加工中心与数控铣手工编程实例
数控铣床编程实例

第五节数控铣床编程实例(参考程序请看超级链接)实例一毛坯为70㎜×70㎜×18㎜板材,六面已粗加工过,要求数控铣出如图3-23所示的槽,工件材料为45钢。
1.根据图样要求、毛坯及前道工序加工情况,确定工艺方案及加工路线1)以已加工过的底面为定位基准,用通用台虎钳夹紧工件前后两侧面,台虎钳固定于铣床工作台上。
2)工步顺序①铣刀先走两个圆轨迹,再用左刀具半径补偿加工50㎜×50㎜四角倒圆的正方形。
②每次切深为2㎜,分二次加工完。
2.选择机床设备根据零件图样要求,选用经济型数控铣床即可达到要求。
故选用XKN7125型数控立式铣床。
3.选择刀具现采用φ10㎜的平底立铣刀,定义为T01,并把该刀具的直径输入刀具参数表中。
4.确定切削用量切削用量的具体数值应根据该机床性能、相关的手册并结合实际经验确定,详见加工程序。
5.确定工件坐标系和对刀点在XOY平面内确定以工件中心为工件原点,Z方向以工件表面为工件原点,建立工件坐标系,如图2-23所示。
采用手动对刀方法(操作与前面介绍的数控铣床对刀方法相同)把点O作为对刀点。
6.编写程序按该机床规定的指令代码和程序段格式,把加工零件的全部工艺过程编写成程序清单。
考虑到加工图示的槽,深为4㎜,每次切深为2㎜,分二次加工完,则为编程方便,同时减少指令条数,可采用子程序。
该工件的加工程序如下(该程序用于XKN7125铣床):N0010 G00 Z2 S800 T1 M03N0020 X15 Y0 M08N0030 G20 N01 P1.-2 ;调一次子程序,槽深为2㎜N0040 G20 N01 P1.-4 ;再调一次子程序,槽深为4㎜N0050 G01 Z2 M09N0060 G00 X0 Y0 Z150N0070 M02 ;主程序结束N0010 G22 N01 ;子程序开始N0020 G01 ZP1 F80N0030 G03 X15 Y0 I-15 J0N0040 G01 X20N0050 G03 X20 YO I-20 J0N0060 G41 G01 X25 Y15 ;左刀补铣四角倒圆的正方形N0070 G03 X15 Y25 I-10 J0N0080 G01 X-15N0090 G03 X-25 Y15 I0 J-10N0100 G01 Y-15N0110 G03 X-15 Y-25 I10 J0N0120 G01 X15N0130 G03 X25 Y-15 I0 J10N0140 G01 Y0N0150 G40 G01 X15 Y0 ;左刀补取消N0160 G24 ;主程序结束实例二毛坯为120㎜×60㎜×10㎜板材,5㎜深的外轮廓已粗加工过,周边留2㎜余量,要求加工出如图2-24所示的外轮廓及φ20㎜的孔。
数控铣加工程序示例

通过一个简单的数控铣加工零件及其数控铣加工程序的介绍,进一步了解数控铣程序的结构、特点和常用代码的含义。
下图为某外形轮廓的零件图,轮廓深度为5mm,数控编程采用刀心编程,图中所示坐标点为刀具中心的刀位点坐标值。
图数控铣编程实例(1)数控铣加工程序(见下表)表数控铣加工程序续表:(2)数控程序介绍大多数代码看起来非常熟悉,数控铣程序分为程序开始、程序内容和程序结束三部分内容。
第一部分程序开始部分程序开始部分主要定义程序号,调出零件加工坐标系、加工刀具,启动主轴、打开冷却液等方面的内容。
O6666为定义程序号,程序号为O6666。
N1数控铣程序由多个程序组成,每一个程序可以单列,也可以连在一起,为了容易区别,将该程序定义为N1程序。
G54G90G17G21G94G49G40G54:为建立工件坐标系指令,并选择G54作为当前的加工坐标系;如不作特殊指明,数控系统默认G54坐标系。
G90:采用绝对编程方式。
G17:加工平面选择XY平面。
G21:选择公制编程。
G94:进给方式定义,选择每分钟毫米,单位为mm/m。
G49:取消刀具长度补偿。
G40:取消刀具半径补偿。
G0X300.0Y300.0 Z300.0机床主轴移动到X300.0Y300.0 Z300.0的安全位置。
为避免换刀过程中出现刀具与工件或夹具之间的碰撞或干涉现象发生,一个有效的方法是使得机床主轴和加工零件有一定的安全距离。
M06 T09选择刀具指令,调9号端铣刀;同时确定了9号刀具在当前加工坐标系中相对于零点的偏置值。
