12SX14-T;中文规格书,Datasheet资料
STTH12S06FP;中文规格书,Datasheet资料
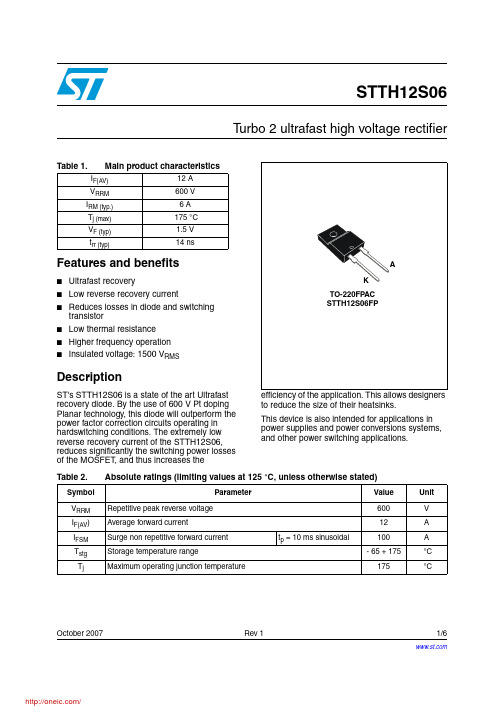
October 2007 Rev 11/6STTH12S06Turbo 2 ultrafast high voltage rectifierFeatures and benefits■Ultrafast recovery■Low reverse recovery current■Reduces losses in diode and switching transistor■Low thermal resistance ■Higher frequency operation ■Insulated voltage: 1500 V RMSDescriptionST's STTH12S06 is a state of the art Ultrafast recovery diode. By the use of 600 V Pt doping Planar technology, this diode will outperform the power factor correction circuits operating in hardswitching conditions. The extremely low reverse recovery current of the STTH12S06, reduces significantly the switching power losses of the MOSFET, and thus increases theto reduce the size of their heatsinks.This device is also intended for applications in power supplies and power conversions systems, and other power switching applications.Table 1.Main product characteristicsI F(AV)12 A V RRM600 V I RM (typ.) 6 A T j (max) 175 °C V F (typ) 1.5 V t rr (typ)14 nsTable 2.Absolute ratings (limiting values at 125 °C, unless otherwise stated)Symbol ParameterValue Unit V RRM Repetitive peak reverse voltage 600V I F(AV )Average forward current12A I FSM Surge non repetitive forward current t p = 10 ms sinusoidal100A T stg Storage temperature range- 65 + 175 °C T jMaximum operating junction temperature175°CCharacteristics STTH12S062/61 CharacteristicsTable 3.Thermal resistancesSymbol ParameterValue Unit Rth (j-c)Junction to case4.6°C/WTable 4.Static electrical characteristicsSymbol ParameterTests conditions Min.Typ.Max.Unit I RReverse leakage currentV R = 600 VT j = 25 °C 30µAT j = 125 °C 35400V FForward voltage dropI F = 12 AT j = 25 °C 3.4VT j = 150 °C1.5 1.9Table 5.Dynamic electrical characteristicsSymbol Tests conditionsMin.Typ.Max.Unit t rr I F = 1 A dI F /dt = - 200 A/µs V R = 30 V 1421ns I RM V R = 400 V I F = 12A dI F /dt = - 200 A/µs T j = 125 °C6.08.0AS factor V R = 200 V I F = 12A dI F /dt = - 200 A/µs0.3Q rr160nCFigure 1.Conduction losses versus Figure 2.Forward voltage drop versus Tδ=tp/TtpSTTH12S06Characteristics3/6Figure 3.Relative variation of thermal impedance, junction to case,Figure 4.Peak reverse recovery current versus dI F /dt (typical values)Figure 5.Reverse recovery time versusFigure 6.Reverse recovery charges versus Figure 7.Junction capacitance versus reverse voltage appliedPackage information STTH12S064/62 Package information●Epoxy meets UL94, V0●Cooling method: by conduction (C)●Recommended torque value: 0.55 Nm ●Maximum torque value: 0.7 NmIn order to meet environmental requirements, ST offers these devices in ECOPACK®packages. These packages have a lead-free second level interconnect. The category of second level interconnect is marked on the package and on the inner box label, in compliance with JEDEC Standard JESD97. The maximum ratings related to soldering conditions are also marked on the inner box label. ECOPACK is an ST trademark. ECOPACK specifications are available at: .STTH12S06Ordering information5/63 Ordering information4 Revision historyTable 7.Ordering informationPart number Marking Package Weight Base qtyDelivery modeSTTH12S06FPSTTH12S06FPTO-220FP AC1.6450T ubeTable 8.Revision historyDate RevisionChanges02-Oct-20071Initial release.STTH12S066/6Please Read Carefully:Information in this document is provided solely in connection with ST products. STMicroelectronics NV and its subsidiaries (“ST”) reserve the right to make changes, corrections, modifications or improvements, to this document, and the products and services described herein at any time, without notice.All ST products are sold pursuant to ST’s terms and conditions of sale.Purchasers are solely responsible for the choice, selection and use of the ST products and services described herein, and ST assumes no liability whatsoever relating to the choice, selection or use of the ST products and services described herein.No license, express or implied, by estoppel or otherwise, to any intellectual property rights is granted under this document. If any part of this document refers to any third party products or services it shall not be deemed a license grant by ST for the use of such third party products or services, or any intellectual property contained therein or considered as a warranty covering the use in any manner whatsoever of such third party products or services or any intellectual property contained therein.UNLESS OTHERWISE SET FORTH IN ST’S TERMS AND CONDITIONS OF SALE ST DISCLAIMS ANY EXPRESS OR IMPLIED WARRANTY WITH RESPECT TO THE USE AND/OR SALE OF ST PRODUCTS INCLUDING WITHOUT LIMITATION IMPLIED WARRANTIES OF MERCHANTABILITY, FITNESS FOR A PARTICULAR PURPOSE (AND THEIR EQUIVALENTS UNDER THE LAWS OF ANY JURISDICTION), OR INFRINGEMENT OF ANY PATENT, COPYRIGHT OR OTHER INTELLECTUAL PROPERTY RIGHT. UNLESS EXPRESSLY APPROVED IN WRITING BY AN AUTHORIZED ST REPRESENTATIVE, ST PRODUCTS ARE NOT RECOMMENDED, AUTHORIZED OR WARRANTED FOR USE IN MILITARY, AIR CRAFT, SPACE, LIFE SAVING, OR LIFE SUSTAINING APPLICATIONS, NOR IN PRODUCTS OR SYSTEMS WHERE FAILURE OR MALFUNCTION MAY RESULT IN PERSONAL INJURY, DEATH, OR SEVERE PROPERTY OR ENVIRONMENTAL DAMAGE. ST PRODUCTS WHICH ARE NOT SPECIFIED AS "AUTOMOTIVE GRADE" MAY ONLY BE USED IN AUTOMOTIVE APPLICATIONS AT USER’S OWN RISK.Resale of ST products with provisions different from the statements and/or technical features set forth in this document shall immediately void any warranty granted by ST for the ST product or service described herein and shall not create or extend in any manner whatsoever, any liability of ST.ST and the ST logo are trademarks or registered trademarks of ST in various countries.Information in this document supersedes and replaces all information previously supplied.The ST logo is a registered trademark of STMicroelectronics. All other names are the property of their respective owners.© 2007 STMicroelectronics - All rights reservedSTMicroelectronics group of companiesAustralia - Belgium - Brazil - Canada - China - Czech Republic - Finland - France - Germany - Hong Kong - India - Israel - Italy - Japan - Malaysia - Malta - Morocco - Singapore - Spain - Sweden - Switzerland - United Kingdom - United States of America分销商库存信息: STMSTTH12S06FP。
MDL-ACIM;中文规格书,Datasheet资料
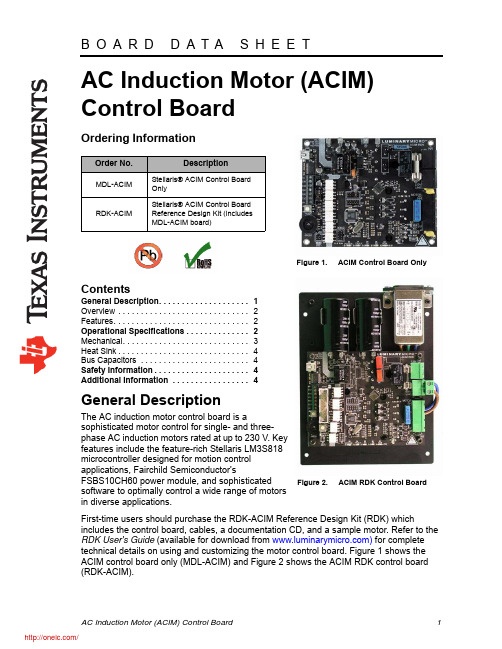
AC Induction Motor (ACIM) Control BoardOrdering InformationContentsGeneral Description. . . . . . . . . . . . . . . . . . . . 1Overview . . . . . . . . . . . . . . . . . . . . . . . . . . . . . 2Features. . . . . . . . . . . . . . . . . . . . . . . . . . . . . . 2Operational Specifications . . . . . . . . . . . . . . 2Mechanical. . . . . . . . . . . . . . . . . . . . . . . . . . . . 3Heat Sink. . . . . . . . . . . . . . . . . . . . . . . . . . . . . 4Bus Capacitors . . . . . . . . . . . . . . . . . . . . . . . . 4Safety Information. . . . . . . . . . . . . . . . . . . . . 4Additional Information . . . . . . . . . . . . . . . . . 4General DescriptionThe AC induction motor control board is asophisticated motor control for single- and three-phase AC induction motors rated at up to 230V. Key features include the feature-rich Stellaris LM3S818 microcontroller designed for motion control applications, Fairchild Semiconductor'sFSBS10CH60 power module, and sophisticated software to optimally control a wide range of motors in diverse applications.First-time users should purchase the RDK-ACIM Reference Design Kit (RDK) whichincludes the control board, cables, a documentation CD, and a sample motor. Refer to the RDK User's Guide (available for download from ) for complete technical details on using and customizing the motor control board. Figure 1 shows the ACIM control board only (MDL-ACIM) and Figure 2 shows the ACIM RDK control board (RDK-ACIM).Order No.DescriptionMDL-ACIMStellaris® ACIM Control Board OnlyRDK-ACIMStellaris® ACIM Control Board Reference Design Kit (includesMDL-ACIM board)Figure 1.ACIM Control Board OnlyFigure 2.ACIM RDK Control BoardOverviewThe MDL-ACIM motor control board controls three-phase and single-phase AC induction motors. The board has an integrated USB port (Virtual COM port) and logic-level serial port connections along with a quadrature encoder/tachometer input for speed and position monitoring. Extensive configuration options using Windows Graphical User Interface (GUI) are available and the board is easy to customize—full source code and design files are available.FeaturesThe MDL-ACIM motor control board provides the following features:End-user customizable line filter, bus capacitors, and JTAG interfaceSplit low-side current sensing for accurate current sensingDynamic braking circuitActive in-rush control circuitElectrically isolated JTAG port for software debugging or production programming (RDK only)Integrated AC line filter (RDK only)USB/Serial UART–FTDI FT232R USB to serial UART–Virtual COM port, 115.2k,8,n,1 operation–Stellaris MCC protocolOperational SpecificationsTable 1 shows the operating parameters for the MDL-ACIM motor control board.Table 1.MDL-ACIM Operating SpecificationsParameter Name Min Nom Max UnitAC Input Voltage (50/60Hz)230V operation195230265V AC 115V w/ voltage doubler95115135V ACDC Bus Voltage270320370V DC Frequency Range0400Hz Continuous Output Current 3.2A RMS Electrical Isolation2500V RMS Supply Current10A RMS Operating Temperature Range0–70°C Storage Temperature Range-25–85°C Digital Input Low Level Input Voltage-0.3 1.3V DCTable 1.MDL-ACIM Operating Specifications (Continued)Parameter Name Min Nom Max Unit Digital Input High Level Input Voltage 2.0 5.0V DC MechanicalFigure 3 shows the mechanical drawing for the MDL-ACIM.PCB size: 3.65" x 4.55" (93mm x115mm)Heatsink is required (MDL-ACIM only)Bus capacitors are required (MDL-ACIM only)Motor connector on PCB–RIA Connect part #31262104Power connector on PCB–RIA Connect part #31262102Figure 3.MDL-ACIM Mechanical DiagramHeat SinkThe ACIM motor module does not come with a heatsink like the RDK-ACIM, but does require a heatsink for operation. Underwriters Laboratories (UL) standards generally require that surfaces that could be touched by a user or service person must not exceed 70°C, so this must be considered when choosing the size material of the heatsink.Bus CapacitorsThe ACIM motor module requires that the customer supply bus capacitors for the board. The recommended capacitors to use are 1500uF, 200V electrolytic capacitors. Safety InformationWARNING – Risk of Electric ShockThe microcontroller in the RDK is not referenced to ground; it is at AC line potential. Do not make direct connection to the JTAG header or any other microcontroller-related circuit. Read the Quickstart Guide first for additional warnings.This RDK operates from AC line voltage. Improper use or application carries electric shock, fire, and other risks that may result in serious injury or death. Please read and follow these safety notices:This documentation and kit must only be used by people with training and experience in working with voltage potentials up to 230 V.The control board has both high-voltage potential and safety low-voltage sections.Do not connect high-voltage potential circuits to safety low-voltage circuits or to ground-referenced equipment such as computers or test equipment.After power is removed, high voltages remain until the bus capacitors discharge. Wait at least one minute after removing power before working with high-voltage circuitry.Use caution when using the on-board controls to adjust motor speed etc. High-voltage circuits are in close proximity.Never perform work on the control board, motor or, wiring while power is applied. Always wear eye protection and use care when operating the motor.In addition to safety risks, other factors that may damage the control hardware, the motor, and its load include improper configuration, wiring, or software. Minimize the risk of damage by following these guidelines.Additional InformationThe following documents are available for download at :RDK-ACIM User’s Manual, Publication Number RDK-ACIM-UMRDK-ACIM QuickstartCopyright © 2008–2009 Texas Instruments, Inc. All rights reserved. Stellaris and StellarisWare are registered trademarks of TexasInstruments. ARM and Thumb are registered trademarks, and Cortex is a trademark of ARM Limited. Other names and brands may be claimed as the property of others.RDK-ACIM-DS-01August 10, 2009Important NoticeTexas Instruments Incorporated and its subsidiaries (TI) reserve the right to make corrections, modifications, enhancements,improvements, and other changes to its products and services at any time and to discontinue any product or service without notice. Customers should obtain the latest relevant information before placing orders and should verify that such information is current and complete. All products are sold subject to TI’s terms and conditions of sale supplied at the time of order acknowledgment.TI warrants performance of its hardware products to the specifications applicable at the time of sale in accordance with TI’s standard warranty. Testing and other quality control techniques are used to the extent TI deems necessary to support this warranty. Except where mandated by government requirements, testing of all parameters of each product is not necessarily performed.TI assumes no liability for applications assistance or customer product design. Customers are responsible for their products and applications using TI components. To minimize the risks associated with customer products and applications, customers should provide adequate design and operating safeguards.TI does not warrant or represent that any license, either express or implied, is granted under any TI patent right, copyright, mask work right, or other TI intellectual property right relating to any combination, machine, or process in which TI products or services are used. Information published by TI regarding third-party products or services does not constitute a license from TI to use such products or services or a warranty or endorsement thereof. Use of such information may require a license from a third party under the patents or other intellectual property of the third party, or a license from TI under the patents or other intellectual property of TI.Reproduction of TI information in TI data books or data sheets is permissible only if reproduction is without alteration and isaccompanied by all associated warranties, conditions, limitations, and notices. Reproduction of this information with alteration is an unfair and deceptive business practice. TI is not responsible or liable for such altered documentation. Information of third parties may be subject to additional restrictions.Resale of TI products or services with statements different from or beyond the parameters stated by TI for that product or service voids all express and any implied warranties for the associated TI product or service and is an unfair and deceptive business practice. TI is not responsible or liable for any such statements.TI products are