棒材粗轧机组接轴扭矩均衡分配孔型优化设计
棒材连轧机生产圆钢的孔型优化
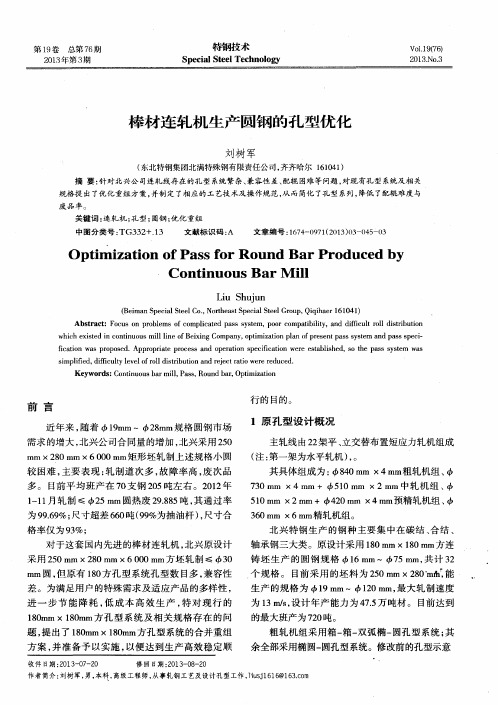
中图分类号 : TG3 3 2 +. 1 3
文献 标 识 码 : A
文章编号 : 1 6 7 4 - 0 9 7 1 ( 2 0 1 3 ) 0 3 — 0 4 5 — 0 3
O pt i mi z a t i o n 0 f Pa s s f o r Ro und Ba r Pr o duc e d by C0 nt i nu0 us Ba r M i l l
较 困难 , 主要 表 现 : 轧制道次多 , 故 障率 高 , 废 次 品
多 。 目前 平 均 班 产 在 7 0 支钢 2 0 5吨左 右 。2 0 1 2 年
其具体组成为 : 8 4 0 m m× 4 m m粗轧机组 、
7 3 0 mm x 4 mm+ 西5 1 0 n l m ×2 mm中 轧 机 组 、 5 1 0 m m X 2 m m+ 4 , 4 2 0 mm x 4 mm预精轧 机组 、 3 6 0 mm x6 mm精轧 机组 。
1 - 1 1 月轧制 ≤西2 5 m m圆热废 2 9 . 8 8 5 吨, 其通过率
为9 9 . 6 9 %; 尺寸 超差 6 6 0 吨( 9 9 %为抽 油杆 ) , 尺寸 合
格 率仅 为 9 3 %;
北 兴 特 钢 生 产 的钢 种 主要 集 中在 碳 结 、 合结 、 轴 承 钢 三大 类 。原 设计 采 用 1 8 0 mm x 1 8 0 mm方连 铸 坯 生 产 的 圆 钢 规 格 1 6 mm~西7 5 l n m, 共计 3 2
第1 9 卷 总第 7 6 期 2 0 1 3 年第 3 期
特 钢技 术
S p e c i a l S t e e l Te c h n o l o g y
棒材轧制孔型设计

孔型设计本设计以φ28mm圆钢为代表产品进行设计。
1 孔型系统的选择圆钢孔型系统一般由延伸孔型系统和精轧孔型系统两部分组成。
延伸孔型的作用是压缩轧件断面,为成品孔型系统提供合适的红坯。
它对钢材轧制的产量、质量有很大的影响,但对产品最后的形状尺寸影响不大。
常用的延伸孔型系统一般有箱形、菱—方、菱—菱、椭—方、六角—方、椭圆—圆、椭圆—立椭圆等;精轧孔型系统一般是方—椭圆—螺或圆—椭圆—螺孔型。
本设计采用无孔型和椭圆—圆孔型系统。
1.1无孔型轧制法优点:(1)由于轧辊无孔型,改轧产品时,可通过调节辊缝改变压下规程。
因此,换辊、换孔型的次数减少了,提高了轧机作业率。
(2)由于轧辊不刻轧槽,轧辊辊身能充分利用;由于轧件变形均匀,轧辊磨损量少且均匀,轧辊寿命提高了2~4倍。
(3)轧辊车削量少且车削简单,节省了车削工时,可减少轧辊加工车床。
(4)由于轧件是在平辊上轧制,所以不会出现耳子、充不满、孔型错位等孔型轧制中的缺陷。
(5)轧件沿宽度方向压下均匀,故使轧件两端的舌头、鱼尾区域短,切头、切尾小,成材率高。
(6)由于减小了孔型侧壁的限制作用,沿宽度方向变形均匀,因此降低了变形抗力,故可节约电耗7%。
1.2椭圆—圆孔型系统优点:(1)孔型形状能使轧件从一种断面平滑的过渡到另一种断面,从而避免由于剧烈不均匀变形而产生的局部应力。
(2)孔型中轧出的轧件断面圆滑无棱、冷却均匀,从而消除了因断面温度分布不均而引起轧制裂纹的因素。
(3)孔型形状有利于去除轧件表面氧化铁皮,改善轧件的表面质量。
(4)需要时可在延伸孔型中生产成品圆钢,从而减少换辊。
缺点:(1)延伸系数小。
通常延伸系数不超过1.30~1.40,使轧制道次增加。
(2)变形不太均匀,但比椭圆—方孔型要好一些。
(3)轧件在圆孔型中稳定性差,需要借助于导卫装置来提高轧件在孔型中的稳定性,因而对导卫装置的设计、安装及调整要求严格。
(4)圆孔型对来料尺寸波动适应能力差,容易出耳子,故对调整要求高。
承钢棒材厂轧制节奏优化实验研究
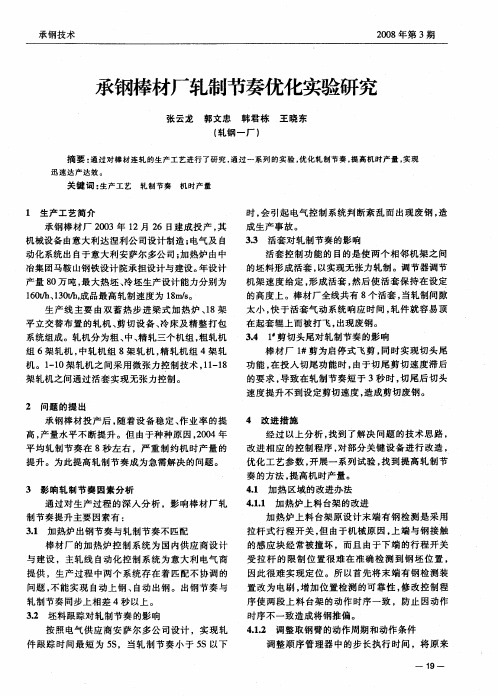
因此 很 难 实 现 定位 。所 以首 先 将 末 端 有钢 检 测 装
置改为 电刷 , 增加位置检测的可靠性 , 修改控制程
序 使 两 段 上 料 台架 的动作 时序 一 致 ,防止 因动 作 时序 不 一致 造成 将 钢推偏 。 41 调整 取 钢臂 的动作 周期 和 动作 条 件 .. 2 调 整 顺 序 管理 器 中的步 长 执 行 时 间 ,将 原 来
3 影响 轧制 节奏 因 素分 析
ห้องสมุดไป่ตู้
4 改进 措 施
经 过 以上 分 析 , 到 了解 决 问题 的技 术 思 路 , 找 改进 相 应 的控 制 程 序 , 部 分 关 键设 备 进 行 改 造 , 对 优化 工 艺 参 数 , 开展 一 系列 试 验 , 到 提 高 轧 制 节 找
奏 的方 法 , 高机 时产 量 。 提
承 钢 技术
20 0 8年 第 3期
承钢棒材厂轧制节奏优化实验研究
张 云龙 郭文 忠 韩君 栋 王 晓东
( 轧钢 一厂 )
摘要 : 通过对棒材连轧的生产工艺进行了研究, 通过一系列的实验, 优化轧制节奏, 提高机时产量 , 实现
迅 速 达 产 达效 。
关键 词 : 生产工艺 轧制节奏 机时产量 1 生产 工 艺简 介
41 加 热 区域 的改 进 办法 .
