事故原点分析技术.docx
安全事故根源及防范事故对策.doc

安全事故根源及防范事故对策近几年来,各类事故接连发生,飞机失事、商场起火、轮船沉河、人身伤亡等,损失惨重,令人怵目惊心。
安全事故对电力系统来说更是大忌,安全历来具有一票否决权,如何使电力安全生产处于在控和可控状态,是我们每个电力生产职工面对的课题。
萍乡供电公司变电部担负着萍乡电网主网的运行和检修任务,安全责任至关重大。
我们务必剖析事故案例,找出造成事故根源,吸取事故教训,采取防范措施,防止各类事故的发生。
一、造成事故的根源:众所周知,安全是电力系统永恒的主题。
提起安全工作,大家都认为很重要,但在日常工作中,形成了说起来重要,干起来次要,忙起来不要的怪圈。
每年印发的安全文件最多,开展安全学习的时间最多,各级领导对安全的要求也最多,但安全事故仍然屡禁不止,值得我们深刻反思,寻根求源,笔者认为主要有以下造成事故的根源:1、危险点控制不严格。
危险点就是指在作业过程中可能发生事故的地点、部位、场所、工器具或行为等,它是诱发事故的因素,如果作业人员不进行防范和采取措施,在一定条件下,就会演变成事故。
变电运行检修的危险点主要表现在倒闸操作、大型检修、设备缺陷、恶劣天气作业等。
凡在操作中发生事故,都是没有认真把好操作六关,即填写、审核、模拟、监护、唱票、检查。
凡在施工检修中发生事故,都是在安全措施的布置和有效的监护环节上出了问题。
恶劣天气作业和设备带病情况下发生事故则是没有加强设备巡视和采取积极的预防措施。
2、工作中存在麻痹思想和侥幸心理。
运行工作,年复一年,久而久之,产生麻痹思想和懈怠情绪,无形中发生习惯性违章。
凡发生人为安全事故,必定存在违章因素,而违章不一定出现安全事故,所以有的职工存在侥幸心理,图省事,在工作中不知不觉地违了章,玩走钢丝绳的游戏,殊不知一旦发生安全事故,给企业造成损失,给家庭带来不幸,悔之晚矣。
在长期的运行工作中,运行人员普遍存在麻痹思想和侥幸心理,认为自己运气好就不会出事故,机遇不好的人才会出事故,于是该到现场检查的没有去检查,该立即停用的压板而去跳项操作,该履行监护职责的没有到位,留下隐患,最终导致事故的发生。
事故原因分析及对策-原因分析(标准版)

Safety is the goal, prevention is the means, and achieving or realizing the goal of safety is the basic connotation of safety prevention.(安全管理)单位:___________________姓名:___________________日期:___________________事故原因分析及对策-原因分析(标准版)事故原因分析及对策-原因分析(标准版)导语:做好准备和保护,以应付攻击或者避免受害,从而使被保护对象处于没有危险、不受侵害、不出现事故的安全状态。
显而易见,安全是目的,防范是手段,通过防范的手段达到或实现安全的目的,就是安全防范的基本内涵。
卢世红中国石化集团安全局为了保障加油站的安全生产,国家不断强化安全法制建设和标准建设,如在加油站标准的制定完善上,于1992年发布了《小型石油库及汽车加油站设计规范》。
2002年根据变化的形势,发布了《汽车加油气站设计与施工规范》(GB50156-2002);在加油站的安全法制建设上,最近颁布的《中华人民共和国安全生产法》、《危险化学品安全管理条例》、《危险化学品经营企业安全评价导则》、《安全生产许可证条例》等法规对加油站的安全管理都提出了严格的管理要求。
但是,尽管如此,加油站的事故还是屡屡发生,总结这些事故的原因,主要有以下8点:1.1加油站的建设存在先天性隐患加油站建筑不按照国家标准规定进行建设,就会造成安全间距不足、建筑物耐火等级不够、电气设备不防爆等严重威胁加油站安全的先天性隐患。
目前大多数的个体或家庭式加油点,均未按国家的有关规定、标准及程序进行审批建站,存在布局不合理,防火间距不足等诸多问题,并引发重大事故的发生。
如,2000年1月4日,厦门海沧镇一加油站发生爆炸,造成3人死亡,1人受伤;该加油站为石板条搭盖的半地下式建筑。
事故分析报告范文
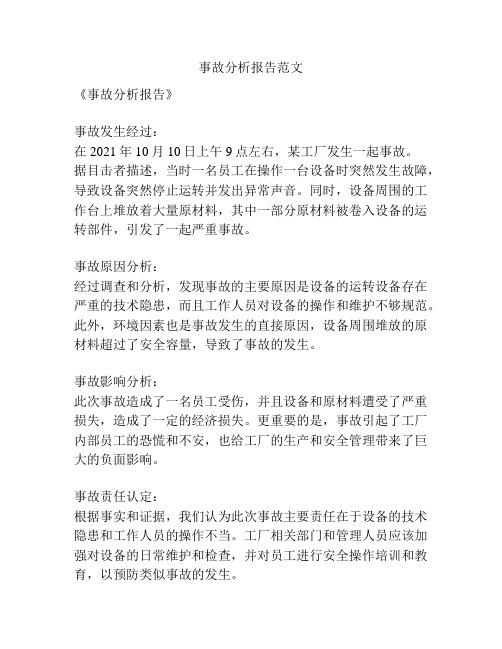
事故分析报告范文
《事故分析报告》
事故发生经过:
在2021年10月10日上午9点左右,某工厂发生一起事故。
据目击者描述,当时一名员工在操作一台设备时突然发生故障,导致设备突然停止运转并发出异常声音。
同时,设备周围的工作台上堆放着大量原材料,其中一部分原材料被卷入设备的运转部件,引发了一起严重事故。
事故原因分析:
