6sigma-design
32六西格玛设计
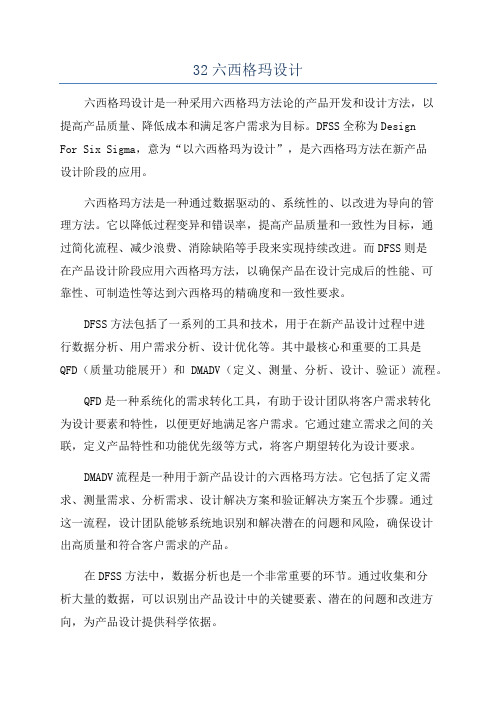
32六西格玛设计六西格玛设计是一种采用六西格玛方法论的产品开发和设计方法,以提高产品质量、降低成本和满足客户需求为目标。
DFSS全称为DesignFor Six Sigma,意为“以六西格玛为设计”,是六西格玛方法在新产品设计阶段的应用。
六西格玛方法是一种通过数据驱动的、系统性的、以改进为导向的管理方法。
它以降低过程变异和错误率,提高产品质量和一致性为目标,通过简化流程、减少浪费、消除缺陷等手段来实现持续改进。
而DFSS则是在产品设计阶段应用六西格玛方法,以确保产品在设计完成后的性能、可靠性、可制造性等达到六西格玛的精确度和一致性要求。
DFSS方法包括了一系列的工具和技术,用于在新产品设计过程中进行数据分析、用户需求分析、设计优化等。
其中最核心和重要的工具是QFD(质量功能展开)和DMADV(定义、测量、分析、设计、验证)流程。
QFD是一种系统化的需求转化工具,有助于设计团队将客户需求转化为设计要素和特性,以便更好地满足客户需求。
它通过建立需求之间的关联,定义产品特性和功能优先级等方式,将客户期望转化为设计要求。
DMADV流程是一种用于新产品设计的六西格玛方法。
它包括了定义需求、测量需求、分析需求、设计解决方案和验证解决方案五个步骤。
通过这一流程,设计团队能够系统地识别和解决潜在的问题和风险,确保设计出高质量和符合客户需求的产品。
在DFSS方法中,数据分析也是一个非常重要的环节。
通过收集和分析大量的数据,可以识别出产品设计中的关键要素、潜在的问题和改进方向,为产品设计提供科学依据。
六西格玛设计的目标是确保设计的产品在生产和使用过程中能够保持高质量和高性能的特点。
通过应用DFSS方法,可以减少产品的变异性、缺陷和浪费,提高生产效率和客户满意度。
同时,通过对用户需求和市场环境的深入理解和分析,设计的产品能更好地满足市场需求,提高竞争力和盈利能力。
总之,六西格玛设计是一种以六西格玛方法论为基础的产品设计方法,通过数据分析、用户需求转化、改进流程等手段,确保设计出高质量和符合客户需求的产品。
六西格玛设计

Design For Six Sigma
高级六西格玛管理从一开始就注重设计质量,进行六西格玛 设计(DFSS),要从改善达到六西格玛逾越的障碍和代价是可 想而知的,21世纪需要六西格玛设计的高级复合型人才。
通用电气(GE)人力资源总裁 Bell Jason
– 当市场期待新的产品或服务时。
• 当一般公差影响了期待的质量水平时。
– 产品和部件的装配 – 订单的周期时间 – 集装箱/产品包装配合不当
DFSS和生产能力的设计注重系统中个体和总体的关系
为什么要(六西格玛)设计
产品 设计
工艺 设计
生产 控制
产品 质量
质量杠杆图
质量控制的认识过程
质量是检验出来的 质量是制造出来的 质量是设计出来的 质量是定义出来的
质量特性关系矩阵
新产品升级计划(MGP)
质量损失函数
蒙特卡罗分析(Montr Carlo Simulation)
模型模拟实验(MDOE) 计算机仿真
人-机工学分析
迭代计划(MGDP)
可靠性设计
设计优先模型
概念化设计
决策矩阵
优化方法
PDCA循环
测量系统分析(MSA) 软件评价
散布图
回归分析
结构树
关系图
可靠性 设计
顾客
1 效率量化指标
强度和
2 系统效率分析
刚度
1 经济性量化指标 2 可维修性和维修保障性分析
制造工艺
1 安全性指标
自动报警 零件加
2 安全参数分析
装置设计 工技术
3 干扰作用分析 1 运输与包装的量化指标 2 防护性措施 1 顾客的CTQ指标 2 顾客需求分析 3 顾客调查分析
六西格玛设计
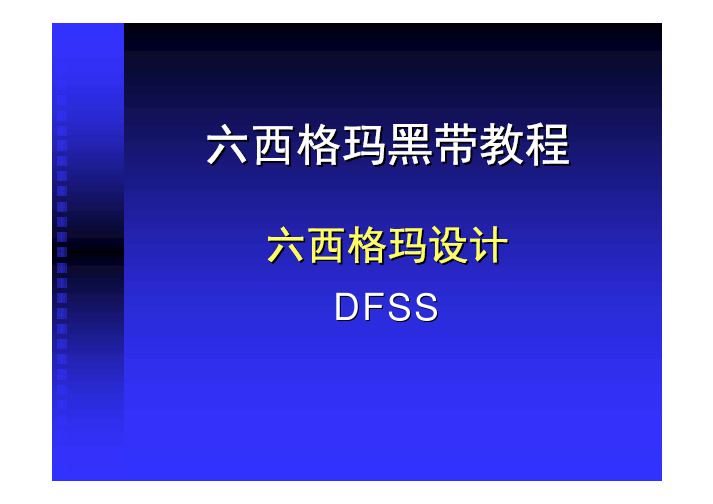
六西格玛设计六西格玛设计六西格玛设计全新六西格玛设计全新六西格玛设计D C C D I六西格玛管理的三部曲6SIGMA 过程(I FSS )OFSS I FSSPFSS 6SIGMA过程改进DMAIC过程设计DMADV 过程管理DMAIDMAIC DMADV概念产生概念产生更改DMADVDMADV发现当前的过程绩效同顾客的需求相差甚远,以至于仅仅通过“修理”已经不能解决问题。
使过程恶化的原因(关键的X)数目太多了,最好是用一个新的过程取代老过程顾客要求更大的灵活性,但是经过团队改进后的过程也还是太死板。
新技术可能会淘汰企业当前的一些做法政府政策法规的变化构成了机遇或挑战。
新的竞争者带着新技术出现,随时会抢占你的市场。
原先做的假设变得不适用。
企业假定能源的价格在一年内不翻倍的话,就能获得成功。
