中国现有乙烯装置及其技术水平.doc
乙烯装置主要设备

国内乙烯装置的典型工艺流程,设备组成和运行现状乙烯装置是以石油或天然气为原料,以生产高纯度乙烯和丙烯为主,同时副产多种石油化工原料的石油化工装置。
裂解原料在乙烯装置中通过高温裂解、压缩、分离得到乙烯,同时得到丙烯、丁二烯、苯、甲苯及二甲苯等重要的副产品。
国内乙烯装置工艺流程简述:1、裂解工序接收来自界外的炼厂C3/C4、粗混合C4、C5循环物流、分离部分返回的循环乙烷/循环丙烷、芳烃提余油、轻石脑油、重石脑油、以及加氢裂化石脑油(HCN),分别送入SL-1 型及SL-2型炉内,加稀释蒸汽(DS进行裂解,得到的裂解气(即:氢气、甲烷、乙烯、乙烷、丙烯、丙烷、丁二烯、裂解汽油、裂解燃料油等组分的混合物)经废热锅炉急冷,油冷、水冷至常温,回收部分热量,并把其中大部分油类产品分离后送入后续工序。
负责接收从界外来的高压锅炉给水并将其转化为压力11.7Mpa、温度500〜525 C的超高压蒸汽(VHS。
接收本装置分离工序返回的甲烷氢及从界外补充的碳三/碳四等物料经混合、汽化后做为裂解炉燃料气。
2、压缩工序将来自裂解工序的裂解气,经五段压缩后,将压力提高到 4.173 MPag,为深冷分离提供条件。
裂解气在压缩过程中,逐段冷却和分离,除去重烃和水,并在三段出口设有碱洗,除去裂解气中的酸性气体,为分离系统提供合格的裂解气。
制冷系统由丙烯制冷系统和乙烯、甲烷二元制冷系统构成,为深冷分离提供- 40 C,—27 C,—3 C、13 C四个级别的丙烯冷剂;—40 C〜—135 C的二元冷剂。
丙烯、二元制冷系统为多段压缩,多级节流的封闭循环系统。
3、分离工序将压缩工序来的裂解气,经脱水、深冷、加氢和精馏等过程,获得高纯度的乙烯、丙烯,同时得到付产品Ha、CH、GLPG混合碳四馏份及裂解汽油。
4、汽油加氢裂解汽油加氢工序的任务是将来自乙烯单元的裂解汽油中的GS及C9脱除,剩余的C6〜C8中心馏份经过二次加氢后作为二段加氢产品,去芳烃装置,作为芳烃抽提的原料,C5S及C+9作为副产品送出界区。
乙烯装置技术水平分析及节能措施

乙烯装置技术水平分析及节能措施近年来,随着新的乙烯装置建设及老装置的扩能改造,新技术、新工艺及相关系统的设计优化的应用,我国乙烯装置能耗显著下降,随着国家“节能、降耗、减排”的要求提高,作为石油工企业耗能大户的乙烯装置将面临更大的节能降耗压力。
乙烯企业应严格控制工艺参数、工况条件,保证装置平稳运行、延长运行周期;通过用能数据、产品收率的对比分析以及对工艺单元的模拟计算,提出具体节能增效的措施。
乙烯企业应减少非计划停工事故发生,并结合装置特点逐步降低负荷、逐台有序停炉,尽可能回收物料,实现乙烯装置的无排放开停工。
标签:乙烯装置;综合能耗;节能措施1乙烯装置节能增效措施的研究1.1裂解炉系统优化原料的裂解性能在很大程度上决定了乙烯生产的能耗水平,但乙烯装置原料的优化和其上游炼厂的配制有很大关系。
大炼油小乙烯的配制,乙烯装置的原料就有很大的灵活性,相反小炼油或自身没有炼厂的乙烯装置其对原料就没有多少选择的余地。
我国优化裂解原料的重要措施就是实行“煉油化工一体化”,采用“宜烯则烯,宜芳则芳”的原则,它有利于炼厂和乙烯装置之间的原料互供和优化。
1.2装置精细化管理和无排放开停工创建节约型企业是企业增强核心竞争力的根本要求,石油化工企业通过精细化管理来实现节能增效具有重要的现实意义。
乙烯生产具备流程长、设备多、工艺机理复杂等特点,装置工艺指标约有上百个关键指标,因此在乙烯实际生产过程中,实施精细化管理、不断提升管理水平显得尤为重要。
乙烯企业应严格控制工艺参数、工况条件,例如裂解炉单元应加强烟道气氧含量、炉出口温度、炉管出口温度偏差、排烟温度及燃烧状况等工艺指标的管理,保证装置平稳运行、延长运行周期,为装置节能增效打下坚实基础。
例如独山子乙烯装置通过进细化管理和操作,裂解炉出口温度偏差保持在±2℃之间,双烯收率平均提高0.59%,经济效益显著。
同时应对重点耗能单元制订能耗消减措施,对易波动的工艺指标实行跟踪监控;通过用能数据的对比分析以及产品收率的对比评估,以及应用如Aspon等化工辅助模拟软件对工艺单元进行模拟计算,提出具体节能增效的措施。
我国乙烯生产工艺现状与发展趋势分析

我国乙烯生产工艺现状与发展趋势分析2017.6世界乙烯工业已走过90多年历程。
2014年,世界乙烯产能为1.53亿吨,乙烯生产装置271套,平均规模为56.5万吨/年,同比增长4.3%。
世界范围内,已建和在建生产能力在100万吨/年以上的裂解装置已达40多套。
美国是世界大的乙烯生产国,2014年乙烯生产能力为2842.6万吨,占世界总产能的18.5%;中国排名第二,占世界总产能的13.4%。
过去几年,中国乙烯产能和需求量均呈现增长态势,产能从2011年的1536.5万吨增至2015年的2137.5万吨,年均增幅为6.8%;产量从2011年的1553.6万吨增至2015年1730.3万吨,年均增幅为2.2%;当量需求量从2011年的3132.4万吨增至2015年的3733.0万吨,年均增幅为3.6%。
