半导体元件生产的简易流程
半导体生产工艺流程
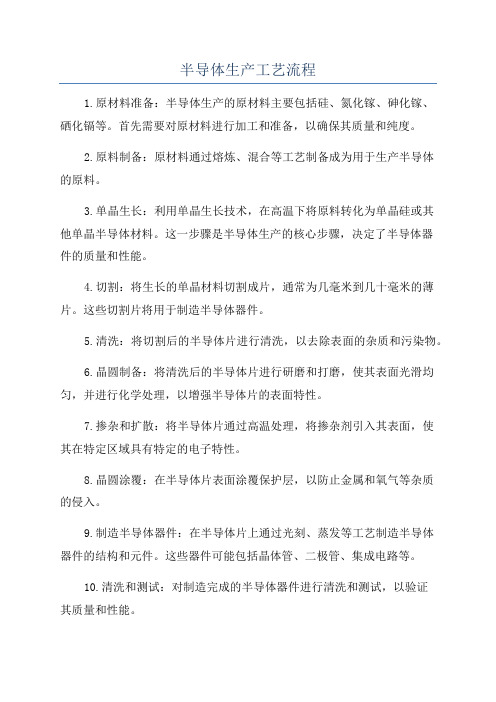
半导体生产工艺流程1.原材料准备:半导体生产的原材料主要包括硅、氮化镓、砷化镓、硒化镉等。
首先需要对原材料进行加工和准备,以确保其质量和纯度。
2.原料制备:原材料通过熔炼、混合等工艺制备成为用于生产半导体的原料。
3.单晶生长:利用单晶生长技术,在高温下将原料转化为单晶硅或其他单晶半导体材料。
这一步骤是半导体生产的核心步骤,决定了半导体器件的质量和性能。
4.切割:将生长的单晶材料切割成片,通常为几毫米到几十毫米的薄片。
这些切割片将用于制造半导体器件。
5.清洗:将切割后的半导体片进行清洗,以去除表面的杂质和污染物。
6.晶圆制备:将清洗后的半导体片进行研磨和打磨,使其表面光滑均匀,并进行化学处理,以增强半导体片的表面特性。
7.掺杂和扩散:将半导体片通过高温处理,将掺杂剂引入其表面,使其在特定区域具有特定的电子特性。
8.晶圆涂覆:在半导体片表面涂覆保护层,以防止金属和氧气等杂质的侵入。
9.制造半导体器件:在半导体片上通过光刻、蒸发等工艺制造半导体器件的结构和元件。
这些器件可能包括晶体管、二极管、集成电路等。
10.清洗和测试:对制造完成的半导体器件进行清洗和测试,以验证其质量和性能。
11.封装和封装测试:将半导体器件封装在塑料或陶瓷封装中,并进行封装测试,以确保器件的可靠性和稳定性。
12.探针测试:将封装好的器件进行探针测试,以验证其电性能和功耗等指标。
13.成品测试和筛选:对探针测试合格的器件进行成品测试和筛选,以确保其质量符合要求。
14.包装和成品测试:将成品封装好,并进行最终的成品测试和筛选,以确保其质量和性能。
15.成品存储和交付:将符合要求的成品进行分类、存储和交付,以供后续使用或销售。
以上是半导体生产工艺流程的主要步骤,其中涉及多种专业技术和设备的应用。
这些步骤的顺序和细节可能会因不同的半导体产品而有所不同,但总体流程是大致相似的。
半导体生产工艺的不断改进和创新,是推动半导体产业发展和技术进步的重要驱动力量。
半导体制造流程详解
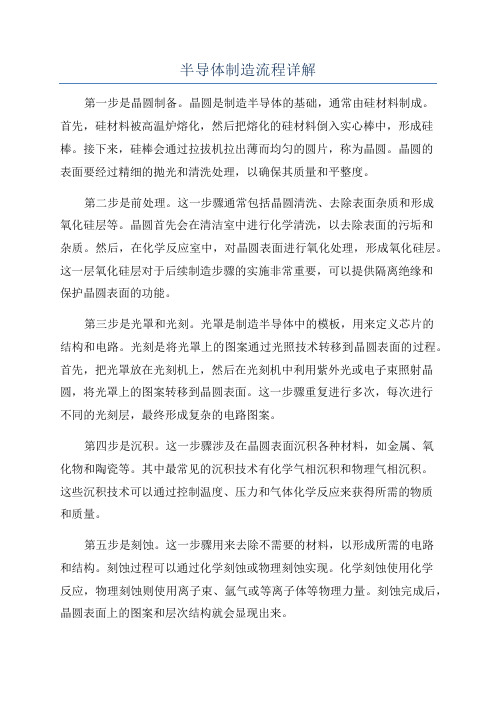
半导体制造流程详解第一步是晶圆制备。
晶圆是制造半导体的基础,通常由硅材料制成。
首先,硅材料被高温炉熔化,然后把熔化的硅材料倒入实心棒中,形成硅棒。
接下来,硅棒会通过拉拔机拉出薄而均匀的圆片,称为晶圆。
晶圆的表面要经过精细的抛光和清洗处理,以确保其质量和平整度。
第二步是前处理。
这一步骤通常包括晶圆清洗、去除表面杂质和形成氧化硅层等。
晶圆首先会在清洁室中进行化学清洗,以去除表面的污垢和杂质。
然后,在化学反应室中,对晶圆表面进行氧化处理,形成氧化硅层。
这一层氧化硅层对于后续制造步骤的实施非常重要,可以提供隔离绝缘和保护晶圆表面的功能。
第三步是光罩和光刻。
光罩是制造半导体中的模板,用来定义芯片的结构和电路。
光刻是将光罩上的图案通过光照技术转移到晶圆表面的过程。
首先,把光罩放在光刻机上,然后在光刻机中利用紫外光或电子束照射晶圆,将光罩上的图案转移到晶圆表面。
这一步骤重复进行多次,每次进行不同的光刻层,最终形成复杂的电路图案。
第四步是沉积。
这一步骤涉及在晶圆表面沉积各种材料,如金属、氧化物和陶瓷等。
其中最常见的沉积技术有化学气相沉积和物理气相沉积。
这些沉积技术可以通过控制温度、压力和气体化学反应来获得所需的物质和质量。
第五步是刻蚀。
这一步骤用来去除不需要的材料,以形成所需的电路和结构。
刻蚀过程可以通过化学刻蚀或物理刻蚀实现。
化学刻蚀使用化学反应,物理刻蚀则使用离子束、氩气或等离子体等物理力量。
刻蚀完成后,晶圆表面上的图案和层次结构就会显现出来。
第六步是清洗和检验。
在制造过程的各个阶段,晶圆表面会沾上各种杂质和残留物。
因此,在完成制造步骤后,晶圆需要经过多次的清洗和检验。
清洗过程会使用酸、碱和溶剂等化学物质,以去除残留物和杂质。
晶圆还要通过光学显微镜和电子显微镜等设备进行质量和结构的检验。
最后一步是封装和测试。
制造完成的芯片需要进行封装,即将芯片连接到适当的封装材料中,并进行密封防护。
然后将封装的芯片连接到电路板上,形成最终的半导体产品。
半导体的生产工艺流程
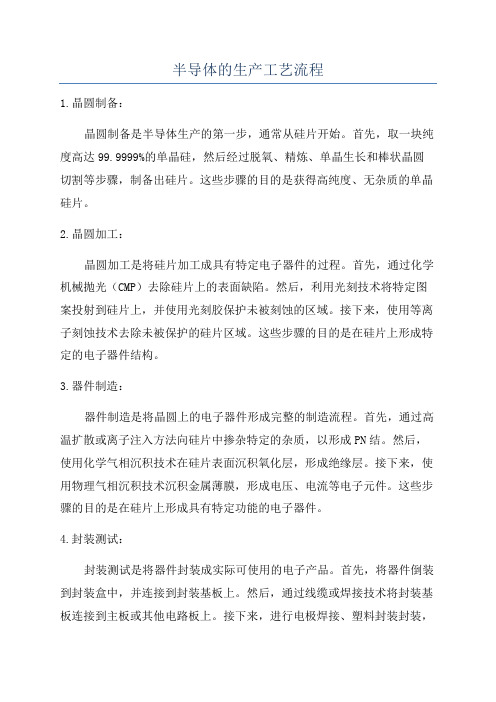
半导体的生产工艺流程1.晶圆制备:晶圆制备是半导体生产的第一步,通常从硅片开始。
首先,取一块纯度高达99.9999%的单晶硅,然后经过脱氧、精炼、单晶生长和棒状晶圆切割等步骤,制备出硅片。
这些步骤的目的是获得高纯度、无杂质的单晶硅片。
2.晶圆加工:晶圆加工是将硅片加工成具有特定电子器件的过程。
首先,通过化学机械抛光(CMP)去除硅片上的表面缺陷。
然后,利用光刻技术将特定图案投射到硅片上,并使用光刻胶保护未被刻蚀的区域。
接下来,使用等离子刻蚀技术去除未被保护的硅片区域。
这些步骤的目的是在硅片上形成特定的电子器件结构。
