通用焊接工艺规程普通碳钢合金钢不锈钢铜管焊接
碳钢管道焊接工艺规程

碳钢管道焊接工艺规程公司内部编号:(GOOD-TMMT-MMUT-UUPTY-UUYY-DTTI-碳钢管道焊接工艺指导书1 范围本标准适用于工业管道和公用管道的碳钢类钢材的焊接施工。
2 规范性引用文件GB 50235-97 《工业金属管道工程施工及验收规范》GB 50236-98 《现场设备、工业管道焊接工程施工及验收规范》《焊工技术考核规程》3 先决条件3.1 材料3.1.1 母材进入现场的管材、管件等应符合相应标准和设计文件规定要求,并具有材料质量证明书或材质复验报告。
3.1.2 焊接材料(以下简称焊材)3.1.2.1 进入现场的焊材应符合相应标准和技术文件规定要求,并具有焊材质量证明书。
3.1.2.2 施工现场的焊材二级库已建立并正常运行。
焊材的管理按《焊接材料管理规范》规定要求执行。
3.2 主要设备及工具3.2.1 设备焊机等设备完好,性能可靠。
计量仪表正常,并经检定合格且有效。
3.2.2 工具角向磨光机、钢丝刷、凿子、榔头等焊缝清理与修磨工具配备齐全。
3.3 焊接工艺评定按相应规程、标准规定的要求已完成。
3.4 焊工按《锅炉压力容器焊工考试规则》规定要求,经考核具有相应的持证项目。
3.5 焊接环境3.5.1 施焊环境应符合下列要求:3.5.1.1 施焊环境温度应能保证焊件焊接时所需的足够温度和焊工操作技能不受影响;3.5.1.2 风速:手工电弧焊小于8m/s,气体保护焊小于2m/s;3.5.1.3 焊接电弧在1m范围内的相对湿度小于90%。
3.5.2 焊件表面潮湿、覆盖有冰雪,或在下雨、下雪、刮风期间,必须采取挡风、防雨、防雪、防寒和预加热等有效措施。
无保护措施,不得进行焊接。
4 焊接工艺流程焊接工艺流程见图1。
5 工艺要点5.1 坡口加工5.1.1 管道的坡口形式和坡口尺寸应按设计文件或焊接工艺规定要求进行。
5.1.2 不等厚对接焊件坡口加工应符合《工业金属管道工程施工及验收规范》规定要求。
焊接工艺通用工艺守则

1.主题内容与适用范围1.1本标准规定了压力容器主要承压元件焊条电弧焊、埋弧焊以及焊缝返修的基本要求和操作规则,常压容器的焊接可参照执行。
1.2 本标准适用于碳素钢、低合金钢、奥氏体不锈钢制D1、D2类压力容器的焊接(不包括有色金属的焊接)。
1.3本守则如与设计文件相矛盾之处,应以设计文件为准。
1.4焊接时,除符合GB150、GB151、JB4710、JB4731、《固定式压力容器安全技术监察规程》和本守则外,还应符合图样的规定。
1.5本守则中引用的法规、标准、守则等如经修改,应以新的版本为准。
2.引用标准TSGR0004《固定式压力容器安全技术监察规程》GB150 《压力容器》GB151 《管壳式换热器》JB4710 《钢制塔式容器》JB4731 《钢制卧式容器》HG20584 《钢制化工容器制造技术要求》NB/T47015《压力容器焊接规程》NB/T47014《承压设备焊接工艺评定》NB/T47016《承压设备产品焊接试件的力学性能检验》TSG Z6002—2010《特种设备焊接操作人员考核细则》GB/T21433《不锈钢压力容器晶间腐蚀敏感性试验》HG20583《钢制化工容器结构设计规定》GB985《气焊、手工电弧焊及气体保护焊缝坡口的基本形式及尺寸》GB986《埋弧焊焊缝坡口的基本形式和尺寸》3. 焊接材料3.1 焊接材料包括焊条、焊丝、焊剂、钢带、气体、电极和衬垫等。
3.2 焊接材料应有产品质量证明书,并符合相应标准的规定,按照材料验收程序进行验收与复验,合格后方可使用。
3.3 焊条药皮应均匀、表面无气孔、没有明显的裂纹、脱皮现象,并存放在干燥的仓库内,要求温度≥5℃、相对湿度≤60%,使用前对焊条按规定温度应进行烘干和保温,烘干后的焊条应放在保温筒内,随用随取,低氢型焊条一般在常温下4h后应重新烘干,烘干次数不宜超过三次,对于焊工退回的焊条,库管员要做好标识,并按牌号、规格、代号存放,使用前应进行烘干,对于二次烘干的焊条应在焊条夹持端的截面用记号笔涂黄色标记,对于第三次烘干的焊条应在焊条夹持端的截面用记号笔涂红色标记。
通用焊接工艺规程(普通碳钢、合金钢、不锈钢、铜管焊接)

通用焊接工艺规范1 碳素钢、合金钢及不锈钢的焊接1.1焊前准备1.1.1 焊缝的坡口形式和尺寸应符合设计文件的规定,当无规定时,符合本规范附录A.0.1的规定.1.1.2 焊件的坡口加工宜采用机械方法,也可采用等离子弧、氧乙炔焰等热加工方法,在采用热加工方法加工坡口后,必须除去坡口表面的氧化皮、熔渣及影响接头质量的表面层,并应将凹凸不平处打磨平整。
1.1.3 焊件组焊前应将坡口及其两侧表面不小于20 mm范围内的油、漆、垢、锈、毛刺及镀锌层等清除干净,不得有裂纹、夹层、加工损伤、毛刺及火焰切割熔渣等缺陷。
油污清理方法如下,首先用丙酮或四氯化碳等有机溶剂擦洗,然后用不锈钢丝刷清理至露出金属光泽,使用的钢丝刷应定期进行脱脂处理。
1.1.4 管子或管件、筒体对接焊缝组对时,内壁应齐平,内壁错边量不宜超过管壁厚度的10%,且不应大于2mm;1.1.5 焊缝的设臵应避开应力集中区,便于焊接和热处理,并应符合下列规定:(1)钢板卷筒或设备、容器的筒节与筒节、筒节与封头组对时,相邻两纵向焊缝间的距离应大于壁厚的3倍,且不应小于100 mm,同一筒节上两相邻纵缝间的距离不应小于200 mm;(2)除焊接及成型管件外的其他管子对接焊缝的中心到管子弯曲起点的距离不应小于管子外径,且不应小于l00 mm;管子对接焊缝与支、吊架边缘之间的距离不应小于50 mm。
