颗粒机环模模孔开孔率
环模颗粒机参数调整

环模颗粒机参数调整分析环模颗粒机是生物质燃料、肥料、饲料等主要制粒设备,压辊环模的间隙是环模颗粒机操作时调整的重要参数之一,其调整过程也是环模颗粒机操作前重要的调整步骤之一,间隙调整的合理性将直接影响颗粒机的使用性能。
今天我们来看看环模颗粒机参数调整分析情况:环模颗粒机压辊环模间隙分析颗粒机压辊与环模的间隙一般为0.1mm-0.5mm,调节时通常使压辊的外表面与旋转环模的内表面轻微接触,并在环模带动下达到似转非转。
正常情况下,模孔小的两者间隙小些,模孔大的两者大些;新环模间隙小些,旧环模间隙大些。
正确调整间隙会使颗粒机获得最大的生产制造费用,节约产品成本,提高经济效益。
有研究数据分析,当压辊环模间隙为零时,粘附层厚度主要取决于压辊环模支承结构的刚性,而当增大压辊环模间隙时,会出现粘附层,这一粘附层使制粒工况发生了变化:在相同生产率条件下,增加了需压实的厚度,粘附层的膨胀部分不断被压实,并使物料受挤压的行程变长,压辊两侧出现严重漏料现象。
这些研究数据表明,模辊间隙大小对制粒性能参数,如生产率、电耗和颗粒加工质量都有着不同程度的影响。
1、间隙过大对制粒的影响压辊环模间隙过大时,其压制区的料层便会增厚,这厚厚的料层会增大压辊运行的阻力,从而使带动压辊运行所需电量增加,变相的提高了电量消耗,并且间隙过大容易导致压辊产生打滑和机身震动的情况,产量也会因此而降低,有时还会不出粒。
2、间隙过小对制粒的影响压辊环模间隙过小时,压辊与环模几乎处于直接接触的状态,在这样的状态下长期工作,容易产生机械磨损,或造成环模爆裂,严重影响机器的使用寿命。
环模导向口也会因压辊的机械性磨损而变形,使模孔进料困难或堵塞模孔。
压辊环模间隙调整注意事项1、正确调整压辊环模间隙,间距不能调成一边大一边小,这样容易造成主轴晃动,出料不畅,电流不稳等情况。
2、不同的物料需要不同的间隙。
3、新模要配新压辊,新环模新压辊可调至较小间隙。
4、配方含油脂较高,或无法降低干燥后的原料含水率时,可适当增大模辊间隙。
环模孔径大小对颗粒成型的影响

环模孔径大小对颗粒成型的影响日前有颗粒用户咨询:环模孔径3.0,现在感觉出的料直径3.3到3.5了,料的硬度也变大了。
环模孔径大小对颗粒成型有什么影响?颗粒料的硬度变大是因为环模孔径变大了吗?针对这些问题,宝壳压辊环模从以下内容与大家细细分析:颗粒机环模孔的相关结构参数1、模孔孔径。
从制粒质量和效率的角度来说,选用不同比例的环模孔径和厚度可产生不同的影响。
环模孔径比例过小,厚度较厚,则导致生产效率下降,增加企业生产成本;环模孔径比例过大则颗粒松散,对质量和制粒效果产生影响,因此为高效和优质生产的结果,必须科学合理选择环模的孔径和厚度等参数。
2、模孔有效长度。
模孔有效长度是饲料原料挤压致密成型的模孔长度。
选用有效长度越长的模孔,可使原料停留在环模内被压制的时间增加,使颗粒成型硬度变强;反之会使粉化率变高,颗粒松散,颗粒质量下降。
3、模孔长径比。
模孔长径比为模孔有效工作长度与模孔直径比。
为取得良好的制粒效果,大多选用较大的长径比,即达到颗粒硬度、颗粒密度和动态耐久性均逐渐变强的效果,提高颗粒质量,但增加能耗,容易造成塞机现象,因此要结合成型燃料产品要求等因素选用合理的长径比。
4、模孔结构常见的模孔结构有5种,即直形孔、压缩阶梯孔、外锥形孔、内锥形孔和释放阶梯孔等。
直形孔加工简单,压缩阶梯孔和外锥形孔被普遍使用,因其模孔有效长度被缩短,使物料被挤压时间缩短,对加工直径小于10mm的颗粒较为适合;释放阶梯孔适宜于加工直径大于10mm 质量低及粗纤维含量高的饲料。
5、模孔的排列传统模孔可排布成2种方式,阵列相对较整齐和错位排列。
从实际使用情况上看,错位排列使用效果更优,可使原料更均匀进入模孔。
依据布孔相互交错角度的差异,把错位排列划分成等腰三角形布孔和等边三角形布孔。
环模孔径大小对颗粒成型的影响调质温度升高,环模孔径降低,致使饲料粉化率降低,淀粉糊化度升高,从而提高饲料转化效率,动物也更喜爱这种颗粒料,即增强适口性,也得到优良的制粒效果;从饲养效果角度来说,小模孔压制的颗粒料,无论饲料是否完整,其饲喂效果都比大模孔的效果更好。
饲料环模最大的压缩比是多少
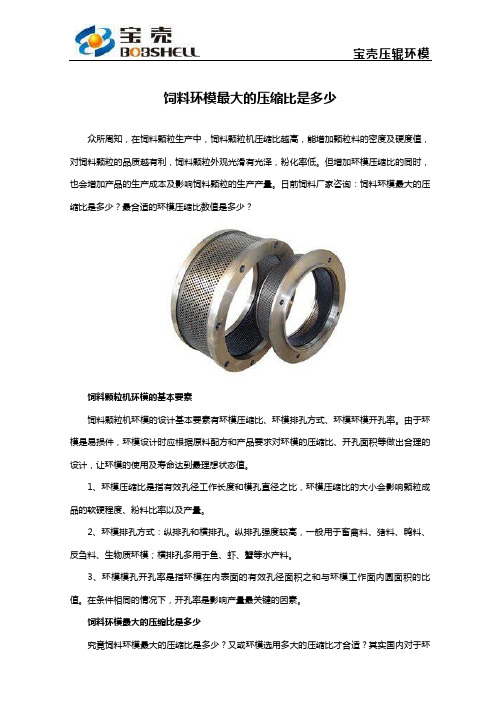
饲料环模最大的压缩比是多少众所周知,在饲料颗粒生产中,饲料颗粒机压缩比越高,能增加颗粒料的密度及硬度值,对饲料颗粒的品质越有利,饲料颗粒外观光滑有光泽,粉化率低。
但增加环模压缩比的同时,也会增加产品的生产成本及影响饲料颗粒的生产产量。
日前饲料厂家咨询:饲料环模最大的压缩比是多少?最合适的环模压缩比数值是多少?饲料颗粒机环模的基本要素饲料颗粒机环模的设计基本要素有环模压缩比、环模排孔方式、环模环模开孔率。
由于环模是易损件,环模设计时应根据原料配方和产品要求对环模的压缩比、开孔面积等做出合理的设计,让环模的使用及寿命达到最理想状态值。
1、环模压缩比是指有效孔径工作长度和模孔直径之比,环模压缩比的大小会影响颗粒成品的软硬程度、粉料比率以及产量。
