铸造成形过程研究与创新
挤压铸造双金属复合材料成型工艺及性能分析

世界有色金属 2023年 5月上10冶金冶炼M etallurgical smelting挤压铸造双金属复合材料成型工艺及性能分析户 芳,高秀峰,叶 云(山西晋中理工学院,山西 晋中 030600)摘 要:双金属复合材料是一种具有高利用率、综合性能优于其它金属材料的新型浇铸材料,为此,本文对挤压铸造工艺和性能进行了分析。
首先,通过对双金属复合材料的模态结构的建模、固液复合度的控制、双金属材料的包覆温度和退温成型等方面的研究,而后对其成型过程进行了分析,最后再对其导电性、轻量化等方面作了较为深入的研究。
关键词:复合材料;性能分析;挤压铸造;成型工艺中图分类号:TG249.2 文献标识码:A 文章编号:1002-5065(2023)09-0010-3Forming Technology and Performance Analysis of Squeeze Casting Bimetal CompositesHU Fang, GAO Xiu-feng, YE Yun(Shanxi Jinzhong Institute of Technology,Jinzhong 030600,China)Abstract: Bimetal composite material is a new type of casting material with high utilization rate and better comprehensive performance than other metal materials. Therefore, the squeeze casting process and performance are analyzed in this paper. First of all, through the research on the modeling of the modal structure of the bimetallic composite, the control of the solid-liquid composite, the coating temperature of the bimetallic material and the annealing molding, the molding process is analyzed, and finally, the conductivity and lightweight of the bimetallic composite are further studied.Keywords: composite materials; Performance analysis; Squeeze casting; Forming process收稿日期:2023-03作者简介:户芳,女,生于1988年,汉族,山东曹县人,硕士研究生,助教,研究方向:材料成型。
大型锻造的质量控制和研究方略
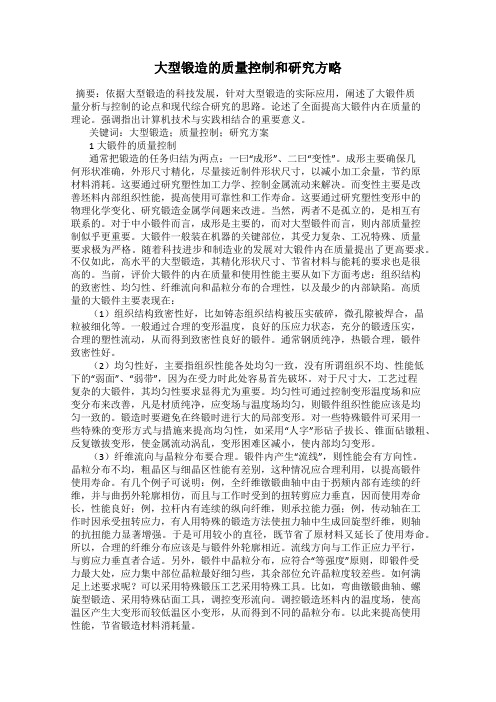
大型锻造的质量控制和研究方略摘要:依据大型锻造的科技发展,针对大型锻造的实际应用,阐述了大锻件质量分析与控制的论点和现代综合研究的思路。
论述了全面提高大锻件内在质量的理论。
强调指出计算机技术与实践相结合的重要意义。
关键词:大型锻造;质量控制;研究方案1大锻件的质量控制通常把锻造的任务归结为两点:一曰“成形”、二曰“变性”。
成形主要确保几何形状准确,外形尺寸精化,尽量接近制件形状尺寸,以减小加工余量,节约原材料消耗。
这要通过研究塑性加工力学、控制金属流动来解决。
而变性主要是改善坯料内部组织性能,提高使用可靠性和工作寿命。
这要通过研究塑性变形中的物理化学变化、研究锻造金属学问题来改进。
当然,两者不是孤立的,是相互有联系的。
对于中小锻件而言,成形是主要的,而对大型锻件而言,则内部质量控制似乎更重要。
大锻件一般装在机器的关键部位,其受力复杂、工况特殊、质量要求极为严格。
随着科技进步和制造业的发展对大锻件内在质量提出了更高要求。
不仅如此,高水平的大型锻造,其精化形状尺寸、节省材料与能耗的要求也是很高的。
当前,评价大锻件的内在质量和使用性能主要从如下方面考虑:组织结构的致密性、均匀性、纤维流向和晶粒分布的合理性,以及最少的内部缺陷。
高质量的大锻件主要表现在:(1)组织结构致密性好,比如铸态组织结构被压实破碎,微孔隙被焊合,晶粒被细化等。
一般通过合理的变形温度,良好的压应力状态,充分的锻透压实,合理的塑性流动,从而得到致密性良好的锻件。
通常钢质纯净,热锻合理,锻件致密性好。
(2)均匀性好,主要指组织性能各处均匀一致,没有所谓组织不均、性能低下的“弱面”、“弱带”,因为在受力时此处容易首先破坏。
对于尺寸大,工艺过程复杂的大锻件,其均匀性要求显得尤为重要。
均匀性可通过控制变形温度场和应变分布来改善,凡是材质纯净,应变场与温度场均匀,则锻件组织性能应该是均匀一致的。
锻造时要避免在终锻时进行大的局部变形。
对一些特殊锻件可采用一些特殊的变形方式与措施来提高均匀性,如采用“人字”形砧子拔长、锥面砧镦粗、反复镦拔变形,使金属流动涡乱,变形困难区减小,使内部均匀变形。
消失模铸造模具的研究与应用
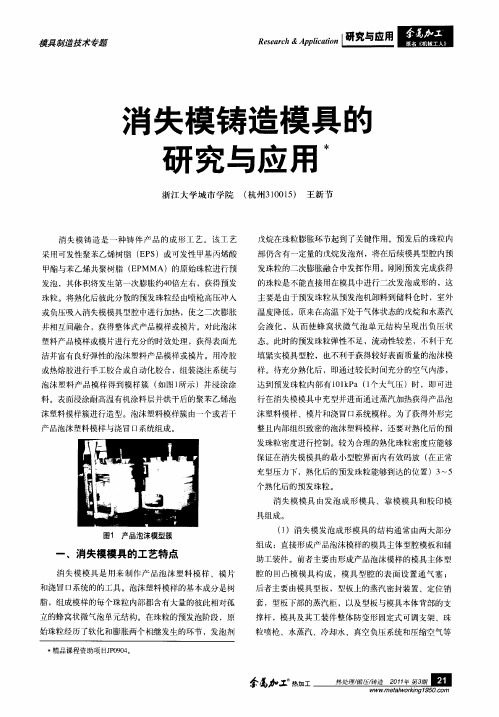
达到预 发珠粒 内部 有l l P 1 O k a( 个大气压 )时 ,即可进
行在消失模模具 中充型并进 而通过蒸汽加 热获得产品泡
沫塑料模样 、模片和浇 冒 口系统 模样 。为 了获得外形完
整且 内部组织致密 的泡沫 塑料模样 , 还要 对熟化后的预
主要 是 由于预发珠粒从预发泡机卸料到储料仓时 ,室外 温 度降低 ,原来在高温下处于气体状态的戌烷和水蒸汽
会液化 ,从 而使 蜂窝 状微 气泡单 元结 构呈 现 出负压状
态 。此时 的预 发珠 粒弹性不足 ,流动性较差 ,不利于充 填 紧实模具 型腔 ,也不利于获得较好表面 质量的泡沫模
垫 丝 堕 生 t!r童塑_U 竺 堡 笪 a !kig1 50.om 堡 _ : me l o n 9 w c
墨 \sc A 兰 Ra & er eh
组成 的安装支架 ( 图2 如 所示)。
|
其优点是制造成本低 ,缺点是使用寿命短 ( 通常少于 1 0 万次开模次数 );后者主要用于大批量生产 ,其优点是
精品课程资助项 目J00 。 P 94
后 者主要 由模具型板 ,型板上的蒸汽密封装 置、定位 销 套 ,型板下部的蒸汽柜 ,以及型板与模具本体 背部 的支 撑 杆 ,模具 及其工装件整体防变形 固定式可调支架 、珠 粒 喷枪 、水蒸汽 、冷却水 、真空负压 系统和压缩空 气等
参磊
热工 加
模 翻 技 专 具造术题
Ra & n I墨 壁 er 却胁 皇 里 sc e 砌!