1.低油价下石油乙烯原料具有更大优化空间蒸汽裂解制乙烯技术的原料适应范围宽,乙烷、轻烃、液化气、石脑油、加氢尾油、柴油等均可,原料成本在总成本中所占比例高达60%~80%。
采用的原料不同,乙烯的生产成本也有很大的差别。
但如果综合考虑乙烯和裂解副产品的价值,在当前原油价格低位运行的情况下,石脑油裂解装置与乙烷裂解装置的竞争差距有所缩小。
石脑油裂解装置的乙烯生产成本约为4500元/吨,北美和中东乙烷裂解装置的乙烯生产成本分别在1500元/吨和1000元/吨左右,中东和北美以乙烷为原料的乙烯生产成本依然保持绝对的竞争优势。
低油价下,替代能源的发展和煤、甲醇等非石油路线生产烯烃将会受到抑制,而石脑油生产烯烃将存在原料低成本化、多元化和炼化一体化的更大优化空间,石油化工竞争力增强。
对于千万吨炼油、百万吨乙烯一体化企业,由于柴汽比的降低以及成品油消费增速的趋缓,炼油从大量生产柴油、汽油将转向生产更多的高标号汽油、航空煤油和清洁柴油以及低成本化工原料。
这种变化趋势是长期的,国家“十三五”期间结构调整步伐还将加快,将会有更多的低成本优质原料进入乙烯裂解装置。
中国成功掌握乙烯成套技术

中国成功掌握乙烯成套技术
中国石油天然气集团公司宣布,成功开发具有自主知识产权的大型乙烯成套工艺技术,在大庆石化年120万吨乙烯改扩建工程成功应用,结束国内乙烯技术长期依靠引进的历史。
9月23日,中国石油天然气集团公司“大型乙烯装置工业化成套技术开发”重大科技专项验收评估会在北京召开。
大型乙烯装置工业化成套技术开发”重大科技专项2008年立项以来,寰球工程公司、大庆石化公司、石油化工研究院和清华大学等单位联合攻关,开发出大型乙烯装置成套工艺技术,打破国外专利商在乙烯领域的垄断,多项核心技术填补国内空白。
大庆石化年120万吨乙烯改扩建项目于2012年10月一次开车成功,并于2013年顺利通过72小时满负荷性能考核。
截至目前,这套装置已平稳运行近两年,双烯收率、综合能耗以及裂解炉热效率等技术指标均达到国际先进水平。
大乙烯专项还实现国内大型乙烯裂解炉计算及工程设计的突破以及配套系列催化剂的工业化应用,并开发出国内首套裂解产物预测软件。
中国石油已成为国内首个实现乙烯成套技术自主开发应用成功的企业,也是开发成功目前国内规模最大乙烯裂解炉的企业,使中国成为世界上第四个具有乙烯成套技术的国家。
我国乙烯生产现状
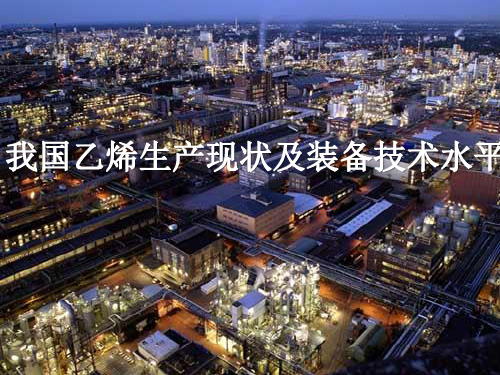
我国乙烯生产技术水平
近年来我国乙烯及其下游加工装置在规模化水平、技术进步、 近年来我国乙烯及其下游加工装置在规模化水平、技术进步、节能 降耗、技术开发和创新等方面取得长足的进步,整体实力明显增强: 降耗、技术开发和创新等方面取得长足的进步,整体实力明显增强: 七套大型乙烯装置在2006年前后完成二轮改造后,平均规模达 年前后完成二轮改造后, 七套大型乙烯装置在 年前后完成二轮改造后 73.3万吨 年,虽大多数装置由二个系列组成,但整体规模已达世界 万吨/年 虽大多数装置由二个系列组成, 万吨 尤其是下游聚乙烯、聚丙烯装置,新建基本都在20万吨 年以上; 万吨/年以上 级,尤其是下游聚乙烯、聚丙烯装置,新建基本都在 万吨 年以上; 节能降耗效果明显, 年乙烯的平均能耗在730万大卡 吨乙烯 万大卡/吨乙烯 节能降耗效果明显,2003年乙烯的平均能耗在 年乙烯的平均能耗在 万大卡 左右,大型乙烯平均能耗691.8万大卡 吨乙烯,吉化乙烯能耗595 万大卡/吨乙烯 左右,大型乙烯平均能耗691.8万大卡/吨乙烯,吉化乙烯能耗595 万大卡/吨乙烯 为国内最佳,全国乙烯原料消耗平均为3.2吨/吨烯, 吨乙烯, 吨烯, 万大卡 吨乙烯,为国内最佳,全国乙烯原料消耗平均为 吨 吨烯 由于我国乙烯原料较重,轻烃比例小( ),石脑油 由于我国乙烯原料较重,轻烃比例小(占5~6%),石脑油(占 ),石脑油( 60%左右)供应不足,重质原料柴油和加氢尾油占 左右) 左右 供应不足,重质原料柴油和加氢尾油占24%~27%的 的 比重。乙烯原料耗量较高;石油化工技术在多年来引进、消化、 比重。乙烯原料耗量较高;石油化工技术在多年来引进、消化、吸收 的基础上,通过开发创新, 的基础上,通过开发创新,已形成了一批具有自主知识产权并可应用 于工业化的技术成果,包括10万吨 年能力的裂解炉, 万吨/年能力的裂解炉 于工业化的技术成果,包括 万吨 年能力的裂解炉,聚丙烯高效催 化剂和环管二代聚丙烯成套技术以及石化装置的催化剂国产化等等。 化剂和环管二代聚丙烯成套技术以及石化装置的催化剂国产化等等。
全国乙烯工业生产现状及改造分析_胡建洪
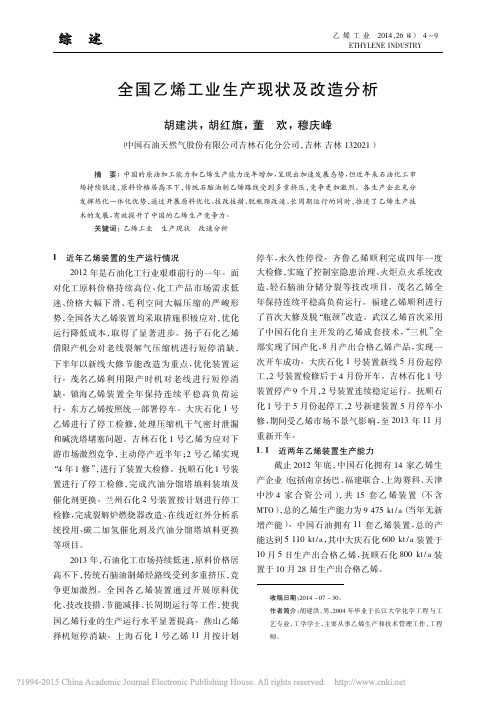
