铝合金的熔炼与铸造
铝合金熔炼与铸造工艺规范与流程
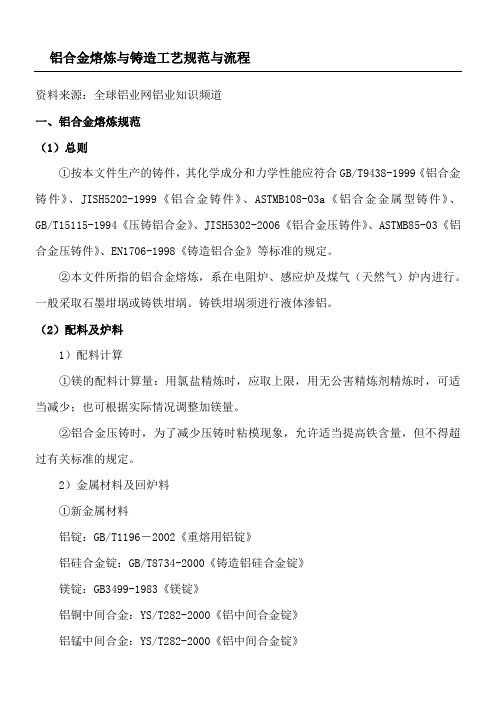
铝合金熔炼与铸造工艺规范与流程资料来源:全球铝业网铝业知识频道一、铝合金熔炼规范(1)总则①按本文件生产的铸件,其化学成分和力学性能应符合GB/T9438-1999《铝合金铸件》、JISH5202-1999《铝合金铸件》、ASTMB108-03a《铝合金金属型铸件》、GB/T15115-1994《压铸铝合金》、JISH5302-2006《铝合金压铸件》、ASTMB85-03《铝合金压铸件》、EN1706-1998《铸造铝合金》等标准的规定。
②本文件所指的铝合金熔炼,系在电阻炉、感应炉及煤气(天然气)炉内进行。
一般采取石墨坩埚或铸铁坩埚。
铸铁坩埚须进行液体渗铝。
(2)配料及炉料1)配料计算①镁的配料计算量:用氯盐精炼时,应取上限,用无公害精炼剂精炼时,可适当减少;也可根据实际情况调整加镁量。
②铝合金压铸时,为了减少压铸时粘模现象,允许适当提高铁含量,但不得超过有关标准的规定。
2)金属材料及回炉料①新金属材料铝锭:GB/T1196-2002《重熔用铝锭》铝硅合金锭:GB/T8734-2000《铸造铝硅合金锭》镁锭:GB3499-1983《镁锭》铝铜中间合金:YS/T282-2000《铝中间合金锭》铝锰中间合金:YS/T282-2000《铝中间合金锭》各牌号的预制合金锭:GB/T8733-2000《铸造铝合金锭》、JISH2117-1984《铸件用再生铝合金锭》、ASTMB197-03《铸造铝合金锭》、JISH2118-2000《压铸铝合金锭》、EN1676-1996《铸造铝合金锭》等。
②回炉料包括化学成分明确的废铸件、浇冒口和坩埚底剩料,以及溢流槽和飞边等破碎的重熔锭。
回炉料的用量一般不超过80%,其中破碎重熔料不超过30%;对于不重要的铸件可全部使用回炉料;对于有特殊要求(气密性等)的铸件回炉料用量不超过50%。
3)清除污物为提高产品质量,必须清除炉料表面的脏物、油污、废铸件上的镶嵌件,应在熔炼前除去(可用一个熔炼炉专门去除镶嵌件)。
铝合金的熔炼与浇铸

铝合金的熔炼与浇铸6.5.1铝合金的性能及应用铝合金是比较年轻的材料,历史不过百年,铝合金以比重小,强度高著称,可以说没有铝合金就不可能有现代化的航空事业和宇航事业,在飞机、导弹、人造卫星中铝合金所占比重高达90%,是铸造生产中仅次于铸铁的第二大合金,其地壳含量达7.5%,在工业上有着重要地位。
铝合金有良好的表面光泽,在大气及淡水中具有良好的耐腐蚀性,故在民用器皿制造中,具有广泛的用途。
纯铝在硝酸及醋酸等氧化性酸类介质中具有良好的耐蚀性,因而铝铸件在化学工业中也有一定的用途。
纯铝及铝合金有良好的导热性能,放在化工生产中使用的热交换装置,以及动力机械上要求具有良好导热性能的零件,如燃机的汽缸盖和活塞等,也适于用铝合金来制造。
铝合金具有良好的铸造性能。
由于熔点较低(纯铝熔点为660℃,铝合金的浇注温度一般约在730~750℃左右),故能广泛采用金属型及压力铸造等铸造方法,以提高铸件的在质量、尺寸精度和表面光洁程度以及生产效率。
铝合金由于凝固潜热大,在重量相同条件下,铝液的凝固过程时间延续比铸钢和铸铁长得多,其流动性良好,有利于铸造薄壁和结构复杂的铸件。
铸造铝合金的分类、牌号:铝合金按照加工方法的不同分为两大类,即压力加工铝合金和铸造铝合金(分别以YL和ZL表示)。
在铸造铝合金中又依主要加入的合金元素的不同而分为四个系列,即铸造铝硅合金、铸造铝铜合金、铸造铝镁合金和铸造铅锌合金(分别以 ZL1X X,ZL2 X X,ZL3 X X和ZL4 X X表示),在每个系列中又按照化学成分及性能的不同而分为若干牌号。
表1中列出了铸造铝合金国家标准所包括的几种铝合金的牌号。
6.5.2 铝合金的熔炼设备合金熔炼的目的是要获得符合一定成分和温度要求的金属熔液。
不同类型的金属,需要采用不同的熔炼方法及设备。
如钢的熔炼是用转炉、平炉、电弧炉、感应电炉等;铸铁的熔炼多采用冲天炉;而非铁金属铝合金的熔化通常采用坩埚电阻炉,炉子的大小一般为30-500kg,电热体有金属(铁铬合金)、非金属(碳化硅)两种,是广泛用来熔化铝合金的炉子,优点是:炉气呈中性,金属也不会强烈氧化,炉温便于控制,操作简单,劳动条件好。
铝合金_实验报告

一、实验目的1. 掌握铝合金熔炼的基本原理和工艺流程。
2. 了解铝合金的铸造方法及其对性能的影响。
3. 通过性能测试,分析铝合金的力学性能。
二、实验原理铝合金是一种轻质高强度的金属材料,广泛应用于航空航天、汽车制造、建筑等领域。
本实验主要研究铝合金的熔炼、铸造及性能测试。
1. 铝合金熔炼:将铝及其他合金元素加热至熔点,使其熔化并形成均匀的熔体。
2. 铝合金铸造:将熔化后的铝熔体浇注到铸模中,使其冷却凝固成铸锭或铸件。
3. 性能测试:通过拉伸试验、硬度测试等方法,分析铝合金的力学性能。
三、实验内容及步骤1. 实验材料:铝锭、合金元素、铸模、熔炼炉、浇注系统、拉伸试验机、硬度计等。
2. 实验步骤:(1)熔炼:将铝锭和合金元素放入熔炼炉中,加热至熔点,使铝及其他合金元素熔化。
(2)铸造:将熔化后的铝熔体浇注到铸模中,使其冷却凝固成铸锭。
(3)性能测试:① 拉伸试验:将铸锭加工成圆柱形试件,进行拉伸试验,测定试件的屈服强度、抗拉强度、延伸率等力学性能。
② 硬度测试:将铸锭加工成标准硬度试件,进行硬度测试,测定试件的布氏硬度。
四、实验结果与分析1. 熔炼结果:熔炼过程中,铝锭和合金元素熔化良好,熔体成分均匀。
2. 铸造结果:铸锭表面光洁,无气孔、裂纹等缺陷。
3. 性能测试结果:(1)拉伸试验:屈服强度为X MPa,抗拉强度为Y MPa,延伸率为Z %。
(2)硬度测试:布氏硬度为A HB。
根据实验结果,分析如下:1. 铝合金熔炼过程中,加热温度、保温时间、搅拌速度等因素对熔体质量有重要影响。
本实验中,加热温度控制在铝的熔点以上50~100℃,保温时间为30分钟,搅拌速度适中,保证了熔体质量。
2. 铸造过程中,铸模材料、浇注温度、冷却速度等因素对铸锭质量有重要影响。
本实验中,铸模材料为耐高温合金,浇注温度控制在铝的液相线温度以上,冷却速度适中,保证了铸锭质量。
3. 铝合金的力学性能与其成分、组织结构等因素有关。
铝合金熔炼与铸造工艺规范与流程

铝合金熔炼与铸造工艺规范与流程Revised by Chen Zhen in 2021铝合金熔炼与铸造工艺规范与流程资料来源:全球铝业网铝业知识频道一、铝合金熔炼规范(1)总则①按本文件生产的铸件,其化学成分和力学性能应符合GB/T 9438-1999《铝合金铸件》、JISH 5202-1999《铝合金铸件》、ASTM B 108-03a《铝合金金属型铸件》、GB/T 15115-1994《压铸铝合金》、JISH 5302-2006《铝合金压铸件》、ASTM B 85-03《铝合金压铸件》、EN1706-1998《铸造铝合金》等标准的规定。
②本文件所指的铝合金熔炼,系在电阻炉、感应炉及煤气(天然气)炉内进行。
一般采取石墨坩埚或铸铁坩埚。
铸铁坩埚须进行液体渗铝。
(2)配料及炉料1)配料计算①镁的配料计算量:用氯盐精炼时,应取上限,用无公害精炼剂精炼时,可适当减少;也可根据实际情况调整加镁量。
②铝合金压铸时,为了减少压铸时粘模现象,允许适当提高铁含量,但不得超过有关标准的规定。
2)金属材料及回炉料①新金属材料铝锭:GB/T 1196-2002《重熔用铝锭》铝硅合金锭:GB/T 8734-2000《铸造铝硅合金锭》镁锭: GB 3499-1983《镁锭》铝铜中间合金:YS/T 282-2000《铝中间合金锭》铝锰中间合金:YS/T 282-2000《铝中间合金锭》各牌号的预制合金锭:GB/T 8733-2000《铸造铝合金锭》、JISH 2117-1984《铸件用再生铝合金锭》、ASTM B 197-03《铸造铝合金锭》、JISH 2118-2000《压铸铝合金锭》、EN1676-1996《铸造铝合金锭》等。
②回炉料包括化学成分明确的废铸件、浇冒口和坩埚底剩料,以及溢流槽和飞边等破碎的重熔锭。
回炉料的用量一般不超过80%,其中破碎重熔料不超过30%;对于不重要的铸件可全部使用回炉料;对于有特殊要求(气密性等)的铸件回炉料用量不超过50% 。
铝合金的熔炼与铸造
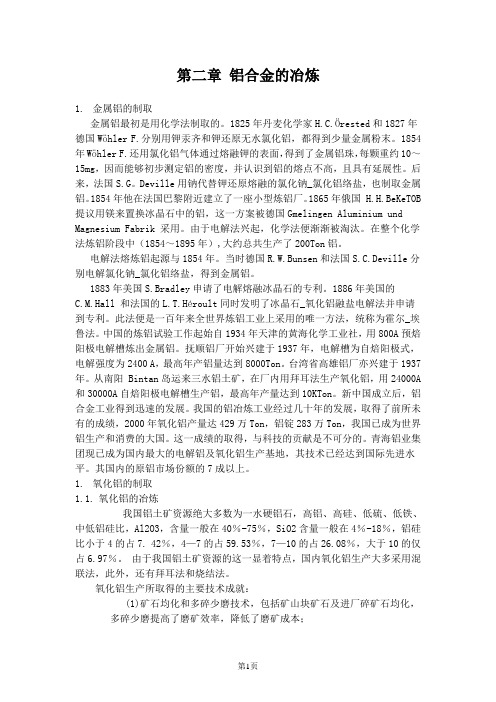
第二章铝合金的冶炼1.金属铝的制取金属铝最初是用化学法制取的。
1825年丹麦化学家H.C.Örested和1827年德国Wöhler F.分别用钾汞齐和钾还原无水氯化铝,都得到少量金属粉末。