M03S3600F680定义主轴的旋转速度,包括主轴正转(M03),转速为3600rpm(S3600),同时定义了进给速度为680mm/m(F680)。
第二部分程序内容部分程序内容是整个程序的主要部分,由多个程序段组成。
每个程序段由若干个字组成,每个字又由地址码和若干个数字组成。
常见的为G指令和M指令以及各个轴的坐标点组成的程序段。
加工中心编程实例(1)

数控铣床编程实例(参考程序请看超级链接)实例一毛坯为70㎜×70㎜×18㎜板材,六面已粗加工过,要求数控铣出如图3-23所示的槽,工件材料为45钢。
1.根据图样要求、毛坯及前道工序加工情况,确定工艺方案及加工路线1)以已加工过的底面为定位基准,用通用台虎钳夹紧工件前后两侧面,台虎钳固定于铣床工作台上。
2)工步顺序①铣刀先走两个圆轨迹,再用左刀具半径补偿加工50㎜×50㎜四角倒圆的正方形。
②每次切深为2㎜,分二次加工完。
2.选择机床设备根据零件图样要求,选用经济型数控铣床即可达到要求。
故选用XKN7125型数控立式铣床。
3.选择刀具现采用φ10㎜的平底立铣刀,定义为T01,并把该刀具的直径输入刀具参数表中。
4.确定切削用量切削用量的具体数值应根据该机床性能、相关的手册并结合实际经验确定,详见加工程序。
5.确定工件坐标系和对刀点在XOY平面内确定以工件中心为工件原点,Z方向以工件表面为工件原点,建立工件坐标系,如图2-23所示。
采用手动对刀方法(操作与前面介绍的数控铣床对刀方法相同)把点O作为对刀点。
6.编写程序按该机床规定的指令代码和程序段格式,把加工零件的全部工艺过程编写成程序清单。
考虑到加工图示的槽,深为4㎜,每次切深为2㎜,分二次加工完,则为编程方便,同时减少指令条数,可采用子程序。
该工件的加工程序如下(该程序用于XKN7125铣床):N0010 G00 Z2 S800 T1 M03N0020 X15 Y0 M08N0030 G20 N01 P1.-2 ;调一次子程序,槽深为2㎜N0040 G20 N01 P1.-4 ;再调一次子程序,槽深为4㎜N0050 G01 Z2 M09N0060 G00 X0 Y0 Z150N0070 M02 ;主程序结束N0010 G22 N01 ;子程序开始N0020 G01 ZP1 F80N0030 G03 X15 Y0 I-15 J0N0040 G01 X20N0050 G03 X20 YO I-20 J0N0060 G41 G01 X25 Y15 ;左刀补铣四角倒圆的正方形N0070 G03 X15 Y25 I-10 J0N0080 G01 X-15N0090 G03 X-25 Y15 I0 J-10N0100 G01 Y-15N0110 G03 X-15 Y-25 I10 J0N0120 G01 X15N0130 G03 X25 Y-15 I0 J10N0140 G01 Y0N0150 G40 G01 X15 Y0 ;左刀补取消N0160 G24 ;主程序结束实例二毛坯为120㎜×60㎜×10㎜板材,5㎜深的外轮廓已粗加工过,周边留2㎜余量,要求加工出如图2-24所示的外轮廓及φ20㎜的孔。
数控铣床和加工中心及编程
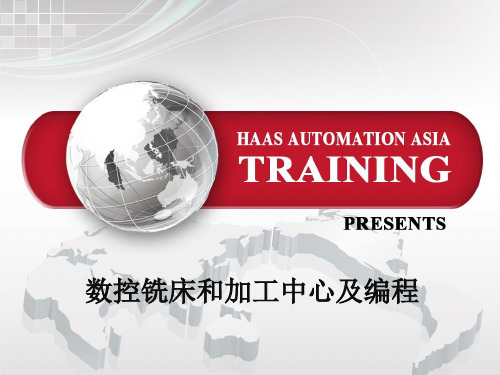
刀具参数补偿指令
➢刀具半径补偿 ➢刀具长度补偿
1、刀具半径补偿
1刀具半径补偿的方法 G41——刀具半径左补偿 G42——刀具半径右补偿 G40——取消刀具半径补偿
注意:正确选择G41 和G42;以保证顺铣和逆 铣的加工要求
2;建立、取消刀具半径补偿指令格式:
建立格式:
取消格式:
注意:1、G41/42只能与G00或 G01一起使用;且刀具必须移动
第二章
- 程序结构 - 辅助功能指令M-codes - 计算转速和进给
程序结构
程序号‘O’
OXXXX 代表程序号
O0001 ~ O7999 ----- 用户区域 O8000 ~ O8999 ----- 用户区域程序可以写保护 O9000 ~ O9999 ----- 厂家区域程序写保护
O0001
O0002
要任何手工的计算& UG\Master CAM
通信的方式
DNC 连接 Direct Numeric Control
- 通过软件采用RS 232 串口线可以将程序 从计算机端传送到机床端 .
