推荐-一汽丰田零件库存管理 精品
丰田汽车零件仓库管理原则

目视化(Visualization)的未来发展
数字化:利用大数据和人工智能技术,实现仓库管理的智能化和自动化 物联网:通过物联网技术,实现仓库设备、货物和信息的实时监控和管理 绿色环保:采用环保材料和节能技术,降低仓库运营成本,提高环保性能 安全保障:加强仓库安全管理,提高仓库防火、防盗等安全措施,确保仓库安全
标准化(Standardization)
统一管理:所有零 件仓库采用统一的 管理标准和流程
标准化操作:所有 操作人员必须按照 标准化的操作流程 进行操作
标准化工具:所有 仓库使用统一的工 具和设备,确保操 作效率和质量
标准化数据:所有 仓库的数据必须按 照统一的格式进行 记录和存储,便于 管理和分析
品和信息
实施方法:使 用颜色、形状、 标签等视觉元 素,对物品进 行分类和标识
实施效果:提 高工作效率, 减少错误率, 提高仓库管理
水平
实施案例:丰 田汽车零件仓 库的目视化管
理实践
丰田仓库管理原则的优点 与挑战
章节副标题
准时制(JIT)的优点与挑战
优点:提高产品质量,减少 浪费
挑战:对供应链管理要求高, 需要与供应商紧密合作
优点:减少库存,降低成本, 提高生产效率
挑战:对员工素质要求高, 需要员工具备良好的技能和
责任心
自动化(Jidoka)的优点与挑战
优点:提高生产效率,减少人工 成本
挑战:需要投入大量资金进行设 备更新和维护
添加标题
添加标题
添加标题
添加标题
优点:提高产品质量,减少不良 品率
挑战:需要员工具备一定的操作 技能和知识
标准化(Standardization)的优点与挑战
优点:提高效率, 降低成本,提高 产品质量
丰田仓库管理七原则(最新)
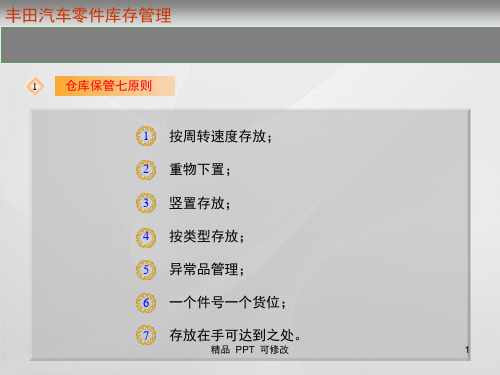
所以一定要贯彻一个件号一个货精位品。PPT 可修改
9
丰田汽车零件库存管理
第四章 仓库保管七原则
2.7.存放于手可达到的高度
这是从方便作业、提高工作效率角度考虑的。 如果零件存放在过高的地方,提取及上架时 不得不使用梯子,就会造成作业不方便、 效率低下。所以,应该将零件存放在 手能达到的位置。
精品 PPT 可修改
丰田汽车零件库存管理
1 仓库保管七原则
1 按周转速度存放;
2 重物下置;
3 竖置存放;
4 按类型存放;
5 异常品管理;
6 一个件号一个货位;
7 存放在手可达到之处。
精品 PPT 可修改
1
丰田汽车零件库存管理
第四章 仓库保管七原则
2.1.按周转速度存放
* 常流动件远离作业区,效率低下。
* 常流动件存放于作业区附近,作业方便。
作业区
作业区
为常流动件;
为慢流动件;
为出入库行走路线。
精品 PPT 可修改
2
丰田汽车零件库存管理
第四章 仓库保管七原则
① 常流动件存放于远离作业区的货位,延长了出入库作业路线; ② 且存放在货架上不易取放的位置,大大降低了工作效率。
① 常流动件存放于靠近作业的货位,缩短了出入库作业路线; ② 存放在易于取放的位置,提高了工作效率。
精品 PPT 可修改
3
丰田汽车零件库存管理
第四章 仓库保管七原则
2.2.重物下置
这是从出入库作业的安全性和高效率方面来考虑的。有些像半轴、缸体、轮毂等 重零件如存放在货架上方会产生如下问题:
① 重零件有落下伤人及损坏的危险; ② 上架、提取不便。
危险!
不便!