综述乙烯工业2014,26(4)4 9ETHYLENE INDUSTRY 全国乙烯工业生产现状及改造分析胡建洪,胡红旗,董欢,穆庆峰(中国石油天然气股份有限公司吉林石化分公司,吉林吉林132021)摘要:中国的原油加工能力和乙烯生产能力逐年增加,呈现出加速发展态势,但近年来石油化工市场持续低迷,原料价格居高不下,传统石脑油制乙烯路线受到多重挤压,竞争更加激烈。
各生产企业充分发挥炼化一体化优势,通过开展原料优化、技改技措、脱瓶颈改造、长周期运行的同时,推进了乙烯生产技术的发展,有效提升了中国的乙烯生产竞争力。
关键词:乙烯工业生产现状改造分析1近年乙烯装置的生产运行情况2012年是石油化工行业艰难前行的一年。
面对化工原料价格持续高位、化工产品市场需求低迷、价格大幅下滑、毛利空间大幅压缩的严峻形势,全国各大乙烯装置均采取措施积极应对,优化运行降低成本,取得了显著进步。
扬子石化乙烯借限产机会对老线裂解气压缩机进行短停消缺,下半年以新线大修节能改造为重点,优化装置运行。
茂名乙烯利用限产时机对老线进行短停消缺。
镇海乙烯装置全年保持连续平稳高负荷运行。
东方乙烯按照统一部署停车。
大庆石化1号乙烯进行了停工检修,处理压缩机干气密封泄漏和碱洗塔堵塞问题。
吉林石化1号乙烯为应对下游市场激烈竞争,主动停产近半年;2号乙烯实现“4年1修”,进行了装置大检修。
抚顺石化1号装置进行了停工检修,完成汽油分馏塔填料装填及催化剂更换。
兰州石化2号装置按计划进行停工检修,完成裂解炉燃烧器改造、在线近红外分析系统投用、碳二加氢催化剂及汽油分馏塔填料更换等项目。
2013年,石油化工市场持续低迷,原料价格居高不下,传统石脑油制烯烃路线受到多重挤压,竞争更加激烈。
全国各乙烯装置通过开展原料优化、技改技措、节能减排、长周期运行等工作,使我国乙烯行业的生产运行水平显著提高。
燕山乙烯择机短停消缺。
上海石化1号乙烯11月按计划停车,永久性停役。
齐鲁乙烯顺利完成四年一度大检修,实施了控制室隐患治理、火炬点火系统改造、轻石脑油分储分裂等技改项目。
近年来国内外乙烯产需以及生产技术情况

近年来国内外乙烯产需以及生产技术情况--------------------------------------------------------------------------------卓创资讯 doris 编辑于:2007-5-28 14:47:45乙烯作为石化基础原材料,其生产能力是衡量一个国家石化工业水平的重要标志。
中国经济发展一支独秀,对乙烯及其下游制品的需求急剧增加,乙烯行业正处于前所未有的黄金发展时期。
乙烯生产是石油化学工业的龙头,其生产规模、产量和技术确实标志着一个国家的石油化学工业的发展水平经过20世纪80年代和90年代的技术引进和建设,中国乙烯行业生产有了飞跃性的发展。
特别是近几年,原有的老装置进行了一系列的配套平衡和技术改造,使国内乙烯生产能力有了很大提高。
乙烯主要是通过裂解石油产品来获得的,因此乙烯发展与裂解工艺技术的发展是分不开的。
长期以来,各种热裂解制乙烯的技术是朝着高温、短停留时间、低烃分压,加大操作弹性,增长运转周期,简化操作等方面努力,以期达到高效率、低能耗、对原料变化适应性强的目的。
世界乙烯产需情况――1.世界乙烯产能演变透视2004年世界乙烯生产能力增速明显放缓,从2003年的11077.8万吨/年增至2004年的11290.6万吨/年,仅净增212.8万吨/年,增长率为1.9%。
其中美国增加67万吨/年,得州DeerPark乙烯装置的能力由100万吨/年增加到145.2万吨/年;俄罗斯、泰国、匈牙利乙烯装置能力均增加30万吨/年左右。
中国乙烯装置能力增加35万吨/年,主要是中国石化齐鲁分公司生产能力由45万吨/年扩大到72万吨/年和中国石油兰州石化公司由16万吨/年增加到24万吨/年。
还有泰国由于在Rayong建设了新装置,乙烯装置能力增加了30万吨/年。
匈牙利乙烯装置能力的增加是因为TVK公司25万吨/年乙烯新装置的投产。
2005年世界乙烯生产能力为11733万吨/年,净增442.4万吨/年,增长率为3.9%。
中国现有乙烯装置及其技术水平讲解
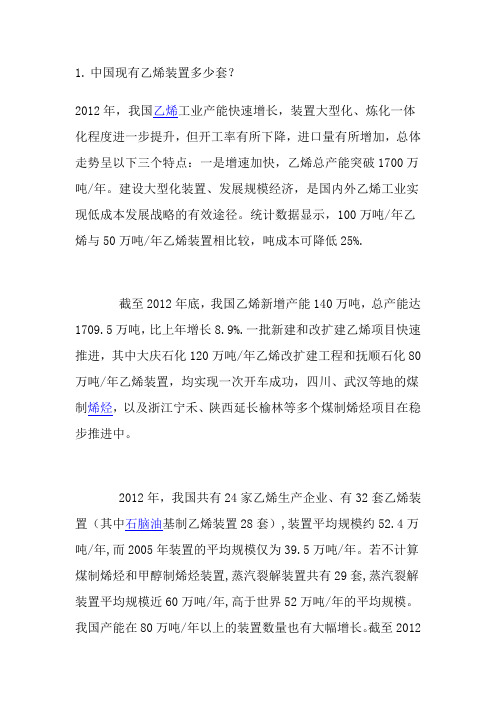
1.中国现有乙烯装置多少套?2012年,我国乙烯工业产能快速增长,装置大型化、炼化一体化程度进一步提升,但开工率有所下降,进口量有所增加,总体走势呈以下三个特点:一是增速加快,乙烯总产能突破1700万吨/年。
建设大型化装置、发展规模经济,是国内外乙烯工业实现低成本发展战略的有效途径。
统计数据显示,100万吨/年乙烯与50万吨/年乙烯装置相比较,吨成本可降低25%.截至2012年底,我国乙烯新增产能140万吨,总产能达1709.5万吨,比上年增长8.9%.一批新建和改扩建乙烯项目快速推进,其中大庆石化120万吨/年乙烯改扩建工程和抚顺石化80万吨/年乙烯装置,均实现一次开车成功,四川、武汉等地的煤制烯烃,以及浙江宁禾、陕西延长榆林等多个煤制烯烃项目在稳步推进中。
2012年,我国共有24家乙烯生产企业、有32套乙烯装置(其中石脑油基制乙烯装置28套),装置平均规模约52.4万吨/年,而2005年装置的平均规模仅为39.5万吨/年。