- 如果NC控制器的内存不足时;采用这种方 式可以边传边做&
- 但是这种传送方式稳定性不好;很容易发 生断线;而且传送端口很容易烧坏&
注意:2、D为刀具半径补偿号 码;一般补偿量应为正值;若为负值; 则G41和G42正好互换&
刀补功能在模具加工中的应用
刀具半径补偿过程中的刀心轨迹
• 外轮廓加工→ • 内轮廓加工↓
注意:铣刀的直线移动量及铣削内侧圆弧的半径值要大于或等于 刀具半径;否则补偿时会产生干涉;系统会报警;停止执行&
4;刀具半径补偿的建立
RS 232 cable
数控铣床编程实例

第五节数控铣床编程实例(参考程序请看超级链接)实例一毛坯为70㎜×70㎜×18㎜板材,六面已粗加工过,要求数控铣出如图3-23所示的槽,工件材料为45钢。
1.根据图样要求、毛坯及前道工序加工情况,确定工艺方案及加工路线1)以已加工过的底面为定位基准,用通用台虎钳夹紧工件前后两侧面,台虎钳固定于铣床工作台上。
2)工步顺序①铣刀先走两个圆轨迹,再用左刀具半径补偿加工50㎜×50㎜四角倒圆的正方形。
②每次切深为2㎜,分二次加工完。
2.选择机床设备根据零件图样要求,选用经济型数控铣床即可达到要求。
故选用XKN7125型数控立式铣床。
3.选择刀具现采用φ10㎜的平底立铣刀,定义为T01,并把该刀具的直径输入刀具参数表中。
4.确定切削用量切削用量的具体数值应根据该机床性能、相关的手册并结合实际经验确定,详见加工程序。
5.确定工件坐标系和对刀点在XOY平面内确定以工件中心为工件原点,Z方向以工件表面为工件原点,建立工件坐标系,如图2-23所示。
采用手动对刀方法(操作与前面介绍的数控铣床对刀方法相同)把点O作为对刀点。
6.编写程序按该机床规定的指令代码和程序段格式,把加工零件的全部工艺过程编写成程序清单。
考虑到加工图示的槽,深为4㎜,每次切深为2㎜,分二次加工完,则为编程方便,同时减少指令条数,可采用子程序。
该工件的加工程序如下(该程序用于XKN7125铣床):N0010 G00 Z2 S800 T1 M03N0020 X15 Y0 M08N0030 G20 N01 P1.-2 ;调一次子程序,槽深为2㎜N0040 G20 N01 P1.-4 ;再调一次子程序,槽深为4㎜N0050 G01 Z2 M09N0060 G00 X0 Y0 Z150N0070 M02 ;主程序结束N0010 G22 N01 ;子程序开始N0020 G01 ZP1 F80N0030 G03 X15 Y0 I-15 J0N0040 G01 X20N0050 G03 X20 YO I-20 J0N0060 G41 G01 X25 Y15 ;左刀补铣四角倒圆的正方形N0070 G03 X15 Y25 I-10 J0N0080 G01 X-15N0090 G03 X-25 Y15 I0 J-10N0100 G01 Y-15N0110 G03 X-15 Y-25 I10 J0N0120 G01 X15N0130 G03 X25 Y-15 I0 J10N0140 G01 Y0N0150 G40 G01 X15 Y0 ;左刀补取消N0160 G24 ;主程序结束实例二毛坯为120㎜×60㎜×10㎜板材,5㎜深的外轮廓已粗加工过,周边留2㎜余量,要求加工出如图2-24所示的外轮廓及φ20㎜的孔。
数控铣床编程30例带图
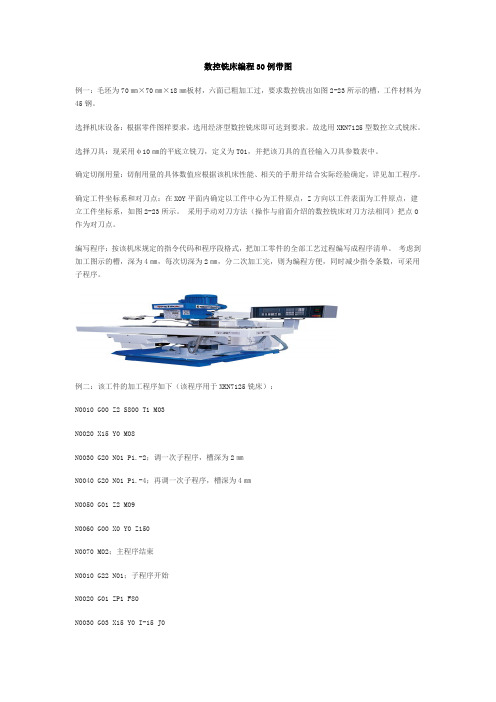
数控铣床编程30例带图例一:毛坯为70㎜×70㎜×18㎜板材,六面已粗加工过,要求数控铣出如图2-23所示的槽,工件材料为45钢。
选择机床设备:根据零件图样要求,选用经济型数控铣床即可达到要求。
故选用XKN7125型数控立式铣床。
选择刀具:现采用φ10㎜的平底立铣刀,定义为T01,并把该刀具的直径输入刀具参数表中。
确定切削用量:切削用量的具体数值应根据该机床性能、相关的手册并结合实际经验确定,详见加工程序。
确定工件坐标系和对刀点:在XOY平面内确定以工件中心为工件原点,Z方向以工件表面为工件原点,建立工件坐标系,如图2-23所示。
采用手动对刀方法(操作与前面介绍的数控铣床对刀方法相同)把点O 作为对刀点。
编写程序:按该机床规定的指令代码和程序段格式,把加工零件的全部工艺过程编写成程序清单。
考虑到加工图示的槽,深为4㎜,每次切深为2㎜,分二次加工完,则为编程方便,同时减少指令条数,可采用子程序。