但如果翻倍了,结果又将如何呢?先思考后行动六西格玛过程过程改进过程设计/重新设计界定发现问题定义要求确定目标界定特定的或大体的问题定义目标/改变愿景阐明范围和顾客要求测量证实问题/过程修改问题/目标测量关键步骤/输入测量要求是否达到集过程效率的数据分析得出关于原因的假设界定“关键的少数”根本原因证实假设界定“最好的运作方法”评估过程设计增值/不增值;瓶颈/断开;其它途径修改要求改进提出去除根本原因的建议测试解决方法把解决方法标准化/测量结果设计新过程质疑挑战;应用创造力;工作流原则控制建立标准的测量手段,以维持绩效若有必要,修正问题建立测量和审查手段,维持绩效若有必要,纠正问题六西格玛设计愿景六西格玛设计/重新设计步骤一、愿景1.在开始之前:有一个愿景1.最初的一次或几次头脑风暴会议就过程,服务,产品,能力进行描述。
2.需要时间审视和评价在头脑风暴过程中得出的结论。
包括将愿景与企业的战略目标、顾客需求、和组织的竞争力等相比较。
3.使整个团队或者把团队分成几部分,把从头脑风暴中得出的想法整合成初步的愿景,然后安排时间让大家参与讨论,就这个初步的愿景提出自己的意见。
工业4.0术语:DFSS六西格玛设计
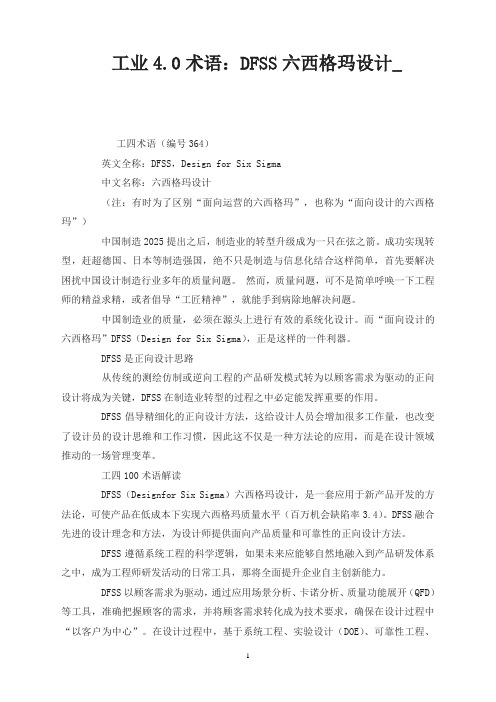
工业4.0术语:DFSS六西格玛设计_工四术语(编号364)英文全称:DFSS,Design for Six Sigma中文名称:六西格玛设计(注:有时为了区别“面向运营的六西格玛”,也称为“面向设计的六西格玛”)中国制造2025提出之后,制造业的转型升级成为一只在弦之箭。
成功实现转型,赶超德国、日本等制造强国,绝不只是制造与信息化结合这样简单,首先要解决困扰中国设计制造行业多年的质量问题。
然而,质量问题,可不是简单呼唤一下工程师的精益求精,或者倡导“工匠精神”,就能手到病除地解决问题。
中国制造业的质量,必须在源头上进行有效的系统化设计。
而“面向设计的六西格玛”DFSS(Design for Six Sigma),正是这样的一件利器。
DFSS是正向设计思路从传统的测绘仿制或逆向工程的产品研发模式转为以顾客需求为驱动的正向设计将成为关键,DFSS在制造业转型的过程之中必定能发挥重要的作用。
DFSS倡导精细化的正向设计方法,这给设计人员会增加很多工作量,也改变了设计员的设计思维和工作习惯,因此这不仅是一种方法论的应用,而是在设计领域推动的一场管理变革。
工四100术语解读DFSS(Designfor Six Sigma)六西格玛设计,是一套应用于新产品开发的方法论,可使产品在低成本下实现六西格玛质量水平(百万机会缺陷率3.4)。
DFSS融合先进的设计理念和方法,为设计师提供面向产品质量和可靠性的正向设计方法。
DFSS遵循系统工程的科学逻辑,如果未来应能够自然地融入到产品研发体系之中,成为工程师研发活动的日常工具,那将全面提升企业自主创新能力。
DFSS以顾客需求为驱动,通过应用场景分析、卡诺分析、质量功能展开(QFD)等工具,准确把握顾客的需求,并将顾客需求转化成为技术要求,确保在设计过程中“以客户为中心”。
在设计过程中,基于系统工程、实验设计(DOE)、可靠性工程、面向制造性和装配性的设计(DFMA)等技术与方法,确定顾客需求与系统、子系统、部件、零件之间的传递函数,实现定量化描述顾客需求转化的过程,并逐层优化设计参数和公差,权衡分析后得到最优的设计结果。
6σ(六西格玛) 工作流程

6 Sigma/Lean (6 西格玛/精益)1. 六标准差(Six Sigma) 是要为您确定什麼是您不知道的、并且强调什麼是您必须知道的,同时须采取那些措施减少错误,以及重新整合、组织您浪费的时间成本、金钱、成功机会及错失的客户。
2. 六标准差(Six Sigma) 利用统计学的概念来衡量流程中的瑕疵。
达到六标准差,即意味著您的生产流程中仅会有百万之3.4 的不良率(Defects per Million Opportunities, DPMO) ;换句话说,这表示已经接近完美状况。
Sigma (σ) 是希腊字元,为「标准差(Standard Deviation)」的衡量。
在商业术语中,其代表「流程」与「完美」的偏差值3. 6西格玛管理不仅是理念,同时也是一套业绩突破的方法。
它将理念变为行动,将目标变为现实。
这套方法就是6西格玛改进方法DMAIC和6西格玛设计方法DFSS。
DMAIC是指定义(Define)、测量(Measure)、分析(Analyze)、改进(Improve)、控制(Control)五个阶段构成的过程改进方法,一般用于对现有流程的改进,包括制造过程、服务过程以及工作过程等等。
DFSS是Design for Six Sigma的缩写,是指对新流程、新产品的设计方法。
4.一个完整的6西格玛改进项目应完成“定义D”、“测量M”、“分析A”、“改进I”和“控制C”5个阶段的工作。
每个阶段又由若干个工作步骤构成。
虽然,Motorola、GE、6Sigma Plus、Smart Solution等采用的工作步骤不尽相同,有的采用6步法,有的采用12步法或24步法。
