2、机械加工表面质量及影响因素
浅谈机械加工表面质量及影响因素
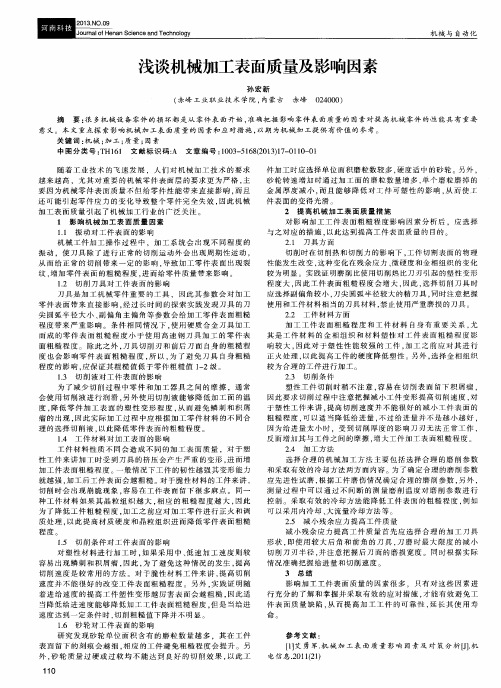
因此 要 求 切 削 过 程 中注 意 把 握 减 小 工 件 变 形 提 高 切 削 速 度 , 对
于塑性工件来讲 . 提 高切 削 速 度并 不能 很 好 的减 小 工 件 表 面 的 粗糙程度 , 可 以 适 当 降低 给进 量 , 不过给进量并不是越小越好 , 因为 给 进 量 太 小 时 .受 到 切 削 厚 度 的 影 响 刀 刃 无 法 正 常 工 作 , 反 而 增 加 其 与 工件 之 间 的摩 擦 , 增 大 工 件 加 T 表面 粗 糙 程 度 。 2 _ 4 加 工 方 法 选 择 合 理 的机 械 加 工 方 法 主要 包 括选 择 合 理 的 磨 削 参 数 和 采 取 有 效 的 冷 却方 法 两 方 面 内 容 。为 了确 定 合 理 的 磨 削参 数 应先进性试磨 , 根 据 工件 磨 伤情 况 确定 合 理 的磨 削参 数 , 另外 ,
意 义 。本 文 重 点 探 索 影 响 机械 加 工表 面质 量 的 因素 和 应 对措 施 , 以 期 为机 械 加 工提 供 有 价 值 的参 考 。
关键词 : 机械 ; 加工 ; 质量 ; 因 素
中 图分 类 号 : T HI 6 1 文献标识码: A 文章 编号 : 1 0 0 3 — 5 1 6 8 ( 2 0 1 3 ) 1 7 — 0 1 1 O — O 1
2 . 2 工 件 材料 方 面 加 工 工 件 表 面 粗 糙 程 度 和 工 件 材 料 自身 有 重 要 关 系 , 尤
影响机械加工表面质量的若干因素和改进方法
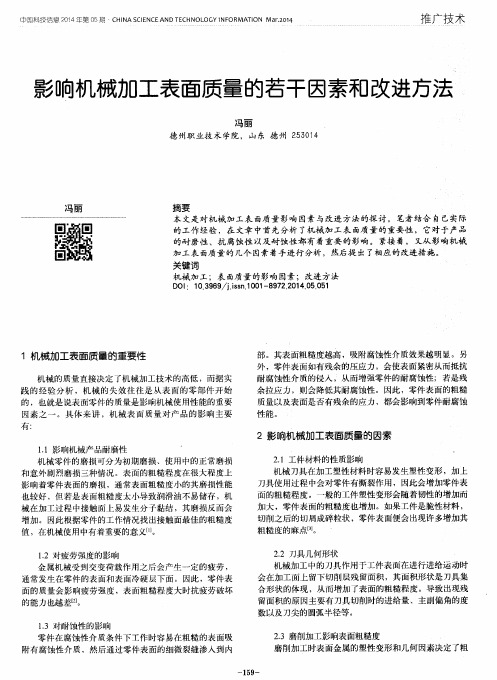
践 的经验 分析 ,机械的失效往 往是从 表面的零部件开始 的 ,也就是说表面零件的质量是影响机械使用性能的重要 因素 之一 。具体来讲 ,机械表 面质量对产品的影响主要
有:
2 影响机械加工 表面质量 的因素
1 . 1影 响机 械产 品耐磨 性 ‘ 机 械零 件 的 磨 损可 分 为初 期 磨损 、使用 中的正 常 磨 损 和 意 外 剧 烈磨 损 三种 情况 。表面 的粗 糙 程 度在 很 大程 度 上 影 响着 零件 表 面 的磨 损 ,通 常表 面粗 糙 度 小 的其 磨损 性 能 也 较 好 ,但 若 是表 面 粗糙 度 太小 导 致润 滑 油不 易 储存 ,机 械在加工过程 中接触面上 易发生分子黏结 ,其磨损反而会 2 . 1工件 材料 的性 质影 响 机 械 刀具 在加 工 塑性 材 料 时容 易 发生 塑性 变 形 ,加 上 刀具使用过程中会对零件有撕裂作用 ,因此会增加零件表 面 的粗 糙程 度 。一 般 的工 件 塑性 变形 会随 着 韧性 的 增加 而 加大 ,零件表面的粗糙度也增加。如果工件是脆性材料 ,
冯丽
德 州职业技术 学院,山东 德 州 2 5 3 0 1 4
冯丽
摘要 本 文是对 机械加 工表 面质量影 响 因素 与改进方 法的探 讨 。笔者 结合 自己实际 的工作 经验 ,在 文章 中首 先分析 了机械 加工表 面质 量的重要性 ,它对于产 品 的耐 磨性 、抗腐 蚀性 以及耐 蚀性都有 着重要 的影 响。 紧接 着,又从 影响机械 加工表 面质量 的几个 因素 着手进行 分析 ,然后提 出 了相应 的改进措施 。
的 塑性 和材 料 的金 相组 织 。对 塑性 大 的 低碳 钢 、低 合金 钢 材 料 而言 ,加 工 前先 用正 火 处理 来 降低 塑性 性 ,切 削加 上 后 便 可以获 得 较 小的粗 糙 度 。 同时 ,工 件材 料应 有 合适 的 金 相组 织 ,包括 均匀 的晶粒 度大 小 、分布及 状态 等 。 3 - 3 刀具 方 面
2、机械加工表面质量及影响因素

机械加工外表质量及影响因素一、外表质量定义任何机械加工所得的外表,实际上不行能是抱负的光滑外表,总是存在确定的微观几何外形误差。
另外,外表材料在加工时受切削力、切削热的影响,也会使原有的物理—机械性能发生变化。
因此,加工外表质量应包括:1、加工外表粗糙度。
是指加工外表的较小间距和微小峰谷的微观几何外形误差。
它主要是由于切削加工过程中的刀痕、切削分别时的塑性变形、刀具与被加工外表的摩擦、工艺系统的高频振动等缘由造成的。
2、外表层的物理———机械性能变化。
外表层的材料在加工时,物理—机械性能变化主要有以下三个方面的内容:1)外表层的冷作硬化。
工件在机械加工过程中,外表层金属产生猛烈的塑性变化,使表层的强度和硬度都有所提高,这种现象称外表冷作硬化。
2)外表层剩余应力。
在切削加工过程中,由于切削变形和切削热的影响,在加工外表会产生剩余应力,假设剩余应力超过材料的屈服强度,就会产生外表裂纹,外表的微观裂将给零件带来严峻的隐患。
3)外表层金相组织的变化。
工件外表经磨削精加工时,磨削产生的高温,一般可达800~1000 ℃,高的磨削温度会烧坏工作外表,使淬火钢件外表退火,引起表层金属发生相变,将大大降低外表层的物理—机械性能。
二、影响外表粗糙度的因素1、切削加工影响外表粗糙度的因素刀具几何外形及切削运动的影响刀具相对于工件作进给运动时,在加工外表留下了切削层残留面积,从而产生了外表粗糙度,残留面积的外形是刀具几何外形的复映,其高度H 受刀具的几何角度和切削用量大小的影响。
减小进给量vf、主偏角、副偏角以及增大刀尖圆弧半径,均可减小残留面积的高度。
此外,适当增大刀具的前角,以减小切削时的塑性变形的程度,合理选择润滑液和提高刀具刃磨质量,以减小切削时的塑性变形和抑制刀瘤、鳞刺的生成,也是减小外表粗糙度值的有效措施。
2、工件材料的性质加工塑性材料时,由于刀具对金属的挤压,产生了塑性变形,加之刀具迫使切屑与工件分别的撕裂作用,使外表粗糙度值加大。
影响机械加工表面质量的因素及改进措施

影响机械加工表面质量的因素及改进措施首先,加工工艺参数对机械加工表面质量有着重要影响。
加工工艺参数包括切削速度、进给量和切削深度。