例二:该工件的加工程序如下(该程序用于XKN7125铣床):N0010 G00 Z2 S800 T1 M03N0020 X15 Y0 M08N0030 G20 N01 P1.-2;调一次子程序,槽深为2㎜N0040 G20 N01 P1.-4;再调一次子程序,槽深为4㎜N0050 G01 Z2 M09N0060 G00 X0 Y0 Z150N0070 M02;主程序结束N0010 G22 N01;子程序开始N0020 G01 ZP1 F80N0030 G03 X15 Y0 I-15 J0N0040 G01 X20N0050 G03 X20 YO I-20 J0N0060 G41 G01 X25 Y15 ;左刀补铣四角倒圆的正方形N0070 G03 X15 Y25 I-10 J0N0080 G01 X-15N0090 G03 X-25 Y15 I0 J-10N0100 G01 Y-15N0110 G03 X-15 Y-25 I10 J0N0120 G01 X15N0130 G03 X25 Y-15 I0 J10N0140 G01 Y0N0150 G40 G01 X15 Y0;左刀补取消N0160 G24;主程序结束例三:毛坯为70㎜×70㎜×18㎜板材,六面已粗加工过,要求数控铣出如图3-23所示的槽,工件材料为45钢。
加工中心编程实例
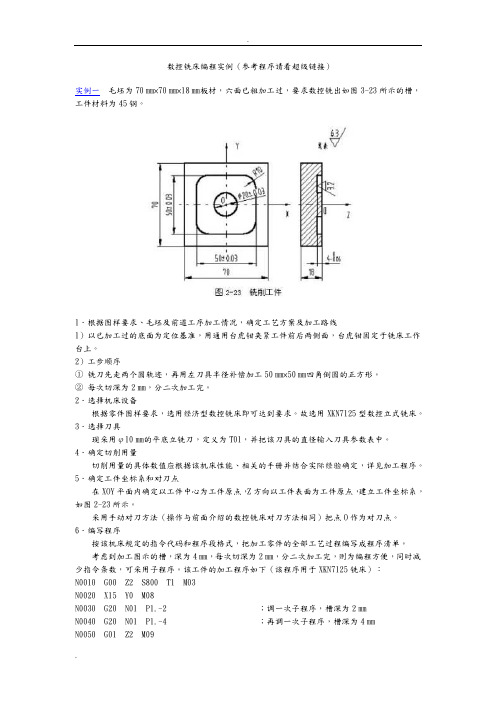
数控铣床编程实例(参考程序请看超级链接)实例一毛坯为70㎜×70㎜×18㎜板材,六面已粗加工过,要求数控铣出如图3-23所示的槽,工件材料为45钢。
1.根据图样要求、毛坯及前道工序加工情况,确定工艺方案及加工路线1)以已加工过的底面为定位基准,用通用台虎钳夹紧工件前后两侧面,台虎钳固定于铣床工作台上。
2)工步顺序①铣刀先走两个圆轨迹,再用左刀具半径补偿加工50㎜×50㎜四角倒圆的正方形。
②每次切深为2㎜,分二次加工完。
2.选择机床设备根据零件图样要求,选用经济型数控铣床即可达到要求。
故选用XKN7125型数控立式铣床。
3.选择刀具现采用φ10㎜的平底立铣刀,定义为T01,并把该刀具的直径输入刀具参数表中。
4.确定切削用量切削用量的具体数值应根据该机床性能、相关的手册并结合实际经验确定,详见加工程序。
5.确定工件坐标系和对刀点在XOY平面内确定以工件中心为工件原点,Z方向以工件表面为工件原点,建立工件坐标系,如图2-23所示。
采用手动对刀方法(操作与前面介绍的数控铣床对刀方法相同)把点O作为对刀点。
6.编写程序按该机床规定的指令代码和程序段格式,把加工零件的全部工艺过程编写成程序清单。
考虑到加工图示的槽,深为4㎜,每次切深为2㎜,分二次加工完,则为编程方便,同时减少指令条数,可采用子程序。
该工件的加工程序如下(该程序用于XKN7125铣床):N0010 G00 Z2 S800 T1 M03N0020 X15 Y0 M08N0030 G20 N01 P1.-2 ;调一次子程序,槽深为2㎜N0040 G20 N01 P1.-4 ;再调一次子程序,槽深为4㎜N0050 G01 Z2 M09N0060 G00 X0 Y0 Z150N0070 M02 ;主程序结束N0010 G22 N01 ;子程序开始N0020 G01 ZP1 F80N0030 G03 X15 Y0 I-15 J0N0040 G01 X20N0050 G03 X20 YO I-20 J0N0060 G41 G01 X25 Y15 ;左刀补铣四角倒圆的正方形N0070 G03 X15 Y25 I-10 J0N0080 G01 X-15N0090 G03 X-25 Y15 I0 J-10N0100 G01 Y-15N0110 G03 X-15 Y-25 I10 J0N0120 G01 X15N0130 G03 X25 Y-15 I0 J10N0140 G01 Y0N0150 G40 G01 X15 Y0 ;左刀补取消N0160 G24 ;主程序结束实例二毛坯为120㎜×60㎜×10㎜板材,5㎜深的外轮廓已粗加工过,周边留2㎜余量,要求加工出如图2-24所示的外轮廓及φ20㎜的孔。
数控铣床编程实例
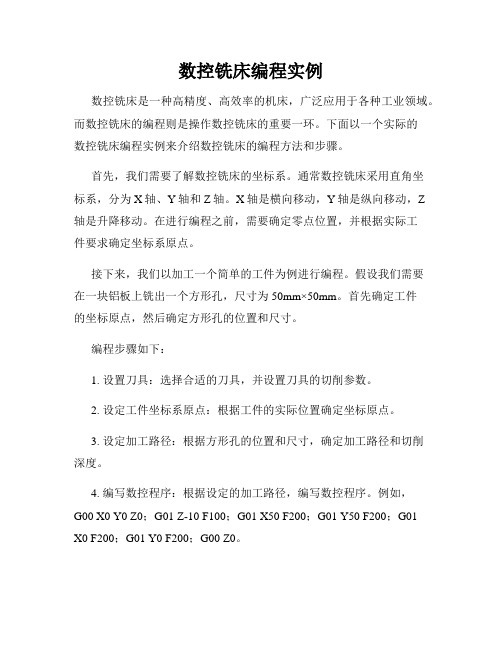
数控铣床编程实例数控铣床是一种高精度、高效率的机床,广泛应用于各种工业领域。
而数控铣床的编程则是操作数控铣床的重要一环。
下面以一个实际的数控铣床编程实例来介绍数控铣床的编程方法和步骤。
首先,我们需要了解数控铣床的坐标系。
通常数控铣床采用直角坐标系,分为X轴、Y轴和Z轴。