消 失模 铸 造模 具 的 研 究与应 用 术
浙江大学城市 学院 ( 杭州3 0 1 ) 王新节 10 5
镁合金低压铸造的研究进展

镁合金低压铸造的研究进展摘要:伴随航空航天和国防工业的不断发展,镁合金作为轻合金结构材料,在该领域中受到了广泛应用。
镁合金铸件的成型技术成为了研制镁合金的关键,其作为反重力精密成型技术的低压铸造,在镁合金成型期间发展迅速。
本文主要论述了镁合金低压铸造的进展。
关键词:镁合金;低压铸造;研究进展镁合金主要是以镁为基本的元素,在铸造期间,通过添加其它元素从而形成合金。
镁合金材料自身具备密度小、强度高、散热性能好以及承受能力强等优点,在这些优点的基础上,其被应用到了航空、运输等各个工业部门中,并且产生的效果明显。
1 镁合金低压铸造的论述镁合金作为一种轻型的金属结构材料,在基于强度高、刚度性能好以及抗冲击力强等一系列特点的基础上,被广泛应用到了汽车和电子工业等各个领域中。
在市场中,镁合金铸件大部分都是压铸成形的,仅仅有一小部分镁合金铸件是使用重力砂型铸造而成的。
在进行镁合金铸件压铸的时候,对于成形工艺有着严格要求,并且输出成本较多,市场如果发生了一些变化情况,那么压铸成形的铝合金铸件弊端便会凸显出来,无法较好的应对市场变化情况。
而砂铸件自身还存在着精度低下以及质量性能差等缺陷,这些缺陷的出现使其在发展期间受到了限制。
因此为了提升镁合金铸件的精密化程度,满足不断变化的市场需求,低压铸造工艺由此出现。
低压铸造工艺本身是一种反重力精密成形技术,由于性能良好,当前已经被应用到了各个机械生产行业中去了。
镁合金低压铸造保护技术,镁和常见的镁合金自身较为灵活,并且熔点低,在氧气充足的情况下,比较容易产生化学反应。
所以在进行熔炼的时候,应当展开有效的阻燃保护。
从当前情况来看,在铸造镁合金中,经常使用到的保护技术是溶剂保护法、合金化法以及气体保护法等。
2 镁合金低压铸造技术研究现状随着社会经济发展,环境问题日益严重,我国为了解决缓解这一现象,实施了节能减排政策,同时将节能减排落实到国家经济发展战略中去,以此保护环境,推动各个行业的发展。
通用汽车中国科学研究院院长杜江凌博士的演讲

通用汽车中国科学研究院院长杜江凌博士的演讲•大家早上好,在接下来的十几分钟内,我将向大家介绍一下为实现引领汽车产业技术创新这一目标,我们将在通用中国做些什么。
•一年多以前,就在通用中国主楼的这一侧,我们举行了前瞻技术中心的破土动工奠基仪式。
一年多以后的今天,我们在这刚刚建成的先进材料实验大楼里,也就是前瞻技术中心一期,和大家一起见证它的启用。
•在这栋科研大楼里,我们的研究与工程人员将主要从事当今汽车行业最重要的两个方面的技术研究工作。
一是未来车用轻型材料;二是未来电动车动力电池。
•在明年的下半年,前瞻技术中心二期将会竣工。
在那里,将有Brain刚刚提到的先进汽车设计中心,先进内燃机动力总成研究与工程,先进汽车研究与工程以及先进汽车制造工艺研究。
到那时,通用前瞻技术中心将成为中国首个最全面大规模的先进汽车技术研究中心。
•大家看到的是先进材料实验大楼的示意图。
大家现在所在的大厅是我们的铸造与成形实验室。
是的,别看它现在布置得像北京798似儿的,但一旦等今天的剪彩仪式结束,这里将奇迹般的变成世界上最先进的汽车材料铸造与成形实验室。
•在这里,世界上最新的金属镁合金将在这里被发明,世界上最先进的镁合金汽车零件铸造与成形工艺也将在这里产生。
•在我汇报结束之后,我们还将首次向大家展示在这座先进材料实验大楼里的其它几个世界级的材料及电池实验室。
•为什么我们要投资进行材料研发呢?这事儿还真和我们每一个人都息息相关。
•作为一名车主,难道你不期望你的爱车造型美观、安全、省油、实惠和耐用吗?当然希望,对吧!所有这些,全都与汽车所用的材料紧密相联。
•比如,我们车前面部分就是由强度和韧性兼具的材料构成的,这样,当碰撞发生时,材料即先会变形以尽可能地吸收能量;但又恰到好处以保证驾驶舱不会变形。
•我们都喜欢造型时尚的汽车,然而你们可能不知道,正是材料科学的进步给了Brian和他的设计师们足够的空间去自由设计这些流线造型和视觉效果超酷的轿车。
金属工艺学(青岛理工大学)智慧树知到答案章节测试2023年

第一章测试1.以下哪些是本课程的研究内容?A:金属材料成形B:金属的物理、化学性质C:贵金属的鉴别D:零件加工方法答案:AD2.机械制造根据成形过程的不同,分为热加工和冷加工两种。
A:对B:错答案:A3.以下属于热加工的有A:压力加工B:焊接C:铸造D:热处理与表面改性答案:ABCD4.以下属于冷加工的是()A:磨削B:压锻C:铸造D:切削答案:AD5.采用模拟技术,优化工艺设计可以帮助金属加工的成形质量向近无“缺陷”方向发展。
A:对B:错答案:A第二章测试1.影响液态金属充型能力的主要因素有()。
A:合金的流动性B:化学成分C:浇注条件D:铸型条件答案:ACD2.铸造生产中所用模样的形状和尺寸应与零件完全相同A:对B:错答案:B3.铸造热应力的性质是铸件薄壁处快冷受拉应力,厚壁处缓冷受压应力。
A:对B:错答案:B4.确定铸件的浇注位置时,将铸件薄壁部分置于铸型下部的主要目的是()。
A:避免浇不足B:避免裂纹C:利于补缩铸件D:利于排除型腔内气体答案:A5.凝固温度区间大的合金容易产生缩松。
A:对B:错答案:A6.收缩率较大的合金、壁厚差异悬殊或有热节的铸件、对气密性要求高的铸件应采用顺序凝固。
A:错B:对答案:B7.按照砂箱特征分,手工造型有()。
A:三箱造型B:地坑造型C:刮板造型D:两箱造型答案:ABD8.尽量使铸件全部或大部分放在同一砂箱中,其主要目的是为了防止()缺陷。
A:冷隔B:浇不足C:错箱D:夹砂答案:C9.铸件在凝固收缩阶段受阻碍时,会在铸件内产生内应力A:错B:对答案:A10.大批量铸造精密小型黑色金属零件时,宜采用()。
A:金属型铸造B:离心铸造C:熔模铸造D:砂型铸造答案:C11.壁厚不均匀的铸件,在厚壁处会形成热节,由此产生()。
A:黏砂B:变形和裂纹C:冷隔和浇不足D:缩孔和缩松答案:D12.铸造生产的一个显著优点是能够生产形状复杂的铸件,因此铸件的结构越复杂越好。
A:错B:对答案:A第三章测试1.以下哪个不是压力加工的优点:A:生产率高B:节省金属C:力学性能高D:易获得截面形状复杂的产品答案:D2.对于大间隙冲裁件,单边修量一般为板料厚度的______;对于小间隙冲裁件,单边修量一般为板料厚度的______。
铝合金铸造
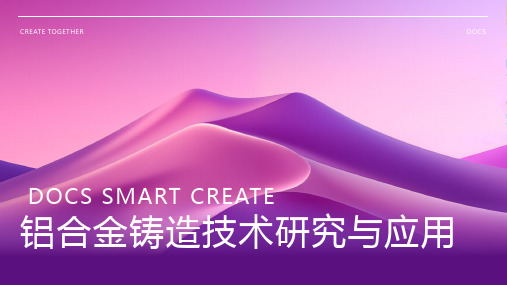
铝合金铸造的基本原理
铝合金铸造的基本原理