经过调查和分析,发现事故的主要原因是设备的运转设备存在严重的技术隐患,而且工作人员对设备的操作和维护不够规范。
此外,环境因素也是事故发生的直接原因,设备周围堆放的原材料超过了安全容量,导致了事故的发生。
事故影响分析:
此次事故造成了一名员工受伤,并且设备和原材料遭受了严重损失,造成了一定的经济损失。
更重要的是,事故引起了工厂内部员工的恐慌和不安,也给工厂的生产和安全管理带来了巨大的负面影响。
事故责任认定:
根据事实和证据,我们认为此次事故主要责任在于设备的技术隐患和工作人员的操作不当。
工厂相关部门和管理人员应该加强对设备的日常维护和检查,并对员工进行安全操作培训和教育,以预防类似事故的发生。
事故处理措施:
针对此次事故,工厂已经采取了以下处理措施:一是对设备进行全面检修和维护,确保设备的安全运转;二是加强对员工的安全培训和教育,提高员工的安全意识和操作技能;三是对工作环境进行整改,确保原材料的堆放符合安全标准。
结论:
通过对此次事故的分析和处理,我们深刻认识到安全生产是企业的首要任务,任何一起事故都会给企业和员工带来巨大的损失。
我们将以此次事故为鉴,进一步加强安全管理,确保类似事故不再发生。
事故报告分析范文
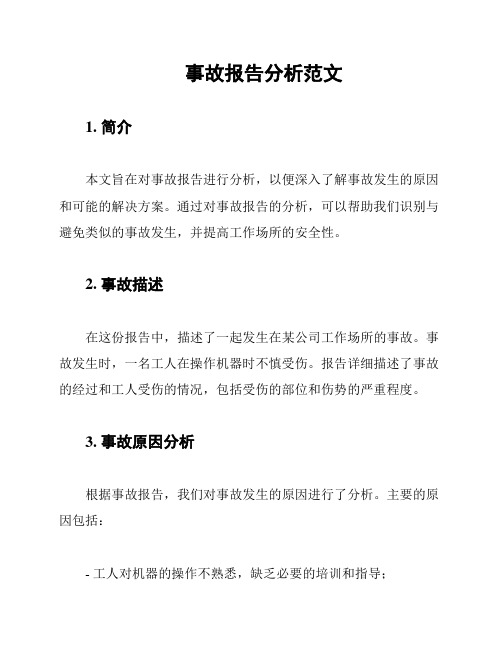
事故报告分析范文
1. 简介
本文旨在对事故报告进行分析,以便深入了解事故发生的原因和可能的解决方案。
通过对事故报告的分析,可以帮助我们识别与避免类似的事故发生,并提高工作场所的安全性。
2. 事故描述
在这份报告中,描述了一起发生在某公司工作场所的事故。
事故发生时,一名工人在操作机器时不慎受伤。
报告详细描述了事故的经过和工人受伤的情况,包括受伤的部位和伤势的严重程度。
3. 事故原因分析
根据事故报告,我们对事故发生的原因进行了分析。
主要的原因包括:
- 工人对机器的操作不熟悉,缺乏必要的培训和指导;
- 工作场所存在一些安全隐患,未及时发现和解决;
- 缺乏规范和安全措施使得工人容易受伤。
4. 解决方案
基于对事故原因的分析,我们提出了以下解决方案:
- 加强对工人的培训,确保他们了解机器的操作方法和安全规范;
- 定期对工作场所进行安全检查,及时发现和解决安全隐患;
- 建立并执行相关的工作流程和安全措施,确保工人的安全。
5. 结论
通过对事故报告的分析,我们可以得出以下结论:
- 工人的培训和知识储备是防止事故发生的重要因素;
- 工作场所安全的持续监管和改进是确保工人安全的关键。
这份事故报告的分析可以为我们研究和改进工作场所的安全性提供宝贵的经验和教训。
> 注意:本文为模拟事故报告分析范文,所述事故为虚构,纯属文档内容写作示例,提供给用户参考。
安全事故分析赵明明

唐山弘基传动科技有限公司安委办
关于赵明明发生安全事故的分析
制造部齿形班班长赵明明2011年3月14日在生产中,发生了右手背被砂轮碰伤缝合四针的安全事故。
根据制造部报告,事故是操作者在内圆磨(数控机床)没有停车,砂轮旋转状态下调整零件过程中发生的。
下面将事故原因及措施分析如下:
一、属于违章作业。
所有操作规程都有停车后才能调刀、调件、调工装卡具的规定;在2010年三级教育测试中,部门级试卷第四题的提问是:调整刀具、装夹、工件,擦拭机床为什么必须停车?从提问上就肯定了调整刀具、装夹、工件,擦拭机床必须停车。
赵明明参加了培训和考试。
二、本人对安全生产认识不足,有麻痹侥幸心理。
在2010年三级教育测试中,公司级试卷第一题(选择题4、怎么对待运动着的工件、刀具和传动部分。
答案A 小心;B 允许;C不准接触。
正确答案是C。
选择题5、调整刀具、装夹、工件,擦拭机床应当怎样操作。
答案A 小心操作;B 注意安全;C 必须停车。
正确答案是C)。
这两个问题都明确了调整工件必须停车,赵明明的试卷填写也正确,可是在实际操作中却没能按照操作规程去做,导致事故发生。
三、总经办和制造部都有安全生产教育不到位、不深入的问题。
没能实现让每一位职工把安全生产入脑入心。
四、措施
第一,总经办把安全生产操作规程印发到班组;
第二,制造部要以班组为单位组织职工反复学习,实现让每位职工都真正入脑入心;
第三,强化上岗前安全生产培训,并把赵明明安全事故作为典型案例教育新职工。
唐山弘基传动科技有限公司安委办
2011年3月16日。
事故根源分析法

15
步骤六: 根源分析(RCA)
关键 因素
直接 原因
间接原因
根本(系统) 原因
• 事故根源2分020析/9法/2的4 应用
根源分析法的步骤
损失
事故
事
直接原因
故
调
查
根本原因
缺乏控制
4
调查的目的
• 引发事故的两个关键条件:人的不安全行为和物的不安全状态。
调查的结论: 重物意外坠落?现场没有摆放围栏?
