平压平模切版制作中变形现象的解决办法
PCB生产过程中产生变形的原因及改善

PCB生产过程中产生变形的原因及改善摘要;21世纪是人类科学技术发展的顶峰时期,各种高科技油然而生。
近几年来随着表面安装和芯片安装的迅速发展,为了能够在日益激烈的信息科学技术领域占得一席之地,为此下游客户对电路板平整度的要求也越来越高。
本文针对PCB生产过程中出现变形的原因进行分析探讨,并提出相应的改善措施,希望能为以后类似工程提供借鉴作用。
关键词:PCB;变形;压合;改善1.引言电路板作为自动化表面贴装线上的重要部分,其平整度要求是非常高的,若出现电路板不平整情况就很容易以下严重后果,比如定位不准、元器件没法插装或贴装到板子的孔和表面贴装焊盘上,严重时还可能毁坏自动插装机。
为此只有提高各种元器件PCB板的平整度,才能更好的适应当前迅速发展的表面贴装技术,为人类的福祉做出更大的贡献。
根据当前IPC标准,带有表面贴装器件的PCB板和没有表面贴装器件所允许的最大变形量是不一样的,其分别为0.75%、1.5%。
不过在实际中,有些电子装联厂家为了更好适应当前高精度、高速度贴装需求,会对PCB板提出更高的要求,因此只有不断努力提高PCB板平整度才是相关企业的生存之道。
1.PCB板出现变形原因分析PCB板是由铜箔、树脂以及玻璃布等各种物理、化学性能不同材料所组成的,因此其在压合过程中就肯定会受到残留热应力影响而出现变形,加上其需要经过高温、机械切割、湿处理等环节,这些环节同样会让其出现变形,总的可以归结为以下几方面;1.1压合材料、结构、图形对板件变形的影响分析在压合过程中,PCB板中的芯板与外层铜箔会因为受热而出现变形。
而其中做好内层图形的芯板出现变形原因是因为图形分布跟芯板厚度或者材料特性不相同而有所差别,只有在图形分布比较均衡、材料化学物理性能一致以及厚度相同时,在压合过程中不同芯板的变形才会跟铜箔间的变形保持相同,才不容易出现变形情况。
因此可以得出PCB板会因为层压结构、材料类型不同、图形分布不均匀等原因而在压合过程中出现变形。
纸盒平压平模切技术及相关问题分析(二)
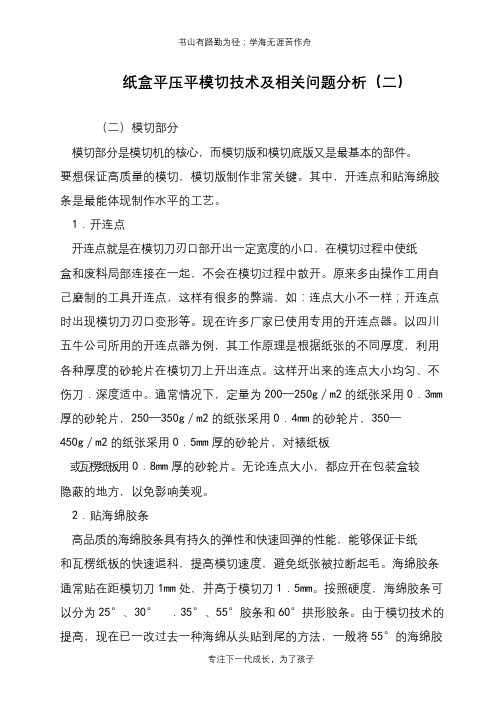
书山有路勤为径;学海无涯苦作舟纸盒平压平模切技术及相关问题分析(二)(二)模切部分模切部分是模切机的核心,而模切版和模切底版又是最基本的部件。
要想保证高质量的模切,模切版制作非常关键。
其中,开连点和贴海绵胶条是最能体现制作水平的工艺。
1.开连点开连点就是在模切刀刃口部开出一定宽度的小口,在模切过程中使纸盒和废料局部连接在一起,不会在模切过程中散开。
原来多由操作工用自己磨制的工具开连点,这样有很多的弊端,如:连点大小不一样;开连点时出现模切刀刃口变形等。
现在许多厂家已使用专用的开连点器。
以四川五牛公司所用的开连点器为例,其工作原理是根据纸张的不同厚度,利用各种厚度的砂轮片在模切刀上开出连点。
这样开出来的连点大小均匀、不伤刀.深度适中。
通常情况下,定量为200—250g/m2的纸张采用0.3mm 厚的砂轮片,250—350g/m2的纸张采用0.4mm的砂轮片,350—450g/m2的纸张采用0.5mm厚的砂轮片,对裱纸板或瓦楞纸板用0.8mm厚的砂轮片。
无论连点大小,都应开在包装盒较隐蔽的地方,以免影响美观。
2.贴海绵胶条高品质的海绵胶条具有持久的弹性和快速回弹的性能,能够保证卡纸和瓦楞纸板的快速退科,提高模切速度,避免纸张被拉断起毛。
海绵胶条通常贴在距模切刀1mm处,并高于模切刀1.5mm。
按照硬度,海绵胶条可以分为25°、30°.35°、55°胶条和60°拱形胶条。
由于模切技术的提高,现在已一改过去一种海绵从头贴到尾的方法,一般将55°的海绵胶专注下一代成长,为了孩子。
钢板切割变形的控制措施
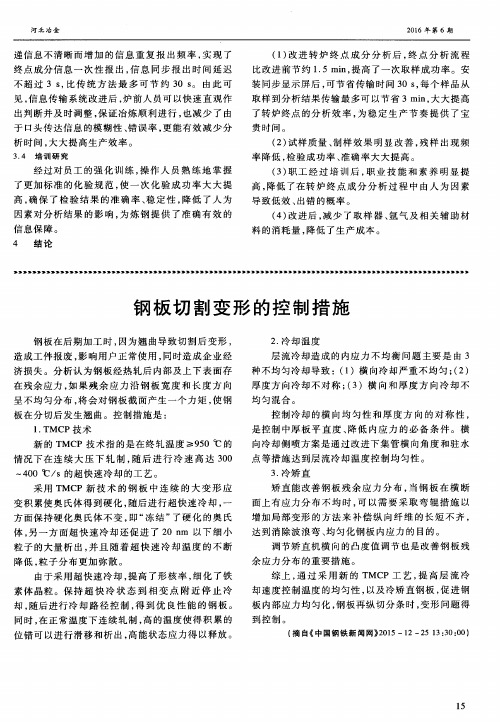
(1)改进 转 炉 终 点 成 分 分 析 后 ,终 点 分 析 流 程 比改进 前节 约 1.5 min,提高 了一 次取 样成 功率 。安 装 同步显 示屏 后 ,可节 省传 输 时间 30 S,每 个 样 品从 取样 到分 析结 果传 输最 多 可 以节 省 3 min,大大 提高 了转 炉终 点 的分 析 效 率 ,为 稳 定 生 产 节奏 提供 了宝 贵 时 间 。
河 北 冶金
2016年 第 6期
递信 息不 清 晰而 增 加 的信 息 重 复 报 出频 率 ,实 现 了 终点 成分 信 息一 次 性 报 出 ,信 息 同步 报 出 时 间 延 迟 不超 过 3 S,比传 统 方 法 最 多 可 节 约 30 S。 由此 可 见 ,信 息传 输 系统 改进 后 ,炉前人 员 可 以快速 直 观作 出判 断并 及 时调 整 ,保 证冶 炼顺 利进 行 ,也减 少 了由 于 口头传 达信 息 的模糊 性 、错误 率 ,更能 有效 减 少分 析时 间 ,大大 提高 生产 效率 。