3.器件制造:器件制造是将晶圆上的电子器件形成完整的制造流程。
首先,通过高温扩散或离子注入方法向硅片中掺杂特定的杂质,以形成PN结。
然后,使用化学气相沉积技术在硅片表面沉积氧化层,形成绝缘层。
接下来,使用物理气相沉积技术沉积金属薄膜,形成电压、电流等电子元件。
这些步骤的目的是在硅片上形成具有特定功能的电子器件。
4.封装测试:封装测试是将器件封装成实际可使用的电子产品。
首先,将器件倒装到封装盒中,并连接到封装基板上。
然后,通过线缆或焊接技术将封装基板连接到主板或其他电路板上。
接下来,进行电极焊接、塑料封装封装,形成具有特定外形尺寸和保护功能的半导体芯片。
最后,对封装好的半导体芯片进行功能性测试和质量检查,以确保其性能和可靠性。
总结起来,半导体的生产工艺流程包括晶圆制备、晶圆加工、器件制造和封装测试几个主要步骤。
这些步骤的有机组合使得我们能够生产出高性能、高效能的半导体器件,广泛应用于电子产品和信息技术领域。
半导体元件生产的简易流程课件
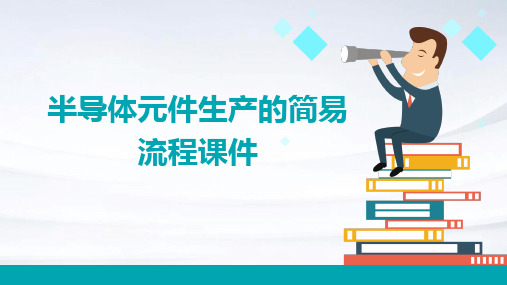
产品测试是质量控制的重要环节之一。通过全面检测产品的性能和可靠性,可以 及时发现和解决潜在问题,提高产品的质量和可靠性。同时,还需要对测试数据 进行深入分析,持续改进生产工艺和流程,提高产品的性能和可靠性。
05 未来发展趋势与挑战
技术创新与进步
纳米技术
人工智能与机器学习
随着纳米技术的不断发展,半导体元 件的尺寸将进一步缩小,提高集成度 和性能。
国际合作与标准制定
积极参与国际环保组织和标准制定机构,推动行业环保标准的制定 和实施。
市场变化与竞争格局
市场需求多样化
随着5G、物联网、人工智能等技 术的普及,半导体元件的市场需
求将呈现多样化趋势。
产业转移
随着全球产业布局的调整,半导体 产业的生产基地可能会向新兴市场 转移,带来新的发展机遇和挑战。
半导体元件的发展历程
总结词
半导体元件的发展历程经历了晶体管的发明、集成电路的出现、微电子技术的进步等重要阶段。
详细描述
晶体管的发明是半导体技术发展的里程碑,随后集成电路的出现将多个晶体管集成在一个芯片上,大 大推动了半导体技术的发展。随着微电子技术的进步,半导体元件的尺寸不断缩小,性能不断提高, 为现代电子工业的发展奠定了基础。
退火技术
总结词
通过退火技术使注入的离子在硅片内部扩散和激活, 以实现掺杂效果。
详细描述
退火技术是半导体制造中的重要步骤,它通过加热使注 入的离子在硅片内部扩散和激活,实现掺杂效果。退火 过程中需要控制温度和时间,以确保掺杂效果符合设计 要求,并保持硅片的完整性。
04 生产过程中的质量控制
原材料的质量控制
详细描述
在清洗过程中,使用特定的化学试剂和工艺去除硅片上的微粒、有机物和其他污 染物。切割则通常使用激光或机械方法将大块硅片切割成更小的片,以便于后续 的加工和制造。
半导体制造主要流程

半导体制造主要流程
半导体是现代电子设备的关键组成部分,它们被广泛应用于计算机、手机、电视和其他电子产品中。
半导体的制造过程是一个复杂而精密的过程,涉及到多个步骤和技术。
下面我们将简要介绍半导体制造的主要流程。
1. 原料准备,半导体的主要原料是硅,通常是以二氧化硅的形式存在。
在制造过程中,硅晶圆被用作半导体芯片的基础。
此外,还需要其他材料,如磷、砷、硼等用于掺杂。
2. 晶圆生长,首先,通过化学气相沉积或其他方法,将硅晶圆表面生长一层细微的氧化硅薄膜。
然后,将硅晶圆放入高温炉中,通过化学反应使硅晶圆表面生长出单晶硅层。
3. 光刻,在光刻过程中,将光刻胶覆盖在硅晶圆表面,然后使用紫外光通过光刻掩膜,将图案投影到光刻胶上。
随后,通过化学处理将光刻胶图案转移到硅晶圆表面。
4. 掺杂和扩散,在这一步骤中,使用离子注入或扩散等技术向硅晶圆中引入掺杂物质,如磷、砷或硼。
这些掺杂物质改变了硅晶
圆的导电性能,形成了半导体材料。
5. 金属化和封装,在这一步骤中,使用金属化工艺在硅晶圆表面沉积金属层,形成电路的连接线。
然后,将硅晶圆切割成单个芯片,并进行封装,以便将芯片连接到电子设备中。
总的来说,半导体制造是一个高度精密和复杂的过程,涉及到多个步骤和技术。
随着科技的不断进步,半导体制造技术也在不断发展和完善,以满足不断增长的电子产品市场需求。
半导体器件制造

半导体器件制造半导体器件是现代电子技术的基础,广泛应用于计算机、通讯、医疗、汽车等各个领域。
而半导体器件的制造过程则是一个复杂而精细的工程,需要经过多个步骤才能得到高质量的产品。
本文将介绍半导体器件制造的一般过程,并深入讨论关键步骤和技术。
一、晶圆制备半导体器件的制造从准备晶圆开始,晶圆是一个平坦的硅片,通常直径为12英寸(300毫米)。
首先,选择高纯度的硅单晶材料作为晶圆的基材,然后通过石墨电弧炉等方法进行熔炼和拉晶,将硅材料拉制成使用尺寸。
二、晶圆清洗晶圆经过初步制备后,需要进行清洗以去除表面的杂质和污染物。
清洗流程一般包括多个步骤,如溶剂洗、酸洗、去膜等。
