高硫高酸原油对80×10 4t/a焦化装置的影响及对策
含硫原油对输油管道及设备的腐蚀分析

研究硫化物对输送油管和设备的腐蚀,消解法是现在使用最为多的方法,研究各种形态的硫和硫酸根,经过试验得出结论,硫含量是这两种的综合,活性硫含量则是原油中硫含量之差,也得出原油腐蚀的顺序:哈油I>俄油II>哈油II>俄油I,在室温下,这四种油在200和400小时后没有发生腐蚀,没有很大的变化,但是时间增长后续,钢板就会有质量减少,腐蚀就会产生了。腐蚀作用与时间和温度有一定的关系,原油也和设备的材料有很大的关系。
关键词:原油硫 腐蚀性 管道
一、研究腐蚀现状的发展趋势
国内现行的腐蚀标准《钢质管道及储罐腐蚀控制工程设计规范》,管道壁的腐蚀控制污染要求,决定需要采取腐蚀和隔离的情况。也得出相应的措施。输送介质的标准发现,现在我们达不到国家的需要,级别的分级相差也很大,根据不同的级别选择不同的策略来预防,先前国内的腐蚀标准很少,但是现在我们在不断的研究和发展,控制的方法和指标更加详细和有效,我国的油质量很好,并没有对这些进行研究,输油的设备腐蚀问题相应的也会加大,我们的腐蚀研究很少,我们国家有统一的用油标准,但是各个企业对油质量的标准是不同的,也没有采用什么措施来防备油的腐蚀,也不知道油中的微生物也会带来一定程度的腐蚀,少数的企业知道,但是也只是添加一些缓蚀剂和灭菌剂等等。
(文章来源于:长沙制卡 )
影响原油的硫化物的腐蚀有温度、含水量、流速、氯离子和PH值的因素,这些因素对研究原油是最为基本的。
储存罐、加热炉和换热器都是输油的设备,这些设备的腐蚀程度会依据使用条件和使用产生不同的结果,原油中含有一些污水时,腐蚀的速度会很快,在较短的时间内可能发生管道的腐蚀,造成了穿孔,造成严重的泄漏。腐蚀严重的设备则不能再使用,使用寿命就会缩短,如果不能及时的提供有效的措施,可能造成更为严重的事故,直接威胁着企业的安全生产。
加工高含硫原料对装置的影响和对策

加工高含硫原料对装置的影响和对策景录昌中石化金陵分公司(南京210033)摘要金陵分公司作为集团公司进口油加工基地,原料硫含量逐年上升,RFCC作为分公司重油加工的要紧装置之一,硫对装置的阻碍越来越明显,本文将就硫对装置的阻碍,降低产品硫含量和减少硫污染的手段进行调研并简要分析。
关键词高硫原料污染汽油总硫腐蚀1 前言中国石化金陵分公司是一个大型燃料型原油加工基地,依照集团公司的“十五”规划,金陵分公司作为进口油加工基地,“十五”末,高含硫原油加工能力将达到500万吨/年,占加工能力的50%,这其中的绝大部分今后自中东地区。
重油催化装置是按照处理管输蜡油与渣油的混合料而设计的,其设计的原料硫含量只有0.54 %。
而中东原油如典型的沙特轻质原油硫含量为1.7%,中质、重质原油硫含量达2.8%,其催化原料硫含量将达到2%~3%,远远高出装置设计值。
原料中硫杂质的存在不仅阻碍产品质量,对设备腐蚀、环境污染和安全生产也构成一定的威逼。
2 硫在加工过程中分布及危害2.1 硫在加工过程中的分布在催化裂化过程中,原料油中的硫化物以不同形式转化分布到裂化产品中,对产品质量和环境造成一定污染。
清晰地了解和把握了催化裂化过程中硫分布规律,能够估算出再生烟气、酸性气、汽油、柴油中的硫含量,为满足产品质量的要求、防止大气污染、减缓设备腐蚀而采取相应的措施。
表1为国内部分催化裂化装置的硫分布。
从表中能够发觉,硫在气体产品中达到40%以上,催化裂化要紧产品汽油硫含量为原料硫含量的7%~10%(与汽油馏分的切割范畴有关)。
2.2 RFCC装置原料硫含量的变化及装置硫平稳表2是金陵分公司重油催化裂化装置的原料硫分析数据,说明原料硫含量总体呈上升趋势,缘故是进厂原油品种发生了变化,进口原油比例增加,表3为2000年装置硫平稳标定数据。
表2 原料硫含量分析数据时刻1999-06 2000-01 2000-06 2000-10 2001-01 2001-06 2001-09 2002-06硫含0.590.550.580.640.500.650.80.87量,%从表3能够看到,在装置加工过程中,有约50%的硫以硫化氢的形式去硫磺回收制硫,其余的硫则随产品带出,在产品使用中以SO X的方式排入大气,造成污染。
加工高硫高酸原油注意事项

加工高硫、高酸原油注意事项常减压装置单独加工马瑞油,硫含量高达2.9%并含有硫化氢,给储运、装置加工带来很大安全隐患,并且严重影响产品质量,各生产环节要注意防止硫化氢中毒,装置要24小时不间断巡检。
对加工高硫、高酸原油安全注意事项重申如下:高硫高酸原油对装置的影响:高硫、高酸原油中的比重大、硫含量和重金属含量高,深度脱盐较为困难。
加工这类原油能够造成设备腐和催化剂中毒以及环境污染。
如电脱盐装置会因原油乳化而影响脱盐效果,从而造成分馏塔顶腐性,还会造成分馏塔、加热炉等设备高温部位的腐蚀。
加工高酸原油带来的腐性问题主要集中在蒸馏装置,而加工高硫原油带来的腐性问题,贯穿于整个原油加工过程中。
高温硫化物的腐性是指240℃以上的部位元素硫、硫化氢和硫醇等形成的腐蚀。
典型的高温硫化物腐蚀存在于常、减压塔的下部及塔底管线,常压渣油和减压渣油换热器,催化裂化装置分馏塔的下部,以及焦化装置高温部位等。
在高温条件下,活性硫与金属直接反应它出现在与物流接触的各个部位,表现为均匀腐性,其中以硫化氢的腐位性最强。
燃料重油中通常含有1%-3%的硫及硫化物,在燃烧中大部分生成SO2,其中约有1%-5%在一定条件下反应生成SO3,对设备几乎不发生腐性,但当它与烟气中的水蒸汽结合形成硫酸蒸汽时,在装置的落点部位发生凝结,严重腐蚀设备。