411 加 热 炉上 料 台架 的改进 ..
通 过对 生 产 过程 的深 入 分 析 ,影 响棒 材 厂 轧 制 节奏提 升 主要 因素 有 : 31 加热 炉 出钢节 奏 与轧 制 节奏 不 匹配 .
加 热 炉上 料 台架原 设 计 末 端 有 钢检 测 是 采 用
棒材粗中轧轧件头部开裂成因及改进方案

自2019年以来,生产线堆钢事故频发,而粗轧 堆钢事故占了很大比例,其中前9机架堆钢的最主 要原因就是头部开裂(劈头)。对于产量、坯耗、能耗 等方面产生了很大影响,亟待解决。
1粗轧过程中头部开裂的成因分析 线棒作业区棒材主要生产规格为012 mm、
014 mm、O16 mm的HRB400E,这是一条由高速线 材轧线改造的。故有必要对其棒材生产工艺进行简 单介绍。
1.1该生产线的主要工艺设备 1) 200 n?蓄热式步进加热炉,最大加热能力为
每小时1101,加热钢坯长度为5.7-6.25 mo 2) 粗中轧机组为单线连续式布置,直流调速电
机单独传动。其中1—4架轧辐直径600 mm,5—9 架 480 mm,中轧 10—13 架 350 mm0
3) 预精轧机组为德国德马克公司进口 ,14,16架 为悬臂水平轧机,15、17架为悬臂立式机架,单线连 续式布置,直流调速电机单独传动。其中14—17架 轧辐直径275 mm。
4 )/1棒R轧机组为德国德马克公司进口 ,15。/75°交 替布置的悬臂式精轧机,直流调速电机集体传动。高 速无扭轧制,全部碳化铸辐环,表面光洁、尺寸精度
棒材线精轧机接轴托架的优化改进
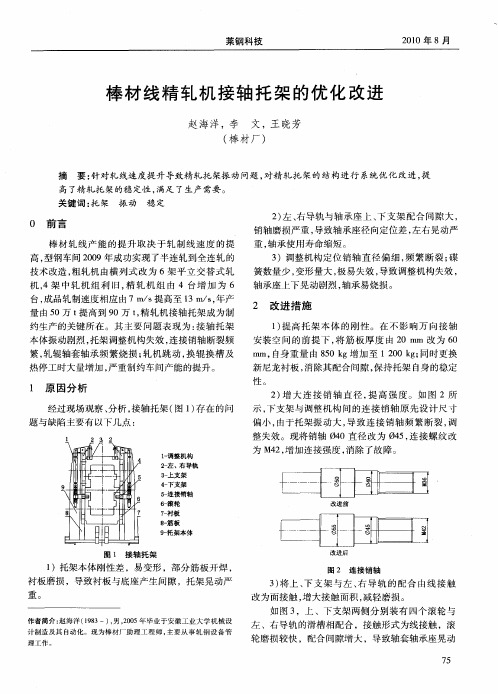
21 0 0年 8月
棒 材 线精 轧机 接轴 托 架 的优 化 改进
赵海洋 ,李 文,王晓芳 ( 棒材厂 )
摘
要 : 对 轧线速 度提 升 导致精 轧托 架振 动 问题 , 针 对精 轧 托 架 的结 构进 行 系统优 化 改进 , 提
振动 稳 定
高 了精轧 托 架的稳 定性 , 满足 了生产 需要 。
关键 词 : 架 托
0 前 言
棒 材 轧 线 产 能 的提 升 取 决 于 轧 制 线 速 度 的提 高, 型钢 车 间 2 0 0 9年 成功 实现 了半 连轧 到全 连 轧 的 技术 改造 , 粗轧 机 由横 列 式 改 为 6架平 立 交 替 式 轧
2 左 、 导轨 与轴 承 座 上 、 支架 配 合 间隙 大 , ) 右 下 销轴 磨损 严重 , 致轴 承座径 向定 位差 , 导 左右 晃 动严
衬 板磨 损 ,导致 衬板 与底 座产 生 间隙 ,托架 晃动 严
重。
作者简介 : 赵海洋( 9 3一) 男 ,05年毕业于安徽工业大学机 械设 18 , 20 计制造及其 自动化。现 为棒材厂助理 工程师 , 主要从事 轧钢设备 管
理工作。
3 将 上 、 支 架 与左 、 导 轨 的 配 合 由线 接 触 ) 下 右
严重 ,轴 承频 繁烧损 。现将 上下 两滚轮 改为 一块 直
第 4期 ( 总第 18期 ) 4 调 整 困难 ,上下轴 承座 跳动 严重 ,影 响轴承使 用 寿
命 。现将 调 整螺栓 长度加 长 ,安装 8片 碟簧 ,预 紧
键板 ,并 与支架 焊为 一体 ,使上 下支架 与左 、右 导 轨配 合 由线 接 触 改 为 面接 触 ,消 除 轴 向与 径 向 间
优化轧辊孔型配置 提高轧辊周期轧制量
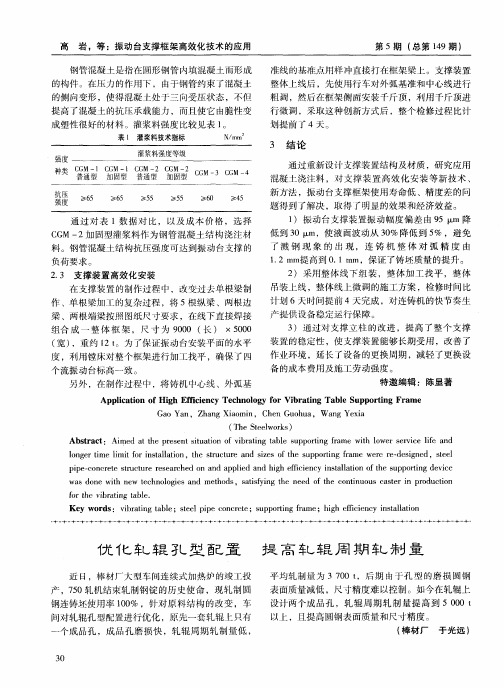
C M一 G 2加 固型灌浆 料作 为钢 管 混凝 土结 构浇 注材 料 。钢管混 凝土 结构抗 压 强度可 达到振 动 台支撑 的
负荷要 求 。 2 3 支 撑装 置高效 化安 装 .
