轴承套圈超精研技术的改进要点

我国轴承套圈超精研技术的改进要点我曾经在《怎么样提高高精度轴承的超精质量?》一文中写到:“超精加工主要要提高和改善被加工工件表面的微观质量,这些微观质量包括粗糙度、沟形、圆度和金属条纹的走向。
”轴承套圈沟道超精研工序主要是为了降低被加工沟道的粗糙度,这是最基本的要求,无论是最原始的棍棒超精机还是采用无心支撑结构的自动化超精机,原理大同小异,都是如此。
高水平的和低档的轴承套圈超精研设备的主要区别是轴承套圈沟道形状精度的改善程度和被加工工件表面应力状态的差异。
轴承套圈沟道形状精度的改善主要取决于三个方面:首先,要约束超精前的轴承沟道磨加工形状的基础精度,轴承沟道的基准精度和位置精度在磨削工序也要精确地控制,因为这些需要约束的被加工工件的磨削工序的精度及其对超精加工的结果的影响是不容忽视的;其次,超精研设备的制造精度也会对被超精工件沟道表面形状的变化起到很大的影响,品质较差的超精机非但不能够改善磨削工序形成的形状精度,反而会破坏磨削工序形成的形状精度;第三,超精余量的大小不仅与超精加工的节拍有关,而且也与轴承沟道超精后的表面质量有关系。
假如我们的轴承产品没有对轴承的噪音和轴承的寿命提出特殊的要求,假如我们的轴承产品仅仅满足于参与国内外市场的低价格竞争,假如我们的轴承产品不想走出国门或者不想替代进口产品,那么,使用低价位的超精研设备是可以的。
因为,在中低档产品的轴承市场上,中国的轴承企业打了很多顽强的战役,在空调类家电市场和电机市场,我们的微型和小型轴承取得了不俗的销售业绩,这些成绩的取得也部分得益于我国轴承加工设备的发展和进步。
而在我国高精尖产品领域,大量的高附加值高利润轴承还是依靠进口。
我国生产的最好的轴承设备,即使出口到国外,也只是应用在普通轴承生产线上;部分大陆境内的外资和合资的轴承加工企业采购国内的轴承设备,也主要用在中低档轴承的生产线上。
迄今为止,我国高水平的进口轴承设备所占的比率很小,部分原因是由于高水平的进口轴承设备的价格普遍高于国产的轴承设备,其主要原因还是国内大部分企业生产的轴承精度和效率要求偏低,在引进更好水平的进口轴承设备方面的要求还不是特别强烈。
特大型薄壁轴承套圈加工中的问题与改进

摘要 : 大型薄壁轴承 由于直径大且套 圈壁厚较 薄 , 特 加工 比较 困难 。针对特大型薄壁轴 承加工 中经 常 出现 的 问 题, 采取了相应改进措施 , 达到了 良好的效果。 关键词 : 薄壁轴承 ; 圈 ; 套 电磁无心夹具 ; 车加工 ; 磨加工 ; 热处理 中图分类 号 :H13 3 ;H1 1 5 T 3 .3 T 6 . 文献标志码 : B 文章编号 :0 0—36 ( 0 7 0 0 2 0 10 7 2 2 0 ) 8— 0 2— 2
快, 笔尖 不 够锋利 。针 对 此 , 磨 削 用 砂 轮 的 硬度 将
内应力及外加工应力 等。因此我们可 以在车削加 工 中 间增加 消 除应力 退火 工 序 , 以减小 淬 火 变形 。 消 除应力 退 火 的退火 温 度 为 60— 7 I, 火 时 0 60c 退 二
间 为 4—8h 。据 统 计 , 除应 力 退 火 可使 淬 火后 消 的变 形 量减 少三 分 之 一左 右 。消 除 应力 退 火 可 在
加 工要 求 。
2 热 处 理 变 形
对 于特 大 型 薄壁 轴 承 套 圈 , 处 理 后 极 易 发 热 生形 状 公 差 严 重 超 差 现 象 。导 致 变 形 的 主 要 原 因 : 方面 是套 圈 内部 组 织发 生 相 变 , 一方 面 是 一 另