环烷酸腐蚀经常发生在酸值大于0.5mgKOH/g, 温度在270-400℃之间高流速介质中。
它与金属表面或硫化铁膜直接反应生成环烷酸铁,环烷酸铁是油溶性的,再加上介质的流动,使金属表面不断暴露并受到腐性,故环烷酸腐蚀的金属表面清洁,光滑无垢。
在物料的高温高流速区域,环烷酸腐呈顺流向产生的尖锐边缘的流线沟槽,在低流速区域,则呈边缘锐利的凹坑状。
环烷酸腐蚀都发生在塔盘、塔壁、转油线等部位。
另外由于环烷酸盐具有表面活性,会造成油品乳化,从而引起装置操作波动,并造成塔顶腐蚀。
装置在加工此类原油时要做好安全防范措施并从生产工艺上进行调整,保证产品质量合格和污水处理合格。
含硫原油对炼油设备的腐蚀与对策

含硫原油对炼油设备的腐蚀与对策摘要:在实际的炼油中,经常会有含硫原油和高含硫原油需要加工,这种原油对炼油设备的腐蚀是剧烈的,生产中需要提出有效可行的办法来减少腐蚀保证生产。
关键词:腐蚀硫化物对策目前含硫原油尤其是高含硫原油大大的超过了设备要求含硫量的设计值。
在加工这些原油的过程中就会产生大量的硫化氢,对炼油设备、管路等都带来了极大的腐蚀,严重的甚至会造成安全事故。
因此,如何做好含硫原油加工的防腐工作就成为了眼前必要的课题。
本文主要是从腐蚀的情况、腐蚀机理出发来讨论相关的应对策略。
一、腐蚀情况原油中的硫包括了多种形式:元素硫、硫化氢、硫醇、硫醚、二硫化物、咪吩类化合物,以及分子量大、结构复杂的含硫化合物。
根据原油中硫含量的不同可以分为超低硫原油(S2 ),一般将原油中存在的硫分为活性硫和非活性硫,,元素硫、硫化氢和低分子硫醇等能直接与金属作用而引起设备的腐蚀,统称为活性硫,其余不能直接与金属作用的硫化物统称为非活性硫。
在实际的加工过程中,非活性硫还有可能转变成为活性硫,,使得硫腐蚀会从一次加工装置转移到二次加工装置,甚至逐渐延伸到下游的化工装置。
加上硫腐蚀与氧化物、氯化物、氮化物、氰化物等腐蚀介质的共同作用,形成了错综复杂的腐蚀体系,炼厂装置设备管线因此而发生腐蚀,造成泄漏而停工检修,甚至导致发生安全事故,严重影响生产的稳定运行。
另外腐蚀也是造成企业运营成本的一个重要因素,出现的腐蚀导致了设备的使用寿命减少,维修次数和费用增加,从经济方面考虑也急需控制好设备的腐蚀情况。
二、腐蚀机理在炼油过程中,存在于原油中的各种硫化物会在加工过程分解成硫化氢,从而对设备进行腐蚀,腐蚀的形式也是具有多样性,包括全面腐蚀、坑蚀、氢鼓泡、氢诱发阶梯裂纹、氢脆及硫化物应力腐蚀破裂等。
1.HCI-H2S-H2OS腐蚀此类腐蚀主要是由于无机盐与原油中的硫反应而造成的。
无机盐包括NaCl、MgCI2、CaCI2等盐类,经加热水解后与硫生成氯化氢,而硫化物就会分解生成硫化氢。
含硫含酸原油腐蚀问题和对策论文
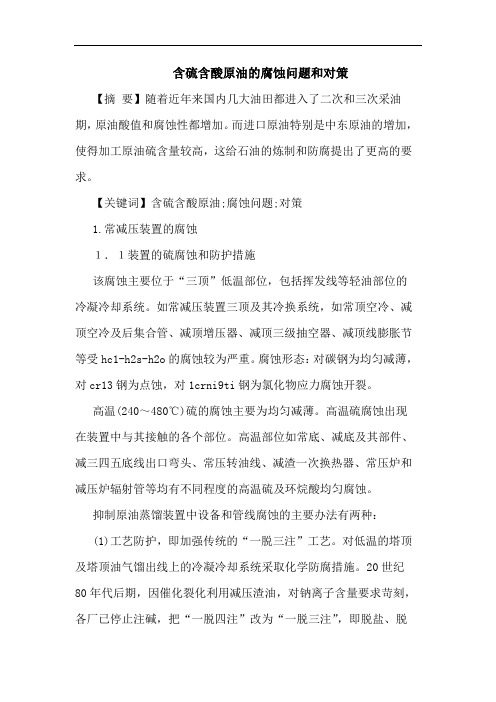
含硫含酸原油的腐蚀问题和对策【摘要】随着近年来国内几大油田都进入了二次和三次采油期,原油酸值和腐蚀性都增加。
而进口原油特别是中东原油的增加,使得加工原油硫含量较高,这给石油的炼制和防腐提出了更高的要求。
【关键词】含硫含酸原油;腐蚀问题;对策1.常减压装置的腐蚀1.1装置的硫腐蚀和防护措施该腐蚀主要位于“三顶”低温部位,包括挥发线等轻油部位的冷凝冷却系统。
如常减压装置三顶及其冷换系统,如常顶空冷、减顶空冷及后集合管、减顶增压器、减顶三级抽空器、减顶线膨胀节等受hc1-h2s-h2o的腐蚀较为严重。
腐蚀形态:对碳钢为均匀减薄,对cr13钢为点蚀,对1crni9ti钢为氯化物应力腐蚀开裂。
高温(240~480℃)硫的腐蚀主要为均匀减薄。
高温硫腐蚀出现在装置中与其接触的各个部位。
高温部位如常底、减底及其部件、减三四五底线出口弯头、常压转油线、减渣一次换热器、常压炉和减压炉辐射管等均有不同程度的高温硫及环烷酸均匀腐蚀。
抑制原油蒸馏装置中设备和管线腐蚀的主要办法有两种:(1)工艺防护,即加强传统的“一脱三注”工艺。
对低温的塔顶及塔顶油气馏出线上的冷凝冷却系统采取化学防腐措施。
20世纪80年代后期,因催化裂化利用减压渣油,对钠离子含量要求苛刻,各厂已停止注碱,把“一脱四注”改为“一脱三注”,即脱盐、脱水、注中和剂和水等。
提高深度电脱盐的合格率,对后续防腐的控制十分关键。
目前炼油厂常减压蒸馏装置“三顶”大部分采用注氨,但中和效果差,必须过量注入。
生成的nh4cl容易结垢,形成垢下腐蚀,并容易堵塞管道。
注入缓蚀剂是在金属表面形成保护膜,使金属不被腐蚀。
有炼厂注有机胺,中和效果好,但有机胺价格贵,因此,有炼厂采用胺和有机胺混注的方式,效果也很好。
国内有开发的中和缓释剂,一剂多用,应用效果也很好,但加入量较大,成本并不合算。
(2)对温度大于250℃的塔体和塔底出口系统的设备和管线等高温部位的防腐措施,主要是选用合适的耐蚀材料。
炼油厂加工高硫高酸值原油遇到的问题及对策
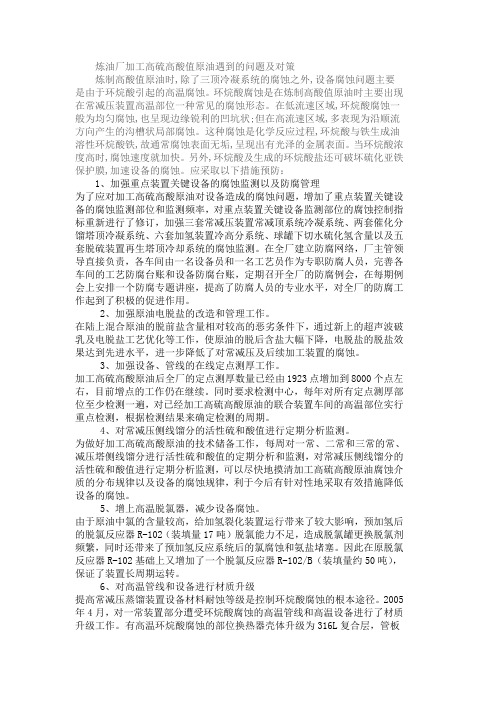
炼油厂加工高硫高酸值原油遇到的问题及对策炼制高酸值原油时,除了三顶冷凝系统的腐蚀之外,设备腐蚀问题主要是由于环烷酸引起的高温腐蚀。
环烷酸腐蚀是在炼制高酸值原油时主要出现在常减压装置高温部位一种常见的腐蚀形态。
在低流速区域,环烷酸腐蚀一般为均匀腐蚀,也呈现边缘锐利的凹坑状;但在高流速区域,多表现为沿顺流方向产生的沟槽状局部腐蚀。