这些步骤可以确保晶圆表面的纯净度和光洁度达到制造要求。
三、光刻光刻是制造半导体器件中的关键步骤之一,通过光刻技术可以在晶圆表面形成所需的微细结构。
首先,在晶圆表面涂覆一层光刻胶,然后使用掩膜和紫外光刻机将光刻胶暴露于紫外光下,形成所需的图案。
随后,通过显影和清洗等工艺步骤,去除多余的光刻胶,形成希望得到的微细结构。
四、离子注入和扩散离子注入和扩散是控制半导体器件电性能的重要工艺步骤。
通过离子注入,将所需的杂质或离子注入晶圆表面,形成导电或绝缘区域。
而通过扩散,则是在高温下使杂质或离子在晶圆内部扩散,改变晶圆的导电性能。
这些步骤的精确控制和调整对于器件性能至关重要。
五、薄膜沉积薄膜沉积是形成半导体器件的关键步骤之一,通过化学气相沉积或物理气相沉积等方法,在晶圆表面沉积一层薄膜材料,用于形成电极、介电层或其他需要的结构。
沉积薄膜的材料种类繁多,如二氧化硅、聚酰亚胺、金属等,其选择和优化可以有效改善器件的性能。
六、金属线路的制作金属线路的制作是连接和布线半导体器件的重要步骤。
通过光刻和薄膜沉积等技术,在晶圆表面形成金属线路的图案,用于实现电子元器件之间的连接。
这些金属线路通常使用铝、铜或其他导电性能良好的材料制作,而且需要考虑线宽、线距、电阻率等因素。
请简述半导体器件工艺的十大流程
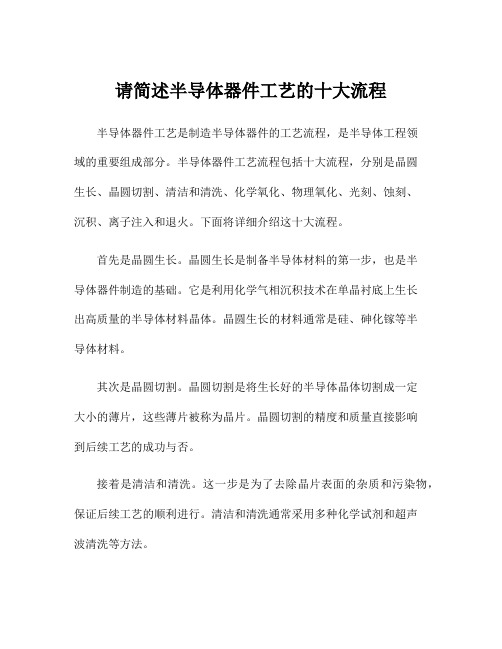
请简述半导体器件工艺的十大流程半导体器件工艺是制造半导体器件的工艺流程,是半导体工程领域的重要组成部分。
半导体器件工艺流程包括十大流程,分别是晶圆生长、晶圆切割、清洁和清洗、化学氧化、物理氧化、光刻、蚀刻、沉积、离子注入和退火。
下面将详细介绍这十大流程。
首先是晶圆生长。
晶圆生长是制备半导体材料的第一步,也是半导体器件制造的基础。
它是利用化学气相沉积技术在单晶衬底上生长出高质量的半导体材料晶体。
晶圆生长的材料通常是硅、砷化镓等半导体材料。
其次是晶圆切割。
晶圆切割是将生长好的半导体晶体切割成一定大小的薄片,这些薄片被称为晶片。
晶圆切割的精度和质量直接影响到后续工艺的成功与否。
接着是清洁和清洗。
这一步是为了去除晶片表面的杂质和污染物,保证后续工艺的顺利进行。
清洁和清洗通常采用多种化学试剂和超声波清洗等方法。
然后是化学氧化和物理氧化。
化学氧化和物理氧化是为了在晶片表面形成一层氧化物膜,以保护晶片表面并提供绝缘层,以便后续形成电路结构。
接下来是光刻。
光刻是一种非常重要的半导体器件制造工艺,它通过选择性照射光源和光刻胶的方式,在晶片表面形成所需的图案。
这是制造半导体器件电路结构的关键步骤。
然后是蚀刻。
蚀刻是利用化学或物理方法去除光刻胶未被照射的部分,从而形成所需的图案。
蚀刻的精度和准确度对电路的性能和稳定性有着很大的影响。
接着是沉积。
沉积是将金属、氧化物等材料以化学气相沉积或物理气相沉积的方式沉积在晶片表面,形成电路结构所需的电极、导线和绝缘层等材料。
然后是离子注入。
离子注入是将掺杂剂以离子束的方式注入晶片内部,改变晶片的电学性能,以形成所需的电子器件。
最后是退火。
退火是通过加热晶片,以改变晶体结构和去除注入后的损伤,提高器件的性能和稳定性。
以上就是半导体器件工艺的十大流程。
这些流程相互关联,缺一不可,任何一步出现问题都会影响整个器件的性能和稳定性。
因此,在实际生产中,需要严格控制每一个环节,不断优化工艺流程,不断提高制造技术水平,以满足市场需求和技术发展的要求。
半导体制造流程范文

半导体制造流程范文1.设计和模拟:半导体制造的第一步是在计算机上进行设计和模拟。
半导体芯片的功能和性能要求在这个阶段确定,并进行电路设计和电子器件模拟。
2.掩膜制作:在实际制造之前,需要制作掩膜,即将设计的电路图案转移到硅片上的光刻掩膜。
这是通过将光刻胶涂在硅片上,然后使用光刻机将掩膜图案转移到光刻胶上完成的。
3.硅片制备:硅片是半导体芯片的基础材料,它需要经过一系列处理步骤来准备。
首先,从高纯度硅中制备出硅片。
然后将硅片进行切割和抛光,使其具有平滑的表面。
4.清洗和去除杂质:硅片需要进行清洗和去除杂质的处理,以确保表面干净。
这可以通过化学方法和高温处理来实现。
5.沉积:在硅片上沉积各种材料的薄膜是半导体制造的一个关键步骤。
这可以通过物理气相沉积或化学气相沉积来实现。
薄膜可以是导电层、绝缘层或其他材料。
6.硅片外延生长:外延生长通过化学气相沉积或分子束外延等方法在硅片上生长晶体。
这使得可以在硅片上生长具有不同晶格结构和成分特性的材料,这对半导体器件的性能和功能至关重要。
7.刻蚀:刻蚀是一种去除不需要的材料的过程,以暴露出需要的电路图案。
通过使用化学蚀刻或物理蚀刻的方法,可以将薄膜或材料从硅片上去除。
8.接触:接触工艺是将金属电极、导线等材料连接到芯片上的过程。
这可以通过金属沉积、光刻和蚀刻等方法完成。
9.封装和测试:在芯片制造的最后阶段,芯片会被封装在塑料或陶瓷封装中,以保护芯片并提供便于连接的引脚。