切削速度过高会导致刀具与被加工材料摩擦热量过高,使刀具和被加工材料磨损严重,表面产生裂纹、烧伤等缺陷。
进给量过小会使机械切削过程中削屑排除不畅,产生热量过高,表面质量下降。
切削深度过大会使切削力过大,导致表面粗糙度增加。
因此,合理选择切削速度、进给量和切削深度,是保证机械加工表面质量的重要措施之一其次,机床的性能对机械加工表面质量也有很大影响。
机床的刚性、稳定性和振动特性等性能密切关系着机械加工表面质量。
刚性不足会导致机床在切削过程中产生振动,进而使工件表面出现脱落、粗糙度增加等现象。
稳定性差的机床会使切削过程中的切削力和切削振荡产生不规律波动,直接影响加工表面质量。
因此,加强机床的刚性和稳定性,减小机床的振动,是改善机械加工表面质量的关键。
刀具的质量和尺寸对机械加工表面质量也有很大影响。
刀具的尺寸偏差会导致切削力不均匀,进而使机械加工表面质量下降。
刀具的刀片强度、硬度和刀具的几何形状等也会直接影响切削过程中的刀具磨损和寿命,进而影响机械加工表面质量。
因此,选择质量好、尺寸准确的刀具,并及时更换磨损的刀具,均能改善机械加工表面质量。
被加工材料的性质对机械加工表面质量也有很大影响。
不同材料具有不同的硬度、韧性、热导率等性质,这些性质会直接影响材料的切削性能。
例如,硬度大的材料难切割,易损伤刀具,容易产生表面裂纹;热导率低的材料容易产生热损伤,使刀具和被加工材料磨损加剧。
因此,针对不同的材料特性,在加工过程中选择合适的切削工艺参数和工艺条件,可以改善机械加工表面质量。
改进措施主要包括以下几个方面:首先,对加工工艺参数进行优化调整,合理选择切削速度、进给量和切削深度,以达到最佳的加工表面质量。
其次,提高机床的性能,加强机床的刚性和稳定性,减小振动,以确保切削过程的稳定性,促进机械加工表面质量的提高。
简析机械加工表面质量对零件使用性能的影响问题

简析机械加工表面质量对零件使用性能的影响问题
机械加工表面质量对零件的使用性能有很大的影响,它直接影响到零件的摩擦、磨损、耐蚀性和疲劳寿命等方面。
以下是对机械加工表面质量影响因素的简析:
1. 摩擦和磨损:机械加工表面的粗糙度会直接影响零件与其他物体之间的摩擦及磨
损情况。
如果表面太光滑,摩擦系数往往会较高,在摩擦过程中容易产生滑脱现象;而如
果表面太粗糙,摩擦系数虽然较低,但易引起磨损严重。
要根据实际情况选择合适的加工
表面质量,以达到最佳的摩擦和磨损阻力。
2. 耐蚀性:机械加工表面质量对零件的耐蚀性也有很大影响。
粗糙表面易于积存氧
化物和磨料,从而加速零件的腐蚀过程;而光滑表面往往能更好地抵御外部环境的侵蚀。
所以,在需要耐蚀性较高的零件上,要尽可能采用较为光滑的加工表面质量。
3. 疲劳寿命:机械加工表面质量还会对零件的疲劳寿命产生影响。
粗糙表面容易形
成微小的裂纹和应力集中点,从而加速零件的疲劳破坏;而光滑表面则能减少应力集中,
延长零件的使用寿命。
在需要较高疲劳寿命的零件上,应该优先考虑提高加工表面的光滑度。
机械加工的表面质量对零件的使用性能有着显著的影响。
为了提高零件的使用寿命和
工作效率,需要根据具体应用需求选择合适的加工表面质量,并通过合理的加工工艺和设备,确保零件的表面质量达到要求。
机械加工表面质量的影响因素及控制措施

机械加工表面质量的影响因素及控制措施机械加工表面质量表面是影响机械产品性能的重要环节,故对机械加工表面质量影响因素进行分析,把握影响根源,才能够对症下药,做到有效控制。
本文就机械加工表面质量的影响及原因进行了分析,并提出了解决措施。
伴随着近几年现代机械技术的快速发展,各种自能化设备及机械成为了人们生产、生活的工具,使得各种机械零件长时间处于高温、高速、高压环境,为此,当前各行各业对机械零件加工质量要求也随之提高,一旦出现零件质量问题,势必会导致原有工作性能因此受到影响。
通过综合分析,不难发现导致零件工作性能受到影响的关键因素当属零件表面质量,由于其可能对零件上的物理动能造成影响,故本文就机械加工表面质量影响进行探索,旨在为机械加工提出相应的解决对策。
机械加工表面质量的影响因素分析1.1零件加工的原材料机械加工中原材料是非常重要的基础性部分,在进行机械加工时,不管拥有何种技术手段和技术条件,若加工材料欠佳那么机械加工表面质量也势必会受到影响。
为此,机械加工企业要重视长远发展就必须对原材料有更深的认识,并尽可能选择良好的原材料。
1.2零件加工的技术零件加工本身就需要采用强大的技术作为支撑,除去原材料可使机械加工表面受到影响,加工技术也是影响机械加工表面的重要因素之一。
优秀的技术条件和技术支持,在很大程度上可使机械加工原材料上的小缺点受到影响;但若技术非常落后,那么即使拥有再好的原材料也是无法使机械零件质量得到保证的。
为此,提高切削和打磨等加工技术均是提升机械加工表面质量的重要方法。
1.3零件表层的冷作硬化在机械零件加工时,“切削力作用产生的塑性变形”是左右零件表面质量的因素之一,其可导致零件表面出现扭曲变形,“晶粒之间所形成的剪切滑动,晶粒因此出现纤维化和被拉长的变化,严重情况下甚至出现破碎”,这些因素都可能对机械零件表层的硬度造成影响,也就是我们所说的“冷作硬化”。
这种反应的存在也在一定程度上,可致使金属的变形阻力发生变化,相应的物理性质也会因此发生变化。
浅析机械加工表面质量影响因素

浅析机械加工表面质量影响因素作者:王凯为来源:《数字化用户》2013年第05期【摘要】机器的组成离不开零件,因此零件在质量和性能上的好坏也决定了机器能否有效运行。
因而零部件在质量上的要求也在一定程度上对机械加工表面的质量有一定的要求,因此,本文将对机械加工表面质量影响因素进行分析,从而提高机械加工方面的质量水平,改善机械加工在加工表面的质量问题。
【关键词】零件加工质量机械表面影响因素残余应力科学技术的发展为我们的生产技术的进步提供一个良好的技术基础,使得人们机械零件的要求质量的越来越高,因此,随着仪器的不断升级,机械零件的要求也越来越高,因此为了确保机械的安全有效的运行,对机械零件的质检也要进行严格把守。
在机械零件质量问题我们不仅强调精度上的精密,在其表面质量上的要求也是有一定的要求。
