优化热轧直条冷床上钢系统案例分析
热轧工艺优化在钢材成形性能提升中的应用与研究
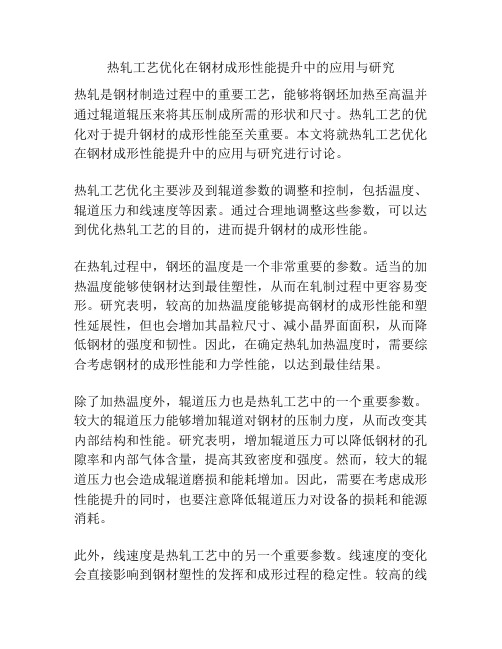
热轧工艺优化在钢材成形性能提升中的应用与研究热轧是钢材制造过程中的重要工艺,能够将钢坯加热至高温并通过辊道辊压来将其压制成所需的形状和尺寸。
热轧工艺的优化对于提升钢材的成形性能至关重要。
本文将就热轧工艺优化在钢材成形性能提升中的应用与研究进行讨论。
热轧工艺优化主要涉及到辊道参数的调整和控制,包括温度、辊道压力和线速度等因素。
通过合理地调整这些参数,可以达到优化热轧工艺的目的,进而提升钢材的成形性能。
在热轧过程中,钢坯的温度是一个非常重要的参数。
适当的加热温度能够使钢材达到最佳塑性,从而在轧制过程中更容易变形。
研究表明,较高的加热温度能够提高钢材的成形性能和塑性延展性,但也会增加其晶粒尺寸、减小晶界面面积,从而降低钢材的强度和韧性。
因此,在确定热轧加热温度时,需要综合考虑钢材的成形性能和力学性能,以达到最佳结果。
除了加热温度外,辊道压力也是热轧工艺中的一个重要参数。
较大的辊道压力能够增加辊道对钢材的压制力度,从而改变其内部结构和性能。
研究表明,增加辊道压力可以降低钢材的孔隙率和内部气体含量,提高其致密度和强度。
然而,较大的辊道压力也会造成辊道磨损和能耗增加。
因此,需要在考虑成形性能提升的同时,也要注意降低辊道压力对设备的损耗和能源消耗。
此外,线速度是热轧工艺中的另一个重要参数。
线速度的变化会直接影响到钢材塑性的发挥和成形过程的稳定性。
较高的线速度能够在一定程度上提高热轧效率,但也会增加钢材受力速度和变形应变率,从而对钢材的力学性能造成一定的影响。
因此,在确定线速度时,需要综合考虑热轧效率和钢材力学性能之间的平衡。
除了调整这些工艺参数外,使用先进的辊道和设备也能够有效提升热轧工艺的性能。
例如,采用热连轧工艺可以减少轧制过程中的加热和冷却时间,提高钢材的塑形能力。
采用轧辊和轧辊形状的优化设计,可以改善钢材的表面质量和力学性能。
综上所述,热轧工艺优化在提升钢材的成形性能方面具有重要的应用价值和研究意义。
热轧工艺优化在钢材成形性能提升中的应用与研究

热轧工艺优化在钢材成形性能提升中的应用与研究热轧是一种常用的钢材成形加工方法,通过加热钢坯至高温状态,并在一系列辊道间进行挤压和变形,最终得到所需形状和尺寸的钢材产品。
热轧工艺优化是指通过调整热轧过程中的工艺参数和控制策略,以期达到提高钢材成形性能和质量的目的。
本文将从工艺优化的应用和研究两个方面对热轧工艺优化在钢材成形性能提升中的作用进行探讨。
首先,热轧工艺优化在钢材成形性能提升中的应用可以从以下几个方面来进行分析。
首先,热轧工艺优化可以优化钢坯的形状和尺寸分布。
通过合理调整轧制温度、轧制压力、轧制速度等工艺参数,可以使得钢坯的变形力得到最大化利用,从而达到更好的压下效果,提高钢材的成形性能。
此外,通过优化轧制规程和轧制过程的参数控制策略,可以减小钢材的粗晶度和颗粒度,从而提高钢材的综合机械性能和耐腐蚀性能。
其次,热轧工艺优化可以改善钢材的微观组织和相变行为。
通过调整加热温度、保温时间、冷却速率等工艺参数,可以控制钢材的相变行为和组织形态,从而改善钢材的晶粒细化程度和均匀性,提高钢材的织构均匀性和物理性能。
此外,优化热轧工艺可以减少钢材的奥氏体转变率,提高钢材的强度和塑性。
再次,热轧工艺优化可以降低钢材的残余应力和细小缺陷。
通过优化轧制规程和轧制机组的参数控制策略,可以减少轧制过程中的应力集中和应力彼此相互作用,从而减小钢材的残余应力。
此外,优化喷水冷却过程和冷却介质的选择,可以有效控制钢材的冷却速率和温度梯度,减少钢材表面和内部的细小缺陷,提高钢材的表面质量和内部杂质的均匀性。
最后,热轧工艺优化可以提高钢材的生产效率和降低成本。
通过合理调整热轧工艺的参数和控制策略,可以减少钢材的轧制次数和工序,提高生产效率和产量。
此外,优化轧制过程和控制系统,可以减少故障率和停机时间,降低钢材生产过程中的能耗和成本。
其次,热轧工艺优化在钢材成形性能提升中的研究主要包括以下几个方面。
首先,研究热轧工艺参数对钢材成形性能的影响。
天铁1750热轧层冷模型的调整和优化

平 直 度 合格 率
98 9 5% 1 0% 0 99 6 2%
99 46% g7 9 9%
精 轧 出 出 口温 度 合 格 率
9 5% 99 9 9 44% 10 0%
10 0% 9 2% 9 9
卷取 温 度 合 格 率
其控 制 时序 为 :精 轧 模 型 在 预 计 算 时 启 动 层 流 冷 却 区 的 预 设 定计 算 , 照 工 艺 要 求 的终 轧温 度 、 取 温 度 和 精 轧 的速 按 卷 度 等 关键 数 据 ,预 设 定 层 冷 区 所 需 的 喷 淋 模 式 和 开 关 水 阀的 数量 , 精轧 F 在 2咬 钢 后 , 照 设 定 值 开 关 水 阀 , 带 钢 的 头 部 按 对
线 钢 X7 、 6 0 X 0等 , 冷 温 度 控 制模 型 不 支 持 , 取 入 口实 测 温 层 卷