• 熔炼:将铝合金原料加热至熔化状态,形成铝合金液 • 浇注:将铝合金液倒入模具中,使其充满整个模具 • 凝固:通过冷却使铝合金液在模具中凝固成型,形成铸件
铝合金铸造过程中的关键因素
• 合金成分:影响铸件的性能和组织结构 • 铸造温度:影响铝合金液的流动性和充型能力 • 冷却速度:影响铸件的组织结构和性能
铝合金铸造设备的维护与保养
铝合金铸造设备的维护
• 定期检查:定期对铸造设备进行检查,确保正常运行 • 清洁保养:定期对铸造设备进行清洁保养,防止杂质污染 • 润滑保养:定期对铸造设备进行润滑保养,保证设备运行顺畅 • 故障排除:及时发现并排除铸造设备的故障,避免影响生产
铝合金铸造设备的保养
• 定期更换易损件:定期更换铸造设备中的易损件,保证设备正常运行 • 设备调试:根据生产需求,对铸造设备进行调试,确保生产质量 • 设备升级:根据生产需求,对铸造设备进行升级,提高生产效率 • 安全操作:遵守安全操作规程,确保铸造设备的安全运行
• 高纯度铝合金:研究高纯度铝合金,提高铸件性能 • 复合铝合金:研究复合铝合金,提高铸件的综合性能 • 新型铝合金:开发新型铝合金,满足特殊领域的需求 • 环保型铝合金:研究环保型铝合金,降低对环境的影响
铝合金铸造行业的创新与突破
铝合金铸造行业的创新
• 材料创新:研究新型铝合金材料,提高铸件性能 • 工艺创新:研究新型铸造工艺,提高铸件质量和生产效率 • 产品创新:开发新型铝合金铸件,满足市场需求 • 管理创新:优化企业管理,提高铝合金铸造行业的管理水平
DOCS
谢谢观看
THANK YOU FOR WATCHING
铝合金铸造行业的发展
汽车铝合金转向节锻造成形模拟与试验研究
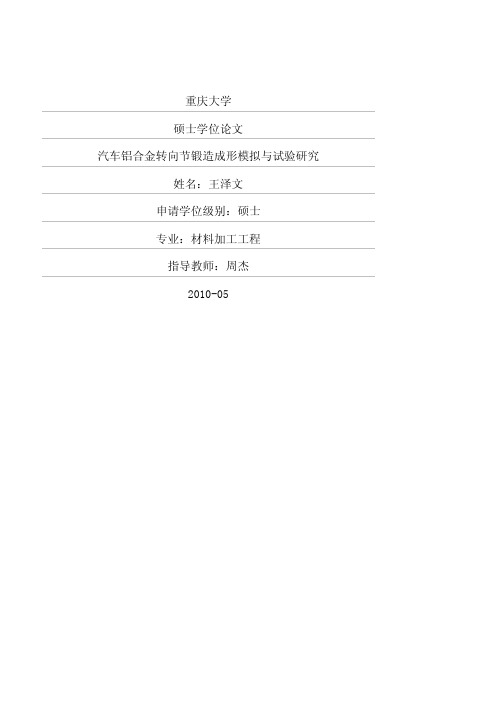
重庆大学硕士学位论文汽车铝合金转向节锻造成形模拟与试验研究姓名:王泽文申请学位级别:硕士专业:材料加工工程指导教师:周杰2010-05摘要随着汽车制造业的高速发展,汽车轻量化和性能要要求越来越严格,汽车零部件生产中,尺寸精度高、外形复杂的锻件所占比重越来越大。
因此,开发材料利用率高并能节约能源的锻造新工艺,对于汽车零件制造业的发展极为重要。
近年来,铝合金结构零件在汽车轻量化要求日益提高的情况下运用越来越广泛。
将铝合金锻件运用到汽车转向系统中,不但可以满足汽车行驶过程中的强度要求,还因为重量的减轻提高其操纵性能。
但是由于铝合金材料本身的特性,如锻造时变形抗力大、流动性差和外摩擦系数较大等导致铝合金锻件的成形困难,阻碍了其在汽车工业中的运用。
转向节是汽车转向系统中的重要零件,既承载一定的车体重量,又在汽车行驶过程中承受交变载荷和刹车时的力矩,是汽车上的重要安全零件之一。
转向节的主要工艺为锻造成形,因此组织性能和外形尺寸的要求非常严格,对于该类锻件锻造方法探索研究将对我国汽车工业的发展产生重要意义。
本文研究的奥迪汽车铝合金转向节,外形极其复杂,主要依靠从国外进口,国内尚无成功的制造经验。
在研究过程中,对该转向节原有的工艺方案进行了分析,运用所建立汽车铝合金转向节弯曲成形制坯过程和终锻成形过程的三维有限元模型,利用三维有限元数值模拟软件DEFORM-3D对汽车转向节锻造成形工艺进行系统分析,模拟其弯曲制坯和终锻成形过程,研究其缺陷产生的原因和演化机理。
找出了影响工厂试制质量的关键因素,提出了既能满足产品精度要求,又能提高材料率、改善弯曲成形质量和终锻模具寿命的优化措施,改进了模锻工艺,使其趋向合理化。
通过模拟验证,给出了二次弯曲成形模具的最优结构参数。
本文的研究工作,结合了模锻工艺、有限元理论、数值模拟仿真技术及模具CAD技术,达到了缩短产品开发周期、提高模具寿命、降低成本等目的。
得到的工作成果解决了奥迪轿车铝合金转向节的锻造成形难题,为同类锻件的生产提供了工艺参考,具有一定的指导意义。
铸造专业的毕业论文

铸造专业的毕业论文随着工业的快速发展,不断有更高效、更环保、更节能的新工艺路线和新技术出现,铸造技术也在不断发展和更新。
本篇毕业论文将从铸造技术、材料、工艺三个方面进行研究,探讨现代铸造技术的发展和应用。
一、现代铸造技术的发展铸造技术是一种重要的制造工艺,在汽车、机械、航空、船舶等行业中都有广泛的应用。
随着技术的不断进步,铸造技术经历了许多变化和发展。
1. 全自动化铸造技术随着计算机和自动化技术的应用,铸造技术也有了很大的进步。
全自动化铸造技术采用自动铸造机,实现了金属熔炼、浇注、晾凉、清理后的整个铸造流程的自动控制。
这种技术大大提高了产量和质量,节省了人力和材料,减少了环保污染。
2. 数值模拟铸造技术数值模拟铸造技术是通过计算机模拟软件,将真实的铸造过程抽象成数学模型,进行数值模拟,并通过模拟结果对实际铸造过程进行优化和控制。
该技术可以预测铸件的内部缺陷,优化喷砂、涂料等工艺,避免金属流动中的缺陷和失误。
3. 智能铸造技术智能铸造技术是将计算机、控制、通讯等先进技术与铸造技术相结合,形成智能化、自动化的铸造生产网络。
这种技术不仅能监控铸造过程中的数据,还可以根据数据预测问题的解决方案并进行控制,大大提高了产品的质量和稳定性。
二、现代铸造材料的应用1. 高强度铸造合金高强度铸造合金是现代铸造材料的一种,其具有高强度、高韧性、高温稳定性等特性。
这种材料在国防、航空、航天等领域得到广泛应用。
2. 稀土元素稀土元素是一类具有重要物理、化学和生物学性质的元素,具有遮蔽轻有害辐射、提高合金耐热性能、增强弹性等优异特性,因此,稀土元素在铸造中应用广泛。
3. 新型材料随着材料科学的发展,新型材料的不断涌现和应用,使得铸造技术也更加精密和全面。
例如,金属陶瓷材料、碳纤维等,这些材料在汽车、飞行器、高速列车等轻质化方面具有广泛的应用前景,为铸造技术带来了新的发展机遇。
三、现代铸造工艺的探索1. 小型化和精密化随着科学技术的不断发展,小型化和精密化成为了现代工业发展的趋势和方向。
金属铸造工艺改进
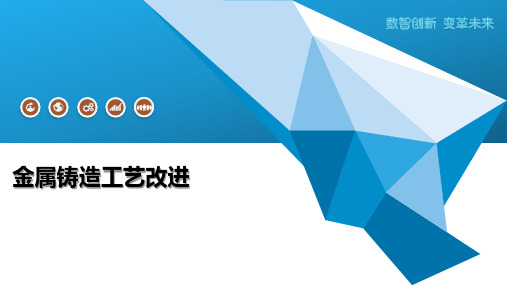
▪ 改进方案一:加强技术研发与创新
工艺改进原理与方法
▪ 热处理与表面处理
1.热处理工艺优化:改进热处理工艺,提高铸件的性能和延长 使用寿命。 2.表面处理技术:采用先进的表面处理技术,提高铸件的耐腐 蚀性、耐磨性和外观质量。 3.环保与能源效率:优先选择环保、节能的热处理和表面处理 技术,降低生产成本和环境负担。
▪ 检测与质量控制
铸造工艺简介与现状
▪ 铸造工艺类型
1.常见的铸造工艺有砂型铸造、精密铸造、离心铸造等。 2.各种铸造工艺有其特点和应用范围,需根据产品特点选择合适的工艺。 3.随着新技术的不断发展,新的铸造工艺类型也在不断涌现。
▪ 铸造工艺材料