这种腐蚀是化学反应过程,环烷酸与铁生成油溶性环烷酸铁,故通常腐蚀表面无垢,呈现出有光泽的金属表面。
当环烷酸浓度高时,腐蚀速度就加快。
另外,环烷酸及生成的环烷酸盐还可破坏硫化亚铁保护膜,加速设备的腐蚀。
应采取以下措施预防:1、加强重点装置关键设备的腐蚀监测以及防腐管理为了应对加工高硫高酸原油对设备造成的腐蚀问题,增加了重点装置关键设备的腐蚀监测部位和监测频率,对重点装置关键设备监测部位的腐蚀控制指标重新进行了修订,加强三套常减压装置常减顶系统冷凝系统、两套催化分馏塔顶冷凝系统、六套加氢装置冷高分系统、球罐下切水硫化氢含量以及五套脱硫装置再生塔顶冷却系统的腐蚀监测。
在全厂建立防腐网络,厂主管领导直接负责,各车间由一名设备员和一名工艺员作为专职防腐人员,完善各车间的工艺防腐台账和设备防腐台账,定期召开全厂的防腐例会,在每期例会上安排一个防腐专题讲座,提高了防腐人员的专业水平,对全厂的防腐工作起到了积极的促进作用。
2、加强原油电脱盐的改造和管理工作。
在陆上混合原油的脱前盐含量相对较高的恶劣条件下,通过新上的超声波破乳及电脱盐工艺优化等工作,使原油的脱后含盐大幅下降,电脱盐的脱盐效果达到先进水平,进一步降低了对常减压及后续加工装置的腐蚀。
3、加强设备、管线的在线定点测厚工作。
加工高硫高酸原油后全厂的定点测厚数量已经由1923点增加到8000个点左右,目前增点的工作仍在继续。
同时要求检测中心,每年对所有定点测厚部位至少检测一遍,对已经加工高硫高酸原油的联合装置车间的高温部位实行重点检测,根据检测结果来确定检测的周期。
浅析高硫原油对炼油设备的腐蚀与防护

浅析高硫原油对炼油设备的腐蚀与防护Abstract This article describes the corrosion characteristics of Middle East crude oil,main types of sulphide cor rosion and relevant preventive measures as well as the way to strengthen the cor rosion preventing research and implement scientific management.1 概述广州石油化工总厂经过二期扩建和改造,原油处理能力已达770万t/a,原油来源多数为进口原油,1997年原油进口量达总处理量的97%,预测亚太地区石油产量日趋减少,中东地区,特别是沙特原油仍稳定供应,中东原油占世界贮量的65%。
由于中东原油普遍含硫高且价格相对较低,所以广石化总厂选择炼中东高硫原油的比例越来越多,从而造成炼油装置中硫的腐蚀将越加严重。
需要尽快对设备防腐蚀问题进行深入研究,正确选择有关装置的设备材料及防腐措施,确保加工含高硫原油装置的正常运转。
2 中东油的腐蚀特点2.1含硫原油的腐蚀源原油中的硫化物主要有硫醇(RSH)、硫醚(RSR')、硫化氢(H2S)、多硫化物(RMS N )等。
这些硫化物中参与腐蚀反应的主要是H2S、S、RSH和易分解成H2S的硫化物,一般称其为腐蚀源或活性硫。
不同的原油所含硫化物的组成不同,即使总含量接近,在加工过程中生成的活性硫化物量也可能出现较大的差别。
如图1所示。
以含硫相近的阿拉伯原油(含硫1.7%)与伊朗原油(含硫1.4%)相比,在250~330℃馏分中的H2S含量,阿拉伯原油高达180mg/L,而伊朗原油只有20mg /L,就是说该馏分所在常减压分馏塔部位前其腐蚀基本没有,而炼阿拉伯原油时要比炼伊朗原油时产生H2S含量严重得多.硫含量不同的原油,腐蚀部位也不一样。
炼制高硫原油对设备的腐蚀与安全对策

收到初稿:2002203228;收到修改稿:2002207208作者简介:卜全民,男,1976年生,硕士生Tel :025-******* E -mail :buquanmin @炼制高硫原油对设备的腐蚀与安全对策卜全民 温 力 姜 虹 崔克清南京工业大学安全工程研究所南京210009摘要 介绍了炼制高硫原油对设备的危害性,并着重论述了炼制高硫原油的安全对策.关键词 高硫原油 加工 腐蚀 安全对策中图分类号 TQ441.12;TQ086.3 文献标识码 A 文章编号 100226495(2002)0620362203ON HIGH-SU LFUR CRU DE OI L IN D UCED CORR OSION OF PR OCESSING EQUIPMENT AN D COUNTERMEASURESBU Quanhmin ,WEN Li ,J IAN G Hong ,CU I KeqingInstitution of S af ety Engineering ,N anjing U niversity of Technology ,N anjing 210009ABSTRACT The harmful effect of high sulfur containing crude oil on the processing facilities of re 2fineries was summerized and the emphasis is placed on the countermeasures for giving assurance of safe 2ty operation.KE Y WOR DS high -sulfur crude oil ,processing ,corrosion ,safety countermeasures 近年来,国内原油产量已不能满足原油加工能力的要求,进口原油加工量逐年增加,已占原油加工总量的40%左右.