PCB印制电路板表面镀镍工艺
PCB印制电路板表面镀镍工艺

1概述镍,元素符号Ni,原子量58.7,密度8.88g/cm3,Ni2+的电化当量1.095g /AH。
用于印制板的镍镀层分为半光亮镍(又称低应力镍或哑镍)和光亮镍两种。
主要作为板面镀金或插头镀金的底层,根据需要也可作为面层,镀层厚度按照IPC-6012(1996)标准规不低于2~2.5μm。
镍镀层应具有均匀细致,孔隙率低,延展性好等特点,而且低应力镍应具有宜于钎焊或压焊的功能。
2低应力镍2.1镀镍机理阴极:在阴极上,镀液中的镍离子获得电子沉积出镍原子,同时伴有少量氢气析出。
Ni2++2e+Ni0Ni2+/Ni=-0.25V2H++2e+H20Ni2+/N2=-0.0V虽然Ni的标准电极电位很负,但由于氢的过电位以及镀液中镍离子的浓度、温度、pH等操作条件的影响,阴极上析出氢极少,这时镀液的电流效率可达98%以上。
只有当pH很低时,才会有大量氢气析出,此时阴极上无镍沉积。
阳极:普通镀镍使用可溶性镍阳极。
阳极的主反响为金属镍的电化学溶解:Ni-2e→Ni2+当阳极电流密度过高,电镀液中又缺乏阳极活化剂时,阳极将发生钝化并伴有氧气析出:2H20-4e→02↑+4H+当镀液中有氯离子存在时,也可能发生析出氯气得反响:2C1--2e→C12↑阳极上金属镍电化学溶解使镍离子不断进入溶液,从而提供了阴极电沉积所需的镍离子。
但当阴极面积不够大或镀液中活化剂不够时,将导致阳极钝化而析出氧,生成的氧进步氧化阳极外表,生成棕色的Ni203氧化膜。
2Ni+3[O]→Ni2O3由于阳极钝化,使电流密度降低,槽电压升高,电能损失增加。
当使用高速镀镍工艺时,阳极采用非溶性材料如:铂、钛上镀铂网或钛上镀钌网,也可以采用含硫的活性镍阳极。
2.2镀液配方及操作条件2.3镀液配制1)在备用槽中,用热去离子水溶解计量的硫酸镍、氯化镍和计量1/2的硼酸。
2)加热至55~60℃,加活性炭3g/L,搅拌2h,静置2h,过滤,将无炭粒的溶液转人已清洗干净的工作槽中。
印制电路板化学镀镍金工艺知识

印制电路板化学镀镍金工艺知识在一个印制电路板的制造工艺流程中,产品最终之表面可焊性处理,对最终产品的装配和使用起着至关重要的作用。
综观当今国内外,针对印制电路板最终表面可焊性涂覆表面处理的方式,主要包括以下几种:Electroless Nickel and Immersion Gold (1)热风整平;(2)有机可焊性保护剂;(3)化学沉镍浸金;(4)化学镀银;(5)化学浸锡;(6)锡/ 铅再流化处理;(7)电镀镍金;(8)化学沉钯。
其中,热风整平是自阻焊膜于裸铜板上进行制作之制造工艺(SMOBC采用以来,迄今为止使用最为广泛的成品印制电路板最终表面可焊性涂覆处理方式。
对一个装配者来说,也许最重要的是容易进行元器件的集成。
任何新印制电路板表面可焊性处理方式应当能担当N次插拔之重任。
除了集成容易之外,装配者对待处理印制电路板的表面平坦性也非常敏感。
与热风整平制程所加工焊垫之较恶劣平坦度有关的漏印数量,是改变此种表面可焊性涂覆处理方式的原因之一。
镀镍/金早在70年代就应用在印制板上。
电镀镍/ 金特别是闪镀金、镀厚金、插头镀耐磨的Au-Co 、Au-Ni 等合金至今仍一直在带按键通讯设备、压焊的印制板上应用着。
但它需要“工艺导线”达到互连,受高密度印制板SMT安装限制。
90年代,由于化学镀镍/金技术的突破,加上印制板要求导线微细化、小孔径化等,而化学镀镍/金,它具有镀层平坦、接触电阻低、可焊性好,且有一定耐磨等优点,特别适合打线(Wire Bonding)工艺的印制板,成为不可缺少的镀层。
但化学镀镍/金有工序多、返工困难、生产效率低、成本高、废液难处理等缺点。
铜面有机防氧化膜处理技术,是采用一种铜面有机保焊剂在印制板表面形成之涂层与表面金属铜产生络合反应,形成有机物- 金属键,使铜面生成耐热、可焊、抗氧化之保护层。
目前,其在印制板表面涂层也占有一席之地,但此保护膜薄易划伤,又不导电,且存在下道测试检验困难等缺点。
PCB电镀工艺流程

PCB电镀工艺流程PCB电镀工艺流程是在印刷电路板(PCB)制造过程中的最后一个重要工艺环节。
电镀工艺主要是为了提高PCB的导电性能、耐腐蚀性和表面质量,以便满足电子产品中对高可靠性和耐久性的要求。
下面将详细介绍PCB电镀工艺的流程。
首先是预处理部分。
这一步骤主要是为了去除PCB表面的污垢、氧化物、油脂等杂质,以便于后续工艺的进行。
预处理通常包括以下几个步骤:1.清洁:使用溶液或化学品将PCB表面的污垢和油脂去除。
2.酸洗:使用酸性溶液去除PCB表面的氧化物和金属污染物。
3.去氧化:将PCB浸泡在去氧化溶液中,去除PCB表面的氧化层。
接下来是化学镀铜。
这是为了在PCB表面形成一层均匀的铜层,以提高PCB的导电性能。
化学镀铜通常分为以下几个步骤:1.均匀化处理:为了提供一个合适的表面形状和结构,以便于后续的电镀过程。
在这一步骤中,通常会在PCB表面涂覆一层金属催化剂。
2.化学镀铜:PCB浸入含有金属铜离子的电解液中,金属铜离子在电解液中被还原为铜金属,沉积在PCB表面。
3.沉积调节:通过调节电解液中的添加剂浓度和操作条件,控制铜层的均匀性和厚度分布。
然后是锡镀。
锡镀是为了提高PCB表面的耐腐蚀性和焊接性能。
锡镀通常包括以下几个步骤:1.表面处理:通过酸洗和化学活化处理,去除PCB表面的氧化物和污染物。