机械加工表面质量是指机械零部件加工完成后,其表面所表现的出的状态[1]。
机械表面质量会随身机器在运行的过程不断的受到磨损和腐蚀,从而能也在一定程度影响了机器的质量问题。
因此对机械加工的表面质量影响因素进行阐述,从而能够改善机器使用寿命。
一、机械加工零件表面质量含义及要求(一)表面质量含义机械的表面是难以做到绝对光滑的程度的技术水平,在零件表面进行加工时对受切削力、切削热的影响产生机械性能的改变,因此我们一般从三个方面对表面质量进行含义概括。
1.机械加工零件表面粗糙度。
粗糙度的产生是由于加工表面在进行切削的加工过程中产生的微小峰谷从而导致在微观形成一定几何形状的误差,也由于加热和切割工具在使用过程中产生的摩擦和高频振动也会形成机械表面的粗糙度。
2.机械性能的变化。
由于受到物理作用的原因,在机械表面往往在加工过程中受到切削变形或者是切削热的影响,因此产生的残余应力是会在一定程度上使得表面产生裂纹。
从而影响了金属表面质量的稳定度,存在着一定的威胁性。
3.表面层金相组织的变化。
对机械表面惊醒磨削时,所产生的高温容易破坏到机械零件表面,使得钢件表面退火,从而导致表面的金属发生了相变。
影响机械加工表面质量的因素及改进措施
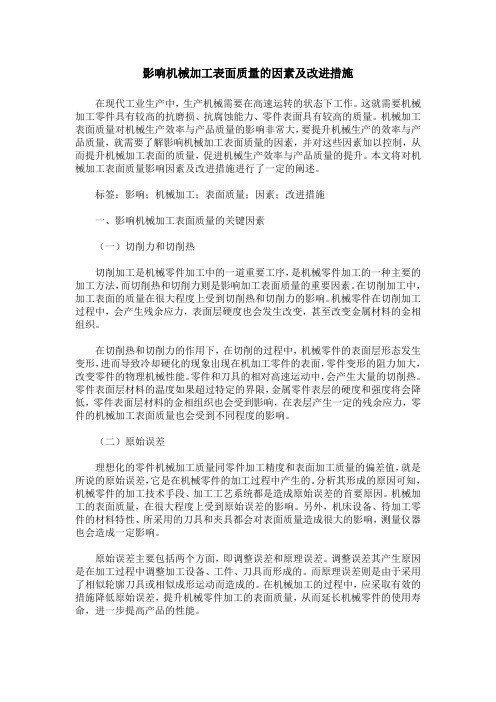
影响机械加工表面质量的因素及改进措施在现代工业生产中,生产机械需要在高速运转的状态下工作。
这就需要机械加工零件具有较高的抗磨损、抗腐蚀能力、零件表面具有较高的质量。
机械加工表面质量对机械生产效率与产品质量的影响非常大,要提升机械生产的效率与产品质量,就需要了解影响机械加工表面质量的因素,并对这些因素加以控制,从而提升机械加工表面的质量,促进机械生产效率与产品质量的提升。
本文将对机械加工表面质量影响因素及改进措施进行了一定的阐述。
标签:影响;机械加工;表面质量;因素;改进措施一、影响机械加工表面质量的关键因素(一)切削力和切削热切削加工是机械零件加工中的一道重要工序,是机械零件加工的一种主要的加工方法,而切削热和切削力则是影响加工表面质量的重要因素。
在切削加工中,加工表面的质量在很大程度上受到切削热和切削力的影响。
机械零件在切削加工过程中,会产生残余应力,表面层硬度也会发生改变,甚至改变金属材料的金相组织。
在切削热和切削力的作用下,在切削的过程中,机械零件的表面层形态发生变形,进而导致冷却硬化的现象出现在机加工零件的表面,零件变形的阻力加大,改变零件的物理机械性能。
零件和刀具的相对高速运动中,会产生大量的切削热。
零件表面层材料的温度如果超过特定的界限,金属零件表层的硬度和强度将会降低,零件表面层材料的金相组织也会受到影响,在表层产生一定的残余应力,零件的机械加工表面质量也会受到不同程度的影响。
(二)原始误差理想化的零件机械加工质量同零件加工精度和表面加工质量的偏差值,就是所说的原始误差,它是在机械零件的加工过程中产生的。
分析其形成的原因可知,机械零件的加工技术手段、加工工艺系统都是造成原始误差的首要原因。
机械加工的表面质量,在很大程度上受到原始误差的影响。
另外,机床设备、待加工零件的材料特性、所采用的刀具和夹具都会对表面质量造成很大的影响,测量仪器也会造成一定影响。
原始误差主要包括两个方面,即调整误差和原理误差。
影响机械加工表面质量的因素及措施
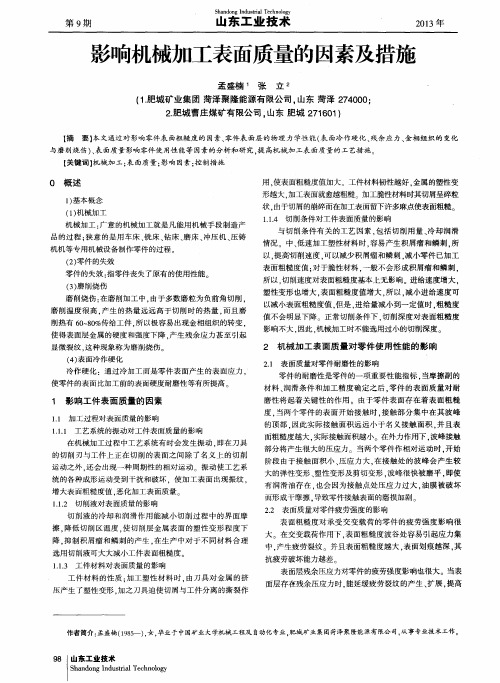
零件 的耐 磨性 是零 件的一项重要性 能指标 , 当摩擦副 的
材料 、 润滑条 件和加工 精度确定 之后 . 零件 的表面 质量对 耐
磨性将起着 关键性 的作用 由于零件 表面存 在着 表面粗糙
1 影 响工件 表 面质量 的 因素
1 . 1 加 工 过 程 对 表 面 质量 的影 响
0 概 述
1 ) 基 本 概 念 ( 1 ) 机 械加 工
用, 使表面粗糙 度值加大。工件材料 韧性越好 . 金属的塑性 变
形越 大. 加工表面就愈越粗糙 加工胞 洼材料时其切屑呈碎粒 状, 由于切屑 的崩碎而在加工表面 留下许多麻点使表面粗糙 。
1 . 1 . 4 切削条件对工件 表面质量 的影 响
( 1 9 8 5 -) , 女, 毕业 于中国矿业大 学机械工程及 自动化专业 , 肥城矿业集 团菏泽聚隆能源有限公司 , 从事专业技 术工作。
9 8 I 山东工业技术
1 S h a n d o n g I n d u s t r i a l T e c h n o l o g y
1 . 1 . 2 切 削液 对 表 面 质 量 的影 响
切 削液 的冷 却和润 滑作用能 减小切 削过程 中 的界 面摩
擦, 降低切 削区温度 . 使切 削层金属表 面 的塑性 变形程 度下
降. 抑制积 屑瘤和鳞刺 的产生 . 在生产 中对于不 同材料 合理
选用切削液可大大减小工件表 面粗糙度 。 I . 1 . 3 工件材料对表面质量 的影响 工 件材料 的性 质 : 加工塑性材 料时 . 由刀具对 金属 的挤
值不会 明显下 降。正常切 削条件 下 . 切 削深度对表 面粗糙度 影响不大 , 因此 . 机械加工时不能选用过小 的切削深度 。
影响机械加工表面质量的因素及改进措施

影响机械加工表面质量的因素及改进措施
一、影响机械加工表面质量的因素。
1.机床和刀具破损:机床体系及其附件的破损,会影响刀具的正常安
装及运行,从而产生肉眼可见的小硬斑、节肢及拉伤着痕等。
刀具的破损,也会影响机加工表面的质量,表现在高点、拉伤、刀印等方面,增大机加
工表面质量不稳定性及表面粗糙度。
2.刀具磨损:刀具工作经过一段时间,就会变得锋利变尖,从而影响
机械加工表面质量,表现为断刃,切口拉伤等,给进程控制带来更多的困难,增加了失效率。
3.加工环境:通常条件下,温度、湿度、噪声及污染等外界环境因素,会影响机械加工表面质量,表现为减少刀具的硬度,使刀具失去钝化作用,从而影响机械加工表面的质量。
4.加工工艺:在机械加工过程中,不同的加工工艺选择,会影响机械
加工表面的质量,如使用过大的进给量或过长的切削时间,则会使刀具快
速磨损,影响加工表面质量。