国际上多把含硫量大于2%的原油称为高硫原油〔1〕,而把含硫量在015~210%的原油称为含硫原油.一般说来,含硫量在1%以上的原油在加工过程中就会引起严重的腐蚀问题,所以在行业内部又把含硫量在1%以上的原油泛称为高硫原油〔2〕.典型含硫原油的含硫分布情况如表1列出的10种情况〔3〕.由表1中典型含硫原油的分布情况数据可以看出:中东原油含硫量高,尤其是重质原油.我国进口原油绝大多数是中东原油,因此,在加工炼制过程中,产生的设备及管线腐蚀问题相当严重,从而导致一系列由于硫腐蚀而引发的各类事故和潜伏的隐患,对此必须给予高度的重视并采取有效的安全防范措施.1腐蚀机制原油中的硫包括元素硫、硫化氢、硫醇以及分子量大、结构复杂的含硫化合物.通常将原油中的元素硫、硫化氢和低分子硫醇等能直接与金属作用而引起设备腐蚀的,统称为活性硫;而其余不能直接与金属作用的硫化物统称为非活性硫.在加热炉出口温度为358℃~366℃时,高硫原油中硫化物分解产生的H 2S 量约占蒸馏塔顶瓦斯量的114%~311%.由于硫化氢呈弱酸性,在硫化氢的水溶液中,含有氢离子、硫化氢离子、硫离子和硫化氢分子,故可与金属产生化学反应,从而产生H 2S 腐蚀.原油中所含的CaCl 2和MgCl 2两种氯盐不仅在电脱盐过程中难以脱除,而且又极易产生水解,具有关资料介绍在炉出口温度(358℃~366℃)时,Mg 2Cl 2的水解率为95%,CaCl 2水解率约为10%,具体水解方程式如下:CaCl 2+H 2O →Ca (OH )2+2HClMgCl 2+H 2O →Mg (OH )2+2HCl故当脱盐达不到一定的深度时,即使氯化物含量降低很多,钙离子和镁离子的含量也不会降得太多〔4〕.产生的HCl 气体遇水形成盐酸后,其腐蚀性更强,其腐蚀原理按下反应式进行:Fe +2HCl →FeCl 2+H 2且盐酸的腐蚀主要在初凝相变区.在H 2S 的水溶液中,当有氯离子存在时,不仅H 2S 的腐蚀作用大大增强,而且HCl 也能破坏金属表面上已经生成的具有保护作用的硫化亚铁膜,使第14卷第6期2002年11月 腐蚀科学与防护技术CORR OSION SCIENCE AN D PR OTECTION TECHN OLOG Y Vol 114No 16Nov 12002T able1Distribution of typical crude oil containing sulfur序号原油名称原油含硫汽油含硫分布煤油含硫分布柴油含硫分布蜡油含硫分布减渣含硫分布1胜利1100010080102010120105013435100168171911547610 2伊朗轻11350105015011721111181515116216193105514 3伊朗重11780109017013231111449141187131531517319 4阿曼111501030130110811401488171110201121556915 5伊拉克轻1195010180120140741411127152142381241564915 6北海混合11230103401701414512111410121152341331214915 7卡塔塔尔1142010460180131317112410132109331831095114 8沙特轻质117501036014014331911217152148441541104315 9沙特中质214801034013016331511516123101351551515313 10沙特重质218301033012015421411484192185321161006014金属表面裸露于H2S的腐蚀环境中.促使H2S再次与Fe反应,并不断循环,其反应方程式如下: H2S+Fe→FeS+H2FeS+2HCl→FeCl2+H2S即使金属表面因腐蚀而生成氧化铁保护膜,氧化铁仍能溶于HCl,而生成FeCl3,其反应原理按下反应式进行:Fe2O3+6HCl→2FeCl3+3H2O而这些反应产物均易溶于水,因此H2S和HCl 可进一步与金属发生反应,故可对设备造成严重的腐蚀.2设备腐蚀在高硫原油的加工过程中,由于非活性硫不断向活性硫转变,使硫腐蚀不仅存在于一次加工装置,而且也存在于二次加工装置,甚至延伸到下游加工装置.因此,可以说硫腐蚀贯穿于炼油的全过程.同时硫腐蚀又与氧化物、氯化物、氮化物等腐蚀介质共同作用,形成一系列错综复杂的腐蚀体系.在炼油装置的低温部位、高温部位以及储运系统等均有腐蚀发生.常见腐蚀问题主要集中于以下环境:1脱硫、酸性水气提等装置的某些部位,其主要腐蚀环境为:H2S-CO2-乙醇胺-H2O;2常减压蒸馏装置的初馏塔、常压塔顶低温部位,包括挥发线等轻油部位的冷凝冷却系统,和催化重整装置的某些冷却系统,主要腐蚀环境为:H2S-HCl-H2O;3催化裂化、延迟焦化等二次加工装置的冷凝冷却系统,其主要腐蚀环境为:H2S-HCN-N H3-H2O;4加热炉、转化线、塔器、转换器等高温部位,其主要腐蚀环境为:高温硫和H2S;5其它还有低温部位的H2S-H2O和高温部位的H2S-H2及连多硫酸等腐蚀环境.