(2)试 样质 量 、制 样 效果 明显 改 善 ,残 样 出现 频 率 降低 ,检验成 功 率 、准 确率 大 大提 高 。
(3)职工 经 过 培 训 后 ,职 业 技 能 和 素 养 明显 提 高 ,降低 了在转 炉终 点 成 分 分 析 过 程 中 由人 为 因素 导致 低效 、出错 的概率 。
(4)改进后 ,减 少 了取 样 器 、氩 气 及 相关 辅 助 材 料 的消耗 量 ,降低 了生 产成 本 。
钢 板 切 割 变 形 的控 制措 施
ቤተ መጻሕፍቲ ባይዱ
钢板 在后 期加 工时 ,因为翘 曲导 致切 割 后 变形 , 造 成 工件 报废 ,影 响用 户正 常使 用 ,同时造 成 企业 经 济损 失 。分析 认 为钢板 经 热轧后 内部及 上下 表 面存 在残余 应 力 ,如 果残 余 应 力 沿 钢 板 宽 度 和 长 度方 向 呈 不 均匀 分布 ,将会 对 钢板 截面 产生 一个 力 矩 ,使钢 板 在 分切 后发 生翘 曲。控 制措施 是 :
PCB生产过程中产生变形的原因及改善
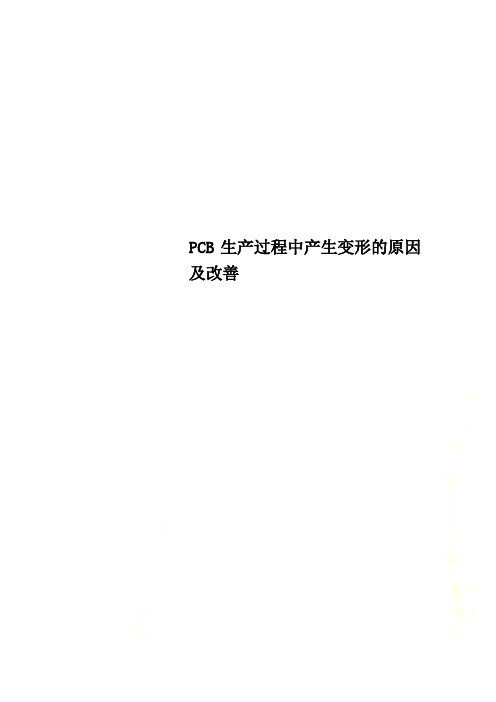
PCB生产过程中产生变形的原因及改善PCB生产过程中产生变形的原因及改善(刘海龙)(深南电路有限公司,广东深圳518053)摘要随着表面安装和芯片安装时代的到来,下游客户对电路板平整度的要求必定越来越严格.本文围绕印制电路板设备和制造的全流程,重点研究了压合、阻焊、整平、出货前校平等制程对板件变形的影响。
并根据试验结果和生产经验提出了一些有效的控制板件变形的方法。
1前言在自动化表面贴装线上,电路板若不平整,会引起定位不准,元器件无法插装或贴装到板子的孔和表面贴装焊盘上,甚至会撞坏自动插装机。
装上元器件的电路板焊接后发生弯曲,元件脚很难剪平整齐。
板子也无法装到机箱或机内的插座上,所以,装配厂碰到板翘同样是十分烦恼。
目前的表面贴装技术正在朝着高精度、高速度、智能化方向发展,这就对做为各种元器件家园的PCB板提出了更高的平整度要求。
在IPC标准中特别指出带有表面贴装器件的PCB板允许的最大变形量为0.75%,没有表面贴装的PCB板允许的最大变形量为1.5%。
实际上,为满足高精度和高速度贴装的需求,部分电子装联厂家对变形量的要求更加严格,如我公司有多个客户要求允许的最大变形量为0.5%,甚至有个别客户要求0.3%。
PCB板由铜箔、树脂、玻璃布等材料组成,各材料物理和化学性能均不相同,压合在一起后必然会产生热应力残留,导致变形。
同时在PCB的加工过程中,会经过高温、机械切削、湿处理等各种流程,也会对板件变形产生重要影响,总之可以导致PCB板变形的原因复杂多样,如何减少或消除由于材料特性不同或者加工引起的变形,成为PCB制造商面临的最复杂问题之一。
2变形产生原因分析PCB板的变形需要从材料、结构、图形分布、加工制程等几个方面进行研究,本文将对可能产生变形的各种原因和改善方法进行分析和阐述。
2.1压合材料、结构、图形对板件变形的响分析PCB板由芯板和半固化片以及外层铜箔压合而成,其中芯板与铜箔在压合时受热变形,变形量取决于两种材料的热膨胀系数(CTE),铜箔的热膨胀系数(CTE)为17X10-6左右,而普通FR-4基材在Tg点下Z向CTE为(50~70)X10-6,TG点以上为(250~350)X10-6,X向CTE由于玻璃布存在,一般与铜箔类似。
平压平模切版制作中变形现象的解决办法
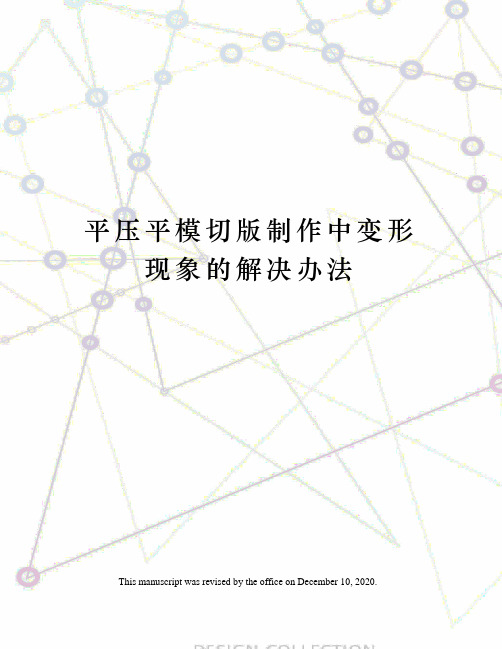
平压平模切版制作中变形现象的解决办法This manuscript was revised by the office on December 10, 2020.模切压痕工艺是利用钢刀、钢线等排成的模版区域报道,在压力的作用下,将品轧切成型的工艺。
其加工效果是品表面既有变形(压痕),又有裂变(模切)。
模切版的制作,俗称排刀,是指将钢刀、钢线、衬空材料等按照规定的要求雅昌,拼组成模切版的工艺操作过程。
模切版制作的一般过程如下:绘制模切版轮廓图→切割底版→钢刀钢线裁切成型→组合拼版→开连接点→粘贴海绵胶条→试切垫版→制作压痕底摸→试模切、签样一、绘制模切版轮廓图首先应根据要求设计模切版版面,版面设计的任务包括:(1)确定版面的大小,应与所选用设备的规格和工作能力相匹配;(2)确定模切版的种类;(3)选择模切版所用材料及规格。
设计好的版面应满足以下要求,即模切版的格位应与印刷格位相符;工作部分应居于模切版的中央位置;线条、图形的移植要保证产品所要求的精度;版面刀线要对直,纵横刀线互成直角并与模切版侧边平行;断刀、断线要对齐等。
模切版轮廓图是整版产品的展开图艾司科,是模切版制作的第一个关键环节。
如果采用的是整页拼版系统,可以在印刷制版工序直接输出模切版轮廓图,可以有效保证印刷版和模切版的统一。
如果印刷采用的是手工软片拼版,就需要根据印样排版的实际尺寸绘制模切版轮廓图。