若不计算煤制烯烃和甲醇制烯烃装置,蒸汽裂解装置共有29套,蒸汽裂解装置平均规模近60万吨/年,高于世界52万吨/年的平均规模。
我国产能在80万吨/年以上的装置数量也有大幅增长。
截至2012年,共有10套80万吨以上的蒸汽裂解装置,合计产能达988万吨/年,占总产能的58.9%。
单套最大规模为上海赛科119万吨/年的乙烯装置。
乙烯生产企业平均规模74.1万吨/年,比2011年的68万吨/年增加了6.1万吨/年;乙烯装置平均规模57万吨/年,比2011年的56.1万吨/年上升了0.9万吨/年,高于世界52万吨/年的平均规模。
若不计算煤制烯烃和甲醇制烯烃装置,我国石脑油裂解乙烯装置的平均规模为59.2万吨/年,单套规模达80万吨/年以上的装置有8套,合计产能774万吨/年,占总产能的45%;单套规模60万吨/年以下的装置降至12套,产能合计263.5万吨/年,占总产能的16%.据美国《油气杂志》最新统计数据显示,当前全球十大乙烯生产商排名情况如下:排名第一的是埃克森美孚公司,共有19套装置,总产能1251.5万吨/年;排名第二的是陶氏化学,共有18套装置,产能1214.48万吨/年;排名第三的是沙伯公司,共有13套装置,产能1084.22万吨/年;排名第四的是壳牌化学,共有13套装置,产能935.84万吨/年;排名第五的是中国石化集团公司,共有12套装置,产能637.5万吨/年;排名第六的是道达尔公司,共有11套装置,产能593.3万吨/年;排名第七的是利安德巴赛尔公司,共有8套装置,产能520万吨/年;排名第八的是伊朗国家石化公司,共有7套装置,产能473.4万吨/年;排名第九的是英力士公司,共有6套装置,产能465.6万吨/年;排名第十的是台湾石化公司,共有5套装置,产能447.6万吨/年。
我国全密度聚乙烯装置发展情况分析

我国全密度聚乙烯装置发展情况分析全密度装置情况介绍1977年美国UCC公司在原有Unipol低压气相法HDPE装置上,通过改进原有的催化剂体系,成功实现LLDPE的工业化生产。
随后DOW化学公司也开发成功了溶剂法LLDPE的生产技术。
其他石化也争相开发LLDPE。
70年代,LLDPE大量投入市场,改变了高压法生产LDPE,低压法生产HDPE的传统观念。
由于LLDPE的分子结构与HDPE相似,也是呈线型,生产工艺上与一部分HDPE的生产工艺上有相同的地方,因此,许多新设计的装置,通过改变进料组成和工艺参数,来生产0.910-0.960g/cm3的全密度聚乙烯(即LLDPE/HDPE),这种装置成为全密度聚乙烯装置。
这种装置具有相当大的灵活性及市场的应变能力,使得全密度聚乙烯装置发展较快,成为目前最主要的一种聚乙烯的生产技术,也是聚乙烯生产装置的一个发展趋势。
我国全密度装置发展情况从工艺上看,我国的全密度装置基本是引进的上世纪90年代初期之前的工艺,主要为美国UCC公司的气相法与英国BP气相法工艺。
其技术工艺相对较为落后,不过经过近年来的不断改进,已经显著提高。
不过目前依旧存在较多问题,主要表现在:通用料多,专用料少;中低端产品多,高端产品少;利润低、低附加值产品多,利润高、高附加值产品少;多数生产企业的建设重点仍以扩大规模为主,产品依旧较为单一。
不过随着石化生产技术日益改善及研发能力的不断提高,国内生产企业已经开始专注专用料、高附加值的产品的生产,且成果较为显著。
从产能上看,据卓创统计,截止2013年我国聚乙烯总产能已经达到1330万吨,其中全密度装置总产能达445万吨,占比约三分之一左右。
随着全密度装置的(LLDPE/HDPE)陆续投产,低压、线性、高压的传统“433”比例在2009年被打破。
目前聚乙烯低压、线性、高压品种的产能比例维持在“442”。
由于全密度装置可以通过改变进料组成和工艺参数来生产LLDPE/HDPE,因此具有相当大的灵活性及市场应变能力,国内石化生产企业均对全密度装置亲睐有加,近年来我国新投产的装置多数为全密度装置,预计未来LDPE产能比例将进一步被压缩。
乙烯装置技术水平分析及节能措施

乙烯装置技术水平分析及节能措施作者:李雪民来源:《中国化工贸易·上旬刊》2017年第08期摘要:近年来,随着新的乙烯装置建设及老装置的扩能改造,新技术、新工艺及相关系统的设计优化的应用,我国乙烯装置能耗显著下降,随着国家“节能、降耗、减排”的要求提高,作为石油工企业耗能大户的乙烯装置将面临更大的节能降耗压力。
乙烯企业应严格控制工艺参数、工况条件,保证装置平稳运行、延长运行周期;通过用能数据、产品收率的对比分析以及对工艺单元的模拟计算,提出具体节能增效的措施。
乙烯企业应减少非计划停工事故发生,并结合装置特点逐步降低负荷、逐台有序停炉,尽可能回收物料,实现乙烯装置的无排放开停工。
关键词:乙烯装置;综合能耗;节能措施1乙烯装置节能增效措施的研究1.1裂解炉系统优化原料的裂解性能在很大程度上决定了乙烯生产的能耗水平,但乙烯装置原料的优化和其上游炼厂的配制有很大关系。
