第4章 表面粗糙度
抛光汇总第4章节-表面粗糙度简介与标注概述

第四节表面粗糙度简介与标注概述一、表面粗糙度的定义:是指加工表面具有的较小间距和微小峰谷的不平度。
其两波峰或两波谷之间的距离(波距)很小(在1mm以下),用肉眼是难以区别的,因此,它属于微观几何形状误差。
表面粗糙度越小,则表面越光滑。
具体指微小峰谷Z高低程度和间距S状况,一般按S分:●S<1㎜为表面粗糙度;●1≤S≤10㎜为波纹度;●S>10㎜为f形状;如右图所示二、表面粗糙度对工件的影响:表面粗糙度一般是由所采用的加工方法和其他因素所形成的,例如加工过程中刀具与零件表面间的摩擦、切屑分离时表面层金属的塑性变形以及工艺系统中的高频振动等。
由于加工方法和工件材料的不同,被加工表面留下痕迹的深浅、疏密、形状和纹理都有差别。
表面粗糙度的大小,对机械零件的使用性能有很大的影响,主要表现在以下几个方面:1)影响零件的耐磨性:表面越粗糙,配合表面间的有效接触面积越小,压强越大,磨损就越快。
2)影响配合的稳定性:对间隙配合来说,表面越粗糙,就越易磨损,使工作过程中间隙逐渐增大;对过盈配合来说,由于装配时将微观凸峰挤平,减小了实际有效过盈,降低了连接强度。
3)影响零件的疲劳强度:粗糙零件的表面存在较大的波谷,它们像尖角缺口和裂纹一样,对应力集中很敏感,从而影响零件的疲劳强度。
4)影响抗腐蚀性:粗糙零件的表面,易使腐蚀性气体或液体通过表面的微观凹谷渗入到金属内层,造成表面腐蚀。
5)影响零件的密封性:粗糙的表面之间无法严密地贴合,气体或液体通过接触面间的缝隙渗漏。
6)影响接触刚度:接触刚度是零件结合面在外力作用下,抵抗接触变形的能力,机器的刚度在很大程度上取决于各零件之间的接触刚度。
7)影响测量精度:零件被测表面和测量工具面的表面粗糙度都会直接影响测量的精度,尤其是在精度测量时。
此外,表面粗糙度对零件的镀涂层、导热性各接触电阻、反射能力和辐射性能、液体和气体流动阻力等也有影响。
三、表面粗糙度评定依据:1.取样长度:取样长度是评定表面粗糙度所规定一段基准线长度。
表面 粗糙度
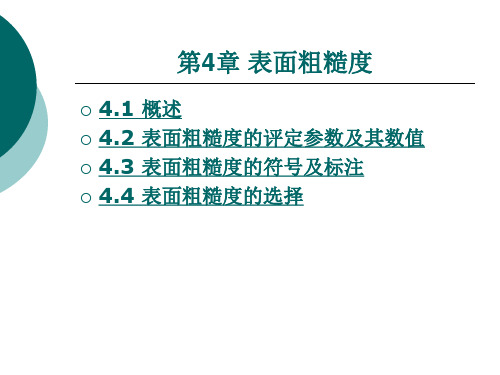
及状态列于引脚列表中,用于显示引脚信息。
4、Mode元件模式区域
主要功能是指定元件的模式,包括 Normal、De-Morgan和IEEE三种模式。
注意:上述元件管理器的功能也可以通过 Tools菜单命令来实现。
二、查找元件
在元件管理器中,单击Find按钮,系统将 弹出如下图所示的查找元件对话框。
表面粗糙度参数及其数值的上限值(下限值)和最大值(最小 值).取样长度等的正确注写
上一页 下一页 返回
表4-6 表面粗糙度代号标注示例(1)
下一页 返回
表4-6 表面粗糙度代号标注示例(2)
上一页 返回
4.3 表面粗糙度的符号及标注
表面粗糙度代号在图样上的标注方法,如表4-7和图4-8所 示,表面粗糙度代号在图样上一般注在可见轮廓线,尺寸界 线,引出线或它们的延长线上;符号的尖端必须从材料外指 向表面;代号中数字及符号的注写方向必须与尺寸数字方向 一致
如下图所示,IEEE工具栏的打开与关闭可 以通过执行菜单命令View→Toolbars→IEEE Toolbars来实现。
IEEE工具栏中各个按钮的功能见下表所示。
此外,元件库编辑器IEEE工具栏中的各项 命令也可以在Place菜单中的IEEE Symbols子菜 单找到。
任务二:手工创建原理图元器件
上一页 下一页 返回
4. 2表面粗糙度的评定参数及其数值
R之出y和现值,较是因深微此加观它 工不不 痕平如 迹度值 ,十经R点z常反中承映最受的高交几点变何和应特最力性低作准点用确至的.中但工线对作的某表垂些面直不,距允如离许 齿廓表面常标注及,参数,此外,当被测表面很小,不宜采 用面R加a工或的评痕定迹时越,深也常采用Ry参数.测得的Ry值越大,表示表
机械制造基础第四章表面粗糙度

※给出Rmr(c)参数时,必须同时给出轮廓水平截距c值。
(2)轮廓的实体材料长度Ml(c)
▲定义:评定长度内,一平行于X轴的直线从峰顶线向下 移一水平截距c时,与轮廓相截所得各段截线长度之和。
n
Ml(c) b1 b2 bi bn bi i 1
■轮廓的水平截距c大小可用微米或用它占轮廓制了长波轮廓成分相 对应的中线,即具有几何轮廓形状并划分轮廓的 基准线,用来评定表面粗糙度参数值的给定线。
轮
轮廓的最小二乘中线
廓
中
线
轮廓的算术平均中线
△以中线为基准线评定轮廓的计算制称为中线制
(1)轮廓的最小二乘中线
▲定义:在取样长度内,使轮廓线上各点轮廓偏距zi的