总之,炼制高硫原油时,设备和装置的其它机械、配管由硫化物引起的各类腐蚀比原来要严重的多,必须给予足够的重视.3安全对策311提高装置的抗腐蚀能力对H2S浓度大于50mg/L的腐蚀环境,壳体宜选用抗拉强度不小于414MPa的碳钢或碳锰钢材料;对H2S浓度大于50mg/L且氰化物大于20mg/ L的腐蚀环境,壳体宜选用碳钢或碳锰钢+OCr13复合钢板,内件选用OCr13〔5〕.用碳锰钢作壳体材料时,由于Mn的偏析容易产生马氏体和贝氏体,使焊后组织增加开裂倾向,故含Mn的低合金钢不宜用于制造湿H2S环境中的压力容器.目前通用的做法是控制Mn含量,如国内的16MnR钢规定Mn的含量必须小于1160mass%,日本规定的Mn含量约为114mass%〔6〕.312采用“一脱三注”的防腐手段由于蒸馏装置塔顶腐蚀环境中氯离子浓度较高,再加上各种应力的影响,极易造成氯离子腐蚀开裂,因此低温轻油部位的材料升级难度较大,故采用“一脱三注”为核心内容的工艺防腐蚀手段显得异常重要,一脱即:脱硫,三注即:注胺(氨)、注缓蚀剂和注水.3636期卜全民等:炼制高硫原油对设备的腐蚀与安全对策 T able2Optimal pH valueHS,mg/L p H值(max)p H值20516511~51650514419~514100513418~513200511416~511在塔顶系统注氨水是国内控制p H值的常用方法,但也是设备发生垢下腐蚀的主要原因(约占设备腐蚀的80%),其腐蚀速度是均匀腐蚀的20倍.垢下沉积中的FeS约占70%~80%,FeS是原油塔顶系统中溶解度最低的盐,其溶解性取决于p H值和硫化物浓度.一些研究结果表明,塔顶系统最佳p H 值范围比推荐的范围(515~710)要低,如表2所示〔7〕.在此范围内操作,易于控制沉积物形成,从而减少中和剂用量,延长设备寿命.目前多数塔顶系统采用的p H值范围为511~516,即使在含硫量较高的情况下,p H值最低下限也不能低于416.313高温硫腐蚀对策在高温条件下,硫化氢与奥氏体不锈钢将发生化学反应生成硫化亚铁.为此,炼油装置的高温部位应可选用碳钢+OCr13或+OCr18Ni10Ti(SUS405)等铁素体不锈钢复合板.塔内件选用+ OCr13112AlMoV钢渗铝等,换热器的管子选用Cr5Mo和碳钢渗铝.塔体材料也可选择+ OCr18Ni10Ti(SUS321),其耐硫腐蚀和环烷酸腐蚀性要优于+OCr13或OCr13Al,并且加工性好.管线通常选用Cr5Mo防腐蚀是合适的,但对于转油线弯头等冲刷严重的部位,则应选用316L〔8〕.314高温烟气硫酸露点对策基于烟气在露点以上基本不存在硫酸露点腐蚀的问题,而采用在准确测定烟气露点的基础上,通过提高排烟温度以达到预防烟气露点腐蚀的目的.烧结合金涂层的方法也可解决高温烟气硫酸露点腐蚀的问题.烧结合金涂层即采用超合金化原理,在具有保护和还原环境中烧结而成,其最高使用温度在600℃左右,其导热性能也十分良好,与基体结合也极为紧密,从而也可达到预防烟气露点腐蚀的目的.4结束语炼制高硫原油不仅要根据原油的性质确定合理的加工流程和工艺,更要注意其对设备的要求以及对设备的腐蚀情况.为此,加工高硫原油时,应从源头、过程和后处理三方面综合考虑,重点解决好腐蚀严重、容易造成事故的重点装置和重点部位.参考文献:〔1〕崔克清主编.安全工程大词典.北京:化学工业出版社,1995.11〔2〕崔克清主编.化工安全技术.北京:化学工业出版社,1984.11〔3〕Ushlo M,K am iya K,Y oshlda T,et al.Production of High VI Base Oil by V G O Deep Hydrocaking.ACS(automatic controlsystem)Prepr,1998,37(4):1293〔4〕刘积贤.工业锅炉安全技术.北京:化学工业出版社,1999.3〔5〕崔克清主编.化工过程安全工程.北京:化学工业出版社, 2002.1〔6〕刘羽辉.金属材料物理性能检验标准工作手册.北京:技术标准出版社,1992.46〔7〕Hennico,Billon A,Bigenrd PH,et al.Revue de L’institute du Petrole,Princeton,1993,4:5〔8〕徐坚、戴新民、夏再筑.腐蚀金属学及耐腐蚀金属材料.杭州:浙江科学技术出版社,2001.6(上接第325页3结论在本实验条件下,含锌铬黄防锈颜料的环氧树脂涂层的老化过程实际是有机高分子进一步反应与分子键破坏的竞争过程;当老化时间一定时(672小时),含锌铬黄防锈颜料的环氧树脂涂层的最佳老化温度为80℃,老化温度越高,涂层耐蚀性能越差,但比不老化的涂层的耐蚀性能好;在涂层老化时间的筛选中,用EIS技术快速评价的结果与实际观察到的现象一致.参考文献:〔1〕M K endig,F Mansfeld.Corrosion,1983,39:466〔2〕F Mansfeld.Corrosion,1988,44:856〔3〕G Reinhard,V Rammelt,K Rammelt.Corrosion Science,1986, 26:109〔4〕F Mansfeld,M W K endig,S Tsai.Corrosion,1982,38:478〔5〕M K endig,J Scully.Corrosion,1990,46(1):22〔6〕M K endig,F Mansfeld,S Tsai,Corrosion Science,1983,23:317463腐蚀科学与防护技术第14卷。
浅谈原油加工中含硫酸性物质对设备的腐蚀与防护