not authorized for use in safety-critical applications (such as life support) where a failure of the TI product would reasonably be expected to cause severe personal injury or death, unless officers of the parties have executed an agreementspecifically governing such use. Buyers represent that they have all necessary expertise in the safety and regulatory ramifications of their applications, and acknowledge and agree that they are solely responsible for all legal, regulatory and safety-related requirements concerning their products and any use of TI products in such safety-critical applications, notwithstanding anyapplications-related information or support that may be provided by TI. Further, Buyers must fully indemnify TI and its representatives against any damages arising out of the use of TI products in such safety-critical applications.TI products are neither designed nor intended for use in military/aerospace applications or environments unless the TI products are specifically designated by TI as military-grade or "enhanced plastic." Only products designated by TI as military-grade meet military specifications. Buyers acknowledge and agree that any such use of TI products which TI has not designated as military-grade is solely at the Buyer's risk, and that they are solely responsible for compliance with all legal and regulatory requirements in connection with such use.TI products are neither designed nor intended for use in automotive applications or environments unless the specific TI products are designated by TI as compliant with ISO/TS 16949 requirements. Buyers acknowledge and agree that, if they use any non-designated products in automotive applications, TI will not be responsible for any failure to meet such requirements.Following are URLs where you can obtain information on other Texas Instruments products and application solutions:Mailing Address: Texas Instruments, Post Office Box 655303, Dallas, Texas 75265Copyright © 2009, Texas Instruments IncorporatedProducts Applications AmplifiersAudio/audioData Converters Automotive /automotive DLP® Products Broadband /broadband DSPDigital Control /digitalcontrol Clocks and Timers /clocks Medical /medical Interface Military/militaryLogic Optical Networking /opticalnetwork Power Mgmt Security /security Microcontrollers Telephony/telephony RFID Video & Imaging /video RF/IF and ZigBee® Solutions/lprfWireless/wireless分销商库存信息: TIMDL-ACIM。
74279245;中文规格书,Datasheet资料

5.1 5.0 4.02012-06-262012-03-292005-12-16SStSStSStSStSMu-Würth Elektronik eiSos GmbH & Co. KGEMC & Inductive SolutionsMax-Eyth-Str. 174638 WaldenburgGermanyTel. +49 (0) 79 42 945 - 0A Dimensions: [mm]F Typical Impedance Characteristics:Test Equipment: E4991A or equivalentF Derating Curve:H1: Classification Reflow Profile for SMT components:H2: Classification Reflow ProfilesProfile FeaturePreheat- Temperature Min (T smin ) - Temperature Max (T smax ) - Time (t s ) from (T smin to T smax )Ramp-up rate (T L to T P )Liquidous temperature (T L )Time (t L ) maintained above T L Peak package body temperature (T p )Time within 5°C of actual peak temperature (t p )Ramp-down rate (T P to T L )Time 25°C to peak temperature Pb-Free Assembly 150°C 200°C60-180 seconds 3°C/ second max.217°C60-150 seconds See Table H320-30 seconds 6°C/ second max.8 minutes max.refer to IPC/JEDEC J-STD-020DH3: Package Classification Reflow TemperaturePB-Free Assembly PB-Free Assembly PB-Free Assembly Package Thickness< 1.6 mm 1.6 - 2.5 mm ≥ 2.5 mmVolume mm³<350260°C 260°C 250°CVolume mm³350 - 2000260°C 250°C 245°CVolume mm³>2000260°C 245°C 245°Crefer to IPC/JEDEC J-STD-020DH Soldering Specifications:I Cautions and Warnings:The following conditions apply to all goods within the product series of WE-CBFof Würth Elektronik eiSos GmbH & Co. KG:General:All recommendations according to the general technical specifications of the data-sheet have to be complied with.The disposal and operation of the product within ambient conditions which probably alloy or harm the component surface has to be avoided.If the product is potted in customer applications, the potting material might shrink during and after hardening. Accordingly to this the product is exposed to the pressure of the potting material with the effect that the ferrite body and termination is possibly damaged by this pressure and so the electrical as well as the mechanical characteristics are endanger to be affected. After the potting material is cured, the ferrite body and termination of the product have to be checked if any reduced electrical or mechanical functions or destructions have occurred.The responsibility for the applicability of customer specific products and use in a particular customer design is always within the authority of the customer. All technical specifications for standard products do also apply for customer specific products.Washing varnish agent that is used during the production to clean the application might damage or change the characteristics of the plating. The washing varnish agent could have a negative effect on the long term function of the product.Direct mechanical impact to the product shall be prevented as the ferrite material of the ferrite body could flake or in the worst case it could break.Product specific:Follow all instructions mentioned in the datasheet, especially:•The solder profile has to be complied with according to the technical reflow soldering specification, otherwise no warranty will be sustai-ned.• Wave soldering is only allowed after evaluation and approval.•All products are supposed to be used before the end of the period of 12 months based on the product date-code, if not a 100% solderabi-lity can´t be warranted.•Violation of the technical product specifications such as exceeding the nominal rated current will result in the loss of warranty.1. General Customer ResponsibilitySome goods within the product range of Würth Elektronik eiSos GmbH & Co. KG contain statements regarding general suitability for certain application areas. These statements about suitability are based on our knowledge and experience of typical requirements concerning the are-as, serve as general guidance and cannot be estimated as binding statements about the suitability for a customer application. The responsibi-lity for the applicability and use in a particular customer design is always solely within the authority of the customer. Due to this fact it is up to the customer to evaluate, where appropriate to investigate and decide whether the device with the specific product characteristics described in the product specification is valid and suitable for the respective customer application or not.2. Customer Responsibility related to Specific, in particular Safety-Relevant ApplicationsIt has to be clearly pointed out that the possibility of a malfunction of electronic components or failure before the end of the usual lifetime can-not be completely eliminated in the current state of the art, even if the products are operated within the range of the specifications.In certain customer applications requiring a very high level of safety and especially in customer applications in which the malfunction or failure of an electronic component could endanger human life or health it must be ensured by most advanced technological aid of suitable design of the customer application that no injury or damage is caused to third parties in the event of malfunction or failure of an electronic component.3. Best Care and AttentionAny product-specific notes, warnings and cautions must be strictly observed.4. Customer Support for Product SpecificationsSome products within the product range may contain substances which are subject to restrictions in certain jurisdictions in order to serve spe-cific technical requirements. Necessary information is available on request. In this case the field sales engineer or the internal sales person in charge should be contacted who will be happy to support in this matter.5. Product R&DDue to constant product improvement product specifications may change from time to time. As a standard reporting procedure of the Product Change Notification (PCN) according to the JEDEC-Standard inform about minor and major changes. In case of further queries regarding the PCN, the field sales engineer or the internal sales person in charge should be contacted. The basic responsibility of the customer as per Secti-on 1 and 2 remains unaffected.6. Product Life CycleDue to technical progress and economical evaluation we also reserve the right to discontinue production and delivery of products. As a stan-dard reporting procedure of the Product Termination Notification (PTN) according to the JEDEC-Standard we will inform at an early stage about inevitable product discontinuance. According to this we cannot guarantee that all products within our product range will always be available. Therefore it needs to be verified with the field sales engineer or the internal sales person in charge about the current product availability ex-pectancy before or when the product for application design-in disposal is considered.The approach named above does not apply in the case of individual agreements deviating from the foregoing for customer-specific products.7. Property RightsAll the rights for contractual products produced by Würth Elektronik eiSos GmbH & Co. KG on the basis of ideas, development contracts as well as models or templates that are subject to copyright, patent or commercial protection supplied to the customer will remain with Würth Elektronik eiSos GmbH & Co. KG.8. General Terms and ConditionsUnless otherwise agreed in individual contracts, all orders are subject to the current version of the “General Terms and Conditions of Würth Elektronik eiSos Group”, last version available at .J Important Notes:The following conditions apply to all goods within the product range of Würth Elektronik eiSos GmbH & Co. KG:分销商库存信息: WURTH-ELECTRONICS 74279245。
RTH14012;中文规格书,Datasheet资料

04-2011, Rev. 0411© 2011 Tyco Electronics Corporation, a TE Connectivity Ltd. company Datasheets and product specificationaccording to IEC 61810-1 and to be usedonly together with the ‘Definitions’ section.Datasheets and product data is subject to theterms of the disclaimer and all chapters ofthe ‘Definitions’ section, available at/definitionsDatasheets, product data, ‘Definitions’ sec-tion, application notes and all specificationsare subject to change.1n 1 pole 16A, 1 form C (CO) or 1 form A (NO) contact n Ambient temperature 105°Cn Sensitive coil 400mWn 5kV/10mm coil-contactn Reinforced insulationn WG version: Product in accordance to IEC 60335-1 Typical applicationsOven control, cooking plate controlApprovalsVDE REG.-Nr. 6106, UL E214025, cCSAus 14385Contact DataContact arrangement 1 form C (CO) or 1 form A (NO) Rated voltage 250VACMax. switching voltage 400VACRated current 16A1)Limiting continuous current, form A/form B 16 / 26ALimiting making current (form A contact)max. 4 s, duty factor 10 % 30ABreaking capacity max. 4000VAContact material AgNi 90/10Frequency of operation, with/without load 360/72000h-1Operate/release time max. 8/6msBounce time max., form A/form B 4/6msContact ratingsType Contact Load Cycles IEC 61810RTH14 A (NO) 10A, 250VAC resistive,105°C 150x103 RTH14 C (CO) 16A, 250VAC resistive, 105°C 10x103 RTH14 B (NC) 26A, 250VAC resistive, 85°C 500 RTH34 A (NO) 10A, 400VAC resistive, 105°C 150x103 RTHH4 A (NO) 10A, 250VAC resistive, 105°C 250x103 UL 508RTH14 A/B (NO/NC) 16A, 250VAC, resistive, 105°C 30x103 RTH34 A (NO) 20A, 250VAC, general purpose, 105°C 6x103 Mechanical endurance >30x106 operations1) Continuous thermal load >10A at 105°C requires reduction of coil power to 64% ofrated power after 100ms Coil DataCoil voltage range 5 to 60VDCOperative range, IEC 61810 90...110% U RTDCoil insulation system according UL1446 class FCoil versions, DC coilCoil Rated Operate Release Coil Rated coil code voltage voltage voltage resistance power VDC VDC VDC Ω±10% mW009 9 6.3 0.9 203 3991) 012 12 8.4 1.2 360 4001) 024 24 16.8 2.4 1440 4001) 1) Continuous thermal load > 10 A at 105°C requires reduction of coil power to 64% ofrated power after 100ms.All figures are given for coil without pre-energization, at ambient temperature +23°C. Other coil voltages on request.Insulation DataInitial dielectric strengthbetween open contacts 1000V rmsbetween contact and coil 5000V rmsClearance/creepagebetween contact and coil ≥10/10mmMaterial group of insulation parts IIIaTracking index of relay base PTI250VPower PCB Relay RTH 105°C 16AF0220-DZV b04-2011, Rev. 0411© 2011 Tyco Electronics Corporation,a TE Connectivity Ltd. companyDatasheets and product specificationaccording to IEC 61810-1 and to be usedonly together with the ‘Definitions’ section.Datasheets and product data is subject to theterms of the disclaimer and all chapters ofthe ‘Definitions’ section, available at/definitionsDatasheets, product data, ‘Definitions’ sec-tion, application notes and all specificationsare subject to change.2Power PCB Relay RTH 105°C 16A (Continued)Other DataMaterial compliance: EU RoHS/ELV, China RoHS, REACH, Halogen contentrefer to the Product Compliance Support Center at/customersupport/rohssupportcenterResistance to heat and fireWG version according EN 60335-1, par.30Ambient temperature -40 to 105°CCategory of environmental protectionIEC 61810 RTII - flux proofVibration resistance (functional)form A/form B contact, 30 to 150Hz 20/5gShock resistance (destructive) 100gTerminal type PCB-THTWeight 14gResistance to soldering heat THTIEC 60068-2-20 270°C/10sPackaging/unit tube/20 pcs., box/500 pcs.PCB layout / terminal assignmentBottom view on solder pinsDimensions16 A, pinning 5 m mS0163-BES0272-BA S0163-BF*) With the recommended PCB hole sizes a gridpattern from 2.5 m m to 2.54 m m can be used.Product code structure Typical product code RT H 3 4 012 WGTypeRT Power PCB Relay RTH 105°C 16AVersionH 16A, pinning 5mm, 105°CContact configuration1 1 form C (CO) contact3 1 form A (NO) contact H 1 form A (NO) contact …High Performance“Contact material4 AgNi 90/10CoilCoil code: please refer to coil versions tableVersionBlank Standard versionWG Product in accordance with IEC 60335-1 (domestic appliances)Product code Version Contact configuration Contact Material Coil Part number RTH14012 16A, 105°C 1 form C (CO) AgNi 90/10 12VDC 8-1415006-1 RTH14012WG contact 1-1415538-1 RTH14024WG 24VDC 9-1415535-4 RTH34012 1 form A (NO) 12VDC 9-1415006-1 RTH34012WG contact 1-1415536-9 RTH34024 24VDC 1415039-1 RTH34024WG 2-1415536-0 RTHH4009WG 16A, 105°C, 9VDC 1-1415540-6 RTHH4012 High Performance 12VDC 8-1415047-1 RTHH4012WG 4-1415536-2 RTHH4024 24VDC 9-1415047-1 This list represents the most common types and does not show all variants covered by this datasheet.分销商库存信息:TE Connectivity / Schrack RTH14012。
YS12S16-0G;中文规格书,Datasheet资料
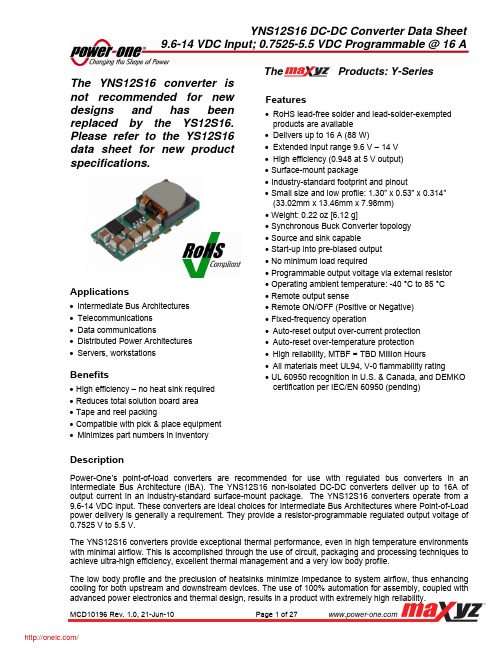
Electrical Specifications (continued)
Conditions: TA=25ºC, Airflow=200 LFM (1 m/s), Vin=12 VDC, Vout = 0.7525 - 5.5V, unless otherwise specified.
