MgO对水泥熟料煅烧的影响
高镁石原料对煅烧质量带来的影响与对策措施
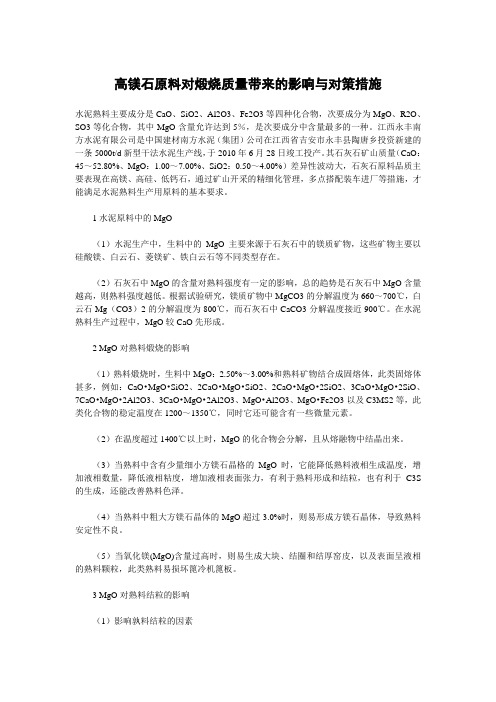
高镁石原料对煅烧质量带来的影响与对策措施水泥熟料主要成分是CaO、SiO2、Al2O3、Fe2O3等四种化合物,次要成分为MgO、R2O、SO3等化合物,其中MgO含量允许达到5%,是次要成分中含量最多的一种。
江西永丰南方水泥有限公司是中国建材南方水泥(集团)公司在江西省吉安市永丰县陶唐乡投资新建的一条5000t/d新型干法水泥生产线,于2010年6月28日竣工投产。
其石灰石矿山质量(CaO:45~52.80%、MgO:1.00~7.00%、SiO2:0.50~4.00%)差异性波动大,石灰石原料品质主要表现在高镁、高硅、低钙石,通过矿山开采的精细化管理,多点搭配装车进厂等措施,才能满足水泥熟料生产用原料的基本要求。
1水泥原料中的MgO(1)水泥生产中,生料中的MgO主要来源于石灰石中的镁质矿物,这些矿物主要以硅酸镁、白云石、菱镁矿、铁白云石等不同类型存在。
(2)石灰石中MgO的含量对熟料强度有一定的影响,总的趋势是石灰石中MgO含量越高,则熟料强度越低。
根据试验研究,镁质矿物中MgCO3的分解温度为660~700℃,白云石Mg(CO3)2的分解温度为800℃,而石灰石中CaCO3分解温度接近900℃。
在水泥熟料生产过程中,MgO较CaO先形成。
2 MgO对熟料煅烧的影响(1)熟料煅烧时,生料中MgO:2.50%~3.00%和熟料矿物结合成固熔体,此类固熔体甚多,例如:CaO•MgO•SiO2、2CaO•MgO•SiO2、2CaO•MgO•2SiO2、3CaO•MgO•2SiO、7CaO•MgO•2Al2O3、3CaO•MgO•2Al2O3、MgO•Al2O3、MgO•Fe2O3以及C3MS2等,此类化合物的稳定温度在1200~1350℃,同时它还可能含有一些微量元素。
(2)在温度超过1400℃以上时,MgO的化合物会分解,且从熔融物中结晶出来。
(3)当熟料中含有少量细小方镁石晶格的MgO时,它能降低熟料液相生成温度,增加液相数量,降低液相粘度,增加液相表面张力,有利于熟料形成和结粒,也有利于C3S 的生成,还能改善熟料色泽。
水泥的颜色影响因素以及调整水泥颜色的方法介绍

水泥的颜色影响因素及控制水泥的颜色主要受熟料的颜色和混合材颜色和掺量的影响。
熟料的颜色主要受氧化铁、氧化镁、氧化铬等氧化物以及煅烧气氛的影响。
在氧化镁含量正常情况下,熟料颜色主要取决于煅烧气氛。
在氧化气氛下,氧化铁为黑色,但在还原气氛下,根据还原气氛的强弱所表现出来的颜色有所不同。
比如:黄色、绿色。
如果还原气氛很强,甚至可以把三价铁还原成金属铁,此时表现为白色。
因此,氧化铁在不同程度的还原气氛下,可以表现出黄色、绿色或白色等不同的颜色。
如果熟料中氧化镁含量很低,也会使熟料颜色偏黄不太美观,因此,生产中有时人为地添加白云石来改善水泥的颜色。
一般熟料中很少含有氧化铬,如果在不含氧化铁的生料中(如白水泥生料)添加0.5%-1%左右的氧化铬,即可生产出绿色水泥熟料。
水泥颜色除了受熟料颜色影响外,很大一部分原因是受混合材的影响,如采用煅烧或自燃过的煤矸石作混合材,或者用红砖、红瓦等作混合材,均会使水泥颜色偏红,影响水泥颜色的美观。
采用白色矿渣等作为混合材,又会使水泥颜色偏淡,均不受用户欢迎。
采用煤渣、粉煤灰等含有煤炭的混合材,将使水泥成黑色,虽然从颜色上会受到用户欢迎,但在水泥中混入太多的炭对水泥性能会带来不好的影响。
调整水泥颜色的方法水泥颜色主要取决于熟料和混合材的颜色,石膏虽然也可改变水泥颜色,但由于国标中SO3含量的限定,所以调整范围有限,再加上掺加比例小,对水泥颜色影响不大。
水泥颜色应有专用的色差计进行测定,但由于一般企业不配置相应的仪器,工程施工方也不进行定量的测定,主要依靠目测判断,而客户水泥颜色主要有变白、变黑、变黄三种颜色,我们通过对水泥胶砂强度检测中成型试件端面颜色的对比观察,总结出一些规律,见表3。
据有关资料介绍,熟料的颜色与所用原材料的颜色无关,影响熟料颜色的主要因素有:熟料的主要化学成分;微量化学成分;矿物组成;煅烧过程的氧化还原气氛;熟料开始冷却的温度,冷却速度等因素的影响。
具体影响程度如表4。
氧化镁对熟料影响
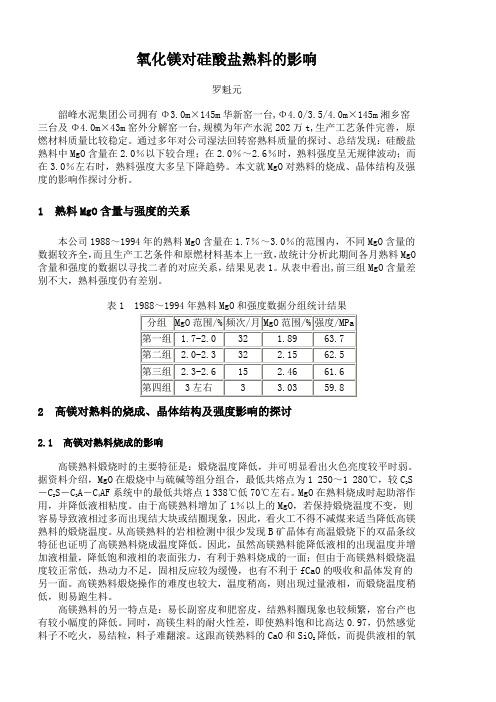
氧化镁对硅酸盐熟料的影响罗魁元韶峰水泥集团公司拥有Φ3.0m×145m华新窑一台,Φ4.0/3.5/4.0m×145m湘乡窑三台及Φ4.0m×43m窑外分解窑一台,规模为年产水泥202万t,生产工艺条件完善,原燃材料质量比较稳定。
通过多年对公司湿法回转窑熟料质量的探讨、总结发现:硅酸盐熟料中MgO含量在2.0%以下较合理;在2.0%~2.6%时,熟料强度呈无规律波动;而在3.0%左右时,熟料强度大多呈下降趋势。
本文就MgO对熟料的烧成、晶体结构及强度的影响作探讨分析。
1 熟料MgO含量与强度的关系本公司1988~1994年的熟料MgO含量在1.7%~3.0%的范围内,不同MgO含量的数据较齐全,而且生产工艺条件和原燃材料基本上一致,故统计分析此期间各月熟料MgO 含量和强度的数据以寻找二者的对应关系,结果见表1。
从表中看出,前三组MgO含量差别不大,熟料强度仍有差别。
表1 1988~1994年熟料MgO和强度数据分组统计结果2 高镁对熟料的烧成、晶体结构及强度影响的探讨2.1 高镁对熟料烧成的影响高镁熟料煅烧时的主要特征是:煅烧温度降低,并可明显看出火色亮度较平时弱。
据资料介绍,MgO在煅烧中与硫碱等组分组合,最低共熔点为1 250~1 280℃,较C3S-C2S-C3A-C4AF系统中的最低共熔点1 338℃低70℃左右。
MgO在熟料烧成时起助溶作用,并降低液相粘度。
由于高镁熟料增加了1%以上的MgO,若保持煅烧温度不变,则容易导致液相过多而出现结大块或结圈现象,因此,看火工不得不减煤来适当降低高镁熟料的煅烧温度。
从高镁熟料的岩相检测中很少发现B矿晶体有高温煅烧下的双晶条纹特征也证明了高镁熟料烧成温度降低。