在绘制过程中,为了保证在制版过程中模切版不散版橡胶制品,要在大面积封闭图形部分留出若干处“过桥”,过桥宽度对于小块版可设计成3毫米~6毫米,对于大块版可留出8毫米~9毫米。
为使模切版的钢刀、钢线具有较好的模切适性,产品设计和版面绘图时应注意以下问题: PS版1、开槽开孔的刀线应尽量采用整线,线条转弯处应带圆角数码机,防止出现相互垂直的钢刀拼接。
2、两条线的接头处,应防止出现尖角现象。
3、避免多个相邻狭窄废边的联结,应增大连接部分,使其连成一块,便于清废。
纸盒平压平模切技术及相关问题分析(一)

书山有路勤为径;学海无涯苦作舟
纸盒平压平模切技术及相关问题分析(一)
模切压痕是纸盒印后加工中不可或缺的一道工序,由于人们对商品
外包装质量的要求越来越高,模切压痕的质量也必然随之提高。
平压平模切方式目前在国内模切领域占有较大的市场份额,虽然其技术已经非常成熟,但是仍不可避免地会出现这样那样的问题。
无论是在输纸部分、模切部分、清废部分,还是在收纸部分,均有诸多问题困扰着包装印刷行业的从业人员。
将问题汇总起来,找出问题的症结所在,并集思广义将其解决,为同行提供参考是我们要努力做到的。
为此,我们采访了四川五牛印务有限公司技术部的晏科先生、济南天一印务有限公司生产总监杜豪新先生。
浙江宁波大红鹰彩色包装有限公司技术主管莫言文先生和杭州清泰包装印刷厂厂长郑勇先生。
请他们结合本企业的生产实践,对平压平模切过程中各环节常出现的故障、产生的原因和故障排除办法谈了谈自己的经验。
下面则以平压平模切的工艺流程(输纸——模切——清废——收纸)为主线,
将他们的经验和看法进行归纳总结。
(一)输纸部分
平压平模切机的纸张供给主要是靠飞达的吸纸和送纸动作完成,采用
输纸带加压纸轮的方法传递纸张,在输纸过程中会出现以下故障。
1.走纸不稳,需经常调节
该故障主要是针对国产模切机而言的,由于国产模切机多数没有采用
带吸气的传送带,容易导致走纸不稳,纸张定位精度不高,输纸导轮、输纸带、压纸毛轮、前规挡块、侧规挡块等容易磨损。
在走纸之前对纸张进行敲纸、十丁边并在走纸过程中加以调节可有效解决此问题。
2.输纸不顺畅
专注下一代成长,为了孩子。
模切压痕常见的质量问题

模切压痕常见的质量问题全文共四篇示例,供读者参考第一篇示例:模切和压痕作为印刷后加工的重要环节,常常会出现一些质量问题,影响整个产品的质量和美观度。
下面就来详细介绍一些模切压痕常见的质量问题,以及如何避免和解决这些问题。
1. 边缘不整齐:在模切或压痕过程中,如果刀具或模具使用不当,会导致产品边缘不整齐,甚至出现错位或切断现象。
这种问题会给产品的外观带来很大影响,降低整体质量。
解决方法是选择质量好的刀具或模具,确保模切和压痕的精准度。
2. 压痕深浅不一:在压痕过程中,如果压力不均匀或调节不当,容易导致压痕深浅不一的情况出现。
这会导致产品表面不平整,影响整体美观度。
解决方法是严格控制压力和调节参数,保证压痕的一致性。
3. 模切残留:有时模切或压痕后会出现一些残留物,如纸屑或碎片,这不仅会影响产品的整洁度,还会在后续加工过程中产生不良影响。
避免这种问题的方法是及时清理模切或压痕后的残留物,保持产品表面干净。
5. 模切位置不准确:模切或压痕的位置不准确会导致产品尺寸不匹配或错位,影响产品的使用效果。
避免这种问题的方法是在设计模切或压痕位置时,慎重考虑并确保准确性。
模切和压痕是印刷后加工中非常重要的步骤,质量问题会直接影响整体产品的质量和美观度。
为了避免这些问题的发生,印刷厂家和加工厂家需要定期检查设备和工具的状况,加强员工培训,规范操作流程,确保产品质量。
只有这样,才能生产出高质量的产品,满足客户需求。
第二篇示例:模切压痕是一种常见的加工方法,广泛应用于各种行业的生产中,如印刷包装、电子产品制造、纸品制作等。
模切压痕的质量直接影响到产品的成型质量和使用效果,因此需要对常见的质量问题及其解决方法有所了解。
下面将就模切压痕常见的质量问题进行详细介绍。
一、模切压痕常见的质量问题1. 压痕不清晰压痕不清晰是模切过程中比较常见的质量问题,主要表现为压痕不规整、边缘生毛等。
造成该问题的原因可能有以下几点:(1)模刀磨损严重,刀口不锋利;(2)模刀与底板的间隙设置不合理;(3)受压力不均匀,导致部分区域的压痕不清晰。
如何解决板材加工中出现波浪纹的问题

如何解决板材加工中出现波浪纹的问题
作者:木业中国
最近,经常有板材企业的技术人员网友向我们咨询,为什么会在板材加工时出现波浪纹的问题,从而影响到板材质量. 波浪纹重时,直接面队就可以看的见,实测厚度,各部分数据有变化,加工后的板材只能沦为低档产品.波浪纹轻时,直观近乎没有,但如果是端起从一侧看,确能看到,如果遇到有经验的客户就很难蒙混过去,造成板材品质的降低.就此,我们咨询了临沂德利德机械制造的技术人员.他们说,其实出现波浪纹的原因很简单,就是因为砂光机在工作时出现的不断震荡造成的.