直接原因
很多时候事故调查在找到直接原因
后就停止了,但是这种调查只停留
在表层,并不能从根本上预防事故。
Hazard
Incident
Near Miss
正确地分析对待每一起事故,那每一 起事故都可能是一笔可贵的财富
• 事故根源2分020析/9法/2的4 应用
在采取行动前澄清真正的问题是什 么,并确信已找到了问题的根源
9
九大步骤
调查阶段(WHAT)
收集证据 (4P+E) 整理证据
建立时间事件链
• 事故根源2分020析/9法/2的4 应用
根源分析法的步骤
事故根源分析法
9/24/2020
1
目录
CONTENTS
事故致因理论 调查方法及主要步骤 案例
• 事故根源2分020析/9法/2的4 应用
2
事故致因理论
瑞士奶酪模型- James Reason
在一个组织中事故的发生有4个层面的因素(4片奶 酪),即组织影响、不安全的监督、不安全行为的前 兆、不安全的操作行为。 每一片奶酪代表一层防御体系,奶酪上的孔代表防御 体系中存在的漏洞或缺陷,这些孔的位置和大小都在 不断变化,当每篇奶酪上的孔在某一时刻排列在一条 直线上,危险就会穿过所有防御措施导致事故发生。
事故分析报告范文

事故分析报告范文事故分析报告。
报告编号,2022001。
报告日期,2022年3月15日。
报告人,XXX。
1. 事故概况。
2022年3月14日晚上8点左右,在XXX工厂生产车间发生了一起严重的机械事故。
事故发生时,工人正在对一台旧设备进行维修,突然设备发生故障,导致工人受伤,设备受损。
事故现场迅速得到控制,伤者已经得到及时救治,情况稳定。
2. 事故原因分析。
经初步调查,事故原因主要有以下几点:(1)设备老化,事故设备已经使用了10年以上,设备老化严重,部分零部件已经出现磨损和腐蚀,导致设备运行不稳定。
(2)维修不当,在进行维修时,工人未按照操作规程进行操作,存在操作失误的可能性。
同时,工人对设备的维修知识和技能不够熟练,导致维修过程中出现了失误。
(3)管理不善,工厂对设备的定期检修和维护管理不到位,设备运行状态未能得到及时监控和维护,导致设备故障发生时未能及时发现和处理。
3. 事故影响分析。
此次事故造成了严重的人员伤害和设备损坏,给工厂生产带来了重大影响。
首先,工人的伤亡给家庭带来了不可挽回的损失,对工厂的员工士气和生产秩序也造成了严重的影响。
其次,设备的损坏导致了生产线的停工,给工厂的生产计划和订单交付带来了严重的延误,给企业的经济效益造成了巨大损失。
4. 事故处理措施。
针对此次事故,我们将采取以下几项措施进行处理:(1)立即对事故设备进行全面检修和维护,确保设备的安全运行。
(2)对工人进行全面的安全培训和技能培训,提高工人的安全意识和操作技能。
(3)加强对设备的定期检修和维护管理,建立健全的设备管理制度,确保设备的安全运行。
(4)对事故的原因进行深入分析和总结,制定相关的预防措施,避免类似事故再次发生。
5. 结论。
此次事故给工厂的生产和员工的安全带来了严重影响,我们将从事故中吸取教训,加强对设备的管理和维护,提高员工的安全意识和技能,确保工厂的安全生产和稳定运行。
同时,我们也将对事故的原因进行深入分析和总结,制定相关的预防措施,避免类似事故再次发生。
事故技术分析报告

事故技术分析报告一、事故概述2023年9月23日,我司发生了一起严重的事故,导致设备损坏,人员受伤。
为了确保类似事故不再发生,我们需要对事故进行深入的技术分析,找出事故原因,并提出相应的改进措施。
二、事故经过当天上午10点30分,我司某车间内正在进行生产作业。
由于操作员操作不当,导致设备发生故障。
随后,设备突然失控,引发了事故。
事故发生时,车间内有5名工作人员在场,其中2人受伤,1人重伤。
设备也受到了严重的损坏。
三、事故原因分析1. 设备故障:设备故障是事故发生的直接原因。
根据现场调查,设备故障是由于操作员操作不当引起的。
2. 操作员失误:操作员在操作设备时,没有按照操作规程进行操作,导致设备发生故障。
3. 安全意识淡薄:车间内工作人员的安全意识淡薄,没有及时发现设备故障,也没有采取相应的安全措施。
四、事故改进措施1. 加强设备维护:定期对设备进行维护,确保设备正常运行。
2. 提高操作员技能:对操作员进行培训,提高其操作技能,确保其能够正确操作设备。
