事故伤害的主要原因.docx
一例手指压伤事故的警示docx
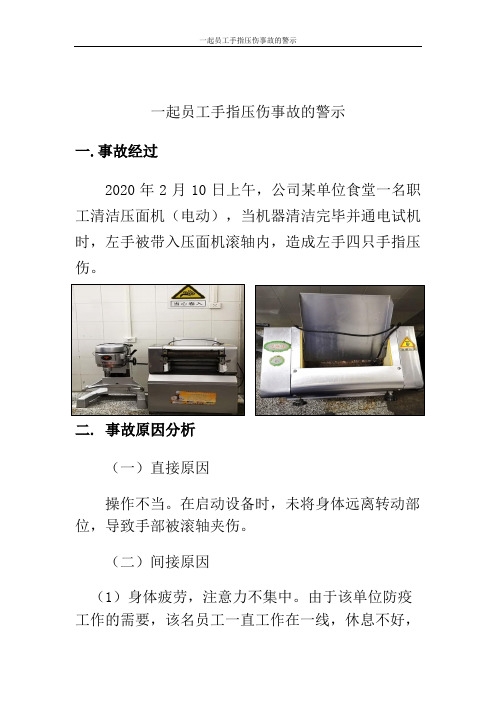
ห้องสมุดไป่ตู้三.事故警示
1、加强转动设备的安全管理,在维护保养时,电源断开并上锁加标签,使用工具进行相关操作,防止手部伤害。
2、加强手部伤害防护培训,培养员工的手部防护意识。
3、现场张贴安全操作规程及警示标语并严格执行。
4、开展安全行为观察与沟通,减少不安全行为,做到“四不伤害”。
5、加强“五想五不干”的宣传力度,进一步提高员工安全意识。
6、合理控制员工劳动强度、科学安排作息时间,避免疲劳作业。
北海天然气股份有限公司
2020年2月17日
一起员工手指压伤事故的警示
一.事故经过
2020年2月10日上午,公司某单位食堂一名职工清洁压面机(电动),当机器清洁完毕并通电试机时,左手被带入压面机滚轴内,造成左手四只手指压伤。
二.事故原因分析
(一)直接原因
操作不当。在启动设备时,未将身体远离转动部位,导致手部被滚轴夹伤。
(二)间接原因
(1)身体疲劳,注意力不集中。由于该单位防疫工作的需要,该名员工一直工作在一线,休息不好,存在一定程度的疲劳状态,造成其注意力不够集中。
造成生产安全事故的原因
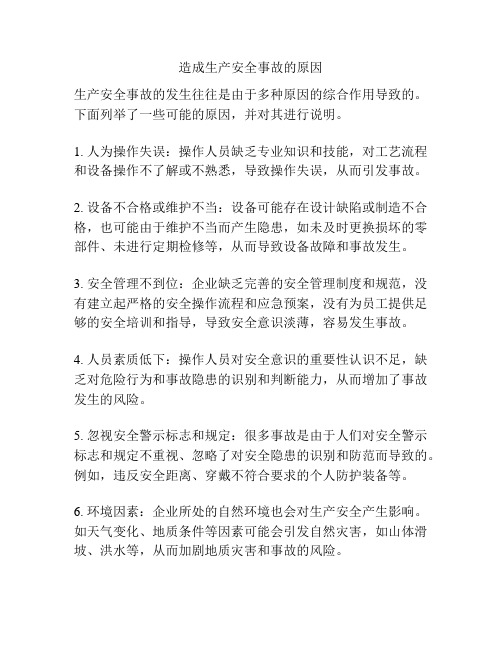
造成生产安全事故的原因生产安全事故的发生往往是由于多种原因的综合作用导致的。
下面列举了一些可能的原因,并对其进行说明。
1. 人为操作失误:操作人员缺乏专业知识和技能,对工艺流程和设备操作不了解或不熟悉,导致操作失误,从而引发事故。
2. 设备不合格或维护不当:设备可能存在设计缺陷或制造不合格,也可能由于维护不当而产生隐患,如未及时更换损坏的零部件、未进行定期检修等,从而导致设备故障和事故发生。
3. 安全管理不到位:企业缺乏完善的安全管理制度和规范,没有建立起严格的安全操作流程和应急预案,没有为员工提供足够的安全培训和指导,导致安全意识淡薄,容易发生事故。
4. 人员素质低下:操作人员对安全意识的重要性认识不足,缺乏对危险行为和事故隐患的识别和判断能力,从而增加了事故发生的风险。
5. 忽视安全警示标志和规定:很多事故是由于人们对安全警示标志和规定不重视、忽略了对安全隐患的识别和防范而导致的。
例如,违反安全距离、穿戴不符合要求的个人防护装备等。
6. 环境因素:企业所处的自然环境也会对生产安全产生影响。
如天气变化、地质条件等因素可能会引发自然灾害,如山体滑坡、洪水等,从而加剧地质灾害和事故的风险。
7. 人为犯罪或恶意行为:有些生产安全事故是由于恶意破坏、盗窃、放火、蓄意泄漏危险物质等恶意行为引起的。
综上所述,生产安全事故的原因是多种多样的,包括人为因素、设备问题、管理不到位、环境因素等等。
为了有效预防和减少生产安全事故的发生,企业需要加强安全管理,建立健全的安全生产制度和应急预案;加强员工的安全教育培训,提高员工的安全意识和操作技能;定期检修和维护设备,确保其正常运行;加强对环境和自然灾害的监测和预警;加强安全监管,打击恶意犯罪行为。
只有综合施策,才能有效降低生产安全事故的风险。
一起机械伤害事故案例调查报告.docx

8月4日19:40分左右,机修厂检一车间在返修合成车间119-C 时,造成管工孙贵生(男38岁);头部受伤,住院救治;管工廖启伦(男49岁),氨中毒住院治疗;现场检修5名工人吸入微量氨住院观察。
1、事故经过:8月3日晚,大检修后,合成装置开车冷冻系统引氨过程中,发现119-C管侧导淋有液氨排出,分析确定是119-C内部换热管泄漏。
我厂于8月4日上午在合成车间一楼会议室组织化肥厂和机修厂相关人员参加的119-C检修专业会上,讨论了合成装置119-C检修的一些相关事宜,会后出了会议纪要,并制定了119- C检修方案,提出要求并写出会议纪要。
8月4日上午,合成车间对管、壳两侧系统进行排氨处理。
15:30分管程管箱内通入氮气进行置换,且有三个排放点进行排放。
当天下午13:10分,机修厂检一车间检修工人在119-C壳侧的入口和出口分别加了三块盲板,大约17:10分加完,然后,合成车间给119-C壳侧充满水,并进行排放,共充水排放二次,然后边充水边排放。