而出现震荡现象的原因有多种:
一是因为机型较小,而采用的动力偏大,加工强度和速度加大造成.特别是支架式砂光机因先天性的原因就更容易产生震荡,而市场上的产品有90%以上为支架式;如果是框架式砂光机这个问题可能就没有.当然,也有一些小的砂光机制造企业因自身经验不足随意乱配置也是原因之一.
二是砂光机使用的轴承误差较大,造成震荡.
三是砂光机的砂辊不标准,各部分之间有误差.四是砂带,传送带有收缩性也会造成误差性波纹.
改进方法是:
一尽量结合现有机型和结构,配置适当电机,不易随意提高加工速度和加工强度.以利于机器的稳定.
二是尽量去选用误差较小的优质轴承,德利德的技术人员推荐说,最好选用德国进口轴承.
三是经常对砂光机进行精度检修,及时调节,调整.四是尽量选购整体框架式的砂光机,虽然价格稍贵,但生产的板材质量相对提高了.同时,输送部分也应该说辊式输送产生的误差要更小些.。
平压平模切机常见故障及处理【技巧】

在模切机工作过程中,会出现精度不高等问题,影响生产的顺利进行.以下是小编整理出相关问题的具体排查方法,以便模切机出现问题后,操作员可以做到具体问题具体分析,找出故障原因,并采取相应措施解决。
模切机精度不高1模切版本身有误差模切版的制作方法主要有手工制版和激光制版两种,激光制版的精度比较高,设计和切割由计算机和机械完成,适合中高档包装的模切;手工制版则对制版者的技术水平要求高,适合精度要求不高的中短版包装模切。
2纸板规矩不一首先要分清这是在印刷流程还是在模切流程中造成的。
模切之前,应先查看印刷品的规矩是否一致,再检查模切机的输纸部分、规矩定位部分、收纸链条部分的调节是否适当。
3模切压痕与印刷位置套不准解决方法是根据产品要求重新校正模切版,也可通过调整纸张输送侧定位规矩或前定位规矩来校正。
4工作环境不同模切压痕和印刷的工作环境不同会造成纸张纤维变形,从而造成模切精度不高。
应尽量保证模切压痕与印刷在同一工作环境中进行,或保证整个工作环境的同一性(即相同的温湿度等)。
此外,对上光和覆膜的纸张要进行模切预处理,尽量减小纸张变形对模切精度的影响。
出现“暗线”或“爆线”“暗线”是指不应该有的压痕线;“爆线”是指由于模切压痕压力过大,超过了纸张纤维的承受极限,使纸张纤维断裂或部分断裂。
1压痕底模和压痕线不合适2模切机的压力不合适当整版压力调整为能将印品待模切部分的70%~80%切穿时,即可进行局部垫版调节。
3垫版纸的厚度不准确由于纸垫得过低或过高而造成“暗线”或“爆线”,调节方法是重新垫纸。
4纸质太差或纸张含水量过低纸张因含水量变化导致脆性增大、韧性降低,也会产生“爆线”,可以通过增大环境湿度来解决。
此外,在模切硬盒烟包小盒时,由于一些位置的压痕线距离很近,如果按正常情况配置压痕线的高度,模压时会对纸张产生较大拉力,造成“爆线”。
这时应设法将纸张受到的拉力降到最小。
较好的方法是降低压痕线的高度,降低的高度一般为0.1~0.2mm。
如何解决平压平模切纸模切部分故障

如何解决平压平模切纸模切部分故障编辑:oa161商务办公网模切压痕是纸盒印后加工中不可或缺的一道工序,因为大家对商品外包装质量的需求越来越高,模切压痕的质量也必定随之进步。
平压平模切办法当前在国内模切范畴占有较大的市场份额,尽管其技能现已十分老练,可是仍不可防止地会呈现这样那样的疑问。
无论是在输纸有些,模切有些.清废有些,仍是在收纸有些,均有许多疑问困惑着包装印刷职业的从业人员。
模切有些模切有些是模切机的中心,而模切版和模切底版又是最基本的部件。
要想确保高质量的模切,模切版制造十分要害。
其间,开连点和贴海绵胶条是最能体现制造水平的技能。
1.开连点开连点就是在模切刀刃口部开出必定宽度的小口,在模切过程中使纸盒和废料部分衔接在一起,不会在模切过程中散开。
本来多由操作工用自个磨制的东西开连点,这样有许多的坏处,如:连点巨细不一样:开连点时呈现模切刀刃口变形等。
如今许多厂家已运用专用的开连点器。
以四川五牛公司所用的开连点器为例,其作业原理是依据纸张的不一样厚度,运用各种厚度的砂轮片在模切刀上开出连点。
这样开出来的连点巨细均匀、不伤刀、深度适中。
一般情况下,定量为200~250g/m2的纸张选用0.3mm厚的砂轮片,250~350g/m2的纸张选用0.4mm的砂轮片,350~450g/m2的纸张选用0.5mm厚的砂轮片,对裱纸板或瓦楞纸板用0.8mm厚的砂轮片。
无论连点巨细,都应开在包装盒较荫蔽的当地,防止影响漂亮。
2.贴海绵胶条高品质的海绵胶条具有耐久的弹性和疾速回弹的功能,能够确保卡纸和瓦楞纸板的疾速退料,进步模切速度,防止纸张被拉断起毛。
海绵胶条一般贴在距模切刀1mm处,并高于模切刀1.5mm。
依照硬度,海绵胶条能够分为25°、30°、35°、55°胶条和60°拱形胶条。
因为模切技能的进步,如今已一改曩昔一种海绵从头贴到尾的办法,一般将55°的海绵胶条贴在窄缝处;60°拱形胶条贴在连点和刀线之间。
PCB生产过程中产生变形的原因及改善
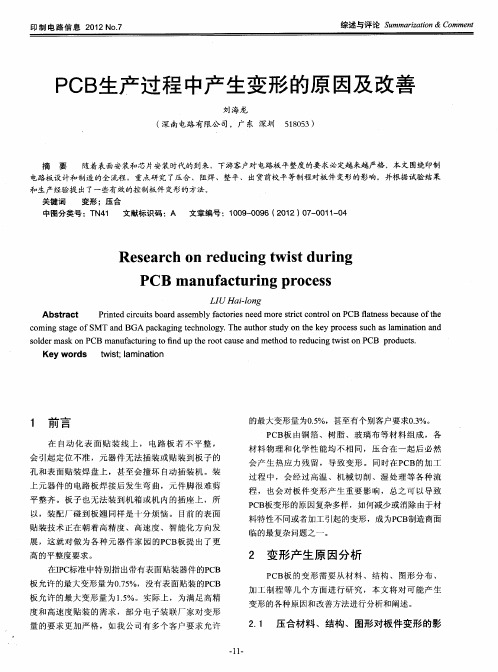
料特 性 不 同或者 加工 引起 的变 形 ,成为P B i 商面 C ¥造 J
临的最 复杂 问题之 一 。
贴装 技 术 正 在朝 着 高 精 度 、高 速 度 、智 能 化 方 向发
展 ,这 就 对 做 为各 种 元 器 件家 园 的P CB板 提 出 了更 高 的平整 度要求 。 在I C 准 中特别 指 出带有 表 面贴装 器件 的P B P标 C 板允 许 的最 大变 形量 为07 %,没有 表面 贴装 的P B .5 C
印 制 电路信 息 2 1 o7 0 2N .