PARAMETER INPUT CHARACTERISTICS
YNS12S16 DC-DC Converter Data Sheet 9.6-14 VDC Input; 0.7525-5.5 VDC Programmable @ 16 A
The Products: Y-Series
The YNS12S16 converter is not recommended for new designs and has been replaced by the YS12S16. Please to the YS12S16 data sheet for new product specifications.
FEATURE CHARACTERISTICS
Switching Frequency Output Voltage Programming Range 1 Remote Sense Compensation Turn-On Delay Time With Vin = (Module Enabled, then Vin applied) With Enable (Vin = Vin(nom) applied, then enabled) Rise time ON/OFF Control (Positive Logic) Module Off Module On ON/OFF Control (Negative Logic) Module Off Module On Note: 1. The output voltage should not exceed 5.5V (taking into account both the programming and remote sense compensation). 2. Converter is on if ON/OFF pin is left open. 3. Note that start-up time is the sum of turn-on delay time and rise time.
BQ20Z80ADBT-V110;BQ20Z80DBTG4;BQ20Z80DBT;BQ20Z80DBTR;BQ20Z80DBTRG4;中文规格书,Datasheet资料
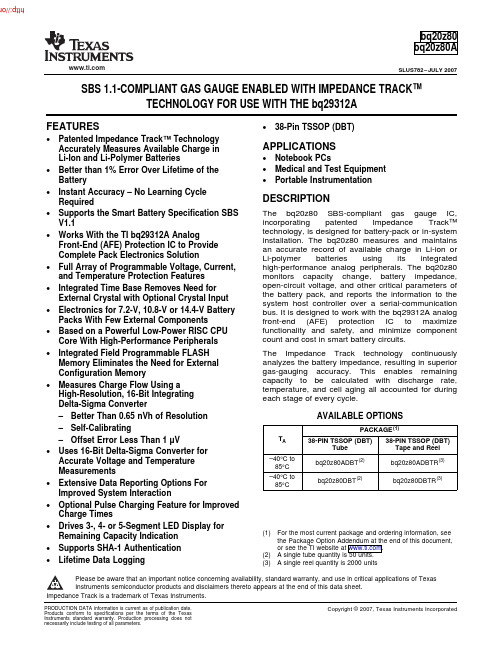
FEATURESAPPLICATIONSDESCRIPTIONbq20z80bq20z80ASLUS782–JULY2007 SBS1.1-COMPLIANT GAS GAUGE ENABLED WITH IMPEDANCE TRACK™TECHNOLOGY FOR USE WITH THE bq29312A•38-Pin TSSOP(DBT)•Patented Impedance Track™TechnologyAccurately Measures Available Charge in•Notebook PCsLi-Ion and Li-Polymer Batteries•Medical and Test Equipment•Better than1%Error Over Lifetime of the•Portable Instrumentation Battery•Instant Accuracy–No Learning CycleRequiredThe bq20z80SBS-compliant gas gauge IC,•Supports the Smart Battery Specification SBSincorporating patented Impedance Track™V1.1technology,is designed for battery-pack or in-system •Works With the TI bq29312A Analoginstallation.The bq20z80measures and maintains Front-End(AFE)Protection IC to Provide an accurate record of available charge in Li-ion orComplete Pack Electronics Solution Li-polymer batteries using its integrated •Full Array of Programmable Voltage,Current,high-performance analog peripherals.The bq20z80monitors capacity change,battery impedance, and Temperature Protection Featuresopen-circuit voltage,and other critical parameters of •Integrated Time Base Removes Need forthe battery pack,and reports the information to the External Crystal with Optional Crystal Inputsystem host controller over a serial-communication •Electronics for7.2-V,10.8-V or14.4-V Battery bus.It is designed to work with the bq29312A analog Packs With Few External Components front-end(AFE)protection IC to maximizefunctionality and safety,and minimize component •Based on a Powerful Low-Power RISC CPUcount and cost in smart battery circuits.Core With High-Performance Peripherals•Integrated Field Programmable FLASH The Impedance Track technology continuouslyanalyzes the battery impedance,resulting in superior Memory Eliminates the Need for Externalgas-gauging accuracy.This enables remaining Configuration Memorycapacity to be calculated with discharge rate,•Measures Charge Flow Using atemperature,and cell aging all accounted for during High-Resolution,16-Bit Integrating each stage of every cycle.Delta-Sigma Converter–Better Than0.65nVh of Resolution AVAILABLE OPTIONS–Self-Calibrating PACKAGE(1)T A–Offset Error Less Than1μV38-PIN TSSOP(DBT)38-PIN TSSOP(DBT)Tube Tape and Reel •Uses16-Bit Delta-Sigma Converter for–40°C toAccurate Voltage and Temperature bq20z80ADBT(2)bq20z80ADBTR(3)85°CMeasurements–40°C tobq20z80DBT(2)bq20z80DBTR(3)•Extensive Data Reporting Options For85°CImproved System Interaction•Optional Pulse Charging Feature for ImprovedCharge Times•Drives3-,4-or5-Segment LED Display for(1)For the most current package and ordering information,seeRemaining Capacity Indicationthe Package Option Addendum at the end of this document,or see the TI website at .•Supports SHA-1Authentication(2)A single tube quantity is50units.•Lifetime Data Logging(3)A single reel quantity is2000unitsPlease be aware that an important notice concerning availability,standard warranty,and use in critical applications of TexasInstruments semiconductor products and disclaimers thereto appears at the end of this data sheet.Impedance Track is a trademark of Texas Instruments.PRODUCTION DATA information is current as of publication date.Copyright©2007,Texas Instruments Incorporated Products conform to specifications per the terms of the TexasInstruments standard warranty.Production processing does notnecessarily include testing of all parameters. SYSTEM DIAGRAMXCK1 / VSSAFIL TVDDASR2SR1VSSAVSSATNC - No internal connectionbq20z80bq20z80ASLUS782–JULY2007These devices have limited built-in ESD protection.The leads should be shorted together or the device placed in conductive foam during storage or handling to prevent electrostatic damage to the MOS gates.TSSOP(DBT)(TOP VIEW)2Submit Documentation Feedbackbq20z80bq20z80ASLUS782–JULY2007 TERMINAL FUNCTIONSTERMINALI/O(1)DESCRIPTION1VIN I Voltage measurement input from the AFE2TS1I1st Thermistor voltage input connection to monitor temperature3TS2I2nd Thermistor voltage input connection to monitor temperature4PU O Output to pull up the PRES pin for system detection5PRES I Active low input to sense system insertion and typically requires additional ESD protection6SCLK I/OD Communication clock to the AFE7SAFE O Active high output to enforce additional level of safety protection;e.g.,fuse blow.(Inverse of pin12) 8VDDD P Positive supply for digital circuitry and I/O pinsBackup power to the bq20z80data registers during periods of low operating voltage.RBI accepts a 9RBI Pstorage capacitor or a battery input.10SDATA I/O Data transfer to and from the AFE12SAFE O Active low output to enforce additional level of safety protection;e.g.,fuse blow.(Inverse of pin7) 13NC–Not used—leave floating14NC–Not used—leave floating15SMBC I/OD SMBus clock open-drain bidirectional pin used to clock the data transfer to and from the bq20z80 16SMBD I/OD SMBus data open-drain bidirectional pin used to transfer address and data to and from the bq20z80Display control for the LEDs.This pin is typically connected to bq29312A REG via a100-kΩresistor 17DISP Iand a push-button switch to VSSD.Active low input to detect secondary protector output status and allows the bq20z80to report the 18PFIN Istatus of the2nd level protection output20LED5O LED5display segment that drives an external LED depending on the firmware configuration21LED4O LED4display segment that drives an external LED depending on the firmware configuration22LED3O LED3display segment that drives an external LED depending on the firmware configuration23LED2O LED2display segment that drives an external LED depending on the firmware configuration24LED1O LED1display segment that drives an external LED depending on the firmware configuration25XALERT I Input from bq29312A XALERT output.26MRST I Master reset input that forces the device into reset when held highConnections for a small-value sense resistor to monitor the battery charge-and discharge-current 27SR2IAflowConnections for a small-value sense resistor to monitor the battery charge-and discharge-current 28SR1IAflow31VDDA P Positive supply for analog circuitryAnalog input connected to the external PLL filter components which are a150-pF capacitor to V SSA, 32FILT IA in parallel with a61.9-kΩresistor and a2200-pF capacitor in series.Place these components asclose as possible to the bq20z80to ensure optimal performance.32.768-kHz crystal oscillator output pin or connected to a100-kΩ,50-ppm or better resistor if the33XCK2/ROSC Ointernal oscillator is used.34XCK1/VSSA I32.768-kHz crystal oscillator input pin or connected to VSSA if the internal oscillator is used35CLKOUT O32.768-kHz output for the bq29312.This pin should be directly connected to the AFE.36,37NC-Not used—leave floating11,19,38VSSD P Negative supply for digital circuitry29,30VSSA P Negative supply for analog circuitry.(1)I=Input,IA=Analog input,I/O=Input/output,I/OD=Input/Open-drain output,O=Output,OA=Analog output,P=Power3Submit Documentation FeedbackABSOLUTE MAXIMUM RATINGSELECTRICAL CHARACTERISTICSbq20z80bq20z80ASLUS782–JULY 2007over operating free-air temperature range (unless otherwise noted)(1)RANGEV DDA and V DDD relative to V SS (2)Supply voltage range –0.3V to 4.1V V (IOD)relative to V SS (2)Open-drain I/O pins–0.3V to 6V V I relative to V SS (2)Input voltage range to all other pins –0.3V to VDDA +0.3VT A Operating free-air temperature range –40°C to 85°C T stg Storage temperature range–65°C to 150°C(1)Stresses beyond those listed under absolute maximum ratings may cause permanent damage to the device.These are stress ratings only,and functional operation of the device at these or any other conditions beyond those indicated under recommended operating conditions is not implied.Exposure to absolute-maximum-rated conditions for extended periods may affect device reliability.(2)V SS refers to the common node of V (SSA)and V (SSD).V DD =3V to 3.6V,T A =–40°C to 85°C (unless otherwise noted)PARAMETERTEST CONDITIONS MIN TYP MAX UNIT V DD Supply voltageVDDA and VDDD 33.3 3.6V No flash programming 350(1)I DDOperating mode currentμA bq20z80+bq29312A 375Sleep mode8(1)I (SLP)Low-power storage mode current μA bq20z80+bq29312A 28Shutdown Mode 0.1(1)I (SLP)Shutdown CurrentμAbq20z80+bq29312A 0.1Output voltage low SMBC,SMBD,SDATA,SCLK,SAFE,I OL =0.5mA 0.4V SAFE,PU V OLLED1–LED5I OL =10mA 0.4V V OH Output high voltage,SMBC,SMBD,SDATA,SCLK,SAFE,I OH =–1mAV DD –0.5V SAFE,PUV ILInput voltage low SMBC,SMBD,SDATA,SCLK,XALERT,–0.30.8V PRES,PFIN DISP–0.30.8V V IHInput voltage high SMBC,SMBD,SDATA,SCLK,XALERT,26V PRES,PFIN DISP2V DD +0.3V C INInput capacitance5pF V (AI1)Input voltage range VIN,TS1,TS2V SS –0.30.8x V DDV V (AI2)Input voltage range SR1,SR2V SS –0.250.25Z (AI1)Input impedance SR1,SR20V–1V 2.5M ΩZ (AI2)Input impedance VIN,TS1,TS20V–1V8M Ω(1)This value does not include the bq29312A4Submit Documentation FeedbackPOWER-ON RESET2.102.152.202.252.302.352.402.452.50T A - Free-Air Temperature - °C- N e g a t i v e G o i n g I n p u t T h r e s h o l d V o l t a g e - VPOWER ON RESET BEHAVIORvsFREE-AIR TEMPERATUREV I T V h y s - H y s t e r i s i s V o l t a g e - m VINTEGRATING ADC (Coulomb Counter)CHARACTERISTICSPLL SWITCHING CHARACTERISTICSOSCILLATORbq20z80bq20z80ASLUS782–JULY 2007V DD =3V to 3.6V,T A =–40°C to 85°C (unless otherwise noted)PARAMETERTEST CONDITIONS MIN TYP MAX UNIT V IT–Negative-going voltage input 2.1 2.3 2.5V V HYSPower-on reset hysteresis50150200mVV DD =3V to 3.6V,T A =–40°C to 85°C (unless otherwise noted)PARAMETERTEST CONDITIONSMIN TYPMAX UNIT V (SR)Input voltage range,V (SR2)and V (SR1)V (SR)=V(SR2)–V(SR1)–0.250.25V V (SROS)Input offset1μVINLIntegral nonlinearity error0.004%0.019%V DD =3V to 3.6V,T A =–40°C to 85°C (unless otherwise noted)PARAMETERTEST CONDITIONSMIN TYP MAXUNIT t (SP)Start-up time(1)0.5%frequency error25ms(1)The frequency error is measured from the trimmed frequency of the internal system clock which is 128oscillator frequency,nominally 4.194MHz.V DD =3V to 3.6V,T A =–40°C to 85°C (unless otherwise noted)PARAMETERTEST CONDITIONSMIN TYP MAX UNITROSC =100k Ω–2%0.25%2%f (exo)Frequency error from 32.768kHzROSC =100k Ω,V DD =3.3V –1%0.25%1%XCK1=12-pF XTAL–0.25%0.25%ROSC =100k Ω250μs f (sxo)Start-up time(1)XCK1=12-pF XTAL200ms(1)The start-up time is defined as the time it takes for the oscillator output