6、配合性质高的表面、小间隙配合表面、受重载的过 盈配合表面Ra和Rz值要小; 7、配合性质相同,零件尺寸越小,Ra和Rz值越小;同 一精度等级,小尺寸比大尺寸、轴比孔的Ra和Rz参数值 要小; 8、抗腐蚀性、密封性、外观性要求高的表面的Ra和Rz 参数值要小; 9、标准规定的按规定的参数值选用; 10、尺寸公差值和形状公差值小,其Ra和Rz参数值相应 要小,一般情况下,可取Ra为形状公差值的20-25%。
■轮廓支承长度率(Rmr(c))随着轮廓的水平截距c 大小而变化。其关系曲线称为支承长度率曲线。
■支承长度率曲线对于 反映零件表面耐磨性有 着显著的功效。
Rmr(c) % 支承长度率曲线
c%
■ 轮廓峰顶线:在取样长度内,平行于基准线并通过 轮廓最高点的线。
■ 轮廓谷底线:在取样长度内,平行于基准线并通过 轮廓最低点的线。
规定取样长度是为了限制减弱宏观几何误差,尤其是表面波 纹度对测量结果的影响,表面越粗糙,取样长度就应越大,它 至少应包含5个以上的轮廓峰和轮廓谷,
第四章 表面粗糙度测量
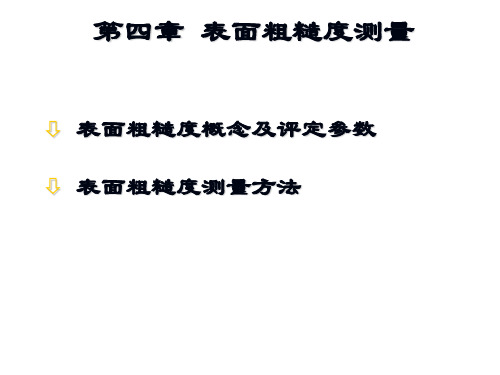
第四章表面粗糙度测量⇩表面粗糙度概念及评定参数⇩表面粗糙度测量方法4.1 表面粗糙度概念及评定参数一、表面粗糙度概念表面粗糙度是指由加工表面上具有的较小间距和峰谷组成的微观几何形状特性,亦称微观不平度。
它是由于在加工过程中刀具和零件的摩擦、切削分离时的塑性变形和金属撕裂,以及加工系统的振动等原因形成的。
零件的横截面形状是复杂的,一般按波距(间距)分成三类:表面粗糙度:波距小于1mm表面波度:波距在1~10mm形状误差:波距大于等于10mm表面粗糙度对零件使用性能的影响:1、对摩擦磨损的影响2、对配合性质的影响3、对抗腐蚀性的影响4、对抗疲劳强度的影响5、对结合密封性的影响(一)基本术语1、取样长度(l)在测量和评定表面粗糙度时所规定的具有表面轮廓特征的一段基准线长度。
一般至少包含5个以上轮廓峰谷。
2、评定长度(l n)在测量和评定表面粗糙度时所规定的一段最小长度。
一般情况下为5个取样长度。
(一)基本术语3、轮廓中线(m )2) 轮廓的算术平均中线:具有几何轮廓形状,在取样长度内与轮廓走向一致的基准线,该线划分轮廓并使上下两部分的面积相等.1) 轮廓的最小二乘中线: 具有几何轮廓形状并划分轮廓的基准线,在取样长度内使轮廓线上各点的轮廓偏距的平方和最小.[]20()min l y x dx =⎰1212n n F F F F F F'''++⋅⋅⋅+=++⋅⋅⋅+(二) 表面粗糙度评定参数1、轮廓算术平均偏差(R a)2、轮廓微观不平度十点高度(R z )3、轮廓最大高度(R y)1、轮廓算术平均偏差(R a )在取样长度内,轮廓偏距绝对值的算术平均值。
0111()()a nl i i R y x dx y x l n ==∑⎰2、轮廓微观不平度十点高度(R z )在取样长度内,5个最大轮廓的峰高y pi 和5个最大轮廓的谷深y vi和的平均值之和。
55111()5z pi vi i i R y y ===+∑∑3、轮廓最大高度(R y )在取样长度内轮廓最高点与轮廓最低点之间的距离.max max y p v R y y =+国标规定采用中线制来评定表面粗糙度,粗糙度的评定参数一般从轮廓算术平均偏差、微观不平度十点高度、轮廓最大高度中选取,推荐优先选用轮廓算(一)测量方向的选取原则1.当图样上未规定测量方向时,对于一般切削加工表面,应在垂直于加工痕迹的方向上测量;2.当图样上明确规定测量方向的特定要求时,则应按要求测量;3.当无法确定表面加工纹理方向时(如经研磨的加工表面),应通过选定的几个不同方向测量,然后取其中的最大值作为被测表面的粗糙度参数值。
第4章 表面粗糙度
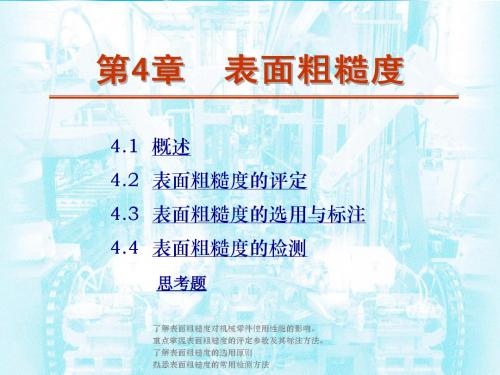
表面粗糙度的选用与标注
表4-2 表面粗糙度高度参数的标注 (摘自GB/T131-1993) 代号 意义 用任何方法获得的表面粗糙度,Ra的上限值为3.2μm
用去除材料的方法获得的表面粗糙度,Ra的上限值为3.2μm
用不去除材料的方法获得的表面粗糙度,Ra的上限值为3.2μm
用去除材料的方法获得的表面粗糙度,Ra的最大值为3.2μm,最 小值为1.6μm
标准规定以轮廓的最小二乘中线(简称中线m)作为基准线。 最小二乘中线是唯一的,从理论上讲是理想的基准线。但在轮廓图形上 确定其位臵比较困难,而算术平均中线与最小二乘中线的的差别很小, 所以通常用算术平均中线来代替最小二乘中线,用目测估计来确定轮廓 的算术平均中线。 当轮廓很不规则时,算术平均中线不是唯一的中线。