综述 与评论 S m r ain&C mm n u mai t z o o et
P 生产 过程 中产 生变形 的原 因及 改善 CB
刘 海龙
( 南 电路 有 限公 司 ,广 东 深圳 5 8 5 深 10 3)
摘 要
随着表 面安装和 芯片安装 时代 的到来 ,下游客户对 电路板平整度的要求必定越来越严格 。本文 围绕印制
Re e r h o e s a c n r duc ng t s urng i witd i
PCB a m nuf c ur ng pr c s a t i o es
LI Ha —o g U iln Abs r ct ta P it dc ru t o r s e l a t re e dmo e src o to n PCB an s e a s f h rn e ic isb a da s mby f co isn e r titc n r lo l f t e sb c u eo e t
c m i gsa eo M T n o n t g fS a d BGA a k g n e h lg . ea t o t d n t ek y p o e ss c slm i ain a d p c a i g tc noo y Th u h rsu y o h e r c s u h a a n to n s le a ko od r s nPCB a u a t rn n p t er o a s ndm eh dt e u ig t s nPCB p o u t . m m n f cu i gt f d u h o t u ea t o r d cn wito oi c o r d cs
板材变形矫正基本方法
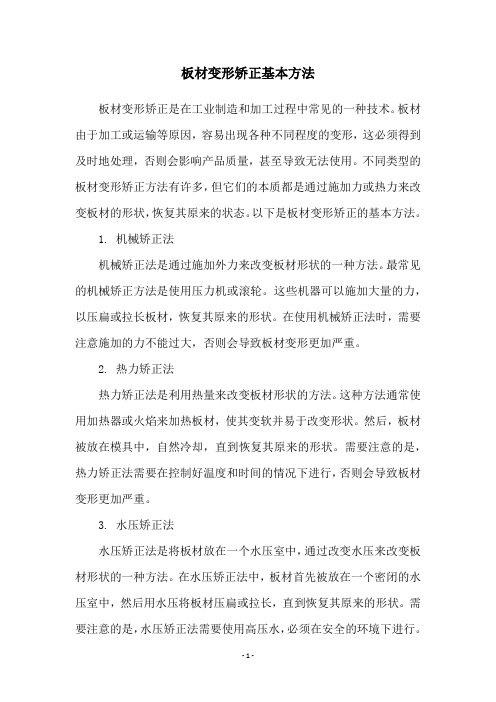
板材变形矫正基本方法
板材变形矫正是在工业制造和加工过程中常见的一种技术。
板材由于加工或运输等原因,容易出现各种不同程度的变形,这必须得到及时地处理,否则会影响产品质量,甚至导致无法使用。
不同类型的板材变形矫正方法有许多,但它们的本质都是通过施加力或热力来改变板材的形状,恢复其原来的状态。
以下是板材变形矫正的基本方法。
1. 机械矫正法
机械矫正法是通过施加外力来改变板材形状的一种方法。
最常见的机械矫正方法是使用压力机或滚轮。
这些机器可以施加大量的力,以压扁或拉长板材,恢复其原来的形状。
在使用机械矫正法时,需要注意施加的力不能过大,否则会导致板材变形更加严重。
2. 热力矫正法
热力矫正法是利用热量来改变板材形状的方法。
这种方法通常使用加热器或火焰来加热板材,使其变软并易于改变形状。
然后,板材被放在模具中,自然冷却,直到恢复其原来的形状。
需要注意的是,热力矫正法需要在控制好温度和时间的情况下进行,否则会导致板材变形更加严重。
3. 水压矫正法
水压矫正法是将板材放在一个水压室中,通过改变水压来改变板材形状的一种方法。
在水压矫正法中,板材首先被放在一个密闭的水压室中,然后用水压将板材压扁或拉长,直到恢复其原来的形状。
需要注意的是,水压矫正法需要使用高压水,必须在安全的环境下进行。
总的来说,板材变形矫正方法各有优缺点,应根据具体情况,选择合适的方法进行矫正。
同时,在进行板材变形矫正时,应注意安全,避免损坏板材,确保最终的产品质量。
变形不均匀原因及防止措施
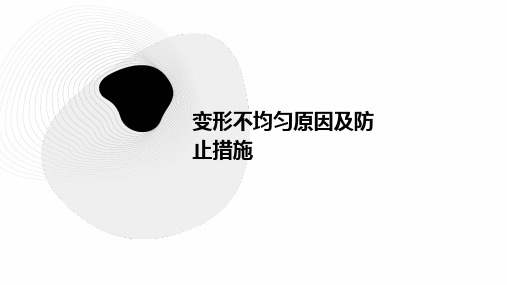
加工过程中温度控制不当,导致材料热胀冷缩;刀具磨损严重,切削力不均;装夹方式 不合理,导致应力分布不均。
变形不均匀对产品质量的影响
影响精度
变形不均匀会导致产品尺寸精度下降,影响发应力集中,降低产品疲劳寿命。
不良外观
变形严重的产品可能存在明显的凹凸不平,影响外观质量。
变形不均匀对产品质量的影响
影响精度
变形不均匀会导致产品尺寸精度下降,影响装配和使用性能。
降低寿命
变形不均匀可能引发应力集中,降低产品疲劳寿命。
不良外观
变形严重的产品可能存在明显的凹凸不平,影响外观质量。
从案例中总结的防止措施
控制加工温度
保持恒温环境,减少温度波动对 材料的影响。
加强质量检测
定期对产品进行尺寸和形状检测, 及时发现并处理变形问题。
纤维方向
材料中纤维方向不一致, 导致各方向热膨胀系数不 同,引发变形。
材料缺陷
材料内部存在如气泡、杂 质等缺陷,影响其受力性 能和稳定性,导致变形。
材料因素
材料成分不均
材料内部化学成分分布不 均,导致热膨胀系数不一 致,引发变形。
纤维方向
材料中纤维方向不一致, 导致各方向热膨胀系数不 同,引发变形。
02
变形不均匀不仅影响产品的外观 ,还可能影响其性能和使用寿命 。
变形不均匀现象的普遍性
01
在各种材料加工过程中,如铸造 、锻造、焊接等,都可能出现变 形不均匀的现象。
02
变形不均匀不仅影响产品的外观 ,还可能影响其性能和使用寿命 。
对生产和生活的影响
变形不均匀可能导致产品报废,增加 生产成本。
湿度变化
工作环境温度波动大,影 响材料热膨胀系数,进而 引发变形。
板材加工中的变形控制技术

板材加工中的变形控制技术一、引言板材加工是一种广泛应用于各类产品制造的手段,但是在加工过程中经常会出现板材变形的问题,影响了产品的质量。
因此,板材加工中的变形控制技术显得至关重要。