X轴是横向移动,Y轴是纵向移动,Z轴是升降移动。
在进行编程之前,需要确定零点位置,并根据实际工件要求确定坐标系原点。
接下来,我们以加工一个简单的工件为例进行编程。
假设我们需要在一块铝板上铣出一个方形孔,尺寸为50mm×50mm。
首先确定工件的坐标原点,然后确定方形孔的位置和尺寸。
编程步骤如下:1. 设置刀具:选择合适的刀具,并设置刀具的切削参数。
2. 设定工件坐标系原点:根据工件的实际位置确定坐标原点。
3. 设定加工路径:根据方形孔的位置和尺寸,确定加工路径和切削深度。
4. 编写数控程序:根据设定的加工路径,编写数控程序。
例如,G00 X0 Y0 Z0;G01 Z-10 F100;G01 X50 F200;G01 Y50 F200;G01X0 F200;G01 Y0 F200;G00 Z0。
通过以上步骤,我们完成了一个简单方形孔的数控铣床编程。
在实际操作中,需要结合数控铣床的操作界面和编程软件进行编程,确保加工路径的准确性和精度。
总之,数控铣床编程是一个需要技术和经验的过程。
通过不断的实践和学习,掌握数控铣床编程技巧,可以提高加工效率和产品质量,实现更精密的加工要求。
希望以上实例对您有所帮助,谢谢阅读!。
数控铣床编程实例(铣内外圆并钻孔) 8
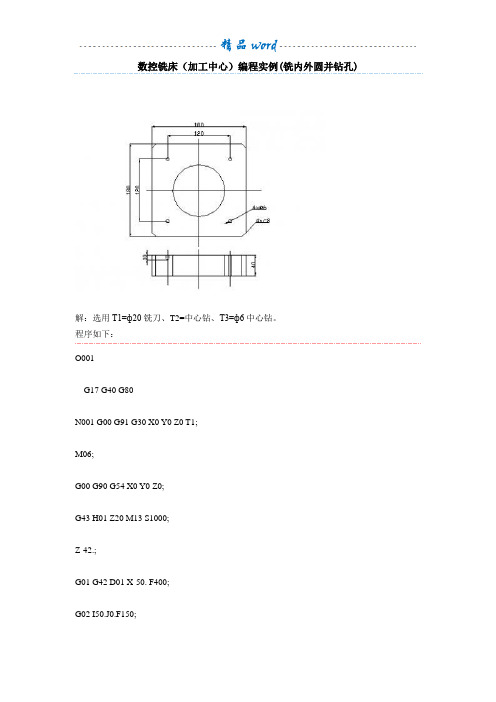
数控铣床(加工中心)编程实例(铣内外圆并钻孔)解:选用T1=ф20铣刀、T2=中心钻、T3=ф6中心钻。
程序如下:O001G17 G40 G80N001 G00 G91 G30 X0 Y0 Z0 T1;M06;G00 G90 G54 X0 Y0 Z0;G43 H01 Z20 M13 S1000;Z-42.;G01 G42 D01 X-50. F400;G02 I50.J0.F150;G00 Y0.;G40 Z100.;G00 G90 G54 X-110. Y-100.;Z-42.;G01 G41 X-90. F500;Y82X-82. Y90.;X82.;X82. Y90.;X-82.;X82. Y-90.;X-82.;G00 Z100.;G40;N002 G00 G91 G30 X0 Y0 Z0 T1; M06;G00 G90 G54 X-60. Y-60.;G43 H02 Z10 M03 S2000;G99 G81 Z-3. R5. F150;Y60.;X60.;Y-60.;GOO G80 Z100.;N003 G91 G30 X0 Y0 Z0 T3; M6;G00 G90 G54 X-60. Y-60.;G43 H02 Z10 M03 S2000;G99 G81 Z-12 R3. F150;Y60.;X60. Z-42.;Y-60.;GOO G80 Z100.;G00 G28 Y0;数控加工工艺分析主要包括的内容数控加工工艺分析的主要内容实践证明,数控加工工艺分析主要包括以下几方面:1)选择适合在数控机床上加工的零件,确定工序内容。
2)分析被加工零件图样,明确加工内容及技术要求,在此基础上确定零件的加工方案,制定数控加工工艺路线,如工序的划分、加工顺序的安排、与传统加工工序的衔接等。
3)设计数控加工工序。
如工步的划分、零件的定位与夹具的选择、刀具的选择、切削用量的确定等。
4)调整数控加工工序的程序。
数控铣床手工编程范例与练习

数控铣床手工编程范例与练习
机电工程学院《数控CAD/CAM及加工实训》教学组范例练习1___凸轮轮廓lian_xi_tu_ji_shougong_NC_G51_tu_lun_lun_kuo.prt
加工图形
凸轮轮廓草图、拉伸高度2mm
基本要求:(a) 毛坯大小80*80*10 D5平底刀加工深度2-3mm S10000 F500 G54编程;
(b) 手工编程写出NC代码,并在机床上加工毛坯验证程序;
拓展要求:(c) 在原有程序基础之上,添加缩放命令G51/G50和调用子程序指令M98/M99,在同一毛坯块上加工出一个Scale1.3的同形状凸轮;
范例练习2___G68旋转轮廓
(lian_xi_tu_ji_shougong_NC_G68xuanzhuan_lun_kuo.prt)
加工图形:
A B
C
F
基本要求:(a) 毛坯大小80*80*10 D5平底刀加工深度2-3mm S10000 F500 G54编程;
(b) 手工编程写出NC代码,并在机床上加工毛坯验证程序;
拓展要求:(c) NC程序要求采用G68/G69旋转指令和M98/M99调用子程序指令;。
数控铣床编程实例.