Rmr(C)的数学表达式为:
Ml (C ) Rmr (C ) lr
Ml (i)
i 1
n
lr
(%)
同一轮廓上取不同水平截距C值可得到不同的Rmr(C)值 Rmr(C) 综合反映了峰高和间距的影响
表面粗糙度的评定
图(a)的 Rmr(C)值大,表示该轮廓的凸起实体部分较多,即起支承载荷作 用的长度长,接触刚度高,承载能力及耐磨性好。
4.1 概述 4.2 表面粗糙度的评定
4.3 表面粗糙度的选用与标注
4.4 表面粗糙度的检测
思考题
了解表面粗糙度对机械零件使用性能的影响。 重点掌握表面粗糙度的评定参数及其标注方法。 了解表面粗糙度的选用原则 熟悉表面粗糙度的常用检测方法
上海应用技术学院
概述
一. 概念 表面粗糙度是零件表面加工后形成的有较小间距和峰谷组成的微量高低不 平的痕迹。
yi2 min
第4章-表面粗糙度

58
59
推削(精)
推削(精密)
0.8~0.2
0.4~0.025
60
外圆磨内圆磨(半精、一次加工)
6.3~0.8
• 磨削
61 62
外圆磨内圆磨(精) 外圆磨内圆磨(精密)
63 外圆磨内圆磨(精密、超精密磨削) 64 65 66 67 68 69 70 71 外圆磨内圆磨(镜面磨削外圆磨) 平面磨(精) 平面磨(精密) 珩磨(粗、一次加工) 珩磨(精、精密) 研磨(粗) 研磨(精) 研磨(精密)
4. 几何参数
• 轮廓峰 • 轮廓谷 • 轮廓单元(相邻轮廓峰与轮廓谷的组合)
4.2.2 表面粗糙度的主要评定参数
基本参数
幅度(高度) 轮廓算术平均偏差Ra 特征参数
轮廓最大高度Rz
间距特征参数 轮廓单元的平均宽度Rsm 附加参数 (辅助参数) 形状特征参数 轮廓的支承长度率Rmr(c)
1.轮廓算术平均偏差(Ra)
– 例如:一些机器、仪器上的手柄、手轮以及卫生设备、食品机械 上的某些机械零件的修饰表面,它们的表面要求加工得很光滑即 表面粗糙度要求很高,但其尺寸公差要求却很低。
三种公差值之间的对应关系
• 一般地,尺寸公差、表面形状公差小时,表面粗 糙度参数值也小,但也不存在确定的函数关系。 如机床的手轮或手柄。 表面粗糙度<形状公差<尺寸公差
离。 • 常与Ra联合使用
– 用来控制微观不平度的谷深,以达到控制表面微观裂缝的目的。 – 常用于受交变应力作用的工作表面。
3.轮廓单元的平均宽度Rsm
• • • • 【定义】在一个取样长度内,轮廓单元宽度Xs的平均值。 可反映被测表面加工痕迹的细密程度, 反映了轮廓与中线的交叉密度, 对评价承载能力、耐磨性和密封性有指导意义。
第四章 表面粗糙度及检测

聊城大学机械与汽车工程学院
干涉法
利用光波干涉原理。 采用的仪器:干涉显微镜。 适宜测量极光滑的表面,Rz=0.025~0.8µm
聊城大学机械与汽车工程学院
聊城大学机械与汽车工程学院
2)轮廓的算术平均中线 在一个取样长度lr范围内,轮廓的算术平均中线将实际 轮廓划分为上、下两部分,使上部分各个峰面积之和等 于下部分各个谷面积之和。
聊城大学机械与汽车工程学院
4. 取样长度lr
规定取样长度,是为了抑制和减弱表面波纹度对表面粗糙 测量结果的影响,5个以上完整轮廓的峰和谷。标准取样长 度的数值见附表4-5。
《产品几何技术规范 表面结构 轮廓法 表面结构的术语、 定义及参数》(GB/T3505-2009) 《表面粗糙度 参数及其数值》 (GB/T1031-2009) 《技术产品文件中表面结构的表示法》(GB/T131-2006)
聊城大学机械与汽车工程学院
二、基本术语:
1、λc滤波器(传输带):确定粗糙度与波纹度成分
聊城大学机械与汽车工程学院
针描法
利用触针直接在被测表面上轻轻滑过, 从而测量出表面粗糙度Ra值。
测量仪器:电动轮廓测量仪
测量范围:Ra=0.025~5µm表面。 特点:快速可靠,操作简便,易于实现自动 测量和微机数据处理;被测表面易被划伤。
聊城大学机械与汽车工程学院
光切法
利用光切原理测量表面粗糙度的方法。 采用仪器:光切显微镜(双管显微镜) 适宜测量车、铣、刨或其他类似方法加工的金属 零件的平面或外圆表面。 适宜测量Rz=0.5~60µm的表面。
聊城大学机械与汽车工程学院
3. 轮廓单元的平均宽度(间距参数)
一个轮廓峰与相邻的轮廓谷的组合叫做轮廓单元,在一个取样长 度lr范围内,中线与各个轮廓单元相交线段的宽度(轮廓的宽度 Xsi)的平均值RSm,即 m
第4章__表面粗糙度

理 轮廓总的走向上量取。
工
大
学
《
互
换
性
与
测
量