frequency to be within 1%of the specified frequency.5Submit Documentation FeedbackDATA FLASH MEMORY CHARACTERISTICSREGISTER BACKUPbq20z80bq20z80ASLUS782–JULY 2007V DD =3V to 3.6V,T A =–40°C to 85°C (unless otherwise noted)PARAMETERTEST CONDITIONS MIN TYP MAX UNIT t DRData retentionSee (1)10Years Flash programming write-cyclesSee (1)20,000Cyclest (WORDPROG)Word programming time See (1)2ms I (DDPROG)Flash-write supply currentSee(1)815mA(1)Specified by design.Not production testedV DD =3V to 3.6V,T A =–40°C to 85°C (unless otherwise noted)PARAMETERTEST CONDITIONSMINTYP MAX UNIT I (RBI)RBI data-retention input current V (RBI)>3V,V DD <V IT10100nA V (RBI)RBI data-retention voltage (1)1.3V(1)Specified by design.Not production tested.6Submit Documentation FeedbackSMBus TIMINGSPECIFICATIONSbq20z80bq20z80ASLUS782–JULY 2007V DD =3V to 3.6V,T A =–40°C to 85°C (unless otherwise noted)PARAMETERTEST CONDITIONSMIN TYP MAX UNIT f SMB SMBus operating frequency Slave mode,SMBC 50%duty cycle 10100kHzf MAS SMBus master clock frequency Master mode,no clock low slave extend51.2t BUF Bus free time between start and stop 4.7t HD:STA Hold time after (repeated)start 4μst SU:STA Repeated start setup time 4.7t SU:STO Stop setup time 4Receive mode 0t HD:DAT Data hold time Transmit mode 300nst SU:DAT Data setup time 250t TIMEOUT Error signal/detect See(1)2535ms t LOW Clock low period 4.7μs t HIGH Clock high periodSee (2)450t LOW:SEXT Cumulative clock low slave extend time See (3)25ms t LOW:MEXT Cumulative clock low master extend time See(4)10t F Clock/data fall time (V ILMAX –0.15V)to (V IHMIN +0.15V)300ns t R Clock/data rise time0.9VDD to (VILMAX –0.15V)1000(1)The bq20z80times out when any clock low exceeds t TIMEOUT .(2)t HIGH:MAX .is minimum bus idle time.SMBC =1for t >50μs causes reset of any transaction involving the bq20z80that is in progress.(3)t LOW:SEXT is the cumulative time a slave device is allowed to extend the clock cycles in one message from initial start to the stop.(4)t LOW:MEXT is the cumulative time a master device is allowed to extend the clock cycles in one message from initial start to the stop.SMBus TIMING DIAGRAM7Submit Documentation FeedbackFEATURE SETPrimary (1st Level)Safety FeaturesSecondary (2nd Level)Safety FeaturesCharge Control Featuresbq20z80bq20z80ASLUS782–JULY 2007NOTEThe bq20z80-V102is designed to work with the bq29312A AFE.The bq20z80features are only available with the bq29312A..The bq20z80supports a wide range of battery and system protection features that care easily configured.The primary safety features includes:•Battery cell over/undervoltage protection •Battery pack over/undervoltage protection •2independent charge overcurrent protection •3independent discharge overcurrent protection •Short circuit protection•Overtemperature protection •Host watchdogThe secondary safety features of the bq20z80can be used to indicate more serious faults via the SAFE (pin 7)and SAFE (pin 12)pins.These pins can be used to blow a in-line fuse to permanently disable the battery pack from charging or discharging.The secondary safety features includes:•Safety over voltage •Battery cell imbalance•2nd level protection IC input •Safety overcurrent•Safety overtemperature •Open thermistor•Charge FET and 0Volt Charge FET fault •Discharge FET fault•Fuse blow failure detection •AFE communication error •Internal flash data errorThe bq20z80charge control features includes:•Report the appropriate charging current needed for constant current charging and the appropriate charging voltage needed for constant voltage charging to a smart charger using SMBus broadcasts.•Determines the chemical state of charge of each battery cell using Impedance Track™and can reduce the charge difference of the battery cells in fully charged state of the battery pack gradually using cell balancing algorithm during charging.This prevents fully charged cells from overcharging causing excessive degradation and also increases the usable pack energy by preventing to early charge termination •supports pre-charging/zero-volt charging •support fast charging •supports pulse charging •detects charge termination•report charging faults and also indicate charge status via charge and discharge alarms.8Submit Documentation FeedbackGas GaugingLED DisplayLifeTime Data Logging FeaturesAuthenticationPower ModesCONFIGURATIONOscillator Functionbq20z80bq20z80ASLUS782–JULY2007 FEATURE SET(continued)The bq20z80uses the Impedance Track™Technology to measure and calculate the available charge in battery cells.The achievable accuracy is better than the coulomb counting method over the lifetime of the battery and there is no full charge discharge learning cycle required.See Theory and Implementation of Impedance Track Battery Fuel-Gauging Algorithm application note (SLUA364)for further details.The bq20z80can drive3-,4-,or5-segment LED display for remaining capacity indication.The bq20z80offers a lifetime data logging array,where all important measurements are stored for warranty and analysis purposes.The data monitored includes:•Lifetime maximum temperature•Lifetime minimum temperature•Lifetime maximum battery cell voltage•Lifetime minimum battery cell voltage•Lifetime maximum battery pack voltage•Lifetime minimum battery pack voltage•Lifetime maximum charge current•Lifetime maximum discharge current•Lifetime maximum charge power•Lifetime maximum discharge power•Lifetime maximum average discharge current•Lifetime maximum average discharge power•Lifetime average temperatureThe bq20z80supports authentication by the host using SHA-1.The bq20z80supports3different power modes to reduce power consumption:•In Normal Mode,the bq20z80performs measurements,calculations,protection decision,data update in1 second intervals.Between these intervals,the bq20z80is in a reduced power stage.•In Sleep Mode,the bq20z80performs measurements,calculations,protection decision,data update in adjustable time intervals.Between these intervals,the bq20z80is in a reduced power stage.•In Shutdown Mode the bq20z80is completely disabled.The oscillator of the bq20z80can be set up for internal or external operation.On power up,the bq20z80 automatically attempts to start the internal oscillator.If a100-kΩresistor is not connected to ROSC(pin33), then it attempts to start the oscillator using an external32.768-kHz crystal.NOTEInstall either the100-kΩROSC resistor or the12-pF,32.768-kHz crystal.Do notinstall both.9Submit Documentation FeedbackSystem Present OperationBATTERY PARAMETER MEASUREMENTSCharge and Discharge CountingVoltageCurrentAuto CalibrationTemperatureCOMMUNICATIONSSMBus On and Off Statebq20z80bq20z80ASLUS782–JULY 2007FEATURE SET (continued)The performance of the internal oscillator depends on the tolerance of the 100-k Ωresistor between RSOC (pin 33)and VSSA (pin 34).Choose a resistor with a tolerance of ±0.1%,and 50-ppm or better temperature drift.Place this resistor as close as possible to the bq20z80.If a 12-pF crystal is used,place it as close as possible to the XCK1(pin 34)and XCK2(pin 33)pins.If not properly implemented,the PCB layout in this area can degrade oscillator performance.The bq20z80pulls the PU pin high periodically (1s).Connect this pin to the PRES pin of the bq20z80via a resistor of approximately 5k Ω.The bq20z80measures the PRES input during the PU-active period to determine its state.If PRES input is pulled to ground by external system,the bq20z80detects this as system present.The bq20z80uses an integrating delta-sigma analog-to-digital converter (ADC)for current measurement,and a second delta-sigma ADC for individual cell and battery voltage,and temperature measurement.The integrating delta-sigma ADC measures the charge/discharge flow of the battery by measuring the voltage drop across a small-value sense resistor between the SR1and SR2pins.The integrating ADC measures bipolar signals from -0.25V to 0.25V.The bq20z80detects charge activity when V SR =V (SR1)-V (SR2)is positive and discharge activity when V SR =V (SR1)-V (SR2)is negative.The bq20z80continuously integrates the signal over time,using an internal counter.The fundamental rate of the counter is 0.65nVh.The bq20z80updates the individual series cell voltages through the bq29312A at one second intervals.The bq20z80configures the bq29312A to connect the selected cell,cell offset,or bq29312A VREF to the CELL pin of the bq29312A,which is required to be connected to VIN of the bq20z80.The internal ADC of the bq20z80measures the voltage,scales and calibrates it appropriately.This data is also used to calculate the impedance of the cell for the Impedance Track™gas-gauging.The bq20z80uses the SR1and SR2inputs to measure and calculate the battery charge and discharge current using a 5m Ωto 20m Ω(typical)sense resistor.The bq20z80provides an auto-calibration feature to cancel the voltage offset error across SR1and SR2for maximum charge measurement accuracy.The bq20z80performs auto-calibration when the SMBus lines stay low continuously for a minimum of 5s.The bq20z80TS1and TS2inputs,in conjunction with two identical NTC thermistors (default are Semitec 103AT),measure the battery environmental temperature.The bq20z80can also be configured to use its internal temperature sensor.The bq20z80uses SMBus v1.1with Master Mode and package error checking (PEC)options per the SBS specification.The bq20z80detects an SMBus off state when SMBC and SMBD are logic-low greater than an adjustable period of time.Clearing this state requires either SMBC or SMBD to transition high.Within 1ms,the communication bus is available.10Submit Documentation Feedback分销商库存信息:TIBQ20Z80ADBT-V110BQ20Z80DBTG4BQ20Z80DBT BQ20Z80DBTR BQ20Z80DBTRG4。
YM12S05-G;中文规格书,Datasheet资料

Turn-On Delay Time Full resistive load With Vin = (Converter Enabled, then Vin applied) From Vin = Vin(min) to Vo=0.1* Vo(nom) With Enable (Vin = Vin(nom) applied, then enabled) From enable to Vo= 0.1*Vo(nom) Rise time (Full resistive load) ON/OFF Control 2 Converter Off Converter On
Description Power-One’s point-of-load converters are recommended for use with regulated bus converters in an Intermediate Bus Architecture (IBA). The YM12S05 non-isolated DC-DC converters deliver up to 5A of output current in an industry-standard surface-mount package. Operating from a 9.6-14 VDC input, the YM12S05 converters are ideal choices for Intermediate Bus Architectures where Point-of-Load power (POL) delivery is generally a requirement. They provide an extremely tight regulated programmable output voltage of 0.7525 V to 5.5 V. The Y-Series converters provide exceptional thermal performance, even in high temperature environments with minimal airflow. No derating is required up to 85 C (up to 70 C for 5 V and 3.3 V outputs), even without airflow at natural convection. This is accomplished through the use of advanced circuitry, packaging and processing techniques to achieve a design possessing ultra-high efficiency, excellent thermal management and a very low body profile. The low body profile and the preclusion of heat sinks minimize impedance to system airflow, thus enhancing cooling for both upstream and downstream devices. The use of 100% automation for assembly, coupled with advanced power electronics and thermal design, results in a product with extremely high reliability.