1854年Wöhler F.还用氯化铝气体通过熔融钾的表面,得到了金属铝珠,每颗重约10~15mg,因而能够初步测定铝的密度,并认识到铝的熔点不高,且具有延展性。
后来,法国S.G。
Deville用钠代替钾还原熔融的氯化钠_氯化铝络盐,也制取金属铝。
1854年他在法国巴黎附近建立了一座小型炼铝厂。
1865年俄国 H.H.BeKeTOB 提议用镁来置换冰晶石中的铝,这一方案被德国Gmelingen Aluminium und Magnesium Fabrik 采用。
由于电解法兴起,化学法便渐渐被淘汰。
在整个化学法炼铝阶段中(1854~1895年),大约总共生产了200Ton铝。
电解法熔炼铝起源与1854年。
当时德国R.W.Bunsen和法国S.C.Deville分别电解氯化钠_氯化铝络盐,得到金属铝。
1883年美国S.Bradley申请了电解熔融冰晶石的专利。
1886年美国的C.M.Hall 和法国的L.T.Héroult同时发明了冰晶石_氧化铝融盐电解法并申请到专利。
此法便是一百年来全世界炼铝工业上采用的唯一方法,统称为霍尔_埃鲁法。
中国的炼铝试验工作起始自1934年天津的黄海化学工业社,用800A预焙阳极电解槽炼出金属铝。
抚顺铝厂开始兴建于1937年,电解槽为自焙阳极式,电解强度为2400 A,最高年产铝量达到8000Ton。
台湾省高雄铝厂亦兴建于1937年。
从南阳 Bintan岛运来三水铝土矿,在厂内用拜耳法生产氧化铝,用24000A 和30000A自焙阳极电解槽生产铝,最高年产量达到10KTon。
新中国成立后,铝合金工业得到迅速的发展。
我国的铝冶炼工业经过几十年的发展,取得了前所未有的成绩,2000年氧化铝产量达429万Ton,铝锭283万Ton,我国已成为世界铝生产和消费的大国。
铝合金熔炼与铸造技术

铝合金熔炼与铸造技术一、引言铝合金是一种重要的结构材料,具有轻质、高强度和良好的耐腐蚀性能,在航空航天、汽车制造、建筑工程等领域广泛应用。
铝合金的制备过程中,熔炼与铸造技术起到关键作用,本文将对铝合金熔炼与铸造技术进行详细探讨。
二、铝合金熔炼技术2.1 熔炼原料准备熔炼铝合金的原料主要包括铝、合金元素和辅助材料。
铝采用高纯度的铝锭,合金元素可以通过添加铝合金粉末或其他化合物来实现。
辅助材料包括熔剂、脱气剂等。
这些原料的准备对于保证铝合金的成分和质量非常重要。
2.2 熔炼设备和工艺熔炼铝合金的常用设备有电阻加热炉、感应加热炉和气体燃烧炉等。
其中,感应加热炉在铝合金熔炼中应用最广泛,具有加热速度快、能耗低和温度控制准确等优点。
熔炼工艺包括预热、熔化、调温和净化等步骤,其中净化技术对于铝合金的纯净度和性能起到重要作用。
2.3 熔炼过程控制与优化熔炼过程中,熔体温度、保温时间、搅拌方式等因素对铝合金的成分和组织结构有重要影响。
熔炼过程需要进行温度控制、气氛控制和搅拌控制等,以确保铝合金的成分均匀、杂质含量低。
三、铝合金铸造技术3.1 铸造方法铝合金的常用铸造方法包括压铸、重力铸造、低压铸造和砂型铸造等。
压铸是最常用的铸造方法,适用于生产复杂形状和尺寸精度要求高的铝合金件。
重力铸造适用于大型铝合金零部件的生产,低压铸造适用于长条状和壳状铝合金件的生产,砂型铸造适用于非常大型和特殊形状的铝合金件的生产。
3.2 铝合金铸造过程铝合金的铸造过程主要包括熔炼、准备模具、浇注、冷却和后处理等步骤。
熔炼过程中,需要根据具体合金配方和要求,控制熔体温度、浇注温度和浇注速度等参数。
准备模具是确保铸造件尺寸和表面质量的重要环节。
浇注过程需要保证熔体充分填充模腔,并避免气孔和缺陷的产生。
冷却过程中需控制冷却速率,以避免铝合金件出现应力和变形。
3.3 铝合金铸造工艺改进为了提高铝合金铸造件的质量和效率,可以采取一些工艺改进措施。
铝合金的实习报告

实习报告:铝合金生产工艺及应用一、实习背景及目的随着我国经济的快速发展,铝合金作为一种重要的金属材料,其在建筑、汽车、航空等领域的应用越来越广泛。
为了更好地了解铝合金的生产工艺及其应用,提高自己的实践能力,我参加了为期一个月的铝合金生产实习。
本次实习主要在一家专业的铝合金生产企业进行,通过实地观察、操作和与员工的交流,我对铝合金的生产工艺及应用有了更深入的了解。
二、实习内容与过程1. 铝合金的熔炼与铸造实习的第一周,我主要了解了铝合金的熔炼与铸造过程。
铝合金的熔炼是在高温下将铝及其合金元素熔化,并通过精炼、除杂等手段提高铝合金的纯度和质量。
铸造则是将熔化的铝合金倒入模具中,冷却凝固成型的过程。
在这一过程中,我了解到铝合金的熔炼温度、熔炼时间、精炼方法等因素对铝合金质量的影响。
2. 铝合金的挤压与拉伸实习的第二周,我参与了铝合金的挤压与拉伸过程。
挤压是将铝合金熔体通过挤压机,使其通过模具,形成所需形状和尺寸的工艺过程。
拉伸则是将铝合金坯料在拉伸机上进行拉伸,以获得所需的拉伸强度和塑性。
在这一过程中,我了解到挤压与拉伸工艺参数(如挤压速度、拉伸速度、温度等)对铝合金性能的影响。
3. 铝合金的表面处理实习的第三周,我学习了铝合金的表面处理技术。
表面处理是为了提高铝合金的耐腐蚀性、耐磨性等性能,主要包括阳极氧化、电镀、涂层等工艺。
在这一过程中,我了解到不同表面处理工艺对铝合金性能的影响及其应用领域。
4. 铝合金的应用实习的第四周,我了解了铝合金在建筑、汽车、航空等领域的应用。
铝合金因其优良的性能,在建筑领域广泛应用于门窗、幕墙等;在汽车领域,铝合金用于车身、发动机等部件;在航空领域,铝合金则是飞机结构材料的主要选择。
在这一过程中,我认识到铝合金在现代工业中的重要地位。
三、实习收获与反思通过本次实习,我对铝合金的生产工艺及其应用有了更深入的了解,认识到理论知识与实际生产相结合的重要性。
在实际生产过程中,要注重工艺参数的优化,严格控制产品质量,提高生产效率。
铝合金熔炼与铸造

1. FILD法(无烟在线脱气法)
在耐火坩埚或耐火砖衬里 的容器中,用耐火隔板将容 器分成两个室。从静置炉中 流出的铝液,经倾斜流槽进 入第一室,在熔剂覆盖下进 行吹氮脱气和除渣,然后通 过涂有熔剂的氧化铝球滤床 除去夹渣,再流到第二室, 通过氧化铝球滤床,以除去 铝液夹带的熔剂和夹渣。
2. SNIF法(旋转喷气净化法)
2.组合式结晶器:一般用于Cu、Al及其合金 圆锭,Al及其合金扁锭上。
圆锭用结晶器,组成:内套— Cu : T2、铜 合金、石墨,Al : LD5、LY11 。外壳— 铸 铁、钢、锻Al。
易大常细量形硬加化的AA系成脆入晶lT-熔li-C熔来粗 相 少 粒C炼u炼u-技-M技首 先 原 材 料 的 清 洁 度 要 高 然 后 加 强 对 熔 体 的 精 炼 除 气 最 每 个 熔 次 后 要 彻 底 大 清 炉其 次 操 作 时 避 免 频 繁 搅 动 熔 体M术g术g-特-F特FSF量 下e点eei-点系、控 限N/NiN制 并i=i在 使含1
续直接水冷铸锭法。其中包括可调液流的中间包 或炉头箱、漏斗、结晶器、引锭托座和铸造机等 部分。
特点
优点:
1.液流平稳、减少了吸气和夹渣。
2.直接水冷,冷却强度大,结晶速度快, 组织致密
3.自下而上连续结晶,有利于排气和补缩。
4. 生产连续进行,几何废料少,成品率 高。
5.易实现机械化、自功化,铸坯质量较好。
• 由美国联合碳化物公司开发的,是一 种最新的、效率最高的、最易操作的 在线式精练工艺。
• 特点:省时节能;无环境污染;战地 面积小;熔体质量高等。
影响熔剂除渣精炼效果的因素
➢精炼温度:一般先用高温进行除渣精 炼,然后在较低的温度下进行脱气, 最后保温静置。
铝合金的熔炼与铸造(Meltingandcastingofaluminumalloy)