但每个阶段的主要内容是大致相同的5. 6 Sigma 流程图6σ的DMAIC方法最初是作为一种质量绩效测量方法而引入的,现在已经演变成为一种制定发展战略、降低生产成本、提高产品质量和改进经营业绩的管理模式,并在一些企业中获得得到成功,于是被普遍重视和采用。
DFSS简介

DFSSDFSS(Design For Six Sigma)是六西格玛设计的英文缩写,“六西格玛设计”是一个广义概念,它包容的一揽子方法适用于引入新产品和新服务,适用于应付DMAIC 六西格玛模型的内在局限。
六西格玛设计框架是在早期六西格玛改进方法的基础上逐渐演变生成,仅凭愿望产生不了更好的“设计”过程或者更好的新产品和新服务交付过程。
中文名六西格玛设计外文名Design For Six Sigma简称DFSS应用范围新的产品或服务流程的设计目录1.1综述2.2概念3.3方法论4.▪必须实施DFSS1.▪DFSS应运而生2.▪实用价值3.▪工作内容4.▪保障5.4流程1.5培训内容2.6新产品开发作业的结合综述编辑六西格玛设计作为六西格玛管理核心方法系统之一,虽然和BPR 一样是一个面向流程再造的管理方法和思想。
然而不同的是,DFSS 的应用绝不仅仅局限于对现有业务流程的再造,而且还广泛应用于新的产品或服务流程的设计,它是六西格玛管理战略实施的最高境界。
作为一个方法体系,它可以与DMAIC(即D定义、M测量、A分析、I 改善、C控制,是应用六西格玛原理于现有流程的优化)相结合,从而实现对现有流程的突破性改善。
概念编辑六西格玛设计从六西格玛改进自然演变而来,是六西格玛改进的外延。
更准确地说,六西格玛设计是综合考虑所要实现的六西格玛全部意图以及在新产品设计和商业投放中遭遇的各种挫折的产物,没有任何一个单独的六西格玛设计模型足以应付所有问题,而各自对六西格玛做这样或那样的调整又存在非常现实的危险——很可能遗漏顾客的根本需求。
六西格玛改进可以显著地降低过程缺陷和差错率,使之达到一般商业组织普遍接受的水平。
这种改进的极限是相当于最坏差错率的最大回报率。
随着组织逐渐地向“每百万3.4个缺陷”的六西格玛目标推进,从世界水平质量得到的硬回报将逐渐减少,转而支持柔性效益,例如,为更好的顾客满意度和更高昂的雇员积极性而拼搏。
6Sigma实验设计介绍

6Sigma 实验设计介绍实验设计实验设计介绍Page6Sigma 实验设计课程规划各节内容11>.课程介绍2.实验设计介绍3.全因数4.部分因数5.实验设计规划6.案例Page实验设计-1全因数Page根本原因分析的两种方法(Two method for root cause analysis)用历史数据观察流程散布图,进行图,控制图,分层(scatterplot/run chart/control chart/deplay相关性,差异分析,回归分析(correlation/ANOVA/regression)流程的实验,用一个规划好的方法变流程并衡量结果实验设计实验设计是有效率和有效果地探究许多流程变量(X)和产出衡量或关键量点(Y)的因果关系的一种方法。
Page使用历史数据的一些限制some limitation when using history data记录常是不完整的(省略的变量(X)缺少的值或观察数据包含数据惧错误流程变量通常是有相互关系的重要变量可能没有变化得足够充分到能了解它们的影响的程度通常来就,必要数据不是立刻可得到的,获得正确数据是非常必要的。
Page识别关键变量(Identify key variables)历史方法(history method)Page练习:确定最佳关键变量设置-历史方法目标:了解到识别影响化学流程产量的关键变量的难点(30分钟)说明:用下页的信息来设置一个衡量计划,从而发现能使流程产量最大化的各变量最好设置。
每个实验运行成本$2,000你对初始调查的总体预算是$30,000如果有足够的证据,另外有$50,000可用于将来的研究确定在给定的不同标准内可能的变量组合总数确定在现在预算内你可作出的变量组合总数你会检验什么组合?你用什么策略来识别关键变量?Page练习:确定最佳关键变量设置-历史方法练习:流程中的关键变量是:原料卖主。
(A,B,C)原料放进混合桶中的温度。
什么是六西格玛

什么是六西格玛西格玛是一个希腊字母,在统计学上表示为标准差,在质量上是流程变异的衡量。
流程变异是企业的敌人,流程的变异包括了原材料的波动、参数的变化、工艺的不一致等等,流程的变异导致了企业无法保证产品的质量和交期的稳定性,也导致了成本的上升。
六西格玛的目标是是企业的质量水平达到六个西格玛水平,即每百万个机会中只有3.4个缺陷,目前国内大多数企业的质量水平是在3到4个西格玛水平之间,也就是每百万个机会中大概有6200到68000个缺陷。
是企业的质量水平达到6s水平是六西格玛的目标,为了达成此目标,六西格玛发展出一套结构化的严谨的流程改善方法论。