1.铸造工艺使用的材料主要有各种金属和合金。 2.不同材料具有不同的物理和化学性质,对铸造工艺有着重要影响。 3.新材料的应用和研发对铸造工艺的发展具有重要意义。
▪ 改进方案一:引入3D打印技术
1.提高铸造精度:3D打印技术可以实现复杂结构的精确制造, 减少传统铸造过程中的材料浪费和误差。 2.快速原型制造:通过3D打印技术,可以快速制造出产品原型 ,缩短产品研发周期,提高生产效率。 3.降低生产成本:采用3D打印技术可以减少生产工序和原材料 消耗,从而降低生产成本。
1.检测技术应用:采用先进的检测技术,对铸件进行全面检测 ,确保产品质量。 2.质量管理体系:建立完善的质量管理体系,实施全面的质量 控制,提高铸件的一致性和可靠性。 3.数据分析与优化:运用数据分析工具,对检测数据进行深入 挖掘和分析,为工艺改进提供数据支持。
铸造生产过程在线快速检测技术研究及应用进展_1
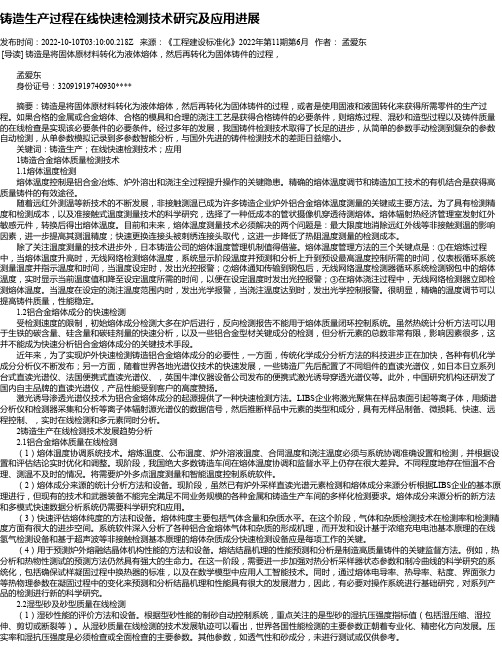
铸造生产过程在线快速检测技术研究及应用进展发布时间:2022-10-10T03:10:00.218Z 来源:《工程建设标准化》2022年第11期第6月作者:孟爱东[导读] 铸造是将固体原材料转化为液体熔体,然后再转化为固体铸件的过程,孟爱东身份证号:32091919740930****摘要:铸造是将固体原材料转化为液体熔体,然后再转化为固体铸件的过程,或者是使用固液和液固转化来获得所需零件的生产过程。
如果合格的金属或合金熔体、合格的模具和合理的浇注工艺是获得合格铸件的必要条件,则熔炼过程、混砂和造型过程以及铸件质量的在线检查是实现该必要条件的必要条件。
经过多年的发展,我国铸件检测技术取得了长足的进步,从简单的参数手动检测到复杂的参数自动检测,从单参数模拟记录到多参数智能分析,与国外先进的铸件检测技术的差距日益缩小。
关键词:铸造生产;在线快速检测技术;应用1铸造合金熔体质量检测技术1.1熔体温度检测熔体温度控制是铝合金冶炼、炉外溶出和浇注全过程提升操作的关键隐患。
精确的熔体温度调节和铸造加工技术的有机结合是获得高质量铸件的有效途径。
随着远红外测温等新技术的不断发展,非接触测温已成为许多铸造企业炉外铝合金熔体温度测量的关键或主要方法。
为了具有检测精度和检测成本,以及准接触式温度测量技术的科学研究,选择了一种低成本的管状摄像机穿透待测熔体。
熔体辐射热经济管理室发射红外敏感元件,转换后得出熔体温度。
目前和未来,熔体温度测量技术必须解决的两个问题是:最大限度地消除远红外线等非接触测温的影响因素,进一步提高其测温精度;快速更换连接头被刺绣连接头取代,这进一步降低了热阻温度测量的检测成本。
除了关注温度测量的技术进步外,日本铸造公司的熔体温度管理机制值得借鉴。
熔体温度管理方法的三个关键点是:①在熔炼过程中,当熔体温度升高时,无线网络检测熔体温度,系统显示阶段温度并预测和分析上升到预设最高温度控制所需的时间,仪表板循环系统测量温度并指示温度和时间,当温度设定时,发出光控报警;②熔体通知传输到钢包后,无线网络温度检测器循环系统检测钢包中的熔体温度,实时显示当前温度值和降至设定温度所需的时间,以便在设定温度时发出光控报警;③在熔体浇注过程中,无线网络检测器立即检测熔体温度。
铸造技术工作计划范文

铸造技术工作计划范文一、工作计划制定背景铸造技术是一门古老而又重要的制造工艺,它是现代工业生产中不可或缺的一部分,尤其在汽车工业、机械工业和航空航天工业中发挥着重要作用。
随着时代的发展和技术的进步,铸造技术也在不断升级和完善。
因此,为了提高公司的生产效率和产品质量,我们有必要对铸造技术进行全面的研究和改进,制定详细的工作计划,以便在研究过程中能有效地监管和执行。
二、工作计划目标1. 提高生产效率:通过改进铸造技术,减少人工和时间成本,提高生产效率,实现生产线的自动化和智能化。
2. 优化产品质量:通过改进铸造工艺和材料技术,提高产品的质量和性能,降低产品的次品率,提高客户满意度。
3. 减少生产成本:通过优化生产工艺,提高原材料的利用率,降低废品率,减少生产成本,提高企业的竞争力。
4. 加强技术创新:通过开展铸造技术的研究和创新,提高企业的核心竞争力,实现可持续发展。
三、工作计划内容1. 铸造技术调研:开展国内外铸造技术的调研,了解行业的最新发展动态和技术趋势,制定公司的技术发展战略。
2. 铸造工艺改进:对公司现有的铸造工艺进行分析和评估,发现存在的问题和瓶颈,提出改进方案并实施,以提高生产效率和产品质量。
3. 材料技术研究:开展新型铸造材料的研究和开发,寻找替代传统材料的新材料,提高产品的性能和使用寿命。
4. 设备更新改造:对公司现有的铸造设备进行评估和更新改造,引进先进的生产设备和技术,实现生产线的自动化和智能化。
5. 生产工艺优化:对公司的生产工艺进行优化和改进,提高产品的一致性和稳定性,降低生产成本,提高生产效率。
6. 质量管理提升:加强铸造产品的质量管理和监控,建立健全的质量管理体系,降低产品的次品率,提高产品的合格率。
7. 人员培训和技术支持:对公司的员工进行铸造技术的培训和技术支持,提高员工的技术水平和专业能力,为技术改进提供有力支持。
四、工作计划实施方法1. 制定详细的工作计划和时间表,明确各项工作的内容、责任人和进度,确保工作有序进行,达到既定目标。
大型锻件的锻造工艺研究进展

大型锻件的锻造工艺研究进展发布时间:2021-08-26T11:39:59.990Z 来源:《工程管理前沿》2021年7卷4月第12期作者:刘威李新宇[导读] 镦粗和拔长是大型锻件锻造的基本工序,随着数值模拟技术的进步,对二者的研究也逐渐深入。
刘威1 李新宇2中国一重铸锻钢事业部水压机锻造厂,黑龙江省齐齐哈尔市, 161041中国一重铸锻钢事业部工艺技术部,黑龙江省齐齐哈尔市,161041摘要:镦粗和拔长是大型锻件锻造的基本工序,随着数值模拟技术的进步,对二者的研究也逐渐深入。
扭转镦粗将锻件与模具的摩擦力转化成利于锻件变形的剪切应力,从而提高锻件的等效应变值,提升锻件的力学性能。
随着对扭转镦粗各工艺参数的优化和扭转镦粗设备的研发,扭转镦粗将在改善锻件质量上发挥更大的作用。
关键词:大型锻件;锻造工艺;镦粗;拔长;研究进展大型锻件广泛应用于能源、交通、国防、钢铁、石化等工业,通常是机械设备的核心部件,例如:重型压力容器、水轮机大轴、汽轮机主轴、齿轮轴、发电机转子、船用大型曲轴、大型模块等,所以对大型锻件的晶粒组织和力学性能要求都比较高。
在某种意义上,大型锻件的制造技术是衡量国家重工业发展水平的一个重要标志。
随着相关工业的快速发展,大型锻件的尺寸越来越大,对质量的要求也日益提高。