铝合金的熔炼与铸造(Melting and casting of aluminum alloy)Melting and castingMelting and pouring of aluminum alloy is the main link in casting production. The whole process of melting and casting is strictly controlled, which plays an important role in preventing casting defects such as pinholes, inclusions, castings, cracks, porosity and shrinkage. Because the aluminum melt absorbs the hydrogen tendency, the oxidation ability is strong, dissolves the iron easily, in smelting and the casting process, must take the simple and careful preventive measure, obtains the high-quality casting.1 、 preparation and quality control of aluminum alloy burdenIn order to smelt high quality aluminum melt, the qualified raw material should be selected first. To carry out scientific management and proper processing of raw materials, otherwise it will seriously affect the quality of the alloy, the production practice has proved that the raw materials (including metal materials and auxiliary materials) lax control will make batch scrap castings.(1) raw materials must have qualified chemical composition and organization, and the specific requirements are as follows:In addition to the analysis of the main components and impurities in the alloy ingots, the microstructure and fracture of the alloy were examined. Practice has proved that the use of serious shrinkage cavity, pinhole, and bubbles of aluminum liquid, it is difficult to obtain dense castings, and even causethe whole furnace, batch castings scrapped.It was found in the study of Al Si alloy ingots of Aluminum Alloy pinhole, does not appear in the molten pure sand casting pinhole test block, when the aluminum silicon alloy ingot with low and unqualified specimens, pinhole serious, and the grain size large. The reason is the heredity of the material. The heredity of Al Si alloy and heredity increased with the increase of content and the amount of silicon reached 7%. Continue to increase silicon content to eutectic component, heredity decreases slightly again. In order to solve the casting defects caused by the heredity of the burden, aluminum ingots, intermediate alloys and other charging materials with high metallurgical quality must be selected. Specific standards are as follows:(1) there should be no pinholes or holes in the fracture surfacePinhole shall be within grade three, and local (not exceeding 25% of the inspected area) shall not exceed three grade. Over three grade shall be taken by means of heavy smelting to reduce the degree of puncture. Remelting refining method and the general Aluminum Alloy smelting, casting temperature should not exceed 660 degrees, for the original grain large aluminum ingot, alloy ingot, should be the first to use the lower mold temperature, making them rapid solidification, grain refinement.2 、 burden treatmentBefore using the burden, it should be treated by blowing sandto remove the surface rust, grease and other dirt. The time is not long, Aluminum Alloy ingot and metal scrap surface is clean without blowing sand, but should be in charge of the elimination of mixed iron filters and inserts, all shall be in charge of preheating furnace, to remove the surface of the water, shorten the melting time in 3 hours above.3 、 management and storage of burdenReasonable storage and management of burden is important to ensure the quality of alloy. The burden shall be stored in a dry warehouse with little change in temperature.2 、 preparation of crucible and melting tools(1) crucible casting aluminum alloy commonly used iron crucible, also can use cast steel and steel plate welding crucible.New and old is not for a long time in the crucible crucible, before use should be blowing sand, and heated to 700--800 degrees, to keep 2--4 hours, to burn water and attached to the inner wall of the crucible of combustible material, to be cooled to 300 degrees below, carefully clean the inside of the crucible, at a temperature not lower than 200 degrees when spraying paint.The crucible should be preheated to dark red (500--600 degrees) before use and kept warm for more than 2 hours. Before the new outer crucible melting, melting scrap with the best grades of a furnace.