这套方法论中核心的方法是DMAIC和DMADV。
DMAIC主要针对现有的不能满足要求的流程或产品,通过Define(定义)、Measure(测量)、Analyze(分析)、Improve(改进)和Control(控制)有步骤有条理的提高流程或产品的质量;而DMADV主要针对新的流程或产品,通过Define(定义)、Measure (测量)、Analyze(分析),Design(设计)和Verify(验证)来使新流程新产品达到六西格玛的水平。
流程和产品的改进是通过一个个改善项目的完成达到的。
黑带(BlackσBelt)和绿带(Green Belt)是六西格玛改善项目的实施负责人。
六西格玛在使用结构化的严谨的方法提高企业流程和产品质量的同时也倡导着一种高效的企业运营的文化。
这种文化通过关注客户的需求出发,应用事实和数据对流程进行改善和和管理,从而达到最大化企业。
六西格玛文化提倡建立以测量和数据为基础的企业决策流程、企业部门间的无边界合作。
六西格玛是中国企业规范企业运作、提高竞争力的有效的途径。
σ概括地讲,六西格玛是这样三件事:1)统计度量;2)业务策略;3)思维哲学.什么是六西格玛管理法?六西格码管理法是以质量作为主线,以客户需求为中心,利用对事实和数据的分析,改进提升一个组织的业务流程能力,是一套灵活的,综合性的管理方法体系。
六西格玛设计在实际工作中的运用

/ 六西格玛设计在实际工作中的运用什么是六西格玛设计:设计是通过组合已知思想和事物在解决问题过程中形成有补充价值的新的合成方案,它不同于发明和发现。
而设计自身并不是工程师们独有的知识领域,设计是每一个人的事情,如果你在工作你就在设计,我们设计项目、设计流程、设计报告和计划。
六西格玛的设计可以被成功而有效地运用到我们每天实际参与的每个行动中。
比如我们可以用六西格玛设计来设计一个成本效率高且无缺陷的昼夜交付系统;或者设计一个重量更轻更结实的汽车轮轴盖;或者为公司设计一个效率更高的内部电子邮件系统,以减少公司内部电子邮件的地址错误等等。
六西格玛设计就是按照合理的流程、运用科学的方法准确理解和把握顾客需求,对新产品、新流程进行健壮设计,使产品、流程在低成本下实现六西格玛质量水平。
同时使产品、流程本身具有抵抗各种干扰的能力,既是使用环境恶劣或操作者瞎折腾,产品仍能满足顾客的需求。
六西格玛设计就是帮助你实现在提高产品质量和可靠性的同时降低成本和缩短研制周期的有效方法,具有很高的实用价值。
通过六西格玛设计的产品、流程的质量水平甚至可达到七西格玛水平。
六西格玛设计是6Sigma管理的最高境界。
进收益和数据收集难度及其成本,对于收据收集比较困难或者数据收集成本较高的项目,则可以采取快速群策群力的形式来做。
六西格玛设计按照I-D-O-V(Identify(识别)、Design(设计)、Optimize(优化)、Verify(验证))路径,并结合实际案例研讨和现场试验来教学。
课程学习旨在实现以下目标:①了解DFSS方法论的发展背景,熟悉DFSS的实施路径及特点;②掌握IDOV研发路线图各阶段的核心工作与关键输出;③理解IDOV研发路线图与传统研发管理流程的关系及区别;④掌握统计方法及工具在IDOV研发过程中的应用,包括:MSA、DOE、ANOVA、SPC、假设检定、相关与回归、蒙特卡罗模拟、可靠性分析等;⑤能够熟练运用质量功能展开(QFD)准确挖掘顾客心声,并识别出关键的设计要求(买点、改善与蛙跳机会);⑥能够运用TRIZ创新路线图解决设计中遭遇的技术矛盾问题,并产生专利;⑦掌握试验设计的建模优化思路及步骤(筛选、量化、优化、稳健);⑧理解田口品质损失函数和S/N比等概念,掌握稳健设计方法;⑨能够独立带领团队实施DFSS项目。
验证六西格玛设计项目三大步骤

验证六西格玛设计项目三大步骤通常,DMAIC项目的重点都是去除少数引起过程或产品缺陷以及高额成本的主要原因:但是,这些改进性项目并不能满足企业变革的所有要求。
有些过程就像老破车一样:你能把这个或那个恼人的毛病修好,让它重新上路,但是可能由此花费更多的费用。
最后你会意识到,最好还是换辆新车,既好用又合理。
那么,对于企业进行改进来说,这时就应该重新建立或“设计”一个新的过程。
六西格玛设计(DFSS)就是这样一种方法。
那么,今天验证六西格玛设计项目三大步骤:1、验证生产过程的能力。
也就是确定人员配备、培训过程、评估仪器、衡量体系以及校准程序等方面的生产能力,以保证能够以最低的成本交付无缺陷的产品。
2、建立、测试并固定原型。
这是验证的中心环节,它将工程人员、制造人员和服务人员与顾客组织起来,一起对所交付的高质量、低成本的产品和服务进行验证。
最具创新性的验证方法是定额测试。
在定额测试中,要先确定一个可接受的最低绩效水平,并确定一个有效期限(通常用时间或周期数来计算)。
如果有相当数量的原型成功通过了测试,就可以说设计是成功的。