因此,提高大型锻件的锻造水平,规范其生产工艺,具有非常重要的意义。
1大型锻件的锻造工艺大型锻件主要特点是体形大、质量要求高、批量小、生产费用高、周期长,其生产过程包括:冶炼、铸造、锻造、热处理等多道工序。
钢锭在铸造过程中,不可避免的会有一些偏析、缩孔、疏松等缺陷,并且钢锭体形越大,钢锭内部的缺陷就越明显,钢锭内部缺陷对大锻件的性能有着重要影响。
锻造消除或改善钢锭内部缺陷的主要目的有两个:“成形”和“改性”,前者将坯料变形到锻件所需要的形状,后者通过改变坯料的微观组织使锻件的力学性能达到要求。
大型锻件所用到的基本锻造工序是镦粗和拔长。
压铸 发展趋势-概述说明以及解释

压铸发展趋势-概述说明以及解释1.引言1.1 概述概述压铸是一种重要的制造工艺,通过将熔化的金属或合金注入到铸型中,然后冷却固化,最终得到所需形状的零件。
随着制造技术的不断发展,压铸技术也在不断演进和改进。
本文旨在探讨压铸技术的发展趋势,以及压铸材料的发展方向。
通过对压铸技术与材料的研究,我们可以深入了解这个领域的发展现状,从而帮助制造业更好地应对日益增长的市场需求和技术挑战。
文章将首先介绍压铸技术的发展趋势。
随着计算机技术的快速发展,压铸模具设计和模拟仿真技术不断改进,使得压铸过程更加精确和高效。
自动化和智能化设备的应用也推动了压铸技术的发展,提高了生产效率和产品质量。
此外,新型的压铸设备和工艺不断涌现,为压铸技术带来了新的发展机遇。
其次,本文将探讨压铸材料的发展趋势。
随着对材料性能要求的不断提高,传统的压铸材料已经无法满足需求。
因此,研究人员不断寻求新的合金材料和改进现有材料的性能。
包括铝合金、镁合金和锌合金等新材料在压铸领域表现出良好的应用潜力。
此外,可再生材料和复合材料等环保型材料也被越来越多地应用于压铸工艺中。
在结论部分,本文将总结压铸的发展趋势。
压铸技术将继续以更高的精度、更高的效率和更低的成本应对市场需求。
同时,压铸材料的发展将朝着更加轻量化、环保和高性能的方向发展。
在展望未来压铸的发展方向时,本文将提出一些思考和建议。
例如,通过进一步提升模拟仿真技术,优化压铸工艺参数的选择和优化,可以实现更好的产品设计和质量控制。
此外,加强合金材料的研发,提高其性能和可塑性,将会进一步推动压铸行业的发展。
总之,压铸技术和材料的发展将为制造业提供更多的机遇和挑战。
本文将通过探讨压铸技术的发展趋势和压铸材料的发展方向,为读者提供对压铸行业未来发展的全面认识和深入思考。
文章结构部分的内容可以按照以下方式编写:文章结构:本文分为引言、正文和结论三个部分,主要探讨压铸的发展趋势。
具体结构如下:1. 引言引言部分主要对文章内容进行概述,并介绍文章的结构和目的。
哈工大铸造方向导师简介

一、微精密铸造成形
率先研发成功了微米尺度的三维复杂构件微铸造成形工艺,并成功制备 出国内外最小的三维微铸件——直径仅为580微米的微齿轮铸件,同时借助 计算机数值模拟和实际实验等方法,对微铸造过程中涉及 的基础理论问题
进行研究了深入系统的研究,诸如微米尺度条件下液态金属的微流动、微 传热、微传质及微凝固规律,以及微铸件的显微组织与力学性能的变化规 律等。
钛合金叶片
定向凝固组织
电磁约束成型
卫星帆板支架
汽车滤清器
某型号导 弹舱体
微观组织模拟
徐达鸣 教授、博导
2 2 新新材材料料定定向向凝凝固固和和特特种种成成形形方方向向
钛合金离心铸造充型与传热过程耦合计算机模拟与工艺实
验研究
冷 坩
电磁场等外场作用下合金
埚 定
凝固耦合传输计算机模拟
向
金属凝固理论与组织控制
非平衡凝固理论 快速凝固喷射成形技术与新材料 非晶及非晶丝软磁合金形成的物理基础、制备与表征 大型复杂轻合金件的凝固过程与工艺理论
△Z/Z (%) 1400
4T
6T
1200
12T
1000
800
600
400
200
0
-200 -100 -80 -60 -40 -20 0 20 40 60 80 100
针对航空、航天、汽车等行业需求的先进精密复杂结构件 精密成型技术,达到:
减重、节能、降低制造成本 结构整体化、轻量化、薄壁化 高精度、高性能、低成本、短周期
孔凡涛 副教授、硕导
11 TTii及及TTiiAAll基基合合金金精精密密热热成成形形
TiAl金属间化合物制备与精密热成形技术 高温钛合金制备与熔模精密铸造技术 核电用材料的制备与成形技术
铸造技术的发展现状与前景探究

铸造技术的发展现状与前景探究铸造技术是一项古老而重要的制造工艺,广泛应用于各个工业领域。
随着科技的进步和需求的增加,铸造技术也在不断发展,不断涌现出新的成果和应用。
本文将探究铸造技术的现状和前景,并对其未来的发展进行展望。
1.1 传统铸造技术传统铸造技术是指基于传统模具和工艺的铸造过程。
它使用沙土、石膏等材料作为模具,在模具中注入熔融金属或合金,经过冷却后取出成品。
传统铸造技术简单、成本低,广泛应用于冶金、机械、汽车等行业。
随着科技的进步,先进铸造技术不断涌现。
其中包括精密铸造技术、快速凝固铸造技术、数字化铸造技术等。
精密铸造技术利用先进的模具制造技术和精确的铸造工艺,生产出高精度、高质量的铸件。
快速凝固铸造技术通过控制金属凝固速度,优化铸件的内部结构,提高铸件的性能。
数字化铸造技术利用计算机辅助设计和制造技术,实现铸件的快速设计和生产。
智能化铸造技术是指运用传感器、自动化控制和人工智能等技术,实现铸造过程的自动化和智能化。
智能化铸造技术可以提高生产效率和产品质量,减少人工操作和能源消耗。
目前,智能化铸造技术已经在一些大型铸造企业得到应用,并取得了良好的效果。
2.1 优化设计和模拟仿真随着计算机技术的发展,优化设计和模拟仿真技术在铸造领域的应用越来越广泛。
优化设计和模拟仿真可以通过数学模型和仿真软件,对铸件的几何形状、工艺参数等进行优化和模拟。
这将大大提高铸造过程的效率和产品的质量,降低成本和能源消耗。
2.2 精密铸造和材料创新精密铸造技术可以生产出高精度、高质量的铸件,广泛应用于航空、航天等高端领域。
随着科技的进步,新型材料不断涌现,对铸造技术提出了更高的要求。
材料创新和精密铸造技术的结合,将推动铸造技术的进一步发展。
2.3 绿色铸造和资源循环利用绿色铸造是指在铸造过程中减少环境污染和资源浪费的铸造技术。
绿色铸造技术可以通过节能、减排等手段,降低能源消耗和环境污染。
铸造过程中产生的废料和废渣可以通过资源循环利用进行再生利用。
铸造技术的发展现状与前景探究

铸造技术的发展现状与前景探究铸造技术是一种利用熔融金属或合金借助模具来制造金属零件的方法,是制造工业中最重要、最基础的工艺之一。
随着现代制造技术的不断发展,铸造技术也在不断创新与改进,取得了一系列重大突破与进展,拓宽了应用领域,具有广阔的发展前景。