大炼油小乙烯的配制,乙烯装置的原料就有很大的灵活性,相反小炼油或自身没有炼厂的乙烯装置其对原料就没有多少选择的余地。
我国优化裂解原料的重要措施就是实行“炼油化工一体化”,采用“宜烯则烯,宜芳则芳”的原则,它有利于炼厂和乙烯装置之间的原料互供和优化。
1.2装置精细化管理和无排放开停工创建节约型企业是企业增强核心竞争力的根本要求,石油化工企业通过精细化管理来实现节能增效具有重要的现实意义。
乙烯生产具备流程长、设备多、工艺机理复杂等特点,装置工艺指标约有上百个关键指标,因此在乙烯实际生产过程中,实施精细化管理、不断提升管理水平显得尤为重要。
乙烯企业应严格控制工艺参数、工况条件,例如裂解炉单元应加强烟道气氧含量、炉出口温度、炉管出口温度偏差、排烟温度及燃烧状况等工艺指标的管理,保证装置平稳运行、延长运行周期,为装置节能增效打下坚实基础。
例如独山子乙烯装置通过进细化管理和操作,裂解炉出口温度偏差保持在±2℃之间,双烯收率平均提高0.59%,经济效益显著。
乙烯装置节能技术进展

乙烯装置节能技术进展摘要:对目前国内外乙烯装置采用的新技术进行了介绍,分析了各种技术的特点,指出了它们的适用范围、节能效果或对减少投资的作用。
结合国内各乙烯装置采用的工艺技术路线,对其技术水平进行了分析和定位,并分析了采用新技术进行技术改造后的节能潜力。
结果表明,我国大多数乙烯装置采用的工艺技术处于国际领先水平,技术改造的节能潜力很小;同时也指出数套规模小、技术水平落后的乙烯装置需进行扩能、节能技术改造或拆除重建。
关键词:乙烯;装置;节能技术乙烯生产主要是将烃类物质通过裂解炉裂解后制备烯烃,在蒸汽裂解的过程中,会消耗大量的能源,因此,乙烯生产具备了高耗能性。
当前,我国处于能源紧缺状态,环境也面临着较大问题,因此节能减排低能耗是我国经济发展的主要趋势,也是乙烯装置技术改进的趋势。
1乙烯装置节能增效技术1.1裂解炉的节能改造提高裂解选择性烃类蒸气热裂解制乙烯的反应是在辐射段炉管中进行的。
采用高选择性辐射段炉管,由于提高了乙烯收率,降低了原料消耗,因而起到节能的作用。
对于同一种石脑油原料,高选择性辐射段炉管乙烯收率可提高约0.68%,乙烯的燃料消耗可降低4.83%。
还可以通过采用强化传热技术和轻质优质原料来提高乙烯收率,降低单位乙烯的燃料消耗。
目前Lummus,S&W,KBR公司均有裂解炉与燃气轮机匹配的设计和经验。
裂解炉与燃气轮机联合系统有很大的节能潜力。
裂解炉热效率与排烟温度直接相关。
1975年之前裂解炉设计排烟温度一般为190~240℃,相应的热效率为87%~90%;20世纪70年代末期,裂解炉排烟温度降至120~140℃,相应的热效率提高到92%~93%;近年来,新设计的裂解炉进一步将排烟温度降至100~120℃,相应的热效率提高到93.0%~94.5%;如果排烟温度达到80~100℃,相应的热效率可提高到94.5%~95.5%。
但在降低排烟温度的同时,必须充分考虑烟气中酸性气体露点温度,即排烟温度的确定取决于燃料中的硫含量以及二氧化碳在蒸汽中的溶解量,以防止对流段炉管被腐蚀。
中国乙烯装置规模直追国际水平
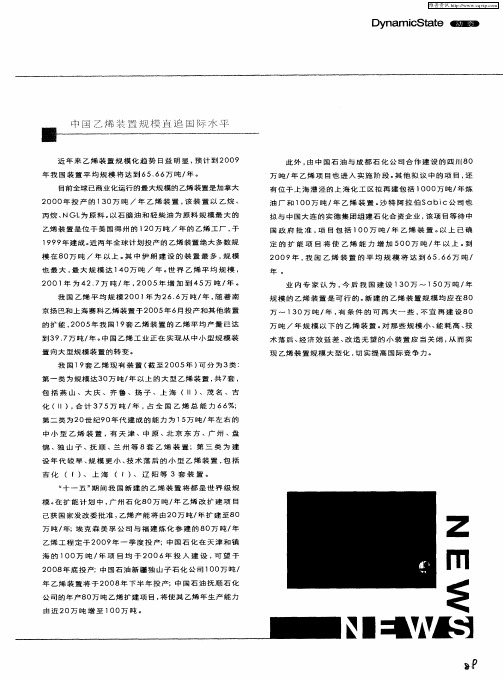
京 扬 巴和 上 海 赛 科 乙烯 装 置 于 20 05年 6月投 产 和 其 他 装 置 的扩 能 , 2005年 我 国 1 9套 乙 烯 装 置 的 乙烯 平 均 产 量 已 达
到 39. 吨 / 。 国 乙 烯 工 业 正 在 实 现 从 中 小 型 规 模 装 7万 年 中
置 向大 型 规 模 装 置 的 转 变 。
年 。
模 在 80万 吨 / 年 以 上 。 中 伊 朗 建 设 的 装 置 最 多 , 模 其 规
也 最大 , 大 规 模达 1 最 40万 吨 / 年 。 界 乙 烯 平 均 规 模 , 世 200 1 为 42、 年 7万 吨 /年 , 2005年 增 加 到 45万 吨 / 。 年 我 国 乙 烯 平 均 规 模 200 1 为 26、 年 6万 吨 / , 着 南 年 随
维普资讯
Dy am i St t ●圈 n c ae 日
中 国 乙 烯 装 置 规 模 舟 追 圈 水
近 年 来 乙 烯 装 置 规 模 化 趋 势 日 益 明 显 , 计 到 2009 预
此 外 , 中 国 石 油 与 成 都 石 化 公 司 合 作 建 设 的 四 川 80 由
拟 与 中 国大 连 的 实 德 集 团组 建 石 化 合 资 企 业 , 项 目等 待 中 该 国 政 府 批 准 , 目 包 括 100万 吨 / 乙 烯 装 置 。 上 已 确 项 年 以 定 的 扩 能 项 目 将 使 乙 烯 能 力 增 加 500万 吨 / 以 上 。 年 到 2009年 , 国 乙 烯 装 置 的 平 均 规 模 将 达 到 65. 我 66万 吨 /