(two) preparation of smelting toolsZhong Zhao, press ladle, mixing spoon, ladleAt the other before use shall be preheated, and at 150 degrees ---200 degrees temperature, coated with a protective coating, and thorough drying, the drying temperature is 200--400 degrees, holding time of 2 hours, after use should be thoroughly removed attached on the surface of oxide and fluoride (preferably blowing sand).3, smelting temperature controlThe melting temperature is too low, is not conducive to the dissolution of alloying elements and gas inclusions, discharge, tendency segregation, cold shut, undercasting increase formation, but also because of insufficient heat riser, the casting without reasonable feeding, has information that,The melting temperature of all aluminum alloys should be up to 705 degrees and should be stirred. The melting temperature is too high, not only a waste of energy, more serious is because the higher the temperature, the hydrogen absorption of the grain becomes thick, aluminum oxide is more serious, some of the burning loss of alloy elements is more serious, which leads to a decrease in the mechanical properties of the alloy, casting the deterioration of mechanical properties and modification, weaken the effect of air the castings reduce.The production practice shows that the molten alloy rapid heating to high temperature, reasonable stirring to dissolve all alloy elements (especially refractory metals), scrapingscum down after the pouring temperature, so that the minimum degree of segregation, melting of hydrogen is less favorable, to obtain the uniform and compact alloy mechanical properties high. Because the aluminum melt temperature is difficult to determine with the naked eye, so no matter what type of the melting furnace, should use temperature control instrument. The instrument should be regularly checked and the maintenance cycle should thermowell with metal brush clean, coated with a protective coating, in order to ensure the accuracy and prolong the service life of the measurement result.4 、 control of smelting timeIn order to reduce the oxidation, gettering and dissolution of molten aluminum, the residence time and rapid melting of molten aluminum should be shortened. From the beginning of the melt to the end of the casting, the sand casting shall not exceed 4 hours, the die casting shall not exceed 6 hours, and the die casting shall not exceed 8 hours.In order to speed up the smelting process, should first join the scrap aluminum silicon intermediate alloy medium size, low melting point, in order to accompany the formation of molten pool as soon as possible in the crucible bottom, then add the returns for larger pieces and pure aluminum ingot, so that they can gradually expand slowly immersed in molten pool, fast melting. When the main part of the furnace is melted, the intermediate alloy with higher melting point and small quantity is melted and stirred to accelerate the melting. Finally, cool down and press the oxidizable alloy elements to reduce the loss.5, melt transfer and pouringAlthough the density of the solid alumina is similar to the density of the aluminum melt, it will take a long time to sink to the bottom of the crucible after entering the interior of the molten aluminum. Alumina film is oxidized and aluminum melt formation, but only in contact with the molten aluminum side is dense, and exposed to the air side loose and there is a lot of 60--100A diameter holes, its large surface area, strong adsorption, easy adsorption in water vapor, the tendency of anti floating. Therefore, in this film and aluminum melt proportion difference is small, be mixed with the melt, and the speed is very slow, it is difficult to exclude from