丰田库存级别管理制度范文
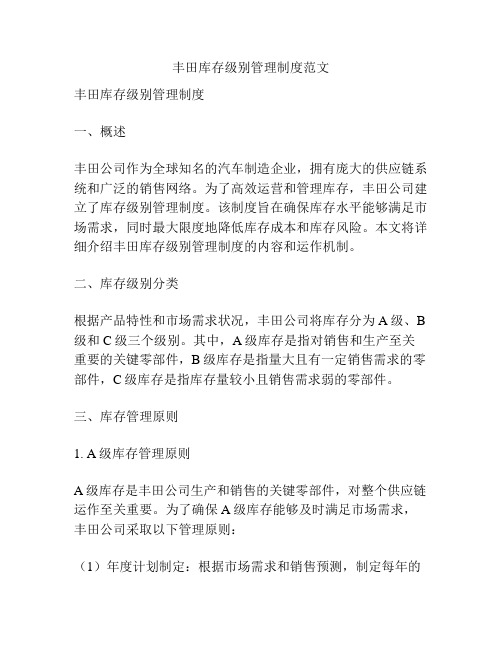
丰田库存级别管理制度范文丰田库存级别管理制度一、概述丰田公司作为全球知名的汽车制造企业,拥有庞大的供应链系统和广泛的销售网络。
为了高效运营和管理库存,丰田公司建立了库存级别管理制度。
该制度旨在确保库存水平能够满足市场需求,同时最大限度地降低库存成本和库存风险。
本文将详细介绍丰田库存级别管理制度的内容和运作机制。
二、库存级别分类根据产品特性和市场需求状况,丰田公司将库存分为A级、B 级和C级三个级别。
其中,A级库存是指对销售和生产至关重要的关键零部件,B级库存是指量大且有一定销售需求的零部件,C级库存是指库存量较小且销售需求弱的零部件。
三、库存管理原则1. A级库存管理原则A级库存是丰田公司生产和销售的关键零部件,对整个供应链运作至关重要。
为了确保A级库存能够及时满足市场需求,丰田公司采取以下管理原则:(1)年度计划制定:根据市场需求和销售预测,制定每年的A级库存计划,包括库存量、采购计划和供应商协商等内容。
(2)预测准确性管理:通过与销售团队密切合作,不断优化销售预测模型,提高预测准确性,确保A级库存的准确配备。
(3)供应商管理:与A级库存供应商建立长期稳定的合作关系,定期评估供应商绩效,确保供应商能够按时交付高质量的产品。
2. B级库存管理原则B级库存是丰田公司生产和销售的中等规模的零部件,对供应链的正常运作有一定影响。
为了有效管理B级库存,丰田公司采取以下管理原则:(1)定期审查库存:定期审查B级库存水平,分析市场需求变化和库存周转率,根据实际情况进行库存调整。
(2)销售推动措施:通过销售团队提供市场需求信息,积极推动B级库存产品的销售,降低库存风险。
(3)供需协调管理:与供应商保持密切联系,根据市场需求和供应能力,协商库存采购和供应计划,确保库存和需求之间的平衡。
3. C级库存管理原则C级库存是丰田公司生产和销售的小规模零部件,销售需求较弱。
为了最大限度地降低C级库存的成本和风险,丰田公司采取以下管理原则:(1)库存优化管理:定期分析C级库存产品的销售情况和周转率,削减低销售量的库存,提高库存利用率。
丰田零库存管理精品PPT课件

看板方式
根据拉动式生产的实际情况,把生产计划下达给 最后的组装线,在指定的时间生产指定数量的指定 车型,组装线便依次向前一道工序领取所需要的各 种零部件。
用于领取工件或者传达生产指令的媒介,看似 非常小的却承载着非常至关重要的信息,从而彻 底消除浪费。
础在于人,以及人 所创造的“带人字边的自动化”,它表现出丰田的 另一个生产理念:先进的设备只是起点,人才是品 质的最终保障。
升华篇
1 取其精华
中国汽车企业虽然近年来发展迅猛,但不可 否认的是时至今日其仍存在一块“短板”,那 就是缺少核心竞争力。所以我们企业确实要想 丰田学习,并且总结反思。能将他们核心的 TPS运用到咋们自己的企业,而不产生后遗症。
2 去其糟粕
可以这样说,现在的丰田正在为当年挖的“大坑” 还债。客观的说,丰田在针对消费者售后方面做的 确实有点滞后。假如丰田能提前的召回有问题的车 辆,假如丰田章男能找点出面道歉,假如丰田把防 范措施做的充足一点,也不至于这样兵败如山倒的 局面了。而这是我们值得思考的地方,历史虽然不 会重演,但是历史确实惊人的相似。所以我们记得, 对客户不要傲慢,吃亏的会是你自己。
注完美,近乎苛求
简介篇 问题分析篇 升华篇
简介篇
拉式生 产模式
零库存
Add Y自ou动r Te化xt 作业方 式
看板 管理
拉动式生产