同一直管段上两对接焊缝中心面间的距离:当公称直径大于或等于150mm时不应小于150mm;公称直径小于150mm时不应小于管子外径;(3)不宜在焊缝及其边缘上开孔。
(4)不锈钢焊件焊接部位两侧各l00 mm范围内,在施焊前应采取防止焊接飞溅物粘污焊件表面的措施:可将石棉置于焊接部位两侧等。
1.1.6 焊条、焊丝在使用前应按规定进行烘干、保温,并应在使用过程中保持干燥。
焊丝使用前应清除其表面的油污、锈蚀等。
常用焊材烘干温度及保持时间见表4。
表4 常用焊材烘干温度及保持时间接上表:1.2焊接工艺要求1.2.1 碳素钢及合金钢焊接材料的选用,应符合设计文件的规定,当无规定时,符合本规范附录B第 B.0.1条及第B.0.2条的规定。
4碳钢和不锈钢管子焊接工艺规范
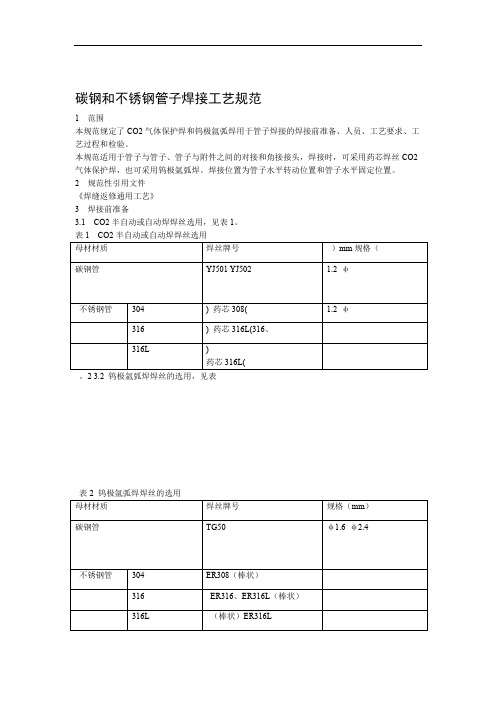
碳钢和不锈钢管子焊接工艺规范1 范围本规范规定了CO2气体保护焊和钨极氩弧焊用于管子焊接的焊接前准备、人员、工艺要求、工艺过程和检验。
本规范适用于管子与管子、管子与附件之间的对接和角接接头,焊接时,可采用药芯焊丝CO2气体保护焊,也可采用钨极氩弧焊。
焊接位置为管子水平转动位置和管子水平固定位置。
2 规范性引用文件《焊缝返修通用工艺》3 焊接前准备3.1 CO2半自动或自动焊焊丝选用,见表1。
表1 CO2半自动或自动焊焊丝选用。
2 3.2 钨极氩弧焊焊丝的选用,见表3.3 保护气体无论是药芯焊丝CO2气体保护焊所用的CO2,还是钨极氩弧焊所用的纯Ar气体,均应符合气体质量使用标准,其纯度达99.9 %。
3.4 焊接设备使用的焊机应严格进行定期检测维修,确保良好的操作性能。
3.5 焊接坡口3.5.1 壁厚t≤2mm时,管子对接拼缝均不开坡口焊接,见图1。
t图1的管子对接拼缝,均应开坡口,见图2mm2。
壁厚3.5.2 t>60°t图2焊前清洁3.63.6.1 焊工必须对焊缝坡口面和坡口两侧各宽20mm范围内(角接焊缝在焊接面两侧各宽20mm 范围内)作清理,并去除油、锈等污物。
对于碳钢管的锈蚀,应用钢刷打磨除锈。
不锈钢管应用丙酮进行清理。
3.6.23.6.3 坡口加工残留毛刺应除去,并应重新清理。
4 人员凡从事该工艺焊接的焊工,必须经过船级社资格认可考试,考试合格并经船级社认可后,方能参与相应等级项目的焊接。
5 工艺要求5.1 装配要求5.1.1 装配工在安装管子对接时,首先要检查管子接口同心度,防止安装错边。
5.1.2 管子对接定位可选用定位“马”固定,或在焊缝内作定位焊固定。
5.1.3 装配间隙,见表3。
表3 装配间隙弧焊(TIG焊)打底。
5.3 船上安装要求单面焊双面成型的管子拼缝,因无法进行充气保护,焊接中应仔细观察熔池,以确保背面焊缝质量。
对于不锈钢管,焊后,管内要作钝化处理。
5.4 焊接参数为确保管子的焊接质量,焊接时应参照表4的焊接参数进行。
不锈钢焊接工艺规程1
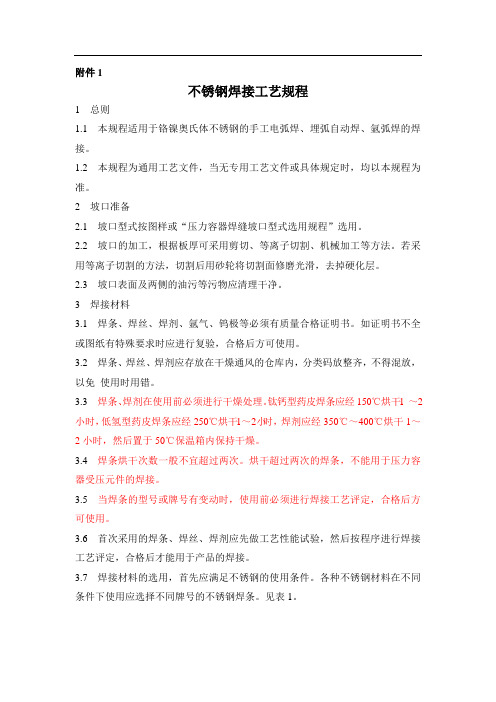
附件1不锈钢焊接工艺规程1 总则1.1 本规程适用于铬镍奥氏体不锈钢的手工电弧焊、埋弧自动焊、氩弧焊的焊接。
1.2 本规程为通用工艺文件,当无专用工艺文件或具体规定时,均以本规程为准。
2 坡口准备2.1 坡口型式按图样或“压力容器焊缝坡口型式选用规程”选用。
2.2 坡口的加工,根据板厚可采用剪切、等离子切割、机械加工等方法。
若采用等离子切割的方法,切割后用砂轮将切割面修磨光滑,去掉硬化层。
2.3 坡口表面及两侧的油污等污物应清理干净。
3 焊接材料3.1 焊条、焊丝、焊剂、氩气、钨极等必须有质量合格证明书。
如证明书不全或图纸有特殊要求时应进行复验,合格后方可使用。
3.2 焊条、焊丝、焊剂应存放在干燥通风的仓库内,分类码放整齐,不得混放,以免使用时用错。
3.3 焊条、焊剂在使用前必须进行干燥处理。
钛钙型药皮焊条应经150℃烘干1~ 2小时,低氢型药皮焊条应经250℃烘干1~ 2小时,焊剂应经350℃~400℃烘干1~2小时,然后置于50℃保温箱内保持干燥。
3.4 焊条烘干次数一般不宜超过两次。
烘干超过两次的焊条,不能用于压力容器受压元件的焊接。
3.5 当焊条的型号或牌号有变动时,使用前必须进行焊接工艺评定,合格后方可使用。
3.6 首次采用的焊条、焊丝、焊剂应先做工艺性能试验,然后按程序进行焊接工艺评定,合格后才能用于产品的焊接。
3.7 焊接材料的选用,首先应满足不锈钢的使用条件。
各种不锈钢材料在不同条件下使用应选择不同牌号的不锈钢焊条。
见表1。
表1 焊接奥氏体不锈钢选用焊条举例3.8 埋弧自动焊、氩弧焊用的焊丝,其成分与性能应与母材相近。
4 焊工4.1 凡参加铬镍奥氏体不锈钢焊接的焊工,应熟悉不锈钢焊接的要领,并经焊工考试合格。
焊工考试按国家劳动人事部颁发的《锅炉压力容器焊工考试规则》进行。
4.2 焊工所施焊的项目必须与焊工合格证的项目相符。
禁止无项操作。
4.3 压力容器主体焊缝、重要接管及人孔处的焊缝,焊工必须遵照焊接工艺卡的要求,焊后在所焊部位附近留有标记,并认真填写施焊记录。
焊接通用规程

一、气焊通用工艺规程1. 主题内容和适用范围本标准规定了气焊操作规程。
本标准适用于本公司金属结构件的气焊。
2. 引用标准YB/JQ10/15 《钢铁企业制造通用技术条件焊接结构件》。
3. 准备工作3.1 熟悉图纸和工艺要求,了解材质、规格、焊肉等工艺规程。
3.2 准备好氧、乙炔气。
3.2.1氧气含量不低于99.2%,水份不超过10ml/瓶;乙炔的杂质符合标准,磷化氢≤0.08%硫化物≤0.15,电石出气率≥235升/公斤。
