铸件机械粘砂的产生原因及其防止措施【建筑工程类独家文档首发】
铸造工艺中常见铸件缺陷与防治
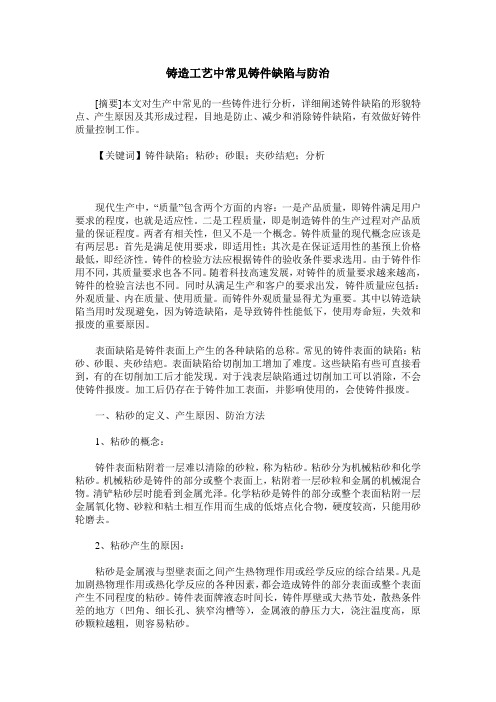
铸造工艺中常见铸件缺陷与防治[摘要]本文对生产中常见的一些铸件进行分析,详细阐述铸件缺陷的形貌特点、产生原因及其形成过程,目地是防止、减少和消除铸件缺陷,有效做好铸件质量控制工作。
【关键词】铸件缺陷;粘砂;砂眼;夹砂结疤;分析现代生产中,“质量”包含两个方面的内容:一是产品质量,即铸件满足用户要求的程度,也就是适应性。
二是工程质量,即是制造铸件的生产过程对产品质量的保证程度。
两者有相关性,但又不是一个概念。
铸件质量的现代概念应该是有两层思:首先是满足使用要求,即适用性;其次是在保证适用性的基预上价格最低,即经济性。
铸件的检验方法应根据铸件的验收条件要求选用。
由于铸件作用不同,其质量要求也各不同。
随着科技高速发展,对铸件的质量要求越来越高,铸件的检验言法也不同。
同时从满足生产和客户的要求出发,铸件质量应包括:外观质量、内在质量、使用质量。
而铸件外观质量显得尤为重要。
其中以铸造缺陷当用时发现避免,因为铸造缺陷,是导致铸件性能低下,使用寿命短,失效和报废的重要原因。
表面缺陷是铸件表面上产生的各种缺陷的总称。
常见的铸件表面的缺陷:粘砂、砂眼、夹砂结疤。
表面缺陷给切削加工增加了难度。
这些缺陷有些可直接看到,有的在切削加工后才能发现。
对于浅表层缺陷通过切削加工可以消除,不会使铸件报废。
加工后仍存在于铸件加工表面,并影响使用的,会使铸件报废。
一、粘砂的定义、产生原因、防治方法1、粘砂的概念:铸件表面粘附着一层难以清除的砂粒,称为粘砂。
粘砂分为机械粘砂和化学粘砂。
机械粘砂是铸件的部分或整个表面上,粘附着一层砂粒和金属的机械混合物。
清铲粘砂层时能看到金属光泽。
化学粘砂是铸件的部分或整个表面粘附一层金属氧化物、砂粒和粘土相互作用而生成的低熔点化合物,硬度较高,只能用砂轮磨去。
2、粘砂产生的原因:粘砂是金属液与型壁表面之间产生热物理作用或经学反应的综合结果。
凡是加剧热物理作用或热化学反应的各种因素,都会造成铸件的部分表面或整个表面产生不同程度的粘砂。
铸件常见缺陷的产生原因及防止方法
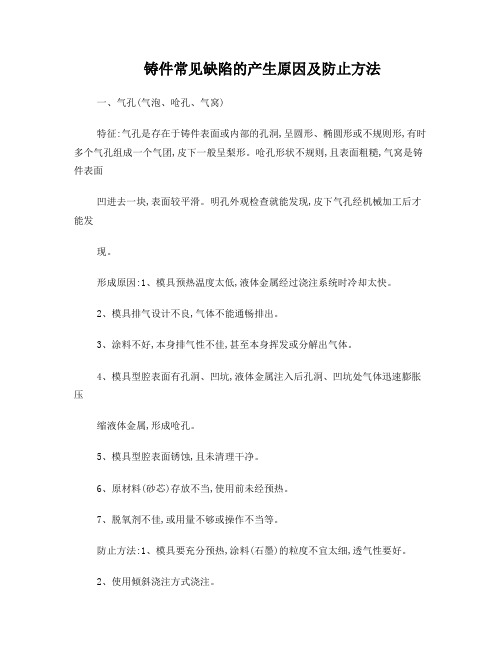
铸件常见缺陷的产生原因及防止方法一、气孔(气泡、呛孔、气窝)特征:气孔是存在于铸件表面或内部的孔洞,呈圆形、椭圆形或不规则形,有时多个气孔组成一个气团,皮下一般呈梨形。
呛孔形状不规则,且表面粗糙,气窝是铸件表面凹进去一块,表面较平滑。
明孔外观检查就能发现,皮下气孔经机械加工后才能发现。
形成原因:1、模具预热温度太低,液体金属经过浇注系统时冷却太快。
2、模具排气设计不良,气体不能通畅排出。
3、涂料不好,本身排气性不佳,甚至本身挥发或分解出气体。
4、模具型腔表面有孔洞、凹坑,液体金属注入后孔洞、凹坑处气体迅速膨胀压缩液体金属,形成呛孔。
5、模具型腔表面锈蚀,且未清理干净。
6、原材料(砂芯)存放不当,使用前未经预热。
7、脱氧剂不佳,或用量不够或操作不当等。
防止方法:1、模具要充分预热,涂料(石墨)的粒度不宜太细,透气性要好。
2、使用倾斜浇注方式浇注。
3、原材料应存放在通风干燥处,使用时要预热。
4、选择脱氧效果较好的脱氧剂(镁)。
5、浇注温度不宜过高。
二、缩孔(缩松)特征:缩孔是铸件表面或内部存在的一种表面粗糙的孔,轻微缩孔是许多分散的小缩孔,即缩松,缩孔或缩松处晶粒粗大。
常发生在铸件内浇道附近、冒口根部、厚大部位,壁的厚薄转接处及具有大平面的厚薄处。
形成原因:1、模具工作温度控制未达到定向凝固要求。
2、涂料选择不当,不同部位涂料层厚度控制不好。
3、铸件在模具中的位置设计不当。
4、浇冒口设计未能达到起充分补缩的作用。
5、浇注温度过低或过高。
防治方法:1、提高磨具温度。
2、调整涂料层厚度,涂料喷洒要均匀,涂料脱落而补涂时不可形成局部涂料堆积现象。
3、对模具进行局部加热或用绝热材料局部保温。
4、热节处镶铜块,对局部进行激冷。
5、模具上设计散热片,或通过水等加速局部地区冷却速度,或在模具外喷水,喷雾。
6、用可拆缷激冷块,轮流安放在型腔内,避免连续生产时激冷块本身冷却不充分。
7、模具冒口上设计加压装置。
8、浇注系统设计要准确,选择适宜的浇注温度。
呋喃树脂砂铸钢件的粘砂机理及预防措施研究
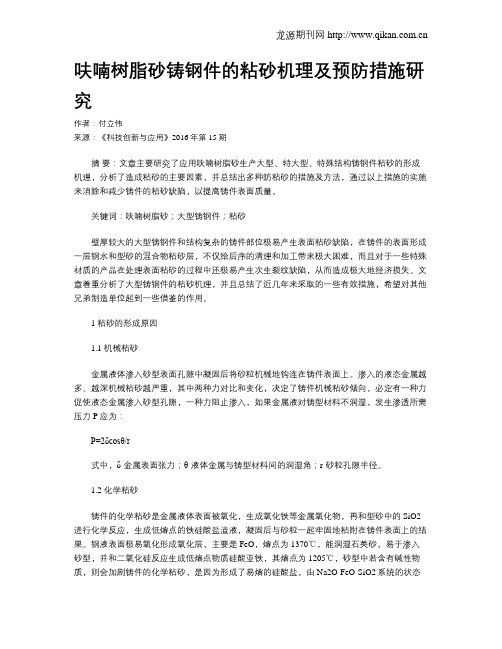