the melt, porosity inclusion formation in castings too. Therefore, the key to transfer aluminum melt is to minimize the agitation of molten metal and minimize the contact between the melt and the air.By tilting the crucible melt injection, in order to avoid mixing melt and air, should be as far as possible by the ladle furnace nozzle, and inclined, melt down along the side wall of the ladle, no direct impact on the bottom of the bag, occurrence of agitation, splash.The proper and reasonable pouring method is one of the important conditions to obtain high quality castings. In the production practice, it is effective to prevent and reduce casting defects by paying attention to the following items.(1) the temperature of the melt, the capacity of the ladle and the degree of dryness of the coating on the surface shall beexamined carefully before pouring, and whether the preparation of other tools meets the requirements or not. The metal gate Cup before casting 3--5 minutes in the sand on a good place, the ladle with the temperature less than 150 degrees for premature or excessive temperature, pouring tract hold large amounts of gas, there is a danger of explosion when pouring.(two) not in the "draught" casting occasions, as well as strong melt oxidation, combustion, the casting defects such as oxide inclusions.(three) obtained by melt in the crucible, should first use of bottom oxide layer or the flux through gently melt surface, slowly immersed in the melt with the ladle, ladle a wide mouth melt, and then gently lift the ladle.(four) the end of the package should not be flat; the pace should be steady; the ladle should not be raised too high; the metal level in the ladle must be stable and free from movement.(five) to be cast, with net ladle slag should be,In order to avoid pouring slag, oxide, etc. into the mold.(six) in the casting, the melt flow is stable, can not be interrupted, not into the mouth with the bottom. Sprue should be full from beginning to end, liquid level shall not turn, casting speed should be properly controlled. Usually, the casting starts slightly slower, filling the melt, stabilizing it, then slightly faster, and keeping the casting speed constant.(seven) in the pouring process, pouring ladle and gate distance as close as possible, not more than 50 mm limit, so as not to melt too much oxidation.(eight) with a blocked gate, the plug cannot be dialed too early. After the melt has filled the gate, it is slowly tilted out so as to prevent the melt from producing eddy current when it is injected into the sprue.(nine) the melt less than 60 mm from the bottom of the crucible shall not be poured into the casting.Aluminum alloy casting (ZL)According to the main elements other than aluminum, silicon, copper, magnesium and zinc are divided into four kinds, and the codes are 100, 200, 300 and 400 respectively.In order to obtain high quality precision castings of various shapes and specifications, aluminum alloys for casting usually have the following characteristics.(1) a narrow slot filled with good liquidity part(2) there is a melting point lower than that of a general metal, but it can meet most of the requirements(3) the thermal conductivity is good, the heat of molten aluminum can be transferred rapidly to the mold, and the casting cycle is shorter(4) hydrogen and other harmful gases in the melt can be effectively controlled by treatment(5) Aluminum Alloy casting, no cracking and tearing cracking tendency(6) good chemical stability and strong corrosion resistance(7) it is not easy to produce surface defects, the casting surface has good surface finish and gloss, and easy to surface treatment(8) Aluminum Alloy casting processing performance is good, can die, die, sand and dry sand mold, gypsum type casting casting, vacuum casting, can also be used for low and high pressure casting, extrusion casting, semi-solid casting, centrifugal casting forming method, with different purposes, different varieties of production specifications and different properties of various castings.Cast aluminum alloy has been widely used in cars, such as cylinder head, intake manifold, piston, wheel hub, steering booster housing, etc.。