使 以上两项指标超差 。砂轮存 在较多钝化磨粒的 原因一方面是砂轮硬度高 , 自锐性差 , 磨粒不易脱 落 , 一方 面 是修 正 砂 轮 用 的金 刚 笔 笔 尖 磨 损 较 另
正 , 差 较大 。且套 圈径 向 没有 支 承 力 , 有 效 壁 误 在
粗车后 , 精车后各进行一次 , 也可 以只进行一次消 除应 力退 火 。 只进 行一次 消除应 力退 火 的 , 好放 最
- 1、下载文档前请自行甄别文档内容的完整性,平台不提供额外的编辑、内容补充、找答案等附加服务。
- 2、"仅部分预览"的文档,不可在线预览部分如存在完整性等问题,可反馈申请退款(可完整预览的文档不适用该条件!)。
- 3、如文档侵犯您的权益,请联系客服反馈,我们会尽快为您处理(人工客服工作时间:9:00-18:30)。
过后拉 杆推 动销子 通过 导 向底 座使 卡 头 向右 移 动
时, 在弹簧箍的收缩作用下 , 使卡头恢复到原始状
态( 4 。 图 )
分体式瓣 状弹簧胀卡是各部位分别受力 , 而
1 导向部分 ;一簧瓣 ;一卡爪 一 2 3
1 传 统 的整 体 式 弹簧 胀 卡
1 1 结构及 工作原 理 .
图1 所示 为整 体式 弹簧胀 卡 结 构 。其 工 作 原 理为 : 当原始 作用 力 F 通 过 后 拉杆 连 带 小 拉 杆 使 弹簧 卡头 向左 移 动 时 , 用 胀 芯 的锥 面 作 用 使 弹 利
F
簧胀卡的簧瓣扩张 , 从而对工件定心夹紧; 当原始 作 用力 F通过后 拉杆 推动 销子使 弹 簧胀 卡 向 右移 动时 , 通过弹簧胀卡簧瓣 的 自身收缩 , 使卡头恢复 到放松 状态 ( 2 。对 于不 同型 号 的工 件需 要 更 图 ) 换 不 同 的弹簧 胀卡 。
维普资讯
曼 ! = 2 Q
C 1一l 4 / H N4 18T
轴承
B a i g2 0 No 1 e rn 0 8, . 0
2 0 年 1期 08 O
5 0—5 1
轴承 套圈车 削加工用弹簧胀卡的改进
苏 中安 , 党虹 宇 , 王成 凯
卡为例 。整 体 式 胀 卡 的 材 料 利 用 率 仅 为 1 % 左 5 右 , 体式 弹簧 卡 头 的材 料 利用 率 可 达 7 % 左 而分 0
右 。显 著提 高 了材 料 利 用率 , 对 原 材料 规 格 尺 且 寸 的要 求也 降低 了。
3 改进 前 、 胀 卡 的 对 比 后
( ) 工过程 。整 体 式 胀 卡 的 结构 决 定 其对 1加 车制加工 技术 的要 求 较 高 , 同时 由于卡 爪 的硬 度 和簧瓣 的硬度要 求不 同 , 要 满足 卡爪 的高硬度 、 既 高耐磨性 , 又要满 足簧瓣 的 良好 韧性 , 得 热处理 使 工 艺较复 杂 、 定 性 差 。分 体 式 弹簧 胀 卡 由分 开 稳
不是胀 卡 的整 体 受 力 , 头 的收缩 是 以弹 簧箍 的 卡
图 1 整体式弹簧胀卡结构
弹力为作用力 , 而不是簧瓣 的 回弹力 。结构上采 用分体式四瓣设计 , 通过弹簧箍束紧 , 向底座与 导 分 体 式瓣 状 弹 簧 卡头 之 间 通过 卡 隼 连 接 ; 组 成 各
收 稿 日期 :0 8— 5—0 ; 回 日期 :0 8 5— O 20 0 5修 2 0 —0 2
( 瓦轴辽 阳轴承制造有 限责任公 司, 宁 辽 阳 1 1 0 辽 10 ) 关键 词: 动轴 承; 滚 套圈 ; 车削 ; 卡具 ; 弹簧胀卡
中图分类号 :'13 3 ;G 1T 7 1 1 '- 3 .3 T S ;G 5 . 1I 1 文献标 志码 : B 文章编号 :00— 7 2 20 )0— 0 0—0 1 36 (0 8 1 0 5 2
12 存 在 的问题及 分析 .