呋喃树脂砂铸钢件的粘砂机理及预防措施研究作者:付立伟来源:《科技创新与应用》2016年第15期摘要:文章主要研究了应用呋喃树脂砂生产大型、特大型、特殊结构铸钢件粘砂的形成机理,分析了造成粘砂的主要因素,并总结出多种防粘砂的措施及方法,通过以上措施的实施来消除和减少铸件的粘砂缺陷,以提高铸件表面质量。
关键词:呋喃树脂砂;大型铸钢件;粘砂壁厚较大的大型铸钢件和结构复杂的铸件部位极易产生表面粘砂缺陷,在铸件的表面形成一层钢水和型砂的混合物粘砂层,不仅给后序的清理和加工带来极大困难,而且对于一些特殊材质的产品在处理表面粘砂的过程中还极易产生次生裂纹缺陷,从而造成极大地经济损失。
文章着重分析了大型铸钢件的粘砂机理,并且总结了近几年来采取的一些有效措施,希望对其他兄弟制造单位起到一些借鉴的作用。
1 粘砂的形成原因1.1 机械粘砂金属液体渗入砂型表面孔隙中凝固后将砂粒机械地钩连在铸件表面上。
渗入的液态金属越多、越深机械粘砂越严重,其中两种力对比和变化,决定了铸件机械粘砂倾向,必定有一种力促使液态金属渗入砂型孔隙,一种力阻止渗入,如果金属液对铸型材料不润湿,发生渗透所需压力P应为:P=2δcosθ/r式中,δ-金属表面张力;θ-液体金属与铸型材料间的润湿角;r-砂粒孔隙半径。
1.2 化学粘砂铸件的化学粘砂是金属液体表面被氧化,生成氧化铁等金属氧化物,再和型砂中的SiO2进行化学反应,生成低熔点的铁硅酸盐渣液,凝固后与砂粒一起牢固地粘附在铸件表面上的结果。
钢液表面极易氧化形成氧化层,主要是FeO,熔点为1370℃,能润湿石英砂,易于渗入砂型,并和二氧化硅反应生成低熔点物质硅酸亚铁,其熔点为1205℃,砂型中若含有碱性物质,则会加剧铸件的化学粘砂,是因为形成了易熔的硅酸盐,由Na2O-FeO-SiO2系统的状态图可知其中熔点最低的可低于500℃。
低熔点物生成后,由于流动性好又能润湿型壁故易于渗入砂型孔隙内,扩大氧化铁和型砂的作用面积,加剧化学粘砂,化学反应的结果又扩大了砂粒间孔隙更有利于低熔点物质向砂型深处渗入,从而将金属和砂型联成一体。
铸钢件常见铸造缺陷及预防措施
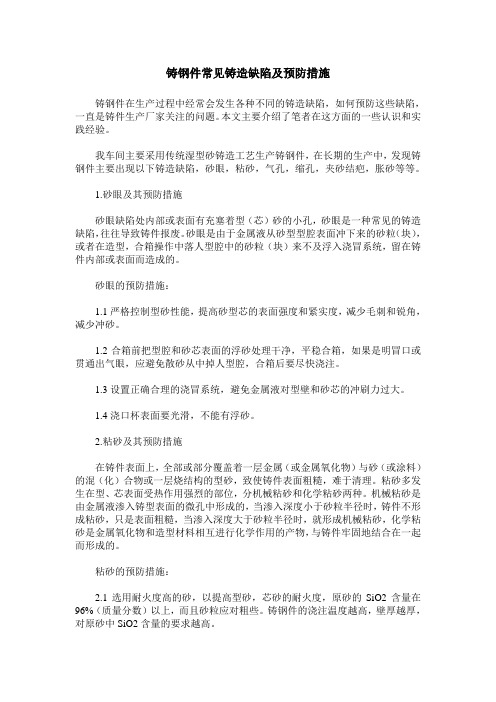
铸钢件常见铸造缺陷及预防措施铸钢件在生产过程中经常会发生各种不同的铸造缺陷,如何预防这些缺陷,一直是铸件生产厂家关注的问题。
本文主要介绍了笔者在这方面的一些认识和实践经验。
我车间主要采用传统湿型砂铸造工艺生产铸钢件,在长期的生产中,发现铸钢件主要出现以下铸造缺陷,砂眼,粘砂,气孔,缩孔,夹砂结疤,胀砂等等。
1.砂眼及其预防措施砂眼缺陷处内部或表面有充塞着型(芯)砂的小孔,砂眼是一种常见的铸造缺陷,往往导致铸件报废。
砂眼是由于金属液从砂型型腔表面冲下来的砂粒(块),或者在造型,合箱操作中落人型腔中的砂粒(块)来不及浮入浇冒系统,留在铸件内部或表面而造成的。
砂眼的预防措施:1.1严格控制型砂性能,提高砂型芯的表面强度和紧实度,减少毛刺和锐角,减少冲砂。
1.2合箱前把型腔和砂芯表面的浮砂处理干净,平稳合箱,如果是明冒口或贯通出气眼,应避免散砂从中掉人型腔,合箱后要尽快浇注。
1.3设置正确合理的浇冒系统,避免金属液对型壁和砂芯的冲刷力过大。
1.4浇口杯表面要光滑,不能有浮砂。
2.粘砂及其预防措施在铸件表面上,全部或部分覆盖着一层金属(或金属氧化物)与砂(或涂料)的混(化)合物或一层烧结构的型砂,致使铸件表面粗糙,难于清理。
粘砂多发生在型、芯表面受热作用强烈的部位,分机械粘砂和化学粘砂两种。
机械粘砂是由金属液渗入铸型表面的微孔中形成的,当渗入深度小于砂粒半径时,铸件不形成粘砂,只是表面粗糙,当渗入深度大于砂粒半径时,就形成机械粘砂,化学粘砂是金属氧化物和造型材料相互进行化学作用的产物,与铸件牢固地结合在一起而形成的。
粘砂的预防措施:2.1选用耐火度高的砂,以提高型砂,芯砂的耐火度,原砂的SiO2含量在96%(质量分数)以上,而且砂粒应对粗些。
铸钢件的浇注温度越高,壁厚越厚,对原砂中SiO2含量的要求越高。
2.2适当降低浇注温度和提高浇注速度,减轻金属液对砂型的热力学和物理化学作用。
2.3砂型紧实度要高(通常大于85)且均匀,减少砂粒间隙;型、芯修补到位,不能有局部疏松。
V法造型防止铸件粘砂的对策
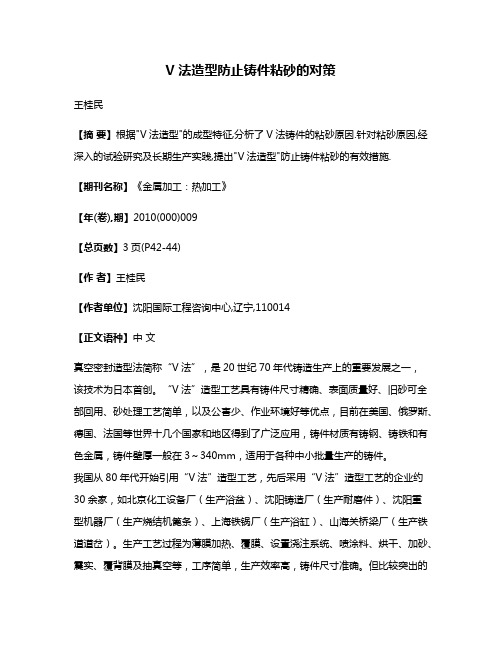