3. 加强安全意识教育:对车间内工作人员进行安全意识教育,提高他们的安全意识,确保他们能够及时发现设备故障,并采取相应的安全措施。
4. 完善应急预案:完善应急预案,确保在事故发生时能够迅速、有效地进行处理。
六、事故损失评估事故发生后,我们对损失进行了详细的评估。
设备方面,损坏的主要是生产线上的关键部件,预计维修费用约为人民币50万元。
人员方面,重伤员工已送至医院接受治疗,预计医疗费用约为人民币20万元。
事故还导致车间停产一周,预计直接经济损失约为人民币100万元。
七、事故责任认定根据事故调查结果,操作员因操作不当,未能遵守操作规程,对事故负有直接责任。
同时,车间负责人因未能有效监督操作员,未能及时发现和纠正操作员的错误行为,对事故负有管理责任。
八、事故处理与整改1. 对操作员进行严肃处理,给予相应的行政处罚,并要求其承担部分经济损失。
2. 对车间负责人进行诫勉谈话,要求其加强管理,提高安全意识。
事故分析总结范文

一、事故概述2023年3月15日,某工厂在生产过程中发生了一起安全事故,导致一名工人受伤。
事故发生后,厂部立即启动应急预案,将伤者送往医院救治,并对事故现场进行了初步勘查。
经初步调查,事故原因为操作人员违规操作,导致设备故障引发。
二、事故原因分析1. 人员因素(1)操作人员缺乏安全意识,未按照操作规程进行作业。
(2)操作人员对设备性能了解不足,未能及时发现设备隐患。
(3)操作人员培训不到位,未能掌握必要的安全知识和技能。
2. 设备因素(1)设备存在设计缺陷,未能满足安全生产要求。
(2)设备维护保养不及时,导致设备故障。
(3)设备操作界面不符合人性化设计,增加了操作难度。
3. 管理因素(1)安全生产责任制不明确,导致责任追究不到位。
(2)安全管理制度不完善,未能覆盖所有生产环节。
(3)安全教育培训工作流于形式,未能提高员工安全意识。
三、事故处理及整改措施1. 事故处理(1)对受伤工人进行救治,确保其生命安全。
(2)对事故现场进行清理,恢复生产秩序。
(3)对事故原因进行调查,查明责任。
2. 整改措施(1)加强安全教育培训,提高员工安全意识。
(2)完善安全管理制度,确保安全生产。
(3)加强设备维护保养,消除安全隐患。
(4)对违规操作人员进行严肃处理,追究相关责任。
(5)开展安全大检查,全面排查安全隐患。
四、总结本次事故的发生,给我们敲响了安全生产的警钟。
我们必须深刻反思,认真总结教训,采取切实有效的措施,防止类似事故再次发生。
以下是本次事故的几点启示:1. 安全生产是企业发展的生命线,必须始终把安全生产放在首位。
2. 加强安全教育培训,提高员工安全意识,是预防事故的重要手段。
3. 完善安全管理制度,落实安全生产责任制,是确保安全生产的关键。
4. 加强设备维护保养,消除安全隐患,是预防事故的根本措施。
让我们以此次事故为鉴,共同努力,确保企业安全生产形势持续稳定。
事故的原点
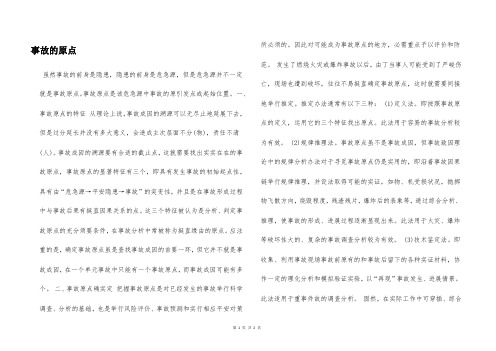
事故的原点虽然事故的前身是隐患,隐患的前身是危急源,但是危急源并不一定就是事故原点。
事故原点是该危急源中事故的原引发点或起始位置。
一、事故原点的特征从理论上说,事故成因的溯源可以无尽止地延展下去,但是过分延长并没有多大意义,会造成主次层面不分(物),责任不清(人)。
事故成因的溯源要有合适的截止点,这就需要找出实实在在的事故原点,事故原点的显著特征有三个,即具有发生事故的初始起点性,具有由“危急源→平安隐患→事故”的突变性,并且是在事故形成过程中与事故后果有挺直因果关系的点。
这三个特征被认为是分析、判定事故原点的充分须要条件,在事故分析中常被称为挺直缘由的原点。
应注重的是,确定事故原点虽是查找事故成因的首要一环,但它并不就是事故成因,在一个单元事故中只能有一个事故原点,而事故成因可能有多个。
二、事故原点确实定把握事故原点是对已经发生的事故举行科学调查、分析的基础,也是举行风险评价、事故预测和实行相应平安对策所必须的。
因此对可能成为事故原点的地方,必需重点予以评价和防范。
发生了燃烧火灾或爆炸事故以后,由丁当事人可能受到了严峻伤亡,现场也遭到破坏,往往不易挺直确定事故原点,这时就需要间接地举行推定。