浅谈原油加工中含硫酸性物质对设备的腐蚀与防护摘要:炼油厂进行原油加工,含硫酸性物质对于设备及管道的腐蚀不可避免。
通过讨论硫腐蚀的腐蚀机理,以及其对设备腐蚀所造成的危害,提出了设备防腐的工艺和措施。
关键词:炼油厂设备硫化氢腐蚀防腐Discussion on crude processing of sulfuric acid containing material corrosion and protection of equipmentAbstract:Refinery of crude oil processing,of sulfuric acid containing material for equipment and pipeline corrosion is inevitable.Through the discussion of sulfur corrosion corrosion mechanism,corrosion of equipment and its harm,put forward equipment Anti-corrosion Technology and measures.KeyWords:Oilrefinery;Equipment;Hydrogensulfide;Corrosion;Antic orrosive随着采油技术的不断进步,我国原油产量稳步增长,尤其是重质原油产量增长较快,使炼厂加工的原油种类日益复杂、性质变差、含硫量和酸值都有所提高。
因而在原油的加工处理过程中,含硫酸性物质对于设备的腐蚀不可避免。
近年来国内炼油厂在正常生产中由于硫腐蚀而引起的破裂、燃烧、爆炸等恶性事故频繁发生,甚至造成多人死亡,同时还导致严重的环境污染。
以玉门油田分公司炼油化工总厂为例,该炼化厂一脱硫再生系统于2005年7月建成投产,但该系统通过近年来的运行发现,系统腐蚀情况复杂,腐蚀程度严重,造成管线减薄乃至泄露、阀门故障、仪表失灵等问题,严重影响了正常的工作和生产。
高含硫原油接卸与储运过程的危害及防范措施

高含硫原油接卸与储运过程的危害及防范措施高含硫原油是指硫含量在0.5%以上的原油,属于中低硫原油。
高含硫原油的接卸与储运过程中存在着多种危害,对环境和人身安全造成潜在威胁。
制定有效的防范措施至关重要。
本文将从高含硫原油的危害、接卸与储运过程中的风险以及相应的防范措施等方面进行论述。
一、高含硫原油的危害1. 环境污染:高含硫原油在接卸和储运过程中,若发生泄漏、挥发或溢出,会对周围环境造成污染。
硫化物与空气中的水分、氧气结合生成二氧化硫,对大气造成污染;硫化物还会污染土壤和地下水,对植被和生态环境造成危害。
2. 健康危害:高含硫原油中的硫化氢是一种无色有毒气体,对人体呼吸道及消化系统有较强的刺激作用,严重时还会导致窒息、中毒甚至死亡。
接触高含硫原油的工作人员容易受到健康威胁。
3. 爆炸危险:高含硫原油中的硫化氢易燃易爆,一旦遇到明火或高温,容易引发爆炸、火灾事故,对周围区域和人员安全构成威胁。
1. 接卸过程中的危害:高含硫原油在接卸时,如管道、储罐或运输设备发生泄漏或溢出,会导致硫化氢等有毒气体释放,对接触人员造成威胁。
三、防范措施1. 接卸过程的防范措施:加强原油接卸工作人员的安全培训,提高其对高含硫原油的认识和防范意识;使用适当的个人防护装备,如防毒面具、防护服等;定期对接卸设备和管道进行检查和维护,及时消除潜在的泄漏隐患。
2. 储运过程的防范措施:严格遵守储运设施操作规程,如定期检查储罐、管道等设施,及时消除漏点和破损;使用先进的监测设备,对储运设施进行实时监控,及时发现异常情况;设立安全防护区域,对储运区域进行安全隔离,确保人员安全。
3. 应急处理措施:建立完善的应急处理预案,对高含硫原油泄漏、泄露等突发情况进行预案演习和应急处置演练,提高工作人员的应急处理能力;配备应急处理装备和药品,在发生事故时能够及时采取有效的应急处理措施。
高含硫原油接卸与储运过程中存在着多种潜在危害,需采取有效的防范措施来保障环境和人身安全。
炼制含硫原油对硫黄回收装置的影响

炼制含硫原油对硫黄回收装置的影响摘要:目前石油化工企业在进行炼制含硫原油的时候,会使用炼油装置工艺,由于工艺落后,设备以及安全等等都会出现隐患。
根据目前中石化股份有限公司所采用的硫磺回收装置展开分析,对其进行合理调节,对炼油质量适当提升,避免在炼油时掺杂一些劣质硫原油,在提炼中一定要加强巡检,并且密切注意鼓风机在工作中的输出电流,鼓风机在震动时产生的一系列状况要及时进行测定,以及记录。
根据工作时产生的变化,要对设备及时维护,并且对于容易腐蚀的零部件也要加强监测力度。
而能够完善管理体制,并且提升安全意识。
关键词:含硫原油;硫黄回收;对策引言:目前国内的国民经济在不断地发展,并且发展得非常迅速,所以人们的生产以及生活对于能源有很大的需求,进口原油目前数量在不断的增加,所以含硫原油也在不断的增加进口量。
目前原油资源比较重视质量,同时也重视硫含量,在进行深加工时,需要提升环保意识,所以硫磺回收装置要不断的扩大规模,要不断提升设计水准。
硫磺回收装置主要的作用是在进行炼油时,会产生硫化氢的酸性气,所以要是用较为合理的工艺方式,才能将硫磺进行回收,可达到清洁生产,还可以将废物变成有用的成分等。
但是制作工艺要满足产品质量的需求,所以回收装置在长期使用后会产生安全隐患。
对于硫磺产品目前的需求量比较大,所以产生市场价格不断被抬高,但是硫磺回收装置在炼制含硫原油中是非常必要的一种装置,会为企业生产带来更多的利。