规定和选取取样长度的目的是为了限制和削弱表面波纹度对表面粗糙度测量结果的影响。
技
术
》
2.评定长度ln(evaluation length)——指评定轮廓所必须的一段长度,它包括一个或几个取
样长度。 ln=5l
3.基准线——用于评定表面粗糙度参数给定的线。
《
互
换
性
与
测
量
技
术
(2)轮廓的单峰平均间距S——在取样长度内,轮廓的单峰间距的平均值。
》
S=
1 n
n ∑ Si
i=1
3.形状特征参数——用轮廓支承长度率tp表示。
轮廓支承长度率tp——在取样长度内,一平行于中线与轮廓相截所得到的各段截线长度bi之和 与取样长度之比。
武 汉 理
tp=
1
n ∑
bi
l
i=1
理
工
大 学
3.2
C×45
《
表面粗糙度符号、代号一般注
互 在可见轮廓线、尺寸界线、引出线
换 或它们的延长线上。符号的尖端必 性 须从材料外指向表面
与
0.4
测
1.6 3.2
12.5
量
技 术
1.6
》
武
汉
理
工
表面粗糙度代号中
大 数值方向应与尺寸数
学 值方向一致
《
互 换 性 与 测 量 技 术 》
12.5
3.2 12.5
换
性
与
表面不平度按表面轮廓误差曲线相邻两波峰或波谷之间的距离(波距)λ的大小划分为三
第四章 表面粗糙度及测量讲解

达式为
Rmr(c) Ml(c) ln
Ml(c)=Ml1+Ml2+…+Mln
(4-5) (4-6)
选用Rmr(c)值时必须同时给出c值。c值可用μm或c值与Rz值的百
分比表示。
Rmr (c)是评定轮廓的曲线和相关参数,当c一定时,Rmr (c)
值越大,则支承能力和耐磨性越好。如图4-10所示。 上一页 下一页
§4. 3 表面粗糙度的选用
一、表面粗糙度评定参数的选用
国家标准规定,轮廓的幅度参数(如Ra或Rz)是必须标注的参数,
而其他参数(如RSm , Rmr (c ))是附加参数。一般情况下,选用
Ra或Rz就可以满足要求。RSm主要在涂漆性能,冲压成形时防止
引起裂纹、抗振性、抗腐蚀性、减小流体流动摩擦阻力等要求时附加
上一页 下一页
§4. 4表面粗糙度的符号、代号及图样标注
三、表面粗糙度的标注示例
表面粗糙度参数的各种标注方法及其意义见表4-10,加工纹理方 向符号见表4-11。Ra只标数值,本身符号不标。Rz除标注数值外 还需在数值前标出相应的符号。在一个符号上可同时标出两个参数值。 当允许在表面粗糙度参数的所有实测值中超过规定的个数少于总数的 16%时,应在图样上标注表面粗糙度参数的上限值或下限值。当要 求在表面粗糙度参数的所有实测值中不得超过规定值时,应在图样上 标注表面粗糙度参数的最大值或最小值。
选用表面粗糙度参数值的方法通常采用类比法。
上一页 下一页
§4. 3 表面粗糙度的选用
表4-6列出了轴和孔的表面粗糙度参数推荐值,表4 -7给出不同表
面粗糙度的表面特征、经济加工方法及应用举例,可供选用时参考。
根据类比法初步确定表面粗糙度参数值后,再对比工作条件,应
第四章 表面粗糙度及波纹度

③ 受循环载荷的表面及易引起应力集中的部分
Ra要小。
16
④ 配合性质要求高的结合表面Ra要小;
配合间隙小的的配合表面Ra要小;
要求连接可靠、受重载的过盈配合表面Ra要小。
⑤ 配合性质相同,零件尺寸小Ra要小; 同一精度等级时小尺寸比大尺寸、轴比孔Ra要小。
17
2、参数值的选用原则
◆ 没有特别的表面功能要求时,一般只考虑与尺寸公
②表面波纹度:零件表面峰谷的波距介于1~10
mm 之间呈周期性。 ③形状误差:零件表面峰谷的波距大于10mm的 不平程度。
4
二、主要术语及定义
⑴ 取样长度L(表4-5)
— 用于判别被评定轮廓的不规则特征的X轴方向
上的长度。在轮廓总的走向上量取。
基准线
L
L
L
n
L
L
⑵ 评定长度Ln(表4-5)
— 用于判别被评定轮廓的X轴方向上的长度。
选用较大的数值。 ◆ 综合考虑因素:运动速度、工作温度、载荷、润 滑状况、材料、结构、成本要求等。参见下表: 表4-7 表面粗糙度参数值与所适应的零件表面
15
一般情况:
① 同一零件上,工作表面比非工作表面Ra要小。 ② 摩擦表面比非摩擦表面Ra要小; 滚动摩擦表面比滑动摩擦表面Ra要小; 运动速度高、单位压力大的摩擦表面Ra要小。
幅度参数:
① 最大轮廓峰 高Rp、谷深Rv; ② 轮廓最大高 度RZ(表4-2);
③ 轮廓算术平均偏差Ra(表4-1): ━在一个取样长度内,轮廓所有纵坐标值∣Z(x)∣
的算术平均值。
1 l 1 n Ra Z ( x) dx Z ( xi ) l 0 n i 1
Ra
9
表面粗糙度及检测

h?
h??cos2 45? ?