度 达 不 到 目标 温 度 , 度 偏 低 , 制 模 型 不 能 有 效 调 节 , 重 温 控 严 影 响 了 管 线 钢 的 机 械 性 能 以 及 钢 种 的 研 发 工 作 。 表 2为 XT 、 O X6 的 各 项 指 标 。图 1为 X7 0 0卷 取 入 口 实 测 温 度 , 钢 的 卷 取 带 温 度 命 中 率 只 有 30 左 右 。 %
出每 块 带钢 在 层 冷 的 开 阀数 目,卷 取温 度 命 中率 基 本 在 8 0%
以上 。
但 对 卷取 目标 温度 低 于 5 0。 5 C的钢 种 进 行 计 算 时 ,如 管
92. 27% 64. 8% 4 85 05%
76 4 3% 80 71 %
12 卷 取 目标 温 度 无 法 实 现 低 温 控 制 _ 在 对 卷 取 目标 温 度 为 5 0 4 ℃ 的 钢 种 进 行 计 算 时 , 9 ~6 0 层 冷 温 度 控 制模 型根 据 带 钢原 始数 据 和 高温 计 反馈 值 周 期计 算
《热轧钢板超快速冷却工艺的研究》范文

《热轧钢板超快速冷却工艺的研究》篇一一、引言热轧钢板作为重要的金属材料,在汽车制造、机械制造、桥梁建筑等多个领域都有着广泛的应用。
为了满足工业发展的需求,热轧钢板的性能提升变得尤为重要。
超快速冷却工艺作为一项先进的钢铁制造技术,能显著改善热轧钢板的性能,因而成为了近年来的研究热点。
本文将对热轧钢板超快速冷却工艺进行研究,以期为工业生产提供理论支持。
二、热轧钢板超快速冷却工艺概述热轧钢板超快速冷却工艺,即通过高效率的冷却设备和方法,将高温状态下的热轧钢板在极短时间内降低到常温,以改善钢板的组织结构,从而提高其机械性能、抗腐蚀性能等。
这种工艺在保证钢板质量的同时,还能提高生产效率,降低能耗。
三、热轧钢板超快速冷却工艺的研究内容1. 冷却速率对热轧钢板性能的影响本研究首先关注了冷却速率对热轧钢板性能的影响。
通过对比不同冷却速率下的钢板性能,我们发现,适当的超快速冷却可以显著提高钢板的强度和韧性,同时也能提高其抗腐蚀性能。
这主要是因为超快速冷却可以使得钢板的组织结构更加均匀、致密。
2. 冷却过程中组织结构的变化本研究还关注了超快速冷却过程中钢板组织结构的变化。
通过金相显微镜和电子显微镜观察发现,超快速冷却能够使得钢板的组织结构变得更加致密、晶粒更加细小。
这种组织结构的改变,使得钢板的机械性能和抗腐蚀性能得到了显著提升。
3. 工艺参数的优化为了进一步提高超快速冷却工艺的效果,我们还对工艺参数进行了优化。
通过调整冷却设备的参数、优化冷却介质的选择等措施,我们成功提高了冷却效率,同时保证了钢板的性能和质量。
四、研究方法本研究采用了理论分析、实验研究和数值模拟相结合的方法。
首先,我们通过查阅文献和资料,对超快速冷却工艺的原理和影响因素进行了理论分析。
然后,我们设计了实验方案,通过实验研究了不同条件下超快速冷却对热轧钢板性能的影响。
最后,我们还采用了数值模拟的方法,对实验结果进行了验证和预测。
五、结论通过对热轧钢板超快速冷却工艺的研究,我们得出以下结论:1. 超快速冷却工艺可以显著提高热轧钢板的性能,包括强度、韧性以及抗腐蚀性能等。
《2024年热轧钢板超快速冷却工艺的研究》范文

《热轧钢板超快速冷却工艺的研究》篇一一、引言随着现代工业的快速发展,对钢材的需求与日俱增,特别是在机械制造、建筑桥梁、船舶制造等重要领域中,对热轧钢板的质量与性能提出了更高的要求。
为了满足市场对高强度、高韧性、高耐腐蚀性等特性的需求,热轧钢板的加工工艺成为了研究的热点。
其中,超快速冷却工艺作为一种新型的加工技术,对于提高热轧钢板的综合性能具有显著的效果。
本文旨在研究热轧钢板超快速冷却工艺,探讨其工艺特点、影响因素及优化措施。
二、热轧钢板超快速冷却工艺概述热轧钢板超快速冷却工艺是一种通过快速降低钢板温度,以改善其组织和性能的加工技术。
该工艺主要利用高压水或冷却气体等介质,在极短的时间内将钢板从高温状态冷却至室温,从而达到优化钢板组织和性能的目的。
超快速冷却工艺具有冷却速度快、组织细化、性能提升等优点,在提高钢材的强度、韧性、耐磨性等方面具有显著效果。
三、热轧钢板超快速冷却工艺的特点及影响因素1. 工艺特点:(1)冷却速度快:超快速冷却工艺的冷却速度可达每秒数百至数千摄氏度,远高于传统冷却工艺。
(2)组织细化:快速冷却使得钢板的组织得到细化,提高了材料的力学性能。
(3)性能提升:通过优化组织和性能,提高了钢板的强度、韧性、耐磨性等。
2. 影响因素:(1)冷却介质:不同的冷却介质对钢板的冷却效果和组织性能有显著影响。
(2)冷却速度:冷却速度是影响钢板组织和性能的关键因素。
(3)钢板成分与初始状态:钢板的化学成分及初始组织状态对超快速冷却工艺的效果也有重要影响。
四、热轧钢板超快速冷却工艺的优化措施为了进一步提高热轧钢板超快速冷却工艺的效果,可以采取以下优化措施:1. 优化冷却介质:选择合适的冷却介质,以提高钢板的冷却效果和组织性能。
2. 控制冷却速度:根据钢板的特点和性能要求,合理控制冷却速度。
3. 调整钢板成分与初始状态:通过调整钢板的化学成分和初始组织状态,以提高超快速冷却工艺的效果。