然后,芯片还会经过一系列测试来确保其质量和性能。
10.成品检验:制造完成的芯片需要经过严格的质量检验来确保其符合设计要求和规范。
这包括功能测试、可靠性测试和封装外观检查等。
11.成品分选和包装:最后,芯片会根据性能和规格进行分选分类,并进行最终的包装处理。
分选是为了满足不同的客户需求和市场需求。
半导体制造流程及生产工艺流程
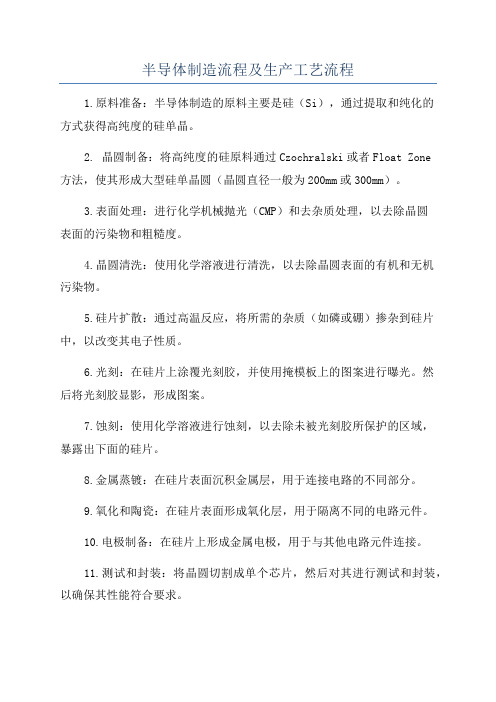
半导体制造流程及生产工艺流程1.原料准备:半导体制造的原料主要是硅(Si),通过提取和纯化的方式获得高纯度的硅单晶。
2. 晶圆制备:将高纯度的硅原料通过Czochralski或者Float Zone方法,使其形成大型硅单晶圆(晶圆直径一般为200mm或300mm)。
3.表面处理:进行化学机械抛光(CMP)和去杂质处理,以去除晶圆表面的污染物和粗糙度。
4.晶圆清洗:使用化学溶液进行清洗,以去除晶圆表面的有机和无机污染物。
5.硅片扩散:通过高温反应,将所需的杂质(如磷或硼)掺杂到硅片中,以改变其电子性质。
6.光刻:在硅片上涂覆光刻胶,并使用掩模板上的图案进行曝光。
然后将光刻胶显影,形成图案。
7.蚀刻:使用化学溶液进行蚀刻,以去除未被光刻胶所保护的区域,暴露出下面的硅片。
8.金属蒸镀:在硅片表面沉积金属层,用于连接电路的不同部分。
9.氧化和陶瓷:在硅片表面形成氧化层,用于隔离不同的电路元件。
10.电极制备:在硅片上形成金属电极,用于与其他电路元件连接。
11.测试和封装:将晶圆切割成单个芯片,然后对其进行测试和封装,以确保其性能符合要求。
以上是半导体制造的主要步骤,不同的半导体产品可能还涉及到其他特定的工艺流程。
此外,半导体制造过程还需要严格的质量控制和环境控制,以确保产品的可靠性和性能。
不同的半导体生产流程会有所不同,但大致上都包含以下几个关键的工艺流程:1. 前端制程(Front-end Process):包括晶圆清洗、来料检测、扩散、光刻、蚀刻、沉积等步骤。
这些步骤主要用于在硅片上形成电子元件的结构。
2. 中端制程(Middle-end Process):包括溅射、化学机械抛光、化学物理蚀刻、金属蒸镀等步骤。
这些步骤主要用于在晶圆上形成连接电子元件的金属线路。
3. 后端制程(Back-end Process):包括划片、电极制备、测试、封装等步骤。
这些步骤主要用于将芯片进行切割、封装,以及测试芯片的性能。
半导体的生产工艺流程(精)

半导体的生产工艺流程(精)什么是半导体半导体是一种电子特性介于导体和绝缘体之间的固体材料。
它具备一部分导体材料的性质,如可对电流进行某种程度上的控制,同时又保留了部分绝缘材料的性质,如电阻值较高。
由于半导体具备这些特性,它成为了现代电子工业中不可或缺的材料之一。
半导体生产的基本流程半导体的生产工艺流程日趋复杂,但基本的工艺流程依然是从硅田采购到成品的集成电路,一般包含以下几个基本步骤:1.半导体材料生长2.晶圆加工3.掩膜制作4.晶圆刻蚀5.金属化6.化学机械研磨7.微影光刻8.其他工序如离子注入、退火等半导体材料生长半导体材料生长是制造半导体器件的第一步。
硅材料生长主要采用CVD或单晶生长法,CVD是一种化学气相沉积方法,通过反应气体在衬底表面沉积。
而锗的生长则使用另一种方法——分子束外延法,将纯净的气态的锗芯片熔化以后喷到介质上,并通过化学反应来沉积到介质表面。
相比之下,单晶生长法是生长单晶硅的主要方法,它使铸锭通过高温坩埚中的液体硅进行熔硅石化学反应,得到单晶硅,并通过磨削和切割等多个工艺步骤得到晶圆。
晶圆加工晶圆加工是将生长出的单晶硅切成薄片(通常厚度为0.3~0.75mm),通过化学改性等方式得到半导体材料。
该过程中硅片会被加热,然后用钨丝切成薄片,一般需要晶片翻转,重复切削,直至得到标准的直径200mm或更大的薄片。
掩膜制作光刻技术是制造集成电路的核心工艺之一。
它通过将光刻胶覆盖在晶圆表面,然后将加工好的掩膜对准涂有光刻胶的晶片,利用紫外线照射胶层,然后用化学方法去除未凝固的光刻胶,实现对半导体片的局部改性。
晶圆刻蚀刻蚀是制造半导体器件的另一个核心工艺之一。
该工艺主要通过使用化学液体或离子束等方法进行化学或物理改性,以清除不需要的表面材料,留下所需形状的导电区域和非导电区域。
通常包括干法刻蚀、湿法刻蚀和离子束刻蚀等方法。
金属化金属化是将晶圆表面金属化来保护芯片和连接电路,通常采用电子束蒸发或物理气相沉积等方式将金属材料加热,使其蒸发后再沉积在晶圆表面。
(工艺流程)最简易的半导体制造工艺流程