二、板材变形的原因1. 工艺参数不合理:在板材加工中,切割和折弯工艺参数的错误调整、材料的选择和加工工艺的不当使用都会导致板材变形。
2. 板材内部应力: 板材加工过程中,由于内部位错产生了应力,在板材中存在应力差的区域,很容易会导致板材的变形。
3. 环境因素:加工环境的不良,如温度、湿度等,强制变形造成的板材变形。
三、板材加工中的变形控制技术在板材加工中,为了尽可能减少变形,我们必须要采用一些控制变形的技术。
1. 合理的切割和折弯工艺参数在板材加工中,切割和折弯工艺参数的选择非常重要。
我们要根据材料的强度、厚度、变形容量、板材折曲角度等因素来选择工艺参数,确保板材变形尽可能小。
2. 合理的材料选择在板材加工过程中,选择合适的材料是十分关键的。
对于具有较细晶粒和均匀化学成分的材料,具有更好的可塑性和可靠性,有很好的抗变形能力。
选择材料时应注意避免含有应力或缺陷的材料,因为这样的材料会在加工过程中容易导致变形。
3. 合理的加工过程在板材加工中,加工过程也非常重要。
需要注意:加工过程中板材应基本保持水平,垂直地柱轴线;缝隙应尽量小,压力均匀性好;板材加热时应注意加热区域和加热温度的均匀性等方面的细节。
4. 板材加工后的处理板材加工后的处理也是应该注意的方面之一。
必要的退火、弯曲和焊接等工艺可以控制板材的变形,从而保证产品的质量。
四、结论综上所述,板材加工中的变形控制技术对于产品的成品率有至关重要的影响,必须积极采取措施,逐步加强对变形的控制。
将来,在材料科学和制造技术方面的研究将为变形控制提供更多的技术支持。
铝合金平板加工变形 -回复
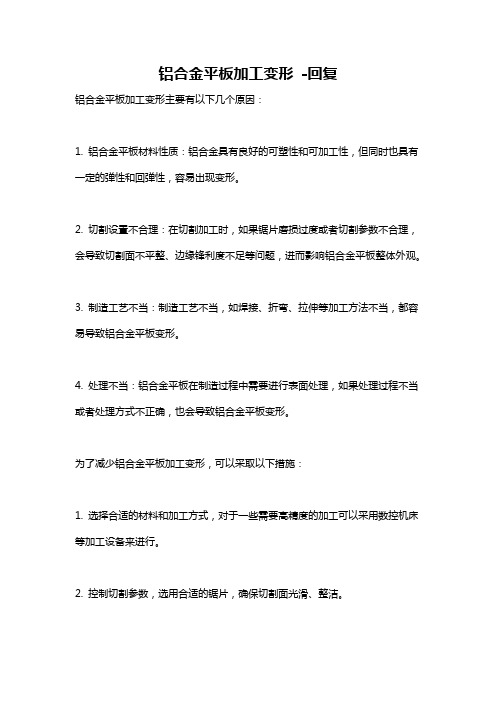
铝合金平板加工变形-回复
铝合金平板加工变形主要有以下几个原因:
1. 铝合金平板材料性质:铝合金具有良好的可塑性和可加工性,但同时也具有一定的弹性和回弹性,容易出现变形。
2. 切割设置不合理:在切割加工时,如果锯片磨损过度或者切割参数不合理,会导致切割面不平整、边缘锋利度不足等问题,进而影响铝合金平板整体外观。
3. 制造工艺不当:制造工艺不当,如焊接、折弯、拉伸等加工方法不当,都容易导致铝合金平板变形。
4. 处理不当:铝合金平板在制造过程中需要进行表面处理,如果处理过程不当或者处理方式不正确,也会导致铝合金平板变形。
为了减少铝合金平板加工变形,可以采取以下措施:
1. 选择合适的材料和加工方式,对于一些需要高精度的加工可以采用数控机床等加工设备来进行。
2. 控制切割参数,选用合适的锯片,确保切割面光滑、整洁。
3. 采用合适的工艺方法,根据实际情况选择焊接、折弯、拉伸等加工方式,避免产生过大的内部应力。
4. 严格控制表面处理过程,确保表面光滑、均匀,避免因处理不当而导致铝合金平板变形。
制作平压平模切版-变形及裂变(下)
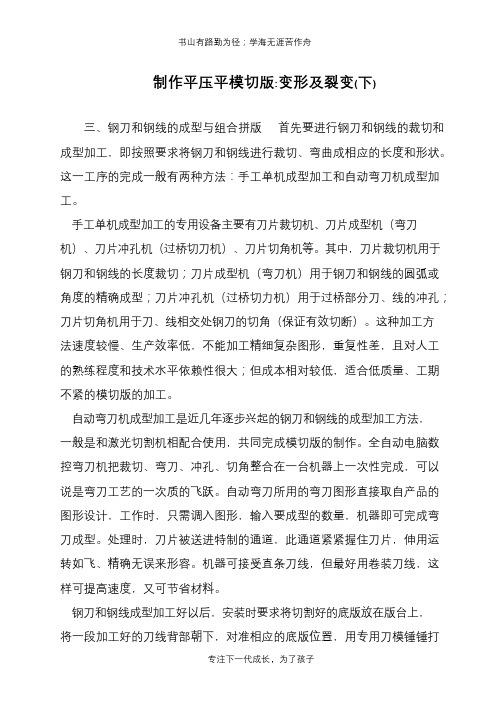
制作平压平模切版:变形及裂变(下)三、钢刀和钢线的成型与组合拼版首先要进行钢刀和钢线的裁切和成型加工,即按照要求将钢刀和钢线进行裁切、弯曲成相应的长度和形状。
这一工序的完成一般有两种方法:手工单机成型加工和自动弯刀机成型加工。
手工单机成型加工的专用设备主要有刀片裁切机、刀片成型机(弯刀机)、刀片冲孔机(过桥切刀机)、刀片切角机等。
其中,刀片裁切机用于钢刀和钢线的长度裁切;刀片成型机(弯刀机)用于钢刀和钢线的圆弧或角度的精确成型;刀片冲孔机(过桥切力机)用于过桥部分刀、线的冲孔;刀片切角机用于刀、线相交处钢刀的切角(保证有效切断)。
这种加工方法速度较慢、生产效率低,不能加工精细复杂图形,重复性差,且对人工的熟练程度和技术水平依赖性很大;但成本相对较低,适合低质量、工期不紧的模切版的加工。
自动弯刀机成型加工是近几年逐步兴起的钢刀和钢线的成型加工方法,一般是和激光切割机相配合使用,共同完成模切版的制作。
全自动电脑数控弯刀机把裁切、弯刀、冲孔、切角整合在一台机器上一次性完成,可以说是弯刀工艺的一次质的飞跃。
自动弯刀所用的弯刀图形直接取自产品的图形设计,工作时,只需调入图形,输入要成型的数量,机器即可完成弯刀成型。
处理时,刀片被送进特制的通道,此通道紧紧握住刀片,伸用运转如飞、精确无误来形容。
机器可接受直条刀线,但最好用卷装刀线,这样可提高速度,又可节省材料。
钢刀和钢线成型加工好以后,安装时要求将切割好的底版放在版台上,将一段加工好的刀线背部朝下,对准相应的底版位置,用专用刀模锤锤打上部刃口,将其镶入模版。
锤打时一定要用专用的刀模锤或木锤,刀模锤头部采用高弹橡胶制成,在打刀线刃口时,可以保证不伤刃口。
近年来,自动装力机也已出现,使装刀速度和质量都有了很大的提高。
四、开连接点在模切版制版过程中,开连接点是一项必不可少的工序。
连接点就是在模切刀刃口部开出一定宽度的小口,在模切过程中,使废边在模切后仍有局部连在整个印张上而不散开,以便于下一步走纸顺畅。
板式家具板类部件的变形及解决方法

板式家具板类部件的变形及解决方法制造板式家具时,大都采用中密度纤维板、细木工板、刨花板以及胶合板等作为板式家具的基材,这些基材具有幅面大、表面平整、易于加工、便于涂饰等优点,但也有吸湿、弹性变形等缺点。