推定办法通常有以下三种: (1)定义法。
即按照事故原点的定义,运用它的三个特征找出原点。
此法用于容易的事故分析较为有效。
(2)规律推理法。
事故原点虽不是事故成因,但事故致因理论中的规律分析办法对于寻觅事故原点仍是实用的,即沿着事故因果链举行规律推理,并设法取得可能的实证,如物、机受损状况,抛掷物飞散方向,烧毁程度,残渣残片,爆炸后的表象等,通过综合分析、推理,使事故的形成、进展过程逐渐显现出来。
此法用于火灾、爆炸等破坏性大的、复杂的事故调查分析较为有效。
(3)技术鉴定法。
即收集、利用事故现场事故前原有的和事故后留下的各种实证材料,协作一定的理化分析和模拟验证实验,以“再现”事故发生、进展情景。
此法适用于重事件故的调查分析。
事故原点分析技术

事故原点分析技术事故原点理论是事故调查工作的基础理论之一,这一理论自20世纪80年以后得到了广泛的应用。
一、事故原点的概念及事故原点的确定方法(一) 事故原点的概念事故原点就是事故隐患转化为事故的具有初始性突变特征并与事故发展过程有直接因果联系的点。
这个点是具有时空意义的广义点。
事故原点是构成事故的最初起点。
如火灾事故的第一起火点,爆炸事故的第一起煤点等。
事故原点具有时间和空间的双重概念。
对某一单元事故,它表示某一时间或空间的某一点。
事故原点具有如下特征:(1) 事故原点是从事故隐患转化为事故的具有突变特征的点,没有突变特征的点不是事故原点。
(2) 事故原点是从事故隐患转化为事故的具有初始性的点,只有突变特征没有初始性的点也不是事故原点。
(3) 事故原点是在事故发展过程中与事故后果有直接因果联系的点,只有突变特征和初始性而与事故后果无直接因果联系的点不是事故原点。
在任何单元事故中,事故原点只能有一个。
事故原点不是事故原因,也不是事故的终点,它们之间有严格的区别,这一点必须注意。
事故原点理论为调查事故提供了科学方法。
在事故调查工作中,必须首先查清和验证事故原点的位置,然后才能对事故调查过程中的各个环节进行定性定量分析。
在比较简单的单元事故中,如冲床伤手事故,发生事故的人机接触部位,即是事故的起点(事故原点),也是事故的终点。
对比较复杂的大事故,应首先查到事故原点,调查工作才能按程序深入下去。
如果在未确定事故原点之前,就对事故原因作了结论,则该结论必然是失误的,所采取的措施必然无针对性。
因此,确定事故点在事故调查过程中是个关键问题。
(二) 事故原点的确定方法事故原点的确定方法有三种:定义法、逻辑推理法、技术鉴定法。
(1)定义法定义法就是用事故原点的定义,查证落实事故的最初起点。
此法适用于事故发生、发展过程比较明显,凭直观可基本确定事故原点和事故原因的事故。
如机具伤害事故等。
(2)逻辑推理法逻辑推理法是用发生事故的生产过程的工艺条件,结合事故的发生、发展过程的因果链进行逻辑推理。
事故根源分析方法-Root Cause Analysis (RCA)

International Isocyanate Institute
•事故根源分析方法(RCA)的定义:
•是研究产生事故各相关因子的一种系统的方法, 调查跟踪事 故和事故原因之间的因果关系,直到找到问题的根本原因。
设计、规划
设备 & 维修、维护
过程计划 & 材料
生产操作 & 质量保证
International Isocyanate Institute
是叉车漏的油 叉车没有及时保养维修 没有计划安排好预防维护工作 没有足够的技工来实施 工厂预算不足
结果-问:"为什么"至少五次可阻止错误诱因的出现并能找到根本原 因。停止本例中的根本因素缺乏现象很可能将导致清除漏油或修复特定的 升降叉车。未来重复发生事故的机率(或意外事件)仍然存在。
International Isocyanate Institute
International Isocyanate Institute
五个“为什么”Æ“鱼刺图法” 案件讨论:
发起滑倒和摔倒的调查。一个人在有一层油覆盖的地板上滑倒,那 么这直接/最近的致因就被认定是地板表面上存在的油。
提问 回答
为什么地板上有油? 为什么会这样? 为什么会这样? 为什么会这样? 为什么会这样?
那里为什么 会有一个原子?
International Isocyanate Institute
为什么不能生产出合格的零件?