VLS252012T-2R2M1R3;VLS252012T-1R0N1R7;VLS252012T-1R5N1R4;中文规格书,Datasheet资料

SMD Inductors(Coils)For Power Line(Wound, Magnetic Shielded)VLS Series VLS252012FEATURES •Miniature sizeMount area: 2.5×2mm Height: 1.2mm max.•Generic use for portable DC to DC converter line.•High magnetic shield construction should actualize high resolution for EMC protection.•Available for automatic mounting in tape and real package.•The products do not contain lead and support lead-free soldering.APPLICATIONSDVCs, DSCs, PDAs, LCD displays, cellular phones, HDDs, etc.SHAPES AND DIMENSIONSRECOMMENDED PC BOARD PATTERNELECTRICAL CHARACTERISTICS∗Rated current: Value obtained when current flows and the temperature has risen to 40°C or when DC current flows and the nominal value of inductance has fallen by 30%, whichever is smaller.•Operating temperature range: –40 to +105°C (Including self-temperature rise)TYPICAL ELECTRICAL CHARACTERISTICSINDUCTANCE vs. DC SUPERPOSITION CHARACTERISTICS VLS252012T -R47N2R1VLS252012T -1R0N1R7Conformity to RoHS DirectivePart No.Inductance (µH)Inductance tolerance (%)Test frequency (MHz)DC resistance (Ω)Rated current(A)Based on inductance change Based ontemperature rise typ.max.typ.max.typ.VLS252012T -R47N2R10.47±3010.0560.047 3.3 3.7 2.2VLS252012T -1R0N1R71±3010.0880.073 2.4 2.7 1.8VLS252012T -1R5N1R4 1.5±3010.1260.1052 2.2 1.5VLS252012T -2R2M1R3 2.2±2010.1550.129 1.82 1.3VLS252012T -3R3MR99 3.3±2010.2720.227 1.4 1.61VLS252012T -4R7MR81 4.7±2010.4060.338 1.2 1.30.8VLS252012T -6R8MR66 6.8±2010.6120.510.99 1.10.66VLS252012T -100MR5910±2010.7560.630.810.90.59•Conformity to RoHS Directive: This means that, in conformity with EU Directive 2002/95/EC, lead, cadmium, mercury, hexavalent chromium, and specificbromine-based flame retardants, PBB and PBDE, have not been used, except for exempted applications.TYPICAL ELECTRICAL CHARACTERISTICSINDUCTANCE vs. DC SUPERPOSITION CHARACTERISTICS VLS252012T -1R5N1R4VLS252012T -2R2M1R3VLS252012T -3R3MR99VLS252012T -4R7MR81VLS252012T -6R8MR66VLS252012T -100MR59TEST CIRCUIT分销商库存信息:TDKVLS252012T-2R2M1R3VLS252012T-1R0N1R7VLS252012T-1R5N1R4 VLS252012T-R47N2R1VLS252012T-4R7MR81VLS252012T-3R3MR99 VLS252012T-6R8MR66VLS252012T-100MR59。
29123;中文规格书,Datasheet资料

Web Site: Forums: Sales: sales@Technical: support@Office: (916) 624-8333Fax: (916) 624-8003Sales: (888) 512-1024Tech Support: (888) 997-8267 Hitachi® HM55B Compass Module (#29123)General DescriptionThe Hitachi HM55B Compass Module is a dual-axis magnetic field sensor that can add a sense of direction to your next electronic or robotic project. The sensing device on the Compass Module is a Hitachi HM55B chip. An onboard regulator and resistor protection make the 3 volt HM55B chip compatible with 5 volt BASIC Stamp® microcontroller supply and signal levels. The Compass Module also makes all the power and signal connections on the tiny surface mount HM55B chip accessible in a breadboard-friendly 0.3 inch wide 6-pin DIP package. Acquiring measurements from the module is made easy with the BASIC Stamp 2 microcontroller's SHIFTIN and SHIFTOUT commands, which are designed for synchronous serial communication with chips like the HM55B.Features•Sensitive to microtesla (µT) variations in magnetic field strength•Simplifies direction by resolving magnetic field measurements into two component axes•Good for 6-bit (64-direction) resolution measurements after software calibration•Only 30 to 40 ms between start measurement and data-ready•Built-in resistor protection for data pins eliminates bus conflict risks•Compact and breadboard-friendly 0.3 inch, 6-pin DIP package•Compatible with all BASIC Stamp, Javelin Stamp and SX microcontrollers•Makes communication and direction calculations especially easy with the PBASIC commands SHIFTOUT, SHIFTIN, and ATN for the BASIC Stamp 2 series of microcontrollersApplication Ideas•Mobile robot direction sensor•Handheld electronic compass•Weathervane indicator for remote weather stations•Audible compass for the vision impaired•Automotive electronic compassQuick Start Circuit29123Downloading the Example ProgramsThe example programs featured in the Source Code section (pages 12 - 24) are also available for download from the Hitachi HM55B Compass Module product page at .√Go to /detail.asp?product_id=29123.√Click the "Hitachi HM55B Compass Module Source Code (.zip)" link and download the file.√Unzip to a convenient folder.Connecting and Testing the Compass ModuleThis section contains connection and test instructions for the Parallax BASIC Stamp 2® series and Ubicom SX microcontrollers.BASIC Stamp 2 SeriesUse the instructions in this section to test your Hitachi HM55B Compass Module if you have a BASIC Stamp 2, 2sx, 2e, 2p, 2pe, or 2px. The goal of this first test is to verify that the module is connected, functional, and communicating properly with the BASIC Stamp. Since this first test is run before calibration, there may sizeable differences between magnetic compass directions and what the module reports.√Build the circuit shown on page 1.√Place your board on a level surface away from magnetic field disturbances. Common culprits include magnetic compasses, motors, bar/horseshoe/ring magnets, and large metal objects.Also, make sure your programming cable and power cords do not wrap around or pass near the sensor.√Open TestHm55bCompass.bs2 with the BASIC Stamp Editor (v2.0 or later). Update the $STAMP directive if needed, then run the program.√Test your Compass Module for direction detection as shown below, comparing your degree measurements to the compass legend in the figure.CalibrationThe calibration and test-calibration programs will compensate for the effects of magnetic fields that may be resident to the module PCB and the carrier board it's mounted on, as well as nearby jumper wires and batteries. It also corrects for the HM55B chip's axis sensitivity, offset and skew errors, if any. You will need a magnetic compass to verify magnetic north as a reference. After calibration, the Hitachi HM55B Compass Module should be able to accurately discern 64 or more angles, referenced to magnetic north.√Make a printout of the 16-segment compass shown below.√Align the printout to magnetic north with the aid of the magnetic compass.√Affix the aligned printout to your work surface.√Make sure to set the magnetic compass well away from the printout before continuing.√Align the Compass Module to magnetic north by lining up the edge of your carrier board with the dashed line that passes through the 0° mark.The program CalibrateHm55bCompass.bs2 will prompt you to take a first series of measurements at 90°increments to gather compass offsets. Then, you will take a second series of measurements at 22.5° increments to gather information for a linear interpolation table. Both sets of measurements will be saved in the BASIC Stamp EEPROM so that the TestCalibratedHM55BCompass.bs2 program can use them.√Run CalibrateHm55bCompass.bs2.√Make sure to click the Transmit windowpane shown in this figure before following and responding to the Debug Terminal prompts.√When you have completed the calibration process, run TestCalibratedHM55BCompass.bs2. Array ArrayCalibrateHM55BCompass.bs2 writes the calibration values to EEPROM, so they will be available for TestCalibratedHM55BCompass.bs2 even after the power is reset. TestCalibratedHM55BCompass.bs2 will display the angle from north in both binary radians (brads) and degrees. When you run this program after calibration, the accuracy of the degree measurements should be significantly improved. While degrees parse a full circle into 360 equal segments, brads parse the circle into 256 segments. North is still 0, but the brad measurements for east, south and west are 64, 128, and 192 respectively. In applications where accuracy is the top priority, use the brad measurements because they introduce one less rounding error into the measurement. Further accuracy improvements can be realized if both the calibration and calibration-test programs are modified to average multiple measurements.Testing SensitivityThe Compass Module operates by comparing the magnetic field intensities sensed by its two perpendicular axes. The magnetic field strength corresponding to a measurement of 1 should resolve to somewhere between 1 and 1.6 µT. To find out how many microteslas per unit each axis reports with your particular Compass Module, use TestCalibratedHM55BCompass.bs2. Start by finding the maximum possible axis measurement. Do this by orienting the x-axis to magnetic north, then tilt up and down until you find the highest value. Compare this to the total magnetic field intensity in your area. In thecontinental US, you can find a Total Intensity Map on this page:/articles/geology/a_geomag.html.Make sure to divide their nanotesla (nT) values by 1000 to convert to microteslas (µT).SX MicrocontrollerWhile this connection and testing procedure is set up for the SX-28, it should work on any of the SX series of microcontrollers with a simple update of the device directive. Make sure you are using the SX-Key v3.1 IDE v3.10 or newer, along with the SX-Key and an SX-28 chip.√Build the circuit shown below.√Open TestHm55bCompass.SXB with the SX-Key IDE.√Save, Compile, and Debug (CTRL-S, A, D)√Click the Debug window's Poll button. If the Watch window is not visible, also click the Watch button to bring it to the foreground.√Monitor the Watch window as you point the module in various directions.√Use arctan(-y/x) to calculate the heading angle, counterclockwise from north.Resources and DownloadsCheck out the Hitachi HM55B Compass Module product page for example programs, the HM55B datasheet, and more:/detail.asp?product_id=29123Theory of OperationThe Hitachi HM55B Compass Module has two axes, x and y. Each axis reports the strength of the magnetic field's component parallel to it. The x-axis reports (field strength) × cos(θ), and the y-axis reports the (field strength) × sin(θ). To resolve θ into a clockwise angle from north, use arctan(-y/x), which in PBASIC 2.5 is x ATN -y. The ATN command returns the angle in binary radians. To convert to degrees with PBASIC, just apply */ 360 to the variable storing the binary radian measurement.The Hitachi HM55B chip on the Compass Module reports its x and y axis measurements in terms of microteslas (µT) in 11-bit signed values. The HM55B is designed to return a value of 1 for a north magnetic field of 1 µT parallel to one of its axes. If the magnetic field is south, the value will be -1. Keep in mind that these are nominal values. According to the HM55B datasheet, the actual µT value for a measurement of 1 could range anywhere from 1 to 1.6 µT. Also keep in mind that a negative 11-bit value will not appear negative in a word variable unless a mask is applied. For example, when bit-10 is 1, bits 11 to 15 are also changed to 1 with a mask in the test and calibration programs.The microcontroller connected to the HM55B must control its enable and clock inputs and use synchronous serial communication to get the axis measurements from its data input and data output pins. For example, a BASIC Stamp 2 can be programmed to control the Compass Module's enable lines with HIGH/LOW and send values that reset the device and start a measurement with SHIFTOUT commands. The SHIFTOUT command controls the Compass Module’s clock input as it sends data bit values to its data input. The converse of SHIFTOUT is SHIFTIN, which also controls the device's clock input as it collects data bits sent by the device's data output pin.It takes the HM55B 30 to 40 ms to complete a given measurement. The microcontroller can either perform other tasks during this time or poll until the measurement is complete. The polling is a combination of SHIFTOUT commands that request the status, and SHIFTIN commands that acquire the status. When the SHIFTIN receives status flags indicating that the measurement is complete, a second and third SHIFTIN command can then store the 11-bit x and y axis measurements in variables.Precautions• Do not apply voltages to the device that are outside the values stated in the Pin Definitions and Ratings section.