因此,虽然高镁熟料能降低液相的出现温度并增加液相量,降低饱和液相的表面张力,有利于熟料烧成的一面;但由于高镁熟料煅烧温度较正常低,热动力不足,固相反应较为缓慢,也有不利于fCaO的吸收和晶体发育的另一面。
混凝土中掺入氧化镁的影响原理
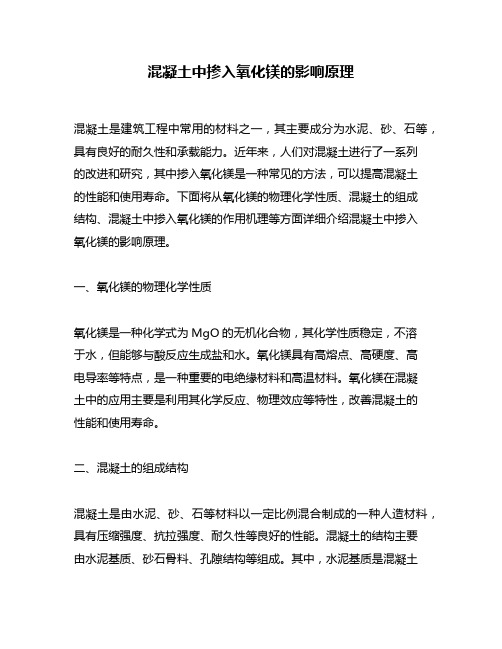
混凝土中掺入氧化镁的影响原理混凝土是建筑工程中常用的材料之一,其主要成分为水泥、砂、石等,具有良好的耐久性和承载能力。
近年来,人们对混凝土进行了一系列的改进和研究,其中掺入氧化镁是一种常见的方法,可以提高混凝土的性能和使用寿命。
下面将从氧化镁的物理化学性质、混凝土的组成结构、混凝土中掺入氧化镁的作用机理等方面详细介绍混凝土中掺入氧化镁的影响原理。
一、氧化镁的物理化学性质氧化镁是一种化学式为MgO的无机化合物,其化学性质稳定,不溶于水,但能够与酸反应生成盐和水。
氧化镁具有高熔点、高硬度、高电导率等特点,是一种重要的电绝缘材料和高温材料。
氧化镁在混凝土中的应用主要是利用其化学反应、物理效应等特性,改善混凝土的性能和使用寿命。
二、混凝土的组成结构混凝土是由水泥、砂、石等材料以一定比例混合制成的一种人造材料,具有压缩强度、抗拉强度、耐久性等良好的性能。
混凝土的结构主要由水泥基质、砂石骨料、孔隙结构等组成。
其中,水泥基质是混凝土的主要强度来源,砂石骨料是其主要承载构件,孔隙结构则影响混凝土的密度、抗渗性等性能。
三、混凝土中掺入氧化镁的作用机理1.改善水泥基质的性能水泥基质是混凝土的主要强度来源,其中主要成分为水泥熟料和水。
在混凝土中掺入一定比例的氧化镁可以改善水泥基质的性能,使其具有更好的抗压、抗弯强度和耐久性。
这是因为氧化镁与水泥熟料反应生成硬质钙镁水泥,其抗压、抗弯强度和耐久性均优于传统的硅酸盐水泥。
此外,氧化镁还能够吸收水泥基质中的游离氢氧根离子,减少空隙和孔隙的存在,提高水泥基质的密实度和抗渗性。
2.优化砂石骨料的结构砂石骨料是混凝土的主要承载构件,其大小、形状、表面性质等因素会影响混凝土的力学性能和耐久性。
混凝土中掺入适量的氧化镁可以优化砂石骨料的结构,使其具有更好的力学性能和稳定性。
这是因为氧化镁能够与砂石骨料表面的游离氢氧根离子反应生成氢氧根离子,从而中和骨料表面的酸性物质,减少骨料表面的活性位点,增加骨料表面的亲水性和胶凝性,提高混凝土中砂石骨料的密实度和稳定性。
水泥熟料的成分
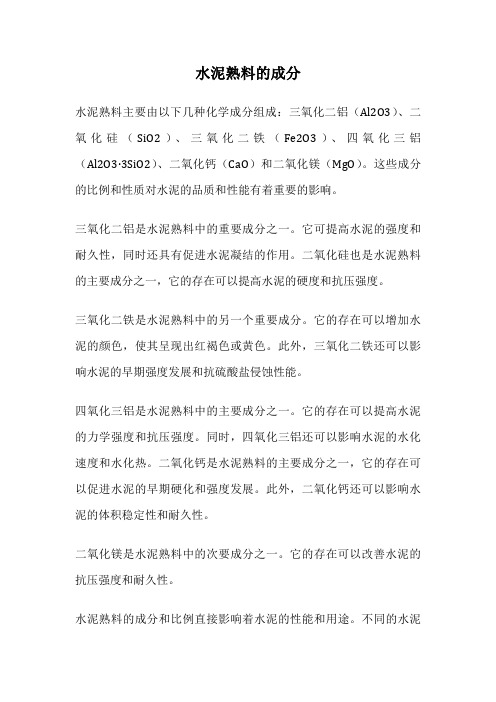
水泥熟料的成分水泥熟料主要由以下几种化学成分组成:三氧化二铝(Al2O3)、二氧化硅(SiO2)、三氧化二铁(Fe2O3)、四氧化三铝(Al2O3·3SiO2)、二氧化钙(CaO)和二氧化镁(MgO)。
这些成分的比例和性质对水泥的品质和性能有着重要的影响。
三氧化二铝是水泥熟料中的重要成分之一。
它可提高水泥的强度和耐久性,同时还具有促进水泥凝结的作用。
二氧化硅也是水泥熟料的主要成分之一,它的存在可以提高水泥的硬度和抗压强度。
三氧化二铁是水泥熟料中的另一个重要成分。
它的存在可以增加水泥的颜色,使其呈现出红褐色或黄色。
此外,三氧化二铁还可以影响水泥的早期强度发展和抗硫酸盐侵蚀性能。
四氧化三铝是水泥熟料中的主要成分之一。
它的存在可以提高水泥的力学强度和抗压强度。
同时,四氧化三铝还可以影响水泥的水化速度和水化热。
二氧化钙是水泥熟料的主要成分之一,它的存在可以促进水泥的早期硬化和强度发展。
此外,二氧化钙还可以影响水泥的体积稳定性和耐久性。
二氧化镁是水泥熟料中的次要成分之一。
它的存在可以改善水泥的抗压强度和耐久性。
水泥熟料的成分和比例直接影响着水泥的性能和用途。
不同的水泥熟料可以生产出不同性能的水泥,如硅酸盐水泥、铝酸盐水泥和磷酸盐水泥等。
因此,在生产过程中,需要根据不同的需求选择合适的水泥熟料成分和比例。
水泥熟料的成分是制造水泥的重要因素之一。
三氧化二铝、二氧化硅、三氧化二铁、四氧化三铝、二氧化钙和二氧化镁是水泥熟料中的主要成分。
它们的存在和比例直接影响着水泥的性能和品质。
通过合理调配和控制水泥熟料的成分,可以生产出符合不同需求的高性能水泥。
矿化剂对熟料煅烧和质量的影响

矿化剂的分类:矿化剂:能改善水泥生料的易烧性,加速熟料矿物形成的少量外加剂。
助熔剂:能降低液相出现温度的少量外加剂。
氟化钙的影响:其它组分的影响:萤石、石膏复合矿化剂:掺氟硫复合矿化剂,形成熟料矿物的影响因素较多:熟料组成、CaF2/SO3的比值、烧成温度的高低。
(1)多采用高饱和系数、低硅率和高铝率配料。
(2)石膏掺量,以熟料中SO3=1.0~1.5%为宜;萤石掺量,以熟料中CaF2=0.4~0.8%为宜;CaF2/SO3=0.35~0.6%为宜。
(3)降低液相出现的温度,降低液相粘度,使A矿形成温度降低150~200℃,促进A矿形成。
有时出现不正常凝结现象:CaF2/SO3比偏高,煅烧温度偏低,KH偏低,IM偏高,窑内出现还原气氛,形成较多的C11A7·CaF2,若所加石膏不足以阻止其迅速水化,就会发生闪凝。
CaF2/SO3比偏高,煅烧温度过高,KH偏高,IM偏低,形成C6AF2,C3A少;C6AF2和氟固溶在C3S中,减缓C3S的水化,从而慢凝。
碱:(1)降低液相出现的温度,增加液相量,起助熔作用;(2)增加液相粘度,液相中质点扩散困难,烧结后料散;当有矿化剂时,R2O转变为R2SO4,液相粘度下降;(3)粘附在旋风预热器上形成结皮,严重时堵塞卸料管,影响窑正常生产;(4)取代CaO形成KC23S12、NC8A3等无胶凝性含碱化合物,析出CaO,使C2S难以再吸收CaO形成C3S,增加fCaO含量,C3S发育差,影响28天强度;当有矿化剂时,可促使含碱矿物分解;(5)水泥中含碱量高,易生成钾石膏(K2SO4·CaSO4·H2O),使水泥快凝;(6)在混凝土中,水泥中的碱能与活性集料发生“碱集料反应” ,使混凝土膨胀破坏;(7)碱还能使混凝土表面起霜(白斑)。
氧化钙:(1)降低熟料烧成温度,增加液相量,降低液相粘度,具有助熔作用;(2)主要固溶于铁相,能改善水泥色泽;(3)MgO过多,形成游离方镁石结晶,影响水泥的安定性。