要保证定额测试公平有效,需要首先决定在一个测试中应该测试的原型数量。
这就需要平衡对样品型号的需求程度与增加原型数量所耗费的时间、金钱之间的关系。
如果所有的原型都通过了测试,那么就需要确定对它们的设计是不是超过了标准,即设计时所定的标准比它们应该达到的要高。
如果这种情况发生,我们就需要进行失效测试,以便更加全面地研究上述意外情况。
失效测试是对所有的原型进行测试直到所有原型都失效为止。
通过对原型进行非常严格的测试,就可以将它们根据不同的型号区分开来,从而研究哪一个表现最好及其原因。
由于定额测试只衡量持久性,而失效测试又只衡量绩效,所以我们就要运用功能降级测试(Functional Degradation Testing,FDT),这一方法不仅衡量持久性,也衡量绩效,而且这两点也正是顾客会关注和衡量的方面。
DFSS简介

DFSS(Design For Six Sigma)是六西格玛设计的英文缩写,“六西格玛设计”是一个广义概念,它包容的一揽子方法适用于引入新产品和新服务,适用于应付DMAIC 六西格玛模型的内在局限。
六西格玛设计框架是在早期六西格玛改进方法的基础上逐渐演变生成,仅凭愿望产生不了更好的“设计”过程或者更好的新产品和新服务交付过程。
中文名六西格玛设计外文名Design For Six Sigma简称DFSS应用范围新的产品或服务流程的设计目录1. 1 综述2. 2 概念3. 3 方法论4.▪必须实施DFSS综述编辑六西格玛设计作为六西格玛管理核心方法系统之一,虽然和BPR 一样是一个面向流程再造的管理方法和思想。
然而不同的是,DFSS 的应用绝不仅仅局限于对现有业务流程的再造,而且还广泛应用于新的产品或服务流程的设计,它是六西格玛管理战略实施的最高境界。
作为一个方法体系,它可以与DMAIC(即D定义、M测量、A分析、I 改善、C控制,是应用六西格玛原理于现有流程的优化)相结合,从而实现对现有流程的突破性改善。
概念编辑六西格玛设计从六西格玛改进自然演变而来,是六西格玛改进的外延。
更准确地说,六西格玛设计是综合考虑所要实现的六西格玛全部意图以及在新产品设计和商业投放中遭遇的各种挫折的产物,没有任何一个单独的六西格玛设计模型足以应付所有问题,而各自对六西格玛做这样或那样的调整又存在非常现实的危险——很可能遗漏顾客的根本需求。
六西格玛改进可以显著地降低过程缺陷和差错率,使之达到一般商业组织普遍接受的水平。
这种改进的极限是相当于最坏差错率的最大回报率。
随着组织逐渐地向“每百万个缺陷”的六西格玛目标推进,从世界水平质量得到的硬回报将逐渐减少,转而支持柔性效益,例如,为更好的顾客满意度和更高昂的雇员积极性而拼搏。
这种柔性效益将使他们在新产品和新服务领域里感受到好得多的回报,并且得到这些回报。
方法论编辑DFSS是独立与传统六西格玛DMAIC的又一个方法论。
6sigma改善项目各阶段主要任务、活动要点及常用质量工具和方法
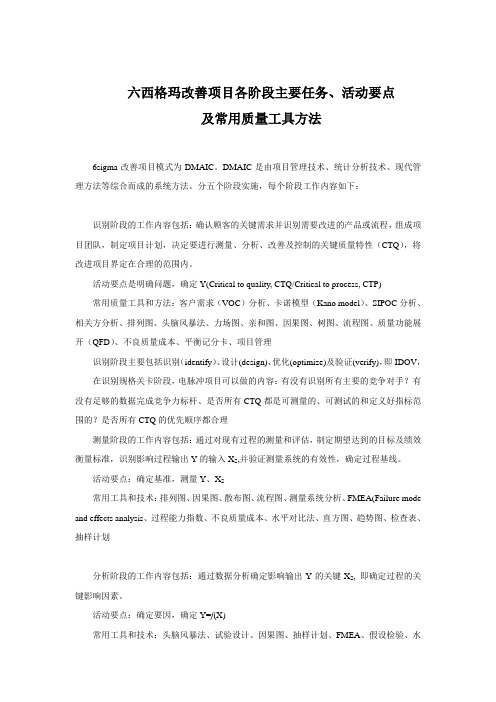
六西格玛改善项目各阶段主要任务、活动要点及常用质量工具方法6sigma改善项目模式为DMAIC。
DMAIC是由项目管理技术、统计分析技术、现代管理方法等综合而成的系统方法。
分五个阶段实施,每个阶段工作内容如下:识别阶段的工作内容包括:确认顾客的关键需求并识别需要改进的产品或流程,组成项目团队,制定项目计划,决定要进行测量、分析、改善及控制的关键质量特性(CTQ),将改进项目界定在合理的范围内。
活动要点是明确问题,确定Y(Critical to quality, CTQ/Critical to process, CTP)常用质量工具和方法:客户需求(VOC)分析、卡诺模型(Kano model)、SIPOC分析、相关方分析、排列图、头脑风暴法、力场图、亲和图、因果图、树图、流程图、质量功能展开(QFD)、不良质量成本、平衡记分卡、项目管理识别阶段主要包括识别(identify)、设计(design)、优化(optimize)及验证(verify),即IDOV,在识别规格关卡阶段,电脉冲项目可以做的内容:有没有识别所有主要的竞争对手?有没有足够的数据完成竞争力标杆、是否所有CTQ都是可测量的、可测试的和定义好指标范围的?是否所有CTQ的优先顺序都合理测量阶段的工作内容包括:通过对现有过程的测量和评估,制定期望达到的目标及绩效衡量标准,识别影响过程输出Y的输入X S,并验证测量系统的有效性,确定过程基线。
活动要点:确定基准,测量Y、X S常用工具和技术:排列图、因果图、散布图、流程图、测量系统分析、FMEA(Failure mode and effects analysis、过程能力指数、不良质量成本、水平对比法、直方图、趋势图、检查表、抽样计划分析阶段的工作内容包括:通过数据分析确定影响输出Y的关键X S, 即确定过程的关键影响因素。