2、环模排孔方式:纵排孔和横排孔。
纵排孔强度较高,一般用于畜禽料、猪料、鸭料、反刍料、生物质环模;横排孔多用于鱼、虾、蟹等水产料。
3、环模模孔开孔率是指环模在内表面的有效孔径面积之和与环模工作面内圆面积的比值。
在条件相同的情况下,开孔率是影响产量最关键的因素。
饲料环模最大的压缩比是多少究竟饲料环模最大的压缩比是多少?又或环模选用多大的压缩比才合适?其实国内对于环模压缩比并没有一个固定的标准,因为这个环模压缩比需与与模孔、直径、生产品种等有关。
建议从原料入手,鱼饲料可用12-11:1,猪和禽颗粒饲料可用10:1的压缩比。
另外含谷物高的配合饲料压缩比建议在8-12.5之间,热敏感饲料及尿素饲料压缩比建议在5-8之间,含天然蛋白质高的浓缩饲料压缩比适用于5-11之间,奶牛配合饲料压缩比建议在7~15之间。
从环模孔径方面考虑,有饲料厂家专门作为记录分析:鼠饲料建议环模孔径3.0,压缩比1:12左右,鸡饲料建议环模孔径3.0,压缩比1:10-1:13左右。
其他参考值:环模孔径3mm环模压缩比大概为12-12.5,而孔径3.5mm环模为13,孔径4mm为14,。
当然,根据配方来说生产含纤维比较高的品种,环模压缩比应相对取小些,对于粗饲料环模的压缩比建议在8:1左右。
制粒机环模孔径越小制粒硬度

制粒机环模孔径越小制粒硬度环模是制粒机的重要零部件,它的设计、材质、生产工艺及正常使用都影响着颗粒的产量及质量。
颗粒机环模模孔对制粒有什么影响呢?制粒机环模孔径越小制粒硬度又会有什么变化?颗粒机环模的主要参数1、环模厚度:环模厚决定于物料特性和模孔孔径,压制不同的饲料需要采用相应的最佳长(深)径比,以获得高质颗粒。
环模模孔孔径对颗粒饲料硬度影响不大,但对于产量却有明显的影响。
孔径、深径比孔径大的环模,制粒产量高,但也应选择合适的深径比。
模孔厚度过大,产量低,硬度高;模孔厚度小,则颗粒硬度小,达不到质量要求。
对一定厚度的环模来说,孔径越大,则模孔长度与孔径之比(长径比)越小,一般来说,模孔的长径比6-12为宜。
2、环模模孔深度:随着制粒机模孔有效深度的增加,颗粒饲料产量显著降低,能耗增加,颗粒的硬度提高。
这是因为随着制粒机模孔深度的增加,饲料所受摩擦力增加之故。
不同类型饲料的适宜模孔直径和深度范围:3、模孔的形状:一般来说,模孔的形状有以下几种:(1)圆柱型孔,直型孔。
这种孔适宜于加工各种配合饲料,应用最为广泛。
(2)内锥型孔(进口大,出口小)。
这种孔型便于物料进入,但是,物料进入模孔后被逐渐压缩,因此,内锥型孔用于压制密度大,硬度高而且粉化率低的颗粒,适宜于加工成粒性能较差的牧草粉等体积大的饲料。
(3)外锥型孔(进口小,出口大)。
与前者相反,物料进入后压力逐渐减小,有利于颗粒直接通过,因此压制出的颗粒密度较小,硬度低而且粉化率高。
适宜于加工如脱脂米糠等有后膨胀现象的高纤维饲料,以免颗粒滞留在孔里,造成堵塞。
(4)阶梯型孔(外大内小)。
压模厚度不变而模孔有效深度减少,减少了饲料的摩擦,从而降低了制粒温度,适宜于加工一些含有较多热敏感饲料的物料。
4、模孔间距:模孔间距与压制饲料的性质有关,如压制磨损性较小的饲料,可用孔距很近的环模。
压制磨损性大的饲料如含矿物高的饲料或高纤维料则用孔距大的环模。
5、模孔的粗糙度模孔的粗糙度越低(即光洁度愈高),物料在模孔内易于挤压成形,生产率高,而且成形后的颗粒表面光滑,不易开裂,颗粒质量好。
颗粒机环模开裂怎样修复

颗粒机环模开裂怎样修复环模颗粒机属于饲料制粒设备,是以玉米、豆粕、秸秆、草、稻壳等的粉碎物直接压制颗粒的饲料加工机械,是生产颗粒饲料的主要饲料机械设备。
环模颗粒机在农业方面的应用很广泛,其产量高、制粒精细,很受用户的欢迎。
环模是环模颗粒机的核心部件,也是易损部件,很多用户在使用过程中,通常会出现环模模具开裂的情况,到底导致环模颗粒机模具损坏的原因有哪些呢?颗粒机环模开裂怎样修复?今天宝壳压辊环模与大家一起分析分析。
颗粒机环模开裂的原因分析1、颗粒机环模所用的材质性能不稳定,不均匀,有局部内应力存在。
2、颗粒机环模的开孔率太高,造成颗粒机环模自身的强度、韧性下降。
颗粒机环模的厚度太薄,以致颗粒机环模强度下降;因此在选购颗粒机模具时应问清楚厂家模具的具体用料以及厚度情况。
3、颗粒机环模在运行过程中,被硬物强行挤压(如落在制粒腔内的轴承滚珠等金属物)所致;制粒室内如果掺杂进这些东西,轻则颗粒机模具损坏,重则很可能会伤害到颗粒机的操作人员,因此下料时一定要加强对原料的检查。
4、颗粒机环模在安装过程中有偏心状态或不均匀受力(与压辊总成等在同心位置)造成颗粒机环模不断承受单向冲击。
环模颗粒机压辊与环模模具的间隙调整不当,间隙过大则颗粒成型度差,硬度不够,间隙过小的话,如果颗粒机作业时间较长,模具便会因长时间压力过大而导致损坏。
因此用户应该严格按照厂家的说明来调整压模间隙。
颗粒机环模开裂怎样修复(1)当抱箍工作面有道像光亮点以及传动轮工作面有磨损痕迹,这时抱箍内卡可能已磨损或变形而造成环模开裂。
解决办法:必须及时更换抱箍。
(2)由于传动轮配合面磨损,模、辊配合面明显松动而造成环模开裂。