铸造技术的发展现状主要体现在以下几个方面:1. 材料的创新:过去,铸造只能用于一些低熔点材料的制造,如铁、铜等。
而现在,随着高温合金和精细合金的研发,铸造技术可以应用于更具挑战性的材料,如钛合金、高温合金等。
2. 工艺的改进:传统的铸造工艺存在一些问题,如缺陷率高、尺寸难控制等。
针对这些问题,工程师们通过改良模具设计、优化熔炼与浇注工艺等手段,大幅度提高了产质量与生产效率。
3. 数字化技术的应用:随着计算机技术的飞速发展,数字化铸造技术(Digital Casting)逐渐成为现代铸造技术的重要组成部分。
通过数字化仿真、虚拟实验等手段,可以在减少试验成本的预测产品形态与性能,提高生产效率。
1. 3D打印技术与铸造的结合:3D打印技术的出现为铸造技术带来了巨大的变革。
通过3D打印技术,可以直接生产出复杂形状的铸造模具,并且可以根据需要调整材料的组成,提高产品性能。
3D打印技术与传统铸造技术的结合,将进一步提高产品的准确性和复杂性。
2. 精密铸造技术的发展:精密铸造技术是近年来铸造技术的研究热点之一。
通过优化模具设计、改善熔炼工艺等手段,可以制造出更精密、更高质量的铸件。
精密铸造技术的发展,将推动铸造工艺向更高端领域发展。
3. 轻质化材料的应用:在航空航天、汽车等领域,轻质化材料的需求越来越大。
铸造技术在制造轻质材料零件方面具有独特的优势。
随着轻质材料的不断研发,铸造技术将在这些领域发挥重要作用。
4. 绿色、环保铸造技术的发展:传统铸造工艺中,燃煤熔炼与浇注过程会产生大量的废气、废渣和废水,对环境造成污染。
绿色、环保铸造技术的研发势在必行。
随着环保意识的提高,绿色铸造技术将成为未来铸造行业的发展方向。
晋公盘的铸造工艺分析

晋公盘的铸造工艺分析丁忠明1 苏荣誉2(1.上海博物馆 2.中国科学院自然科学史研究所)摘要:晋公盘是一件失去考古背景的春秋中期的晋国珍奇青铜器,具有双附耳,三人形足,内底有五类共十九只可旋转的圆雕动物附件,其中鸟喙能启闭,鳖头上半部能伸缩。
本研究采用计算机断层扫描技术(X-ray CT)分析盘的内部结构,揭示出圆雕动物内的立柱结构分两种,动物体内均设有对应的卯与之配合,构成间隙连接;据CT图像,可以判断人形足与盘体铸焊,附耳铸接,而立柱铸焊连接。
这一研究揭示了高级贵族对以特殊工艺铸造玩好器具的偏爱,并在结构和形式及工艺技术上均有所创新。
将晋公盘与子仲姜盘的铸造工艺进行比较,不仅反映出二者在设计、制作中的紧密联系,也体现了春秋中期铸造技术发生的重要变革。
关键词:晋公盘 X-CT 技术铸焊铸接春秋青铜器Abstract: The bronze ritual basin of Jin gong is a rare treasure of the Jin State in the Mid Spring and Autumn Period, but its archaeological context were lost completely.The basin is an elaborated vessel with double handles and three human figure-shaped feet and 19 rotatable animal accessories on the inner bottom,such as birds, turtle and so on. As even the bird beak can opened and closed flexibly, the upper part of the turtle head can stretch out and draw back. Through X-ray CT scanning, it reveals that there are two kinds of column structures in the animal body, which are equipped with sockets to match them and remained some interstitial space.Three basin feet and these small columns are cast welded with the body.The handles are cast joint with the body. This study revealed that the aristocrats preferred to such exquisite bronze artifacts that involved many special techniques and innovation on structure and art forms. Meanwhile, there are some close relationship between the bronze basin of Jin Gong and Zizhong Jiang through comparing their casting techniques. It reflects the important reform and innovation of casting technology during the Mid Spring and Autumn Period.Keywords: Bronze basin of Jin Gong X-CT Technology Cast welding Cast joint Bronzes of the Spring and Autumn Period晋公盘是追缴归藏山西博物院暨山西青铜博物馆的重要文物,腹内铸造七段183字铭文,可据以判断它是春秋中期晋文公为其大女儿孟姬所作的媵器[1]。
复杂镁合金精密铸件的熔模铸造工艺探讨

复杂镁合金精密铸件的熔模铸造工艺探讨摘要:采取熔模型壳铸造WE54镁合金,分析复杂精密铸件成形过程。
经重力浇筑成形得知,铸件充型流动性很差,且有明显的冷隔、流纹以及缩陷问题;采取低压浇铸后,铸件问题得以消除,铸件外表光洁,轮廓清楚,大小精度提升。
关键词:镁合金铸件;熔模型壳;重力;低压镁合金铸件于航空航天、汽车以及电子通讯等行业得到普遍使用,其中石膏型熔模铸造方法简单,复制性好,而且保温性较好,可以成形出内外结构非常繁琐、壁厚较小的零件。
但是,因为镁合金的密度与比热容小,铸造时冷却迅速,极易产生冷隔等问题,制约了镁合金用于航空航天以及国防等领域。
低压浇铸可以在低压作用下顺利底注充型、结晶,已经是关键的接近成型方法模拟。