2.镀锡:PCB浸入含有锡离子的电解液中,锡离子在电解液中被还原为锡金属,在PCB表面生成均匀的锡层。
3.镀锡后处理:主要是通过热处理或化学处理,使锡层表面平整、致密,并提高焊接性能。
最后是金属保护层的制备。
这一步骤主要是为了保护PCB表面镀铜和镀锡层,防止其在运输和使用过程中受到腐蚀。
金属保护层通常包括以下几个步骤:1.表面处理:通过酸洗和化学活化处理,去除PCB表面的氧化物和污染物。
2.镀金属:PCB浸入含有金属离子的电解液中,金属离子在电解液中被还原为金属,沉积在PCB表面形成保护层。
3.镀金属后处理:通过热处理或化学处理,使金属保护层表面平整、致密,并提高耐腐蚀性能。
PCB电镀制程讲解
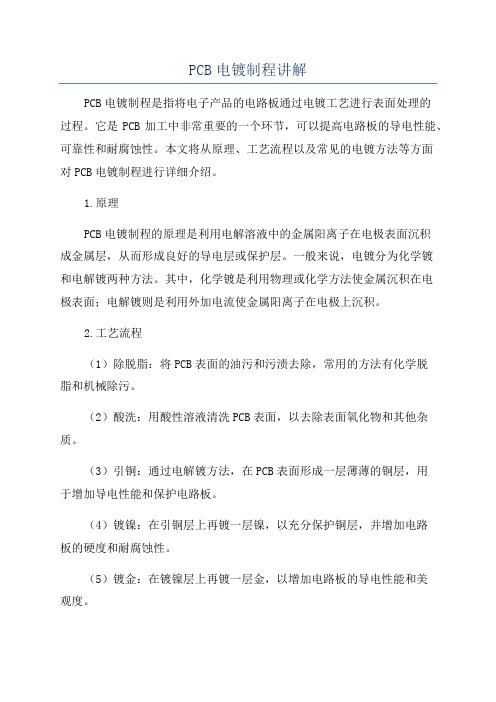
PCB电镀制程讲解PCB电镀制程是指将电子产品的电路板通过电镀工艺进行表面处理的过程。
它是PCB加工中非常重要的一个环节,可以提高电路板的导电性能、可靠性和耐腐蚀性。
本文将从原理、工艺流程以及常见的电镀方法等方面对PCB电镀制程进行详细介绍。
1.原理PCB电镀制程的原理是利用电解溶液中的金属阳离子在电极表面沉积成金属层,从而形成良好的导电层或保护层。
一般来说,电镀分为化学镀和电解镀两种方法。
其中,化学镀是利用物理或化学方法使金属沉积在电极表面;电解镀则是利用外加电流使金属阳离子在电极上沉积。
2.工艺流程(1)除脱脂:将PCB表面的油污和污渍去除,常用的方法有化学脱脂和机械除污。
(2)酸洗:用酸性溶液清洗PCB表面,以去除表面氧化物和其他杂质。
(3)引铜:通过电解镀方法,在PCB表面形成一层薄薄的铜层,用于增加导电性能和保护电路板。
(4)镀镍:在引铜层上再镀一层镍,以充分保护铜层,并增加电路板的硬度和耐腐蚀性。
(5)镀金:在镀镍层上再镀一层金,以增加电路板的导电性能和美观度。
(6)阻焊:在电路板的焊盘或导线上涂覆一层阻焊油墨,用于保护焊盘、防止短路和提供焊接位置。
(7)喷涂:根据需要,在电路板表面喷涂一层保护漆,以增加电路板的保护性能和耐热性。
(8)检验:对电路板进行严格的品质检测,确保其符合相应的标准要求。
3.常见的电镀方法(1)化学镀:利用化学反应使金属沉积在电极表面。
常见的化学镀有化学沉积铜、化学沉积镍、化学沉积金等。
化学镀的优点是能够形成钝化层,提高金属的耐腐蚀性。
(2)电解镀:利用外加电流使金属阳离子在电极上沉积。
常见的电解镀有电解铜、电解镍、电解金等。
电解镀的优点是能够形成均匀的金属层,提高电路板的导电性能和可靠性。
(3)电镍金:电镍金指将镍和金通过电解方法分层沉积在电路板表面。
这种方法可以在保证导电性能的同时,使电路板更具装饰性和耐腐蚀性。
综上所述,PCB电镀制程是电子产品制造中不可或缺的一环。
印制电路板(PCB)表面镀镍工艺(中)
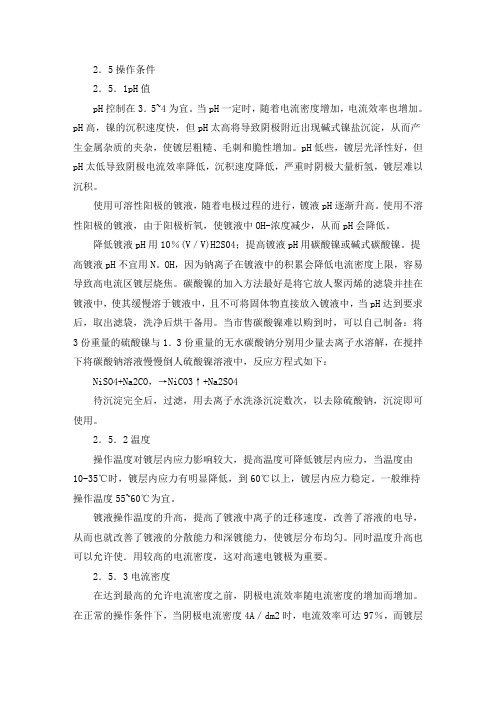
2.5操作条件2.5.1pH值pH控制在3.5~4为宜。
当pH一定时,随着电流密度增加,电流效率也增加。
pH高,镍的沉积速度快,但pH太高将导致阴极附近出现碱式镍盐沉淀,从而产生金属杂质的夹杂,使镀层粗糙、毛刺和脆性增加。
pH低些,镀层光泽性好,但pH太低导致阴极电流效率降低,沉积速度降低,严重时阴极大量析氢,镀层难以沉积。
使用可溶性阳极的镀液,随着电极过程的进行,镀液pH逐渐升高。
使用不溶性阳极的镀液,由于阳极析氧,使镀液中OH-浓度减少,从而pH会降低。
降低镀液pH用10%(V/V)H2S04;提高镀液pH用碳酸镍或碱式碳酸镍。
提高镀液pH不宜用N。
OH,因为钠离子在镀液中的积累会降低电流密度上限,容易导致高电流区镀层烧焦。
碳酸镍的加入方法最好是将它放人聚丙烯的滤袋并挂在镀液中,使其缓慢溶于镀液中,且不可将固体物直接放入镀液中,当pH达到要求后,取出滤袋,洗净后烘干备用。
当市售碳酸镍难以购到时,可以自己制备:将3份重量的硫酸镍与1.3份重量的无水碳酸钠分别用少量去离子水溶解,在搅拌下将碳酸钠溶液慢慢倒人硫酸镍溶液中,反应方程式如下:NiSO4+Na2CO,→NiCO3↑+Na2SO4待沉淀完全后,过滤,用去离子水洗涤沉淀数次,以去除硫酸钠,沉淀即可使用。
2.5.2温度操作温度对镀层内应力影响较大,提高温度可降低镀层内应力,当温度由10-35℃时,镀层内应力有明显降低,到60℃以上,镀层内应力稳定。
一般维持操作温度55~60℃为宜。
镀液操作温度的升高,提高了镀液中离子的迁移速度,改善了溶液的电导,从而也就改善了镀液的分散能力和深镀能力,使镀层分布均匀。
同时温度升高也可以允许使.用较高的电流密度,这对高速电镀极为重要。
2.5.3电流密度在达到最高的允许电流密度之前,阴极电流效率随电流密度的增加而增加。
在正常的操作条件下,当阴极电流密度4A/dm2时,电流效率可达97%,而镀层外观和延展性都很好。
电镀镍金工艺

还会使镀层脆性增加。
PH较低的镀镍液,阳极溶解较好,可以提高电解液中镍盐的含量,允许使用较高的电流密度,从而强化生产。
但是PH 过低,将使获得光亮镀层的温度范围变窄。
加入碳酸镍或碱式碳酸镍,PH值增加;加入氨基磺酸或硫酸,PH值降低,在工作过程中每四小时检查调整一次PH值。
c)阳极——目前所能见到的PCB常规镀镍均采用可溶性阳极,用钛篮作为阳极内装镍角已相当普遍。
其优点是其阳极面积可做得足够大且不变化,阳极保养比较简单。