解决办法:必须及时更换传动轮或修复,或增大环模装配面配合尺寸公差。
(3)由于压模衬圈磨损或变形而造成环模开裂。
解决办法:必须及时检查和更换压模衬圈。
(4)由于传动键磨损而导致环模撞击开装。
解决办法:与传动轮松也有关系,定期测量键与键槽的间隙,及时更换传动键。
环模开孔率计算公式

制粒机环模开孔率的计算及其影响因素制粒机是一种将粉状物料压缩成颗粒状的设备,广泛应用于农业、化工、食品、医药等领域。
制粒机的核心部件是环模,它是一种多孔的圆环形金属件,其上布满了许多模孔,用于将物料挤压成颗粒。
环模的开孔率是指环模上模孔的总面积与环模的有效工作面积之比,它是反映环模性能的一个重要参数,直接影响制粒机的生产效率、能耗、产品质量等。
本文将介绍制粒机环模开孔率的计算方法及其影响因素,以期为制粒机的设计和使用提供参考和指导。
一、制粒机环模开孔率的计算方法制粒机环模开孔率的计算方法较为简单,只需要知道环模的几何参数,如内径、外径、宽度、模孔直径、模孔数量等,就可以利用以下公式求得:开孔率 = (模孔数量× π× (模孔直径/2)^2) / (π×(环模外径^2 - 环模内径^2) × 环模宽度/环模外径)其中,环模外径和环模内径是指环模的最大和最小直径,环模宽度是指环模的有效工作宽度,模孔直径是指模孔的最小直径,模孔数量是指环模上的模孔总数。
这些参数可以通过测量或查阅环模的技术资料得到。
例如,某制粒机的环模参数如下:环模内径为300 mm,环模外径为400 mm,环模宽度为80 mm,模孔直径为6 mm,模孔数量为360个。
则该环模的开孔率为:开孔率= (360 × π× (6/2)^2) / (π× (400^2 - 300^2) × 80/400) = 0.21也就是说,该环模的开孔率为21%。
二、制粒机环模开孔率的影响因素制粒机环模开孔率的大小,不仅取决于环模的几何参数,还受到以下几个方面的影响:物料性质:不同的物料有不同的物理和化学特性,如密度、粘度、弹性、热稳定性等,这些特性会影响物料在模孔中的流动和成形情况。
一般来说,物料密度越大,粘度越高,弹性越小,热稳定性越好,对环模的开孔率要求越低,反之则越高。
颗粒机环模模孔结构

颗粒机环模模孔结构颗粒机环模的结构特性参数,通常由模孔直径、环模厚度、有效工作长度、减压孔深度、进料孔口直径、进料孔口角度、环模开孔率和长径比来表示。
其参数对颗粒成型品质有着一定的影响。
颗粒机环模模孔结构在环模上开有相互间隔的多排成型通孔,通孔主要由进料孔(导料孔)、成型直孔、出料孔三部分构成。
模孔形式是依据不同的原料特点进行设计选择。
1、进料孔进料孔口直径应大于模孔直径,这样可减少物料的入孔阻力,以利于它们进入模孔。
进料孔有3种基本形式,即直孔、锥孔和曲线形孔。
目前最常见的进料孔是锥孔形式,呈漏斗形结构,也叫喇叭口,使物料更容易进入成型直孔,防止物料堆积在环模内壁造成闷车现象。
2、成型直孔成型直孔的有效长度与其孔径的比值称为长径比(压缩比),这个压缩比是与压制成型的颗粒密度、强度密切相关的参数,是反映颗粒挤压强度的一个指标。
压缩比越大,挤出的颗粒越结实。
对于直形孔的环模压缩比来说,环模孔的有效长度即为环模的总厚度,最小直径即为模孔本身的直径。
3、出料孔出料孔的形式有可设计成减压孔(释放孔)、外锥形孔或内锥形孔。
减压孔朝外呈喇叭状,目的是使已经挤压成型的颗粒更容易脱模出料。
成型直孔是制粒的重要结构,当直孔孔径不变而延长其长度时,压缩比变大,原料被挤压进直孔后保压时间也将变长,压制出的颗粒密度大,外观光滑且不易破裂变形,但由于颗粒保压时间长,会引起颗粒机生产效率下降,增加生产成本。
因此成型通孔的直径和长度应根据物料状况与成型颗粒大小粒度的要求而定。
另外,环模模孔粗糙度也是衡量环模质量的重要指标。
在同样的压缩比下,粗糙度值越大,颗粒挤出阻力就越大,出料越困难,过大的粗糙度也影响着颗粒表面的质量。
一般合适的粗糙度值应在0.8-1.6之间。
木屑颗粒机环模的设计参数
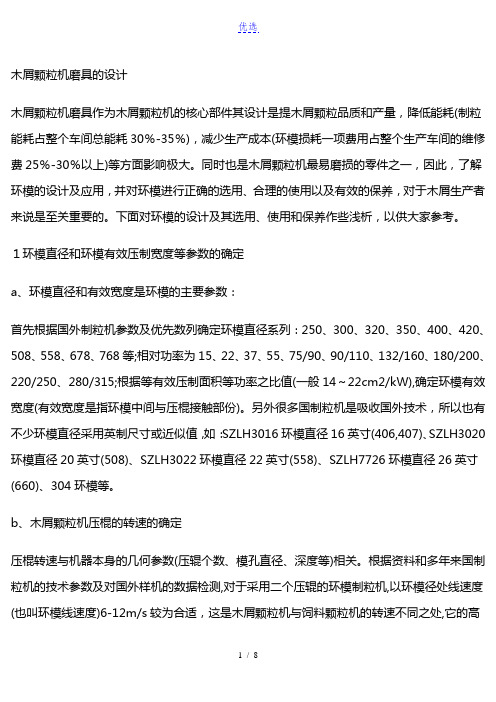
木屑颗粒机磨具的设计木屑颗粒机磨具作为木屑颗粒机的核心部件其设计是提木屑颗粒品质和产量,降低能耗(制粒能耗占整个车间总能耗30%-35%),减少生产成本(环模损耗一项费用占整个生产车间的维修费25%-30%以上)等方面影响极大。
同时也是木屑颗粒机最易磨损的零件之一,因此,了解环模的设计及应用,并对环模进行正确的选用、合理的使用以及有效的保养,对于木屑生产者来说是至关重要的。
下面对环模的设计及其选用、使用和保养作些浅析,以供大家参考。
1环模直径和环模有效压制宽度等参数的确定a、环模直径和有效宽度是环模的主要参数:首先根据国外制粒机参数及优先数列确定环模直径系列:250、300、320、350、400、420、508、558、678、768等;相对功率为15、22、37、55、75/90、90/110、132/160、180/200、220/250、280/315;根据等有效压制面积等功率之比值(一般14~22cm2/kW),确定环模有效宽度(有效宽度是指环模中间与压棍接触部份)。