1 后 拉 杆 ;一 销 子 ; 一 胀 芯 底 座 ; 一 定 位 环 底 座 ; 一 定 位 环 ; 一 2 3 4 5
6 弹簧卡头 ;一胀芯 ;一小拉 杆;一工件 一 7 8 9
() 1 卡爪与 簧 瓣 断 裂 。 由于 整 体 式 弹 簧 胀 卡 的导 向部分 与 卡 爪 的 淬 火硬 度 要 求不 一致 , 爪 卡 为 5 6 R 簧瓣 为 4 4 R 热 处理 工 艺 5~ 0H C, O~ 5H C,
维普资讯
苏中安等 : 轴承套圈车削加工用弹簧胀卡的改进
・ 1・ 5
部分可 以单 独进 行 热 处 理 ; 当某 一 部位 失 效 时 可 以单独更换 维修 ; 向底座 可 以采 取通 用 化设 计 , 导 不 同型号 之 间只需更换分 瓣式 弹簧卡 头 。
图 2 整 体 式 弹 簧 胀 卡 工作 原理
() 3 卡爪 磨 损 。 由于 整体 式 胀 卡 在 淬火 过 程
较复杂。当热处理不当时, 就会使簧瓣部分 的硬
度不稳 定 , 性不够 , 韧 卡爪 与簧 瓣就 可能 断裂 。 () 2 簧瓣 与 导 向部 分 断裂 。 由于 工 作 时 产 生 的 弹力 集 中作用 在 簧瓣 与导 向部 分 的连 接 部 位 , 且 簧 瓣 强度 较低 , 相对 薄 弱 的部 位 容 易 产 生 断 使
裂。
中是分段回火, 工艺不易掌握 , 使卡爪的淬火硬度
偏 低 。造成 卡爪过早 磨损源自无法夹 紧工件 。 ( ) 用 寿命 短 。实 测使 用 寿命 大 约 为每 个 4使
弹簧胀 卡加 工 500件套 圈 。 0
2 改进 后 的分 体 式 瓣状 弹簧 胀 卡
图 3所 示为分 体式 瓣 状 弹簧 胀卡 结 构 。其工 作原理 为 : 当原始 作 用 力 F通 过 后 拉 杆 连 带 小拉 杆使 卡头 向左 移 动 时 , 用 胀 芯 的 锥 面 作 用使 卡 利
5 6 7 8 9
l 一导向底座 ;一弹簧箍 ;一 弹簧卡头 2 3
的两部分构 成 , 以分别 进行 淬 火 , 可 不仅 降低 了热
处理 工艺 的复杂程 度 , 加 了稳 定性 , 且可 以对 增 而
m
¨
图 3 分 体 式 瓣 状 弹 簧 胀 卡 结 构
各部 分 的质 量要求 进行分别 控制 。 () 2 使用寿命与性价 比。分 体式胀 卡 由于卡爪 的硬度得 到提 高 , 磨性 提 高 , 效地 解决 了整体 耐 有 式胀卡 由于热处理硬 度 、 作用 力集 中等原 因导致 的 过早失效 , 了使用 寿命 。并 且 由于导 向底 座 的 提高 通用性 , 提高 了使用效率 , 减少 了工装制作费用 。 () 3 材料利 用率 。 以制作 内径为 10m 的胀 5 m