V法造型防止铸件粘砂的对策王桂民【摘要】根据"V法造型"的成型特征,分析了V法铸件的粘砂原因.针对粘砂原因,经深入的试验研究及长期生产实践,提出"V法造型"防止铸件粘砂的有效措施.【期刊名称】《金属加工:热加工》【年(卷),期】2010(000)009【总页数】3页(P42-44)【作者】王桂民【作者单位】沈阳国际工程咨询中心,辽宁,110014【正文语种】中文真空密封造型法简称“V法”,是20世纪70年代铸造生产上的重要发展之一,该技术为日本首创。
“V法”造型工艺具有铸件尺寸精确、表面质量好、旧砂可全部回用、砂处理工艺简单,以及公害少、作业环境好等优点,目前在美国、俄罗斯、德国、法国等世界十几个国家和地区得到了广泛应用,铸件材质有铸钢、铸铁和有色金属,铸件壁厚一般在3~340mm,适用于各种中小批量生产的铸件。
我国从80年代开始引用“V法”造型工艺,先后采用“V法”造型工艺的企业约30余家,如北京化工设备厂(生产浴盆)、沈阳铸造厂(生产耐磨件)、沈阳重型机器厂(生产烧结机篦条)、上海铁锅厂(生产浴缸)、山海关桥梁厂(生产铁道道岔)。
生产工艺过程为薄膜加热、覆膜、设置浇注系统、喷涂料、烘干、加砂、震实、覆背膜及抽真空等,工序简单,生产效率高,铸件尺寸准确。
但比较突出的问题是“V法”造型如果控制不好铸件极易产生粘砂,其特征是呈大面积均匀的片状,或出现在型腔面膜受损贴补处,虽然大部分粘砂经强力抛丸可清除,但会破坏铸件表面粗糙度,影响铸件的表面质量。
针对铸件粘砂问题,我们从“V法”造型的工艺特点入手,经过认真的研究分析和生产实践认为:①除了与有关铸件粘砂的共性因素有关外,还与V法铸造成型方法有关。
②出现的基本为机械粘砂。
③控制原砂的成分、粒度及其级配,使用V法专用涂料能有效地防止粘砂。
V法造型是利用抽真空形成的压力差使密封在砂箱内的单一干砂紧实成型,型砂中不加任何粘结剂和附加物,大大减少了型砂混制成本及设备投入,并且可消除水、粘结剂及附加物所引起的铸造缺陷,但同时也为机械粘砂创造了条件:铸型中缺乏防止粘砂的气氛,型砂润湿角小,砂粒之间呈点接触,透气性增加,加之抽真空,几乎不存在铸型背压,形成铁液向型砂渗透的条件。
铸件机械粘砂的产生原因及其防止措施【建筑工程类独家文档首发】
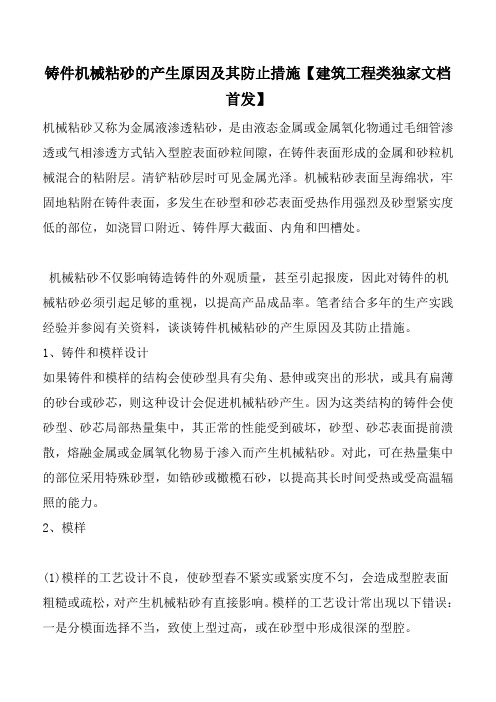
铸件机械粘砂的产生原因及其防止措施【建筑工程类独家文档首发】机械粘砂又称为金属液渗透粘砂,是由液态金属或金属氧化物通过毛细管渗透或气相渗透方式钻入型腔表面砂粒间隙,在铸件表面形成的金属和砂粒机械混合的粘附层。
清铲粘砂层时可见金属光泽。
机械粘砂表面呈海绵状,牢固地粘附在铸件表面,多发生在砂型和砂芯表面受热作用强烈及砂型紧实度低的部位,如浇冒口附近、铸件厚大截面、内角和凹槽处。
机械粘砂不仅影响铸造铸件的外观质量,甚至引起报废,因此对铸件的机械粘砂必须引起足够的重视,以提高产品成品率。
笔者结合多年的生产实践经验并参阅有关资料,谈谈铸件机械粘砂的产生原因及其防止措施。
1、铸件和模样设计如果铸件和模样的结构会使砂型具有尖角、悬伸或突出的形状,或具有扁薄的砂台或砂芯,则这种设计会促进机械粘砂产生。
因为这类结构的铸件会使砂型、砂芯局部热量集中,其正常的性能受到破坏,砂型、砂芯表面提前溃散,熔融金属或金属氧化物易于渗入而产生机械粘砂。
对此,可在热量集中的部位采用特殊砂型,如锆砂或橄榄石砂,以提高其长时间受热或受高温辐照的能力。
2、模样(1)模样的工艺设计不良,使砂型舂不紧实或紧实度不匀,会造成型腔表面粗糙或疏松,对产生机械粘砂有直接影响。
模样的工艺设计常出现以下错误:一是分模面选择不当,致使上型过高,或在砂型中形成很深的型腔。
二是模样在模底板上的位置布置不当,使凹陷处难于舂实,这可能是由于模样距箱壁太近,或模样排列过密所致。
由于模样排列过于拥挤,会引起铸件产生胀砂,即使没有明显的胀砂,也会发生机械粘砂。
由于产生缺陷的根源相同,机械粘砂和胀砂会出现在同一个铸件上。
三是直浇道、冒口和横浇道的位置布置不当,会出现不易舂实的凹陷部位,这与浇冒口系统的布局有关。
四是起模斜度<1.5°时,即使整个砂型的紧实度合适,也会使砂型表面撕裂,易于使金属或金属氧化物渗入。
(2)模样的工艺结构不良,导致金属液静压力过高。
熔模铸件缺陷分析--粘砂

熔模铸件缺陷分析--粘砂熔模铸件常见缺陷分析及处理——表面缺陷类之一化学粘砂与机械粘砂潘玉洪摘要:机械粘砂和化学粘砂是熔模铸件常见的铸造缺陷之一,它是指在铸件的表面上牢固地粘结着一层金属与型壳材料结合物。