数控铣床编程实例(参考程序请看超级)实例一毛坯为70㎜×70㎜×18㎜板材,六面已粗加工过,要求数控铣出如图3-23所示的槽,工件材料为45钢。
1.根据图样要求、毛坯与前道工序加工情况,确定工艺方案与加工路线1)以已加工过的底面为定位基准,用通用台虎钳夹紧工件前后两侧面,台虎钳固定于铣床工作台上。
2)工步顺序①铣刀先走两个圆轨迹,再用左刀具半径补偿加工50㎜×50㎜四角倒圆的正方形。
②每次切深为2㎜,分二次加工完。
2.选择机床设备根据零件图样要求,选用经济型数控铣床即可达到要求。
故选用XKN7125型数控立式铣床。
3.选择刀具现采用φ10㎜的平底立铣刀,定义为T01,并把该刀具的直径输入刀具参数表中。
4.确定切削用量切削用量的具体数值应根据该机床性能、相关的手册并结合实际经验确定,详见加工程序。
5.确定工件坐标系和对刀点在XOY平面内确定以工件中心为工件原点,Z方向以工件表面为工件原点,建立工件坐标系,如图2-23所示。
采用手动对刀方法(操作与前面介绍的数控铣床对刀方法一样)把点O作为对刀点。
6.编写程序按该机床规定的指令代码和程序段格式,把加工零件的全部工艺过程编写成程序清单。
考虑到加工图示的槽,深为4㎜,每次切深为2㎜,分二次加工完,则为编程方便,同时减少指令条数,可采用子程序。
该工件的加工程序如下(该程序用于XKN7125铣床):N0010 G00 Z2 S800 T1 M03N0020 X15 Y0 M08N0030 G20 N01 P1.-2 ;调一次子程序,槽深为2㎜N0040 G20 N01 P1.-4 ;再调一次子程序,槽深为4㎜N0050 G01 Z2 M09N0060 G00 X0 Y0 Z150N0070 M02 ;主程序结束N0010 G22 N01 ;子程序开始N0020 G01 ZP1 F80N0030 G03 X15 Y0 I-15 J0N0040 G01 X20N0050 G03 X20 YO I-20 J0N0060 G41 G01 X25 Y15 ;左刀补铣四角倒圆的正方形N0070 G03 X15 Y25 I-10 J0N0080 G01 X-15N0090 G03 X-25 Y15 I0 J-10N0100 G01 Y-15N0110 G03 X-15 Y-25 I10 J0N0120 G01 X15N0130 G03 X25 Y-15 I0 J10N0140 G01 Y0N0150 G40 G01 X15 Y0 ;左刀补取消N0160 G24 ;主程序结束实例二毛坯为120㎜×60㎜×10㎜板材,5㎜深的外轮廓已粗加工过,周边留2㎜余量,要求加工出如图2-24所示的外轮廓与φ20㎜的孔。
数控铣常用指令及编程实例

• 按绝对方式编程 N10 G92 X0.0 Y0.0 Z50 N20 G90 G17 G00 N30 G41 X20.0 Y10.0 D01 N35 Z2 M03 S500 N38 G01 Z-10 F200 N40 G01 Y50.0 F100 N50 X50.0 N60 Y20.0 N70 X10.0 N80 G00 Z50 M05 N85 G40 X0 Y0 N90 M30
)
R2
X P4 P5
5
R 65
P6 P7
P3 P2
(-45 ,-40 )
P9 P 1 (-45,-75) P8
P 0 (-65,-95)
数控铣床编程实例 三
例. 见下图所示,用Φ8的刀具,沿双点画线加工距离工件上表面3mm深凹槽
8 8 R10
80
60
10 15 70 100
数控铣床编程实例三
例. 见下图所示,用Φ8的刀具,沿双点画线加工距离工件上表面3mm深凹槽 %5002 N1 G92 X0 Y0 Z50 N2 M03 S500 N3 G00 X19 Y24 N4 Z5 N5 G01 Z-3 F40 N6 Y56 N7 G02 X29 Y66 R10 8 (N7 G02 X29 Y66 I10) N8 G01 X71 8 N9 G02 X81 Y56 R10 R10 (N9 G02 X81 Y56 J-10) N10 G01 Y24 80 60 N111 G02 X71 Y14 R10 (N11 G02 X71 Y14 I-10) N12 G01 X29 N13 G02 X19 Y24 R10 (N13 G02 X19 Y24 J10) 10 N14 G00 Z50 15 70 N15 X0 Y0 N16 M30 100