4. 引入智能控制技术:利用计算机技术和自动化控制技术,实现超快速冷却工艺的智能化控制,提高生产效率和产品质量。
安钢260机组冷床控制系统改进
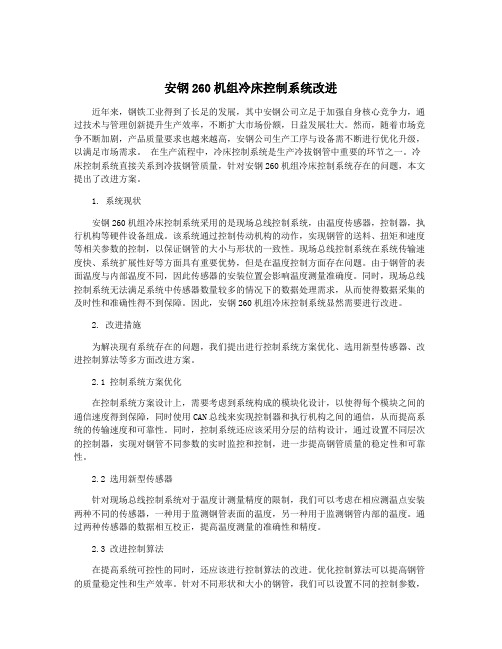
安钢260机组冷床控制系统改进近年来,钢铁工业得到了长足的发展,其中安钢公司立足于加强自身核心竞争力,通过技术与管理创新提升生产效率,不断扩大市场份额,日益发展壮大。
然而,随着市场竞争不断加剧,产品质量要求也越来越高,安钢公司生产工序与设备需不断进行优化升级,以满足市场需求。
在生产流程中,冷床控制系统是生产冷拔钢管中重要的环节之一。
冷床控制系统直接关系到冷拔钢管质量,针对安钢260机组冷床控制系统存在的问题,本文提出了改进方案。
1. 系统现状安钢260机组冷床控制系统采用的是现场总线控制系统,由温度传感器,控制器,执行机构等硬件设备组成。
该系统通过控制传动机构的动作,实现钢管的送料、扭矩和速度等相关参数的控制,以保证钢管的大小与形状的一致性。
现场总线控制系统在系统传输速度快、系统扩展性好等方面具有重要优势,但是在温度控制方面存在问题。
由于钢管的表面温度与内部温度不同,因此传感器的安装位置会影响温度测量准确度。
同时,现场总线控制系统无法满足系统中传感器数量较多的情况下的数据处理需求,从而使得数据采集的及时性和准确性得不到保障。
因此,安钢260机组冷床控制系统显然需要进行改进。
2. 改进措施为解决现有系统存在的问题,我们提出进行控制系统方案优化、选用新型传感器、改进控制算法等多方面改进方案。
2.1 控制系统方案优化在控制系统方案设计上,需要考虑到系统构成的模块化设计,以使得每个模块之间的通信速度得到保障,同时使用CAN总线来实现控制器和执行机构之间的通信,从而提高系统的传输速度和可靠性。
同时,控制系统还应该采用分层的结构设计,通过设置不同层次的控制器,实现对钢管不同参数的实时监控和控制,进一步提高钢管质量的稳定性和可靠性。
2.2 选用新型传感器针对现场总线控制系统对于温度计测量精度的限制,我们可以考虑在相应测温点安装两种不同的传感器,一种用于监测钢管表面的温度,另一种用于监测钢管内部的温度。
通过两种传感器的数据相互校正,提高温度测量的准确性和精度。
中厚板生产中自动化控制系统的应用与优化

中厚板生产中自动化控制系统的应用与优化摘要:中厚板轧制自动化系统反映了线材轧制控制的自动化程度,采用中厚板轧机自动控制系统不仅可以提高生产质量和利用率,而且可以满足特殊的控制要求。
从AGC绝对厚度控制、轧区跟踪系统和自动轧制三个方面介绍了自动控制优化的实际应用关键词“绝对AGC”;中厚板;自动化系统钢铁行业是典型的制造生产过程包括各种钢铁工业,具有很高的针对性和渗透性。
生产过程不仅包括成本、质量和效率等市场竞争因素,还包括资源、能效和可承受性等因素,以及过程排放、环境兼容性和工业生态系统等可持续发展因素。
一、中厚板生产工艺概述轧制产品(各种钢材)作为钢铁行业长流终端技术,直接服务于各行各业。
轧钢工艺的品种和质量首先代表了钢铁行业的整体生产水平,经过检查和清理的坯料被送到铸坯车间原料跨进行切割所需的长度。
按类型、来源、钢种和生产计划储存。
推料机将一个轧制坯料一个接一个推入辊道,并将其送入加热炉;送料机将板材加热至1150-1250℃后将其推入热炉,板材通过辊子输送至轧机。
除鳞箱经过首先氧化铁皮从高压水中去除;然后进入轧机。
四辊可逆式轧机。
轧机配有锥形工作辊,用于轧制工件。
高压水去除轧制表面的氧化铁。
通用13-17次往复轧,至最终产品的尺寸,轧制后,钢板由钢板矫直机矫直,钢板矫直后由冷床冷却。
在生产过程中,钢板的加工主要包括厚度、宽度、钢板长度等物理尺寸。
为了提高轧制板材的机械性能,通常在轧机后部安装快速冷却装置,将轧制板材冷却到一定温度,以获得所需的板材性能。
厚板自动轧制系统的控制功能包括:将工件从原来的厚度、宽度和长度轧制到所需的厚度、宽度和工件长度。
快速冷却板具有良好的机械性能。
计划在该地区增加产量,以提高生产速度和生产率。
在生产过程中,操作者必须在生产过程中进行指导和控制,维修人员必须有一定的控制手段,以便于错误的处理。
二、案例分析1.AGC厚度绝对控制。
厚钢板轧机的自动控制系统采用AGC绝对厚度控制系统建立轧制宏微观跟踪平台,根据L2系统数据和自动轧制的主要功能,实现可逆自动轧制过程。
棒材冷床电动裙板上钢装置结构型式分析与优化
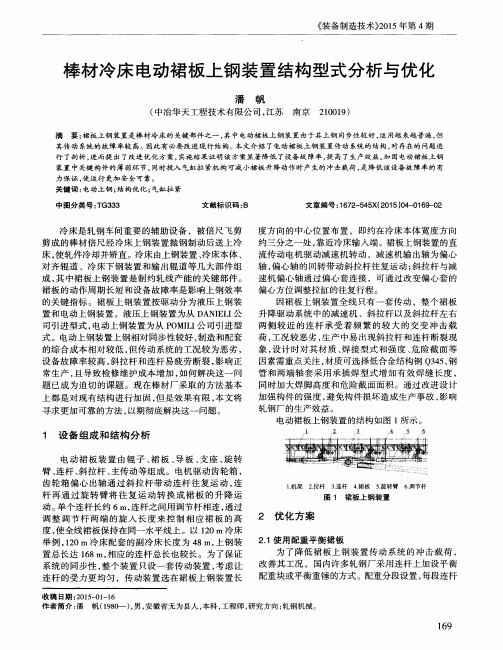
1 设 备 组 成 和 结 构 分 析
电动裙 板装 置 由辊 子 、 裙板 、 导板 、 支座 、 旋 转 臂、 连杆 、 斜拉杆 、 主传动等组成。电机驱动齿轮箱 , 齿 轮 箱 偏 心 出轴 通 过 斜 拉 杆 带 动 连 杆 往 复 运 动 , 连 杆再 通过 旋转 臂将 往复运 动转 换 成裙 板 的升 降运 动。 单 个 连杆 长 约 6 m, 连 杆 之 间用 调 节杆 相 连 , 通 过 调 整 调 节 杆 两 端 的 旋 人 长 度 来 控 制 相 应 裙 板 的 高 度, 使 全 线 裙板 保 持 在 同一水 平 线 上 。以 1 2 0 m冷 床 举例 , 1 2 0 m冷床配套的副冷床长度为 4 8 m, 上钢装 置总长达 1 6 8 m, 相 应 的 连 杆 总长 也 较 长 。为 了保 证 系 统 的 同步 性 , 整 个 装 置 只设 一 套 传 动装 置 , 考 虑 让 连杆 的受力更均匀 ,传动装置选在裙板上钢装置长