由后一道工序在需要的时刻到前一道工序去领取 需要数量的特定零部件,而前一道工序则只生产所需 要领取的数量。
在丰田的车间,看不到分门别类堆积在物架上的 零部件,也见不到其他工厂“零部件搬运工往来穿 梭”的繁忙景象。
一种发现异常和发现质量缺陷的技术手段,是 一种当异常或质量缺陷发生时,能使生产线或者 机器自动停止工作的技术装置。
丰田汽车零件仓库管理原则

5.按零件类型存放 B
长零件伸出至 通道影响作业
空间浪费 中型零件如:空 滤、离合器片等
长型零件如消声 器等
空间浪费 微小型零件(油 封、火花塞等)
大型零件如:缸体、 轮毂、水箱等
所以当我们感到库存空间不足的时候是否可以审视一下自己的货架,是否有的货位 上还有很大的空间尚未利用。如果存在这些问题可以建议由订货和仓库组成改善小 组对保管进行改善,一定会有好的效果。
2.重物下置 B
有些像半轴、缸体、轮毂等重零件如存放在货架上方会产生如下问题
不便 危险
1、重零件有落下伤人、及损坏可能 2、上架、下架不方便
3.竖立放置 A
有些象车门、排气管、挡风玻璃等扁平或 细长形状的零件如平放会产生如下问题: 1.上面零件的重量会损伤下面的零件 2.此类零件平放会浪费很大空间 3.由于排气管一类的零件过长,如平放会从 货架伸出通道,从而影响通行且不安全 4.难以提取
3.竖立放置 B
4.一个零件号一个货位 A 在各个TASS中通常有这样的做法,就是把各种 零件混放在一起或一个货位里有几种零件.一个 优秀的仓库管理员即使能凭记忆力记住几千个 零件号也难免出现错误,况且库存还要不断变化. 当出入库作业时由于一时记不起零件的存放位 置就容易产生待工的现象,或当熟知仓库情况的 管理员因某种原因不在岗位上时,其他人员也不 能顺利的找到零件.上述状况都有可能造成工作 效率低下.
6.异常管理 A
常常会有这样情况,由于订货管理不善及某些品种因市场需求 增加而需要追加订货,这时原来设定的货位容量就会显的不足, 新到的货没有地方放。每当遇到这样的问题时我们往往是另找 个地方先暂时存放起来,但这样做却有如下缺点: 1.容易因疏忽而忘记的临时存放零件位置 2.库存空间浪费 3.无法观察库存效率(不易发觉不良库存)
丰田零件业务管理简述
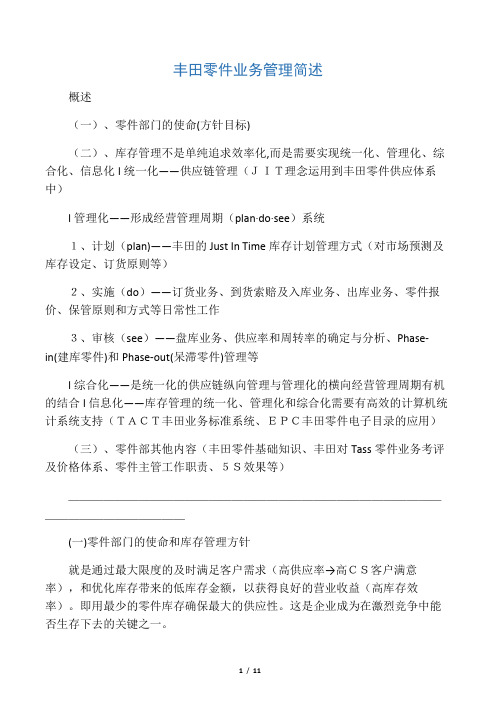
丰田零件业务管理简述概述(一)、零件部门的使命(方针目标)(二)、库存管理不是单纯追求效率化,而是需要实现统一化、管理化、综合化、信息化l统一化——供应链管理(JIT理念运用到丰田零件供应体系中)l管理化——形成经营管理周期(plan·do·see)系统1、计划(plan)——丰田的Just In Time库存计划管理方式(对市场预测及库存设定、订货原则等)2、实施(do)——订货业务、到货索赔及入库业务、出库业务、零件报价、保管原则和方式等日常性工作3、审核(see)——盘库业务、供应率和周转率的确定与分析、Phase-in(建库零件)和Phase-out(呆滞零件)管理等l综合化——是统一化的供应链纵向管理与管理化的横向经营管理周期有机的结合l信息化——库存管理的统一化、管理化和综合化需要有高效的计算机统计系统支持(TACT丰田业务标准系统、EPC丰田零件电子目录的应用)(三)、零件部其他内容(丰田零件基础知识、丰田对Tass零件业务考评及价格体系、零件主管工作职责、5S效果等)____________________________________________(一)零件部门的使命和库存管理方针就是通过最大限度的及时满足客户需求(高供应率→高CS客户满意率),和优化库存带来的低库存金额,以获得良好的营业收益(高库存效率)。