半导体制造工艺流程N型硅:掺入V族元素-- 磷P、砷As、锑Sb P 型硅:掺入III 族元素—镓Ga、硼BPN结:半导体元件制造过程可分为前段(FrontEnd )制程晶圆处理制程(WaferFabrication ;简称WaferFab)、晶圆针测制程(WaferProbe);後段(BackEnd)构装(Packaging )、测试制程(InitialTestandFinalTest )一、晶圆处理制程晶圆处理制程之主要工作为在矽晶圆上制作电路与电子元件(如电晶体、电容体、逻辑闸等),为上述各制程中所需技术最复杂且资金投入最多的过程,以微处理器(Microprocessor )为例,其所需处理步骤可达数百道,而其所需加工机台先进且昂贵,动辄数千万一台,其所需制造环境为为一温度、湿度与含尘(Particle )均需控制的无尘室(Clean-Room),虽然详细的处理程序是随著产品种类与所使用的技术有关;不过其基本处理步骤通常是晶圆先经过适当的清洗(Cleaning )之後,接著进行氧化(Oxidation )及沈积,最後进行微影、蚀刻及离子植入等反覆步骤,以完成晶圆上电路的加工与制作。
二、晶圆针测制程经过WaferFab 之制程後,晶圆上即形成一格格的小格,我们称之为晶方或是晶粒(Die ),在一般情形下,同一片晶圆上皆制作相同的晶片,但是也有可能在同一片晶圆上制作不同规格的产品;这些晶圆必须通过晶片允收测试,晶粒将会一一经过针测(Probe)仪器以测试其电气特性,而不合格的的晶粒将会被标上记号(InkDot ),此程序即称之为晶圆针测制程(WaferProbe)。
然後晶圆将依晶粒为单位分割成一粒粒独立的晶粒三、IC 构装制程IC 構裝製程(Packaging ):利用塑膠或陶瓷包裝晶粒與配線以成積體電路目的:是為了製造出所生產的電路的保護層,避免電路受到機械性刮傷或是高溫破壞。
半导体制造工艺分类半导体制造工艺分类一双极型IC 的基本制造工艺:A 在元器件间要做电隔离区(PN结隔离、全介质隔离及PN结介质混合隔离)ECL(不掺金)(非饱和型)、TTL/DTL(饱和型)、STTL(饱和型)B 在元器件间自然隔离I2L (饱和型)半导体制造工艺分类二MOSIC的基本制造工艺:根据栅工艺分类A铝栅工艺B硅栅工艺其他分类1、(根据沟道)PMO、S NMO、S CMOS2、(根据负载元件)E/R、E/E、E/D 半导体制造工艺分类三Bi-CMOS工艺:A 以CMOS工艺为基础P 阱N阱B以双极型工艺为基础双极型集成电路和MOS集成电路优缺点半导体制造环境要求主要污染源:微尘颗粒、中金属离子、有机物残留物和钠离子等轻金属例子。
半导体制备工艺流程

半导体制备工艺流程1.原材料准备:首先,需要准备半导体材料的原料,如硅、锗等。
这些原料通常以多晶体或单晶体的形式存在,并需要进行纯化和化学处理,以去除杂质和提高纯度。
2. 制备单晶体:在这一步骤中,需要通过一种称为Czochralski方法的技术,将纯化后的原料制备成单晶体。
该方法利用一个熔融的原料,通过加入引导晶体和控制温度的方式,使晶体在慢慢生长的过程中形成。
3.切割晶片:获得的单晶体需要进行切割,以获得具有所需尺寸和形状的晶片。
这通常通过使用金刚石工具进行切割,因为金刚石具有很高的硬度,可以有效地切割晶体。
4.磨削和研磨:切割后的晶片可能会有表面不平整或粗糙的问题,需要进行磨削和研磨处理。
这一步骤将使用机械磨削和化学机械研磨的方法,逐渐将晶片表面磨平和研磨至所需的光洁度和平整度。
5.清洗和去除杂质:在晶片表面研磨完成后,需要进行清洗和去除杂质的处理。
这一步骤通常使用酸、溶剂或等离子体处理,以去除表面的有机和无机杂质,并提高单晶片的表面质量和净化度。
6.氧化处理:经过清洗和净化的单晶片需要进行表面氧化处理,以形成一层氧化膜。
氧化处理可以通过热氧化或湿氧化的方法进行,其中热氧化是利用高温下的氧气将晶片表面氧化,而湿氧化则是在有水蒸汽的条件下进行。
7.控制掺杂:在制备半导体器件时,通常需要对晶片进行掺杂处理,以改变其电子性能。
掺杂可以通过离子注入或扩散的方式进行,其中离子注入将所需的杂质离子直接注入晶片中,而扩散则是将杂质担体直接接触至晶片表面,然后通过高温处理使其扩散至晶片内部。
8.图案化处理:在制备半导体芯片时,需要根据所需的电路设计,在晶片表面进行图案化处理。
这一步骤通常包括光刻、蚀刻、沉积和清洗等工艺步骤,以逐步形成器件所需的结构和层次。
9.金属化处理:在芯片制备的最后阶段,需要进行金属化处理,以将电路连接至芯片的引脚或电极。
这一步骤通常涉及金属沉积、刻蚀和清洗等工艺步骤,以形成电路和引脚之间的良好电气连接。
半导体制造主要流程
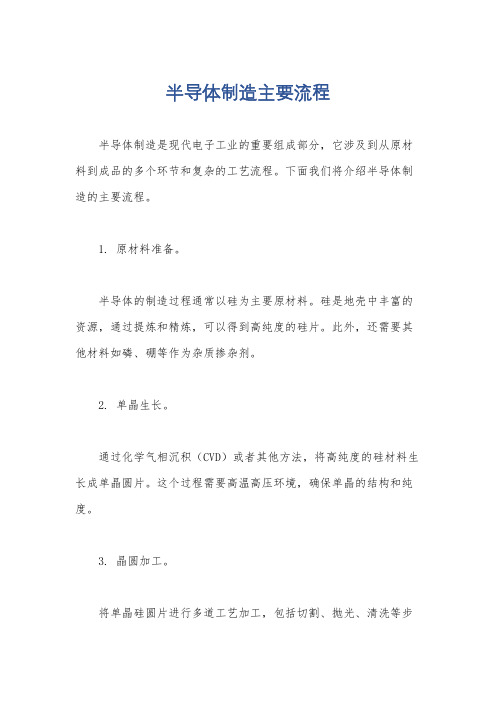
半导体制造主要流程
半导体制造是现代电子工业的重要组成部分,它涉及到从原材料到成品的多个环节和复杂的工艺流程。
下面我们将介绍半导体制造的主要流程。
1. 原材料准备。
半导体的制造过程通常以硅为主要原材料。
硅是地壳中丰富的资源,通过提炼和精炼,可以得到高纯度的硅片。
此外,还需要其他材料如磷、硼等作为杂质掺杂剂。
2. 单晶生长。
通过化学气相沉积(CVD)或者其他方法,将高纯度的硅材料生长成单晶圆片。
这个过程需要高温高压环境,确保单晶的结构和纯度。
3. 晶圆加工。
将单晶硅圆片进行多道工艺加工,包括切割、抛光、清洗等步
骤,最终得到薄而均匀的晶圆。