约17:35分,化验车间对119 -C管程进行测爆分析,含氨4.68%不合格;约18:35分化验车间对119 -C管程进行第二次测爆分析合格(控制指标小于1%),工艺侧氮气置换合格后保持微正压。
然后合成车间开动火票,同时现场配有二套长管呼吸面具,一台干粉灭火器,看火员蒋春军和机动处副处长刘延海始终在检修现场。
19:10分,机修厂电焊工赵明伦开始用气刨割密封板,将直径为510mm,厚5mm的密封板割开,但有断断续续的连接处,这时管工孙贵生和管工廖启伦取来大锤和撬棒,气焊工刘荣用16磅的大锤敲击密封板西侧一下,霎时,119-C密封板弹出,打在距离密封板1.2米(估计值)远处的孙贵生头部的右侧,同时余氨泄出在场其他8名人员吸入少量氨气。
我厂人员立即找来救护车把伤者送往医院进行抢救,孙贵生21:00点进手术室,23:30分手术结束;机修厂6名工人住院观察。
2、事故原因此次119-c作业是机修厂返修作业,由于事前引入了大量的氨,加之系统流程长、设备多,虽经水洗和N2置换,但系统还是残余1%的氨。
安全生产事故发生原因
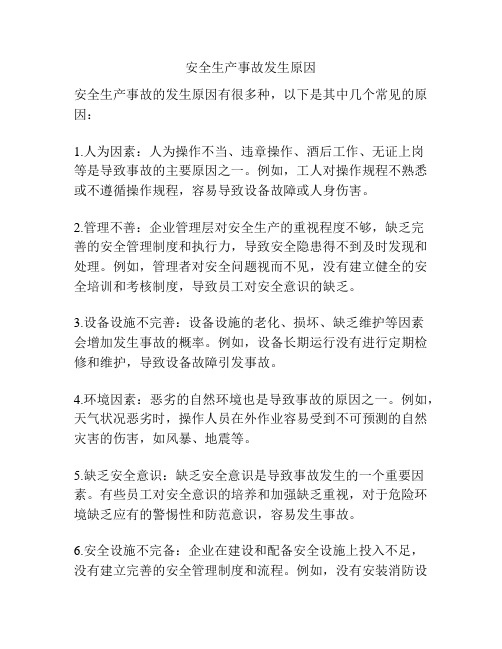
安全生产事故发生原因
安全生产事故的发生原因有很多种,以下是其中几个常见的原因:
1.人为因素:人为操作不当、违章操作、酒后工作、无证上岗
等是导致事故的主要原因之一。
例如,工人对操作规程不熟悉或不遵循操作规程,容易导致设备故障或人身伤害。
2.管理不善:企业管理层对安全生产的重视程度不够,缺乏完
善的安全管理制度和执行力,导致安全隐患得不到及时发现和处理。
例如,管理者对安全问题视而不见,没有建立健全的安全培训和考核制度,导致员工对安全意识的缺乏。
3.设备设施不完善:设备设施的老化、损坏、缺乏维护等因素
会增加发生事故的概率。
例如,设备长期运行没有进行定期检修和维护,导致设备故障引发事故。
4.环境因素:恶劣的自然环境也是导致事故的原因之一。
例如,天气状况恶劣时,操作人员在外作业容易受到不可预测的自然灾害的伤害,如风暴、地震等。
5.缺乏安全意识:缺乏安全意识是导致事故发生的一个重要因素。
有些员工对安全意识的培养和加强缺乏重视,对于危险环境缺乏应有的警惕性和防范意识,容易发生事故。
6.安全设施不完备:企业在建设和配备安全设施上投入不足,
没有建立完善的安全管理制度和流程。
例如,没有安装消防设
施、遮挡警示标志、缺乏安全通道等导致事故的发生。
综上所述,安全生产事故的发生原因是多方面的,需要企业和职工共同努力,加强安全管理和规范操作,提高安全意识,完善安全设施和设备维护,减少事故的发生。
安全生产事故致伤原因分类
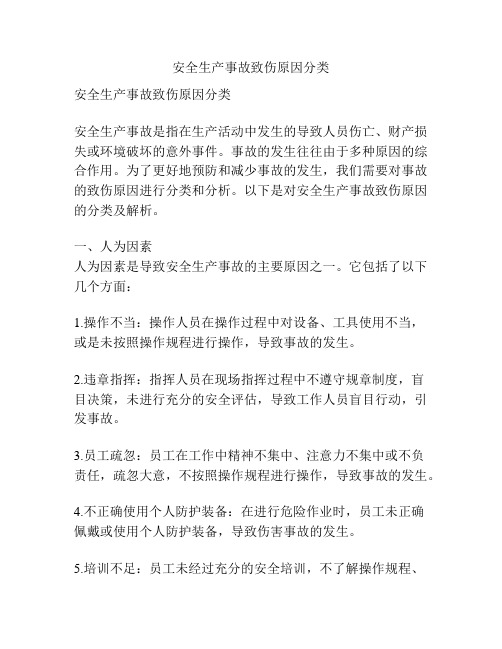
安全生产事故致伤原因分类安全生产事故致伤原因分类安全生产事故是指在生产活动中发生的导致人员伤亡、财产损失或环境破坏的意外事件。
事故的发生往往由于多种原因的综合作用。
为了更好地预防和减少事故的发生,我们需要对事故的致伤原因进行分类和分析。
以下是对安全生产事故致伤原因的分类及解析。
一、人为因素人为因素是导致安全生产事故的主要原因之一。
它包括了以下几个方面:1.操作不当:操作人员在操作过程中对设备、工具使用不当,或是未按照操作规程进行操作,导致事故的发生。
2.违章指挥:指挥人员在现场指挥过程中不遵守规章制度,盲目决策,未进行充分的安全评估,导致工作人员盲目行动,引发事故。
3.员工疏忽:员工在工作中精神不集中、注意力不集中或不负责任,疏忽大意,不按照操作规程进行操作,导致事故的发生。
4.不正确使用个人防护装备:在进行危险作业时,员工未正确佩戴或使用个人防护装备,导致伤害事故的发生。
5.培训不足:员工未经过充分的安全培训,不了解操作规程、安全操作要点和风险控制措施,使用不当导致事故。
6.意外动作:员工因个人原因进行非正常行为,例如酗酒、吸毒等导致工作不稳定、失误,从而造成事故。
二、设备因素设备因素也是导致安全生产事故的重要原因之一。