铝合金熔炼与铸造

铝合金熔炼与铸造铝合金是一种常见且广泛使用的金属材料,具有较低的密度、良好的导热性和耐腐蚀性,因此在许多行业中得到了广泛的应用。
铝合金的熔炼和铸造是制造铝合金制品的关键步骤。
本文将介绍铝合金熔炼和铸造的基本原理、工艺和注意事项。
一、铝合金熔炼1.1 熔炼原理铝合金熔炼的主要原理是将铝及其他合金元素加热至其熔点,使其融化成液态,以便进行后续的铸造工艺。
铝的熔点较低,约为660°C,因此相对较容易熔化。
而其他合金元素的加入可以改变铝合金的性质,例如提高其强度、耐腐蚀性或者改善加工性能。
1.2 熔炼工艺铝合金熔炼工艺一般分为两种:批量熔炼和连续熔炼。
批量熔炼是将一定量的铝和其他合金元素加入炉内,通过加热熔化成液态,并进行充分混合。
这种方法适用于小规模生产,常用的炉型有电阻炉和燃气炉。
而连续熔炼是将铝合金材料加入熔炉的顶部,通过炉内的加热和熔化过程,使得底部的液态铝合金不断流出。
这种方法适用于大规模生产,常用的炉型有回转炉和隧道炉。
1.3 熔炼注意事项在铝合金的熔炼过程中,需要注意以下几个方面。
首先,炉内的温度需要控制在适当的范围内,以避免过度燃烧或者过度冷却。
其次,需要保持良好的熔炼环境,防止氧气、水分或杂质等对炉内材料的影响。
最后,在加入其他合金元素时,需要根据配比和工艺要求进行准确的添加,以保证最终铝合金的性能。
二、铝合金铸造2.1 铸型设计铝合金铸造的第一步是进行铸型设计。
铸型设计的目的是根据最终产品的形状和要求,确定合适的铸造方法和材料,以及适当的铸型结构。
常见的铸型结构有砂型、金属型和陶瓷型等。
其中砂型是最常用的铸造方法,可以应用于各种形状和尺寸的产品。
2.2 铸造工艺铝合金的铸造工艺可以分为传统铸造和压铸两种。
传统铸造是将熔融的铝合金液体倒入铸型中,并通过自然冷却形成最终产品。
这种方法适用于小批量生产,但精度和表面光滑度相对较低。
压铸是将高压液压机将铝合金液体注入铸型中,通过压力传递和快速冷却,实现快速成型。
铝合金的熔炼和砂型铸造成型的流程
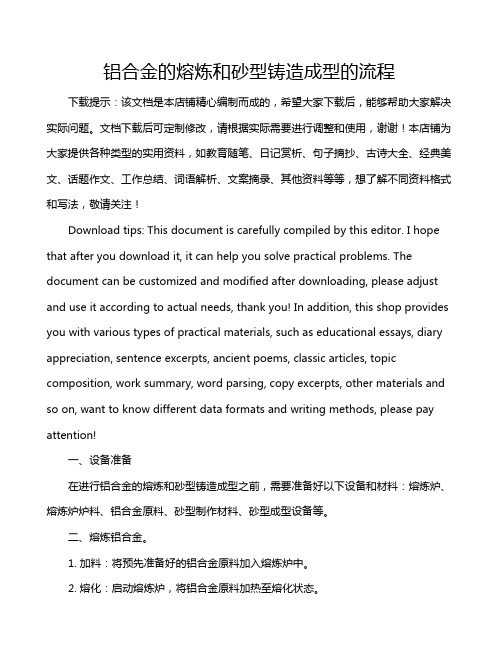
铝合金的熔炼和砂型铸造成型的流程下载提示:该文档是本店铺精心编制而成的,希望大家下载后,能够帮助大家解决实际问题。
文档下载后可定制修改,请根据实际需要进行调整和使用,谢谢!本店铺为大家提供各种类型的实用资料,如教育随笔、日记赏析、句子摘抄、古诗大全、经典美文、话题作文、工作总结、词语解析、文案摘录、其他资料等等,想了解不同资料格式和写法,敬请关注!Download tips: This document is carefully compiled by this editor. I hope that after you download it, it can help you solve practical problems. The document can be customized and modified after downloading, please adjust and use it according to actual needs, thank you! In addition, this shop provides you with various types of practical materials, such as educational essays, diary appreciation, sentence excerpts, ancient poems, classic articles, topic composition, work summary, word parsing, copy excerpts, other materials and so on, want to know different data formats and writing methods, please pay attention!一、设备准备在进行铝合金的熔炼和砂型铸造成型之前,需要准备好以下设备和材料:熔炼炉、熔炼炉炉料、铝合金原料、砂型制作材料、砂型成型设备等。
铝合金的熔炼、铸锭与固溶处理

铝合金的熔炼、铸锭与固溶处理一、实验目的:掌握铝合金熔炼的基本原理,并应用在熔炼的实践中。
熔炼是使金属合金化的一种方法,它是采用加热的方式改变金属物态,使基体金属和合金组元按要求的配比熔制成成分均匀的熔体,并使其满足部纯洁度、铸造温度和其他特定条件的一种工艺过程。
熔体的质量对铝材的加工性能和最终使用性能产生决定性的影响,如果熔体质量先天不足,将给制品的使用带来潜在的危险。
因此,熔炼又是对加工制品的质量起支配作用的一道关键工序。
而铸造是一种使液态金属冷凝成型的方法,它是将符合铸造的液态金属通过一系列浇注工具浇入到具有一定形状的铸模(结晶器)中,使液态金属在重力场或外力场(如电磁力、离心力、振动惯性力、压力等)的作用下充满铸模型腔,冷却并凝固成具有铸模型腔形状的铸锭或铸件的工艺过程。
铝合金的铸锭法有很多,根据铸锭相对铸模(结晶器)的位置和运动特征,可将铝合金的铸锭方法分类如下:二、实验容:铝铜合金熔炼基本工艺流程三、实验要求严格控制熔化工艺参数和规程1. 熔炼温度熔炼温度愈高,合金化程度愈完全,但熔体氧化、吸氢倾向愈大,铸锭形成粗晶组织和裂纹的倾向性愈大。
通常,铝合金的熔炼温度都控制在合金液相线温度以上50~100℃的围。
从图1的Al-Cu相图可知,Al-5%Cu的液相线温度大致为660~670℃,因此,它的熔炼温度应定在710(720)℃~760(770)℃之间。
浇注温度为730℃左右。
图1 铝铜二元状态图2.熔炼时间熔炼时间是指从装炉升温开始到熔体出炉为止,炉料以固态和液态形式停留于熔炉中的总时间。
熔炼时间越长,则熔炉生产率越低,炉料氧化吸气程度愈严重,铸锭形成粗晶组织和裂纹的倾向性愈大。
精炼后的熔体,在炉中停留愈久,则熔体重新污染,成分发生变化,变形处理失效的可能性愈大。
因此,作为一条总的原则,在保证完成一系列的工艺操作所必需的时间的前提下,应尽量缩短熔炼时间。
3.合金化元素的加入方式与铝相比,铜的比重大,熔点虽高(1083℃),但在铝中的溶解度大,溶解热也很大,无需将预热即可溶解,因此,可以以纯金属板的形式在主要炉料熔化后直接加入熔体中,亦可与纯铝一同加入。
铝合金熔炼与铸造简介课件

目录
• 铝合金熔炼基础 • 铝合金熔炼工艺 • 铝合金铸造技术 • 铝合金的应用 • 铝合金熔炼与铸造的挑战与未来发展
01
铝合金熔炼基础
铝合金的特性
01
02
03
物理特性
铝合金具有优良的导电性 、导热性和耐腐蚀性。
化学特性
铝合金易于氧化形成致密 的氧化膜,具有良好的耐 腐蚀性。
熔炼设备
常用的熔炼设备有坩埚炉 、电炉、感应炉等。
熔炼工艺参数
包括熔炼温度、熔炼时间 、熔炼气氛等,这些参数 对铝合金的性能和成分有 重要影响。
02
铝合金熔炼工艺
熔炼前的准备
原材料选择
配料计算
选择高质量的原材料,如铝锭、合金 元素和添加剂,以确保熔炼出的铝合 金具有所需的性能。
根据产品要求,计算所需的原材料配 比,以获得所需的化学成分和性能。
理。
热处理
根据需要,对铸件进行 热处理以提高其机械性
能。
铸造后处理
清理
去除铸件表面的毛刺、飞边等杂质,确保表 面质量。
质量检测
对铸件进行质量检测,确保其符合相关标准 和客户要求。
机械加工
对铸件进行机械加工,以满足其使用要求。
包装运输
对铸件进行包装,并选择合适的运输方式将 其送达目的地。
04
铝合金的应用
THANK YOU
感谢观看
模具准备