二、改善措施。
1.检查机床及刀具:定期检查机床及刀具的破损情况,及时更换破损
的部件,使刀具能够正常工作。
2.控制刀具磨损:合理控制刀具的运行时间,根据不同材料选择合适
的刀具,以满足机械加工工艺要求,并减少刀具的损。
机械加工质量的影响因素及防治措施

机械加工质量的影响因素及防治措施摘要:在加工过程中,影响工件表面质量的因素很多,导致产品质量不合格,进而影响其使用寿命和性能。
因此,它是进一步提高加工质量水平和工作效率的有效手段,也是加工人员和相关管理人员在加工前必须面对和考虑的问题。
关键词:机械加工质量;影响因素;防治措施1机械加工质量对产品性能的影响加工质量直接影响到产品的实际性能,因此要注意具体的影响程度,采取合理的方法,适当避免干涉程度,以保证加工质量更好,产品性能得到保证。
1.1 耐磨性加工质量是影响零件磨损的决定性因素。
在零件的具体操作过程中,如果加工表面粗糙,势必影响零件的操作效果,也会产生更为严重的后果。
零件的磨损可分为不同的阶段,主要包括两个阶段,即初始磨损阶段和正常磨损阶段。
表面的基本粗糙度是一个不容忽视的重要问题。
它会直接影响零件的使用。
如果表面粗糙度控制得当,损伤越小,使用寿命越长,其他部件的干涉越小。
如果表面粗糙度值太小,润滑油就不易保存,这就增加了部件在运行过程中与其他部件的接触面,相应的磨损程度也就大大提高。
1.2 疲劳强度金属易受多种因素和载荷的影响。
在各种因素和载荷的影响下,金属能够反映变形,同时又呈现冷热交替的状态,加剧了金属本身的疲劳。
零件一旦受到影响,加工阶段的表面粗糙度会显著提高,抗疲劳效果较差。
1.3耐腐蚀性一般来说,零件往往表现出相应的耐腐蚀性因素,而外观的表面质量会严重影响零件的耐腐蚀性。
零件是否会发生严重腐蚀与表面质量的好坏密切相关[3]。
如果零件的实际粗糙度很明显,则表明其耐腐蚀性很低。
如果表面光滑,基本防腐效果极佳。
2 影响机械加工表面质量的因素根据机械加工原理以及实际生产经验,影响机械加工表面质量的因素可以分为以下几个方面:2.1影响表面粗糙度的因素2.1.1材料的性能影响粗糙度机械零件基体材料的性能是决定加工后表面性能的重要因素。
例如,发现合金材料在加工前经过热处理。
这种热处理可以改善合金材料在加工过程中的磨损机理,提高合金材料的耐磨性,获得表面耐磨性好的机械零件。
机械加工表面质量影响因素及对策分析

1 机 械 加工 后零 件 表 面质 量要 求
() 工后 的 零件 表 面 的尺 寸公 差 必须 符 合零 件 的 规定 。 () 1加 2
糙 度变 大 而 引起 的 。 零 件表 面 各个 部 位 的形 状及 位 置应 当 符合 零件 的规 定 ( 直 度 、 垂 平 2 3 表 面质 量 会影 响 到耐 蚀性 . 行 度 等) 3 零 件 的表 面硬 度 必须 符 合其 硬度 测 定 的标准 。() 。() 4 测 零 件表 面 的 耐腐 蚀性 一般 取 决于 零 件表 面 的粗 糙 度 ,粗 糙度
在 间 隙配 合 中 , 糙 度越 大 , 粗 磨损 就越 大 , 间隙就 会增 加 , 致 配合 导 的要 求 受到破 坏 。但 是 , 如果 零 件过 于盈 合 , 会将 零 件 的表 面 凸 峰
挤 压 得相 对 过平 , 会 降低零 件 表面 的实 际盈量 , 也 导致 降低 与 之配 合 工件 问的连 接 强度 。
z n h a j 。 g eY ni u
机械 加工表面质量影响因素及对策分析
艾 勇 军
( 贵州双阳飞机制造 厂, 贵卅I 安顺 5 1 1) 6 0 8
摘 要: 机械零件 表面层 的质量 决定了零件 的可靠 性与耐久度 。现概述 了机械加工后零 件表面 的质量要求 , 影响机械 加工表面质 量的因 对 素进行 了分析 , 并从 5个方面探讨 了提高机械加工表 面质量的对策措施 。
零 件 加工 表面 的 磨损 主 要包 括 初 期 、正 常 以及 剧烈 3个阶 段 的磨损 。零件 加 工表 面 的粗 糙度 很 大程 度 上影 响 到 了其 表 面 的磨 损 。 般 来说 , 件表 面 的粗 糙 度越 小 , 一 零 磨损 也 就越 小。 果 表面 的 如 粗 糙度 太 小 , 不适 合润 滑 剂 的储 存 , 反而 会 引起 磨损 的增加 。 因此 , 其 粗糙 度 需要 一 个最 佳值 。
机械加工表面质量影响因素及改善

2、加工表面层的残余应力
2)表面层残余应力的影响因素 (1)刀具方面 ①刀具几何因素 前角对残余应力有很大影响。图p188 454 ②刀具磨损;图p189 4-55 (2)工件方面 工件材料塑性越大,切削加工后产生的残余拉应力越大。 (3)切削条件方面 切削用量三要素对残余应力影响较大。图p189 4-57 、4-58
高速钢、硬质合金或陶瓷刀具在切削低碳钢、中碳钢等塑
性金属,加工工序中都可能产生鳞刺。会使表面粗糙度加工。 成为塑性金属材料精加工的一个障碍。 在物理因素方面,降低表面粗糙度主要措施,即消除积 屑瘤和鳞刺的措施。
2、切削加工表面粗糙度的产生原因及其控制
4)切削机理的变化:
在挤裂切屑或单元切屑形成的过程中,由于单元切屑 周期性的断裂在切屑表面以下深入,在加工表面上留下挤 裂痕迹而呈现波浪形。在崩碎切屑形成过程中,从主切削 刃处开始的裂纹在接近主应力方向斜着向下延伸,造成加 工表面凹凸不平。p182图4-39 切削刃两侧的工件材料被挤压后因没有侧面的约束力
在精密磨削时不能判断试切时的吃
刀量,很不方便。
(3) 磨削用量的选择
1)提高工件速度和采用小的切深能够有效地减小残余拉应
力和消除烧伤、裂纹等磨削缺陷。
3、 磨削烧伤及磨削裂纹及其控制
2)降低砂轮速度也能得 3)提高砂轮速度的同时相应 提高工件速度,可以避免烧伤。
到残余压应力,但是会影响
生产效率,故一般不常采用。
2、切削加工表面粗糙度的产生原因及其控制
1)理论粗糙度P181:
刀具几何参数中的主偏角、副偏角和刀尖圆弧半径及切削
用量中的进给量是产生理论粗糙度的最基本因素。
Rmax
f cot cot '
影响机械加工表面质量的因素及改进措施