钛篮应装入聚丙烯材料织成的阳极袋内防止阳极泥掉入镀液中。
并应定期清洗和检查孔眼是否畅通。
新的阳极袋在使用前,应在沸腾的水中浸泡。
d)净化——当镀液存在有机物污染时,就应该用活性炭处理。
但这种方法通常会去除一部分去应力剂(添加剂),必须加以补充。
其处理工艺如下;(1)取出阳极,加除杂水5ml/l,加热(60—80度C)打气(气搅拌)2小时。
(2)有机杂质多时,先加入3—5ml/lr的30%双氧水处理,气搅拌3小时。
(3)将3—5g/l粉末状活性在不断搅拌下加入,继续气搅拌2小时,关搅拌静置4小时,加助滤粉使用备用槽来过滤同时清缸。
(4)清洗保养阳极挂回,用镀了镍的瓦楞形铁板作阴极,在0.5—0.1安/平方分米的电流密度下进行拖缸8—12小时(当镀液存在无机物污染影响质量时,也常采用)(5)换过滤芯(一般用一组棉芯一组碳芯串联连续过滤,按周期性便换可有效延期大处理时间,提高镀液的稳定性),分析调整各参数、加入添加剂润湿剂即可试镀。
e)分析——镀液应该用工艺控制所规定的工艺规程的要点,定期分析镀液组分与赫尔槽试验,根据所得参数指导生产部门调节镀液各参数。
f)搅拌——镀镍过程与其它电镀过程一样,搅拌的目的是为了加速传质过程,以降低浓度变化,提高允许使用的电流密度上限。
对镀液进行搅拌还有一个十分重要的作用,就是减少或防止镀镍层产生针孔。
因为,电镀过程中,阴极表面附近的镀离子贫乏,氢气的大量析出,使PH值上升而产生氢氧化镍胶体,造成氢气泡的滞留而产生针孔。
(整理)印制电路板pcb表面镀镍工艺下
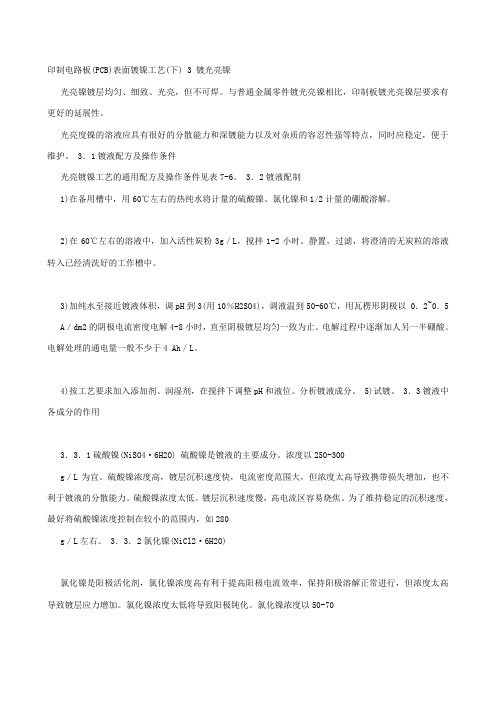
印制电路板(PCB)表面镀镍工艺(下) 3 镀光亮镍光亮镍镀层均匀、细致、光亮,但不可焊。
与普通金属零件镀光亮镍相比,印制板镀光亮镍层要求有更好的延展性。
光亮度镍的溶液应具有很好的分散能力和深镀能力以及对杂质的容忍性强等特点,同时应稳定,便于维护。
3.1镀液配方及操作条件光亮镀镍工艺的通用配方及操作条件见表7-6。
3.2镀液配制1)在备用槽中,用60℃左右的热纯水将计量的硫酸镍、氯化镍和1/2计量的硼酸溶解。
2)在60℃左右的溶液中,加入活性炭粉3g/L,搅拌1-2小时。
静置,过滤,将澄清的无炭粒的溶液转入已经清洗好的工作槽中。
3)加纯水至接近镀液体积,调pH到3(用10%H2SO4),调液温到50-60℃,用瓦楞形阴极以 0.2~0.5 A/dm2的阴极电流密度电解4-8小时,直至阴极镀层均匀一致为止。
电解过程中逐渐加人另一半硼酸。
电解处理的通电量一般不少于4 Ah/L。
4)按工艺要求加入添加剂、润湿剂,在搅拌下调整pH和液位。
分析镀液成分。
5)试镀。
3.3镀液中各成分的作用3.3.1硫酸镍(NiSO4·6H2O) 硫酸镍是镀液的主要成分。
浓度以250-300g/L为宜。
硫酸镍浓度高,镀层沉积速度快,电流密度范围大,但浓度太高导致携带损失增加,也不利于镀液的分散能力。
硫酸镍浓度太低。
镀层沉积速度慢,高电流区容易烧焦。
为了维持稳定的沉积速度,最好将硫酸镍浓度控制在较小的范围内,如280g/L左右。
3.3.2氯化镍(NiCl2·6H2O)氯化镍是阳极活化剂,氯化镍浓度高有利于提高阳极电流效率,保持阳极溶解正常进行,但浓度太高导致镀层应力增加。
氯化镍浓度太低将导致阳极钝化。
氯化镍浓度以50-70g/L为宜。
3.3.3硼酸(H2BO3) 硼酸是镀液的缓冲剂,其浓度40-50g/L为宜。
硼酸浓度太低,影响溶液的导电率,同时镀液缓冲效果差;提高硼酸浓度,溶液导电率提高,镀层均匀度改善。
pcb电镀原理
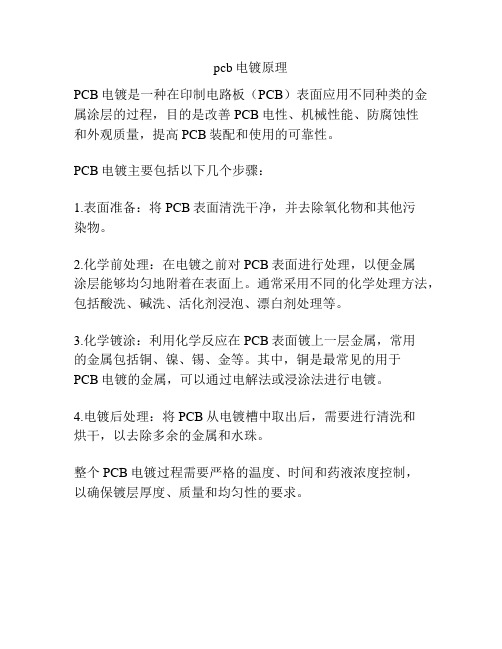
pcb电镀原理
PCB电镀是一种在印制电路板(PCB)表面应用不同种类的金属涂层的过程,目的是改善PCB电性、机械性能、防腐蚀性
和外观质量,提高PCB装配和使用的可靠性。
PCB电镀主要包括以下几个步骤:
1.表面准备:将PCB表面清洗干净,并去除氧化物和其他污
染物。
2.化学前处理:在电镀之前对PCB表面进行处理,以便金属
涂层能够均匀地附着在表面上。
通常采用不同的化学处理方法,包括酸洗、碱洗、活化剂浸泡、漂白剂处理等。
3.化学镀涂:利用化学反应在PCB表面镀上一层金属,常用
的金属包括铜、镍、锡、金等。
其中,铜是最常见的用于
PCB电镀的金属,可以通过电解法或浸涂法进行电镀。
4.电镀后处理:将PCB从电镀槽中取出后,需要进行清洗和
烘干,以去除多余的金属和水珠。
整个PCB电镀过程需要严格的温度、时间和药液浓度控制,
以确保镀层厚度、质量和均匀性的要求。
PCB印制电路板电镀铜及镍金工艺
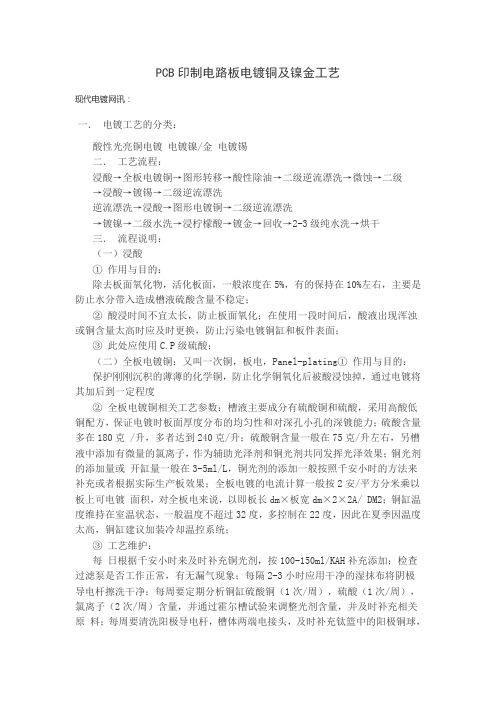