业 内 专 家 认 为 , 后我 国建 设 1 乙 烯 装 置 是 可 行 的 。 建 的 乙 烯 装 置 规 模 均 应 在 80 新 万~ 1 30万 吨 / , 条 件 的 可 再 大 一 些 , 宜 再 建 设 80 年 有 不 万 吨 / 年 规 模 以 下 的 乙 烯 装 置 。对 那 些 规 模 小 、 耗 高 、 能 技 术 落 后 、 济 效 益 差 、 造 无 望 的 小 装 置 应 当 关 闭 , 而 实 经 改 从 现 乙烯 装 置 规 模 大 型 化 , 实 提 高 国 际 竞 争 力 。 切
乙烯装置分离技术及国产化研究开发进展
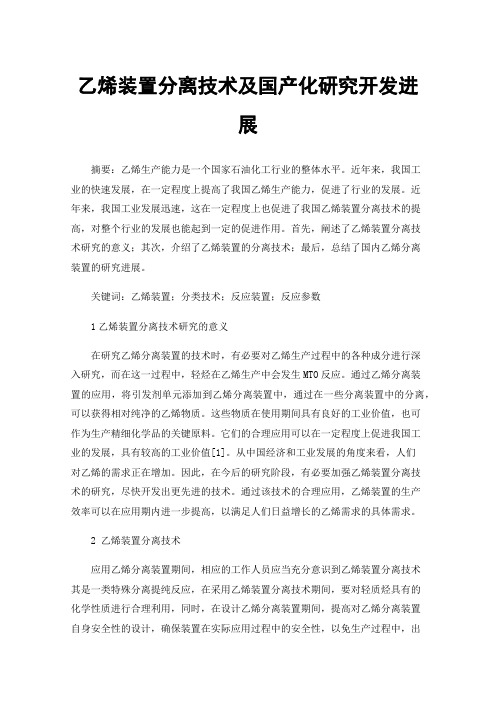
乙烯装置分离技术及国产化研究开发进展摘要:乙烯生产能力是一个国家石油化工行业的整体水平。
近年来,我国工业的快速发展,在一定程度上提高了我国乙烯生产能力,促进了行业的发展。
近年来,我国工业发展迅速,这在一定程度上也促进了我国乙烯装置分离技术的提高,对整个行业的发展也能起到一定的促进作用。
首先,阐述了乙烯装置分离技术研究的意义;其次,介绍了乙烯装置的分离技术;最后,总结了国内乙烯分离装置的研究进展。
关键词:乙烯装置;分类技术;反应装置;反应参数1乙烯装置分离技术研究的意义在研究乙烯分离装置的技术时,有必要对乙烯生产过程中的各种成分进行深入研究,而在这一过程中,轻烃在乙烯生产中会发生MTO反应。
通过乙烯分离装置的应用,将引发剂单元添加到乙烯分离装置中,通过在一些分离装置中的分离,可以获得相对纯净的乙烯物质。
这些物质在使用期间具有良好的工业价值,也可作为生产精细化学品的关键原料。
它们的合理应用可以在一定程度上促进我国工业的发展,具有较高的工业价值[1]。
从中国经济和工业发展的角度来看,人们对乙烯的需求正在增加。
因此,在今后的研究阶段,有必要加强乙烯装置分离技术的研究,尽快开发出更先进的技术。
通过该技术的合理应用,乙烯装置的生产效率可以在应用期内进一步提高,以满足人们日益增长的乙烯需求的具体需求。
2 乙烯装置分离技术应用乙烯分离装置期间,相应的工作人员应当充分意识到乙烯装置分离技术其是一类特殊分离提纯反应,在采用乙烯装置分离技术期间,要对轻质烃具有的化学性质进行合理利用,同时,在设计乙烯分离装置期间,提高对乙烯分离装置自身安全性的设计,确保装置在实际应用过程中的安全性,以免生产过程中,出现安全问题,引发安全事故,对生产工作造成不良影响[2]。
同时,在设计乙烯分离装置期间,要全面结合MTO反应过程中涉及的动力学公式,以及MTO反应期间涉及到的压力参数、传递方面、温度参数等多项数值,只有保证各项参数内容准确无误,才能确保乙烯分离装置在应用中,可以正常运行,以免出现生产事故。
乙烯装置生产技术
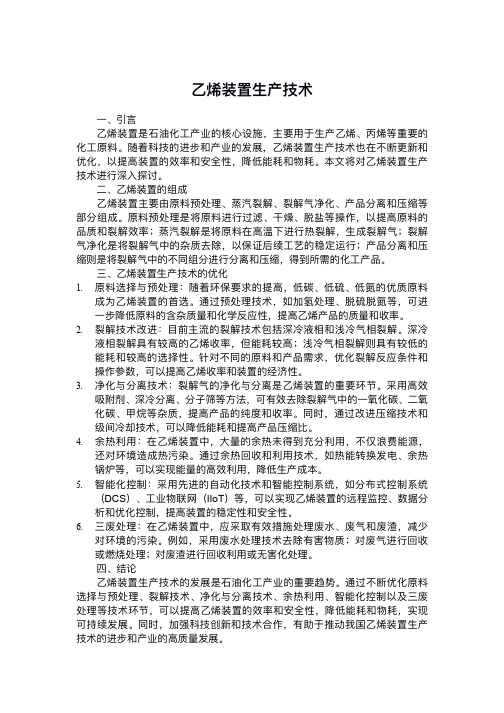
⼄烯装置⽣产技术⼀、引⾔⼄烯装置是⽯油化⼯产业的核⼼设施,主要⽤于⽣产⼄烯、丙烯等重要的化⼯原料。
随着科技的进步和产业的发展,⼄烯装置⽣产技术也在不断更新和优化,以提⾼装置的效率和安全性,降低能耗和物耗。
本⽂将对⼄烯装置⽣产技术进⾏深⼊探讨。
⼆、⼄烯装置的组成⼄烯装置主要由原料预处理、蒸汽裂解、裂解⽓净化、产品分离和压缩等部分组成。
原料预处理是将原料进⾏过滤、⼲燥、脱盐等操作,以提⾼原料的品质和裂解效率;蒸汽裂解是将原料在⾼温下进⾏热裂解,⽣成裂解⽓;裂解⽓净化是将裂解⽓中的杂质去除,以保证后续⼯艺的稳定运⾏;产品分离和压缩则是将裂解⽓中的不同组分进⾏分离和压缩,得到所需的化⼯产品。
三、⼄烯装置⽣产技术的优化1.原料选择与预处理:随着环保要求的提⾼,低碳、低硫、低氮的优质原料成为⼄烯装置的⾸选。
通过预处理技术,如加氢处理、脱硫脱氮等,可进⼀步降低原料的含杂质量和化学反应性,提⾼⼄烯产品的质量和收率。
2.裂解技术改进:⽬前主流的裂解技术包括深冷液相和浅冷⽓相裂解。
深冷液相裂解具有较⾼的⼄烯收率,但能耗较⾼;浅冷⽓相裂解则具有较低的能耗和较⾼的选择性。
针对不同的原料和产品需求,优化裂解反应条件和操作参数,可以提⾼⼄烯收率和装置的经济性。
3.净化与分离技术:裂解⽓的净化与分离是⼄烯装置的重要环节。
采⽤⾼效吸附剂、深冷分离、分⼦筛等⽅法,可有效去除裂解⽓中的⼀氧化碳、⼆氧化碳、甲烷等杂质,提⾼产品的纯度和收率。
同时,通过改进压缩技术和级间冷却技术,可以降低能耗和提⾼产品压缩⽐。
4.余热利⽤:在⼄烯装置中,⼤量的余热未得到充分利⽤,不仅浪费能源,还对环境造成热污染。
通过余热回收和利⽤技术,如热能转换发电、余热锅炉等,可以实现能量的⾼效利⽤,降低⽣产成本。
5.智能化控制:采⽤先进的⾃动化技术和智能控制系统,如分布式控制系统(DCS)、⼯业物联⽹(IIoT)等,可以实现⼄烯装置的远程监控、数据分析和优化控制,提⾼装置的稳定性和安全性。
- 1、下载文档前请自行甄别文档内容的完整性,平台不提供额外的编辑、内容补充、找答案等附加服务。
- 2、"仅部分预览"的文档,不可在线预览部分如存在完整性等问题,可反馈申请退款(可完整预览的文档不适用该条件!)。
- 3、如文档侵犯您的权益,请联系客服反馈,我们会尽快为您处理(人工客服工作时间:9:00-18:30)。