1
h??
M
2M
(三)干涉法
干涉法是利用光波干涉原理来测量表面粗糙度数值的 一种方法。干涉法所用的仪器是干涉显微镜,通常 用来测量 Rc和Rz值,测量Rc值的范围一般为 0.4~1 μm。
1.干涉显微镜的测量原理
干涉显微镜的外形如图 4-22所示,其测量原理如图 423所示。由光源 1发出的光线,经聚光滤色镜组 2聚 光和滤色,再经反射镜 3转向,通过光栏 4、5和物 镜6,投射于分光镜 7的半透明半反射膜后分成两路 光束,一路光束透过分光镜 7和补偿镜 10、物镜11 射向工件被测表面 P2,经P2反射后原路返回,再射 在分光镜上,射向观察目镜 16。另一路光束由分光 镜7反射,经滤色片 8、物镜9射向标准反射镜 P1, 再由P1反射也经原路返回,透过分光镜,射向观察 目镜16。
图4-11 干涉显微镜的外形
1—光源;2—光源调节螺钉; 3、5—工作台微动千分尺; 4—工作台; 6—工作台固定螺钉; 7—仪器调修时用的手柄; 8—遮光板转动手柄; 9—调整干涉条纹方向及宽度的手柄; 10—调焦旋钮; 11—底座;12—照相机; 13—侧微目镜调节手轮; 14—目镜; 15—遮光片移动手柄
比较法使用简便,但判断的准确程度有限,所以适用 于车间中近似评定粗糙度较大的工件 。
(二)光切法
光切法是利用光切原理来测量表面粗糙度数值的一种方法。 光切法所用的仪器是光切显微镜 (又称为双管显微镜),它适 宜测量轮廓单元的平均高度Rc和轮廓最大高度Rz值,测量 Rc值范围一般为0.8~6.3 μm。
3、轮廓单元的平均宽度 RSm :是指在一个取样长度 内,轮廓单元宽度值 Xs的平均值
? RSm ?
表面粗糙度的评定参数

? 4.表面缺陷:评定过程中,不应把表面缺陷(如沟槽、气孔、 划伤等)包含进去。必要时,应单独规定表面缺陷要求。
? 5 .测量部位:为了完整地反映零件表面的实际状况,需要在其 若干具有代表性的位置上进行测量,一般可采取在均匀分布的三 个以上的位置上取其平均值作为最终结果。
1.5 表而粗糙度测量方法综述及测量的基本原则
? 15.1 测量方法综述 ? 对加工表面质量的评定,除了用视觉和触觉进行定性地比较检验的方
第四章 表面粗糙度的测量
一.表面形貌误差的概念与形成
1.表面形貌误差分类: 实际加工表面通常包含如下三种表面形貌误差:
? 表面粗糙度:波距λ小于1mm ,大体呈周期性变化, 属于微观几何形状误差;
? 表 面 波度:波距λp在1~10mm ,呈周期性变化, 属于中间几何形状误差;
? 形状 误 差:波距大于10mm ,无明显周期性变化, 属于宏观几何状误差 。
形的美观等等。
三.表面形貌测量的特点与范围
? 特点:通常为量程小、测量分辨率高( nm )、 ? 表面粗糙度测量的范围
现在表面分析技术已远走出机器零件,如 :
? 微电子工业:硅片、磁盘表面、光盘、光学元件、 窗片
? 材料科学:表面形貌分析、材料微裂纹 ? 生物工程:细胞生物、芯片、遗传学 ? 科学研究:纳米技术、物理、化学、生物等基础
实际轮廓图
横向实际轮廓图
2.取样长度l:用于判别和测量表面粗糙度时所规定的一段基 准线长度。
第4章表面粗糙度-陈

基准线
lr
lr
lr
lr
lr
ln
二、表面(粗糙度)结构的评定
3.基准线 通过测量手段获得表面轮廓曲线以后, 需要提供一条定量评定表面粗糙度量值的基 准线,作为计算各种参数的基础。 轮廓算术平均中线 轮廓最小二乘中线
二、表面(粗糙度)结构的评定
3.基准线
①轮廓算术平均中线: 具有理想的直线形状并在取样长度lr 内与轮 廓走向一致的基准线,该基准线将实际轮廓分成 上、下两个部分,且使上部分面积之和等于下部 分面积之和。
2.表面粗糙度高度参数值的注写及涵义
①给定上限值:同一评定长度范围内,幅度
参数所有实测值中,大于上限值的个数少于总数
的16%,则认为合格。
Ra 6.3 Rz 12.5