加工中心编程及实例

加工中心加工编程及实例加工中心加工编程实践实践:法兰克系统加工中心编程实践在加工中心上加工如图所示零件,其材料为Q235-A ,毛胚大小为36*34*19。
326.5307162-M 8通15工件一、确定装夹方案根据毛胚和零件图,确定工件的装夹方式。
由于该工件是一个方形零件,并且这个零件的尺寸较小,单边余量只有2mm ,无法用压块装夹,而厚度余量有4mm ,故采用虎钳装夹加工。
在毛胚的下面垫一垫块,使毛胚的上表面与虎钳的压块表面距离至少超过15.5mm ,并采用毛胚的左上角跟虎钳上压块的左下角重合点作为为定位基准。
使用虎钳夹紧工件,并且两次装夹即可完成全部加工。
正、背面加工取两坐标系(G54、G55),G54取毛胚中心为工件坐标系原点,G55取虎钳上压块的左下角为工件坐标系原点。
二、确定加工顺序与走刀路线(一)、确定工件坐标系(1)正面加工:将工件坐标系原点设置在零件毛胚中心处。
(G54)(2)背面加工:将工件坐标系原点设置在虎钳上压块的左下角。
(G55)(二)、确定刀具运动路线(1)正面加工:1、先面铣毛胚表面(面铣后的表面为Z轴零点)。
2、再外形铣削32*30*15.2。
3、打2*M8中心点4、钻2*Ø6.8通孔5、攻2*M8螺纹孔。
(2)背面加工:面铣去除多余厚度,保证厚度15mm。
(三)、选择刀具及切削用量。
(1)正面加工:1、用Ø16平面铣刀(白钢四刃铣刀)进行加工表面及外形。
2、用Ø3中心钻打2*M8中心点3、用Ø6.8麻花钻头钻2*Ø6.8通孔4、用M8右旋牙丝锥攻2*M8螺纹孔。
(2)背面加工:1、用Ø16平面铣刀(白钢四刃铣刀)进行面铣去余料。
A、毛胚为Q235-A钢,选用白钢刀加工已经足够,根据加工方案和工件材料,选择刀具如下表所示。
B、根据刀具材料、工件材料和加工精度,选择切削用量,如下表所示。
切削用量详见加工程序。
节数控铣床编程实例

第五节数控铣床编程实例 <参照程序请看超级链接)实例一毛坯为 70 ㎜×70 ㎜×18 ㎜板材,六面已粗加工过,要求数控铣出如图3-23 所示的槽,工件资料为45 钢。
1.依据图样要求、毛坯及前道工序加工状况,确立工艺方案及加工路线1)以已加工过的底面为定位基准,用通用台虎钳夹紧工件前后双侧面,台虎钳固定于铣床工作台上。
2)工步次序①铣刀先走两个圆轨迹,再用左刀具半径赔偿加工50 ㎜×50 ㎜四角倒圆的正方形。
②每次切深为 2 ㎜,分二次加工完。
2.选择机床设施依据部件图样要求,采纳经济型数控铣床即可达到要求。
应采纳XKN7125型数控立式铣床。
3.选择刀具现采纳φ 10 ㎜的平底立铣刀,定义为T01,并把该刀具的直径输入刀具参数表中。
4.确立切削用量切削用量的详细数值应依据该机床性能、有关的手册并联合实质经验确定,详见加项目序。
5.确立工件坐标系和对刀点在 XOY平面内确立以工件中心为工件原点, Z 方向以工件表面为工件原点,成立工件坐标系,如图 2-23 所示。
采纳手动对刀方法 <操作与前方介绍的数控铣床对刀方法相同)把点O 作为对刀点。
6.编写程序按该机床规定的指令代码和程序段格式,把加工部件的所有工艺过程编写成程序清单。
考虑到加工图示的槽,深为 4 ㎜,每次切深为 2 ㎜,分二次加工完,则为编程方便,同时减少指令条数,可采纳子程序。
该工件的加项目序以下<该程序用于 XKN7125铣床):N0010 G00 Z2 S800 T1 M03N0020 X15 Y0 M08N0030G20N01P1.-2;调一次子程序,槽深为 2 ㎜N0040G20N01P1.