4. 掺杂。
通过掺入磷、硼等杂质,改变硅的导电性质,形成N型和P型
半导体材料。
5. 晶体管制造。
在晶圆上制造晶体管,包括光刻、蚀刻、沉积等工艺,将导电
性区域和绝缘区域精确地形成。
6. 封装测试。
将晶体管封装到芯片内,进行测试和封装成最终的半导体器件。
以上就是半导体制造的主要流程,这是一个高度精密和复杂的
过程,需要先进的设备和技术,同时也需要严格的质量控制和环境
管理。
半导体制造的发展推动了现代电子科技的进步,也为人类社
会的发展带来了巨大的便利和进步。
半导体制造工艺流程
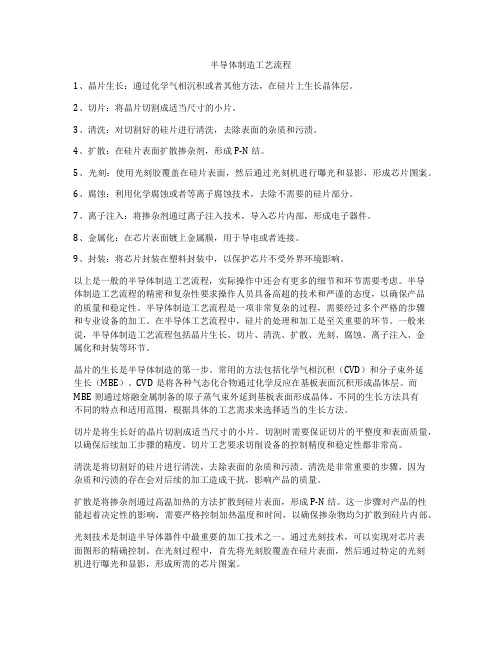
半导体制造工艺流程1、晶片生长:通过化学气相沉积或者其他方法,在硅片上生长晶体层。
2、切片:将晶片切割成适当尺寸的小片。
3、清洗:对切割好的硅片进行清洗,去除表面的杂质和污渍。
4、扩散:在硅片表面扩散掺杂剂,形成P-N结。
5、光刻:使用光刻胶覆盖在硅片表面,然后通过光刻机进行曝光和显影,形成芯片图案。
6、腐蚀:利用化学腐蚀或者等离子腐蚀技术,去除不需要的硅片部分。
7、离子注入:将掺杂剂通过离子注入技术,导入芯片内部,形成电子器件。
8、金属化:在芯片表面镀上金属膜,用于导电或者连接。
9、封装:将芯片封装在塑料封装中,以保护芯片不受外界环境影响。
以上是一般的半导体制造工艺流程,实际操作中还会有更多的细节和环节需要考虑。
半导体制造工艺流程的精密和复杂性要求操作人员具备高超的技术和严谨的态度,以确保产品的质量和稳定性。
半导体制造工艺流程是一项非常复杂的过程,需要经过多个严格的步骤和专业设备的加工。
在半导体工艺流程中,硅片的处理和加工是至关重要的环节。
一般来说,半导体制造工艺流程包括晶片生长、切片、清洗、扩散、光刻、腐蚀、离子注入、金属化和封装等环节。
晶片的生长是半导体制造的第一步。
常用的方法包括化学气相沉积(CVD)和分子束外延生长(MBE)。
CVD是将各种气态化合物通过化学反应在基板表面沉积形成晶体层。
而MBE则通过熔融金属制备的原子蒸气束外延到基板表面形成晶体。
不同的生长方法具有不同的特点和适用范围,根据具体的工艺需求来选择适当的生长方法。
切片是将生长好的晶片切割成适当尺寸的小片。
切割时需要保证切片的平整度和表面质量,以确保后续加工步骤的精度。
切片工艺要求切削设备的控制精度和稳定性都非常高。
清洗是将切割好的硅片进行清洗,去除表面的杂质和污渍。
清洗是非常重要的步骤,因为杂质和污渍的存在会对后续的加工造成干扰,影响产品的质量。
扩散是将掺杂剂通过高温加热的方法扩散到硅片表面,形成P-N结。
这一步骤对产品的性能起着决定性的影响,需要严格控制加热温度和时间,以确保掺杂物均匀扩散到硅片内部。
半导体六大制造工艺流程
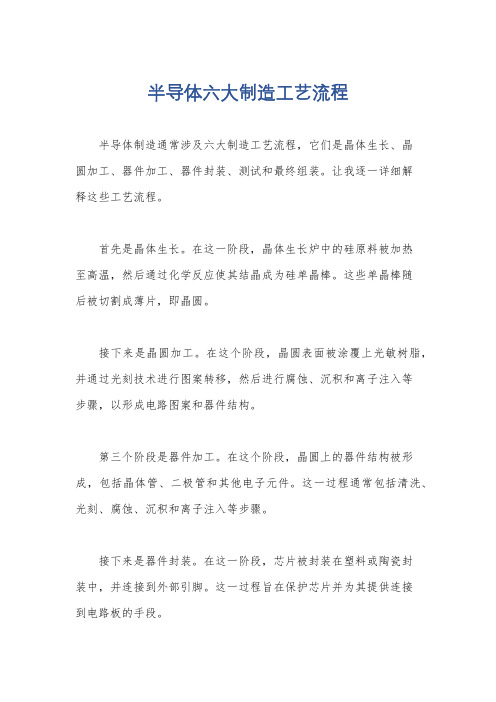
半导体六大制造工艺流程
半导体制造通常涉及六大制造工艺流程,它们是晶体生长、晶
圆加工、器件加工、器件封装、测试和最终组装。
让我逐一详细解
释这些工艺流程。
首先是晶体生长。
在这一阶段,晶体生长炉中的硅原料被加热
至高温,然后通过化学反应使其结晶成为硅单晶棒。
这些单晶棒随
后被切割成薄片,即晶圆。
接下来是晶圆加工。
在这个阶段,晶圆表面被涂覆上光敏树脂,并通过光刻技术进行图案转移,然后进行腐蚀、沉积和离子注入等
步骤,以形成电路图案和器件结构。
第三个阶段是器件加工。
在这个阶段,晶圆上的器件结构被形成,包括晶体管、二极管和其他电子元件。
这一过程通常包括清洗、光刻、腐蚀、沉积和离子注入等步骤。
接下来是器件封装。
在这一阶段,芯片被封装在塑料或陶瓷封
装中,并连接到外部引脚。
这一过程旨在保护芯片并为其提供连接
到电路板的手段。
第五个阶段是测试。
在这一阶段,封装的芯片将被测试以确保
其功能正常。
这可能涉及电学测试、可靠性测试和其他类型的测试。
最后一个阶段是最终组装。
在这一阶段,封装的芯片被安装到
电路板上,并连接到其他组件,如电源、散热器等。
这一阶段也包
括整个产品的最终组装和包装。
总的来说,半导体制造的六大工艺流程涵盖了从原材料到最终
产品的整个生产过程,每个阶段都至关重要,对最终产品的质量和
性能都有着重要的影响。
半导体制造的工艺流程
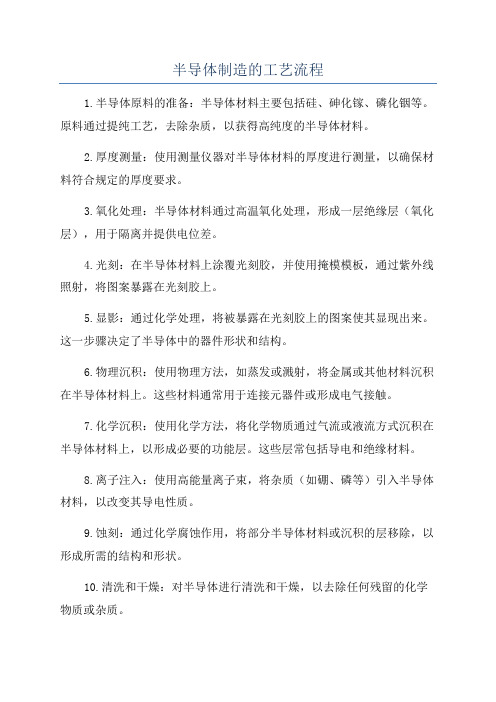
半导体制造的工艺流程
1.半导体原料的准备:半导体材料主要包括硅、砷化镓、磷化铟等。
原料通过提纯工艺,去除杂质,以获得高纯度的半导体材料。
2.厚度测量:使用测量仪器对半导体材料的厚度进行测量,以确保材料符合规定的厚度要求。
3.氧化处理:半导体材料通过高温氧化处理,形成一层绝缘层(氧化层),用于隔离并提供电位差。
4.光刻:在半导体材料上涂覆光刻胶,并使用掩模模板,通过紫外线照射,将图案暴露在光刻胶上。
5.显影:通过化学处理,将被暴露在光刻胶上的图案使其显现出来。
这一步骤决定了半导体中的器件形状和结构。