即用最少的零件库存确保最大的供应性。
这是企业成为在激烈竞争中能否生存下去的关键之一。
(二)库存管理不是单纯追求效率化,而是需要实现统一化、管理化、综合化、信息化要达到CS和库存效率化这两个相互矛盾的目标,库存管理实现上述“四化”是首要条件。
一、统一化——应把库存管理作为构成供应链纵向统一系统的一环加以定位。
1、丰田的零件供应体系是建立在JIT零件供应理论基础上的,即卖一买一原则,就是零件的物流按要求的步调沿供应线流动。
2、TASS经销店是丰田整个零件供应链中的重要一环。
零部件库存管理(丰田JIT库存管理法)
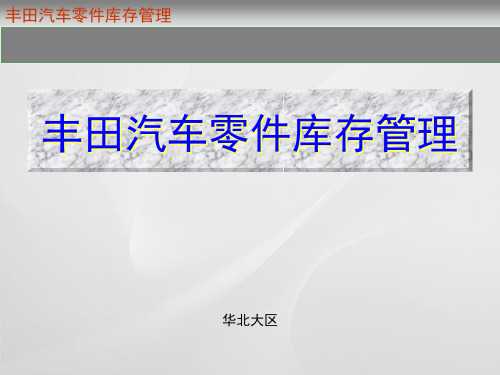
库存深度
零件部门的重要使命
需求
减少库存
减少库存
库存
提高供应率 减少浪费
提高零件供应性
库存宽度
丰田汽车零件库存管理
第一章.零件管理概述-目标和管理指标
目标: 以最低的库存量达到高供货能力的 目标
管理指标: •供应率 •库存月数
丰田汽车零件库存管理
第一章 零件管理概述-供应率的计算
1 零件供应率的计算方法
对应MAD波动 的安全库存
对应L/T 的安全库存
丰田汽车零件库存管理 第二章 库存管理的必要性
丰田汽车零件库存管理
第二章 科学的库存管理的必要性
零件的流动具有偏向性
——最大的销量往往只集中在最少的品种当中
3万种 90%
涉及订货的27万种零件
3万种 9万种 15万种
15万种 3%
9万种 7%
丰田汽车零件库存管理
1
2
3
订货
天数
4
5
上图所示的订货周期为两天,此时的O/C = 2/30 = 1/15(月)
丰田汽车零件库存管理
第三章 Just In Time的库存管理方式-库存多少
③ SSQ= MAD ×(O/C + L/T + S/S )
■ L / T― 到货周期 (在途时间, 单位:月)
订
订
单
订
零
单
到
单
件
运
计算时点:入厂时?维修期间?
G√ H√
2 在库月数
I√ J√
库存月数=
月均零件库存金额(进货价) 月零件销售金额(进货价)
合计 10 9 供应率 90%
件供 数应
一汽丰田零件库存管理

原则上,经销店是不用现有库存来供应人为需求的。这是因为现有库存是对过去实际需求进行分析而预测 出来的库存,其中没有包含人为需求的因素。如果没有注意这一点,很有可能在发生实际需求时,库存无法 正常供应。
订货方式:经销店应将人为需求以F/O的形式向FPD发出订货(如:服务周备货,大客户采购等)。
3万种 9万种 15万种
15万种 3%
9万种 7%
丰田汽车零件库存管理
第三章 Just In Time的库存管理方式-零件周期
零件的生命周期
零件生命周期图 某一零件需求
存多少?
活跃期
建立库存 新车型上市
何时买? 买多少?
退出库存 存活期
存多久? 停止订货
老车型淘汰
丰田汽车零件库存管理 第三章 Just In Time的库存管理方式
丰田汽车零件库存管理
第一章 零件管理概述-供应率/在库月的计算
即时供应率的指标: 1、零件件号即时供应率 从库存宽度的角度反映零件供应状况
件供 件 供 号应 数 应
A√ 5 5
2、零件件数即时供应率
从库存宽度和深度两个角度全面衡量零件 供应状况
B√ 6 4 C√ 3 3 D√ 3 1
3、零件施工单即时供应率
(3)客观的分析L/S的记录,合理的加入到MAD的计算中去。 ※L/S― Lost Sales,即流失的业务。 对于非库存零件或库存不足零件,有时客人会取消订货。这时要把它记录下来, 考虑取消的项目是否需要增加库存量,如果是非库存项目,就要考虑是否需要纳入库存项目。 没有库存
不买了!