Ga n, Zh ng Xio n, Ch r Gu h a, W a g Ye i o Ya a a mi e o u t n xa
( h te ok ) T eSel rs w
Absr c t a t:Ai d a h r s n iu to fvb ai g tb e s p o tn r me wi o r s r ie l e a d me tt e p e e tst ain o ir tn a l u p ri g fa t l we e v c i n h f ln e i i tf ri t lain,t e sr cu e a d sz s o he s pp ri g fa r e d sg e o g rt me l o nsa lto mi h tu t r n ie ft u otn me we e r — e in d,se l l t e
一
表 面质 量减低 ,尺寸精 度难 以控 制 。如 今在 轧辊 上 设 计两 个成 品 孔 ,轧 辊 周 期 轧制 量提 高到 500t 0
以上 ,且提高圆钢表面质量和尺寸精度 。
( 棒材 厂 于光远 )
个成 品孔 ,成 品孔磨 损 快 ,轧 辊 周 期 轧制 量 低 ,
3 0
低到 3 m,使液 面波动 从 3 % 降低 到 5 ,避 免 0 0 %
圆钢孔型系统的优化改进

体系,但每种规格几乎都有一套独立 的孑 型系统 , L
各种 规 格之 间 的孑 型共用 性极 差 ,致使 在频 繁换 规 L 格 的情 况下频 繁 换辊 ,而 且每 更换 一种 规格 ,几 乎
所有轧机都要拆装一次 ,轧机作业率很低。同时, 也加大了生产准备 的工作量 ,职工疲于拆装轧机而 无 法 对轧 机 进 行 正 常 维 护 和 维 修 ,轧 机 准 备 不 充 分 ,产量 和产 品 质量一 直 在低 谷徘 徊 ;另外 ,由于
程。
表 1 第 二 套 孔 型 系统 优 化 后 工 艺流 程表 mm
机架
来
料
备 注
从以上规格可 以看 出,除 0 2m 1 m规格以外 , 其余规格均是以成前一成品的连续式孔型组成 ,更 换 规格 非常方 便 。
32 中、精 轧孔型 系统 的优化 配置 . 中 、精 轧孔 型系统 优化 改进 以后 ,虽然在 很大 程度 上增加 了生 产工 艺 的柔 性化 ,但是 ,由于规格 多 ,批量 小 ,规 格 跨 度 较 大 ( 0 2 m 到 5 从 1 m
—
9道 采 用 六 角一 方孑 型 。连 铸 坯 经 50mm 轧 L 5
机轧 制 7 道 或 9道 后 出 半 成 品 进 入 中 轧 机 组 ,
10m 2 0mmX 0 0mm的连 铸 坯从第 一 道 进 , 8 mX 2 30 10mm×10m × 0 0m 的连 铸坯 从第 三 道 进 , 5 5 m 3 0 m 近似 10mm 0 坯从 第 七 道 出 , 于 生 产 2 m 以 用 5m 上规 格 圆 钢 , 0 m 坯 从 第 九 道 出 , 于 生 产 7 m 用
成品坯料为 50 m 5 m粗 轧机轧 出 的近似 10m 0 m 坯 ,由于 此孑 型系 统所 生产 的规 格大 。虽 然省 去 了 L 六角一方孑 型的扭转轧制,生产也比较顺行 、效率 L
棒材连轧机生产圆钢的孔型优化

出了优化合并重组方案 , 并制定 了相应的工艺技术及操作规 范 , 从而 简化 了孔型系列 , 降低 了配辊难 度 , 减少 了
操作废品率 , 生产稳定运行 。 使
效 生产 , 现对 现行 的 孔 型 系 统 及 相 关 规 格 存 在 的
2 l架孔 型 的共 用性 差 , 型系 统复 杂 , 孔 具体 为 从
1 3架开始 q 4 m, 2 oO m, 3 q 8 5  ̄ m ‘ 9~q m ‘ 5~  ̄ mm, 2 p 3 p 3 ~q 8 m 同走 1  ̄m 4 条轧 制 路线 ; ‘ 0~q 3 m, 5 而 P 2  ̄m 2 ~q 8 m,3  ̄ m ‘ 2~q 4 m, 2 p  ̄m 3 ~‘ 4 p mm组 距 同走 另 4
weee tbih d . h rcia rd cin s o h ttee i rv me t i l e as s s m n r ห้องสมุดไป่ตู้sa l e s te p a t lp o u t h w ta h s mpd e ns s c o mpi d p s yt i f e ad
问题 , 出 了孔 型系统 的优 化 合 并 重 组 方案 , 予 提 并
以实施 , 达到 了生产高效稳定顺行 的目的。
1条 轧制 路线 。因而 更换 规 格时 , 换辊 量 大且 时 间 长 , 机作 业率 低 , 轧 而且 轧辊 及 导 卫 装 置 等备 件 种 类多 , 消耗 大 , 生 产成 本增 加 。 使
( em nS eil t l oLd D n b i p c l te G o p ii  ̄ 6 0 1 B i a p c e t , o ge S ei el ru ,Qqh r 14 ) aS eC aS a 1
连轧棒材孔型系统的改进

刚度 闭 口轧机 ;
中轧机 组 : 4 0 6 水 平 二辊 高 刚度 闭 口 0 1x
l 8
连轧棒材孔型系统 的改进
谭翠英 ( 型轧钢 厂) 小
提 要 本文介 绍 了柳钢小 型轧 钢厂连 轧棒材 生产线 fT 型系统 的配 置和共用 性改 进 。 l L g 连轧 棒材 孑 型 L
关键 词 轧钢
l 概
况