1.中国现有乙烯装置多少套?2012年,我国乙烯工业产能快速增长,装置大型化、炼化一体化程度进一步提升,但开工率有所下降,进口量有所增加,总体走势呈以下三个特点:一是增速加快,乙烯总产能突破1700万吨/年。
建设大型化装置、发展规模经济,是国内外乙烯工业实现低成本发展战略的有效途径。
统计数据显示,100万吨/年乙烯与50万吨/年乙烯装置相比较,吨成本可降低25%.截至2012年底,我国乙烯新增产能140万吨,总产能达1709.5万吨,比上年增长8.9%.一批新建和改扩建乙烯项目快速推进,其中大庆石化120万吨/年乙烯改扩建工程和抚顺石化80万吨/年乙烯装置,均实现一次开车成功,四川、武汉等地的煤制烯烃,以及浙江宁禾、陕西延长榆林等多个煤制烯烃项目在稳步推进中。
2012年,我国共有24家乙烯生产企业、有32套乙烯装置(其中石脑油基制乙烯装置28套),装置平均规模约52.4万吨/年,而2005年装置的平均规模仅为39.5万吨/年。
若不计算煤制烯烃和甲醇制烯烃装置,蒸汽裂解装置共有29套,蒸汽裂解装置平均规模近60万吨/年,高于世界52万吨/年的平均规模。
我国产能在80万吨/年以上的装置数量也有大幅增长。
截至2012年,共有10套80万吨以上的蒸汽裂解装置,合计产能达988万吨/年,占总产能的58.9%。
单套最大规模为上海赛科119万吨/年的乙烯装置。
乙烯生产企业平均规模74.1万吨/年,比2011年的68万吨/年增加了6.1万吨/年;乙烯装置平均规模57万吨/年,比2011年的56.1万吨/年上升了0.9万吨/年,高于世界52万吨/年的平均规模。
若不计算煤制烯烃和甲醇制烯烃装置,我国石脑油裂解乙烯装置的平均规模为59.2万吨/年,单套规模达80万吨/年以上的装置有8套,合计产能774万吨/年,占总产能的45%;单套规模60万吨/年以下的装置降至12套,产能合计263.5万吨/年,占总产能的16%.据美国《油气杂志》最新统计数据显示,当前全球十大乙烯生产商排名情况如下:排名第一的是埃克森美孚公司,共有19套装置,总产能1251.5万吨/年;排名第二的是陶氏化学,共有18套装置,产能1214.48万吨/年;排名第三的是沙伯公司,共有13套装置,产能1084.22万吨/年;排名第四的是壳牌化学,共有13套装置,产能935.84万吨/年;排名第五的是中国石化集团公司,共有12套装置,产能637.5万吨/年;排名第六的是道达尔公司,共有11套装置,产能593.3万吨/年;排名第七的是利安德巴赛尔公司,共有8套装置,产能520万吨/年;排名第八的是伊朗国家石化公司,共有7套装置,产能473.4万吨/年;排名第九的是英力士公司,共有6套装置,产能465.6万吨/年;排名第十的是台湾石化公司,共有5套装置,产能447.6万吨/年。
2.中国目前的乙烯生产能力及其技术水平如何?经过数十年的发展,特别是在“十一五”期间,我国乙烯工业取得了举世瞩目的进步,同期世界新建的乙烯装置大多集中在中国。
随着一系列乙烯装置的建成投产,到2010年底我国乙烯总产能达到1494.9×104t/a,成为全球仅次于美国(2755.4×104t/a)的第二大乙烯生产国。
设备国产化程度提升,乙烯原料趋向多元化。
从装置国产化程度上看,乙烯生产工艺中所用的大型裂解炉、裂解气压缩机等关键设备已实现了国产化。
2012年10月,大庆石化年产120万吨乙烯改扩建工程龙头项目已生产出合格产品,实现了国内大型乙烯技术工艺包采用完全自主知识产权并实现完全国产化的目标。
在抚顺石化大乙烯建设中,国产设备达到72%,实现了关键设备乙烯压缩机组的国产化,使我国成为世界上少数几个掌握这一技术的国家之一。
从乙烯原料上看,受资源限制,目前我国乙烯使用的原料以石脑油为主,其次是轻柴油、加氢尾油等。
其中,石脑油占64%、加氢尾油占10%、轻柴油占10%,90%乙烯原料来自炼厂。
原料的构成在目前或将来都不占优势。
丰富的煤炭资源加上烯烃市场巨大的需求量,使煤制烯烃项目具有一定的市场竞争力。
随着神华包头等多个示范项目的投产,我国以煤等非石油基原料制乙烯的技术取得突破性进展。
截至2012年底,我国共有煤制烯烃、甲醇制烯烃工业化装置4套,合计烯烃产能218万吨,生产聚乙烯56万吨,聚丙烯162万吨。
2009年8月28日,国家乙烯工业新原料来源示范项目———沈阳石蜡化工有限公司50×104t/a催化热裂解(CPP)制乙烯项目(以下简称CPP项目)在沈阳投产。
该项目采用中国石化石油化工科学研究院研发的重油深度催化裂解制乙烯技术,以重质渣油为原料富产乙烯和丙烯,这是该技术首次工业化应用。
由于操作条件缓和、设备材料要求低、投资相对较小以及主要原料常压渣油价格较低,与国内现有的乙烯装置相比,CPP项目生产的乙烯成本可降低20%。
我国西部大开发标志性工程、国内最大的炼化一体化工程———独山子石化千万吨炼油百万吨乙烯工程于2009年9月21日建成投产,该工程包括100×104t/a乙烯。