无论是B/O需求,还是L/S需求,我们在统计计算MAD时都需要视具体 情况而定,对于那些非常规的B/O和L/S需求,我们要谨慎统计。
零库存管理的典型—丰田看板方式
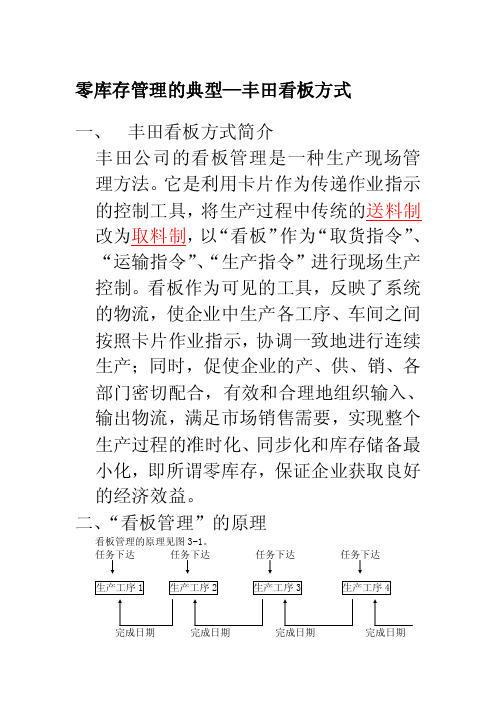
零库存管理的典型—丰田看板方式一、丰田看板方式简介丰田公司的看板管理是一种生产现场管理方法。
它是利用卡片作为传递作业指示的控制工具,将生产过程中传统的送料制改为取料制,以“看板”作为“取货指令”、“运输指令”、“生产指令”进行现场生产控制。
看板作为可见的工具,反映了系统的物流,使企业中生产各工序、车间之间按照卡片作业指示,协调一致地进行连续生产;同时,促使企业的产、供、销、各部门密切配合,有效和合理地组织输入、输出物流,满足市场销售需要,实现整个生产过程的准时化、同步化和库存储备最小化,即所谓零库存,保证企业获取良好的经济效益。
二、“看板管理”的原理看板管理的原理见图3-1。
任务下达任务下达任务下达任务下达完成日期完成日期完成日期完成日期图3-1 看板原理示意图由图3-1可以看出,“看板管理”是由代表客户需求的定单开始,根据定单按产品结构自上而下进行分解,得出完成定单所需零部件的数量。
生产控制人员检查现有零部件库存,是否能满足定单的要求,如果不足,就由最后一道加工工序开始,反工艺顺序地逐级“拉动”前面的工序。
在此过程中,看板起到指令的作用,通过看板的传递或运动来控制物流。
二、看板的形式和分类看板形式很多。
常见的有塑料夹内装着的卡片或类似的标识牌、存件箱上的标签、流水生产线上各种颜色的小球或信号灯、电视图象等。
看板主要可以分为生产看板和取货看板两种不同的类型。
生产看板生产看板是在工厂内指示某工序加工制造规定数量工件所用的看板,内容包括需加工工件的件号、件名、类型、工件存放位置、工件背面编号、加工设备等,如表3-1所示。
表3-1 企业生产看板实例取货看板取货看板是后工序的操作者按看板上所列件号、数量等信息,到前工序领取零部件的看板。
它指出应领取的工件件号、件名、类型、工件存放位置、工件背面编号、前加工工序号、后加工工序号等,如表3-2所示。
表3-2 企业取货看板实例四、看板管理的过程日本丰田公司利用看板进行生产现场管理的过程如图3-2所示。
库存管理(一汽丰田零件)
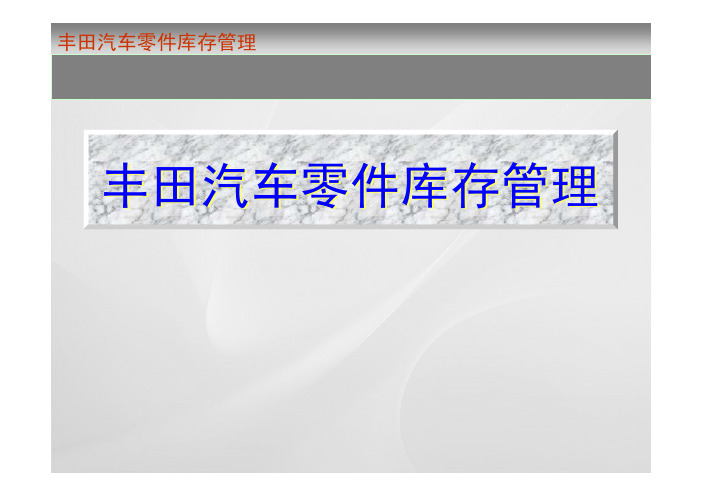
2.2 如何建立并管理库存品种
①建立库存 概念:建立库存指伴随新车型的上市,原非库存零件开始进行库存管理的时点。
②报废 概念:报废指伴随老车型逐渐从市场中淘汰掉,原库存零件不再进行库存管理 的时点。
丰田汽车零件库存管理
第三章 Just In Time的库存管理方式
③建立库存/报废时点的确定 各经销店可以通过从零件需求的历史记录中统计出来的月均需求(MAD)和需 求频度,发现零件需求的规律,从而确定需要库存的零件范围。
需一买一
库存管理项目
卖一买一
报废
非库存 管理项目
只卖不买
时间
丰田汽车零件库存管理
TACT系统零件管理-TACT使用要点
2. 推荐S/O订货清单
因为在TACT系统中预 设了图示的订货公式, 所以TACT系统可以在 统计后,提交推荐S/O 订货清单。各网点在订 货时,只需要按一下订 货计算键,系统就会将 推荐的订货项目、数量 以清单的方式提交出 来,这样以来,订货计 算的过程就大大简化 了。