另外很多国制粒机是吸收国外技术,所以也有不少环模直径采用英制尺寸或近似值,如:SZLH3016环模直径16英寸(406,407)、SZLH3020环模直径20英寸(508)、SZLH3022环模直径22英寸(558)、SZLH7726环模直径26英寸(660)、304环模等。
b、木屑颗粒机压棍的转速的确定压棍转速与机器本身的几何参数(压辊个数、模孔直径、深度等)相关。
根据资料和多年来国制粒机的技术参数及对国外样机的数据检测,对于采用二个压辊的环模制粒机,以环模径处线速度(也叫环模线速度)6-12m/s较为合适,这是木屑颗粒机与饲料颗粒机的转速不同之处,它的高低影响到挤压区的料层厚度及物料通过模孔的时间,进而影响制粒机产量和颗粒质量。
线速度过高时,相同产量条件下环模每转产出颗粒少,挤压区料层薄,轴向料层分布不均匀,有可能使挤压区的物料形成断层,制粒不连续,制出的颗粒松软,轴向压出颗粒长度不匀,粉料多,而且对于水分含量较高的物料还易打滑,甚至根本不能制粒;较低的环模线速度虽然制出的颗粒质量好,但对产量影响较大。
环模怎么看型号

环模怎么看型号作为一家20年专注压辊环模定制的生产厂家,宝壳常常遇到有用户咨询:饲料颗粒机怎样选、环模颗粒机好不好、如何选环模、环模怎么看型号、环模用什么材料好等种种问题,今天宝壳就以上这些问题作一些浅析,希望能帮助到大家。
饲料颗粒机饲料颗粒机,分为环模饲料颗粒机、平模饲料颗粒机、对辊饲料颗粒机;按用途可分为:小型家用颗粒饲料机,家禽饲料颗粒机,小型家禽颗粒饲料机,鱼饲料颗粒机,兔子饲料颗粒机,猪饲料颗粒机,秸秆饲料颗粒机;按生产又可分为:秸秆饲料颗粒机,麦麸饲料颗粒机,豆粕饲料颗粒机,玉米秸秆饲料颗粒机,木屑饲料颗粒机等。
各种不同的饲料颗粒机,以外观和生产方式的不同于以分类。
饲料颗粒机广泛适用于大、中、小型水产养殖,粮食饲料加工厂,畜牧场,家禽养殖场,个体养殖户及中小型养殖场,养殖户或大、中、小型饲料加工厂使用,大家在选购饲料颗粒机时要按自己的生产需要购买。
环模颗粒机环模颗粒机是颗粒饲料生产中的关键设备,它将配合好的各种粉状饲料压制成颗粒,改变了饲料的物理性能和生化性能,提高了饲料利用率和喂养适口性,是现代化饲料厂必不可少的重要设备。
环模作为制粒机的核心部件之一,是颗粒机的最主要易损件,它在饲料生产中起着至关重要的作用,它的好坏会直接影响生产产量以及颗粒饲料的品质。
要如何选购优质的环模,为自己带来更高的生产效率与经济效益?宝壳带大家一起看看以下资料:环模的基本要素1、压缩比环模的压缩比是指有效孔径工作长度和模孔直径之比。
环模的压缩比会影响颗粒成品的软硬程度、粉料比率以及产量。
低压缩比能增加产量,降低能耗,减轻环模和压辊的磨损,但颗粒松散,长短不一,饲料粉化率高;高压缩比会使颗粒结实,外表光滑且有光泽,粉化率低,但生产成本高。
2、排孔方式通常分两种排孔方式:纵排孔和横排孔。
纵排孔强度较高,一般用于畜禽料、猪料、鸭料、反刍料、生物质环模;横排孔多用于鱼、虾、蟹等水产料,对薄型切料刀的磨损均匀,能延长切料刀的使用寿命。
颗粒机常见的问题及名词解释
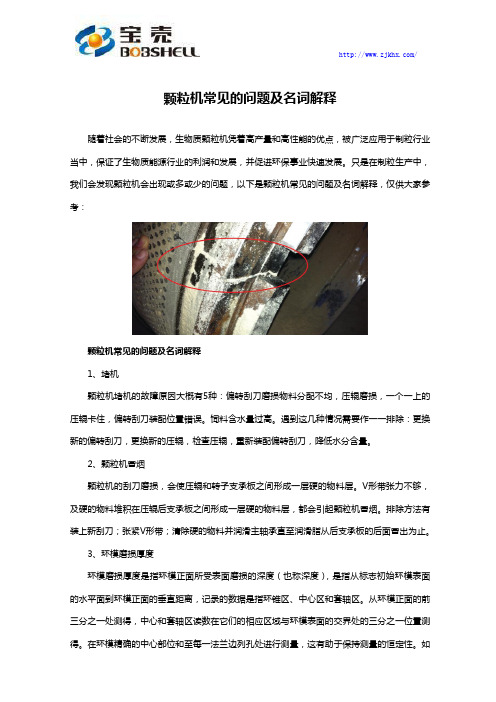
颗粒机常见的问题及名词解释随着社会的不断发展,生物质颗粒机凭着高产量和高性能的优点,被广泛应用于制粒行业当中,保证了生物质能源行业的利润和发展,并促进环保事业快速发展。
只是在制粒生产中,我们会发现颗粒机会出现或多或少的问题,以下是颗粒机常见的问题及名词解释,仅供大家参考:颗粒机常见的问题及名词解释1、堵机颗粒机堵机的故障原因大概有5种:偏转刮刀磨损物料分配不均,压辊磨损,一个一上的压辊卡住,偏转刮刀装配位置错误。
饲料含水量过高。
遇到这几种情况需要作一一排除:更换新的偏转刮刀,更换新的压辊,检查压辊,重新装配偏转刮刀,降低水分含量。
2、颗粒机冒烟颗粒机的刮刀磨损,会使压辊和转子支承板之间形成一层硬的物料层。
V形带张力不够,及硬的物料堆积在压辊后支承板之间形成一层硬的物料层,都会引起颗粒机冒烟。
排除方法有装上新刮刀;张紧V形带;清除硬的物料并润滑主轴承直至润滑脂从后支承板的后面冒出为止。
3、环模磨损厚度环模磨损厚度是指环模正面所受表面磨损的深度(也称深度),是指从标志初始环模表面的水平面到环模正面的垂直距离,记录的数据是指环锥区、中心区和套轴区。
从环模正面的前三分之一处测得,中心和套轴区读数在它们的相应区域与环模表面的交界处的三分之一位置测得。
在环模精确的中心部位和至每一法兰边列孔处进行测量,这有助于保持测量的恒定性。
如果一个区域有特别深的磨损带,则测量时应放在最深点。
用一个测微计或小直径圆棒,从模孔出口端插入测微计的深度标尺或小圆棒,直至它从模孔入口端出现,在模孔出口端给圆棒作记号或检查测微计表盘读数。
你已经测出了留存的环模坯厚度,这个测量值可以从初始坯厚减掉,以得到磨损浓度,这种测量应以千分之英寸给出。
磨损深度测量值给出了有关饲料分布的重要信息,可以评价环模哪一部分磨损最深,这种测量还指明了磨损刮板和匀料器以及不均匀磨损的压辊壳的情况。
4、压延压延是环模工作面孔进口处平延封闭的一种状况。