收 稿 日期 : 2 o 1 5 一 O 1 — 1 6 作者简介 : 潘 帆( 1 9 8 o _ _ ) , 男, 安 徽省无为县人 , 本科 , 工程师 , 研究方 向 : 轧钢机械 。
l 6 9
Eq u i p me n t Ma n u f a c t u r i n g T e c h n o l o g y N o . 4, 2 0 1 5
其传动 系统的故 障率较 高。因此有 必要 改进现行 结构。 本 文介绍 了电动裙板 上钢装置传动 系统 的结构 , 对存在 的问题进
行 了剖 析 , 进 而提 出 了 改进 优 化 方 案 , 实施 结 果 证 明 该 方 案 显 著 降低 了设 备 故 障率 , 提 高 了 生产 效 益 。 加 固 电 动 裙板 上 钢
棒材冷床乱钢、头尾弯钢现象分析及性能优化

•酒钢科技2019年第3期•棒材冷床乱钢、头尾弯钢现象分析及性能优化梁新建,康开军(酒钢集团宏兴股份公司炼轧厂,甘肃,嘉峪关,735100)摘要:通过对大棒线棒材冷床乱钢、头尾弯钢现象分析及改进,介绍涉及冷床乱钢、头尾弯钢的诊断思路、步骤及运行机理,并对此类故障现象进行了诊断与分析,提高设备运行稳定性及工艺控制指标。
简单介绍冷床乱钢、头尾弯钢现象控制技术。
关键词:冷床;乱钢;头尾弯钢;改进措施;性能优化Analysis and Performance Optimization of Bar Chaos and Head-tailBending at Bar Cooling BedLiang Xinjian,Kang Kaijun(Steel-making and Rolling Plant of Hongxing Iron&Steel Co.Ltd..Jiuquan Iron and Steel(Group)Corporation,Jiayuguan,Gansu,735100)Abstract::Through the analysis and improvement of bar chaos and head-tail bending at cooling hed,the diagnosis ideas,steps and operation mechanism of the phenomenon are introduced.The diagnosis and analysis of such fault phenomena were carried out to improve equipment operation stability and process control indicators.Its control technology is introduced Briefly.Key words:cooling bed;bar chaos;head-tail bending;improvement measures;performance optimization1«•*刖g酒钢集团宏兴钢铁公司炼轧厂大棒线作业区设计能力年产100万吨。
冷床上钢装置影响轧钢生产指标的原因分析

213管理及其他M anagement and other冷床上钢装置影响轧钢生产指标的原因分析闫同辉(陕钢集团汉中钢铁有限责任公司轧钢厂,陕西 汉中 724200)摘 要:通过实际生产中对于冷床运行情况的观察和有关问题的探究,分析出冷床上钢装置影响成定尺率,成材率,作业率的操作因素和相关联的设备因素。
关键词:液压步进式冷床 ;输入辊道 ;升降裙板 ;同步轴 ;限位接近开关中图分类号:TF341 文献标识码:A 文章编号:11-5004(2020)01-0213-2收稿日期:2020-01作者简介:闫同辉,男,生于1973年,汉族,陕西西安人,大专,轧钢高级技师,研究方向:轧钢。
轧钢厂棒线车间冷床装置为液压裙板式步进冷床,曾经在一段时期轧钢生产的过程中,由于液压裙板上钢装置相关原因产生弯钢,乱钢,导致了收集过程中增加一定量的非定尺钢材和废品材,增加了收集作业强度,降低了轧钢生产节奏,影响了定尺率,成材率和作业率。
1 轧钢冷床相关工序流程(1)冷床工序流程。
从成品架次轧制出钢材经过分段剪切成为倍尺钢材,由倾斜放置的圆柱形输入辊道【由0°逐渐过渡到12°】输送至制动裙板,经由裙板进行升降动作将倍尺钢材分隔传送并适时托起到高位使钢材滑入过渡板,进入冷床本体进行冷却,齐头,收集。
如下图。
图1 冷床相关工序流程图L1倍尺剪到裙板前端的距离;L2为升降裙板端部到冷床入口的距离;L3为冷床的长度;L 为倍尺钢的长度;I 为倍尺钢到分钢点的距离;S 为倍尺钢所需的制动距离;d 为倍尺钢端部到冷床端部的距离。