PCB印制电路板电镀铜及镍金工艺现代电镀网讯:一.电镀工艺的分类:酸性光亮铜电镀电镀镍/金电镀锡二.工艺流程:浸酸→全板电镀铜→图形转移→酸性除油→二级逆流漂洗→微蚀→二级→浸酸→镀锡→二级逆流漂洗逆流漂洗→浸酸→图形电镀铜→二级逆流漂洗→镀镍→二级水洗→浸柠檬酸→镀金→回收→2-3级纯水洗→烘干三.流程说明:(一)浸酸①作用与目的:除去板面氧化物,活化板面,一般浓度在5%,有的保持在10%左右,主要是防止水分带入造成槽液硫酸含量不稳定;②酸浸时间不宜太长,防止板面氧化;在使用一段时间后,酸液出现浑浊或铜含量太高时应及时更换,防止污染电镀铜缸和板件表面;③此处应使用C.P级硫酸;(二)全板电镀铜:又叫一次铜,板电,Panel-plating①作用与目的:保护刚刚沉积的薄薄的化学铜,防止化学铜氧化后被酸浸蚀掉,通过电镀将其加后到一定程度②全板电镀铜相关工艺参数:槽液主要成分有硫酸铜和硫酸,采用高酸低铜配方,保证电镀时板面厚度分布的均匀性和对深孔小孔的深镀能力;硫酸含量多在180克 /升,多者达到240克/升;硫酸铜含量一般在75克/升左右,另槽液中添加有微量的氯离子,作为辅助光泽剂和铜光剂共同发挥光泽效果;铜光剂的添加量或开缸量一般在3-5ml/L,铜光剂的添加一般按照千安小时的方法来补充或者根据实际生产板效果;全板电镀的电流计算一般按2安/平方分米乘以板上可电镀面积,对全板电来说,以即板长dm×板宽dm×2×2A/ DM2;铜缸温度维持在室温状态,一般温度不超过32度,多控制在22度,因此在夏季因温度太高,铜缸建议加装冷却温控系统;③工艺维护:每日根据千安小时来及时补充铜光剂,按100-150ml/KAH补充添加;检查过滤泵是否工作正常,有无漏气现象;每隔2-3小时应用干净的湿抹布将阴极导电杆擦洗干净;每周要定期分析铜缸硫酸铜(1次/周),硫酸(1次/周),氯离子(2次/周)含量,并通过霍尔槽试验来调整光剂含量,并及时补充相关原料;每周要清洗阳极导电杆,槽体两端电接头,及时补充钛篮中的阳极铜球,用低电流0。
PCB电镀镍金工艺介绍一、PCB电镀金工艺1、作用与特性PCB上用...
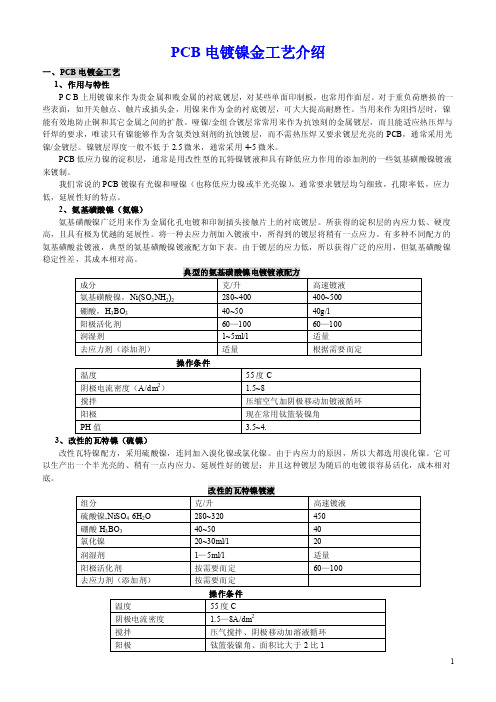
PCB电镀镍金工艺介绍一、PCB电镀金工艺1、作用与特性P C B上用镀镍来作为贵金属和贱金属的衬底镀层,对某些单面印制板,也常用作面层。
对于重负荷磨损的一些表面,如开关触点、触片或插头金,用镍来作为金的衬底镀层,可大大提高耐磨性。
当用来作为阻挡层时,镍能有效地防止铜和其它金属之间的扩散。
哑镍/金组合镀层常常用来作为抗蚀刻的金属镀层,而且能适应热压焊与钎焊的要求,唯读只有镍能够作为含氨类蚀刻剂的抗蚀镀层,而不需热压焊又要求镀层光亮的PCB,通常采用光镍/金镀层。
镍镀层厚度一般不低于2.5微米,通常采用4-5微米。
PCB低应力镍的淀积层,通常是用改性型的瓦特镍镀液和具有降低应力作用的添加剂的一些氨基磺酸镍镀液来镀制。
我们常说的PCB镀镍有光镍和哑镍(也称低应力镍或半光亮镍),通常要求镀层均匀细致,孔隙率低,应力低,延展性好的特点。
2、氨基磺酸镍(氨镍)氨基磺酸镍广泛用来作为金属化孔电镀和印制插头接触片上的衬底镀层。
所获得的淀积层的内应力低、硬度高,且具有极为优越的延展性。
将一种去应力剂加入镀液中,所得到的镀层将稍有一点应力。
有多种不同配方的氨基磺酸盐镀液,典型的氨基磺酸镍镀液配方如下表。
由于镀层的应力低,所以获得广泛的应用,但氨基磺酸镍稳定性差,其成本相对高。
3、改性的瓦特镍(硫镍)改性瓦特镍配方,采用硫酸镍,连同加入溴化镍或氯化镍。
由于内应力的原因,所以大都选用溴化镍。
它可以生产出一个半光亮的、稍有一点内应力、延展性好的镀层;并且这种镀层为随后的电镀很容易活化,成本相对底。
4、镀液各组分的作用:主盐──氨基磺酸镍与硫酸镍为镍液中的主盐,镍盐主要是提供镀镍所需的镍金属离子并兼起着导电盐的作用。
镀镍液的浓度随供应厂商不同而稍有不同,镍盐允许含量的变化较大。
镍盐含量高,可以使用较高的阴极电流密度,沉积速度快,常用作高速镀厚镍。
但是浓度过高将降低阴极极化,分散能力差,而且镀液的带出损失大。
镍盐含量低沉积速度低,但是分散能力很好,能获得结晶细致光亮镀层。
PCB化学镀镍金工艺介绍
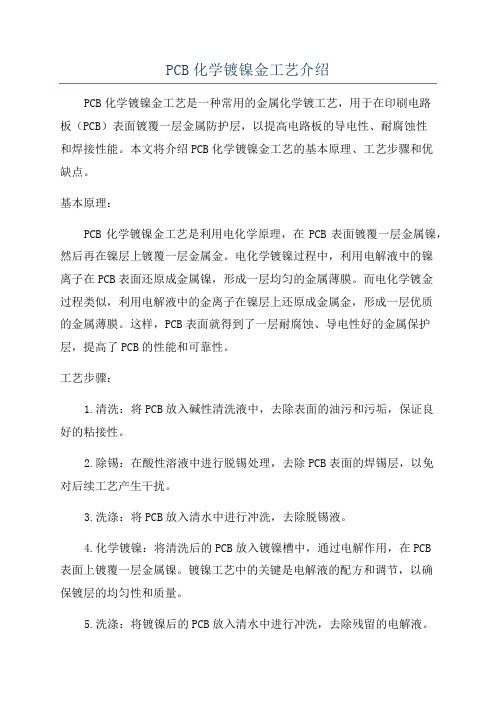
PCB化学镀镍金工艺介绍PCB化学镀镍金工艺是一种常用的金属化学镀工艺,用于在印刷电路板(PCB)表面镀覆一层金属防护层,以提高电路板的导电性、耐腐蚀性和焊接性能。
本文将介绍PCB化学镀镍金工艺的基本原理、工艺步骤和优缺点。
基本原理:PCB化学镀镍金工艺是利用电化学原理,在PCB表面镀覆一层金属镍,然后再在镍层上镀覆一层金属金。
电化学镀镍过程中,利用电解液中的镍离子在PCB表面还原成金属镍,形成一层均匀的金属薄膜。
而电化学镀金过程类似,利用电解液中的金离子在镍层上还原成金属金,形成一层优质的金属薄膜。
这样,PCB表面就得到了一层耐腐蚀、导电性好的金属保护层,提高了PCB的性能和可靠性。
工艺步骤:1.清洗:将PCB放入碱性清洗液中,去除表面的油污和污垢,保证良好的粘接性。
2.除锡:在酸性溶液中进行脱锡处理,去除PCB表面的焊锡层,以免对后续工艺产生干扰。
3.洗涤:将PCB放入清水中进行冲洗,去除脱锡液。
4.化学镀镍:将清洗后的PCB放入镀镍槽中,通过电解作用,在PCB表面上镀覆一层金属镍。
镀镍工艺中的关键是电解液的配方和调节,以确保镀层的均匀性和质量。
5.洗涤:将镀镍后的PCB放入清水中进行冲洗,去除残留的电解液。
6.电镀:将镀镍后的PCB放入金镀槽中,通过电解作用,在镀镍层上镀覆一层金属金。
和镀镍工艺一样,金镀工艺中的关键是电解液的配方和调节,以确保金属镀层的均匀性和质量。
7.洗涤:将金镀后的PCB放入清水中进行冲洗,去除残留的电解液。
8.烘干:将洗涤后的PCB放入烘干箱中进行烘干,去除水分,使PCB表面干燥。
优缺点:1.镀层均匀:化学镀镍金工艺能够在PCB表面形成一层均匀的镍层和金属金层,不仅提高了密着性,还提高了导电性能。