这种延展作用极大地影响颗粒质量和环模产量,常使两者都降低。
木屑颗粒机环模压缩比
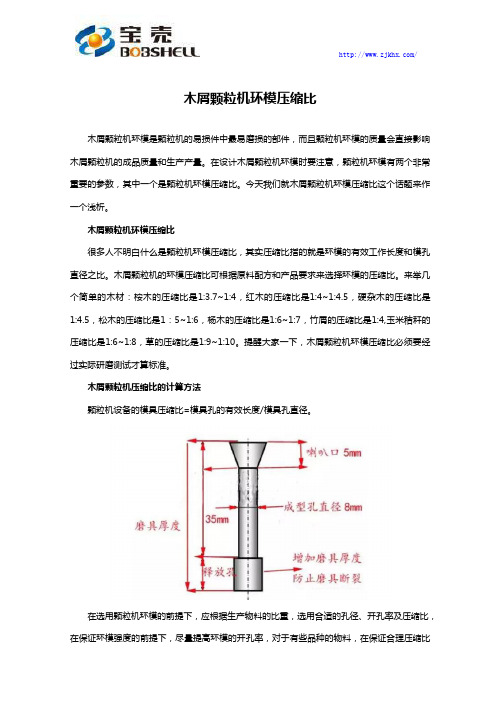
木屑颗粒机环模压缩比木屑颗粒机环模是颗粒机的易损件中最易磨损的部件,而且颗粒机环模的质量会直接影响木屑颗粒机的成品质量和生产产量。
在设计木屑颗粒机环模时要注意,颗粒机环模有两个非常重要的参数,其中一个是颗粒机环模压缩比。
今天我们就木屑颗粒机环模压缩比这个话题来作一个浅析。
木屑颗粒机环模压缩比很多人不明白什么是颗粒机环模压缩比,其实压缩比指的就是环模的有效工作长度和模孔直径之比。
木屑颗粒机的环模压缩比可根据原料配方和产品要求来选择环模的压缩比。
来举几个简单的木材:桉木的压缩比是1:3.7~1:4,红木的压缩比是1:4~1:4.5,硬杂木的压缩比是1:4.5,松木的压缩比是1:5~1:6,杨木的压缩比是1:6~1:7,竹屑的压缩比是1:4,玉米秸秆的压缩比是1:6~1:8,草的压缩比是1:9~1:10。
提醒大家一下,木屑颗粒机环模压缩比必须要经过实际研磨测试才算标准。
木屑颗粒机压缩比的计算方法颗粒机设备的模具压缩比=模具孔的有效长度/模具孔直径。
在选用颗粒机环模的前提下,应根据生产物料的比重,选用合适的孔径、开孔率及压缩比,在保证环模强度的前提下,尽量提高环模的开孔率,对于有些品种的物料,在保证合理压缩比的条件下,环模过于壁薄,以致环模强度不够,生产中会出现模具开裂现象,此时应当在保证模孔有效长度的前提下,增加环模的厚度和增开减压孔。
颗粒机设备的环模压缩比是指环模孔的有效长度和环模孔径的比值,它是反映生物质颗粒机挤压强度的一个指标。
压缩比越大,挤出的颗粒越结实。
对于直形孔的环模压缩比来说,环模孔的有效长度即为环模的总厚度,最小直径即为模孔本身的直径,对于释放式阶梯孔和外锥形孔来说,模孔的有效长度即为环模的总厚度减去释放孔的长度或外锥孔的长度,小直径段的孔径即为计算压缩比的孔径。
对于压缩式阶梯孔和内锥形孔来说,这种情况比较特殊,一般把整个环模厚度作为模孔的有效长度,最小直径取小直径段的孔径。
当然,这样计算出的环模压缩比的含义和前两种情况是有区别的。
颗粒机环模不耐磨的原因
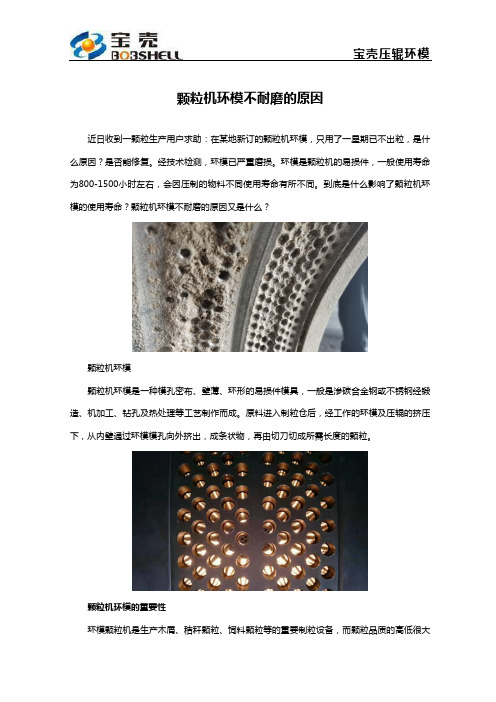
颗粒机环模不耐磨的原因近日收到一颗粒生产用户求助:在某地新订的颗粒机环模,只用了一星期已不出粒,是什么原因?是否能修复。
经技术检测,环模已严重磨损。
环模是颗粒机的易损件,一般使用寿命为800-1500小时左右,会因压制的物料不同使用寿命有所不同。
到底是什么影响了颗粒机环模的使用寿命?颗粒机环模不耐磨的原因又是什么?颗粒机环模颗粒机环模是一种模孔密布、壁薄、环形的易损件模具,一般是渗碳合金钢或不锈钢经锻造、机加工、钻孔及热处理等工艺制作而成。
原料进入制粒仓后,经工作的环模及压辊的挤压下,从内壁通过环模模孔向外挤出,成条状物,再由切刀切成所需长度的颗粒。
颗粒机环模的重要性环模颗粒机是生产木屑、秸秆颗粒、饲料颗粒等的重要制粒设备,而颗粒品质的高低很大程度上是由机颗粒机环模质量来决定的。
若选用的环模选用寿命短,耐磨性差,将直接影响着颗粒的生产成本和颗粒的品质。
优质的环模应是模孔分度均匀,模孔间壁厚均匀,模孔内壁光洁度高,初次安装可直接生产,表面硬度达HRC58-62,具有较强的耐磨性。
颗粒机环模不耐磨的原因1、使用劣质环模劣质环模选用劣质低价的钢坯作为原材料,这种钢坯分子结构不严密,韧性达不到要求,耐磨程度差,加工精度达不到要求,环模模孔加工孔内壁粗糙并存在罗纹,环模压缩比深浅不一。
如选用这样的环模,长此以往,颗粒机的正常工作必定会受到严重影响,根本达不到制粒机安全、高产、低耗的目的。
2、原料含杂质过多原料的除杂除铁十分重要,比如铁质杂质进入制粒室对环模、压辊,甚至设备造成强烈的破坏,砂石类等杂质会加快压模的磨损。
3、环模压缩比过大环模的设计很重要,特别是环模压缩比,如果环模的压缩比太大,会造成颗粒压出太难,产量低,还会加剧模具的磨损。
4、环模压辊间隙没及时调整环模和压辊之间的间隙需要正确调整。
如果间隙太小,压辊会加重摩擦环模,缩短环模的使用时间。
如果间隙太大,压力辊会打滑,排放不顺畅,从而降低输出。
环模与压辊间的正常间隙应为0.3-0.5mm。
颗粒机模具压缩比是怎么算出来的

颗粒机模具压缩比是怎么算出来的作为一名优秀的颗粒人,关于颗粒机的常识,比如模具开孔率、压缩比等,必定是了如指掌。
What?你说你不懂?呃,好吧!今天就和大家聊一聊颗粒机模具压缩比是怎么算出来的和如何选合适的模具压缩比。
颗粒机模具压缩比颗粒机模具压缩比是指模具模孔的有效长度和模具孔径的比值,是反映颗粒机挤压强度的一个指标。
颗粒机模具压缩比是怎么算出来的颗粒机模具压缩比=模具孔直径/模具模孔的有效工作长度对于直形孔的模具来说,模具模孔的有效长度即为模具的总厚度,最小直径即为模孔本身的直径。
假设:模孔直径是6mm,环模模具厚度45mm压缩比=6/45=1:7.5此环模压缩比为1:7.5对于释放式阶梯孔和外锥形孔来说,模孔的有效长度为模具的总厚度减去释放孔的长度或外锥形孔的长度,最小直径段的孔径为计算压缩比的孔径。