到货周期的S/S
平均 L/T(到货周期)
95%
最长3天
L/T天数
例如:经过统计发现,平均L/T=1天; 最长=4天;95% 的情况下都是3天内到货,则:
L/T安全库存 =3 – 1=2天
丰田汽车零件库存管理
为应付MAD的波动而需要的安全库存天数:
确保供应的S/S
MAD
目标即时供应率95%
最大需求点
没有库存
帮我订B/O
丰田汽车零件库存管理
(3)客观的分析L/S的记录,合理的加入到MAD的计算中去。 ※L/S― Lost Sales,即流失的业务。 对于非库存零件或库存不足零件,有时客人会取消订货。这时要把它记录下来, 考虑取消的项目是否需要增加库存量,如果是非库存项目,就要考虑是否需要纳入库存项目。
【推荐精品】Toyota丰田零件库存管理中级进阶篇(1)
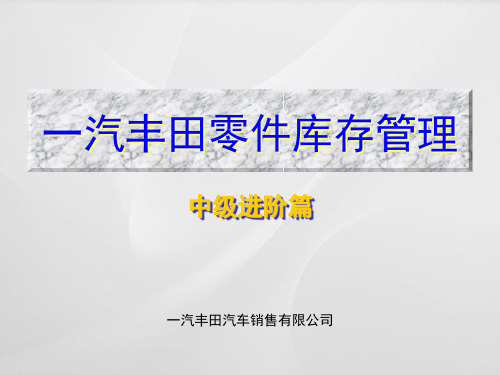
到
···
货
订
拆
订
单
订
零
箱
单
到
单
件
运
上
发
达
处
装
输
架
出
F
理
箱
录
P
入
D
系
统
1
2
3
4
5
6
上图所示的到货周期为六天,此时的L / T = 6/30 = 1/5(月)
步骤
11
丰田汽车零件库存管理
第一章 库存宽度和深度的管理
④ SSQ= MAD ×(O/C + L/T + S/S )
■ S/S― 安全库存周期(受到货期延迟和需求波动两个因素影响,单位:月)
Phase Out 谨慎执行,建议 一年内没有需求
记录
5
丰田汽车零件库存管理
第一章 库存宽度和深度的管理
库存深度的确定
标准库存量(SSQ-即Standard Stock Quantity)
SSQ=MAD×(O/C + L/T + S/S)
Standard Month Stock Average
Quantity Demand 标准库存量 月均需求
22
丰田汽车零件库存管理
第三章 库存级别管理
TACT库存级别管理功能
库存级别管理(ICC)
• 所谓库存管理级别就是将所有的库存零件按照一定的规律进行分组管理。
• ICC目的是划分零件所处的生命周期,实施不同的订货策略。
• 区分要管理/不用管理、重点管理/一般管理的项目,根据各个项目的特征实施相应
的对策。
月均需求
零件生命周期图
学习笔记--丰田汽车零件库存管理

Learning note----丰田汽车零件库存管理2014年1月20日星期一农历腊月20/大寒天晴内容:Page 1~11笔记:1、零部件管理目标:以最低的库存量达到高供货能力;2、零部件管理指标:供应率、库存月数;a)供应率:零件即时供应率、施工单供应率;i.零件即时供应率 = 可以供应的零件/号数接受订货的零件/号数*100%;可以全面衡量零件的供应情况,包括库存深度和宽度。
注:零件件号及时供应率,从库存宽度的角度反应零件供应状况;零件件数及时供应率,从库存宽度和深度两个角度全面衡量零件供应状况;零件施工单即时供应率,从客户(车间)的角度衡量供应状况。
ii.施工单及时供应率 = 完全供应了零件的施工单所有有零件需求的施工单*100%;是服务部门衡量零部件部门零件供应的尺度。
b)库存月数 = 月均零件库存金额(进货价)月零件销售金额(进货价);2014年1月21日星期二农历腊月21 天晴内容:Page11-笔记:1、零部件管理要点:只有库存与需求相互协调,才能做到以最低的库存量实现高供货能力。