设计和制作铸造模具,确保其 结构合理、尺寸精确。
设备检查
对熔炼炉、浇注机等设备进行 检查和调试,确保其正常运转
。
工艺准备
制定合理的铸造工艺流程,明 确各环节的技术要求和操作规
范。
铸造过程
铝合金的熔炼与铸造

针孔应在三级以内,局部(不超过受检面积的25%)不应超过三级,超过三级者必须采取重熔炼的办法以减少针孔度。重熔精炼方法与一般铝合金熔炼相同,浇铸温度不宜超过660℃,对于那些原始晶粒大的铝锭、合金锭等,应先用较低的锭模温度,使它们快速凝固,细化晶粒。
2、炉料处理
(二)熔炼工具的准备
钟罩、压瓢、搅拌勺、浇包
锭模等使用前均应预热,并在150度---200度温度下涂以防护性涂料,并彻底烘干,烘干温度为200--400度,保温时间2小时以上,使用后应彻底清除表面上附着的氧化物、氟化物,(最好进行吹砂)。
3、熔炼温度的控制
熔炼温度过低,不利于合金元素的溶解及气体、夹杂物的排出,增加形成偏析、冷隔、欠铸的倾向,还会因冒口热量不足,使铸件得不到合理的补缩,有资料指出,所有铝合金的熔炼温度到少要达705度并应进行搅拌。熔炼温度过高不仅浪费能源,更严重的是因为温度愈高,吸氢愈多,晶粒亦愈粗大,铝的氧化愈严重,一些合金元素的烧损也愈严重,从而导致合金的机械性能的下降,铸造性能和机械加工性能恶化,变质处理的效果削弱,铸件的气密性降低。
5、熔体的转送和浇注
尽管固态氧化铝的密度近似于铝熔体的密度,在进入铝熔体内部后,经过足够长的时间才会沉至坩埚底陪。而铝熔体被氧化后形成的氧化铝膜,却仅与铝熔体接触的一面是致密的,与空气接触的一面疏松且有大量直径为60--100A的小孔,其表面积大,吸附性强,极易吸附在水汽,反有上浮的倾向。因此,在这种氧化膜与铝熔体的比重差小,将其混入熔体中,浮沉速度很慢,难以从熔体中排除,在铸件中形成气孔太夹杂。所以,转送铝熔体中关键是尽量减少熔融金属的搅拌,尽量减少熔体与空气的接触。
(五)即将浇注时,应扒净浇包的渣子,以免在浇注中将熔渣、氧化皮等带入铸型中。
铝合金的熔炼与铸造

铝合金的熔炼与铸造铝合金的熔炼与铸造发布时间:2012-4-3 21:37:13 | 38 人感兴趣| 评分:3 | 收藏:01 配料及其计算配料是熔体铸的第一道工序。
它的首要任务是控制成分和杂质含量使之符合要求,其次是根据对合金的加工和使用性能的要求,确定各种炉料品种及配料比;再次是正确地计算每炉的全部炉料量。
合理地吊装各种原辅材料,管理好各种金属及废料(旧料)。
铝合金熔炼时,炉料大致分为三类,即:工业纯金属,或称新料或新金属;回炉的金属或合金废料,也称旧料或返回料;以及中间合金或配制合金用的纯金属。
正确地选择配制合金的炉料,对于合金成分控制,铸锭质量的保证,以及金属原料的节约,都有重要的意义。
总之,在保证性能合乎要求的前提下,允许利用各种废料,节约新金属和贵重金属。
换句话说,就是能用废料应少用纯金属,能用低品位纯金属绝不用高品位的纯金属。
做到废料用尽,次料代替好料,好料精用,搭配适当,保证质量。
1.1 工业纯金属--新料铝合金是在纯金属熔炼的基础上,加上其它合金元素配制而成.因此,在配制合金以前,首先应依所需配制的合金成分的要求,选择所需的纯金属之品位。
有色金属的工业纯金属多来源于冶炼厂,如工业纯铝(称原铝),工业纯铜(称紫铜或电解铜),工业纯镁,以及金属镍等都是从电解工厂制得的。
原铝多铸成15-20公斤的小锭(称铝锭);镁以锭状供应,镁锭的重量可分为2.5公斤和9公斤两种;纯铜和金属镍一般多以电解铜板和电解镍板的形式供应;金属锌一般铸成重40公斤左右的扁平锌锭,而金属锰和铬分别以不同的粒度供应。
这些所谓的纯金属中,杂质仍是不可避免的。
例如,原铝锭中仍含有Fe和Si两种主要杂质。
它们大多数是从炼铝原料---铝矿石中带来的。
这两种杂质元素对铝及其合金的性能有极大的影响,因而使用原铝锭时,必须注意这些杂质的含量,根据所配制合金的要求正确地选用原铝锭。
铝冶炼厂生产的原铝新料,是按所含铁和硅二种主要杂质元素的多少而定其品位的。
第3章-熔炼和铸造
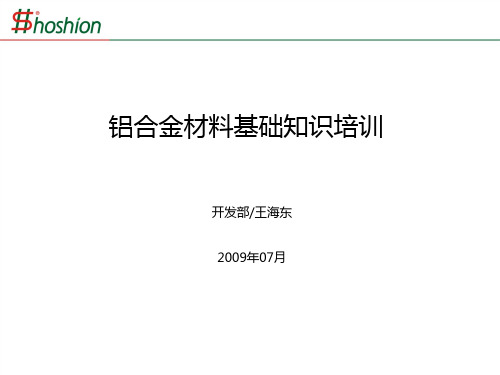
可见提高燃烧的气流速度是有效的 。 2、合金元素的溶解和蒸发 熔炼温度下(700℃)几种元素在铝中的扩散系数为(cm2/s): Ti:0.66,Mo:1.38(760℃),Co:0.79,Ni:1.44,Si:14.4, 通常情况下,与铝形成易熔共晶的元素,一般较易熔解,与铝形成包晶 转变的,特别是熔点相差大的元素较难于溶解。 在相同溶解条件下,一般蒸气压高的元素容易挥发,可把常用的铝合金 分为两组:Cu、Cr、Fe、Ni、Ti、Si、V、Zr等元素的蒸气压比铝的小, 蒸发慢,Mn、Li、Mg、Zn、Na、Cd等元素蒸气压比铝的大,容易蒸 发,在熔炼过程中损失较大。
三、熔体的净化过程
有色金属及其合金熔体在熔炼过程中存在气体、各种非金属夹杂物等, 影响金属的纯洁度,往往会使铸锭产生气孔、夹杂、疏松、裂纹等缺陷, 影响铸锭的加工性能及制品的强度、塑性、抗蚀性、阳极氧化性和外观质 量。 所谓的净化,即是利用物理化学原理和相应的工艺措施,除掉液态金属 中的气体、夹杂和有害元素以便获得纯净金属熔体的工艺方法。熔体净化 包括传统的炉内精炼和后来发展的炉外净化过程。 一般来说,铝熔体含氢量应控制在0.15~0.20ml/100g.Al以下,对于一 些特殊要求的应控制在0.10ml/100g.Al以下。 氢气在熔体中的熔解量与温度的关系如下:
铝及铝合金净化处理可分为吸附净化和非吸附净化。具体包括: 炉内处理: a.惰性气体吹洗法 b.活性气体吹洗法 c.混合气体吹洗法 d.气体—溶剂混合吹洗法 e.静态真空处理 f.动态真空处理 其中:e、f为非吸附净化 常用的溶剂中都含有C2Cl6。C2Cl6为白色晶体,密度为2091kg/m3。 C2Cl6与铝熔体反应生成C2Cl4 和Cl2。其分别和铝熔体继续反应生成AlCl3、 HCl等。 C2Cl6的升华温度为185.5℃,C2Cl4的沸点为121℃,不熔于铝。工业通用 的溶剂是各种碱金属的氯盐和氟盐的混合物。他的净化作用主要是通过其 吸附和熔解氧化夹杂的能力。氯化钾和氯化钠盐等的混合物,对氧化铝有 极强的润湿和吸附能力。氧化铝特别是悬混于熔体中氧化铝碎片,被具有 凝聚性和润湿性的溶剂吸附包围后,便改变了氧化物的性质、密度及形态, 通过上浮很快被除去。 加入少量的氟盐(NaF、Na3AlF6、CaF2)增加熔融金属与杂质之间的表 面张力,提高了溶剂的分离性,防止产生溶剂夹杂。
- 1、下载文档前请自行甄别文档内容的完整性,平台不提供额外的编辑、内容补充、找答案等附加服务。
- 2、"仅部分预览"的文档,不可在线预览部分如存在完整性等问题,可反馈申请退款(可完整预览的文档不适用该条件!)。
- 3、如文档侵犯您的权益,请联系客服反馈,我们会尽快为您处理(人工客服工作时间:9:00-18:30)。
铝合金的熔炼与铸造发布时间:2012-4-3 21:37:13 | 38 人感兴趣| 评分:3 | 收藏:01 配料及其计算配料是熔体铸的第一道工序。
它的首要任务是控制成分和杂质含量使之符合要求,其次是根据对合金的加工和使用性能的要求,确定各种炉料品种及配料比;再次是正确地计算每炉的全部炉料量。
合理地吊装各种原辅材料,管理好各种金属及废料(旧料)。
铝合金熔炼时,炉料大致分为三类,即:工业纯金属,或称新料或新金属;回炉的金属或合金废料,也称旧料或返回料;以及中间合金或配制合金用的纯金属。
正确地选择配制合金的炉料,对于合金成分控制,铸锭质量的保证,以及金属原料的节约,都有重要的意义。
总之,在保证性能合乎要求的前提下,允许利用各种废料,节约新金属和贵重金属。
换句话说,就是能用废料应少用纯金属,能用低品位纯金属绝不用高品位的纯金属。
做到废料用尽,次料代替好料,好料精用,搭配适当,保证质量。
1.1 工业纯金属--新料铝合金是在纯金属熔炼的基础上,加上其它合金元素配制而成.因此,在配制合金以前,首先应依所需配制的合金成分的要求,选择所需的纯金属之品位。
有色金属的工业纯金属多来源于冶炼厂,如工业纯铝(称原铝),工业纯铜(称紫铜或电解铜),工业纯镁,以及金属镍等都是从电解工厂制得的。
原铝多铸成15-20公斤的小锭(称铝锭);镁以锭状供应,镁锭的重量可分为2.5公斤和9公斤两种;纯铜和金属镍一般多以电解铜板和电解镍板的形式供应;金属锌一般铸成重40公斤左右的扁平锌锭,而金属锰和铬分别以不同的粒度供应。
这些所谓的纯金属中,杂质仍是不可避免的。
例如,原铝锭中仍含有Fe 和Si两种主要杂质。
它们大多数是从炼铝原料---铝矿石中带来的。
这两种杂质元素对铝及其合金的性能有极大的影响,因而使用原铝锭时,必须注意这些杂质的含量,根据所配制合金的要求正确地选用原铝锭。