6.物理沉积:使用物理方法,如蒸发或溅射,将金属或其他材料沉积在半导体材料上。
这些材料通常用于连接元器件或形成电气接触。
7.化学沉积:使用化学方法,将化学物质通过气流或液流方式沉积在半导体材料上,以形成必要的功能层。
这些层常包括导电和绝缘材料。
8.离子注入:使用高能量离子束,将杂质(如硼、磷等)引入半导体材料,以改变其导电性质。
9.蚀刻:通过化学腐蚀作用,将部分半导体材料或沉积的层移除,以形成所需的结构和形状。
10.清洗和干燥:对半导体进行清洗和干燥,以去除任何残留的化学物质或杂质。
11.终测和选判:对半导体器件进行电性能测试,以确保其质量和性能满足规定的要求。
12.封装和测试:将半导体芯片封装在塑料或陶瓷封装中,并对封装完成的器件进行功能测试。
半导体器件制造方法
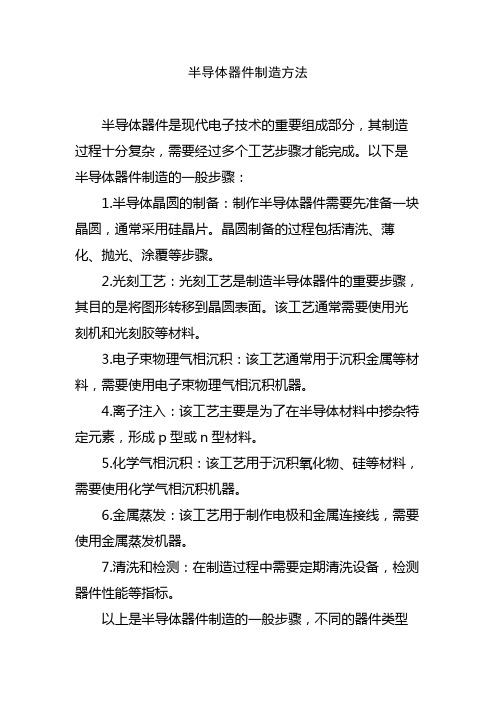
半导体器件制造方法
半导体器件是现代电子技术的重要组成部分,其制造过程十分复杂,需要经过多个工艺步骤才能完成。
以下是半导体器件制造的一般步骤:
1.半导体晶圆的制备:制作半导体器件需要先准备一块晶圆,通常采用硅晶片。
晶圆制备的过程包括清洗、薄化、抛光、涂覆等步骤。
2.光刻工艺:光刻工艺是制造半导体器件的重要步骤,其目的是将图形转移到晶圆表面。
该工艺通常需要使用光刻机和光刻胶等材料。
3.电子束物理气相沉积:该工艺通常用于沉积金属等材料,需要使用电子束物理气相沉积机器。
4.离子注入:该工艺主要是为了在半导体材料中掺杂特定元素,形成p型或n型材料。
5.化学气相沉积:该工艺用于沉积氧化物、硅等材料,需要使用化学气相沉积机器。
6.金属蒸发:该工艺用于制作电极和金属连接线,需要使用金属蒸发机器。
7.清洗和检测:在制造过程中需要定期清洗设备,检测器件性能等指标。
以上是半导体器件制造的一般步骤,不同的器件类型
和制造工艺可能会有所不同。
在制造过程中需要严格的质量控制和安全措施,以确保器件的性能和可靠性。
半导体生产流程
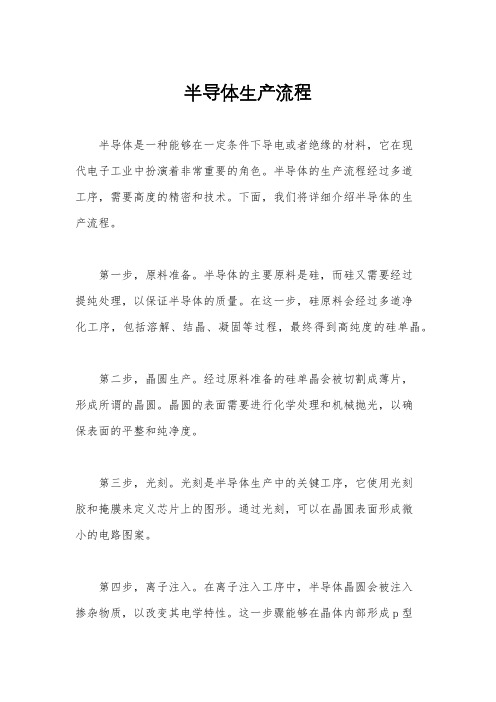
半导体生产流程半导体是一种能够在一定条件下导电或者绝缘的材料,它在现代电子工业中扮演着非常重要的角色。
半导体的生产流程经过多道工序,需要高度的精密和技术。
下面,我们将详细介绍半导体的生产流程。
第一步,原料准备。
半导体的主要原料是硅,而硅又需要经过提纯处理,以保证半导体的质量。
在这一步,硅原料会经过多道净化工序,包括溶解、结晶、凝固等过程,最终得到高纯度的硅单晶。
第二步,晶圆生产。
经过原料准备的硅单晶会被切割成薄片,形成所谓的晶圆。
晶圆的表面需要进行化学处理和机械抛光,以确保表面的平整和纯净度。
第三步,光刻。
光刻是半导体生产中的关键工序,它使用光刻胶和掩膜来定义芯片上的图形。
通过光刻,可以在晶圆表面形成微小的电路图案。
第四步,离子注入。
在离子注入工序中,半导体晶圆会被注入掺杂物质,以改变其电学特性。
这一步骤能够在晶体内部形成p型和n型半导体区域,从而形成晶体管和二极管等元件。
第五步,薄膜沉积。
在薄膜沉积工序中,半导体晶圆会被涂覆上一层薄膜,通常是氧化层或者氮化层。
这些薄膜可以用来隔离不同的电路元件,或者作为绝缘层。
第六步,金属化。
在金属化工序中,半导体晶圆的表面会被涂覆上金属层,通常是铝或者铜。
这些金属层可以用来连接不同的电路元件,形成完整的电路结构。
第七步,封装测试。
最后,半导体芯片会被封装在塑料或者陶瓷封装体中,以保护其免受外部环境的影响。
之后,芯片会被进行测试,以确保其性能和质量符合标准要求。
总的来说,半导体的生产流程经过多道工序,需要高度的精密和技术。
每一个工序都对半导体的质量和性能有着重要的影响,因此在生产过程中需要严格控制每一个环节,以确保最终产品的质量和可靠性。
半导体生产流程
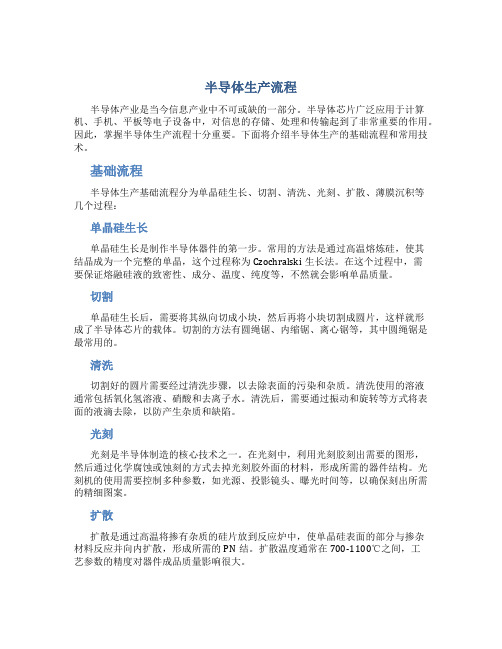
半导体生产流程半导体产业是当今信息产业中不可或缺的一部分。
半导体芯片广泛应用于计算机、手机、平板等电子设备中,对信息的存储、处理和传输起到了非常重要的作用。
因此,掌握半导体生产流程十分重要。
下面将介绍半导体生产的基础流程和常用技术。
基础流程半导体生产基础流程分为单晶硅生长、切割、清洗、光刻、扩散、薄膜沉积等几个过程:单晶硅生长单晶硅生长是制作半导体器件的第一步。
常用的方法是通过高温熔炼硅,使其结晶成为一个完整的单晶,这个过程称为Czochralski生长法。
在这个过程中,需要保证熔融硅液的致密性、成分、温度、纯度等,不然就会影响单晶质量。
切割单晶硅生长后,需要将其纵向切成小块,然后再将小块切割成圆片,这样就形成了半导体芯片的载体。
切割的方法有圆绳锯、内缩锯、离心锯等,其中圆绳锯是最常用的。
清洗切割好的圆片需要经过清洗步骤,以去除表面的污染和杂质。
清洗使用的溶液通常包括氧化氢溶液、硝酸和去离子水。
清洗后,需要通过振动和旋转等方式将表面的液滴去除,以防产生杂质和缺陷。
光刻光刻是半导体制造的核心技术之一。