为此,需要特别注意存什么?-库存宽度;存多少,库存深度;怎么存,订货方式。
a)存什么?建立库存之前,根据需求订货;库存建立之后,根据销耗制定订货需求;对于进入报废提醒阶段的,只提供相关零件不再购入。
i.建立库存:原非库存零件开始进行库存管理的时点;ii.报废:原库存零件不在进行库存管理的时点;iii.建立库存/报废时点的确定:可以根据零件需求的历史记录中统计出需求频度,以及B/O,流失等发现零件去修的规律,从而确定需要库存的零件范围。
注:B/O,Back Ordere,即追加订货。
当没有库存货库存不足的时候,所发生的替客户做的追加订货。
b)库存政策:phase in/out ,零件报废政策;i.Phase in,逐步纳入(从没有库存到建立安全库存,依据有关材料统计筛选过去6个月内2次以上的零件);ii.Phase out,逐步取消(从有库存开始逐步试验取消库存,依据有关材料筛选过去6个月内不足2次的零件);iii.零件报废政策:简单而严格的规定报废有效管理时限、报废义务和基本权责等;注:Phase/feɪz/:[词典义] n. 相;阶段,[天] 位相;vt. 使定相,逐步执行;vi. 逐步前进;[网络短语]Phase相位,阶段,相;phase diagram相图,相位图,状态图;phase difference相位差,相差,位相差;c)标准库存公式:SSQ = MAD * (O/C + L/T + S/S)标准库存量月度需求订货周期到货周期安全库存周期MAD的确定要素中要是具体情况统计B/O和L/S,对于那些非常规的B/O和L/S的需求需谨慎统计。
- 1、下载文档前请自行甄别文档内容的完整性,平台不提供额外的编辑、内容补充、找答案等附加服务。
- 2、"仅部分预览"的文档,不可在线预览部分如存在完整性等问题,可反馈申请退款(可完整预览的文档不适用该条件!)。
- 3、如文档侵犯您的权益,请联系客服反馈,我们会尽快为您处理(人工客服工作时间:9:00-18:30)。
库存宽度
第一章.零件管理概述-目标和管理指标
目标: 以最低的库存量达到高供货能力的 目标
管理指标: •供应率 •库存月数
第一章 零件管理概述-供应率的计算
1 零件供应率的计算方法
1.1 零件即时供应率
零件即时供应率=
可以供应的零件/号数 接受订货的零件/号数
×100%
零件即时供应率可以全面衡量零件的供应情况,包括库存深度和宽度。
B/O L/S
Phase out 死库
怎么存
存多少
B/O
L/S
大-大
大-小
订货周期 到货周期 安全库存
MAD
对应MAD波动 的安全库存
对应L/T 的安全库存
第二章 库存管理的必要性
第二章 科学的库存管理的必要性
零件的流动具有偏向性
——最大的销量往往只集中在最少的品种当中
3万种 90%
涉及订货的27万种零件
逐步取消
需求数据--以过去6个月 过去6个月内2次
(从库存到不库存) 内的零件编号来统计。 或少于2次
第三章 Just In Time的库存管理方式-库存多少
SSQ=MAD×(O/C + L/T + S/S)
标准库存量 月均需求 标准库存公式图解
需求量 SSQ
MAD×L/T MAD×O/C
订货周期 到货周期 安全库存周期
从库存宽度和深度两个角度全面衡量零件 供应状况
3、零件施工单即时供应率
LINE
从客户(车间)的角度衡量零件供应状况
B√ C√ D√ E√ FX
计算时点:入厂时?维修期间?