3.2.2 使用临时乙炔发生器时。
发生器至少离火源10米,取暖设备1米,发生器内要保持足够的干净水,水封回火防止器要保持一定的水位。
3.2.3 发生器内用的电石按规定的一次加入量添加,块度为50—80mm,不得加电石粉末。
3.2.4氧气瓶严禁沾油,且装表前要放气吹去接下来头处的尘土杂物。
移动气瓶应避免撞击,禁止用起重机吊运。
3.3 检查焊炬、管带及氧气表、乙炔表是否正常,连接处是否紧密。
3.4 清理操作场地,检查焊件的装配质量。
焊缝间隙应均匀一致,符合要求,清除干净焊缝两侧10mm内的铁锈、油污,焊缝表面应进行打磨。
4. 气焊工艺4.1 根据工艺要求选用焊丝、焊剂,焊丝不允许有油污和铁锈。
对无要求的,可根据焊件的材质和板厚选用,焊丝直径可参考表1。
表1 焊丝直径与焊件厚度的关系4.2 根据焊件厚度选择焊咀型号工艺参数(表2,表3)4.3 根据焊件材质选择火焰类型。
4.3.1 碳化焰用于气焊高碳钢、高速钢、硬质合金、铝。
青铜及铸铁。
4.3.2 中性焰用于气焊低碳钢、低合金钢、高铬钢、不锈钢、紫铜、锡青铜、铝及铝合金、镁合金。
4.3.3 氧化焰用于气焊黄铜、锰钢。
镀锌铁皮等。
4.4 气焊时焊咀与工件之间要倾斜一定的角度,大小取决于板厚(表4)。
对于熔点高,导热性好的材料,角度要大些;始焊时为迅速加热焊件,应用80o—90o的角,然后再逐渐减小,收尾时应减小倾角,焊咀提高。
表4 焊咀倾角4.5 焊时先将金属加热到熔融状态,再填充焊丝,焊丝与焊件表面倾斜20 o—40o,且焊时焊咀和焊丝要交叉均匀摆动,以避免焊接缺陷。
通用焊接工艺规程(普通碳钢、合金钢、不锈钢、铜管焊接)

通用焊接工艺规范1 碳素钢、合金钢及不锈钢的焊接1.1焊前准备1.1.1 焊缝的坡口形式和尺寸应符合设计文件的规定,当无规定时,符合本规范附录A.0.1的规定.1.1.2 焊件的坡口加工宜采用机械方法,也可采用等离子弧、氧乙炔焰等热加工方法,在采用热加工方法加工坡口后,必须除去坡口表面的氧化皮、熔渣及影响接头质量的表面层,并应将凹凸不平处打磨平整。
1.1.3 焊件组焊前应将坡口及其两侧表面不小于20 mm范围内的油、漆、垢、锈、毛刺及镀锌层等清除干净,不得有裂纹、夹层、加工损伤、毛刺及火焰切割熔渣等缺陷。
油污清理方法如下,首先用丙酮或四氯化碳等有机溶剂擦洗,然后用不锈钢丝刷清理至露出金属光泽,使用的钢丝刷应定期进行脱脂处理。
1.1.4 管子或管件、筒体对接焊缝组对时,内壁应齐平,内壁错边量不宜超过管壁厚度的10%,且不应大于2mm;1.1.5 焊缝的设臵应避开应力集中区,便于焊接和热处理,并应符合下列规定:(1)钢板卷筒或设备、容器的筒节与筒节、筒节与封头组对时,相邻两纵向焊缝间的距离应大于壁厚的3倍,且不应小于100 mm,同一筒节上两相邻纵缝间的距离不应小于200 mm;(2)除焊接及成型管件外的其他管子对接焊缝的中心到管子弯曲起点的距离不应小于管子外径,且不应小于l00 mm;管子对接焊缝与支、吊架边缘之间的距离不应小于50 mm。
同一直管段上两对接焊缝中心面间的距离:当公称直径大于或等于150mm时不应小于150mm;公称直径小于150mm时不应小于管子外径;(3)不宜在焊缝及其边缘上开孔。
(4)不锈钢焊件焊接部位两侧各l00 mm范围内,在施焊前应采取防止焊接飞溅物粘污焊件表面的措施:可将石棉置于焊接部位两侧等。
1.1.6 焊条、焊丝在使用前应按规定进行烘干、保温,并应在使用过程中保持干燥。
焊丝使用前应清除其表面的油污、锈蚀等。
常用焊材烘干温度及保持时间见表4。
表4 常用焊材烘干温度及保持时间接上表:1.2焊接工艺要求1.2.1 碳素钢及合金钢焊接材料的选用,应符合设计文件的规定,当无规定时,符合本规范附录B第 B.0.1条及第B.0.2条的规定。
焊接通用工艺守则

焊接工艺守则GY—CT—G22编制:审核:批准:XXXXXXXXXX有限公司1.主题内容和适用范围本守则规定了焊接件的焊前准备、组装和各种焊接方法技术规范本守则适用于公司消防车系列产品结构件焊接,凡产品图纸或技术文件中无特殊要求时,手工电弧焊、半自动电弧焊、电阻焊、气焊均按本守则执行。
2.引用标准JB/T5943-91 工程机械焊接件通用技术条件JB/T50077—96 气体保护电弧焊用碳钢、低合金钢焊丝产品质量分等GB985—88 气焊、手工电弧焊及气体保护焊焊缝坡口的基本形式和尺寸GB324—88 焊缝符号表示法3.一般规定3。
1 焊工考核焊工必须持证上岗并经人事部及有关部门考查合格后才能焊接产品,并定期考查。
3.1。
1 焊工应有较强的识图能力,能准确地找出图样上的焊接部位.焊接符号识别见附录Ⅰ;3.1。
2焊工应具有一定的电工知识、金属材料知识、焊接结构的装配知识。
3.1。
3焊工应具有各种位置焊接的熟练操作技能。
并能识别各种焊接缺陷,找出原因,采取相应纠正措施.3.1.4焊工应有一定的安全意识,特别是进行气焊、气割时,必须正确使用设备.3.2 材料公司常用被焊材料有普通炭素钢、优质碳素钢(只限45钢以下)、低合金结构钢(16Mn 15MnVN等)、不锈钢(1Cr18Ni9Ti Sus304N1 1Cr13)、铝合金钢板、铜管.3。
2.1进厂原材料(板材、型材、焊接材料)的钢号、规格、尺寸应符合有关国家标准、图样和工艺要求,不符合要求的,应按制度办理代用手续.3。
2。
2 进厂原材料必须经质检部门检查合格后,方可投入生产。
3。
2。
3焊接材料选用原则:碳钢和低合金钢按等强度原则选用,不锈钢和有色金属按等成分原则选用。