在光刻中,利用光刻胶刻出需要的图形,然后通过化学腐蚀或蚀刻的方式去掉光刻胶外面的材料,形成所需的器件结构。
光刻机的使用需要控制多种参数,如光源、投影镜头、曝光时间等,以确保刻出所需的精细图案。
扩散扩散是通过高温将掺有杂质的硅片放到反应炉中,使单晶硅表面的部分与掺杂材料反应并向内扩散,形成所需的PN结。
扩散温度通常在700-1100℃之间,工艺参数的精度对器件成品质量影响很大。
薄膜沉积薄膜沉积是制造半导体器件的另一个重要工艺。
该方法被应用在淀粉糖、硅酸盐和其他高技术行业中。
薄膜用于电容器、数据储存等各种各样的应用中。
化学气相沉积和物理气相沉积是两种主要的薄膜沉积技术。
常用技术半导体制造技术有许多种类,这里列出一些重要的技术。
暴露在制备半导体处理器时,将电路图案透过掩膜映射在感光剂上,然后暴露于紫外线下,以形成图案。
- 1、下载文档前请自行甄别文档内容的完整性,平台不提供额外的编辑、内容补充、找答案等附加服务。
- 2、"仅部分预览"的文档,不可在线预览部分如存在完整性等问题,可反馈申请退款(可完整预览的文档不适用该条件!)。
- 3、如文档侵犯您的权益,请联系客服反馈,我们会尽快为您处理(人工客服工作时间:9:00-18:30)。
滴有凝胶(solder)的框架 wafer
日本 NEC
Die bond完成品
3 连线(Wire bond)
用金线.铜线或铝线做导线把chip上的线路与框架的管脚进行连接,从而行 成元件的各个电极。 金线稳定性最好,但做大功率管时需要线数多,成本较高,所以 现在不少产品改为铝线和铜线。
阳极 阴极 控制极 门极gate 源极source
1 晶圆切割(sawing)
把整片晶片切割成一个独立的单元 Chip ; Die。 首先要进行贴膜,把晶圆贴在蓝色的膜(wafer tube)上,以膜为载体, 以便切割。 通过自动切片机按照要求的尺寸来进行切割。有的产品在切片之前还要进 行晶圆背面的打磨。使其厚度达到要求,晶圆不能太薄以免在运输过程中 破碎。常用全自动切片机日本的 Disco。 晶圆材料主要用的模具
待注模产品
5 镀锡(Planting)
用镀锡机对元件的裸铜管脚进行镀锡。 主要目的是防止管脚氧化而影响元件性能。
裸铜框架
框架镀锡
6 切筋(tram form)
分割成独立的元件,对剩余部分进行加工形成元件的管脚。 T/F所用设备多以PLC为控制单元,通过电磁阀的通.断来控制汽缸的动作, 完成工作。
晶圆
经贴膜.切割后的晶片 (wafer)
Die
2 贴片(Die bond )
把chip 粘贴到铜框架上. 切好的晶圆放到贴片机上,通过真空(collect)把晶片吸起然后粘贴在滴有凝胶的铜 框架上。常用的凝胶有两种:Epoxy,solder。Solder产品贴片后可直接进行下一 工序焊线;Epoxy产品需要加热凝固后才可进行焊线。 目前大芯片贴片机常用瑞士的 ESEC; 小芯片.LED等贴片常用新加坡的 ASM. 日本的佳能(Canon)
一.测试工程
测试工程主要分为三部分
打印 (Marking)
测试 (Test)
包装 (Packing)
7 打印(marking)
激光打印机(Laser Marking)在产品外壳上打印上 客户名称,产品型号等。
8 测试(Final Test)
对元件的各种性能.参数进行最终测试,检出不良品并记录不良类型。 采用电磁振动螺旋型的料盘把散装的被测元件整理成有序的排列,然后 依次送到测试点,在测试位上安装有电磁发生器,电磁发生器的磁场大 小和方向受测试系统控制。测试系统对被测器件进行电性能测试,分选 系统再把测试完的元件按测试结果分类放到对应的料桶里。
半导体元件生产的简易流程
封装.测试
一.封装工程
封装总的分为两大工程:前工程(FRONT END)
后工程 (BACK END)
贴膜 切片 贴片 焊线 打印 切筋 镀锡 注膜 测试 包装
前工程主要分三大部分
晶圆切割 (Wafer Sawing)
贴片 (Die bond )
连线 (Wire bond)
示意图
铝 线
金线
Wire bond 主要设备:高精密超声波焊线机。
美国 Kns
日本 kaijo
基本原理通过超声波发生器(USG)产生的超声波振动来进行连接。 可以生产大功率MOS管.LED. IC .BGA 等产品。一般可连接的线径为(15um——50um)。
后工程主要三大部分
注模 (Molding )
镀锡 (Planting)
切筋(Trim Form)
4 注模(Molding)
用注模机对wire bond 的完成品进行封装形成元件的壳体。 基本原理是利用塑料的热塑性,把EMC(环氧塑封料)加热融化后,加 以高的压力使其快速流入密闭的模腔,经一段时间的保压和冷却,开模 成型。
日本 TOWA
注膜完成品 Molding完成品
进料端 测试点 测试系统
常用设备韩国的SE-TECH
Bin
9 包装(packing)
最后对产品进行包装。 有的设备可以对元件的打印.测试.包装一起完 成。