原料材质不合格 不合格零件 设计不合理 不合适的生产工具 工艺过程出错 • 除了你个人所能知道的原因之外,要把所有有可能的影响条件、因素 都尽量考虑进去,在这个阶段“头脑风暴”是一个很有用的方法。 •“头脑风暴”(Brain Storming - BS): 9一种通过集思广益、发挥团体智慧,从各种不同角度找出问题所有 原因或构成要素的会议方法。 9BS几大原则:严禁批评、思维自由奔放、结果多多益善。
事故原因分析控制措施范本

整体解决方案系列事故原因分析控制措施(标准、完整、实用、可修改)编号:FS-QG-81861事故原因分析控制措施Accident cause analysis and control measures说明:为明确各负责人职责,充分调用工作积极性,使人员队伍与目标管理科学化、制度化、规范化,特此制定从传统的经验管理过渡到科学安全管理,需要对事故原因进行科学的分析和控制。
事故致因理论证明,造成事故的直接原因不外乎人的不安全行为和物的不安全状态两种因素。
在现代社会生产生活中,物的不安全因素具有一定的稳定性,而人则由于其自身及社会的影响,具有相当大的随意性和偶然性,是激发事故发生的主要因素。
有资料表明:有70%~80%的事故是由于人为失误造成的。
人为失误是事故发生的首要原因,研究人为失误规律,对控制事故发生具有重要意义。
一、基本行为模式行为科学在安全管理中的应用,推动了安全科学的发展。
行为科学是专门研究人的行为规律,以便实现预测和控制人的一门科学。
行为科学认为,人在生产生活及生存的过程中,遵循着“人的原理”而行动。
人的原理包括生物学、心理学、文化学及社会学等许多原理。
人的行为模式可表示为(刺激)→(人体)→(反应),这是一个不断循环的过程。
人是管理中的决定因素,而且人是非常复杂的,会对各种刺激作出反应,而这种反应必然对他从事的工作和生活乃至生存活动产生影响。
当人的内在因素与外部环境相“匹配”时,表现为“正确”,当人的内在因素的某些要素与外部环境的某些要素发生冲突时,其行为表现为“失误”。
行为科学另一主要理论是人的需要层次论。
在人的需要中,安全需要是最基本的需要,安全需要产生安全动机,进而实现安全目标。
然而,安全生产作为安全综合需要的一个原因子,常常并未得到足够的重视,相反在受到各种刺激时作出错误反应。
人的安全表现模型可用下图表示。
是否能坚持安全目标,实现安全目的,问题的根本在于受到“挫折”后的反应。
二、人为失误系统分析人为失误,或通常称之为人的不安全行为,就是指不符合安全规程,有可能导致伤亡事故和财产损失的行为。
关于12.10事故分析

关于12.10事故分析第一篇:关于12.10事故分析“12.10事故”后自查及整改措施集团公司质安部:12月19日上午9点半,集团公司组织召开“12.10”事故调查分析视频会议,会后我公司立即组织输配部、质安部、客户部、行政部、财务部、技术工程部、监理等有关人员,针对“12.10”事故”召开安全生产会议由总经助理王志平主持。
事故是沉痛的,教训是深刻,事故给集团公司带来严重的后果,我公司高度重视,在“12.10”事故调查分析视频会议召开之前我公司12月11日组织班了组长以上人员围绕“12.10”事故展开会议,随后又在12月13日组织各部门负责人、监理、施工单位、安全管理人员分析讨论“12.10”事故,会后专门签发了会议纪要,使每名员工吸取此次的深刻教训。
我公司严格按照集团质安部要求,结合公司实际情况认真仔细查找自身存在的管理漏洞,提出整改意见和措施,把今后公司的安全生产工作做细,做扎实,杜绝安全事故的发生。
会上由总经理助理兼质安部部长王志平主持,王志平要求参会人员深刻认识此次会议的重要性,认真分析总结事故原因,从中吸取教训。
总工程师谢伟介绍了“12.10事故调查分析会”的会议内容,叙述了“12.10事故” 发生的全过程,各部门负责人对此次安全事故发表了意见,同时也找出存在的问题加以分析讨论。
对过去两年多来公司的安全工作进行梳理,对存在问题加以整改。
1、我公司原来在带气作业时,操作人员不佩戴防护用具(安全帽)时有发生,今后不论是在施工工地、抢险带气作业现场、户内改管、高空作业等工作中,都必须佩戴防护用具,发现有违规操作行为立即制止责令改正并按公司相关制度进行处理。
2、以往在带气作业,准备工作不是很充分,带气方案评审往往是即将要开始作业才进行,没有足够时间对现场进行分析了解情况。
要吸取此次事故教训,在带气作业前,要充分了解情况后,严格按照逐级审批程序,提前计划提前评审绝不能盲目操作,凭经验做事。
3、部门与部门之间的交接不是很清楚,以后要加强各部门的沟通与合作。
事故分析报告 (2)

事故分析报告概述本报告旨在对最近发生的事故进行分析,以便了解事故原因,并提供预防措施和改进建议,以确保类似事故不再发生。