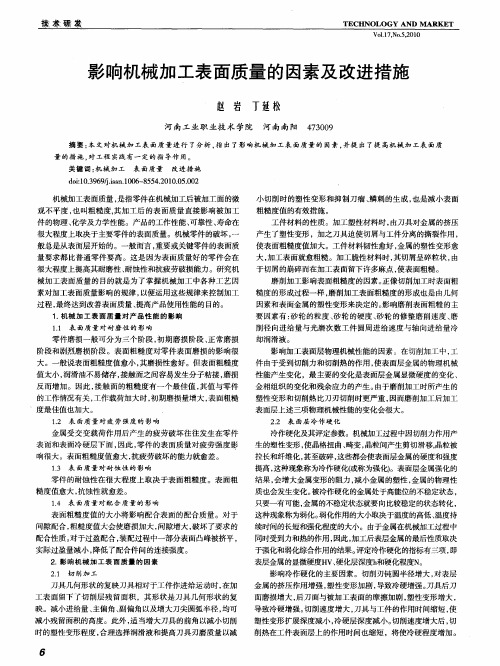
很大程度上提高其耐磨性 、 耐蚀性和抗疲劳破损能力。研究机
械加工表面质量 的目的就是为 了掌 握机械加工 中各种工艺 因
于切 屑的崩碎而在加工表面留下许多麻点 , 使表面粗糙 。 磨削加工影响表 面粗糙度的因素。 正像切削加工时表 面粗
糙度 的形成过程一样 , 磨削加工表面粗糙度的形成也是 由几何
di 03 6/i n10 - 5 4 0 0 5 0 o: . 9 .s.06 85 . 1 . . 2 1 9 js 2 00
机械加工表面质量 , 是指零件在机械加 工后被加工面的微
小切削时 的塑性变形 和抑制 刀瘤 、 鳞刺 的生 成 , 也是减小表 面
观不平 度 , 叫粗糙度 , 也 其加工 后的表面质量 直接影响被加 工 件 的物理 、 化学及力学性 能。产品的工作性 能、 可靠性 、 寿命 在 很大程度上取决 于主要零件的表面质量 。机械零件 的破坏 , 一
1 表 面质 量 对 耐蚀 性 的影 响 . 3
冷作硬化及其评定参数 。机械加工过程 中因切削力作用产 生的塑性变形 , 使晶格扭曲 、 畸变 , 间产生剪切滑移, 晶粒 晶粒被 拉长和纤维化 , 甚至破碎 , 这些都会使表面层金属 的硬度和强度
提高 , 这种现象称为冷作硬化( 为强4) 或称 L 。表面层金属强化的
塑性变形扩展深度减小 , 冷硬层深度减小。 切削速度增大后 , 切
攮 砥 发
T C N L G N A K T E H o 0 YA DM R E
Vo. 7 No 52 0 11 , . ,01
影 响机械加 工表面质量 的 因素及 改进措施
赵 丁延松 岩
河 南工业 职业技 术 学院 河 南南阳 430 709
影响机械加工表面质量的因素
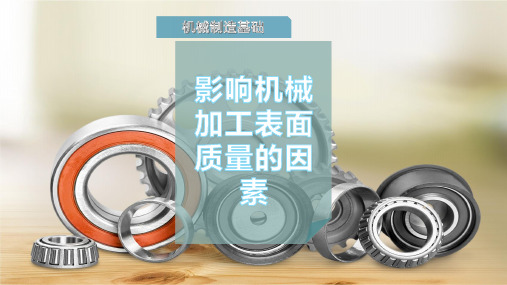
影响机械加工表面质量的因素
1.2影响加工表面层物理力学性能的因素
2)切削热的影响 切削过程中产生的热作用在不引起相变的情况下,使工件表面层产生拉伸 残余应力,里层产生压缩残余应力。工件加工表面在切削热作用下产生热膨胀, 此时表层金属温度高于基体温度,因此表层产生热压应力。当表层温度超过材 料的弹性变形允许的范围时,就会产生热塑性变形(在压应力作用下材料相对 缩短)。当切削过程结束后,表面温度下降,由于表层已产生热塑性缩短变形, 并受到基体的限制,故而在表面层产生残余拉应力。
影响机械加工表面质量的因素
1.2影响加工表面层物理力学性能的因素
2.表面层材料金相组织变化 当切削热使被加工表面的温度超过相变温度后,表层金属的金相组织将会发生变化。 一般切削加工(如车、铣、刨削等),产生切削热的工件加工表面温升不会达到相变的临 界温度,因此不会发生金相组织变化。磨削加工时,由于磨粒在高速下进行切削、刻划 和划擦,使工件表面温度很高,常达 900℃以上,达到相变温度,引起表面层金相组织发 生变化,从而使表面层的硬度下降,并伴随出现残余应力,甚至产生细微裂纹,这种现 象称为磨削烧伤。磨削烧伤将严重影响零件的使用性能。因此,磨削是一种典型的容易 产生加工表面金相组织变化的加工方法。 严重的磨削烧伤使零件的使用寿命成倍下降,甚至无法使用。工件磨削出现的烧伤 色是工件表面烧伤时产生的氧化膜颜色,由于烧伤程度不同,氧化膜厚度不等,氧化膜 呈现的颜色不同,有黄、褐、紫、蓝等色,紫色和蓝色氧化膜为烧伤程度严重。改善磨 削烧伤有两个途径:一是尽可能地减少磨削热的产生;二是改善冷却条件,尽量使产生 的热量少传入工件。
影响机械加工表面质量的因素
1.1影响表面粗糙度的因素
3)工件材料 工件材料的硬度、塑性、韧性和导热性能等对表面粗糙度有显著影响。工件材料太 硬时,磨粒易钝化;太软时砂轮易堵塞;韧性大和导热性差的材料,使磨粒早期崩落而 破坏了微刃的等高性,因此均使表面粗糙度增大。 4)磨削用量 ①砂轮速度。提高砂轮速度可以增加在工件单位面积上的刻痕,同时使塑性变形造 成的隆起量下降,这是由于高速度下塑性变形的传播速度小于磨削速度,材料来不及变 形所致,因而表面粗糙度可以显著降低。 ②进给量。进给量小,则单位时间内加工的长度短,故表面粗糙度值小。 ③背吃刀量。减小背吃刀量,将减小工件材料的塑性变形,从而减小表面粗糙度值。 为兼顾磨削效率,通常先采用较大的磨削深度,而后采用小的背吃刀量或光磨。
影响机械加工表面质量的因素及控制措施
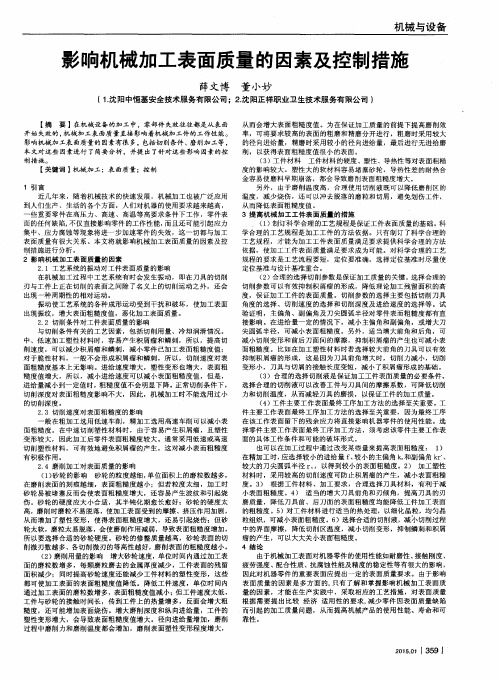
影响机械 加工表面质 量 的因素及控 制措施
薛文博 董 小妙
( 1 . 沈阳中恒基安全技术服务有 限公司 ;ห้องสมุดไป่ตู้ 2 . 沈 阳正 祥职 业卫生技术服务有 限公司 )
【 摘 要】 在机械设备 的加 工中,零 部件 失效往往都是从表面
从而会增大表面粗糙度值 。为在保证加工质量的前提下提高磨削效 率,可将要求较高 的表面 的粗 磨和精磨分开进行,粗磨时采用较大 的径向进给量 ,精磨 时采 用较 小的径 向进给量,最后进行无进给磨 削, 以获得表面粗糙度值很小 的表面 。 ( 3 )工件材料 工件材料 的硬度 、塑性 、导热性等对表面粗糙 度 的影响较大。塑性大 的软材料 容易堵塞砂 轮,导热性差的耐热合 金容 易使 磨 料 早 期 崩 落 ,都 会 导 致 磨 削 表 面 粗 糙 度 增 大 。 另外 ,由于磨 削温度 高,合理使用切削液既可 以降低磨削区 的 温 度 , 减 少 烧 伤 ,还 可 以冲 去 脱 落 的 磨 粒和 切 屑 , 避 免 划 伤 工 件 , 从 而 降低 表 面粗 糙 度值 。 3 提高机械加工工 件表面 质量 的措施 ( 1 ) 制订科学合理 的工艺 规程是 保证工件表面质量 的基础 。科 学 合 理 的 工 艺 规 程 是 加 工 工 件 的方 法 依 据 。 只有 制 订 了科 学 合 理 的 工 艺规程 ,才能为加工工件表面质量满 足要 求提供科 学合 理的方法 依 据 ,使 加 工 工 件 表 面 质 量 满 足 要求 成 为可 能 。