2.镀层良好的硬度:化学镀镍金镀层具有一定的硬度,提高PCB的耐磨、耐刮性能。
3.阻焊性好:镀金层在PCB表面形成一层阻焊层,提高了PCB的焊接性能和可靠性。
4.节省成本:与其他金属化工艺相比,化学镀镍金工艺更加节省成本,适用于大批量生产。
PCB电镀镍工艺详解

PCB图形电镀工艺流程

PCB图形电镀工艺流程PCB图形电镀是制造印制电路板时的重要工艺流程之一。
电镀工艺流程能够为PCB提供良好的导电性和耐腐蚀性,在电子产品中起到关键的作用。
下面将介绍一下PCB图形电镀的工艺流程。
首先,PCB进入电镀前会经过清洗工序,以去除表面污垢。
常用的清洗方式有化学清洗、喷洗清洗和超声波清洗等。
清洗工序的目的是为了保证电镀时的良好粘附性。
接下来,PCB会进入化学镀垫层的工序。
镀垫层的主要作用是增加PCB表面粘附力和电导性,以便更好地进行后续的电镀工艺。
常用的镀垫层材料有金、镍、锡等。
镀垫层工艺主要包括化学镀垫和电镀垫两种方式。
在化学镀垫工艺中,首先将金属盐溶液制备好,并调节好浓度和温度。
然后将PCB浸入溶液中,经过一段时间的处理,金属盐溶液中的金属离子会被还原成金属沉积在PCB表面。
最后再经过清洗和干燥等工序,形成均匀的金属薄层。
而电镀垫层工艺则是通过电化学的方式进行。
首先在PCB上涂覆一层金属催化剂,如钯金盐或铅盐等,然后将PCB浸入金属盐溶液中,通过电流作用,金属离子会被还原成金属沉积在PCB表面。
这种方法可以实现较厚的镀垫层。
完成了镀垫层工艺后,PCB会进入电镀层的工序。
电镀层主要是通过电化学方式,在PCB表面镀上一层金属保护层,以提高PCB的导电性和耐腐蚀性。
常用的电镀层材料有金、银、锡、铜等。
具体的电镀层工艺流程包括:首先是准备好金属盐溶液,调节好浓度和温度。
然后将PCB浸入溶液中,通过电流的作用,金属离子会被还原成金属离子在PCB表面沉积下来。
最后通过清洗和干燥等工序,形成均匀的电镀层。
最后,完成了上述工艺流程的PCB还需要进行检验和修复。
检验是为了确保PCB表面的镀层均匀且符合要求,常用的检验方法有厚度测量、锡膏检查、可焊性测试等。
如果发现镀层不符合要求,需要进行修复或重新进行电镀工序。
总之,PCB图形电镀是制造印制电路板的重要工艺流程之一。
通过化学镀垫和电镀垫两种方式,以及电化学的方式进行电镀层的制备,能够为PCB提供良好的导电性和耐腐蚀性。
印制电路板(PCB)表面镀镍工艺

印制电路板表面镀镍工艺在印制电路板(PCB)的制造过程中,表面镀镍工艺是一个至关重要的步骤。
镀镍可以提高PCB的耐腐蚀性能、焊接性能和导电性能,同时还可以有效防止金属之间的氧化反应,保持电路板的长期稳定性。
镀镍的作用提高PCB的耐腐蚀性能PCB在使用过程中易受到氧化、化学腐蚀等因素的影响,而表面镀上一层镍可以有效防止这些因素对PCB的侵蚀,延长PCB的使用寿命。
提高PCB的焊接性能PCB的焊接需要通过烙铁或波峰焊等方式进行,镀上一层镍可以提高PCB与焊接材料的粘附性,确保焊接效果的稳定和可靠。
提高PCB的导电性能镍是一种优良的导电金属,镀上镍可以提高PCB的导电性能,减少信号损耗,保证电路传输的准确性和稳定性。
防止金属之间的氧化反应PCB中金属之间的接触往往会引起氧化反应,造成连接不良或者虚焊等问题,而镀上一层镍可以有效隔绝金属之间的接触,避免氧化反应的发生。
镀镍工艺的步骤镀镍工艺通常包括以下几个步骤:1.准备工作:清洁PCB表面,去除表面的油污、氧化物等杂质,确保表面干净平整。
2.化学镀镍:将清洁后的PCB浸入镀液中,通过化学反应在PCB表面沉积一层均匀的镍层。
3.电镀:将化学镀镍后的PCB置于电镀槽中,通过电化学方法在PCB表面镀上一层致密且均匀的镍层。
4.清洗和干燥:将镀镍后的PCB进行清洗和干燥处理,确保PCB表面干净无杂质,保证镀层的质量和稳定性。
5.光刻和蚀刻:根据PCB设计要求进行光刻和蚀刻处理,将不需要的镀镍部分去除,得到最终的PCB产品。
镀镍工艺的发展趋势随着电子技术的不断发展,对PCB的要求也日益提高,镀镍工艺也在不断创新和改进。
未来,随着新型材料和新工艺的应用,镀镍工艺将更加环保、高效和智能化,为PCB的性能提升和品质保障提供更好的支持。
总之,印制电路板表面镀镍工艺在PCB制造中具有重要作用,不仅可以提高PCB的性能和稳定性,还可以保证电路传输的准确性和可靠性。
随着技术的不断进步,镀镍工艺将不断完善和创新,为PCB行业的发展贡献更多的力量。
PCB电镀镍工艺

PCB电镀镍工艺1、作用与特性P C B(是英文Printed Circuie Board印制线路板的简称)上用镀镍来作为贵金属和贱金属的衬底镀层,对某些单面印制板,也常用作面层。
对于重负荷磨损的一些表面,如开关触点、触片或插头金,用镍来作为金的衬底镀层,可大大提高耐磨性。
当用来作为阻挡层时,镍能有效地防止铜和其它金属之间的扩散。
哑镍/金组合镀层常常用来作为抗蚀刻的金属镀层,而且能适应热压焊与钎焊的要求,唯读只有镍能够作为含氨类蚀刻剂的抗蚀镀层,而不需热压焊又要求镀层光亮的PCB,通常采用光镍/金镀层。
镍镀层厚度一般不低于2.5微米,通常采用4-5微米。
PCB低应力镍的淀积层,通常是用改性型的瓦特镍镀液和具有降低应力作用的添加剂的一些氨基磺酸镍镀液来镀制。
我们常说的PCB镀镍有光镍和哑镍(也称低应力镍或半光亮镍),通常要求镀层均匀细致,孔隙率低,应力低,延展性好的特点。