精 轧 机组 : 3 0 6 短 应力 线轧 机 ,平 立 0 5x
柳 钢小 型轧 钢 厂连 轧 棒 材 生 产 线 是 19 99
年 对原 6 0轧钢厂 改造而 成 的生 产线 ,保 留 了 5
交替布置 ,7轧 机为平 立可转 换轧机 。 l
2 孔型 系统改进前存在的问题
连 轧棒 材生 产线 单线轧 制时采 用箱形孔 型
和椭 圆一 圆孑 型系统 , 中 , L 其 第一 架采用箱 形孑 L
连轧 状态 的稳 定 和保证产 品表 面质量 ,孑 型 系 L 统 的选择 适应 了连 轧生 产的要求 ,但 仍存在 以
下 问题 :
及精轧机组 , 轧机均 由直 流 电机 单独 传动 , 各架
粗 中轧 机组采用 微张 力控制 轧制 ,在 中轧机组 与精轧 机组之 间 、精轧 机组 各架轧 机之 间设有
生 裂纹 。
件 的料 形 、料厚 ,并 严格执 i l 钢操 作 ‘ 艺 规 L i I
程, 不喂 低 温钢 、 黑头 钢 , 头钢 必 须割 除 后 才 烂
棒材轧机精轧系统工艺优化
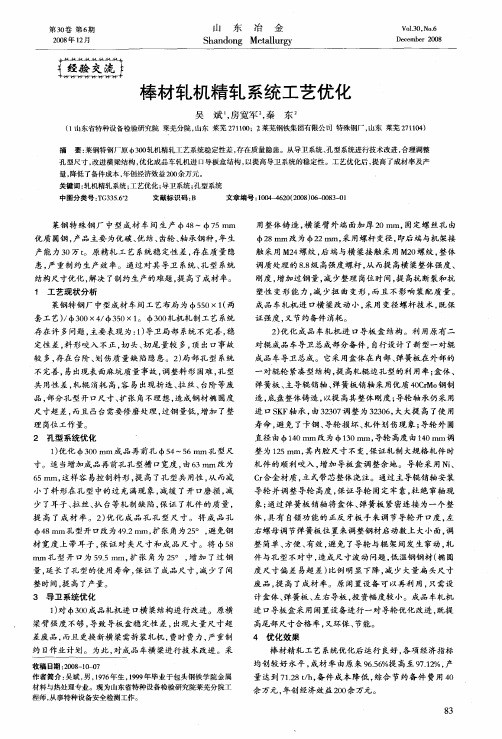
对辊 轮 紧凑 型 结构 , 高轧辊 边孔 型 的利 用 率 ; 提 盒体 、
弹簧板 、 导辊 销 轴 、 主 弹簧 板销 轴 采 用优 质 4 CMo 制 0r 钢 造 , 盘 整体 铸造 , 底 以提 高其整 体 刚度 ; 导轮 轴 承仍 采 用 进 口S F 承 , 337 整 为 336 大 大提 高 了使 用 K 轴 由 20 调 20 ,
棒 材轧机精 轧 系统工艺优化
吴 斌 。房宽军 秦 , , 东
( 山东省特种设 备检验研究院 莱芜分院 , 1 山东 莱芜 2 10 ;2 7 10 莱芜钢铁集 团有 限公司 特殊钢厂 , 山东 莱芜 2 10 ) 7 14
摘
要: 莱钢特钢厂原 30 机精 轧工艺系统稳定性差 , 在质量隐患 。从导卫 系统 、 型系统进行技术改进 , 0轧 存 孔 合理调整
莱钢 特 殊 钢 厂 中型 成 材 车 间 生产 4 ~ 7 L 8 51r Tn
优 质 圆钢 , 品 主要 为优 碳 、 结 、 产 优 齿轮 、 轴承 钢 种 , 生 年
用整 体 铸 造 , 梁臂 外 端 面加 厚 2 1 , 横 0n1 固定 螺 丝孔 由 l 1 2 l 改为 2 1 用螺杆 变径 , 端 与机 架接 8nl IT 2I , ml采 即后
孔型尺寸 , 改进横粱结构 , 优化成 品车轧机进 口导板盒结 构 , 以提高导卫 系统 的稳定性 。工艺优化 后 , 提高 了成材 率及产 量, 降低了备件成本 , 经济效 益2 0 年创 0 余万元 。
关键词 : 轧机精 轧系统 ; 艺优化 ; 工 导卫 系统 ; 型系统 孔 中图分类 号 :G 3 . T 3 562 文献标识码 : B 文章编号 :0 4 4 2 (0 8 0 — 0 3 0 10 - 6 0 2 0 )6 0 8 — 1
邢钢高速线材轧机粗轧孔型优化实践
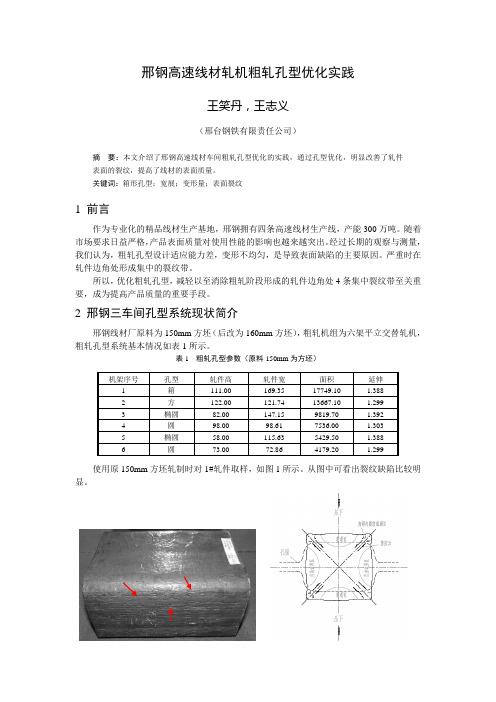
邢钢高速线材轧机粗轧孔型优化实践王笑丹,王志义(邢台钢铁有限责任公司)摘要:本文介绍了邢钢高速线材车间粗轧孔型优化的实践,通过孔型优化,明显改善了轧件表面的裂纹,提高了线材的表面质量。
关键词:箱形孔型;宽展;变形量;表面裂纹1 前言作为专业化的精品线材生产基地,邢钢拥有四条高速线材生产线,产能300万吨。
随着市场要求日益严格,产品表面质量对使用性能的影响也越来越突出。
经过长期的观察与测量,我们认为,粗轧孔型设计适应能力差,变形不均匀,是导致表面缺陷的主要原因。
严重时在轧件边角处形成集中的裂纹带。
所以,优化粗轧孔型,减轻以至消除粗轧阶段形成的轧件边角处4条集中裂纹带至关重要,成为提高产品质量的重要手段。
2 邢钢三车间孔型系统现状简介邢钢线材厂原料为150mm方坯(后改为160mm方坯),粗轧机组为六架平立交替轧机,粗轧孔型系统基本情况如表1所示。
表1 粗轧孔型参数(原料150mm为方坯)使用原150mm方坯轧制时对1#轧件取样,如图1所示。
从图中可看出裂纹缺陷比较明显。
图1 粗轧1#(Q195)侧面图2 钢坯在1#孔型变形示意图改用160孔型轧制150mm方坯后,通过对1#、2#轧件取样分析,发现1#比原150孔型表面质量有所改善,但在1#料两侧边角处存在“黑线”,说明“黑线”在过第一架粗轧机时就出现了,由于孔型所限,钢坯角部在前两架变形量过大,轧制后形成褶皱,并在随后的轧制中逐渐形成集中的裂纹带。
图3-a、3-b分别为1#、2#轧出钢坯侧面酸洗样照片(钢种为Q195)。
图3-a Q195 1#料对称侧面照片图3-b Q195 2#料对称侧面照片3 孔型优化方案实施与效果3.1方案一:减小1#孔型圆角。
将1#孔型(建立在160孔型轧制150mm方坯孔型基础上)圆角从R=25mm改为R=15mm。
3.1.1方案一原理分析:对于粗轧机架,特别是K1,K2孔表面皱褶已经形成。
为了减轻箱型孔角部过渡圆弧部位的影响,角部圆弧半径由R25mm改为R15mm左右,减少角部变形量,减轻角部折叠和表面皱褶。
棒材线轧机系统优化

棒材线轧机系统优化中图分类号:TG333 文献标识码:A 文章编号:1009-914X(2017)13-0151-01宣钢二棒生产线自投产以来,主要生产两切分(20、22)、三切分(14)的螺纹钢。
随着二棒线生产节奏加快产量日益提高,原来的轧机系统设备常出现事故停机,不能满足现今生产需要。