活动要点:确定要因,确定Y=f(X)常用工具和技术:头脑风暴法、试验设计、因果图、抽样计划、FMEA、假设检验、水平对比法、多变异分析、方差分析、回归分析改善阶段的工作内容包括:寻找最优改进方案,优化过程输出Y并消除或减少关键X S 的影响,使过程的缺陷或变异降至最低。
六西格玛设计不仅仅是工具

六西格玛设计不仅仅是工具说起六西格玛,相信绝大多数企业并不陌生,但真正能够持续用好六西格玛,大幅提升效益的企业恐怕为数不多。
业界一项调查显示,超过50%的企业在导入六西格玛3年后还是选择了放弃。
是六西格玛推进的问题,还是创新本身的问题?日前,六西格玛设计交流(国际)研讨会在北京举行,上百家企业踊跃报名参加。
在企业热情高涨的背后,是传统的六西格玛管理遭遇发展瓶颈的现状。
但是谈起会议上说的最多的一个词——“六西格玛设计”(Design For Six Sigma,简称DFSS)时,多数企业都眉开眼笑、胸有成竹。
六西格玛管理的最新质量理念是什么?六西格玛设计为何受到企业追捧?不仅仅是改进工具“有些项目真正做成的话,就是几千万元的效益。
”山东莱芜钢铁集团有限公司培训中心朱迎春谈起六西格玛管理的优势时如此表示。
她举了一个企业之前应用六西格玛的项目,在钢铁厂内,运输原料时需要一些铁道运输。
比如把铁水、钢坯等从一地运到另一地,在车辆不能增加的情况下,就需要合理的调度,那么就可以用六西格玛的方法来做,一旦做好了,调度好了,铁水、钢坯的运输都不用等待,车辆也不用增加,利于提高工作效率,降低生产成本。
这个项目做完了大约带来了1亿元的效益,非常可观。
作为当今有效的质量改进模式之一,六西格玛已经被公认为是实现高质量和营运优越的高效工具,在国内外得到广泛应用,并取得积极成效。
据了解,六西格玛管理理念进入我国已有十多年的时间。
其中,报考黑带的人数不断增加,目前已经超过15000人次。
六西格玛质量理念不断衍变发展是客观事实,但是朱迎春的一席话给了我们另一番思考:如果说产品设计或者流程现状已经定型,即使把它的缺陷都消除了,也只能是在原来设计的基础上达到一个最优,但是如果说能够改变它的设计,从源头上抓好,产品或流程肯定比原来要好。
根据相关研究,通过传统的六西格玛管理方法(DMAIC)改进流程,质量水平无法突破5.7~5.8sigma界线(理想状态下)。
6 sigma设计_产品开发流程及工具(CTQ,DFMEA,TRIZ,QFD,Design for X)

FS R&DHuang Yonglin31th October 2010A Roadmap for Product Development培训对象与目的培训目的和必要性1.使工程师掌握6Sigma相关的基础知识.2.使工程师熟悉先进的产品开发流程和工具方法的运用.培训对象机械设计工程师工业工程师项目工程师质量工程师工艺工程师培训课时8小时一、Six Sigma Fundamentals introduction /六西格玛基本知识介绍二、Design for six sigma/6 sigma Design for six sigma/6 sigma设计原理设计原理三、优质设计管理模式3.1Sigma 设计流程(IDDOV )3.2Sigma 设计流程之确认I3.3Sigma 设计流程之定义产品概念D 3.4Sigma 设计流程之产品开发D 3.5Sigma 设计流程之优化设计O 3.6Sigma 设计流程之验证设计V本讲稿以6Sigma 设计原理(IDDOV)为主轴,结合新产品开发的系统理论,相关的新产品设计案例分析,深入浅出地讲述如何识别客户需求,运用系统设计原理、健壮式设计技术和实验设计法(DOE )等6Sigma 理论和工具(CTQ/QFD/TRIZ/Axiomatic design/ Robust design/ Design for X/ FMEA / Design review/ CAD Simulation/ Process management 等),设计出优质的产品。
本讲稿浓缩了产品开发理论精华和6Sigma 常用技术的应用技巧,让你在短短的一天时间里,轻松学到质量管理的专门知识。
四、系统设计理论及工具4.1 质量功能展开(QFD)技术:以经济的手段设计出市场适用的产品4.2 质量屋构成要素解释/制作质量屋详解4.3潜在失效模式分析(DFMEA):提高产品可靠度的良方4.4健壮式设计技术4.5实验设计法(DOE):寻找控制质量波动的最佳参数组合4.6参数设计:4.7容差设计:一、六西格玛背景介绍八十年代末期,六西格玛(6σ或Six Sigma)最早作为一种突破性的质量管理战略在摩托罗拉公司(Motorola)制造业领域付诸实践,使产品的不合格率大幅度下降。
6SIGMA品质管理方法

1、进料管制 2、成品管制 3、制程管制 4、设计管制
A QFD B 项目计划,执行与管制 C FMEA D MAIC,SPC E DOE,田口,参数设计 F QIT,CFT