•Do not operate or store the Compass Module near sources of strong magnetic fields. Strong magnetic fields can be created by bar and ring magnets, electric motors, and other coil elements such as solenoids, relays, and large inductors.• Do not apply magnetic fields in excess of 300 µT to the Compass Module. Magnetic fields stronger than 300 µT can permanently damage the sensor.•Mount the Compass Module as far away as possible from magnetic field disturbances. These include magnets (including compass needles), motors, power cords, coils, metal boxes, and sometimes the ground.angle θ= arctan(-y/x)SpecificationsSymbol Quantity MinimumTypical MaximumUnitsB SE Sensitivity † 1.0 1.6 µT/lsbH Linear measurement range † -180 180 µT d θIndividual axis offset36°T CONV Conversion time † 30 40 ms T OPE Operating temperature 070 °C† From Hitachi HM55B DatasheetPin Definitions and RatingsSymbol QuantityMinimum Typical Maximum UnitsVcc Supply Voltage 4.8 5.0 5.2 VIcc(Ave) Average active supply current * 5 7mA Icc(Pk) Peak instantaneous current ** 30 45 mA Icc(Sb) Standby supply current 2 3 mA GND Ground reference connection 0 V V OH Signal high transmit (Dout) Vcc × 0.9 Vcc Vcc + 0.5 V V OL Signal low transmit (Dout) GND - 0.3 GND Vcc × 0.15 V V IH Signal high receive (/En, CLK, Din) Vcc × 0.8 Vcc Vcc + 0.3 V V ILSignal low receive (/En, CLK, Din)- 0.3GNDVcc × 0.12V** Typical duration is 5 µs(1) Din - Serial data input (2) Dout - Serial data output (3) GND - Ground -> 0 V(4) CLK - Synchronous clock input (5) /EN - Active-low device enable (6) Vcc -+5 V power input29123Connection DiagramsThe 3-wire interface is recommended for most applications. While all the connections shown here are to individual I/O pins, the /EN pin is the only one that needs a dedicated I/O pin. The Din/Dout pins can share a line with other synchronous serial devices, and likewise with CLK.The Din and Dout pins do not have to be tied together; they can also be controlled individually. This makes it possible to share communication lines with other synchronous serial devices that have dedicated input and output lines.Command SetThese commands are shifted-out to the Compass Module.Binary ValueQuantity0000 Reset device 0001 Start measurement 0011Report measurement status (and transmit the measurement if it's ready)4-wire interface3-wire interfaceStatus FlagsThe Compass Module will reply to the report measurement status command with one of these values.Binary Value QuantityBits - 3210 3 and 2 indicate measurement completion, 1 and 0 indicate measurement errors 1100 11 -> Measurement completed; 00 -> no errors00XX Measurement still in progress, or the device has been reset.XX11 /EN did not receive low-high-low signal between start and report commandsCommunication ProtocolAll values transmitted to and received from the Compass Module are most significant bit first, with the bit value valid after the clock signal's rising edge. For the BASIC Stamp 2, this means set the SHIFTOUT command’s Mode argument to MSBFIRST, and the SHIFTIN command’s Mode argument to MSBPOST.To reset the HM55B, take /EN from high to low, and shift-out %0000, then set /EN high again.After reset, start a measurement by taking /EN low again, then shift-out %1000. Leave /EN low until checking the measurement status.To check the measurement status, start by sending a positive pulse to /EN. Then, shift-out %1100, and shift-in the status flags. While the measurement is in progress, the end flag and error flag will both be 00. The compass Module may be polled for status repeatedly until the measurement is complete, at which point the end flag will change to 11. Upon receipt of %1100, discontinue polling. Leave /EN low, and move on to shifting-in the x and y-axis values.Shifting-in the x and y-axis values is a simple matter of shifting-in 11 bits for the x-axis measurement followed by 11 more bits for the y-axis measurement. After completing the y-axis shift-in, set the /EN pin high again.Module Dimensions分销商库存信息: PARALLAX 29123。
LTC4446EMS8E#PBF;LTC4446EMS8E#TRPBF;LTC4446IMS8E#PBF;LTC4446IMS8E#TRPBF;中文规格书,Datasheet资料
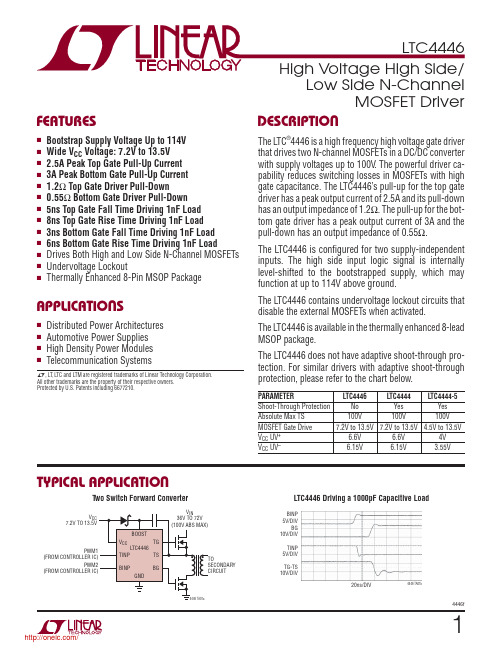
14446fTYPICAL APPLICATIONFEATURESAPPLICATIONSDESCRIPTIONLow Side N-ChannelMOSFET DriverThe L TC ®4446 is a high frequency high voltage gate driver that drives two N-channel MOSFETs in a DC/DC converter with supply voltages up to 100V . The powerful driver ca-pability reduces switching losses in MOSFETs with high gate capacitance. The L TC4446’s pull-up for the top gate driver has a peak output current of 2.5A and its pull-down has an output impedance of 1.2Ω. The pull-up for the bot-tom gate driver has a peak output current of 3A and the pull-down has an output impedance of 0.55Ω.The L TC4446 is confi gured for two supply-independent inputs. The high side input logic signal is internally level-shifted to the bootstrapped supply, which may function at up to 114V above ground.The L TC4446 contains undervoltage lockout circuits that disable the external MOSFETs when activated. The L TC4446 is available in the thermally enhanced 8-lead MSOP package.The L TC4446 does not have adaptive shoot-through pro-tection. For similar drivers with adaptive shoot-through protection, please refer to the chart below.PARAMETER L TC4446L TC4444L TC4444-5Shoot-Through Protection No Yes Yes Absolute Max TS 100V 100V 100V MOSFET Gate Drive 7.2V to 13.5V 7.2V to 13.5V 4.5V to 13.5VV CC UV +6.6V 6.6V 4V V CC UV– 6.15V 6.15V 3.55V nBootstrap Supply Voltage Up to 114V n Wide V CCVoltage: 7.2V to 13.5V n 2.5A Peak Top Gate Pull-Up Current n 3A Peak Bottom Gate Pull-Up Current n 1.2Ω Top Gate Driver Pull-Down n 0.55Ω Bottom Gate Driver Pull-Down n 5ns Top Gate Fall Time Driving 1nF Load n 8ns Top Gate Rise Time Driving 1nF Load n 3ns Bottom Gate Fall Time Driving 1nF Load n 6ns Bottom Gate Rise Time Driving 1nF Loadn Drives Both High and Low Side N-Channel MOSFETs n Undervoltage Lockoutn Thermally Enhanced 8-Pin MSOP PackagenDistributed Power Architecturesn Automotive Power Supplies n High Density Power Modules n Telecommunication SystemsT wo Switch Forward ConverterL TC4446 Driving a 1000pF Capacitive LoadL , L T , L TC and L TM are registered trademarks of Linear Technology Corporation. All other trademarks are the property of their respective owners. Protected by U.S. Patents including 6677210.V BINP 5V/DIVBG 10V/DIV TINP 5V/DIV TG-TS 10V/DIV20ns/DIV4446 TA01b/24446fPIN CONFIGURATIONABSOLUTE MAXIMUM RATINGSSupply VoltageV CC.........................................................–0.3V to 14V BOOST – TS ...........................................–0.3V to 14V TINP Voltage .................................................–2V to 14V BINP Voltage .................................................–2V to 14V BOOST Voltage ........................................–0.3V to 114V TS Voltage ...................................................–5V to 100V Operating Temperature Range (Note 2)....–40°C to 85°C Junction Temperature (Note 3) .............................125°C Storage Temperature Range ...................–65°C to 150°C Lead Temperature (Soldering, 10 sec) ..................300°C(Note 1)1234TINP BINP V CC BG8765TS TG BOOST NCTOP VIEW9MS8E PACKAGE 8-LEAD PLASTIC MSOPT JMAX = 125°C, θJA = 40°C/W , θJC = 10°C/W (NOTE 4)EXPOSED PAD (PIN 9) IS GND, MUST BE SOLDERED TO PCBORDER INFORMATIONELECTRICAL CHARACTERISTICSSYMBOL PARAMETER CONDITIONSMIN TYP MAX UNITS Gate Driver Supply, V CC V CC Operating Voltage7.213.5V I VCCDC Supply Current TINP = BINP = 0V350550μA UVLO Undervoltage Lockout ThresholdV CC Rising V CC Falling Hysteresis l l6.005.606.606.154507.206.70V V mV Bootstrapped Supply (BOOST – TS)I BOOSTDC Supply Current TINP = BINP = 0V 0.12μA Input Signal (TINP , BINP)V IH(BG)BG Turn-On Input Threshold BINP Ramping High l 2.25 2.75 3.25V V IL(BG)BG Turn-Off Input Threshold BINP Ramping Low l 1.85 2.3 2.75V V IH(TG)TG Turn-On Input Threshold TINP Ramping High l 2.25 2.75 3.25V V IL(TG)TG Turn-Off Input Threshold TINP Ramping Lowl 1.852.3 2.75V I TINP(BINP)Input Pin Bias Current ±0.01±2μA High Side Gate Driver Output (TG)V OH(TG)TG High Output Voltage I TG = –10mA, V OH(TG) = V BOOST – V TG 0.7V V OL(TG)TG Low Output Voltage I TG = 100mA, V OL(TG) = V TG –V TSl 120220mV I PU(TG)TG Peak Pull-Up Current l 1.72.5A R DS(TG)TG Pull-Down Resistance l1.22.2ΩThe l denotes the specifi cations which apply over the full operating temperature range, otherwise specifi cations are at T A = 25°C. V CC = V BOOST = 12V , V TS = GND = 0V , unless otherwise noted.LEAD FREE FINISH TAPE AND REEL PART MARKING*PACKAGE DESCRIPTION TEMPERATURE RANGE L TC4446EMS8E#PBF L TC4446EMS8E#TRPBF L TDPZ 8-Lead Plastic MSOP –40°C to 85°C L TC4446IMS8E#PBFL TC4446IMS8E#TRPBFL TDPZ8-Lead Plastic MSOP–40°C to 85°CConsult L TC Marketing for parts specifi ed with wider operating temperature ranges. *The temperature grade is identifi ed by a label on the shipping container .Consult L TC Marketing for information on non-standard lead based fi nish parts.For more information on lead free part marking, go to: http://www.linear .com/leadfree/ For more information on tape and reel specifi cations, go to: http://www.linear .com/tapeandreel//34446fNote 1: Stresses beyond those listed under Absolute Maximum Ratings may cause permanent damage to the device. Exposure to any Absolute Maximum Rating condition for extended periods may affect device reliability and lifetime.Note 2: The L TC4446E is guaranteed to meet specifi cations from 0°C to 85°C. Specifi cations over the –40°C to 85°C operatingtemperature range are assured by design, characterization and correlationELECTRICAL CHARACTERISTICS The l denotes the specifi cations which apply over the full operatingtemperature range, otherwise specifi cations are at T A = 25°C. V CC = V BOOST = 12V , V TS = GND = 0V , unless otherwise noted.SYMBOL PARAMETERCONDITIONSMINTYP MAXUNITS Low Side Gate Driver Output (BG)V OH(BG)BG High Output Voltage I BG = –10mA, V OH(BG) = V CC – V BG0.7VV OL(BG)BG Low Output Voltage I BG = 100mAl 55110mV I PU(BG)BG Peak Pull-Up Current l 23A R DS(BG)BG Pull-Down Resistance l0.55 1.1ΩSwitching Time (BINP (TINP) is Tied to Ground While TINP (BINP) is Switching. Refer to Timing Diagram)t PLH(TG)TG Low-High (Turn-On) Propagation Delay l 2545ns t PHL(TG)TG High-Low (Turn-Off) Propagation Delay l 2240ns t PLH(BG)BG Low-High (Turn-On) Propagation Delay l 1935ns t PHL(BG)BG High-Low (Turn-Off) Propagation Delay l 1430ns t DM(BGTG)Delay Matching BG Turn-Off and TG Turn-On l –151035ns t DM(TGBG)Delay Matching TG Turn-Off and BG Turn-On l –25–325ns t r(TG)TG Output Rise Time 10% – 90%, C L = 1nF 10% – 90%, C L = 10nF880ns ns t f(TG)TG Output Fall Time 10% – 90%, C L = 1nF 10% – 90%, C L = 10nF550ns ns t r(BG)BG Output Rise Time 10% – 90%, C L = 1nF 10% – 90%, C L = 10nF660ns ns t f(BG)BG Output Fall Time 10% – 90%, C L = 1nF 10% – 90%, C L = 10nF 330ns nswith statistical process controls. The L TC4446I is guaranteed over the full –40°C to 85°C operating temperature range.Note 3: T J is calculated from the ambient temperature T A and power dissipation P D according to the following formula: T J = T A + (P D • θJA °C/W)Note 4: Failure to solder the exposed back side of the MS8E package to the PC board will result in a thermal resistance much higher than 40°C/W .TYPICAL PERFORMANCE CHARACTERISTICSV CC Supply Quiescent Current vs VoltageBOOST-TS Supply Quiescent Current vs VoltageV CC Supply Current vs TemperatureV CC SUPPL Y VOL TAGE (V)00Q U I E S C E N T C U R R E N T (μA )501502002506789101112134504446 G011001234514300350400BOOST SUPPL Y VOL TAGE (V)00Q U I E S C E N T C U R R E N T (μA )501502002506789101112134004446 G021001234514300350TEMPERATURE (°C)V C C S U P P L Y C U R R E N T (μA )3503603704446 G03330300–40–25–105203550658095110125380340320310/44446fTYPICAL PERFORMANCE CHARACTERISTICSBoost Supply Current vs TemperatureOutput Low Voltage (V OL ) vs Supply VoltageOutput High Voltage (V OH ) vs Supply VoltageInput Thresholds (TINP , BINP) vs Supply VoltageInput Thresholds (TINP , BINP) vs TemperatureInput Thresholds (TINP , BINP) Hysteresis vs VoltageInput Thresholds (TINP , BINP) Hysteresis vs TemperatureV CC Undervoltage Lockout Thresholds vs TemperatureRise and Fall Time vs V CC Supply VoltageTEMPERATURE (°C)B O O S T S U P P L YC U R R E N T (μA )2503003504446 G041500–40–25–10520355065809511012540020010050SUPPL Y VOL TAGE (V)7O U T P U T V O L T A G E (m V )140104446 G058040891120016012010060121314SUPPL Y VOL TAGE (V)75T G O R B G O U T P U T V O L T A G E (V )689101512911124446 G0671314118101314SUPPL Y VOL TAGE (V)72.1T G O R B G I N P U T T H R E S H O L D (V )2.22.42.52.63.12.8911124446 G072.32.93.02.78101314TEMPERATURE (°C)–25T G O R B G I N P U T T H R E S H O L D (V )2.62.83.0954446 G082.42.22.52.72.92.32.12.053565–10–40110205080125SUPPL Y VOL TAGE (V)78375T G O R B G I N P U T T H R E S H OL D H Y S T E R E S I S (m V )425500911124446 G09400475450101314TEMPERATURE (°C)–40–25375T G O R B G I N P U T T H R E S H O L D H Y S T E R E S I S(m V )425500–105205065804446 G104004754503511095125TEMPERATURE (°C)–406.0V C C S U P L L Y V O L T A G E (V )6.16.36.46.56.7–2535654446 G116.26.62095125110–1055080SUPPL Y VOL TAGE (V)7R I S E /F A L L T I M E (n s )122830222632911124446 G12820161024618148101314/54446fTYPICAL PERFORMANCE CHARACTERISTICSRise and Fall Time vs Load CapacitancePeak Driver (TG, BG) Pull-Up Current vs TemperatureOutput Driver Pull-Down Resistance vs TemperaturePropagation Delay vs V CC Supply VoltagePropagation Delay vs TemperatureLOAD CAPACITANCE (nF)1R I S E /F A L L T I M E (n s )40506094445 G1330200357210468108070TEMPERATURE (°C)–402.0P U L L -U P C U R R E N T (A )2.22.62.83.03.4–2535654446 G142.43.22095125110–1055080TEMPERATURE (°C)–25O U T P U T D R I V E R P U L L -D O W N R E S I S T A C N E (Ω)1.21.62.0954446 G150.80.41.01.41.80.60.253565–10–40110205080125SUPPL Y VOL TAGE (V)710P R O P A G A T I O N D E L A Y (n s )121618203024911124444 G16142628228101314TEMPERATURE (°C)–402P R O P A G A T I O N D E L A Y (n s )717222737–2535654446 G1712322095125110–1055080Switching Supply Current vs Input FrequencySwitching Supply Current vs Load CapacitanceSWITCHING FREQUENCY (kHz)S U P P L Y C U R R E N T (m A )1.52.02.560010004446 G181.00.502004008003.03.54.0LOAD CAPACITANCE (nF)1S U P P L Y C U R R E N T (m A )1010013450.127896104446 G19/64446fPIN FUNCTIONSBLOCK DIAGRAMTINP (Pin 1): High Side Input Signal. Input referenced to GND. This input controls the high side driver output (TG).BINP (Pin 2): Low Side Input Signal. This input controls the low side driver output (BG).V CC (Pin 3): Supply. This pin powers input buffers, logic and the low side gate driver output directly and the high side gate driver output through an external diode con-nected between this pin and BOOST (Pin 6). A low ESR ceramic bypass capacitor should be tied between this pin and GND (Pin 9).BG (Pin 4): Low Side Gate Driver Output (Bottom Gate). This pin swings between V CC and GND.NC (Pin 5): No Connect. No connection required.BOOST (Pin 6): High Side Bootstrapped Supply. An ex-ternal capacitor should be tied between this pin and TS (Pin 8). Normally, a bootstrap diode is connected between V CC (Pin 3) and this pin. Voltage swing at this pin is from V CC – V D to V IN + V CC – V D , where V D is the forward volt-age drop of the bootstrap diode.TG (Pin 7): High Side Gate Driver Output (Top Gate). This pin swings between TS and BOOST .TS (Pin 8): High Side MOSFET Source Connection (Top Source).Exposed Pad (Pin 9): Ground. Must be soldered to PCB ground for optimal thermal performance.TIMING DIAGRAMTINP (BINP)BG (TG)BINP (TINP)TG (BG)/OPERATIONOverviewThe L TC4446 receives ground-referenced, low voltage digi-tal input signals to drive two N-channel power MOSFETs in a synchronous buck power supply confi guration. The gate of the low side MOSFET is driven either to V CC or GND, depending on the state of the input. Similarly, the gate of the high side MOSFET is driven to either BOOST or TS by a supply bootstrapped off of the switching node (TS). Input StageThe L TC4446 employs CMOS compatible input thresholds that allow a low voltage digital signal to drive standard power MOSF ETs. The LTC4446 contains an internal voltage regulator that biases both input buffers for high side and low side inputs, allowing the input thresholds (V IH = 2.75V, V IL = 2.3V) to be independent of variations inV CC. The 450mV hysteresis between V IH and V IL eliminates false triggering due to noise during switching transitions. However, care should be taken to keep both input pins (TINP and BINP) from any noise pickup, especially in high frequency, high voltage applications. The L TC4446 input buffers have high input impedance and draw negligible input current, simplifying the drive circuitry required for the inputs.Output StageA simplifi ed version of the L TC4446’s output stage is shown in Figure 1. The pull-up devices on the BG and TG outputs are NPN bipolar junction transistors (Q1 and Q2). The BG and TG outputs are pulled up to within an NPN V BE (~0.7V) of their positive rails (V CC and BOOST, respectively). Both BG and TG have N-channel MOSFET pull-down devices (M1 and M2) which pull BG and TG down to their nega-tive rails, GND and TS. The large voltage swing of the BG and TG output pins is important in driving external power MOSFETs, whose R DS(ON) is inversely proportional to the gate overdrive voltage (V GS − V TH).Rise/Fall TimeThe L TC4446’s rise and fall times are determined by the peak current capabilities of Q1 and M1. The predriver that drives Q1 and M1 uses a nonoverlapping transition scheme to minimize cross-conduction currents. M1 is fully turned off before Q1 is turned on and vice versa.Since the power MOSFET generally accounts for the ma-jority of the power loss in a converter, it is important to quickly turn it on or off, thereby minimizing the transition time in its linear region. An additional benefi t of a strong pull-down on the driver outputs is the prevention of cross- conduction current. For example, when BG turns the low side (synchronous) power MOSFET off and TG turns the high side power MOSFET on, the voltage on the TS pin will rise to V IN very rapidly. This high frequency positive voltage transient will couple through the C GD capacitance of the low side power MOSFET to the BG pin. If there is an insuffi cient pull-down on the BG pin, the voltage on the BG pin can rise above the threshold voltage of the low side power MOSFET, momentarily turning it back on. With Figure 1. Capacitance Seen by BG and TG During Switching/74446fOPERATIONboth the high side and low side MOSFETs conducting, signifi cant cross-conduction current will fl ow through the MOSFETs from V IN to ground and will cause substantial power loss. A similar effect occurs on TG due to the C GS and C GD capacitances of the high side MOSFET.The powerful output driver of the L TC4446 reduces the switching losses of the power MOSFET, which increase with transition time. The L TC4446’s high side driver is capable of driving a 1nF load with 8ns rise and 5ns fall times using a bootstrapped supply voltage V BOOST-TS of 12V while its low side driver is capable of driving a 1nF Power DissipationTo ensure proper operation and long-term reliability, the L TC4446 must not operate beyond its maximum tem-perature rating. Package junction temperature can be calculated by:T J = T A + P D (θJA)where:T J = Junction temperatureT A = Ambient temperatureP D = Power dissipationθJA = Junction-to-ambient thermal resistance Power dissipation consists of standby and switching power losses:P D = P DC + P AC + P QGwhere:P DC = Quiescent power lossP AC = Internal switching loss at input frequency, f INP QG = Loss due turning on and off the external MOSFET with gate charge QG at frequency f IN load with 6ns rise and 3ns fall times using a supply volt-age V CC of 12V.Undervoltage Lockout (UVLO)The L TC4446 contains an undervoltage lockout detector that monitors V CC supply. When V CC falls below 6.15V, the output pins BG and TG are pulled down to GND and TS, respectively. This turns off both external MOSFETs. When V CC has adequate supply voltage, normal operation will resume.APPLICATIONS INFORMATIONThe L TC4446 consumes very little quiescent current. TheDC power loss at V CC = 12V and V BOOST-TS = 12V is only(350μA)(12V) = 4.2mW.At a particular switching frequency, the internal power lossincreases due to both AC currents required to charge anddischarge internal node capacitances and cross-conduc-tion currents in the internal logic gates. The sum of thequiescent current and internal switching current with noload are shown in the Typical Performance Characteristicsplot of Switching Supply Current vs Input Frequency.The gate charge losses are primarily due to the large ACcurrents required to charge and discharge the capacitanceof the external MOSFETs during switching. For identicalpure capacitive loads C LOAD on TG and BG at switchingfrequency f IN, the load losses would be:P CLOAD = (C LOAD)(f)[(V BOOST-TS)2 + (V CC)2]In a typical synchronous buck confi guration, V BOOST-TSis equal to V CC – V D, where V D is the forward voltagedrop across the diode between V CC and BOOST. If thisdrop is small relative to V CC, the load losses can beapproximated as:P CLOAD = 2(C LOAD)(f IN)(V CC)2/84446fAPPLICATIONS INFORMATIONUnlike a pure capacitive load, a power MOSF ET’s gate capacitance seen by the driver output varies with its V GS voltage level during switching. A MOSFET’s capacitive load power dissipation can be calculated using its gate charge, Q G. The Q G value corresponding to the MOSFET’s V GS value (V CC in this case) can be readily obtained from the manufacturer’s Q G vs V GS curves. For identical MOSFETs on TG and BG:P QG = 2(V CC)(Q G)(f IN)To avoid damage due to power dissipation, the L TC4446 includes a temperature monitor that will pull BG and TG low if the junction temperature rises above 160°C. Normal operation will resume when the junction temperature cools to less than 135°C.Bypassing and GroundingThe LTC4446 requires proper bypassing on the V CC and V BOOST-TS supplies due to its high speed switching (nanoseconds) and large AC currents (Amperes). Careless component placement and PCB trace routing may cause excessive ringing.To obtain the optimum performance from the L TC4446: A. Mount the bypass capacitors as close as possible between the V CC and GND pins and the BOOST and TS pins. The leads should be shortened as much as possible to reduce lead inductance.B. Use a low inductance, low impedance ground plane to reduce any ground drop and stray capacitance. Remember that the L TC4446 switches greater than 3A peak currents and any signifi cant ground drop will degrade signal integrity.C. Plan the power/ground routing carefully. Know where the large load switching current is coming from and going to. Maintain separate ground return paths for the input pin and the output power stage.D. Keep the copper trace between the driver output pin and the load short and wide.E. Be sure to solder the Exposed Pad on the back side of the L TC4446 package to the board. Correctly soldered to a 2500mm2 doublesided 1oz copper board, the L TC4446 has a thermal resistance of approximately 40°C/W for the MS8E package. Failure to make good thermal contact between the exposed back side and the copper board will result in thermal resistances far greater than 40°C/W./94446f104446fTYPICAL APPLICATIONL T C 3722/L T C 4446 420W 36V -72V I N t o 12V /35A I s o l a t e d F u l l -B r i d g e S u p p l yL 1V I –V I 36V T /分销商库存信息:LINEAR-TECHNOLOGYLTC4446EMS8E#PBF LTC4446EMS8E#TRPBF LTC4446IMS8E#PBF LTC4446IMS8E#TRPBF。
EV12s 技术规范书
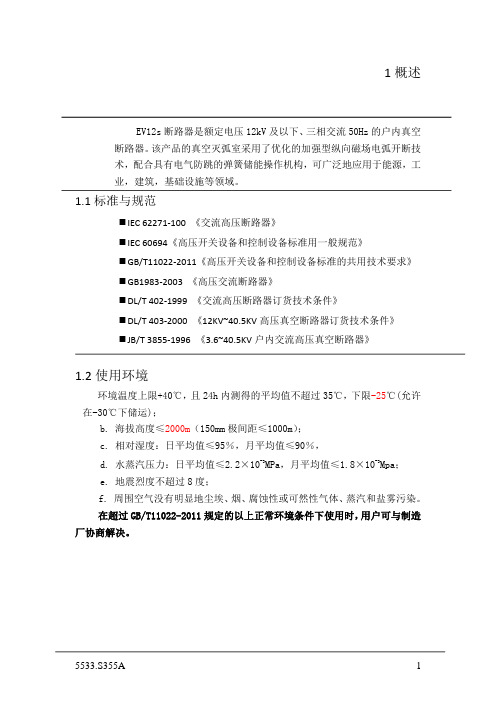
1概述EV12s断路器是额定电压12kV及以下、三相交流50Hz的户内真空断路器。
该产品的真空灭弧室采用了优化的加强型纵向磁场电弧开断技术,配合具有电气防跳的弹簧储能操作机构,可广泛地应用于能源,工业,建筑,基础设施等领域。