2、氨基磺酸镍(氨镍)氨基磺酸镍广泛用来作为金属化孔电镀和印制插头接触片上的衬底镀层。
所获得的淀积层的内应力低、硬度高,且具有极为优越的延展性。
将一种去应力剂加入镀液中,所得到的镀层将稍有一点应力。
有多种不同配方的氨基磺酸盐镀液,典型的氨基磺酸镍镀液配方如下表。
由于镀层的应力低,所以获得广泛的应用,但氨基磺酸镍稳定性差,其成本相对高。
3、改性的瓦特镍(硫镍)改性瓦特镍配方,采用硫酸镍,连同加入溴化镍或氯化镍。
由于内应力的原因,所以大都选用溴化镍。
它可以生产出一个半光亮的、稍有一点内应力、延展性好的镀层;并且这种镀层为随后的电镀很容易活化,成本相对底。
4、镀液各组分的作用:主盐──氨基磺酸镍与硫酸镍为镍液中的主盐,镍盐主要是提供镀镍所需的镍金属离子并兼起着导电盐的作用。
镀镍液的浓度随供应厂商不同而稍有不同,镍盐允许含量的变化较大。
镍盐含量高,可以使用较高的阴极电流密度,沉积速度快,常用作高速镀厚镍。
但是浓度过高将降低阴极极化,分散能力差,而且镀液的带出损失大。
电镀镍工艺资料
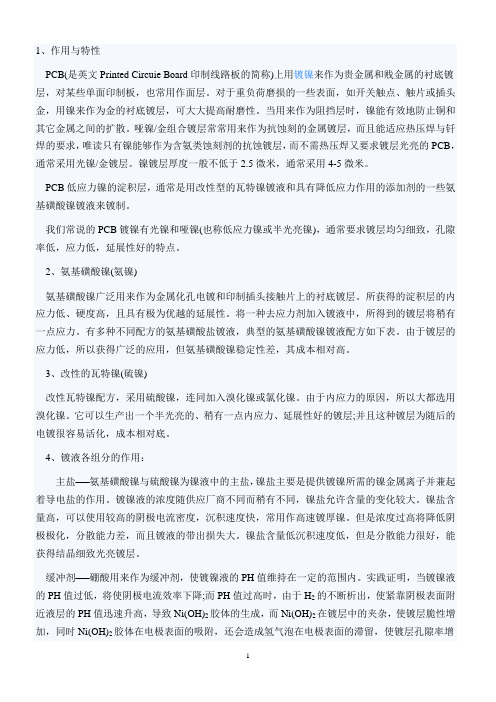
1、作用与特性PCB(是英文Printed Circuie Board印制线路板的简称)上用镀镍来作为贵金属和贱金属的衬底镀层,对某些单面印制板,也常用作面层。
对于重负荷磨损的一些表面,如开关触点、触片或插头金,用镍来作为金的衬底镀层,可大大提高耐磨性。
当用来作为阻挡层时,镍能有效地防止铜和其它金属之间的扩散。
哑镍/金组合镀层常常用来作为抗蚀刻的金属镀层,而且能适应热压焊与钎焊的要求,唯读只有镍能够作为含氨类蚀刻剂的抗蚀镀层,而不需热压焊又要求镀层光亮的PCB,通常采用光镍/金镀层。
镍镀层厚度一般不低于2.5微米,通常采用4-5微米。
PCB低应力镍的淀积层,通常是用改性型的瓦特镍镀液和具有降低应力作用的添加剂的一些氨基磺酸镍镀液来镀制。
我们常说的PCB镀镍有光镍和哑镍(也称低应力镍或半光亮镍),通常要求镀层均匀细致,孔隙率低,应力低,延展性好的特点。
2、氨基磺酸镍(氨镍)氨基磺酸镍广泛用来作为金属化孔电镀和印制插头接触片上的衬底镀层。
所获得的淀积层的内应力低、硬度高,且具有极为优越的延展性。
将一种去应力剂加入镀液中,所得到的镀层将稍有一点应力。
有多种不同配方的氨基磺酸盐镀液,典型的氨基磺酸镍镀液配方如下表。
由于镀层的应力低,所以获得广泛的应用,但氨基磺酸镍稳定性差,其成本相对高。
3、改性的瓦特镍(硫镍)改性瓦特镍配方,采用硫酸镍,连同加入溴化镍或氯化镍。
由于内应力的原因,所以大都选用溴化镍。
它可以生产出一个半光亮的、稍有一点内应力、延展性好的镀层;并且这种镀层为随后的电镀很容易活化,成本相对底。
4、镀液各组分的作用:主盐──氨基磺酸镍与硫酸镍为镍液中的主盐,镍盐主要是提供镀镍所需的镍金属离子并兼起着导电盐的作用。
镀镍液的浓度随供应厂商不同而稍有不同,镍盐允许含量的变化较大。
镍盐含量高,可以使用较高的阴极电流密度,沉积速度快,常用作高速镀厚镍。
但是浓度过高将降低阴极极化,分散能力差,而且镀液的带出损失大。
pcb线路板电镀工艺流程图
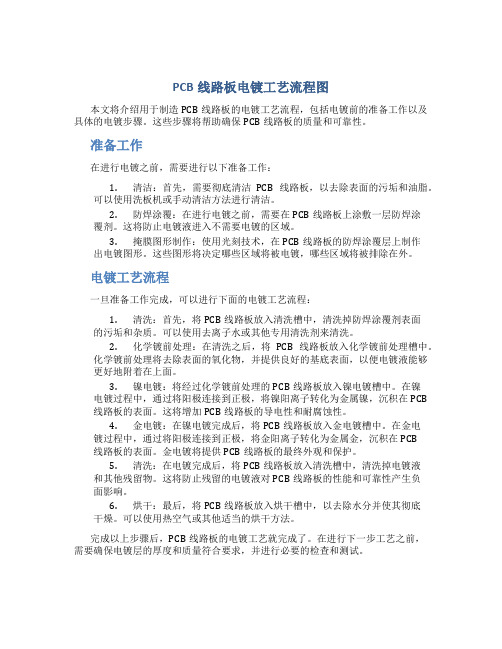
PCB线路板电镀工艺流程图本文将介绍用于制造PCB线路板的电镀工艺流程,包括电镀前的准备工作以及具体的电镀步骤。
这些步骤将帮助确保PCB线路板的质量和可靠性。
准备工作在进行电镀之前,需要进行以下准备工作:1.清洁:首先,需要彻底清洁PCB线路板,以去除表面的污垢和油脂。
可以使用洗板机或手动清洁方法进行清洁。
2.防焊涂覆:在进行电镀之前,需要在PCB线路板上涂敷一层防焊涂覆剂。
这将防止电镀液进入不需要电镀的区域。
3.掩膜图形制作:使用光刻技术,在PCB线路板的防焊涂覆层上制作出电镀图形。
这些图形将决定哪些区域将被电镀,哪些区域将被排除在外。
电镀工艺流程一旦准备工作完成,可以进行下面的电镀工艺流程:1.清洗:首先,将PCB线路板放入清洗槽中,清洗掉防焊涂覆剂表面的污垢和杂质。
可以使用去离子水或其他专用清洗剂来清洗。
2.化学镀前处理:在清洗之后,将PCB线路板放入化学镀前处理槽中。
化学镀前处理将去除表面的氧化物,并提供良好的基底表面,以便电镀液能够更好地附着在上面。
3.镍电镀:将经过化学镀前处理的PCB线路板放入镍电镀槽中。
在镍电镀过程中,通过将阳极连接到正极,将镍阳离子转化为金属镍,沉积在PCB 线路板的表面。
这将增加PCB线路板的导电性和耐腐蚀性。
4.金电镀:在镍电镀完成后,将PCB线路板放入金电镀槽中。
在金电镀过程中,通过将阳极连接到正极,将金阳离子转化为金属金,沉积在PCB线路板的表面。
金电镀将提供PCB线路板的最终外观和保护。
5.清洗:在电镀完成后,将PCB线路板放入清洗槽中,清洗掉电镀液和其他残留物。
这将防止残留的电镀液对PCB线路板的性能和可靠性产生负面影响。
6.烘干:最后,将PCB线路板放入烘干槽中,以去除水分并使其彻底干燥。
可以使用热空气或其他适当的烘干方法。
完成以上步骤后,PCB线路板的电镀工艺就完成了。
在进行下一步工艺之前,需要确保电镀层的厚度和质量符合要求,并进行必要的检查和测试。
- 1、下载文档前请自行甄别文档内容的完整性,平台不提供额外的编辑、内容补充、找答案等附加服务。
- 2、"仅部分预览"的文档,不可在线预览部分如存在完整性等问题,可反馈申请退款(可完整预览的文档不适用该条件!)。