它包括以下几个方面:1.设备老化:设备长时间使用,没有进行及时的检修和维护,导致设备的老化、损坏,从而引发事故。
2.设备故障:设备在运行过程中由于设计、制造等原因,出现故障或者失灵,从而导致事故。
3.缺乏安全保护设施:设备缺乏相应的安全保护设施或者设施失效,无法保护员工的安全,因而导致事故。
4.设备操作和维修不当:设备操作员在操作、维修设备的过程中,没有按照操作规程进行操作,或者没有接受系统的培训,导致事故的发生。
5.设备设计缺陷:设备在设计阶段存在缺陷或不合理之处,使得设备使用时存在隐患,增加了事故发生的风险。
三、管理因素管理因素也是导致安全生产事故的重要原因之一。
它包括以下几个方面:1.缺乏安全意识:管理层对安全生产的重要性认识不足,对员工的安全培训和管理不够重视,从而导致事故的发生。
造成生产安全事故的原因

造成生产安全事故的原因
《生产安全事故的原因》
造成生产安全事故的原因有很多,其中一些主要原因包括:
1. 不合理的生产安排:部分企业为了追求利润最大化,可能会加班加点地安排生产,导致工人疲劳过度,从而增加事故发生的可能性。
2. 设备故障:设备老化、维护不当或是缺乏定期检查也是造成事故的原因之一。
如果设备出现故障,可能会对生产过程造成严重的影响,甚至引发事故。
3. 人为因素:员工素质不高、技术培训不到位、操作不当等因素也会造成生产安全事故。
4. 管理不善:企业生产管理不善,工艺流程混乱、疏于维护设备等也会增加生产安全事故的风险。
5. 缺乏安全意识:员工缺乏安全意识,没有严格遵守相关安全操作规程、佩戴安全防护用具等也是造成事故的重要原因。
综合起来,造成生产安全事故的原因多种多样,需要企业全面加强管理,严格执行相关安全规定,提高员工整体素质,加强设备维护,从而减少生产事故的发生。
皮带机滚筒伤害事故案例调查报告.docx

2007年1月24日11时20分左右,安徽某化工集团公司煤焦车间l7皮带机岗位上发生一起皮带机机尾大辊筒伤害事故,造成操作工章某右臂肱骨骨折,右侧三根肋骨骨折。
一、事故经过1月24日11时20分左右,l7皮带机操作工章某在l7皮带运行时进行巡检,发现皮带上无煤,皮带机跑偏。
章某于是到机尾查看,看到正在运行的l7皮带机机尾大辊筒上粘有原煤,就用戴着手套的右手去清除大辊筒上的原煤。
手套、衣袖被卷入正在运行的大辊筒内,造成右臂肱骨骨折,身体右侧三根肋骨骨折。
二、事故原因1、章某安全意识淡薄,违反《煤焦车间技术操作规程》第四节“安全技术制度第10条,皮带运行时严禁清扫设备、地面;第11条,调整皮带时要注意安全,不得在转动辊筒上清理焦、煤等杂物,以免发生人身事故”的规定。
章某抱着侥幸心理,用戴着手套的手去刮辊筒上的原煤,严重违反了煤焦车间技术操作规程,是导致伤害事故的主要原因。
2、车间在安全管理和安全教育方面,虽然有要求、有检查、有教育、有考试,但考核的少,从某种程度上影响了职工的安全意识和对安全工作的重视程度。
3、部分设备防护设施不全,也是导致这一起事故的原因之一。
4、皮带超负荷运行,岗位分散,每条皮带只有1名操作工,处于无人监护情况下操作,一但发生安全事故处于无人救护状态,很容易导致恶性事故。
三、防范措施1、在全车间内利用调度会、白班早会、交接班会的各种会议,通报124事故经过,分析事故原因,在职工中广泛进行“提高安全意识,增强防护能力”的安全教育。
2、在职工中开展“一日一题”的安全教育活动,把安全教育制度化、经常化落到实处。
3、完善安全网络,分别在皮带机焦系统、2O1系统、德士古系统和629系统设安全负责人,确保安全工作能落实到每一个岗位、每一个人。
使安全隐患能得到及时消除,使违章行为能得到及时纠正。
4、对发现隐患、纠正违章的职工要给予奖励或鼓励,对消除重大隐患的职工要给予重奖,对违章职工要给予重罚。
宝地砖厂机械伤害事故调查报告.docx

2005年4月,疏勒县宝地砖厂发生一起机械伤害事故。
该厂制砖机一名女工,在下班前5分钟,为了早点完成任务,在机器未停止的情况下清扫机器台面的泥土,造成左手无名指第一指关节以上的手指切伤,造成轻伤事故。
分析:事故主要原因,是人的不安全行为,职工违章操作。