有些刚刚加工好的家具的部件过不了几天就发生了变形,如原先平整的柜门发生了翘曲,而且基本上没有办法恢复。
如何解决这些令人头痛的问题呢?实际上,可以从产生变形的原因来进行探讨。
众所周知,构成板式家具的主要零部件有旁板,搁板、门板、顶板或面板以及背板等,板件所存在的主要变形有板件的弹性弯曲、翘曲、蠕变等,其中,翘曲和蠕变在很大程度上取决于基材本身的内在质量,而零部件的弹性弯曲,除了板件本身的质量之外,主要还取决于生产过程的管理和工艺的处理。
对于基材本身的问题,可以选用内应力较小,强度较大的品牌产品。
而对于在外力作用下的弹性变形,则是一个比较复杂的问题,下面就以搁板和高柜的长门为例来加以分析。
1 搁板的弯曲变形1.1 搁板的受力情况板式家具的搁板重要承受到以下几种应力:1)压应力是承载物件的压力及搁板自重形成的应力。
是造成搁板变形的主要原因。
2)弯曲压力是承载弯距形成的应力,能使搁板弯曲和蠕变。
3)剪切应力由承载搁板支撑或连接件接口处压力与支撑力产生的剪切作用而形成。
4)涂料固化应力由于搁板表面涂料固化的内表收缩不一致而产生的内应力,使得搁板弯曲变形。
以上4种应力造成板式家具搁板弯曲变形。
1.2搁板的受力分析:在上述应力中,对搁板的弯曲影响最大的是压应力,其弯曲程度取决于负荷的大小,配置的情况以及材料的尺寸和本身的特性。
搁板在负荷下产生的弯曲变形可以用下列公式来计算:1)负荷集中于搁板中心时(图1)Y=PL3/4Ebh32)当负荷均匀分布时(图2)Y=5QL4/32Ebh3式中:y——弯曲变形量(m)p——负荷(N)L——支点间的距离(m)b——搁板断面的宽度(m)H——搁板的厚度(m)E——材料的弹性模量(Pa)Q——均布负荷(N/m)在对上述的公式进行分析时就会发现,搁板材料的弹性模量最能体现出抗弯强度的主要特征,材料的弹性模量是由材料本身的材质决定的,弹性模量越大,材料的抗变形能力越强。
- 1、下载文档前请自行甄别文档内容的完整性,平台不提供额外的编辑、内容补充、找答案等附加服务。
- 2、"仅部分预览"的文档,不可在线预览部分如存在完整性等问题,可反馈申请退款(可完整预览的文档不适用该条件!)。
- 3、如文档侵犯您的权益,请联系客服反馈,我们会尽快为您处理(人工客服工作时间:9:00-18:30)。
模切压痕工艺是利用钢刀、钢线等排成的模版区域报道,在压力的作用下,将印刷品轧切成型的工艺。
其加工效果是印刷品表面既有变形(压痕),又有裂变(模切)。
模切版的制作,俗称排刀,是指将钢刀、钢线、衬空材料等按照规定的要求雅昌,拼组成模切版的工艺操作过程。
模切版制作的一般过程如下:
绘制模切版轮廓图→切割底版→钢刀钢线裁切成型→组合拼版→开连接点→粘贴海绵胶条→试切垫版→制作压痕底摸→试模切、签样
一、绘制模切版轮廓图
首先应根据要求设计模切版版面,版面设计的任务包括:(1)确定版面的大小,应与所选用设备的规格和工作能力相匹配;(2)确定模切版的种类;(3)选择模切版所用材料及规格。
设计好的版面应满足以下要求,即模切版的格位应与印刷格位相符;工作部分应居于模切版的中央位置;线条、图形的移植要保证产品所要求的精度;版面刀线要对直,纵横刀线互成直角并与模切版侧边平行;断刀、断线要对齐等。
模切版轮廓图是整版产品的展开图艾司科,是模切版制作的第一个关键环节。
如果印刷采用的是整页拼版系统,可以在印刷制版工序直接输出模切版轮廓图,可以有效保证印刷版和模切版的统一。
如果印刷采用的是手工软片拼版,就需要根据印样排版的实际尺寸绘制模切版轮廓图。
在绘制过程中,为了保证在制版过程中模切版不散版橡胶制品,要在大面积封闭图形部分留出若干处“过桥”,过桥宽度对于小块版可设计成3毫米~6毫米,对于大块版可留出8毫米~9毫米。
为使模切版的钢刀、钢线具有较好的模切适性,产品设计和版面绘图时应注意以下问题:PS版
1、开槽开孔的刀线应尽量采用整线,线条转弯处应带圆角数码印刷机,防止出现相互垂直的钢刀拼接。
2、两条线的接头处,应防止出现尖角现象。
3、避免多个相邻狭窄废边的联结,应增大连接部分,使其连成一块,便于清废。
4、防止出现连续的多个尖角爱色丽,对无功能性要求的尖角,可改成圆角。
5、防止尖角线截止于另一个直线的中间段落,这样会使固刀困难、钢刀易松动,并降低模切适性,应改为圆弧或加大其相遇角。
二、切割模版(开槽)
模切版常用的衬空材料(底版)有金属衬空材料和非金属材空材料;其中多层胶合板使用最多Adobe,胶合板的厚度一般为18毫米~20毫米。
底版(衬空材料)的切割主要有锯床切割、激光切割等方式。
锯床切割是目前中小企业自行加工模切版的主要方法,锯床的工作是利用特制锯条的上下往返运动,在底版上加工出可装钢刀和钢线的窄槽,锯条的厚度等于相应位置钢刀和钢线的厚度。
锯床上配有电钻,可以在底版上钻孔收纸,钻孔后,将锯条穿过底版,再进行切割。
现在的锯床根据使用的场合和制版种类不同,规格丰富且功能完善,有的锯床配有吸尘系统爱普生,可以把锯切的锯末自动收集,锯条可以进行电动装夹,有些大版面锯床工作台面上还配有气浮系统。
可以使大版面锯割轻快灵活。
近年来,CAD/CAM技术也已应用于模切版的制作,其原理是利用CAD/CAM技术和计算机控制技术CTF,控制锯床完成切割,开槽质量有较大提高。
金属包装
激光切割是在由电脑控制的激光切割机上进行的,它是以激光作为能源,通过激光产生的高温对底版材料进行切割。