一.我国炼油厂硫磺回收装置概况1.原油的硫含量原油主要包含三个部分,碳、氢、硫。
虽然硫磺的含量并不是最多,但却是原油中的重要成分,正常情况下,原油中含硫的数量应该在0.2%~0.5,个别原油中含硫量可达到7%。
原油中含硫的数量大多可分为低硫原油,其中硫的含量应该小于0.5%。
第二种是含硫原油,其中含硫磺的量应该在小于0.2%,但是会大于0.5%。
第三种是高硫原油,其中硫磺的含量已经大于2%。
目前在全球低硫原油达到17%,含硫原油达到31%,高硫原油达到60%。
含硫原油对催化裂化装置催化剂性能的影响分析

含硫原油对催化裂化装置催化剂性能的影响分析【摘要】催化裂化装置是石油加工中常用的重要设备,而含硫原油作为主要原料之一,在催化裂化过程中会对催化剂的性能产生影响。
本文通过分析含硫原油对催化剂性能的影响机理和处理技术,探讨了含硫原油深度加工中的问题与挑战。
结合催化剂再生技术的研究进展,对含硫原油对催化裂化装置催化剂性能的影响进行了综述。
未来研究可以进一步探索改进催化剂的设计和再生技术,以解决含硫原油加工带来的挑战。
本研究旨在为提高含硫原油加工效率和减少环境污染提供参考。
【关键词】关键词:含硫原油、催化裂化装置、催化剂、性能影响、机理分析、处理技术、深度加工、问题与挑战、再生技术、研究进展、综述、未来研究方向、结论总结。
1. 引言1.1 研究背景原油是石油加工产业的重要原料,其中硫含量是评价原油质量的重要指标之一。
含硫原油中的硫化物对催化剂具有一定的中毒作用,影响催化裂化装置的正常运行和催化剂的活性。
随着原油资源的逐渐枯竭和环境保护意识的增强,含硫原油的加工和利用已成为炼油行业亟待解决的重要问题。
传统的催化裂化装置在处理含硫原油时往往遇到催化剂中毒、活性降低、稳定性下降等问题,影响装置的运行效率和经济效益。
研究含硫原油对催化裂化装置催化剂性能的影响,探究其影响机理,寻找合适的处理技术和催化剂再生方法,对提高含硫原油加工的效率和质量具有重要意义。
本研究旨在深入探讨含硫原油对催化剂性能的影响机理,分析含硫原油处理技术对催化剂性能的影响,探讨含硫原油深度加工中存在的问题与挑战,总结催化剂再生技术的研究进展,为优化含硫原油加工工艺提供理论指导与技术支撑。
1.2 研究意义研究硫对催化裂化装置催化剂性能的影响具有重要的意义。
硫是原油中一种常见的杂质,其中的硫化物会对催化剂的活性和稳定性产生不利影响,降低催化剂的使用寿命,增加生产成本。
随着原油资源的逐渐枯竭,含硫原油的开采比例逐渐增加,因此研究含硫原油对催化剂性能的影响,有助于优化催化裂化装置的运行参数,提高生产效率。
掺炼高硫原油对催化重整装置的影响与防护

掺炼高硫原油对催化重整装置的影响与防护摘要对掺炼高硫原油造成催化重整装置硫腐蚀的机理和影响进行了详细分析,结合装置的生产实际情况,提出了相应的防护措施。
主题词催化重整装置高硫原油硫腐蚀影响防护1.前言哈尔滨石化公司2007年加工原油约300万吨,其中大庆原油200万吨、俄罗斯原油100万吨,掺炼比约33%。
与以往相比,原料组成发生了较大的变化,尤其是原料中的硫含量大幅度增加,对设备及管线的腐蚀将会加剧,从而给相关生产装置的安全平稳生产带来极大的隐患。
以下着重讨论掺炼高硫原油对催化重整装置的影响及防护措施。
2.原料性质对比哈尔滨石化公司以往所炼大庆原油平均含硫量为 0.16%(m/ m),为低硫-石蜡基原油,而从2005年4月份开始掺炼的俄罗斯瓦涅干油田原油平均含硫量为0.53%(m/ m),为含硫-中间基原油,全年混合原料平均含硫量为 0.33%(m/ m),硫含量增加了一倍之多,如此势必造成原料性质恶化。
掺炼高硫原油前后催化重整装置原料石脑油中硫含量对比见表1。
表1 硫含量对比油品单位掺炼前掺炼后石脑油 ppm 50~60 90~1403.硫腐蚀简述硫腐蚀在炼油的全过程都可能发生,腐蚀程度取决于含硫化合物的种类、含量和稳定性。
原料中参与腐蚀反应的有效硫化物如活性硫和易分解为H2S的硫化物含量越高,对设备、管线的腐蚀就越强。
而且在生产过程中,硫腐蚀并不是孤立存在的,含硫化合物与氧化物、氯化物、氮化物、氰化物、环烷酸和氢气等其它腐蚀性介质共同作用,形成多种复杂的含硫腐蚀环境,对设备、管线造成腐蚀破坏。
4.重点影响部位4.1 石脑油管线。
石脑油管线属于低温部位,在此温度下,大部分硫化物没有分解,由于石脑油中含水,在此部位多形成H2S-H2O型腐蚀,此种腐蚀较难以控制。
管线腐蚀一般造成两种后果:一是腐蚀管壁减薄产生漏点;二是腐蚀产生的FeS积聚堵塞管线设备。
重整装置石脑油管线近期频繁出现漏点,装置内尤为严重。
浅析炼制高硫原油的危险性及对策

As long as you do things with integrity, don't ask about success or failure.同学互助一起进步(页眉可删)浅析炼制高硫原油的危险性及对策1 前言长岭分公司原油车间担负着各生产装置原料油的供给任务。
随着分公司加工原油中含硫量的增加,使得车间各罐区内外的硫化氢含量严重超标的现象时有发生。
同时,分公司为追求效益最大化而实施的蜡油加氢、掺炼粗苯等一系列技改措施,也使得罐区储存高含H2S原料油的时间和次数越来越多。
因此,罐区发生硫化氢中毒事故的几率也随之增加,针对高硫原油的危险性制定相应的防治对策是保证罐区安全生产的必要工作。