1、轧机故障及原因分析(1)、二棒?预穿水、穿水辊道辊子安装在1.6米长轴的轴端,依靠辊子与轴的过盈量结合键槽内平键实现周向固定和联接,为防止辊子在使用过程中退出,轴端加工有螺栓孔,通过旋紧压盖螺栓压紧辊子起到防退作用。
但在实际生产过程中,辊子的不停旋转造成孔径逐渐变大、轴径变小和平键磨损,过盈量无法保证,径向跳动加剧,严重时还会发生堆钢事故。
(2)、轧机平衡机构完全依靠2cm宽的链条带动接轴头套来实现上下接轴位置的调节,由于链条强度较小,经常断裂或扭曲。
这样就会加大头套调节的难度,当需要更换轧机时,需要用天车配合将上接轴头套吊起与轧机配合安装,就会无形中的加大更换轧机的难度,造成停机时间。
(3)、万向轴的强度、扭矩较低导致7#、8#、9#、10#、13#、15#主机接轴损坏次数较多。
(4)、由于轧制工艺的不同,当扎件从6#轧机出来进入1#剪实施切头时,轧件头部属于下弯状态,这样就导致1#剪入口导槽磨损严重,扎件无法正常进入1#剪剪切范围,导致压钢。
2、方案设计与改造针对目前问题,为提升设备技术性能、降低备件费用和故障停机,对轧机系统实施技术适应性改进,解决上述生产问题,降低系统故障停机率,维护成本得到有效控制,停机时间取得大幅降低,实现降本增效的目的。
(1)预穿水、穿水辊道将长轴端部切除一部分,安装鼓形齿式联轴器,辊子改为带轴颈的辊子,安装另一半鼓形齿式联轴器,最后轴侧与辊子侧联轴器联接。
由于鼓形齿式联轴器能传递很大的转矩,并允许有较大的偏移量,且安装精度要求不高,所以在满足了实际需求的同时,极大地方便了拆检更换工作,30分钟即可更换一颗辊子而轴不需更换,在降低备材费用和劳动强度方面取得较大突破。
一棒粗轧4号扭转辊孔型的改进
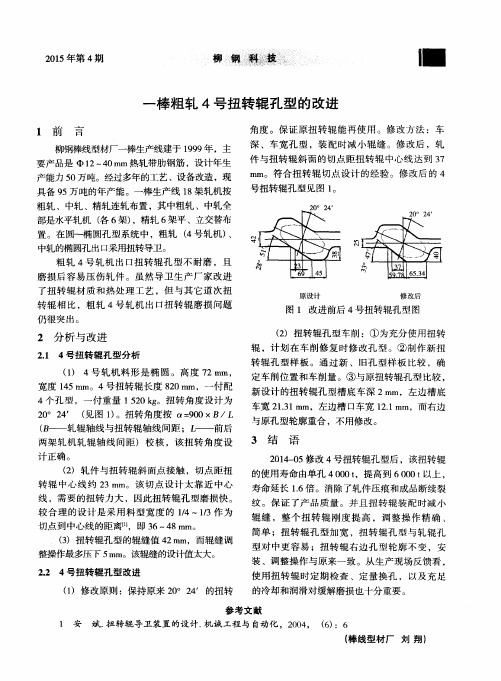
辊缝 ,整个扭转 辊刚度 提高 ,调整操作精 确 、
号扭 转辊 孔 型见布置 ,其中粗轧 、中轧全 部是水平轧机 ( 各 6架 ) ,精 轧 6架平 、立交替 布
置 。在 圆—椭 圆孔 型 系统 中 ,粗轧 ( 4号 轧 机) 、
中轧 的椭 圆孑 L 出 口采用扭转导卫 。
粗轧 4 号 轧机 出 口扭转辊孔 型不耐磨 ,且
新设计 的扭转辊孑 L 型槽底车深 2 m m,左边槽 底
车宽 2 1 . 3 1 m m,左 边槽 口车宽 1 2 . i m m,而右边 与 原孔 型轮 廓重合 ,不用修 改 。
( B 一
轧辊 轴 线 与扭转 辊 轴线 间距 ;E 一 前 后
两架轧机轧辊轴线间距)校核 ,该扭转角度设 计 正确 。
简 单 ;扭 转 辊 孔 型 加 宽 ,扭 转 辊 孔 型 与 轧 辊 孔 型对 中更 容 易 ;扭 转 辊 右 边 孑 L 型 轮 廓 不 变 ,安 装 、调整 操作 与原 来一 致 。从 生 产 现场 反馈 看 ,
使用扭转辊时定期检查 、定量换孔 ,以及充足
的冷 却和 润滑 对缓 解磨 损也 十分 重要 。
2 0 1 5 年第 4 期
撅薹
|
q
陵 - 畿 L|
一
棒 粗 轧 4号 扭 转 辊孔 型 的改进
角度 。保证原扭转辊能再使用 。修改方法 :车
深 、车 宽 孔 型 ,装 配 时 减 小 辊 缝 。修 改 后 ,轧
棒材机组生产线轧机区设备改造

第2 卷 2 1年第4 ( 8 00 期 总第 18 ) 4期
棒材机组 生产 线轧机 区设备 改造
安 青 范海 军 韩彩 凤 ( 阳钢铁 公 司第一轧 钢厂 安钢 4 5 0 ) 安 5 0 4
摘 要 为 了挖 掘 生 产 潜 力 , 高 经 济技 术 指 标 , 过 自行 设 计 制 造 相 关装 置 , 功 解 决 了轧 机 区设 备 设 计 提 通 成
连 续 出坯 提 供 了可 靠 的设 备 保 障 。对 国 内 同类 型 设备 的改 造具 有一 定 的借 鉴 意义 。
( 0 0 1 9收 稿 ) 2 1 -0 —1
铸 坯 输 送 辊 道 的改 造 , 对 铸 机 各 方 面性 能 未
・---— —
43 -— - - - —
第 2 卷 2 1 年第4 总第 18 ) 8 00 期( 4期
组 的 8 和 1 号 轧机 的锁 紧 和横 移全 部 采用 了液 号 0 压 控制 。
图 1 机组半连续式工艺平面布置
1 改造 前存在 问题
( ) 品规 格范 围窄 : 组 现有 的装 备水 平 只 3产 机
能生 产 2 r ~ 2m 0 m 8 m的 圆钢 , 品种 、 格 上 a 在 规 不 能 与其他 机组 形成 产 品系 列 。 2 改 造方 案 ( ) 进 轧机 横 移 装 置 , 1改 采用 国 内外先 进 的锁 紧机构 和控 制 系统 , 并完 善润 滑 系统 。
() 4 系统实现信息化数字处理 , 采用三 级网络 三
自动化控制 , 实现 全过程 自动 化。 ( ) ,,0 电动 机改直 流后 , 58 9 1 架 可对 轧机 进行 调速 , 高生产 能力 , 提 增加产 量 。
棒材全连轧工艺优化

椭 一 圆 孔 型 系 统 , 、 轧 采 用 椭 一 圆孔 型 系 中 精
统 。中轧 、 轧之 间有 3 距 离 , 为超 级 钢轧 制 精 0i n 是 准备 穿水 冷却 预 留的空 间 。粗 轧 系统微 张力 轧 制 , 中轧 、 轧之 间和精 轧轧 机 之间设 有立 式活 套器 采 精
生 。紧 急 停 车 会 造 成 整 个 粗 轧 机 组 夹 钢 , 至少 要 1 ~2 h的处理 时间 , 严重 影响生产 节奏 。
22 原 因分析及 改进措施 .