3。
2.4新研制或公司从末使用过的材料(含焊接材料),需经技术部门进行焊接工艺评定,经主管领导或主管设计认可后,方能投入生产。
3.2。
5 用于钢结构焊接的焊条,购买、保管、贮存、使用均应按JB3223《焊条质量管理规程》的规定执行,3.2。
碳钢、不锈钢电弧焊焊接工艺规范

Q/GRSX—JW—002—2014碳钢、不锈钢电弧焊焊接工艺规范类别姓名日期拟制审核批准版本受控号Q/GRSX—JW—002—2014南京国睿三信机械装备制造有限公司Q/GRSX—JW—002—20142013年06月05日相关变更内容及细节日期版本变更章节变更内容备注2014年6月5日A创建创建Q/GRSX—JW—002—2014碳钢、不锈钢电弧焊焊接工艺规范1、范围本标准规定了碳钢、不锈钢电弧焊焊接操作规程。
本工艺规范适用于板厚为3mm-40mm的所有牌号的碳钢不锈钢材料焊接。
2、引用文件Q/GRSX-QA(HJ)-2014焊接质量手册GJB481-1988焊接质量控制要求QZ/AL2025-2012钢熔化焊生产外协通用要求(十四所)GB/T324-2008焊缝符号表示法GB/T8110-2008气体保护电弧焊用碳钢、低合金钢焊丝GB/T19418-2003钢的弧焊接头缺陷质量分级指南GB/T10045-2001碳钢药芯焊丝GBT985.1-2008气焊、焊条电弧焊、气体保护焊和高能束焊的推荐坡口GBT15169-2003钢熔化焊焊工技能评定GBT19869-1/ISO15614-1钢、镍及镍合金的焊接工艺评定试验3、一般要求3.1、焊接设计对焊缝的设计,应能保证易于施焊。
接头形式和坡口尺寸要求根据GBT985.1-2008《气焊、焊条电弧焊、气体保护焊和高能束焊的推荐坡口》。
3.2、焊工3.2.1焊工必须是技校焊接专业毕业或具有同等学历,经过焊接理论和操作培训,按规定GBT15169-2003《钢熔化焊焊工技能评定》考试合格并持有资格的焊工考试委员会的有效合格证书或按《特种设备焊接操作人员考核细则》要求考试合格,具备相应的焊接资格.3.2.2焊工只能在考试合格项范围内施焊。
3.2.3焊工要严格按焊接工艺规程或焊接作业指导书施焊,自检合格后在焊缝附近标明焊工钢印号或进行标记(如果要求)。
3.2.4持证焊工中断焊接工作在六个月以上,重新担任焊接工作时,必须重新考试。
通用焊接工艺规程(普通碳钢、合金钢、不锈钢、铜管焊接)
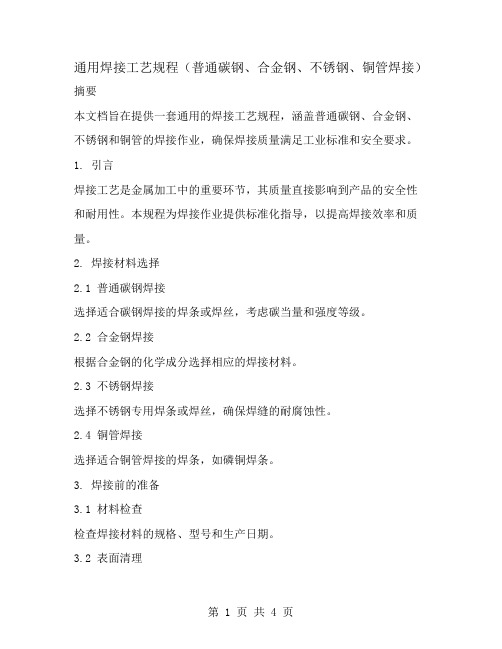
通用焊接工艺规程(普通碳钢、合金钢、不锈钢、铜管焊接)摘要本文档旨在提供一套通用的焊接工艺规程,涵盖普通碳钢、合金钢、不锈钢和铜管的焊接作业,确保焊接质量满足工业标准和安全要求。
1. 引言焊接工艺是金属加工中的重要环节,其质量直接影响到产品的安全性和耐用性。
本规程为焊接作业提供标准化指导,以提高焊接效率和质量。
2. 焊接材料选择2.1 普通碳钢焊接选择适合碳钢焊接的焊条或焊丝,考虑碳当量和强度等级。
2.2 合金钢焊接根据合金钢的化学成分选择相应的焊接材料。
2.3 不锈钢焊接选择不锈钢专用焊条或焊丝,确保焊缝的耐腐蚀性。
2.4 铜管焊接选择适合铜管焊接的焊条,如磷铜焊条。
3. 焊接前的准备3.1 材料检查检查焊接材料的规格、型号和生产日期。
3.2 表面清理清除焊接区域的油污、锈蚀和杂质。
3.3 焊接环境确保焊接环境符合安全标准,通风良好。
4. 焊接工艺参数4.1 电流和电压根据焊接材料的厚度和类型调整电流和电压。
4.2 焊接速度控制焊接速度,防止焊缝过热或不均匀。
4.3 焊接角度保持正确的焊接角度,确保焊缝质量。
5. 焊接操作步骤5.1 定位对接焊接材料,确保接缝对齐。
5.2 预热对于合金钢和不锈钢,进行适当的预热处理。
5.3 焊接按照既定的工艺参数进行焊接。
5.4 后热处理对于某些合金钢和不锈钢焊接,进行后热处理以消除应力。
6. 焊接质量控制6.1 外观检查检查焊缝的外观,确保无裂纹、气孔等缺陷。
6.2 无损检测根据需要进行射线检测、超声波检测等无损检测。
6.3 力学性能测试对焊缝进行拉伸、冲击等力学性能测试。
7. 安全与环境保护7.1 安全防护焊接操作人员应穿戴适当的个人防护装备。
7.2 环境控制控制焊接烟尘和有害气体的排放。
7.3 应急预案制定焊接事故的应急预案。
8. 焊接工艺的持续改进8.1 工艺反馈收集焊接过程中的问题和反馈。
8.2 工艺优化根据反馈结果不断优化焊接工艺。
8.3 技术培训定期对焊接操作人员进行技术和安全培训。
通用焊接工艺规范
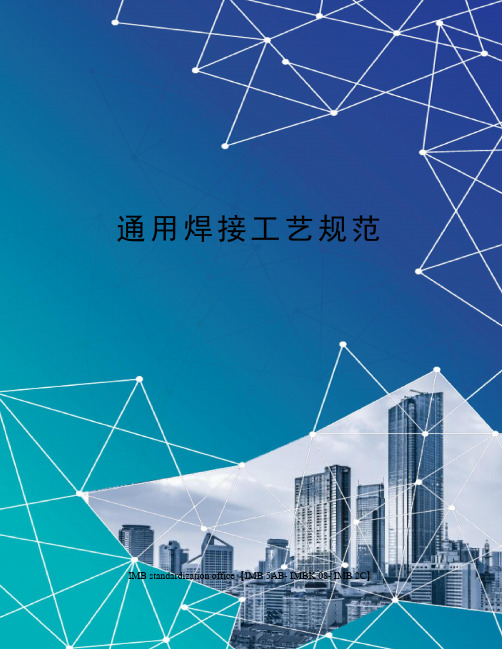
通用焊接工艺规范 IMB standardization office【IMB 5AB- IMBK 08- IMB 2C】通用焊接工艺规范1范围本规范规定了钢结构产品焊接的要求、常用焊接方法、工艺参数及检验等。
本规范适用于钢结构产品的焊接件,其它产品的焊接件可参照执行。
2?规范性引用文件本规范引用下列文件中的条款而成为本规范的条款。
GB/T19867 电弧焊焊接工艺规程GB/T985 气焊、手工电弧焊及气体保护焊焊缝坡口的基本型式与尺寸GB/T3323? 钢融化焊对接接头射线照相和质量分级GB 11345-88钢焊缝手工超声波探伤方法和探伤结果分级GB 50205-2001钢结构工程施工质量验收规范GB/T19804焊接结构的一般尺寸公差和形位公差JB/T9186二氧化碳气体保护焊工艺规程JB/T3223 焊接材料质量管理规程JB/T5943工程机械焊接件通用技术条件JB/T6046碳钢、低合金钢焊接构件焊后热处理方法JB/T6061焊缝磁粉检验方法和缺陷磁痕的分级Q/XZ?GY022桥梁构件产品焊接工艺通用规范TB 10212 铁路钢桥制造规范3.要求焊接件的原材料(钢板、型钢、钢筋等)和焊接材料(焊条、焊丝、焊剂、保护气体等)进厂时,应经质检部门按有关标准检验合格后方可入库和使用。