-4;再调一次子程序,槽深为 4 ㎜N0050G01Z2 M09N0060G00X0 Y0 Z150N0070M02;主程序结束N0010G22N01;子程序开始N0020G01ZP1 F80N0030G03X15Y0 I-15 J0N0040G01X20N0050G03X20YO I-20 J0N0060G41G01 X25 Y15;左刀补铣四角倒圆的正方形N0070G03X15Y25 I-10 J0N0080G01X-15N0090G03X-25 Y15 I0 J-10N0100G01Y-15N0110G03X-15 Y-25 I10 J0N0120G01X15N0130G03X25Y-15 I0 J10N0140G01Y0N0150G40G01 X15 Y0;左刀补撤消N0160G24;主程序结束实例二毛坯为 120 ㎜×60 ㎜×10 ㎜板材, 5 ㎜深的外轮廓已粗加工过,周边留2 ㎜余量,要求加工出如图2-24 所示的外轮廓及φ 20 ㎜的孔。
数控铣床编程实例讲解
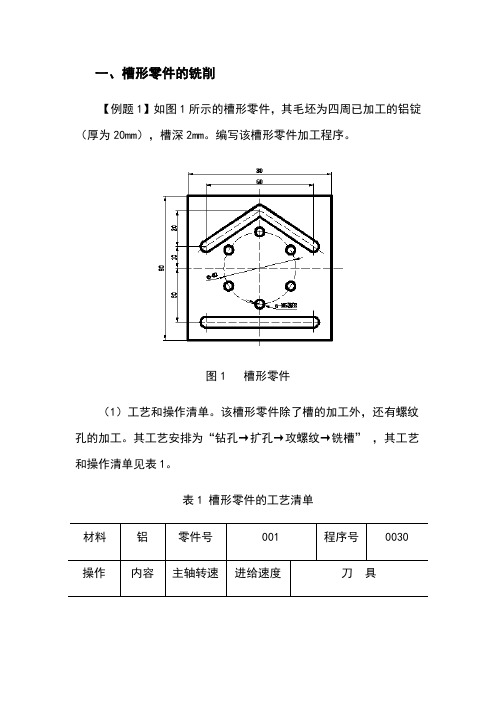
一、槽形零件的铣削【例题1】如图1所示的槽形零件,其毛坯为四周已加工的铝锭(厚为20mm),槽深2mm。
编写该槽形零件加工程序。
图1 槽形零件(1)工艺和操作清单。
该槽形零件除了槽的加工外,还有螺纹孔的加工。
其工艺安排为“钻孔→扩孔→攻螺纹→铣槽”,其工艺和操作清单见表1。
表1 槽形零件的工艺清单材料铝零件号001 程序号0030 操作内容主轴转速进给速度刀具(2)程序清单及说明。
该工件在数控铣钻床ZJK7532A-2上进行加工,程序见表2。
表2 槽形零件的加工程序二、平面凸轮的数控铣削工艺分析及程序编制【例题2】平面凸轮零件图如图2所示,工件的上、下底面及内孔、端面已加工。
完成凸轮轮廓的程序编制。
图2 凸轮零件图解:(1)工艺分析。
从图2的要求可以看出,凸轮曲线分别由几段圆弧组成,内孔为设计基准,其余表面包括4-φ13H7孔均已加工。
故取内孔和一个端面为主要定位面,在联接孔φ13的一个孔内增加削边销,在端面上用螺母垫圈压紧。
因为孔是设计和定位的基准,所以对刀点选在孔中心线与端面的交点上,这样很容易确定刀具中心与零件的相对位置。
(2)加工调整。
零件加工坐标系X、Y位于工作台中间,在G53坐标系中取X=-400,Y=-100。
Z坐标可以按刀具长度和夹具、零件高度决定,如选用φ20的立铣刀,零件上端面为Z向坐标零点,该点在G53坐标系中的位置为Z=-80处,将上述三个数值设置到G54加工坐标系中。
凸轮轮廓加工工序卡见表3。
表3 铣凸轮轮廓加工工序卡(3)数学处理。
该凸轮加工的轮廓均为圆弧组成,因而只要计算出基点坐标,才可编制程序。
在加工坐标系中,各点的计算坐标如下:BC弧的中心O1点: X=-(175+63.8) sin8°59'=-37.28Y=-(175+63.8) cos 8°59'=-235.86EF弧的中心O2点: X2+Y2=692(X-64)2+Y2=212解之得 X=65.75,Y=20.93HI弧的中心O4点: X=-(175+61)cos24°15'=-215.18 Y=(175+61)sin24°15'=96.93DE弧的中心O5点:X2+Y2=63.72(X-65.75)2+(Y-20.93)2=21.302解之得 X=63.70,Y=-0.27B点: X=-63.8sin8°59'=-9.96Y=-63.8cos8°59'=-63.02C点: X2+Y2=642(X+37.28)2+(Y+235.86)2=1752解之得 X=-5.57,Y=-63.76D点: (X-63.70)2+(Y+0.27)2=0.32X2+Y2=642解之得 X=63.99,Y=-0.28E点: (X-63.7)2+(Y+0.27)2=0.32(X-65.75)2+(Y-20.93)2=212解之得 X=63.72,Y=-0.03F点: (X+1.07)2+(Y-16)2=462(X-65.75)2+(Y-20.93)2=212解之得 X=44.79,Y=19.6G点: (X+1.07)2+(Y-16)2=462X2+Y2=612解之得 X=14.79,Y=59.18H点: X=-61 cos24°15'=-55.62Y=61sin 24°15'=25.05I点: X2+Y2=63.802(X+215.18)2+(Y-96.93)2=1752解之得 X=-63.02,Y=9.97根据上面的数值计算,可画出凸轮加工走刀路线图,如图3示。