济钢 一小 型厂 进行 了全 连轧 改造 , 由原 来 的半 连 轧改为 1 架全 连轧 , 轧 、 8 粗 中轧 和精轧 各 6 , 1 万 t 2万 , 0 以上 , 高成 品轧 最
机 出 口速度 1 . m s 7 /。工 艺 流 程 为 : 料一 蓄 热步 5 坯
卫 方 面 的影 响 ; 析 认 为 , 分 主要 原 因是粗 轧 孔 型结 构 尺寸 不合理 。原 粗 ̄ : 型为双 斜度 箱形 孔 , LL f 槽底
轧 采用 平立 交 替 布置 , 、 机组 采 用 平辊 扭 转 轧 中 精
制; 加热炉 改 为蓄热 步进 式 , 效尺 寸 1.mx2 . 有 11 1 9 m; 、 3飞剪 为 启停 式 ; 床 改 为 10i x1.1 1 2、 冷 2 25T n I 步进齿条式 。使用原料为 10mmx10m 96 0 5 5 mx( 0
量 大 ( 图 l) 见 a 。接近 槽底 的侧 壁宽度 为 10m 小 4 m, 于轧 制坯 料宽度 (5 m) 10m 。同时 , 双斜度 箱形孔本 身靠 近辊 缝两 侧壁 成一 定 的外 张 角度 , 这样 在轧辊 压力 和接 近槽 底两 夹持 侧壁 的作 用下 , 以侧 壁直线 的交 点 曰为分 界点 , 咬人 时轧件 金属 流 动受 到夹持 侧壁 A B作用 , 持挤 压沿 着扩 张侧 壁 B 夹 C向辊 缝处 流动 , 造成 了轧件两边 凸起 。又 由于 A 段 孔型尺寸 B 小 于坯料 本 身 尺寸 , 使得 金 属 向箱形 孔 4 角流 动时 受 到侧 壁 的强 烈摩擦 阻力 , 中间不会 受 到摩擦 力作
关于提高550粗轧共轭孔型过钢量的优化设计
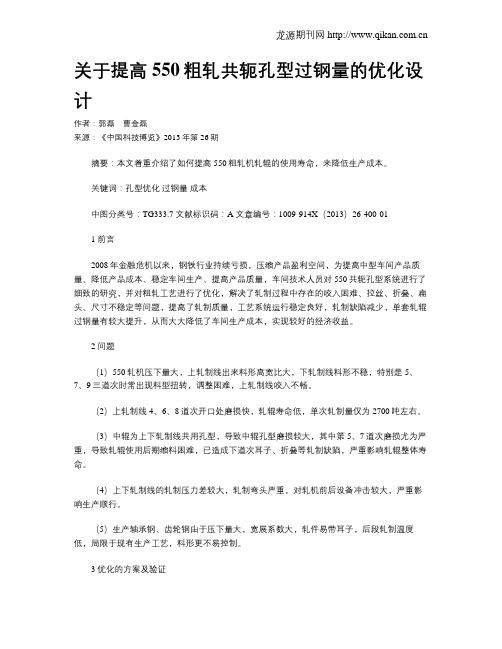
关于提高550粗轧共轭孔型过钢量的优化设计作者:郭磊曹金磊来源:《中国科技博览》2013年第26期摘要:本文着重介绍了如何提高550粗轧机轧辊的使用寿命,来降低生产成本。
关键词:孔型优化过钢量成本中图分类号:TG333.7 文献标识码:A 文章编号:1009-914X(2013)26-400-011 前言2008年金融危机以来,钢铁行业持续亏损,压缩产品盈利空间,为提高中型车间产品质量、降低产品成本、稳定车间生产、提高产品质量,车间技术人员对550共轭孔型系统进行了细致的研究,并对粗轧工艺进行了优化,解决了轧制过程中存在的咬入困难、拉丝、折叠、扁头、尺寸不稳定等问题,提高了轧制质量,工艺系统运行稳定良好,轧制缺陷减少,单套轧辊过钢量有较大提升,从而大大降低了车间生产成本,实现较好的经济收益。
2 问题(1)550轧机压下量大,上轧制线出来料形高宽比大,下轧制线料形不稳,特别是5、7、9三道次时常出现料型扭转,调整困难,上轧制线咬入不畅。
(2)上轧制线4、6、8道次开口处磨损快,轧辊寿命低,单次轧制量仅为2700吨左右。
(3)中辊为上下轧制线共用孔型,导致中辊孔型磨损较大,其中第5、7道次磨损尤为严重,导致轧辊使用后期缩料困难,已造成下道次耳子、折叠等轧制缺陷,严重影响轧辊整体寿命。
(4)上下轧制线的轧制压力差较大,轧制弯头严重,对轧机前后设备冲击较大,严重影响生产顺行。
(5)生产轴承钢、齿轮钢由于压下量大,宽展系数大,轧件易带耳子,后段轧制温度低,局限于现有生产工艺,料形更不易控制。
3 优化的方案及验证在原有孔型系统基础上,保证轧件在辊道上平稳运行;各道次咬入方便;提高孔型系统的兼容性;在第一道次中辊、第二道次上辊增加孔型凸度;增加孔型系统的侧壁斜度,方便孔型对中。
增大孔型上下轧制线的辊缝值,提高孔型系统的可调性。
减少轧件在轧制时的扭转,咬入不正,翻钢等工艺问题;特制定了以下优化方案,并实施,实施过程如下:3.1 在第一道次中辊,第二道次上辊增加高为6mm的槽底凸度,增加第一、第二道次的轧辊咬入能力,保证轧件断面稍凹,便于轧件在辊道上的稳定运行;给翻钢后的3、5、7、9道次增加宽展余地,减少出耳子的几率;保证轧件侧面平直;减轻轧槽磨损,提高轧槽的使用寿命。
大棒材开坯轧机压下系统研究及优化设计
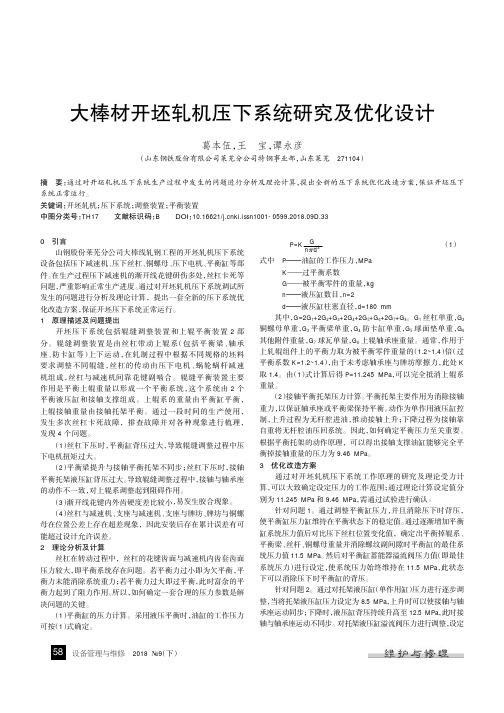
大棒材开坯轧机压下系统研究及优化设计葛本伍,王宝,谭永彦(山东钢铁股份有限公司莱芜分公司特钢事业部,山东莱芜271104)摘要:通过对开坯轧机压下系统生产过程中发生的问题进行分析及理论计算,提出全新的压下系统优化改造方案,保证开坯压下系统正常运行。
关键词:开坯轧机;压下系统;调整装置;平衡装置中图分类号:TH17文献标识码:B DOI:10.16621/ki.issn1001-0599.2018.09D.330引言山钢股份莱芜分公司大棒线轧钢工程的开坯轧机压下系统设备包括压下减速机、压下丝杠、铜螺母、压下电机、平衡缸等部件。
在生产过程压下减速机的渐开线花键研伤多处,丝杠卡死等问题,严重影响正常生产进度。
通过对开坯轧机压下系统调试所发生的问题进行分析及理论计算,提出一套全新的压下系统优化改造方案,保证开坯压下系统正常运行。
1原理描述及问题提出开坯压下系统包括辊缝调整装置和上辊平衡装置2部分。
辊缝调整装置是由丝杠带动上辊系(包括平衡梁、轴承座、防卡缸等)上下运动,在轧制过程中根据不同规格的坯料要求调整不同辊缝,丝杠的传动由压下电机、蜗轮蜗杆减速机组成,丝杠与减速机间靠花键副啮合。
辊缝平衡装置主要作用是平衡上辊重量以形成一个平衡系统,这个系统由2个平衡液压缸和接轴支撑组成。
上辊系的重量由平衡缸平衡,上辊接轴重量由接轴托架平衡。
通过一段时间的生产使用,发生多次丝杠卡死故障,排查故障并对各种现象进行梳理,发现4个问题。
(1)丝杠下压时,平衡缸背压过大,导致辊缝调整过程中压下电机扭矩过大。
(2)平衡梁提升与接轴平衡托架不同步;丝杠下压时,接轴平衡托架液压缸背压过大。
导致辊缝调整过程中,接轴与轴承座的动作不一致,对上辊系调整起到阻碍作用。
(3)渐开线花键内外齿硬度差比较小,易发生胶合现象。
(4)丝杠与减速机、支座与减速机、支座与牌坊、牌坊与铜螺母在位置公差上存在超差现象,因此安装后存在累计误差有可能超过设计允许误差。
棒材轧线粗机控制系统的优化和应用
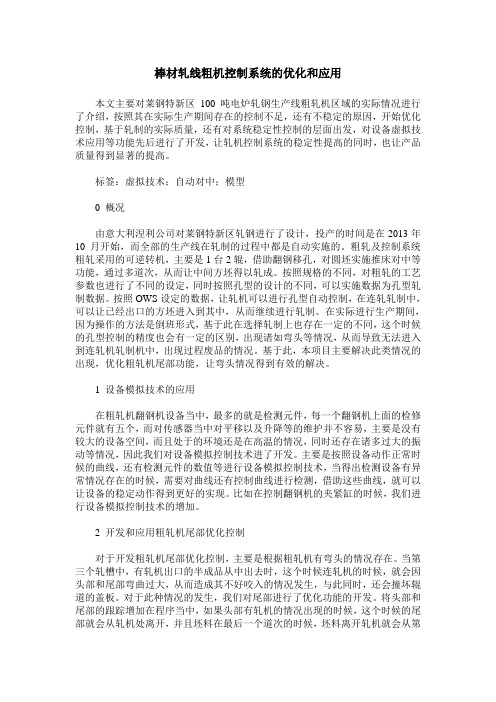
棒材轧线粗机控制系统的优化和应用本文主要对莱钢特新区100吨电炉轧钢生产线粗轧机区域的实际情况进行了介绍,按照其在实际生产期间存在的控制不足,还有不稳定的原因,开始优化控制,基于轧制的实际质量,还有对系统稳定性控制的层面出发,对设备虚拟技术应用等功能先后进行了开发,让轧机控制系统的稳定性提高的同时,也让产品质量得到显著的提高。
标签:虚拟技术;自动对中;模型0 概况由意大利涅利公司对莱钢特新区轧钢进行了设计,投产的时间是在2013年10月开始,而全部的生产线在轧制的过程中都是自动实施的。