铝冶炼厂生产的原铝新料,是按所含铁和硅二种主要杂质元素的多少而定其品位的。
纯铜内所含杂质元素种类很多,所以一般工业纯铜基本上是按照铜的含量多少而定其品位的。
总的来讲,在选择金属品位时,为了保证质量,应尽量选择杂质较少,纯度较高的高品位的纯金属;但纯度越高,生产越困难,成本也越高,因而应尽量避免使用过高纯度的原料,以节约生产成本。
因此正确地选用金属原料的品位,在配料过程中是十分重要的。
铝合金中常用的金属原料有铝锭,镁锭,紫铜板、锌锭和用于制作中间合金的电解镍板,金属锰,金属铬,结晶硅以及海棉钛,海棉锆等。
1.2 废料--回炉料1.2.1废料的来源和使用原则废料,又称回炉料,也叫旧料。
按其来源不同,大致可分为本厂废料及厂外废料两大类.(1)本厂废料这部份废料来源于熔铸车间及各加工车间各工序所得的加工余料(一般称几何废料)及不合格的报废料(一般称工艺废料)。
铝合金成品率一般在60~80%左右,也就是说,将有20-40%的原料在加工过程中变成废料。
这部份废料大致都有可能保持质量不受掺杂,是高质量的废料,是熔炼铝合金的重要原料之一。
对本厂废料要加以仔细分离、分级,并按合金归类分组保管。
只要管理得好,这些废料一般都能保持良好的质量,不受掺杂,污染及混料,在工厂里称为一级废料或二级废料。
这部份废料通常不需处理就可以直接入炉使用。
只有从车床,刨床,锯床等回炉的铣,锯、刨边碎屑料,常被油污或氧化,或含杂质过多,这些料质量低劣,通常称之为三级废料。
这部份废料不能直接入炉,事先要经过洗涤,干燥处理,再重熔复化,经化验取得准确的成分后才能入炉使用.在使用废料时,要求入炉的废料不得混合金,混级,应清洁无油泥污染。
如果混料,则宁愿将少量的低成分合金(低合金)混于高成分合金(高合金),不可使少量的高成分合金混于低成分合金。
例如,纯铝混入LF21合金中,则用于LF21合金炉料中;防锈铝(LF2--LF21)各合金废料分别混于L Y12合金中;则可用于L Y12合金炉料中;LD6合金废料混于LD2合金中,则可用于LD5合金炉料中;LD7、LD8,LD9合金废料互混在一起,则可酌量用于LD8合金或LD9合金中。
有的合金废料互混在一起,则不能用于生产,如LD10合金料混入LC4合金中,则必须挑选后,经检查确定无混料时,方能分别用于该合金炉料中。
还有一些合金废料互混后,又难于挑选,不易检查分辨的,应重熔复化,取得准确的成分后方可作为炉料。
另外,某些废料,虽未混料,但放置时间过长,严重腐蚀,或油泥污染严重的,也应回炉重熔复化。
总的来讲,所有牌号不明,成分含量不清,腐蚀污染严重的一级和二级废料和车,刨、铣、锯碎屑都不能直接入炉,属于工厂里规定的三级废料范围,应重熔复化。
(2) 厂外废料源于用制造工厂或市场上回收的废料,大都掺杂混合,其质量多不可靠,甚至无准确的化学成分,最好不直接入炉使用。
如确实保证不掺杂其它金属者,方可按本厂废料分级归类使用。
必须注意,这些厂外回收废料,往往含有一般化验方法难于检查出来的有害杂质元素,其含量即使仅万分之一,甚至十万分之一,也会严重影响产品质量及工艺性能。
因此,凡制造高质量的产品,最好不使用这些厂外回收废料。
那些化学成分不明,或不符合标准的杂料,有时被称为化学废料,工厂里也称之为号外料.也应当进行复化重熔,明确其化学成分后,才能适量入炉.1.2.2 废料的分级和归类管理铝合金废料的分离,分级,按合金系统门类保管的要求是十分严格的。
因为铝合金一经混杂入炉,就无法使之除去,除非加入大量纯金属予以冲淡。
因此管理好废料,正确的使用废料对保证产品质量,降低消耗,节约金属极为重要。
某些铝合金的成分含差异很大,如果一种合金废料混入另一种合金,即使数量不多,也会造成废料无法使用。
例如,超硬铝中含Zn 量都很高,而其它系列铝合金中要求含Zn量却很低,如果有5-10%的超硬铝合金废料混入L Y12合金炉料中,就会使炉料全部报废。
又如Al-Cu-Mg-Fe-Ni系锻造铝合金中含Ni量都在1.0%以上,而其它铝合金中一般要求含Ni量低于0.1%,当有百之几的高Ni废料混入其它合金炉料中,同样会造成全炉报废。
如果各合金废料互混在一起,废料中同时含有较多量的Si,Zn、Ni等元素。
那么此废料很难用于任何一种铝合金铸锭生产中,即使用量少也可能形成杂质元素的恶性循环,影响产品的机械性能及加工性能。
其结就只好积压大批废料而使用较多的新金属,浪费金属材料。
因此对本厂废料要分合金或按合金系统严格管理。
所有一、二级废料必须分合金装架打捆,三级废料应按合金系统归类装箱,所有废料都必须合理分组归类堆放,而且要有明显的标牌或标示。
在铝合金铸锭生产中,某些制品由于用途不同,要求其杂质含量和铸锭的内部质量也不相同、因而对炉料的几何尺寸和表面清洁度的要求也不一样。
例如,制作大梁、型材,和锻件的合金铸锭,要求其杂质含量较低,非金属夹杂物愈少愈好,其炉料一般不用碎片及薄板和油泥较多的废料。
因而,各种合金废料除不混料外,还必须按照工艺规程的规定,根据废料的外形尺寸和表面清洁度而分级装架和堆码。
铝合金废料一般分四级,一二级废料可直接入炉熔制成品合金铸锭,某些特殊制品不得使用二级废料;三、四级废料须经干燥,重熔复化,分析化学成分后才能使用。
下表列出了某生产厂的废料分类。
废料分级的标准铝合金一,二级废料存放专区的划分LC4,LC5、LC6,LC9、LC10,LB1LD7,LD8,LD9LD2、LD5、LD10LF2、LF3、LF5、LF6、lF11、LF12、LT66等L1-7、LB2、LF21L Y11、L Y2,L Y16,L Y17,等L Yl1、LT2,LT2-1工艺过程中产生的一、二级废料是分合金,按不同的级别装架或打捆,每架,每捆废料的上,中、下部多处应标明合金牌号和级别;大块废料用钢印在其端部打上合金牌号及熔次号,并尽快返回熔铸车间。
实际上,一种合金的生产不是连续的,而是间断式周期性的生产。
各工序的废料是按照产生→运输→积存→待用的规律循环着。
在这些过程中,由于吊装、堆码等多方面的原因,料架与料架之间,捆与捆之间仍有混料的可能。
为了减少再次混料的几率,便于配料吊装,所有的一、二级废料应按合金成分含量归类,每类合金存放在指定的区域内统一称之为废料专区。
废料专区的划分应根据合金的化学成分,品种规格和料场情况而合理归类,—而般而言,铝合金一、二级废料场可分为高锌、高镍、高硅、高镁、纯铝和L Y12及L Y11专区,因L Yl2,L Y11合金的生产量大,可单列一专区存放。
按合金分级装架,打捆的一、二级废料必须存放在规定的专区内。
备专区内的料架或整捆废料要放置平稳可靠,不易倾倒,滑动,并要定期清理,核对,以免发生混料,混级.生产中的三级废料大多为细碎之残屑,分合金装箱、堆放是有困难的,一般都分组装箱,堆放,分组重熔复化。
当然也可将三级废料分合金堆放,复化,这要视工艺要求条件而合理安排。
生产实践表明,三级废料只要不混组,经重熔复化后,都可作为合金铸锭生产的原料。
四级料也称号外料,大部份是成分不清的混合料。
由于四级料质量低劣,成分复杂,必须重熔复化,因此,四级料也是复化料的一部份。
如果废料管理得好,四级废料是极少的,生产中要求四级料越少越好.混合料经重熔复化后, 用于成品合金炉料时,要仔细调配各杂质元素的含量,并视合金性能的要求少量用于生产。
1.3 配料计算配料计算是合金铸锭生产的重要工序,是合金成分及杂质含量控制的首要关卡,它的首要任务是控制成分和杂质含量使之符合要求;根据合金的加工和使用性能的要求,确定各种炉料品种的配料比;正确地计算出每炉的全部炉料量。
1.3.1 使用纯(新)金属和废料的比例在确定配料比例时,应根据下列一些原则:(1)考虑到经济原则,在保证产品质量和性能的前提下,根据合金制品用途和加工工艺的要求,应充分利用本身废料,降低新料用量,做到能自身平衡,即该合金加工的产生的废料,能全部回炉使用。
例如,在熔制L Y1l及L Yl2、LC4合金的板材时,某些熔次可全部使用lOO%的本身一、二级废料;而另一些熔次则可使用一部份低合金及纯铝废料,同时配入一部份复化料及少量新金属。
(2)在考虑尽可能使用低品位纯金属的原则下,还应注意到废料循环使用及操作上的原因所造成的杂质逐渐增加,使原料晶位逐步降级。
例如在熔制工业纯铝时,为防止杂质增高而使品位降级,不但应限制废料用量不超过50%,而且应使用一部份比制品要求品位高一级的原料,例如,全部使用新铝熔制L3纯铝时,常用50%的A1-1品位的原铝和50%A1-0品位的原铝锭。
(3)对质量要求较高的制品,应尽量少用废料,而选用高品位新铝。
例如生产LY12合金的大梁型材,一般只允许使用20%以下的废料,甚至全部用原铝锭和新料,并且还要求选用Al-0品位以上的原铝锭。