事故间接原因,机器设计缺陷,安全防护措施不到位;企业对职工的安全教育不到位,安全管理不到位。
责任划分:该职工应承担事故的直接责任。
企业现场管理人员应承担间接责任,即管理责任。
而且,企业应承担事故的赔偿责任。
一、事故经过:2007年1月11日,按照当班班前会安排,刘尊江负责看护焖渣3#、4#运送皮带工作,10时30分,刘发现4#皮带尾轮内有残渣掉入,便在没有停运皮带的情况下用铁锹欲将内部渣块清除,不慎被运转的皮带将其带入尾轮内,造成头部挤伤,当场死亡。
二、原因分析:1、刘尊江违反了我厂《安全技术规程》中皮带工安全规程2.3款“设备维护、检修、注油、处理故障、打扫卫生应停机进行,严禁在设备运转的情况下进行维护、清理障碍物等各项作业,防止意外事故发生”的规定,违章作业是这起事故发生的主要原因。
2、临时工工作时间安排不合理(每日7—19时和19时—次日7时,每半个月一轮换)造成工人身体疲劳程度增加,精力不易集中是本次事故发生的另一主要因素。
3、皮带尾轮防护罩间隙过大,致使防护性能降低,是造成这起事故发生的又一原因。
三、防范措施:1、强化各项规章制度的执行和落实,特别是要害岗位的操作知识和技能的培训,更要加强。
2、对厂内所有的防护装置,进行一次普查,发现问题逐项落实整改,未完全整改前要制定出切实有效的防范措施。
2009年8月5日下午15时20分左右,徐州振航钢结构工程有限公司岱山分公司在舟山市金海湾船业有限公司分段车间流水线工段作业过程中,发生一起机械伤害事故,造成1名工人死亡。
接到事故报告后,市安全监管局、市经贸委、市监察局、市公安局、市总工会等部门组成了事故联合调查组并邀请市检察院派员参加,对该起事故进行了调查,现将调查处理情况公示如下:一、事故基本情况:8月5日下午15时左右,岱山晨东船舶工程公司邱某班组的四名装配工在金海湾分段车间4F流水线J0005HS11P分段进行装配工作。
安全生产事故主要原因

安全生产事故主要原因
《安全生产事故主要原因》
安全生产事故是指在生产过程中发生的导致人身伤亡、财产损失的意外事件。
在工业化和现代化的社会中,安全生产事故已经成为一个严重的社会问题。
那么,究竟是什么原因导致了这些事故的发生呢?
首先,人为因素是导致安全生产事故的主要原因之一。
比如,员工的操作失误、违章指挥、违规操作等情况都容易导致事故的发生。
另外,管理人员的失职失责、对安全生产的重视不足、对安全规定的执行不力等也是人为因素造成事故的原因之一。
其次,技术设备是安全生产事故的另一个主要原因。
设备的老化、缺乏必要的维护保养、缺陷设备的使用等都是导致事故发生的重要原因。
此外,技术设备的设计不合理、生产工艺的不安全等也是造成安全生产事故的重要原因。
最后,环境因素也是导致安全生产事故的主要原因。
比如,天气、气候等自然因素的影响,以及工作环境的不安全因素都是造成事故的重要原因。
综上所述,安全生产事故的主要原因有人为因素、技术设备和环境因素等。
要想减少安全生产事故的发生,必须从源头上解决这些问题,加强员工的安全培训、加强对技术设备的维护和管理、改善工作环境等措施都是减少事故的重要途径。
只有消除这些原因,才能真正实现安全生产。
事故分析报告范文

事故分析报告范文事故分析报告。
报告编号,2022001。
报告日期,2022年3月15日。
报告人,XXX。
1. 事故概况。
2022年3月14日晚上8点左右,在XXX工厂生产车间发生了一起严重的机械事故。
事故发生时,工人正在对一台旧设备进行维修,突然设备发生故障,导致工人受伤,设备受损。
事故现场迅速得到控制,伤者已经得到及时救治,情况稳定。
2. 事故原因分析。
经初步调查,事故原因主要有以下几点:(1)设备老化,事故设备已经使用了10年以上,设备老化严重,部分零部件已经出现磨损和腐蚀,导致设备运行不稳定。
(2)维修不当,在进行维修时,工人未按照操作规程进行操作,存在操作失误的可能性。
同时,工人对设备的维修知识和技能不够熟练,导致维修过程中出现了失误。
(3)管理不善,工厂对设备的定期检修和维护管理不到位,设备运行状态未能得到及时监控和维护,导致设备故障发生时未能及时发现和处理。
3. 事故影响分析。