(2)液压裙板上钢装置结构图。
图2 步进冷床上钢装置结构图1同步轴;2液压缸;3输入辊道;4辊道电机;5倍尺钢材;6矫直板;7升降裙板;8过渡滑板;9裙板支撑连杆;10底座1;11底座2;12底座32 液压裙板上钢装置动作原理及参数的设置2.1 液压裙板式上钢装置各部件功能轧钢生产的冷床长120m,步进周期5s。
冷床上料设备优化

设备管理与维修2018翼11(上)冷床上料设备优化魏嘉兵,赵燕晖(河钢集团唐钢公司型钢厂,河北唐山063016)摘要:针对不对称断面型钢上冷床冷却时变形不均匀,产生较大侧弯的问题,结合型钢厂大型线全液压步进式冷床结构和性能参数,对上料小车进行了局部改造,通过编写自动化程序,实现不对称断面轧件的预弯功能,提高矫直工序加工质量。
关键词:冷床;小车;推头;预弯中图分类号:TG335.4文献标识码:BDOI :10.16621/ki.issn1001-0599.2018.11.600引言河钢唐钢型钢厂属于大型型钢生产线,可生产铁塔用角钢、船用型钢、矿用U 形钢、圆钢、电极扁钢及其他规格型材等多个品种。
各种规格产品化学成分均匀,物理性能稳定,尺寸精度高,表面质量好,受到国内外用户的一致认可和赞同。
型钢冷床是大型型钢生产线中的重要设备之一,是生产中不可缺少的重要环节,主要作用是承载高温轧件及冷却。
目前根据钢铁市场形式,成功研发生产了(14耀18)英寸铁路垫板、PU(热轧U 形钢板桩)400mm伊170mm 热轧钢板桩、(36#耀40#)(a ,b ,c )槽钢和D8履带钢等建筑工程机械系列用钢。
随着生产品种的不断研发,目前的型钢生产线设备,已不能满足要求越来越高的工艺要求。
为此,介绍大型线型钢冷床的主要结构创新和优化,探讨及研究新的上料结构型式采用的原因。
以求不断提高轧件质量,克服轧件弯曲对矫直工序造成的不利影响,有利于企业持续生存发展。
攻关过程中,结合理论知识,以科学计算为手段,经过现场仔细观摩,发现左右不对称断面型钢在冷却时,由于轧件温度变化速率不同,造成轧件在冷却时产生侧弯,甚至S 弯,随着不对称程度的加大,轧件弯曲程度增大,形状变化随着增大。
当弯曲达到一定程度时,弯曲轧件在冷床冷却、辊道运输、后序矫直困难,导致工艺流程受阻,甚至不能生产。
现有的型钢冷床在冷却轧件过程中发生侧弯现象严重,尤其对履带钢轧件不利。
安钢260机组冷床控制系统改进

安钢260机组冷床控制系统改进背景安钢260机组是安阳钢铁集团的主要生产线之一,生产高质量的钢材。
冷床是钢材生产过程中的重要环节,需要控制温度、重量、位置等各种参数,确保钢材冷却均匀、不变形。
然而,现有的冷床控制系统存在一些问题。
首先,系统稳定性不够,容易出现故障导致生产中断。
其次,用户操作不够简单,需要经验丰富的操作员才能正常操作系统。
最后,数据采集不够准确,导致生产数据分析和质量控制不够精准。
为了解决这些问题,需要对冷床控制系统进行改进。
改进方案为了增强系统稳定性,我们选择了更加可靠的硬件和通信协议。
首先,我们替换掉了原有的采集板和通信协议。
新采集板采用了国内领先的压力变送器、温度传感器和流量计,能够更加精准地采集冷却水的温度、流量和压力等参数。
通信协议采用了Modbus协议,能够在数据传输中检测和纠错,提高了数据传输的可靠性。
为了提高用户操作的简便性,我们对系统的界面进行了改进。
新的界面采用了人性化的设计,可以让使用用户更加容易理解和操作系统。
同时,我们增加了联网功能,可以通过互联网远程控制冷床的参数和状态,提高了生产的效率。
为了提高数据采集的准确性,我们采用了更加精准的算法和模型。
之前的数据采集方式主要依赖于采集器采集的原始数据,不够准确。
现在我们引入了模型算法,能够更加准确地估计冷却水的温度、流量和压力等参数。
同时,我们还加入了数据分析功能,可以对采集的数据进行分析,实现生产数据的监控和质量控制。
总结通过以上的改进,安钢260机组冷床控制系统的稳定性、操作便捷性和数据准确性都得到了大幅提升,能够更好地满足生产需要。
同时,我们还将继续关注新的技术和工艺的发展,不断地对系统进行优化和改进,提高生产的效率和质量。
安钢260机组冷床控制系统改进

安钢260机组冷床控制系统改进随着我国钢铁行业的快速发展,安钢260机组已成为了安钢公司的标志性生产线。
作为生产线中的重要部件,冷床在钢铁生产中扮演者至关重要的角色。
因此,为了提高钢铁生产效率,减少安全隐患,现对安钢260机组冷床控制系统进行改进。
目前,安钢260机组冷床控制系统采用PLC控制系统,通过PLC程序来实现对注油、换块、修整、上下料等控制。
但是,采用PLC控制系统存在以下问题:其一、PLC控制器功能受限。
PLC主要以自动化控制为主,对于申编程和编程语言都有比较高的要求,针对冷床运行中复杂的生产环境,PLC控制器所能完成的控制功能比较有限,容易出现控制上的不足。
其二、PLC 难以适应网络化环境。
PLC控制器大多运用于工业现场,与无线通讯和互联网接口不兼容,难以适应安全运行和工业大数据方面的需求。
以上这些问题,制约了安钢260机组冷床控制系统的长远发展,不能满足市场的需求。