1.1标准与规范⏹IEC 62271-100 《交流高压断路器》⏹IEC 60694《高压开关设备和控制设备标准用一般规范》⏹GB/T11022-2011《高压开关设备和控制设备标准的共用技术要求》⏹GB1983-2003 《高压交流断路器》⏹DL/T 402-1999 《交流高压断路器订货技术条件》⏹DL/T 403-2000 《12KV~40.5KV高压真空断路器订货技术条件》⏹JB/T 3855-1996 《3.6~40.5KV户内交流高压真空断路器》1.2使用环境环境温度上限+40℃,且24h内测得的平均值不超过35℃,下限-25℃(允许在-30℃下储运);b. 海拔高度≤2000m(150mm极间距≤1000m);c. 相对湿度:日平均值≤95%,月平均值≤90%,d. 水蒸汽压力:日平均值≤2.2×10-3MPa,月平均值≤1.8×10-3Mpa;e. 地震烈度不超过8度;f. 周围空气没有明显地尘埃、烟、腐蚀性或可然性气体、蒸汽和盐雾污染。
在超过GB/T11022-2011规定的以上正常环境条件下使用时,用户可与制造厂协商解决。
1.3 EV12s真空断路器的电气性能工作电压:10kV 额定电压:12 kV 额定频率:50HZ额定电流:630-1250-1600-2000-2500-3150-4000(强制风冷)额定短时耐受电流及时间:25-31.5-40 kA 4s额定峰值耐受电流:63-80-100 kA操作顺序:O-0.3s-CO-180s-CO额定绝缘水平工频耐压(50HZ, 1min):相间及对地42Kv,真空断口48Kv;雷电冲击耐压(1.2/50μs,peak):相间及对地75Kv,真空断口85Kv;辅助电压分闸线圈:110/220V DC/AC合闸线圈:110/220V DC/AC储能电机:110/220V DC/AC安全距离相间距(中心距):150mm/210mm/275mm裸导体相间及对地空气距离:125mm爬电距离:>240mm温升运行人员易触及部位≤30K 可触及但操作无需触及部位≤40K运行人员不易触及的个别部位≤65K2 技术参数2.1主要技术参数2 5533.S355A注:(1) 额定电流4000A时开关柜需带强制风冷;(2) 海拔1000m及以下试验时,42可修正为48,75可修正为85。
744355090;中文规格书,Datasheet资料

Bezeichnung :description :Marking = part numberEigenschaften / properties Lerrlaufinduktivität/initial inductance Nenn-Induktivität /33%Umgebungstemperatur / temperature:+20°CWE-Perm ME 08-01-01ME 06-11-19ME 05-04-16ME05-03-30ME 05-03-15NameDatum / dateÄnderung / modificationVersion 1Version 2Version 3Version 4Version 5Umgebungstemp. / ambient temperature: -40°C - +105°C It is recommended that the temperature of the part does F Werkstoffe & Zulassungen / material & approvals :Elektrische Eigenschaften / electrical properties :SPEICHERDROSSEL WE-HCI POWER-CHOKE WE-HCIArtikelnummer / part number :744355090Würth Elektronik eiSos GmbH & Co. KGD-74638 Waldenburg · Max-Eyth-Strasse 1 - 3 · Germany · Telefon (+49) (0) 7942 - 945 - 0 · Telefax (+49) (0) 7942 - 945 - 400Geprüft / checked ...................................................................................................................................................................................Unterschrift / signatureKontrolliert / approvedWürth Elektronik..................................................................................E Testbedingungen / test conditions :HP 34401 A & Fluke 54II für/for I DC; Luftfeuchtigkeit / humidity:Metra HIT 27I für/for R DCWAYNE KERR 3260B für/for L 0; I SAT D Prüfgeräte / test equipment :G Eigenschaften / general specifications :not exceed 155°C under worst case operating conditions.Draht / wire:AIEIW-200Arbeitstemperatur / operating temperature: -40°C - +155°C Basismaterial / base material:Freigabe erteilt / general release:Kunde / customerhttp://www.we-online.deDatum / dateBezeichnung :description :H Induktivitätskurve / Inductance curve :ME 08-01-01ME 06-11-19ME 05-04-16ME05-03-30ME 05-03-15NameDatum / dateSPEICHERDROSSEL WE-HCI POWER-CHOKE WE-HCIDATUM / DATE : 2008-01-01Freigabe erteilt / general release:Kunde / customer....................................................................................................................................................................Version 5Datum / dateUnterschrift / signature Version 4Würth ElektronikVersion 3Version 2..............................................................................................................................................Version 1D-74638 Waldenburg · Max-Eyth-Strasse 1 - 3 · Germany · Telefon (+49) (0) 7942 - 945 - 0 · Telefax (+49) (0) 7942 - 945 - 400http://www.we-online.deGeprüft / checked Kontrolliert / approvedÄnderung / modificationWürth Elektronik eiSos GmbH & Co. KGBezeichnung :description :I Temperaturanstieg / Temperature rise curve :ME 08-01-01ME 06-11-19ME 05-04-16ME05-03-30ME 05-03-15NameDatum / dateVersion 1D-74638 Waldenburg · Max-Eyth-Strasse 1 - 3 · Germany · Telefon (+49) (0) 7942 - 945 - 0 · Telefax (+49) (0) 7942 - 945 - 400...............................................................................................................................................................Version 5Datum / dateUnterschrift / signatureVersion 4 http://www.we-online.deGeprüft / checked Kontrolliert / approvedÄnderung / modificationWürth Elektronik eiSos GmbH & Co. KGFreigabe erteilt / general release:Kunde / customerDATUM / DATE : 2008-01-01Würth ElektronikVersion 3Version 2..........................................................................................................................................Bezeichnung :description :ME 06-11-19ME 05-04-16ME05-03-30ME 05-03-15NameDatum / dateSPEICHERDROSSEL WE-HCI POWER-CHOKE WE-HCIFreigabe erteilt / general release:Kunde / customer....................................................................................................................................................................Datum / dateUnterschrift / signature Version 4Würth ElektronikVersion 3Version 2................................................................................................................................................Version 1D-74638 Waldenburg · Max-Eyth-Strasse 1 - 3 · Germany · Telefon (+49) (0) 7942 - 945 - 0 · Telefax (+49) (0) 7942 - 945 - 400Geprüft / checked Kontrolliert / approvedÄnderung / modificationWürth Elektronik eiSos GmbH & Co. KGThe Force for tearing off cover tape is 20 to 70 grams in arrow direction150°feeding directionespecially required or if there is the possibility of direct damage or injury to human body, for example in the range of aerospace, aviation, nuclear control, submarine, transportation, (automotive control, train control, ship control), transportation signal, disaster prevention, medical, public information network etc, Würth Elektronik eiSos GmbH must be informed before the design-in stage. In addition, sufficient reliability evaluation checks for safety must be performed on every electronic component which is used in electrical circuits that require high safety and reliability functions or performance.分销商库存信息: WURTH-ELECTRONICS 744355090。
Electro-Voice Sx Sb-Series 12英寸系统挂钩手册说明书

Sx/Sb-Series 12” SystemsRigging ManualSx-SeriesThe Mb KitsElectro-Voice® manufactures three accessories to make the sus-pension of Sx/Sb-Series enclosures safe, easy and cost-effective: the Mb100 Eyebolt Attachment Kit, the Mb200 Installation Kit and the Mb300 Horizontal Array Kit. This instruction sheet gives a brief overview of how each of these suspension kits could be used so the correct kit can be selected. In addition, each of the suspension kits includes a separate instruction sheet with complete dimensions and full details for use.Suspending Sx/Sb-Series EnclosuresThe molded enclosures used in Sx/Sb-Series are lightweight and structurally sound. Each enclosure has four metric M8 x 1.25 metal inserts molded into the enclosure to aid in suspension and aiming. A single insert, correctly used, will safely suspend the weight of one enclosure with a safety factor in excess of 5 to 1. It will not support additional weight with a sufficient safety factor for overhead lifting. If multiple Sx/Sb-Series enclosures are suspended, Mb200 Installation Kits must be used to support and aim each enclosure.Mb100 Eyebolt Attachment KitThe Mb100 Eyebolt Attachment Kit is intended for very simple instal-lations only, to suspend an individual Sx/Sb-Series loudspeaker in a near-vertical orientation (see Figure 1). A second, redundant insert point is provided in the top of the enclosure so a supplementaryindependent means of suspension can be attached when regulations specify. The enclosure can be positioned to angle downward slightly through the use of the pull-up point at the back of the enclosure.Note that two top suspension cables should be used at all times to provide needed stability to the installation (see Figure 1).Do not suspend Sx/Sb-Series enclosures face down from the ceiling using the Mb100 Eyebolt Attachment Kit. The M8 eyebolts are not rated for lifting loads at 90°, and such a configuration makes stabilization of the enclosure difficult. Instead, use the Mb200 Installation Kit for this and most other situations (see the Mb200 Installation Kit section).Mb200 Installation KitThe Mb200 Installation Kit provides a cost-effective and safe means of attaching Sx/Sb-Series loudspeakers to walls or suspending them overhead (see Figure 2). The kit contains a large, reinforced-steel bracket with a selection of thru-holes which allow the bracket to be mounted to different surfaces in a range of orientations. This kit is rec-ommended for most installations, and is essential when arraying Sx/Sb-Series loudspeakers.The Mb200 U-bracket extends from top to bottom of the Sx/Sb-Se-ries loudspeaker and attaches at both ends. This securely “captures” the enclosure, allowing further loudspeaker systems to be added without increasing the stress on the first enclosure. It also allows the loudspeaker to be aimed in the desired direction and locked in place. For even greater flexibility, three-hole-pattern groups compatible with the OmniMount® 60.0 (originally Series 100)1 support system have also been incorporated into the Mb200 Installation Kit's U-bracket (see Figure 2B, reference A).Vertical arrays can be constructed by "daisy chaining" Mb200's to-gether (see Figure 3). To achieve a slight downward angle, attach an additional cable to the lower Mb200 and use this cable to pull up the array, securing the cable at the desired angle and position.No more than two enclosures should be suspended in a vertical array in this manner. If a taller array is required, you should provide a means of independent suspension for the remaining enclosures.Again, note the use of two top suspension cables (see Figure 3) which provide stability and should be used at all times.Horizontal ArrayNumber of Enclosuresin Array:Number of Kits Required Mb200Mb3002213324435546(Complete Circle)66Each Mb300 Horizontal Array Kit consists of two connector brackets (one top, one bottom) plus the hardware required to join these brack-ets to the U-brackets from two Mb200 Installation Kits. This combina-tion of one Mb300 Horizontal Array Kit plus two Mb200 Installation Kits forms a solid frame suitable for suspending two Sx/Sb-Series loudspeakers in a horizontal array (see Figure 4). Holes are provided in the Mb300 brackets for attaching cables for suspension.Two mounting angles, 50° and 60°, are possible using the Mb300 Horizontal Array Kit. Use of the 50° angle results in a tight array with speaker sides touching (see Figure 5); use of the wider orientation results in improved coverage for multiple loudspeakers and allows construction of a complete, 360° array (see Figure 6 for diagram of one half of a 360° array). A vertical array can also be constructed using the Mb300 Horizontal Array Kit, but relatively few aiming angles are available.1. OmniMount® is a registered trademark of OmniMount Systems, Inc.For more information, visit Mb300 Horizontal Array KitThe Mb300 Horizontal Array Kit must be used in conjunction with the Mb200 Installation Kit. Select the required number of kits from the chart below:Figure 1:Overhead Suspension Using the Mb100 Eyebolt Attachment Kit Figure 2a:Wall Mounting Using the Mb200 Installation KitFigure 2b:Vertical Overhead Suspension Using theMb200 Installation KitFigure 2c:Horizontal Overhead Suspension Using the Mb200 Installation KitFigure 3:Vertical Array Using the Mb200 Installation Kit12000 Portland Avenue South, Burnsville, MN 55337Phone: 952/884-4051, Fax: 952/884-0043Electro-Voice ®Figure 4a:Brackets from One Mb300 Horizontal Array Kit and TwoMb200 Installation Kits, Positioned for AssemblyFigure 4b:Assembled Horizontal Array Mounting Frame Consisting ofOne Mb300 Horizontal Array Kit and Two Mb200Installation KitsFigure 4c:Two Enclosure Horizontal Array Using the Mb300Horizontal Array Kit Figure 4d:Orientation for Full Circle (360°) Array Using the Mb300Horizontal Array Kit (Partial Array Shown)U.S.A. and Canada only. For customer orders, contact Customer Service at:800/392-3497 Fax: 800/955-6831Europe, Africa, and Middle East only. For customer orders, contact Customer Service at:+ 49 9421-706 0 Fax: + 49 9421-706 265Other Internatonal locations. For customer orders, Contact Customer Service at:+ 1 952 884-4051 Fax: + 1 952 887-9212。