本文重点阐述熔模铸件化学粘砂和机械粘砂的外部特征,产生的部位、机理以及主要原因,同时提出了从熔模铸造的选材、制壳工艺、焙烧工艺、熔炼工艺等方面采取实用、有效的对策,从而提高熔模铸件的合格率。
关键词:熔模铸件;粘砂缺陷;分析与处理1.引言在熔模铸造生产中,当灼热的金属液浇入型壳中,金属液与型腔表面就发生极为复杂的、物理的和化学的相互作用,往往导致铸件产生各种类型的铸造缺陷,机械粘砂和化学粘砂就是其中之一。
如果铸件局部产生粘砂,还不至于使铸件报废;但它影响了铸件的外观,增加了清理铸件的工时和劳动量;尤其对于需要机械加工的铸件,粘砂会给切削加工带来很多的麻烦,提高了生产成本,甚至影响正常的生产进度和交货期。
所以,熔模铸造工作者必须在生产中尽量减少,甚至消除铸件的机械粘砂和化学粘砂缺陷。
目前,国内外一些资料把粘砂分为两种、三种或四种,作者认为分为化学粘砂和机械粘砂两种比较合适。
2.化学粘砂2.1概述2.1.1特征金属液在高温下与型腔表面发生相互作用,冷凝后在铸件的表面上牢固地粘结一层难以清除的金属液与型壳材料之间化学反应生成粘砂。
如图1:图1 化学粘砂左A-化学粘砂右-正常2.1.2 部位常常产生在大型铸件、铸件的厚大部位,铸件浇注部位的下端,靠近内浇口或冒口等部位。
2.1.3 机理按照化学粘砂产生的主要原因,把化学粘砂的形成过程分为三种情况,如图2:图2 化学粘砂形成过程的示意图A型:a—金属液浇入型腔中;b—金属液被型砂中的空气或水分氧化,生成低熔点的、与石英砂浸润能力很强的氧化铁:2Fe +O2=2FeO(液、固)(气)(液、固)c—氧化铁与石英砂(粉)作用:2FeO+SiO2=2FeO ·SiO2生成液态的铁硅酸盐(也称铁橄榄石),因为其熔点低(为1205℃)、流动性好、浸润能力强,所以渗入型砂孔隙中的能力增强;d——铁硅酸盐渗入型砂的孔隙中,与石英砂化合而成粘砂。
铸件机械粘砂的产生原因及其防止措施【建筑工程类独家文档首发】
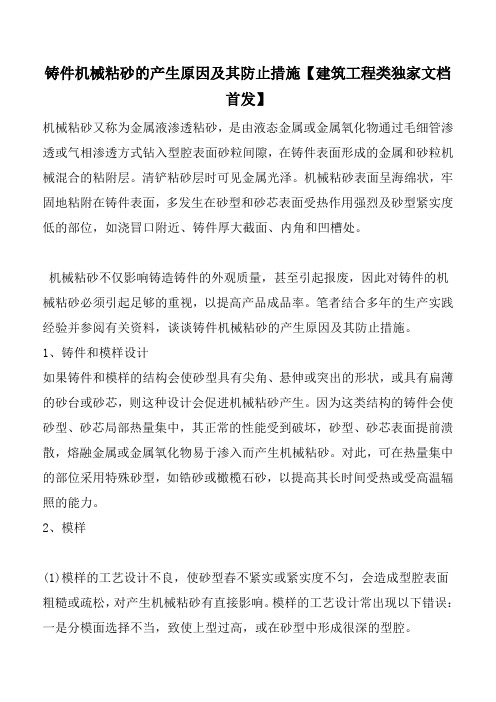
铸件机械粘砂的产生原因及其防止措施【建筑工程类独家文档首发】机械粘砂又称为金属液渗透粘砂,是由液态金属或金属氧化物通过毛细管渗透或气相渗透方式钻入型腔表面砂粒间隙,在铸件表面形成的金属和砂粒机械混合的粘附层。
清铲粘砂层时可见金属光泽。
机械粘砂表面呈海绵状,牢固地粘附在铸件表面,多发生在砂型和砂芯表面受热作用强烈及砂型紧实度低的部位,如浇冒口附近、铸件厚大截面、内角和凹槽处。
机械粘砂不仅影响铸造铸件的外观质量,甚至引起报废,因此对铸件的机械粘砂必须引起足够的重视,以提高产品成品率。
笔者结合多年的生产实践经验并参阅有关资料,谈谈铸件机械粘砂的产生原因及其防止措施。
1、铸件和模样设计如果铸件和模样的结构会使砂型具有尖角、悬伸或突出的形状,或具有扁薄的砂台或砂芯,则这种设计会促进机械粘砂产生。
因为这类结构的铸件会使砂型、砂芯局部热量集中,其正常的性能受到破坏,砂型、砂芯表面提前溃散,熔融金属或金属氧化物易于渗入而产生机械粘砂。
对此,可在热量集中的部位采用特殊砂型,如锆砂或橄榄石砂,以提高其长时间受热或受高温辐照的能力。
2、模样(1)模样的工艺设计不良,使砂型舂不紧实或紧实度不匀,会造成型腔表面粗糙或疏松,对产生机械粘砂有直接影响。
模样的工艺设计常出现以下错误:一是分模面选择不当,致使上型过高,或在砂型中形成很深的型腔。
二是模样在模底板上的位置布置不当,使凹陷处难于舂实,这可能是由于模样距箱壁太近,或模样排列过密所致。
由于模样排列过于拥挤,会引起铸件产生胀砂,即使没有明显的胀砂,也会发生机械粘砂。
由于产生缺陷的根源相同,机械粘砂和胀砂会出现在同一个铸件上。
三是直浇道、冒口和横浇道的位置布置不当,会出现不易舂实的凹陷部位,这与浇冒口系统的布局有关。
四是起模斜度<1.5°时,即使整个砂型的紧实度合适,也会使砂型表面撕裂,易于使金属或金属氧化物渗入。
(2)模样的工艺结构不良,导致金属液静压力过高。
必收藏之壳体粘砂篇,针对铸件粘砂的关键原因,提出7项改进措施
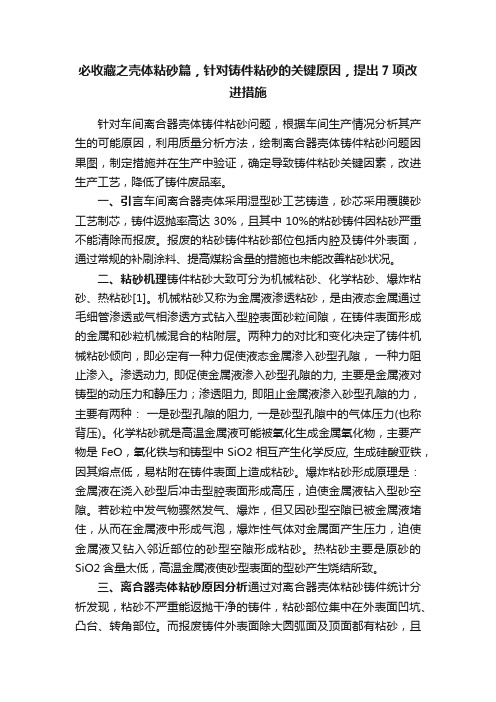
必收藏之壳体粘砂篇,针对铸件粘砂的关键原因,提出7项改进措施针对车间离合器壳体铸件粘砂问题,根据车间生产情况分析其产生的可能原因,利用质量分析方法,绘制离合器壳体铸件粘砂问题因果图,制定措施并在生产中验证,确定导致铸件粘砂关键因素,改进生产工艺,降低了铸件废品率。