焊接件材料的钢号、规格尺寸应符合设计图样要求。
焊接材料的使用及管理应符合JB/T?3223的规定。
钢材在下料前的形状公差应符合国家或行业标准的有关规定,否则应予矫正,使之达到要求。
矫正时,其伤痕深度:钢板应不大于,,型钢应不大于1mm。
焊接零件在下料后及焊装前的未注公差(一般公差)下料零件未注公差尺寸的极限偏差应符合TB 10212中的有关规定。
下料零件的未注形位公差应符合JB/T?5943中的有关规定。
焊前要求焊接前的零件应经检验合格后方可焊接。
焊接前应清除焊接区域的铁锈、氧化皮、油污、油漆等杂质,使焊接零件表面露出金属光泽。
通用焊接工艺规程
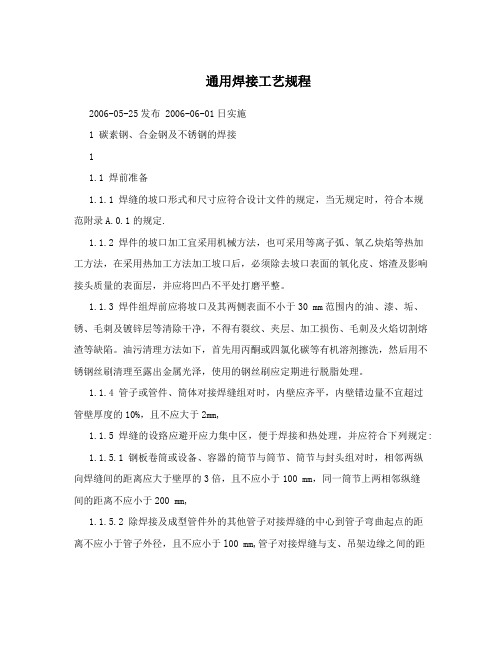
通用焊接工艺规程2006-05-25发布 2006-06-01日实施1 碳素钢、合金钢及不锈钢的焊接11.1 焊前准备1.1.1 焊缝的坡口形式和尺寸应符合设计文件的规定,当无规定时,符合本规范附录A.0.1的规定.1.1.2 焊件的坡口加工宜采用机械方法,也可采用等离子弧、氧乙炔焰等热加工方法,在采用热加工方法加工坡口后,必须除去坡口表面的氧化皮、熔渣及影响接头质量的表面层,并应将凹凸不平处打磨平整。
1.1.3 焊件组焊前应将坡口及其两侧表面不小于30 mm范围内的油、漆、垢、锈、毛刺及镀锌层等清除干净,不得有裂纹、夹层、加工损伤、毛刺及火焰切割熔渣等缺陷。
油污清理方法如下,首先用丙酮或四氯化碳等有机溶剂擦洗,然后用不锈钢丝刷清理至露出金属光泽,使用的钢丝刷应定期进行脱脂处理。
1.1.4 管子或管件、筒体对接焊缝组对时,内壁应齐平,内壁错边量不宜超过管壁厚度的10%,且不应大于2mm,1.1.5 焊缝的设臵应避开应力集中区,便于焊接和热处理,并应符合下列规定:1.1.5.1 钢板卷筒或设备、容器的筒节与筒节、筒节与封头组对时,相邻两纵向焊缝间的距离应大于壁厚的3倍,且不应小于100 mm,同一筒节上两相邻纵缝间的距离不应小于200 mm,1.1.5.2 除焊接及成型管件外的其他管子对接焊缝的中心到管子弯曲起点的距离不应小于管子外径,且不应小于l00 mm,管子对接焊缝与支、吊架边缘之间的距离不应小于50 mm。
同一直管段上两对接焊缝中心面间的距离:当公称直径大于或等于150mm时不应小于150mm,公称直径小于150mm时不应小于管子外径,1.1.5.3 不宜在焊缝及其边缘上开孔。
1.1.5 不锈钢焊件焊接部位两侧各l00 mm范围内,在施焊前应采取防止焊接飞溅物沾污焊件表面的措施:可将石棉臵于焊接部位两侧等。
21.1.6 焊条、焊丝在使用前应按规定进行烘干、保温,并应在使用过程中保持干燥。
焊丝使用前应清除其表面的油污、锈蚀等。
9碳钢和不锈钢管子的焊接工艺规范

碳钢和不锈钢管子的焊接工艺规范1.范围本工艺规定了CO2气体保护焊和钨极氩弧焊用于管子焊接的焊前准备、人员、工艺要求、工艺过程和检验。
本工艺适用于管子与管子、管子与附件之间的对接和角接接头,焊接时,可采用纯CO2气体或CO2+Ar混合气体的CO2半自动或自动焊接,也可采用钨极氩弧焊接。
2.一般要求2.1人员凡从事管子焊接的焊工,必须经过船级社资格认可考试,考试合格后,并经船级社认可,方能参与相应等级项目的焊接。
2.2材料无论是CO2焊所用的CO2气体、CO2+Ar混合气体,还是钨极氩弧焊所用的纯Ar气体,均应符合气体质量标准,氩气纯度应达到99.9%。
2.3环境为确保焊接质量,应对焊接场所进行保护,防风、防湿、防严寒。
如焊接过程中遇到刮风或下雨,应采取有效的防风、防雨措施或停止作业。
2.4焊接设备使用的焊机必须保持有效的工作状态,并应严格的进行定期检测和维修,确保焊机有良好的操作性能。
3.焊接3.1焊前准备3.1.1坡口形式3.1.1.1 壁厚t≤2mm时,管子对接拼缝均不开坡口焊接,见图1图 13.1.1.2壁厚t>2mm时的管子对接缝,均应开坡口焊接,见图2图 23.1.2焊前清洁3.1.2.1焊工必须对焊缝坡口两侧各宽20mm范围内(角焊缝在焊接面两侧各宽20mm范围内)作清理,去除加工残留毛刺、油污、铁锈等污物。
3.1.2.2对于钢管的锈蚀,应用砂轮或钢丝刷清理,直至露出金属光泽。
不锈钢管应用丙酮进行清理。
3.1.3焊前装配与检查3.1.3.1装配工在安装管子对接时,首先要检查管子接口同心度,防止安装错边。
3.1.3.2管子对接定位可选用定位“马”固定,或在焊缝内作定位焊固定。
3.2.1不锈钢管氩弧焊打底层焊接3.2.1.1焊前充气焊前先用铝箔胶带对所焊管子接缝两端面及坡口面封住(对于较长管子采用海绵、泡沫、可溶纸等工具做成堵板,设置于距离焊缝150~200mm的两侧形成一个气室)。
管子一端充氩气,另一端开一个5mm的小孔排空气,等气管内空气排尽并被氩气充满后,方可进行焊接。
碳钢管道焊接工艺规程
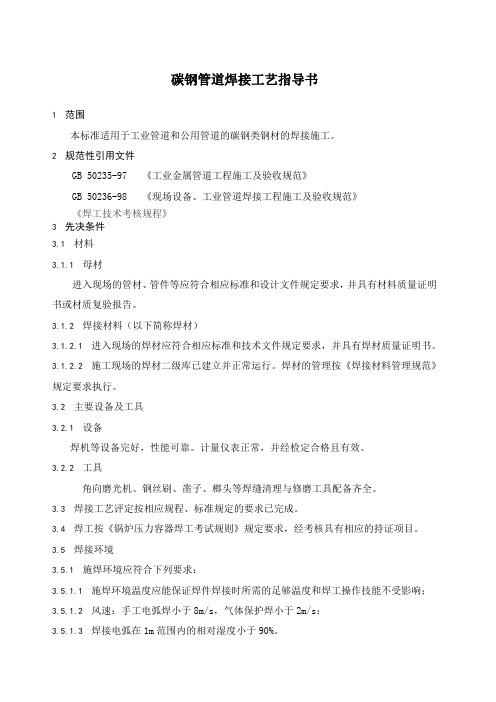
碳钢管道焊接工艺指导书1 范围本标准适用于工业管道和公用管道的碳钢类钢材的焊接施工。