粗轧及控制系统粗轧采用的可逆转机,主要是1台2辊,借助翻钢移孔,对圆坯实施推床对中等功能,通过多道次,从而让中间方坯得以轧成。
按照规格的不同,对粗轧的工艺参数也进行了不同的设定,同时按照孔型的设计的不同,可以实施数据为孔型轧制数据。
按照OWS设定的数据,让轧机可以进行孔型自动控制,在连轧轧制中,可以让已经出口的方坯进入到其中,从而继续进行轧制。
在实际进行生产期间,因为操作的方法是倒班形式,基于此在选择轧制上也存在一定的不同,这个时候的孔型控制的精度也会有一定的区别,出现诸如弯头等情况,从而导致无法进入到连轧机轧制机中,出现过程废品的情况。
基于此,本项目主要解决此类情况的出现,优化粗轧机尾部功能,让弯头情况得到有效的解决。
1 设备模拟技术的应用在粗轧机翻钢机设备当中,最多的就是检测元件,每一个翻钢机上面的检修元件就有五个,而对传感器当中对平移以及升降等的维护并不容易,主要是没有较大的设备空间,而且处于的环境还是在高温的情况,同时还存在诸多过大的振动等情况,因此我们对设备模拟控制技术进了开发。
主要是按照设备动作正常时候的曲线,还有检测元件的数值等进行设备模拟控制技术,当得出检测设备有异常情况存在的时候,需要对曲线还有控制曲线进行检测,借助这些曲线,就可以让设备的稳定动作得到更好的实现。
比如在控制翻钢机的夹紧缸的时候,我们进行设备模拟控制技术的增加。
- 1、下载文档前请自行甄别文档内容的完整性,平台不提供额外的编辑、内容补充、找答案等附加服务。
- 2、"仅部分预览"的文档,不可在线预览部分如存在完整性等问题,可反馈申请退款(可完整预览的文档不适用该条件!)。
- 3、如文档侵犯您的权益,请联系客服反馈,我们会尽快为您处理(人工客服工作时间:9:00-18:30)。
收稿日期:2001-04-02 作者简介:李立新(1963—),男,武汉科技大学材料与冶金学院,副教授.棒材粗轧机组接轴扭矩均衡分配孔型优化设计李立新,黄 宁,周家林,唐 力(武汉科技大学材料与冶金学院,湖北武汉,430081)摘要:以某棒材粗轧机组力矩均衡分配为目标,对各孔型尺寸进行了优化设计。
结果表明:优化后各机架力矩富余比较均衡,最小力矩富余有较大提高。
关键词:轧机;扭矩;孔型;优化中图分类号:TG 335.6+2 文献标识码:A 文章编号:1001-4985(2001)03-0233-03 某棒材车间粗轧机组由6台平2立交替布置的轧机组成。
该机组第1、第2架采用箱型孔;第3架、第5架为椭圆孔;第4架、第6架为圆孔。
粗轧机组各机架采用十字型万向联轴器连接。
在使用过程中,部分机架联轴器的花键轴常发生具有静强度损坏性质的局部扭曲变形。
经计算,各架接轴扭矩均有富余,但各架富余值相差很大,即各架负荷分配极不均匀。
因此,当某一工艺参数波动时,富余值小的接轴有可能被损坏。
为此,作者在粗轧机组原料、成品孔型系统、开轧温度等不变的条件下,通过对孔型尺寸进行优化设计,以达到各机架万向接轴扭矩均衡分配的目的。
1 优化模型的建立1.1 设计变量的选取延伸孔型系统一般为间隔出现等轴断面轧件的孔型系统。
在保证坯料、产品及孔型系统不变的条件下,显然选取第二孔轧件边长x 1及第四孔圆半径x 2作为设计变量,其他各孔型的轧件尺寸即可确定。
1.2 目标函数设M (i )为第i 架轧机实际轧制时接轴传递的扭矩,M M (i )为第i 架轧机接轴额定扭矩,则粗轧机组各轧机接轴扭矩均衡分配可表述为求下述函数的极小值:f (x )=max (M (i )/M M (i ))-min (M (j )/M M (j ))(1)1.3 约束条件约束条件包括设备条件的限制,亦含工艺因素的制约,即:(1)不同孔型中的延伸系数有一个适宜的范围(μi min ,μi max ),即各架延伸系数应满足:μi min <μi <μi max (i =1,2, (6)(2) (2)扁轧件的稳定性指标,即奇数道次轧件宽高比不得超过允许轴比:b i /H 1i <[a w i ] (i =1,3,5)(3) (3)咬入条件。
各架实际压下量不得超过最大允许咬入角所对应的压下量,即:Δh i <D i (1-cos αmax )(i =1,2, (6)(4)式中:Δh i ———压下量;D i ———接触点处辊径;αmax ———最大允许咬入角。
(4)接轴扭矩限制。
各架接轴实际承受扭矩不得超过其额定值:M (i )<M M (i ) (i =1,2, (6)(5) (5)轧辊强度条件:1)辊身强度条件。
辊身主要承受弯曲应力σw ,其值不得超过轧辊材料的许用弯曲正应力[σ],即:σi w <[σi ] (i =1,2,…,6)(6) 2)辊颈强度条件。
辊颈既要承受弯曲应力,又要承受扭转应力,因轧辊为铸铁辊,故可采用第二强度理论来计算折合应力σwτ,其值不得超过[σ],即:σi w τ<[σi ] (i =1,2,…,6)(7) 3)辊头强度条件。
辊头处承受扭转应力τ,其值不得超过轧辊材料的许用扭转应力[τ],即:τi <[τi ] (i =1,2,…,6)(8) (6)电机能力:1)电机过载能力。
电机的最大功率N max 应小于过载系数K 与额定功率N od 的乘积,即:N max <KN od (i =1,2, (6)(9) 2)电机发热校核。
电机均方根功率N z 应小 第24卷第3期武汉科技大学学报(自然科学版)Vol.24,No.32001年9月J.of Wuhan Uni.of Sci.&Tech.(Natural Science Edition )Sep.2001于电机额定功率,即:N z<N od (i=1,2,…,6)(10) 上述约束条件均可写作g i(x)<0的形式,于是粗轧机组孔型的优化设计问题可归结为求如下带不等式约束的非线性优化问题: min f(x) st.g i(x)<0 (i=1,2,…,m)(11)式中:m=57。
2 计算模型及优化方法2.1 轧件尺寸的计算借助于相邻等轴断面轧件的尺寸,利用前后两道次轧制时的宽展公式可以建立一个以中间扁轧件宽b、高H1为未知量的非线性方程组,即:β1(b,H1)=0β2(b,H1)=0(12)解此方程组,即可得到中间轧件的尺寸。
2.2 宽展模型常用的宽展模型有Wusatowski模型、斯米尔诺夫宽展公式[1]、斋藤好弘模型[2]等。
因斯米尔诺夫公式比较齐全,计算也较方便,故本文选用该式,即宽展系数为:β=1+c(1/η-1)c1・A c2a0c3a k c4δ0c5Ψc6tan<c7(13)式中:1/η———压下系数;A———轧辊转换直径D3/H1,其中:D3为槽底直径,H1为孔型高度; a0———轧件轧前轴比;a k———孔型轴比;δ0———轧件在前一孔型中的充满度;Ψ———摩擦指数; tan<———箱型孔的侧壁斜度;c i(i=0,1,…, 7)———与孔型系统有关的常数。