熟料质量控制及煅烧方面的影响因素

培训材料熟之三料质量控制及煅烧方面的影响因素一、熟料质量控制的重要性1、熟料质量是确保水泥质量的核心,熟料质量达不到要求,难以磨制优质的水泥产品。
其中配料和煅烧是决定熟料质量的关键。
2、从生料到熟料,是一个化学反应过程。
化学反应,最基本的核心就是要求参预化学反应的物质间的比例要满足理论要求。
参预化学反应的某一物质的量,不得过剩或者不足,否则,化学反应形成的结果,不是当初设计的结果。
因此,熟料生产过程实际上要求是很精细的,不是表面上的那种粗糙现象。
3、设计合理的熟料率值,通过良好的煅烧,才干生产出优质的水泥熟料。
1、原料磨工艺变化现代水泥企业,以节能高效为主要导向,装备和工艺流程日益简化和高效。
2、原料磨由过去的球磨机改为现代立磨,原料磨工艺装备的改变,对产品质量的影响。
3、球磨机的工艺特点,决定了生料细度更加均匀,900 孔细度小,只在 3.0%以内, 1800 孔细度在 12%以内。
立磨的生料细度粗, 900 孔细度在 6.0-8.0%, 1800 孔细度在 22%摆布。
由上看出,现代水泥工业改成立磨后,生料的颗粒级配产生了较大的变化,立磨的生料粗大颗粒占比例明显上升,中等颗粒的比例,也较球磨机增加了一倍。
4、现代水泥工业、细度标准的变化。
80 年代,国家旋窑管理规程对细度有控制要求,最开始的标准规定生料细度小于等于 10%,作为一次水泥工艺管理的标准来执行,其后更改为 12%。
后来随着先进水泥工艺发展,生料细度作为一次过程控制指标,再也不强制执行,由企业根据自身生产需要自行控制。
质量体系认证,也将细度标准作为企业自行制定来审核,细度标准被企业自身不断放松标准。
按照现行立磨的生产工艺,生料细度按 10%、12%、16% 等等标准,已经无法满足当前立磨工艺的要求,根据立磨的特点及与窑的产能关系,细度只能控制在 20-22%之间,即使控制较好的工厂细度也在 8 摆布。
但是 , 目前的细度控制指标,不表示细度粗对煅烧没有影响。
熟料氧化钙和氧化镁含量标准
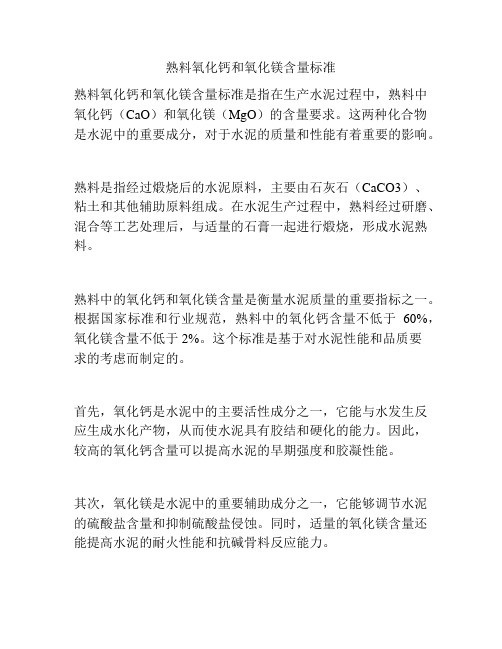
熟料氧化钙和氧化镁含量标准熟料氧化钙和氧化镁含量标准是指在生产水泥过程中,熟料中氧化钙(CaO)和氧化镁(MgO)的含量要求。
这两种化合物是水泥中的重要成分,对于水泥的质量和性能有着重要的影响。
熟料是指经过煅烧后的水泥原料,主要由石灰石(CaCO3)、粘土和其他辅助原料组成。
在水泥生产过程中,熟料经过研磨、混合等工艺处理后,与适量的石膏一起进行煅烧,形成水泥熟料。
熟料中的氧化钙和氧化镁含量是衡量水泥质量的重要指标之一。
根据国家标准和行业规范,熟料中的氧化钙含量不低于60%,氧化镁含量不低于2%。
这个标准是基于对水泥性能和品质要求的考虑而制定的。
首先,氧化钙是水泥中的主要活性成分之一,它能与水发生反应生成水化产物,从而使水泥具有胶结和硬化的能力。
因此,较高的氧化钙含量可以提高水泥的早期强度和胶凝性能。
其次,氧化镁是水泥中的重要辅助成分之一,它能够调节水泥的硫酸盐含量和抑制硫酸盐侵蚀。
同时,适量的氧化镁含量还能提高水泥的耐火性能和抗碱骨料反应能力。
除了国家标准和行业规范外,不同地区和不同企业对于熟料中氧化钙和氧化镁含量也有一定的差异要求。
一方面,这是因为不同地区的原材料成分和特点存在差异;另一方面,也与不同企业的生产工艺和技术水平有关。
为了保证水泥的质量和性能,生产企业需要对原材料进行严格的检测和控制。
常见的检测方法包括化学分析、X射线衍射等。
通过这些方法可以准确地测定熟料中氧化钙和氧化镁的含量,并及时调整生产工艺,以满足产品质量要求。
总之,熟料中的氧化钙和氧化镁含量标准是衡量水泥品质的重要指标之一。
根据国家标准和行业规范,熟料中的氧化钙含量不低于60%,氧化镁含量不低于2%。
生产企业需要通过严格的检测和控制,确保产品质量达到标准要求。
高MgO石灰石对生产的影响及对策
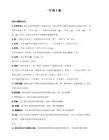
高MgO石灰石对生产的影响及对策一、MgO对熟料生产和性能的影响概述原料中所含的MgO经高温煅烧,其中部分与熟料矿物结合成固溶体,部分溶于液相中。
当熟料含有少量MgO时,能降低熟料的烧成温度,增加液相数量,降低液相粘度,有利于熟料烧成,还能改善水泥的色泽。
在硅酸盐水泥中,MgO 与主要熟料矿物相化合的最大含量为2%(以质量计),超过该数量的部分就在熟料中呈游离状态,以方镁石的形式出现。
方镁石与水反应生成Mg(OH)2,体积较f-MgO增大,而且反应速度缓慢,导致已经硬化的水泥石膨胀,造成MgO膨胀性皲裂。
石灰石中MgO可以碳酸镁、白云石、菱镁矿、铁白云石、水镁石( Mg(O H)2)等不同形式存在。
业已发现,在同样细度和快冷条件下,MgO在石灰石中以硅酸镁形式存在时,可获得均匀分布和细小(1~5微米)的方镁石晶体,而以白云石或菱镁矿形式存在时,则易产生粗大的(25~30微米)方镁石晶体。
众所周知,当熟料中含有粗颗粒方镁石晶体时,MgO含量超过2%就会产生有害作用。
熟料中方镁石晶体的生长速度明显地与不同含镁矿物分解出MgO的温度有关,分解温度越低,晶体生长的机会就越大,这在MgO与其它氧化物反应形成过度相的情况下尤其如此。
MgO可能形成过度相,否则将会影响熟料形成程序。
在水泥生料中存在极限范围的MgO是合乎需要的,它能使液相最初出现温度降低10°C,然而MgO不能显著地影响熟料的形成速度。
熟料中的MgO高至3%时,阿利特相含有恒定的MgO的比例,一般可达0.74%。
由于降低了活化能,加快了α—C2S→α’—C2S的转化,导致冷却时弱水硬性的β-C2S的稳定,降低了熟料活性。
二、国家有关技术标准规定GB175-2007通用硅酸盐水泥规定:硅酸盐水泥、普通硅酸盐水泥中Mg O≤5.0%,如果水泥压蒸安定性试验合格,允许放宽至6.0%;矿渣水泥、火山灰水泥、粉煤灰水泥、复合水泥中MgO≤6.0%,大于6.0%时,需进行压蒸安定性试验并合格。
《水泥质量与检验题库》简答题两篇