2 规范性引用文件GB 50235-97 《工业金属管道工程施工及验收规范》GB 50236-98 《现场设备、工业管道焊接工程施工及验收规范》《焊工技术考核规程》3 先决条件3.1 材料3.1.1 母材进入现场的管材、管件等应符合相应标准和设计文件规定要求,并具有材料质量证明书或材质复验报告。
3.1.2 焊接材料(以下简称焊材)3.1.2.1 进入现场的焊材应符合相应标准和技术文件规定要求,并具有焊材质量证明书。
3.1.2.2 施工现场的焊材二级库已建立并正常运行。
焊材的管理按《焊接材料管理规范》规定要求执行。
3.2 主要设备及工具3.2.1 设备焊机等设备完好,性能可靠。
计量仪表正常,并经检定合格且有效。
3.2.2 工具角向磨光机、钢丝刷、凿子、榔头等焊缝清理与修磨工具配备齐全。
3.3 焊接工艺评定按相应规程、标准规定的要求已完成。
3.4 焊工按《锅炉压力容器焊工考试规则》规定要求,经考核具有相应的持证项目。
3.5 焊接环境3.5.1 施焊环境应符合下列要求:3.5.1.1 施焊环境温度应能保证焊件焊接时所需的足够温度和焊工操作技能不受影响;3.5.1.2 风速:手工电弧焊小于8m/s,气体保护焊小于2m/s;3.5.1.3 焊接电弧在1m范围内的相对湿度小于90%。
3.5.2 焊件表面潮湿、覆盖有冰雪,或在下雨、下雪、刮风期间,必须采取挡风、防雨、防雪、防寒和预加热等有效措施。
无保护措施,不得进行焊接。
4 焊接工艺流程 焊接工艺流程见图1。
焊接工艺流程图5 工艺要点5.1 坡口加工 5.1.1 管道的坡口形式和坡口尺寸应按设计文件或焊接工艺规定要求进行。
5.1.2 不等厚对接焊件坡口加工应符合《工业金属管道工程施工及验收规范》规定要求。
5.1.3 坡口加工宜采用机械方法,也可采用等离子切割、氧乙炔切割等热加工方法。
碳钢管道焊接通用工艺.doc
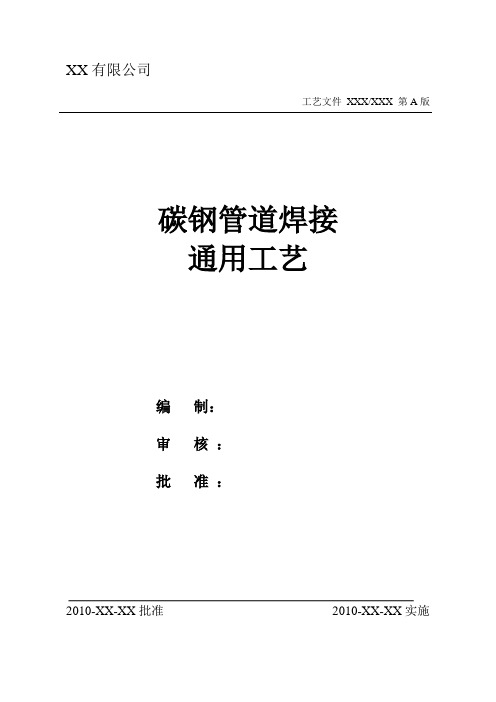
XX有限公司工艺文件XXX/XXX 第A版碳钢管道焊接通用工艺编制:审核:批准:2010-XX-XX批准2010-XX-XX实施更改状态表1.适用范围本工艺标准适用于碳钢类管材采用氩弧焊和手工电弧焊的焊接施工。
2.施工准备2.1材料要求2.1.1施工现场应配有符合要求的固定焊条库或流动焊条库。
2.1.2焊材必须具有质量证明书或材质合格证,焊材的保管、烘干、发放、回收严格按《压力管道安装质量保证手册》中有关规定执行,焊条的烘干工艺按生2.1.3焊丝使用前,应除去表面的油脂、锈等杂物。
2.1.4保温材料性能应符合预热及其热处理要求。
2.2机具要求2.2.1焊机为直流焊机,性能安全可靠,双表指示灵敏,且在校准周期内。
2.2.2预热及热处理的设备完好,性能可靠,检测仪表在校准周期内,且符合《压力管道质保手册》中的计量要求。
2.2.3焊工所用的焊条保温筒,刨锤、钢丝刷等工具齐全。
2.3作业条件2.3.1人员资格焊工必须持有《锅炉压力容器焊工合格证》,且具有施焊所需相应合格项目。
2.3.2环境条件施焊前应确认环境符合下列要求A)风速:手弧焊小于8m/s;氩弧焊小于2m/s;B)相对湿度:相对湿度小于90%;C)环境温度:当环境温度小于0℃时,对不预热的管道焊接前应在始焊处预热15℃以上;对焊接工艺要求预热的管道焊接前按要求进行预热,当环境温度低于-20℃时,必须采取保暖缓冷措施。
3. 焊接3.1 焊接施工程序,见图1。
带“*”者为当有要求时图13.2 坡口要求A ) 壁厚小于等于20mm,坡口形式及尺寸见图2。
2返修图3C)组对时质量要求内壁整齐,其错边量不宜超过壁厚的10%,且不大于2mm。
3.3焊接方法A)管径DN≤50mm碳钢管焊口采用氩弧焊进行焊接。
B)管径DN>50mm碳钢管焊口宜用氩弧打底,手工电弧焊盖面;若用手工电弧焊打底则应保证打底焊道的质量。
C)承插或角焊缝采用手工电弧焊进行焊接。
3.4点焊点焊方式为过桥方式,其工艺和焊材与正式焊接工艺相同,点焊数为2~5点,焊点厚度为70%壁厚且不大于6mrn。
铜的焊接工艺规程

铜及铜合金的焊接工艺钢与铜的焊接工艺。
钢与铜及铜合金焊接时的主要困难是在焊缝及熔合区易产生裂纹。
实践证实,为了保证焊缝具有足够高的抗裂性能,焊缝中铁的质量分数以控制在10%~43%为宜。
⑴焊接方法及焊接材料低碳钢与铜及铜合金焊接时,可以分别采用手弧焊、埋弧焊和钨极氩弧焊。
低碳钢与纯铜焊接时采用纯铜作为填充金属材料,如焊条TCu(T107);钨极氩弧焊时,采用硅锰青铜QSi3-1焊丝。
低碳钢与硅青铜、铝青铜焊接时,可采用铝青铜作填充金属材料。
不锈钢与铜焊接时,采用镍或镍基合金作填充金属材料。
铜和铝的熔点相差达423℃,很难同时熔化,在熔池中会产生脆性化合物AlCu2、Al2Cu3、AlCu、Al2Cu等。
当铜铝合金中含铜量在12%~13%以下时,综合性能最好,所以常采用铝焊丝。
铜-铝接头的埋弧焊见图7-19。
为加速铜的熔化,焊丝应偏离铜板坡口上缘0.5~0.6δ(δ为焊件厚度)。
铜侧开半∪形坡口,铝侧为直边,坡口中预置ф3mm的焊丝。
当焊件厚度为10mm时,焊丝直径2.5mm,焊接电流400~420A,电弧电压38~39V,送丝速度332m/h,焊接速度21m/h。
焊后,焊缝金属中铜的质量分数8%~10%为符合要求铜具有优良的导电性、导热性、耐腐蚀性、延展性及一定的强度等特性。
在电气、电子、化工、食品、动力、交通及航空航天工业中得到广泛应用。
在纯铜(紫铜)中添加10余种合金元素,形成固溶体的各类铜合金,如加锌为黄铜;加镍为白铜;加硅为硅青铜;加铝为铝青铜等等。
铜及铜合金可用钎焊、电阻焊等工艺方法实现连接,在工业发达的今天、熔焊已占据主导地位。