假设:环模模孔直径是8mm,模具厚度66mm,释放孔为18mm压缩比=8/(66-18)=1:6此环模压缩比为1:6宝壳压辊环模提醒大家,压缩比是一个比值,同一个压缩比,它的孔径与有效工作长度均有可能是不相同的。
如何选合适的模具压缩比颗粒成品的好坏取决于模具的压缩比。
有研究团队分别采用玉米秸秆、稻壳、锯末、芦苇、豆秆5种原料,在环模压缩比为1:3.5,1:4.0,1:4.5,1:5.0,1:5.5的工况下,测试不同原料的成型条件,推算出颗粒燃料成型的趋势,确定各类原料成型时产品的质量、密度与环模压缩比的关系,以下内容仅供大家参考。
环模压缩比的大小决定了成型压力的大小。
玉米秸秆、芦苇等原料的纤维素含量少,受到外力挤压时易发生形变,因此成型时所需的环模压缩比小,即成型压力较小;锯末的纤维素含量高,成型时所需的环模压缩比大,即成型压力较大。
因而,采用不同生物质原料生产成型颗粒燃料,应采用不同的环模压缩比,原料中纤维素含量接近的生物质物料可采用相同压缩比的环模。
同一种原料在不同压缩比环模中成型,颗粒燃料的密度随压缩比的增大而逐渐增大,并在一定压缩比范围内,密度保持相对稳定,当压缩比增大到一定程度时,原料会因为压力过大造成出料不畅而不能成型。
颗粒机环模孔的深度和环模孔径比

颗粒机环模孔的深度和环模孔径比
环模颗粒机是制作颗粒饲料主要机器之一,很大程度上决定了饲料加工产量,在饲料加工过程中占有非常重要的地位。
制粒系统主要工作部件为环模、压辊。
环模是具有这么多均布小孔的模具,制粒过程的强烈中,物料在环模与压辊挤压下强制通过环模小孔,所以环模应具有较好的强度和耐磨性。
环模的孔型有直形孔、阶梯形孔、外锥形孔和内锥形孔。
期中直形孔和阶梯形孔适合压制配合饲料;外锥形孔适用于加工脱脂糠一类的高纤维物料;内锥形孔适宜压制体积较大的牧草颗粒饲料。
环模孔的深度和环模孔径比
模孔的深度是对于一定厚度的环模减去释放孔的长度,其孔径的大小就形成了一定的孔径比,有效孔长度除以有效孔直径等于压缩比的倍数(径长比)。
见图模孔压缩比:
有效孔越短径长比就越小,物料在模孔中受到地挤压力就小,挤压时间也短。
易于物料挤
出,生产效率高,电耗低,但是生产出的颗粒质量松散,易当导致含粉偏高,颗粒长度不整齐等质量问题。
有效孔越长孔径比就越大,物料在模孔中的挤压力就越大,挤压时间也长,这时生产效率越低。
电耗随之增加,生产出的颗粒坚硬、强度好。
随着有效孔的加长,制粒产量明显下降,甚至导致堵模制不出粒。
为了获得最佳的制粒性能,使产量和质量都能达到最佳状态,选用好环模压缩比,是非常重要的。
每种配方的物料制粒时,都有比较适宜的孔径比值,要根据各种原料配方的性质和粉碎粒度、机械性能等综合因素,合理选用环模压缩比。
如果订购的环模孔径比,不能很好地适宜配方的制粒要求,适度地调整配方原料是很有必要的,因为最终的目的是要达到最佳的制粒效率。
颗粒机环模在什么情况下需要扩孔?
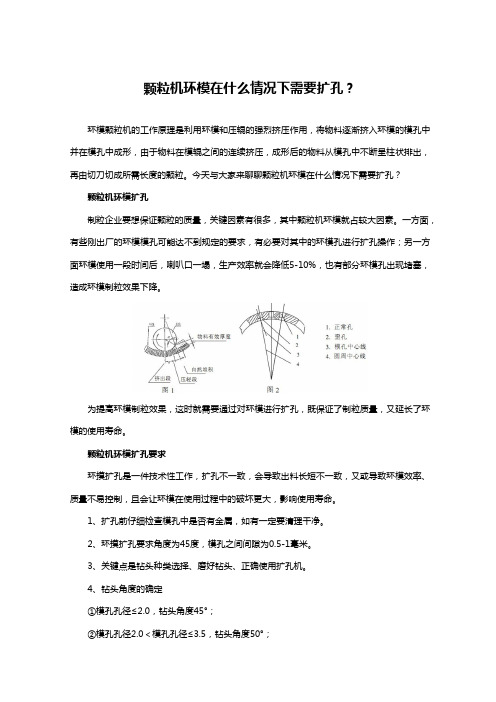
颗粒机环模在什么情况下需要扩孔?环模颗粒机的工作原理是利用环模和压辊的强烈挤压作用,将物料逐渐挤入环模的模孔中并在模孔中成形,由于物料在模辊之间的连续挤压,成形后的物料从模孔中不断呈柱状排出,再由切刀切成所需长度的颗粒。
今天与大家来聊聊颗粒机环模在什么情况下需要扩孔?颗粒机环模扩孔制粒企业要想保证颗粒的质量,关键因素有很多,其中颗粒机环模就占较大因素。
一方面,有些刚出厂的环模模孔可能达不到规定的要求,有必要对其中的环模孔进行扩孔操作;另一方面环模使用一段时间后,喇叭口一塌,生产效率就会降低5-10%,也有部分环模孔出现堵塞,造成环模制粒效果下降。
为提高环模制粒效果,这时就需要通过对环模进行扩孔,既保证了制粒质量,又延长了环模的使用寿命。
颗粒机环模扩孔要求环摸扩孔是一件技术性工作,扩孔不一致,会导致出料长短不一致,又或导致环模效率、质量不易控制,且会让环模在使用过程中的破坏更大,影响使用寿命。
1、扩孔前仔细检查模孔中是否有金属,如有一定要清理干净。
2、环摸扩孔要求角度为45度,模孔之间间隙为0.5-1毫米。
3、关键点是钻头种类选择、磨好钻头、正确使用扩孔机。
4、钻头角度的确定①模孔孔径≤2.0,钻头角度45°;②模孔孔径2.0<模孔孔径≤3.5,钻头角度50°;③3.5<模孔孔径≤5.0,钻头角度55°;④模孔孔径>5.0,钻头角度60°。
5、修磨钻头注意每个钻头切削刃角度保持一致不能随意改变,修磨后没有在中线上会影响修模质量。
6、由于模孔数量较多,应有顺序进行。
扩孔后仔细检查有无遗漏未扩的模孔,并将环模内表面打磨一谝,去除毛刺。
7、环模上机后要求用油料反复压5-8分钟后,才能投料正式制粒。
以上是颗粒机环模在什么情况下需要扩孔及扩孔技术要求等内容,仅供广大制粒用户参考。
制粒机环模开孔率的计算方法(图文结合)

制粒机环模开孔率的计算方法(图文结合)
鉴于行业朋友经常会问到,制粒机环模开孔率的计算方法,今天就给大家详细解答下。