改变带头人
CHAMPION-强式领导,负成败之责。 MASTER BLACK BELT-专业知识,提供技术支援
6,200
1.33
0.83
4.5
1990-1995
1,350
1.50
1.00
5.0
1995-1997
223
1.67
1.17
5.5
1997-1998
31.8
1.83
1.33
6.0
1998-2000
3.4
2.0
1.50
6σ-PPM 质量保证为3.4PPM,几乎全良品,在竞争策略理念下, 其产品质量就占有极强质量竞争优势。
常态分配
fxx
1 2
e
(
X 2
2
)2
P( X Z)
P( X 2)
X -2σ -1σ
1σ 2σ X
-2
2-VALUE
设Z为常态随机变量则 X ~ N(, ) Z ~ N(0,1) 则
0
称Z为标准常态随机变量 以
1
代入得
X 2
其机率密度函数为
(Z) Z
1 e Z2 2 2
Z
代入
=P( (─u─-a3─σ─)-<u z <( ─(─u─+3─aσ))-u
1.增加顾客满意度 2.减少制造成本 3.减少修护保证成本 4.增加质量保证 5.留住顾客
(4)没有DFM和高DPU效应
6SigmaDC 功能介绍

Details Option 1 Like for Like: Install one in each of the two racks that already have Sun M5000s installed. Option 2 Mix server types: Install one in each of the server racks with the most available space. Option 3 Install both in the empty rack in the row allocated to blades
Reclaiming Lost Capacity
Reclaiming cooling capacity using the Virtual Facility
Simulation can enable deployments that are beyond the original design
Nothing is Impossible
1 MW of total power available 820 kW of cooling capacity 3202 units of IT equipment drawing 770 kW Total energy bill: £ 850k per year £400k per year in cooling energy costs £430k per year in IT equipment energy costs
6SigmaDC 功能介绍 6SigmaDC
朱戈
北京天源博通科技有限公司 © 2009 All rights reserved
6SigmaDC 6SigmaDC 背景 Facilities公司 Future Facilities公司
六西格玛曲面设计介绍

六西格玛曲面设计介绍
六西格玛设计(Six Sigma Design)是一种以顾客需求和期望为导向的设计方法,它旨在通过最小化产品的缺陷和提高产品的质量来满足顾客的需求。
六西格玛曲面设计是六西格玛设计的一个重要组成部分,它使用统计分析和计算机模拟来优化产品的性能和功能。
六西格玛曲面设计的基本思想是通过对产品的各个部件和系统进行模拟和分析,找出可能影响产品性能和功能的因素,然后通过优化设计来改善这些因素,从而提高产品的质量。
在六西格玛曲面设计中,设计师通常会使用计算机辅助设计(CAD)和计算机辅助工程(CAE)软件来创建产品的三维模型,然后使用这些软件进行模拟和分析。
这些软件可以帮助设计师了解产品的性能和功能,找出可能影响产品质量的因素,然后通过优化设计来改善这些因素。
总的来说,六西格玛曲面设计是一种科学的设计方法,它可以帮助设计师更好地理解产品的性能和功能,找出可能影响产品质量的因素,然后通过优化设计来改善这些因素,从而提高产品的质量。
6Sigma设计的概念一

6Sigma设计的第二阶段:概念设计
? 确定可供选择的概念 ? 确认供选概念能否达到客户的要求和目标 ? 选择最有希望满足客户要求和目标的概念 ? 确保选择的概念展开后风险最小
6Sigma设计中概念设计的工具
? 头脑风暴法 ? TRIZ 创造性问题解决理论 ? 普式方法(一种对概念进行评估和发展的
6Sigma设计的项目预算
? 利润=销售量× (单价-单位制造成本)(项目一般管理费用+开发成本+质量成本)
创建6Sigma设计项目商业案例
? 这个项目是否与公司的战略目标和财务目 标相吻合?
? 为什么这个项目值得做? ? 为什么一定要现在开始做? ? 如果不做会有什么后果?