为了进一步提高安钢260机组冷床控制系统的生产效率和安全性,需要进行改进。
针对这些问题,我们提出了一种基于高通量数据处理和网络化通讯的冷床控制系统改进方案。
该方案的关键技术包括:高速数据处理、驱动和通讯技术、计算与分析技术、智能算法技术。
1.高速数据处理技术传统PLC是通过一系列逻辑操作对进来的数据进行处理,然后控制输出。
但是在当前工业大数据环境下,数据处理量巨大,对处理速度的要求也越来越高,如何对进来的数据快速、准确地进行处理才能提高生产效率。
因此,我们采用FPGA芯片作为数据的处理器,它可以非常快速地进行信号处理、数据转换、图像处理、信号滤波和其他复杂算法的运算和计算。
2.驱动和通讯技术在新的控制系统中,我们采用了CAN总线技术,实现不同模块间的通信协议。
此外,我们还引入了无线通信技术,方便远程监控和控制。
3.计算与分析技术这种改进使冷床控制系统具有网络化能力,通过与计算中心的连接,可以实现数据的即时分析。
通过大规模数据分析,我们可以实时判断冷床运行状态,从而预测潜在故障和维护需求,减少停机时间和降低维修成本。
优特钢冷床上钢系统的优化与改造
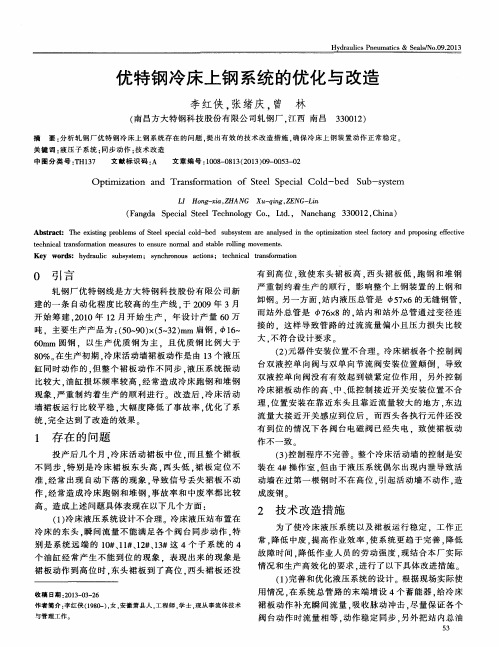
优 特钢冷床 上钢 系统 的优化 与改造
李红侠 , 张绪庆 , 曾 林
( 南 昌方 大特 钢科 技 股份 有 限公 司轧钢 厂 , 江西 南 昌
摘
3 3 0 0 1 2 )
墙裙 板 运行 比较 平稳 . 大 幅度 降低 了 事故 率 , 优 化 了系
统. 完全 达 到 了改造 的效 果 。
1 存 在 的 问题
投 产后 几 个 月 . 冷 床 活 动裙 板 中位 . 而且 整 个 裙 板 不 同步 , 特 别是 冷 床裙 板 东 头 高 , 西头低 , 裙 板 定 位 不
Байду номын сангаас
要: 分 析 轧 钢 厂 优 特 钢 冷 床 上 钢 系统 存 在 的 问题 , 提 出有 效 的 技 术 改 造 措 施 , 确 保 冷床 上钢 装 置 动 作 正 常 稳 定 。
关键词 : 液 压 子 系统 ; 同步动作 ; 技 术 改 造 中图分类号 : T H1 3 7 文献标识码 : A 文章编号 : 1 0 0 8 — 0 8 1 3 ( 2 0 1 3 ) 0 9 — 0 0 5 3 — 0 2
成废 钢
准。 经 常 出现 自动 下落 的现 象 。 导 致 信号 丢 失 裙板 不 动 作. 经 常造 成 冷 床 跑钢 和 堆 钢 . 事 故 率 和 中废 率 都 比较 高 造 成上 述 问题 具体 表 现在 以下 几个 方 面 : ( 1 ) 冷 床液 压 系统设 计 不合 理 。冷 床液 压站 布 置在
O 引 言
轧钢 厂 优 特 钢线 是 方 大特 钢 科 技股 份 有 限公 司新
优化冷床上钢系统,提高上钢稳定性

优化冷床上钢系统,提高上钢稳定性尹莹莹;李希宝【摘要】本文主要介绍了山东石横特钢公司棒材车间在生产小规格多切分螺纹时(φ10×5、φ12×4),冷床上钢系统不稳定,乱钢现象严重,针对此现象成功地对冷床上钢系统进行了优化改造,可有效降低设备故障时间,提高成材率,保证产品质量,创造较高的经济效益。
%This paper mainly introduces the unstable bedsteel system and steel chaos phenomenon in the production of small size multi cutting thread (Φ10 “5 ,12”,4 ) in workshops of Shandong Shiheng Special Steel Company. In accordance with this phenomenon, this paper described how to optimize the bedsteel system , which can effectively reduce the fault time , improve yield rate , ensure product quality and create higher economic benefits.【期刊名称】《现代制造技术与装备》【年(卷),期】2014(000)002【总页数】2页(P55-56)【关键词】小规格多切分;冷床上钢系统;分钢装置【作者】尹莹莹;李希宝【作者单位】山东石横特钢集团有限公司,泰安 271612;山东石横特钢集团有限公司,泰安 271612【正文语种】中文山东石横特钢集团有限公司第一棒材车间(以下简称一棒)是国产棒材全连轧生产线,于2005年4月份建成投产年设计能力为60万t,现已达到100万t的生产能力。
优特钢冷床上钢系统的优化与改造

优特钢冷床上钢系统的优化与改造
李红侠;张绪庆;曾林
【期刊名称】《液压气动与密封》
【年(卷),期】2013(033)009
【摘要】分析轧钢厂优特钢冷床上钢系统存在的问题,提出有效的技术改造措施,确保冷床上钢装置动作正常稳定.