《水泥质量与检验题库》简答题两篇水泥质量与检验题库——简答题(一)简答题:1. 什么是熟料立升重?答:就是每立升5~7mm粒径的熟料重量,正常生产时每升重的波动范围为±75克之内。
2. 什么是结皮?答:物料在设备或气体管道内壁上, 逐步分层粘挂形成的覆盖物。
它多发部位是窑尾下料斜坡、烟道,特别是缩口下部,以及最后一级旋风预热器的锥体部位。
3. 什么是均化效果?答:衡量各类均化设备性能的重要依据之一。
均化前后,被均化物料中某组分的标准偏差之比,称为该均化设备的均化效果。
4. 何为凝结时间?答:指水泥从加水拌合开始到失去流动性,即从可塑状态发展到固体状态所需要的时间。
5. 水泥凝结时间分为哪两种?分别是什么?答:水泥的凝结时间分为初凝时间和终凝时间。
初凝为水泥加水拌合时起至标准稠度净浆开始失去可塑性所需的时间;终凝为水泥加水拌合时起至标准稠度净浆完全失去可塑性并开始产生强度所需的时间。
6. 安定性的定义是什么?答:安定性又称体积安定性,是指水泥硬化后体积变化的均匀性。
7. 引起安定性不良的原因有哪三个?答:①熟料中游离氧化镁(方镁石)过多。
水泥中的方镁石(MgO)在水泥凝结硬化后,会与水生成Mg(OH)2。
该反应比过烧的氧化钙与水的反应更加缓慢,且体积膨胀(148%),会在水泥硬化几个月后导致水泥石开裂。
②水泥中SO3含量过高。
当石膏掺量过多时,水泥硬化后,在有水存在的情况下,它还会继续与水化铝酸钙反应生成高硫型水化硫铝酸钙(钙矾石,简写成AFt),体积约增大1.5倍,引起水泥石开裂。
③熟料中游离氧化钙过多。
水泥熟料中含有游离氧化钙,其中部分经较高温度煅烧的CaO在水泥凝结硬化后,会缓慢与水生成Ca(OH)2。
该反应体积膨胀(98%) ,使水泥石发生不均匀体积变化。
8. 什么是筛余?答:粉状物料细度的表示方法。
一定质量的粉状物料在试验筛上筛分后所残留于筛上部分的质量百分数。
9. 什么是试验筛?答:测定粉状物料细度时所用的具有标准规格的筛子。
碱和MgO对熟料性能的影响
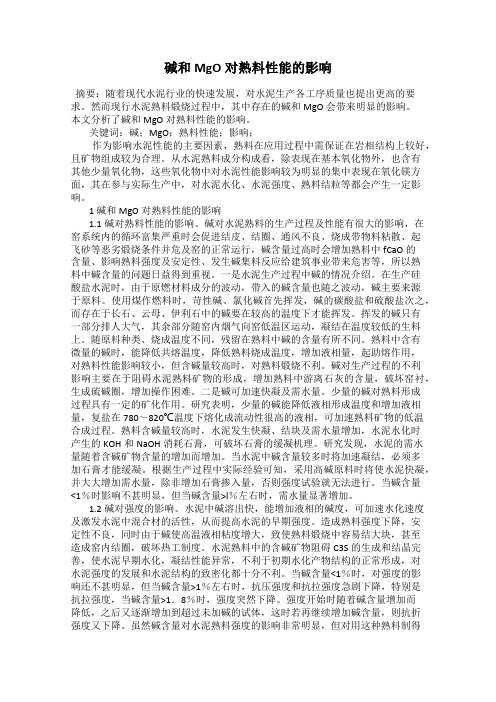
碱和MgO对熟料性能的影响摘要:随着现代水泥行业的快速发展,对水泥生产各工序质量也提出更高的要求。
然而现行水泥熟料煅烧过程中,其中存在的碱和MgO会带来明显的影响。
本文分析了碱和MgO对熟料性能的影响。
关键词:碱;MgO;熟料性能;影响;作为影响水泥性能的主要因素,熟料在应用过程中需保证在岩相结构上较好,且矿物组成较为合理。
从水泥熟料成分构成看,除表现在基本氧化物外,也含有其他少量氧化物,这些氧化物中对水泥性能影响较为明显的集中表现在氧化镁方面,其在参与实际生产中,对水泥水化、水泥强度、熟料结粒等都会产生一定影响。
1 碱和MgO对熟料性能的影响1.1碱对熟料性能的影响。
碱对水泥熟料的生产过程及性能有很大的影响,在窑系统内的循环富集严重时会促进结皮、结圈、通风不良、烧成带物料粘散、起飞砂等恶劣煅烧条件并危及窑的正常运行,碱含量过高时会增加熟料中fCaO的含量、影响熟料强度及安定性、发生碱集料反应给建筑事业带来危害等,所以熟料中碱含量的问题日益得到重视。
一是水泥生产过程中碱的情况介绍。
在生产硅酸盐水泥时,由于原燃材料成分的波动,带入的碱含量也随之波动,碱主要来源于原料。
使用煤作燃料时,苛性碱、氯化碱首先挥发,碱的碳酸盐和硫酸盐次之,而存在于长石、云母、伊利石中的碱要在较高的温度下才能挥发。
挥发的碱只有一部分排人大气,其余部分随窑内烟气向窑低温区运动,凝结在温度较低的生料上。
随原料种类、烧成温度不同,残留在熟料中碱的含量有所不同。
熟料中含有微量的碱时,能降低共熔温度,降低熟料烧成温度,增加液相量,起助熔作用,对熟料性能影响较小,但含碱量较高时,对熟料煅烧不利。
碱对生产过程的不利影响主要在于阻碍水泥熟料矿物的形成,增加熟料中游离石灰的含量,破坏窑衬,生成硫碱圈,增加操作困难。
二是碱可加速快凝及需水量。
少量的碱对熟料形成过程具有一定的矿化作用。
研究表明,少量的碱能降低液相形成温度和增加液相量,复盐在780~820℃温度下熔化成流动性很高的液相,可加速熟料矿物的低温合成过程。
水泥中控技能大赛案例分析题

水泥中控技能大赛案例分析题案例分析:1.熟料样的化学全分析结果如表所示,请对该结果作分析。
解:看熟料全分析结果时,一要看三率值(KH、n、p 是否在要求的范围内;二要看熟料中C3S + C2S含量是否高,C3A+C4AF含量是否为20~22%;三要看MgO 是否超出范围, 如超出范围, 就是废品,不能直接粉磨出厂,只能与低MgO 熟料搭配合格后才能粉磨出厂; 四要看熟料化学组成及矿物含量多少,以便分析煅烧难易的影响因素。
由上表可见,C3A+C4AF只有17.89%,KH为0.833,都太低,而n高达2.81。
该熟料化学成分波动太大,煅烧中因熔剂矿物成分含量过少,结粒困难,易出现“飞砂",熟料标号也不会高。
根据这种情况,要建议提高KH值和熔剂矿物含量,增加铁含量, 降低n值,减少SiO2含量,使配料达到要求。
2. 蓖冷机出口熟料温度总是偏高,试分析产生的原因并提出处理建议。
解:可能的原因和现象:⑴冷却风量不够; ⑵蓖床速度过快, 熟料冷却后移;⑶蓖床上出现“红料流”或熟料结大块;⑷冷却机内有高温区的热风窜至冷端。
主要操作处理:⑴适当增加有关风室的风量;⑵适当减慢蓖速;⑶冷却机如无隔墙,可以增加隔墙,以控制冷端风量的分布。
3. Y水泥厂的增湿塔有湿底现象,该如何解决这个问题?答:原因分析:⑴喷嘴调整不佳; ⑵喷嘴内结垢堵塞或喷嘴接缝处漏水(喷嘴密封垫失效);⑶管路漏水,压力不足;⑷水泵故障.处理方法:⑴停窑检修时重新调整喷嘴;⑵停窑检修时清洗或更换喷嘴; ⑶堵漏管路、调整水泵工作压力;⑷启动备用水泵。
查明原因, 尽快检修更换部件;⑸湿窑灰立刻从旁路排出。
4. 煤源紧张,ZD水泥厂在煅烧时掺用了灰分较大的劣质煤,要注意什么问题? 答:劣质煤的特点是灰份高,燃烧慢,发热量低。
使用劣质煤煅烧时,黑火头长,窑内温度低后不易烧起来,而且易结圈。
使用劣质煤时,首先应根据煤的成分改变配料, 采用比较易烧的方案;同时改进喷煤系统,加强煤风混合,加快燃烧速度。