一、引言车间离合器壳体采用湿型砂工艺铸造,砂芯采用覆膜砂工艺制芯,铸件返抛率高达30%,且其中10%的粘砂铸件因粘砂严重不能清除而报废。
报废的粘砂铸件粘砂部位包括内腔及铸件外表面,通过常规的补刷涂料、提高煤粉含量的措施也未能改善粘砂状况。
二、粘砂机理铸件粘砂大致可分为机械粘砂、化学粘砂、爆炸粘砂、热粘砂[1]。
机械粘砂又称为金属液渗透粘砂,是由液态金属通过毛细管渗透或气相渗透方式钻入型腔表面砂粒间隙,在铸件表面形成的金属和砂粒机械混合的粘附层。
两种力的对比和变化决定了铸件机械粘砂倾向,即必定有一种力促使液态金属渗入砂型孔隙,一种力阻止渗入。
渗透动力, 即促使金属液渗入砂型孔隙的力, 主要是金属液对铸型的动压力和静压力;渗透阻力, 即阻止金属液渗入砂型孔隙的力,主要有两种:一是砂型孔隙的阻力, 一是砂型孔隙中的气体压力(也称背压)。
化学粘砂就是高温金属液可能被氧化生成金属氧化物,主要产物是FeO,氧化铁与和铸型中SiO2相互产生化学反应, 生成硅酸亚铁,因其熔点低,易粘附在铸件表面上造成粘砂。
爆炸粘砂形成原理是:金属液在浇入砂型后冲击型腔表面形成高压,迫使金属液钻入型砂空隙。
若砂粒中发气物骤然发气、爆炸,但又因砂型空隙已被金属液堵住,从而在金属液中形成气泡,爆炸性气体对金属面产生压力,迫使金属液又钻入邻近部位的砂型空隙形成粘砂。
热粘砂主要是原砂的SiO2含量太低,高温金属液使砂型表面的型砂产生烧结所致。
三、离合器壳体粘砂原因分析通过对离合器壳体粘砂铸件统计分析发现,粘砂不严重能返抛干净的铸件,粘砂部位集中在外表面凹坑、凸台、转角部位。
而报废铸件外表面除大圆弧面及顶面都有粘砂,且内腔除砂芯刷涂部位都有粘砂(如图1、2所示),且粘砂密集、粘砂层厚。
消失模铸造工艺防止粘砂的措施

消失模铸造工艺防止粘砂的措施贾国芳1,李增民2,谭建波2摘要:粘砂是消失模铸件常见的铸造缺陷,造成粘砂的工艺因素多种多样。
防止铸件粘砂应从多方面着手,综合分析生产过程各工艺环节,抓住主要影响因素,理顺操作规范和工艺参数,有针对地采取防治措施才能收到良好效果。
本文结合消失模铸造铁套件产生粘砂部位和粘砂的形式,从多角度分析造成铸件粘砂的原因,提出防止措施和生产中的注意事项。
关键词:消失模铸造;铁套;防粘砂措施1 铁套的结构特点和易产生粘砂的形式铁套和钢背铜套装配后构成轴瓦,是车辆上重要的承载和传动部件。
铁套为回转体结构,有筒体和法兰组成,筒体上有储油凹槽和过油孔,其材质HT250,要求HB190~220。
铁套单重一般小于10kg,平均壁厚约25mm,最大轮廓尺寸不超过200mm,因而可以用“厚壁小件、结构紧凑”来形容铁套的结构特点。
采用消失模工艺铸造铁套,能够将油槽、油孔直接铸出,最大限度地减小加工余量,节省加工工时和成本。
为了提高铸造生产效率,充分利用砂箱容积,消失模工艺通常采用组树串铸方案以实现一箱多铸,但存在的突出问题是粘砂缺陷。
垂直串铸时粘砂部出现在下层铸件内浇口周围,往往是铁套法兰下面凹槽处、法兰与筒体拐角处及筒体内部。
粘砂层较厚,粘砂形式以机械粘砂为主,抛丸清理无法去处。
铁套粘砂情况如图所示。
2 造成粘砂的工艺因素分析粘砂是金属液渗入到涂层和型砂中形成的机械混合物,消失模工艺生产铁套造成粘砂的原因一般是多方面的:(1)涂层太薄不足以抵抗金属液的浸蚀和冲刷而形成机械粘砂;(2)涂层耐火度不够,涂料被高温金属液熔合而形成化学粘砂;(3)造型时型砂的紧实度不足,填充不满,金属液冲破涂层而机械粘砂;(4)内浇口引入位置太集中,容易造成局部过热而粘砂;(5)涂层干燥不透强度低、发气量大,被金属液冲蚀而粘砂;(6)浇注温度太高,浇注速度慢,铁水对局部(内角口周围)冲刷过热时间长;(7)原材料锈蚀和杂质多、铁水高温熔化时间长等原因,造成铁水氧化严重,容易和涂层和型砂反应,形成低熔点化合物,降低了涂料的耐火度而造成粘砂。
V法铸造铸件粘砂成因及对策

V 法铸造铸件粘砂成因及对策合肥铸锻厂(安徽省合肥市230022) 崔明胜 吴友坤 单宝华 方世良摘 要 根据铸件粘砂机理,从V 法铸造的成型特征的角度分析了V 法铸件的粘砂的原因。
经长期生产实践的探索,总结出V 法铸件防止粘砂的有效措施。