此次事故造成了严重的人员伤害和设备损坏,给工厂生产带来了重大影响。
首先,工人的伤亡给家庭带来了不可挽回的损失,对工厂的员工士气和生产秩序也造成了严重的影响。
其次,设备的损坏导致了生产线的停工,给工厂的生产计划和订单交付带来了严重的延误,给企业的经济效益造成了巨大损失。
4. 事故处理措施。
针对此次事故,我们将采取以下几项措施进行处理:(1)立即对事故设备进行全面检修和维护,确保设备的安全运行。
(2)对工人进行全面的安全培训和技能培训,提高工人的安全意识和操作技能。
(3)加强对设备的定期检修和维护管理,建立健全的设备管理制度,确保设备的安全运行。
(4)对事故的原因进行深入分析和总结,制定相关的预防措施,避免类似事故再次发生。
5. 结论。
此次事故给工厂的生产和员工的安全带来了严重影响,我们将从事故中吸取教训,加强对设备的管理和维护,提高员工的安全意识和技能,确保工厂的安全生产和稳定运行。
同时,我们也将对事故的原因进行深入分析和总结,制定相关的预防措施,避免类似事故再次发生。
安全生产事故主要原因
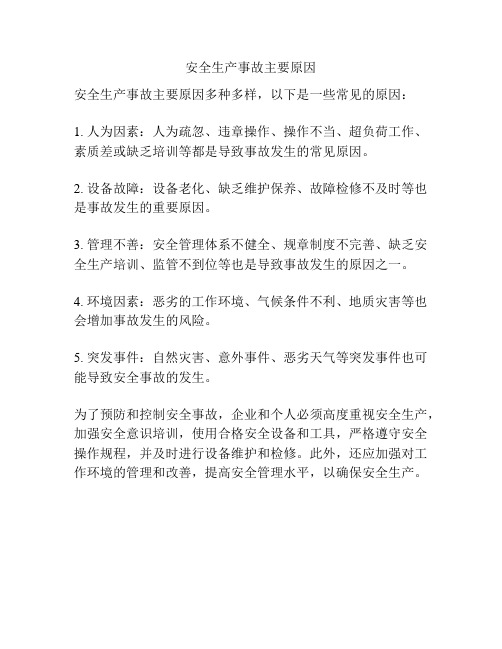
安全生产事故主要原因
安全生产事故主要原因多种多样,以下是一些常见的原因:
1. 人为因素:人为疏忽、违章操作、操作不当、超负荷工作、素质差或缺乏培训等都是导致事故发生的常见原因。
2. 设备故障:设备老化、缺乏维护保养、故障检修不及时等也是事故发生的重要原因。
3. 管理不善:安全管理体系不健全、规章制度不完善、缺乏安全生产培训、监管不到位等也是导致事故发生的原因之一。
4. 环境因素:恶劣的工作环境、气候条件不利、地质灾害等也会增加事故发生的风险。
5. 突发事件:自然灾害、意外事件、恶劣天气等突发事件也可能导致安全事故的发生。
为了预防和控制安全事故,企业和个人必须高度重视安全生产,加强安全意识培训,使用合格安全设备和工具,严格遵守安全操作规程,并及时进行设备维护和检修。
此外,还应加强对工作环境的管理和改善,提高安全管理水平,以确保安全生产。
发生安全事故的主要原因
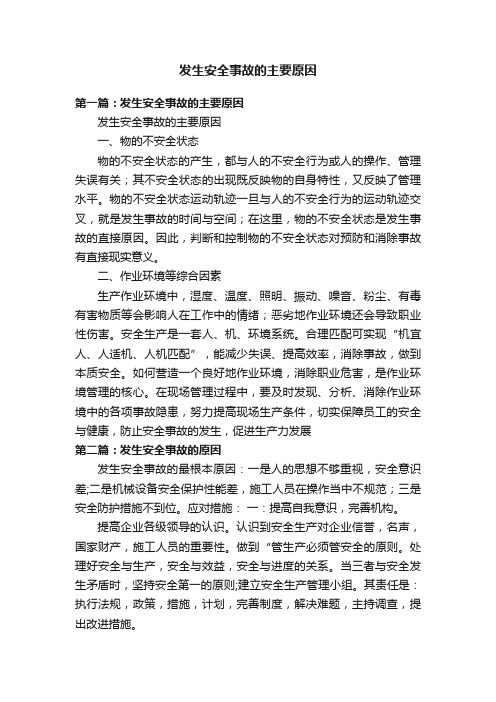
发生安全事故的主要原因第一篇:发生安全事故的主要原因发生安全事故的主要原因一、物的不安全状态物的不安全状态的产生,都与人的不安全行为或人的操作、管理失误有关;其不安全状态的出现既反映物的自身特性,又反映了管理水平。
物的不安全状态运动轨迹一旦与人的不安全行为的运动轨迹交叉,就是发生事故的时间与空间;在这里,物的不安全状态是发生事故的直接原因。
因此,判断和控制物的不安全状态对预防和消除事故有直接现实意义。
二、作业环境等综合因素生产作业环境中,湿度、温度、照明、振动、噪音、粉尘、有毒有害物质等会影响人在工作中的情绪;恶劣地作业环境还会导致职业性伤害。
安全生产是一套人、机、环境系统。
合理匹配可实现“机宜人、人适机、人机匹配”,能减少失误、提高效率,消除事故,做到本质安全。
如何营造一个良好地作业环境,消除职业危害,是作业环境管理的核心。
在现场管理过程中,要及时发现、分析、消除作业环境中的各项事故隐患,努力提高现场生产条件,切实保障员工的安全与健康,防止安全事故的发生,促进生产力发展第二篇:发生安全事故的原因发生安全事故的最根本原因:一是人的思想不够重视,安全意识差;二是机械设备安全保护性能差,施工人员在操作当中不规范;三是安全防护措施不到位。
应对措施:一:提高自我意识,完善机构。
提高企业各级领导的认识。
认识到安全生产对企业信誉,名声,国家财产,施工人员的重要性。
做到“管生产必须管安全的原则。
处理好安全与生产,安全与效益,安全与进度的关系。
当三者与安全发生矛盾时,坚持安全第一的原则;建立安全生产管理小组。
其责任是:执行法规,政策,措施,计划,完善制度,解决难题,主持调查,提出改进措施。
二:健全制度,严加防范1.建立,健全各级各部门的安全生产责任制。
使任何人,任何部门都负有安全生产的责任,增强各级管理,施工人员的责任心,如对机械组人员要求必须做到施工前检查机械各项性能,施工中严格按照操作规程操作,施工后做好保养,维修工作,确保机器无故障,无超负荷运转等等,消除一切可能引发安全事故的隐患,避免安全事故发生。