环模开孔率直接影响制粒机产能,开孔率越高,则出料越多,有利于提高生产率,但模孔间壁厚度变小,模具强度减小,容易开裂,同时摩擦减少,温度相对降低。
环模开孔率与产量的关系
制粒机环模开孔率的计算方法:
开孔率=孔面积总和(M)/工作总面积(N)
M=孔个数×π(2/d)²
N=K×πR
d=有效孔径(如图)
K=工作面宽度(不含两边沟槽和沟槽以外的非工作区宽度,如图)
R=环模内径(如图)
制粒机环模开孔率的计算方法就这么简单,大家可结合压缩比等参数,对照实际需求寻找专业厂家定制合适的环模,以达到最优产能。
生物质环模直径取值
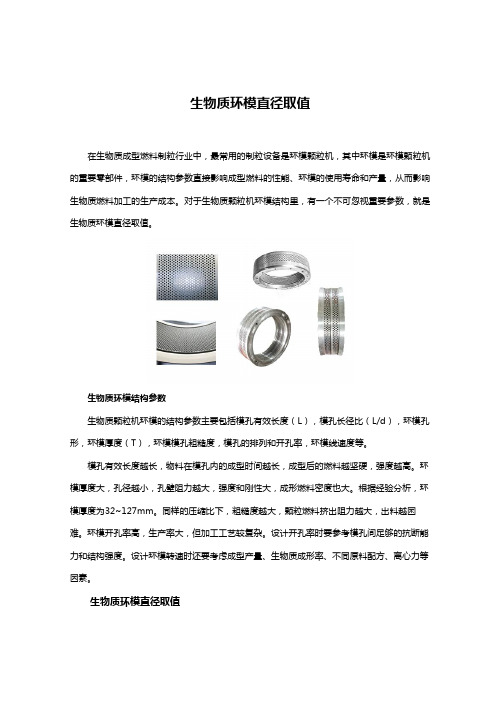
生物质环模直径取值
在生物质成型燃料制粒行业中,最常用的制粒设备是环模颗粒机,其中环模是环模颗粒机的重要零部件,环模的结构参数直接影响成型燃料的性能、环模的使用寿命和产量,从而影响生物质燃料加工的生产成本。
对于生物质颗粒机环模结构里,有一个不可忽视重要参数,就是生物质环模直径取值。
生物质环模结构参数
生物质颗粒机环模的结构参数主要包括模孔有效长度(L),模孔长径比(L/d),环模孔形,环模厚度(T),环模模孔粗糙度,模孔的排列和开孔率,环模线速度等。
模孔有效长度越长,物料在模孔内的成型时间越长,成型后的燃料越坚硬,强度越高。
环模厚度大,孔径越小,孔壁阻力越大,强度和刚性大,成形燃料密度也大。
根据经验分析,环模厚度为32~127mm。
同样的压缩比下,粗糙度越大,颗粒燃料挤出阻力越大,出料越困难。
环模开孔率高,生产率大,但加工工艺较复杂。
设计开孔率时要参考模孔间足够的抗断能力和结构强度。
设计环模转速时还要考虑成型产量、生物质成形率、不同原料配方、离心力等因素。
生物质环模直径取值
生物质环模直径取值与模孔长径比(L/d)有关。
模孔长径比即模孔有效长度L与模孔直径d之比。
长径比越大,燃料产品密度越大,燃料越结实,表面硬度也越高,相应的能耗大,产量小,反之亦然。
选择多大的长径比与环模材料、模孔、直径、生产品种等很多因素有关。
其取值范围一般在5~13之间。
由于生物质颗粒机环模的成本昂贵,用户在制定环模时应根据自身的制粒原料及质量要求,选择环模材料,合理设计环模环模结构参数,以保证环模的强度和提高生产效率、颗粒成型产量、成型品质和颗粒机的稳定性。
颗粒机生产一段时间后产量下降的原因

颗粒机生产一段时间后产量下降的原因不少做颗粒的朋友遇到这样的问题:颗粒机生产了一段时间后,发现产量下降了,到底是什么原因?不要着急,建议您从以下几个要点一一排查:颗粒机生产一段时间后产量下降的原因1、由环模引起的●环模表面喇叭口表面压延,重新倒角即可。
●环模压缩比选用不当,更换适合的压缩比环模。
●模孔被堵塞了,由环模外向里敲打堵塞的模孔,清除孔内杂质即可。
●环模的开孔率过低,模孔数过低,导致产量低,更换开孔率合理的环模。
●环模磨损严重,所生产的颗粒成形率也随之下降,产量降低,需及时更换新环模。
2、由压辊引起的●压辊严重磨损,更换压辊壳即可。
●新环模和旧压辊、新压辊和旧环模配合配合不当造成产量低。
要坚持新配新的原则,保证压辊和环模整体接触间隙一致。
●模辊间隙过小,会增加压辊磨损的机会,进而缩短环模的使用寿命;而间隙过大会使压辊打滑,降低颗粒的输出能力,应及时调整模辊间隙。
3、由调质器引起的●调质器桨叶磨损后会大大影响调质,使物料混合、蒸汽吸收较差,所以降低了调质效果,降低了颗粒机产量。
●调质温度过低,请调整为适合的调质温度。
●检查一下蒸汽管道,看疏水阀是否正常排水。
只有疏水阀工作正常,才能保证蒸汽不含冷凝水的饱和蒸汽。
4、由电机引起的●检查电机皮带松紧,如皮带过松需要张紧。
5、由原料引起的●原料的含水率在13%-18%,水分过高过低都会使产量下降。
另外喂料不匀也会影响产量。
6、由刮刀引起的●检查原料在环模内的分布情况,不能让原料跑单边,如发生类似情况,必须调整大小喂料刮刀的位置,让原料在环模内分布均匀,这样既可延长环模使用寿命,同时出料也更顺畅。
颗粒机使用不当会使产量低于预期产量,装配调试不当、维护和保养不良等原因,也会影响其性能,导致产量降低。
制粒环模关键参数设计
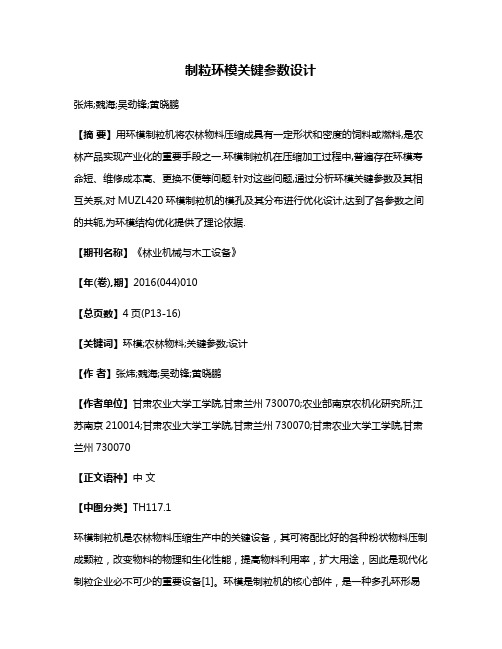
制粒环模关键参数设计张炜;魏海;吴劲锋;黄晓鹏【摘要】用环模制粒机将农林物料压缩成具有一定形状和密度的饲料或燃料,是农林产品实现产业化的重要手段之一.环模制粒机在压缩加工过程中,普遍存在环模寿命短、维修成本高、更换不便等问题.针对这些问题,通过分析环模关键参数及其相互关系,对MUZL420环模制粒机的模孔及其分布进行优化设计,达到了各参数之间的共轭,为环模结构优化提供了理论依据.【期刊名称】《林业机械与木工设备》【年(卷),期】2016(044)010【总页数】4页(P13-16)【关键词】环模;农林物料;关键参数;设计【作者】张炜;魏海;吴劲锋;黄晓鹏【作者单位】甘肃农业大学工学院,甘肃兰州730070;农业部南京农机化研究所,江苏南京210014;甘肃农业大学工学院,甘肃兰州730070;甘肃农业大学工学院,甘肃兰州730070【正文语种】中文【中图分类】TH117.1环模制粒机是农林物料压缩生产中的关键设备,其可将配比好的各种粉状物料压制成颗粒,改变物料的物理和生化性能,提高物料利用率,扩大用途,因此是现代化制粒企业必不可少的重要设备[1]。