【总页数】2页(P53-54)
【作者】李红侠;张绪庆;曾林
【作者单位】南昌方大特钢科技股份有限公司轧钢厂,江西南昌330012;南昌方大特钢科技股份有限公司轧钢厂,江西南昌330012;南昌方大特钢科技股份有限公司轧钢厂,江西南昌330012
【正文语种】中文
【中图分类】TH137
【相关文献】
1.优化热轧直条冷床上钢系统案例分析 [J], 杨凤华;张其斌;王水龙;唐嘉;阳志清;陈积华
2.南钢棒材冷床上钢液压系统分析与技术改造 [J], 熊季就;刘清华;唐嘉;李红侠
3.优特钢棒材冷床技术 [J], 张荣滨;荣崎
4.红钢棒材线冷床上钢装置故障分析与改造 [J], 杨文磊
5.优化冷床上钢系统,提高上钢稳定性 [J], 尹莹莹;李希宝
因版权原因,仅展示原文概要,查看原文内容请购买。
工程最优化设计MATLAB大作业-棒材连轧车间倍尺飞剪至冷床距离的优化
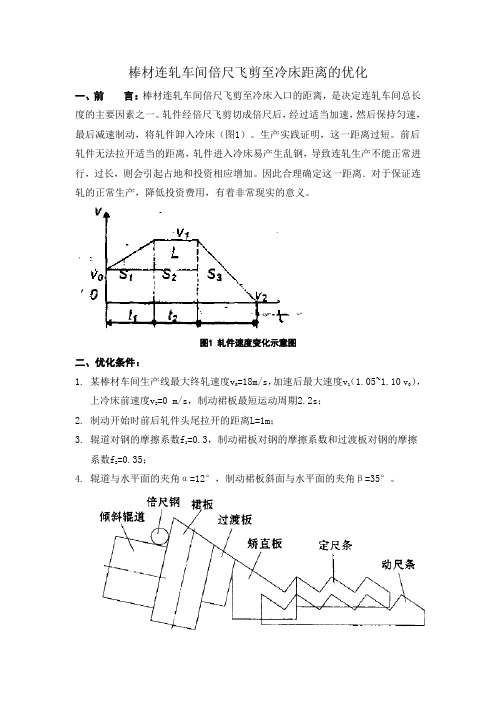
棒材连轧车间倍尺飞剪至冷床距离的优化一、前言:棒材连轧车间倍尺飞剪至冷床入口的距离,是决定连轧车间总长度的主要因素之一。
轧件经倍尺飞剪切成倍尺后,经过适当加速,然后保持匀速,最后减速制动,将轧件卸入冷床(图1)。
生产实践证明,这一距离过短。
前后轧件无法拉开适当的距离,轧件进入冷床易产生乱钢,导致连轧生产不能正常进行,过长,则会引起占地和投资相应增加。
因此合理确定这一距离.对于保证连轧的正常生产,降低投资费用,有着非常现实的意义。
图1 轧件速度变化示意图二、优化条件:1.某棒材车间生产线最大终轧速度v0=18m/s,加速后最大速度v1(1.05~1.10 v),上冷床前速度v2=0 m/s,制动裙板最短运动周期2.2s;2.制动开始时前后轧件头尾拉开的距离L=1m;3.辊道对钢的摩擦系数f1=0.3,制动裙板对钢的摩擦系数和过渡板对钢的摩擦系数f2=0.35;4.辊道与水平面的夹角α=12°,制动裙板斜面与水平面的夹角β=35°。
图2 上冷床装置结构5.轧件上冷床的过程(1)轧件向冷床区传送。
由于辊道呈倾斜布置,轧件将在辊道和裙板侧面形成的夹角处向前传送,此时裙板必须处于高位(如图2所示)。
同时,为了满足相邻两根轧件都能顺利上冷床,轧件尾部到达分钢点(裙板下降到低位的时刻所对应的位置)时与下一根轧件头部必须拉开一定距离。
因此,倾斜辊道向冷床区传送轧件的过程是一个加速过程。
一般将倾斜辊道分成三段控制,并使每段辊道线速度超前于成品机架出口速度。
(2)倍尺钢尾部到达分钢点时裙板由高位下降到低位,倍尺钢沿裙板顶面从倾斜辊道滚落到裙板顶面与过渡板侧面形成的夹角处,倍尺钢开始摩擦制动。
(3)为了接收来自倍尺剪的下一根倍尺钢,裙板到达低位后立刻返回到中位并延长一定时间,倍尺钢完成摩擦制动。
(4)为了将完成制动的倍尺钢输送到矫直板的第一个槽,裙板上升到高位并延长一定时间,以等待下一根倍尺钢尾部到达分钢点。
- 1、下载文档前请自行甄别文档内容的完整性,平台不提供额外的编辑、内容补充、找答案等附加服务。
- 2、"仅部分预览"的文档,不可在线预览部分如存在完整性等问题,可反馈申请退款(可完整预览的文档不适用该条件!)。
- 3、如文档侵犯您的权益,请联系客服反馈,我们会尽快为您处理(人工客服工作时间:9:00-18:30)。
1 8 6 7 mi n , 平均每月 3 . 4 6 h 。 对后道工序影响非常大。 冷床跑钢
和飘钢造成冷床上的钢比较乱 , 弯钢 和钢不齐现象较多 , 从而对 冷剪剪切和包装影响较大 , 而且 产生 大量非定尺 , 对成材率和包
装质量影响较大。
( 1 ) 3 飞剪后( 保 留直辊道 1 0件 ) 所有辊道和辊道架进行改
最辛 苦的岗位 。安全危 害相 当大 。
在冷床周 围做的安全 防护非 常多 ,
图 1 对辊道和辊道架进行改进设计
豳 设 置 鼍 理 与 维 俺2 0 1 5 N o l 0
S I MODR I V E 6 1 1 D 数 字伺 服 驱 动故 障处 理
姜娟娟 张耀词
电路
故 障处理
D OI 1 0 . 1 6 6 2ቤተ መጻሕፍቲ ባይዱ1 / j . c n k i . i s s n l 0 0 1 — 0 5 9 9 . 2 0 1 5 . 1 0 . 2 4
( 中航 飞机 西 安 飞机 分公 司设 备 总 厂 西安 )
摘 要 针对 S I MO D R I V E 6 1 1 D 数字伺服驱动故障现 象, 结合 6 1 1 D电源模块指示灯状态 , 分析故障原 因, 给 出故障处理方法。 关键词 数控设备 数字伺服驱动 电源模块