安全事故主要原因
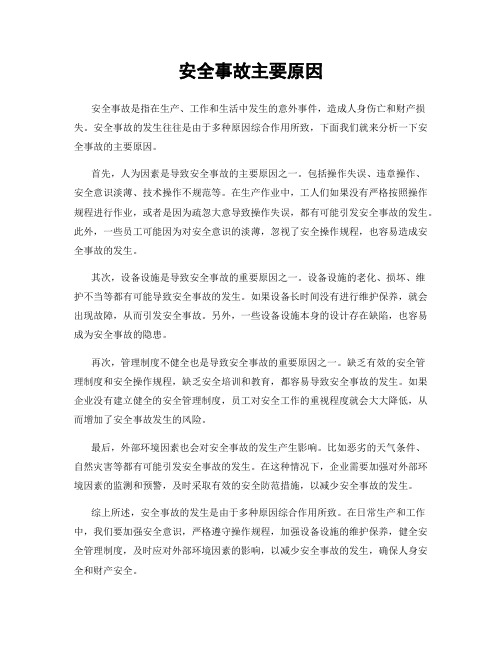
安全事故主要原因安全事故是指在生产、工作和生活中发生的意外事件,造成人身伤亡和财产损失。
安全事故的发生往往是由于多种原因综合作用所致,下面我们就来分析一下安全事故的主要原因。
首先,人为因素是导致安全事故的主要原因之一。
包括操作失误、违章操作、安全意识淡薄、技术操作不规范等。
在生产作业中,工人们如果没有严格按照操作规程进行作业,或者是因为疏忽大意导致操作失误,都有可能引发安全事故的发生。
此外,一些员工可能因为对安全意识的淡薄,忽视了安全操作规程,也容易造成安全事故的发生。
其次,设备设施是导致安全事故的重要原因之一。
设备设施的老化、损坏、维护不当等都有可能导致安全事故的发生。
如果设备长时间没有进行维护保养,就会出现故障,从而引发安全事故。
另外,一些设备设施本身的设计存在缺陷,也容易成为安全事故的隐患。
再次,管理制度不健全也是导致安全事故的重要原因之一。
缺乏有效的安全管理制度和安全操作规程,缺乏安全培训和教育,都容易导致安全事故的发生。
如果企业没有建立健全的安全管理制度,员工对安全工作的重视程度就会大大降低,从而增加了安全事故发生的风险。
最后,外部环境因素也会对安全事故的发生产生影响。
比如恶劣的天气条件、自然灾害等都有可能引发安全事故的发生。
在这种情况下,企业需要加强对外部环境因素的监测和预警,及时采取有效的安全防范措施,以减少安全事故的发生。
综上所述,安全事故的发生是由于多种原因综合作用所致。
在日常生产和工作中,我们要加强安全意识,严格遵守操作规程,加强设备设施的维护保养,健全安全管理制度,及时应对外部环境因素的影响,以减少安全事故的发生,确保人身安全和财产安全。
常见安全事故原因分析
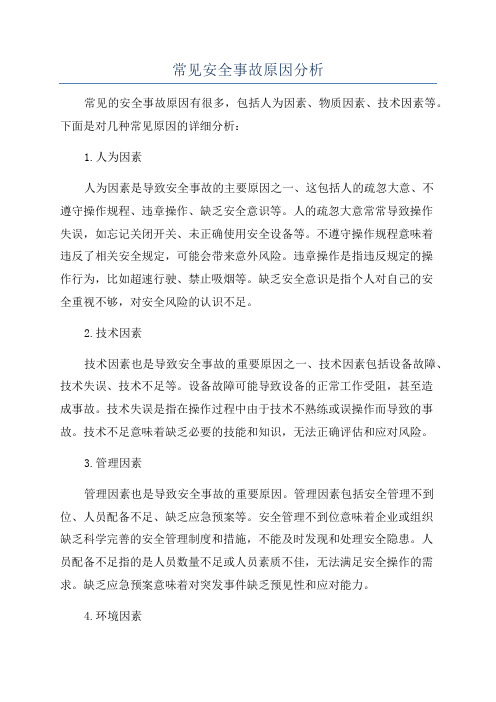
常见安全事故原因分析常见的安全事故原因有很多,包括人为因素、物质因素、技术因素等。
下面是对几种常见原因的详细分析:1.人为因素人为因素是导致安全事故的主要原因之一、这包括人的疏忽大意、不遵守操作规程、违章操作、缺乏安全意识等。
人的疏忽大意常常导致操作失误,如忘记关闭开关、未正确使用安全设备等。
不遵守操作规程意味着违反了相关安全规定,可能会带来意外风险。
违章操作是指违反规定的操作行为,比如超速行驶、禁止吸烟等。
缺乏安全意识是指个人对自己的安全重视不够,对安全风险的认识不足。
2.技术因素技术因素也是导致安全事故的重要原因之一、技术因素包括设备故障、技术失误、技术不足等。
设备故障可能导致设备的正常工作受阻,甚至造成事故。
技术失误是指在操作过程中由于技术不熟练或误操作而导致的事故。
技术不足意味着缺乏必要的技能和知识,无法正确评估和应对风险。
3.管理因素管理因素也是导致安全事故的重要原因。
管理因素包括安全管理不到位、人员配备不足、缺乏应急预案等。
安全管理不到位意味着企业或组织缺乏科学完善的安全管理制度和措施,不能及时发现和处理安全隐患。
人员配备不足指的是人员数量不足或人员素质不佳,无法满足安全操作的需求。
缺乏应急预案意味着对突发事件缺乏预见性和应对能力。
4.环境因素环境因素也是导致安全事故的重要原因之一、环境因素包括天气、地质、气候、设备设施等。
恶劣的天气条件,如暴风雪、大雨等,可能导致道路积水、结冰等不利于交通安全的情况。
地质条件不良,如山区、河流等地形复杂,容易导致交通事故。
气候因素如大雾、高温等也可能导致安全事故的发生。
设备设施的状况也是影响安全的重要因素,如果设备老化、损坏,就会增加事故的风险。
总结起来,常见的安全事故原因包括人为因素、技术因素、管理因素和环境因素。
这些因素之间相互作用,导致了安全事故的发生。
通过加强安全教育培训、提高人员素质、完善管理制度和采取相应的应急措施,可以降低安全事故的发生率,减少人身财产损失,确保生产和生活的安全。
工程施工常见事故原因(3篇)