关键词:V 法铸造 机械粘砂 防止措施R eason and Prevention Measures of Metal Penetration in V 2processCui Mingsheng Wu Y oukun Shan Baohua Fang Shiliang(Hefei Casting and Forging Factory )Abstract According to the mechanism of metal penetration and the technological process of vacuum sealed mould 2ing casting process.The reason of metal penetration is found out after long period of productive practic.K ey w ords :V 2process Metal penetration Prevention measure V 法铸造具有设备投资少、简化工序、生产效率高、铸件尺寸准确、表面粗糙度低等优点。
我厂应用V 法铸造技术生产叉车、挖掘机等工程机械平衡重类铸件已有七年的历史,年产量达8000余吨,其中1/3出口日本、韩国等国,共有四十多个品种,重量从几十公斤到五吨多,材质均为HT150,做法基本参照日本TCM 公司工艺技术执行。
总体而言,与原表干型铸造相比,铸件质量得到大大提高,但粘砂问题相当严重,尤以3t 叉车以上平衡重(铸件重量大于1800kg ,平均壁厚50mm 以上)为甚,严重粘砂缺陷率曾一度达50%,粘砂特征呈大面积均匀的片状,或出现在型腔面膜受损贴补处,均属机械粘砂。
大型铸钢件粘砂机理及防粘砂措施的研究

分 子式
S i O 2 A l 2 0 3
化学性质
酸 性 中性
密度( g / C m )
2 . 6 5 3 . 8 - 3 . 9
熔点 ( )
1 7 1 3 2 0 0 0 ~ 2 5 0 0
烧结温度( ℃) 在F e O作用下 的烧结温度( ℃)
中性 碱性 中性
中性 碱性
4  ̄ 4 . 8 3 _ 3 5 ~ 3 . 5 8 2 - 2 5
> 1 9 0 0 > 2 0 0 0 3 0 0 0
≈2 l O O
2 . 7
8 o o ~ 1 3 5 0
8 0 0 - 1 3 0 0
注: 表中熔点等部分性能会随其杂质含量 的多少而改变。
除 了型砂 本身 的原 因 以外 ,钢 液 的浇 注温 度对 粘 砂也 起着举 足轻 重 的作用 。作 为用树脂 砂 为粘结 剂 的型砂 ,当钢液 进入 型腔 时 由于高温金 属液 作用 使 树脂 烧结 , 型砂 强度 降低 , 液态金 属渗透 到砂 粒 间 的孔 隙而形 成粘砂 , 并 随着 浇注温 度 的提 高 , 铸 件 的 粘砂倾 向也 增大 。 因此 , 根 据铸件 情况选 择合 适 的浇
生产技术 P r o d u c t i o n T e c h n i q u e s
芯( 如图 1 示) , 这些部 位散 热条 件差 , 持续 长时 间高 温作 用 , 金 属液 容易渗 透砂 型 , 导 致机 械粘砂 。 目前
对 于结构 性粘砂 只有 通过 采取正 确 的特殊 措施来 解 决减 少铸 件 的粘砂情 况 。应使砂粒分布分散 到 3 0 、 4 0 、 5 0 、 7 0四个筛号
铸件粘砂的原因及处理
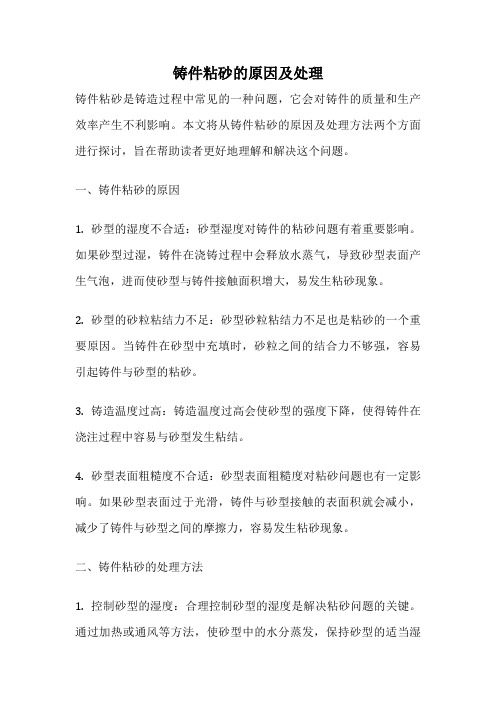
铸件粘砂的原因及处理铸件粘砂是铸造过程中常见的一种问题,它会对铸件的质量和生产效率产生不利影响。
本文将从铸件粘砂的原因及处理方法两个方面进行探讨,旨在帮助读者更好地理解和解决这个问题。
一、铸件粘砂的原因1. 砂型的湿度不合适:砂型湿度对铸件的粘砂问题有着重要影响。
如果砂型过湿,铸件在浇铸过程中会释放水蒸气,导致砂型表面产生气泡,进而使砂型与铸件接触面积增大,易发生粘砂现象。
2. 砂型的砂粒粘结力不足:砂型砂粒粘结力不足也是粘砂的一个重要原因。
当铸件在砂型中充填时,砂粒之间的结合力不够强,容易引起铸件与砂型的粘砂。
3. 铸造温度过高:铸造温度过高会使砂型的强度下降,使得铸件在浇注过程中容易与砂型发生粘结。
4. 砂型表面粗糙度不合适:砂型表面粗糙度对粘砂问题也有一定影响。
如果砂型表面过于光滑,铸件与砂型接触的表面积就会减小,减少了铸件与砂型之间的摩擦力,容易发生粘砂现象。
二、铸件粘砂的处理方法1. 控制砂型的湿度:合理控制砂型的湿度是解决粘砂问题的关键。
通过加热或通风等方法,使砂型中的水分蒸发,保持砂型的适当湿度,从而减少粘砂现象的发生。
2. 提高砂型的砂粒粘结力:可以通过调整砂型中的粘结剂含量或改变粘结剂的种类来提高砂型的砂粒粘结力。