事故背景时间和地点事故发生于2021年5月10日,地点为ABC公司的生产车间。
事故描述在当天早上9点左右,一台新购买的机械设备发生了故障,导致车间生产线停工。
故障发生时,机械设备正在进行高速运转,由于故障无法及时停机,造成了设备的严重损坏。
事故影响•生产线停工导致产量下降•设备维修所需费用和时间增加•工人的安全受到威胁事故分析根本原因经过对事故的详细分析,我们发现以下根本原因:1.设备维护不及时:机械设备在出现故障前并没有得到适当的维护,导致故障的发生和进一步损坏。
2.操作员技能不足:操作员对机械设备的操作和维护知识有限,无法及时发现设备故障和维修需求,延误了处理故障的时机。
过程问题事故的发生也与以下过程问题相关:1.维护计划缺失:公司没有制定完善的设备维护计划,导致设备维护工作无法按时进行。
2.培训不足:公司对新购买的机械设备进行操作员培训时,培训内容不够全面,操作员对设备的理解和应对故障的能力有限。
改进措施根据事故分析结果,我们提出了以下改进措施,旨在防止类似事故再次发生。
设备维护1.制定设备维护计划:公司应该制定完善的设备维护计划,并明确各项维护任务的负责人和时间节点。
2.定期检查和保养:设备维护工作应定期进行,包括清洁、润滑、紧固、调整等,以确保设备处于良好工作状态。
3.故障检测和预防:针对常见故障点,制定故障检测方案,并定期进行检测,及时解决潜在问题。
培训与质量控制1.操作员培训:公司应为操作员提供全面的机械设备操作和维护培训,提高操作员的技能水平,使其能够更好地预防和处理故障。
2.质量控制:建立全面的质量控制体系,确保设备符合规范要求,并及时发现和纠正存在的问题。
组织管理1.建立事故报告和学习机制:公司应建立事故报告和学习机制,每次事故发生后进行及时归档和总结,以便进一步改进管理措施。
事故原点理论

事故原点理论事故原点理论一、事故原因分析事故原因分析是理解事故发生原因的重要步骤,对于预防类似事故的再次发生具有至关重要的作用。
事故原因可能源于多个方面,包括设备故障、操作失误、环境影响、管理不当等。
在分析事故原因时,需要详细了解事故发生的经过和现场情况,收集相关数据和信息,并进行分类、整理和分析。
通过对这些信息的综合分析,可以确定事故的主要原因。
二、事故原点确定事故原点是指事故发生的起始点,是事故原点理论的核心概念。
确定事故原点有助于我们更好地理解事故发生的经过和原因,为制定预防措施提供依据。
在确定事故原点时,需要对事故发生的各个阶段进行深入分析,找出导致事故发生的初始原因,并明确事故原点与各阶段之间的关系。
三、事故预防措施根据事故原因分析和事故原点的确定,可以制定相应的预防措施。
预防措施应该针对事故原因进行制定,例如加强设备维护、完善操作规程、改善工作环境、提高管理水平等。
同时,预防措施的制定还需要考虑实际可行性和长期效益,以确保预防措施的有效性和可持续性。
四、事故报告与处理事故发生后,及时报告和处理事故是十分重要的。
事故报告应该详细记录事故发生的经过、原因和后果,为分析事故提供依据。
同时,事故处理也需要及时采取有效措施,以减少事故的影响和损失。
在处理事故时,需要对事故责任进行明确划分,对责任人进行严肃处理,同时加强员工安全教育,提高员工安全意识。
五、事故分析与反思事故分析与反思是提高安全管理水平的重要环节。
通过对事故的深入分析和反思,可以发现安全管理中存在的问题和不足,并提出改进措施。
在分析事故时,需要从多个角度进行思考和研究,找出事故发生的深层次原因,并制定相应的预防措施。
同时,还需要对事故处理过程进行反思和总结,以提高应急响应能力。
总之,事故原点理论是一种有效的安全管理方法论,它通过对事故原因、事故原点、预防措施、事故报告与处理以及事故分析与反思等方面的综合分析和管理,旨在减少和避免类似事故的再次发生。
事故情况分析及解决方案
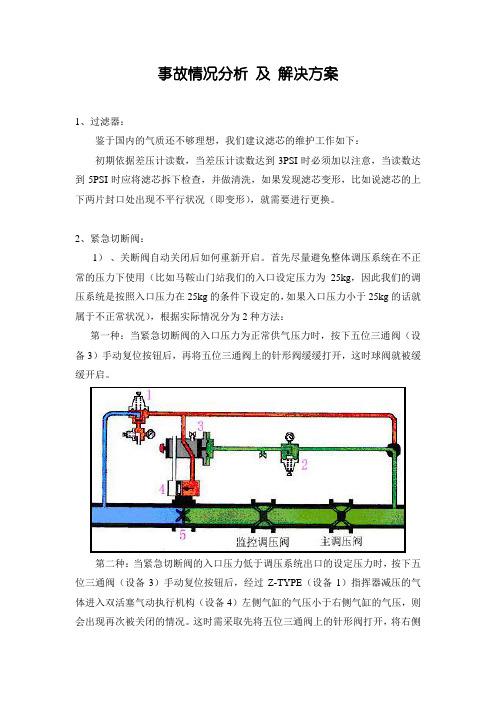
事故情况分析及解决方案1、过滤器:鉴于国内的气质还不够理想,我们建议滤芯的维护工作如下:初期依据差压计读数,当差压计读数达到3PSI时必须加以注意,当读数达到5PSI时应将滤芯拆下检查,并做清洗,如果发现滤芯变形,比如说滤芯的上下两片封口处出现不平行状况(即变形),就需要进行更换。
2、紧急切断阀:1)、关断阀自动关闭后如何重新开启。
首先尽量避免整体调压系统在不正常的压力下使用(比如马鞍山门站我们的入口设定压力为25kg,因此我们的调压系统是按照入口压力在25kg的条件下设定的,如果入口压力小于25kg的话就属于不正常状况),根据实际情况分为2种方法:第一种:当紧急切断阀的入口压力为正常供气压力时,按下五位三通阀(设备3)手动复位按钮后,再将五位三通阀上的针形阀缓缓打开,这时球阀就被缓缓开启。