文献 标 识 码 B
存在高低不平现象 。 升降滑板升 降高度不够 , 导致钢在辊道 内易
弹出。 摩擦板和升降滑板磨损错位较大 , 不能完全保证在同一平 面上 , 裙板设计不合理 , 更换难度大。 ( 4 ) 矫直板设计不合理 , 易撞钢 , 备件消耗 较大 。 升降滑板升 降速度过快 , 造成冲击 大 , 振动大。
优化 热轧直条冷床上钢 系统案例分析
杨风 华 张其斌 王水龙 唐 嘉 阳志清 陈积华
( 南昌方 大特钢科技股份有 限公 司轧钢厂 南 昌)
摘要 轧钢厂棒材生产线冷床 上钢 系统 , 自 切分轧制后存在各种弊 端, 如跑钢严 重。 提 出有效改进措施 , 确保 冷床上钢 系统稳定
跑 钢对生产、 质量 、 指标 、 设 备管理 、 安全、 职 工劳动强度都造成
( 1 ) 变频辊上辊面与导槽底 面高度过大 , 棒材原设计辊面高 度 1 0 m m, 通过考察萍钢 、 石 横特钢 和方 大特钢其他 轧钢生产
线辊面高度都< 6 mm, 钢在辊道 内行走较平稳 , 石横基本 没有弹 跳现象( 辊面高度只有 3 m m) , 萍钢也较平稳。
运行。
关键 词 冷床上钢系统
中图分类号
一
辊道架改进
文献标识码
升降滑板
B
D OI 1 0 . 1 6 6 2 1 / j . e n k i . i s s n l 0 0 1 — 0 5 9 9 . 2 0 1 5 . 1 0 . 2 3
T H1 7
、
概 述
但经常还是存在伤人现象 , 特别是在冷床上处理跑 钢时 , 特别危 险, 2 0 0 6 — 2 0 1 1 年 出现过 3 起 热钢穿脚事故 。
辊、 电机 、 裙板 、 摩擦板 、 矫直 板 、 齿 条等备件 消耗 较大 , 只要有一点缺 陷就下线。 ( 3 ) 职工劳动强度 加大 。由于 冷床上跑 钢 、 飘钢 和变频辊挂钢现 象较 多 ,导致冷床上 的钢较 乱 , 处 理难 度较 大 , 特 别是跑 钢时 , 还要 到高 温的冷床上去处理 , 而且产生
( 2 ) 变频辊 安装角度过小 , 变频辊下钢不利 索 , 特别是 轧直 径1 2 mm棒材 4切分时 , 在辊面方 向的钢较 宽 , 钢还没下完 , 裙 板 已上 升 , 造成 挂钢 , 角度加 大到 1 5 。 对下钢有 利 , 其 他单位 不
存在挂钢现象 。 ( 3 ) 电机卧式安装 方式保证不 了所有 中心高一致 , 所以辊面
非 常大的影响 , 急待改进解决 。
二、 冷床现状
自 切分轧制实施以来 , 冷床跑钢现象就一直存在 , 特别是对
直径 1 2 — 2 5 m m 钢实 现全规格 切分轧制后 ,跑钢现象尤 为突 出, 钢在辊道 内弹跳厉 害 , 3 飞剪剪切后 分叉严重 , 造成跑钢严
重, 造成多方 面影 响。 ( 1 ) 跑钢严重 , 对指标影 响大 , 2 0 1 1 年 1  ̄ 9月产生 中废 1 2 6 支, 平均每月 1 4支 , 严重影响各项生产指标 。跑钢事故多 , 严重 影响生产 节奏 。2 0 1 1年 1 - 9月 ,棒材变 频辊道影 响时间共计
剪后 1 0个直辊道 不动 , 过度辊 道从 平辊后 开始 , 依次倾斜 2 。 、 4 。 、 6 。 、 8 。 、 1 0 。 、 1 2 。 、 1 5 。 ,每一组度数 为 2个辊道架组成 , 6组辊
大量 的非尺都要靠人工挑 出来 , 所 以棒 材 的冷床 冷剪 操作 工是 棒材
进( 图1 ) 。辊道架单个设计 , 变频辊安装在辊道架 中部 , 电机 固
定 方 式 为端 面 固定 , 电机为 3 k W 变频电机( 与优钢通用 ) 。 3 飞
( 2 ) 对设备 的损坏和设 备维 护难度加大 。由于切分轧制后 , 存在 的诸多 隐患 , 导致对设备要 求非常高 , 维护难度加大 , 变频
三、 主 要 问题
方大特钢轧钢厂棒材线 2 0 0 1 年2 月热负荷过钢成功 ,主要 设备有侧进侧出推钢式加热炉 1 座、 轧机为 6 ( 粗轧 ) + 6 ( 中轧 ) + 6
( 精轧 ) 形式 、 步进齿条式冷床( 9 0 x 8 m , 齿距 8 0 m m ) l 套, 5 0 0 t 冷剪 机 2台、 2条精整包装线。主要轧制螺纹钢 , 以切分轧制为 突破 口, 生产能力 大幅度提高 , 2 0 0 6 年 突破 1 0 0万吨 。目前年生 产能力达 1 2 0万吨。 但一直受冷床上钢系统跑钢 问题 困扰 , 由于