- 3、如文档侵犯您的权益,请联系客服反馈,我们会尽快为您处理(人工客服工作时间:9:00-18:30)。
1概述镍,元素符号Ni,原子量58.7,密度8.88g/cm3,Ni2+的电化当量1.095g /AH。
用于印制板的镍镀层分为半光亮镍(又称低应力镍或哑镍)和光亮镍两种。
主要作为板面镀金或插头镀金的底层,根据需要也可作为面层,镀层厚度按照IPC-6012(1996)标准规不低于2~2.5μm。
镍镀层应具有均匀细致,孔隙率低,延展性好等特点,而且低应力镍应具有宜于钎焊或压焊的功能。
2低应力镍2.1镀镍机理阴极:在阴极上,镀液中的镍离子获得电子沉积出镍原子,同时伴有少量氢气析出。
Ni2++2e+Ni0Ni2+/Ni=-0.25V2H++2e+H20Ni2+/N2=-0.0V虽然Ni的标准电极电位很负,但由于氢的过电位以及镀液中镍离子的浓度、温度、pH等操作条件的影响,阴极上析出氢极少,这时镀液的电流效率可达98%以上。
只有当pH很低时,才会有大量氢气析出,此时阴极上无镍沉积。
阳极:普通镀镍使用可溶性镍阳极。
阳极的主反应为金属镍的电化学溶解:Ni-2e→Ni2+当阳极电流密度过高,电镀液中又缺乏阳极活化剂时,阳极将发生钝化并伴有氧气析出:2H20-4e→02↑+4H+当镀液中有氯离子存在时,也可能发生析出氯气得反应:2C1--2e→C12↑阳极上金属镍电化学溶解使镍离子不断进入溶液,从而提供了阴极电沉积所需的镍离子。
但当阴极面积不够大或镀液中活化剂不够时,将导致阳极钝化而析出氧,生成的氧进步氧化阳极表面,生成棕色的Ni203氧化膜。
2Ni+3[O]→Ni2O3由于阳极钝化,使电流密度降低,槽电压升高,电能损失增加。
当使用高速镀镍工艺时,阳极采用非溶性材料如:铂、钛上镀铂网或钛上镀钌网,也可以采用含硫的活性镍阳极。
2.2镀液配方及操作条件2.3镀液配制1)在备用槽中,用热去离子水溶解计量的硫酸镍、氯化镍和计量1/2的硼酸。
2)加热至55~60℃,加活性炭3g/L,搅拌2h,静置2h,过滤,将无炭粒的溶液转人已清洗干净的工作槽中。
3)搅拌下,加入其余量硼酸,调pH到3.0,在55-60℃下,用瓦楞形阴极,在0.3~0.5A/dm2下电解,直至阴极板上镀层颜色均匀一致为止。
一般通电量需达4Ah/L。
4)加入添加剂和润湿剂,搅拌,调pH及液位,分析镀液成分。
试镀。
如果所用硫酸镍、氯化镍等材料纯度低,则需在加活性炭之前,先加H2O21~3ml/L,搅拌半小时,加热至65℃,保持半小时,再加活性炭并继续按步骤进行。
2.4各成分作用2.4.1主盐硫酸镍或氨基磺酸镍是镀镍溶液的主要成分,在普通镀镍中,控制Ni2+浓度65-75g/L。
表7-2中列出了这两种类型镀液所镀出镀层的主要性能比较。
从表中看出,以氨基磺酸盐型的低应力镍镀层的性能更佳。
但氨基磺酸镍稳定性较差,价格较贵。
而用硫酸镍为主盐也能达到技术要求。
提高主盐浓度,可以提高镀层的沉积速度,并能使允许电流密度范围扩大,但主盐浓度太高会导致镀液分散能力降低。
主盐浓度降低导致镀层沉积速度降低,严重时会导致高电流区镀层烧焦。
2.4.2阳极活化剂为了保证阳极正常溶解,防止阳极钝化,镀液中需要阳极活化剂。
镍的卤族化合物如:氯化镍、溴化镍等可以作为镍阳极活化剂。
氯化镍浓度不能太高,否则会使镀层应力增加,一般以氯化镍不大于30g/L为宜;以溴离子作阳极活化剂,它的浓度升高影响不大,但溴化物原料来源不如氯化镍方便。
阳极钝化有以下现象:1)槽电压升高,一般可达6V以上,但电流却很小。
2)阳极表面气泡较多,有时会有刺激性气味,甚至表面呈褐色。
造成阳极钝化的主要原因:镀液中阳极活化剂浓度太低。
阳极面积太小。
此时,将溶液和阳极面积调整后,将阳极取出,经稀硫酸处理后,洗净重新放人镀液。
2.4.3缓冲剂硼酸是镀镍溶液最好的缓冲剂。
它可以将镀液的酸度控制在一定范围之内,为了达到最佳缓冲效果,硼酸浓度不能低于30g/L,最好保持在40-50g/L。
H2BO3的缓冲作用是通过H2BO3的电离来维持的,H2BO3是一种弱酸,它在水溶液中电离反应如下:H2BO3与H++H2BO3-H2BO3与H++HBO32-HBO32与H++BO33-当溶液pH上升时,电离平衡向右进行,维持了溶液pH值的稳定;当溶液pH下降时,使电离平衡向左进行,同样维持了溶液pH的稳定。
硼酸不仅具有pH缓冲能力,而且它能提高阴极极化,改善镀液性能,使在较高的电流密度下,镀层不易烧焦。
硼酸的存在也有利于改善镀层的机械性能。
2.4.4添加剂添加剂的加入,改善了镀液的阴极极化,使镀层均匀细致并具有半光亮镍的光泽,同时改善了镀液的分散能力。
添加剂的主要成分是应力消除剂,由于添加剂的加入,降低了镀层的内应力,随着添加剂的浓度变化,可以使镀层内应力由张应力改变为压应力。
能起到这种作用的材料有如:萘磺酸、对甲苯磺酰胺、糖精等。
添加剂成分选配合适,可以使镀层均匀细致有光泽并且可焊性好。
2.4.5润湿剂润湿剂能降低镀液的表面张力,使表面张力降至35-37dyn /cm,这有利于消除镀层的针孔、麻点。
用于印制板的镀镍溶液宜使用低泡润湿剂,如:二乙基已基硫酸钠、正辛基硫酸钠等。
2.5操作条件2.5.1pH值pH控制在3.5~4为宜。
当pH一定时,随着电流密度增加,电流效率也增加。
pH高,镍的沉积速度快,但pH太高将导致阴极附近出现碱式镍盐沉淀,从而产生金属杂质的夹杂,使镀层粗糙、毛刺和脆性增加。