辽宁华锦化工集团公司500×104t/a油化工程(即乙烯原料工程)、扩能45×104t/a乙烯工程于2009年10月中旬投产,16×104t/a乙烯能力不变,再增加一套45×104t/a装置,产能达到61×104t/a。
2.1.22010年新建和扩能乙烯项目随着几个百万吨级乙烯装置的投产,2010年我国乙烯产能达到1494.9×104t/a,“十一五”期间5年的产能增长接近前10个五年计划的总和。
2010年1月16日,天津石化100×104t/a乙烯装置产出合格产品,项目主要包括100×104t/a乙烯和1000×104t/a 炼油。
由于采用新工艺和新技术,乙烯综合能耗和炼油综合能耗达到国际先进水平。
该项目的建成投产使天津石化炼油一次加工能力达到1500×104t/a,乙烯生产能力达到120×104t/a,成为全国最大的乙烯生产企业之一和华北地区最大的炼油加工基地。
辽宁华锦化工集团“十一五”工程于2010年2月5日全面投产,其中包括45×104t/a乙烯。
2010年4月20日,镇海炼化公司100×104t/a乙烯裂解装置成功投产,标志着这个目前国内单套规模最大、技术最先进、国产化率最高的乙烯工程投产成功,镇海炼化也自此拥有2300×104t/a原油综合加工能力和100×104t/a乙烯生产能力,成为我国最大的炼化一体化企业。
镇海炼化100×104t/a乙烯工程是国家建设项目,主要包括乙烯裂解等10套生产装置及配套公用工程,其中100×104t/a乙烯裂解、45×104t/a聚乙烯、65×104t/a环氧乙烷/乙二醇和28.5×104t/a环氧丙烷/62×104t/a苯乙烯等装置,在世界同类装置中规模最大。
在工艺技术上,大部分装置采用国产技术,其中6套装置采用中国石化自有技术,乙烯综合能耗达到国际水平。
中海壳牌石油化工股份有限公司是壳牌化学公司与中国海洋石油总公司各持股50%的合资企业,该公司于2010年3月在惠州大亚湾石化联合装置实施扩能。
扩建前乙烯裂解装置的产能为80×104t/a,扩建后产能达到95×104t/a。
通过结构调整,“十一五”期间我国乙烯布局优化取得成效,在长三角、环渤海、珠三角和西部等地区形成了一批世界级乙烯生产基地。
2010年乙烯产能按地区分,华东占42.4%、东北占16.4%、中南占12.5%、西北占13.3%、华北占15.5%,西南地区也正在建设乙烯装置,即将实现零的突破。
2009年8月28日,国家乙烯工业新原料来源示范项目———沈阳石蜡化工有限公司50×104t/a催化热裂解(CPP)制乙烯项目(以下简称CPP项目)在沈阳投产。
该项目采用中国石化石油化工科学研究院研发的重油深度催化裂解制乙烯技术,以重质渣油为原料富产乙烯和丙烯,这是该技术首次工业化应用。
由于操作条件缓和、设备材料要求低、投资相对较小以及主要原料常压渣油价格较低,与国内现有的乙烯装置相比,CPP项目生产的乙烯成本可降低20%。
我国西部大开发标志性工程、国内最大的炼化一体化工程———独山子石化千万吨炼油百万吨乙烯工程于2009年9月21日建成投产,该工程包括100×104t/a乙烯。
辽宁华锦化工集团公司500×104t/a油化工程(即乙烯原料工程)、扩能45×104t/a乙烯工程于2009年10月中旬投产,16×104t/a乙烯能力不变,再增加一套45×104t/a装置,产能达到61×104t/a。
2.1.22010年新建和扩能乙烯项目随着几个百万吨级乙烯装置的投产,2010年我国乙烯产能达到1494.9×104t/a,“十一五”期间5年的产能增长接近前10个五年计划的总和。
2010年1月16日,天津石化100×104t/a乙烯装置产出合格产品,项目主要包括100×104t/a乙烯和1000×104t/a 炼油。
由于采用新工艺和新技术,乙烯综合能耗和炼油综合能耗达到国际先进水平。
该项目的建成投产使天津石化炼油一次加工能力达到1500×104t/a,乙烯生产能力达到120×104t/a,成为全国最大的乙烯生产企业之一和华北地区最大的炼油加工基地。
辽宁华锦化工集团“十一五”工程于2010年2月5日全面投产,其中包括45×104t/a乙烯。
2010年4月20日,镇海炼化公司100×104t/a乙烯裂解装置成功投产,标志着这个目前国内单套规模最大、技术最先进、国产化率最高的乙烯工程投产成功,镇海炼化也自此拥有2300×104t/a原油综合加工能力和100×104t/a乙烯生产能力,成为我国最大的炼化一体化企业。
镇海炼化100×104t/a乙烯工程是国家建设项目,主要包括乙烯裂解等10套生产装置及配套公用工程,其中100×104t/a乙烯裂解、45×104t/a聚乙烯、65×104t/a环氧乙烷/乙二醇和28.5×104t/a环氧丙烷/62×104t/a苯乙烯等装置,在世界同类装置中规模最大。
在工艺技术上,大部分装置采用国产技术,其中6套装置采用中国石化自有技术,乙烯综合能耗达到国际水平。
中海壳牌石油化工股份有限公司是壳牌化学公司与中国海洋石油总公司各持股50%的合资企业,该公司于2010年3月在惠州大亚湾石化联合装置实施扩能。