第1篇一、人员因素1. 操作人员素质不高:部分施工人员缺乏必要的专业技能和安全意识,对操作规程和安全生产知识掌握不足,容易引发事故。
2. 疲劳作业:长时间连续工作,导致操作人员精神状态不佳,注意力不集中,容易引发事故。
3. 违章作业:部分施工人员为了追求速度,忽视安全操作规程,进行违章作业,从而引发事故。
二、设备因素1. 设备老化:部分机械设备长期使用,缺乏必要的保养和维护,导致设备性能下降,存在安全隐患。
2. 设备故障:机械设备在运行过程中,由于各种原因可能出现故障,如润滑不良、电气故障等,容易引发事故。
3. 设备操作不当:操作人员对设备性能不熟悉,或操作不规范,导致设备运行不稳定,引发事故。
三、环境因素1. 气象条件:恶劣的气象条件,如强风、暴雨、高温等,容易导致施工事故。
2. 地质条件:地质条件复杂,如土质松软、地基承载力不足等,容易引发坍塌、滑坡等事故。
3. 施工现场环境:施工现场环境杂乱,如材料堆放不规范、施工通道不畅等,容易引发事故。
四、管理因素1. 安全管理制度不健全:部分施工单位安全管理制度不完善,安全责任制不明确,导致安全管理工作不到位。
2. 安全教育培训不足:施工单位对员工的安全教育培训不够,员工安全意识淡薄,容易引发事故。
3. 监督检查不到位:施工现场监督检查不力,安全隐患排查不及时,导致事故发生。
五、其他因素1. 材料因素:部分建筑材料质量不合格,存在安全隐患。
2. 施工工艺因素:施工工艺不合理,导致施工过程中存在安全隐患。
针对以上原因,以下提出一些预防措施:1. 加强人员培训,提高操作人员素质和安全意识。
2. 定期对设备进行检查、保养和维护,确保设备安全运行。
3. 优化施工环境,确保施工现场安全。
4. 建立健全安全管理制度,明确安全责任制。
5. 加强施工现场监督检查,及时排查安全隐患。
6. 选用优质建筑材料,确保施工质量。
通过以上措施,可以有效预防和减少工程施工中常见事故的发生,保障施工安全和工程质量。
造成安全事故的原因
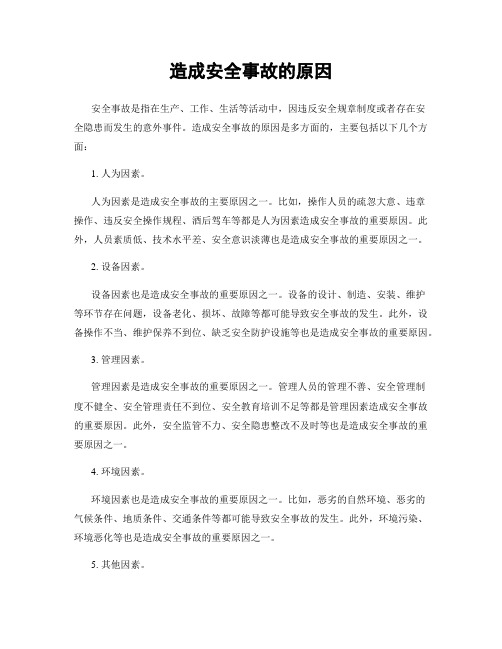
造成安全事故的原因安全事故是指在生产、工作、生活等活动中,因违反安全规章制度或者存在安全隐患而发生的意外事件。
造成安全事故的原因是多方面的,主要包括以下几个方面:1. 人为因素。
人为因素是造成安全事故的主要原因之一。
比如,操作人员的疏忽大意、违章操作、违反安全操作规程、酒后驾车等都是人为因素造成安全事故的重要原因。
此外,人员素质低、技术水平差、安全意识淡薄也是造成安全事故的重要原因之一。
2. 设备因素。
设备因素也是造成安全事故的重要原因之一。
设备的设计、制造、安装、维护等环节存在问题,设备老化、损坏、故障等都可能导致安全事故的发生。
此外,设备操作不当、维护保养不到位、缺乏安全防护设施等也是造成安全事故的重要原因。
3. 管理因素。
管理因素是造成安全事故的重要原因之一。
管理人员的管理不善、安全管理制度不健全、安全管理责任不到位、安全教育培训不足等都是管理因素造成安全事故的重要原因。
此外,安全监管不力、安全隐患整改不及时等也是造成安全事故的重要原因之一。
4. 环境因素。
环境因素也是造成安全事故的重要原因之一。
比如,恶劣的自然环境、恶劣的气候条件、地质条件、交通条件等都可能导致安全事故的发生。
此外,环境污染、环境恶化等也是造成安全事故的重要原因之一。
5. 其他因素。
除了上述几个主要原因外,还有一些其他因素也可能导致安全事故的发生。
比如,突发事件、意外因素、人为破坏、恶意犯罪等也都可能是造成安全事故的重要原因之一。
综上所述,造成安全事故的原因是多方面的,主要包括人为因素、设备因素、管理因素、环境因素和其他因素。
为了预防安全事故的发生,我们需要从多个方面入手,加强安全管理,提高安全意识,加强安全教育培训,加强设备维护保养,加强安全监管等,共同努力,共同维护安全,共同营造安全的生产、工作、生活环境。
- 1、下载文档前请自行甄别文档内容的完整性,平台不提供额外的编辑、内容补充、找答案等附加服务。
- 2、"仅部分预览"的文档,不可在线预览部分如存在完整性等问题,可反馈申请退款(可完整预览的文档不适用该条件!)。