pH低些,镀层光泽性好,但pH太低导致阴极电流效率降低,沉积速度降低,严重时阴极大量析氢,镀层难以沉积。
使用可溶性阳极的镀液,随着电极过程的进行,镀液pH逐渐升高。
使用不溶性阳极的镀液,由于阳极析氧,使镀液中OH-浓度减少,从而pH会降低。
降低镀液pH用10%(V/V)H2S04;提高镀液pH用碳酸镍或碱式碳酸镍。
提高镀液pH不宜用N。
OH,因为钠离子在镀液中的积累会降低电流密度上限,容易导致高电流区镀层烧焦。
碳酸镍的加入方法最好是将它放人聚丙烯的滤袋并挂在镀液中,使其缓慢溶于镀液中,且不可将固体物直接放入镀液中,当pH达到要求后,取出滤袋,洗净后烘干备用。
当市售碳酸镍难以购到时,可以自己制备:将3份重量的硫酸镍与1.3份重量的无水碳酸钠分别用少量去离子水溶解,在搅拌下将碳酸钠溶液慢慢倒人硫酸镍溶液中,反应方程式如下:NiSO4+Na2CO,→NiCO3↑+Na2SO4待沉淀完全后,过滤,用去离子水洗涤沉淀数次,以去除硫酸钠,沉淀即可使用。
2.5.2温度操作温度对镀层内应力影响较大,提高温度可降低镀层内应力,当温度由10-35℃时,镀层内应力有明显降低,到60℃以上,镀层内应力稳定。
一般维持操作温度55~60℃为宜。
镀液操作温度的升高,提高了镀液中离子的迁移速度,改善了溶液的电导,从而也就改善了镀液的分散能力和深镀能力,使镀层分布均匀。
同时温度升高也可以允许使.用较高的电流密度,这对高速电镀极为重要。
2.5.3电流密度在达到最高的允许电流密度之前,阴极电流效率随电流密度的增加而增加。
在正常的操作条件下,当阴极电流密度4A/dm2时,电流效率可达97%,而镀层外观和延展性都很好。
对于印制板电镀,由于拼板面积比较大,至使中心区域与边缘的电流密度可相差数倍,所以实际操作时,可取操作电流密度2A/dm2左右为宜。
2.5.4搅拌搅拌能有效地清除浓差极化,保证电极过程持续有效地进行,同时也有利于阴极表面产生的少量氢气很快逸出,减少可能出现的针孔、麻点。
搅拌方式可采用:镀液连续过滤、阴极移动和空气搅拌,或者选择其中的两者相配合。
对于高速镀镍,其电流密度高达20A/dm2以上,为了更好的清除浓差极化,应配有镀液喷射的专用设备。
镀液连续过滤是必要的,它可及时清除镀液中的机械杂质,又能保持镀液流动。
过滤机的能力以满足每小时过滤镀液2~5次为宜,滤芯用聚丙烯材料,精度以5μm为宜。
若采用阴极移动,振幅20~25mm,15~20次/min。
若采用空气搅拌,则必须与连续过滤相配合,所供的压缩空气应是无油压缩空气,气流中速,如果空气量太大,导致溶液流动太快,将降低镀液的分散能力。
2.5.5镍阳极常规镀镍均采用可溶性镍阳极,可以使用镍板或装在钛篮中的镍角,并用吊钩将阳极悬挂在阳极杆上。
理想的阳极要能够均匀溶解,不产生杂质进入镀液,不形成任何残渣。
因此对阳极材料的成分及阳极的结构都有严格的要求。
目前采用盛有镍球(角)的钛篮作为阳极已相当普遍。
使用钛篮盛阳极材料可以保持足够大的阳极面积而且不变化,阳极保养也比较简单,只要定期将阳极材料补人篮中。
钛篮底部应高出槽底50-70mm,以避免阴极边缘因电力线过于集中而使镍镀层烧焦。
使用钛篮还可利用适当的遮蔽法调整阳极的有效面积来改善阴极镀层分布。
钛是很好的阳极篮结构材料,它强度高、质轻、耐蚀而且表面有层氧化膜,此膜在正常电镀条件下,可以阻止电流通过钛篮而使电流直接通向钛篮内的镍,但镍量不够时,钛就会受到浸蚀,所以应经常充实篮内的阳极镍材防止"架空"。
钛篮常用网目是10x3mm,也有用更宽的。
钛篮应装入聚丙烯材料织成的阳极袋内,阳极袋必须适度套紧并有正确的长度,阳极袋口应高出液面30-40mm,以防阳极泥渣析出。
为防止阳极袋受到意外伤害而使阳极泥渣泄出,可以使用双层袋,这样内袋要套紧,外袋要松些。
高质量的的镍阳极对保护镀层的质量,延长镀液寿命十分重要。
随着钛篮的出现,阳极镍的品种也在改进和提高。
现在常用的有25x25x15mm镍块,有96-12mm的镍球,还有022-10mm形如钮扣状的镍饼。
装载密度一般是:镍球5.4~6ks/dm3,镍饼4.6kS/dm3。
还有一种含硫镍阳极是活性镍阳极,它的形状如圆饼或球形,它的活性来源于精练过程所加人的少量的硫,它能使阳极溶解均匀,即使在没有氯化物的镀液中,也能使阳极效率达100%,阳极所含的硫并未进入镀液而是以不溶性硫化镍残渣形式保存在阳极袋中。
该硫化镍残渣还可吸附镀液中的铜离子而帮助净化镀液。
这种活性镍阳极更适于作高速电镀的阳极。
球形或饼状阳极都是用于自动线操作。
阳极材料的成分应符合国家标准GB6516-86,其它标准如IS06283,ASTMB39,都制定了相应的材料标准。
2.6镀液维护1)定期分析镀液中的主盐成分并及时给以补充,以保持镀液成分稳定。
选择高质量的硫酸镍、氯化镍、硼酸或氨基磺酸镍至关重要。
补人镀液中的主盐应预先溶解后经活性炭处理才可人缸,硼酸可直接加人缸中,加入方式最好是将它置人阳极袋中,使在镀液中缓慢溶入。
2)及时检查和调整镀液的pH值,一般每4小时至少检查调整一次。
3)添加剂根据安时数及时补充,最好能由赫尔槽试验配合补加。
4)镀液的主要污染来自于重金属离子和有机污染,要及时清除。
镀镍液的重金属污染主要是Cu2+,Fe2+,Zn2+,当Cu2+达0.01~0.05g /L时,导致镀层低电流区发黑,严重时镀层无光亮,可焊性差。