U Ra 6.3 U Rz 12.5
②给定上限值和下限值:同一评定长度范围内,
幅度参数所有实测值中,大于上限值的个数少于总
数的16%,且小于下限值的个数少于总数的16%,
轮廓单元的平均宽度是指在一个取样长度 lr 范围内所有轮廓单元的宽度Xsi的平均值。
RSm m 1 i m 1Xsi
二、表面(粗糙度)结构的评定
轮廓单元的平均宽度RSm
RSm m 1 i m 1Xsi
Xs1
Xsi lr
Xsm
二、表面(粗糙度)结构的评定
3.形状特征参数 轮廓支承长度率Rmr(c) 在评定长度ln内,一条平行于中线的直 线从峰顶线向下移动到某一水平位置(移动 距离c)时,轮廓的实体材料长度Ml(c)与评 定长度ln之比(用百分率表示)。
则认为合格。
Ra 6.3 Ra 3.2
U Ra 6.3 L Ra 3.2
2.表面粗糙度高度参数值的注写及涵义
教学课件第4章表面粗糙度

1.幅度参数(高度参数) ⑴ 轮廓的算术平均偏差Ra (arithmetical mean deviation of the
assessed profile) 轮廓的算术平均偏差Ra是指在一个取样长度内,纵坐标Z(x)
绝对值的算术平均值,如图4.5所示。用公式表示为:
Ra 1
二、参数值的选用
国家标准GB/T1031—1995对表面粗糙度的参数值大小进行了规定,Ra、 Rz、RSm、 Rmr(c)的参数值分别见表4-1~表4-4。
表4-1 Ra的参数值(μm) (摘自GB/T1031—1995)
表4-2 Rz的参数值(μm) (摘自GB/T1031—1995)
表4-3 RSm的参数值(mm) (摘自GB/T1031—1995) 表4-4 Rmr(c)的参数值(%) (摘自GB/T1031—1995)
(a.10 附加参数的标注
3 .表面粗糙度其它项目的标注
表面粗糙度的数值及其有关规定在符号中注写的位置如图4.11所示。
如果按国家标准GB10610—1989的规定选用对应的取样长度时,在图 样上可省略标注,否则应按图4.12(a)所示的方法标注取样长度0.8mm。
如果某表面的粗糙度要求由指定的加工方法(如铣削)获得时,可用文 字标注在图4.11规定之处,如图4.12(b)所示。
图4.6 轮廓的最大高度
2.间距参数 轮廓单元的平均宽度RSm(mean width of the profile elements): 轮廓单元的平均宽度RSm是指在一个取样长度内粗糙度轮廓单元宽
度Xs的平均值,如图4.7所示。
RSm
1 m
m i1
Xsi
图4.7 轮廓单元的平均宽度
表面粗糙度及波纹度
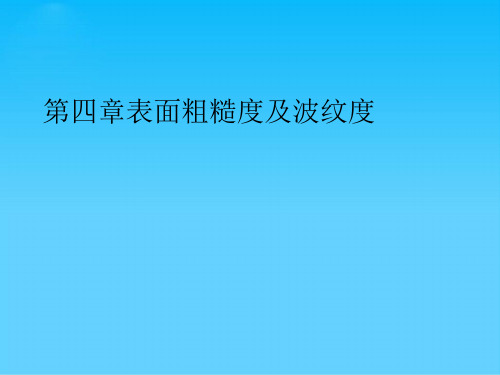
Ra 1
l
y dx
l0
近似为
Ra 1 n
n i1
yi
二、表面轮廓的参数 轮廓的最大高度Rz
在一个取样长度范围内,最大轮廓峰高Zp与最大轮廓 谷深Zv之和称之为轮廓最大高度,用符号Rz表示,即 Rz = Zp + Zv
中线 lr
Zp4 Zp5
Zp6
Zv3 Zv4 Zp3
Zp2
Rz Zp1
Zv1 Zv2
3)完整图形符号
用于标注表面结构参数和各项附加要求
表面粗糙度对零件功能的影响
一、表面粗糙度的符号
表面是用不去除材料方法获得,如铸,锻等
标注在圆柱和棱柱表面上
4 工件轮廓各表面图形符号 评定轮廓的算术平均偏差Ra
) 三、粗糙度在图样上的标注
不同的评定轮廓对应不同的取样长度(lp、lr、lw)
轮廓单元的平均宽度:是指在一个取样长度lr范围内所有轮廓单元的宽度Xsi的平均值,即
表面粗糙度参数值的选择
除前后两表面以 在一个取样长度范围内,最大轮廓峰高Zp与最大轮廓谷深Zv之和称之为轮廓最大高度,用符号Rz表示,即Rz = Zp + Zv
依据《表面粗糙度参数及其数值》(GB/T 1031-1995)有以下数值:
外周边封闭轮廓 第一节 表面粗糙度及波纹度
总的原则是根据GB/T 4458.