影响水泥安定性性能的因素
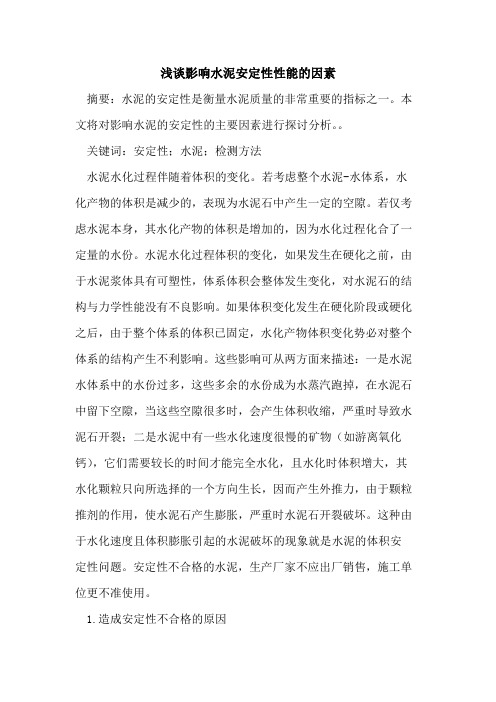
浅谈影响水泥安定性性能的因素摘要:水泥的安定性是衡量水泥质量的非常重要的指标之一。
本文将对影响水泥的安定性的主要因素进行探讨分析。
关键词:安定性;水泥;检测方法水泥水化过程伴随着体积的变化。
若考虑整个水泥-水体系,水化产物的体积是减少的,表现为水泥石中产生一定的空隙。
若仅考虑水泥本身,其水化产物的体积是增加的,因为水化过程化合了一定量的水份。
水泥水化过程体积的变化,如果发生在硬化之前,由于水泥浆体具有可塑性,体系体积会整体发生变化,对水泥石的结构与力学性能没有不良影响。
如果体积变化发生在硬化阶段或硬化之后,由于整个体系的体积已固定,水化产物体积变化势必对整个体系的结构产生不利影响。
这些影响可从两方面来描述:一是水泥水体系中的水份过多,这些多余的水份成为水蒸汽跑掉,在水泥石中留下空隙,当这些空隙很多时,会产生体积收缩,严重时导致水泥石开裂;二是水泥中有一些水化速度很慢的矿物(如游离氧化钙),它们需要较长的时间才能完全水化,且水化时体积增大,其水化颗粒只向所选择的一个方向生长,因而产生外推力,由于颗粒推剂的作用,使水泥石产生膨胀,严重时水泥石开裂破坏。
这种由于水化速度且体积膨胀引起的水泥破坏的现象就是水泥的体积安定性问题。
安定性不合格的水泥,生产厂家不应出厂销售,施工单位更不准使用。
1.造成安定性不合格的原因在水泥矿物中,对安定性有影响的矿物有三种:石膏、方镁石和游离氧化钙,习惯上仅指游离氧化钙的影响。
1.1石膏(so3)影响它是水泥的调凝剂,是水泥不可缺少的成份。
石膏的化学成份为硫酸钙,分子式为caso4.2h2o,其中caso4在水泥化学中看成是cao+so3。
水泥水化时,so3会延缓水泥烹中铝酸三钙的水化,使水泥不会急凝。
石膏在水泥中的掺量应合适,据研究,其合适的掺入量是水泥加水后24小时左右被耗尽。
当石膏过量时,不但对水泥的凝结时间有影响,过多的so3在水泥感化阶段会继续水化,生成钙矾石(3cao·al2o3·3caso4·32h2o),同时体积膨胀,严重时引起水泥石开裂。
石灰石粉对P·O42.5R水泥性能的影响
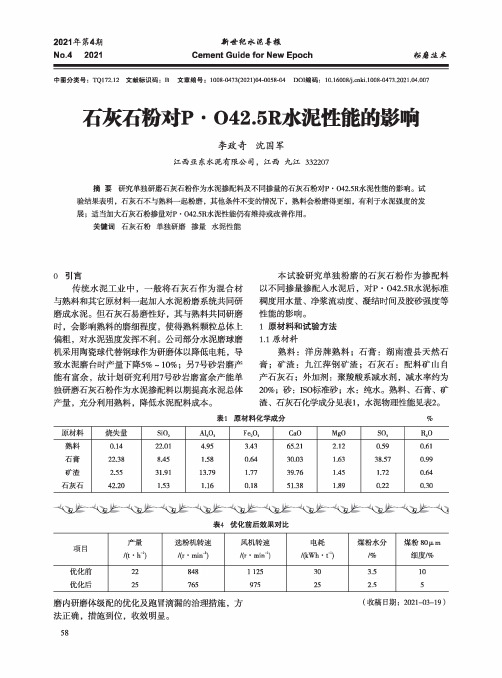
用标准试验小磨按表3配比研磨以熟料为主的 物料A、B,然后分别掺配8%石灰石粉混合均匀配 制成P • O42.5R水泥,与相同配比试验小磨共同粉
磨的P ■ O42.5R水泥(见表4)进行强度对比。 从表5中可以看出,在水泥配方相同的情况
下,单独掺配石灰石粉的P ■ O42.5R水泥强度高于 共同粉磨石灰石的P - O42.5R水泥。结合表3、表4 水泥配方A与C、B与D的小磨研磨时间,掺配石灰 石的水泥更快达到目标比表面积,表明石灰石易磨 性好,共同粉磨时会影响熟料的磨细,对水泥强度 发挥不利。
8.9
抗压强度/MPa
3d
28 d
33.3
49.4
30.7
46.7
33.1
50.0
28.3
45.2
59
2021年第4期 No.4 2021
新橙紀水泥导报 Cement Guide for New Epoch
務磨猛术
表6不同掺量的石灰石粉对PQ42.5R水泥性能的影响
序号
P ■ O42.5R①
P - O42.5R②
数
表2水泥物理性能 抗折强度/MPa
/min
3d
28 d
157
6.4
9.2
抗压强度/MPa
3d
28 d
31.2
57.2
标准稠度 用水量 /%
雷氏夹 安定性
/mm
23.0
1.0
石灰石粉由标准试验小磨($500 mm x 500 mm, 48 r/min )研磨而成,比表面积4 300 cm2/g, 45|JLm 筛余37.6%;矿渣粉也由标准试验小磨研磨而成, 比表面积3 870 cm2/go
31 minlO s
熟料强度

查看文章水泥熟料烧成:一分温度一分强度2010-07-12 14:21水泥生产控制中,一般采用Bouge法计算熟料中各种矿物的含量。
该计算方法的局限性多位学者早有论述。
假定矿物组成计算准确,也常常不能与熟料的性质对应起来。
其原因在于:(1)矿物有多种晶型C3A有立方与正交晶型(2)各种矿物均可固熔一部分杂质离子,导致晶体性质发生变化(3)铁相为连续固溶体,组成范围变化大(4)不同的煅烧温度均会影响矿物晶型、晶粒大小,不同冷却制度也会导致晶型、晶粒大小的变化。
四种熟料矿物中C3S对强度的影响最大。
究竟哪种晶型强度高?哪些因素会影响晶型的存在形式呢?通常认为C3S对称性高的晶型强度高。
R型强度最高,M1型比M3型的强度高10%。
工业熟料中阿利特晶型一般是M1和M3型,Maki认为,两种类型的阿利特在工业生产的熟料中,都很常见。
不规则的M1型核,具有环带结构(M3型)。
影响阿利特相组成(M1和M3的比例)的主要因素是阿利特在从液相中结晶时固溶杂质的种类和数量。
杂质离子在阿利特中的固溶量依赖于阿利特的生长速度以及液相中杂质离子的浓度。
阿利特两种生长模式为:稳定生长模式和不稳定生长模式。
在这两种不同的模式下形成的阿利特微观形貌有很大不同。
不稳定模式下不均匀生长的阿利特,以很快的速率长大,带有大量的包裹体、晶粒尺寸大、形状不规则,其中固溶有较多的杂质及Al2O3和Fe2O3,主要是M1型。
在稳定模式下长大的阿利特,晶体中少见包裹体、杂质固溶量相对较少,主要是M3型。
据此,Chikawa等将阿利特的晶型晶貌形成分为3个动力学阶段:(1)高速成核低速长大(成核控制期);(2)低速成核高速长大(长大控制期);(3)低速成核低速长大(过渡期)。
分别对应于不稳定形成模式、稳定形成模式和过渡模式。
还研究了加热速度和掺杂对阿利特晶体微观形貌的影响,认为加热速率影响阿利特形成环境(液相),尤其是烧成早期的过饱和度,由此改变阿利特结晶的形貌和晶粒大小,但加热速率与阿利特晶体亚微观结构之间的关系不是简单对应的。
煅烧过程中氧化镁行量过高问题

表5调整后熟料物理性能
方案80μm筛余/%比表面积(m2/kg)标准稠度用水量/% SO3
/%凝结时间抗折强度
/MPa抗压强度/MPa