G√ H√
2 在库月数
I√ J√
库存月数=
月均零件库存金额(进货价) 月零件销售金额(进货价)
合计 10 9 供应率 90%
件供 数应
③建立库存/报废时点的确定
各经销店可以通过从零件需求的历史记录中统计出来需求频度,以及B/O,流失, 发现零件需求的规律,从而确定需要库存的零件范围。
月均需求 少 需求频度 低
增长期 较多
低
较多 较高
库存状态 不库存 不一定 建立库存
平稳期
衰退期
多
少(短期)
少(长期)
高
低(短期)
低(长期)
库存管理 “停止库存试验” 报废
55 64 33 31 55 10 0 52 32 31 51 48 24
50%
施工单
需 求
供应 供应率
R/O 1 10 10 100%
R/O 2 8 8 100%
R/O 3 12 12 100% R/O 4 6 5 0% R/O 5 8 8 100%
R/O 6 4 4 100% R/0 7 16 12 0% R/O 8 12 12 100%
第三章 Just In Time的库存管理方式-库存什么
无库存零件的需求历史
零件编号
15600-06010 23300-06010 04465-10160 31250-20251 04479-28010
一月 二月 三月 四月 五月 六月 MAD
0 0 3 5 4 8 3.3 1 0 0 1 0 0 0.33 4 8 8 12 8 20 10 0 0 0 0 0 1 0.17 0 1 1 0 0 0 0.33
丰田汽车零件库存管理
华北大区制作
第一章 库存管理概述 第二章 科学的库存管理的必要性 第三章 Just In Time的库存管理方式 第四章 仓储七原则 第五章 TACT操作方法
第一章 库存管理概述
第一章 库存管理概述
库存深度
零件部门的重要使命
需求
减少库存
减少库存
库存
提高供应率 减少浪费
提高零件供应性
供应率
75%
第一章 库存管理概述
零件部门的职责
满足车间生产的零件需要
获取零件收益 =销售收入-进货成本-运营成本
提高零件供应率
降低经营成本 降低进货成本
以最低库存满足高供货能力
Incentive
零件需求
零件库存
人为需求
实际需求
库存管理品种
Phase out/in
非库存管理品种
存什么
Phase in ICC
第三章 Just In Time的库存管理方式-库存什么
库存什么?
库存状态的对应方法
月均需求
建立库存
非库存 管理项目
需一买一
库存管理项目
卖一买一
报废
非库存 管理项目
只卖不买
时间
第三章 Just In Time的库存管理方式-库存什么
①建立库存 概念:原非库存零件开始进行库存管理的时点。
②报废
概念:原库存零件不再率 施工单即时供应率=
完全供应了零件的施工单 所有有零件需求的施工单 ×100%
施工单供应率是服务部门衡量零件部门零件供应的尺度。
第一章 零件管理概述-供应率/在库月的计算
即时供应率的指标: 1、零件件号即时供应率 从库存宽度的角度反映零件供应状况
件供 号应
A√
2、零件件数即时供应率
3万种 9万种 15万种
15万种 3%
9万种 7%
第三章 Just In Time的库存管理方式-零件周期
零件的生命周期
零件生命周期图 某一零件需求
存多少?
活跃期
建立库存 新车型上市
何时买? 买多少?
退出库存 存活期
存多久? 停止订货
老车型淘汰
第三章 Just In Time的库存管理方式
第三章 Just In Time的库存管理方式— 丰田JIT理念: “卖一买一”
该系统使零件随着物流链,以和顾客需求同样的节奏流动
第二章 科学的库存管理的必要性零件部门的重要使命
库存深度
需求
减少库存
减少库存
库存
提高供应率
减少浪费
库存宽度
只有库存与需求相协调,才能做提高到零以件供最应低性的库存量实现高供货能力。为此, 我们需要特别注意以下方面:
• 存什么?—— 库存宽度 • 存多少?—— 库存深度 • 怎么存?—— 订货方式
库存零件的需求历史
零件编号
一月 二月 三月 四月 五月 六月 MAD
13505-15050 48530-10010 04465-10160 17801-15070 90919-01166
0 1 0 0 2 0 0.5 0 0 0 0 1 0 0.17 9 10 11 9 12 11 10.3 0 1 0 1 0 0 0.33 20 24 16 32 20 24 22.7
逐步纳入
加入 库存 项目 过去六个月内的需
求次数 >2
逐步取消
取消库存项目 过去六个月内的
需求次数 <=2
第三章 Just In Time的库存管理方式-库存什么
库存政策: •Phase in/out •零件报废政策
改变库存
参考资料
定义
过去6个月内2次
逐步纳入
B/O统计
以上需求
(从不库存到库存) L/S(丢失的销售)