有共同的表面结 一、表面粗糙度对零件功能的影响
三、粗糙度在图样上的标注
构参数要求 取样长度:用于判别被评定轮廓的不规则特征的X轴方向上的长度。
三、粗糙度在图样上的标注
三、粗糙度在图样上的标注
表面粗糙度的选择和运用
标注在轮廓线或指引线上
表面粗糙度:零件表面在切削或非切削加工时所产生的微观几何形状误差
- 1、下载文档前请自行甄别文档内容的完整性,平台不提供额外的编辑、内容补充、找答案等附加服务。
- 2、"仅部分预览"的文档,不可在线预览部分如存在完整性等问题,可反馈申请退款(可完整预览的文档不适用该条件!)。
- 3、如文档侵犯您的权益,请联系客服反馈,我们会尽快为您处理(人工客服工作时间:9:00-18:30)。
Ra
(2)对配合性能的影响 对于间隙配合,相对运动的表面因其粗糙不平而迅速 磨损,致使间隙增大;对于过盈配合,表面轮廓峰顶在装 武 汉 配时容易被挤平,使实际有效过盈量减小,致使联接强度 理 降低。
工 大 学 《 互 换 性 与 测 量 技 术 》
(3)对抗腐蚀性的影响 粗糙的表面,易使腐蚀性物质存积在表面的微观凹谷 处,并渗入到金属内部,致使腐蚀加剧。
2H
H=1.4倍的字高
若仅表示需要加工(采用去除材料的方法或不去除材料的方法),但 对表面粗糙度的其他规定没有要求时,允许只注表面粗糙度符号。
H
表面粗糙度基本符号
图样上表示零件表面粗糙度的符号
符号 意义及说明
基本符号,表示表面可用任何方法获得。当不加注粗糙度参数值 或有关说明(例如:表面处理、局部热处理状况等)时,仅适用 于简化代号标注 基本符号加一短划,表示表面是用去除材料的方法获得。例如: 车、铣、钻、磨、剪切、抛光、腐蚀、电火花加工、气割等 基本符号加一小圆,表示表面是用不去除材料的方法获得。例 如:铸、锻、冲压变形、热轧、粉末冶金等。 或者用于保持原供应状况的表面(包括保持上道工序的状况)
4.3.2 评定参数值的选用 表面粗糙度评定参数选定后,应规定其允许值。
武 表面粗糙度参数值选用得适当与否,不仅影响零件的 汉 理 使用性能,还关系到制造成本。 工 一般说来,表面粗糙度参数值愈小,零件的工作性能 大 学 愈好,但加工成本上升。 《 互 表面粗糙度参数值的选用原则: 换 性 在满足使用性能要求的前提下,应尽可能选用较大的参 与 数允许值。 测 量 表面粗糙度的参数值已经标准化,设计时应按国家标准 技 术 规定的参数系列选取。一般指规定上限值,必要时要给出下 》 限值。
2.间距特征参数——沿着评定基准线的方向测量的, 反映表面加工痕迹细密程度。 (1)轮廓微观不平度的平均间距Sm——在取样长度内, 武 轮廓微观不平度的间距的平均值。 n 汉 Sm= 1 ∑ Smi 理 n
工 大 学 《 互 换 性 与 测 量 技 术 》
i=1
(2)轮廓的单峰平均间距S——在取样长度内,轮廓的 n 单峰间距的平均值。 1 ∑ Si S= n
2.表面粗糙度对零件使用性能的影响
表面粗糙度对机械零件的使用性能和寿命都有很大的 影响,尤其是对在高温、高压和高速条件下工作的机械零 武 件影响更大,其影响主要表现在以下几个方面:
汉 理 工 大 学 《 互 换 性 与 测 量 技 术 》
(1)对摩擦和磨损的影响 具有微观几何形状误差的两个表面只能在轮廓的峰顶 发生接触,如下图所示 。 磨损量
4.2 表面粗糙度的评定
4.2.1 与评定参数有关的术语及定义
武 汉 理 工 大 学 《 互 换 性 与 测 量 技 术 》
1.取样长度l(sampling length)——指用于判别具有表面 粗糙度特征的一段基准线长度,它在轮廓总的走向上量取。
规定和选取取样长度的目的是为了限制和削弱表面波纹 度对表面粗糙度测量结果的影响。 2.评定长度ln(evaluation length)——指评定轮廓所必 须的一段长度,它包括一个或几个取样长度。 ln=5l
1.表面粗糙度(roughness)——指零件加工表面所具有 的较小间距和和微小峰谷不平度。 表面粗糙度形成的原因: 在加工过程中由于切削分离时金属断裂、切削层残留 面积、刀瘤脱落、鳞刺、受力所产生的金属塑性变形以及 工艺系统高频振动等原因。 表面粗糙度是一种微观几何形状误差,也称为微观不 平度。 表面不平度按表面轮廓误差曲线相邻两波峰或波谷之 间的距离(波距)λ 的大小划分为三类:
i=1
3.形状特征参数——用轮廓支承长度率tp表示。 轮廓支承长度率tp——在取样长度内,一平行于中线与轮 廓相截所得到的各段截线长度bi之和与取样长度之比。 n 武 1 ∑ bi tp= 汉 l i=1
理 工 大 学 《 互 换 性 与 测 量 技 术 》
与高度特性有关的参数(Ra,Rz,Ry)是标准规定必须 标注的参数,故称为基本评定参数。间距特性参数(Sm,S) 与形状特征参数(tp)称为附加参数,只有零件表面有特殊 使用要求时才选用。
2.附加评定参数的选用
附加评定参数一般情况下不作为独立的参数选用。
只有零件的表面有特殊使用要求时,仅用高度特征参数 武 汉 不能满足零件表面的功能 要求,才在选用了高度参数的基础 理 工 上,附加选用间距特征参数和形状特征参数。 大 一般情况下,对密封性、光亮度有特殊要求的表面,应 学 选用附加参数Sm或S。 《 互 为了使汽车外壳薄钢板具有较好的喷涂结合性和光洁美 换 性 观的外形,规定其高度特征参数Ra(0.9~1.3μm),还应控 与 制间距特征参数S(0.13~0.23mm) 测 量 对耐磨性有特殊要求的表面,应选用附加参数tp。 技 术 》