1、熔模铸造流程、特征及运用相较于与其他铸造手段及零件成形方式,熔棱铸造具备如下特征:应用易熔模,无需开箱启模:选择液体涂料制壳,形壳可以有效复制熔模;热壳铸造,金属液可以有效复制型壳。
所以,熔模铸造出的铸件规格精度能达到CT4~CT6级,压制熔模时,选择型腔表面干净的压型,所以,熔模外表光洁度也很高。
另外,型壳通过耐高温的特别粘结剂与耐火材料加工成的耐火涂料涂挂于熔模上而形成,和熔融金属相接触的型腔内壁粗糙度能达到Ra=0.8 μm~3.2 μm;能够铸造形状非常繁琐的铸件,尤其是能够精密加工高温合金铸件,像喷气式学发动机叶片,它的流线型外廓和冷却用内腔采取机械制造工艺基本不能形成,采取熔模精密铸造既能够实现批量生产,保障铸件的统一性,并防止机械制造后残留刀纹聚集应力;铸件壁厚与最小铸出孔能达到0.5 mm,大小有几毫米甚至上千毫米,质量有1 g~1000kg的零件;加工灵活度高,适应性好,适用于单件、小批量及大批量加工。
因为熔模铸件具有较高的尺寸精度与表层光洁度,能够削减机械生产工作,尽在铸件要求很高的位置留一些生产余量就行,甚至有些零件仅留打磨、抛光余量,无法机械加工就能应用。
- 1、下载文档前请自行甄别文档内容的完整性,平台不提供额外的编辑、内容补充、找答案等附加服务。
- 2、"仅部分预览"的文档,不可在线预览部分如存在完整性等问题,可反馈申请退款(可完整预览的文档不适用该条件!)。
- 3、如文档侵犯您的权益,请联系客服反馈,我们会尽快为您处理(人工客服工作时间:9:00-18:30)。
铸造成形过程研究与创新T he R esearch and Innovati on of Casting Fo r m ing P rocess青岛海洋大学工程学院(266071) 王树杰清华大学(100084) 颜永年 杨伟东【摘要】在对成形系统分解与综合的基础上,提出了成形工艺创新的基本思路。
通过对传统有模型砂型制造过程的分析,指出导致其柔性较低的主要原因是信息过程与物理过程相对独立。
将离散 堆积成形原理与树脂砂工艺有机结合,提出了CAD 模型直接驱动的铸型制造工艺,又称无模型铸型制造。
关键词 成形工艺 快速成形 直接铸型制造 快速铸造Keywords for m ing techn ique ,rap id p ro totyp ing ,direct casting mo ld m anufacturing ,quickcasting成形工艺概述 1.成形的概念成形是利用一定的能量方式,将材料有序地组织成具有确定几何形状和一定功能的三维实体(零件)。
其目标是为了获得物理性能和几何形状都能满足要求的零件。
这个定义包括两方面的内容:一方面指出成形过程是由能量过程、材料过程和信息过程三要素组成;另一方面规定成形的目的是获得要求的几何外形和物理功能。
材料、能量、信息3种主要过程分别可分解为若干子要素。
任何一种成形工艺都可以从这个形态学模型中解释为某些要素状态的组合,成形系统的形态学模型如图1所示。
例如铸造、锻压、金属切削、快速成形等技术的具体工艺。
通过模型可以对各种工艺的可能性和局限性作出综合评价。
2.成形工艺的分类分析成形中物理过程与信息过程的关系,可以将成形工艺分为如下几种类型:1)信息部分地物化于工具之中——受迫成形在此阶段信息经预处理并以形状信息的形式物化于工具之中,如模具、铸型及各种成形型腔就是一种物化信息,铸造、锻压、注射成形及挤压成形等工艺均属此列。
所有此类成形可称为受迫成形,即指利用材料的变形和塑性在特定约束作用下的成形方法。
其特点是一般由模具确定几何形状,信息过程与物理过程在控制上相对独立,相关度低,模具、铸型的制造等辅助过程必须在材料发生变形或变态的物理过程之前完成,而且辅助过程的时间相对较长,当产品或零件的结构发生变化时,必须经过较长的准备时间才能适应,所以导致这类成形工艺的柔性较差。
图1 成形系统的形态学模型2)信息通过对工具的控制结合进物理过程中——去除成形计算机和数控技术的发展使一部分信息处理过程结合进物理过程之中,各种数控机床、电火花加工机床、激光加工设备等均属此类。
这些工艺统称为去除成形,即运用分离的方法把多余的材料有序地从基体上分离出去而成形的方法。
其特点是由几何和性能信息产生控制信息,结合能量过程驱动工具使材料从坯料上减少而成形。
所以信息过程与能量过程紧密相关,相应地减少了零件或产品结构变化时系统的转换时间,尤其是随着成组技术及柔性制造系统的发展,其工艺的柔性有了较大的改善。
3)信息过程与物理过程结合的高级阶段——离散 堆积成形在以上2种成形方法中,成形过程中的材料是完全被动的。
在信息过程与物理过程结合的高级阶・23・《新技术新工艺》・热加工技术 2003年 第6期段,信息通过对工具和材料的同时控制而结合进物理过程之中,材料的形成和零件的成形是同时完成的。
快速成形工艺就属于这种类型,在快速成形工艺中,一个零件可以看作是维数不断增加地堆积而成,有关点、线和面的信息可通过CAD模型或三维扫描获得,这些信息再与工艺参数相结合转化成为N C代码来控制材料的转换和堆积而精确地成形零件,这种过程可看作为离散 堆积成形。
通过离散可获得材料堆积的路径、顺序和约束。
通过堆积,也就是材料的增加,可成形一个三维实体。
其特点是信息过程或与能量过程紧密相关或与材料过程紧密相关,在时间上不独立,使工艺准备和辅助过程省去或与直接成形零件的过程并发,可见快速成形工艺的柔性好,且与批量无关。
铸造成型过程的成形理论分析 铸造的工艺过程从成形学的理论分析,他是典型的受迫成形工艺,以砂型铸造为例,为了使液态金属凝固后具有要求的几何形状,必须依靠铸型提供几何约束。
铸型的制造(造型)是一个重要环节,造型必须先制作工艺模型和准备工艺装备。
模型和工艺装备的制作成本和周期在整个铸件生产过程中所占比例较高。
尤其是对一些大型铸件和单件小批量生产的铸件。
从图2所示传统砂型造型的简化流程中可以看到,制备了模型,就决定了铸件的几何形状。
图2 砂型铸造造型过程简化流程图制作好模型后放入砂箱中,这一过程实质是产生铸件几何形状的信息过程。
再将型砂用某种粘接剂按一定比例混合均匀,填充在放有模型的砂箱中施以震动、冲击或压实,等型砂紧实后取出模型,即可得到浇铸用的砂型,这一过程实质是成形的物理过程。
可见砂型造型过程有2个特点:1.产生几何形状的信息过程和混砂、紧实等的物理过程基本上是分离的,从时间和控制角度看这两个过程可以独立处理;2.砂型的表面成形原理采用整体成形方法,材料基本过程属于在砂箱和模样构成的空腔中的受迫成形过程。
型砂材料的填充、紧实除紧实度要求外,基本上不需要精确控制。