2.3 接触面积的计算参考文献[3],按斯米尔诺夫推导的不同形状轧件在不同孔型中轧制时的接触面积公式计算轧件与轧辊间的接触面积,即:F=H1(B+b)(A(1/η-1)/8)0.5(14)式中:B———轧前轧件宽度。
2.4 单位压力计算轧制时的单位压力常按下式确定:p=1.15σs nσ(15)式中:nσ———不同孔型中的应力状态系数,按斯米尔诺夫或R.B.Sims压力模型确定;σs———金属变形抗力,依热力学系数方法按下式确定:σs=σ0K t KεK u(16)式中:σ0———温度为1000℃、变形程度为10%、变形速度为10s-1时,该钢种的基本变形抗力;K t,Kε,K u———考虑轧件温度t、变形程度ε和变形速度u的热力学系数。
2.5 轧制力矩的计算轧制力矩依斯米尔诺夫公式确定[1],即:M z=0.287σs H13A2n B(17)式中:n B———轧制力矩系数。
2.6 咬入条件允许咬入角αmax与轧件和轧辊间摩擦系数f 存在如下关系:αmax=tan-1f,而摩擦系数可按下式确定[4]:f=k1k2k3(1.05-0.0005t)(18)式中k1,k2,k3———考虑轧辊材质、轧制速度、轧件材质的系数;t———轧制温度,℃。
由于方件进入椭圆孔中轧制时,初始接触处的正压力P向内偏斜了一个角度γ(见图1),故此时允许咬入角αmax=tan-1(f/cosγ),其中γ= sin-1(x1/(2R))。
图1 方件进入椭圆孔时的情况2.7 优化方法鉴于用罚函数法求解非线性约束的优化问题相对于其他优化方法具有很多明显的优点,故本文选用该法。
即将式(11)表示的带不等式约束的非线性优化问题转化为求下述无约束优化问题的极小值:Φ(x,r(k))=f(x)-r(k)6m i=11g i(x)(19)式中:r(k)———惩罚因子,是随优化过程的进行而递减的一正数序列。
注意到各约束表达式的量纲不同,其数值亦可能相差很大,为客观反映各约束条件对罚函数的影响,计算时必须对其进行规范化处理。
3 计算结果为便于比较,令粗轧机组的坯料、成品、开轧温度、第一架轧制速度保持不变。
注意到该机组主要生产优特钢,现以40Cr钢轧制为例,优化后各架接轴转矩富余如图2中实线所示。
由该图可见,通过优化,各架接轴转矩富余较优化前(图2中虚线所示)均匀得多,接轴转矩最小富余量亦432 武汉科技大学学报(自然科学版) 2000年第3期有很大提高,即由优化前的17.97%提高到27.82%,从而大大提高了接轴的安全储备。
图2 各架力矩分配情况4 结论由上述计算可知,用本文提出的优化模型及方法,可使各架接轴扭矩的分配更加均匀,扭矩富余量大为提高,从而大大提高了各架接轴的安全性。
参考文献[1] 赵松筠,唐文林.型钢孔型设计[M ].北京:冶金工业出版社,2000.[2] 斋藤好弘,等.线材、棒钢压延の变形、负荷の数式とその孔型设计への应用[J ].塑性と加工,1983,24(273);1070—1077.[3] 王有铭.型钢生产理论与工艺[M ].北京:冶金工业出版社,1996.[4] 王廷薄.轧制工艺学[M ].北京:冶金工业出版社,1981.Pass Optimization Design of B ar Rolling Mills for TorqueU niform DistributionL I L i 2xi n ,HUA N G N i ng ,ZHO U Jia 2li n ,TA N G L i(College of Meterials and Metallurgy ,Wuhan University of Science and Technology ,Wuhan 430081,China )Abstract :Aimed at a uniform distribution of driving torques ,an optimization design of pass parameters is carried out for primary bar rolling mills.The results show that the surplus of torques is uniform and the minimum one has a significant increase.K eyw ords :rolling mill ;torque ;pass ;optimization (上接第227页) (2)通过对数学模型的校正和模型参数的在线自学习,提高了操作指导控制系统的设定计算精度。
轧制1.6mm 铝板时,厚度误差仅为-0.01mm 。
(3)操作指导控制系统机构简单,造价低,可供手工操作的冷轧机技术改造借鉴。
(4)操作指导控制系统还可用于轧钢专业实验。
(5)该系统若配上自动测厚仪,则可免去人工测量轧件厚度和计算机输入厚度的操作,并可获得轧件沿纵向的厚度分布数据。
The Computerized G uidance and Control Systemfor G ap Preset Operation on Cold MillZHA O Jia 2rong ,HU Y an 2sheng ,Y U Chi 2bi ng ,ZHA O Gang ,ZHA N G Y un 2xiang(College of Meterials and Metallurgy ,Wuhan University of Science and Technology ,Wuhan 430081,China )Abstract :The computerized guidance and control system for gap preset operation on cold mill can display the adjusting parameters of mill on CR T and the roll gap can be adjusted by operators based on the displayed pa 2rameters.All parameters of rolling process can be shown in one picture ,which provides support for cus 2tomers to control and analyze the rolling process.K eyw ords :computer control system ;cold mill ;gap preset5322001年第3期 李立新,等:棒材粗轧机组接轴扭矩均衡分配孔型优化设计。