对 科 学 合 理 的 工 艺 规 程 的 要 求 是 工 艺 流 程 要 短 , 定位 要准 确 , 选 择 定位 基准 时 尽 量 使 定位 基 准 与 设计 基 准 重 合 。 ( 2 )合 理 的选 择 切 削参 数 是保 证 加工 质 量 的关 键 。选 择 合 理 的 切削参数可 以有效抑制积屑瘤 的形成 ,降低 理论加 工残留面积的高 度 ,保证加 工工件的表面质量 。切 削参 数的选择 主要 包括 切削刀具 角度 的选择 、切削速度 的选择和切 削深 度及进给速度 的选 择等 。试 验证 明,主偏角、副偏角及刀尖 圆弧半径对 零件表 而粗糙度都有直 接 影响。在进给量一定 的情况下 ,减 小主偏 角和副偏 角,或增大刀 尖 圆弧半径 ,可减小表面粗糙度 。另外 ,适 当增大前 角和 后角,可 减小切 削变 形和 前后刀面 问的摩擦 ,抑 制积 屑瘤 的产 生也 可减小表 面粗糙度 。 比如在加工塑性材料 时若选 择较 大前角 的刀具可以有效 抑制积 屑瘤 的形成 ,这是 因为 刀具前角 增大 时,切 削力减 小,切削 变 形小,刀具与切屑的接触长度变短 ,减小 了积屑瘤形成的基础 。 ( 3 )合理的选择切削液是保证加工工件表面质量的必要条件。 选择合理 的切削液可 以改善工件与刀具 间的摩擦系数 ,可 降低切削 力和切削温度 ,从而减 轻刀具的磨损 ,以 保 证工件 的加工质量。 ( 4) 工件主要工作表面最 终工序 加工方法 的选择至关重要 。工 件 主要工作表面最终工序加工方法 的选 择至 关重要 ,因为最终工序 在 该工作表面留下 的残余应力将 直接 影响机 器零件 的使用 性能 。选 择零件主要工作表面最终 工序 加工方法,须考虑该零件主要工作表 面 的具体 工作条 件和可 能的破 坏形式 。 也可以在加工过程 中通过 改变某些 量来提 高表面 粗糙 度: 1 ) 在精 加工 时, 应选择较小的进给量 f 、 较小的主偏角 k 和副偏角 k r ’ 、 较大的刀尖圆弧半径 r ,以得 到较 小的表面 粗糙度 。2 ) 加工塑性 材料时,采用较高 的切削速度 可防止积 屑瘤 的产生,减小表面粗糙 度。3 ) 根据工件材料 、加工 要求,合理选 择刀具材料,有利于减 小表 面粗 糙度。4 ) 适 当的增大 刀具前 角和 刃倾 角,提高刀具的刃 磨质 量 , 降 低 刀 具 前 、后 刀面 的表 面 粗 糙度 均 能 降低 工件 加 工 表 面 的粗糙度 。5 )对工件材料进行适 当的热 处理 ,以细化 晶粒 ,均匀晶 粒组织,可减小表面粗糙度 。6 )选择合适的切削液 ,减小切削过程 中的界面摩擦 ,降低切削 区温度 ,减小切削变形,抑制鳞刺和积屑 瘤的产生 ,可 以大大关小表面租 糙度 。 4 结 论 由于机械加工表面对机器零件的使用性能如耐磨性、 接触刚度、 疲劳强度 、配合性质 、抗腐蚀性能及精度的稳定性等有很大的影响 ,
分析机械加工过程中影响工件表面质量的几个因素
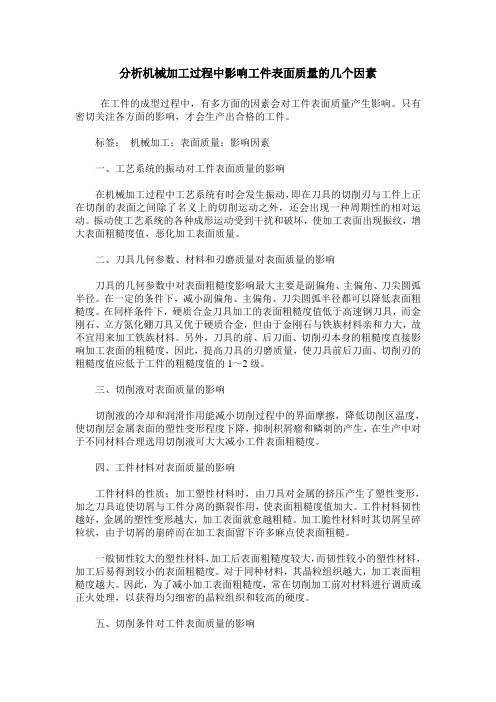
分析机械加工过程中影响工件表面质量的几个因素在工件的成型过程中,有多方面的因素会对工件表面质量产生影响。
只有密切关注各方面的影响,才会生产出合格的工件。
标签:机械加工;表面质量;影响因素一、工艺系统的振动对工件表面质量的影响在机械加工过程中工艺系统有时会发生振动,即在刀具的切削刃与工件上正在切削的表面之间除了名义上的切削运动之外,还会出现一种周期性的相对运动。
振动使工艺系统的各种成形运动受到干扰和破坏,使加工表面出现振纹,增大表面粗糙度值,恶化加工表面质量。
二、刀具几何参数、材料和刃磨质量对表面质量的影响刀具的几何参数中对表面粗糙度影响最大主要是副偏角、主偏角、刀尖圆弧半径。
在一定的条件下,减小副偏角、主偏角、刀尖圆弧半径都可以降低表面粗糙度。
在同样条件下,硬质合金刀具加工的表面粗糙度值低于高速钢刀具,而金刚石、立方氮化硼刀具又优于硬质合金,但由于金刚石与铁族材料亲和力大,故不宜用来加工铁族材料。
另外,刀具的前、后刀面、切削刃本身的粗糙度直接影响加工表面的粗糙度,因此,提高刀具的刃磨质量,使刀具前后刀面、切削刃的粗糙度值应低于工件的粗糙度值的1~2级。
三、切削液对表面质量的影响切削液的冷却和润滑作用能减小切削过程中的界面摩擦,降低切削区温度,使切削层金属表面的塑性变形程度下降,抑制积屑瘤和鳞刺的产生,在生产中对于不同材料合理选用切削液可大大减小工件表面粗糙度。
四、工件材料对表面质量的影响工件材料的性质;加工塑性材料时,由刀具对金属的挤压产生了塑性变形,加之刀具迫使切屑与工件分离的撕裂作用,使表面粗糙度值加大。
工件材料韧性越好,金属的塑性变形越大,加工表面就愈越粗糙。
加工脆性材料时其切屑呈碎粒状,由于切屑的崩碎而在加工表面留下许多麻点使表面粗糙。
一般韧性较大的塑性材料,加工后表面粗糙度较大,而韧性较小的塑性材料,加工后易得到较小的表面粗糙度。
对于同种材料,其晶粒组织越大,加工表面粗糙度越大。
因此,为了减小加工表面粗糙度,常在切削加工前对材料进行调质或正火处理,以获得均匀细密的晶粒组织和较高的硬度。
影响机械加工表面质量因素分析

影响机械加工表面质量的因素分析摘要:机械加工表面质量主要体现在表面光洁度和加工表面层物理机械性能两方面,本文对其各自的影响因素进行分析,并试图通过其原因分析,来解析提升机械加工表面质量的方式,以促进机械加工效能的发挥。
关键词:机械加工;表面质量;影响因素随着工业技术的进步,机器的使用要求越来越高,其不仅要求机械精准性加工,而且要求其表面具备抗磨损、抗腐蚀、抗疲劳等高质量标准,而从机器故障发生的原因来看,很大部分由于机械表面质量因素造成的,这不但影响了机械零件的工作性能、使用寿命,而且对生产加工产生重大经济性、安全性的影响。
所以,在机械加工中,要通过对其质量影响因素的分析,来进行表面质量的控制,一、表面粗糙度的影响因素1、工件材料工件材料的刚硬性或柔韧性是影响表面粗糙度的材料性因素,不同塑性材料,由于其韧性不同,其表面粗糙度就不同。