按照成形工艺创新理论,我们发现砂型造型过程可以改为一个信息过程和物理过程相关并发的过程。
将信息过程与物理过程紧密相关(信息控制材料输送、堆积、固化或粘接而成形,材料是被动的),按照铸件的CAD模型几何信息精确控制混砂和填充过程,取消模型的制作环节,这样就产生了CAD模型直接驱动的铸型制造工艺。
该工艺的一个重要特征是无需工艺模型,所以又称为无模型铸型制造(PC M,Patternless Casting M olding),其基本流程如图3所示。
图3 无模砂型制造工艺流程图无模型铸型制造的基本原理 根据离散 堆积成形的基本原理,使造型材料在信息的控制下按照预定的顺序和轨迹填充、固化堆积成形,由于造型材料的堆积过程是连续的,要求造型材料在堆积过程中要迅速形成强度,以便保证堆积过程的连续性。
树脂砂工艺是利用树脂和固化剂迅速发生胶联反应的原理使型砂快速固化成形的,通过调整树脂和固化剂的比例和加入量可以实现固化速度和固化时间的可控,从而可以满足材料堆积固化成形过程的连续性要求。
将离散 堆积成形的基本原理与树脂砂造型工艺有机结合起来,便可实现无模型铸型的快速制造。
PC M工艺基本原理如图4所示。
图4 无模铸型制造基本原理图首先从零件CAD模型得到铸型CAD模型。
由・33・《新技术新工艺》・热加工技术 2003年 第6期铸型CAD数据得到分层截面轮廓数据,再以层面信息产生控制信息,在计算机的控制下,分别喷射树脂和固化剂的2个喷头在每1层铺好压实的型砂上精确地喷射粘接剂和催化剂,粘接剂与催化剂发生胶联反应,粘接剂和催化剂共同作用的部位型砂被固化在一起,其他区域型砂仍为颗粒态干砂。
固化完1层后再粘接下1层,所有的层粘接完之后就可以得到1个三维实体,原砂在粘接剂没有喷射的部位仍是干砂,比较容易清除。
清理出中间未固化的干砂就可以得到1个有一定壁厚的铸型,在砂型的内表面涂敷或浸渍涂料之后就可用于浇铸液态金属。
无模型铸型制造的特点 和传统的铸型制造技术相比,PC M工艺具有其无可比拟的优越性,具体表现在以下几个方面:1.制造时间短、成本低在传统铸造生产中,模型制造费时耗资,且精度不易保证,特别是对一些大型铸件和单件小批量生产的铸件,模型的加工成本和周期在整个铸件生产过程中所占比例过高。
而PC M工艺则完全省去了模型,在缩短砂型制造时间、降低砂型制造成本等诸多方面,都使砂型制造技术有了一个质的飞跃。
2.可制造大、中型铸型PC M工艺扫描系统的运动精度高,制造铸型的尺寸误差可以控制在0.5~1.0mm以内,而且这一误差不会随铸型尺寸增大而显著增大。
成形设备的运动精度一般远小于这一误差,所以,采用PC M工艺制造大、中型铸型是完全可行的。
3.型、芯一体化造型传统造型由于需要分型面、型芯分别制造。
这样往往限制了铸件设计的自由度,增加了工艺环节。
PC M工艺没有起模过程,所以分型面的设计并不是铸件设计的主要障碍。
对于某些铸件,完全可以不要分型面,采用铸型一次成形、型芯一体化造型方法。
其最显著的优点是省去下芯、合箱,减少设计约束和机加工量,使铸件的尺寸、位置精度更容易保证。
4.无拔模斜度由于PC M工艺是无模样的直接堆积造型,没有拔模问题,所以传统铸型设计必不可少的拔模斜度等约束在此失去意义,因而可减轻铸件重量。
5.可制造含自由曲面(曲线)的铸型传统工艺中,含自由曲面或曲线的铸件精度因模型的制造精度而不易保证。
而基于离散 堆积成形原理的PC M工艺,不存在成形的几何约束,因而能够很容易地实现任意复杂形状的造型,且易保证精度。
6.可制造组合零件(功能零件)由于传统铸造工艺的限制,在零件的设计制造过程中,某些功能件需要分成几个零件,分别进行铸造和加工,然后装配而成。
而基于离散 堆积成形原理的PC M工艺,无需模型,不存在起模问题对零件的形状限制,可将传统工艺下的几个零件组合成功能零件一次成形,减少了机加工和装配工作量,彻底消除了加工和装配误差带来的精度损失。
可见这项新工艺还可以带来设计思想的变革,可大幅度提高生产效率,降低制造成本。
7.铸型CAD CA E CAM一体化在铸件CAD模型的基础上,可进行计算机绘制浇注铸型,补偿收缩的尺寸定标,添加圆角;同时确定铸型数与浇注系统类型。
可将铸件制造过程中的收缩、变形通过有限元模拟和误差数据统计,实现早期的、多回路的、闭换控制的误差反馈系统;进一步可用流动 凝固软件来模拟检查原CAD模型的设计和工艺参数的确定是否合理,以便预测、发现并解决铸造过程中的各种问题,从而实现铸造过程的计算机集成制造。
必须看到,PC M工艺也存在着自身的局限性。
首先,与传统有模型造型法对比,该工艺最适合单件小批量、型腔较复杂的大、中型铸件的造型,其制造周期、制造成本及加工效率都是用传统方法无法相比的。
而对于形状简单、大批量生产的小型铸件,与传统造型法相比,PC M工艺则显示不出太大优势。
按照成形工艺创新理论,使信息过程与物理过程紧密相关而产生CAD模型直接驱动铸型成形工艺,不仅使铸造过程实现高度自动化、柔性化、敏捷化,而且带来了设计思想的变革,尤其适合新产品的开发和样件的制作,在追求产品快速化、多样化和个性化的今天,PC M工艺有着广阔的应用前景,必将给传统铸造带来新的活力。
参考文献1.Yan Yongnian.M odern Shap ing2Science and R P P rocess2 es.(in:)P roc.of I N COM’95.Beijing:1995,10:300~3042.杜昭辉.CAD模型直接驱动铸型制造的研究与开发.北京:清华大学,1997,93.D an Xu,Yongnian Yan,R enji Zhang,Q ingp ing L u,etal.D evel opm ent of a Patternless Casting M anufacturing P rocess in the Peop le′s R epublic of Ch ina.P roceedings of the F irst Internati onal Conferenc on R ap id P rototyp ing&M anufacturing.Beijing,1998,7:307~3154.Yongnian Yan,Q ingp ing L u,R enji Zhang,etal.N um eri2 cal Jetting R ap id P rototyp ing m anufacture,8th European Conference on R ap id P rototyp ing.3th GA R PA Gl oable Sum2 m it,2000,4责任编辑 吕德龙 ・43・《新技术新工艺》・热加工技术 2003年 第6期。