- 3、如文档侵犯您的权益,请联系客服反馈,我们会尽快为您处理(人工客服工作时间:9:00-18:30)。
事故伤害的主要原因
人的不安全行为
人机系统把生产过程中并发挥一定作用的机械、物料、生产对象以及其他生产要素统称为物。
物都具有不同形式、性质的能量,有出现能量意外释放,引发事故的可能性。
由于物的能量可能释放引起事故的状态,称为物的不安全状态。
这是从能量与人的伤害间的联系所给以的定义。
如果从发生事故的角度,也可把物的不安全状态看作为,曾引起或可能引起事故的物的状态。
在生产过程中,物的不安全状态极易出现。
所有的物的不安全状态,都与人的不安全行为或人的操作、管理失误有关。
往往在物的不安全状态背后,隐藏着人的不安全行为或人失误。
物的不安全状态既反映了物的自身特性,又反映了人的素质和人的决策水平。
物的不安全状态的运动轨迹,一旦与人的不安全行为的运动轨迹交*,就是发生事故的时间与空间。
所以,物的不安全状态是发生事故的直接原因。
因此,正确判断物的具体不安全状态,控制其发展,对预防、消除事故有直接的现实意义。
针对生产中物的不安全状态的形成与发展,在进行施工设计、工艺安排、施工组织与具体操作时,采取有效的控制措施,把物的不安全状态消除在生产活动进行之前,或引发为事故之前,是安全管理的重要任务之一。
消除生产活动中物的不安全状态,是生产活动所必须的,又是。
预防为主"方针落实的需要,同时,也体现了生产组织者的素质状况和
工作才能。
(一)能量意外释放与控制方法
生产活动中一时也未间断过能量的利用,在利用中,人们给以能量种种约束与限制,使之按人的意志进行流动与转换,正常发挥能量用以做功。
一旦能量失去人的控制,便会立即超越约束与限制,自行开辟新的流动渠道,出现能量的突然释放,于是,发生事故的可能性就随着突然释放而变得完全可能。
突然释放的能量,如果达及人体又超过人体的承受能力,就会酿成伤害事故。
从这个观点去看,事故是不正常或不希望的能量意外释放的最终结果。
一切机械能、电能、热能、化学能、声能、光能、生物能、辐射能等,都能引发伤害事故。
能量超过人的机体组织的抵抗能力,造成人体的各种伤害。
人与环境的正常能量交换受到干扰,造成窒息或淹溺。
能量媒介或载体与人体接触,将会把能量传递给人体造成伤害。
能量的类别不同,在突然释放时,所造成的人体伤害差别很大,造成事故的类别也是完全不同的。
人与能量接触而受到刺激,能否造成伤害和伤害程度,完全取决于作用能量的大小。
能量与人接触的时间长短,接触频率高低,集中程度,接触人体部位等,也会影响对人的伤害严重程度。
人丧失了对能量的有效约束与控制,是能量意外释放的直接原因和根本原因。
出现能量的意外释放,反应了人对能量控制认识、意识、知识、技术的严重不足。
同时,又反应了安全管理认识、方法、原则
等方面的差距。
发生能量意外释放的根本原因,是对能量正常流动与转换的失控。
是人而不是能量本身。
(二)屏蔽
约束、限制能量意外释放,防止能量与人体接触的措施,统称为屏蔽。
常采用的屏蔽形式大致有:
(1)安全能源代替不安全能源。
(2)限制能量。
(3)防止能量蓄积。
(4)缓释能量。
(5)物理屏蔽。
(6)时空隔离。
(7)信息屏蔽等。
(三)能量意外释放伤害及预防措施
人意外的进入能量正常流动与转换渠道而致伤害。
有效的预防方法是采取物理屏蔽和信息屏蔽,阻止人进入流动渠道。
能量意外逸出,在开辟新流动渠道时达及人体而致伤害。
发生此类事故有突然性,事故发生瞬间,人往往来不及采取措施即已受到伤害。
预防的方法比较复杂,除加大流动渠道的安全性,从根本上防止能量外逸。
同时在能量正常流动与转换时,采取物理屏蔽、信息屏蔽、时空屏蔽等综合措施,能够减轻伤害的机会和严重程度。
出现这类事故时,人的行为是否正确,往往决定人的伤害或生存。
在有毒有害物质渠道出现泄漏时,人的行为对人的伤害与生存关系,尤其明显。
能量意外释放,人进入能量新渠道而受到伤害。
预防此类事故,完善能量控制系统最为重要,如自动报警、自动控制,既需要在出现能量释放时立即报警,又能进行自动疏放或封闭。
同时在能量正常流动与转换时,应考虑非正常时的处理,及早采取时空与物理屏蔽措施。