进行激光切割首先需要将整版模切轮廓图输入电脑,由电脑控制底版的移动平版印刷,用激光进行切割。
但在切割过程中需要的参数较多,如材料质量参数、板材厚度、激光输出功率、辅助气体的种类和压力、喷嘴的直径、口径、材料与喷嘴的距离间隙、透镜的焦距、焦点的位置以及切割速度等。
所以,在实际生产中,借鉴以往经验来确定加
工效果是极其重要的。
激光切割的主要不足是激光切割机价格昂贵,切割成本较高上光,从而使模切版制作成本较高,因此,这种模切版一般由专业厂家生产,用户直接定作。
三、钢刀和钢线的成型与组合拼版
首先要进行钢刀和钢线的裁切和成型加工,即按照要求将钢刀和钢线进行裁切、弯曲成相应的长度和形状。
这一工序的完成一般有两种方法:手工单机成型加工和自动弯刀机成型加工。
手工单机成型加工的专用设备主要有刀片裁切机、刀片成型机(弯刀机)、刀片冲孔机(过桥切刀机)、刀片切角机等。
其中重组,刀片裁切机用于钢刀和钢线的长度裁切;刀片成型机(弯刀机)用于钢刀和钢线的圆弧或角度的精确成型;刀片冲孔机(过桥切力机)用于过桥部分刀、线的冲孔;刀片切角机用于刀、线相交处钢刀的切角(保证有效切断)。
这种加工方法速度较慢、生产效率低,不能加工精细复杂图形,重复性差,且对人工的熟练程度和技术水平依赖性很大;但成本相对较低,适合低质量、工期不紧的模切版的加工。
上海电气自动弯刀机成型加工是近几年逐步兴起的钢刀和钢线的成型加工方法DTP,一般是和激光切割机相配合使用,共同完成模切版的制作。
全自动电脑数控弯刀机把裁切、弯刀、冲孔、切角整合在一台机器上一次性完成,可以说是弯刀工艺的一次质的飞跃。
自动弯刀所用的弯刀图形直接取自产品的图形设计,工作时,只需调入图形重组,输入要成型的数量,机器即可完成弯刀成型。
处理时,刀片被送进特制的通道,此通道紧紧握住刀片,伸用运转如飞、精确无误来形容。
机器可接受直条刀线加网,但最好用卷装刀线,这样可提高速度,又可节省材料。
钢刀和钢线成型加工好以后字库,安装时要求将切割好的底版放在版台上,将一段加工好的刀线背部朝下,对准相应的底版位置,用专用刀模锤锤打上部刃口,将其镶入模版。
锤打时一定要用专用的刀模锤或木锤印刷工艺,刀模锤头部采用高弹橡胶制成,在打刀线刃口时,可以保证不伤刃口。
近年来,自动装力机也已出现,使装刀速度和质量都有了很大的提高。
自动弯刀机成型加工是近几年逐步兴起的钢刀和钢线的成型加工方法光盘印刷,一般是和激光切割机相配合使用,共同完成模切版的制作。
全自动电脑数控弯刀机把裁切、弯刀、冲孔、切角整合在一台机器上一次性完成,可以说是弯刀工艺的一次质的飞跃。
四、开连接点
在模切版制版过程中,开连接点是一项必不可少的工序。
连接点就是在模切刀刃口部开出一定宽度的小口,在模切过程中人物,使废边在模切后仍有局部连在整个印张上而不散开,以便于下一步走纸顺畅。
开连接点应使用的专用设备是刀线打孔机,即用砂轮磨削,而不应用锤子和錾子去开连接点,否则会损坏刀线和搭脚CTP,并在连接部分容易产生毛刺。
连点宽度有0.3mm、0.4mm、0.5mm、0.6mm、0.8mm、1.0mm等大小不同的规格,常用的规格为0.4mm。
连接点通常打在成型产品看不到的隐蔽处,成型后外观处的连接点应越小越好,以免影响成品外观。
另外还应注意不要在过桥位置开连接点(过桥位置模切刀是悬空的)。
纸品包装
五、粘贴海绵胶条
钢刀和钢线安装完后,为了防止模切刀在模切、压痕时粘住纸张过度包装,并使走纸顺畅,在刀线两侧要粘贴弹性海绵胶条。
弹性海绵胶条在模切中所起的作用非常重要,它直接影响模切的速度与质量。
一般来说,海绵胶条应高出模切刀3mm~5mm。
在不同模切机上,应根据模切的速度和模切活件及各相关条件PS版,选用不同硬度、尺寸、形状的海绵胶条。
具体选择弹性海绵胶条时可遵循以下原则:
1、硬性海绵胶条多放在模切刀口下沿的空档处,软性海绵放条多放在模切刀下活或模切刀与模切刀之间的缝隙之中。
2、模切力之间的距离如果小于8mm,则应选择硬度为HS600的海绵胶条。
3、模切刀之间的距离如果大于10mm,则应选择硬度为HS250(瓦楞纸板)或350(卡纸
板)的海绵胶条。
4、模切刀与钢线的距离如果小于10mm,则应选择硬度为HS700的拱型海绵胶条;如果大于10mm数码印刷,则应选择硬度为HS350的海绵胶条。
5、模切刀的打口位置使用硬度为HS700的拱型海绵胶条,用于保护连点不被拉断。
6、模切胶条距离刀线的理想距离为1mm~2mm。
六、试切垫板
模切版加工完成后,要首先将模切版装在模切机上进行试切,若试切试样局部正常,而有一部分切不断时教育,就要在局部范围进行垫板,也叫做“补压”。
垫板就是利用0.05mm厚的垫纸板粘贴在模切版底部,对模切刀进行高度补偿。
当局部垫板后仍有个别刀线模切不透时,就要进行位置垫板,位置垫板就是用窄条垫板直接粘在模切刀底部进行刀线高度补偿。
这一工序对模切质量和速度也有着直接影响德鲁巴,并且对操作工人的经验和技术要求较高。
富士施乐
通过以上几个工序,模切版的制作基本完成,制作好的模切版可以上机生产了,但在正式生产之前,还必须经过“制作压痕底根(以利于压痕的形成烟草包装,常用方法有手工粘底模法和贴压痕模法等)、试模切、客户签样”等工序,才能进行正式生产。