6Sigma设计项目计划
6Sigma设计验证
? 验证过程生产能力 ? 建立、测试并固定原型 ? 进行试生产
技巧) ? FMEA 失效模式及影响分析
6Sigma设计第三阶段:设计优化
? 稳健性设计 ? 底线原理:质量损失函数 ? 设计中的噪音 ? 参数设计 ? 公差设计
6Sigma设计第三阶段:设计优化
? 稳健性设计
? 尽量减少产品或流程的差异性 ? 调整输出信息,使其达到指标
6Sigma设计的噪音因素
? 保持一个老客户的成本只有开发一个新客 户成本的十分之一。
? 好的质量,是设计出来的。
6Sigma设计的概念(三)
? 如果只花费预算的 5%用于设计,而 70%的产品 成本是由设计产生的,就有可能 80%的质量问题 都被设计到产品中。
? 如果用30%的预算检测修改产品,就意味着先造 成一大堆问题,再花钱去更正问题。
? 如果预先打算好检修返工,那么后面必定会需要 进行检修与返工。
- 1、下载文档前请自行甄别文档内容的完整性,平台不提供额外的编辑、内容补充、找答案等附加服务。
- 2、"仅部分预览"的文档,不可在线预览部分如存在完整性等问题,可反馈申请退款(可完整预览的文档不适用该条件!)。
- 3、如文档侵犯您的权益,请联系客服反馈,我们会尽快为您处理(人工客服工作时间:9:00-18:30)。
N/A Used
N/A Used
Pilots complete/verified Commercialization Plan Implement CAP Plan Control Plan in Place Scorecards complete/approved Phase updated & approved
Select High-Level Design Product functions defined Develop Transfer Functions Design Models/Simulations Determine Quality “Gaps” Preliminary FMEA Complete Scorecard Updates Phase updated & approved
of 17
What’s wrong in this process? What’s missing between eacCTQ’s to your customers
3 of 17
How to produce good products
Manufacturing Marketing
MK
How Six Sigma Fits Into Our Process
V D
Market Analysis Competitive Analysis Business Analysis Design for Six Sigma
(Innovation)
A DFSS-i
D
M
M0
Opportunity Selection Requirement Analysis
Problem define with goal Customers identified Functional breakdown Benefits determined Project Funnel
N/A Used
Identify
N/A Used
PRACTICAL PROBLEM
Design
STATISTICAL PROBLEM
Design
Supplier quality
Finance
Sourcing
4 of 17
NPI - New Product Introduction CDRS - Critical to Design Requirement and Specification CTQ - Critical to Quality CV - Change Validation DHF - Design history Files DHR - Device history record DFM - Design for Manufacturing DFR - Design for Reliability FMEA - Failure Mode Effect Analysis FRU - Field Replaceable Unit HALT – Highly Accelerated Life Test HASS - Highly Accelerated Stress Screening HAST - Highly Accelerated Stress Test HLB - High Level Buy ICV - Internal Cost Value IB - Install Base OMS - Operation Manual and Spec. PA - Production Associate P&E - Production and Equipment QFD - Quality Flow Down QFU - Quality Flow Up QFD – Quality Function Deployment ZST - Z short term (6-sigma term) ZLT - Z long term (6-sigma)
Survey Requirement Strategy Capability study MP QCP Equip. V&V Production plan PA training
Service
Customer Satisfaction Warranty Serviceability Training IB FRU
Flowdown/up CTQ’s Determine and Measure CTP’s Predict/Improve Capability Error Proofing applied to FMEA Customer Feedback on Design Prototype/Pilot Verified Control Plan Developed Scorecard Updates Phase updated & approved
Customer Identified/Prioritized Customer Needs Prioritized Determine/Prioritize CTQ’s CTQ Measurements Determined Measurement Sys Capability Architectural models/simulations First Pass Scorecards Phase updated & approved
Statistical Problem Defined Process capability measured Exhaustive list of poss. “x’s” Potential vital few “x’s” Examination of distr. shape Anova/percent contribution
Design concept selected Exhaustive list of poss. “X’s” Potential vital few “X’s” Predict process capability “Y” Anova/percent contribution Advanced DoE optimization employed
Solution in place Confirmation run complete Z, COQ, PPM improvements Documentation in place Financial approved Before and after distributions Re-tolerance process
N/A Used
Business Case/Goal Statement Define Project Scope Integration with MGPP Definition of Team Develop Project Plan Define CAP Plan Estimate of benefits Phase updated & approved
Optimize
N/A Used N/A Used
STATISTICAL SOLUTION
Verify
STATISTICAL CONTROL
Customers needs identified Prioritized needs CTQs and spec define Target Zst Process Map
Introduction to 6-sigma & Mech. Design
1 of 17
1. What is 6-sigma? 2. How to produce good products? 3. 6-sigma process 4. Problem solving techniques 5. Software tools and demo 6. Quality policy
PRACTICAL PROBLEM
Analyze
N/A Used
STATISTICAL PROBLEM
Improve
N/A Used
STATISTICAL SOLUTION
Control
STATISTICAL CONTROL
Define
PRACTICAL PROBLEM
CTQs and spec define Validated Specification Meas. System Analysis Estimate Z Process Map Cost of Un-quality
*Items in BOLD are required or strongly recommended for that phase
8 of 17
DFSSp/SSM
Project Title: Project No.:
Phase Requirements* Measure
N/A Used N/A Used
M3
Pilot Production Full Production Customer Usage 7 of 17
M4
DFSS-i
Project Title:
Project No.:
Phase Requirements*
Date Approved_________ Date Approved_________ Date Approved_________ Date Approved_________ Date Approved_________
I
V O I A D M C
D
D
(Product & Process)
Concept Design
M1
Detailed Design Integration & Test
DFSS-p SSM
Six Sigma Methodology