用焊条电弧焊、TIG焊、MIG焊等工艺方法容易实现铜及铜合金的焊接。
影响铜及铜合金焊接性的工艺难点主要有四项元素:一是高导热率的影响。
铜的热导热率比碳钢大7~11倍,当采用的工艺参数与焊接同厚度碳钢差不多时,则铜材很难熔化,填充金属和母材也不能很好地熔合。
二是焊接接头的热裂倾向大。
- 1、下载文档前请自行甄别文档内容的完整性,平台不提供额外的编辑、内容补充、找答案等附加服务。
- 2、"仅部分预览"的文档,不可在线预览部分如存在完整性等问题,可反馈申请退款(可完整预览的文档不适用该条件!)。
- 3、如文档侵犯您的权益,请联系客服反馈,我们会尽快为您处理(人工客服工作时间:9:00-18:30)。
通用焊接工艺规范1 碳素钢、合金钢及不锈钢的焊接1.1焊前准备1.1.1 焊缝的坡口形式和尺寸应符合设计文件的规定,当无规定时,符合本规范附录A.0.1的规定.1.1.2 焊件的坡口加工宜采用机械方法,也可采用等离子弧、氧乙炔焰等热加工方法,在采用热加工方法加工坡口后,必须除去坡口表面的氧化皮、熔渣及影响接头质量的表面层,并应将凹凸不平处打磨平整。
1.1.3 焊件组焊前应将坡口及其两侧表面不小于20 mm范围内的油、漆、垢、锈、毛刺及镀锌层等清除干净,不得有裂纹、夹层、加工损伤、毛刺及火焰切割熔渣等缺陷。
油污清理方法如下,首先用丙酮或四氯化碳等有机溶剂擦洗,然后用不锈钢丝刷清理至露出金属光泽,使用的钢丝刷应定期进行脱脂处理。
1.1.4 管子或管件、筒体对接焊缝组对时,内壁应齐平,内壁错边量不宜超过管壁厚度的10%,且不应大于2mm;1.1.5 焊缝的设臵应避开应力集中区,便于焊接和热处理,并应符合下列规定:(1)钢板卷筒或设备、容器的筒节与筒节、筒节与封头组对时,相邻两纵向焊缝间的距离应大于壁厚的3倍,且不应小于100 mm,同一筒节上两相邻纵缝间的距离不应小于200 mm;(2)除焊接及成型管件外的其他管子对接焊缝的中心到管子弯曲起点的距离不应小于管子外径,且不应小于l00 mm;管子对接焊缝与支、吊架边缘之间的距离不应小于50 mm。
同一直管段上两对接焊缝中心面间的距离:当公称直径大于或等于150mm时不应小于150mm;公称直径小于150mm时不应小于管子外径;(3)不宜在焊缝及其边缘上开孔。
(4)不锈钢焊件焊接部位两侧各l00 mm范围内,在施焊前应采取防止焊接飞溅物粘污焊件表面的措施:可将石棉置于焊接部位两侧等。
1.1.6 焊条、焊丝在使用前应按规定进行烘干、保温,并应在使用过程中保持干燥。
焊丝使用前应清除其表面的油污、锈蚀等。
常用焊材烘干温度及保持时间见表4。
表4 常用焊材烘干温度及保持时间焊接工艺要求1.2当无规定1.2.1 碳素钢及合金钢焊接材料的选用,应符合设计文件的规定,B.0.2B.0.1条及第条的规定。
第时,符合本规范附录B1.2.2 异种钢材焊接时的焊条选用。
可根据合金含量较低一(1) 当两侧母材均为非奥氏体钢或均为奥氏体钢时,侧母材或介于两者之间的选用焊材;型或含镍量更高的—13Ni25Cr(2) 当两侧母材之一为奥氏体钢时,应选用焊材。
定位焊缝应符合下列规定:1.2.3)焊接定位焊缝时,应采用与根部焊道相同的焊接材料和焊接工艺。
1()定位焊缝的长度、厚度和间距,应能保证焊缝在正式焊接过程中不致(2 开裂。
)在焊接根部焊道前,应对定位焊缝进行检查,如发现有夹渣、气孔和(3 裂纹等缺陷,应将缺陷部分除尽后方可施焊。
应在整个焊与母材焊接的工卡具其材质宜与母材相同或同一类别号,1.2.4拆除工卡具时不应损伤母材,缝焊接及热处理完毕并经检验合格后方可拆除。
拆除后应将残留焊疤打磨修整至与母材表面齐平。
并应防止电弧擦伤母材。
严禁在坡口之外的母材表面引弧和试验电流,1.2.5氩弧焊打的焊件,5%或合金元素总含量大于对含铬量大于或等于1.2.6 3%或采取其他防止内侧焊缝金底焊接时,焊缝内侧应充氩气或其他保护气体,属被氧化的措施。
.1.2.7 焊接时应采取合理的施焊方法和施焊顺序。
1.2.8 施焊过程中应保证起弧和收弧处的质量,收弧时应将弧坑填满。
多层焊的层间接头应错开。
1.2.9 除工艺或检验要求需分次焊接外,每条焊缝宜一次连续焊完,当因故中断焊接,再次焊接前应检查焊层表面,确认无裂纹后,方可按原工艺要求继续施焊。
1.2.10 多层焊每层焊完后,应立即对层间进行清理,并进行外观检查,发现缺陷消除后方可进行下一层的焊接。
1.2.11 低温钢、奥氏体不锈钢、耐热耐蚀高合金钢以及奥氏体与非奥氏体异种钢接头焊接时应符合下列规定:在焊接作业指导书规定的范围内,在保证焊透和熔合良好的条件下,采用小电流、短电弧、快焊速和多层多道焊工艺,并应控制层间温度。
1.2.12 对抗腐蚀性能要求高的双面焊焊缝,与腐蚀介质接触的焊层应最后施焊。
1.2.13 焊接完毕后,应及时将焊缝表面的熔渣及表面飞溅物清理干净。
对奥氏体不锈钢焊缝及其附近表面进行酸洗、钝化处理。
2 铝及铝合金的焊接2.1 焊前准备2.1.1 焊缝的坡口形式和尺寸应符合设计文件的规定,当无规定时,符合本规范附录A.0.2的规定. 切割后的坡口表面应进行清理,并应达到平整光滑、无毛刺和飞边。
焊前清理应符合下列规定:2.1.1.1 施焊前应对焊件坡口、垫板及焊丝进行清理。
清理方法如下,首先用丙酮或四氯化碳等有机溶剂除去表面油污,两侧坡口的清理范围不应小于50 mm。
清除油污后,坡口及其附近的表面用不锈钢丝刷清理至露出金属光泽,使用的钢丝刷应定期进脱脂处理。
2.1.1.2 焊丝去除油污后,应采用化学方法去除氧化膜。