同时,加强砂型的压实度和硬度也可以有效减少粘砂问题。
3. 控制铸造温度:合理控制铸造温度可以有效降低粘砂现象的发生。
通过调整浇注温度和浇注速度等参数,使铸造温度保持在适当范围内,减少铸件与砂型的粘结。
4. 改善砂型表面粗糙度:改善砂型表面粗糙度可以减少铸件与砂型之间的粘附力,降低粘砂的发生概率。
可以通过调整砂型颗粒的大小、表面涂覆剂的种类和涂覆剂的涂布量等方式来改善砂型表面的粗糙度。
5. 使用防粘剂:在砂型中添加适量的防粘剂可以有效地减少粘砂问题的发生。
防粘剂可以形成一层保护膜,减少铸件与砂型之间的接触面积,从而降低粘砂的概率。
铸件粘砂问题是铸造过程中常见的一个难题,但通过合理控制砂型湿度、提高砂型的砂粒粘结力、控制铸造温度、改善砂型表面粗糙度和使用防粘剂等方法,可以有效地解决这个问题。
铸件的常见不良现象及对策
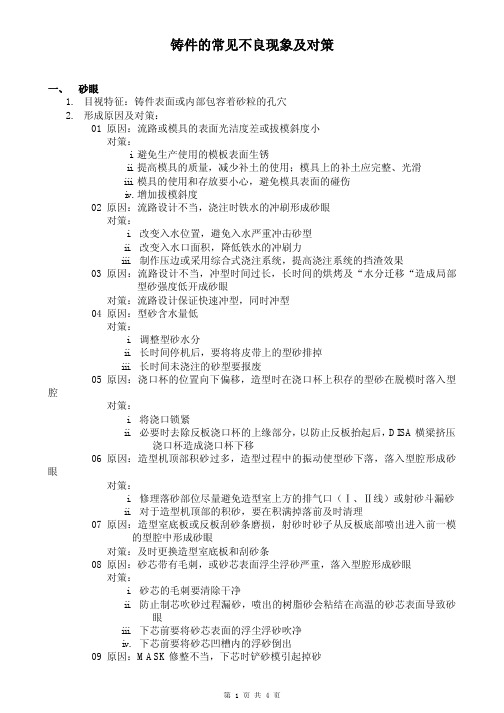
一、砂眼1.目视特征:铸件表面或内部包容着砂粒的孔穴2.形成原因及对策:01 原因:流路或模具的表面光洁度差或拔模斜度小对策:i.避免生产使用的模板表面生锈ii.提高模具的质量,减少补土的使用;模具上的补土应完整、光滑iii.模具的使用和存放要小心,避免模具表面的碰伤iv.增加拔模斜度02 原因:流路设计不当,浇注时铁水的冲刷形成砂眼对策:i.改变入水位置,避免入水严重冲击砂型ii.改变入水口面积,降低铁水的冲刷力iii.制作压边或采用综合式浇注系统,提高浇注系统的挡渣效果03 原因:流路设计不当,冲型时间过长,长时间的烘烤及“水分迁移“造成局部型砂强度低开成砂眼对策:流路设计保证快速冲型,同时冲型04 原因:型砂含水量低对策:i.调整型砂水分ii.长时间停机后,要将将皮带上的型砂排掉iii.长时间未浇注的砂型要报废05 原因:浇口杯的位置向下偏移,造型时在浇口杯上积存的型砂在脱模时落入型腔对策:i.将浇口锁紧ii.必要时去除反板浇口杯的上缘部分,以防止反板抬起后,DISA横梁挤压浇口杯造成浇口杯下移06 原因:造型机顶部积砂过多,造型过程中的振动使型砂下落,落入型腔形成砂眼对策:i.修理落砂部位尽量避免造型室上方的排气口(Ⅰ、Ⅱ线)或射砂斗漏砂ii.对于造型机顶部的积砂,要在积满掉落前及时清理07 原因:造型室底板或反板刮砂条磨损,射砂时砂子从反板底部喷出进入前一模的型腔中形成砂眼对策:及时更换造型室底板和刮砂条08 原因:砂芯带有毛刺,或砂芯表面浮尘浮砂严重,落入型腔形成砂眼对策:i.砂芯的毛刺要清除干净ii.防止制芯吹砂过程漏砂,喷出的树脂砂会粘结在高温的砂芯表面导致砂眼iii.下芯前要将砂芯表面的浮尘浮砂吹净iv.下芯前要将砂芯凹槽内的浮砂倒出09 原因:MASK修整不当,下芯时铲砂模引起掉砂对策:修整MASK或模具消除下芯铲砂现象10 原因:型腔位置偏上时,压型器将砂型压裂,掉砂形成砂眼对策:造型时注意排版状况,适当调整压型器位置11 原因:夹板或底板挂职铁将型腔挤裂造成砂眼对策:生产中及时清模二、气孔A、侵入性气孔1、目视特征01形状:气孔尺寸一般较大,呈圆球形、团球形或梨形;梨形的小头指向外部气源方向02孔壁面貌:孔壁平滑——侵入气体成分主要为CO时孔壁呈蓝色,侵入气体成分主要为氢气时孔壁呈金属本色且发亮,侵入气体成分主要为水蒸气时孔壁呈氧化色且发暗。
消失模铸件易出现的缺陷及消除措施

消失模铸件易出现的缺陷及消除措施―钢铁研究院试验中心建钢1、粘砂金属液渗入型砂中,形成金属与型砂的机械混合物,其中有两种情况:一种是金属液通过涂层开裂处渗入型砂中,形成铁包砂(即机械粘砂),此种缺陷一般可以清除掉;另一种情况是金属透过涂层渗入型砂中,形成难以清除的化学粘砂。
(一)产生的原因(1)在涂层开裂的情况下,由于型砂紧实度不够,型砂颗粒过大及真空度过高产生第一种粘砂情况;(2)在涂层过薄或局部未刷到的情况下,由于金属液温度较高,真空度较大时产生第二种粘砂。
(二)防止措施(1)提高涂层的厚度和耐火度。
(2)造型时紧实力不宜过大以免破坏涂层。
(3)选择合适的负压。
(4)选用较细的原砂。
(5)浇注温度不宜过高。
(6)选择合适的压力头。
2、气孔(一)气孔的分类(1)浇注时卷入空气形成的气孔。
(2)泡沫塑料模样分解产生的气孔。
(3)模样涂层不干引起的气孔。
(4)金属液脱氧不好引起的气孔。
(二)浇注时卷入空气形成的气孔消失模铸造浇注过程中如果直浇道不能充满就会卷入空气,这些气体若不能及时排出,就有产生气孔缺陷的可能。