一般来说,韧性较强,刀具对材料的压力值增大,同时在切屑剥落时的扯拽力量的共同作用下,往往引起加工变形,造成表面加工的严重粗糙;材料韧性越好,金属的塑性变形就越大,而表面粗糙度就越高。
材料脆性较高时,切削时出现碎粉屑,其崩碎在加工表面,往往形成一些麻点,造成表面粗糙。
2、切削加工刀具几何形状往往影响着表面质量。
在加工过程中,通过各种形状的刀具,其在外体作业时,会有残痕,其复映出刀具形状,这就造成表面出现花纹或是条纹,降低了表面光滑度。
针对其问题,则可以采用高速度切削塑性材料的方式来减小进给量,提高表面光滑度;减小主偏角、副偏角和增大刀尖圆弧半径的方式,来减少残留面积的高度;可以用增大刀具前角的方式来减少切削时的塑性变形。
切削液对加工起到冷却、润滑的作用,其以降低切削区的温度,减少刀具和工件之间的摩擦力来实现机械加工表面质量的提高。
所以,在进行加工时,要以合理的润滑液减少刀具与机械表面的摩擦,提升刀具刃磨质量的同时,来抑制刀瘤、鳞刺等现象的发生,以提升加工表面的光洁度。
3、磨削加工磨削加工是表面加工质量的修复阶段,也是表面质量的最后确定阶段,其同表面粗糙度的形成一样,同是由于刀具几何因素和金属塑性变形引起,而其影响因素主要有砂轮粒度、砂轮强度、砂轮的修整、磨削速度、磨削径向进给量和光磨次数等。
- 1、下载文档前请自行甄别文档内容的完整性,平台不提供额外的编辑、内容补充、找答案等附加服务。
- 2、"仅部分预览"的文档,不可在线预览部分如存在完整性等问题,可反馈申请退款(可完整预览的文档不适用该条件!)。
- 3、如文档侵犯您的权益,请联系客服反馈,我们会尽快为您处理(人工客服工作时间:9:00-18:30)。
机械加工表面质量及影响因素一、表面质量定义任何机械加工所得的表面,实际上不可能是理想的光滑表面,总是存在一定的微观几何形状误差。
另外,表面材料在加工时受切削力、切削热的影响,也会使原有的物理—机械性能发生变化。
因此,加工表面质量应包括:1、加工表面粗糙度。
是指加工表面的较小间距和微小峰谷的微观几何形状误差。
它主要是由于切削加工过程中的刀痕、切削分离时的塑性变形、刀具与被加工表面的摩擦、工艺系统的高频振动等原因造成的。
2、表面层的物理———机械性能变化。
表面层的材料在加工时,物理—机械性能变化主要有以下三个方面的内容:1)表面层的冷作硬化。
工件在机械加工过程中,表面层金属产生强烈的塑性变化,使表层的强度和硬度都有所提高,这种现象称表面冷作硬化。
2)表面层残余应力。
在切削加工过程中,由于切削变形和切削热的影响,在加工表面会产生残余应力,如果残余应力超过材料的屈服强度,就会产生表面裂纹,表面的微观裂将给零件带来严重的隐患。
3)表面层金相组织的变化。
工件表面经磨削精加工时,磨削产生的高温,一般可达800~1000 ℃,高的磨削温度会烧坏工作表面,使淬火钢件表面退火,引起表层金属发生相变,将大大降低表面层的物理—机械性能。
二、影响表面粗糙度的因素1、切削加工影响表面粗糙度的因素刀具几何形状及切削运动的影响刀具相对于工件作进给运动时,在加工表面留下了切削层残留面积,从而产生了表面粗糙度,残留面积的形状是刀具几何形状的复映,其高度H受刀具的几何角度和切削用量大小的影响。
减小进给量vf、主偏角、副偏角以及增大刀尖圆弧半径,均可减小残留面积的高度。
此外,适当增大刀具的前角,以减小切削时的塑性变形的程度,合理选择润滑液和提高刀具刃磨质量,以减小切削时的塑性变形和抑制刀瘤、鳞刺的生成,也是减小表面粗糙度值的有效措施。
2、工件材料的性质加工塑性材料时,由于刀具对金属的挤压,产生了塑性变形,加之刀具迫使切屑与工件分离的撕裂作用,使表面粗糙度值加大。
工件材料韧性愈好,金属的塑性变形愈大,加工表面就愈粗糙。
加工脆性材料时,其切屑呈碎粒状,由于切屑的崩碎而在加工表面留下许多麻点,使表面粗糙度增大。
3、磨削加工影响表面粗糙度的因素如同切削加工时表面粗糙度的形成过程一样,磨削加工表面粗糙度的形成,也是由几何因素和表面金属的塑性变形来决定的。
影响磨削表面粗糙的主要因素有:1)砂轮的粒度与硬度。
砂轮硬度应适当,应使磨粒钝后会及时脱落,露出新的磨粒来继续切削,即具有良好的“自砺性”。
砂轮的粒度愈细,即单位面积上的磨粒数愈多,则加工表面的刻痕愈细密,表面粗糙度愈低。
但若粒度过细,则容易堵塞砂轮,而使工件表面塑性变形增加,从而影响表面粗糙度的降低。
2)砂轮的修整。
砂轮应及时修整,以去除已钝化的磨粒,保证砂轮具有微刃性和等高性。
用金刚石修整砂轮相当于在砂轮上“车削”外圆,纵向和横向的进给量愈小,修整出来的砂轮表面的微刃性和等高性就愈好,磨出工件表面的粗糙度也愈低。
3)磨削速度、径向进给量、光磨次数、工件圆周进给速度与轴向进给量。
减小磨削用量和提高砂轮速度,可以增加工件单位面积上的刻痕数,同时可降低因塑性变形造成的表面粗糙度。
因为在高速磨削下,磨削表面来不及塑性变形,因而提高砂轮速度有利于降低表面粗糙度。
增大磨削深度和提高工件速度会使塑性变形加剧,从而增高粗糙度。
为了提高磨削效率,通常在开始磨削时采用较大的磨削深度,而在磨削后期采用小的磨削深度,或进行无进给磨削(光磨),以降低工件表面粗糙度。
4)切削液。
切削液对加工过程起冷却和润滑作用,能降低切削区的温度,减少刀刃与工件的摩擦,从而减少切削过程的塑性变形,抑制积屑瘤和鳞刺的生长,对降低表面粗糙度有很大作用。
5)工件材质。
工件材料的硬度、塑性、韧性和导热性能等,对表面粗糙度有显著的影响。
工件材料太硬时,磨粒易钝化;太软时,砂轮易堵塞;韧性大和导热性能差的材料,使磨粒早期崩落,而破坏了微刃的等高性,因而均使表面粗糙度增高。
三、影响加工表面层物理机械性能的因素在切削加工中,工件由于受到切削力和切削热的作用,使表面层金属的物理机械性能产生变化,最主要的变化是表面层金属显微硬度的变化、金相组织的变化和残余应力的产生。
由于磨削加工时所产生的塑性变形和切削热,比刀刃切削时更严重,因而磨削加工后加工表面层上述3 项物理机械性能的变化会很大。
1、冷作硬化(1)金属的冷作硬化在机械加工过程中,因切削力作用产生的塑性变形,使晶格扭曲、畸变,晶粒间产生剪切滑移,晶粒被拉长和纤维化,甚至破碎,这些都会使表面层金属的硬度和强度提高,这种现象称为冷作硬化(或称为强化)。