初凝终凝3d 28d 3d 28d
如果熟料MgO含量较高(3.2%~4.2%),液相表面张力大幅度下降,含4%MgO时的表面张力为0.51N/m,迫使其煅烧温度要比正常温度低,煅烧范围要比正常窄,不利于f-CaO的吸收和晶体发育。表现在熟料外观结粒细小,飞砂严重。同时,在煅烧方面表现为易烧性好,但烧结范围变窄,操作难度大。
如果熟料MgO含量过高(>4.2%),熟料出现结球严重,窑电流平均达450A以上,频繁出现结大球,冷却破碎之后的熟料大多数为黄块,窑头飞砂严重。我们采取常规的降铁措施,现象不但没有扭转,反而更加恶劣,反常规调整,却有效果。从资料[1]得知,MgO含量>4.2%时,熟料液相黏度增加,使阿利特结晶困难,从而使结粒变大,窑内极易结圈、结蛋。
3.3.2降低并稳定入窑分解率
控制入窑物料表观分解率在90%左右,最高不超过94%。在生产实践中,常出现因为入窑物料分解率过高达96%,熟料升重降低,质量下降。分析认为,由于分解率过高,也就是生料预烧较好,使液相提前出现,窑内碳酸盐分解带缩短,固相反应带相应拉长,使化学反应产物活性降低,从而导致熟料升重降低,熟料实物质量下降。
配方2 2.3 353 23.6 2.3 105 150 6.2 9.0 32.5 62.6
配方3 2.3 350 23.6 2.2 100 145 6.0 8.9 32.1 61.9
预分解窑使用高镁原料的危害及预防措施

在水泥生产中,MgO能够降低熟料煅烧温度,但过多的MgO,在熟料形成过程中生成方镁石晶体,会引起水泥的安定性不良。
对我国大多数预分解窑水泥厂来说,所用原料MgO含量都比较低,但也有一些预分解窑厂使用含镁量较高的原料,不能低估高镁原料给预分解窑煅烧操作带来的危害。
预分解窑采用高镁原料,通常会给煅烧操作带来如下的困难:①熟料液相量增大,液相粘度降低,操作中窑皮明显增长,如由正常煅烧时15-16m左右,增长到22m以上,有时甚至长达30m上。
②浮窑皮厚度增加,最厚时可达到600mm,会严重影响窑内风。
③熟料结粒明显增大,粗细不均,窑内常出现大料块和结大蛋象。
④窑内情况恶化,熟料的质量降低,常因大蛋和后圈而停窑,给窑的连续运转和稳定操作带来很大困难。
针对以上问题,采用高镁原料的预分解窑,在生产中应采取如下措施:①严格控制生料,稳定 MgO含量。
熟料中MgO含量应小于4.6%,生料中MgO 应小于2.6%。
原料进厂应严把质量关,分采点按镁高低分类储存。
在石灰石破碎阶段,合理搭配,使配料用石灰石MgO的含量波动低,变化小。
②调整配料方案。
预分解窑普遍采用“高硅酸率、高铝氧率、中饱和比”的配料方案。
率值的控制一般为KH=0.90±0.02,SM=2.7±0.1,M=1.7±0.1,这一方案,多数能保证熟料中硅酸盐矿物的总量,并有较大的烧结范围。
但由于MgO含量的增加,熟料在高温带的液相量相应增加,液相粘度降低,易结大块。
其作用可看作与Fe2O3相似。
针对这种现象,应适当调整配料方案。
即降低熟料中 Fe2O3含量,同时适当降低AI2O3,含量,提高SM和IM值。
③稳定入窑物料分解率。
稳定炉温,有效地控制入窑物料分解率,可减少因MgO高而造成的结皮堵塞现象,同时避免因入窑物料分解率过低引起的“慢窑”和“跑生”,抑制厚窑皮的生长。
④加强操作,严格检查。
使用高镁原料,C5下料管常会发生堵塞,可在C5的下料管上,增加吹堵装置,完善测压报警系统,可有效防范故障,提高至的运转率。
生料成分对熟料煅烧的影响
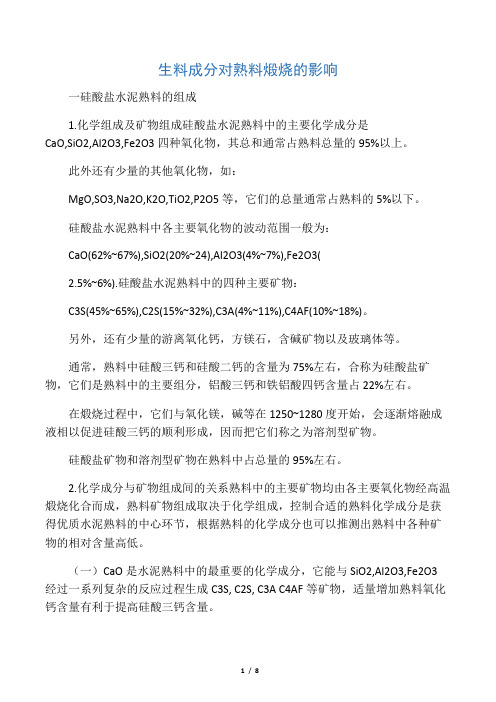
生料成分对熟料煅烧的影响一硅酸盐水泥熟料的组成1.化学组成及矿物组成硅酸盐水泥熟料中的主要化学成分是CaO,SiO2,Al2O3,Fe2O3四种氧化物,其总和通常占熟料总量的95%以上。
此外还有少量的其他氧化物,如:MgO,SO3,Na2O,K2O,TiO2,P2O5等,它们的总量通常占熟料的5%以下。
硅酸盐水泥熟料中各主要氧化物的波动范围一般为:CaO(62%~67%),SiO2(20%~24),Al2O3(4%~7%),Fe2O3(2.5%~6%).硅酸盐水泥熟料中的四种主要矿物:C3S(45%~65%),C2S(15%~32%),C3A(4%~11%),C4AF(10%~18%)。
另外,还有少量的游离氧化钙,方镁石,含碱矿物以及玻璃体等。
通常,熟料中硅酸三钙和硅酸二钙的含量为75%左右,合称为硅酸盐矿物,它们是熟料中的主要组分,铝酸三钙和铁铝酸四钙含量占22%左右。
在煅烧过程中,它们与氧化镁,碱等在1250~1280度开始,会逐渐熔融成液相以促进硅酸三钙的顺利形成,因而把它们称之为溶剂型矿物。
硅酸盐矿物和溶剂型矿物在熟料中占总量的95%左右。
2.化学成分与矿物组成间的关系熟料中的主要矿物均由各主要氧化物经高温煅烧化合而成,熟料矿物组成取决于化学组成,控制合适的熟料化学成分是获得优质水泥熟料的中心环节,根据熟料的化学成分也可以推测出熟料中各种矿物的相对含量高低。
(一)CaO是水泥熟料中的最重要的化学成分,它能与SiO2,Al2O3,Fe2O3经过一系列复杂的反应过程生成C3S, C2S, C3A C4AF等矿物,适量增加熟料氧化钙含量有利于提高硅酸三钙含量。
但并不是说氧化钙越高越好,因氧化钙过多易造成反应不完全而增加未化合的氧化钙(即游离氧化钙)的含量,从而影响水泥的安定性如果熟料中氧化钙过低,则生成硅酸三钙太少,硅酸二钙却相应增加。
会降低水泥的胶凝性。
(二)SiO2主要在高温作用下与CaO化合形成硅酸盐矿物,因此,熟料中的SiO2必须保证一定的量。
水泥细度检验_筛析法

实验六水泥细度检验——筛析法水泥细度就是水泥的分散度,是水泥厂用来作日常检查和控制水泥质量的重要参数。
水泥细度的检验方法有筛析法、比表面积测定法、颗粒平均直径与颗粒组成的测定等方法。
筛析法是最常用的控制水泥或类似粉体细度的方法之一。
一、实验目的掌握测定硅酸盐水泥经过标准筛进行筛分后的筛余量的方法。
二、实验原理本实验按照国家标准GB/T 1345-2005《水泥细度检验方法筛析法》进行。