防止卷入气体的措施:(1)采用封闭式的浇注系统。
(2)浇注时维持浇口盆有一定的液体金属以保持直浇道处于充满状态。
(3)正确掌握浇注方法,采用慢—快—慢的浇注方法。
(三)泡沫塑料模样分解产生的气孔EPS和STMMA热解后产生大量的气体,如果充型平稳,金属与模样逐层置换,这些气体就会顺利通过液体前沿与模样间的气隙经铸型排出,特别在铸型处于负压状态下更有利气体排放,铸件不易产生气孔缺陷。
但是如果充型过程产生紊流或者顶注,侧注情况下、部分模样被金属液包围后进行分解产生的气体不能从金属液中排出时就会产生缺陷,这种气孔表面有炭黑存在。
防止措施:(1)改进浇注方案,使充型过程逐层置换,不产生紊流。
(2)提高浇注温度。
(3)在不发生紊流的情况下,适当提高真空度,如果发生紊流而产生气孔时,可适当降低真空度。
铸件掉砂缺陷的成因及防止措施
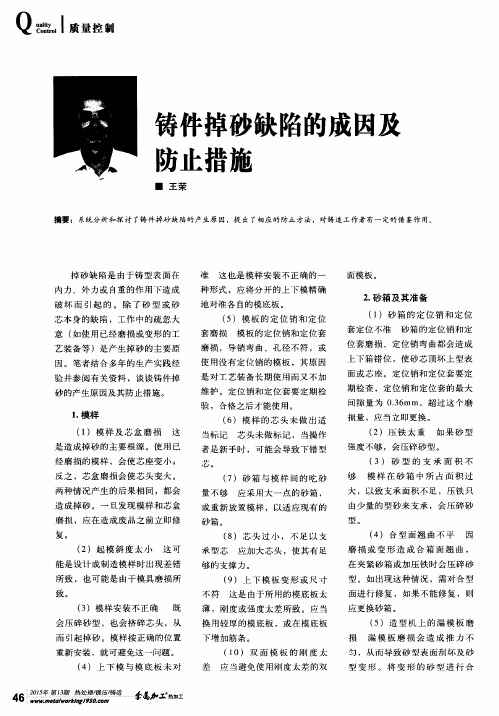
(3) 模样 安 装 不 正 确 既 会 压 碎 砂 型 ,也 会 挤 碎 芯 头 ,从 而 引 起 掉 砂 。模 样 按 正 确 的 位 置 重 新安 装 ,就 可避 免 这 一 问题 。
(4)上 下 模 与 模 底 板 未 对
准 这 也 是 模 样 安 装 不 正 确 的 一 种 形 式 ,应 将 分 开 的 上 下 模 精 确 地 对 准 各 自的模 底板 。
(5)模板 的 定位销 和 定位 套 磨 损 模 板 的 定位 销 和 定 位 套 磨 损 ,导 销 弯 曲 、孔 径 不 符 ,或 使 用 没有 定位 销 的模 板 ,其 原 因 是 对 工 艺 装 备长 期使 用而 又不 加 维 护 。定 位 销 和 定 位 套 要 定期 检 验 ,合格 之 后 才能 使 用 。
(8) 芯 头 过 小 , 不 足 以 支 承 型 芯 应加 大 芯头 ,使其 有 足 够 的支 撑 力 。
(9)上 下 模 板 变 形 或 尺 寸 不 符 这 是 由于 所 用 的 模 底板 太 薄 ,刚 度 或 强 度 太 差 所 致 。 应 当 换用较厚的模底板 ,或在模底板 下 增 加筋 条 。
(6)套箱尺 寸不 符 、内部 脏 污 或 扭 曲 这 都 会 对 砂 型 造 成过量的负荷 ,如果砂 型强度不 够 ,会 造 成 掉 砂 ;如果 砂 型强 度 足以承受这种负荷 ,则有可能在 分型 面 上 出现 跑火 。
(7) 浇 注 底 板 不 平 、脏 污 或 烧 损 会 使 砂 型 底 部 受 压 不 均 ,顶 碎 下 型 而 造 成掉 砂 。底 板 应在平 台上进行校验 ,将其清理 修整好 ,或视情况予以更换。
- 1、下载文档前请自行甄别文档内容的完整性,平台不提供额外的编辑、内容补充、找答案等附加服务。
- 2、"仅部分预览"的文档,不可在线预览部分如存在完整性等问题,可反馈申请退款(可完整预览的文档不适用该条件!)。
- 3、如文档侵犯您的权益,请联系客服反馈,我们会尽快为您处理(人工客服工作时间:9:00-18:30)。
铸件机械粘砂的产生原因及其防止措施【建筑工程类独家文档
首发】
机械粘砂又称为金属液渗透粘砂,是由液态金属或金属氧化物通过毛细管渗透或气相渗透方式钻入型腔表面砂粒间隙,在铸件表面形成的金属和砂粒机械混合的粘附层。
清铲粘砂层时可见金属光泽。
机械粘砂表面呈海绵状,牢
固地粘附在铸件表面,多发生在砂型和砂芯表面受热作用强烈及砂型紧实度
低的部位,如浇冒口附近、铸件厚大截面、内角和凹槽处。
机械粘砂不仅影响铸造铸件的外观质量,甚至引起报废,因此对铸件的机
械粘砂必须引起足够的重视,以提高产品成品率。
笔者结合多年的生产实践
经验并参阅有关资料,谈谈铸件机械粘砂的产生原因及其防止措施。
1、铸件和模样设计
如果铸件和模样的结构会使砂型具有尖角、悬伸或突出的形状,或具有扁薄
的砂台或砂芯,则这种设计会促进机械粘砂产生。
因为这类结构的铸件会使
砂型、砂芯局部热量集中,其正常的性能受到破坏,砂型、砂芯表面提前溃散,熔融金属或金属氧化物易于渗入而产生机械粘砂。
对此,可在热量集中
的部位采用特殊砂型,如锆砂或橄榄石砂,以提高其长时间受热或受高温辐
照的能力。
2、模样
(1)模样的工艺设计不良,使砂型舂不紧实或紧实度不匀,会造成型腔表面
粗糙或疏松,对产生机械粘砂有直接影响。
模样的工艺设计常出现以下错误:一是分模面选择不当,致使上型过高,或在砂型中形成很深的型腔。