表面层金属强化的结果,会增大金属变形的阻力,减小金属的塑性,金属的物理性质也会发生变化。
被冷作硬化的金属于高能位的不稳定状态,只要一有可能,金属的不稳定状态就要向比较稳定的状态转化,这种现象称为弱化。
弱化作用的大小,取决于温度的高低、温度持续时的长短和强化程度的大小。
由于金属在机械加工过程中同时受到力和热的作用,因此加工后表层金属的最后性质,取决于强化和弱化综合作用的结果。
评定冷作硬化的指标有3 项:即表层金属的显微硬度HV、硬化层深度h 和硬化程度N。
(2)影响冷作硬化的主要因素切削刃钝圆半径增大,对表层金属的挤压作用增强,塑性变形加剧,导致冷硬增强。
刀具后刀面磨损增大,后刀面与被加工表面的摩擦加剧,塑性变形增大,导致冷硬增强。
切削刃钝圆半径对加工硬化的影响切削速度增大,刀具与工件的作用时间缩短,使塑性变形扩展深度减小,冷硬层深度减小。
切削速度增大后,切削热在工件表面层上的作用时间也缩短了,将使冷硬程度增加。
进给量增大,切削力也增大,表层金属的塑性变形加剧,冷硬作用加强。
工件材料的塑性愈大,冷硬现象就愈严重。
2、表面层残余应力产生的原因是:加工时在切削力作用下,已加工表面层受拉应力作用,产生伸长塑性变形,表面积趋向增大,此时里层处于弹性变形状态下。
当切削力去除后,里层金属趋向复原,但受到已产生塑性变形的表面层的限制,恢复不到原状,因而在表面层产生残余压应力,里层则为拉应力与之相平衡。
3、表面层材料金相组织的变化(1)磨削烧伤。
当被磨工件表面层的温度达到相变温度以上时,表层金属发生金相组织的变化,使表层金属强度和硬度降低,并伴有残余应力产生,甚至出现微观裂纹,这种现象称为磨削烧伤。
在磨削淬火钢时,可能产生3 种烧伤。
回火烧伤。
如果磨削区的温度未超过淬火钢的相变温度,但已超过马氏体的转变温度,工件表层金属的回火马氏体组织将转变成硬度较低的回火组织(索氏体或托氏体),这种烧伤称为回火烧伤。
淬火烧伤。
如果磨削区温度超过了相变温度,再加上冷却液的急冷作用,表层金属发生二次淬火,使表层金属出现二次淬火马氏体组织,其硬度比原来的回火马氏体的高,在它的下层,因冷却较慢,出现了硬度比原先的回火马氏体低的回火组织(索氏体或托氏体),这种烧伤称为淬火烧伤。
退火烧伤。
如果削区温度超过了相变温度,而磨削区域又无冷却液进入,表层金属将产生退火组织,表面硬度将急剧下降,这种烧伤称为退火烧伤。
磨削热是造成磨削烧伤的根源,故改善磨削烧伤有两个途径:一是正确选择砂轮,合理选择切削用量,尽可能地减少磨削热的产生;二是改善冷却条件,尽量使产生的热量少传入工件。
(2)热塑性变形的影响。
表面层在切削热的作用下产生热膨胀,此时基体温度较低,因此表面层热膨胀受基体的限制产生热压缩应力。
当表面层的温度超过材料的弹性变形范围时,就会产生热塑性变形(在压应力作用下材料相对缩短)。
当切削过程结束,温度下降至与基体温度一致时,因为表面层已产生热塑性变形,但受到基体的限制产生了残余拉应力,里层则产生了压应力。
(3)金相组织变化的影响。
切削时产生的高温,会引起表面层的相变。
由于不同的金相组织有不同的密度,表面层金相变化的结果造成了体积的变化。
表面层体积膨胀时,因受到基体的限制,产生了压应力。
反之,表面层体积缩小,则产生拉应力。
各种金相组织大马氏体比重最小,奥氏体比重最大,磨削淬火钢时若表面层产生回火现象,马氏体转化成索氏体或屈氏体(这两种组织均为扩散度很高的珠光体),因体积缩小,表面层产生残余拉应力,里层产生残余压应力。
若表面层产生二次淬火现象,则表面层产生二次淬火马氏体,其体积比里层的回火组织大,因而表层产生压应力,里层产生拉应力。
(4)零件主要工作表面最终工序加工方法的选择。
选择零件主要工作表面最终工序加工方法,须考虑该零件主要工作表面的具体工作条件和可能的破坏形式。
在交变载荷作用下,机器零件表面上的局部微观裂纹,会因拉应力的作用使原生裂纹扩大,最后导致零件断裂。
从提高零件抵抗疲劳破坏的角度考虑,该表面最终工序应选择能在该表面产生残余压应力的加工方法。
(5)磨削裂纹的产生及防止。
当表面层的残余拉应力超过材料的强度极限时,零件表面就会产生裂纹,有的磨削裂纹也可能不在工件的外表面,而是在表面层下成为肉眼难以发现的缺陷。
裂纹的方向常与磨削方向垂直或成网状,裂纹的产生常与烧伤同时出现。
磨削裂纹的产生与材料及热处理工序有很大的关系,磨削硬质合金时,由于其脆性大,抗拉强度低以及导热性差,所以特别容易产生裂纹。
磨削含碳量高的淬火钢时,由于其晶界脆弱,也容易产生磨削裂纹。
工件在淬火后如果存在残余应力,则即使在正常的磨削条件下也可能会出现裂纹。
渗碳、渗氮时如果工艺不当,就会在表面层晶界面上析出脆性的碳化物、氮化物。
当磨削时,在热应力作用下就容易沿着这些组织发生脆性破坏,而出现网状裂纹。
由于磨削热是产生残余拉应力的根本原因,因此防止产生裂纹的途径,也在于降低磨削热以及改善其散热条件,前面所述的减轻表面热损伤的措施,均有利于避免产生表面残余拉应力和裂纹。
在磨削工序前后进行去除内应力的低温回火处理,亦能有效地减小表面层的拉应力,防止产生磨削裂纹。
四、提高加工表面质量的措施通过前面的分析,我们知道影响表面粗糙度的因素有切削条件(切削速度、进给量、切削液)、刀具(几何参数、切削刃形状、刀具材料、磨损情况)、工件材料及热处理、工艺系统刚度和机床精度等几个方面。
在了解了影响表面粗糙度的因素之后,我们必须根据需要降低加工表面的粗糙度,改善机械加工的表面质量。
提高加工表面质量的措施主要有:1、刀具方面为了减少残留面积,刀具应采用较大的刀尖圆弧半径、较小的副偏角或合适的修光刃或宽刃精刨刀、精车刀等。
选用与工件材料适应性好的刀具材料,避免使用磨损严重的刀具,这些均有利于减小表面粗糙度。
2、工件材料方面工件材料性质中,对加工表面粗糙度影响较大的是材料的塑性和金相组织。
对于塑性大的低碳钢、低合金钢材料,预先进行正火处理以降低塑性,切削加工后能得到较小的粗糙度。
工件材料应有适宜的金相组织(包括状态、晶粒度大小及分布)。