第二种:当紧急切断阀的入口压力低于调压系统出口的设定压力时,按下五位三通阀(设备3)手动复位按钮后,经过Z-TYPE(设备1)指挥器减压的气体进入双活塞气动执行机构(设备4)左侧气缸的气压小于右侧气缸的气压,则会出现再次被关闭的情况。
这时需采取先将五位三通阀上的针形阀打开,将右侧气缸中的压力释放,然后再按下复位按钮,才能保证紧急切断阀的复位成功。
但是这样操作将导致球阀打开太快,会造成下游流量计及仪表设备的损坏。
2)控制箱内的放散阀一直排气:1、Z-TYPE内部流孔被磨损或被卡堵,导致该放散阀持续排气,则需要拆修Z-TYPE指挥器。
2|zsc 320 150坏掉。
3\选线指挥器未开启,温度过高,放散。
3、调压阀:1)由于供气不正常,可能产生工作调压阀和监控调压阀之间压力表度数超过监控调压阀上游压力(对备用路而言)。
2)套环变形,渣滓和腐蚀性气体,导致调压阀出口压力高于设定值。
3)歧管堵上,下游仍然在用气,控制压降低,造成轴流阀全开,下游压力升高。
4、流量计:1)当出现气体仍在流动,但流量计读数误差较大的情况时,可能的原因分析如下:1)首先确定供气是否正常,如果不正常,当流量小于最小流量,压力小于正常工作压力,流量计可能出现停转现象,造成读数误差很大。
- 1、下载文档前请自行甄别文档内容的完整性,平台不提供额外的编辑、内容补充、找答案等附加服务。
- 2、"仅部分预览"的文档,不可在线预览部分如存在完整性等问题,可反馈申请退款(可完整预览的文档不适用该条件!)。
- 3、如文档侵犯您的权益,请联系客服反馈,我们会尽快为您处理(人工客服工作时间:9:00-18:30)。
事故原点分析技术
事故原点理论是事故调查工作的基础理论之一,这一理论自20世纪80年以后得到了广泛的应用。
一、事故原点的概念及事故原点的确定方法
(一) 事故原点的概念
事故原点就是事故隐患转化为事故的具有初始性突变特征并与事故发展过程有直接因果联系的点。
这个点是具有时空意义的广义点。
事故原点是构成事故的最初起点。
如火灾事故的第一起火点,爆炸事故的第一起煤点等。
事故原点具有时间和空间的双重概念。
对某一单元事故,它表示某一时间或空间的某一点。
事故原点具有如下特征:(1) 事故原点是从事故隐患转化为事故的具有突变特征的点,没有突变特征的点不是事故原点。
(2) 事故原点是从事故隐患转化为事故的具有初始性的点,只有突变特征没有初始性的点也不是事故原点。
(3) 事故原点是在事故发展过程中与事故后果有直接因果联系的点,只有突变特征和初始性而与事故后果无直接因果联系的点不是事故原点。
在任何单元事故中,事故原点只能有一个。
事故原点不是事故原因,也不是事故的终点,它们之间有严格的区别,这一点必须注意。
事故原点理论为调查事故提供了科学方法。
在事故调查工作中,必须首先查清和验证事故原点的位置,然后才能对事故调查过程中的各个
环节进行定性定量分析。
在比较简单的单元事故中,如冲床伤手事故,发生事故的人机接触部位,即是事故的起点(事故原点),也是事故的终点。
对比较复杂的大事故,应首先查到事故原点,调查工作才能按程序深入下去。
如果在未确定事故原点之前,就对事故原因作了结论,则该结论必然是失误的,所采取的措施必然无针对性。
因此,确定事故点在事故调查过程中是个关键问题。
(二) 事故原点的确定方法
事故原点的确定方法有三种:定义法、逻辑推理法、技术鉴定法。
(1)定义法
定义法就是用事故原点的定义,查证落实事故的最初起点。
此法适用于事故发生、发展过程比较明显,凭直观可基本确定事故原点和事故原因的事故。
如机具伤害事故等。
(2)逻辑推理法
逻辑推理法是用发生事故的生产过程的工艺条件,结合事故的发生、发展过程的因果链进行逻辑推理。
因为事故的原因与结果在时间上是先后相继的,后一个结果的原因,就是前一个原因的结果,依次推导至终点,便找出事故的原点。
这个方法适用于事故过程不明显而破坏性又比较复杂的事故,如较大的爆炸事故。
(3)技术鉴定法
技术鉴定法是利用事故现场的大量物证进行综合分析,使事故的发生、发展过程逐步复原,进而将事故原点从中揭露出来。
这个方法适用于
极其复杂,而且造成重大损失的事故,如重大爆炸火灾事故。
根据实际工作经验,技术鉴定要查被爆物承受面的痕迹、爆炸散落物的状态和层次、抛射物体方位和状态、人机损伤部位及现场遗留物等五个方面。
还要和爆炸物理学、化学工艺学、物质燃烧理论、结构力学等相结合。
事故原点确定过程举例(应用逻辑推理法)
图3-13 爆炸现场示意示意图
1.爆炸点
2.玻璃碎片
3.装药机
4.药盒
5.传递窗
6.防爆灯
7.提盒
8.贮存器
9.木桌。