用一定孔径的筛子筛分水泥时,留在筛子上面的较粗颗粒占水泥总量的比例,在一定程度上反映了物料的粗细程度。
三、实验设备及材料(一)负压筛法1、仪器设备1.喷气嘴;2.微电机;3.控制板开口;4.负压表接口;5.负压源及收尘器接口;6.壳体图1 负压筛筛座示意图(1)天平:最小分度值不大于0.01g。
(2)负压筛析仪:由筛座、负压筛、负压源及收尘器组成。
其中筛座由转速为30±2 r/min的喷气嘴、负压表、控制板、微电机及壳体等构成(见图1)。
筛析仪负压可调范围为4000~6000Pa。
喷气嘴上口平面与筛网之间距离为2~8mm。
负压源和收尘器由功率≥600w的工业收尘器和小型旋风收尘筒组成或用其他具有相当功能的设备组成。
(3)筛子:采用方孔边长0.080mm的铜丝筛布,筛框上口直径为φ150mm,下口直径为φ142mm,高25mm。
2、硅酸盐水泥样品。
(二)水筛法1、仪器设备(1)天平:最小分度值不大于0.01g 。
(2)筛子:采用方孔边长0.080mm 的铜丝网筛布,筛框有效直径φ125mm,高80mm 。
(3)筛座:用于支承筛子,并能带动筛子转动,转速为50r/min 。
(4)喷头:直径φ55mm,面上均匀分布90个孔,孔径0.5~0.7mm 。
安装高度:喷头底面和筛网之间距离为35~75mm 。
2、硅酸盐水泥样品。
(三)手工干筛法1、仪器设备(1)天平:最小分度值不大于0.01g.。
(2)筛子:采用方孔边长0.08mm 的钢丝网筛布。
- 1、下载文档前请自行甄别文档内容的完整性,平台不提供额外的编辑、内容补充、找答案等附加服务。
- 2、"仅部分预览"的文档,不可在线预览部分如存在完整性等问题,可反馈申请退款(可完整预览的文档不适用该条件!)。
- 3、如文档侵犯您的权益,请联系客服反馈,我们会尽快为您处理(人工客服工作时间:9:00-18:30)。
MgO对水泥熟料煅烧的影响水泥熟料主要成份是CaO、SiO2、Al2O3、Fe2O3等四种化合物,次要成份为MgO、R2O、SO3等化合物,而其中MgO含量允许达到5%,是次要成份中含量最多的一种。
通常人们认为MgO影响水泥产品的安定性,规定了限制值,但实际上MgO在一定程度影响着熟料的煅烧,这种情况往往被忽视。
现根据国内外的研究成果及工厂生产实践,讨论MgO对熟料煅烧及其产品性能的影响,供有关技术人员参考。
1、水泥原料中的MgO水泥生产中,生料中的MgO主要来源于石灰石中的镁质矿物,这些矿物主要以硅酸镁、白云石、菱镁矿、铁白云石等不同类型存在。
当石灰石中MgO以硅酸镁形式存在时,可获得均匀分布和细小(1~5μm)的方镁石晶体,而以白云石或菱镁矿形式存在时,易生成粗大(25~30μm)的方镁石晶体。
我院曾对不同年代所形成的石灰石中MgO含量对熟料强度的影响进行了测试,发现石灰石中MgO的含量对熟料强度有一定的影响,总的趋势是石灰石中MgO含量越高,则熟料强度越低。
根据试验研究,镁质矿物中MgCO3的分解温度为660~700℃,白云石Mg(CO3)2的分解温度为800℃,而石灰石中CaCO3分解温度接近900℃。
在水泥熟料生产过程中,MgO较CaO先形成。
2、MgO对熟料煅烧的影响熟料煅烧时,约有2%的MgO和熟料矿物结合成固熔体,此类固熔体甚多,例如CaO·MgO·SiO2、2CaO·MgO·SiO2、2CaO·MgO·2SiO2、3CaO·MgO·2SiO、7CaO·MgO·2Al2O3、3CaO·MgO·2Al2O3、MgO·Al2O3、MgO·Fe2O3以及C3MS2等,此类化合物的稳定温度在1200~1350℃,同时它还可能含有一些微量元素。
在温度超过1400℃以上时,MgO的化合物会分解,且从熔融物中结晶出来。
当熟料中含有少量细小方镁石晶格的MgO时,它能降低熟料液相生成温度,增加液相数量,降低液相粘度,增加液相表面张力,有利于熟料形成和结粒,也有利于C3S的生成,还能改善熟料色泽。
粗大方镁石晶体的MgO超过2%时,则易形成方镁石晶体,导致熟料安定性不良。
而当氧化镁含量过高时,则易生成大块、结圈和结厚窑皮,以及表面呈液相的熟料颗粒,此类熟料易损坏篦冷机篦板。
3、MgO对熟料结粒的影响3.1影响熟料结粒的因素窑内熟料颗粒是在液相(有些资料称熔体)作用下形成的,液相在晶体外形成毛细管桥。
液相毛细管桥起到两个作用:一是使颗粒结合在一起,另一作用是作为中间介质,使CaO和C2S在熔融态内扩散生成C3S,颗粒的强度取决于毛细管桥的强度,桥的强度即连接颗粒的力随液相表面张力和颗粒直径的降低而增加。
毛细管桥的数量又和颗粒直径的平方根成反比。
要结好粒,必须有足够的液相,并要求颗粒在液相内分布均匀,形成较高的表面张力,较低的液相粘度,适宜的结粒时间和温度等。
3.2MgO对液相性质的影响3.2.1液相量熟料液相量太少不易结粒,太多易结成致密的大块熟料。
液相量与液相中所含的Al2O3、Fe2O3、K2O、Na2O、MgO含量有关。
从近年来国外发表的液相量计算公式中,MgO的系数得以提高,说明MgO对液相量有较大的影响,与Fe2O3的系数接近。
其计算公式为:1400℃时液相量L=3.0Al2O3+2.25Fe2O3+K2O+Na2O+MgO液相量在25~28%时,对结粒最有利。
当MgO含量超过2%以上的值乘以系数1.5。
3.2.2液相表面张力液相表面张力是液相的重要性质,与结粒有着直接的关系。
液相表面张力增大易结粒,熟料颗粒的大小与液相表面张力呈良好的线性关系(见图1)。
图1回转窑内熟料最终尺寸与液相表面张力的关系液相的表面张力与元素外层电子的负电性有关(见图2),有些元素如K、Cl、S的表面张力值较低,不利于结粒;而Mg、Al等元素的表面张力值较高,有利于结粒。
图2液相粘度和表面张力的影响3.2.3液相粘度不同成分熟料的液相粘度值是不同的,一般说来液相粘度值减少,有利于CaO和C2S在液相内扩散生成C3S,也易结粒,液相粘度与温度有关,随温度上升而下降。
几种元素共存的液相粘度值并非单元素的液相粘度值的叠加。
近年来,国内一些单位相继发表了MgO、R2O、SO3对结皮和结粒有较大影响的报导。
为解释此现象,现将MgO-R2O-SO3复合存在时液相等粘度线示于图3。