2 H2S危害分析高硫原油在一次加工和后续加工工艺过程中产生的硫化氢不仅对催化裂化、加氢裂化、催化重整、加氢精制、焦化、减粘等生产装置设备的腐蚀十分明显,而且对储运设施的腐蚀也不容忽视。
加工过程中,储运设施中的轻油、污油和液态烃系统的气相腐蚀最为突出。
各种硫化物在加氢脱硫反应中生成的硫化氢,其腐蚀主要表现在气相腐蚀。
硫化氢与设备接触,生成金属硫化物,常见为硫化铁,常温下硫化铁与空气中的氧气接触,会发生氧化放热反应,发生自然事故。
如1998年2月20日某石化总厂油品车间1座2000m3的焦化汽油罐在送料过程中,因罐内壁硫化铁自然而发生油罐火灾。
1998年4月12日某石化公司炼油厂污水汽提装置1座10000m3含硫污水罐因内壁硫化铁自然突然发生火灾,均系硫化氢对罐的腐蚀所致。
原油车间各类设备被S腐蚀的现象也很严重,如:506#、507#、508#、620#、624#、611#、612#、701#、803#、805#、806#等油罐的罐顶都已被腐蚀穿孔,因生产需要又不能全部停用,给车间的计量安全提出了更为严格的要求。
车间现有5个罐区,油罐共54台,罐区计量仪表存在一些问题,有的计量仪表陈旧老化严重且没有配件;有的计量仪表经常出现故障,而维修力量跟不上,导致对这些油罐必须进行人工检尺;有的计量仪表误差大,导致计量不准,因此也必须进行检尺。
含硫原油对催化裂化装置催化剂性能的影响分析

含硫原油对催化裂化装置催化剂性能的影响分析【摘要】本文主要研究了含硫原油对催化裂化装置催化剂性能的影响。
在研究背景中介绍了催化裂化装置在石油加工中的重要性,并指出了含硫原油中硫对催化剂性能的影响。
通过分析含硫原油对催化剂活性、选择性、稳定性以及产物分布的影响机理,揭示了硫元素对催化剂性能的具体影响。
研究表明,含硫原油会降低催化剂的活性和选择性,同时影响催化剂的稳定性,导致催化剂寿命缩短。
本文总结了含硫原油对催化裂化装置催化剂性能的影响,同时展望了未来研究的方向,为优化催化裂化装置的性能提供了参考。
【关键词】含硫原油、催化裂化装置、催化剂性能、影响分析、机理、活性、选择性、稳定性、产物分布、总结、未来研究方向1. 引言1.1 研究背景催化裂化技术是一种重要的炼油过程,可以将重质石油馏分转化为轻质的高附加值产品,如汽油和石脑油。
由于原油中含有硫等杂质,这些杂质会对催化裂化装置中的催化剂产生不利影响。
含硫原油对催化剂的性能具有一定的影响,包括活性、选择性、稳定性以及产物分布等方面。
目前,全球范围内原油中硫含量逐年增加,原油的含硫量远高于过去。
这意味着催化裂化装置在处理含硫原油时面临更大的挑战。
研究含硫原油对催化裂化装置催化剂性能的影响具有重要意义。
通过深入探讨含硫原油对催化剂性能的影响机理,可以为优化工艺条件、改进催化剂设计以及提高产品质量提供理论依据。
本文旨在分析含硫原油对催化裂化装置催化剂性能的影响机理,及其对催化剂活性、选择性、稳定性以及产物分布的影响进行系统探讨,为进一步研究和优化催化裂化装置运行提供参考。
1.2 研究目的研究目的是为了探究含硫原油对催化裂化装置催化剂性能的影响机理,以解决在实际生产中常遇到的含硫原油对催化剂活性、选择性、稳定性以及产物分布等方面的影响问题。
通过深入分析含硫原油与催化剂之间的相互作用机制,可以为催化裂化装置的优化运行提供理论指导和技术支持。
研究目的还在于为未来的相关研究提供参考和借鉴,促进催化裂化技术的进步和发展。
高含硫原油接卸与储运过程的危害及防范措施

高含硫原油接卸与储运过程的危害及防范措施原油进口总量持续增长,特别是国外高含硫原油的不断开发和原油市场竞争的不断加剧,高含硫或硫化氢原油将会在未来进口原油中占据一定份额。
近年来,国家沿海原油口岸含硫原油接卸过程中发生多起硫化氢溢漏挥发事件,对当地环境和社会生活造成不利影响,因此,加强含硫化氢原油接卸、储运过程中的安全防护尤为重要。
原油进口;含硫化氢;原油接卸;储运过程;安全防护高含硫原油对石油加工和储运设备具有强烈的腐蚀作用,同时在原油的接卸过程中也存在泄漏的风险,一旦在接卸、输转高含硫原油过程中发生大量泄漏或不合理排放,不仅将会造成人、畜中毒事故的发生,而且由于硫的腐蚀,还会导致金属储罐、金属管道腐蚀开裂,严重影响企业的安全生产。
因此,加强对高含硫原油接卸、输转过程的风险控制尤为重要。
1含硫原油的分布及特性目前,含硫原油的产量已占世界原油总产量的75%,其中硫含量超过1%的原油占世界原油总产量的55%以上,硫含量超过2%的原油占30%以上[1]。
通常状况下,将硫含量低于0.5%的原油称为低硫原油,硫含量介于0.5%~2.0%的原油称为含硫原油,含硫量高于 2.0%的原油称为高硫原油。
进口原油产地主要分布在中东和非洲等国家和地区。
尤其是中东地区的进口原油占到原油进口总量的一半,该地区原油含硫量较高,因此,国家进口原油很大一部分是含硫原油和高含硫原油。
含硫原油中大都溶解硫化氢气体,特别是海上进口含硫原油,经过油轮长距离长时间运输,溶解的硫化氢气体更易挥发逸散。
因此,在进口原油接卸操作过程中,检测到的硫化氢浓度可能较高。
2含硫原油的危害硫化氢能溶于水、乙醇、汽油、煤油、原油等,与空气混合可形成爆炸气体,其爆炸极限为 4.3%~45.5%。
硫化氢比空气重,易积聚在低洼处,在受限空间内(如地势低洼、管沟、通风不良处)易造成人员中毒,而且可扩散范围大,能被远处的火源引燃。
硫化氢爆炸不仅会引起火灾,而且会产生有毒气体,比天然气或油品爆炸的危害更大。