可用5%一10%的Na (OH)溶液,在温度为70℃下浸泡30~60 s,然后水洗,再用15%左右的HN03在常温下浸泡2min,然后用温水洗净,并使其干燥。
2.1.1.3 清理好的焊件和焊丝不得有水迹、碱迹,或被粘污。
2.2 焊接工艺要求2.2.1 手工钨极氩弧焊应采用交流电源,熔化极氩弧焊应采用直流电源,焊丝接正极。
2.2.2 焊接前焊件表面应保持干燥,无特殊要求时可不预热。
2.2.3 焊接前应在试板上试焊,当确认无气孔后再进行正式焊接。
2.2.4 宜采用大电流快速施焊法,焊丝的横向摆动不宜超过其直径的3倍。
引弧宜在引弧板上进行,纵向焊缝宜在熄弧板上熄弧。
引弧板和熄 2.2.5弧板的材料应与母材相同。
2.2.6 手工钨极氩弧焊的焊丝端部不应离开氩气保护区,焊丝与焊缝表面的夹角宜为15°,焊枪与焊缝表面的夹角宜为80°~90°。
2.2.7 多层焊时宜减少焊接层数,层间温度宜冷却至室温,且不应高于65℃。
层间的氧化铝等杂物应采用机械方法清理干净。
2.2.8 对厚度大于5mm的立向焊缝,宜采用两人双面同步氩弧焊工艺。
2.2.9 当钨极氩弧焊的钨极前端出现污染或形状不规则时,应进行修正或更换钨极。
当焊缝出现触钨现象时,应将钨极、焊丝、熔池处理干净后方可继续进行施焊。
2.2.10 当熔化极氩弧焊发生导电嘴、喷嘴熔入焊缝时,应将该部位焊缝全部铲除,更换导电嘴和喷嘴后方可继续施焊。
2.2.11 手工钨极氩弧焊和熔化极氩弧焊的焊接工艺参数宜符合表7.3.11-l、表7.3.11-2、表7.3.11-3的规定。
手工钨极氩弧焊工艺参数表7.3.11.-1厚度焊接焊丝直钨棒直径喷嘴直径焊接电氩气流量层数径〔nxn〕(mm) (oKn) (H帅>流(A) (L/min)1 1.6~3.0 1.6~3.2 1~3 8~12 40~140 8~1210~16 4~8 10~14 2~3 3.0~5.0 2.4~5.0 140~32014~208~12 4.0~6.4240~3603~44.0~6.012~167.3.11-2表半自动熔化极氩弧焊工艺参数氩气流量电弧电压焊丝直径厚度喷嘴直径焊接电流min) [nvn](V) (mm) (mm) (L/(A)50~55 1.6~2.5 8~12 180~310 20 20~3060~70202.5~3.014~22 300~47030~427.3.11-3自动熔化极氩弧焊工艺参数表电弧焊丝喷嘴焊接电厚度氩气流量焊接速度流电压直径直径min)/(cm /(mm) (Lmin)(V) (A) (mm) (mm)40 30~33 20~22 2.5 22 6 230~26035~45 22 8 2.5 30~33 20~22 300~32030 30~33 24~27 310~320 10 3.0 2225 30~33 12 27~283.0 22320~35028/17 4.0 380~420 28~32 16 35~40 28~3228/17 28~32 35~40 4.0 480~520 20 28~3228~34550~560 26 30/17 24~2840~604.0焊件应采用下列防止变形措施: 2.2.12具有大收缩量的焊)焊接顺序应对称进行,当从中心向外进行焊接时,(1 缝宜先施焊,整条焊道应连续焊完。
2)焊件宜进行刚性固定或采取反变形方法,并应留有收缩余量。
(焊后外观检查3除设计文件有特殊要求的焊缝外,焊缝应在焊完后立即去除渣皮、飞 3.1溅物,清理干净焊缝表面,然后进行焊缝外观检查。
焊接表面应平滑,不应有裂纹、密集气孔、大弧坑、焊丝头、焊穿、3.2。
深咬边、未熔合,未焊透等缺陷,焊瘤不高于1.5mm附录A 焊件的坡口形式和尺寸 A.0.1 钢焊件坡口形式和尺寸应符合表A.0.1的规定。
表A.0.1 钢焊件坡口形式和尺寸0~1.5单面31~1 --型坡口I2.5~0双面~3693~2~0~275650~2 型坡口V 65559~26 ~03 ~3 0~23~~~69 05 带垫板3 55 45~V型坡口2 9~6 0~4~26 33 ~~004~65~126055型坡口X 3~030~T型接头50~2-2~30-I型坡口0~2 6~100~2 型接头T6-~型V55-45单边100~~~03 3 17坡口17~0~40~430型接头T720~40 接头对称0~3 2~3 45~55型坡口K60~50法兰角焊≤管径Ф830-~23(~76接头)35续表 A.0.1-且,K=1.4T不大于颈法兰角焊部厚度接头、承- 10 ---,且E=6.4插焊接接T不大于头A.0.2 铝及铝合金坡口形式和尺寸应符合表A.0.2的规定。
铝及铝合金被口形式和尺寸表A.0.2T+1度---卷边~112不填加手工钨焊丝极氩弧焊单面焊∠3型坡I--2-口双面焊~53横焊(a) ~701.512~~03~5位置坡80型V3口角度坡口~60 2~~51242~1上半边7040°~50°, 带垫手工钨下半边~50 板极氩弧-12~44~6320°~30°; 60 型V 焊单面(b) 坡口焊坡口根部内~60型X3 2>5122.5~0~侧最好80 坡口倒棱.A.0.2头型接T V头手工钨~50 ≦2 72~0.5106~型坡极氩弧55口焊型接T头对~50 28>8称K≦20~55型坡口型坡I9 ≦10- - 3 ~0口V型60~10 4 ~3 38~20~0 坡口70带垫板V50~熔化极1163~38~25~6 60型坡氩弧焊口40~U型12 ≥20533~0~坡口50~70>83~680型X 1330~坡口60~26>5~870附录B 焊接材料的选用的规定。