从图3来看,R2O含量增加,粘度值增加较大,不利于结粒;SO3含量增加,粘度值降低,但SO3的粘度值较R2O低得多,因此SO3存在时结粒有所改善;若R2O、SO3均存在时,MgO含量增加,液相粘度值大大降低,有利于结粒。
图3MgO-R2O-SO3复合存在时液相等粘度线液相的粘度与元素外层电子的负电性有关,液相粘度按它们碱性降低的次序(K-Na-Ca-Mg)逐渐降低,MgO仅对液相粘度有适当的下降(见图2)从一些实验来看,在煅烧的熟料成份中,适量加入Mg2+、SO32-、K-等离子后,熟料的液相表面张力和粘度均发生变化。
Ocoknh所进行的研究表明,熟料在1450℃含25~35%液相时,粘度为0.16Pa.S,表面张力0.58N/m,加入MgO等化合物后的液相表面张力和液相粘度均发生变化,影响着熟料的结粒(见表1)。
此外,除MgO含量对液相表面张力和液相粘度有影响外,还需考虑液相内其他成份的因素。
表1一些氧化物对液相粘度和表面张力的影响氧化物掺加量(%)液相粘度(Pa.s)液相表面张力(N/m)未加-0.160.580MgOK2OK2OSO3、K2O1.01.02.01.930.150.180.240.160.5730.4550.3500.1354、MgO对熟料强度的影响MgO存在于熟料内,会影响CaO的数量,因而MgO在一定程度影响熟料的强度。
为缓和MgO对熟料强度的影响,在水泥熟料生产中,应尽量提高石灰饱和系数KH和硅酸率SM值,相应提高C3S和C2S的含量,以提高熟料的强度。
5、MgO对产品安定性的影响在硅酸盐水泥熟料中,MgO的固熔体总量可达2%,多余的MgO即结晶出来呈游离状方镁石,就会产生有害作用。
熟料中方镁石晶体的生成速度与镁矿物的分解温度有关,分解温度越低,晶体生长的机遇越大。
总的说来,白云石等高镁原料分解温度较高,易生成大晶格的MgO。
方镁石结晶大小随冷却速度不同而变化,快冷时结晶细小,方镁石水化缓慢,要几个月甚至几年才明显起来,水化生成Mg(OH)2时,体积膨胀148%,导致安定性不良。
方镁石膨胀的严重程度与其含量、晶体尺寸等都有关系,方镁石晶体小于1μm且含量为5%时,只引起轻微膨胀,方镁石晶体为5-7μm且含量为3%时,会引起严重膨胀。
6、缓和MgO对生产和产品质量的影响生料的主要成份为CaO、SiO2、Al2O3、Fe2O3四种,在熟料煅烧过程中,主要受由上述四种氧化物组成计算的石灰饱和系数KH、硅酸率SM、铝氧率AM以及SiO2、CaCO3等颗粒级配的影响,也就是生料的易烧性决定了烧成工况。
但是MgO含量较高时,对熟料液相量、液相表面张力、液相粘度以及熟料煅烧温度、熟料结粒、强度以及窑内结圈、结皮等均有影响。
若生产过程中,出现MgO的影响,应从以下几个方面采取减缓措施。
6.1做好生料配料和均化工作:国外公司在研究中提出,在含有MgO的生料内,石灰饱和系数应作如下调整:LSF=100CaO/(2.80SiO2+1.18Al2O3+0.65Fe2O3)(不含MgO)LSF=100(CaO+0.75MgO)/(2.80SiO2+1.18Al2O3+0.65Fe2O3)(MgO<2%)LSF=100(CaO+1.150MgO)/(2.80SiO2+1.18Al2O3+0.65Fe2O3)(MgO>2%)做好原料的均化,确保生料中MgO含量均匀入窑。
6.2控制合适的液相量、液相表面张力、液相粘度液相量是熟料结粒的重要因素,在计算液相量时,应注意MgO超过2%时的校正系数,还应考虑碱含量的因素。
为缓和MgO对液相量的影响,在提高熟料质量的前提下,适当提高石灰饱和系数KH及硅酸率SM值,减少Al2O3和Fe2O3的含量,减缓MgO对液相量的影响,相应减缓结大球的趋势。
同时KH值和SM值增加,增加了CaO、SiO2的含量,也增加了C3S和C2S的生成量及熟料煅烧温度,有利于提高熟料强度。
MgO含量在一定程度影响液相表面张力和液相粘度,影响熟料结粒。
在生产过程中,当出现液相表面张力和液相粘度造成熟料结大球或过细的粉尘熟料时,在调节措施中,可考虑通过调整配料率值对MgO含量进行调节,但应考虑原、燃料带入的碱化物、硫化物等微量元素的影响。
由于各生产线的生料成份不同、配料率值不同,SiO2、CaCO3等颗粒级配不同,MgO的数量及晶体大小不同,碱(R2O)、SO3及微量元素的含量也不一致,再加上液相量、液相表面张力,液相粘度取样和测定的困难,很难在实际生产中进行计算和测试,只能通过分析、判断进行测算,试烧后进行生产。
从国内一些MgO含量较高的生产线的生产情况来看,通过调整KH和SM值,均能生产结粒较好且强度较高的熟料,总体情况总结如下:(1)生料中MgO含量较高且易烧性较好、SiO2的易磨性好且颗粒较细、碱含量与硫含量对液相粘度影响不大时,C2S有利于与CaO结合生成C3S,则SM值可提高至3.60以上,在生产过程中结粒均齐,f-CaO含量较低,熟料强度较高。
(2)生料中MgO含量较高但易烧性较差、SiO2的易磨性差且颗粒较粗、此外原料中带入的碱含量较高时,对液相粘度影响较大,不利于液相内的C2S与f-CaO结合生成C3S。
在生产过程中,为缓和MgO对液相量的影响,可提高SM值;但SM值提高后,更不利于生成C3S,易使f-CaO含量偏高;为降低f-CaO含量,生产时提高烧成温度,但又易增大C3S的晶格易形成飞砂料,不利于熟料强度的提高;这种工况,SM值是很难提高的。
以上情况表明,各条生产线的生料易烧性不一致,其颗粒级配也不一致,石灰石中MgO含量不等且晶体大小有别,另外带入生料的原燃料中碱含量也不一致,此时只能结合实际状况,通过分析,找出优化点,来提高熟料强度。
6.3操作措施(1)在生产过程中,加大窑尾风机风量,尽量减少窑内还原气氛,避免硫酸盐在还原气氛下分解造成窑后部结长厚窑皮,减缓MgO 含量较高窑料出现结圈、结蛋从而进一步加剧窑内通风不良、还原气氛加重的恶性操作状况的产生。
(2)适当加快窑速,减少结厚窑皮的趋势。
(3)避免窑头过烧,减少表面带液相的大块熟料落入篦冷机内损坏前端篦板,或形成表面带液相的大晶格粉状熟料在冷却机进料口处粘结成雪人的事故。