环模是制粒机的核心部件,是一种多孔环形易损件,模孔密布、壁薄,工作时承受交变载荷,压力大、磨损严重,环模的关键参数直接影响制粒的质量及产量。
环模三维实体模型如图1所示。
1.1 环模动力参数环模制粒机的主电机功率为:1.2 环模运动参数环模线速度是指环模内圆的切线速度。
设计环模转速时还需要考虑制粒量、成形率、环模内径、模孔直径、离心力等因素[2-3]。
模孔直径小的环模,应采用较高的线速度,而模孔直径大的环模线速度应低些[4]。
在一定条件下,环模的线速度提高,产量增大,能耗增加,但制粒的硬度和粉化率指数上升,环模的线速度范围通常为2.5~7.5 m/s。
环模转速:1.3 压缩比压缩比是指模孔的有效长度与模孔最小直径的比值,其是反映颗粒饲料挤压强度的一个指标。
- 1、下载文档前请自行甄别文档内容的完整性,平台不提供额外的编辑、内容补充、找答案等附加服务。
- 2、"仅部分预览"的文档,不可在线预览部分如存在完整性等问题,可反馈申请退款(可完整预览的文档不适用该条件!)。
- 3、如文档侵犯您的权益,请联系客服反馈,我们会尽快为您处理(人工客服工作时间:9:00-18:30)。
颗粒机环模模孔开孔率
颗粒机环模的使用寿命长短,与其主要参数有着一定的联系(环模直径、有效宽度、环模长径比、开孔率),而环模开孔率更直接影响颗粒机产能。
开孔率越高,出料越多,有利于提高生产率,但若过度提高环模开孔率,则会导致模孔间壁厚度变小,模具强度减小,造成环模开裂。
颗粒机环模模孔越多越好这一说法是不成立的,颗粒机环模模孔开孔率应如何计算呢?
颗粒机环模开孔率
环模的开孔率是指环模在内表面的有效孔径面积之和与环模工作面内圆面积的比值。
环模开孔率=[(R/2)2×π×n]/环模工作区总面积
(R:环模孔径,n:环模总孔数)
在条件相同的情况下,环模孔数越多,环模开孔率越高。
环模开孔率对制粒过程的影响
1、物料被压辊挤压进入环模喇叭口及模孔内的过程有一定的挤入时间,在开孔率较低的情况下,即增加模孔数,可以增加挤入量,提升颗粒机产能。
但如果环模开孔率过高,孔与孔之间的间距变小,在喇叭口角度基本确定的情况下,喇叭口的深度必然会变小。
当“因喇叭口深度变小而减少的喇叭口总容积>因增加孔数而增加的喇叭口总容积”时,增加开孔率(即增加孔数),不但起不到增加挤入量、提升颗粒机产能的作用,反而会减少挤入量、降低颗粒机产能。
2、物料通过环模模孔的时间=压缩比倍数×物料压入喇叭口的挤入时间时,物料才能非常流畅地通过环模模孔。
如果:物料通过环模模孔的通过时间<压缩比倍数×物料压入喇叭口的挤入时间,则表明:物料进入喇叭口时间过长,造成环模模孔内供料不足,不能充分发挥颗粒机产能。
如果:物料通过环模模孔的通过时间>压缩比倍数×物料压入喇叭口的挤入时间,则表明:物料进入喇叭口时间过短,挤入模孔的物料来不及通过模孔,从而出现“打滑”等现象,也会降低颗粒机产能。
3、因考虑到颗粒含粉率、耐水性等,用户选用的环模压缩比往往是事前确定的。
当环模开孔率偏低,压辊受压区域内所分布的环模孔数较少,也就是说在挤入过程时间不变的情况下,单个模孔的挤入时间相对较长;同时开孔率低,单个喇叭口深度往往较大、容积大,从而也造成单个模孔的挤入时间相对较长。
这时物料通过环模模孔的通过时间<压缩比倍数×物料压入喇叭口的挤入时间,这样的环模设计制约了颗粒机产能。
4、环模开孔率越高,孔与孔的间距变小,压辊受压区域内所分布的环模孔数越多,也就是说在挤入过程时间不变的情况下,单个模孔的挤入时间肯定缩短。
如果环模开孔率高到影响喇叭口深度,导致单个喇叭口容积变小,又会造成单个模孔的挤入时间再缩短。
这时物料通过
环模模孔的通过时间>压缩比倍数×物料压入喇叭口的挤入时间,这样的环模在使用时,容易出现打滑、烧模等现象,不但起不到提升颗粒机产能的作用,反而会降低颗粒机产能。
如何正确选定环模开孔率
环模表面开孔率直接影响颗粒机的产量和环模强度。
由于选材及环模尺寸的差异,要得到恰当的环模模孔开孔率数值,以更好地协调它的产量及使用寿命。
对于模孔直径为2-12mm的环模,其模孔开孔率一般应选定在20%~30%之间。
模孔越小,开孔率取值越小,反之,开孔率取值越大。
环模的开孔率对应于不同的环模孔径时是不同的,根据以往经验,以压制颗粒饲料为例,如环模孔径为1.8mm,开孔率约为25%,环模孔径为5mm的环模,开孔率约为38%。
在实际生产中,尤其在生产小直径的颗粒料时,如生产1.8mm的虾料,有的用户会抱怨制出的颗粒太长,就是因为小孔径时对应的环模开孔率较低造成的。
总结多年经验,在这里提醒大家不能无限的增大环模开孔率,正确的环模开孔率应根据所选环模材料、环模外形结构与尺寸,在实际生产中采取“逐次逼近”的试验方法来选择合适的开孔率,这样才能保证环模有足够的强度,以防止其承载时破裂而缩短使用寿命。