(4)对疲劳强度的影响 零件表面越粗糙,凹痕就越深,当零件承受交变载荷 时,对应力集中就越敏感,使疲劳强度降低,导致零件表 武 汉 面产生裂纹而损坏。
理 工 大 学 《 互 换 性 与 测 量 技 术 》
(5)对接触刚度的影响 接触刚度影响零件的工作精度和抗振性。这是由于表 面粗糙度使表面间只有一部分面积接触。一般情况下,实 际接触面积只有公称接触面积的百分之几。因此,表面越 粗糙受力后局部变形越大,接触刚度也越低。 (6)对结合面密封性的影响 粗糙的表面结合时,两表面只在局部点上接触,中间 有缝隙,影响密封性。因此,降低表面粗糙度,可提高其 密封性。
代号
意义
用任何方法获得的表面粗糙度,Ra 的最大值为3.2μm 用去除材料方法获得的表面粗糙 度,Ra的最大值为3.2μm 用不去除材料方法获得的表面粗糙 度,Ra的最大值为3.2μm 用去除材料方法获得的表面粗糙 度,Rz的最大值为3.2μm,Rz的最小值 为1.6μm
3.2
3.2max
3.2
3.2
武 汉 理 工 大 学 《 互 换 性 与 测 量 技 术 》
(2)微观不平度十点高度Rz——在取样长度内,5个最 大轮廓峰高的平均值与5个最大轮廓谷深的平均值之和。
武 汉 理 工 大 学 《 互 换 性 与 测 量 技 术 》
∑ ypi + ∑ yvi Rz=
i=1
5
5
5
i=1
(3)轮廓最大高度Ry——在取样长度内,轮廓峰顶线 和轮廓谷底线之间的距离。 Ry=|ypmax|+|yvmax|
武 汉 理 工 大 学 《 互 换 性 与 测 量 技 术 》
4.4 表面粗糙度的标注
GB/T 131—93规定了零件表面粗糙度符号、代号及其 在图样上的注法。图样上所标注的表面粗糙度符号、代号 武 汉 应是该表面完工后的要求。
理 工 大 学 《 互 换 性 与 测 量 技 术 》
4.4.1 表面粗糙度的符号
a1、a2——粗糙度高度参数代号及其 数值 (µm);参数为Ra时,参数值前不 注符号;参数为Ry或Rz时,参数值前 必须注出相应的参数符号 b——加工方法、镀覆、涂覆、表面 处理或其他说明等 c——取样长度(mm)或波纹度(μm)
武 汉 理 工 大 学 《 互 换 性 与 测 量 技 术 》
d——加工纹理方向符号
4.2.2 评定参数 为了完善地评定零件表面实际轮廓的粗糙程度,需要从 不同方向规定适当的参数。 高度特征参数、间距特征参数、形状特征参数 1.高度特征参数——沿着垂直于评定基准线的方向计量。 (1)轮廓算术平均偏差Ra——在取样长度内,轮廓偏距 绝对值的算术平均值。 Ra= 1 ∫l |y(x)| dx l 0
表面粗糙度的代号及其标注位置 e——加工余量(mm) f——粗糙度间距参数值(mm)或轮廓支 承长度率(%)
取样长度2.5mm
武 汉 理 工 大 学 《 互 换 性 与 测 量 技 术 》
加工方法(铣削)
总加工余量(5mm)
附加标注示例
表面加工纹理方向
部分加工纹理方向符号
武 汉 理 工 大 学 《 互 换 性 与 测 量 技 术 》
(3)零件表面粗糙度的选择。
(4)表面粗糙度的测量。 通过本章的学习,要求了解表面粗糙度对零件功能的 影响,掌握表面粗糙度的评定标准和参数,以及在图纸上 的标注方式。学会按零件表面的功能要求选择表面粗糙度 值,并会进行表面粗糙度的测量。
4.1 概 述
武 汉 理 工 大 学 《 互 换 性 与 测 量 技 术 》
4.3 表面粗糙度的选用
4.3.1 评定参数的选用
武 汉 理 工 大 学 《 互 换 性 与 测 量 技 术 》 表面粗糙度评定参数应根据零件的工作条件、使用性能和测量等进 行选择,既要考虑能表针表面的几何特性和表面功能参数,又要考虑表 面粗糙度检测仪器的测量范围和工艺的经济性。
1.高度评定参数的选用
第4章 表面粗糙度
武 汉 理 工 大 学 《 互 换 性 与 测 量 技 术 》
4.1 4.2 4.3 4.4 4.5
概述 表面粗糙度的评定 表面粗糙度的选用 表面粗糙度的标注 表面粗糙度的测量
武 汉 理 工 大 学 《 互 换 性 与 测 量 技 术 》
(1)表面粗糙度的含义及其对机械零件使用性能的影响。 (2)表面粗糙度的的评定标准和参数。
说
武 汉 理 工 大 学 《 互 换 性 与 测 量 技 术 》
明
(1)当允许在表面粗糙度参数的所有实测值中超过规定值的个 数少于总数的16%时,应在图样上标注表面粗糙度参数的上限值或 下限值;
代号 意义
用任何方法获得的表面粗糙度, Ra的上限值为3.2μm 用去除材料的方法获得的表面粗 糙度,Ra的上限值为3.2μm 用不去除材料方法获得的表面粗 糙度,Ra的上限值为3.2μm 用去除材料方法获得的表面粗糙 度,Ra的上限值为3.2μm,Ra的下限 值为1.6μm
(1)波距小于1mm的属于表面粗糙度(微观几何形状误差) (2)波距在1~10mm的属于表面波纹度(中间几何形状误差) (3)波距大于10mm的所示为某工件表面实际轮廓误差曲线,将 这一段轮廓误差曲线按波距的大小分解为三部分的误 差曲线: